Tecnología MRO
Articulo6 de julio de 2021
He aquí un par de observaciones curiosas:
- Los usuarios finales y los proveedores de ERPs (sistemas de gestión empresarial) suelen estar tecnológicamente muy atrasados en esta especialidad de gestión de suministros MRO.
- No hay más que un puñado de especialistas (expertos) en este campo que hayan desarrollado algún tipo de solución tecnológica avanzada, y sin embargo siguen siendo un tanto oscuros.
Aunque se dispone de un conocimiento y una experiencia considerables, no parece que vaya más allá de esos especialistas.
¿Existe complejidad en la gestión de los materiales MRO?
Desgraciadamente, en la industria sigue prevaleciendo una visión reduccionista y equivocada, en la que todo se reduce a asignar manualmente mínimos y máximos a los artículos de un inventario.
Podría escribir decenas de páginas explicando cuál es la verdadera dimensión y complejidad de la disciplina (análisis de riesgos, economía, logística, matemáticas, estadística, ingeniería de la confiabilidad, teoría de las restricciones, etc.). Sin embargo, como no hay espacio para explicaciones extensas, pondré este ejemplo ilustrativo:
Supongamos un inventario de sólo 1.000 artículos (mil códigos de stock); incluso si fijamos un nivel de stock máximo de 1 (permitiendo sólo 2 opciones entre 0 y 1 para cada artículo), hay 21.000 posiciones de inventario distintas, es decir, un número astronómico de posibilidades.
La cuestión que se plantea entonces es: Entre estas posibilidades, ¿cuál o cuáles serían las mejores? Como puede verse, existe un nivel de complejidad razonable y, desde luego, no puede abordarse sin el apoyo de herramientas analíticas avanzadas que, a pesar de estar disponibles en el mercado desde hace bastante tiempo, la mayoría de las empresas industriales aún no conocen o no utilizan.
¿Cuál es el impacto real de los materiales MRO en la industria mundial?
Muchas empresas tienen demasiado de lo que no necesitan y no lo suficiente de lo que sí, los niveles de inventario tienden a ser más altos de lo necesario, lo que resulta en pérdidas financieras con el capital de trabajo atado al inventario.
Hay un hecho inexorable: cada falta de material (stock-out) provoca algún tipo de gasto operativo (pérdida de producción, bajada o pérdida de producto, coste con maniobras de operación y mantenimiento para mantener la planta en funcionamiento, flete acelerado, horas extras y menor productividad laboral, entre otros).
Además, un proceso de gestión de repuestos ineficaz puede suponer al menos un 20% - 35% de tiempo de inactividad de las máquinas debido a su impacto en los tiempos de reparación. Esto suele deberse a la falta de piezas y materiales necesarios para realizar las reparaciones de forma correcta y rápida a la primera. El efecto secundario es una menor disponibilidad y, en consecuencia, un menor volumen de producción, menores ingresos y menores beneficios. Para colmo de males, podemos encontrarnos con mantenedores que se "apañan" con lo que hay, corrompiendo la configuración de los activos y creando potencialmente aún más tiempo de inactividad cuando se producen incidencias posteriores con la misma máquina.
Paradójicamente, a pesar de las importantes pérdidas de producción causadas por la falta de piezas de repuesto, estas pérdidas apenas son aceptadas por la dirección. A menudo escuchamos la afirmación: "Aquí en nuestra empresa no hay pérdidas de producción porque cualquier pérdida siempre se puede recuperar sin afectar al plan de producción".
Excluyendo la capacidad sobrante causada por la falta de demanda de los productos, si siempre hay espacio para "recuperar las pérdidas de producción", entonces se concluiría que los activos se están programando para funcionar con holgura, y una de las razones para ello es ciertamente los supuestos retrasos "inevitables" causados por la falta de materiales. En otras palabras, asumimos que habrá retrasos, construimos una holgura para permitirlo y ¡no podemos quedarnos atrás! La profecía se hace realidad.
Evolución de la tecnología de gestión de materiales MRO
Excluyendo las prácticas primarias que aún prevalecen en la mayoría de las empresas industriales, la evolución de la tecnología de gestión de materiales MRO puede resumirse en tres olas tecnológicas, como se muestra a continuación.
Primera ola: Tecnología convencional
Hay muchas limitaciones tecnológicas graves, aquí hay dos que son particularmente relevantes y fáciles de entender.
Primera: Supongamos que hay dos artículos con exactamente las mismas características y tiempo de reposición, y cada uno es igualmente importante para el funcionamiento de la planta. Uno cuesta 100 dólares y el otro 2.000. Si intentamos asignar un presupuesto fijo para obtener la mayor disponibilidad posible para la planta que contiene los dos artículos, presumiblemente deberíamos comprar relativamente más del artículo barato y menos del caro. Sin embargo, y por extraño que parezca, como el coste se ignora solemnemente, ambos artículos tendrían garantizado un nivel de existencias igual y una protección igual (nivel de servicio o riesgo de escasez).
Segundo: Independientemente del patrón o volumen de la demanda (errática, baja, media o alta) para cada uno de los miles de artículos en inventario, se supone que la demanda se adhiere a la distribución normal (Gauss). Sabemos, desde el ámbito de la Ingeniería de la Confiabilidad, que los propios fallos que dan lugar a la demanda de piezas pueden ser normales, exponenciales negativos o hiperexponenciales. Por tanto, ¿no es la hipótesis gaussiana intrínsecamente arriesgada?
Todos los ERP de hoy en día caen en este estadio tecnológico. Siguen sin estar atados a las realidades de las distribuciones de confiabilidad.
Cursos recomendados




%252FImagen%252FRAMPREDYC-1730060420837.webp%3Falt%3Dmedia%26token%3D2634a7f0-988e-4022-b91f-382503e6e9db&w=3840&q=75)



Segunda ola: Tecnología intermedia
En esta ola añadimos dos mejoras a la primera. La primera es que se asume que la demanda se adhiere a otras distribuciones, especialmente a la de Poisson y Bernoulli, ignorando el hecho de que estas dos distribuciones son incapaces de manejar adecuadamente artículos con patrones de demanda erráticos, de tendencia o estacionales. La segunda es permitir el recálculo automático de los parámetros de control del inventario. A pesar de estas dos mejoras puntuales, se detiene en las limitaciones heredadas de la primera ola.
Muchas herramientas de optimización de inventarios caen en esta segunda etapa tecnológica y siguen sin integrarse con los ERP.
Tercera ola: Tecnología avanzada
En este caso, me refiero a un avance tecnológico que se centra en lo que realmente importa: la consecución de un equilibrio entre la inversión en inventarios y la disponibilidad operativa de los activos. Para ello, se hace uso de tecnología punta plasmada en complejos algoritmos y heurística sin parangón en la especialidad.
Lo paradójico es que, a pesar de ser utilizada con notable éxito desde hace casi dos décadas en los segmentos de: defensa, aeroespacial, aviación, plataformas petrolíferas, ferrocarril y generación de energía; esta tecnología sigue siendo poco conocida y poco utilizada en la industria en general.
Para ilustrar su eficacia, si su empresa experimenta un nivel de servicio global medio de, digamos, el 95%, hemos demostrado que se puede mantener el mismo rendimiento con un 20 a 35% menos de inversión en inventario. Si añadimos el aumento potencial de la producción y la productividad, y la reducción de los costes operativos, entre otros beneficios, no es de extrañar que la mayoría ignore esta capacidad. Sin embargo, en la mayoría de los casos, simplemente no saben lo que no saben.
Conclusión
Existe una oportunidad increíble en términos de aumento de la productividad y la competitividad si adoptamos la segunda y la tercera ola de la tecnología MRO y las explotamos como fueron diseñadas para ser explotadas.

Este artículo fue escrito por David A de Castro, Presidente de Brasman Engenharia, Brasil. Es un ingeniero consultor registrado con una maestría en ingeniería mecánica. David tiene más de 35 años de experiencia en ingeniería de mantenimiento y confiabilidad en grandes empresas y en formación en el puesto de trabajo en Alemania, Italia, España, Suiza, Reino Unido y Estados Unidos. Es autor de más de 20 artículos técnicos sobre ingeniería de mantenimiento y materiales MRO. Durante los últimos 10 años, David se ha especializado en el control científico de inventarios de materiales y repuestos MRO. Su trabajo ha consistido en el desarrollo y la aplicación de mejores prácticas innovadoras y herramientas analíticas en instalaciones de proceso de todo Brasil. David es profesor de postgrado en la Universidad de Salvador, Unifacs, Salvador, Brasil.
– De Conscious Asset: Parte 1, Parte 2.
Autor: James Reyes-Picknell
Presidente, Director y Consultor Principal de Conscious Asset
Correo: james@consciousasset.com
Sitio Web: https://consciousasset.com/
LinkedIn: https://ca.linkedin.com/in/jamesreyespicknell
Traducción: Predictiva21
Dinos qué te ha parecido el artículo
Artículos recomendados
La importancia de los 5 por qué en el ACR

TERMOGRAFIA II

Regulación de carga en motores de combustible pesado (Hfo), para determinar una operación eficiente con respecto al consumo específico de combustible.

Gestión de mantenimiento: administrar la productividad

Publica tu artículo en la revista #1 de Mantenimiento Industrial
Publicar un artículo en la revista es gratis, no tiene costo.
Solo debes asegurarte que no sea un artículo comercial.
¿Qué esperas?
O envía tu artículo directo: articulos@predictiva21.com
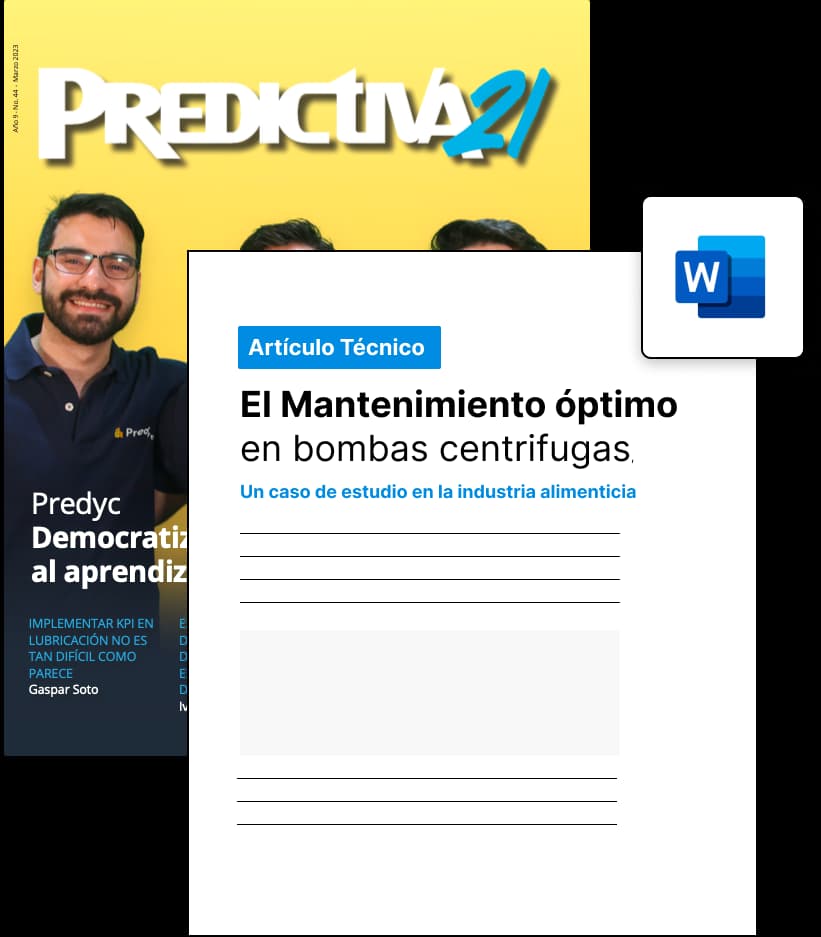
Tecnología MRO
Articulo 6 de julio de 2021He aquí un par de observaciones curiosas:
- Los usuarios finales y los proveedores de ERPs (sistemas de gestión empresarial) suelen estar tecnológicamente muy atrasados en esta especialidad de gestión de suministros MRO.
- No hay más que un puñado de especialistas (expertos) en este campo que hayan desarrollado algún tipo de solución tecnológica avanzada, y sin embargo siguen siendo un tanto oscuros.
Aunque se dispone de un conocimiento y una experiencia considerables, no parece que vaya más allá de esos especialistas.
¿Existe complejidad en la gestión de los materiales MRO?
Desgraciadamente, en la industria sigue prevaleciendo una visión reduccionista y equivocada, en la que todo se reduce a asignar manualmente mínimos y máximos a los artículos de un inventario.
Podría escribir decenas de páginas explicando cuál es la verdadera dimensión y complejidad de la disciplina (análisis de riesgos, economía, logística, matemáticas, estadística, ingeniería de la confiabilidad, teoría de las restricciones, etc.). Sin embargo, como no hay espacio para explicaciones extensas, pondré este ejemplo ilustrativo:
Supongamos un inventario de sólo 1.000 artículos (mil códigos de stock); incluso si fijamos un nivel de stock máximo de 1 (permitiendo sólo 2 opciones entre 0 y 1 para cada artículo), hay 21.000 posiciones de inventario distintas, es decir, un número astronómico de posibilidades.
La cuestión que se plantea entonces es: Entre estas posibilidades, ¿cuál o cuáles serían las mejores? Como puede verse, existe un nivel de complejidad razonable y, desde luego, no puede abordarse sin el apoyo de herramientas analíticas avanzadas que, a pesar de estar disponibles en el mercado desde hace bastante tiempo, la mayoría de las empresas industriales aún no conocen o no utilizan.
¿Cuál es el impacto real de los materiales MRO en la industria mundial?
Muchas empresas tienen demasiado de lo que no necesitan y no lo suficiente de lo que sí, los niveles de inventario tienden a ser más altos de lo necesario, lo que resulta en pérdidas financieras con el capital de trabajo atado al inventario.
Hay un hecho inexorable: cada falta de material (stock-out) provoca algún tipo de gasto operativo (pérdida de producción, bajada o pérdida de producto, coste con maniobras de operación y mantenimiento para mantener la planta en funcionamiento, flete acelerado, horas extras y menor productividad laboral, entre otros).
Además, un proceso de gestión de repuestos ineficaz puede suponer al menos un 20% - 35% de tiempo de inactividad de las máquinas debido a su impacto en los tiempos de reparación. Esto suele deberse a la falta de piezas y materiales necesarios para realizar las reparaciones de forma correcta y rápida a la primera. El efecto secundario es una menor disponibilidad y, en consecuencia, un menor volumen de producción, menores ingresos y menores beneficios. Para colmo de males, podemos encontrarnos con mantenedores que se "apañan" con lo que hay, corrompiendo la configuración de los activos y creando potencialmente aún más tiempo de inactividad cuando se producen incidencias posteriores con la misma máquina.
Paradójicamente, a pesar de las importantes pérdidas de producción causadas por la falta de piezas de repuesto, estas pérdidas apenas son aceptadas por la dirección. A menudo escuchamos la afirmación: "Aquí en nuestra empresa no hay pérdidas de producción porque cualquier pérdida siempre se puede recuperar sin afectar al plan de producción".
Excluyendo la capacidad sobrante causada por la falta de demanda de los productos, si siempre hay espacio para "recuperar las pérdidas de producción", entonces se concluiría que los activos se están programando para funcionar con holgura, y una de las razones para ello es ciertamente los supuestos retrasos "inevitables" causados por la falta de materiales. En otras palabras, asumimos que habrá retrasos, construimos una holgura para permitirlo y ¡no podemos quedarnos atrás! La profecía se hace realidad.
Evolución de la tecnología de gestión de materiales MRO
Excluyendo las prácticas primarias que aún prevalecen en la mayoría de las empresas industriales, la evolución de la tecnología de gestión de materiales MRO puede resumirse en tres olas tecnológicas, como se muestra a continuación.
Primera ola: Tecnología convencional
Hay muchas limitaciones tecnológicas graves, aquí hay dos que son particularmente relevantes y fáciles de entender.
Primera: Supongamos que hay dos artículos con exactamente las mismas características y tiempo de reposición, y cada uno es igualmente importante para el funcionamiento de la planta. Uno cuesta 100 dólares y el otro 2.000. Si intentamos asignar un presupuesto fijo para obtener la mayor disponibilidad posible para la planta que contiene los dos artículos, presumiblemente deberíamos comprar relativamente más del artículo barato y menos del caro. Sin embargo, y por extraño que parezca, como el coste se ignora solemnemente, ambos artículos tendrían garantizado un nivel de existencias igual y una protección igual (nivel de servicio o riesgo de escasez).
Segundo: Independientemente del patrón o volumen de la demanda (errática, baja, media o alta) para cada uno de los miles de artículos en inventario, se supone que la demanda se adhiere a la distribución normal (Gauss). Sabemos, desde el ámbito de la Ingeniería de la Confiabilidad, que los propios fallos que dan lugar a la demanda de piezas pueden ser normales, exponenciales negativos o hiperexponenciales. Por tanto, ¿no es la hipótesis gaussiana intrínsecamente arriesgada?
Todos los ERP de hoy en día caen en este estadio tecnológico. Siguen sin estar atados a las realidades de las distribuciones de confiabilidad.
Cursos recomendados




%252FImagen%252FRAMPREDYC-1730060420837.webp%3Falt%3Dmedia%26token%3D2634a7f0-988e-4022-b91f-382503e6e9db&w=3840&q=75)



Segunda ola: Tecnología intermedia
En esta ola añadimos dos mejoras a la primera. La primera es que se asume que la demanda se adhiere a otras distribuciones, especialmente a la de Poisson y Bernoulli, ignorando el hecho de que estas dos distribuciones son incapaces de manejar adecuadamente artículos con patrones de demanda erráticos, de tendencia o estacionales. La segunda es permitir el recálculo automático de los parámetros de control del inventario. A pesar de estas dos mejoras puntuales, se detiene en las limitaciones heredadas de la primera ola.
Muchas herramientas de optimización de inventarios caen en esta segunda etapa tecnológica y siguen sin integrarse con los ERP.
Tercera ola: Tecnología avanzada
En este caso, me refiero a un avance tecnológico que se centra en lo que realmente importa: la consecución de un equilibrio entre la inversión en inventarios y la disponibilidad operativa de los activos. Para ello, se hace uso de tecnología punta plasmada en complejos algoritmos y heurística sin parangón en la especialidad.
Lo paradójico es que, a pesar de ser utilizada con notable éxito desde hace casi dos décadas en los segmentos de: defensa, aeroespacial, aviación, plataformas petrolíferas, ferrocarril y generación de energía; esta tecnología sigue siendo poco conocida y poco utilizada en la industria en general.
Para ilustrar su eficacia, si su empresa experimenta un nivel de servicio global medio de, digamos, el 95%, hemos demostrado que se puede mantener el mismo rendimiento con un 20 a 35% menos de inversión en inventario. Si añadimos el aumento potencial de la producción y la productividad, y la reducción de los costes operativos, entre otros beneficios, no es de extrañar que la mayoría ignore esta capacidad. Sin embargo, en la mayoría de los casos, simplemente no saben lo que no saben.
Conclusión
Existe una oportunidad increíble en términos de aumento de la productividad y la competitividad si adoptamos la segunda y la tercera ola de la tecnología MRO y las explotamos como fueron diseñadas para ser explotadas.

Este artículo fue escrito por David A de Castro, Presidente de Brasman Engenharia, Brasil. Es un ingeniero consultor registrado con una maestría en ingeniería mecánica. David tiene más de 35 años de experiencia en ingeniería de mantenimiento y confiabilidad en grandes empresas y en formación en el puesto de trabajo en Alemania, Italia, España, Suiza, Reino Unido y Estados Unidos. Es autor de más de 20 artículos técnicos sobre ingeniería de mantenimiento y materiales MRO. Durante los últimos 10 años, David se ha especializado en el control científico de inventarios de materiales y repuestos MRO. Su trabajo ha consistido en el desarrollo y la aplicación de mejores prácticas innovadoras y herramientas analíticas en instalaciones de proceso de todo Brasil. David es profesor de postgrado en la Universidad de Salvador, Unifacs, Salvador, Brasil.
– De Conscious Asset: Parte 1, Parte 2.
Autor: James Reyes-Picknell
Presidente, Director y Consultor Principal de Conscious Asset
Correo: james@consciousasset.com
Sitio Web: https://consciousasset.com/
LinkedIn: https://ca.linkedin.com/in/jamesreyespicknell
Traducción: Predictiva21
Dinos qué te ha parecido el artículo
Artículos recomendados
¿Es el Mantenimiento Centrado en Confiabilidad una tarea fácil?

Gestión de mantenimiento: administrar la productividad

Estudio de Causa de Fallo realizado al Turborreactor Viper MK540 de la AeronaveAermachi, perteneciente a la Armada Argentina

6 Errores a evitar con el software de gestión de activos (EAM)

Publica tu artículo en la revista #1 de Mantenimiento Industrial
Publicar un artículo en la revista es gratis, no tiene costo.
Solo debes asegurarte que no sea un artículo comercial.
¿Qué esperas?
O envía tu artículo directo: articulos@predictiva21.com
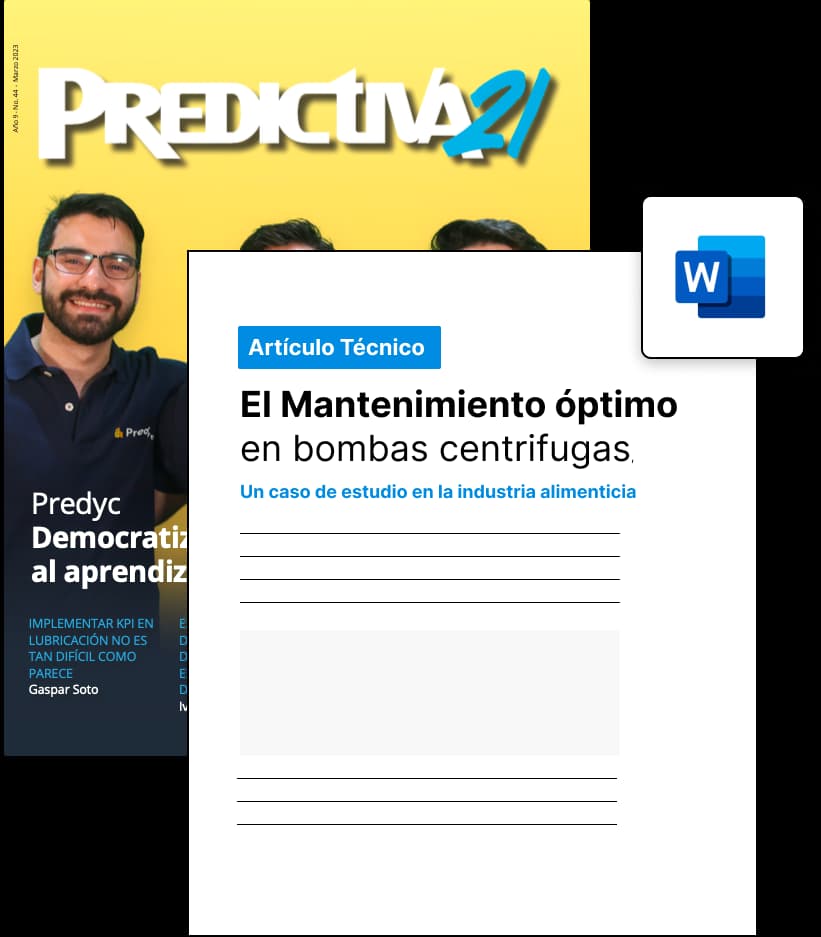