La práctica del Mantenimiento Basado en RCM
Articulo2 de agosto de 2023
El mantenimiento dentro de una planta industrial requiere del engranaje de un gran número de factores. Por ejemplo, el capital humano, materiales, herramientas, entre otros. De todos ellos, uno de los más importantes es la planificación y gestión, los cuáles son basados según un estudio para determinar el plan de acción según los requisitos de las máquinas o la infraestructura. Por eso, en este artículo trataremos sobre el mantenimiento basado en RCM.
Por lo tanto, es necesario la implementación de nuevas técnicas para justificar la toma de decisiones con respecto a la metodología correcta, haciendo referencias al mantenimiento, preventivo, correctivo o predictivo. De esta manera, nace el “Reliability Centered Maintenance” (RCM), es una metodología o procedimiento aplicado para el desarrollo de un plan de mantenimiento teniendo en cuenta el estudio de fallos dentro de las instalaciones de la planta.
El mantenimiento basado en RCM permite estudiar maneras de ahorrar en los costos de manutención o verificar su viabilidad en comparación de la sustitución total de un equipo. A diferencia del consenso universal, el RCM es de fácil aplicación al emplearse pocos recursos y recurriendo a un buen conocimiento de instalación, el desarrollo de la planificación de manutención se simplifica, además su efectividad es garantizada por su aplicación en centrales eléctricas, industria aeronáutica y plantas industriales.
Historia del mantenimiento basado en RCM
El mantenimiento basado en RCM contempla sus antecedentes en la época de los años 50, donde estadísticamente se había previsto un cálculo de dos (2) accidentes aéreos por día en cualquier parte del mundo. Frente a estas deficiencias, las aerolíneas se enfocaron en realizar reparaciones periódicas, estos resultaban ser costosos y poco eficientes, debido al enfoque el cuál era la revisión de los motores y trabajos preventivos. Por eso, a inicios de los años 60, se realizan por parte de la industria de la aviación civil Norteamérica determinan lo ineficientes y peligrosas que eran las prácticas de manutención aplicadas.
Por lo tanto, el RCM se empieza a desarrollar en la época de los 60 y 70, con la intención de guiar al personal de mantenimiento a determinar mejores políticas para la intervención de los activos y obtener resultados óptimos. Por otro lado, en 1978 es documentada por primera vez la definición de RCM por parte de F.S. Nowlan y H.F. Heap y publicado por el departamento de defensa de los Estados Unidos. Desde ese entonces se ha implementado en diferentes industrias y se ha perfeccionado.
Objetivos y fases del mantenimiento basado en RCM
La implementación de la técnica de mantenimiento centrado en la fiabilidad (RCM) en el punto de vista industrial es economizar en gastos y aumentar la capacidad de la planta. La implementación consiste en un análisis del estado de los activos y partiendo desde esa metodología obtener resultados como mejorar la comprensión del funcionamiento de los equipos, analizar las posibilidades de fallo y definir las acciones a tomar garantizando el menor consumo de la empresa.
Para determinar los procedimientos, el RCM se enfoca en analizar los fallos, tanto los documentados como otros deseados a evitar. Siempre teniendo en cuenta acciones para prevenir un desarrollo desfavorable de las actividades. Por lo tanto, el personal encargado de la planificación debe responderse una serie de preguntas antes de definir los pasos a seguir, entre ellas se encuentran: funciones del sistema, tipo de falla, causalidad, consecuencia, secuencia y cómo puede evitarse. Posteriormente se plantean una serie de fases para concretar el RCM
Fase 1: Codificación y listado de los subsistemas
Cada empresa debe tener más de una planta para sus actividades rutinarias. En ellas se deben estipular las máquinas a disposición, como funciona y cuáles son sus dependencias. Por lo tanto, para la codificación y listado, no es conforme para la metodología de RCM el nombrar los motores, bombas, transformadores a disposición. También, es necesario saber su funcionalidad e importancia dentro de la cadena de producción. De esa manera, se podrá detallar en un inventario la prioridad de cada una.
Fase 2: Estudio detallado del funcionamiento del sistema
Cada proceso de la cadena productiva de una planta está compuesta por sistemas y subsistemas. Estos dependen de equipos internos encargados de hacer un trabajo en específico. Por lo tanto, es necesario verificar el cumplimiento correcto de cada uno de los subsistemas. En el caso de encontrarse un fenómeno indeseado o una deficiente evolución de la tarea, se tilda como fallo y se examina el equipo encargado.
Fase 3: Determinación de los fallos funcionales y fallos técnicos
En algunos casos, los fallos no necesariamente pueden paralizar un sistema completo; por el contrario, significan un uso totalmente deficiente por parte de los equipos o uno en específico, lo cuáles pueden derivar en el empeoramiento de condiciones de trabajo o sobre esforzar un componente del subsistema. En ese caso, se identifica la máquina responsable de su propia insuficiencia para no comprometer los demás procesos dentro de la planta.
Cursos recomendados
%252FImagen%252Frcm-1730083250826.webp%3Falt%3Dmedia%26token%3D3775356a-7b11-4c44-b21f-45b3409fb9ed&w=3840&q=75)



%252FImagen%252FRAMPREDYC-1730060420837.webp%3Falt%3Dmedia%26token%3D2634a7f0-988e-4022-b91f-382503e6e9db&w=3840&q=75)



Fase 4: Determinación de los modos de fallo
Para trabajar en la prevención o solución de los fallos detectados, es necesario determinar si la imperfección presentada por el sistema, subsistema o el equipo es por el origen de un funcionamiento defectuoso o es directamente el fenómeno indeseado. Por lo tanto, es importante definir la profundidad deseada para realizar el estudio sobre la anomalía, de tal manera, la intervención sea económicamente factible.
Fase 5: Estudio de las consecuencias de cada modo de fallo
Esta fase hace referencia al nivel de criticidad, por lo tanto el mantenimiento basado en RCM permite desarrollar un análisis de la gravedad de un fallo teniendo en cuenta los aspectos como la probabilidad, causa y consecuencia. Por lo tanto, para definir un fallo como critico debe comprometer la seguridad de los empleados, el medio ambiente o paralizar las labores de la empresa en su totalidad.
Fase 6: Determinación de medidas preventivas
El siguiente paso del RCM, una vez estudiado las causalidades, razón y consecuencia, se procede a programar medidas preventivas con la intención de evitar imperfecciones, disminuir sus efectos. Estas tareas se consideran como la base del mantenimiento preventivo y es fundamental dentro del estudio del RCM. Para ello, se toman en cuenta los siguientes pasos: mantenimiento, mejoras, formación de personal, modificación de las instrucciones operativas y de intervención.
Fase 7: Agrupación de las medidas preventivas en sus diferentes categorías
En el mantenimiento en base al RCM, no se puede prescindir de la definición de las medidas preventivas, haciendo referencia a evitar fallos grandes dentro del sistema. Para esto, es necesario concentrar las actividades en planificación, lista de mejoras, tareas de formación. Por último, enlistar los procedimientos operativos y de manutención. El objetivo es facilitar la implementación.
Fase 8: Puesta en marcha de las medidas preventivas
Por último, el paso final para concluir un mantenimiento basado en RCM, requiere de implementar todas las medidas definidas anteriormente, eso significa sustituir el anterior método por el nuevo. No obstante, se debe tener en cuenta las recomendaciones sugeridas por los proveedores, de tal manera con los planos y manuales se puede cerciorar no excluir ningún procedimiento importante durante la manutención.
Para finalizar, el mantenimiento basado en RCM, es una estrategia implementada desde hace medio siglo aproximadamente y consiste en la elaboración de un plan preventivo de intervención a los equipos, explorando de manera minuciosa cada proceso dentro de la planta con la intención de buscar los posibles fallos a presentar. Para esto se siguen una serie de pasos y se toma en cuenta anteriores reparaciones para prevenir o abordar desde la seguridad de los datos recolectados.
Dinos qué te ha parecido el artículo
Artículos recomendados
Inspección vídeo endoscopica: Estrategia útil del monitoreo basado en condición

Gestión de Activos Proactiva

9.2 Mantenimiento Predictivo y Monitoreo según condición

16.1.- Materiales de Acuerdo con el ASME B73.1

Publica tu artículo en la revista #1 de Mantenimiento Industrial
Publicar un artículo en la revista es gratis, no tiene costo.
Solo debes asegurarte que no sea un artículo comercial.
¿Qué esperas?
O envía tu artículo directo: articulos@predictiva21.com
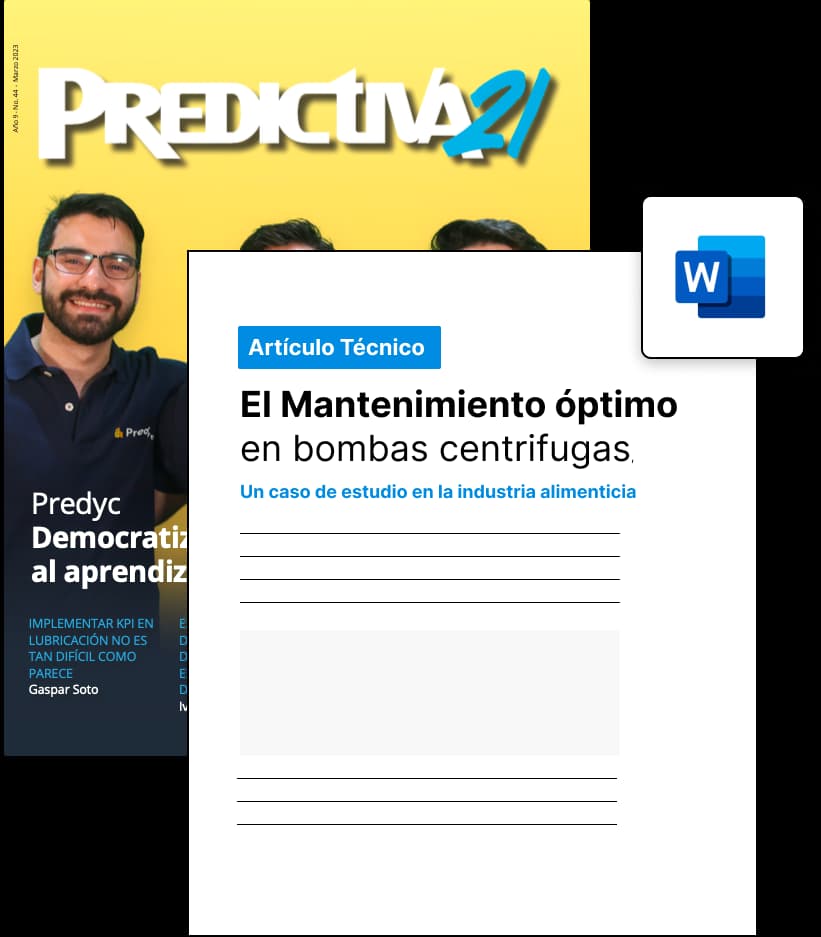
La práctica del Mantenimiento Basado en RCM
Articulo 2 de agosto de 2023El mantenimiento dentro de una planta industrial requiere del engranaje de un gran número de factores. Por ejemplo, el capital humano, materiales, herramientas, entre otros. De todos ellos, uno de los más importantes es la planificación y gestión, los cuáles son basados según un estudio para determinar el plan de acción según los requisitos de las máquinas o la infraestructura. Por eso, en este artículo trataremos sobre el mantenimiento basado en RCM.
Por lo tanto, es necesario la implementación de nuevas técnicas para justificar la toma de decisiones con respecto a la metodología correcta, haciendo referencias al mantenimiento, preventivo, correctivo o predictivo. De esta manera, nace el “Reliability Centered Maintenance” (RCM), es una metodología o procedimiento aplicado para el desarrollo de un plan de mantenimiento teniendo en cuenta el estudio de fallos dentro de las instalaciones de la planta.
El mantenimiento basado en RCM permite estudiar maneras de ahorrar en los costos de manutención o verificar su viabilidad en comparación de la sustitución total de un equipo. A diferencia del consenso universal, el RCM es de fácil aplicación al emplearse pocos recursos y recurriendo a un buen conocimiento de instalación, el desarrollo de la planificación de manutención se simplifica, además su efectividad es garantizada por su aplicación en centrales eléctricas, industria aeronáutica y plantas industriales.
Historia del mantenimiento basado en RCM
El mantenimiento basado en RCM contempla sus antecedentes en la época de los años 50, donde estadísticamente se había previsto un cálculo de dos (2) accidentes aéreos por día en cualquier parte del mundo. Frente a estas deficiencias, las aerolíneas se enfocaron en realizar reparaciones periódicas, estos resultaban ser costosos y poco eficientes, debido al enfoque el cuál era la revisión de los motores y trabajos preventivos. Por eso, a inicios de los años 60, se realizan por parte de la industria de la aviación civil Norteamérica determinan lo ineficientes y peligrosas que eran las prácticas de manutención aplicadas.
Por lo tanto, el RCM se empieza a desarrollar en la época de los 60 y 70, con la intención de guiar al personal de mantenimiento a determinar mejores políticas para la intervención de los activos y obtener resultados óptimos. Por otro lado, en 1978 es documentada por primera vez la definición de RCM por parte de F.S. Nowlan y H.F. Heap y publicado por el departamento de defensa de los Estados Unidos. Desde ese entonces se ha implementado en diferentes industrias y se ha perfeccionado.
Objetivos y fases del mantenimiento basado en RCM
La implementación de la técnica de mantenimiento centrado en la fiabilidad (RCM) en el punto de vista industrial es economizar en gastos y aumentar la capacidad de la planta. La implementación consiste en un análisis del estado de los activos y partiendo desde esa metodología obtener resultados como mejorar la comprensión del funcionamiento de los equipos, analizar las posibilidades de fallo y definir las acciones a tomar garantizando el menor consumo de la empresa.
Para determinar los procedimientos, el RCM se enfoca en analizar los fallos, tanto los documentados como otros deseados a evitar. Siempre teniendo en cuenta acciones para prevenir un desarrollo desfavorable de las actividades. Por lo tanto, el personal encargado de la planificación debe responderse una serie de preguntas antes de definir los pasos a seguir, entre ellas se encuentran: funciones del sistema, tipo de falla, causalidad, consecuencia, secuencia y cómo puede evitarse. Posteriormente se plantean una serie de fases para concretar el RCM
Fase 1: Codificación y listado de los subsistemas
Cada empresa debe tener más de una planta para sus actividades rutinarias. En ellas se deben estipular las máquinas a disposición, como funciona y cuáles son sus dependencias. Por lo tanto, para la codificación y listado, no es conforme para la metodología de RCM el nombrar los motores, bombas, transformadores a disposición. También, es necesario saber su funcionalidad e importancia dentro de la cadena de producción. De esa manera, se podrá detallar en un inventario la prioridad de cada una.
Fase 2: Estudio detallado del funcionamiento del sistema
Cada proceso de la cadena productiva de una planta está compuesta por sistemas y subsistemas. Estos dependen de equipos internos encargados de hacer un trabajo en específico. Por lo tanto, es necesario verificar el cumplimiento correcto de cada uno de los subsistemas. En el caso de encontrarse un fenómeno indeseado o una deficiente evolución de la tarea, se tilda como fallo y se examina el equipo encargado.
Fase 3: Determinación de los fallos funcionales y fallos técnicos
En algunos casos, los fallos no necesariamente pueden paralizar un sistema completo; por el contrario, significan un uso totalmente deficiente por parte de los equipos o uno en específico, lo cuáles pueden derivar en el empeoramiento de condiciones de trabajo o sobre esforzar un componente del subsistema. En ese caso, se identifica la máquina responsable de su propia insuficiencia para no comprometer los demás procesos dentro de la planta.
Cursos recomendados
%252FImagen%252Frcm-1730083250826.webp%3Falt%3Dmedia%26token%3D3775356a-7b11-4c44-b21f-45b3409fb9ed&w=3840&q=75)



%252FImagen%252FRAMPREDYC-1730060420837.webp%3Falt%3Dmedia%26token%3D2634a7f0-988e-4022-b91f-382503e6e9db&w=3840&q=75)



Fase 4: Determinación de los modos de fallo
Para trabajar en la prevención o solución de los fallos detectados, es necesario determinar si la imperfección presentada por el sistema, subsistema o el equipo es por el origen de un funcionamiento defectuoso o es directamente el fenómeno indeseado. Por lo tanto, es importante definir la profundidad deseada para realizar el estudio sobre la anomalía, de tal manera, la intervención sea económicamente factible.
Fase 5: Estudio de las consecuencias de cada modo de fallo
Esta fase hace referencia al nivel de criticidad, por lo tanto el mantenimiento basado en RCM permite desarrollar un análisis de la gravedad de un fallo teniendo en cuenta los aspectos como la probabilidad, causa y consecuencia. Por lo tanto, para definir un fallo como critico debe comprometer la seguridad de los empleados, el medio ambiente o paralizar las labores de la empresa en su totalidad.
Fase 6: Determinación de medidas preventivas
El siguiente paso del RCM, una vez estudiado las causalidades, razón y consecuencia, se procede a programar medidas preventivas con la intención de evitar imperfecciones, disminuir sus efectos. Estas tareas se consideran como la base del mantenimiento preventivo y es fundamental dentro del estudio del RCM. Para ello, se toman en cuenta los siguientes pasos: mantenimiento, mejoras, formación de personal, modificación de las instrucciones operativas y de intervención.
Fase 7: Agrupación de las medidas preventivas en sus diferentes categorías
En el mantenimiento en base al RCM, no se puede prescindir de la definición de las medidas preventivas, haciendo referencia a evitar fallos grandes dentro del sistema. Para esto, es necesario concentrar las actividades en planificación, lista de mejoras, tareas de formación. Por último, enlistar los procedimientos operativos y de manutención. El objetivo es facilitar la implementación.
Fase 8: Puesta en marcha de las medidas preventivas
Por último, el paso final para concluir un mantenimiento basado en RCM, requiere de implementar todas las medidas definidas anteriormente, eso significa sustituir el anterior método por el nuevo. No obstante, se debe tener en cuenta las recomendaciones sugeridas por los proveedores, de tal manera con los planos y manuales se puede cerciorar no excluir ningún procedimiento importante durante la manutención.
Para finalizar, el mantenimiento basado en RCM, es una estrategia implementada desde hace medio siglo aproximadamente y consiste en la elaboración de un plan preventivo de intervención a los equipos, explorando de manera minuciosa cada proceso dentro de la planta con la intención de buscar los posibles fallos a presentar. Para esto se siguen una serie de pasos y se toma en cuenta anteriores reparaciones para prevenir o abordar desde la seguridad de los datos recolectados.
Dinos qué te ha parecido el artículo
Artículos recomendados
Aprende qué es la planificación y control de mantenimiento

Aprende qué es un plan de mantenimiento

Podcast de Gestión de Activos

Análisis de datos: esencial para la toma de decisiones

Publica tu artículo en la revista #1 de Mantenimiento Industrial
Publicar un artículo en la revista es gratis, no tiene costo.
Solo debes asegurarte que no sea un artículo comercial.
¿Qué esperas?
O envía tu artículo directo: articulos@predictiva21.com
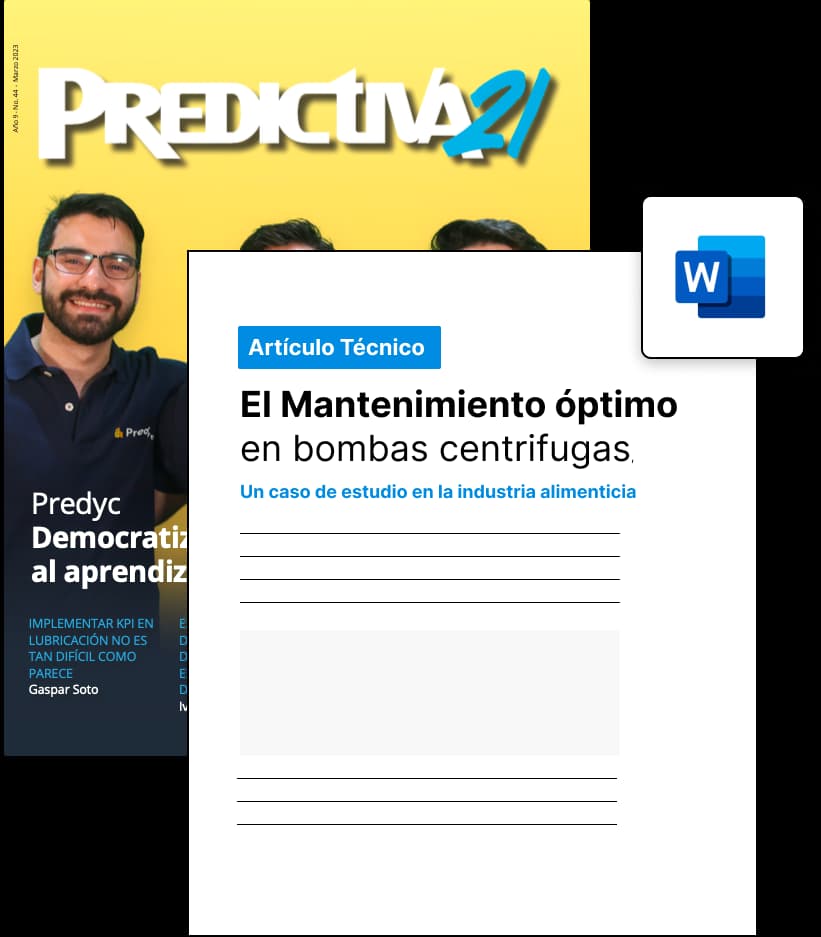