Hablemos de Mantenimiento Productivo Total
Articulo6 de enero de 2020
Introducción
Nace en mí la idea de escribir este artículo porque, en mi opinión, la mayor parte de los especialistas en este concepto, incluyendo a consultores, tienen una idea equivocada de lo que es el Mantenimiento Productivo Total (TPM por sus siglas en inglés) y creen que éste puede ser implementado en cualquier tamaño de empresa (MIPYME). Lo anterior basado en mi experiencia como consultor de mantenimiento industrial, así como en base en los estudios a fondo que, a lo largo de estos años, mis colegas y un servidor, hemos realizado.
Surgen entonces dos preguntas; ¿qué es el Mantenimiento Productivo Total? y ¿cómo pueden ser aprovechados estos conocimientos por las micros, pequeñas y medianas empresas? Pongámonos en contexto y situémonos en la industria norteamericana durante los años de 1919 a 1939. En esa época ya existia la práctica de las ideas de Adam Smith (División del trabajo), empezaba a cobrar importancia la máquina pues se iniciaba la aplicación de trabajos de Mantenimiento correctivo, y se fueron sumando los trabajos de Taylor Administración científica del trabajo y los de Walter A. Shewhart, W. Edwards Deming y Joseph Juran con sus desarrollos sobre Estadística aplicada a la industria, Control estadístico de calidad y Ciclo Shewhart.
Esta situación originó la existencia de un número considerable de consultores y maestros, que impartieron estos conocimientos a todos los niveles de la industria norteamericana durante veinte años. Podemos pensar con certeza que éstos fueron los ingredientes principales que se “fundieron en un crisol” para dar vida al llamado Mantenimiento Productivo (PM, siglas en inglés) Ver Figura 1…

Al inicio de la Segunda Guerra Mundial en septiembre de 1939, Norteamérica se vio envuelta en el compromiso de ser la industria de guerra (proveedor) de Inglaterra y Francia, obligando a sus fábricas a trabajar las 24 horas del día. El interés de las industrias se enfocó solo para atender los problemas de productividad ahora aumentados por la guerra, por lo que se suspendieron las acciones de desarrollo industrial que se habían tenido antes de ésta. Las industrias dedicadas a pertrechar a los ejércitos aliados, comenzaron a perder su eficacia pues eran necesarias nuevas inversiones para obtener activos físicos y humanos adecuados, lo que hizo aparecer de forma palpable, la división de intereses. Por un lado, como sus propietarios burgueses industriales, no tenían estudios científicos sobre lo que debía ser una empresa, solo les interesaban las ganancias y no el cumplimiento con el usuario del producto. Por otro lado, el personal de la industria, aunque simpatizaba con las exigencias de sus clientes, estaba expuesto a presiones que exigían cada vez una mejor calidad y oportunidad. Por tal motivo, el mismo personal tuvo que dar solución a los problemas que surgían, adaptando y arreglando los activos físicos, mejorando e implementando durante casi tres años nuevos procesos de trabajo, etcétera; todo ello bajo su propia responsabilidad.
El 7 de diciembre de 1941 el ataque a Pearl Harbor ejecutado por la Armada Imperial Japonesa unió a la opinión pública estadounidense y al día siguiente el 8 de diciembre, los Estados Unidos declararon la guerra a Japón. A partir de entonces, Norteamérica continuó administrando su industria con su naciente Proceso Administrativo qué tomó el nombre de “Mantenimiento Productivo (PM, siglas en inglés)”, en el cual continuaron poniéndose en práctica nuevas ideas originadas por el personal que componía cada industria. El patriotismo del personal, incrementado por el ambiente y las grandes presiones a que estaban sujetos, aunado a la falta de apoyo de los propietarios, dieron como consecuencia que todo el personal de cada industria resolviera sus propios problemas. Se empezaron a hacer grupos entre todos los trabajadores de cualquier nivel, para dar sus opiniones a fin de resolver cada problema que se les presentaba y éste fue el nacimiento de los “grupos de trabajo”. En el mismo contexto y con el objeto de que el usuario se sintiera atendido en oportunidad y seguridad en cualquier lugar en donde él lo necesitara, las industrias adoptaron e implementaron las ideas castrenses de los ejércitos aliados (logística), las cuales se sumaron a las existentes y quedaron como parte integral del PM, ver Figura 2.

Inicio y consolidación del TPM (1948 - 1971)
Recordemos que Japón quedó destrozado como resultado de la guerra y fue ocupado por las fuerzas norteamericanas en septiembre de 1946, por el Comando Supremo de las Fuerzas Aliadas (SCAP, siglas en inglés). El General estadounidense Douglas MacArthur fue nombrado como responsable de establecer un programa de desarrollo con especialistas norteamericanos, para la reconstrucción de esta nación. Dentro de éstos, los más relevantes a nuestro juicio, fueron: W. Edwards Deming, Walter Andrew Shewhart y Joseph Moses Juran.
Desde los primeros años de su estancia en Japón, estos científicos se dieron a conocer con los máximos niveles industriales de ese país, compartiendo sus conocimientos en estadística, en calidad, en grupos PM, en logística, en síntesis en el PM, cuyos buenos resultados ya estaban a la vista del mundo industrial. Los especialistas mencionados empezaron su asesoría en ese nivel debido a que su objetivo, era la rehabilitación industrial del Japón para que éste pudiera pagar sus deudas de guerra. La experiencia que ellos habían tenido durante el lapso de 1939 a 1945 les había mostrado la incongruencia de no preparar en el PM a los propietarios y altos niveles industriales con poder de decisión. En Japón pudieron hacerlo, porque para la Unión de Científicos e Ingenieros Japoneses (UCIJ) y los altos niveles de la industria Japonesa, esta preparación realmente despertó un interés vital, además de que llenó sus expectativas de un promisorio futuro y estaba plenamente vinculado con la idiosincrasia de su pueblo.
El Dr. Deming durante su larga estancia por el Japón (1950 – 1980) llegó a adquirir un gran reconocimiento y una alta estima. Los japoneses le mostraron su aprecio instituyendo en 1951 el “Premio Deming” (una medalla de plata con su efigie).
Desarrollo del TPM
Para 1939 las empresas tenían una organización simple, desarrollada en base al “Proceso Administrativo” salido de los pensamientos y trabajos de Frederick W. Taylor y Henry Fayol y aún no se tenía un pensamiento sistémico. Cada entidad se consideraba desligada del resto del grupo. No existía una conciencia holística, por lo que las organizaciones eran mostradas cómo lo explica la Figura 3, una dirección general con tres o cuatro subdirecciones o gerencias para encargarse de las funciones primarias; producir, vender, administrar y desarrollar las finanzas.
El Mantenimiento Productivo (PM) se originó en el área de Producción, debido a que se consideró que esta atendía la elaboración del producto y además ahí funcionaban las máquinas, y a estas era necesario hacerles labores de mantenimiento. La tarea se facilitó por que ya existían en ella fundamentos sólidos sobre la división del trabajo, la ciencia y la administración aplicadas a la industria, el uso de la estadística, la búsqueda de la calidad del producto, etcétera.
Estos conocimientos, por razón natural, no existían en las áreas de ventas, administración o finanzas ya que se consideraba que ellas no tenían activos que mantener por que no elaboraban ningún producto. La figura 3 nos muestra un organigrama hipotético de una empresa norteamericana en 1950.


Seiichi Nakajima en 1950 era un alto funcionario del Instituto Japonés de Mantenimiento de la Planta (JIMP) y fue uno de los muchos industriales de alto nivel que recibieron las enseñanzas de Deming sobre el Mantenimiento Productivo Norteamericano PM. Nakajima en esa fecha inició sus estudios de PM sin salir del Japón, encontrando que la industria americana estaba organizada de manera similar a la mostrada en la Figura 3, es decir, ya trabajaban los gerentes, supervisores y obreros, de la Dirección de Producción, formando Grupos de Trabajo PM (GTPM) y ya se empleaba normalmente la Logística. Para facilitar nuestra percepción analicemos solamente la Gerencia de Producción de la mencionada figura y desarrollemos su organigrama (Ver Figura 4); esto fue lo que encontró Seiichi Nakajima cuando empezó a desarrollar sus estudios del Mantenimiento Productivo (PM).

Concepto del Mantenimiento Productivo Total (TPM)
La labor de cualquier industria es la de producir en forma conjunta como un solo equipo, como una orquesta, en donde cada dirección, gerencia, departamento, proveedor o persona, debe esforzarse en forma coordinada para obtener beneficios, para lo cual debe emplear con eficacia el capital de trabajo que integra a la empresa. Es evidente que hasta el departamento más insignificante tiene que conservar sus propios activos físicos, su propio capital de trabajo, así sean escritorios, equipos de cómputo, escobas, cortadoras de césped, etcétera; pues todos ellos colaboran en la obtención del producto y en última instancia en la satisfacción del usuario, que es lo que proporciona la permanencia de la empresa. Por esto, la administración PM debería existir para toda la organización ya que en toda ella existen activos que mantener. Esto fue lo que nos mostró con sus trabajos de más de 20 años el industrial Seiichi Nakajima.
La figura 5 nos proporciona la razón del por qué se le llama “Mantenimiento Productivo Total”.

Estructurando el TPM
En 1971, después de 20 años de esfuerzo, Nakajima puso en marcha en Japón lo que él llamó Mantenimiento Productivo Total (TPM). En este esquema, todo el personal de una empresa está obligado a realizar labores de PM. Lo anterior hace necesario construir sobre el organigrama existente de la empresa y con autoridad Staff , una estructura para administrar el TPM. En la Figura 6 estamos considerando como ejemplo a la Dirección de Producción, en el entendido de que esto se repite en forma similar en las Direcciones restantes. La función Staff está mostrada en color verde. Es necesario aclarar que más del 90% del personal que ejecuta estas funciones es el mismo que ya pertenece a la empresa y el restante porcentaje lo ocupará nuevo personal generalmente especializado en el funcionamiento del TPM.

Aquí podemos observar que el gran avance que proporcionó Nakajima a la industria mundial, fue hacer un nuevo proceso administrativo apoyándose en las ideas existentes de Fayol y Taylor, usando los dos tipos de autoridad conocidos, (de línea y de apoyo o staff ) y considerar al todo como un sistema. Es decir, su actividad es holística por lo que sus propiedades y funcionamiento deben ser analizadas en conjunto.
Implementación y desarrollo del TPM en una empresa
Esta tarea no es sencilla de hacer, pues requiere del absoluto interés del consejo de administración y dirección general y la ayuda de una empresa consultora de alta calidad y experiencia, la cual debe conocer a fondo como implementar los siguientes doce pasos:
Cursos recomendados
%2520para%2520evaluar%2520la%2520gesti%25C3%25B3n%2520del%2520mantenimiento%252FImagen%252Fss-1733758540053.png%3Falt%3Dmedia%26token%3D47b767f7-ea54-48eb-b001-3ada0bb6cbdc&w=3840&q=75)



%252FImagen%252FRAMPREDYC-1730060420837.webp%3Falt%3Dmedia%26token%3D2634a7f0-988e-4022-b91f-382503e6e9db&w=3840&q=75)



1º Paso: Crear el entorno apropiado
El consejo de administración, debe informar oficialmente a todo el personal de la empresa y proveedores, a través de un evento formal; de la decisión de establecer el TPM. Con este evento se busca la participación y compromiso de todos los integrantes, así como la comprensión del tema.
2º Paso: Crear programas de adiestramiento y desarrollo
En este punto se inicia la creación de programas de adiestramiento y desarrollo para todo el personal de la empresa.
3º Paso: Crear la organización para el TPM
Este es el momento de establecer el “Comité Promotor y Coordinador de Desarrollo del TPM” como Staff o apoyo de la alta dirección (Ver Figura 6).
4º Paso: Crear los objetivos y políticas para el TPM
El Comité Promotor y Coordinador definirá los objetivos generales a alcanzar a mediano y largo plazo (uno a tres años) recomendando las políticas necesarias que de éstos se deriven.
5º Paso: Crear el plan maestro para la desarrollo del TPM
El Comité Promotor y Coordinador elabora y establece un plan maestro para el desarrollo e implementación del TPM, este comité debe estar compuesto por verdaderos especialistas en la preservación y mantenimiento de los activos de capital existentes en la empresa, sus conocimientos deberán tener cimientos en la tecnología más avanzada incluyendo temas como la jerarquización de activos, el RCM, etcétera; con lo que se implementarán cursos y programas para preparar y adiestrar a todo el personal en las siguientes cinco tareas:
- Efectividad global del equipo.
- Preservación y Mantenimiento autónomo para todo el personal de Producción, Ventas, Finanzas etc.
- Preservación y Mantenimiento para el personal de mantenimiento.
- Capacitación y Desarrollo para todo el personal de la empresa.
- Preservación y Mantenimiento para los nuevos Activos de Capital.
6º Paso: Acto de iniciación TPM
Se organizará una reunión de todo el personal de la empresa, así como de personas importantes ligadas a ésta ya sean proveedores, empresarios, personas renombradas etcétera, con el objeto de aumentar el interés de los presentes por el evento. Esta junta debe ayudar a crear y desarrollar un clima proactivo y de deseos de superación en todo el personal de la empresa y proveedores. Cada responsable de comité (general, departamental, de sección y de grupo) informará sobre el trabajo planeado y desarrollado en cada uno de los cinco pasos antes mencionados, así como de sus resultados. Finalmente, se anunciará que a partir de ese momento cada persona empezará a trabajar de acuerdo a las enseñanzas recibidas usando las nuevas “herramientas” y conforme vayan progresando abandonen las que deben quedar en desuso.
Con la terminación de los pasos anteriores hemos obtenido el adiestramiento y desarrollo de todos los recursos humanos de la empresa, permitiendo que el Comité General del TPM jerarquice el inventario de recursos a Preservar y Mantener en tres categorías de acuerdo a su criticidad (Vital, Importante y trivial). Así mismo, les asigne prioridad de atención y auxilie en la formación de “equipos de proyecto”, integrados por personal de ingeniería, conservación, producción y círculos de calidad. Todo lo anterior se debe llevar a cabo siguiendo los pasos del 7 al 11.
7º Paso: Mejora de la efectividad global del equipo instalado
Para obtener ésta mejora es preciso hacer dos labores generales:
- 1a. Estudiar a fondo las características y rendimientos de los activos vitales e importantes, con el objeto de obtener el mayor provecho al utilizarlos en la debida forma.
- 2a. Eliminar los obstáculos que se oponen a la eficacia de los activos antes mencionados.
8º Paso: Implementar el plan de preservación y mantenimiento autónomo
Uno de los problemas más graves que existen en nuestra industria es que al personal de producción, ventas, finanzas y cualquier otra especialidad, no se le prepara en labores de Preservación y Mantenimiento de sus herramientas de trabajo. Este es un gran error porque debemos tener como principio que todo el personal que tenga que ver con el uso de una herramienta de trabajo, tiene la obligación de conocer su operación y cuidado, (una planta de fuerza, un vehículo, una computadora, una escoba, una cortadora de césped etcétera). La falta de conocimiento y cuidado a los Activos de Capital produce grandes pérdidas. Esto obliga a racionalizar y documentar el trabajo, implementando los instructivos necesarios y haciendo cursos para preparar a los usuarios en el manejo y pulcritud de sus herramientas personales.
9º Paso: Implementar el plan de preservación y mantenimiento para el personal de mantenimiento
La implementación de este plan debe empezar antes de que termine el octavo paso. Por lo hasta aquí visto, debemos considerar que nuestro Departamento de Preservación y Mantenimiento tendrá las siguientes características generales:
- Una estructura racional que facilite la aplicación de labores estratégicas y tácticas (Planeación y Planificación).
- Un inventario de activos físicos jerarquizado en tres categorías (Vital, Importante y Trivial).
- Planes estratégicos de Preservación y Mantenimiento efectuados por la Dirección general.
- Planes tácticos de Planificación de órdenes de trabajo efectuado por el Departamento de Preservación y Mantenimiento.
- Un sistema computarizado integrando la información de toda la empresa.
10º Paso: Implementar el plan de capacitación y desarrollo para todo el personal de la empresa y también para los proveedores
Con los planes generados por el Comité General Promotor y Coordinador del TPM, deben programarse y realizarse cursos para todo el personal de la empresa y proveedores de acuerdo con las categorías que tengan, utilizando las técnicas más modernas de enseñanza y siguiendo estas dos políticas:
- Todo personal debe ser capacitado, según las técnicas de conservación y operación.
- Todo entrenamiento debe adecuarse a las necesidades específicas de cada área de trabajo.
11º Paso: Implementar el plan de conservación para los nuevos activos de capital
El personal de Producción y el de Conservación (Preservación y Mantenimiento), debe corroborar, que todo equipo recién instalado, se analice desde el punto de vista de la filosofía actual de la conservación industrial, utilizando criterios científicos, ecológicos y sistémicos y además, con base en Costo del Ciclo de Vida (LCC). A esta etapa se le denomina Commissioning (poniendo en uso), y se lleva a cabo durante la vida temprana de la máquina, bajo la responsabilidad del proveedor para que éste nos asegure su garantía. Las actividades de Commissioning estarán enfocadas a:
- Evaluar el costo económico de ciclo de vida del equipo.
- Comprobar que el equipo está en los niveles más altos de confiabilidad, mantenibilidad y operatividad desde el punto de vista de seguridad y economía.
- Lograr el mejor nivel en la planeación de la inversión.
- Reducir el tiempo de vida temprana (de diseño a operación estable).
- Conseguir que las actividades de Commissioning se lleven a cabo con eficacia.
12º Paso: Estabilización
Este es el paso final del programa de implementación y desarrollo del TPM y consiste en una constante medición de resultados para la búsqueda de mejores objetivos. Todo el personal de producción y conservación auxiliado por el Comité General, Promotor y Coordinador del TPM, trabajará para mejorar los resultados y así poder permitir la fijación de metas cada vez más elevadas. Conforme se va logrando una adecuada implementación del TPM, es necesario ser más exigente con los resultados y hay que fijar objetivos de mayor nivel. Lo anterior hace indispensable que todo el personal trabaje en forma coordinada, continua y de manera proactiva.
Conclusión
En síntesis, el TPM es un proceso diseñado para administrar la preservación y mantenimiento de los activos de una gran empresa, esta es una filosofía que ha demostrado su alta calidad de resultados a pesar de las variantes que han sufrido los productos y procedimientos a través de más de 40 años. La implementación del TPM está perfectamente definida y establecida en el seguimiento cuidadosamente programado de cuatro fases que contienen los doce pasos arriba mencionados, que requiere de una gran inversión tanto de recursos económicos como humanos, por lo que solo es posible implementarlo en las grandes empresas y con ayuda de una compañía consultora que ya tenga una gran experiencia y al personal capacitado. Con esto nuestra primera pregunta se resuelve.
Para el caso de nuestro segundo cuestionamiento, ¿cómo pueden ser aprovechados estos conocimientos por las micros, pequeñas y medianas empresas? La respuesta no es tan compleja como parece: Para que éstas obtengan grandes beneficios, el primer paso es capacitar al personal de preservación, mantenimiento y operación en los conocimientos del TPM. Hoy día existen en el mercado empresas certificadas que ofertan diplomados en esta metodología. Con estos conocimientos adquiridos, este personal aplicará las técnicas del TPM que puedan ser utilizadas en su empresa, poniendo especial énfasis en la recolección de datos relevantes ya que se convertirá en información de análisis para encontrar áreas de oportunidad dentro de sus procesos. Finalmente, las mismas técnicas de este modelo los llevarán a aplicar inteligentemente lo que el TPM recomienda para las grandes empresas.
Al final, el resultado no es que las pequeñas y medianas empresas implementen el TPM, sino más bien elegir y aplicar las técnicas de TPM que sirvan mejor para la resolución de sus problemas.
Autor: Ing. Enrique Dounce Villanueva
Dinos qué te ha parecido el artículo
Artículos recomendados
Educación en Mantenimiento

Gerencia de Proyectos e Ingeniería: Salarios y Libertad

17.- Instrumentación y Control

8.7 El Plan de Limpieza

Publica tu artículo en la revista #1 de Mantenimiento Industrial
Publicar un artículo en la revista es gratis, no tiene costo.
Solo debes asegurarte que no sea un artículo comercial.
¿Qué esperas?
O envía tu artículo directo: articulos@predictiva21.com
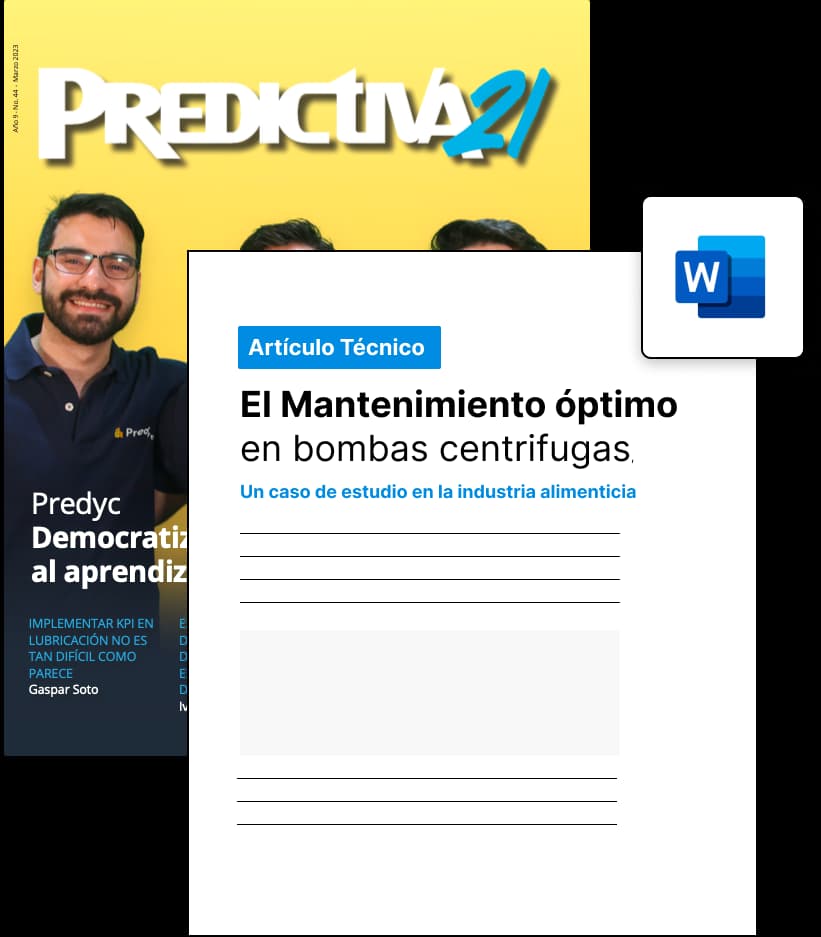
Hablemos de Mantenimiento Productivo Total
Articulo 6 de enero de 2020Introducción
Nace en mí la idea de escribir este artículo porque, en mi opinión, la mayor parte de los especialistas en este concepto, incluyendo a consultores, tienen una idea equivocada de lo que es el Mantenimiento Productivo Total (TPM por sus siglas en inglés) y creen que éste puede ser implementado en cualquier tamaño de empresa (MIPYME). Lo anterior basado en mi experiencia como consultor de mantenimiento industrial, así como en base en los estudios a fondo que, a lo largo de estos años, mis colegas y un servidor, hemos realizado.
Surgen entonces dos preguntas; ¿qué es el Mantenimiento Productivo Total? y ¿cómo pueden ser aprovechados estos conocimientos por las micros, pequeñas y medianas empresas? Pongámonos en contexto y situémonos en la industria norteamericana durante los años de 1919 a 1939. En esa época ya existia la práctica de las ideas de Adam Smith (División del trabajo), empezaba a cobrar importancia la máquina pues se iniciaba la aplicación de trabajos de Mantenimiento correctivo, y se fueron sumando los trabajos de Taylor Administración científica del trabajo y los de Walter A. Shewhart, W. Edwards Deming y Joseph Juran con sus desarrollos sobre Estadística aplicada a la industria, Control estadístico de calidad y Ciclo Shewhart.
Esta situación originó la existencia de un número considerable de consultores y maestros, que impartieron estos conocimientos a todos los niveles de la industria norteamericana durante veinte años. Podemos pensar con certeza que éstos fueron los ingredientes principales que se “fundieron en un crisol” para dar vida al llamado Mantenimiento Productivo (PM, siglas en inglés) Ver Figura 1…

Al inicio de la Segunda Guerra Mundial en septiembre de 1939, Norteamérica se vio envuelta en el compromiso de ser la industria de guerra (proveedor) de Inglaterra y Francia, obligando a sus fábricas a trabajar las 24 horas del día. El interés de las industrias se enfocó solo para atender los problemas de productividad ahora aumentados por la guerra, por lo que se suspendieron las acciones de desarrollo industrial que se habían tenido antes de ésta. Las industrias dedicadas a pertrechar a los ejércitos aliados, comenzaron a perder su eficacia pues eran necesarias nuevas inversiones para obtener activos físicos y humanos adecuados, lo que hizo aparecer de forma palpable, la división de intereses. Por un lado, como sus propietarios burgueses industriales, no tenían estudios científicos sobre lo que debía ser una empresa, solo les interesaban las ganancias y no el cumplimiento con el usuario del producto. Por otro lado, el personal de la industria, aunque simpatizaba con las exigencias de sus clientes, estaba expuesto a presiones que exigían cada vez una mejor calidad y oportunidad. Por tal motivo, el mismo personal tuvo que dar solución a los problemas que surgían, adaptando y arreglando los activos físicos, mejorando e implementando durante casi tres años nuevos procesos de trabajo, etcétera; todo ello bajo su propia responsabilidad.
El 7 de diciembre de 1941 el ataque a Pearl Harbor ejecutado por la Armada Imperial Japonesa unió a la opinión pública estadounidense y al día siguiente el 8 de diciembre, los Estados Unidos declararon la guerra a Japón. A partir de entonces, Norteamérica continuó administrando su industria con su naciente Proceso Administrativo qué tomó el nombre de “Mantenimiento Productivo (PM, siglas en inglés)”, en el cual continuaron poniéndose en práctica nuevas ideas originadas por el personal que componía cada industria. El patriotismo del personal, incrementado por el ambiente y las grandes presiones a que estaban sujetos, aunado a la falta de apoyo de los propietarios, dieron como consecuencia que todo el personal de cada industria resolviera sus propios problemas. Se empezaron a hacer grupos entre todos los trabajadores de cualquier nivel, para dar sus opiniones a fin de resolver cada problema que se les presentaba y éste fue el nacimiento de los “grupos de trabajo”. En el mismo contexto y con el objeto de que el usuario se sintiera atendido en oportunidad y seguridad en cualquier lugar en donde él lo necesitara, las industrias adoptaron e implementaron las ideas castrenses de los ejércitos aliados (logística), las cuales se sumaron a las existentes y quedaron como parte integral del PM, ver Figura 2.

Inicio y consolidación del TPM (1948 - 1971)
Recordemos que Japón quedó destrozado como resultado de la guerra y fue ocupado por las fuerzas norteamericanas en septiembre de 1946, por el Comando Supremo de las Fuerzas Aliadas (SCAP, siglas en inglés). El General estadounidense Douglas MacArthur fue nombrado como responsable de establecer un programa de desarrollo con especialistas norteamericanos, para la reconstrucción de esta nación. Dentro de éstos, los más relevantes a nuestro juicio, fueron: W. Edwards Deming, Walter Andrew Shewhart y Joseph Moses Juran.
Desde los primeros años de su estancia en Japón, estos científicos se dieron a conocer con los máximos niveles industriales de ese país, compartiendo sus conocimientos en estadística, en calidad, en grupos PM, en logística, en síntesis en el PM, cuyos buenos resultados ya estaban a la vista del mundo industrial. Los especialistas mencionados empezaron su asesoría en ese nivel debido a que su objetivo, era la rehabilitación industrial del Japón para que éste pudiera pagar sus deudas de guerra. La experiencia que ellos habían tenido durante el lapso de 1939 a 1945 les había mostrado la incongruencia de no preparar en el PM a los propietarios y altos niveles industriales con poder de decisión. En Japón pudieron hacerlo, porque para la Unión de Científicos e Ingenieros Japoneses (UCIJ) y los altos niveles de la industria Japonesa, esta preparación realmente despertó un interés vital, además de que llenó sus expectativas de un promisorio futuro y estaba plenamente vinculado con la idiosincrasia de su pueblo.
El Dr. Deming durante su larga estancia por el Japón (1950 – 1980) llegó a adquirir un gran reconocimiento y una alta estima. Los japoneses le mostraron su aprecio instituyendo en 1951 el “Premio Deming” (una medalla de plata con su efigie).
Desarrollo del TPM
Para 1939 las empresas tenían una organización simple, desarrollada en base al “Proceso Administrativo” salido de los pensamientos y trabajos de Frederick W. Taylor y Henry Fayol y aún no se tenía un pensamiento sistémico. Cada entidad se consideraba desligada del resto del grupo. No existía una conciencia holística, por lo que las organizaciones eran mostradas cómo lo explica la Figura 3, una dirección general con tres o cuatro subdirecciones o gerencias para encargarse de las funciones primarias; producir, vender, administrar y desarrollar las finanzas.
El Mantenimiento Productivo (PM) se originó en el área de Producción, debido a que se consideró que esta atendía la elaboración del producto y además ahí funcionaban las máquinas, y a estas era necesario hacerles labores de mantenimiento. La tarea se facilitó por que ya existían en ella fundamentos sólidos sobre la división del trabajo, la ciencia y la administración aplicadas a la industria, el uso de la estadística, la búsqueda de la calidad del producto, etcétera.
Estos conocimientos, por razón natural, no existían en las áreas de ventas, administración o finanzas ya que se consideraba que ellas no tenían activos que mantener por que no elaboraban ningún producto. La figura 3 nos muestra un organigrama hipotético de una empresa norteamericana en 1950.


Seiichi Nakajima en 1950 era un alto funcionario del Instituto Japonés de Mantenimiento de la Planta (JIMP) y fue uno de los muchos industriales de alto nivel que recibieron las enseñanzas de Deming sobre el Mantenimiento Productivo Norteamericano PM. Nakajima en esa fecha inició sus estudios de PM sin salir del Japón, encontrando que la industria americana estaba organizada de manera similar a la mostrada en la Figura 3, es decir, ya trabajaban los gerentes, supervisores y obreros, de la Dirección de Producción, formando Grupos de Trabajo PM (GTPM) y ya se empleaba normalmente la Logística. Para facilitar nuestra percepción analicemos solamente la Gerencia de Producción de la mencionada figura y desarrollemos su organigrama (Ver Figura 4); esto fue lo que encontró Seiichi Nakajima cuando empezó a desarrollar sus estudios del Mantenimiento Productivo (PM).

Concepto del Mantenimiento Productivo Total (TPM)
La labor de cualquier industria es la de producir en forma conjunta como un solo equipo, como una orquesta, en donde cada dirección, gerencia, departamento, proveedor o persona, debe esforzarse en forma coordinada para obtener beneficios, para lo cual debe emplear con eficacia el capital de trabajo que integra a la empresa. Es evidente que hasta el departamento más insignificante tiene que conservar sus propios activos físicos, su propio capital de trabajo, así sean escritorios, equipos de cómputo, escobas, cortadoras de césped, etcétera; pues todos ellos colaboran en la obtención del producto y en última instancia en la satisfacción del usuario, que es lo que proporciona la permanencia de la empresa. Por esto, la administración PM debería existir para toda la organización ya que en toda ella existen activos que mantener. Esto fue lo que nos mostró con sus trabajos de más de 20 años el industrial Seiichi Nakajima.
La figura 5 nos proporciona la razón del por qué se le llama “Mantenimiento Productivo Total”.

Estructurando el TPM
En 1971, después de 20 años de esfuerzo, Nakajima puso en marcha en Japón lo que él llamó Mantenimiento Productivo Total (TPM). En este esquema, todo el personal de una empresa está obligado a realizar labores de PM. Lo anterior hace necesario construir sobre el organigrama existente de la empresa y con autoridad Staff , una estructura para administrar el TPM. En la Figura 6 estamos considerando como ejemplo a la Dirección de Producción, en el entendido de que esto se repite en forma similar en las Direcciones restantes. La función Staff está mostrada en color verde. Es necesario aclarar que más del 90% del personal que ejecuta estas funciones es el mismo que ya pertenece a la empresa y el restante porcentaje lo ocupará nuevo personal generalmente especializado en el funcionamiento del TPM.

Aquí podemos observar que el gran avance que proporcionó Nakajima a la industria mundial, fue hacer un nuevo proceso administrativo apoyándose en las ideas existentes de Fayol y Taylor, usando los dos tipos de autoridad conocidos, (de línea y de apoyo o staff ) y considerar al todo como un sistema. Es decir, su actividad es holística por lo que sus propiedades y funcionamiento deben ser analizadas en conjunto.
Implementación y desarrollo del TPM en una empresa
Esta tarea no es sencilla de hacer, pues requiere del absoluto interés del consejo de administración y dirección general y la ayuda de una empresa consultora de alta calidad y experiencia, la cual debe conocer a fondo como implementar los siguientes doce pasos:
Cursos recomendados
%2520para%2520evaluar%2520la%2520gesti%25C3%25B3n%2520del%2520mantenimiento%252FImagen%252Fss-1733758540053.png%3Falt%3Dmedia%26token%3D47b767f7-ea54-48eb-b001-3ada0bb6cbdc&w=3840&q=75)



%252FImagen%252FRAMPREDYC-1730060420837.webp%3Falt%3Dmedia%26token%3D2634a7f0-988e-4022-b91f-382503e6e9db&w=3840&q=75)



1º Paso: Crear el entorno apropiado
El consejo de administración, debe informar oficialmente a todo el personal de la empresa y proveedores, a través de un evento formal; de la decisión de establecer el TPM. Con este evento se busca la participación y compromiso de todos los integrantes, así como la comprensión del tema.
2º Paso: Crear programas de adiestramiento y desarrollo
En este punto se inicia la creación de programas de adiestramiento y desarrollo para todo el personal de la empresa.
3º Paso: Crear la organización para el TPM
Este es el momento de establecer el “Comité Promotor y Coordinador de Desarrollo del TPM” como Staff o apoyo de la alta dirección (Ver Figura 6).
4º Paso: Crear los objetivos y políticas para el TPM
El Comité Promotor y Coordinador definirá los objetivos generales a alcanzar a mediano y largo plazo (uno a tres años) recomendando las políticas necesarias que de éstos se deriven.
5º Paso: Crear el plan maestro para la desarrollo del TPM
El Comité Promotor y Coordinador elabora y establece un plan maestro para el desarrollo e implementación del TPM, este comité debe estar compuesto por verdaderos especialistas en la preservación y mantenimiento de los activos de capital existentes en la empresa, sus conocimientos deberán tener cimientos en la tecnología más avanzada incluyendo temas como la jerarquización de activos, el RCM, etcétera; con lo que se implementarán cursos y programas para preparar y adiestrar a todo el personal en las siguientes cinco tareas:
- Efectividad global del equipo.
- Preservación y Mantenimiento autónomo para todo el personal de Producción, Ventas, Finanzas etc.
- Preservación y Mantenimiento para el personal de mantenimiento.
- Capacitación y Desarrollo para todo el personal de la empresa.
- Preservación y Mantenimiento para los nuevos Activos de Capital.
6º Paso: Acto de iniciación TPM
Se organizará una reunión de todo el personal de la empresa, así como de personas importantes ligadas a ésta ya sean proveedores, empresarios, personas renombradas etcétera, con el objeto de aumentar el interés de los presentes por el evento. Esta junta debe ayudar a crear y desarrollar un clima proactivo y de deseos de superación en todo el personal de la empresa y proveedores. Cada responsable de comité (general, departamental, de sección y de grupo) informará sobre el trabajo planeado y desarrollado en cada uno de los cinco pasos antes mencionados, así como de sus resultados. Finalmente, se anunciará que a partir de ese momento cada persona empezará a trabajar de acuerdo a las enseñanzas recibidas usando las nuevas “herramientas” y conforme vayan progresando abandonen las que deben quedar en desuso.
Con la terminación de los pasos anteriores hemos obtenido el adiestramiento y desarrollo de todos los recursos humanos de la empresa, permitiendo que el Comité General del TPM jerarquice el inventario de recursos a Preservar y Mantener en tres categorías de acuerdo a su criticidad (Vital, Importante y trivial). Así mismo, les asigne prioridad de atención y auxilie en la formación de “equipos de proyecto”, integrados por personal de ingeniería, conservación, producción y círculos de calidad. Todo lo anterior se debe llevar a cabo siguiendo los pasos del 7 al 11.
7º Paso: Mejora de la efectividad global del equipo instalado
Para obtener ésta mejora es preciso hacer dos labores generales:
- 1a. Estudiar a fondo las características y rendimientos de los activos vitales e importantes, con el objeto de obtener el mayor provecho al utilizarlos en la debida forma.
- 2a. Eliminar los obstáculos que se oponen a la eficacia de los activos antes mencionados.
8º Paso: Implementar el plan de preservación y mantenimiento autónomo
Uno de los problemas más graves que existen en nuestra industria es que al personal de producción, ventas, finanzas y cualquier otra especialidad, no se le prepara en labores de Preservación y Mantenimiento de sus herramientas de trabajo. Este es un gran error porque debemos tener como principio que todo el personal que tenga que ver con el uso de una herramienta de trabajo, tiene la obligación de conocer su operación y cuidado, (una planta de fuerza, un vehículo, una computadora, una escoba, una cortadora de césped etcétera). La falta de conocimiento y cuidado a los Activos de Capital produce grandes pérdidas. Esto obliga a racionalizar y documentar el trabajo, implementando los instructivos necesarios y haciendo cursos para preparar a los usuarios en el manejo y pulcritud de sus herramientas personales.
9º Paso: Implementar el plan de preservación y mantenimiento para el personal de mantenimiento
La implementación de este plan debe empezar antes de que termine el octavo paso. Por lo hasta aquí visto, debemos considerar que nuestro Departamento de Preservación y Mantenimiento tendrá las siguientes características generales:
- Una estructura racional que facilite la aplicación de labores estratégicas y tácticas (Planeación y Planificación).
- Un inventario de activos físicos jerarquizado en tres categorías (Vital, Importante y Trivial).
- Planes estratégicos de Preservación y Mantenimiento efectuados por la Dirección general.
- Planes tácticos de Planificación de órdenes de trabajo efectuado por el Departamento de Preservación y Mantenimiento.
- Un sistema computarizado integrando la información de toda la empresa.
10º Paso: Implementar el plan de capacitación y desarrollo para todo el personal de la empresa y también para los proveedores
Con los planes generados por el Comité General Promotor y Coordinador del TPM, deben programarse y realizarse cursos para todo el personal de la empresa y proveedores de acuerdo con las categorías que tengan, utilizando las técnicas más modernas de enseñanza y siguiendo estas dos políticas:
- Todo personal debe ser capacitado, según las técnicas de conservación y operación.
- Todo entrenamiento debe adecuarse a las necesidades específicas de cada área de trabajo.
11º Paso: Implementar el plan de conservación para los nuevos activos de capital
El personal de Producción y el de Conservación (Preservación y Mantenimiento), debe corroborar, que todo equipo recién instalado, se analice desde el punto de vista de la filosofía actual de la conservación industrial, utilizando criterios científicos, ecológicos y sistémicos y además, con base en Costo del Ciclo de Vida (LCC). A esta etapa se le denomina Commissioning (poniendo en uso), y se lleva a cabo durante la vida temprana de la máquina, bajo la responsabilidad del proveedor para que éste nos asegure su garantía. Las actividades de Commissioning estarán enfocadas a:
- Evaluar el costo económico de ciclo de vida del equipo.
- Comprobar que el equipo está en los niveles más altos de confiabilidad, mantenibilidad y operatividad desde el punto de vista de seguridad y economía.
- Lograr el mejor nivel en la planeación de la inversión.
- Reducir el tiempo de vida temprana (de diseño a operación estable).
- Conseguir que las actividades de Commissioning se lleven a cabo con eficacia.
12º Paso: Estabilización
Este es el paso final del programa de implementación y desarrollo del TPM y consiste en una constante medición de resultados para la búsqueda de mejores objetivos. Todo el personal de producción y conservación auxiliado por el Comité General, Promotor y Coordinador del TPM, trabajará para mejorar los resultados y así poder permitir la fijación de metas cada vez más elevadas. Conforme se va logrando una adecuada implementación del TPM, es necesario ser más exigente con los resultados y hay que fijar objetivos de mayor nivel. Lo anterior hace indispensable que todo el personal trabaje en forma coordinada, continua y de manera proactiva.
Conclusión
En síntesis, el TPM es un proceso diseñado para administrar la preservación y mantenimiento de los activos de una gran empresa, esta es una filosofía que ha demostrado su alta calidad de resultados a pesar de las variantes que han sufrido los productos y procedimientos a través de más de 40 años. La implementación del TPM está perfectamente definida y establecida en el seguimiento cuidadosamente programado de cuatro fases que contienen los doce pasos arriba mencionados, que requiere de una gran inversión tanto de recursos económicos como humanos, por lo que solo es posible implementarlo en las grandes empresas y con ayuda de una compañía consultora que ya tenga una gran experiencia y al personal capacitado. Con esto nuestra primera pregunta se resuelve.
Para el caso de nuestro segundo cuestionamiento, ¿cómo pueden ser aprovechados estos conocimientos por las micros, pequeñas y medianas empresas? La respuesta no es tan compleja como parece: Para que éstas obtengan grandes beneficios, el primer paso es capacitar al personal de preservación, mantenimiento y operación en los conocimientos del TPM. Hoy día existen en el mercado empresas certificadas que ofertan diplomados en esta metodología. Con estos conocimientos adquiridos, este personal aplicará las técnicas del TPM que puedan ser utilizadas en su empresa, poniendo especial énfasis en la recolección de datos relevantes ya que se convertirá en información de análisis para encontrar áreas de oportunidad dentro de sus procesos. Finalmente, las mismas técnicas de este modelo los llevarán a aplicar inteligentemente lo que el TPM recomienda para las grandes empresas.
Al final, el resultado no es que las pequeñas y medianas empresas implementen el TPM, sino más bien elegir y aplicar las técnicas de TPM que sirvan mejor para la resolución de sus problemas.
Autor: Ing. Enrique Dounce Villanueva
Dinos qué te ha parecido el artículo
Artículos recomendados
Aplicaciones mecánicas de la Termografía

Congreso de Mantenimiento y Confiabilidad Latinoamérica (Perú 2019)

Industria 4.0: elemento de nueva revolución industrial

The ABC’s of implementing Asset Management

Publica tu artículo en la revista #1 de Mantenimiento Industrial
Publicar un artículo en la revista es gratis, no tiene costo.
Solo debes asegurarte que no sea un artículo comercial.
¿Qué esperas?
O envía tu artículo directo: articulos@predictiva21.com
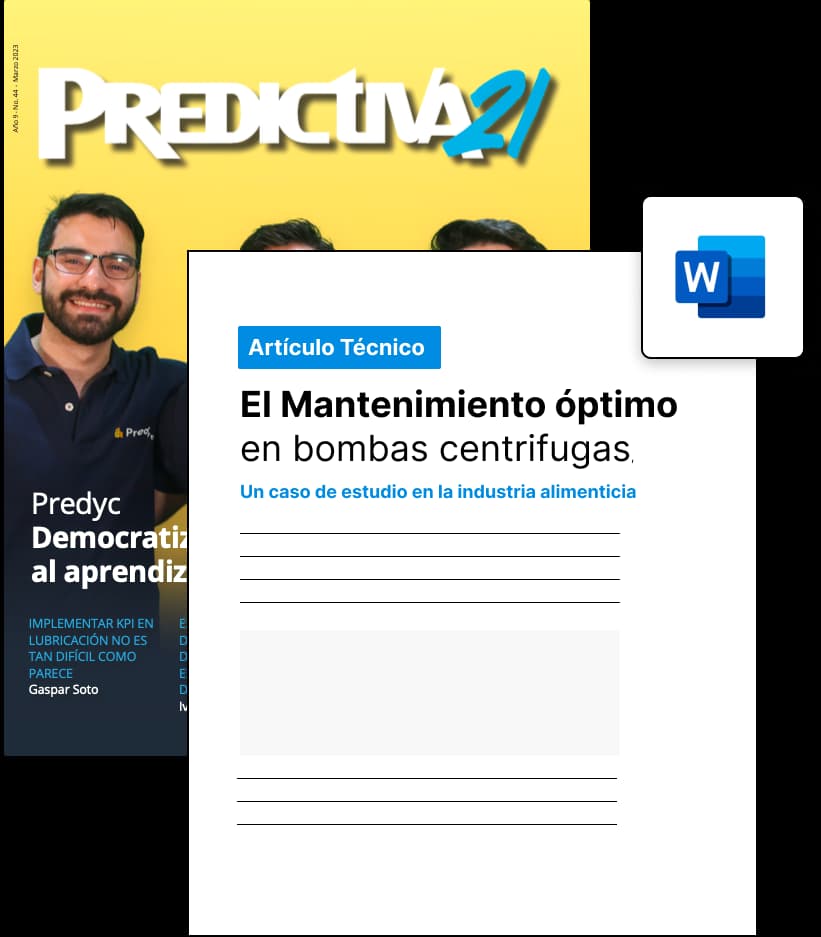