Generar Planes Óptimos de Inspección a Equipos Estáticos y Tuberías de Proceso con base en la metodología de Inspección Basada en Riesgo.
Articulo22 de junio de 2022
Resumen
La Inspección Basada en Riesgo es un enfoque sistemático basado en las normas API-RP-580 y 581, y soportado en otros estándares, que tiene como objetivo: mitigar el riesgo de los equipos estáticos y tuberías de las instalaciones estudiadas, mediante la optimización de las inspecciones, al establecer frecuencias y alcances con base en la valoración del comportamiento histórico, mecanismos de deterioro, factores de daño, características de diseño, condiciones de operación, mantenimiento, inspección y políticas gerenciales, en conjunto con, la calidad y efectividad de las inspecciones, y las consecuencias asociadas a las potenciales fallas. Así mismo, optimiza los programas de inspección en marcha, al determinar los puntos mínimos de inspección requeridos por componente, con base en los mecanismos de deterioro, niveles de riesgos y velocidades de corrosión.
Esta valoración prioriza los componentes, mediante el cálculo de la probabilidad (estableciendo los lazos de corrosión e identificando potenciales mecanismos de deterioro de acuerdo con API-RP-571) y consecuencia de la pérdida de contención, (con base en los grupos de inventario) para cada uno de sus componentes; proporcionando la ubicación de un nivel de riesgo, en una matriz 5 x 5, a fin de reducir el riesgo a través de las inspecciones, para incrementar la seguridad de la instalación, al mitigar el riesgo, mejorar de forma costo-efectiva los recursos de inspección, evaluar requerimientos para incrementar o reducir los ciclos de inspección y proponer recomendaciones para reducir el riesgo a niveles aceptables y optimizar futuras inspecciones o su efectividad.
Palabras Claves
Condición, Consecuencia, CoF, CML, Equipo, Estático, Grupo de Inventario, IBR, Inspección, Inspección en Marcha, Lazo de Corrosión, Mantenimiento, Monitoreo de Condición, Optimización, PoF, Probabilidad, Punto de Medición, Riesgo, TML, Tubería de Proceso.
1. Introducción
Una de las mayores preocupaciones de la industria actual está asociada con el diseño, selección y determinación de adecuadas políticas y estrategias de mantenimiento e inspección de los equipos estáticos y tuberías de proceso, enfocándose en el estudio del deterioro de la pared del recipiente que puede resultar en la pérdida de la función de contención de un fluido o una fuga del producto al medio ambiente con sus respectivas consecuencias; como: comprometer la seguridad del personal, originar paradas del proceso, incurrir en costos por daños ambientales, pérdidas de productos y reparación o remplazo del área afectada del recipiente.
Lo anterior, origina la necesidad de reducir los niveles de riesgos asociados mediante la implementación de metodologías y técnicas que permiten controlar, optimizar, prevenir y predecir la ocurrencia de una falla en equipos estáticos y tuberías; al aplicar la metodología de Inspección Basada en Riesgo (IBR) para generar planes óptimos de inspección, con base en las normas internacionales API-RP-580 y 581, con el soporte de otras normas, como: API-570, 571, 574, 579, 650, 653, 1160 y ASME B31.3, 31.4, 31.8 y 31.8S, así como, procedimientos de ingeniería o estándares de los propietarios de los activos evaluados.
La metodología de IBR se aplica tanto a equipos estáticos (recipientes a presión, intercambiadores, torres, y tanques de almacenamiento) como a circuitos de tuberías de proceso, con el objetivo de valorar los niveles de riesgo de cada equipo, basados en la caracterización de la condición actual, mecanismos de degradación o deterioro, características de diseño, condiciones de operación, calidad y efectividad de las actividades de mantenimiento e inspección y de las políticas gerenciales; así como, las consecuencias asociadas a las potenciales fallas.
Una vez definida la jerarquización de los equipos o tuberías de acuerdo con su nivel de riesgo, se determinan las actividades de inspección y frecuencias (fechas de ejecución), considerando los mecanismos de deterioro presentes y como punto final se realiza una optimización del programa de inspección en marcha, que permite determinar la cantidad requerida de puntos de inspección para cada equipo o circuito de tuberías. El riesgo es un término de naturaleza probabilística, que se define como “egresos o pérdidas probables, consecuencia de la posible ocurrencia de un evento no deseado o falla”; coexistiendo la posibilidad de que un evento se haga realidad o se satisfaga, con las consecuencias que de ello ocurran. En tal sentido, el riesgo asociado a una decisión o evento viene dado matemáticamente, por la expresión universal:
Riesgo(t) = Probabilidad de Falla(t) x Consecuencias. Ec. 1
Con base en la cual se observa que el nivel de riesgo puede ser variable, de acuerdo con una disminución o incremento de la probabilidad o frecuencia de falla, o disminuyendo o incrementando las consecuencias, y de acuerdo con la experiencia sobre la determinación del riego, las acciones dirigidas a disminuir la probabilidad de ocurrencia de fallas son más factibles que las dirigidas a disminuir las consecuencias, misma que involucra mayores inversiones, esfuerzos y decisiones gerenciales.
El análisis del riesgo (Ec. 1), permite comprender su poder, como indicador para diagnosticar situaciones y tomar decisiones, al comparar escenarios que pueden resultar similares, pero que bajo ciertas circunstancias deben evaluarse y considerar en un proceso de toma de decisiones; como distinguir entre una acción de mantenimiento con frecuencias de fallas bajas, aun cuando presenta altas consecuencias.
Los análisis de inspección basados en riesgo (IBR) requieren la caracterización del riesgo con base en el cálculo de probabilidades de falla, considerando, el espesor remanente, la velocidad de corrosión, y la calidad y frecuencia de inspección; mientras que, para el cálculo de las consecuencias, se considera, entre otros el tipo de fluido, los sistemas de mitigación existentes y el inventario de producto (volumen contenido) en el componente evaluado, tal como se muestra en la Figura 1.
Utilizar una matriz de riesgo de rango 5 x 5, tal como se muestra en la Figura 2, permite ubicar gráficamente del nivel de riesgo de los componentes analizados y que puede presentar cuatro (4) niveles de clasificación: bajo (verde), medio (amarillo), medio-alto (naranja) y alto riesgo (rojo).
El producto de los valores de la probabilidad de falla y consecuencias (lados de la matriz) permiten determinar el nivel de riesgo asociado a cada componente (equipo o circuito de tubería), generando una lista jerarquizada de componentes basadas en el riesgo calculado, utilizada para diseñar y optimizar los planes de inspección.


2. Metodología
Una vez delimitado o seleccionado los sistemas, subsistemas, equipos o circuitos de tuberías a los cuales se les aplicara la metodología de Inspección Basada en Riesgo (IBR), la Figura 3 muestra las principales etapas y fases para la aplicación del IBR a fin de generar planes óptimos de inspección a equipos estáticos y tuberías de proceso.

2.1. Recolectar Información Técnica.
Se debe recolectar, capturar y evaluar los datos técnicos e información necesaria para establecer la base de datos necesaria para el análisis tomando en consideración la información relativa al diseño, fabricación, instalación, operación, mantenimiento e inspección de los equipos y tuberías de proceso de la instalación.
La Tabla 1 muestra, como ejemplo, la estructura de una base de datos utilizada para organizar la información requerida por el software o herramienta de cálculo necesaria para determinar los niveles de riesgo de los equipos y circuitos de tuberías, y mantener un registro de las fuentes consultadas. La revisión y captura de los datos es una etapa en la que es posible cometer errores, siendo necesario los procedimientos que permitan asegurar de calidad de los datos necesarios para desarrollar el análisis.

Entre las fuentes de información más importante para el desarrollo de este análisis, se encuentran: los diagramas de flujo de proceso (DFP’s o PFD’s), diagramas de tubería e instrumentación (DTI’s o P&ID’s), selección de materiales, planos localización general (PLG) o “plot plant”, isométricos, historia y registro de inspecciones realizadas, caracterización de los fluidos de los sistemas, hojas de especificación de equipos, hojas de seguridad de las substancias de proceso, filosofía de operación, bitácora o reportes de mantenimiento, estudios previos de riesgo y cualquier otra información técnica que contribuya al desarrollo del estudio.
2.2. Validar / Actualizar la Información
Se debe asegurar que la información recopilada (datos) se validada y este actualizada, actividad a ejecutarse por personas debidamente capacitadas en áreas y equipos específicos, para el beneficio y calidad de los análisis.
La necesidad de asegurar la información, es múltiple, dado que pueden existir documentos, diagramas y datos no actualizados, que no reflejen la realidad de la instalación, la falta de trazabilidad de las inspecciones, errores en el registro de los datos o malas lecturas por parte de los inspectores u otras posibles fallas que puedan afectar negativamente la exactitud de los resultados del análisis, para lo cual se deben hacer todos los esfuerzos que permitan reducir las posibles fuentes de error, realizando, entre otras actividades, las siguientes:
- Verificación en campo de los diagramas e isométricos.
- Reuniones de validación con los expertos de mantenimiento e inspección de cada área.
- Verificación de las variables operacionales con los expertos de operaciones y procesos.
- Comparar las magnitudes de las velocidades de corrosión registradas con base a las inspecciones y las registradas en bibliografía o Instalaciones similares.
- Recorrido para levantamiento y validación de datos de campo.
La actualización de la información se limita a considerar todas las líneas y equipos existentes en las instalaciones y descartar aquellos que han sido retiradas de servicio, con el fin de generar los planes de inspección y acciones de mantenimiento acordes a la realidad operacional, evitando así generar planes y acciones no necesarias, o el almacenamiento y análisis de datos que presente un menor nivel de certeza o sean menos confiables.
2.3. Sistematización de la Instalación.
El proceso de sistematización consiste en la división de una instalación o grupo de unidades menores de proceso para facilitar su análisis y evaluación. La unidad de estudio será el equipoo circuito de tubería de proceso, para lo cual se toman en cuenta los conceptos de lazos de corrosión y de grupo de inventario.
2.3.1. Lazos de Corrosión (CL).
Los lazos de corrosión (CL, por sus siglas en inglés) son indispensables para la determinación de la probabilidad de falla y por definición se establece que los equipos o tuberías de proceso asociados a un mismo lazo de corrosión consideran similares: (1) tipo de materiales, (2) condiciones operacionales, (3) fluidos manejados, (4) condiciones ambientales y (5) mecanismos de deterioro.
Por lo tanto, para establecer los lazos de Corrosión se deben identificar y evaluar los mecanismos de daño presentes o potenciales en cada uno de los componentes, con base en la Norma API-RP-571, misma que permite evaluar las variables principales necesarias para determinar la existencia o no de un mecanismo de deterioro particular, ya sea que esté presente o sea potencialmente factible.
Entre las principales consideraciones para establecer los lazos de corrosión, se tienen:
- Condiciones de operación y Composición química de la sustancia manejada.
- Tipo de servicio de circuito y/o equipo.
- Materiales de construcción.
- Localización de válvulas de corte o aislamiento.
- Tipo de componente, ya sea equipo de proceso o circuito de tubería.
- Aislamiento térmico.
En tal sentido, la Figura 4 muestra un ejemplo del establecimiento de un lazo de corrosión indicado sobre un Diagrama de Flujo de Proceso (DFP), con seis (6) lazos de corrosión, considerando once (11) diferentes mecanismos de daño.

Por tanto, un lazo de corrosión es una forma práctica de describir, comprender y verificar los mecanismos de degradación en una instalación y consta de un grupo de activos (sistema de tuberías y equipos) agrupados con condiciones de proceso similares, construidos de materiales similares y que comparten amenazas similares de corrosión/degradación. o mismos mecanismos de daño activos/potenciales (DM, por sus siglas en inglés) según lo indicados en los estándares:
- ASME PCC-3 Tabla A-1.
- API-RP-580: Risk Based Inspection, Apéndice A-Mecanismos de Deterioro.
- API-RP-571: Mecanismos de Daño que Afectan Equipos Fijos en la Industria de Refinación.
De los cuales los mecanismos de daño por fabricación de soldadura están fuera del alcance de la mayor parte de los IBR.
El mecanismo de daño (DM) es un fenómeno que induce cambios micro y/o macro nocivos para el material, los cuales son perjudiciales para la condición del material o sus propiedades mecánicas. Los mecanismos de daño suelen ser incrementales, acumulativos e irrecuperables, y comúnmente están asociados con:
- Adelgazamiento,
- Ataque químico,
- Fluencia o “creep”,
- Erosión,
- Fatiga,
- Fractura,
- Fragilización o “embrittlement”,
- Envejecimiento térmico.
Para comprender los mecanismos de daño es importante analizar la probabilidad de falla, la selección de intervalos, ubicaciones y técnicas de inspección apropiados; la capacidad de tomar decisiones (por ejemplo, modificaciones al proceso, selección de materiales, monitoreo) que puedan eliminar o reducir la probabilidad de un mecanismo de daño específico.
Además, la identificación de los mecanismos de daño y modos de falla creíbles para el equipo incluido en un análisis de riesgo es esencial para la calidad y la efectividad del análisis de riesgo.
Las directrices establecidas permitirán: asegurar un riesgo mínimo previsible sobre la seguridad y la confiabilidad; asegurar la máxima esperanza de vida de los equipos o identificar áreas de aplicaciones de nuevas tecnologías.
2.3.2. Grupo de Inventario (IG)
Los grupos de inventario (IG por sus siglas en inglés) se definen como un grupo de equipos y tuberías de proceso que pueden ser aislados de manera manual o remota, mediante válvulas, y donde se asume que, el volumen total del grupo de inventario está potencialmente disponible para fugar por cualquiera de los componentes que lo conforman, en caso de que se presente una pérdida de contención o fuga al ambiente; lo cual se utiliza en el cálculo de las consecuencias, ya sea por área o financiera (dependiendo del tipo de equipo en análisis).
Entre las principales consideraciones para establecer los grupos de inventario, se tienen:
- Los sistemas de detección.
- Los sistemas de mitigación.
- Los sistemas de aislamiento (válvulas).
- Localización de válvulas de corte o aislamiento, las cuales serán los elementos que definirán los límites de grupo de inventario, preferiblemente se considerarán en el siguiente orden: (1) válvulas de bloqueo automáticas, (2) válvulas de bloqueo manuales, (3) válvulas de seguridad y en última instancia (4) válvulas de retención.
- Se asume que el “dueño” de un grupo de inventario es el equipo estático de mayor relevancia dentro del IG.
- Un equipo puede estar conformado por varias tuberías de diferentes diámetros, las cuales se identificarán como circuitos, es decir, que una sección de tubería que pueda ser aislada es considerada un equipo para su evaluación individual al igual que un recipiente u otro equipo estático.
- Los sistemas de tuberías y filtros “pequeños” generalmente forman parte de un grupo de inventario mayor, nunca generaran nombres del grupo, a excepción de tuberías o cabezales principales, los cuales se consideran como dueño de su propio grupo de inventario.
En tal sentido, la Figura 11 presenta un par de ejemplos asociados con los grupos de inventario sobre Diagramas de Tuberías e Instrumentación (DTI), donde se pueden observar los componentes de cada uno de grupos de inventario (IG) así como las válvulas consideradas límite de batería de cada IG.
Con la sistematización, cada componente (equipo o circuito de tubería) es una unidad de estudio de riesgo y le corresponde un plan de inspección particular, dependiendo de la cantidad y tipos de mecanismos de deterioro que pueda presentarse. Así mismo, se debe establecer una taxonomía para mantener una estructura reproducible, confiable y ordenada que permita identificar los lazos de corrosión y los grupos de inventarios que se han clasificado y numerado para cada caso.

2.3.3. Valorar los Mecanismos de Deterioro
Para la identificación y evaluación de los mecanismos de deterioro, se debe analizar el efecto del daño producido, durante la operación e inspección, sobre la probabilidad de la detección de los defectos, en tal sentido, se deben ejecutar, entre otros pasos, los siguientes:
- Determinar la velocidad y severidad del daño.
- Determinar el nivel de confianza en la severidad de los daños.
- Determinar la eficacia de los programas de inspección.
- Calcular el efecto del programa de inspección en el mejoramiento del nivel de determinación de los daños.
- Calcular la probabilidad que un nivel dado de daño excederá la tolerancia del componente resultando en una falla.
- Calcula los factores de daño.
- Calcular el factor de daño total para los mecanismos de daño presente y potenciales.
2.4. Análisis de Riesgo
El análisis de riesgo está dirigido a los componentes de los equipos y circuitos de tuberías, que permite determinar el riesgo con base en lo indicado por la norma API-RP-581, permitiendo la planificación de actividades asociadas con la detección de mecanismos específicos de deterioro o daño, que utiliza para obtener una calificación del riesgo de manera determinística, considerando criterios de aceptación de riesgos y plan de inspección.
El análisis de riesgo se centra en la estimación de los factores que modifican la frecuencia de fallas y las zonas afectadas por la posible fuga de producto liberado al medio ambiente, como resultado de la pérdida de la función de contención del equipo o tubería de proceso.El análisis determina en primero lugar un factor que representa la probabilidad de la falla y posteriormente permite valorar un factor para las consecuencias. Ambos se combinan en una matriz de riesgo (5 x 5) para establecer el nivel de riesgo de cada componente.
2.4.2. Probabilidad de Falla (PoF).
Para el cálculo de la probabilidad de falla (PoF) se considera el procedimiento indicado en la sección 4 de la práctica recomendada API-RP-581 mediante la Ecuación 2:

Donde:

La base de datos de la frecuencia de falla genérica se basa en una compilación de expedientes disponibles de las historias de la falla de varios tipos de componentes (equipo y circuitos de tubería de diferentes diámetros), en operación en diversas instalaciones de petróleo y gas que han sido desarrolladas para cuatro (4) diferentes tamaños de agujeros, en caso de eventos de fuga (¼”, 1”, 4” y ruptura total). Como uso más generalizado se cuenta con las evidencias de fallas presentada en la tabla 4.1 “Suggested Component Generic Failure Frequencies”, del API-RP-581, 2da Edición, Sep-2008. Sin embargo, en los casos donde se disponga de suficiente historial de fallas para un componente dado, se puede calcular la frecuencia de falla real.
Para el cálculo del Factor de Daño se utilizan métodos sistemáticos que determinar el efecto de los mecanismos de deterioro específicos, bajo condiciones de funcionamiento normales y extremas, que afectan la probabilidad de la falla de cada componente, estableciendo los factores de daño en las condiciones en que operando el equipo, cuantificado la eficacia del programa de inspección ejecutado (en caso de existir) y calculando los factores de modificación de la frecuencia de falla genérica que apliquen.
Para algunos mecanismos de deterioro existe un índice del daño que modifica significativamente la mayor frecuencia de falla a condiciones extremas, diferentes a las condiciones normales de operación, tales como variaciones de la temperatura o cambios anormales en las concentraciones de un contaminante particular en el fluido procesado y que pueden ocurrir durante periodos de cambios en las condiciones operacionales o durante los arranques y paradas de proceso.
Para analizar el efecto del daño producido en servicio y el efecto de la inspección en la probabilidad de la falla, se debe:
- Determinar la velocidad y severidad del daño.
- Determinar el nivel de confianza en la severidad de los daños.
- Determinar la eficacia de los programas de inspección.
- Calcular el efecto del programa de inspección en el mejoramiento del nivel de determinación de los daños.
- Calcular la probabilidad de que un nivel dado de daño exceda la tolerancia del daño del equipo resultando en una falla.
- Calcular los factores de daño.
- Calcular el factor de daño total para todos los mecanismos de daño.
La norma API-RP-581 considera principalmente los siguientes factores de daño en base a los mecanismos de deterioro:
- Adelgazamiento por corrosión/erosión (presencia de revestimientos internos).
- Agrietamiento por corrosión bajo esfuerzos, SCC (Stress Corrosion Cracking).
- Daño externo.
- Ataque por hidrógeno a alta temperatura, HTHA.
- Fractura frágil.
- Fatiga mecánica.
Dichos factores de daño se pueden consultar en la parte 2 de las normas API-RP-581, donde se establece la correspondiente evaluación de cada mecanismo, presente o potencial en cada componente del proceso. Por lo tanto, si más de uno de los tipos generales de daño está potencialmente presente, los factores de daño individuales deben ser sumados, tal como se indica en la ecuación 3.

Para cada uno de los factores de daño, existe un flujograma de toma de decisiones donde se indica la información de proceso y mantenimiento, empleada para determinar el tipo de mecanismo de deterioro presente en cada equipo. Los aspectos teóricos y detalles de cada mecanismo de deterioro están especificados en la norma API-RP-571 “Damage Mechanisms Affecting Fixed Equipment in the Refining Industry”.De igual manera, se debe cuantificar la efectividad del programa de inspección, basado en la determinación de las técnicas de inspección más recomendables ejecutar para cada mecanismo de deterioro identificado. La efectividad de la inspección permite medir la capacidad de cada técnica de inspección o ensayo no destructivo, para detectar el mecanismo de daño que se puede presentar. En tal sentido, la norma API-RP-581 / Parte 2 presenta las tablas 5.5 a 5. 10, que indica las guías de asignación de la efectividad de inspección para los principales mecanismos de deterioro.
Para la determinación del Factor del Sistema Gerencial, se sigue para aquellas empresas que no lo tiene definido, el procedimiento propuesto en el Anexo 2.a. del API-RP-581 y el cual evalúa trece (13) aspectos:
- Liderazgo y administración.
- Información sobre seguridad de procesos.
- Análisis de peligros de proceso.
- Gerencia del cambio.
- Procedimientos operacionales.
- Prácticas de trabajo seguro.
- Capacitación o Entrenamiento.
- Integridad mecánica.
- Revisión de seguridad previo al arranque.
- Respuesta a emergencias.
- Investigación de incidentes.
- Contratistas.
- Evaluación del Sistema de Gerencia o Auditorias.
La Figura 12 muestra un gráfico tipo “araña” en el cual se presentan los resultados del análisis necesario para determinar el factor del sistema Gerencial con base en el Anexo 2.a. del API-RP-581.

2.4.2. Consecuencia de la Falla (CoF).
Con respecto al otro lado de la matriz de riesgo se debe calcular las consecuencias (CoF), ya sean con base en el área de afectación (pie2/año) o en base financiera (USD/año), considerando lo indicado por la Norma API-RP-581 / Parte 3, tomando en cuenta aspectos como: naturaleza de la falla, cantidad del fluido liberado; velocidad de fluido liberado en función del tamaño del agujero (¼”, 1”, 4” y ruptura total), viscosidad del fluido, densidad y presión de operación, consecuencias hacia las personas (basado en el número de víctimas potenciales), consecuencias ambientales basada en el costo de posibles derrames (saneamiento, recolección, penalizaciones, etc.) y consecuencias de perdida de producción que en caso necesario puede ser estimados empleando la tabla 5.17: “Estimated Equipment Outage” (Norma API-RP-581 / Parte 2).
Como referencia, la rotura de una tubería de alta presión de gran diámetro o de un recipiente a presión, obviamente, tiene una consecuencia diferente de una fuga en una tubería de baja presión de menor diámetro.
En todo caso, las consecuencias totales (Área o Financieras) son definidas como la sumatoria de cada una de las consecuencias de acuerdo con lo indicado en la Ec. 4.

2.4.3. Matriz de Riesgo.
El nivel de riesgo se calcula combinando la probabilidad de falla (PoF) con la consecuencia de la falla (CoF) de cada componente, ubicándolos en una matriz de riesgo de 5 x 5, tal como se muestra en la Figura 13 que presenta un ejemplo de matriz de riesgo para consecuencias en área (equipos y tuberías) o consecuencias financieras (tanques).

Cursos recomendados




%252FImagen%252FRAMPREDYC-1730060420837.webp%3Falt%3Dmedia%26token%3D2634a7f0-988e-4022-b91f-382503e6e9db&w=3840&q=75)



2.5. Diseño de los Planes de Inspección.
Una vez identificados los factores de daño de cada equipo podrá identificarse cuál es la influencia de cada uno de ellos en la probabilidad de falla, así como el efecto del alcance y la efectividad de las actividades de inspección adecuadas en la probabilidad de detectar la manifestación del daño. Para ello, la norma API-RP-581, especifican las actividades de inspección, su alcance y frecuencias de aplicación de acuerdo a los mecanismos de deterioro presentes y su crecimiento en el tiempo.
El propósito de un plan de inspección es definir las actividades necesarias para detectar el deterioro en servicio de los componentes antes de que se produzcan las fallas. Adicionalmente se identifican actividades de mantenimiento u otras acciones de mitigación de riesgo que puedan ser aplicadas.
La concepción de una estrategia de reducción de riesgo de equipos estáticos a través de la metodología inspección basada en riesgo, sólo surtirá efecto si las actividades que han sido identificadas como las de mejor efecto de reducción de riesgo, son aplicadas. Para lo cual se recomienda establecer un mecanismo de control de las recomendaciones derivadas de los análisis a fin de garantizar su cumplimiento.
La Tabla 2 y la Tabla 3, muestran un plan de inspección recomendado para equipo de proceso y tanque de almacenamiento de hidrocarburo, respectivamente; mientras que la Tabla 4 muestra un análisis costo-riesgo-beneficio (ACRB), de la forma en que se puedan realizar las actividades de inspección y las acciones de mantenimiento, mediante la cuantificación y asignación de los recursos, para tanques de almacenamiento de hidrocarburos (HC), que muestra el beneficio al considerar la extensión de los intervalos de inspección controlando adecuadamente el riesgo.



2.6. Análisis de Resultados.
Como producto de las experiencias obtenidas durante la aplicación de la Inspección Basada en Riesgo, se muestran a continuación imágenes de los diferentes productos y resultados obtenidos haciendo uso de programas y herramientas computacionales licenciatarios y propios, basado en la normativa aplicable.
La Figura 14 muestra el resultado del análisis de riesgo, donde se observa la cantidad de componentes para cada nivel de riesgo dentro de la Matriz. Así mismo, se observa una proyección de la distribución de los niveles de riesgo de los componentes si el plan de inspección es o no es ejecutado implementado, que en conjunto con la distribución porcentual de los niveles de riesgo y el efecto de la ejecución o no del plan de inspección recomendado (Ver Tabla 6), facilitan la adecuada toma de decisiones para la implementación del plan de inspección resultante de la aplicación de la Inspección Basada en Riesgo para Equipos Estáticos.


La Figura 15 muestra un caso específico de la evaluación de riesgo para tanques de Almacenamiento de hidrocarburos, en donde se puede ver los niveles de riesgo financieros y su ubicación de acuerdo con un límite de riesgo aceptable para el propietario de los activos y que en conjunto con los resultados mostrados en la Tabla 3 y la Tabla 4, permiten recomendar extensiones en los periodos de inspección y sus consecuentes beneficios financieros mostrados.

La Figura 16 muestra en forma general una lámina de la presentación de final de resultados de la aplicación de la Inspección Basada en Riesgo.

2.7. Optimización de los Programas de Inspección en Marcha.
Una vez desarrollado los planes de inspección para cada uno de los equipos o tuberías y dependiendo del cliente se ejecuta la optimización del Programa de Inspección en Marcha, el cual consiste en optimizar la cantidad de puntos de inspección (CML’s) para cada componente (equipo o circuito de tubería), de acuerdo con los mecanismos de deterioro presentes y niveles de riesgo.
Este proceso se realiza de acuerdo con los procedimientos de ingeniería establecidos por los clientes, en particular los del Medio Oriente.
En tal sentido, la Tabla 6 muestra un resumen de los resultados del proceso de Optimización como referencia.

2.8. Ejecutar Planes de Inspección.
Se deben ejecutar los planes de inspección detallados para cada equipo y tubería de proceso, incluyendo:
- Método de inspección (VT, UT, RT, etc.)
- Alcance de la aplicación de los métodos de inspección (% total de área examinada, etc.)
- Fecha próxima de inspección (indicado en el plan de Inspección).
De igual manera las técnicas de inspección normalmente se refieren a la evaluación de la calidad de alguna característica en relación con un estándar o una especificación, considerando:
1. Equipo:
- Inspección visual (VT),
- Medición de espesor aleatorio por ultrasonido (UT)
- Prueba de partículas magnéticas fluorescentes húmedas (WFMPT)
- Se usan comúnmente para verificar la corrosión localizada y el agrietamiento ambiental.
2. Tubería de Proceso: se usan varias técnicas para medición de espesor por:
- Ultrasónico aleatorio (UT),
- Onda de corte UT (UTSW) de soldaduras
- Radiografía (RT)
- Se utilizan para detectar pérdida de metal, corrosión preferencial de soldadura y agrietamiento fino.
Ejemplo de las recomendaciones para la inspección son:
- Para internos: Realizando 10% MFL de tubos, 100% VT con mediciones aleatorias de UT o 50% VT y UT aleatoria.
- Para externos: 50% UTT de CML’s; El 100% de las LMC utilizan UTSW manual, AUT o radiografía.
- Para CUI: inspección visual 100% externa y 100% perfil o radiografía en tiempo real de daño o área sospechosa.
2.9. Monitoreo y Mejora Continua.
Para cerrar el ciclo y continuar con la mejora continua, una vez se obtengan los resultados de implantar los planes de inspección y acciones de mantenimiento recomendadas, se deben evaluar y revisar los indicadores claves de desempeño y retroalimentar el proceso.
En resumen, los principales productos de la aplicación de la metodología de IBR, se tienen:
- La Jerarquización del riesgo de todos los equipos evaluados.
- La descripción de otras actividades de mitigación (reparaciones, reemplazos o mejoras en la seguridad).
- Métodos, alcance y fechas aproximadas de inspección
- Los niveles de riesgo de todos los equipos y tuberías de proceso antes y después que la inspección y otras actividades de mitigación han sido implementadas.
- Equipos con posibilidades de extender su intervalo de Inspección.
3. Beneficios.
Entre los principales beneficios obtenido, se encuentran:
- Definir y calificar los niveles de riesgo de los equipos y tuberías de proceso, antes y después que la inspección.
- Identificar potencial reducción de pérdidas de producción durante las inspecciones en marcha.
- Aumentar confianza en la integridad y confiabilidad de los equipos y tuberías de proceso.
- Minimizar riesgos para la salud, seguridad y medio ambiente.
- Maximizar utilización de recursos y optimización de puntos de inspección.
- Mejorar eficiencia operativa.
- Métodos, alcance y fechas aproximadas de inspección
- Componentes con posibilidades de extensión del intervalo de Inspección.
- Recomendación de otras actividades de mitigación (reparaciones, reemplazos o mejoras en la seguridad).
4. Conclusiones.
Con base en lo documentado previamente para generar planes óptimos de inspección a equipos estáticos y tuberías de proceso, con base en la metodología de Inspección Basada en Riesgo (IBR), se tienen las principales conclusiones son:
- La Inspección Basada en Riesgo (IBR), permite determinar los niveles de riesgo de los equipos y circuitos de tuberías, así como evaluar las posibilidades de reducción de riesgo de estos y también determinar los beneficios económicos de la implementación de los planes de inspección recomendados por estos análisis.
- Esta metodología permite el direccionamiento de los recursos a las áreas, plantas, sistemas o equipos en donde se encuentra los mayores niveles de riesgo de la instalación analizada.
- La metodología de IBR permite: integrar las evaluaciones económicas en conjunto con los análisis de riesgos de los equipos evaluados en estos estudios, facilitando así la toma de decisiones para determinar la mejor estrategia de inspección de los equipos.
- La metodología de IBR tiene la facilidad de realizar estudios de análisis costo-riesgo-beneficio de los planes de inspección para aplicaciones específicas como tanques.
- Como aspecto innovador con estos estudios se logran optimizar los programas de inspección en marcha y así determinar la cantidad de puntos de inspección requeridos para cada equipo o circuito de tubería analizado.
5. Referencias Bibliográficas y Abreviaturas.
Las principales referencias bibliográficas y abreviaturas a considerar para generar planes óptimos de inspección a equipos estáticos y tuberías de proceso, con base en la metodología de Inspección Basada en Riesgo (IBR), son las siguientes:
- API-510.- Pressure Vessel Inspection Code: Maintenance Inspection, Rating, Repair, and Alteration
- API-570.- Piping Inspection Code Inspection, Repair, Alteration, and Rerating Of In-Service Piping Systems.
- API-571.- Damage Mechanisms Affecting Fixed Equipment in the Refining Industry.
- API-574.- Inspection Practices for Piping System Components.
- API 579.- Fitness-for-Service.
- API-RP-580.- Risk-Based Inspection
- API-RP-581.- Risk-Based Inspection Base Resource Document
- API 650.- Welded Steel Tanks for Oil Storage.
- API 653.- Tank Inspection, Repair, Alteration and Reconstruction.
- API 1160.- Mananging System Integrity for Hazardous Liquid Pipelines.
- ASME Secc. VIII Div. I.- Boiler And Pressure Vessel Code.
- ASME B31.3.- Process Piping.
- ASME B31.G.- Manual for dtermining the remaining strength of corroded pipelines.
- ASME B31.4.- Pipeline transportation system for liquid hydrocarbons & other liquids.
- ASME B31.8.- Gas Transmission And Distribution Piping System
- ASME B31.8S.- Supplement to B31.8 on Managing System Integrity of Gas Pipeline.
- DNV-RP-G101.- Risk Based Inspection Of Offshore Topsides Static Mechanical Equipment.
- DS/CWA-15740: Risk-Based Inspection and Maintenance Procedures for European Industry (RIMAP)
- UNE-16991: Marco de la Inspección Basada en el Riesgo.
CML “Condition Monitoring Location” o Localización de Monitoreo de Condición.
CL “Corrosion Loop” o Lazos de Corrosión.
CoF “Consequence of Failure” o Consecuencia de Falla.
ACRB Análisis Costo-Riesgo-Beneficio.
CUI “Corrosion Under Insulation” o Corrosión bajo el aislamiento.
DFP Diagrama de Flujo de Procesos o PFD: “Process Flow Diagram”.
DM “Damage Mechanics” o Mecanismo de daño.
DTI Diagrama de Tubería e Instrumentación o PID: “Process and Instrumentation Diagram”.
HAZ “Heat Affected Zone” o Zona afectada por el calor de soldadura.
IBR Inspección Basada en Riesgo.
IG “Inventory Group” o Grupo de inventario
MCC Mantenimiento Centrado en Confiabilidad.
OSI “On Stream Inspection” o Inspección en Marcha
PLG Plano de Localización General.
PoF “Probability of Failure” o Probabilidad de Falla.
SCC “Stress Corrosion Cracking” o Agrietamiento por corrosión bajo tensión.
TML “Thickness Monitoring Location” o Localización de Monitoreo de Espesor.
Autor

Elimar Anauro Rojas Monsalve
Consultor Senior & Ejecutivo, Asesor Técnico en Procesos, Confiabilidad, Riesgo, Incertidumbre e Integridad
E-mail:elimar.rojas@gmail.com
Dinos qué te ha parecido el artículo
Artículos recomendados
Planificación de mantenimiento

Comprendiendo las economías de escala

Gestión de Mantenimiento no es Gestión de Activos

Metodología Propuesta para Toma de Decisión de Inspección de Líneas de Flujo de Crudo Basado en Modelos Estadísticos de Criticidad

Publica tu artículo en la revista #1 de Mantenimiento Industrial
Publicar un artículo en la revista es gratis, no tiene costo.
Solo debes asegurarte que no sea un artículo comercial.
¿Qué esperas?
O envía tu artículo directo: articulos@predictiva21.com
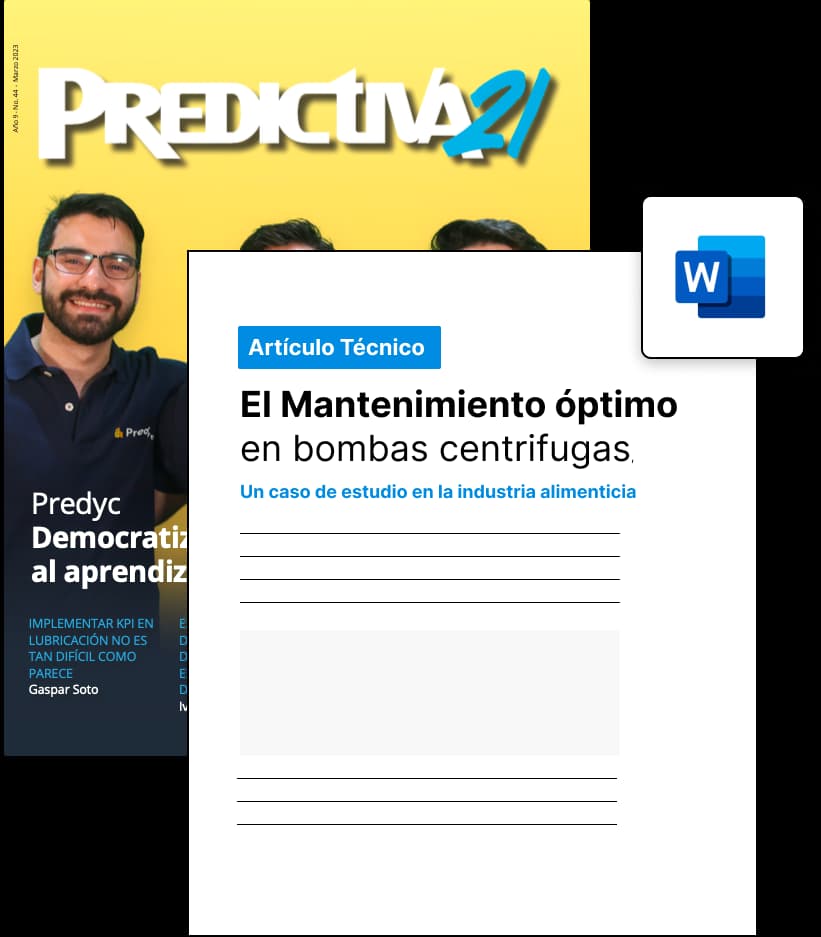
Generar Planes Óptimos de Inspección a Equipos Estáticos y Tuberías de Proceso con base en la metodología de Inspección Basada en Riesgo.
Articulo 22 de junio de 2022Resumen
La Inspección Basada en Riesgo es un enfoque sistemático basado en las normas API-RP-580 y 581, y soportado en otros estándares, que tiene como objetivo: mitigar el riesgo de los equipos estáticos y tuberías de las instalaciones estudiadas, mediante la optimización de las inspecciones, al establecer frecuencias y alcances con base en la valoración del comportamiento histórico, mecanismos de deterioro, factores de daño, características de diseño, condiciones de operación, mantenimiento, inspección y políticas gerenciales, en conjunto con, la calidad y efectividad de las inspecciones, y las consecuencias asociadas a las potenciales fallas. Así mismo, optimiza los programas de inspección en marcha, al determinar los puntos mínimos de inspección requeridos por componente, con base en los mecanismos de deterioro, niveles de riesgos y velocidades de corrosión.
Esta valoración prioriza los componentes, mediante el cálculo de la probabilidad (estableciendo los lazos de corrosión e identificando potenciales mecanismos de deterioro de acuerdo con API-RP-571) y consecuencia de la pérdida de contención, (con base en los grupos de inventario) para cada uno de sus componentes; proporcionando la ubicación de un nivel de riesgo, en una matriz 5 x 5, a fin de reducir el riesgo a través de las inspecciones, para incrementar la seguridad de la instalación, al mitigar el riesgo, mejorar de forma costo-efectiva los recursos de inspección, evaluar requerimientos para incrementar o reducir los ciclos de inspección y proponer recomendaciones para reducir el riesgo a niveles aceptables y optimizar futuras inspecciones o su efectividad.
Palabras Claves
Condición, Consecuencia, CoF, CML, Equipo, Estático, Grupo de Inventario, IBR, Inspección, Inspección en Marcha, Lazo de Corrosión, Mantenimiento, Monitoreo de Condición, Optimización, PoF, Probabilidad, Punto de Medición, Riesgo, TML, Tubería de Proceso.
1. Introducción
Una de las mayores preocupaciones de la industria actual está asociada con el diseño, selección y determinación de adecuadas políticas y estrategias de mantenimiento e inspección de los equipos estáticos y tuberías de proceso, enfocándose en el estudio del deterioro de la pared del recipiente que puede resultar en la pérdida de la función de contención de un fluido o una fuga del producto al medio ambiente con sus respectivas consecuencias; como: comprometer la seguridad del personal, originar paradas del proceso, incurrir en costos por daños ambientales, pérdidas de productos y reparación o remplazo del área afectada del recipiente.
Lo anterior, origina la necesidad de reducir los niveles de riesgos asociados mediante la implementación de metodologías y técnicas que permiten controlar, optimizar, prevenir y predecir la ocurrencia de una falla en equipos estáticos y tuberías; al aplicar la metodología de Inspección Basada en Riesgo (IBR) para generar planes óptimos de inspección, con base en las normas internacionales API-RP-580 y 581, con el soporte de otras normas, como: API-570, 571, 574, 579, 650, 653, 1160 y ASME B31.3, 31.4, 31.8 y 31.8S, así como, procedimientos de ingeniería o estándares de los propietarios de los activos evaluados.
La metodología de IBR se aplica tanto a equipos estáticos (recipientes a presión, intercambiadores, torres, y tanques de almacenamiento) como a circuitos de tuberías de proceso, con el objetivo de valorar los niveles de riesgo de cada equipo, basados en la caracterización de la condición actual, mecanismos de degradación o deterioro, características de diseño, condiciones de operación, calidad y efectividad de las actividades de mantenimiento e inspección y de las políticas gerenciales; así como, las consecuencias asociadas a las potenciales fallas.
Una vez definida la jerarquización de los equipos o tuberías de acuerdo con su nivel de riesgo, se determinan las actividades de inspección y frecuencias (fechas de ejecución), considerando los mecanismos de deterioro presentes y como punto final se realiza una optimización del programa de inspección en marcha, que permite determinar la cantidad requerida de puntos de inspección para cada equipo o circuito de tuberías. El riesgo es un término de naturaleza probabilística, que se define como “egresos o pérdidas probables, consecuencia de la posible ocurrencia de un evento no deseado o falla”; coexistiendo la posibilidad de que un evento se haga realidad o se satisfaga, con las consecuencias que de ello ocurran. En tal sentido, el riesgo asociado a una decisión o evento viene dado matemáticamente, por la expresión universal:
Riesgo(t) = Probabilidad de Falla(t) x Consecuencias. Ec. 1
Con base en la cual se observa que el nivel de riesgo puede ser variable, de acuerdo con una disminución o incremento de la probabilidad o frecuencia de falla, o disminuyendo o incrementando las consecuencias, y de acuerdo con la experiencia sobre la determinación del riego, las acciones dirigidas a disminuir la probabilidad de ocurrencia de fallas son más factibles que las dirigidas a disminuir las consecuencias, misma que involucra mayores inversiones, esfuerzos y decisiones gerenciales.
El análisis del riesgo (Ec. 1), permite comprender su poder, como indicador para diagnosticar situaciones y tomar decisiones, al comparar escenarios que pueden resultar similares, pero que bajo ciertas circunstancias deben evaluarse y considerar en un proceso de toma de decisiones; como distinguir entre una acción de mantenimiento con frecuencias de fallas bajas, aun cuando presenta altas consecuencias.
Los análisis de inspección basados en riesgo (IBR) requieren la caracterización del riesgo con base en el cálculo de probabilidades de falla, considerando, el espesor remanente, la velocidad de corrosión, y la calidad y frecuencia de inspección; mientras que, para el cálculo de las consecuencias, se considera, entre otros el tipo de fluido, los sistemas de mitigación existentes y el inventario de producto (volumen contenido) en el componente evaluado, tal como se muestra en la Figura 1.
Utilizar una matriz de riesgo de rango 5 x 5, tal como se muestra en la Figura 2, permite ubicar gráficamente del nivel de riesgo de los componentes analizados y que puede presentar cuatro (4) niveles de clasificación: bajo (verde), medio (amarillo), medio-alto (naranja) y alto riesgo (rojo).
El producto de los valores de la probabilidad de falla y consecuencias (lados de la matriz) permiten determinar el nivel de riesgo asociado a cada componente (equipo o circuito de tubería), generando una lista jerarquizada de componentes basadas en el riesgo calculado, utilizada para diseñar y optimizar los planes de inspección.


2. Metodología
Una vez delimitado o seleccionado los sistemas, subsistemas, equipos o circuitos de tuberías a los cuales se les aplicara la metodología de Inspección Basada en Riesgo (IBR), la Figura 3 muestra las principales etapas y fases para la aplicación del IBR a fin de generar planes óptimos de inspección a equipos estáticos y tuberías de proceso.

2.1. Recolectar Información Técnica.
Se debe recolectar, capturar y evaluar los datos técnicos e información necesaria para establecer la base de datos necesaria para el análisis tomando en consideración la información relativa al diseño, fabricación, instalación, operación, mantenimiento e inspección de los equipos y tuberías de proceso de la instalación.
La Tabla 1 muestra, como ejemplo, la estructura de una base de datos utilizada para organizar la información requerida por el software o herramienta de cálculo necesaria para determinar los niveles de riesgo de los equipos y circuitos de tuberías, y mantener un registro de las fuentes consultadas. La revisión y captura de los datos es una etapa en la que es posible cometer errores, siendo necesario los procedimientos que permitan asegurar de calidad de los datos necesarios para desarrollar el análisis.

Entre las fuentes de información más importante para el desarrollo de este análisis, se encuentran: los diagramas de flujo de proceso (DFP’s o PFD’s), diagramas de tubería e instrumentación (DTI’s o P&ID’s), selección de materiales, planos localización general (PLG) o “plot plant”, isométricos, historia y registro de inspecciones realizadas, caracterización de los fluidos de los sistemas, hojas de especificación de equipos, hojas de seguridad de las substancias de proceso, filosofía de operación, bitácora o reportes de mantenimiento, estudios previos de riesgo y cualquier otra información técnica que contribuya al desarrollo del estudio.
2.2. Validar / Actualizar la Información
Se debe asegurar que la información recopilada (datos) se validada y este actualizada, actividad a ejecutarse por personas debidamente capacitadas en áreas y equipos específicos, para el beneficio y calidad de los análisis.
La necesidad de asegurar la información, es múltiple, dado que pueden existir documentos, diagramas y datos no actualizados, que no reflejen la realidad de la instalación, la falta de trazabilidad de las inspecciones, errores en el registro de los datos o malas lecturas por parte de los inspectores u otras posibles fallas que puedan afectar negativamente la exactitud de los resultados del análisis, para lo cual se deben hacer todos los esfuerzos que permitan reducir las posibles fuentes de error, realizando, entre otras actividades, las siguientes:
- Verificación en campo de los diagramas e isométricos.
- Reuniones de validación con los expertos de mantenimiento e inspección de cada área.
- Verificación de las variables operacionales con los expertos de operaciones y procesos.
- Comparar las magnitudes de las velocidades de corrosión registradas con base a las inspecciones y las registradas en bibliografía o Instalaciones similares.
- Recorrido para levantamiento y validación de datos de campo.
La actualización de la información se limita a considerar todas las líneas y equipos existentes en las instalaciones y descartar aquellos que han sido retiradas de servicio, con el fin de generar los planes de inspección y acciones de mantenimiento acordes a la realidad operacional, evitando así generar planes y acciones no necesarias, o el almacenamiento y análisis de datos que presente un menor nivel de certeza o sean menos confiables.
2.3. Sistematización de la Instalación.
El proceso de sistematización consiste en la división de una instalación o grupo de unidades menores de proceso para facilitar su análisis y evaluación. La unidad de estudio será el equipoo circuito de tubería de proceso, para lo cual se toman en cuenta los conceptos de lazos de corrosión y de grupo de inventario.
2.3.1. Lazos de Corrosión (CL).
Los lazos de corrosión (CL, por sus siglas en inglés) son indispensables para la determinación de la probabilidad de falla y por definición se establece que los equipos o tuberías de proceso asociados a un mismo lazo de corrosión consideran similares: (1) tipo de materiales, (2) condiciones operacionales, (3) fluidos manejados, (4) condiciones ambientales y (5) mecanismos de deterioro.
Por lo tanto, para establecer los lazos de Corrosión se deben identificar y evaluar los mecanismos de daño presentes o potenciales en cada uno de los componentes, con base en la Norma API-RP-571, misma que permite evaluar las variables principales necesarias para determinar la existencia o no de un mecanismo de deterioro particular, ya sea que esté presente o sea potencialmente factible.
Entre las principales consideraciones para establecer los lazos de corrosión, se tienen:
- Condiciones de operación y Composición química de la sustancia manejada.
- Tipo de servicio de circuito y/o equipo.
- Materiales de construcción.
- Localización de válvulas de corte o aislamiento.
- Tipo de componente, ya sea equipo de proceso o circuito de tubería.
- Aislamiento térmico.
En tal sentido, la Figura 4 muestra un ejemplo del establecimiento de un lazo de corrosión indicado sobre un Diagrama de Flujo de Proceso (DFP), con seis (6) lazos de corrosión, considerando once (11) diferentes mecanismos de daño.

Por tanto, un lazo de corrosión es una forma práctica de describir, comprender y verificar los mecanismos de degradación en una instalación y consta de un grupo de activos (sistema de tuberías y equipos) agrupados con condiciones de proceso similares, construidos de materiales similares y que comparten amenazas similares de corrosión/degradación. o mismos mecanismos de daño activos/potenciales (DM, por sus siglas en inglés) según lo indicados en los estándares:
- ASME PCC-3 Tabla A-1.
- API-RP-580: Risk Based Inspection, Apéndice A-Mecanismos de Deterioro.
- API-RP-571: Mecanismos de Daño que Afectan Equipos Fijos en la Industria de Refinación.
De los cuales los mecanismos de daño por fabricación de soldadura están fuera del alcance de la mayor parte de los IBR.
El mecanismo de daño (DM) es un fenómeno que induce cambios micro y/o macro nocivos para el material, los cuales son perjudiciales para la condición del material o sus propiedades mecánicas. Los mecanismos de daño suelen ser incrementales, acumulativos e irrecuperables, y comúnmente están asociados con:
- Adelgazamiento,
- Ataque químico,
- Fluencia o “creep”,
- Erosión,
- Fatiga,
- Fractura,
- Fragilización o “embrittlement”,
- Envejecimiento térmico.
Para comprender los mecanismos de daño es importante analizar la probabilidad de falla, la selección de intervalos, ubicaciones y técnicas de inspección apropiados; la capacidad de tomar decisiones (por ejemplo, modificaciones al proceso, selección de materiales, monitoreo) que puedan eliminar o reducir la probabilidad de un mecanismo de daño específico.
Además, la identificación de los mecanismos de daño y modos de falla creíbles para el equipo incluido en un análisis de riesgo es esencial para la calidad y la efectividad del análisis de riesgo.
Las directrices establecidas permitirán: asegurar un riesgo mínimo previsible sobre la seguridad y la confiabilidad; asegurar la máxima esperanza de vida de los equipos o identificar áreas de aplicaciones de nuevas tecnologías.
2.3.2. Grupo de Inventario (IG)
Los grupos de inventario (IG por sus siglas en inglés) se definen como un grupo de equipos y tuberías de proceso que pueden ser aislados de manera manual o remota, mediante válvulas, y donde se asume que, el volumen total del grupo de inventario está potencialmente disponible para fugar por cualquiera de los componentes que lo conforman, en caso de que se presente una pérdida de contención o fuga al ambiente; lo cual se utiliza en el cálculo de las consecuencias, ya sea por área o financiera (dependiendo del tipo de equipo en análisis).
Entre las principales consideraciones para establecer los grupos de inventario, se tienen:
- Los sistemas de detección.
- Los sistemas de mitigación.
- Los sistemas de aislamiento (válvulas).
- Localización de válvulas de corte o aislamiento, las cuales serán los elementos que definirán los límites de grupo de inventario, preferiblemente se considerarán en el siguiente orden: (1) válvulas de bloqueo automáticas, (2) válvulas de bloqueo manuales, (3) válvulas de seguridad y en última instancia (4) válvulas de retención.
- Se asume que el “dueño” de un grupo de inventario es el equipo estático de mayor relevancia dentro del IG.
- Un equipo puede estar conformado por varias tuberías de diferentes diámetros, las cuales se identificarán como circuitos, es decir, que una sección de tubería que pueda ser aislada es considerada un equipo para su evaluación individual al igual que un recipiente u otro equipo estático.
- Los sistemas de tuberías y filtros “pequeños” generalmente forman parte de un grupo de inventario mayor, nunca generaran nombres del grupo, a excepción de tuberías o cabezales principales, los cuales se consideran como dueño de su propio grupo de inventario.
En tal sentido, la Figura 11 presenta un par de ejemplos asociados con los grupos de inventario sobre Diagramas de Tuberías e Instrumentación (DTI), donde se pueden observar los componentes de cada uno de grupos de inventario (IG) así como las válvulas consideradas límite de batería de cada IG.
Con la sistematización, cada componente (equipo o circuito de tubería) es una unidad de estudio de riesgo y le corresponde un plan de inspección particular, dependiendo de la cantidad y tipos de mecanismos de deterioro que pueda presentarse. Así mismo, se debe establecer una taxonomía para mantener una estructura reproducible, confiable y ordenada que permita identificar los lazos de corrosión y los grupos de inventarios que se han clasificado y numerado para cada caso.

2.3.3. Valorar los Mecanismos de Deterioro
Para la identificación y evaluación de los mecanismos de deterioro, se debe analizar el efecto del daño producido, durante la operación e inspección, sobre la probabilidad de la detección de los defectos, en tal sentido, se deben ejecutar, entre otros pasos, los siguientes:
- Determinar la velocidad y severidad del daño.
- Determinar el nivel de confianza en la severidad de los daños.
- Determinar la eficacia de los programas de inspección.
- Calcular el efecto del programa de inspección en el mejoramiento del nivel de determinación de los daños.
- Calcular la probabilidad que un nivel dado de daño excederá la tolerancia del componente resultando en una falla.
- Calcula los factores de daño.
- Calcular el factor de daño total para los mecanismos de daño presente y potenciales.
2.4. Análisis de Riesgo
El análisis de riesgo está dirigido a los componentes de los equipos y circuitos de tuberías, que permite determinar el riesgo con base en lo indicado por la norma API-RP-581, permitiendo la planificación de actividades asociadas con la detección de mecanismos específicos de deterioro o daño, que utiliza para obtener una calificación del riesgo de manera determinística, considerando criterios de aceptación de riesgos y plan de inspección.
El análisis de riesgo se centra en la estimación de los factores que modifican la frecuencia de fallas y las zonas afectadas por la posible fuga de producto liberado al medio ambiente, como resultado de la pérdida de la función de contención del equipo o tubería de proceso.El análisis determina en primero lugar un factor que representa la probabilidad de la falla y posteriormente permite valorar un factor para las consecuencias. Ambos se combinan en una matriz de riesgo (5 x 5) para establecer el nivel de riesgo de cada componente.
2.4.2. Probabilidad de Falla (PoF).
Para el cálculo de la probabilidad de falla (PoF) se considera el procedimiento indicado en la sección 4 de la práctica recomendada API-RP-581 mediante la Ecuación 2:

Donde:

La base de datos de la frecuencia de falla genérica se basa en una compilación de expedientes disponibles de las historias de la falla de varios tipos de componentes (equipo y circuitos de tubería de diferentes diámetros), en operación en diversas instalaciones de petróleo y gas que han sido desarrolladas para cuatro (4) diferentes tamaños de agujeros, en caso de eventos de fuga (¼”, 1”, 4” y ruptura total). Como uso más generalizado se cuenta con las evidencias de fallas presentada en la tabla 4.1 “Suggested Component Generic Failure Frequencies”, del API-RP-581, 2da Edición, Sep-2008. Sin embargo, en los casos donde se disponga de suficiente historial de fallas para un componente dado, se puede calcular la frecuencia de falla real.
Para el cálculo del Factor de Daño se utilizan métodos sistemáticos que determinar el efecto de los mecanismos de deterioro específicos, bajo condiciones de funcionamiento normales y extremas, que afectan la probabilidad de la falla de cada componente, estableciendo los factores de daño en las condiciones en que operando el equipo, cuantificado la eficacia del programa de inspección ejecutado (en caso de existir) y calculando los factores de modificación de la frecuencia de falla genérica que apliquen.
Para algunos mecanismos de deterioro existe un índice del daño que modifica significativamente la mayor frecuencia de falla a condiciones extremas, diferentes a las condiciones normales de operación, tales como variaciones de la temperatura o cambios anormales en las concentraciones de un contaminante particular en el fluido procesado y que pueden ocurrir durante periodos de cambios en las condiciones operacionales o durante los arranques y paradas de proceso.
Para analizar el efecto del daño producido en servicio y el efecto de la inspección en la probabilidad de la falla, se debe:
- Determinar la velocidad y severidad del daño.
- Determinar el nivel de confianza en la severidad de los daños.
- Determinar la eficacia de los programas de inspección.
- Calcular el efecto del programa de inspección en el mejoramiento del nivel de determinación de los daños.
- Calcular la probabilidad de que un nivel dado de daño exceda la tolerancia del daño del equipo resultando en una falla.
- Calcular los factores de daño.
- Calcular el factor de daño total para todos los mecanismos de daño.
La norma API-RP-581 considera principalmente los siguientes factores de daño en base a los mecanismos de deterioro:
- Adelgazamiento por corrosión/erosión (presencia de revestimientos internos).
- Agrietamiento por corrosión bajo esfuerzos, SCC (Stress Corrosion Cracking).
- Daño externo.
- Ataque por hidrógeno a alta temperatura, HTHA.
- Fractura frágil.
- Fatiga mecánica.
Dichos factores de daño se pueden consultar en la parte 2 de las normas API-RP-581, donde se establece la correspondiente evaluación de cada mecanismo, presente o potencial en cada componente del proceso. Por lo tanto, si más de uno de los tipos generales de daño está potencialmente presente, los factores de daño individuales deben ser sumados, tal como se indica en la ecuación 3.

Para cada uno de los factores de daño, existe un flujograma de toma de decisiones donde se indica la información de proceso y mantenimiento, empleada para determinar el tipo de mecanismo de deterioro presente en cada equipo. Los aspectos teóricos y detalles de cada mecanismo de deterioro están especificados en la norma API-RP-571 “Damage Mechanisms Affecting Fixed Equipment in the Refining Industry”.De igual manera, se debe cuantificar la efectividad del programa de inspección, basado en la determinación de las técnicas de inspección más recomendables ejecutar para cada mecanismo de deterioro identificado. La efectividad de la inspección permite medir la capacidad de cada técnica de inspección o ensayo no destructivo, para detectar el mecanismo de daño que se puede presentar. En tal sentido, la norma API-RP-581 / Parte 2 presenta las tablas 5.5 a 5. 10, que indica las guías de asignación de la efectividad de inspección para los principales mecanismos de deterioro.
Para la determinación del Factor del Sistema Gerencial, se sigue para aquellas empresas que no lo tiene definido, el procedimiento propuesto en el Anexo 2.a. del API-RP-581 y el cual evalúa trece (13) aspectos:
- Liderazgo y administración.
- Información sobre seguridad de procesos.
- Análisis de peligros de proceso.
- Gerencia del cambio.
- Procedimientos operacionales.
- Prácticas de trabajo seguro.
- Capacitación o Entrenamiento.
- Integridad mecánica.
- Revisión de seguridad previo al arranque.
- Respuesta a emergencias.
- Investigación de incidentes.
- Contratistas.
- Evaluación del Sistema de Gerencia o Auditorias.
La Figura 12 muestra un gráfico tipo “araña” en el cual se presentan los resultados del análisis necesario para determinar el factor del sistema Gerencial con base en el Anexo 2.a. del API-RP-581.

2.4.2. Consecuencia de la Falla (CoF).
Con respecto al otro lado de la matriz de riesgo se debe calcular las consecuencias (CoF), ya sean con base en el área de afectación (pie2/año) o en base financiera (USD/año), considerando lo indicado por la Norma API-RP-581 / Parte 3, tomando en cuenta aspectos como: naturaleza de la falla, cantidad del fluido liberado; velocidad de fluido liberado en función del tamaño del agujero (¼”, 1”, 4” y ruptura total), viscosidad del fluido, densidad y presión de operación, consecuencias hacia las personas (basado en el número de víctimas potenciales), consecuencias ambientales basada en el costo de posibles derrames (saneamiento, recolección, penalizaciones, etc.) y consecuencias de perdida de producción que en caso necesario puede ser estimados empleando la tabla 5.17: “Estimated Equipment Outage” (Norma API-RP-581 / Parte 2).
Como referencia, la rotura de una tubería de alta presión de gran diámetro o de un recipiente a presión, obviamente, tiene una consecuencia diferente de una fuga en una tubería de baja presión de menor diámetro.
En todo caso, las consecuencias totales (Área o Financieras) son definidas como la sumatoria de cada una de las consecuencias de acuerdo con lo indicado en la Ec. 4.

2.4.3. Matriz de Riesgo.
El nivel de riesgo se calcula combinando la probabilidad de falla (PoF) con la consecuencia de la falla (CoF) de cada componente, ubicándolos en una matriz de riesgo de 5 x 5, tal como se muestra en la Figura 13 que presenta un ejemplo de matriz de riesgo para consecuencias en área (equipos y tuberías) o consecuencias financieras (tanques).

Cursos recomendados




%252FImagen%252FRAMPREDYC-1730060420837.webp%3Falt%3Dmedia%26token%3D2634a7f0-988e-4022-b91f-382503e6e9db&w=3840&q=75)



2.5. Diseño de los Planes de Inspección.
Una vez identificados los factores de daño de cada equipo podrá identificarse cuál es la influencia de cada uno de ellos en la probabilidad de falla, así como el efecto del alcance y la efectividad de las actividades de inspección adecuadas en la probabilidad de detectar la manifestación del daño. Para ello, la norma API-RP-581, especifican las actividades de inspección, su alcance y frecuencias de aplicación de acuerdo a los mecanismos de deterioro presentes y su crecimiento en el tiempo.
El propósito de un plan de inspección es definir las actividades necesarias para detectar el deterioro en servicio de los componentes antes de que se produzcan las fallas. Adicionalmente se identifican actividades de mantenimiento u otras acciones de mitigación de riesgo que puedan ser aplicadas.
La concepción de una estrategia de reducción de riesgo de equipos estáticos a través de la metodología inspección basada en riesgo, sólo surtirá efecto si las actividades que han sido identificadas como las de mejor efecto de reducción de riesgo, son aplicadas. Para lo cual se recomienda establecer un mecanismo de control de las recomendaciones derivadas de los análisis a fin de garantizar su cumplimiento.
La Tabla 2 y la Tabla 3, muestran un plan de inspección recomendado para equipo de proceso y tanque de almacenamiento de hidrocarburo, respectivamente; mientras que la Tabla 4 muestra un análisis costo-riesgo-beneficio (ACRB), de la forma en que se puedan realizar las actividades de inspección y las acciones de mantenimiento, mediante la cuantificación y asignación de los recursos, para tanques de almacenamiento de hidrocarburos (HC), que muestra el beneficio al considerar la extensión de los intervalos de inspección controlando adecuadamente el riesgo.



2.6. Análisis de Resultados.
Como producto de las experiencias obtenidas durante la aplicación de la Inspección Basada en Riesgo, se muestran a continuación imágenes de los diferentes productos y resultados obtenidos haciendo uso de programas y herramientas computacionales licenciatarios y propios, basado en la normativa aplicable.
La Figura 14 muestra el resultado del análisis de riesgo, donde se observa la cantidad de componentes para cada nivel de riesgo dentro de la Matriz. Así mismo, se observa una proyección de la distribución de los niveles de riesgo de los componentes si el plan de inspección es o no es ejecutado implementado, que en conjunto con la distribución porcentual de los niveles de riesgo y el efecto de la ejecución o no del plan de inspección recomendado (Ver Tabla 6), facilitan la adecuada toma de decisiones para la implementación del plan de inspección resultante de la aplicación de la Inspección Basada en Riesgo para Equipos Estáticos.


La Figura 15 muestra un caso específico de la evaluación de riesgo para tanques de Almacenamiento de hidrocarburos, en donde se puede ver los niveles de riesgo financieros y su ubicación de acuerdo con un límite de riesgo aceptable para el propietario de los activos y que en conjunto con los resultados mostrados en la Tabla 3 y la Tabla 4, permiten recomendar extensiones en los periodos de inspección y sus consecuentes beneficios financieros mostrados.

La Figura 16 muestra en forma general una lámina de la presentación de final de resultados de la aplicación de la Inspección Basada en Riesgo.

2.7. Optimización de los Programas de Inspección en Marcha.
Una vez desarrollado los planes de inspección para cada uno de los equipos o tuberías y dependiendo del cliente se ejecuta la optimización del Programa de Inspección en Marcha, el cual consiste en optimizar la cantidad de puntos de inspección (CML’s) para cada componente (equipo o circuito de tubería), de acuerdo con los mecanismos de deterioro presentes y niveles de riesgo.
Este proceso se realiza de acuerdo con los procedimientos de ingeniería establecidos por los clientes, en particular los del Medio Oriente.
En tal sentido, la Tabla 6 muestra un resumen de los resultados del proceso de Optimización como referencia.

2.8. Ejecutar Planes de Inspección.
Se deben ejecutar los planes de inspección detallados para cada equipo y tubería de proceso, incluyendo:
- Método de inspección (VT, UT, RT, etc.)
- Alcance de la aplicación de los métodos de inspección (% total de área examinada, etc.)
- Fecha próxima de inspección (indicado en el plan de Inspección).
De igual manera las técnicas de inspección normalmente se refieren a la evaluación de la calidad de alguna característica en relación con un estándar o una especificación, considerando:
1. Equipo:
- Inspección visual (VT),
- Medición de espesor aleatorio por ultrasonido (UT)
- Prueba de partículas magnéticas fluorescentes húmedas (WFMPT)
- Se usan comúnmente para verificar la corrosión localizada y el agrietamiento ambiental.
2. Tubería de Proceso: se usan varias técnicas para medición de espesor por:
- Ultrasónico aleatorio (UT),
- Onda de corte UT (UTSW) de soldaduras
- Radiografía (RT)
- Se utilizan para detectar pérdida de metal, corrosión preferencial de soldadura y agrietamiento fino.
Ejemplo de las recomendaciones para la inspección son:
- Para internos: Realizando 10% MFL de tubos, 100% VT con mediciones aleatorias de UT o 50% VT y UT aleatoria.
- Para externos: 50% UTT de CML’s; El 100% de las LMC utilizan UTSW manual, AUT o radiografía.
- Para CUI: inspección visual 100% externa y 100% perfil o radiografía en tiempo real de daño o área sospechosa.
2.9. Monitoreo y Mejora Continua.
Para cerrar el ciclo y continuar con la mejora continua, una vez se obtengan los resultados de implantar los planes de inspección y acciones de mantenimiento recomendadas, se deben evaluar y revisar los indicadores claves de desempeño y retroalimentar el proceso.
En resumen, los principales productos de la aplicación de la metodología de IBR, se tienen:
- La Jerarquización del riesgo de todos los equipos evaluados.
- La descripción de otras actividades de mitigación (reparaciones, reemplazos o mejoras en la seguridad).
- Métodos, alcance y fechas aproximadas de inspección
- Los niveles de riesgo de todos los equipos y tuberías de proceso antes y después que la inspección y otras actividades de mitigación han sido implementadas.
- Equipos con posibilidades de extender su intervalo de Inspección.
3. Beneficios.
Entre los principales beneficios obtenido, se encuentran:
- Definir y calificar los niveles de riesgo de los equipos y tuberías de proceso, antes y después que la inspección.
- Identificar potencial reducción de pérdidas de producción durante las inspecciones en marcha.
- Aumentar confianza en la integridad y confiabilidad de los equipos y tuberías de proceso.
- Minimizar riesgos para la salud, seguridad y medio ambiente.
- Maximizar utilización de recursos y optimización de puntos de inspección.
- Mejorar eficiencia operativa.
- Métodos, alcance y fechas aproximadas de inspección
- Componentes con posibilidades de extensión del intervalo de Inspección.
- Recomendación de otras actividades de mitigación (reparaciones, reemplazos o mejoras en la seguridad).
4. Conclusiones.
Con base en lo documentado previamente para generar planes óptimos de inspección a equipos estáticos y tuberías de proceso, con base en la metodología de Inspección Basada en Riesgo (IBR), se tienen las principales conclusiones son:
- La Inspección Basada en Riesgo (IBR), permite determinar los niveles de riesgo de los equipos y circuitos de tuberías, así como evaluar las posibilidades de reducción de riesgo de estos y también determinar los beneficios económicos de la implementación de los planes de inspección recomendados por estos análisis.
- Esta metodología permite el direccionamiento de los recursos a las áreas, plantas, sistemas o equipos en donde se encuentra los mayores niveles de riesgo de la instalación analizada.
- La metodología de IBR permite: integrar las evaluaciones económicas en conjunto con los análisis de riesgos de los equipos evaluados en estos estudios, facilitando así la toma de decisiones para determinar la mejor estrategia de inspección de los equipos.
- La metodología de IBR tiene la facilidad de realizar estudios de análisis costo-riesgo-beneficio de los planes de inspección para aplicaciones específicas como tanques.
- Como aspecto innovador con estos estudios se logran optimizar los programas de inspección en marcha y así determinar la cantidad de puntos de inspección requeridos para cada equipo o circuito de tubería analizado.
5. Referencias Bibliográficas y Abreviaturas.
Las principales referencias bibliográficas y abreviaturas a considerar para generar planes óptimos de inspección a equipos estáticos y tuberías de proceso, con base en la metodología de Inspección Basada en Riesgo (IBR), son las siguientes:
- API-510.- Pressure Vessel Inspection Code: Maintenance Inspection, Rating, Repair, and Alteration
- API-570.- Piping Inspection Code Inspection, Repair, Alteration, and Rerating Of In-Service Piping Systems.
- API-571.- Damage Mechanisms Affecting Fixed Equipment in the Refining Industry.
- API-574.- Inspection Practices for Piping System Components.
- API 579.- Fitness-for-Service.
- API-RP-580.- Risk-Based Inspection
- API-RP-581.- Risk-Based Inspection Base Resource Document
- API 650.- Welded Steel Tanks for Oil Storage.
- API 653.- Tank Inspection, Repair, Alteration and Reconstruction.
- API 1160.- Mananging System Integrity for Hazardous Liquid Pipelines.
- ASME Secc. VIII Div. I.- Boiler And Pressure Vessel Code.
- ASME B31.3.- Process Piping.
- ASME B31.G.- Manual for dtermining the remaining strength of corroded pipelines.
- ASME B31.4.- Pipeline transportation system for liquid hydrocarbons & other liquids.
- ASME B31.8.- Gas Transmission And Distribution Piping System
- ASME B31.8S.- Supplement to B31.8 on Managing System Integrity of Gas Pipeline.
- DNV-RP-G101.- Risk Based Inspection Of Offshore Topsides Static Mechanical Equipment.
- DS/CWA-15740: Risk-Based Inspection and Maintenance Procedures for European Industry (RIMAP)
- UNE-16991: Marco de la Inspección Basada en el Riesgo.
CML “Condition Monitoring Location” o Localización de Monitoreo de Condición.
CL “Corrosion Loop” o Lazos de Corrosión.
CoF “Consequence of Failure” o Consecuencia de Falla.
ACRB Análisis Costo-Riesgo-Beneficio.
CUI “Corrosion Under Insulation” o Corrosión bajo el aislamiento.
DFP Diagrama de Flujo de Procesos o PFD: “Process Flow Diagram”.
DM “Damage Mechanics” o Mecanismo de daño.
DTI Diagrama de Tubería e Instrumentación o PID: “Process and Instrumentation Diagram”.
HAZ “Heat Affected Zone” o Zona afectada por el calor de soldadura.
IBR Inspección Basada en Riesgo.
IG “Inventory Group” o Grupo de inventario
MCC Mantenimiento Centrado en Confiabilidad.
OSI “On Stream Inspection” o Inspección en Marcha
PLG Plano de Localización General.
PoF “Probability of Failure” o Probabilidad de Falla.
SCC “Stress Corrosion Cracking” o Agrietamiento por corrosión bajo tensión.
TML “Thickness Monitoring Location” o Localización de Monitoreo de Espesor.
Autor

Elimar Anauro Rojas Monsalve
Consultor Senior & Ejecutivo, Asesor Técnico en Procesos, Confiabilidad, Riesgo, Incertidumbre e Integridad
E-mail:elimar.rojas@gmail.com
Dinos qué te ha parecido el artículo
Artículos recomendados
Precursores de la ingeniería industrial

¿Qué es la gestión de riesgos empresariales?

Santiago Sotuyo: Vocación por el trabajo voluntario

Panorama Minero realizará la Expo San Juan Minera 2020 en modalidad virtual: será la primera del sector

Publica tu artículo en la revista #1 de Mantenimiento Industrial
Publicar un artículo en la revista es gratis, no tiene costo.
Solo debes asegurarte que no sea un artículo comercial.
¿Qué esperas?
O envía tu artículo directo: articulos@predictiva21.com
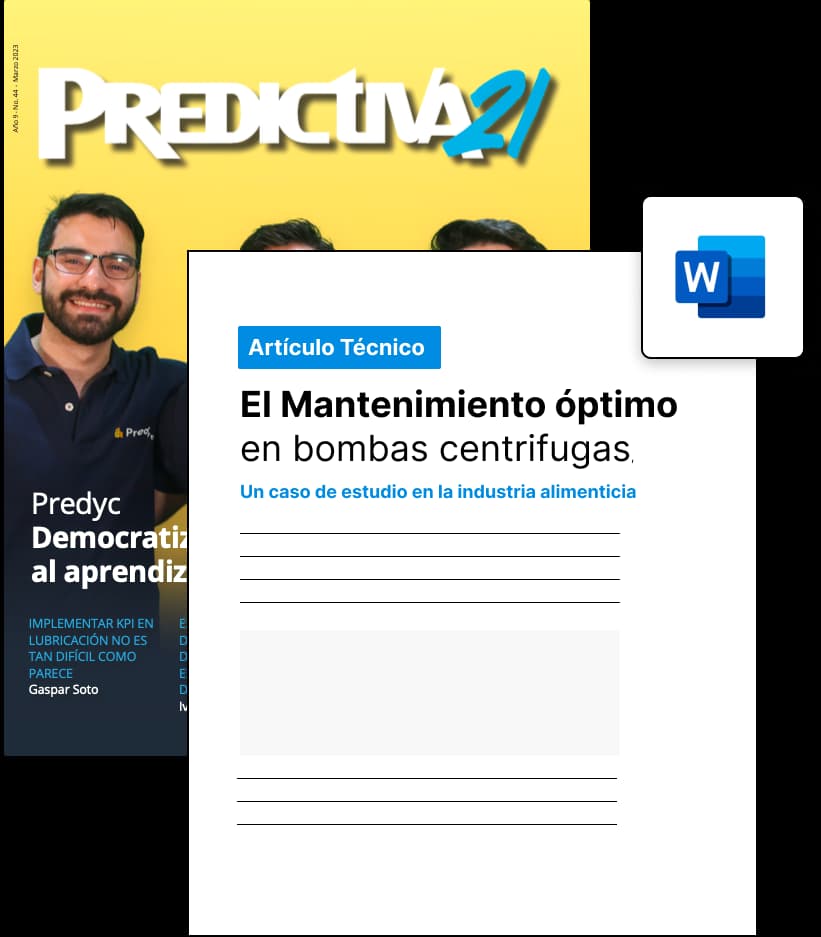