Gestión de paradas de mantenimiento
Articulo2 de julio de 2023
Autor: Predictiva 21La revista digital de Mantenimiento, Confiabilidad y Gestión de Activos.
La gestión de paradas de mantenimiento y sus resultados son, en muchos sentidos, indicativos del rigor de los sistemas de gestión de una empresa. Si bien las actividades de mantenimiento fuera de línea generalmente se planifican, programan y ejecutan de acuerdo con métodos de rutina, y el alcance del trabajo a nivel de tarea y las actividades individuales rara vez cambian, la principal diferencia entre las actividades de rutina y las interrupciones es la intensidad. Se lleva a cabo una gran cantidad de tareas simultáneamente, lo que aumenta significativamente los riesgos relacionados con la seguridad, la calidad y el costo. Y con grupos de trabajo de mantenimiento capaces de crecer de 20 a más de 600 personas, proporcionando más de 7000 horas-hombre por 24 horas y días a semanas, optimizar los horarios de trabajo para equilibrar las necesidades de mantenimiento y el tiempo de actividad de la planta es significativo. Cuando se opera a un nivel moderado, los sistemas débiles pueden ocultarse a simple vista. Cuando son tan intensos como la reacción violenta, simplemente no hay forma de ocultarlos. De alguna manera, son la prueba definitiva de la fortaleza de un sistema. Por ejemplo, una buena programación no compensa una mala ejecución. Con esto en mente, si los clientes desean mejorar su rendimiento de apagado, primero los ayudamos a consolidar o incluso a desarrollar un marco de procesos completo y sólido y luego lo ponemos en práctica a través de aplicaciones prescriptivas. 
Gyogi MitsutaPreparación para la certificación CMRP
Carlos VillegasAplicación de la ISO 14224 en la Gestión de Mantenimiento y Confiabilidad
Jose Contreras MarquezCostos y Presupuestos de Mantenimiento%252FImagen%252FRAMPREDYC-1730060420837.webp%3Falt%3Dmedia%26token%3D2634a7f0-988e-4022-b91f-382503e6e9db&w=3840&q=75)
Enrique GonzálezAnálisis de Confiabilidad, Disponibilidad y Mantenibilidad (RAM)
Características clave de una planificación eficaz de las paradas de mantenimiento y de un sistema de gestión de la calidad
Un sistema sólido de gestión de paradas abarca áreas como:- Proceso coherente y detallado y trabajo normalizado
- Planificación avanzada del trabajo y procesos de cambio rápidos
- Objetivos definidos y expectativas claras
- Visibilidad del progreso del ciclo de parada
- Supervisores formados y grupos de trabajo comprometidos
- Mejora del flujo de información dentro de los equipos
- Mejora de los informes y el suministro de datos
Problemas habituales en los cierres
Estos son los problemas más habituales que se presentan en la gestión de paradas de mantenimiento: Las políticas de cierre y los planes de campaña no están actualizados, detallados o no se cumplen. Esto conduce a la inconsistencia, lo que a su vez deja a la gestión de paradas sin tiempo suficiente para planificar y prepararse para la ejecución. El alcance del trabajo a menudo está mal definido y administrado, y sin un plan de evaluación sólido, se agrega trabajo adicional en las semanas previas a la implementación. No existe un mecanismo efectivo para mantener informada a la alta gerencia sobre el progreso. El cierre puede durar solo unos días, pero la planificación y los preparativos llevan meses. La capacidad de seguir claramente la dirección del proceso es importante. Incluso cuando estas estructuras de alto nivel están en su lugar, la información sobre tareas de mantenimiento específicas a menudo es incompleta o inexacta, como estimaciones infladas de horas-hombre o componentes críticos faltantes. El vínculo entre lo macro y lo micro es obvio y aquí es donde tienden a ocurrir las fallas en los procesos. La importancia y los requisitos de las fases de apertura y cierre del cierre a menudo no se reconocen. Estas fases "cierran" el resto de la operación de parada. Si no se gestionan adecuadamente, pueden tener un efecto negativo en todo.Cursos recomendados


En línea en vivo5 de julio


En línea en vivo5 de julio


En línea en vivo9 de agosto
%252FImagen%252FRAMPREDYC-1730060420837.webp%3Falt%3Dmedia%26token%3D2634a7f0-988e-4022-b91f-382503e6e9db&w=3840&q=75)

En línea en vivo1 de noviembre
Realización del mantenimiento de parada
Los errores inesperados pueden ocurrir en cualquier momento y tener consecuencias graves. Como resultado, ciertos tipos de equipos requieren tiempo de inactividad para realizar el mantenimiento preventivo de estos componentes. Siempre que la planificación y programación de tareas se realice de manera efectiva, el mantenimiento del tiempo de inactividad se puede completar rápidamente.- Planificar las herramientas adecuadas: Con las paradas, la planificación puede variar de las grandes empresas a las pequeñas. Algunas pueden optar por una simple hoja de cálculo o un software de gestión de proyectos, mientras que otras pueden optar por un método que implique el uso de software GMAO o software especializado de planificación de paradas.
- Realización de reuniones de progreso: El período durante las paradas es crucial, ya que puede ayudar a identificar cualquier problema. Establecer un orden del día y revisar los calendarios puede garantizar que la parada va por buen camino y se ajusta a su calendario.
- Documentación adecuada: Con grandes plantas y equipos, es vital que cada paso esté documentado y que se cumplan las directrices de seguridad y calidad. También es una buena práctica dejar constancia de estos puntos para futuras consultas, de modo que el equipo de mantenimiento pueda revisar todos los aspectos de los procedimientos de parada y calidad.
Estrategias clave para mejorar el rendimiento de las paradas
Animamos a los responsables a tener en cuenta siete estrategias clave en su planificación de paradas de mantenimiento y en su gestión más amplia para abordar estos y otros problemas:- Ponga en tela de juicio su sistema de gestión: las grandes instalaciones suelen tener procedimientos de parada muy variados. Estandarizar su enfoque es el primer paso hacia la excelencia en las paradas, es decir, procesos estables y predecibles que impulsen la mejora.
- Gestione su ruta crítica: siempre comprobamos que evaluar las tareas de la ruta crítica en busca de oportunidades de mejora aporta valor. Esto incluye garantizar que las tareas cercanas a la ruta crítica se identifiquen y se comuniquen a los grupos de trabajo para que comprendan lo cerca que están de pasar a la ruta crítica si se producen retrasos.
- Implicar a la alta dirección: es esencial que la alta dirección participe en el proceso de desarrollo y tenga visibilidad del progreso.
- Implantar técnicas de mejora empresarial: desde la determinación avanzada del alcance de los trabajos hasta las técnicas de cambio rápido, la aplicación de técnicas de mejora conocidas y probadas puede reportar grandes beneficios.
- Seguimiento del proceso, no sólo de la preparación: los cierres suelen medir la preparación, pero recomendamos encarecidamente hacer un seguimiento visual de todos los hitos del proceso, es decir, de principio a fin. Esto incluye el cierre efectivo y la captura de aprendizajes para la mejora continua.
- Utilice sus datos: el desarrollo de las paradas genera enormes volúmenes de datos. No pierda la oportunidad de utilizar esos datos para garantizar la gestión de los obstáculos al rendimiento y, más ampliamente, para predecir la probabilidad de éxito.
Dinos qué te ha parecido el artículo
Artículos recomendados
Implementación exitosa de Mantenimiento Lean en la Industria Manufacturera

Autor: Predictiva 21La revista digital de Mantenimiento, Confiabilidad y Gestión de Activos.
Confiabilidad y Disponibilidad en sistemas críticos de informática y telecomunicaciones

Autor: Predictiva 21La revista digital de Mantenimiento, Confiabilidad y Gestión de Activos.
Uptime: gestionar los fallos antes de que se produzcan

Autor: Predictiva 21La revista digital de Mantenimiento, Confiabilidad y Gestión de Activos.
Serie: “Confiabilidad en Sistemas de misión Critica: Empezar por el Principio”. Sistemas de Puesta a Tierra (II Parte)

Autor: Predictiva 21La revista digital de Mantenimiento, Confiabilidad y Gestión de Activos.
Publica tu artículo en la revista #1 de Mantenimiento Industrial
Publicar un artículo en la revista es gratis, no tiene costo.
Solo debes asegurarte que no sea un artículo comercial.
¿Qué esperas?
O envía tu artículo directo: articulos@predictiva21.com
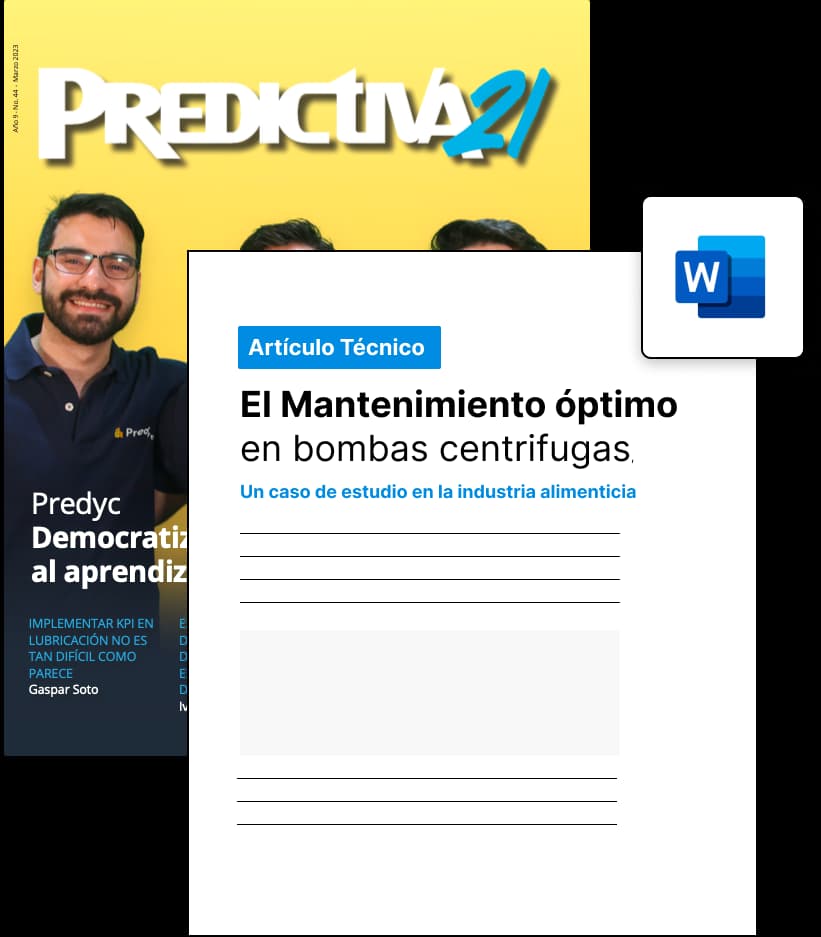
Gestión de paradas de mantenimiento
Articulo 2 de julio de 2023La gestión de paradas de mantenimiento y sus resultados son, en muchos sentidos, indicativos del rigor de los sistemas de gestión de una empresa. Si bien las actividades de mantenimiento fuera de línea generalmente se planifican, programan y ejecutan de acuerdo con métodos de rutina, y el alcance del trabajo a nivel de tarea y las actividades individuales rara vez cambian, la principal diferencia entre las actividades de rutina y las interrupciones es la intensidad. Se lleva a cabo una gran cantidad de tareas simultáneamente, lo que aumenta significativamente los riesgos relacionados con la seguridad, la calidad y el costo. Y con grupos de trabajo de mantenimiento capaces de crecer de 20 a más de 600 personas, proporcionando más de 7000 horas-hombre por 24 horas y días a semanas, optimizar los horarios de trabajo para equilibrar las necesidades de mantenimiento y el tiempo de actividad de la planta es significativo. Cuando se opera a un nivel moderado, los sistemas débiles pueden ocultarse a simple vista. Cuando son tan intensos como la reacción violenta, simplemente no hay forma de ocultarlos. De alguna manera, son la prueba definitiva de la fortaleza de un sistema. Por ejemplo, una buena programación no compensa una mala ejecución. Con esto en mente, si los clientes desean mejorar su rendimiento de apagado, primero los ayudamos a consolidar o incluso a desarrollar un marco de procesos completo y sólido y luego lo ponemos en práctica a través de aplicaciones prescriptivas. 
Gyogi MitsutaPreparación para la certificación CMRP
Carlos VillegasAplicación de la ISO 14224 en la Gestión de Mantenimiento y Confiabilidad
Jose Contreras MarquezCostos y Presupuestos de Mantenimiento%252FImagen%252FRAMPREDYC-1730060420837.webp%3Falt%3Dmedia%26token%3D2634a7f0-988e-4022-b91f-382503e6e9db&w=3840&q=75)
Enrique GonzálezAnálisis de Confiabilidad, Disponibilidad y Mantenibilidad (RAM)
Características clave de una planificación eficaz de las paradas de mantenimiento y de un sistema de gestión de la calidad
Un sistema sólido de gestión de paradas abarca áreas como:- Proceso coherente y detallado y trabajo normalizado
- Planificación avanzada del trabajo y procesos de cambio rápidos
- Objetivos definidos y expectativas claras
- Visibilidad del progreso del ciclo de parada
- Supervisores formados y grupos de trabajo comprometidos
- Mejora del flujo de información dentro de los equipos
- Mejora de los informes y el suministro de datos
Problemas habituales en los cierres
Estos son los problemas más habituales que se presentan en la gestión de paradas de mantenimiento: Las políticas de cierre y los planes de campaña no están actualizados, detallados o no se cumplen. Esto conduce a la inconsistencia, lo que a su vez deja a la gestión de paradas sin tiempo suficiente para planificar y prepararse para la ejecución. El alcance del trabajo a menudo está mal definido y administrado, y sin un plan de evaluación sólido, se agrega trabajo adicional en las semanas previas a la implementación. No existe un mecanismo efectivo para mantener informada a la alta gerencia sobre el progreso. El cierre puede durar solo unos días, pero la planificación y los preparativos llevan meses. La capacidad de seguir claramente la dirección del proceso es importante. Incluso cuando estas estructuras de alto nivel están en su lugar, la información sobre tareas de mantenimiento específicas a menudo es incompleta o inexacta, como estimaciones infladas de horas-hombre o componentes críticos faltantes. El vínculo entre lo macro y lo micro es obvio y aquí es donde tienden a ocurrir las fallas en los procesos. La importancia y los requisitos de las fases de apertura y cierre del cierre a menudo no se reconocen. Estas fases "cierran" el resto de la operación de parada. Si no se gestionan adecuadamente, pueden tener un efecto negativo en todo.Cursos recomendados


En línea en vivo5 de julio


En línea en vivo5 de julio


En línea en vivo9 de agosto
%252FImagen%252FRAMPREDYC-1730060420837.webp%3Falt%3Dmedia%26token%3D2634a7f0-988e-4022-b91f-382503e6e9db&w=3840&q=75)

En línea en vivo1 de noviembre
Realización del mantenimiento de parada
Los errores inesperados pueden ocurrir en cualquier momento y tener consecuencias graves. Como resultado, ciertos tipos de equipos requieren tiempo de inactividad para realizar el mantenimiento preventivo de estos componentes. Siempre que la planificación y programación de tareas se realice de manera efectiva, el mantenimiento del tiempo de inactividad se puede completar rápidamente.- Planificar las herramientas adecuadas: Con las paradas, la planificación puede variar de las grandes empresas a las pequeñas. Algunas pueden optar por una simple hoja de cálculo o un software de gestión de proyectos, mientras que otras pueden optar por un método que implique el uso de software GMAO o software especializado de planificación de paradas.
- Realización de reuniones de progreso: El período durante las paradas es crucial, ya que puede ayudar a identificar cualquier problema. Establecer un orden del día y revisar los calendarios puede garantizar que la parada va por buen camino y se ajusta a su calendario.
- Documentación adecuada: Con grandes plantas y equipos, es vital que cada paso esté documentado y que se cumplan las directrices de seguridad y calidad. También es una buena práctica dejar constancia de estos puntos para futuras consultas, de modo que el equipo de mantenimiento pueda revisar todos los aspectos de los procedimientos de parada y calidad.
Estrategias clave para mejorar el rendimiento de las paradas
Animamos a los responsables a tener en cuenta siete estrategias clave en su planificación de paradas de mantenimiento y en su gestión más amplia para abordar estos y otros problemas:- Ponga en tela de juicio su sistema de gestión: las grandes instalaciones suelen tener procedimientos de parada muy variados. Estandarizar su enfoque es el primer paso hacia la excelencia en las paradas, es decir, procesos estables y predecibles que impulsen la mejora.
- Gestione su ruta crítica: siempre comprobamos que evaluar las tareas de la ruta crítica en busca de oportunidades de mejora aporta valor. Esto incluye garantizar que las tareas cercanas a la ruta crítica se identifiquen y se comuniquen a los grupos de trabajo para que comprendan lo cerca que están de pasar a la ruta crítica si se producen retrasos.
- Implicar a la alta dirección: es esencial que la alta dirección participe en el proceso de desarrollo y tenga visibilidad del progreso.
- Implantar técnicas de mejora empresarial: desde la determinación avanzada del alcance de los trabajos hasta las técnicas de cambio rápido, la aplicación de técnicas de mejora conocidas y probadas puede reportar grandes beneficios.
- Seguimiento del proceso, no sólo de la preparación: los cierres suelen medir la preparación, pero recomendamos encarecidamente hacer un seguimiento visual de todos los hitos del proceso, es decir, de principio a fin. Esto incluye el cierre efectivo y la captura de aprendizajes para la mejora continua.
- Utilice sus datos: el desarrollo de las paradas genera enormes volúmenes de datos. No pierda la oportunidad de utilizar esos datos para garantizar la gestión de los obstáculos al rendimiento y, más ampliamente, para predecir la probabilidad de éxito.
Dinos qué te ha parecido el artículo
Artículos recomendados
¿Cómo serán las fábricas dentro de una década? La transformación progresiva hacia la Smart Factory

Autor: Predictiva 21La revista digital de Mantenimiento, Confiabilidad y Gestión de Activos.
Introducción al Análisis de Fallas Múltiples

Autor: Predictiva 21La revista digital de Mantenimiento, Confiabilidad y Gestión de Activos.
Uso del Programa Life CPR - ComSys© para la Selección del Accionador y el Arreglo Óptimo en Plantas Compresoras de Gas (III Parte)

Autor: Predictiva 21La revista digital de Mantenimiento, Confiabilidad y Gestión de Activos.
Pareto Principle and the “Bad Actors”

Autor: Predictiva 21La revista digital de Mantenimiento, Confiabilidad y Gestión de Activos.
Publica tu artículo en la revista #1 de Mantenimiento Industrial
Publicar un artículo en la revista es gratis, no tiene costo.
Solo debes asegurarte que no sea un artículo comercial.
¿Qué esperas?
O envía tu artículo directo: articulos@predictiva21.com
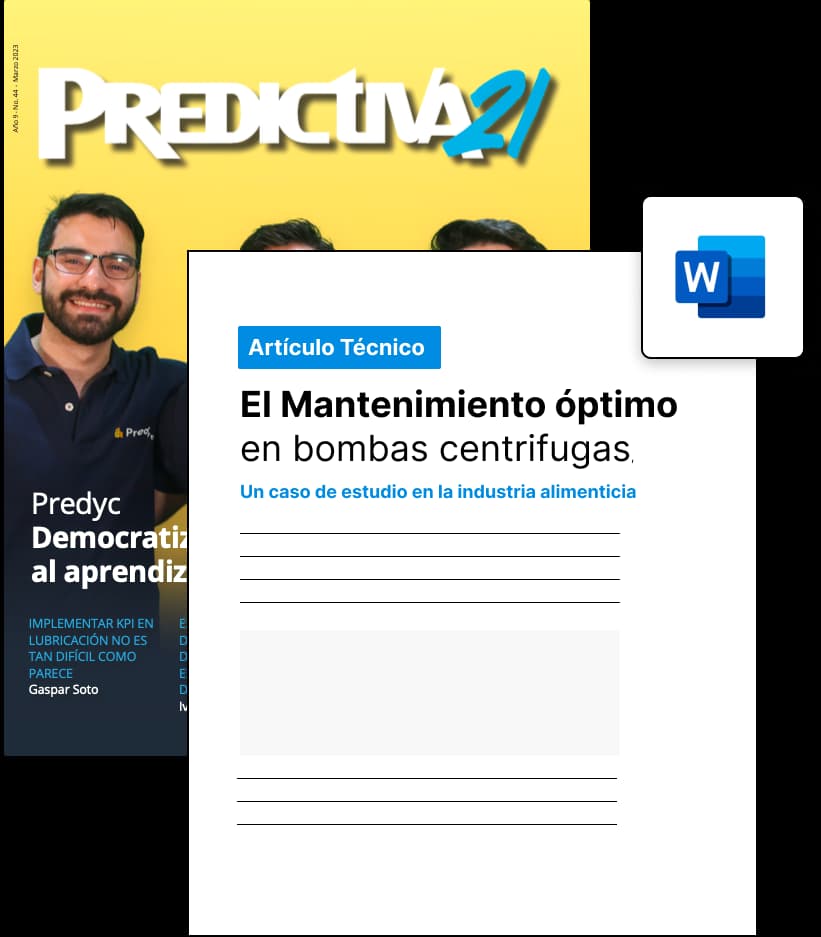