El Internista de la 21, Edición 48
Columna1 de abril de 2024
Soy Rafael Arguelles F., TSU en Informática, Ingeniero Electricista, MSC en Administración de Negocios, con más de 38 años en el mercado de trabajo técnico, profesional y gerencial. Practicante del Silogismo en mi forma de pensar y actuar, por lo tanto, estoico en mi forma de ser. No les contaré mucho mas de mí, pues no es éste el propósito de esta columna.
Debo, en primer lugar, ofrecerles mis excusas por la interrupción en la continuidad de las publicaciones, ya que por razones completamente bajo mi responsabilidad, la columna no fue publicada en la anterior edición de la revista. Dicho esto, entremos en contacto con el tema que estábamos tratando, y que debemos cerrar.
En nuestra anterior columna les enunciamos que la información sería entregada en dos partes, por razones de espacio. En la primera parte, enunciamos conceptualmente a que nos referíamos con el “The KIR Process Work Flow”, es decir, el flujo de trabajo para que se desarrollen las actividades que se requieren para que un activo se mantenga en servicio, sin fallas funcionales disruptivas, manteniendo a raya las fallas funcionales no previstas, de alto impacto económico.
También mencionamos un “documento” muy importante, que es la orden de trabajo, o como también es conocida, la OT. Las comillas, porque la orden de trabajo es muchísimo mas que un documento. La OT es, en síntesis, la definición funcional del proceso que se lleva a cabo para ejecutar una labor de mantenimiento correctivo (programado o no) o de un mantenimiento preventivo (necesariamente programado). Pero . . . ¿y el documento de soporte del Mantenimiento Predictivo? ¿El de Mantenimiento Proactivo?
Las ordenes de trabajo, se generan y gestionan desde un software de gestión de mantenimiento (CMMS por sus siglas en inglés, Computerized Maintenance Management System), en cambio, las herramientas y estrategias de Mantenimiento Predictivo y Mantenimiento Proactivo, son generadas y gestionadas en un software para Gestión de Activos (EAMS por sus siglas en inglés, Enterprise Asset Management System). Esta diferenciación en la gestión, a mi juicio, nos genera una luz sobre donde NO debe residir la gestión de activos. Pero hasta allí dejaré el comentario, pues como comenté en la primera entrega, esto solo genera polémicas, y sobre todo, lo mas importante, es KIR.
Ejemplos de estos sistemas, puede haber muchos. Solo mencionaré algunos con los cuales he trabajado.
- CMMS: Maximo, SAP MM, JDEdwards. De los mencionados, el único realmente diseñado como CMMS exclusivamente, es Maximo. Los otros dos, son modulos para gestión de mantenimiento de la suite de Gestión de Empresas, que incluye compras, inventarios, finanzas, nomina, etc.
- EAMS: Meridium (hoy día GE APM), AMS (Emerson). De los mencionados, solo puedo indicar que Meridium tiene módulos que, además del monitoreo de condición (RCM, IBR, etc.), permiten gestionar los casos documentados de Mantenimiento Proactvo (ACR, etc.)
Ahora bien, es deseable, altamente, que estos dos sistemas de gestión estén completamente integrados. ¿Por qué?
En principio, porque se trata de gestionar activos. ¡Los mismos activos! Adicionalmente, como vimos en la primera parte de este artículo, la Gestión de Mantenimiento es una parte, necesaria e imprescindible, de la gestión de activos. Como vemos en la figura 1, las distintas fases del KIR, se interrelacionan con las distintas herramientas y ambientes de gestión. Las líneas terminadas en punta de flecha que se muestran, dan una idea de como ocurre en secuencia esta interacción. Recordemos que el KIR, al que de ahora en adelante llamaremos por su verdadero nombre, nació como nombre únicamente para evidenciar el objetivo de la implementación de la Confiabilidad Operacional: aumentar la disponibilidad de los activos físicos para producción.

Figura 1. El Proceso KIR, CMMS y EAMS
Logremos, entonces, establecer un recorrido por cada una de esas fases, para algunos ejemplos de casos hipotéticos.
CASO 1: En un equipo rotativo, de criticidad operacional alta, con monitoreo continuo de vibraciones, se produce una alarma por alta vibración en el sistema de control. Esto provoca una solicitud por parte del equipo de operaciones a los técnicos o ingenieros que realizan toma y análisis de estos datos, los cuales se presentan a ejecutar el diagnostico solicitado. Una vez hechas las mediciones, al analizar el espectro, determinan que existe un juego radial mayor al esperado, por lo cual recomiendan reemplazar el cojinete en cuestión. De la misma manera, indican que la maquina puede seguir trabajando, con un monitoreo y análisis más frecuente, de forma de poder preparar el trabajo y hacer una parada ordenada.
Una vez descrito el caso, pasemos a formularnos algunas preguntas:
- La intervención del Técnico que acude a realizar la medición y análisis del caso, ¿en que fase transcurre? ¿En cuál sistema se gestiona?
- El siguiente paso, ¿en qué fase se encuentra y con cual sistema se gestiona?
- El trabajo de llevar el activo a una condición normal de trabajo, ¿en qué fase ocurre? ¿Con cuál sistema se gestiona?
- Una vez hecho el trabajo, ¿Cuál sería el proximo paso y en qué fase ocurre?
- ¿Que tipos de mantenimiento hemos ejecutado hasta ahora?
- El monitoreo frecuente que se menciona, ¿en qué fase ocurre?
Procedamos pues, a responder estas preguntas, invitando al análisis de la respuesta.
La intervención del técnico transcurre en la FASE 1: HERRAMIENTAS DE DIAGNOSTICO APLICADAS EN LA FASE DE OPERACIÓN DEL ACTIVO. Esta, estaba muy facil de responder, pues de hecho en el enunciado se indicó que haría un “toma y análisis de estos datos” para “ejecutar el diagnostico solicitado”. Por supuesto, se gestiona en el EAMS. Si el EAMS y el CMMS están realmente integrados, desde el EAMS saldrá la OT para la corrección del defecto. De no estarlo, alguien tendrá que generar dicha orden de forma manual.
Luego de generarse la orden de trabajo, y ser evaluada por el personal técnico para garantizar que el alcance del trabajo que se específico realmente es el requerido, se inicia la fase de PLANIFICACIÓN DE LA OT. Ya esto responde una parte de la siguiente pregunta: ¿Dónde ocurre el siguiente paso? Este paso, evidentemente, transcurre en la fase 2 “HERRAMIENTAS DE PLANIFICACIÓN PARA KIR” y por supuesto debe gestionarse en el CMMS. Esta fase incluye múltiples etapas, como la preparación, asignación de recursos, gestión de ventana operacional y ejecución del trabajo, que finaliza con la adecuada retroalimentación de la OT, este ultimo un paso muy importante de la gestión que con frecuencia no es debidamente potenciado. Pero del flujo de trabajo del mantenimiento, nos ocuparemos en una entrega posterior, en la que hablaremos del flujo de trabajo en distintas facetas del mantenimiento.
Pues bien, ya se hizo el diagnóstico, se especificó el trabajo, luego el mismo se planificó adecuadamente y se gestionó la ventana operacional . . . Nos corresponde ahora proceder a corregir el defecto, y llevar el Activo a su condición de operación normal. Se reemplaza, en consecuencia, el cojinete con excesivo juego axial, se miden los cojinetes planos que no se cambiaron, se retroalimenta la orden, y se procede a su cierre. La ejecución del trabajo descrito, transcurre en la fase 3, corrección del desperfecto. Y por supuesto, se gestiona en el CMMS.
Ya se hizo el trabajo. ¿Que debe ocurrir ahora? Este proximo paso depende en grado sumo de la madurez de la organización. Debería en esta fase iniciarse una gestión de Pesquisa de Fallas, para determinar la causa del desgaste inesperado del cojinete. En este caso particular, se podría iniciar un Análisis Causa Raíz, que nos ayude a determinar por qu la falla ocurrió, como evitamos una nueva ocurrencia y, muy importante, si genera una lección aprendida que nos ayude a prevenir el mismo tipo de falla en otros activos de la misma familia.
Y entonces, ¿que tipos de Mantenimientos hemos hecho hasta acá? Al diagnosticar, hemos hecho mantenimiento predictivo, o basado en condición. Al corregir un defecto que se ha presentado y hemos podido identificar, estamos haciendo mantenimiento correctivo. Dado que pudimos planificar las actividades requeridas, el mantenimiento correctivo realizado es de tipo planificado.
Si, además de esto, hemos iniciado una pesquisa de fallas, hemos ejecutado un mantenimiento proactivo.
Procedamos ahora a responder la última pregunta, la cual citaré textualmente: “El monitoreo frecuente que se menciona, ¿en qué fase ocurre?” Esta respuesta es quizás, la mas inesperada de todas: En ninguna.
¡Justifique su respuesta! No es necesario hacer un monitoreo y análisis mas continuo. Si ya hemos determinado la causa de la alta vibración, tomando en cuenta la dimensión y frecuencia de la señal, siendo que tenemos un monitoreo continuo con alarmas en el Sistema de control, no se justifica que se tome una medida como la mencionada. Que tomes muestras de espectro y analices más a menudo no cambiará el estado. Si lo que necesitas es saber si el problema se está incrementando, en mi experiencia, lo recomendable es realizar un documento de gestión de cambio temporal, para incrementar el valor de alarma en tu sistema de gestión de alarmas. Esto permitirá que tu equipo no esté en falla permanente en el sistema, a la vez que te permitirá saber cuando el problema ha aumentado. Por supuesto, es necesario también garantizar que, una vez resuelto el problema, el valor de set de la alarma sea restituido a su valor original.
Como indiqué en un principio, este caso, acá descrito, es un caso hipotético. Cualquier parecido con la realidad es pura coincidencia.
CASO 2: Partamos del caso 1. Dado que estaremos interviniendo el equipo rotativo en cuestión, se decide adelantar algunos mantenimientos preventivos que estaban previstos para paradas cortas y que fueron debidamente planificados. Una de esas actividades preventivas, es el ajuste de las conexiones eléctricas, tanto en la caja de conexiones del motor, como en la salida del CCM hacia el motor. Cuando se ejecuta el trabajo, se encuentran conexiones recalentadas a una muy alta temperatura, por lo que se decide reemplazar terminales.
¿Respondemos las mismas preguntas? Veamos:
La intervención original, donde se procede a realizar el reajuste de las conexiones, transcurre en la Fase 3. Atención: ¡esta fase está enunciada como corrección del desperfecto!!! Es cierto, al acudir a ejecutar una tarea de mantenimiento preventivo (reajuste de conexiones cada 3000 horas, por ejemplo), en la práctica, no hemos visualizado ningún defecto. Pero, conceptualmente, el mantenimiento preventivo está concebido para corregir un defecto que estadísticamente está por ocurrir o está ocurriendo. Así que si, es en esta fase que ocurre. Y por supuesto se gestiona en el CMMS.
El siguiente paso, en este segundo ejemplo, es la corrección de la falla funcional detectada. Si, se ha encontrado una falla funcional, que se ha detectado de forma incipiente, pero que está presente de forma indudable. Por supuesto, la ejecución de este trabajo se encuentra también en la fase 3, “CORRECCIÓN DEL DEFECTO” y como ya sabemos, se gestiona en el CMMS. Pero . . . que cosa con los peros en el mantenimiento. Debemos ahora preguntarnos: ¿este trabajo, a todas luces correctivo, debe ejecutarse y documentarse con la misma orden de trabajo? El reemplazo de terminales NO es parte del trabajo preventivo. Por lo tanto, NO debe documentarse con la misma orden. Si nuestro deseo es que el CMMS sea alimentado de forma correcta, este es un trabajo que debe clasificarse como un Mantenimiento Correctivo. ¿Planificado o no Planificado? Evidentemente no es planificado. ¿Es un correctivo de Emergencia? Evidentemente, no ocasionó paros de equipos, por lo que no es de emergencia. Entonces ¿qué tipo de mantenimiento correctivo es? Es un mantenimiento correctivo, de aprovechamiento (el calificativo es mío, pues nunca he visto este concepto debidamente documentado). Digamos que es de aprovechamiento, o de oportunidad, pues es un correctivo que se ejecutó sin parada, y no fue programado ni planificado, si no que es fruto de otro mantenimiento efectuado. Esto, debemos documentarlo, pues este tipo de información nos ayuda a demostrar que actividades de mantenimiento se justifica ejecutar. Esto lleva el activo a operar funcionalmente al 100%, lo cual es de resaltar.
El siguiente paso, una vez ejecutado el trabajo será, nuevamente, documentar la ejecución del mismo, cerrar las ordenes de trabajo (tanto la orden de mtto. preventivo de reajuste de las conexiones como la de mtto. Correctivo de reemplazo de terminales), e iniciar una labor de pesquisa para identificar la causa por la cual la conexión se sobrecalentó. Como ya mencionamos, este trabajo inició como un mantenimiento preventivo (ajuste de las conexiones eléctricas cada 3000 horas), y generó un trabajo correctivo de aprovechamiento (reemplazo de las conexiones).
Nuestra próxima columna, transcurrirá en el tema de la celebración del “DIA INTERNACIONAL DE LA SALUD Y SEGURIDAD EN EL TRABAJO”. Como todos sabemos, la SST es algo que nos atañe a todos los que de alguna manera participamos en la cadena de generación de valor del mismo. Este año, el tema de la conmemoración es el cambio climático, y como este afecta la SST.
Posteriormente, estaremos hablando un poco de los flujos de trabajo requeridos para organizar debidamente la forma en la que la gestión se lleva en el CMMS. Para alimentar, desde ya, esa edición, dejaré una pregunta en el aire: Si, como estrategia al diseñar los planes de mantenimiento centrado en confiabilidad, se decide aplicar “run to failure” a un activo, ¿cómo debe calificarse ese evento cuando ocurre? ¿Es un evento de mantenimiento correctivo? Al levantar mis KPIs, a cual estrategia de mantenimiento debe sumar? Esta discusión, la iniciaremos prontamente en el chat de Predictiva21.
¡Hasta la próxima entrega!
Normas/Documentos:
Familia ISO55000
EN 16646
Dinos qué te ha parecido el artículo
Artículos recomendados
Factores claves para la selección de una bomba centrifuga

El Internista de la 21, Edición 48

El internista de la 21, Edición 51
-1736967700910.png%3Falt%3Dmedia%26token%3Da793b062-6090-4b84-b596-192dde707bc4&w=256&q=75)
El internista de la 21 Edición 45

Publica tu artículo en la revista #1 de Mantenimiento Industrial
Publicar un artículo en la revista es gratis, no tiene costo.
Solo debes asegurarte que no sea un artículo comercial.
¿Qué esperas?
O envía tu artículo directo: articulos@predictiva21.com
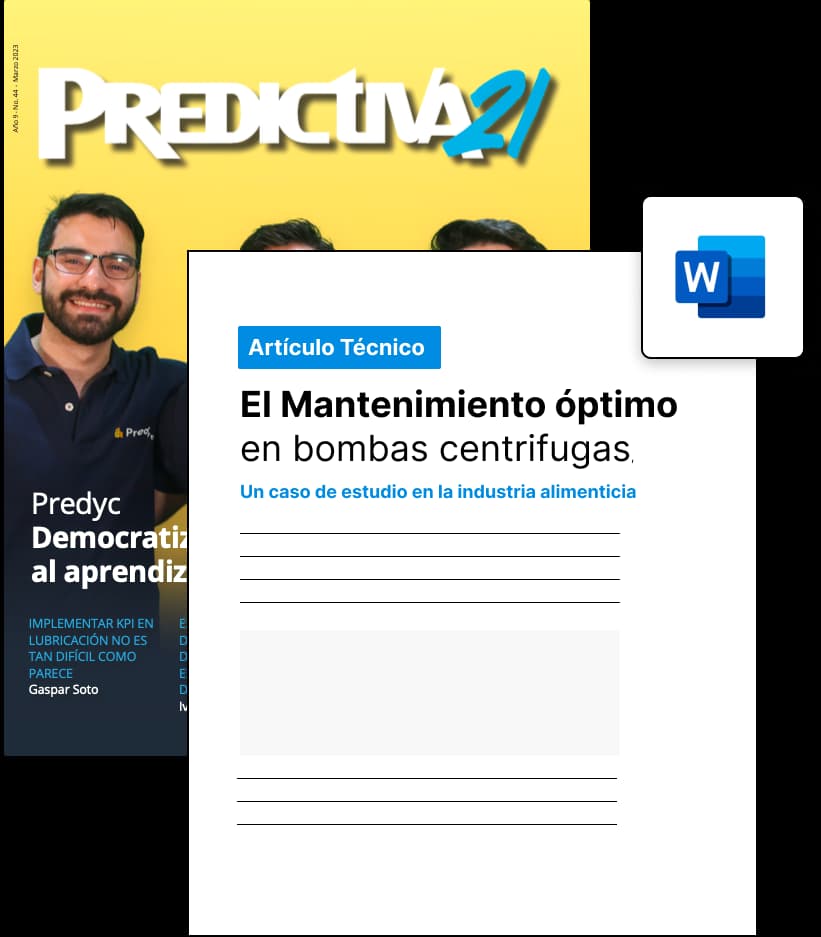
El Internista de la 21, Edición 48
Columna 1 de abril de 2024Soy Rafael Arguelles F., TSU en Informática, Ingeniero Electricista, MSC en Administración de Negocios, con más de 38 años en el mercado de trabajo técnico, profesional y gerencial. Practicante del Silogismo en mi forma de pensar y actuar, por lo tanto, estoico en mi forma de ser. No les contaré mucho mas de mí, pues no es éste el propósito de esta columna.
Debo, en primer lugar, ofrecerles mis excusas por la interrupción en la continuidad de las publicaciones, ya que por razones completamente bajo mi responsabilidad, la columna no fue publicada en la anterior edición de la revista. Dicho esto, entremos en contacto con el tema que estábamos tratando, y que debemos cerrar.
En nuestra anterior columna les enunciamos que la información sería entregada en dos partes, por razones de espacio. En la primera parte, enunciamos conceptualmente a que nos referíamos con el “The KIR Process Work Flow”, es decir, el flujo de trabajo para que se desarrollen las actividades que se requieren para que un activo se mantenga en servicio, sin fallas funcionales disruptivas, manteniendo a raya las fallas funcionales no previstas, de alto impacto económico.
También mencionamos un “documento” muy importante, que es la orden de trabajo, o como también es conocida, la OT. Las comillas, porque la orden de trabajo es muchísimo mas que un documento. La OT es, en síntesis, la definición funcional del proceso que se lleva a cabo para ejecutar una labor de mantenimiento correctivo (programado o no) o de un mantenimiento preventivo (necesariamente programado). Pero . . . ¿y el documento de soporte del Mantenimiento Predictivo? ¿El de Mantenimiento Proactivo?
Las ordenes de trabajo, se generan y gestionan desde un software de gestión de mantenimiento (CMMS por sus siglas en inglés, Computerized Maintenance Management System), en cambio, las herramientas y estrategias de Mantenimiento Predictivo y Mantenimiento Proactivo, son generadas y gestionadas en un software para Gestión de Activos (EAMS por sus siglas en inglés, Enterprise Asset Management System). Esta diferenciación en la gestión, a mi juicio, nos genera una luz sobre donde NO debe residir la gestión de activos. Pero hasta allí dejaré el comentario, pues como comenté en la primera entrega, esto solo genera polémicas, y sobre todo, lo mas importante, es KIR.
Ejemplos de estos sistemas, puede haber muchos. Solo mencionaré algunos con los cuales he trabajado.
- CMMS: Maximo, SAP MM, JDEdwards. De los mencionados, el único realmente diseñado como CMMS exclusivamente, es Maximo. Los otros dos, son modulos para gestión de mantenimiento de la suite de Gestión de Empresas, que incluye compras, inventarios, finanzas, nomina, etc.
- EAMS: Meridium (hoy día GE APM), AMS (Emerson). De los mencionados, solo puedo indicar que Meridium tiene módulos que, además del monitoreo de condición (RCM, IBR, etc.), permiten gestionar los casos documentados de Mantenimiento Proactvo (ACR, etc.)
Ahora bien, es deseable, altamente, que estos dos sistemas de gestión estén completamente integrados. ¿Por qué?
En principio, porque se trata de gestionar activos. ¡Los mismos activos! Adicionalmente, como vimos en la primera parte de este artículo, la Gestión de Mantenimiento es una parte, necesaria e imprescindible, de la gestión de activos. Como vemos en la figura 1, las distintas fases del KIR, se interrelacionan con las distintas herramientas y ambientes de gestión. Las líneas terminadas en punta de flecha que se muestran, dan una idea de como ocurre en secuencia esta interacción. Recordemos que el KIR, al que de ahora en adelante llamaremos por su verdadero nombre, nació como nombre únicamente para evidenciar el objetivo de la implementación de la Confiabilidad Operacional: aumentar la disponibilidad de los activos físicos para producción.

Figura 1. El Proceso KIR, CMMS y EAMS
Logremos, entonces, establecer un recorrido por cada una de esas fases, para algunos ejemplos de casos hipotéticos.
CASO 1: En un equipo rotativo, de criticidad operacional alta, con monitoreo continuo de vibraciones, se produce una alarma por alta vibración en el sistema de control. Esto provoca una solicitud por parte del equipo de operaciones a los técnicos o ingenieros que realizan toma y análisis de estos datos, los cuales se presentan a ejecutar el diagnostico solicitado. Una vez hechas las mediciones, al analizar el espectro, determinan que existe un juego radial mayor al esperado, por lo cual recomiendan reemplazar el cojinete en cuestión. De la misma manera, indican que la maquina puede seguir trabajando, con un monitoreo y análisis más frecuente, de forma de poder preparar el trabajo y hacer una parada ordenada.
Una vez descrito el caso, pasemos a formularnos algunas preguntas:
- La intervención del Técnico que acude a realizar la medición y análisis del caso, ¿en que fase transcurre? ¿En cuál sistema se gestiona?
- El siguiente paso, ¿en qué fase se encuentra y con cual sistema se gestiona?
- El trabajo de llevar el activo a una condición normal de trabajo, ¿en qué fase ocurre? ¿Con cuál sistema se gestiona?
- Una vez hecho el trabajo, ¿Cuál sería el proximo paso y en qué fase ocurre?
- ¿Que tipos de mantenimiento hemos ejecutado hasta ahora?
- El monitoreo frecuente que se menciona, ¿en qué fase ocurre?
Procedamos pues, a responder estas preguntas, invitando al análisis de la respuesta.
La intervención del técnico transcurre en la FASE 1: HERRAMIENTAS DE DIAGNOSTICO APLICADAS EN LA FASE DE OPERACIÓN DEL ACTIVO. Esta, estaba muy facil de responder, pues de hecho en el enunciado se indicó que haría un “toma y análisis de estos datos” para “ejecutar el diagnostico solicitado”. Por supuesto, se gestiona en el EAMS. Si el EAMS y el CMMS están realmente integrados, desde el EAMS saldrá la OT para la corrección del defecto. De no estarlo, alguien tendrá que generar dicha orden de forma manual.
Luego de generarse la orden de trabajo, y ser evaluada por el personal técnico para garantizar que el alcance del trabajo que se específico realmente es el requerido, se inicia la fase de PLANIFICACIÓN DE LA OT. Ya esto responde una parte de la siguiente pregunta: ¿Dónde ocurre el siguiente paso? Este paso, evidentemente, transcurre en la fase 2 “HERRAMIENTAS DE PLANIFICACIÓN PARA KIR” y por supuesto debe gestionarse en el CMMS. Esta fase incluye múltiples etapas, como la preparación, asignación de recursos, gestión de ventana operacional y ejecución del trabajo, que finaliza con la adecuada retroalimentación de la OT, este ultimo un paso muy importante de la gestión que con frecuencia no es debidamente potenciado. Pero del flujo de trabajo del mantenimiento, nos ocuparemos en una entrega posterior, en la que hablaremos del flujo de trabajo en distintas facetas del mantenimiento.
Pues bien, ya se hizo el diagnóstico, se especificó el trabajo, luego el mismo se planificó adecuadamente y se gestionó la ventana operacional . . . Nos corresponde ahora proceder a corregir el defecto, y llevar el Activo a su condición de operación normal. Se reemplaza, en consecuencia, el cojinete con excesivo juego axial, se miden los cojinetes planos que no se cambiaron, se retroalimenta la orden, y se procede a su cierre. La ejecución del trabajo descrito, transcurre en la fase 3, corrección del desperfecto. Y por supuesto, se gestiona en el CMMS.
Ya se hizo el trabajo. ¿Que debe ocurrir ahora? Este proximo paso depende en grado sumo de la madurez de la organización. Debería en esta fase iniciarse una gestión de Pesquisa de Fallas, para determinar la causa del desgaste inesperado del cojinete. En este caso particular, se podría iniciar un Análisis Causa Raíz, que nos ayude a determinar por qu la falla ocurrió, como evitamos una nueva ocurrencia y, muy importante, si genera una lección aprendida que nos ayude a prevenir el mismo tipo de falla en otros activos de la misma familia.
Y entonces, ¿que tipos de Mantenimientos hemos hecho hasta acá? Al diagnosticar, hemos hecho mantenimiento predictivo, o basado en condición. Al corregir un defecto que se ha presentado y hemos podido identificar, estamos haciendo mantenimiento correctivo. Dado que pudimos planificar las actividades requeridas, el mantenimiento correctivo realizado es de tipo planificado.
Si, además de esto, hemos iniciado una pesquisa de fallas, hemos ejecutado un mantenimiento proactivo.
Procedamos ahora a responder la última pregunta, la cual citaré textualmente: “El monitoreo frecuente que se menciona, ¿en qué fase ocurre?” Esta respuesta es quizás, la mas inesperada de todas: En ninguna.
¡Justifique su respuesta! No es necesario hacer un monitoreo y análisis mas continuo. Si ya hemos determinado la causa de la alta vibración, tomando en cuenta la dimensión y frecuencia de la señal, siendo que tenemos un monitoreo continuo con alarmas en el Sistema de control, no se justifica que se tome una medida como la mencionada. Que tomes muestras de espectro y analices más a menudo no cambiará el estado. Si lo que necesitas es saber si el problema se está incrementando, en mi experiencia, lo recomendable es realizar un documento de gestión de cambio temporal, para incrementar el valor de alarma en tu sistema de gestión de alarmas. Esto permitirá que tu equipo no esté en falla permanente en el sistema, a la vez que te permitirá saber cuando el problema ha aumentado. Por supuesto, es necesario también garantizar que, una vez resuelto el problema, el valor de set de la alarma sea restituido a su valor original.
Como indiqué en un principio, este caso, acá descrito, es un caso hipotético. Cualquier parecido con la realidad es pura coincidencia.
CASO 2: Partamos del caso 1. Dado que estaremos interviniendo el equipo rotativo en cuestión, se decide adelantar algunos mantenimientos preventivos que estaban previstos para paradas cortas y que fueron debidamente planificados. Una de esas actividades preventivas, es el ajuste de las conexiones eléctricas, tanto en la caja de conexiones del motor, como en la salida del CCM hacia el motor. Cuando se ejecuta el trabajo, se encuentran conexiones recalentadas a una muy alta temperatura, por lo que se decide reemplazar terminales.
¿Respondemos las mismas preguntas? Veamos:
La intervención original, donde se procede a realizar el reajuste de las conexiones, transcurre en la Fase 3. Atención: ¡esta fase está enunciada como corrección del desperfecto!!! Es cierto, al acudir a ejecutar una tarea de mantenimiento preventivo (reajuste de conexiones cada 3000 horas, por ejemplo), en la práctica, no hemos visualizado ningún defecto. Pero, conceptualmente, el mantenimiento preventivo está concebido para corregir un defecto que estadísticamente está por ocurrir o está ocurriendo. Así que si, es en esta fase que ocurre. Y por supuesto se gestiona en el CMMS.
El siguiente paso, en este segundo ejemplo, es la corrección de la falla funcional detectada. Si, se ha encontrado una falla funcional, que se ha detectado de forma incipiente, pero que está presente de forma indudable. Por supuesto, la ejecución de este trabajo se encuentra también en la fase 3, “CORRECCIÓN DEL DEFECTO” y como ya sabemos, se gestiona en el CMMS. Pero . . . que cosa con los peros en el mantenimiento. Debemos ahora preguntarnos: ¿este trabajo, a todas luces correctivo, debe ejecutarse y documentarse con la misma orden de trabajo? El reemplazo de terminales NO es parte del trabajo preventivo. Por lo tanto, NO debe documentarse con la misma orden. Si nuestro deseo es que el CMMS sea alimentado de forma correcta, este es un trabajo que debe clasificarse como un Mantenimiento Correctivo. ¿Planificado o no Planificado? Evidentemente no es planificado. ¿Es un correctivo de Emergencia? Evidentemente, no ocasionó paros de equipos, por lo que no es de emergencia. Entonces ¿qué tipo de mantenimiento correctivo es? Es un mantenimiento correctivo, de aprovechamiento (el calificativo es mío, pues nunca he visto este concepto debidamente documentado). Digamos que es de aprovechamiento, o de oportunidad, pues es un correctivo que se ejecutó sin parada, y no fue programado ni planificado, si no que es fruto de otro mantenimiento efectuado. Esto, debemos documentarlo, pues este tipo de información nos ayuda a demostrar que actividades de mantenimiento se justifica ejecutar. Esto lleva el activo a operar funcionalmente al 100%, lo cual es de resaltar.
El siguiente paso, una vez ejecutado el trabajo será, nuevamente, documentar la ejecución del mismo, cerrar las ordenes de trabajo (tanto la orden de mtto. preventivo de reajuste de las conexiones como la de mtto. Correctivo de reemplazo de terminales), e iniciar una labor de pesquisa para identificar la causa por la cual la conexión se sobrecalentó. Como ya mencionamos, este trabajo inició como un mantenimiento preventivo (ajuste de las conexiones eléctricas cada 3000 horas), y generó un trabajo correctivo de aprovechamiento (reemplazo de las conexiones).
Nuestra próxima columna, transcurrirá en el tema de la celebración del “DIA INTERNACIONAL DE LA SALUD Y SEGURIDAD EN EL TRABAJO”. Como todos sabemos, la SST es algo que nos atañe a todos los que de alguna manera participamos en la cadena de generación de valor del mismo. Este año, el tema de la conmemoración es el cambio climático, y como este afecta la SST.
Posteriormente, estaremos hablando un poco de los flujos de trabajo requeridos para organizar debidamente la forma en la que la gestión se lleva en el CMMS. Para alimentar, desde ya, esa edición, dejaré una pregunta en el aire: Si, como estrategia al diseñar los planes de mantenimiento centrado en confiabilidad, se decide aplicar “run to failure” a un activo, ¿cómo debe calificarse ese evento cuando ocurre? ¿Es un evento de mantenimiento correctivo? Al levantar mis KPIs, a cual estrategia de mantenimiento debe sumar? Esta discusión, la iniciaremos prontamente en el chat de Predictiva21.
¡Hasta la próxima entrega!
Normas/Documentos:
Familia ISO55000
EN 16646
Dinos qué te ha parecido el artículo
Artículos recomendados
Mundo ACR Edición 48

El Internista de la 21, Edición 48

Mundo ACR Predictiva21 - Un nuevo Año, una Nueva Etapa

El internista de la 21, Edición 51
-1736967700910.png%3Falt%3Dmedia%26token%3Da793b062-6090-4b84-b596-192dde707bc4&w=256&q=75)
Publica tu artículo en la revista #1 de Mantenimiento Industrial
Publicar un artículo en la revista es gratis, no tiene costo.
Solo debes asegurarte que no sea un artículo comercial.
¿Qué esperas?
O envía tu artículo directo: articulos@predictiva21.com
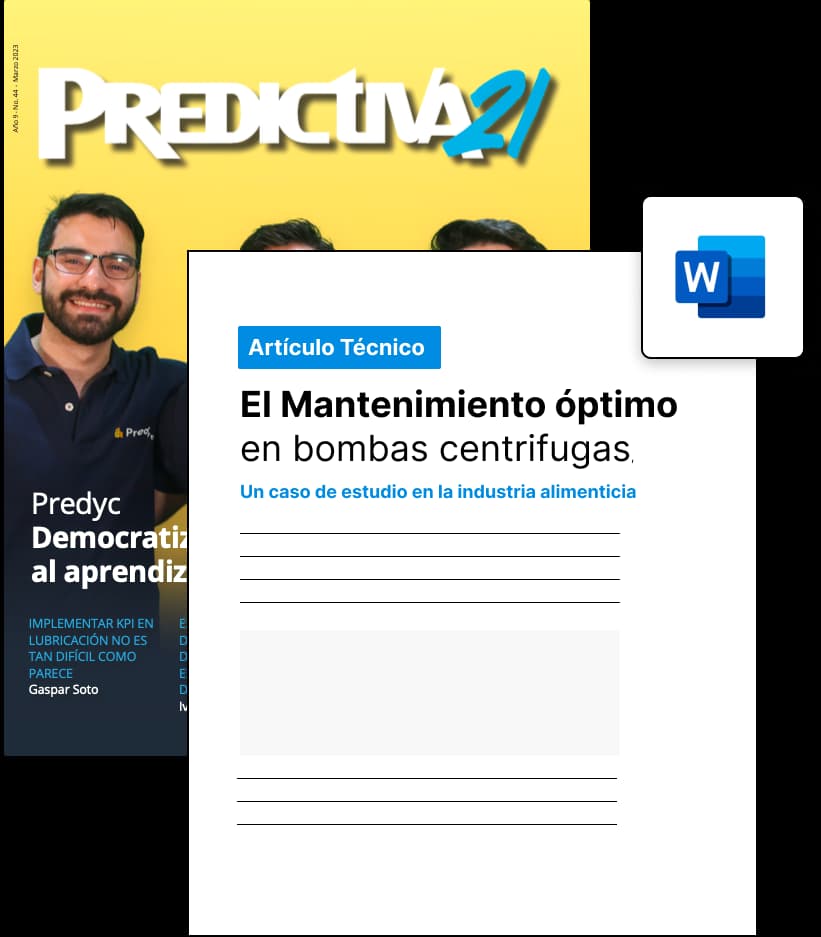