Madurez del Mantenimiento
Articulo5 de enero de 2025
Introducción
En las auditorías administrativas se evalúan, junto al personal de nivel de gestión de la propia empresa, sus condiciones funcionales y administrativas utilizando técnicas sencillas para la identificación de puntos donde puedan aplicarse acciones de mejora.Una de estas técnicas es la evaluación del grado de madurez de la empresa, desarrollado por Du Pont (1990) y perfeccionado por McKinsey (1995) y Topkins (2000).En esta técnica se establecen varios pilares, cada uno con varios niveles, donde dos gestores posicionan, según su juicio, la condición en que se encuentra su empresa.
Propuesta Du Pont
En la propuesta original de Du Pont se establecen 3 pilares:
- Características de una organización de mantenimiento;
- Prácticas y métodos típicos usados por las organizaciones de mantenimiento;
- Medidas de desempeño que tipifican una organización.
Para cada pilar se propone evaluar 3 niveles:
- Personas y Organización (Estructura, Formación, Supervisión, Apoyo, Administración, Sindicato, Terceros);
- Sistemas (Planificación, Sistema de gestión, Capacitación);
- Filosofías (Materiales, Misión, Metas, Expectativas de desempeño, Proyectos esenciales).
La propuesta de Du Pont, a la que siguieron las de McKinsey y Topkins, es que los directivos evalúen el grado de madurez de la empresa en la que trabajan, asignando una calificación (del 1 al 10) para cada pilar según su punto de vista. Para cada uno, también se asigna una calificación del 1 al 10. Es decir, cada pilar tendría su número de evaluación multiplicado por los números de evaluación de cada nivel, lo que daría, para cada evaluador, un mínimo total de 3 puntos (producto de 1 por el pilar por 1 por cada nivel) hasta 300, obteniéndose este valor máximo sumando los valores de los productos de los pilares con los tres niveles respectivos.Dado que el evaluador estaría asignando sus puntos a los tres pilares, su valor máximo general para la empresa sería de 900 puntos.
Por ejemplo: Si un evaluador asignara al pilar 1 una calificación de 8 y para los tres niveles de este pilar los valores de 9, 6 y 9, tendríamos un resultado de 8x9 + 8x6 + 8x9 para este pilar, totalizando 192 puntos. El mismo criterio se aplicaría a los pilares 2 y 3, donde, por ejemplo, el evaluador obtuvo totales de 161 y 180. Por lo tanto, este evaluador estaría obteniendo un total de 533 puntos. Se observa que, en este caso, el evaluador obtuvo una puntuación cercana al 59% del valor máximo, lo que puede considerarse razonable. Tomando las medias de otros tres evaluadores, por ejemplo 580, 605 y 701 puntos, tendríamos una visión de la madurez de esta empresa, que resaltaría los aspectos que es necesario mejorar, dentro de los recursos disponibles (financieros, logísticos, operativos, técnicos, estratégicos, etc.).
Propuesta McKinsey
En la propuesta de McKinsey se establece 12 pilares:
- Características de una organización de mantenimiento.
- Definición y selección de estrategias de mantenimiento (predictivo, preventivo, correctivo).
- Planificación del mantenimiento preventivo.
- Aplicación del mantenimiento predictivo.
- Mantenimiento correctivo.
- Control de resultados.
- Cultura de desempeño.
- Definición de la estrategia de reparaciones con recursos propios vs. Terceros.
- Equipo técnico - Plan de desarrollo del equipo.
- Gestión del equipo de terceros.
- Gestión de suministros - Control de stock.
- Gestión de suministros - Disponibilidad de repuestos.
Para cada pilar se establecen 5 niveles de elección:
- Débil
- Abajo del promedio
- Satisfactorio
- Arriba del promedio
- Clase mundial
Pilar 01 - Evaluación y segmentación de posibles fallas
- Débil: No hay análisis cuantitativo de fallas históricas;
- Abajo del Promedio: Hay un análisis de frecuencia de fallas de forma consolidada para la planta, que subsidia las estrategias de mantenimiento;
- Satisfactorio: Hay un análisis detallado de las posibles fallas por equipo con estimativas de impacto de downtime y pérdida de producción;
- Arriba del Promedio: Además de detallado por máquina y componentes, el análisis considera el grado de previsibilidad y frecuencia de las fallas;
- Clase Mundial: Criterio anterior + los análisis detallados son revisados y realimentan la estrategia de mantenimiento de la planta.
Pilar 02 - Definición y selección de estrategias de mantenimiento (predictivo, preventivo, correctivo)
- Débil: No hay análisis económico para la definición de la estrategia de mantenimiento;
- Abajo del Promedio: Hay una estimativa simple de los costos de suministro de reposición y de mano de obra con cada una de las estrategias;
- Satisfactorio: Hay un análisis detallado del impacto de la posible estrategia de mantenimiento en la probabilidad y en la frecuencia de falla. También hay comprensión de TCO (Total Cost of Ownership) de cada estrategia;
- Arriba del Promedio: Criterio anterior + Hay un análisis detallado de costos del impacto de las posibles estrategias de mantenimiento, considerando frecuencias de fallas, costos hora/máquina, tiempo de corrección y utilización del equipo;
- Clase Mundial: Criterio anterior + Hay una total integración entre los análisis de las posibles estrategias de mantenimiento y las definiciones de CAPEX para la planta, con foco en creación de valor.
Pilar 03 - Planificación del mantenimiento preventivo
- Débil: El planeamiento no posee un estándar definido;
- Abajo del Promedio: El planeamiento incluye la descripción general del trabajo y los materiales;
- Satisfactorio: El planeamiento incluye la descripción general del trabajo, los materiales y el número de horas de técnicos involucrados;
- Arriba del Promedio: El planeamiento incluye la descripción general del trabajo, los materiales, el número de horas de técnicos y el horario para inicio y finalización;
- Clase Mundial: Criterio anterior + Acompañamiento de la curva de aprendizaje (reducción de tiempo y costo). Integración entre predictiva y correctiva con intercambio de datos históricos y análisis.
Pilar 04 - Aplicación del mantenimiento predictivo
- Débil: No hay mantenimiento predictivo;
- Abajo del Promedio: Hay mantenimiento predictivo, pero solo en situaciones visibles de problemas en el funcionamiento;
- Satisfactorio: Hay mantenimiento predictivo para las partes/equipos de fácil identificación y previsibilidad de problemas. Hay análisis estadísticos de fallas;
- Arriba del Promedio: Criterio anterior + Se utilizan herramientas sofisticadas para procesamiento de señales (térmicos, vibratorios, eléctricos, etc.) recolectadas periódicamente;
- Clase Mundial: Criterio anterior + Las señales se recolectan en tiempo real. Acompañamiento de la curva de aprendizaje (reducción de tiempo y costo). Integración entre predictivo y correctivo con intercambio de datos históricos y análisis.
Pilar 05 - Mantenimiento Correctivo
- Débil: La identificación del problema se hace de forma empírica después de la rotura, sin apoyo de la ingeniería. Los operadores no están involucrados en el proceso;
- Abajo del Promedio: Hay un previo estudio de las principales fallas posibles y el proceso de acción sobre esas fallas se mantiene informal. Los operadores no están involucrados en el proceso;
- Satisfactorio: Hay una previsión de las fallas de mayor impacto y probabilidad, y un plan de acción detallado para el abordaje. Los operadores son capaces de realizar pequeñas reparaciones;
- Arriba del Promedio: Criterio anterior + Alto grado de participación de la ingeniería de mantenimiento y de procesos en la identificación de los problemas y en el plan de acción. Los operadores son capaces de prever problemas mayores;
- Clase Mundial: Criterio anterior + Acompañamiento de la curva de aprendizaje (reducción de tiempos y costos). Integración entre predictivo y correctivo con intercambio de datos históricos y análisis.
Pilar 06 - Control de Resultados
- Débil: No hay control de costos ni de tiempo;
- Abajo del Promedio: Hay controles rudimentarios de los principales centros de costos y del tiempo total de parada para actividades de mantenimiento;
- Satisfactorio: Hay controles para todos los costos de mantenimiento y el tiempo gastado en el desempeño de funciones de mantenimiento;
- Arriba del Promedio: Hay controles para todos los costos de mantenimiento, incluidos los costos de pérdida de ingresos y el tiempo gastado en las funciones. Estos controles son utilizados para benchmarking interno;
- Clase Mundial: Los controles son utilizados para imponer metas de mejora continua de tiempo y costo en todos los procesos.
Pilar 07 - Cultura de Desempeño
- Débil: No hay metas de desempeño específicas. Los equipos interfuncionales (Operación y Mantenimiento) tienen poca o ninguna participación en la resolución de problemas;
- Abajo del Promedio: Hay metas, pero no son monitoreadas ni seguidas. Los equipos interfuncionales (mantenimiento y operación) se usan muy raramente;
- Satisfactorio: Hay metas y son monitoreadas, pero poco divulgadas. La responsabilidad por las metas es informal. Los equipos interfuncionales están institucionalizados, pero no logran resultados en la creación de mejores prácticas;
- Arriba del Promedio: Las metas son monitoreadas y divulgadas, pero no existe una cultura de desempeño. Los equipos interfuncionales tienen un alto impacto con ideas generadas por la alta gerencia;
- Clase Mundial: Las metas son monitoreadas, divulgadas y sirven de base para la remuneración variable. Los equipos interfuncionales aportan ideas de mejora a la alta gestión y generan un alto impacto en los cambios.
Pilar 08 - Definición de la estrategia de reparaciones con recursos propios vs. terceros
- Débil: Todos los reparos se hacen internamente, sin análisis crítico;
- Abajo del Promedio: Algunas reparaciones se hacen por terceros, pero no hay un proceso claro de decisión;
- Satisfactorio: Hay un proceso de decisión que toma en cuenta el impacto potencial de reducción de costo con materiales y mano de obra;
- Arriba del Promedio: Criterio anterior + Hay un proceso de decisión que considera el nivel de servicio (grado de habilidad de los terceros vs. el equipo interno) y posibles sinergias o beneficios estratégicos de no tercerizar;
- Clase Mundial: Criterio anterior + Las decisiones de tercerización o no de funciones de mantenimiento son revisadas periódicamente para todos los equipos.
Pilar 09 - Equipo técnico - Plan de desarrollo del equipo
- Débil: No hay un plan de desarrollo definido;
- Abajo del Promedio: Hay un plan de desarrollo, pero las atribuciones y calificaciones en cada nivel no son claras;
- Satisfactorio: Hay una visión clara de las calificaciones necesarias por función en cada nivel, sin embargo, el sistema de evaluación de desempeño y retroalimentación es informal y de bajo impacto;
- Arriba del Promedio: Criterio anterior + Hay gran armonía entre los sistemas de evaluación de desempeño/retroalimentación y el plan de desarrollo/funciones;
- Clase Mundial: Criterio anterior + Los atributos y calificaciones necesarios son constantemente reevaluados según cambios tecnológicos o estratégicos.
Pilar 10 - Gestión del equipo de terceros
- Débil: No hay tercerización de funciones de mantenimiento;
- Abajo del Promedio: No hay monitoreo ni evaluación del prestador de servicios;
- Satisfactorio: El prestador de servicios es evaluado de manera informal o en grandes tareas;
- Arriba del Promedio: La mayor parte de los trabajos son acompañados. El prestador de servicios es evaluado según calidad, cumplimiento de plazos y tareas propuestas;
- Clase Mundial: Todos los trabajos son evaluados (o por lo menos de forma estadística). El pago de los servicios está directamente ligado al desempeño, plazos y desarrollo de las tareas. Hay un esfuerzo de mejora continua junto a los proveedores.
Cursos recomendados


%252FImagen%252FRAMPREDYC-1730060420837.webp%3Falt%3Dmedia%26token%3D2634a7f0-988e-4022-b91f-382503e6e9db&w=3840&q=75)





Pilar 11 - Gestión de Suministros - Control de Stock
- Débil: No hay control formal de ítems de mantenimiento. Hay muchas piezas para equipos ya desactivados. No existen intenciones de desarrollo de contratos de suministro;
- Abajo del Promedio: El control de ítems está constantemente desactualizado. Niveles mínimos y máximos de stock no son definidos. Se desarrollan contratos de suministro sin un plan preestablecido;
- Satisfactorio: Control de stock actualizado para algunos ítems. Niveles mínimos y máximos establecidos para algunos ítems. Existe un plan de desarrollo de contratos de suministro;
- Arriba del Promedio: Control de ítems actualizado para la mayoría de los ítems. Niveles mínimos y máximos establecidos para la mayoría de los ítems. Ítem anterior + 50% de los ítems de stock evaluados con base en el riesgo/frecuencia;
- Clase Mundial: Control de ítems actualizado para todos los ítems. Niveles mínimos y máximos establecidos para todos los ítems. Ítem anterior + 100% de los ítems de stock evaluados con base en el riesgo/frecuencia.
Pilar 12 - Gestión de Suministros - Disponibilidad de repuestos
- Débil: No hay una metodología para la ubicación de las piezas. Menos del 30% de las piezas están disponibles en una primera tentativa. No existe acondicionamiento adecuado. Menos del 30% de las piezas son inspeccionadas o tienen calidad asegurada;
- Abajo del Promedio: Hay diversas metodologías no integradas de búsqueda de piezas. El 30-50% de las piezas están disponibles en la primera búsqueda. Acondicionadas de forma adecuada. El 30-50% de las piezas son inspeccionadas o tienen calidad asegurada;
- Satisfactorio: Hay una metodología única de búsqueda de piezas, pero es poco amigable y de poca confianza. El 50-75% de las piezas están disponibles en la primera búsqueda. Acondicionadas de forma adecuada. El 50-75% de las piezas son inspeccionadas o tienen calidad asegurada;
- Arriba del Promedio: La metodología de búsqueda de piezas tiene un alto grado de confianza, pero es difícil de utilizar. El 75-90% de las piezas están disponibles en la primera búsqueda. Acondicionadas de forma adecuada y 50-75% de los casos entregados en el área. El 75-90% de las piezas son inspeccionadas o tienen calidad asegurada;
- Clase Mundial: La herramienta de búsqueda es fácil de usar y muy confiable. El 95-100% de las piezas están disponibles en la primera búsqueda. Acondicionadas de forma adecuada y más del 75% entregadas en el área. El 100% de las piezas tienen calidad asegurada.
A continuación, el promedio de la aplicación del método en más de 50 empresas:

Propuesta de Topkins
En la propuesta de Topkins se encuentran 7 pilares:
- Actitud de la gestión corporativa de la planta
- Estado organizacional del mantenimiento
- Porcentaje de pérdida de recursos debido al mantenimiento
- Solución de problemas de mantenimiento
- Calificación/entrenamiento del personal de mantenimiento
- Información de mantenimiento y desarrollo de acciones
- Resumen de la posición del mantenimiento en la compañía
Pilar 1 - Actitud de la gestión corporativa de la planta
- Inconsciente: No comprende lo que es mantenimiento preventivo, se repara solo cuando se rompe.
- Despertando: Reconoce que el mantenimiento puede ser mejorado, pero se siente incapaz de implementar cambios.
- Desarrollando: Aprende sobre ROI (retorno de inversión), desarrolla mayor interés y seguridad en mejorar el mantenimiento.
- Capacitado: Actitud participativa, reconoce que la gestión de mantenimiento es esencial y debe ser mandataria.
- Consciente: Integra el mantenimiento como una parte fundamental del sistema global de la compañía.
Pilar 2 - Estado organizacional del mantenimiento
- Inconsciente: Reactivo, trabaja en el equipo solo cuando falla; baja productividad del personal.
- Despertando: Aún reactivo, pero logra mejores recuperaciones de componentes y tiene repuestos disponibles cuando ocurre una falla.
- Desarrollando: Preventivo, realiza rutinas de inspección, lubricación, ajustes y pequeños servicios para mejorar el MTBF (tiempo medio entre fallas).
- Capacitado: Predictivo, utiliza técnicas como análisis de vibración, termografía, ultrasonido, etc., para monitorear la condición de los equipos y anticipar problemas.
- Consciente: Productivo, combina técnicas predictivas con la participación activa de los operadores para liberar a los técnicos de mantenimiento, mejorando la mantenibilidad.
Pilar 3 - Porcentual pérdida de recursos debido al mantenimiento
- Inconsciente: Más del 30%.
- Despertando: Entre 20% y 30%.
- Desarrollando: Entre 10% y 20%.
- Capacitado: Entre 5% y 10%.
- Consciente: Menos del 5%.
Pilar 4 - Solución de problemas de mantenimiento
- Inconsciente: Los problemas se desarrollan hasta que son descubiertos.
- Despertando: Se elaboran algunas acciones básicas. Comienza el análisis de fallas de manera elemental.
- Desarrollando: Los problemas se resuelven mediante la implementación de acciones de mantenimiento e ingeniería.
- Capacitado: Los problemas son anticipados. Se utiliza un fuerte equipo interdisciplinario de solución de problemas.
- Consciente: Los problemas son prevenidos.
Pilar 5 - Calificación/entrenamiento del personal de mantenimiento
- Inconsciente: Baja calidad de mano de obra, supervisión rígida, conocimientos obsoletos, pagos por antigüedad.
- Despertando: El personal siente que falta conocimiento para analizar fallas y comienza a cuestionar la especialización. Se reconoce la necesidad de capacitación.
- Desarrollando: Calidad en el trabajo. Se distribuye el desempeño de tareas, inversión en investigación, pagos por capacidad para resolver problemas.
- Capacitado: Expectativa de calidad en el trabajo. Realización de tareas por "multiespecialistas", conocimiento actualizado.
- Consciente: Orgullo y profesionalismo. Flexibilidad en la designación de tareas. Capacitación constante de los operadores por los mantenedores. Pago basado en la productividad de la planta.
Pilar 6 - Información de mantenimiento y desarrollo de acciones
- Inconsciente: El mantenimiento intenta realizar registros, pero la disciplina no es exigida y los datos son deficientes.
- Despertando: Se utiliza una orden de trabajo manual o computarizada, pero la planificación y programación son escasas o nulas.
- Desarrollando: Se utiliza una orden de trabajo manual o computarizada por mantenimiento, operación e ingeniería, con planificación e implementación de programación de servicios.
- Capacitado: Se utiliza un sistema de control de mantenimiento para todas las áreas de la compañía, con información disponible y consistente.
- Consciente: El sistema de información de mantenimiento está integrado con el sistema de información corporativo.
Pilar 7 - Resumen de la posición del mantenimiento en la compañía
- Inconsciente: “No sabemos cuál equipo se va a romper y por eso pagamos al mantenimiento. Las tasas de pérdidas son altas, pero no es un problema de mantenimiento.”
- Despertando: “¿Acaso nuestros competidores tienen estos problemas con sus equipos? ¡Las refacciones nos están costando mucho!”
- Desarrollando: “Con el nuevo criterio de gestión, empezamos a identificar y resolver los problemas.”
- Capacitado: “Todos reconocen que el mantenimiento es parte de nuestra rutina de calidad operacional. No podemos hacer productos de calidad con un mantenimiento deficiente.”
- Consciente: “No esperamos fallas y es una sorpresa cuando ocurren. ¡El mantenimiento contribuye para mantenernos entre los mejores!”
A continuación, se presenta el promedio de la aplicación del método en más de 100 empresas:

Conclusión
Lo importante de las Técnicas McKinsey y Topkins es que detallan la información de cada nivel en cada pilar.
Dado que estos métodos se aplican a directivos de los niveles operativo, ejecutivo y estratégico, esta información facilita la comprensión de sus posiciones, según el punto de vista de cada uno, sobre la situación de la empresa.
Al final de la evaluación de los directivos, se obtiene un valor promedio que es analizado por un grupo designado por la empresa para valorar la posibilidad de mejorar los niveles obtenidos.
Dinos qué te ha parecido el artículo
Artículos recomendados
Lourival Tavares, pasión por el Mantenimiento

Gestión de Mantenimiento: 7 KPIs imprescindibles

¿Quién debe planificar los trabajos de Mantenimiento?

Cálculo de reducción de costos por filtración de aceites

Publica tu artículo en la revista #1 de Mantenimiento Industrial
Publicar un artículo en la revista es gratis, no tiene costo.
Solo debes asegurarte que no sea un artículo comercial.
¿Qué esperas?
O envía tu artículo directo: articulos@predictiva21.com
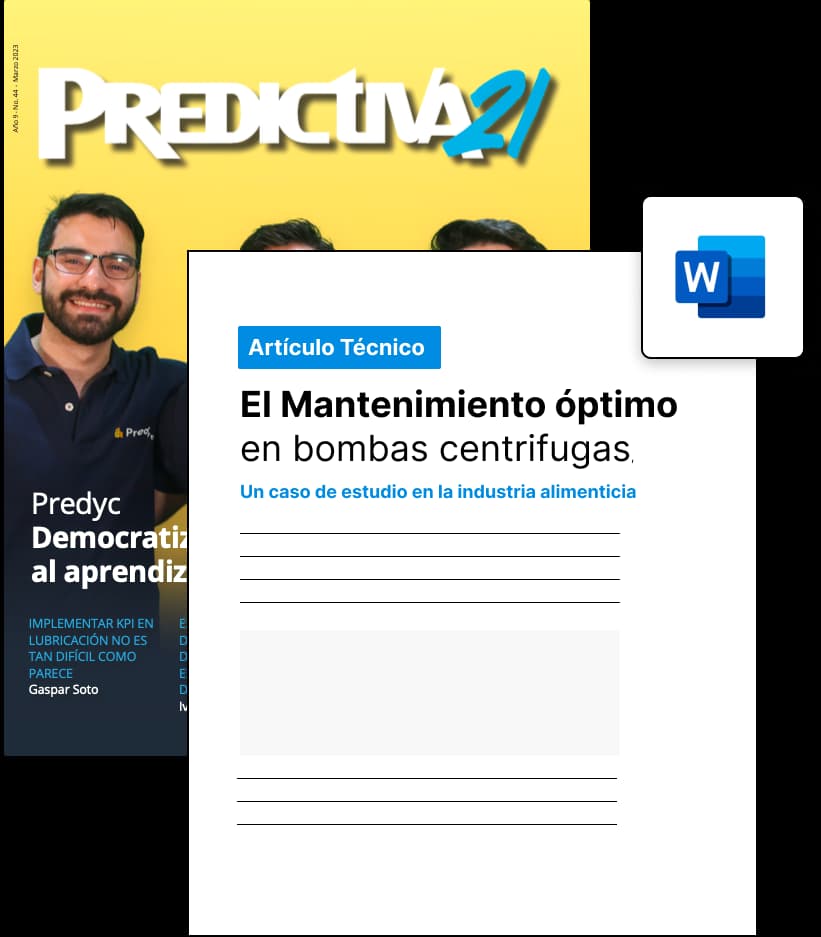
Introducción
En las auditorías administrativas se evalúan, junto al personal de nivel de gestión de la propia empresa, sus condiciones funcionales y administrativas utilizando técnicas sencillas para la identificación de puntos donde puedan aplicarse acciones de mejora.Una de estas técnicas es la evaluación del grado de madurez de la empresa, desarrollado por Du Pont (1990) y perfeccionado por McKinsey (1995) y Topkins (2000).En esta técnica se establecen varios pilares, cada uno con varios niveles, donde dos gestores posicionan, según su juicio, la condición en que se encuentra su empresa.
Propuesta Du Pont
En la propuesta original de Du Pont se establecen 3 pilares:
- Características de una organización de mantenimiento;
- Prácticas y métodos típicos usados por las organizaciones de mantenimiento;
- Medidas de desempeño que tipifican una organización.
Para cada pilar se propone evaluar 3 niveles:
- Personas y Organización (Estructura, Formación, Supervisión, Apoyo, Administración, Sindicato, Terceros);
- Sistemas (Planificación, Sistema de gestión, Capacitación);
- Filosofías (Materiales, Misión, Metas, Expectativas de desempeño, Proyectos esenciales).
La propuesta de Du Pont, a la que siguieron las de McKinsey y Topkins, es que los directivos evalúen el grado de madurez de la empresa en la que trabajan, asignando una calificación (del 1 al 10) para cada pilar según su punto de vista. Para cada uno, también se asigna una calificación del 1 al 10. Es decir, cada pilar tendría su número de evaluación multiplicado por los números de evaluación de cada nivel, lo que daría, para cada evaluador, un mínimo total de 3 puntos (producto de 1 por el pilar por 1 por cada nivel) hasta 300, obteniéndose este valor máximo sumando los valores de los productos de los pilares con los tres niveles respectivos.Dado que el evaluador estaría asignando sus puntos a los tres pilares, su valor máximo general para la empresa sería de 900 puntos.
Por ejemplo: Si un evaluador asignara al pilar 1 una calificación de 8 y para los tres niveles de este pilar los valores de 9, 6 y 9, tendríamos un resultado de 8x9 + 8x6 + 8x9 para este pilar, totalizando 192 puntos. El mismo criterio se aplicaría a los pilares 2 y 3, donde, por ejemplo, el evaluador obtuvo totales de 161 y 180. Por lo tanto, este evaluador estaría obteniendo un total de 533 puntos. Se observa que, en este caso, el evaluador obtuvo una puntuación cercana al 59% del valor máximo, lo que puede considerarse razonable. Tomando las medias de otros tres evaluadores, por ejemplo 580, 605 y 701 puntos, tendríamos una visión de la madurez de esta empresa, que resaltaría los aspectos que es necesario mejorar, dentro de los recursos disponibles (financieros, logísticos, operativos, técnicos, estratégicos, etc.).
Propuesta McKinsey
En la propuesta de McKinsey se establece 12 pilares:
- Características de una organización de mantenimiento.
- Definición y selección de estrategias de mantenimiento (predictivo, preventivo, correctivo).
- Planificación del mantenimiento preventivo.
- Aplicación del mantenimiento predictivo.
- Mantenimiento correctivo.
- Control de resultados.
- Cultura de desempeño.
- Definición de la estrategia de reparaciones con recursos propios vs. Terceros.
- Equipo técnico - Plan de desarrollo del equipo.
- Gestión del equipo de terceros.
- Gestión de suministros - Control de stock.
- Gestión de suministros - Disponibilidad de repuestos.
Para cada pilar se establecen 5 niveles de elección:
- Débil
- Abajo del promedio
- Satisfactorio
- Arriba del promedio
- Clase mundial
Pilar 01 - Evaluación y segmentación de posibles fallas
- Débil: No hay análisis cuantitativo de fallas históricas;
- Abajo del Promedio: Hay un análisis de frecuencia de fallas de forma consolidada para la planta, que subsidia las estrategias de mantenimiento;
- Satisfactorio: Hay un análisis detallado de las posibles fallas por equipo con estimativas de impacto de downtime y pérdida de producción;
- Arriba del Promedio: Además de detallado por máquina y componentes, el análisis considera el grado de previsibilidad y frecuencia de las fallas;
- Clase Mundial: Criterio anterior + los análisis detallados son revisados y realimentan la estrategia de mantenimiento de la planta.
Pilar 02 - Definición y selección de estrategias de mantenimiento (predictivo, preventivo, correctivo)
- Débil: No hay análisis económico para la definición de la estrategia de mantenimiento;
- Abajo del Promedio: Hay una estimativa simple de los costos de suministro de reposición y de mano de obra con cada una de las estrategias;
- Satisfactorio: Hay un análisis detallado del impacto de la posible estrategia de mantenimiento en la probabilidad y en la frecuencia de falla. También hay comprensión de TCO (Total Cost of Ownership) de cada estrategia;
- Arriba del Promedio: Criterio anterior + Hay un análisis detallado de costos del impacto de las posibles estrategias de mantenimiento, considerando frecuencias de fallas, costos hora/máquina, tiempo de corrección y utilización del equipo;
- Clase Mundial: Criterio anterior + Hay una total integración entre los análisis de las posibles estrategias de mantenimiento y las definiciones de CAPEX para la planta, con foco en creación de valor.
Pilar 03 - Planificación del mantenimiento preventivo
- Débil: El planeamiento no posee un estándar definido;
- Abajo del Promedio: El planeamiento incluye la descripción general del trabajo y los materiales;
- Satisfactorio: El planeamiento incluye la descripción general del trabajo, los materiales y el número de horas de técnicos involucrados;
- Arriba del Promedio: El planeamiento incluye la descripción general del trabajo, los materiales, el número de horas de técnicos y el horario para inicio y finalización;
- Clase Mundial: Criterio anterior + Acompañamiento de la curva de aprendizaje (reducción de tiempo y costo). Integración entre predictiva y correctiva con intercambio de datos históricos y análisis.
Pilar 04 - Aplicación del mantenimiento predictivo
- Débil: No hay mantenimiento predictivo;
- Abajo del Promedio: Hay mantenimiento predictivo, pero solo en situaciones visibles de problemas en el funcionamiento;
- Satisfactorio: Hay mantenimiento predictivo para las partes/equipos de fácil identificación y previsibilidad de problemas. Hay análisis estadísticos de fallas;
- Arriba del Promedio: Criterio anterior + Se utilizan herramientas sofisticadas para procesamiento de señales (térmicos, vibratorios, eléctricos, etc.) recolectadas periódicamente;
- Clase Mundial: Criterio anterior + Las señales se recolectan en tiempo real. Acompañamiento de la curva de aprendizaje (reducción de tiempo y costo). Integración entre predictivo y correctivo con intercambio de datos históricos y análisis.
Pilar 05 - Mantenimiento Correctivo
- Débil: La identificación del problema se hace de forma empírica después de la rotura, sin apoyo de la ingeniería. Los operadores no están involucrados en el proceso;
- Abajo del Promedio: Hay un previo estudio de las principales fallas posibles y el proceso de acción sobre esas fallas se mantiene informal. Los operadores no están involucrados en el proceso;
- Satisfactorio: Hay una previsión de las fallas de mayor impacto y probabilidad, y un plan de acción detallado para el abordaje. Los operadores son capaces de realizar pequeñas reparaciones;
- Arriba del Promedio: Criterio anterior + Alto grado de participación de la ingeniería de mantenimiento y de procesos en la identificación de los problemas y en el plan de acción. Los operadores son capaces de prever problemas mayores;
- Clase Mundial: Criterio anterior + Acompañamiento de la curva de aprendizaje (reducción de tiempos y costos). Integración entre predictivo y correctivo con intercambio de datos históricos y análisis.
Pilar 06 - Control de Resultados
- Débil: No hay control de costos ni de tiempo;
- Abajo del Promedio: Hay controles rudimentarios de los principales centros de costos y del tiempo total de parada para actividades de mantenimiento;
- Satisfactorio: Hay controles para todos los costos de mantenimiento y el tiempo gastado en el desempeño de funciones de mantenimiento;
- Arriba del Promedio: Hay controles para todos los costos de mantenimiento, incluidos los costos de pérdida de ingresos y el tiempo gastado en las funciones. Estos controles son utilizados para benchmarking interno;
- Clase Mundial: Los controles son utilizados para imponer metas de mejora continua de tiempo y costo en todos los procesos.
Pilar 07 - Cultura de Desempeño
- Débil: No hay metas de desempeño específicas. Los equipos interfuncionales (Operación y Mantenimiento) tienen poca o ninguna participación en la resolución de problemas;
- Abajo del Promedio: Hay metas, pero no son monitoreadas ni seguidas. Los equipos interfuncionales (mantenimiento y operación) se usan muy raramente;
- Satisfactorio: Hay metas y son monitoreadas, pero poco divulgadas. La responsabilidad por las metas es informal. Los equipos interfuncionales están institucionalizados, pero no logran resultados en la creación de mejores prácticas;
- Arriba del Promedio: Las metas son monitoreadas y divulgadas, pero no existe una cultura de desempeño. Los equipos interfuncionales tienen un alto impacto con ideas generadas por la alta gerencia;
- Clase Mundial: Las metas son monitoreadas, divulgadas y sirven de base para la remuneración variable. Los equipos interfuncionales aportan ideas de mejora a la alta gestión y generan un alto impacto en los cambios.
Pilar 08 - Definición de la estrategia de reparaciones con recursos propios vs. terceros
- Débil: Todos los reparos se hacen internamente, sin análisis crítico;
- Abajo del Promedio: Algunas reparaciones se hacen por terceros, pero no hay un proceso claro de decisión;
- Satisfactorio: Hay un proceso de decisión que toma en cuenta el impacto potencial de reducción de costo con materiales y mano de obra;
- Arriba del Promedio: Criterio anterior + Hay un proceso de decisión que considera el nivel de servicio (grado de habilidad de los terceros vs. el equipo interno) y posibles sinergias o beneficios estratégicos de no tercerizar;
- Clase Mundial: Criterio anterior + Las decisiones de tercerización o no de funciones de mantenimiento son revisadas periódicamente para todos los equipos.
Pilar 09 - Equipo técnico - Plan de desarrollo del equipo
- Débil: No hay un plan de desarrollo definido;
- Abajo del Promedio: Hay un plan de desarrollo, pero las atribuciones y calificaciones en cada nivel no son claras;
- Satisfactorio: Hay una visión clara de las calificaciones necesarias por función en cada nivel, sin embargo, el sistema de evaluación de desempeño y retroalimentación es informal y de bajo impacto;
- Arriba del Promedio: Criterio anterior + Hay gran armonía entre los sistemas de evaluación de desempeño/retroalimentación y el plan de desarrollo/funciones;
- Clase Mundial: Criterio anterior + Los atributos y calificaciones necesarios son constantemente reevaluados según cambios tecnológicos o estratégicos.
Pilar 10 - Gestión del equipo de terceros
- Débil: No hay tercerización de funciones de mantenimiento;
- Abajo del Promedio: No hay monitoreo ni evaluación del prestador de servicios;
- Satisfactorio: El prestador de servicios es evaluado de manera informal o en grandes tareas;
- Arriba del Promedio: La mayor parte de los trabajos son acompañados. El prestador de servicios es evaluado según calidad, cumplimiento de plazos y tareas propuestas;
- Clase Mundial: Todos los trabajos son evaluados (o por lo menos de forma estadística). El pago de los servicios está directamente ligado al desempeño, plazos y desarrollo de las tareas. Hay un esfuerzo de mejora continua junto a los proveedores.
Cursos recomendados


%252FImagen%252FRAMPREDYC-1730060420837.webp%3Falt%3Dmedia%26token%3D2634a7f0-988e-4022-b91f-382503e6e9db&w=3840&q=75)





Pilar 11 - Gestión de Suministros - Control de Stock
- Débil: No hay control formal de ítems de mantenimiento. Hay muchas piezas para equipos ya desactivados. No existen intenciones de desarrollo de contratos de suministro;
- Abajo del Promedio: El control de ítems está constantemente desactualizado. Niveles mínimos y máximos de stock no son definidos. Se desarrollan contratos de suministro sin un plan preestablecido;
- Satisfactorio: Control de stock actualizado para algunos ítems. Niveles mínimos y máximos establecidos para algunos ítems. Existe un plan de desarrollo de contratos de suministro;
- Arriba del Promedio: Control de ítems actualizado para la mayoría de los ítems. Niveles mínimos y máximos establecidos para la mayoría de los ítems. Ítem anterior + 50% de los ítems de stock evaluados con base en el riesgo/frecuencia;
- Clase Mundial: Control de ítems actualizado para todos los ítems. Niveles mínimos y máximos establecidos para todos los ítems. Ítem anterior + 100% de los ítems de stock evaluados con base en el riesgo/frecuencia.
Pilar 12 - Gestión de Suministros - Disponibilidad de repuestos
- Débil: No hay una metodología para la ubicación de las piezas. Menos del 30% de las piezas están disponibles en una primera tentativa. No existe acondicionamiento adecuado. Menos del 30% de las piezas son inspeccionadas o tienen calidad asegurada;
- Abajo del Promedio: Hay diversas metodologías no integradas de búsqueda de piezas. El 30-50% de las piezas están disponibles en la primera búsqueda. Acondicionadas de forma adecuada. El 30-50% de las piezas son inspeccionadas o tienen calidad asegurada;
- Satisfactorio: Hay una metodología única de búsqueda de piezas, pero es poco amigable y de poca confianza. El 50-75% de las piezas están disponibles en la primera búsqueda. Acondicionadas de forma adecuada. El 50-75% de las piezas son inspeccionadas o tienen calidad asegurada;
- Arriba del Promedio: La metodología de búsqueda de piezas tiene un alto grado de confianza, pero es difícil de utilizar. El 75-90% de las piezas están disponibles en la primera búsqueda. Acondicionadas de forma adecuada y 50-75% de los casos entregados en el área. El 75-90% de las piezas son inspeccionadas o tienen calidad asegurada;
- Clase Mundial: La herramienta de búsqueda es fácil de usar y muy confiable. El 95-100% de las piezas están disponibles en la primera búsqueda. Acondicionadas de forma adecuada y más del 75% entregadas en el área. El 100% de las piezas tienen calidad asegurada.
A continuación, el promedio de la aplicación del método en más de 50 empresas:

Propuesta de Topkins
En la propuesta de Topkins se encuentran 7 pilares:
- Actitud de la gestión corporativa de la planta
- Estado organizacional del mantenimiento
- Porcentaje de pérdida de recursos debido al mantenimiento
- Solución de problemas de mantenimiento
- Calificación/entrenamiento del personal de mantenimiento
- Información de mantenimiento y desarrollo de acciones
- Resumen de la posición del mantenimiento en la compañía
Pilar 1 - Actitud de la gestión corporativa de la planta
- Inconsciente: No comprende lo que es mantenimiento preventivo, se repara solo cuando se rompe.
- Despertando: Reconoce que el mantenimiento puede ser mejorado, pero se siente incapaz de implementar cambios.
- Desarrollando: Aprende sobre ROI (retorno de inversión), desarrolla mayor interés y seguridad en mejorar el mantenimiento.
- Capacitado: Actitud participativa, reconoce que la gestión de mantenimiento es esencial y debe ser mandataria.
- Consciente: Integra el mantenimiento como una parte fundamental del sistema global de la compañía.
Pilar 2 - Estado organizacional del mantenimiento
- Inconsciente: Reactivo, trabaja en el equipo solo cuando falla; baja productividad del personal.
- Despertando: Aún reactivo, pero logra mejores recuperaciones de componentes y tiene repuestos disponibles cuando ocurre una falla.
- Desarrollando: Preventivo, realiza rutinas de inspección, lubricación, ajustes y pequeños servicios para mejorar el MTBF (tiempo medio entre fallas).
- Capacitado: Predictivo, utiliza técnicas como análisis de vibración, termografía, ultrasonido, etc., para monitorear la condición de los equipos y anticipar problemas.
- Consciente: Productivo, combina técnicas predictivas con la participación activa de los operadores para liberar a los técnicos de mantenimiento, mejorando la mantenibilidad.
Pilar 3 - Porcentual pérdida de recursos debido al mantenimiento
- Inconsciente: Más del 30%.
- Despertando: Entre 20% y 30%.
- Desarrollando: Entre 10% y 20%.
- Capacitado: Entre 5% y 10%.
- Consciente: Menos del 5%.
Pilar 4 - Solución de problemas de mantenimiento
- Inconsciente: Los problemas se desarrollan hasta que son descubiertos.
- Despertando: Se elaboran algunas acciones básicas. Comienza el análisis de fallas de manera elemental.
- Desarrollando: Los problemas se resuelven mediante la implementación de acciones de mantenimiento e ingeniería.
- Capacitado: Los problemas son anticipados. Se utiliza un fuerte equipo interdisciplinario de solución de problemas.
- Consciente: Los problemas son prevenidos.
Pilar 5 - Calificación/entrenamiento del personal de mantenimiento
- Inconsciente: Baja calidad de mano de obra, supervisión rígida, conocimientos obsoletos, pagos por antigüedad.
- Despertando: El personal siente que falta conocimiento para analizar fallas y comienza a cuestionar la especialización. Se reconoce la necesidad de capacitación.
- Desarrollando: Calidad en el trabajo. Se distribuye el desempeño de tareas, inversión en investigación, pagos por capacidad para resolver problemas.
- Capacitado: Expectativa de calidad en el trabajo. Realización de tareas por "multiespecialistas", conocimiento actualizado.
- Consciente: Orgullo y profesionalismo. Flexibilidad en la designación de tareas. Capacitación constante de los operadores por los mantenedores. Pago basado en la productividad de la planta.
Pilar 6 - Información de mantenimiento y desarrollo de acciones
- Inconsciente: El mantenimiento intenta realizar registros, pero la disciplina no es exigida y los datos son deficientes.
- Despertando: Se utiliza una orden de trabajo manual o computarizada, pero la planificación y programación son escasas o nulas.
- Desarrollando: Se utiliza una orden de trabajo manual o computarizada por mantenimiento, operación e ingeniería, con planificación e implementación de programación de servicios.
- Capacitado: Se utiliza un sistema de control de mantenimiento para todas las áreas de la compañía, con información disponible y consistente.
- Consciente: El sistema de información de mantenimiento está integrado con el sistema de información corporativo.
Pilar 7 - Resumen de la posición del mantenimiento en la compañía
- Inconsciente: “No sabemos cuál equipo se va a romper y por eso pagamos al mantenimiento. Las tasas de pérdidas son altas, pero no es un problema de mantenimiento.”
- Despertando: “¿Acaso nuestros competidores tienen estos problemas con sus equipos? ¡Las refacciones nos están costando mucho!”
- Desarrollando: “Con el nuevo criterio de gestión, empezamos a identificar y resolver los problemas.”
- Capacitado: “Todos reconocen que el mantenimiento es parte de nuestra rutina de calidad operacional. No podemos hacer productos de calidad con un mantenimiento deficiente.”
- Consciente: “No esperamos fallas y es una sorpresa cuando ocurren. ¡El mantenimiento contribuye para mantenernos entre los mejores!”
A continuación, se presenta el promedio de la aplicación del método en más de 100 empresas:

Conclusión
Lo importante de las Técnicas McKinsey y Topkins es que detallan la información de cada nivel en cada pilar.
Dado que estos métodos se aplican a directivos de los niveles operativo, ejecutivo y estratégico, esta información facilita la comprensión de sus posiciones, según el punto de vista de cada uno, sobre la situación de la empresa.
Al final de la evaluación de los directivos, se obtiene un valor promedio que es analizado por un grupo designado por la empresa para valorar la posibilidad de mejorar los niveles obtenidos.
Dinos qué te ha parecido el artículo
Artículos recomendados
Lourival Tavares, pasión por el Mantenimiento

Gestión de Mantenimiento: 7 KPIs imprescindibles

Aplicación de la Metodología de Análisis Causa Raíz. Caso: Fallas Recurrentes del Sistema de Distribución Eléctrica en 34,5kv de un Campo Petrolero

Definición del desempeño

Publica tu artículo en la revista #1 de Mantenimiento Industrial
Publicar un artículo en la revista es gratis, no tiene costo.
Solo debes asegurarte que no sea un artículo comercial.
¿Qué esperas?
O envía tu artículo directo: articulos@predictiva21.com
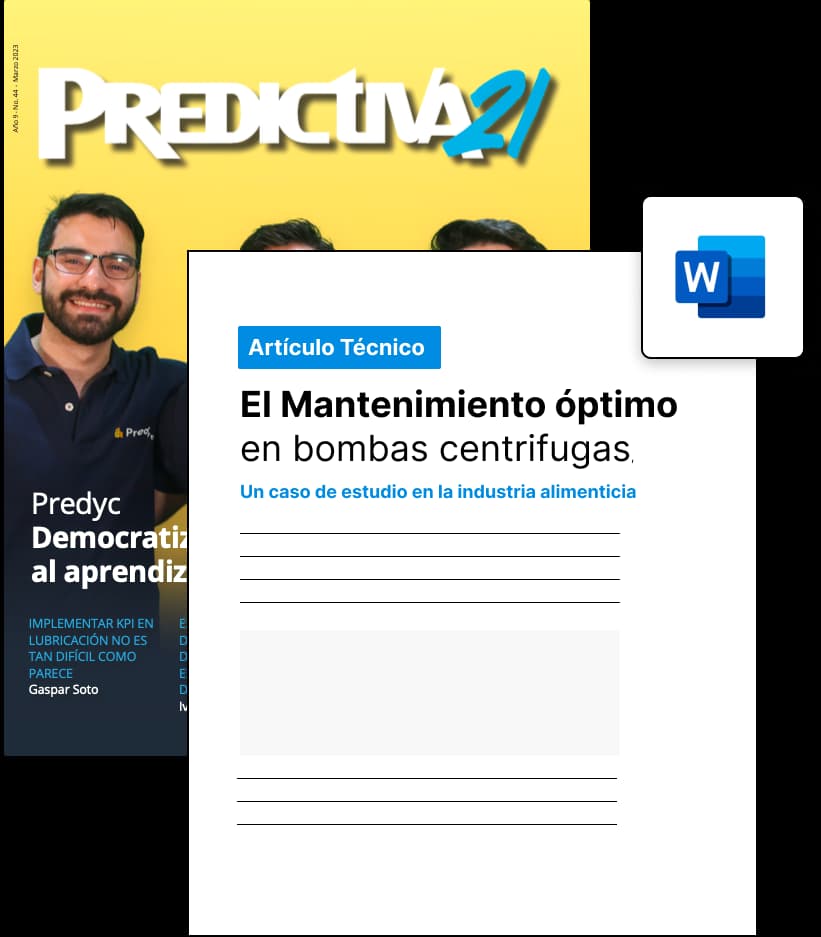