Lazos de corrosión, como parte fundamental de la metodología de inspección basada en riesgo
Articulo11 de abril de 2022
La metodología de Inspección Basada en Riesgo (IBR o RBI por sus siglas en inglés: “Risk Based Inspection”), esta soportada principalmente en las normas API-RP-580, API-RP-581 y la norma API-RP-571 que plantea los mecanismos de degradación aplicables, con el propósito de generar planes o programas de inspección que permitan reducir o mitigar la probabilidad de ocurrencia y por ende el riesgo en caso de ocurrir la perdida de contención de los involucrados en el proceso, sistema o instalación bajo estudio, tal como se muestra esquemáticamente en la Figura 1.

Se usan métodos que guíen hacia un proceso uniforme y efectivo de selección y definición de tareas de inspección de los equipos o componentes en estudio, con base en la identificación de los mecanismos de daño o deterioro, la condición y velocidad de corrosión, soportado en la valoración del comportamiento histórico (en caso de estar disponible), características de diseño, condiciones de operación, mantenimiento, inspección y políticas gerenciales en conjunto con la calidad y efectividad de la inspección que permitan estimar la probabilidad de ocurrencia y cuantificar las consecuencias para determinar los niveles de riesgo entre aplicar o no los planes de inspección basado en riesgo, proponiendo acciones específicas a los equipos o componentes que mayor riesgo presenten y generales a los de menor riesgo, permitiendo controlar el riesgo y el uso adecuado de los recursos destinados a la gestión del mantenimiento, con beneficios técnicos y económicos a las personas, entorno, seguridad e instalaciones.
Los principales etapas, pasos o actividades secuenciales para la aplicación de la metodología de Inspección Basada en Riesgo (IBR) son:
- Recolectar – recopilar y validar la información.
- Sistematizar o Identificar los nodos de estudio con los equipos a evaluar, momento en el cual:
- Se identifican de los Mecanismos de Daño: Corrosión, Agrietamiento, etc., con base en:
- Tipo de Materiales.
- Condiciones Operacionales.
- Fluidos manejados.
- Condiciones ambientales.
- Configuración de los equipos para a definir lo lazos de corrosión, entre otros.
- Se identifican los grupos de inventario, considerando
- Los sistemas de aislamiento (válvulas).
- Detección.
- Mitigación, entre otros.
- Se identifican de los Mecanismos de Daño: Corrosión, Agrietamiento, etc., con base en:
- Valorar el riesgo, donde se:
- Evalúan las frecuencia o probabilidades de ocurrencia de la falla, con base en la determinación de los factores de daño de cada uno de los mecanismos de deterioro previamente identificados.
- Evalúan / Determinan las consecuencias de la falla con base en lo grupos de inventario previamente establecidos, ya sea por consecuencia en área de afectación (Ej. Recipientes de presión) o consecuencia financiera (Ej. Tanques).
- Valoran / Cuantificación del Riesgo mediante la localización de cada componente o equipo considerado en el análisis dentro de la matriz de riesgo establecidas para el análisis.
- Establecer los planes de mantenimiento e inspección óptimos para asegurar la integridad mecánica de los componentes/equipos/sistemas y mantener la continuidad operacional en la instalación.
- Desarrollar un Análisis Costo-Riesgo-Beneficio, de la forma en que se puedan realizar las actividades de inspección y acciones de mantenimiento, mediante la cuantificación y asignación de los recursos.
- Identificar áreas de atención y mejora y validar los resultados y recomendaciones del IBR.
- Ciclo de mejora continua una vez se obtengan los resultados de implantar los planes de inspección y acciones de mantenimiento recomendadas por el IBR, con el fin de evaluar / revisar sus indicadores clave y retroalimentar el proceso.
Como puede apreciarse, el paso 2, considera la sistematización y el desarrollo de los lazos de corrosión es una etapa fundamental y critica en la aplicación de la metodología de inspección basada en riesgo, que requiere un análisis cuidadoso y detallado que requiere del suficiente conocimiento del diseño, los equipos, el proceso, los mecanismos de falla y las condiciones de operación para realizarlo, por tanto, los documentos asociados con la selección de los materiales son pieza fundamental, ya que consideran los escenarios considerados en su diseño y selección.
En tal sentido, se deben considerar todos los modos básicos de degradación al identificar los mecanismos de daño para cada uno de los componentes (equipos, tuberías) de la instalación, entre los que se encuentran:
- Adelgazamiento interno debido a la corrosión o erosión.
- Adelgazamiento externo debido a la corrosión.
- Agrietamiento.
- Cambios metalúrgicos.
- Fuerzas mecánicas, etc.
Lo anterior permitirá evaluar las consecuencias y los métodos de mitigación en etapas posteriores de la aplicación de la metodología de inspección basada en riesgo
Así mismo, proporciona lineamientos para gestionar proactivamente los riesgos por corrosión, identificar y monitorear los daños, y brindar opciones de control de la corrosión en las fases de operación y mantenimiento del ciclo de vida de los activos de cualquier instalación.
Además, requerirá revisiones periódicas, con base en la evaluación de desempeño de la instalación, auditorías, hallazgos de pruebas, inspecciones o mantenimiento mayor, cambios en: el diseño, composición química de la alimentación, capacidad y parámetros operativos o posterior a la actualización de un estudio previo de IBR, entre otros.
Cada unidad de proceso se divide en lazos de corrosión (LC o CL, por sus siglas en inglés) con los principales mecanismos de daño y se marcará en cada diagrama de flujo de proceso (DFP o PFD, por sus siglas en inglés) con colores distintivos y únicos que mostrarán el grupo de tuberías y equipos dentro de cada lazo de corrosión. Tal como se puede observar en la Figura 2, la cual muestra un DFP con seis (6) lazos de corrosión, considerando once (11) diferentes mecanismos de daño.

Por tanto, un lazo de corrosión es una forma práctica de describir, comprender y verificar los mecanismos de degradación en una instalación y consta de un grupo de activos (sistema de tuberías y equipos) agrupados con condiciones de proceso similares, construidos de materiales similares y que comparten amenazas similares de corrosión/degradación. o mismos mecanismos de daño activos/potenciales (DM, por sus siglas en inglés) según lo indicados en los estándares:
- ASME PCC-3 Tabla A-1.
- API-RP-580: Risk Based Inspection, Apéndice A-Mecanismos de Deterioro.
- API-RP-571: Mecanismos de Daño que Afectan Equipos Fijos en la Industria de Refinación.
De los cuales los mecanismos de daño por fabricación de soldadura están fuera del alcance de la mayor parte de los estudios de IBR.
El mecanismo de daño (DM) es un fenómeno que induce cambios micro y/o macro nocivos para el material, los cuales son perjudiciales para la condición del material o sus propiedades mecánicas. Los mecanismos de daño suelen ser incrementales, acumulativos e irrecuperables, y comúnmente están asociados con:
- Adelgazamiento.
- Ataque químico.
- Fluencia o “creep”.
- Erosión.
- Fatiga.
- Fractura.
- Fragilización o “embrittlement”.
- Envejecimiento térmico.
Para comprender los mecanismos de daño es importante analizar la probabilidad de falla, la selección de intervalos, ubicaciones y técnicas de inspección apropiados; la capacidad de tomar decisiones (por ejemplo, modificaciones al proceso, selección de materiales, monitoreo) que puedan eliminar o reducir la probabilidad de un mecanismo de daño específico.
Además, la identificación de los mecanismos de daño y modos de falla creíbles para el equipo incluido en un análisis de riesgo es esencial para la calidad y la efectividad del análisis de riesgo.
Las directrices establecidas permitirán: asegurar un riesgo mínimo previsible sobre la seguridad y la confiabilidad; asegurar la máxima esperanza de vida de los equipos o identificar áreas de aplicaciones de nuevas tecnologías.
Con base en base a lo anterior, algunos de los principales desafíos contra la corrosión son:
- Agrietamiento por corrosión bajo tensión (SCC-Stress Corrosion Cracking): SCC es el agrietamiento inducido por la influencia combinada de la tensión de tracción y un ambiente corrosivo (ver Figura 3).


El impacto de SCC en un material generalmente se encuentra entre el agrietamiento en seco y el umbral de fatiga de dicho material. Los esfuerzos de tracción requeridos pueden estar en forma de esfuerzos aplicados directamente o en forma de esfuerzos residuales.
La deformación y el conformado en frío, la soldadura, el tratamiento térmico, el mecanizado y el esmerilado pueden introducir tensiones residuales. La magnitud y la importancia de tales tensiones a menudo se subestiman.
Las tensiones residuales creadas como resultado de las operaciones de soldadura tienden a aproximarse al límite elástico. La acumulación de productos de corrosión en espacios confinados también puede generar tensiones significativas y no debe pasarse por alto. SCC generalmente ocurre en ciertas combinaciones específicas de aleación-ambiente-esfuerzo.
Por lo general, la mayor parte de la superficie permanece sin atacar, pero con grietas finas que penetran en el material. En la microestructura, estas grietas pueden tener morfología intergranular o transgranular. Macroscópicamente, las fracturas por SCC tienen una apariencia frágil.
El SCC se clasifica como una forma catastrófica de corrosión, ya que la detección de grietas tan finas puede ser muy difícil y el daño no es fácil de predecir.
- Corrosión localizada: puede adoptar muchas formas, como picaduras que dan lugar a numerosas cavidades superficiales, corrosión galvánica selectiva en la región entre dos metales electroquímicamente diferentes, ataque de corrosión selectivo a lo largo de una zona afectada por el calor de soldadura (HAZ-heat affected zone), ataque de corrosión en grietas resultantes de la concentración de especie(s) química(s) agresiva(s), o ranurado local debido al impacto (ver Figura 4).
En general, cuanto más resistente es una aleación a la corrosión general, más probable es que la corrosión, si se produce, sea localizada.

- Erosión-Corrosión: es la aceleración en la tasa de ataque de corrosión en el metal debido al movimiento relativo de un fluido corrosivo y una superficie metálica.
El aumento de la turbulencia causado por las picaduras en las superficies internas de un tubo puede provocar un rápido aumento de las tasas de erosión y, finalmente, una fuga (Ver Figura 5).

Una combinación de erosión y corrosión puede conducir a tasas de picaduras extremadamente altas. La selección de materiales juega un papel importante en la minimización de los daños por erosión y corrosión.
Se debe tener precaución cuando se predice el comportamiento de erosión-corrosión sobre la base de la dureza. Una alta dureza en un material no garantiza necesariamente un alto grado de resistencia a la erosión-corrosión.
Las características de diseño también son particularmente importantes; los diseños que crean turbulencia, restricciones de flujo y obstrucciones son indeseables por lo que deben evitarse los cambios bruscos en la dirección del flujo, en lo posible; y en cuyo caso colocar accesorios que disminuyan su impacto.
- Corrosión bajo el aislamiento (CUI-Corrosion under Insulation): es cualquier tipo de corrosión que ocurre debido a la acumulación de humedad en la superficie externa del equipo aislado, por al menos uno de muchos factores (filtración, falla del aislamiento, condensación, entre otros), siendo la entrada de agua el problema clave en CUI.
La corrosión en sí es más comúnmente corrosión por cloruro, ácida o alcalina. Se debe tener especial cuidado durante el diseño para no promover la corrosión al permitir que el agua ingrese al sistema, ya sea directa o indirectamente por acción capilar. La humedad puede ser externa o puede estar presente en el propio material aislante. La corrosión puede atacar el revestimiento, el material de aislamiento o el equipo propiamente dicho (Ver Figura 6).

Para equipos de alta temperatura, el agua que ingresa a un material aislante y se difunde hacia adentro eventualmente alcanzará una región seca en la tubería caliente o en la pared del equipo. Junto a esta región seca hay una zona en la que los poros del aislamiento están llenos de una solución salina saturada. Cuando ocurre una parada o cambio de proceso y la temperatura de la pared metálica disminuye, la zona de solución salina saturada se mueve hacia la pared metálica.
Al recalentarse, la pared estará temporalmente en contacto con la solución saturada y puede comenzar el agrietamiento por corrosión bajo tensión.
Los ciclos de secado/humectación en los problemas asociados con CUI son un fuerte acelerador del daño por corrosión, ya que provocan la formación de una química cada vez más agresiva que puede conducir a los peores problemas de corrosión posibles, por ejemplo: agrietamiento por corrosión bajo tensión y fallas catastróficas prematuras del equipo.
- Corrosión externa: puede resultar en la reducción gradual del espesor de la pared del equipo o tubería y la consiguiente pérdida de resistencia.
Puede ocurrir de manera relativamente uniforme sobre la superficie de un área (a veces denominada corrosión genera») o en puntos aislados (corrosión localizada) debido a las condiciones ambientales en el exterior del equipo o tubería (Ver Figura 7).

Esta pérdida de resistencia podría provocar fugas o rupturas debido a las presiones internas, a menos que se repare el componente.
Por lo general, la superficie externa del equipo o tubería está recubierta para evitar que el ambiente o suelo circundante u otras condiciones ambientales entren en contacto con el material, evitando así el proceso de oxidación.
- Corrosión general: la corrosión de ataque general avanza más o menos uniformemente sobre una superficie expuesta sin una localización apreciable; lo que conduce a un adelgazamiento relativamente uniforme en los materiales de láminas y placas y un adelgazamiento general en un lado o en el otro (o ambos) para las tuberías. Se reconoce por una rugosidad de la superficie y generalmente por la presencia de productos de corrosión (ver Figura 8).

El mecanismo del ataque típicamente es un proceso electroquímico que tiene lugar en la superficie del material. Las diferencias en composición u orientación entre pequeñas áreas en la superficie del metal crean ánodos y cátodos que facilitan el proceso de corrosión.
La corrosión general es causada con mayor frecuencia por la mala aplicación de materiales en ambientes corrosivos, la corrosión general a menudo se puede tolerar porque el efecto de la pérdida de metal es relativamente fácil de evaluar y se pueden hacer concesiones en el diseño inicial.
Algunas de las estrategias recomendables para el adecuado manejo de la corrosión o métodos de prevención, control y mitigación que deben considerarse, se encuentran:
- Selección de materiales: desde un punto de vista puramente técnico, una respuesta obvia a los problemas de corrosión sería utilizar materiales más resistentes a la corrosión. Siendo en muchos casos, este enfoque, una alternativa económica a otros métodos de control de la corrosión.
La resistencia a la corrosión no es la única propiedad que se debe tener en cuenta al seleccionar los materiales, pero es de gran importancia en las industrias de procesos químicos.
Por ejemplo, el acero al carbono es el material más utilizado; sin embargo, con mayor capacidad y contaminantes, los aceros inoxidables se especifican cada vez más para resistir altas velocidades y ataques agresivos.En todo caso, se deben realizar los análisis de los fluidos a transportar o contener, así como sus contaminantes y condiciones de proceso para su adecuada selección.
- Selección de revestimientos protectores: Los revestimientos se aplican sobre diversas estructuras y equipos operativos externa o internamente para proteger contra la corrosión/erosión, actuar como barreras térmicas, evitar el ensuciamiento, etc.
Los revestimientos pueden ser orgánicos, metálicos, cerámicos o compuestos y se pueden usar como películas de barrera para evitar las picaduras y la corrosión, la erosión y los ataques químicos inducidos por microbios.
Se aplican, externa o internamente en inmersión, enterrados, atmosféricos y bajo aislamientos. Existen diferentes tecnologías de recubrimiento que se pueden especificar y personalizar para adaptarse al propósito además de otras estrategias de manejo de la corrosión. Por ejemplo:
- Se pueden usar recubrimientos epoxi especiales rellenos de cerámica que contienen pigmento antibacteriano para proteger los codos de las tuberías, las cajas del intercambiador y las válvulas internas de la corrosión por MIC (microbiological induce corrosion). Además, el recubrimiento especial para los tubos de los rehervidores aplicados por inundación puede evitar las picaduras y la corrosión debajo de los depósitos.
- Los recubrimientos de encapsulación de óxido o epoxi tolerantes a la superficie se pueden usar durante el trabajo de mantenimiento de la estructura de acero con un alto lavado con agua en lugar de la limpieza con chorro abrasivo.
- Los tipos de revestimiento viscoelástico o epoxi 100 % sólido se utilizan para proteger los desagües enterrados y las tuberías ascendentes de acero para agua contra incendios, debido a corrosión del suelo según la temperatura.
- Los revestimientos de inmersión se utilizan para proteger equipos y tuberías de acero al carbono e inoxidable contra picaduras y agrietamiento por corrosión bajo tensión de cloruro bajo aislamiento térmico y protección contra incendios.
- Se pueden usar tipos de recubrimientos aislantes térmicos de película delgada (40 – 100 mils) con recubrimientos primarios anticorrosión en lugar del aislamiento convencional, para reducir el riesgo de corrosión debajo del aislamiento térmico.
- Se pueden usar recubrimientos epoxi rellenos de cerámica para proteger los codos de las tuberías, las placas de tubos del intercambiador y las válvulas internas de la corrosión y la erosión.
- Monitoreo de la corrosión: el manejo exitoso de la corrosión se obtiene mediante la creación de un historial de resultados de monitoreo y la correlación de esos datos con los resultados reales de pruebas e inspecciones(T&I) o Inspección en marcha.
Los métodos siguientes pueden utilizarse para monitorear el comportamiento de la corrosión:
- Cupones de Corrosión.
- Sondas de Corrosión.
- Pruebas no destructivas (NDT) o en línea (OSI).
- Análisis de laboratorio.
- Análisis de productos de corrosión.
- Recuentos de hierro.
- Recuento de bacterias.
- Análisis de salmueras.
- Composición de los fluidos manejados o transportados.
- Monitoreo de cambios en las variables del proceso; es decir, presión, temperatura y/o flujo.
- Análisis de fallas.
- Inspección visual.
Los cupones de corrosión y las sondas en línea se utilizan a menudo para estudiar la eficacia de los programas de inhibidores de la corrosión o los efectos de los cambios de procesos específicos sobre la corrosión. Sin embargo, no miden con precisión la corrosión localizada (picaduras). Las lecturas se deben usar para crear un indicador de pérdida de índice de corrosión a través de la tendencia de los datos. Siempre que este indicador muestre una tendencia ascendente, el ingeniero de corrosión revisará la inhibición de la corrosión y los parámetros del proceso de las tuberías y el equipo de la planta.
Recientemente, los métodos no intrusivos han mejorado y se han vuelto más confiables para monitorear la corrosión en sistemas donde no se pueden usar técnicas intrusivas, como en ubicaciones de alta velocidad o ubicaciones de alta presión. La mayoría de estas tecnologías se encuentran actualmente en evaluación. Algunas de las siguientes técnicas avanzadas de pruebas no destructivas o NDT pueden ser de utilidad en la inspección progresiva de equipos y tuberías:
- Mapeo de UT automatizado (P-Scan): este método se utiliza para inspeccionar recipientes y tuberías en busca de corrosión, ampollas de hidrógeno y grietas ambientales, en particular para las tuberías.
- Escáner UT avanzado: esta técnica se usa para inspeccionar tuberías y equipos a temperaturas elevadas (550 °F) y se usa para verificar el agrietamiento y la formación de ampollas por pasos.
- Tiempo de Difracción de Vuelo (TOFD): Este sistema se utiliza para detectar y dimensionar metales base y defectos de soldadura (grietas) en recipientes a presión y tuberías.
- Técnicas de Inspección: La inspección normalmente se refiere a la evaluación de la calidad de alguna característica en relación con un estándar o una especificación.
- Equipo: la inspección visual (VT), la medición de el espesor aleatorio por ultrasonido (UT) y la prueba de partículas magnéticas fluorescentes húmedas (WFMPT) se usan comúnmente para verificar la corrosión localizada y el agrietamiento ambiental.
- Tubería: Varias técnicas como espesor ultrasónico aleatorio (UT), onda de corte UT (UTSW) de soldaduras y radiografía (RT) se utilizan para detectar pérdida de metal, corrosión preferencial de soldadura y agrietamiento fino.
Algunas de las recomendaciones para la inspección son:
- Para Interno: Realizar 10% MFL (Magnetic flux leakage) de tubos, 100% VT con medidas de UT aleatorio o 50% VT y UT aleatorio.
- Para Externa: 50% UTT de CML’s (condition monitoring locations); 100% de los CML’s usando UTSW manual, AUT o radiografía.
- Para CUI: 100% inspección visual externa y 100% perfil o radiografía en tiempo real de daño o área sospechosa.
Así mismo, se deben evaluar nuevas tecnologías para obtener mejores resultados debido a las actividades de inspección que se deben realizar, es decir:
- Sistema de monitoreo de erosión-corrosión con abrazadera en línea: El sistema de monitoreo es un dispositivo no intrusivo que permite medir el daño por corrosión o erosión en el sistema de tuberías. Se basa en técnicas acústicas de ondas de cordero guiadas.
El uso del enfoque no intrusivo brindará flexibilidad en la selección de las ubicaciones de monitoreo en áreas congestionadas donde las herramientas necesarias para mantener los dispositivos intrusivos pueden no tener espacio para funcionar.
Se puede mejorar la seguridad y confiabilidad de la planta al identificar y monitorear la pérdida en el espesor de la pared de la tubería. La corrosión detectada por estos dispositivos podría abordarse mediante la implementación de medidas adecuadas de mitigación de la corrosión.
- Recubrimientos protectores: entre los que destacan:
- Recubrimiento aislante térmico: Se aplica como alternativa al aislamiento existente en equipos, tuberías y válvulas.
- Revestimiento de PTFE para tubería/brida de instrumentación: Previene la corrosión por estancamientos y ayuda a un mejor control del proceso.
- Revestimiento de vidrio: Puede ser utilizado en sondas de termopozo de temperatura.
- Recubrimientos cerámicos: Puede ser utilizado para tubos calentadores y refractarios.
- Recubrimiento del tubo del intercambiador de calor: se puede aplicar tanto en la superficie externa como interna de los tubos.
- Prueba de componentes de aislamiento: utiliza el método de corriente de Foucault pulsada para medir el espesor de pared promedio restante bajo el aislamiento de acero al carbono de baja aleación/objeto ferromagnético y analizar su descomposición y es el método más confiable para la detección de corrosión.
Es una técnica excelente para aplicar en objetos que están aislados y también se puede aplicar en objetos que son de difícil acceso o de costo extremo. El rango de aplicación es enorme ya que contribuye a reducir significativamente los costos de inspección. Esta tecnología de corriente de Foucault pulsada es una excelente herramienta en línea para posicionar más trabajos de inspección durante el apagado o los trabajos de mantenimiento periódico.
Cursos recomendados




%252FImagen%252FRAMPREDYC-1730060420837.webp%3Falt%3Dmedia%26token%3D2634a7f0-988e-4022-b91f-382503e6e9db&w=3840&q=75)



Bibliografía
- API-510: “Pressure Vessel Inspection Code: In-Service Inspection, Rating, Repair, and Alteration”.
- API-570: “Piping Inspection Code: In-Service Inspection, Rating, Repair, and Alteration of Piping Systems”.
- API-RP-571: “Damage Mechanisms Affecting Fixed Equipment in Refining Industry”.
- API-RP-572: “Inspection Practices for Pressure Vessels”.
- API-RP-574: “Inspection Practices for Piping System Components”.
- API-RP-580: “Risk-Based Inspection”.
- API-RP-581: “Risk-Based Inspection Technology”.
- ASME PCC-3: “Inspection Planning Using Risk Based Methods”.
Autor

Elimar Anauro Rojas Monsalve
Consultor Senior & Ejecutivo, Asesor Técnico en Procesos, Confiabilidad, Riesgo, Incertidumbre e Integridad
Email: elimar.rojas@gmail.com
Dinos qué te ha parecido el artículo
Artículos recomendados
Dirección y Gestión de Paradas de Planta, Bajo los Lineamientos del PMI

Averías

Como un CMMS ayuda a impulsar la Excelencia Operativa

Programación del mantenimiento preventivo

Publica tu artículo en la revista #1 de Mantenimiento Industrial
Publicar un artículo en la revista es gratis, no tiene costo.
Solo debes asegurarte que no sea un artículo comercial.
¿Qué esperas?
O envía tu artículo directo: articulos@predictiva21.com
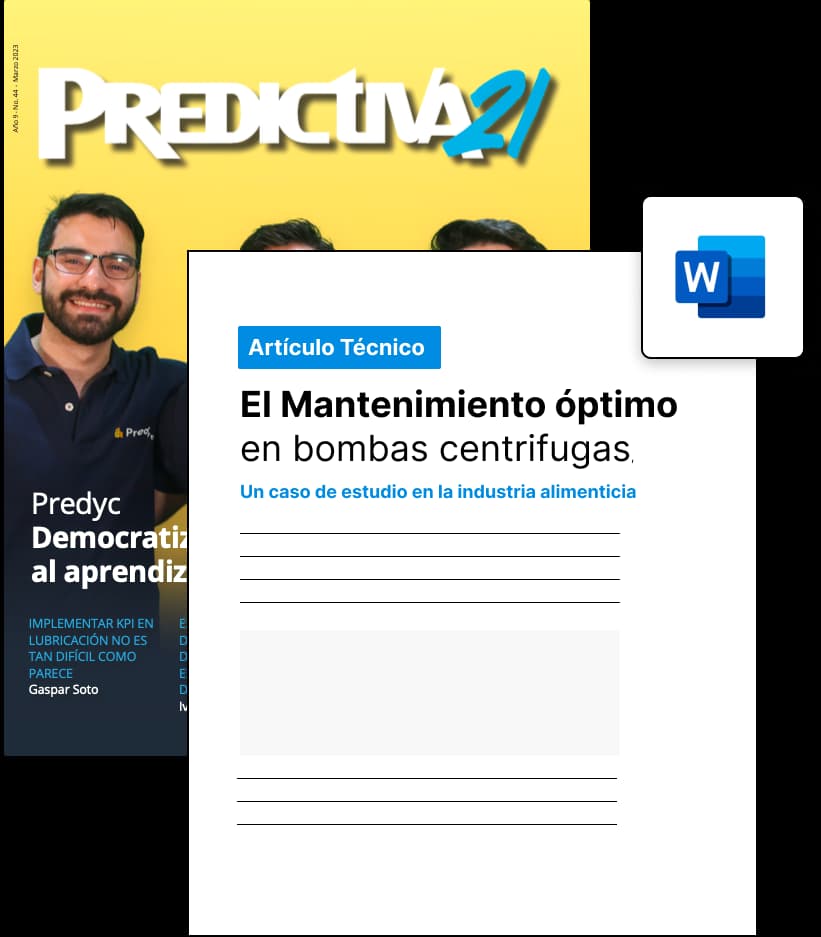
Lazos de corrosión, como parte fundamental de la metodología de inspección basada en riesgo
Articulo 11 de abril de 2022La metodología de Inspección Basada en Riesgo (IBR o RBI por sus siglas en inglés: “Risk Based Inspection”), esta soportada principalmente en las normas API-RP-580, API-RP-581 y la norma API-RP-571 que plantea los mecanismos de degradación aplicables, con el propósito de generar planes o programas de inspección que permitan reducir o mitigar la probabilidad de ocurrencia y por ende el riesgo en caso de ocurrir la perdida de contención de los involucrados en el proceso, sistema o instalación bajo estudio, tal como se muestra esquemáticamente en la Figura 1.

Se usan métodos que guíen hacia un proceso uniforme y efectivo de selección y definición de tareas de inspección de los equipos o componentes en estudio, con base en la identificación de los mecanismos de daño o deterioro, la condición y velocidad de corrosión, soportado en la valoración del comportamiento histórico (en caso de estar disponible), características de diseño, condiciones de operación, mantenimiento, inspección y políticas gerenciales en conjunto con la calidad y efectividad de la inspección que permitan estimar la probabilidad de ocurrencia y cuantificar las consecuencias para determinar los niveles de riesgo entre aplicar o no los planes de inspección basado en riesgo, proponiendo acciones específicas a los equipos o componentes que mayor riesgo presenten y generales a los de menor riesgo, permitiendo controlar el riesgo y el uso adecuado de los recursos destinados a la gestión del mantenimiento, con beneficios técnicos y económicos a las personas, entorno, seguridad e instalaciones.
Los principales etapas, pasos o actividades secuenciales para la aplicación de la metodología de Inspección Basada en Riesgo (IBR) son:
- Recolectar – recopilar y validar la información.
- Sistematizar o Identificar los nodos de estudio con los equipos a evaluar, momento en el cual:
- Se identifican de los Mecanismos de Daño: Corrosión, Agrietamiento, etc., con base en:
- Tipo de Materiales.
- Condiciones Operacionales.
- Fluidos manejados.
- Condiciones ambientales.
- Configuración de los equipos para a definir lo lazos de corrosión, entre otros.
- Se identifican los grupos de inventario, considerando
- Los sistemas de aislamiento (válvulas).
- Detección.
- Mitigación, entre otros.
- Se identifican de los Mecanismos de Daño: Corrosión, Agrietamiento, etc., con base en:
- Valorar el riesgo, donde se:
- Evalúan las frecuencia o probabilidades de ocurrencia de la falla, con base en la determinación de los factores de daño de cada uno de los mecanismos de deterioro previamente identificados.
- Evalúan / Determinan las consecuencias de la falla con base en lo grupos de inventario previamente establecidos, ya sea por consecuencia en área de afectación (Ej. Recipientes de presión) o consecuencia financiera (Ej. Tanques).
- Valoran / Cuantificación del Riesgo mediante la localización de cada componente o equipo considerado en el análisis dentro de la matriz de riesgo establecidas para el análisis.
- Establecer los planes de mantenimiento e inspección óptimos para asegurar la integridad mecánica de los componentes/equipos/sistemas y mantener la continuidad operacional en la instalación.
- Desarrollar un Análisis Costo-Riesgo-Beneficio, de la forma en que se puedan realizar las actividades de inspección y acciones de mantenimiento, mediante la cuantificación y asignación de los recursos.
- Identificar áreas de atención y mejora y validar los resultados y recomendaciones del IBR.
- Ciclo de mejora continua una vez se obtengan los resultados de implantar los planes de inspección y acciones de mantenimiento recomendadas por el IBR, con el fin de evaluar / revisar sus indicadores clave y retroalimentar el proceso.
Como puede apreciarse, el paso 2, considera la sistematización y el desarrollo de los lazos de corrosión es una etapa fundamental y critica en la aplicación de la metodología de inspección basada en riesgo, que requiere un análisis cuidadoso y detallado que requiere del suficiente conocimiento del diseño, los equipos, el proceso, los mecanismos de falla y las condiciones de operación para realizarlo, por tanto, los documentos asociados con la selección de los materiales son pieza fundamental, ya que consideran los escenarios considerados en su diseño y selección.
En tal sentido, se deben considerar todos los modos básicos de degradación al identificar los mecanismos de daño para cada uno de los componentes (equipos, tuberías) de la instalación, entre los que se encuentran:
- Adelgazamiento interno debido a la corrosión o erosión.
- Adelgazamiento externo debido a la corrosión.
- Agrietamiento.
- Cambios metalúrgicos.
- Fuerzas mecánicas, etc.
Lo anterior permitirá evaluar las consecuencias y los métodos de mitigación en etapas posteriores de la aplicación de la metodología de inspección basada en riesgo
Así mismo, proporciona lineamientos para gestionar proactivamente los riesgos por corrosión, identificar y monitorear los daños, y brindar opciones de control de la corrosión en las fases de operación y mantenimiento del ciclo de vida de los activos de cualquier instalación.
Además, requerirá revisiones periódicas, con base en la evaluación de desempeño de la instalación, auditorías, hallazgos de pruebas, inspecciones o mantenimiento mayor, cambios en: el diseño, composición química de la alimentación, capacidad y parámetros operativos o posterior a la actualización de un estudio previo de IBR, entre otros.
Cada unidad de proceso se divide en lazos de corrosión (LC o CL, por sus siglas en inglés) con los principales mecanismos de daño y se marcará en cada diagrama de flujo de proceso (DFP o PFD, por sus siglas en inglés) con colores distintivos y únicos que mostrarán el grupo de tuberías y equipos dentro de cada lazo de corrosión. Tal como se puede observar en la Figura 2, la cual muestra un DFP con seis (6) lazos de corrosión, considerando once (11) diferentes mecanismos de daño.

Por tanto, un lazo de corrosión es una forma práctica de describir, comprender y verificar los mecanismos de degradación en una instalación y consta de un grupo de activos (sistema de tuberías y equipos) agrupados con condiciones de proceso similares, construidos de materiales similares y que comparten amenazas similares de corrosión/degradación. o mismos mecanismos de daño activos/potenciales (DM, por sus siglas en inglés) según lo indicados en los estándares:
- ASME PCC-3 Tabla A-1.
- API-RP-580: Risk Based Inspection, Apéndice A-Mecanismos de Deterioro.
- API-RP-571: Mecanismos de Daño que Afectan Equipos Fijos en la Industria de Refinación.
De los cuales los mecanismos de daño por fabricación de soldadura están fuera del alcance de la mayor parte de los estudios de IBR.
El mecanismo de daño (DM) es un fenómeno que induce cambios micro y/o macro nocivos para el material, los cuales son perjudiciales para la condición del material o sus propiedades mecánicas. Los mecanismos de daño suelen ser incrementales, acumulativos e irrecuperables, y comúnmente están asociados con:
- Adelgazamiento.
- Ataque químico.
- Fluencia o “creep”.
- Erosión.
- Fatiga.
- Fractura.
- Fragilización o “embrittlement”.
- Envejecimiento térmico.
Para comprender los mecanismos de daño es importante analizar la probabilidad de falla, la selección de intervalos, ubicaciones y técnicas de inspección apropiados; la capacidad de tomar decisiones (por ejemplo, modificaciones al proceso, selección de materiales, monitoreo) que puedan eliminar o reducir la probabilidad de un mecanismo de daño específico.
Además, la identificación de los mecanismos de daño y modos de falla creíbles para el equipo incluido en un análisis de riesgo es esencial para la calidad y la efectividad del análisis de riesgo.
Las directrices establecidas permitirán: asegurar un riesgo mínimo previsible sobre la seguridad y la confiabilidad; asegurar la máxima esperanza de vida de los equipos o identificar áreas de aplicaciones de nuevas tecnologías.
Con base en base a lo anterior, algunos de los principales desafíos contra la corrosión son:
- Agrietamiento por corrosión bajo tensión (SCC-Stress Corrosion Cracking): SCC es el agrietamiento inducido por la influencia combinada de la tensión de tracción y un ambiente corrosivo (ver Figura 3).


El impacto de SCC en un material generalmente se encuentra entre el agrietamiento en seco y el umbral de fatiga de dicho material. Los esfuerzos de tracción requeridos pueden estar en forma de esfuerzos aplicados directamente o en forma de esfuerzos residuales.
La deformación y el conformado en frío, la soldadura, el tratamiento térmico, el mecanizado y el esmerilado pueden introducir tensiones residuales. La magnitud y la importancia de tales tensiones a menudo se subestiman.
Las tensiones residuales creadas como resultado de las operaciones de soldadura tienden a aproximarse al límite elástico. La acumulación de productos de corrosión en espacios confinados también puede generar tensiones significativas y no debe pasarse por alto. SCC generalmente ocurre en ciertas combinaciones específicas de aleación-ambiente-esfuerzo.
Por lo general, la mayor parte de la superficie permanece sin atacar, pero con grietas finas que penetran en el material. En la microestructura, estas grietas pueden tener morfología intergranular o transgranular. Macroscópicamente, las fracturas por SCC tienen una apariencia frágil.
El SCC se clasifica como una forma catastrófica de corrosión, ya que la detección de grietas tan finas puede ser muy difícil y el daño no es fácil de predecir.
- Corrosión localizada: puede adoptar muchas formas, como picaduras que dan lugar a numerosas cavidades superficiales, corrosión galvánica selectiva en la región entre dos metales electroquímicamente diferentes, ataque de corrosión selectivo a lo largo de una zona afectada por el calor de soldadura (HAZ-heat affected zone), ataque de corrosión en grietas resultantes de la concentración de especie(s) química(s) agresiva(s), o ranurado local debido al impacto (ver Figura 4).
En general, cuanto más resistente es una aleación a la corrosión general, más probable es que la corrosión, si se produce, sea localizada.

- Erosión-Corrosión: es la aceleración en la tasa de ataque de corrosión en el metal debido al movimiento relativo de un fluido corrosivo y una superficie metálica.
El aumento de la turbulencia causado por las picaduras en las superficies internas de un tubo puede provocar un rápido aumento de las tasas de erosión y, finalmente, una fuga (Ver Figura 5).

Una combinación de erosión y corrosión puede conducir a tasas de picaduras extremadamente altas. La selección de materiales juega un papel importante en la minimización de los daños por erosión y corrosión.
Se debe tener precaución cuando se predice el comportamiento de erosión-corrosión sobre la base de la dureza. Una alta dureza en un material no garantiza necesariamente un alto grado de resistencia a la erosión-corrosión.
Las características de diseño también son particularmente importantes; los diseños que crean turbulencia, restricciones de flujo y obstrucciones son indeseables por lo que deben evitarse los cambios bruscos en la dirección del flujo, en lo posible; y en cuyo caso colocar accesorios que disminuyan su impacto.
- Corrosión bajo el aislamiento (CUI-Corrosion under Insulation): es cualquier tipo de corrosión que ocurre debido a la acumulación de humedad en la superficie externa del equipo aislado, por al menos uno de muchos factores (filtración, falla del aislamiento, condensación, entre otros), siendo la entrada de agua el problema clave en CUI.
La corrosión en sí es más comúnmente corrosión por cloruro, ácida o alcalina. Se debe tener especial cuidado durante el diseño para no promover la corrosión al permitir que el agua ingrese al sistema, ya sea directa o indirectamente por acción capilar. La humedad puede ser externa o puede estar presente en el propio material aislante. La corrosión puede atacar el revestimiento, el material de aislamiento o el equipo propiamente dicho (Ver Figura 6).

Para equipos de alta temperatura, el agua que ingresa a un material aislante y se difunde hacia adentro eventualmente alcanzará una región seca en la tubería caliente o en la pared del equipo. Junto a esta región seca hay una zona en la que los poros del aislamiento están llenos de una solución salina saturada. Cuando ocurre una parada o cambio de proceso y la temperatura de la pared metálica disminuye, la zona de solución salina saturada se mueve hacia la pared metálica.
Al recalentarse, la pared estará temporalmente en contacto con la solución saturada y puede comenzar el agrietamiento por corrosión bajo tensión.
Los ciclos de secado/humectación en los problemas asociados con CUI son un fuerte acelerador del daño por corrosión, ya que provocan la formación de una química cada vez más agresiva que puede conducir a los peores problemas de corrosión posibles, por ejemplo: agrietamiento por corrosión bajo tensión y fallas catastróficas prematuras del equipo.
- Corrosión externa: puede resultar en la reducción gradual del espesor de la pared del equipo o tubería y la consiguiente pérdida de resistencia.
Puede ocurrir de manera relativamente uniforme sobre la superficie de un área (a veces denominada corrosión genera») o en puntos aislados (corrosión localizada) debido a las condiciones ambientales en el exterior del equipo o tubería (Ver Figura 7).

Esta pérdida de resistencia podría provocar fugas o rupturas debido a las presiones internas, a menos que se repare el componente.
Por lo general, la superficie externa del equipo o tubería está recubierta para evitar que el ambiente o suelo circundante u otras condiciones ambientales entren en contacto con el material, evitando así el proceso de oxidación.
- Corrosión general: la corrosión de ataque general avanza más o menos uniformemente sobre una superficie expuesta sin una localización apreciable; lo que conduce a un adelgazamiento relativamente uniforme en los materiales de láminas y placas y un adelgazamiento general en un lado o en el otro (o ambos) para las tuberías. Se reconoce por una rugosidad de la superficie y generalmente por la presencia de productos de corrosión (ver Figura 8).

El mecanismo del ataque típicamente es un proceso electroquímico que tiene lugar en la superficie del material. Las diferencias en composición u orientación entre pequeñas áreas en la superficie del metal crean ánodos y cátodos que facilitan el proceso de corrosión.
La corrosión general es causada con mayor frecuencia por la mala aplicación de materiales en ambientes corrosivos, la corrosión general a menudo se puede tolerar porque el efecto de la pérdida de metal es relativamente fácil de evaluar y se pueden hacer concesiones en el diseño inicial.
Algunas de las estrategias recomendables para el adecuado manejo de la corrosión o métodos de prevención, control y mitigación que deben considerarse, se encuentran:
- Selección de materiales: desde un punto de vista puramente técnico, una respuesta obvia a los problemas de corrosión sería utilizar materiales más resistentes a la corrosión. Siendo en muchos casos, este enfoque, una alternativa económica a otros métodos de control de la corrosión.
La resistencia a la corrosión no es la única propiedad que se debe tener en cuenta al seleccionar los materiales, pero es de gran importancia en las industrias de procesos químicos.
Por ejemplo, el acero al carbono es el material más utilizado; sin embargo, con mayor capacidad y contaminantes, los aceros inoxidables se especifican cada vez más para resistir altas velocidades y ataques agresivos.En todo caso, se deben realizar los análisis de los fluidos a transportar o contener, así como sus contaminantes y condiciones de proceso para su adecuada selección.
- Selección de revestimientos protectores: Los revestimientos se aplican sobre diversas estructuras y equipos operativos externa o internamente para proteger contra la corrosión/erosión, actuar como barreras térmicas, evitar el ensuciamiento, etc.
Los revestimientos pueden ser orgánicos, metálicos, cerámicos o compuestos y se pueden usar como películas de barrera para evitar las picaduras y la corrosión, la erosión y los ataques químicos inducidos por microbios.
Se aplican, externa o internamente en inmersión, enterrados, atmosféricos y bajo aislamientos. Existen diferentes tecnologías de recubrimiento que se pueden especificar y personalizar para adaptarse al propósito además de otras estrategias de manejo de la corrosión. Por ejemplo:
- Se pueden usar recubrimientos epoxi especiales rellenos de cerámica que contienen pigmento antibacteriano para proteger los codos de las tuberías, las cajas del intercambiador y las válvulas internas de la corrosión por MIC (microbiological induce corrosion). Además, el recubrimiento especial para los tubos de los rehervidores aplicados por inundación puede evitar las picaduras y la corrosión debajo de los depósitos.
- Los recubrimientos de encapsulación de óxido o epoxi tolerantes a la superficie se pueden usar durante el trabajo de mantenimiento de la estructura de acero con un alto lavado con agua en lugar de la limpieza con chorro abrasivo.
- Los tipos de revestimiento viscoelástico o epoxi 100 % sólido se utilizan para proteger los desagües enterrados y las tuberías ascendentes de acero para agua contra incendios, debido a corrosión del suelo según la temperatura.
- Los revestimientos de inmersión se utilizan para proteger equipos y tuberías de acero al carbono e inoxidable contra picaduras y agrietamiento por corrosión bajo tensión de cloruro bajo aislamiento térmico y protección contra incendios.
- Se pueden usar tipos de recubrimientos aislantes térmicos de película delgada (40 – 100 mils) con recubrimientos primarios anticorrosión en lugar del aislamiento convencional, para reducir el riesgo de corrosión debajo del aislamiento térmico.
- Se pueden usar recubrimientos epoxi rellenos de cerámica para proteger los codos de las tuberías, las placas de tubos del intercambiador y las válvulas internas de la corrosión y la erosión.
- Monitoreo de la corrosión: el manejo exitoso de la corrosión se obtiene mediante la creación de un historial de resultados de monitoreo y la correlación de esos datos con los resultados reales de pruebas e inspecciones(T&I) o Inspección en marcha.
Los métodos siguientes pueden utilizarse para monitorear el comportamiento de la corrosión:
- Cupones de Corrosión.
- Sondas de Corrosión.
- Pruebas no destructivas (NDT) o en línea (OSI).
- Análisis de laboratorio.
- Análisis de productos de corrosión.
- Recuentos de hierro.
- Recuento de bacterias.
- Análisis de salmueras.
- Composición de los fluidos manejados o transportados.
- Monitoreo de cambios en las variables del proceso; es decir, presión, temperatura y/o flujo.
- Análisis de fallas.
- Inspección visual.
Los cupones de corrosión y las sondas en línea se utilizan a menudo para estudiar la eficacia de los programas de inhibidores de la corrosión o los efectos de los cambios de procesos específicos sobre la corrosión. Sin embargo, no miden con precisión la corrosión localizada (picaduras). Las lecturas se deben usar para crear un indicador de pérdida de índice de corrosión a través de la tendencia de los datos. Siempre que este indicador muestre una tendencia ascendente, el ingeniero de corrosión revisará la inhibición de la corrosión y los parámetros del proceso de las tuberías y el equipo de la planta.
Recientemente, los métodos no intrusivos han mejorado y se han vuelto más confiables para monitorear la corrosión en sistemas donde no se pueden usar técnicas intrusivas, como en ubicaciones de alta velocidad o ubicaciones de alta presión. La mayoría de estas tecnologías se encuentran actualmente en evaluación. Algunas de las siguientes técnicas avanzadas de pruebas no destructivas o NDT pueden ser de utilidad en la inspección progresiva de equipos y tuberías:
- Mapeo de UT automatizado (P-Scan): este método se utiliza para inspeccionar recipientes y tuberías en busca de corrosión, ampollas de hidrógeno y grietas ambientales, en particular para las tuberías.
- Escáner UT avanzado: esta técnica se usa para inspeccionar tuberías y equipos a temperaturas elevadas (550 °F) y se usa para verificar el agrietamiento y la formación de ampollas por pasos.
- Tiempo de Difracción de Vuelo (TOFD): Este sistema se utiliza para detectar y dimensionar metales base y defectos de soldadura (grietas) en recipientes a presión y tuberías.
- Técnicas de Inspección: La inspección normalmente se refiere a la evaluación de la calidad de alguna característica en relación con un estándar o una especificación.
- Equipo: la inspección visual (VT), la medición de el espesor aleatorio por ultrasonido (UT) y la prueba de partículas magnéticas fluorescentes húmedas (WFMPT) se usan comúnmente para verificar la corrosión localizada y el agrietamiento ambiental.
- Tubería: Varias técnicas como espesor ultrasónico aleatorio (UT), onda de corte UT (UTSW) de soldaduras y radiografía (RT) se utilizan para detectar pérdida de metal, corrosión preferencial de soldadura y agrietamiento fino.
Algunas de las recomendaciones para la inspección son:
- Para Interno: Realizar 10% MFL (Magnetic flux leakage) de tubos, 100% VT con medidas de UT aleatorio o 50% VT y UT aleatorio.
- Para Externa: 50% UTT de CML’s (condition monitoring locations); 100% de los CML’s usando UTSW manual, AUT o radiografía.
- Para CUI: 100% inspección visual externa y 100% perfil o radiografía en tiempo real de daño o área sospechosa.
Así mismo, se deben evaluar nuevas tecnologías para obtener mejores resultados debido a las actividades de inspección que se deben realizar, es decir:
- Sistema de monitoreo de erosión-corrosión con abrazadera en línea: El sistema de monitoreo es un dispositivo no intrusivo que permite medir el daño por corrosión o erosión en el sistema de tuberías. Se basa en técnicas acústicas de ondas de cordero guiadas.
El uso del enfoque no intrusivo brindará flexibilidad en la selección de las ubicaciones de monitoreo en áreas congestionadas donde las herramientas necesarias para mantener los dispositivos intrusivos pueden no tener espacio para funcionar.
Se puede mejorar la seguridad y confiabilidad de la planta al identificar y monitorear la pérdida en el espesor de la pared de la tubería. La corrosión detectada por estos dispositivos podría abordarse mediante la implementación de medidas adecuadas de mitigación de la corrosión.
- Recubrimientos protectores: entre los que destacan:
- Recubrimiento aislante térmico: Se aplica como alternativa al aislamiento existente en equipos, tuberías y válvulas.
- Revestimiento de PTFE para tubería/brida de instrumentación: Previene la corrosión por estancamientos y ayuda a un mejor control del proceso.
- Revestimiento de vidrio: Puede ser utilizado en sondas de termopozo de temperatura.
- Recubrimientos cerámicos: Puede ser utilizado para tubos calentadores y refractarios.
- Recubrimiento del tubo del intercambiador de calor: se puede aplicar tanto en la superficie externa como interna de los tubos.
- Prueba de componentes de aislamiento: utiliza el método de corriente de Foucault pulsada para medir el espesor de pared promedio restante bajo el aislamiento de acero al carbono de baja aleación/objeto ferromagnético y analizar su descomposición y es el método más confiable para la detección de corrosión.
Es una técnica excelente para aplicar en objetos que están aislados y también se puede aplicar en objetos que son de difícil acceso o de costo extremo. El rango de aplicación es enorme ya que contribuye a reducir significativamente los costos de inspección. Esta tecnología de corriente de Foucault pulsada es una excelente herramienta en línea para posicionar más trabajos de inspección durante el apagado o los trabajos de mantenimiento periódico.
Cursos recomendados




%252FImagen%252FRAMPREDYC-1730060420837.webp%3Falt%3Dmedia%26token%3D2634a7f0-988e-4022-b91f-382503e6e9db&w=3840&q=75)



Bibliografía
- API-510: “Pressure Vessel Inspection Code: In-Service Inspection, Rating, Repair, and Alteration”.
- API-570: “Piping Inspection Code: In-Service Inspection, Rating, Repair, and Alteration of Piping Systems”.
- API-RP-571: “Damage Mechanisms Affecting Fixed Equipment in Refining Industry”.
- API-RP-572: “Inspection Practices for Pressure Vessels”.
- API-RP-574: “Inspection Practices for Piping System Components”.
- API-RP-580: “Risk-Based Inspection”.
- API-RP-581: “Risk-Based Inspection Technology”.
- ASME PCC-3: “Inspection Planning Using Risk Based Methods”.
Autor

Elimar Anauro Rojas Monsalve
Consultor Senior & Ejecutivo, Asesor Técnico en Procesos, Confiabilidad, Riesgo, Incertidumbre e Integridad
Email: elimar.rojas@gmail.com
Dinos qué te ha parecido el artículo
Artículos recomendados
Estrategias metacognitivas para el análisis de falla en la unidad curricular optimización del mantenimiento del Proyecto Ingeniería de Mantenimiento Mecánico de la UNERMB.

Comprendiendo las economías de escala

Mantenimiento Tercerizado - Beneficios y Consideraciones

La sensibilización de la seguridad en las operaciones

Publica tu artículo en la revista #1 de Mantenimiento Industrial
Publicar un artículo en la revista es gratis, no tiene costo.
Solo debes asegurarte que no sea un artículo comercial.
¿Qué esperas?
O envía tu artículo directo: articulos@predictiva21.com
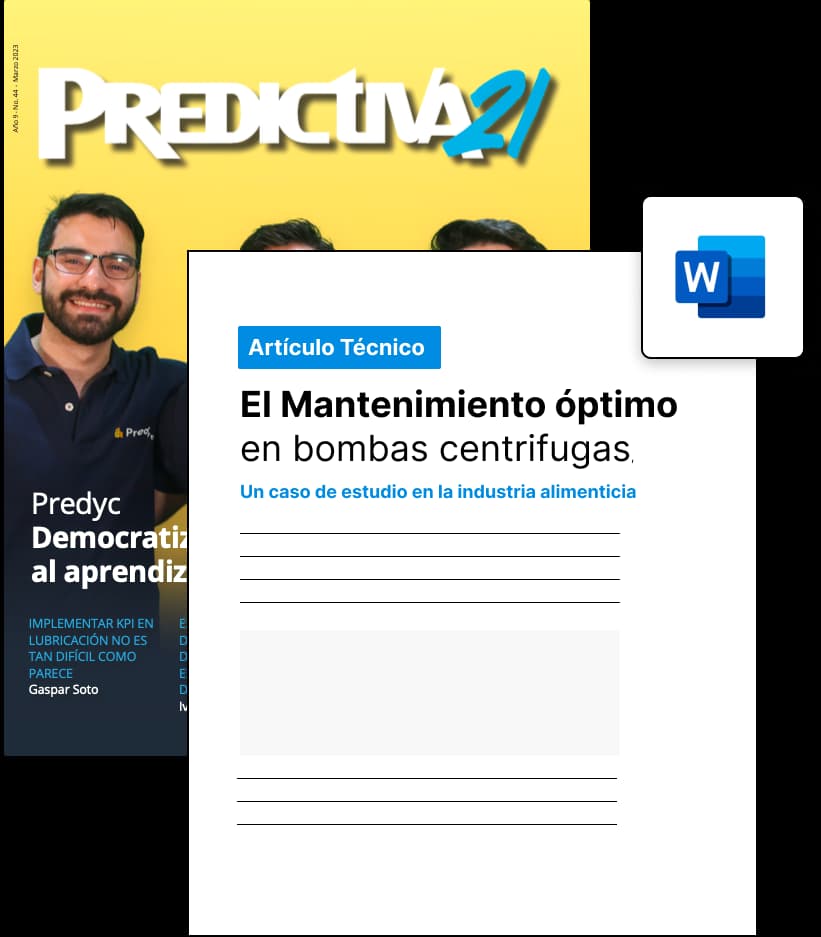