Ingeniería de Confiabilidad Práctica y Análisis para el diseño de sistemas y el mantenimiento del ciclo de vida
Libros26 de enero de 2021

Sobre el Libro
Ingeniería de Confiabilidad Práctica y Análisis para el diseño de sistemas y el mantenimiento del ciclo de vida (Practical Reliability Engineering and Analysis for System Design and Life-Cycle Sustainment) es un libro de 500 páginas escrito por William R. Wessels. Fue publicado por la editorial CRC Press en el año 2010 en su primera edición.
Descripción del Libro
En el mundo sofisticado de hoy, la confiabilidad se erige como el máximo árbitro de la calidad. La comprensión de la confiabilidad y el compromiso final de falla es esencial para determinar el valor de la mayoría de los productos modernos y absolutamente crítico para otros, grandes o pequeños. Ya sea que las vidas dependan del rendimiento de un escudo térmico o de un chip en un laboratorio, la falla aleatoria nunca es un resultado aceptable.
Escrito para ingenieros en ejercicio, Ingeniería de Confiabilidad Práctica y Análisis para el diseño de sistemas y el mantenimiento del ciclo de vida se apartan del enfoque convencional del tiempo para la ingeniería y el análisis de confiabilidad basados en fallas. El libro emplea un enfoque mucho más analítico que los libros de texto que se basan en la distribución de probabilidad exponencial para caracterizar el fracaso. En cambio, el autor, que ha sido un ingeniero de confiabilidad desde 1970, se enfoca en aquellas distribuciones de probabilidad que describen con mayor precisión el verdadero comportamiento de falla. Él enfatiza las fallas que resultan del desgaste, considerando los sistemas, los componentes individuales dentro de esos sistemas y las fuerzas ambientales que se ejercen sobre ellos.
Los productos confiables no son un accidente: un camino claro hacia la creación de productos consistentemente confiables.
Tomando un enfoque paso a paso que se complementa con tablas actuales para configurar el desgaste, la carga, la distribución y otros factores esenciales, este libro explora los elementos de diseño necesarios para la confiabilidad y la integración y el sostenimiento de sistemas confiables. Luego analiza los mecanismos, modos y efectos de fallas, así como la conciencia y participación del operador, y también profundiza en el modelado de fallas de confiabilidad basado en datos de tiempo hasta fallas considerando una variedad de enfoques.
A partir de ahí, el texto demuestra y luego considera las ventajas y desventajas del enfoque de análisis de tensión-resistencia, incluidas varias fases de simulación de prueba. Llevando el enfoque práctico aún más lejos, el autor cubre el análisis de fallas centrado en la confiabilidad, así como el mantenimiento basado en condiciones y dirigido en el tiempo.
Como ciencia, la confiabilidad se consideró una vez el juguete de los estadísticos que informan sobre las mediciones del tiempo de falla, pero en manos de un ingeniero en ejercicio, la confiabilidad es mucho más que la medida de un resultado; es algo que se debe lograr, algo que se debe construir deliberadamente en un sistema. El análisis de confiabilidad del diseño mecánico para estructuras y componentes dinámicos exige un enfoque minucioso y experimentado que primero busca comprender por qué falla una pieza, luego aprende cómo repararla y finalmente aprende cómo prevenir su falla. En última instancia, la confiabilidad del diseño mecánico se basa en la relación entre el estrés y la resistencia a lo largo del tiempo. Este libro combina el sentido común de las lecciones aprendidas con el diseño de ingeniería mecánica y la integración de sistemas, con miras al sostenimiento. Esto es lo que permite a las organizaciones lograr productos valorados por su confiabilidad de clase mundial.
Tabla de Contenido
- Requisitos para la ingeniería de confiabilidad: diseño de confiabilidad, integración de sistemas de confiabilidad y sostenimiento del sistema basado en confiabilidad.
- Modelado de confiabilidad de piezas / LRU para datos de tiempo de falla.
- Modelado de fallas de confiabilidad basado en datos de tiempo de falla.
- Disponibilidad y mantenimiento de piezas.
- Fiabilidad de la pieza basada en el análisis de resistencia a la tensión.
- Las funciones de ingeniería de confiabilidad forman la resistencia al estrés.
- Modelado de fallas basado en el mecanismo de fallas.
- Modelado de confiabilidad para niveles de diseño de ensamblajes.
- Análisis de confiabilidad del sistema de sistemas.
- Mantenimiento centrado en la confiabilidad.
- Análisis de fallas centrado en la confiabilidad.
- Mantenimiento basado en condiciones.
- Mantenimiento dirigido por tiempo.
Confiabilidad de la Pieza
La confiabilidad de la pieza se define como la probabilidad de que una pieza realice su función sin fallas durante la duración de la misión especificada en las condiciones de uso establecidas.
La confiabilidad se expresa como un porcentaje, cuando el período de tiempo es una misión, como el tiempo medio entre fallas (MTBF), cuando el período de tiempo es el ciclo de vida. Las condiciones de uso tienen dos fuentes:
- Entorno operativo: tensiones (cargas térmicas, vibratorias y mecánicas; reactividad química, corrosión o biológica) causadas por el funcionamiento de la pieza, su siguiente ensamblaje superior y piezas próximas que el ingeniero de diseño rara vez conoce.
- Medio ambiente: tensiones (cargas térmicas, vibratorias y mecánicas; reactividad química, corrosión o biológica) provocadas por el clima y los sistemas próximos.
Los libros de Kapur y Lamberson y O'Conner muestran que esta definición no ha cambiado mucho en las últimas décadas. La definición pasa la prueba del tiempo. De lo contrario, mucho de lo que sabemos, o creemos saber, sobre confiabilidad ha ido evolucionando durante el mismo período de tiempo. Este es un punto importante porque la disciplina de confiabilidad es relativamente joven (de hecho, yo soy mayor que la disciplina). La ingeniería civil puede rastrear su práctica durante varios miles de años. La ingeniería mecánica nació con la Revolución Industrial hace unos cientos de años, alcanzando el estatus de disciplina a fines del siglo XIX. La ingeniería eléctrica y química surgió a principios del siglo XX. La primera sociedad técnica de confiabilidad fue formada por el Instituto de Ingenieros Eléctricos y Electrónicos (IEEE) a principios de la década de 1950; el primer libro de texto sobre confiabilidad fue publicado en 1961 por Igor Bazowsky.
La inclusión de los programas espaciales y las guerras en la línea de tiempo muestra que la creación y evolución de la disciplina de ingeniería de confiabilidad en los Estados Unidos ha estado estrechamente relacionada con la Administración Nacional de Aeronáutica y del Espacio (NASA). y programas de desarrollo de sistemas militares. De hecho, incluso hoy en día, la mayoría de los ingenieros de confiabilidad están empleados por la NASA, el Departamento de Defensa (DoD) y sus contratistas. La aviación ha sido y sigue siendo el motivo principal de su enorme inversión en ingeniería de confiabilidad. Pero la NASA y el Departamento de Defensa han expandido su uso de la ingeniería de confiabilidad a sistemas de armas, sistemas de vehículos terrestres y sistemas de radar, por nombrar algunos. Se puede afirmar que la aviación comercial ha compartido los beneficios de las aplicaciones gubernamentales en ingeniería de confiabilidad porque las mismas empresas operan en ambos sectores.
La aplicación del sector privado de la ingeniería de confiabilidad ha sido menos extensa. La industria automotriz de EE. UU. Se vio obligada a aplicar la ingeniería de confiabilidad en la década de 1970 como resultado de los automóviles japoneses y alemanes que rápidamente se reconoció por ofrecer una mayor confiabilidad. La economía global exige ahora la confiabilidad de las piezas como factor competitivo.
Afortunadamente, la ingeniería de confiabilidad no es un análisis mutuamente excluyente del análisis de diseño; sólo la orientación difiere. El análisis del diseño de la pieza se orienta tradicionalmente a cumplir con la especificación funcional que fluye desde las especificaciones del sistema hasta la estructura de desglose del trabajo (WBS). Este enfoque da como resultado un diseño de pieza que se puede esperar que funcione sin fallas la primera vez que se usa el sistema. Cuántas veces funcionará sin fallas después de esa primera vez es una incógnita. El análisis de diseño de confiabilidad de la pieza aplica la misma especificación funcional derivada de las especificaciones del sistema a través de la WBS para determinar los mecanismos de falla que harán que la pieza falle.
Cursos recomendados




%252FImagen%252FRAMPREDYC-1730060420837.webp%3Falt%3Dmedia%26token%3D2634a7f0-988e-4022-b91f-382503e6e9db&w=3840&q=75)



Mecanismos de Falla
Las teorías de falla de material afirman que la falla de una pieza ocurre cuando un esfuerzo excede una de las propiedades de resistencia del material uniaxial en tensión o en compresión (teoría de falla de Rankine) o cuando la tensión excede las propiedades de resistencia del material al cortante (teoría de falla de Tresca-Guest). Un mecanismo de falla es un factor de estrés que debilita una pieza. Los efectos de un mecanismo de falla son los cambios en la geometría y las propiedades del material de un material.
La fuente de un mecanismo de falla puede ser funcional, ambiental o la interacción de los dos. Un mecanismo de falla funcional es una tensión que se produce por el uso de la pieza. Por ejemplo, un eje giratorio que entrega torque a una transmisión de polea experimenta un esfuerzo de torsión que causa un esfuerzo de torsión, un perno que sujeta una tapa de presión a un recipiente a presión experimenta un esfuerzo de tracción que causa un esfuerzo de tracción y una placa de circuito electrónico experimenta un esfuerzo térmico en las conexiones de soldadura. que puede causar tensión térmica.
Un mecanismo de falla ambiental es un estrés que se produce por condiciones externas de uso: por ejemplo, la temperatura del aire que rodea la pieza en función de las condiciones climáticas estacionales y la altitud, la vibración del sistema que actúa sobre la pieza y la exposición a materiales corrosivos.
Las fuentes funcionales y ambientales de tensiones a menudo son bien conocidas durante el análisis del diseño de la pieza, pero menos entendida es la interacción de las dos. A menudo, las tensiones que actúan sobre una pieza no se mitigan cuando las fuentes se evalúan como un mecanismo de falla insignificante. La falla de una pieza puede ocurrir cuando dos de tales tensiones crean un mecanismo de falla combinado. Por ejemplo, la falla de la junta tórica en el transbordador espacial Challenger se debió a la falta de comprensión de las tensiones combinadas de baja temperatura (ambiental) y cargas de presión interna (funcional) en el sello. Otro ejemplo es el mecanismo de falla de la combinación de humedad (ambiental) y estrés térmico (funcional) que produce corrosión.
Los mecanismos de falla mecánica están representados por las principales categorías de esfuerzos: fuerza, temperatura y reactividad. Las fuerzas actúan como cargas sobre la geometría del material y se describen gráficamente en seis grados de libertad. Las fuerzas uniaxiales más básicas cargan un material en tensión (orientación del eje “+”), compresión (orientación del eje “-”) o en torsión (+ "o“ - ”) alrededor de cada eje. Un vector de fuerza que no se alinea a lo largo uno de los tres ejes se puede reducir a sus resultantes de los ejes x, y y z.
La fuerza se puede describir y medir como cargas estáticas y dinámicas. Las cargas estáticas son de magnitud constante y de ubicación fija. Las cargas estáticas pueden fijarse en un punto o distribuirse en un segmento de uno o más ejes.
Las cargas dinámicas son variables en magnitud, dirección y ubicación. La variación puede tener un patrón o ser aleatoria en cuanto a magnitud de fuerza y frecuencia de ocurrencia. Las fuerzas que actúan sobre la unión o interfaz entre dos partes provocan cargas de corte y flexión.
La tensión del material es la respuesta más básica a una fuerza; la magnitud y el efecto de la deformación son función de la propiedad elástica del material. La resistencia del material es la capacidad de sobrevivir a cada aplicación de estrés. La teoría de la falla por tensión asume que la falla ocurre cuando la tensión excede la resistencia. Esto puede suceder de dos maneras:
- Se aplica una única tensión que supera la resistencia del material.
- Se aplica repetidamente una única tensión que excede la resistencia y fatiga el material.
El primero es el método de análisis de diseño más sencillo para la especificación de materiales y se aplica con mayor frecuencia. Es más fácil de enseñar, más rápido y más económico de aplicar, y está respaldado por una amplia información publicada sobre las propiedades del material. Es el enfoque del "factor de seguridad" para el análisis de diseño.
Referencias
Dinos qué te ha parecido el artículo
Artículos recomendados
Análisis de costos de garantía

Confiabilidad y Riesgo: una perspectiva bayesiana

13.1.- Tipos de Lubricación

1.1.- ¿Qué es una bomba?

Publica tu artículo en la revista #1 de Mantenimiento Industrial
Publicar un artículo en la revista es gratis, no tiene costo.
Solo debes asegurarte que no sea un artículo comercial.
¿Qué esperas?
O envía tu artículo directo: articulos@predictiva21.com
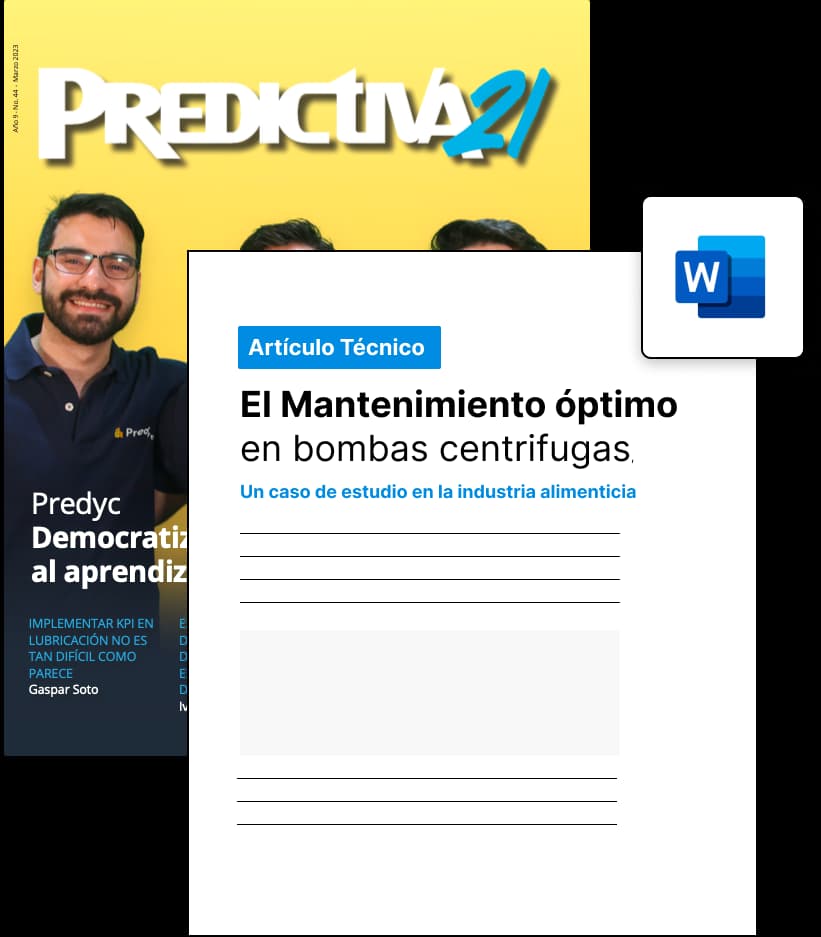
Ingeniería de Confiabilidad Práctica y Análisis para el diseño de sistemas y el mantenimiento del ciclo de vida
Libros 26 de enero de 2021
Sobre el Libro
Ingeniería de Confiabilidad Práctica y Análisis para el diseño de sistemas y el mantenimiento del ciclo de vida (Practical Reliability Engineering and Analysis for System Design and Life-Cycle Sustainment) es un libro de 500 páginas escrito por William R. Wessels. Fue publicado por la editorial CRC Press en el año 2010 en su primera edición.
Descripción del Libro
En el mundo sofisticado de hoy, la confiabilidad se erige como el máximo árbitro de la calidad. La comprensión de la confiabilidad y el compromiso final de falla es esencial para determinar el valor de la mayoría de los productos modernos y absolutamente crítico para otros, grandes o pequeños. Ya sea que las vidas dependan del rendimiento de un escudo térmico o de un chip en un laboratorio, la falla aleatoria nunca es un resultado aceptable.
Escrito para ingenieros en ejercicio, Ingeniería de Confiabilidad Práctica y Análisis para el diseño de sistemas y el mantenimiento del ciclo de vida se apartan del enfoque convencional del tiempo para la ingeniería y el análisis de confiabilidad basados en fallas. El libro emplea un enfoque mucho más analítico que los libros de texto que se basan en la distribución de probabilidad exponencial para caracterizar el fracaso. En cambio, el autor, que ha sido un ingeniero de confiabilidad desde 1970, se enfoca en aquellas distribuciones de probabilidad que describen con mayor precisión el verdadero comportamiento de falla. Él enfatiza las fallas que resultan del desgaste, considerando los sistemas, los componentes individuales dentro de esos sistemas y las fuerzas ambientales que se ejercen sobre ellos.
Los productos confiables no son un accidente: un camino claro hacia la creación de productos consistentemente confiables.
Tomando un enfoque paso a paso que se complementa con tablas actuales para configurar el desgaste, la carga, la distribución y otros factores esenciales, este libro explora los elementos de diseño necesarios para la confiabilidad y la integración y el sostenimiento de sistemas confiables. Luego analiza los mecanismos, modos y efectos de fallas, así como la conciencia y participación del operador, y también profundiza en el modelado de fallas de confiabilidad basado en datos de tiempo hasta fallas considerando una variedad de enfoques.
A partir de ahí, el texto demuestra y luego considera las ventajas y desventajas del enfoque de análisis de tensión-resistencia, incluidas varias fases de simulación de prueba. Llevando el enfoque práctico aún más lejos, el autor cubre el análisis de fallas centrado en la confiabilidad, así como el mantenimiento basado en condiciones y dirigido en el tiempo.
Como ciencia, la confiabilidad se consideró una vez el juguete de los estadísticos que informan sobre las mediciones del tiempo de falla, pero en manos de un ingeniero en ejercicio, la confiabilidad es mucho más que la medida de un resultado; es algo que se debe lograr, algo que se debe construir deliberadamente en un sistema. El análisis de confiabilidad del diseño mecánico para estructuras y componentes dinámicos exige un enfoque minucioso y experimentado que primero busca comprender por qué falla una pieza, luego aprende cómo repararla y finalmente aprende cómo prevenir su falla. En última instancia, la confiabilidad del diseño mecánico se basa en la relación entre el estrés y la resistencia a lo largo del tiempo. Este libro combina el sentido común de las lecciones aprendidas con el diseño de ingeniería mecánica y la integración de sistemas, con miras al sostenimiento. Esto es lo que permite a las organizaciones lograr productos valorados por su confiabilidad de clase mundial.
Tabla de Contenido
- Requisitos para la ingeniería de confiabilidad: diseño de confiabilidad, integración de sistemas de confiabilidad y sostenimiento del sistema basado en confiabilidad.
- Modelado de confiabilidad de piezas / LRU para datos de tiempo de falla.
- Modelado de fallas de confiabilidad basado en datos de tiempo de falla.
- Disponibilidad y mantenimiento de piezas.
- Fiabilidad de la pieza basada en el análisis de resistencia a la tensión.
- Las funciones de ingeniería de confiabilidad forman la resistencia al estrés.
- Modelado de fallas basado en el mecanismo de fallas.
- Modelado de confiabilidad para niveles de diseño de ensamblajes.
- Análisis de confiabilidad del sistema de sistemas.
- Mantenimiento centrado en la confiabilidad.
- Análisis de fallas centrado en la confiabilidad.
- Mantenimiento basado en condiciones.
- Mantenimiento dirigido por tiempo.
Confiabilidad de la Pieza
La confiabilidad de la pieza se define como la probabilidad de que una pieza realice su función sin fallas durante la duración de la misión especificada en las condiciones de uso establecidas.
La confiabilidad se expresa como un porcentaje, cuando el período de tiempo es una misión, como el tiempo medio entre fallas (MTBF), cuando el período de tiempo es el ciclo de vida. Las condiciones de uso tienen dos fuentes:
- Entorno operativo: tensiones (cargas térmicas, vibratorias y mecánicas; reactividad química, corrosión o biológica) causadas por el funcionamiento de la pieza, su siguiente ensamblaje superior y piezas próximas que el ingeniero de diseño rara vez conoce.
- Medio ambiente: tensiones (cargas térmicas, vibratorias y mecánicas; reactividad química, corrosión o biológica) provocadas por el clima y los sistemas próximos.
Los libros de Kapur y Lamberson y O'Conner muestran que esta definición no ha cambiado mucho en las últimas décadas. La definición pasa la prueba del tiempo. De lo contrario, mucho de lo que sabemos, o creemos saber, sobre confiabilidad ha ido evolucionando durante el mismo período de tiempo. Este es un punto importante porque la disciplina de confiabilidad es relativamente joven (de hecho, yo soy mayor que la disciplina). La ingeniería civil puede rastrear su práctica durante varios miles de años. La ingeniería mecánica nació con la Revolución Industrial hace unos cientos de años, alcanzando el estatus de disciplina a fines del siglo XIX. La ingeniería eléctrica y química surgió a principios del siglo XX. La primera sociedad técnica de confiabilidad fue formada por el Instituto de Ingenieros Eléctricos y Electrónicos (IEEE) a principios de la década de 1950; el primer libro de texto sobre confiabilidad fue publicado en 1961 por Igor Bazowsky.
La inclusión de los programas espaciales y las guerras en la línea de tiempo muestra que la creación y evolución de la disciplina de ingeniería de confiabilidad en los Estados Unidos ha estado estrechamente relacionada con la Administración Nacional de Aeronáutica y del Espacio (NASA). y programas de desarrollo de sistemas militares. De hecho, incluso hoy en día, la mayoría de los ingenieros de confiabilidad están empleados por la NASA, el Departamento de Defensa (DoD) y sus contratistas. La aviación ha sido y sigue siendo el motivo principal de su enorme inversión en ingeniería de confiabilidad. Pero la NASA y el Departamento de Defensa han expandido su uso de la ingeniería de confiabilidad a sistemas de armas, sistemas de vehículos terrestres y sistemas de radar, por nombrar algunos. Se puede afirmar que la aviación comercial ha compartido los beneficios de las aplicaciones gubernamentales en ingeniería de confiabilidad porque las mismas empresas operan en ambos sectores.
La aplicación del sector privado de la ingeniería de confiabilidad ha sido menos extensa. La industria automotriz de EE. UU. Se vio obligada a aplicar la ingeniería de confiabilidad en la década de 1970 como resultado de los automóviles japoneses y alemanes que rápidamente se reconoció por ofrecer una mayor confiabilidad. La economía global exige ahora la confiabilidad de las piezas como factor competitivo.
Afortunadamente, la ingeniería de confiabilidad no es un análisis mutuamente excluyente del análisis de diseño; sólo la orientación difiere. El análisis del diseño de la pieza se orienta tradicionalmente a cumplir con la especificación funcional que fluye desde las especificaciones del sistema hasta la estructura de desglose del trabajo (WBS). Este enfoque da como resultado un diseño de pieza que se puede esperar que funcione sin fallas la primera vez que se usa el sistema. Cuántas veces funcionará sin fallas después de esa primera vez es una incógnita. El análisis de diseño de confiabilidad de la pieza aplica la misma especificación funcional derivada de las especificaciones del sistema a través de la WBS para determinar los mecanismos de falla que harán que la pieza falle.
Cursos recomendados




%252FImagen%252FRAMPREDYC-1730060420837.webp%3Falt%3Dmedia%26token%3D2634a7f0-988e-4022-b91f-382503e6e9db&w=3840&q=75)



Mecanismos de Falla
Las teorías de falla de material afirman que la falla de una pieza ocurre cuando un esfuerzo excede una de las propiedades de resistencia del material uniaxial en tensión o en compresión (teoría de falla de Rankine) o cuando la tensión excede las propiedades de resistencia del material al cortante (teoría de falla de Tresca-Guest). Un mecanismo de falla es un factor de estrés que debilita una pieza. Los efectos de un mecanismo de falla son los cambios en la geometría y las propiedades del material de un material.
La fuente de un mecanismo de falla puede ser funcional, ambiental o la interacción de los dos. Un mecanismo de falla funcional es una tensión que se produce por el uso de la pieza. Por ejemplo, un eje giratorio que entrega torque a una transmisión de polea experimenta un esfuerzo de torsión que causa un esfuerzo de torsión, un perno que sujeta una tapa de presión a un recipiente a presión experimenta un esfuerzo de tracción que causa un esfuerzo de tracción y una placa de circuito electrónico experimenta un esfuerzo térmico en las conexiones de soldadura. que puede causar tensión térmica.
Un mecanismo de falla ambiental es un estrés que se produce por condiciones externas de uso: por ejemplo, la temperatura del aire que rodea la pieza en función de las condiciones climáticas estacionales y la altitud, la vibración del sistema que actúa sobre la pieza y la exposición a materiales corrosivos.
Las fuentes funcionales y ambientales de tensiones a menudo son bien conocidas durante el análisis del diseño de la pieza, pero menos entendida es la interacción de las dos. A menudo, las tensiones que actúan sobre una pieza no se mitigan cuando las fuentes se evalúan como un mecanismo de falla insignificante. La falla de una pieza puede ocurrir cuando dos de tales tensiones crean un mecanismo de falla combinado. Por ejemplo, la falla de la junta tórica en el transbordador espacial Challenger se debió a la falta de comprensión de las tensiones combinadas de baja temperatura (ambiental) y cargas de presión interna (funcional) en el sello. Otro ejemplo es el mecanismo de falla de la combinación de humedad (ambiental) y estrés térmico (funcional) que produce corrosión.
Los mecanismos de falla mecánica están representados por las principales categorías de esfuerzos: fuerza, temperatura y reactividad. Las fuerzas actúan como cargas sobre la geometría del material y se describen gráficamente en seis grados de libertad. Las fuerzas uniaxiales más básicas cargan un material en tensión (orientación del eje “+”), compresión (orientación del eje “-”) o en torsión (+ "o“ - ”) alrededor de cada eje. Un vector de fuerza que no se alinea a lo largo uno de los tres ejes se puede reducir a sus resultantes de los ejes x, y y z.
La fuerza se puede describir y medir como cargas estáticas y dinámicas. Las cargas estáticas son de magnitud constante y de ubicación fija. Las cargas estáticas pueden fijarse en un punto o distribuirse en un segmento de uno o más ejes.
Las cargas dinámicas son variables en magnitud, dirección y ubicación. La variación puede tener un patrón o ser aleatoria en cuanto a magnitud de fuerza y frecuencia de ocurrencia. Las fuerzas que actúan sobre la unión o interfaz entre dos partes provocan cargas de corte y flexión.
La tensión del material es la respuesta más básica a una fuerza; la magnitud y el efecto de la deformación son función de la propiedad elástica del material. La resistencia del material es la capacidad de sobrevivir a cada aplicación de estrés. La teoría de la falla por tensión asume que la falla ocurre cuando la tensión excede la resistencia. Esto puede suceder de dos maneras:
- Se aplica una única tensión que supera la resistencia del material.
- Se aplica repetidamente una única tensión que excede la resistencia y fatiga el material.
El primero es el método de análisis de diseño más sencillo para la especificación de materiales y se aplica con mayor frecuencia. Es más fácil de enseñar, más rápido y más económico de aplicar, y está respaldado por una amplia información publicada sobre las propiedades del material. Es el enfoque del "factor de seguridad" para el análisis de diseño.
Referencias
Dinos qué te ha parecido el artículo
Artículos recomendados
8.2. La Competitividad Industrial

Estadísticas prácticas no paramétricas

8.1.- Flujo Mínimo Térmico

Confiabilidad y Riesgo: una perspectiva bayesiana

Publica tu artículo en la revista #1 de Mantenimiento Industrial
Publicar un artículo en la revista es gratis, no tiene costo.
Solo debes asegurarte que no sea un artículo comercial.
¿Qué esperas?
O envía tu artículo directo: articulos@predictiva21.com
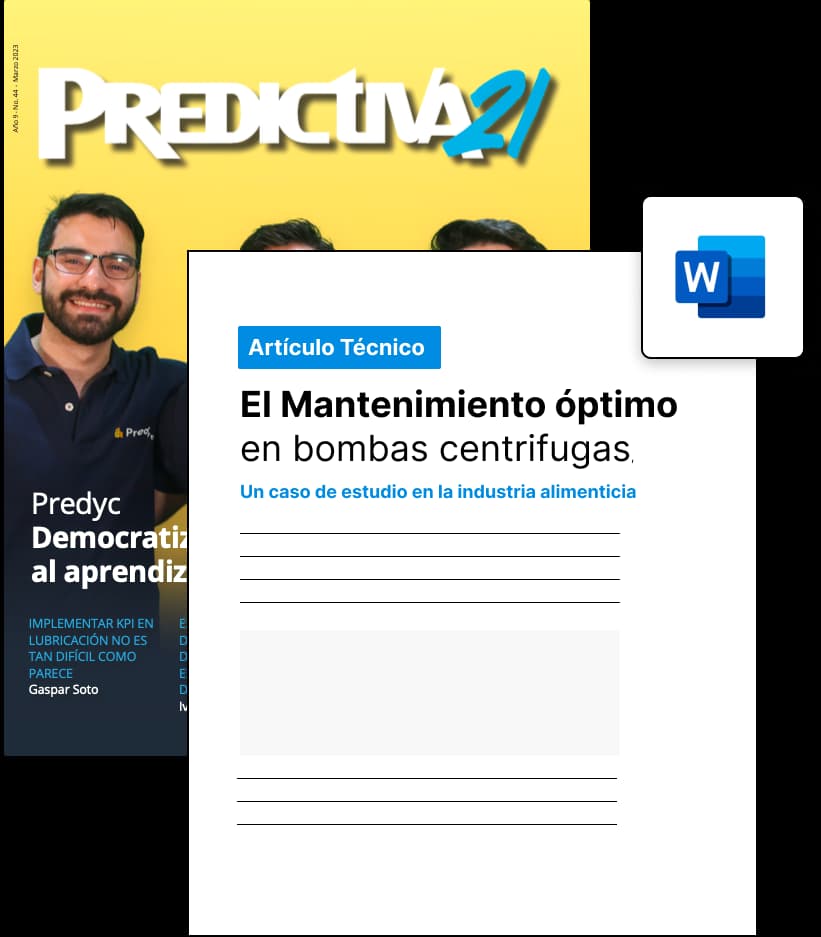