Gestión de Integridad de Activos para Infraestructuras basado en Fiabilidad e Inteligencia Artificial
Articulo4 de septiembre de 2023
Hoy en día, el mundo invierte alrededor de 2,5 billones de dólares al año en activos físicos de infraestructura, como sistemas de transporte, energía, água y telecomunicaciones.
Sin embargo, esta cantidad sigue siendo inferior a las necesidades cada vez mayores del mundo, lo que se traduce en crecimiento económico y (Informe de 2013 de la MGI Productividad de la infraestructura). Además de ser un facilitador clave de la inversión, la infraestructura también puede ser un receptor lucrativo de entradas de inversión. Inversión privada en redes de infraestructura, junto o en lugar de operadores estatales, ha ido en aumento en todo el mundo durante várias décadas.
Sin embargo, desde la crisis financiera mundial, este impulso ha flaqueado un poco: en 2010-2012 (OCDE, 2013a). De hecho, la crisis económica de 2008 ya provocó enormes recortes de gastos en todo el mundo. En Europa, la infraestructura de la posguerra, especialmente los puentes, está envejeciendo. A pesar de eso, el mantenimiento trabajo atrasado, es decir. la cantidad de mantenimiento y rehabilitación que debería haberse completado en para mantener las carreteras en buen estado, pero se ha aplazado, está creciendo considerablemente. Este problema podría ser amplificado debido a la pandemia COVID-19, que causan más servicio cancelados, retrasos y consecuentemente recortes de gastos.
La parte esencial de la inversión en activos físicos de infraestructura se refiere a las actividades de mantenimiento. Por lo tanto, el retraso o la falta de mantenimiento resulta en costos más amplios: impide la movilidad en el mercado interior, aumenta el riesgo de accidentes y conduce a mayores emisiones de CO2 sector del transporte. Además, «ahorros» de retrasar o la falta de mantenimiento será falso economía como la infraestructura se degradará hasta el punto en que debe ser reemplazado que es más costoso que el mantenimiento regular y aumentar el riesgo de accidentes graves y graves. (European Federación de la Industria de la Construcción (FIEC) – 2021).

Antes de pensar en el mantenimiento, el primer aspecto a considerar en el logro de alto rendimiento es la fiabilidad. La fiabilidad se define como la probabilidad de éxito que un activo físico tiene para cumplir su función durante un período de tiempo específico bajo condiciones de operación específicas. El mantenimiento es la ación para restaurar la función de activo físico antes o después de que la falla funcional ocurre. De hecho, muchos de los activos físicos de infraestructura como la construcción, puentes, paso elevado, paso subterráneo, encubierto, carretera y equipos estáticos (Buque, torres, tuberías) tienen una alta fiabilidad a lo largo de su ciclo de vida, que se basa en la robustez de dicha integridad de los activos físicos. Sin Embargoo, factores externos como las condiciones ambientales, el estrés de carga y el uso pueden afectar a la fiabilidad de las infraestructuras.
El principal concepto de mantenimiento, o en otras palabras, mantenimiento preventivo, es detectar tales condiciones y la degradación de los activos físicos antes de que ocurra el fallo, para evitar el impacto en la interrupción del servicio público o incluso desencadenar un accidente grave. De hecho, el principio general de mantenimiento también se aplica a los activos de infraestructuras, que consideran la implementación de diferentes métodos de mantenimiento preventivo en lugar de mantenimiento correctivo.El mantenimiento preventivo em las infraestruras también evitan acidentes graves.
Al aplicar el mantenimiento preventivo, el sistema de infraestructura recuperará gran parte o total de la confiabilidad inicial, acercando el sistema de infraestructura al estado como nuevo, teniendo un efecto positivo en la confiabilidad del sistema de infraestructura.
El mantenimiento preventivo se puede dividir en Programado y Predictivo. El mantenimiento programado se basa en el calendario que se define teniendo en cuenta los datos de fiabilidad, así como una recomendación del proveedor o procedimientos internos. El Mantenimiento predictivo se basa en los valores de facture de estrés medidos por el sensor o incluso mediante la aplicación de pruebas no destructivas como ultrasonidos, infrarrojos, radiografías y otros.
La correcta implementación de las tareas de mantenimiento para renovar la fiabilidad debe definirse desde el concepto de sistema de Infraestructura basado en el Programa de Confiabilidad y Mantenimiento como se discutirá en el próximo ítem.
2 – Programa de Confiabilidad y Mantenimiento para Infraestructura
Las actividades de mantenimiento aplicadas a los activos físicos de infraestructuras deben enmarcarse en un Programa de Mantenimiento, que se implementa a lo largo de las diferentes fases del ciclo de vida, desde el concepto hasta el desmantelamiento.
Durante la fase conceptual, el análisis preliminar de peligros (PHA) es el principal inicial análisis relativo a la seguridad, que tiene como objetivo capturar los diferentes riesgos ocupacionales desencadenados por errores humanos o por la degradación de fallas de activos físicos de infraestructura a lo largo de las fases de ciclos de vida diferentes, como el diseño, la construcción y la operación. De hecho, muchas de esas causas de peligro, como gritea, la corrosión y la fatiga, pueden mitigarse mediante un mantenimiento preventivo definido inicialmente por el método MCR.
El Mantenimiento Centrado en la Confiabilidad (MCR) es un método aplicado inicialmente durante la fase de diseño, que tiene como objetivo definir las tareas de mantenimiento basadas en el modo y efecto de falla del equipo, así como el riesgo asociado. El MCR se realiza en un taller con diferentes expertos en mantenimiento y operación para discutir sobre la tarea de mantenimiento del equipo, así como el intervalo de la prueba y el mantenimiento preventivo. La información de entrada para realizar el MCR son las infraestructuras de Activos Físicos modos de falla, causas, consecuencias y riesgo. Dicha información se define sobre la base del Análisis de Efectos y Modo de Fallo (FMEA). El MCR se aplica a diferentes activos físicos de infraestructura. En la industria ferroviaria, estos activos físicos representan un importante agujero en términos de seguridad y rendimiento del ferrocarril. Un buen ejemplo es el componente ferroviario que, en caso de fallo, provocará un impacto en la disponibilidad operativa del sistema ferroviario y puede desencadenar un accidente grave, como el descarrilamiento, como muestra la figura 2.

En la figura 2 se describen los modos de fallo, las causas y las consecuencias del ferrocarril, así como el riesgo que se considera intolerable sobre la base de la combinación de las frecuencias de causa y la gravedad de las consecuencias. Sobre la base de dicha evaluación, se definen diferentes tipos de tareas de mantenimiento y sus frecuencias para mitigar el riesgo, como la inspección visual y la inspección de vehículos de carretera (prueba ultrasónica). Los métodos similares en comparación con el enfoque de MCR es el RBI.
La inspección basada en el riesgo (RBI) se aplica inicialmente en la fase de diseño y más tarde durante la fase de operación. El RBI tiene un concepto similar del MCR, sin embargo el alcance del análisis es un activo físico, que en caso de fallo puede desencadenar un accidente grave. Los métodos RBI se implementan en base a procedimientos y estándares específicos como: API 580, API 581 y EN 1691, que pueden ser cualitativos o semicuantitativos basados en los niveles de aplicación de RBI. El RBI cualitativo (nivel 0) se basa en la simple evaluación del riesgo que considera la probabilidad de fracaso y la categoría de gravedad. Tal RBI se aplica en alto nivel y durante el diseño. El RBI Semi-Quantitative (Nivel 1 y 2) considera el factor de degradación (DF), al calcular la probabilidad de fallo basado en el sistema de infraestructura. El DF considera el espesor de degradación de grietas o corrosión u otros modos de falla medidos durante el funcionamiento por la prueba no destructiva aplicada para diferentes modos de falla, como la corrosión, la erosión y el crack.
La figura 3 muestra un ejemplo de RBI aplicado para un puente, que puede ser un puente ferroviario, un puente de carretera, un paso elevado que depende de su integridad y la correcta inspección y aplicación de tareas de mantenimiento preventivo en una frecuencia adecuada para evitar accidentes graves.

Además de los métodos cualitativos, es importante contar con un análisis cuantitativo para predecir los activos físicos de la infraestructura, como el análisis de datos de vida útil, también conocido como análisis de Weibull, que tiene como objetivo definir la función de densidad de probabilidad de equipos/ componentes para definir las curvas de fiabilidad y el patrón de tasa de fallo del equipo basada en el princípio de la curva de la bañera, que representan diferentes tipos de formas de tasa de fracaso, como la vida temprana, la vida útil y el desgaste. Depende del tipo de patrón de tasa de fallo, se llevan a cabo diferentes estrategias de mantenimiento, así como la predicción del tiempo de intervención.
En el caso de los Activos Físicos de Infraestructuras, el Análisis de Degradación Probabilística (PDA) es más apropiado para predecir dicha fiabilidad física de los activos y la probabilidad de fallo. El PDA tiene como objetivo definir la fiabilidad del activo físico basado en los datos de fallas de degradación de integridad relacionados con el espesor de grietas, corrosión, erosión medida por métodos no destructivos. Mediante la aplicación de este método, es posible predecir cuándo se logrará el fallo funcional sobre la base de la tendencia del espesor de evolución en el tiempo y el límite de espesor o profundidad (grieta o corrosión) logro como muestra la figura 4. Además, mediante la recopilación de diferentes puntos de degradación en diferentes momentos, la fiabilidad o probabilidad de fallo de la función de degradación también se puede definir como muestra la figura 4.

La línea rosa de 1,5 mm es el límite de corrosión, donde se espera que ocurra el fallo funcional. Las otras líneas son diferentes mediciones que proyectan la evolución de la corrosión en puntos de diffente a lo largo del tiempo. Por lo tanto, si proyectamos la intercepción de cada una de estas líneas con la línea recta (1,5 en axxis Y) en x axxis, habrá diferentes tiempos de fallas funcionales. Tenga en cuenta que este perfil puede cambiar a lo largo del tiempo y, en consecuencia, la frecuencia de inspección también cambiará. Estos tiempos se utilizan para predecir la confiabilidad, aumentar la tasa de fallas y, en base a dicha información, definimos cuándo debe realizarse la inspección, como muestra la figura 5.

Sobre la base de la cifra anterior, después de 20.983 año, la fiabilidad disminuirá. Por lo tanto, en este caso, 20.983 años es un tiempo de referencia para realizar un overhall en esta infraestructura debido a que la corrosión está alcanzando un valor cercano al fallo funcional (1.5mm). Sin embargo, la primera corrosión se detectó después de 10 años. (como se define en el primer gráfico). Por lo tanto, este tipo de información ayuda a definir el intervalo inicial de inspección cuando estos datos están disponibles para proyectos anteriores en condiciones similares, así como durante la operación.
Basado en la primera cifra, el intervalo de inspección (no – prueba destructiva para detectar la corrosión tickness) se puede definir como cada 5 años y después del 10º año, para realizar la inspección anualmente.
Tenga en cuenta que inicialmente, el intervalo de inspección general se definió para cada 5 años (basado en la recomendación RCM/ RBI), pero después del 10º año, comienzan a realizar la inspección (no – prueba destructiva) cada año.
La línea rosa de 1,5 mm es el límite de corrosión, donde se espera que ocurra el fallo funcional. Las otras líneas son diferentes mediciones que proyectan la evolución de la corrosión en puntos de diffente a lo largo del tiempo.
Por lo tanto, si proyectamos la intercepción de cada una de estas líneas con la línea recta (1,5 en axxis Y) en x axxis, habrá diferentes tiempos de fallas funcionales. Tenga en cuenta que este perfil puede cambiar a lo largo del tiempo y, en consecuencia, la frecuencia de inspección también cambiará.
Estos tiempos se utilizan para predecir la confiabilidad, aumentar la tasa de fallas y, en base a dicha información, definimos cuándo debe realizarse la inspección, como muestra la figura 4.
El Análisis RAM es también un método importante que permite abarcar diferentes equipos que forman parte de un Sistema de Infraestructura como el Sistema de Agua o el Sistema de Distribución de Energía o incluso estructuras Civiles específicas como una carretera o un puente. Con el fin de representar la combinación de la falla del equipo y su impacto en la disponibilidad operativa de infraestructura de alto nivel
El Análisis de Crecimiento de Confiabilidad (RGA, por sus siglas en inglés), como muestra la figura 6, tiene como objetivo verificar el efecto de las condiciones de mantenimiento y operación en el rendimiento del equipo al observar la tendencia del MTBF y la intensidad del gráfico de fallas. Cada vez que el MTBF disminuye a lo largo del tiempo hay una degradación de la confiabilidad. Cada vez que el MTBF aumenta a lo largo del tiempo, hay un crecimiento de confiabilidad. Y cada vez que el MTBF es constante a lo largo del tiempo, no hay degradación o crecimiento de confiabilidad. Por lo general, el crecimiento de la fiabilidad del equipo se lleva a cabo solo si se produce un rediseño, pero la sustitución de un equipo específico por otro mediante el uso de diferentes proveedores con mejores equipos también puede producir el aumento de MTBF que también se interpreta como crecimiento de la fiabilidad por los expertos en mantenimiento. Tenga en cuenta que el modelo de crecimiento de la fiabilidad aplica el concepto correcto de MTBF porque no es un valor absoluto, sino una función que demuestra la disminución (constante o aumento) de mantenimiento, inspección o intervalo de falla a lo largo del tiempo. Los métodos de crecimiento de la confiabilidad se aplican muy bien al sistema de infraestructura para permitir la predicción de la próxima vez a la inspección basada en la reducción de la tendencia de MTBI (tiempo entre inspecciones). Tal método se llama inspección basada en el crecimiento de la confiabilidad basado en la inspección (RGBI), Calixto E, 2016.

La Figura 6 muestra el siguiente tiempo de inspección considerando el tiempo de inspección anterior que se reduce basado en el efecto de envejecimiento y degradación sobre la confiabilidad de los activos físicos de la estructura. Este métodos junto con el PDA son los dos métodos de ingeniería de confiabilidad cuantitativa más importantes aplicados a los sistemas de infraestructura para apoyar el mejor momento para realizar una inspección o mantenimiento preventivo.
Finalmente, el Total Productive Maintenance (TPM) es una filosofía para tener una tarea de mantenimiento muy productiva al reducir el tiempo de reparación/reemplazo eliminando los errores y manteniendo el servicio de mantenimiento de alta calidad. Este enfoque se aplica en todo el mundo y también se puede aplicar durante el Sistema de Infraestructura durante el servicio de mantenimiento para reducir el tiempo de inactividad del servicio y que afecta la falta de disponibilidad de servicios cruciales para el público como el transporte, la energía y las telecomunicaciones.
3 – Mantenimiento 4.0 aplicado para infraestructuras.
La Inteligencia Artificial (A.I) tiene como objetivo permitir a la máquina pensar y tomar su propia decisión sobre la base de los datos recogidos y evaluados automáticamente sin ninguna intervención humana. La principal diferencia de la aplicación de aprendizaje automático A.I y los métodos anteriores, en eso. en lugar de la interfaz humana constante con nuevos datos de entrada, el aprendizaje automático A.I dará nuevas salidas basadas en nuevos datos que vienen sin y la interfaz humana. La A:I se ha aplicado a diferentes campos como estudios de biología, medicina, finanzas e ingeniería con casos exitosos de uso de datos numéricos y categóricos, texto e imágenes.
Basado en el EFNMS – Comité Europeo de Mantenimiento 4.0 (ECM4.0) 2021, la Industria 4.0 es un nuevo paradigma y la última revolución industrial, que se ha implementado en todo el mundo intensivamente en los últimos cinco años y está respaldado por la utilización de Habilitación de Tecnologías Digitales llamado 4.0.
El Maintenance 4.0 es el uso de dicha tecnología digital aplicada a los activos físicos para el mejor uso de los datos, transformados en información para permitir una decisión estratégica de Mantenimiento rápida, automática y en algunos casos independiente.
El uso de diferentes tecnologías de habilitación 4.0 basado en la figura 7, facilita la función de mantenimiento para realizar diferentes actividades y apoyar el activo físico para lograr un alto rendimiento.

La mayoría de estos permite especialmente el Análisis de Big Data, Machine Learning, Deep Learning y Cloud Computing se puede aplicar para monitorear la degradación del Sistema de Infraestructura, clasificar y alertar la degradación y predecir la Vida Útil Restante (RUL) y el estado de salud (SoH). Dado que el objetivo principal del trabajo es discutir los métodos que permiten definir el intervalo de inspección y el mantenimiento preventivo para un mayor rendimiento en la disponibilidad operativa y la seguridad, nos centraremos en los métodos de aprendizaje automático.
La aplicación de machine learning se aplica para la clasificación de criticidad de equipos, predicciones de regresión de fallas y la aplicación automática de la Gestión de Salud Pronóstica (PHM). El PHM tiene como objetivo definir los equipos de vida útil restante (RUL) y el estado de salud (SoH) sobre la base de datos de monitoreo en línea o prueba no destructiva mediante la medición de los factores estresantes. En el caso del sistema de infraestructura, el factor de tensión son la vibración, el voltaje, la temperatura, la humedad, el espesor de grietas, la profundidad de corrosión y otros parámetros físicos que conducen al equipo se degradan a un fallo funcional.
El concepto detrás de Machine Learning es utilizar el conjunto de datos (con diferentes variables de datos) para agrupar, clasificar o predecir la respuesta de las variables futuras automaticamente sin intervención humana. El aprendizaje automático aplicado a los clústeres se denomina aprendizaje automático sin supervisión. Por otro lado, el Aprendizaje Automático Supervisado puede ser clasificado y Clasificación y regresión. La Supervise Machine Learning Classification tiene como objetivo definir una nueva clasificación de datos (etiqueta) basada en el conocimiento predefinido de la clasificación de un conjunto de datos anterior.
La regresión de la Clasificación de Aprendizaje Automático No Supervisado tiene como objetivo predecir la variable de respuesta basada en predictores considerando el conjunto de datos conocidos predefinidos. El proceso de UML se aplica para organizar y agrupar diferentes infraestructuras físicas basadas en sus variables de datos.
En el caso de SMLC o SMLR, para clasificar y predecir la respuesta de datos, el modelo de aprendizaje automático divide el conjunto de datos en los datos de entrenamiento (~70% del conjunto de datos) y los datos de prueba (~30% del conjunto de datos). El paso siguiente es aplicar un algoritmo a los datos de entrenamiento para el proceso de aprendizaje y luego elaborar un modelo. El modelo se aplicará a los datos de la prueba y se verificará el resultado. Si el resultado es satisfactorio, el nuevo conjunto de datos puede utilizar el mismo modelo definido sobre la base del conjunto de datos anterior para hacer predicciones y si el resultado es satisfactorio, se valida el modelo.
Además de SML y UML, los métodos de aprendizaje profundo también se pueden aplicar para apoyar el mantenimiento preventivo del sistema de infraestructura. El DL es un método de aprendizaje automático más sofisticado que aplica una red neuronal profunda que abarca várias capas ocultas como muestra la figura 8. Los principios de la red neuronal profunda consideran diferentes capas como capa de convolución, capa de agrupación, ReLu, completamente conectado, Softmax y la clasificación de la imagen de salida.

A pesar de la A.I Deep Machine Learning y otros métodos, así como los métodos de ingeniería de fiabilidad, es necesario integrar tales soluciones en un Sistema de Gestión de Activos para permitir la gestión de las tareas de mantenimiento preventivo definidas para todos estos métodos y asegurarse de que los recursos adecuados se asignan en el momento adecuado para mitigar la Infraestructura Riesgo de Activo Físico de indisponibilidad a lo largo del tiempo y accidentes mayores. El siguiente punto discutirá la Gestión de Integridad de Activos como parte de la Gestión de Activos.
4 – Gestión de la integridad de los activos de Infraestructura
Por lo tanto, los elementos críticos de seguridad (SCE, por sus siglas en inglés) son los activos físicos, que en caso de fallo, pueden conducir a un accidente grave, como un incendio de avión, liberación de nubes tóxicas, explosión, incendio, derrame de productos tóxicos, accidente aéreo, colisión de trenes o descarrilamiento. De hecho, el accidente mayor puede ser provocado por un fallo de integridad de la infraestructura, software, hardware o error humano o una combinación de factores tales como muestra la figura 9.
Para mitigar tal riesgo de accidente grave es necesario en el primer paso la implementación del Programa de Confiabilidad y Mantenimiento (R&M) en la primera etapa del concepto de ciclo de vida del activo físico e implementar todas las recomendaciones de tales métodos de R&M. Después de eso, es necesario implementar el programa de gestión de riesgos e inspección y prueba durante la fase de operación.

El Programa de Integridad de Activos puede aplicar los mismos elementos de la AM definidos en la norma ISO 55000, como el contexto de la organización, el liderazgo, la planificación, el apoyo, la operación y la evaluación del desempeño, pero debe centrarse en la gestión de los elementos críticos de seguridad.
Desde 2010, la nueva era de la Industria 4.0 se convierte en realidad para muchas industrias en todo el mundo. En los últimos cinco años se ha aplicado al desarrollo de la nueva tecnología IOT AM en base a diferentes temas como Big Data, Prognostic Health Maintenance y Machine Learning, siendo parte del llamado Maintenance 4.0.
A pesar de todo el desarrollo, que permiten una AM integrada demasiado enfoque se ha dado para el mantenimiento y una falta de esfuerzo para la seguridad en relación con la gestión de los elementos críticos de seguridad.
Sin embargo, es muy importante establecer un proceso que permita un flujo AIM efectivo integrado al proceso AM.

Dado que el elemento crítico de seguridad se define sobre la base de un análisis de riesgo previo teniendo en cuenta la gravedad crítica, la gestión de riesgos de dicha SCE se realiza mediante el modelo de barrera se actualiza automáticamente y permite a los gestores de integridad de activos y seguridad gestionar el riesgo de los elementos críticos de seguridad en la base diaria.
El Deep Learning A.I, u otro tipo de aprendizaje automático debe integrarse en el proceso AIM para permitir la detección y predicción de degradación automática. Además, es necesario que todas las predicciones que provienen de los métodos A.I y Fiabilidad se traduzcan en órdenes de trabajo relacionadas con los servicios de Servicio de Mantenimiento que deben implementarse a lo largo del tiempo, incluidos los KPI de Mantenimiento y Fiabilidad, plan estratégico de gestión de activos y mitigación de riesgos operativos.
5 – Conclusión
La gestión de Integridade de Ativos para el sistema de infraestructura deve empecar en la fase de concepto y necesita ser implementada adecuadamente a lo largo del ciclo de vida de la infraestructura considerando lo siguiente:
- Fase conceptual: análisis preliminar de los peligros para la mitigación de los riesgos internos y la definición de los requisitos de seguridad
- Fase de Deseno: Implementación de métodos cualitativos y cuantitativos como FMEA, RCM, RBI, PDA, RAM para requisitos cualitativos y cuantitativos detallados y definiciones de tareas de mantenimiento
- Fase de Construcción: Análisis preliminar de peligros para la fase de construcción teniendo en cuenta el requisito de seguridad definido durante el diseño
- Fase de verificación y validación: Ti impulsa la prueba de verificación y validación necesaria para garantizar la seguridad.
- Fase de Operacion: Gestion de integridade de Activos físicos de infrastructura basado em ISSO 55001 e cons A.I
Autor: Eduardo Calixto, ECC Germany.
Bibliography
Calixto.E. «Gas and Oil Reliability Engineering: Modelling and Simulation. Second edition, Elsevier ISBN: 9780123919144, Release in 26 May2016.
Calixto.E. «Safety Science: Methods to Prevent Incident and worker Health Damage at Workplace. Bentham Science, Release in December 2014.
Calixto.E. “RAMS and LCC engineering applied to railway industry: Analysis, Modelling and Optimization”. 18-04-2018.Amazon. ISBN-13: 978-1986524704.
Calixto.E. “Asset Management based on Operational Availability And Life Cycle Cost Optimization Achievement:” The Offshore Process Case Study. Euromaintenance 2016 – Greece Atennas.
Calixto.E. “Asset Management Program implementation as the basis for sustaining asset high performance.” The 2nd Indonesia Conference and Exibition. Oil and Gas Asset Integrity. Maintenance and Inspection Management. Jakarta – Indonesia 2017
Calixto.E .“Good Practices of RCM and RBI applied to AIM.” The 2nd Indonesia Conference and Exibition. Oil and Gas Asset Integrity. Maintenance and Inspection Management. Jakarta – Indonesia 2017
Calixto.E .“Asset Integrity Management from Concepts to Operation phase”. ARDC 2018, Denmark – Copenhagen.
Calixto.E. “RAMS Program implementation for Electrics and Electronics in Railways Industry”. The Electric and Electronic Engineering Conference 2018. Guangzhou -China 2018.
Calixto.E. “Asset Integrity Management throughout the Asset Lifecycle”. Euromaintenance 2018, Antwerp – Belgium.
Calixto.E. RAMS Program Implementation for Railways Industry: Lessons Learned with Reliability Engineering Applications throughout the Railways Assets Life Cycle Case ”. ARDC 2018, Shanghai, China.
Calixto.E. Human Reliability analysis applied to reliability and safety analysis. ARDC 2019, Berlin, Germany.
Calixto.E. “Reliability 4.0: The oil and Gas industry case study”. Indonesia Maintenance 4.0 conference, Jakarta, Indonesia 2019.
Calixto.E. “Artificial Intelligence for Maintenance 4.0”. ISBN:9798671514919 28. Released: August 2020.
Calixto.E. Artificial Intelligence Unsupervised Machine Learning applied for Maintenance plan optimization, OMAINTEC, OMAN.2020
Calixto.E. “The Adaptative Prognostic Health management as part of Intelligent asset Management. Maintenance Workshop (APMI), Portugal.2020
Calixto.E. “The reliability 4.0 and FRACAS 4.0 as part of Asset Management solution for Water Facilities. Asset Performance 4.0 Conference (BEMAS), Belgium.2020.
Dinos qué te ha parecido el artículo
Artículos recomendados
Plan modular de Alineación Láser y Condition Monitoring

6.2 Funciones y sus Estándares de Funcionamiento

IoT para mantenimiento de planta: un paso a la industria 4.0

8.7 El Plan de Limpieza

Publica tu artículo en la revista #1 de Mantenimiento Industrial
Publicar un artículo en la revista es gratis, no tiene costo.
Solo debes asegurarte que no sea un artículo comercial.
¿Qué esperas?
O envía tu artículo directo: articulos@predictiva21.com
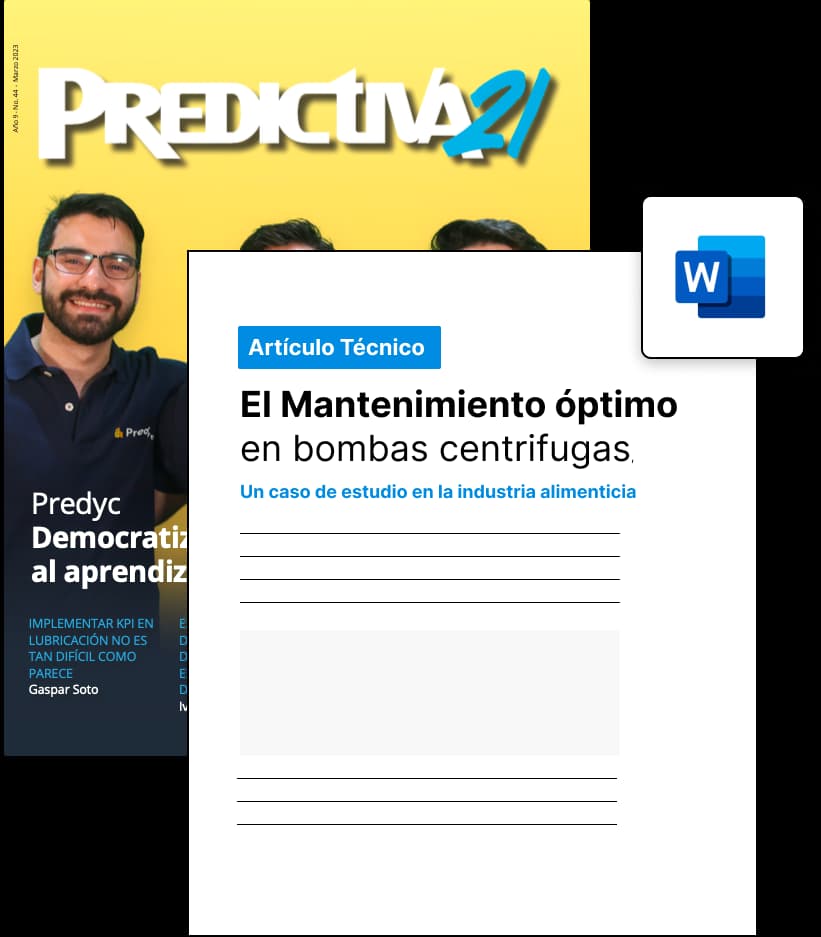
Gestión de Integridad de Activos para Infraestructuras basado en Fiabilidad e Inteligencia Artificial
Articulo 4 de septiembre de 2023Hoy en día, el mundo invierte alrededor de 2,5 billones de dólares al año en activos físicos de infraestructura, como sistemas de transporte, energía, água y telecomunicaciones.
Sin embargo, esta cantidad sigue siendo inferior a las necesidades cada vez mayores del mundo, lo que se traduce en crecimiento económico y (Informe de 2013 de la MGI Productividad de la infraestructura). Además de ser un facilitador clave de la inversión, la infraestructura también puede ser un receptor lucrativo de entradas de inversión. Inversión privada en redes de infraestructura, junto o en lugar de operadores estatales, ha ido en aumento en todo el mundo durante várias décadas.
Sin embargo, desde la crisis financiera mundial, este impulso ha flaqueado un poco: en 2010-2012 (OCDE, 2013a). De hecho, la crisis económica de 2008 ya provocó enormes recortes de gastos en todo el mundo. En Europa, la infraestructura de la posguerra, especialmente los puentes, está envejeciendo. A pesar de eso, el mantenimiento trabajo atrasado, es decir. la cantidad de mantenimiento y rehabilitación que debería haberse completado en para mantener las carreteras en buen estado, pero se ha aplazado, está creciendo considerablemente. Este problema podría ser amplificado debido a la pandemia COVID-19, que causan más servicio cancelados, retrasos y consecuentemente recortes de gastos.
La parte esencial de la inversión en activos físicos de infraestructura se refiere a las actividades de mantenimiento. Por lo tanto, el retraso o la falta de mantenimiento resulta en costos más amplios: impide la movilidad en el mercado interior, aumenta el riesgo de accidentes y conduce a mayores emisiones de CO2 sector del transporte. Además, «ahorros» de retrasar o la falta de mantenimiento será falso economía como la infraestructura se degradará hasta el punto en que debe ser reemplazado que es más costoso que el mantenimiento regular y aumentar el riesgo de accidentes graves y graves. (European Federación de la Industria de la Construcción (FIEC) – 2021).

Antes de pensar en el mantenimiento, el primer aspecto a considerar en el logro de alto rendimiento es la fiabilidad. La fiabilidad se define como la probabilidad de éxito que un activo físico tiene para cumplir su función durante un período de tiempo específico bajo condiciones de operación específicas. El mantenimiento es la ación para restaurar la función de activo físico antes o después de que la falla funcional ocurre. De hecho, muchos de los activos físicos de infraestructura como la construcción, puentes, paso elevado, paso subterráneo, encubierto, carretera y equipos estáticos (Buque, torres, tuberías) tienen una alta fiabilidad a lo largo de su ciclo de vida, que se basa en la robustez de dicha integridad de los activos físicos. Sin Embargoo, factores externos como las condiciones ambientales, el estrés de carga y el uso pueden afectar a la fiabilidad de las infraestructuras.
El principal concepto de mantenimiento, o en otras palabras, mantenimiento preventivo, es detectar tales condiciones y la degradación de los activos físicos antes de que ocurra el fallo, para evitar el impacto en la interrupción del servicio público o incluso desencadenar un accidente grave. De hecho, el principio general de mantenimiento también se aplica a los activos de infraestructuras, que consideran la implementación de diferentes métodos de mantenimiento preventivo en lugar de mantenimiento correctivo.El mantenimiento preventivo em las infraestruras también evitan acidentes graves.
Al aplicar el mantenimiento preventivo, el sistema de infraestructura recuperará gran parte o total de la confiabilidad inicial, acercando el sistema de infraestructura al estado como nuevo, teniendo un efecto positivo en la confiabilidad del sistema de infraestructura.
El mantenimiento preventivo se puede dividir en Programado y Predictivo. El mantenimiento programado se basa en el calendario que se define teniendo en cuenta los datos de fiabilidad, así como una recomendación del proveedor o procedimientos internos. El Mantenimiento predictivo se basa en los valores de facture de estrés medidos por el sensor o incluso mediante la aplicación de pruebas no destructivas como ultrasonidos, infrarrojos, radiografías y otros.
La correcta implementación de las tareas de mantenimiento para renovar la fiabilidad debe definirse desde el concepto de sistema de Infraestructura basado en el Programa de Confiabilidad y Mantenimiento como se discutirá en el próximo ítem.
2 – Programa de Confiabilidad y Mantenimiento para Infraestructura
Las actividades de mantenimiento aplicadas a los activos físicos de infraestructuras deben enmarcarse en un Programa de Mantenimiento, que se implementa a lo largo de las diferentes fases del ciclo de vida, desde el concepto hasta el desmantelamiento.
Durante la fase conceptual, el análisis preliminar de peligros (PHA) es el principal inicial análisis relativo a la seguridad, que tiene como objetivo capturar los diferentes riesgos ocupacionales desencadenados por errores humanos o por la degradación de fallas de activos físicos de infraestructura a lo largo de las fases de ciclos de vida diferentes, como el diseño, la construcción y la operación. De hecho, muchas de esas causas de peligro, como gritea, la corrosión y la fatiga, pueden mitigarse mediante un mantenimiento preventivo definido inicialmente por el método MCR.
El Mantenimiento Centrado en la Confiabilidad (MCR) es un método aplicado inicialmente durante la fase de diseño, que tiene como objetivo definir las tareas de mantenimiento basadas en el modo y efecto de falla del equipo, así como el riesgo asociado. El MCR se realiza en un taller con diferentes expertos en mantenimiento y operación para discutir sobre la tarea de mantenimiento del equipo, así como el intervalo de la prueba y el mantenimiento preventivo. La información de entrada para realizar el MCR son las infraestructuras de Activos Físicos modos de falla, causas, consecuencias y riesgo. Dicha información se define sobre la base del Análisis de Efectos y Modo de Fallo (FMEA). El MCR se aplica a diferentes activos físicos de infraestructura. En la industria ferroviaria, estos activos físicos representan un importante agujero en términos de seguridad y rendimiento del ferrocarril. Un buen ejemplo es el componente ferroviario que, en caso de fallo, provocará un impacto en la disponibilidad operativa del sistema ferroviario y puede desencadenar un accidente grave, como el descarrilamiento, como muestra la figura 2.

En la figura 2 se describen los modos de fallo, las causas y las consecuencias del ferrocarril, así como el riesgo que se considera intolerable sobre la base de la combinación de las frecuencias de causa y la gravedad de las consecuencias. Sobre la base de dicha evaluación, se definen diferentes tipos de tareas de mantenimiento y sus frecuencias para mitigar el riesgo, como la inspección visual y la inspección de vehículos de carretera (prueba ultrasónica). Los métodos similares en comparación con el enfoque de MCR es el RBI.
La inspección basada en el riesgo (RBI) se aplica inicialmente en la fase de diseño y más tarde durante la fase de operación. El RBI tiene un concepto similar del MCR, sin embargo el alcance del análisis es un activo físico, que en caso de fallo puede desencadenar un accidente grave. Los métodos RBI se implementan en base a procedimientos y estándares específicos como: API 580, API 581 y EN 1691, que pueden ser cualitativos o semicuantitativos basados en los niveles de aplicación de RBI. El RBI cualitativo (nivel 0) se basa en la simple evaluación del riesgo que considera la probabilidad de fracaso y la categoría de gravedad. Tal RBI se aplica en alto nivel y durante el diseño. El RBI Semi-Quantitative (Nivel 1 y 2) considera el factor de degradación (DF), al calcular la probabilidad de fallo basado en el sistema de infraestructura. El DF considera el espesor de degradación de grietas o corrosión u otros modos de falla medidos durante el funcionamiento por la prueba no destructiva aplicada para diferentes modos de falla, como la corrosión, la erosión y el crack.
La figura 3 muestra un ejemplo de RBI aplicado para un puente, que puede ser un puente ferroviario, un puente de carretera, un paso elevado que depende de su integridad y la correcta inspección y aplicación de tareas de mantenimiento preventivo en una frecuencia adecuada para evitar accidentes graves.

Además de los métodos cualitativos, es importante contar con un análisis cuantitativo para predecir los activos físicos de la infraestructura, como el análisis de datos de vida útil, también conocido como análisis de Weibull, que tiene como objetivo definir la función de densidad de probabilidad de equipos/ componentes para definir las curvas de fiabilidad y el patrón de tasa de fallo del equipo basada en el princípio de la curva de la bañera, que representan diferentes tipos de formas de tasa de fracaso, como la vida temprana, la vida útil y el desgaste. Depende del tipo de patrón de tasa de fallo, se llevan a cabo diferentes estrategias de mantenimiento, así como la predicción del tiempo de intervención.
En el caso de los Activos Físicos de Infraestructuras, el Análisis de Degradación Probabilística (PDA) es más apropiado para predecir dicha fiabilidad física de los activos y la probabilidad de fallo. El PDA tiene como objetivo definir la fiabilidad del activo físico basado en los datos de fallas de degradación de integridad relacionados con el espesor de grietas, corrosión, erosión medida por métodos no destructivos. Mediante la aplicación de este método, es posible predecir cuándo se logrará el fallo funcional sobre la base de la tendencia del espesor de evolución en el tiempo y el límite de espesor o profundidad (grieta o corrosión) logro como muestra la figura 4. Además, mediante la recopilación de diferentes puntos de degradación en diferentes momentos, la fiabilidad o probabilidad de fallo de la función de degradación también se puede definir como muestra la figura 4.

La línea rosa de 1,5 mm es el límite de corrosión, donde se espera que ocurra el fallo funcional. Las otras líneas son diferentes mediciones que proyectan la evolución de la corrosión en puntos de diffente a lo largo del tiempo. Por lo tanto, si proyectamos la intercepción de cada una de estas líneas con la línea recta (1,5 en axxis Y) en x axxis, habrá diferentes tiempos de fallas funcionales. Tenga en cuenta que este perfil puede cambiar a lo largo del tiempo y, en consecuencia, la frecuencia de inspección también cambiará. Estos tiempos se utilizan para predecir la confiabilidad, aumentar la tasa de fallas y, en base a dicha información, definimos cuándo debe realizarse la inspección, como muestra la figura 5.

Sobre la base de la cifra anterior, después de 20.983 año, la fiabilidad disminuirá. Por lo tanto, en este caso, 20.983 años es un tiempo de referencia para realizar un overhall en esta infraestructura debido a que la corrosión está alcanzando un valor cercano al fallo funcional (1.5mm). Sin embargo, la primera corrosión se detectó después de 10 años. (como se define en el primer gráfico). Por lo tanto, este tipo de información ayuda a definir el intervalo inicial de inspección cuando estos datos están disponibles para proyectos anteriores en condiciones similares, así como durante la operación.
Basado en la primera cifra, el intervalo de inspección (no – prueba destructiva para detectar la corrosión tickness) se puede definir como cada 5 años y después del 10º año, para realizar la inspección anualmente.
Tenga en cuenta que inicialmente, el intervalo de inspección general se definió para cada 5 años (basado en la recomendación RCM/ RBI), pero después del 10º año, comienzan a realizar la inspección (no – prueba destructiva) cada año.
La línea rosa de 1,5 mm es el límite de corrosión, donde se espera que ocurra el fallo funcional. Las otras líneas son diferentes mediciones que proyectan la evolución de la corrosión en puntos de diffente a lo largo del tiempo.
Por lo tanto, si proyectamos la intercepción de cada una de estas líneas con la línea recta (1,5 en axxis Y) en x axxis, habrá diferentes tiempos de fallas funcionales. Tenga en cuenta que este perfil puede cambiar a lo largo del tiempo y, en consecuencia, la frecuencia de inspección también cambiará.
Estos tiempos se utilizan para predecir la confiabilidad, aumentar la tasa de fallas y, en base a dicha información, definimos cuándo debe realizarse la inspección, como muestra la figura 4.
El Análisis RAM es también un método importante que permite abarcar diferentes equipos que forman parte de un Sistema de Infraestructura como el Sistema de Agua o el Sistema de Distribución de Energía o incluso estructuras Civiles específicas como una carretera o un puente. Con el fin de representar la combinación de la falla del equipo y su impacto en la disponibilidad operativa de infraestructura de alto nivel
El Análisis de Crecimiento de Confiabilidad (RGA, por sus siglas en inglés), como muestra la figura 6, tiene como objetivo verificar el efecto de las condiciones de mantenimiento y operación en el rendimiento del equipo al observar la tendencia del MTBF y la intensidad del gráfico de fallas. Cada vez que el MTBF disminuye a lo largo del tiempo hay una degradación de la confiabilidad. Cada vez que el MTBF aumenta a lo largo del tiempo, hay un crecimiento de confiabilidad. Y cada vez que el MTBF es constante a lo largo del tiempo, no hay degradación o crecimiento de confiabilidad. Por lo general, el crecimiento de la fiabilidad del equipo se lleva a cabo solo si se produce un rediseño, pero la sustitución de un equipo específico por otro mediante el uso de diferentes proveedores con mejores equipos también puede producir el aumento de MTBF que también se interpreta como crecimiento de la fiabilidad por los expertos en mantenimiento. Tenga en cuenta que el modelo de crecimiento de la fiabilidad aplica el concepto correcto de MTBF porque no es un valor absoluto, sino una función que demuestra la disminución (constante o aumento) de mantenimiento, inspección o intervalo de falla a lo largo del tiempo. Los métodos de crecimiento de la confiabilidad se aplican muy bien al sistema de infraestructura para permitir la predicción de la próxima vez a la inspección basada en la reducción de la tendencia de MTBI (tiempo entre inspecciones). Tal método se llama inspección basada en el crecimiento de la confiabilidad basado en la inspección (RGBI), Calixto E, 2016.

La Figura 6 muestra el siguiente tiempo de inspección considerando el tiempo de inspección anterior que se reduce basado en el efecto de envejecimiento y degradación sobre la confiabilidad de los activos físicos de la estructura. Este métodos junto con el PDA son los dos métodos de ingeniería de confiabilidad cuantitativa más importantes aplicados a los sistemas de infraestructura para apoyar el mejor momento para realizar una inspección o mantenimiento preventivo.
Finalmente, el Total Productive Maintenance (TPM) es una filosofía para tener una tarea de mantenimiento muy productiva al reducir el tiempo de reparación/reemplazo eliminando los errores y manteniendo el servicio de mantenimiento de alta calidad. Este enfoque se aplica en todo el mundo y también se puede aplicar durante el Sistema de Infraestructura durante el servicio de mantenimiento para reducir el tiempo de inactividad del servicio y que afecta la falta de disponibilidad de servicios cruciales para el público como el transporte, la energía y las telecomunicaciones.
3 – Mantenimiento 4.0 aplicado para infraestructuras.
La Inteligencia Artificial (A.I) tiene como objetivo permitir a la máquina pensar y tomar su propia decisión sobre la base de los datos recogidos y evaluados automáticamente sin ninguna intervención humana. La principal diferencia de la aplicación de aprendizaje automático A.I y los métodos anteriores, en eso. en lugar de la interfaz humana constante con nuevos datos de entrada, el aprendizaje automático A.I dará nuevas salidas basadas en nuevos datos que vienen sin y la interfaz humana. La A:I se ha aplicado a diferentes campos como estudios de biología, medicina, finanzas e ingeniería con casos exitosos de uso de datos numéricos y categóricos, texto e imágenes.
Basado en el EFNMS – Comité Europeo de Mantenimiento 4.0 (ECM4.0) 2021, la Industria 4.0 es un nuevo paradigma y la última revolución industrial, que se ha implementado en todo el mundo intensivamente en los últimos cinco años y está respaldado por la utilización de Habilitación de Tecnologías Digitales llamado 4.0.
El Maintenance 4.0 es el uso de dicha tecnología digital aplicada a los activos físicos para el mejor uso de los datos, transformados en información para permitir una decisión estratégica de Mantenimiento rápida, automática y en algunos casos independiente.
El uso de diferentes tecnologías de habilitación 4.0 basado en la figura 7, facilita la función de mantenimiento para realizar diferentes actividades y apoyar el activo físico para lograr un alto rendimiento.

La mayoría de estos permite especialmente el Análisis de Big Data, Machine Learning, Deep Learning y Cloud Computing se puede aplicar para monitorear la degradación del Sistema de Infraestructura, clasificar y alertar la degradación y predecir la Vida Útil Restante (RUL) y el estado de salud (SoH). Dado que el objetivo principal del trabajo es discutir los métodos que permiten definir el intervalo de inspección y el mantenimiento preventivo para un mayor rendimiento en la disponibilidad operativa y la seguridad, nos centraremos en los métodos de aprendizaje automático.
La aplicación de machine learning se aplica para la clasificación de criticidad de equipos, predicciones de regresión de fallas y la aplicación automática de la Gestión de Salud Pronóstica (PHM). El PHM tiene como objetivo definir los equipos de vida útil restante (RUL) y el estado de salud (SoH) sobre la base de datos de monitoreo en línea o prueba no destructiva mediante la medición de los factores estresantes. En el caso del sistema de infraestructura, el factor de tensión son la vibración, el voltaje, la temperatura, la humedad, el espesor de grietas, la profundidad de corrosión y otros parámetros físicos que conducen al equipo se degradan a un fallo funcional.
El concepto detrás de Machine Learning es utilizar el conjunto de datos (con diferentes variables de datos) para agrupar, clasificar o predecir la respuesta de las variables futuras automaticamente sin intervención humana. El aprendizaje automático aplicado a los clústeres se denomina aprendizaje automático sin supervisión. Por otro lado, el Aprendizaje Automático Supervisado puede ser clasificado y Clasificación y regresión. La Supervise Machine Learning Classification tiene como objetivo definir una nueva clasificación de datos (etiqueta) basada en el conocimiento predefinido de la clasificación de un conjunto de datos anterior.
La regresión de la Clasificación de Aprendizaje Automático No Supervisado tiene como objetivo predecir la variable de respuesta basada en predictores considerando el conjunto de datos conocidos predefinidos. El proceso de UML se aplica para organizar y agrupar diferentes infraestructuras físicas basadas en sus variables de datos.
En el caso de SMLC o SMLR, para clasificar y predecir la respuesta de datos, el modelo de aprendizaje automático divide el conjunto de datos en los datos de entrenamiento (~70% del conjunto de datos) y los datos de prueba (~30% del conjunto de datos). El paso siguiente es aplicar un algoritmo a los datos de entrenamiento para el proceso de aprendizaje y luego elaborar un modelo. El modelo se aplicará a los datos de la prueba y se verificará el resultado. Si el resultado es satisfactorio, el nuevo conjunto de datos puede utilizar el mismo modelo definido sobre la base del conjunto de datos anterior para hacer predicciones y si el resultado es satisfactorio, se valida el modelo.
Además de SML y UML, los métodos de aprendizaje profundo también se pueden aplicar para apoyar el mantenimiento preventivo del sistema de infraestructura. El DL es un método de aprendizaje automático más sofisticado que aplica una red neuronal profunda que abarca várias capas ocultas como muestra la figura 8. Los principios de la red neuronal profunda consideran diferentes capas como capa de convolución, capa de agrupación, ReLu, completamente conectado, Softmax y la clasificación de la imagen de salida.

A pesar de la A.I Deep Machine Learning y otros métodos, así como los métodos de ingeniería de fiabilidad, es necesario integrar tales soluciones en un Sistema de Gestión de Activos para permitir la gestión de las tareas de mantenimiento preventivo definidas para todos estos métodos y asegurarse de que los recursos adecuados se asignan en el momento adecuado para mitigar la Infraestructura Riesgo de Activo Físico de indisponibilidad a lo largo del tiempo y accidentes mayores. El siguiente punto discutirá la Gestión de Integridad de Activos como parte de la Gestión de Activos.
4 – Gestión de la integridad de los activos de Infraestructura
Por lo tanto, los elementos críticos de seguridad (SCE, por sus siglas en inglés) son los activos físicos, que en caso de fallo, pueden conducir a un accidente grave, como un incendio de avión, liberación de nubes tóxicas, explosión, incendio, derrame de productos tóxicos, accidente aéreo, colisión de trenes o descarrilamiento. De hecho, el accidente mayor puede ser provocado por un fallo de integridad de la infraestructura, software, hardware o error humano o una combinación de factores tales como muestra la figura 9.
Para mitigar tal riesgo de accidente grave es necesario en el primer paso la implementación del Programa de Confiabilidad y Mantenimiento (R&M) en la primera etapa del concepto de ciclo de vida del activo físico e implementar todas las recomendaciones de tales métodos de R&M. Después de eso, es necesario implementar el programa de gestión de riesgos e inspección y prueba durante la fase de operación.

El Programa de Integridad de Activos puede aplicar los mismos elementos de la AM definidos en la norma ISO 55000, como el contexto de la organización, el liderazgo, la planificación, el apoyo, la operación y la evaluación del desempeño, pero debe centrarse en la gestión de los elementos críticos de seguridad.
Desde 2010, la nueva era de la Industria 4.0 se convierte en realidad para muchas industrias en todo el mundo. En los últimos cinco años se ha aplicado al desarrollo de la nueva tecnología IOT AM en base a diferentes temas como Big Data, Prognostic Health Maintenance y Machine Learning, siendo parte del llamado Maintenance 4.0.
A pesar de todo el desarrollo, que permiten una AM integrada demasiado enfoque se ha dado para el mantenimiento y una falta de esfuerzo para la seguridad en relación con la gestión de los elementos críticos de seguridad.
Sin embargo, es muy importante establecer un proceso que permita un flujo AIM efectivo integrado al proceso AM.

Dado que el elemento crítico de seguridad se define sobre la base de un análisis de riesgo previo teniendo en cuenta la gravedad crítica, la gestión de riesgos de dicha SCE se realiza mediante el modelo de barrera se actualiza automáticamente y permite a los gestores de integridad de activos y seguridad gestionar el riesgo de los elementos críticos de seguridad en la base diaria.
El Deep Learning A.I, u otro tipo de aprendizaje automático debe integrarse en el proceso AIM para permitir la detección y predicción de degradación automática. Además, es necesario que todas las predicciones que provienen de los métodos A.I y Fiabilidad se traduzcan en órdenes de trabajo relacionadas con los servicios de Servicio de Mantenimiento que deben implementarse a lo largo del tiempo, incluidos los KPI de Mantenimiento y Fiabilidad, plan estratégico de gestión de activos y mitigación de riesgos operativos.
5 – Conclusión
La gestión de Integridade de Ativos para el sistema de infraestructura deve empecar en la fase de concepto y necesita ser implementada adecuadamente a lo largo del ciclo de vida de la infraestructura considerando lo siguiente:
- Fase conceptual: análisis preliminar de los peligros para la mitigación de los riesgos internos y la definición de los requisitos de seguridad
- Fase de Deseno: Implementación de métodos cualitativos y cuantitativos como FMEA, RCM, RBI, PDA, RAM para requisitos cualitativos y cuantitativos detallados y definiciones de tareas de mantenimiento
- Fase de Construcción: Análisis preliminar de peligros para la fase de construcción teniendo en cuenta el requisito de seguridad definido durante el diseño
- Fase de verificación y validación: Ti impulsa la prueba de verificación y validación necesaria para garantizar la seguridad.
- Fase de Operacion: Gestion de integridade de Activos físicos de infrastructura basado em ISSO 55001 e cons A.I
Autor: Eduardo Calixto, ECC Germany.
Bibliography
Calixto.E. «Gas and Oil Reliability Engineering: Modelling and Simulation. Second edition, Elsevier ISBN: 9780123919144, Release in 26 May2016.
Calixto.E. «Safety Science: Methods to Prevent Incident and worker Health Damage at Workplace. Bentham Science, Release in December 2014.
Calixto.E. “RAMS and LCC engineering applied to railway industry: Analysis, Modelling and Optimization”. 18-04-2018.Amazon. ISBN-13: 978-1986524704.
Calixto.E. “Asset Management based on Operational Availability And Life Cycle Cost Optimization Achievement:” The Offshore Process Case Study. Euromaintenance 2016 – Greece Atennas.
Calixto.E. “Asset Management Program implementation as the basis for sustaining asset high performance.” The 2nd Indonesia Conference and Exibition. Oil and Gas Asset Integrity. Maintenance and Inspection Management. Jakarta – Indonesia 2017
Calixto.E .“Good Practices of RCM and RBI applied to AIM.” The 2nd Indonesia Conference and Exibition. Oil and Gas Asset Integrity. Maintenance and Inspection Management. Jakarta – Indonesia 2017
Calixto.E .“Asset Integrity Management from Concepts to Operation phase”. ARDC 2018, Denmark – Copenhagen.
Calixto.E. “RAMS Program implementation for Electrics and Electronics in Railways Industry”. The Electric and Electronic Engineering Conference 2018. Guangzhou -China 2018.
Calixto.E. “Asset Integrity Management throughout the Asset Lifecycle”. Euromaintenance 2018, Antwerp – Belgium.
Calixto.E. RAMS Program Implementation for Railways Industry: Lessons Learned with Reliability Engineering Applications throughout the Railways Assets Life Cycle Case ”. ARDC 2018, Shanghai, China.
Calixto.E. Human Reliability analysis applied to reliability and safety analysis. ARDC 2019, Berlin, Germany.
Calixto.E. “Reliability 4.0: The oil and Gas industry case study”. Indonesia Maintenance 4.0 conference, Jakarta, Indonesia 2019.
Calixto.E. “Artificial Intelligence for Maintenance 4.0”. ISBN:9798671514919 28. Released: August 2020.
Calixto.E. Artificial Intelligence Unsupervised Machine Learning applied for Maintenance plan optimization, OMAINTEC, OMAN.2020
Calixto.E. “The Adaptative Prognostic Health management as part of Intelligent asset Management. Maintenance Workshop (APMI), Portugal.2020
Calixto.E. “The reliability 4.0 and FRACAS 4.0 as part of Asset Management solution for Water Facilities. Asset Performance 4.0 Conference (BEMAS), Belgium.2020.
Dinos qué te ha parecido el artículo
Artículos recomendados
7.6 Aplicación del Análisis Causa Raíz

Un procedimiento para analizar el riesgo en el proceso de innovación de sistemas de gestión del mantenimiento

Confiabilidad Humana y el Humano Confiable Parte II

Capacitación en mantenimiento industrial

Publica tu artículo en la revista #1 de Mantenimiento Industrial
Publicar un artículo en la revista es gratis, no tiene costo.
Solo debes asegurarte que no sea un artículo comercial.
¿Qué esperas?
O envía tu artículo directo: articulos@predictiva21.com
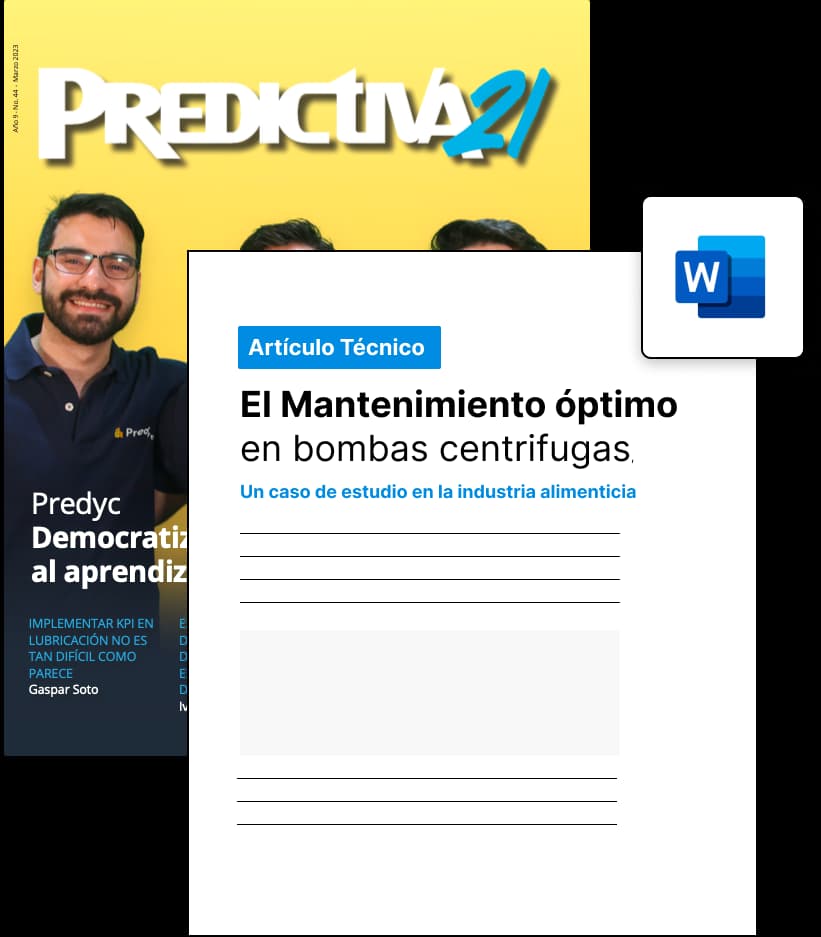