13.3.- Lubricación con Aceite
Libros6 de septiembre de 2021
Los sistemas de lubricación por aceite son los más usados en bombas de procesos de potencia media, alta y en bombas API 610/ISO 13709 de cualquier rango de potencia, porque garantiza mayor rendimiento de los rodamientos, en casi todos los servicios industriales.
Tanto el ASME B73.1 como el API 610/ISO 13709 especifican la lubricación por aceite como el sistema preferencial de lubricación. El ASME B73.1 en la sección 4.7.5 Lubrication, indica que la lubricación por aceite es la lubricación estándar para las bombas fabricadas siguiendo esta norma principalmente el método de lubricación por baño de aceite, sin embargo, deja abiertaopciones para el uso de otros métodos de lubricación como la lubricación por Neblina de Aceite o “Oil Mist” y hasta lubricación por grasa.
En el API 610/ISO 13709 11ava edición en el capítulo 6.11. se indica que los cojinetes y las cajeras de cojinetes deben ser diseñadas para ser lubricadas con aceite mineral a menos que expresamente se indique lo contrario. Indicando también que si también es solicitado se deben dejar las previsiones para la instalación de sistemas de lubricación por niebla o de “Oil Mist”.
Los aceites minerales básicos son producidos a partir de la destilación del petróleo crudo, tomando como materia prima el residuo largo del proceso de destilación. En la destilación, el petróleo es separado en diferentes componentes usando para ello un calentamiento inicial en hornos que lleva al petróleo a varios cientos de grados de temperatura, lo que facilita la separación de los diferentes componentes que lo forman. El petróleo luego es bombeado a una torre de destilación atmosférica, que es la etapa inicial del proceso de destilación en las refinerías convencionales.
En este proceso de destilación los componentes más livianos son captados en el tope de la torre para producir gasolina y nafta, los componentes medianos son captados en las bandejas intermedias para producir diesel y gasóleo, el fondo de la torre es la fracción más pesada es calentado en hornos y bombeado a las torres de destilación al vacío.
El lubricante base es captado en las bandejas intermedias de la torre de destilación al vacío. Este lubricante base es tratado para retirar componentes indeseables como es el asfalto, después es hidrogenado para completar las cadenas de hidrocarburos y para homogenizarlo. Las tres clases básicas de aceites lubricantes minerales son:
- Los aceites Parafínicos, que representan más del 90% de las bases de aceites lubricantes derivados del petróleo que son producidas.
- Los aceites Neftánicos.
- Los aceites Aromáticos.
Los grados de los aceites lubricantes aplicados a nivel industrial son definidos por la ISO, designados como ISOVG (ISO Viscosity Grade). La ISO establece 18 grados de viscosidad para los aceites lubricantes industriales comprendidos entre 2 y 1500 cST referidos a una temperatura de 40 ºC (104 ºF). Esta clasificación no especifica la calidad del aceite, solamente establece la viscosidad cinemática correspondiente a cada grado para la temperatura de 40 ºC (104 ºF).
En las bombas centrífugas se utilizan principalmente los aceites lubricantes grados ISOVG 32 (viscosidad cinemática entre 28,8 y 35,20 SSU, equivalente a 1,5 a 2,56 cST), ISOVG 46 (viscosidad cinemática entre 41,40 y 50,60 SSU, equivalente a 4,30 a 7,40 cST), y el ISOVG 68 (viscosidad cinemática entre 61,2 y 74,8 SSU, equivalente a 10,3 a 14 cST).
13.3.1.- Porque se Degradan los Aceites Lubricantes Minerales
Los lubricantes derivados del petróleo tienen comportamientos aceptables hasta 105 °C (220 °F). Sobre los 66 °C (150 °F) los lubricantes minerales inician un proceso acelerado de oxidación que reduce la vida del aceite de forma acelerada.
La degradación del aceite mineral se produce básicamente por oxidación. El oxígeno se diluye en el aceite lubricante durante la dinámica de funcionamiento y circulación del lubricante en el sistema de lubricación, mezclándose con los componentes y aditivos del aceite. Está mezcla es favorecida por el incremento de temperatura y genera reacciones químicas para formar peróxidos, ácidos y residuos.
Como regla general se debe tener en consideración que los lubricantes derivados del petróleo tienen una vida de treinta años si opera a una temperatura de 30 °C (86 °F). Estos 30 años se reducen a la mitad cada 18 °F (10 °C) que se incrementa la temperatura de trabajo del aceite, es decir que a 40 ºC (104 °F) el aceite tendrá una vida esperada de 15 años; a 80 ºC (176 °F) tendrá una vida de once meses. A una temperatura de trabajo de 90 ºC (194 °F) el aceite durará solo cinco meses y medio, debido al incremento acelerado del deterioro del aceite por la oxidación y por la pérdida de propiedades con la viscosidad.
Otro elemento con gran influencia en la degradación de las propiedades de los aceites lubricantes es la presencia de agua en el aceite lubricante. El agua forma emulsiones, disminuye la viscosidad del aceite por dilución o por cambio de las propiedades, así como es un contribuyente a la corrosión de los componentes metálicos tales como cojinetes, ejes, cajera de cojinetes, etc.
Solo la contaminación del lubricante con 200 ppm de agua reduce la vida de los cojinetes de bolas a la mitad. Las principales fuentes de agua para contaminación de los cojinetes son las fugas de agua en las bombas, el agua proveniente de las actividades de limpieza de los equipos y de la aspiración de humedad del ambiente.
Es importante para prevenir la contaminación del aceite lubricante con agua mantener el sellado de las cajeras de cojinetes. En la actualidad el sellado de las cajeras se realiza con sellos de laberinto que garantizan mayor durabilidad (las partes móviles no tienen roce entre sí) y adicionalmente facilita el venteo de las cajeras de cojinetes. Algunos diseños de sellos de laberinto tienen configuraciones que le permiten, cuando son salpicados con agua, centrifugar el agua hacia la parte externa del sello evitando el ingreso de humedad en la cajera de cojinetes.
La principal desventaja de los sellos de laberinto es su costo inicial muy superior al de las estoperas y ya que permiten el contacto con el ambiente hacen la cajera de cojinetes sensible a las variaciones de temperatura y a la humedad.
En los diseños más antiguos de bombas centrífugas los elementos sellantes de las cajeras de cojinetes son las estoperas. La figura 13-7 muestra el corte de una estopera montada sobre un eje protegiendo un cojinete, es posible observar la ranura del eje donde desliza el labio de la estopera.
Las estoperas son anillos hechos generalmente de elastómeros combinados con partes metálicas, ellas poseen un labio que roza contra la superficie del eje.
Este labio tiene un resorte o muelle que genera una fuerza para mantener el ajuste del labio contra la ranura del eje. Como el labio roza constantemente contra la superficie del eje la vida de estos elementos antes de permitir fugas o fallar este alrededor de las 3.000 horas de operación.

Fuente: www.machinerylubrication.com/Read/932/labyrinth-seal
Es decir que la vida de la estopera se limita un poco más de cuatro meses de funcionamiento, lo cual entra en contradicción con la vida esperada del aceite lubricante y de los cojinetes que es mayor a un año. Los rangos temperatura en los cuales operan las estoperas es de entre 0 °C (32 °F) y 175 °C (380 °F).
Finalmente, el debilitamiento o dilución de los aditivos que posee el aceite también contribuye al deterioro y en la caída del rendimiento del aceite lubricante.
Para operara a temperaturas por arriba de 110 °C (230 °F) es recomendable la utilización de lubricantes con bases sintéticas.
13.3.2.- Aceites Sintéticos
El uso de los lubricantes sintéticos se ha extendido debido a las limitaciones que se observa en los lubricantes minerales en aplicaciones muy exigentes tales como operación en ambientes de muy baja temperatura, donde los lubricantes convencionales de base parafínica (representan más del 90% de los aceites minerales en el mercado) tienen tendencia a formar cera, la cual tapona los conductos de lubricación en los equipos y reduce las propiedades lubricantes del aceite.
Otra ventaja de los aceites sintéticos sobre los aceites lubricantes minerales es que el aceite mineral a altas temperaturas es afectado por altas ratas de oxidación, degradando el aceite a velocidades que incrementan las necesidades de cambio y mantenimiento de manera exponencial.
Los principales aceites sintéticos utilizados para lubricación son los PAOs (Polialfaoleofinas), los PAGs (Polialkalin Glicol), Diester y Silicón.
Los PAOs (Polialfaoleofinas), son los aceites sintéticos más usados en la actualidad tienen un precio alto pero moderado, excelente rendimiento con un reducido número de desventajas. Las ventajas de los PAOs son:
- Su alta resistencia a la oxidación;
- Gran estabilidad en presencia de agua;
- Muy buena estabilidad térmica;
- Alto Índice de Viscosidad(VI).
Este aceite resulta una muy buena selección para lubricar equipos que trabajan a temperaturas extremas, tanto a altas como a bajas temperaturas. Los principales aspectos negativos de los PAOs son:
- Su alto precio;
- La poca solubilidad con otros productos, como por ejemplo los aditivos.
Los aceites sintéticos PAGs (Polialkalin Glicol) tienen las siguientes ventajas:
- Excelente resistencia a la oxidación;
- Estabilidad térmica;
- Alto Índice de Viscosidad (IV).
- Gran capacidad de carga de la película lubricante;
- Bajo coeficiente de fricción, lo que genera ahorros en la energía consumida;
- Poca tendencia a generar residuos que pudiesen convertirse en depósitos indeseables.
Las principales desventajas de este aceite sintético son:
- Costo alto.
- Tendencia a ser hidrolíticamente inestable (tendencia a reaccionar con el agua).
Las propiedades de los aceites sintéticos Diesters es similar a la de los PAGs tienen como ventajas:
- resistencia a la oxidación;
- Alta estabilidad térmica;
- Alto Índice de Viscosidad (IV);
- Excepcional solubilidad. Por esta capacidad de solubilidad es usado como aditivo en los aceites sintéticos PAOs con la finalidad de ayudar a la dilución del paquete de aditivos necesarios en estos aceites.
- Excelente detergencia.
Los principales aspectos negativos de los Diesters son al igual que los PAGs:
- Alto costo;
- Tendencia a ser hidrolíticamente inestable.
Los aceites sintéticos a base de Silicón destacan por:
- Alto Índice de Viscosidad (IV);
- Alta estabilidad térmica;
- Muy buena resistencia a la oxidación;
Las principales desventajas de este aceite lubricante son:
- Altísimo precio;
- Poca capacidad para soportar cargas de deslizamiento, debido a su baja tensión superficial.
Al igual que en las grasas se realizó un estudio comparativo de los costos del aceite mineral con los costos de los aceites sintéticos. Para el análisis se utilizó como base de referencia un aceite mineral estándar al cual se le asignó el valor de uno (1), para comparar su precio el precio de los principales aceites sintéticos. La tabla N° 13-2 muestra la comparación entre los diferentes tipos de aceites.

Como ya se observó en el caso de las grasas la principal desventaja de los aceites sintéticos, tal como lo indica la tabla 13-2 son los costos de los productos, la diferencia del costo del aceite mineral con el más económico de ellos, en este caso los PAOs, es de 3 veces.
13.3.3.- Aditivos para Aceites Lubricates
Los aceites lubricantes modernos para aplicaciones industriales poseen un alto grado de contenido de aditivos que mejoran las propiedades y alargan la vida del aceite en servicio.
Los aditivos son agregados tanto a los aceites lubricantes minerales como a los aceites sintéticos. Los tipos y cantidades de aditivos a incluir en los lubricantes dependen del servicio previsto para el aceite. Los aditivos se agregan en los lubricantes como:
- Elementos Detergentes: y dispersantes, utilizados para suspender las partículas indeseables, controlar depósitos de sucio y prevenir corrosión.
- Antidesgaste: Para prevenir el desgaste excesivo en situaciones de lubricación limite por lo general se usa el Bisulfuro de Zinc como aditivo.
- Antioxidantes: son elementos que reaccionan con el exceso de oxigeno evitando la reacción química del aceite o sus componentes con el oxígeno y de esta forma retarda la formación de ácidos corrosivos.
- Mejoradores del Índice de Viscosidad: Para garantizar una viscosidad de trabajo uniforme a las diferentes temperaturas de operación.
- Inhibidores de Corrosión: Son elementos que reaccionan con los agentes corrosivos y contribuyen a pasivarlos.
- Antiespumantes:Cambian la tensión superficial de lubricante para facilitar la ruptura de las burbujas de aire.
- Extrema Presión (EP): Forman una capa protectora entre las superficies en movimiento ayudando al lubricante a soportar la carga
No se profundizará mucho más en las características de los diferentes aditivos ya que esta fuera del alcance del libro.
En la Industria Petrolera los principales métodos de lubricación son la lubricación por Baño de Aceite, lubricación por Anillo de Aceite, lubricación Forzada y la lubricación por Neblina.
13.3.4.- Lubricación por Baño de Aceite
El sistema de lubricación por aceite más sencillo aplicado a las bombas centrífugas equipadas con cojinetes de elementos rodantes es la lubricación por Baño de Aceite. En este sistema la caja de cojinetes tiene un reservorio en el cual se mantiene un nivel de aceite que cubre por completo o a medias las esferas inferiores del cojinete de elementos rodantes.
La figura N° 13-8 muestra el diagrama de una cajera de cojinetes para el sistema de lubricación por baño de aceite. En ella es posible observar que el nivel de aceite contenido en la cajera de cojinetes cubre la parte inferior del rodamiento en un baño permanente de aceite lubricante al cojinete, de allí su nombre.
El nivel de aceite lubricante es mantenido, usualmente, mediante un lubricador de nivel constante del tipo botella. Esta botella debe ser de vidrio resistente al calor, cubierta por una malla metálica, protectora y debe tener capacidad de al menos 120 ml (4 onzas).

Fuente: www.reliabilityweb.com/ee-assets/my-uploads/a…
En bombas de procesos desarrolladas partir de mediados de los años ochenta del siglo XX, se popularizó la eliminación de los lubricadores o botellas de lubricación, ya que este componente representa otro renglón que puede fallar al atascarse romperse y dar una perfección errónea del nivel real de lubricante existente en la bomba. Se sustituyó por un simple indicador de nivel, tipo “ojo de buey”, que en ocasiones tiene una un buen tamaño para facilitar la lectura. Este indicador de nivel tiene marcas para indicar cuando es necesario proceder a la reposición del aceite lubricante.
La figura N° 13-9 muestra el diagrama de un indicador de nivel tipo “ojo de buey” instalado en la cajera de cojinetes de una bomba centrifuga de procesos.

Fuente: http://mid-states-sales.com/product_detail.cfm/……
Otra mejora introducida en esta época es el incremento de la capacidad de las cajeras de cojinetes e incorporar aletas en la parte externa de la carcasa, ambas acciones con la finalidad de facilitar la disipación del calor transmitido al aceite lubricante.
Con estas mejoras se reemplazan los sistemas de enfriamiento por circulación de agua que se aplicaba en las cajeras de cojinetes en bombas de procesos. Por ser un sistema de lubricación simple y que requiere un mínimo de equipos es muy usado en bombas de baja energía aplicadas en servicios poco severos.
La norma ASMEB73.1, establece como sistema de lubricación preferencial la lubricación por inundación o baño de aceite.
En la práctica existen dos problemas comunes en este tipo de lubricación, el primero de ellos es el sobre nivel de aceite que puede producir espuma y sobre temperatura en el reservorio, debido al aumento de la fricción por mayor contacto del cojinete con el aceite lubricante. El otro problema observado es el bajo nivel que puede causar alta temperatura en el cojinete por disminución de la cantidad de aceite lubricante en contacto con el cojinete y pude producir hasta falla por insuficiencia de aceite.
La figura 13-10 muestra el nivel correcto de aceite que se debe dejar en una bomba que posee el sistema de lubricación por baño de aceite.

Fuente:www.reliableplant.com/Read/22602/api-centrifu…
El rango entre el alto nivel y el bajo nivel es pequeño resultando esta una característica sensible de este tipo de lubricación. De acuerdo con los especialistas el nivel de aceite debe cubrir como máximo la parte media de las bolas o elementos rodantes que se encuentran en la parte inferior del cojinete y como mínimo el nivel debe alcanzar la punta inferior de la bola que se encuentra en la parte inferior del cojinete.
13.3.5.- Lubricación por Anillo de Aceite
El sistema de lubricación por anillo de aceite se utiliza para lubricar bombas centrífugas de mayor energía a las bombas donde se aplica baño de aceite, las cuales tienen cojinetes de mayor superficie, donde el sistema de baño aceite no es suficiente para lograr una buena lubricación y para retirar el calor generado en la superficie de los cojinetes. También es aplicado en sistemas con cojinetes radiales planos donde es necesario la circulación de un mayor flujo de aceite en las superficies activas del cojinete.
Otra ventaja de este sistema de lubricación es que favorece la creación de una atmósfera que contiene partículas de aceite generadas por el movimiento del aceite lubricante en los anillos, lo cual inhibe la corrosión de la parte interna de la cajera de cojinetes.
Dependiendo de la configuración el sistema puede ser integrado por un solo anillo de lubricación o por dos anillos, todo esto condicionado por las necesidades de aceite lubricante de las cajas de cojinetes. Los anillos de aceite son colocados perpendiculares al eje en el área próxima a los cojinetes radiales y de empuje.
La lubricación por anillo de aceite funcionada de la siguiente forma: La punta de los anillos de aceite se encuentran sumergidas en el reservorio de aceite de la caja de cojinetes, cuando se acciona la bomba la rotación del eje mueve los anillos de aceite, transportando aceite desde el reservorio de aceite de la caja de cojinetes hasta el eje y los cojinetes. La figura N° 13-11 muestra una cajera de cojinetes para un sistema de lubricación por anillo de aceite.
Como regla general se debe limitar la aplicación de lubricación por anillo de aceite a equipos con velocidades superficiales, en el eje donde se aplica el anillo, inferiores a 3000 pies/minuto, por arriba de esta velocidad el aceite que sube por el anillo tiende a centrifugarse.

Fuente:www.gouldspumps.com/download_files/3700/GP_724-1_3700.pdf
El aceite movido por el anillo es recogido mediante deflectores, creando una atmósfera de aceite lubricando en cada cojinete, el aceite sobrante regresa al reservorio de la caja de cojinetes.
El nivel de aceite es mantenido mediante un lubricador de nivel constante o botella. Para que el sistema funcione adecuadamente el anillo debe mantenerse sumergido entre 6 y 12 mm (1/4 a 3/8 de pulgada) en el interior del aceite.
Los anillos son fabricados fundamentalmente de bronce y su diámetro debe ser de al menos 1,75 a 2,0 veces el diámetro del eje. El anillo debe ser perfectamente redondo, deformaciones y ovulaciones tan pequeñas como de 127mm (0,005 pulgadas) hacen que el anillo tienda a atascarse y pierda Eficiencia, causando una disminución del flujo de aceite hacia los cojinetes originando en muchos casos una elevación de la temperatura de operación del cojinete, reducción de la vida de los cojinetes y hasta fallas.
En algunas situaciones los anillos pueden dislocarse de las ranuras que los contienen a causa de vibración excesiva, bajo nivel de aceite en la cajera de cojinetes o deformación del mismo anillo, por esta razón se le colocan guías y topes en la cajera que obligan a los anillos a regresar a sus ranuras de trabajo. Las cajas de cojinetes para este sistema de lubricación tienen ventanas de inspección para verificar el funcionamiento del anillo de aceite y si los anillos están posicionados adecuadamente.
Cursos recomendados
-1730145694747.webp%3Falt%3Dmedia%26token%3D719f647e-063f-47e9-a9f4-c3b59cb3a8ab&w=3840&q=75)



%252FImagen%252Frcm-1730083250826.webp%3Falt%3Dmedia%26token%3D3775356a-7b11-4c44-b21f-45b3409fb9ed&w=3840&q=75)

%252FImagen%252FRAMPREDYC-1730060420837.webp%3Falt%3Dmedia%26token%3D2634a7f0-988e-4022-b91f-382503e6e9db&w=3840&q=75)

13.3.6.- Sistema de Lubricación Forzada
Para bombas centrífugas de altas cargas, alta energía y altas velocidades que por lo general son equipadas con cojinetes de empuje planos se debe aplicar un sistema de lubricación forzada, donde tanto el cojinete de empuje como los cojinetes radiales son alimentados por este sistema de lubricación. Estos sistemas de lubricación están en la clasificación de los sistemas hidrostáticos, donde la generación de la película de lubricación es ayudada por el suministro del lubricante a una determinada presión suministrada por una bomba externa.
Debido a los niveles de energía que manejan este tipo de bombas la película de lubricación ejerce también una función en la rotodinámica al estabilizar el rotor de la bomba donde es un pilar fundamental en la estabilidad del rotor. LaFigura N° 13-12 muestra el arreglo típico de una caja de cojinetes para el uso de la lubricación forzada.

Fuente:Pump HandBook-Igor J. Karassik, Joseph P. Messina, Paul Cooper, Charles C. Heald-McGraw Hill-Third Edition-2001.
En el diagrama es posible observar la bomba de lubricación principal que es accionada por el eje de la bomba centrífuga. Estas bombas son de tornillos o de engranajes. En el diagrama también son presentados los cojinetes radiales planos y los cojinetes de empuje de zapatas pivotantes.
Existen varios arreglos ya estandarizados a nivel industrial para los sistemas de lubricación forzada para bomba centrífugas, el más usado en la Industria Petrolera es el recomendado en el API 610/ISO 13709 11ava Edición, en el anexo B, “Cooling water and lubrication system schematics”, específicamente en la figura B.8 y la tabla B.1.
En el API se pide que el sistema de lubricación forzada debe cumplir también con los lineamientos de la ISO 10438-3“Petroleum, petrochemical and natural gas industries – Lubrication, shaft-sealing and control-oil systems and auxiliaries -Part 3: General-purpose oil Systems”. En esta norma se profundiza en las características constructivas del sistema de lubricación. En la figura B.10 se indica en un esquemático los principales componentes del sistema de lubricación y en la tabla B.1 se indican cuales elementos son opcionales y cuáles deben ser adicionados a las recomendaciones de la norma la ISO 10438-3.
Las exigencias de la ISO 10438-3 son bastante completas e intentan dar características de robustez al sistema de lubricación, esta norma es idéntica a la norma API 614“Lubrication, Shaft-sealing and Oil-control Systems and Auxiliaries”, la cual era usada como referencia hasta la 8va edición del API 610.
El direccionamiento básico del API 610 y de la norma ISO 10438-3 indican que el sistema debe tener un tanque de almacenamiento de aceite, una bomba de aceite lubricante accionada por la bomba centrífuga, una bomba auxiliar accionada con motor eléctrico, un enfriador para el aceite, un sistema de filtros dobles o “duplex”. La instrumentación para control y seguridad incluye una válvula de seguridad y de retención para cada bomba, interruptores de presión, indicadores de nivel del tanque, indicadores de presión e indicadores de temperatura.
El tanque de almacenamiento debe ser fabricado en acero inoxidable austenítico, con un tiempo de retención de al menos tres minutos, equipado con un indicador de nivel protegido o blindado preferiblemente del mismo material de fabricación del tanque. Para facilitar el flujo a través del tanque y dar garantía de suficiente tiempo de circulación y retención se deben colocar deflectores y pantallas dentro del tanque.
El fondo del tanque debe ser construido con una inclinación de 20 mm/m (0,25 pulgada/pie), además debe estar equipado con drenaje, respiradero protegido con maya y elemento de filtración para prevenir la ingestión de humedad y partículas extrañas. Los tanques para suministro de aceite de emergencia o “run down tank” pueden ser especificados para este tipo de sistemas, sin embargo, no están indicados como equipo obligatorio.
Este sistema de lubricación forzada incluye al menos dos bombas para la circulación del aceite una principal accionada por el eje de la bomba y una auxiliar generalmente accionada por motores eléctricos, la cual asegura un suministro continuo de aceite lubricante en caso de falla de la bomba principal. La bomba principal es de desplazamiento positivo y está instalada en el eje de la bomba a la cual lubrica. Los tipos de bomba más usados son las de engranajes y las de tornillos. Para velocidades menores a 1.800 RPM las bombas de engranajes ofrecen buen rendimiento, para velocidades mayores la mejor selección son las bombas de tornillos. El API 610 manifiesta que a nivel de industria los aceites lubricantes más usado tiene viscosidades ISO VG de entre 32 y 68.
La norma exige que los filtros deben ser dobles o “duplex”, con cartuchos reemplazables, resistentes a la corrosión un micronaje de 10mm, equipados con válvulas de transferencia para hacer el cambio de filtro sin parar el proceso. El sistema de filtrado no debe tener derivación o “Bypass” automático en caso de ensuciamiento del filtro. Para acompañar e indicar el ensuciamiento del filtro la norma recomienda instalar un indicador de presión diferencial.
La tubería tanto de circulación como de retorno de aceite debe ser tuberías sin costura, fabricada en acero inoxidable 304, 316 o equivalente.
Los enfriadores deben ser capaces de mantener la temperatura del aceite en 50 °C (120 °F), adicionalmente indica que si es especificado el arreglo de enfriadores puede ser doble. Haciendo la acotación que cada enfriador debe tener capacidad para trabajar con la carga térmica total del sistema. La Figura N. 13-13 muestra como es arreglo de un sistema de lubricación construido bajo las especificaciones del API 610/ISO 13709.
Tanto la bomba principal como la bomba auxiliar poseen válvulas de alivio o de seguridad que descargan al tanque principal. El sistema estándar está equipado con indicadores de presión, indicadores de flujo (sobre todo en la línea de drenaje). Por lo general tiene alarma por alta presión diferencial de los filtros, por baja presión de aceite lubricante y finalmente paro por baja presión de aceite.

Fuente:PUMP MAINTENANCE HANDBOOK,Lubrication Systemsfor RotatingEquipment, BY SCOTT HANSEN AND SAM HOPKINS
En el 95% de las aplicaciones típicas de la Industria Petrolera donde es necesario un sistema de lubricación forzada para bombas centrífugas es suficiente con la utilización del arreglo recomendado por el API 610/ISO 13709 y la ISO 10438-3.
13.3.7.- Lubricación por Neblina
La Lubricación por Neblina o “Oil Mist” es un sistema de lubricación en la cual se utiliza una mezcla de aire y aceite a presión que se inyecta como un aerosol directamente en el interior de la caja de cojinetes. Los sistemas de Lubricación por Neblina o “Oil Mist” fueron desarrollados en Europa en la década de los años 30 del siglo XX, para lubricar los molinos giratorios de alta velocidad utilizados en las siderurgias y procesadoras de metales. Estos molinos eran difíciles de lubricar con grasa, ya que la grasa se centrifugaba o con aceite ya que los molinos se recalentaban con la fricción y degradaban el aceite lubricante a un ritmo mayor al esperado.
Los sistemas de Lubricación por Neblina se han popularizado desde mediado de loa años 50 del siglo XX, debido a que representan un buen balance entre los costos de inversión, los costos de mantenimiento y la efectividad del sistema.
El sistema de Lubricación por Neblina consiste en una unidad generadora de Neblina con compresor de aire (en la actualidad se generalizó el uso del aire de instrumentos de las plantas), filtros, tanques de aceite, tuberías para transportar la neblina, instrumentación, reclasificadores, boquillas de distribución y bombas auxiliares. De la unidad generadora de neblina parten las tuberías para la distribución de la neblina y llegan las tuberías de retorno del aceite condensado.
En la década de los años ochenta se generalizó el uso de los recursos de aire de instrumento centralizado disponible en las plantas de procesos, logrando el reemplazo de los compresores dedicados para cada generador de neblina. Esta sustitución solo es posible en plantas donde el aire para instrumentos o servicios esté disponible, en sistemas para plantas pequeñas o sistemas aislados se continúa utilizando el compresor como parte del sistema de generación de neblina.
En los desarrollos iniciales de los generadores de neblina los compresores representaban el punto débil del sistema causando el paro de los sistemas si su confiabilidad era baja o la política de mantenimiento inadecuada, lo que dio una reputación con opiniones divididas entre los usuarios. La figura 13-14 muestra una consola de Lubricación por Neblina con las tuberías de distribución y colector ecológico.

Fuente:www.oilmistinstitute.com/imagens/image/….
La neblina lubricante es la dispersión de pequeñísimas gotas con tamaño de 1 a 3μm (entre 4×10-4 y 12×10-3pulgadas) suspendidas en el aire en una relación aire-aceite de 200.000 a 1. Esta relación aire-aceite hace que la mezcla se encuentre por debajo de los límites de inflamabilidad.
El sistema tiene muchas ventajas que favorecen su uso. Una sola consola puede atender un número importante de equipos, como por ejemplo en el área de proceso de una planta química o una refinería una consola puede generar la neblina lubricante para todas las bombas del sistema, incluyendo los motores eléctricos, turbinas a vapor (pequeñas) y cajas de engranajes.
Una desventaja evidente es que si falla el sistema de generación de Neblina afecta a una población importante de equipos, sin embargo, la disponibilidad de los sistemas que no tienen compresores de aire (los sistemas que usan el aire del sistema general de aire de instrumentos) es altísima, complementada con el uso de sistemas de redundantes. Por ejemplo, las consolas tienen dos tanques de aceite uno principal y otro auxiliar para facilitar el mantenimiento del tanque principal sin necesidad de parar la unidad, además que los sistemas de aire centrales permiten la continuidad de operación del sistema durante varios minutos luego de un paro del sistema, debido a los volúmenes de neblina y de aire contenidos en las tuberías.
Las gotas o la mezcla aire-aceite generadas por el sistema de Lubricación por Neblina son transportadas por un sistema de tuberías a los puntos de lubricación. Las tuberías principales por lo general son de dos (2) pulgadas de diámetro, fabricadas normalmente con hierro galvanizado, roscadas y unidas con conexiones en T donde se colocan los ramales de distribución que son de ¾ de pulgada de diámetro.
Las tuberías finalizan en la proximidad de los equipos a lubricar, en un múltiple donde se fijan las tuberías de acero inoxidable y los reclasificadores que llevan la neblina a las cajas de cojinetes. Los reclasificadores son unas boquillas que regulan el flujo de Neblina a cada cojinete, este volumen va a depender de las características y diámetro de la boquilla de cada reclasificador y de las necesidades de aceite de cada punto de lubricación.La figura N° 13-15 muestra el esquema de cómo sería el arreglo de tuberías para transportar la neblina a los equipos a lubricar.
La instalación del sistema de Lubricación por Neblina es crítico respecto a otros elementos del sistema. Si el sistema de distribución no es instalado correctamente y/o las juntas no están suficientemente ajustadas se propician las fugas y perdidas de fluidos en las tuberías de neblina, el gradiente de inclinación y los soportes para sostener las tuberías también son determinantes para el buen funcionamiento. La inclinación para ayudar al desplazamiento de la neblina y los soportes evitan deformaciones y la flexión en los tubos que favorecen la formación de bolsas de aceite lubricante que interrumpen el flujo de la neblina.

Fuente:www.machinerylubrication.com/read/326/……
El sistema de Lubricación por Neblina posee multipuntos de inyección que trabajan a baja presión, por el orden de 5 kPa (20 pulgadas de H2O). La presión positiva en la cajera de cojinetes evita la entrada de humedad y garantiza la impregnación de los cojinetes con la neblina de aceite.
El sistema provee venteos en la parte posterior de los cojinetes con lo que se garantiza que el aceite pase a través de todos los cojinetes. Un drenaje en el fondo de la caja de cojinetes permite drenar el aceite que se va condensando. La figura N° 13-16 muestra como es el flujo de Neblina en la caja de cojinetes de una bomba API 610.
El sistema de Lubricación por Neblina no es un sistema obligatorio en lo referente a las normas API 610/ISO 13709 y la ASME B73.1. Ambas normas dejan al usuario en libertad de especificar el sistema si lo considera necesario, solamente el API 610 establece unos cuidados específicos para reducir la temperatura a nivel de los cojinetes para servicios a altas temperaturas, específicamente cuando la temperatura superar los 300 °C (570 °F).

Fuente:www.reliability web/…../0609/lubrication.jpg
Entre las principales ventajas de este sistema está que crea en el interior de la caja de cojinetes un ambiente libre de contaminación y con una Neblina de aceite que permite retirar calor de los cojinetes.
Por las características del diseño los sistemas de Lubricación por Neblina utilizan menos aceite que los sistemas convencionales. Un estudio realizado en el estado Norte Americano de Texas determinó que es posible extender la vida de loscojinetes hasta en tres veces más que la vida esperada con los sistemas tradicionales.
La discusión entre los usuarios actuales es que estos sistemas requieren más atención que un sistema tradicional, sin embargo, la tecnología de Lubricación por Neblina de aceite o “Oil Mist” es madura y depurada. Los sistemas de Lubricación por Neblina de aceite o “Oil Mist” actuales poseen alarmas, instrumentos de control y otros recursos que minimizan las paradas imprevistas y la falla de los sistemas.
Existen esencialmente dos tipos de sistemas para la Lubricación por Neblina de aceite:
- El sistema de Neblina Pura o “Pure Mist”.
- El sistema de Neblina por Purga o “Purge Mist”.
13.3.7.1.- Lubricación por Neblina Pura o “Pure Mist”
El sistema de Lubricación por Neblina Pura o “Pure Mist” es el sistema de Lubricación por Neblina más usado es aplicado fundamentalmente a bombas equipadas con cojinetes antifricción. El sistema consiste en el suministro de neblina lubricante directamente a los cojinetes, es decir que no se mantiene un nivel de aceite en las cajeras de cojinetes, también son eliminados los anillos de lubricación, los lubricadores (botellas para mantener el nivel de aceite) y los deflectores de aceite. El aceite entra a la cajera de cojinetes, lubrica los cojinetes, luego se condensa en la cajera y es drenado por el fondo de la cajera al colector ecológico.
La Figura N° 13-17 muestra el diagrama de una bomba de succión frontal equipada con un sistema de Lubricación por Neblina Pura.

Fuente:Centrifugal Pump Handbook_Antifriction Bearings in Centrifugal Pumps_By Ed Nelson.
El sistema de Lubricación por Neblina Pura favorece el mantenimiento de las propiedades del aceite lubricante prolongando su vida útil, ya que, al limitar la exposición del aceite a las altas temperaturas relativas a periodos muy cortos de tiempo, lo que desacelera la pérdida de las propiedades y la oxidación del aceite.
Para el suministro de la neblina lubricadora a las cajeras de los cojinetes se deriva la línea de lubricación del múltiple hasta los reclasificadores instalados en cada cojinete. Los reclasificadores son boquillas de acero inoxidable que están dimensionadas para suministrar diferentes cantidades de neblina a las cajeras de cojinetes y de esta manera satisfacer las necesidades de neblina de cada cojinete. Para recoger el aceite que se condensa y que es drenado de la cajera de cojinetes se instala una botella o recipiente ecológico en el drenaje.
La figura 13-18 muestra una bomba centrífuga con sus conexiones para Lubricación por Neblina Pura.

Fuente:oilmistinstitute.com
En la figura 13-18 se observan los reclasificadores,el drenaje del fondo de la caja de cojinetes y el colector ecológico. La Lubricación por Neblina Pura es ampliamente usada para preservar equipos fuera de servicio como es el caso de los equipos que necesitan ser almacenados por largos periodos a la espera de ser instalados en alguna planta de procesos o refinería en construcción. También esta situación se presenta cuando una planta es retirada de servicio temporalmente por no necesitarse o para realizar reparaciones mayores y prolongadas en algunos equipos principales.
De hecho, algunas normas y prácticas de ingeniería como la API RP 686 en la sección 3.2.3 “General Instructions-Jobsite Protection”da como una opción válida el uso del “Oil Mist” en proyectos de cierta magnitud cuando más de 10 piezas deben estar almacenadas por más de seis meses esperando su instalación.
La figura 13-19 muestra como ejemplo de cómo puede ser instalado el sistema de Neblina pura en una bomba almacenada.

Fuente:oilmistinstitute.com
Como se observa en la figura 12-19 el sistema es muy sencillo de instalar en una bomba que se encuentra almacenada, ya que no es necesario desmontar el equipo lo que en algunos casos origina problemas debido a complicaciones con la reinstalación de las piezas y perdida de componentes, adicionalmente los equipos a preservar con esta técnica no requieren ser preparados especialmente por ejemplo llenar las cajas de cojinetes y carcasas con aceite anticorrosivo u otro tipo de fluido de preservación. Estos dos aspectos permiten que el equipo almacenado esté listo para su instalación inmediata sin necesidad de preparación adicional.
13.3.7.2.- Lubricación por Neblina por Purga o “Purge Mist”
En los sistemas de Lubricación por Neblina de Purga al igual que en los sistemas de Niebla Pura o “Pure Mist” se inyecta la Niebla lubricante por medio de boquillas o reclasificadores a los cojinetes. La diferencia que tiene este método con el de del Lubricación con Neblina Pura es que se mantiene el nivel de aceite en la cajera de cojinetes, así como los deflectores, los lubricadores y anillos de lubricación.
Este arreglo es comúnmente usado en bombas que están equipadas con cojinetes de deslizamiento o planos y en equipos dotados con cojinetes de rodamientos donde es difícil lubricarlos apropiadamente. Este flujo de aceite adicional no puede ser suministrado por ninguno de los arreglos de boquillas y de conexiones del sistema de Lubricación por Niebla Pura por esta razón se mantienen el nivel de aceite, los anillos de lubricación y el nivel de aceite para aumentar el flujo de aceite lubricante hacia los cojinetes.
La figura N° 13-20 muestra el diagrama de una bomba de succión frontal equipada con un sistema de Lubricación por Neblina de Purga o “Purge Mist”, allí es posible observar que se mantiene el nivel de aceite en la caja de cojinetes de la bomba, así como el deflector para el salpicado.

Fuente:Centrifugal Pump Handbook_Antifriction Bearings in Centrifugal Pumps_By Ed Nelson.
En la experiencia industrial este sistema de Lubricación por Neblina de Purga requiere bastante atención por parte del mantenimiento, debido a que por no ser vital la neblina para el funcionamiento de los cojinetes es descuidado por los operarios y mantenedores, ya que se mantiene el nivel de aceite en las cajeras; así como los anillos y deflectores, el mal funcionamiento del sistema de “Oil Mist” no genera una falla inmediata, pero desvirtúa el sentido de su utilización y elimina las posibles ventajas que significa su uso.
Tanto el ASME B73.1 como el API 610/ISO 13709 especifican la lubricación por aceite como el sistema preferencial de lubricación. El ASME B73.1 en la sección 4.7.5 Lubrication, indica que la lubricación por aceite es la lubricación estándar para las bombas fabricadas siguiendo esta norma principalmente el método de lubricación por baño de aceite, sin embargo, deja abiertaopciones para el uso de otros métodos de lubricación como la lubricación por Neblina de Aceite o “Oil Mist” y hasta lubricación por grasa.
En el API 610/ISO 13709 11ava edición en el capítulo 6.11. se indica que los cojinetes y las cajeras de cojinetes deben ser diseñadas para ser lubricadas con aceite mineral a menos que expresamente se indique lo contrario. Indicando también que si también es solicitado se deben dejar las previsiones para la instalación de sistemas de lubricación por niebla o de “Oil Mist”.
Los aceites minerales básicos son producidos a partir de la destilación del petróleo crudo, tomando como materia prima el residuo largo del proceso de destilación. En la destilación, el petróleo es separado en diferentes componentes usando para ello un calentamiento inicial en hornos que lleva al petróleo a varios cientos de grados de temperatura, lo que facilita la separación de los diferentes componentes que lo forman. El petróleo luego es bombeado a una torre de destilación atmosférica, que es la etapa inicial del proceso de destilación en las refinerías convencionales.
En este proceso de destilación los componentes más livianos son captados en el tope de la torre para producir gasolina y nafta, los componentes medianos son captados en las bandejas intermedias para producir diesel y gasóleo, el fondo de la torre es la fracción más pesada es calentado en hornos y bombeado a las torres de destilación al vacío.
El lubricante base es captado en las bandejas intermedias de la torre de destilación al vacío. Este lubricante base es tratado para retirar componentes indeseables como es el asfalto, después es hidrogenado para completar las cadenas de hidrocarburos y para homogenizarlo. Las tres clases básicas de aceites lubricantes minerales son:
- Los aceites Parafínicos, que representan más del 90% de las bases de aceites lubricantes derivados del petróleo que son producidas.
- Los aceites Neftánicos.
- Los aceites Aromáticos.
Los grados de los aceites lubricantes aplicados a nivel industrial son definidos por la ISO, designados como ISOVG (ISO Viscosity Grade). La ISO establece 18 grados de viscosidad para los aceites lubricantes industriales comprendidos entre 2 y 1500 cST referidos a una temperatura de 40 ºC (104 ºF). Esta clasificación no especifica la calidad del aceite, solamente establece la viscosidad cinemática correspondiente a cada grado para la temperatura de 40 ºC (104 ºF).
En las bombas centrífugas se utilizan principalmente los aceites lubricantes grados ISOVG 32 (viscosidad cinemática entre 28,8 y 35,20 SSU, equivalente a 1,5 a 2,56 cST), ISOVG 46 (viscosidad cinemática entre 41,40 y 50,60 SSU, equivalente a 4,30 a 7,40 cST), y el ISOVG 68 (viscosidad cinemática entre 61,2 y 74,8 SSU, equivalente a 10,3 a 14 cST).
Dinos qué te ha parecido el artículo
Artículos recomendados
8.1. Principios Básicos del Control de Procesos Industriales

1.2. Costos y productividad

Una guía elemental para la confiabilidad

Análisis de datos mediante regresión y modelos jerárquicos / multinivel

Publica tu artículo en la revista #1 de Mantenimiento Industrial
Publicar un artículo en la revista es gratis, no tiene costo.
Solo debes asegurarte que no sea un artículo comercial.
¿Qué esperas?
O envía tu artículo directo: articulos@predictiva21.com
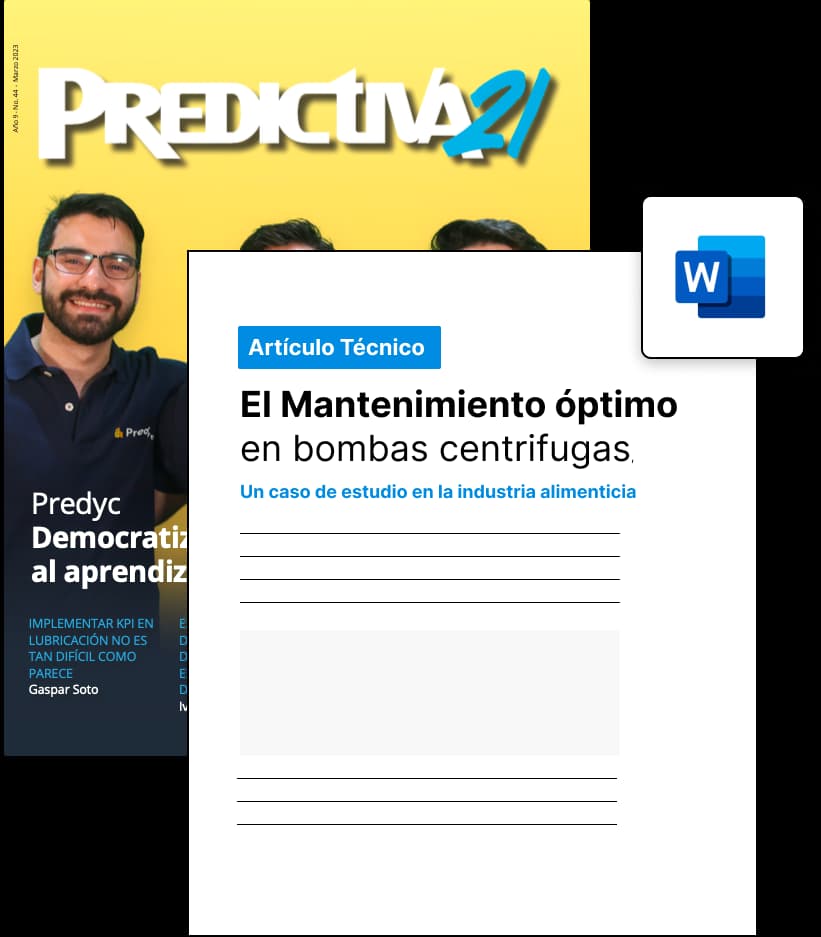
13.3.- Lubricación con Aceite
Libros 6 de septiembre de 2021Los sistemas de lubricación por aceite son los más usados en bombas de procesos de potencia media, alta y en bombas API 610/ISO 13709 de cualquier rango de potencia, porque garantiza mayor rendimiento de los rodamientos, en casi todos los servicios industriales.
Tanto el ASME B73.1 como el API 610/ISO 13709 especifican la lubricación por aceite como el sistema preferencial de lubricación. El ASME B73.1 en la sección 4.7.5 Lubrication, indica que la lubricación por aceite es la lubricación estándar para las bombas fabricadas siguiendo esta norma principalmente el método de lubricación por baño de aceite, sin embargo, deja abiertaopciones para el uso de otros métodos de lubricación como la lubricación por Neblina de Aceite o “Oil Mist” y hasta lubricación por grasa.
En el API 610/ISO 13709 11ava edición en el capítulo 6.11. se indica que los cojinetes y las cajeras de cojinetes deben ser diseñadas para ser lubricadas con aceite mineral a menos que expresamente se indique lo contrario. Indicando también que si también es solicitado se deben dejar las previsiones para la instalación de sistemas de lubricación por niebla o de “Oil Mist”.
Los aceites minerales básicos son producidos a partir de la destilación del petróleo crudo, tomando como materia prima el residuo largo del proceso de destilación. En la destilación, el petróleo es separado en diferentes componentes usando para ello un calentamiento inicial en hornos que lleva al petróleo a varios cientos de grados de temperatura, lo que facilita la separación de los diferentes componentes que lo forman. El petróleo luego es bombeado a una torre de destilación atmosférica, que es la etapa inicial del proceso de destilación en las refinerías convencionales.
En este proceso de destilación los componentes más livianos son captados en el tope de la torre para producir gasolina y nafta, los componentes medianos son captados en las bandejas intermedias para producir diesel y gasóleo, el fondo de la torre es la fracción más pesada es calentado en hornos y bombeado a las torres de destilación al vacío.
El lubricante base es captado en las bandejas intermedias de la torre de destilación al vacío. Este lubricante base es tratado para retirar componentes indeseables como es el asfalto, después es hidrogenado para completar las cadenas de hidrocarburos y para homogenizarlo. Las tres clases básicas de aceites lubricantes minerales son:
- Los aceites Parafínicos, que representan más del 90% de las bases de aceites lubricantes derivados del petróleo que son producidas.
- Los aceites Neftánicos.
- Los aceites Aromáticos.
Los grados de los aceites lubricantes aplicados a nivel industrial son definidos por la ISO, designados como ISOVG (ISO Viscosity Grade). La ISO establece 18 grados de viscosidad para los aceites lubricantes industriales comprendidos entre 2 y 1500 cST referidos a una temperatura de 40 ºC (104 ºF). Esta clasificación no especifica la calidad del aceite, solamente establece la viscosidad cinemática correspondiente a cada grado para la temperatura de 40 ºC (104 ºF).
En las bombas centrífugas se utilizan principalmente los aceites lubricantes grados ISOVG 32 (viscosidad cinemática entre 28,8 y 35,20 SSU, equivalente a 1,5 a 2,56 cST), ISOVG 46 (viscosidad cinemática entre 41,40 y 50,60 SSU, equivalente a 4,30 a 7,40 cST), y el ISOVG 68 (viscosidad cinemática entre 61,2 y 74,8 SSU, equivalente a 10,3 a 14 cST).
13.3.1.- Porque se Degradan los Aceites Lubricantes Minerales
Los lubricantes derivados del petróleo tienen comportamientos aceptables hasta 105 °C (220 °F). Sobre los 66 °C (150 °F) los lubricantes minerales inician un proceso acelerado de oxidación que reduce la vida del aceite de forma acelerada.
La degradación del aceite mineral se produce básicamente por oxidación. El oxígeno se diluye en el aceite lubricante durante la dinámica de funcionamiento y circulación del lubricante en el sistema de lubricación, mezclándose con los componentes y aditivos del aceite. Está mezcla es favorecida por el incremento de temperatura y genera reacciones químicas para formar peróxidos, ácidos y residuos.
Como regla general se debe tener en consideración que los lubricantes derivados del petróleo tienen una vida de treinta años si opera a una temperatura de 30 °C (86 °F). Estos 30 años se reducen a la mitad cada 18 °F (10 °C) que se incrementa la temperatura de trabajo del aceite, es decir que a 40 ºC (104 °F) el aceite tendrá una vida esperada de 15 años; a 80 ºC (176 °F) tendrá una vida de once meses. A una temperatura de trabajo de 90 ºC (194 °F) el aceite durará solo cinco meses y medio, debido al incremento acelerado del deterioro del aceite por la oxidación y por la pérdida de propiedades con la viscosidad.
Otro elemento con gran influencia en la degradación de las propiedades de los aceites lubricantes es la presencia de agua en el aceite lubricante. El agua forma emulsiones, disminuye la viscosidad del aceite por dilución o por cambio de las propiedades, así como es un contribuyente a la corrosión de los componentes metálicos tales como cojinetes, ejes, cajera de cojinetes, etc.
Solo la contaminación del lubricante con 200 ppm de agua reduce la vida de los cojinetes de bolas a la mitad. Las principales fuentes de agua para contaminación de los cojinetes son las fugas de agua en las bombas, el agua proveniente de las actividades de limpieza de los equipos y de la aspiración de humedad del ambiente.
Es importante para prevenir la contaminación del aceite lubricante con agua mantener el sellado de las cajeras de cojinetes. En la actualidad el sellado de las cajeras se realiza con sellos de laberinto que garantizan mayor durabilidad (las partes móviles no tienen roce entre sí) y adicionalmente facilita el venteo de las cajeras de cojinetes. Algunos diseños de sellos de laberinto tienen configuraciones que le permiten, cuando son salpicados con agua, centrifugar el agua hacia la parte externa del sello evitando el ingreso de humedad en la cajera de cojinetes.
La principal desventaja de los sellos de laberinto es su costo inicial muy superior al de las estoperas y ya que permiten el contacto con el ambiente hacen la cajera de cojinetes sensible a las variaciones de temperatura y a la humedad.
En los diseños más antiguos de bombas centrífugas los elementos sellantes de las cajeras de cojinetes son las estoperas. La figura 13-7 muestra el corte de una estopera montada sobre un eje protegiendo un cojinete, es posible observar la ranura del eje donde desliza el labio de la estopera.
Las estoperas son anillos hechos generalmente de elastómeros combinados con partes metálicas, ellas poseen un labio que roza contra la superficie del eje.
Este labio tiene un resorte o muelle que genera una fuerza para mantener el ajuste del labio contra la ranura del eje. Como el labio roza constantemente contra la superficie del eje la vida de estos elementos antes de permitir fugas o fallar este alrededor de las 3.000 horas de operación.

Fuente: www.machinerylubrication.com/Read/932/labyrinth-seal
Es decir que la vida de la estopera se limita un poco más de cuatro meses de funcionamiento, lo cual entra en contradicción con la vida esperada del aceite lubricante y de los cojinetes que es mayor a un año. Los rangos temperatura en los cuales operan las estoperas es de entre 0 °C (32 °F) y 175 °C (380 °F).
Finalmente, el debilitamiento o dilución de los aditivos que posee el aceite también contribuye al deterioro y en la caída del rendimiento del aceite lubricante.
Para operara a temperaturas por arriba de 110 °C (230 °F) es recomendable la utilización de lubricantes con bases sintéticas.
13.3.2.- Aceites Sintéticos
El uso de los lubricantes sintéticos se ha extendido debido a las limitaciones que se observa en los lubricantes minerales en aplicaciones muy exigentes tales como operación en ambientes de muy baja temperatura, donde los lubricantes convencionales de base parafínica (representan más del 90% de los aceites minerales en el mercado) tienen tendencia a formar cera, la cual tapona los conductos de lubricación en los equipos y reduce las propiedades lubricantes del aceite.
Otra ventaja de los aceites sintéticos sobre los aceites lubricantes minerales es que el aceite mineral a altas temperaturas es afectado por altas ratas de oxidación, degradando el aceite a velocidades que incrementan las necesidades de cambio y mantenimiento de manera exponencial.
Los principales aceites sintéticos utilizados para lubricación son los PAOs (Polialfaoleofinas), los PAGs (Polialkalin Glicol), Diester y Silicón.
Los PAOs (Polialfaoleofinas), son los aceites sintéticos más usados en la actualidad tienen un precio alto pero moderado, excelente rendimiento con un reducido número de desventajas. Las ventajas de los PAOs son:
- Su alta resistencia a la oxidación;
- Gran estabilidad en presencia de agua;
- Muy buena estabilidad térmica;
- Alto Índice de Viscosidad(VI).
Este aceite resulta una muy buena selección para lubricar equipos que trabajan a temperaturas extremas, tanto a altas como a bajas temperaturas. Los principales aspectos negativos de los PAOs son:
- Su alto precio;
- La poca solubilidad con otros productos, como por ejemplo los aditivos.
Los aceites sintéticos PAGs (Polialkalin Glicol) tienen las siguientes ventajas:
- Excelente resistencia a la oxidación;
- Estabilidad térmica;
- Alto Índice de Viscosidad (IV).
- Gran capacidad de carga de la película lubricante;
- Bajo coeficiente de fricción, lo que genera ahorros en la energía consumida;
- Poca tendencia a generar residuos que pudiesen convertirse en depósitos indeseables.
Las principales desventajas de este aceite sintético son:
- Costo alto.
- Tendencia a ser hidrolíticamente inestable (tendencia a reaccionar con el agua).
Las propiedades de los aceites sintéticos Diesters es similar a la de los PAGs tienen como ventajas:
- resistencia a la oxidación;
- Alta estabilidad térmica;
- Alto Índice de Viscosidad (IV);
- Excepcional solubilidad. Por esta capacidad de solubilidad es usado como aditivo en los aceites sintéticos PAOs con la finalidad de ayudar a la dilución del paquete de aditivos necesarios en estos aceites.
- Excelente detergencia.
Los principales aspectos negativos de los Diesters son al igual que los PAGs:
- Alto costo;
- Tendencia a ser hidrolíticamente inestable.
Los aceites sintéticos a base de Silicón destacan por:
- Alto Índice de Viscosidad (IV);
- Alta estabilidad térmica;
- Muy buena resistencia a la oxidación;
Las principales desventajas de este aceite lubricante son:
- Altísimo precio;
- Poca capacidad para soportar cargas de deslizamiento, debido a su baja tensión superficial.
Al igual que en las grasas se realizó un estudio comparativo de los costos del aceite mineral con los costos de los aceites sintéticos. Para el análisis se utilizó como base de referencia un aceite mineral estándar al cual se le asignó el valor de uno (1), para comparar su precio el precio de los principales aceites sintéticos. La tabla N° 13-2 muestra la comparación entre los diferentes tipos de aceites.

Como ya se observó en el caso de las grasas la principal desventaja de los aceites sintéticos, tal como lo indica la tabla 13-2 son los costos de los productos, la diferencia del costo del aceite mineral con el más económico de ellos, en este caso los PAOs, es de 3 veces.
13.3.3.- Aditivos para Aceites Lubricates
Los aceites lubricantes modernos para aplicaciones industriales poseen un alto grado de contenido de aditivos que mejoran las propiedades y alargan la vida del aceite en servicio.
Los aditivos son agregados tanto a los aceites lubricantes minerales como a los aceites sintéticos. Los tipos y cantidades de aditivos a incluir en los lubricantes dependen del servicio previsto para el aceite. Los aditivos se agregan en los lubricantes como:
- Elementos Detergentes: y dispersantes, utilizados para suspender las partículas indeseables, controlar depósitos de sucio y prevenir corrosión.
- Antidesgaste: Para prevenir el desgaste excesivo en situaciones de lubricación limite por lo general se usa el Bisulfuro de Zinc como aditivo.
- Antioxidantes: son elementos que reaccionan con el exceso de oxigeno evitando la reacción química del aceite o sus componentes con el oxígeno y de esta forma retarda la formación de ácidos corrosivos.
- Mejoradores del Índice de Viscosidad: Para garantizar una viscosidad de trabajo uniforme a las diferentes temperaturas de operación.
- Inhibidores de Corrosión: Son elementos que reaccionan con los agentes corrosivos y contribuyen a pasivarlos.
- Antiespumantes:Cambian la tensión superficial de lubricante para facilitar la ruptura de las burbujas de aire.
- Extrema Presión (EP): Forman una capa protectora entre las superficies en movimiento ayudando al lubricante a soportar la carga
No se profundizará mucho más en las características de los diferentes aditivos ya que esta fuera del alcance del libro.
En la Industria Petrolera los principales métodos de lubricación son la lubricación por Baño de Aceite, lubricación por Anillo de Aceite, lubricación Forzada y la lubricación por Neblina.
13.3.4.- Lubricación por Baño de Aceite
El sistema de lubricación por aceite más sencillo aplicado a las bombas centrífugas equipadas con cojinetes de elementos rodantes es la lubricación por Baño de Aceite. En este sistema la caja de cojinetes tiene un reservorio en el cual se mantiene un nivel de aceite que cubre por completo o a medias las esferas inferiores del cojinete de elementos rodantes.
La figura N° 13-8 muestra el diagrama de una cajera de cojinetes para el sistema de lubricación por baño de aceite. En ella es posible observar que el nivel de aceite contenido en la cajera de cojinetes cubre la parte inferior del rodamiento en un baño permanente de aceite lubricante al cojinete, de allí su nombre.
El nivel de aceite lubricante es mantenido, usualmente, mediante un lubricador de nivel constante del tipo botella. Esta botella debe ser de vidrio resistente al calor, cubierta por una malla metálica, protectora y debe tener capacidad de al menos 120 ml (4 onzas).

Fuente: www.reliabilityweb.com/ee-assets/my-uploads/a…
En bombas de procesos desarrolladas partir de mediados de los años ochenta del siglo XX, se popularizó la eliminación de los lubricadores o botellas de lubricación, ya que este componente representa otro renglón que puede fallar al atascarse romperse y dar una perfección errónea del nivel real de lubricante existente en la bomba. Se sustituyó por un simple indicador de nivel, tipo “ojo de buey”, que en ocasiones tiene una un buen tamaño para facilitar la lectura. Este indicador de nivel tiene marcas para indicar cuando es necesario proceder a la reposición del aceite lubricante.
La figura N° 13-9 muestra el diagrama de un indicador de nivel tipo “ojo de buey” instalado en la cajera de cojinetes de una bomba centrifuga de procesos.

Fuente: http://mid-states-sales.com/product_detail.cfm/……
Otra mejora introducida en esta época es el incremento de la capacidad de las cajeras de cojinetes e incorporar aletas en la parte externa de la carcasa, ambas acciones con la finalidad de facilitar la disipación del calor transmitido al aceite lubricante.
Con estas mejoras se reemplazan los sistemas de enfriamiento por circulación de agua que se aplicaba en las cajeras de cojinetes en bombas de procesos. Por ser un sistema de lubricación simple y que requiere un mínimo de equipos es muy usado en bombas de baja energía aplicadas en servicios poco severos.
La norma ASMEB73.1, establece como sistema de lubricación preferencial la lubricación por inundación o baño de aceite.
En la práctica existen dos problemas comunes en este tipo de lubricación, el primero de ellos es el sobre nivel de aceite que puede producir espuma y sobre temperatura en el reservorio, debido al aumento de la fricción por mayor contacto del cojinete con el aceite lubricante. El otro problema observado es el bajo nivel que puede causar alta temperatura en el cojinete por disminución de la cantidad de aceite lubricante en contacto con el cojinete y pude producir hasta falla por insuficiencia de aceite.
La figura 13-10 muestra el nivel correcto de aceite que se debe dejar en una bomba que posee el sistema de lubricación por baño de aceite.

Fuente:www.reliableplant.com/Read/22602/api-centrifu…
El rango entre el alto nivel y el bajo nivel es pequeño resultando esta una característica sensible de este tipo de lubricación. De acuerdo con los especialistas el nivel de aceite debe cubrir como máximo la parte media de las bolas o elementos rodantes que se encuentran en la parte inferior del cojinete y como mínimo el nivel debe alcanzar la punta inferior de la bola que se encuentra en la parte inferior del cojinete.
13.3.5.- Lubricación por Anillo de Aceite
El sistema de lubricación por anillo de aceite se utiliza para lubricar bombas centrífugas de mayor energía a las bombas donde se aplica baño de aceite, las cuales tienen cojinetes de mayor superficie, donde el sistema de baño aceite no es suficiente para lograr una buena lubricación y para retirar el calor generado en la superficie de los cojinetes. También es aplicado en sistemas con cojinetes radiales planos donde es necesario la circulación de un mayor flujo de aceite en las superficies activas del cojinete.
Otra ventaja de este sistema de lubricación es que favorece la creación de una atmósfera que contiene partículas de aceite generadas por el movimiento del aceite lubricante en los anillos, lo cual inhibe la corrosión de la parte interna de la cajera de cojinetes.
Dependiendo de la configuración el sistema puede ser integrado por un solo anillo de lubricación o por dos anillos, todo esto condicionado por las necesidades de aceite lubricante de las cajas de cojinetes. Los anillos de aceite son colocados perpendiculares al eje en el área próxima a los cojinetes radiales y de empuje.
La lubricación por anillo de aceite funcionada de la siguiente forma: La punta de los anillos de aceite se encuentran sumergidas en el reservorio de aceite de la caja de cojinetes, cuando se acciona la bomba la rotación del eje mueve los anillos de aceite, transportando aceite desde el reservorio de aceite de la caja de cojinetes hasta el eje y los cojinetes. La figura N° 13-11 muestra una cajera de cojinetes para un sistema de lubricación por anillo de aceite.
Como regla general se debe limitar la aplicación de lubricación por anillo de aceite a equipos con velocidades superficiales, en el eje donde se aplica el anillo, inferiores a 3000 pies/minuto, por arriba de esta velocidad el aceite que sube por el anillo tiende a centrifugarse.

Fuente:www.gouldspumps.com/download_files/3700/GP_724-1_3700.pdf
El aceite movido por el anillo es recogido mediante deflectores, creando una atmósfera de aceite lubricando en cada cojinete, el aceite sobrante regresa al reservorio de la caja de cojinetes.
El nivel de aceite es mantenido mediante un lubricador de nivel constante o botella. Para que el sistema funcione adecuadamente el anillo debe mantenerse sumergido entre 6 y 12 mm (1/4 a 3/8 de pulgada) en el interior del aceite.
Los anillos son fabricados fundamentalmente de bronce y su diámetro debe ser de al menos 1,75 a 2,0 veces el diámetro del eje. El anillo debe ser perfectamente redondo, deformaciones y ovulaciones tan pequeñas como de 127mm (0,005 pulgadas) hacen que el anillo tienda a atascarse y pierda Eficiencia, causando una disminución del flujo de aceite hacia los cojinetes originando en muchos casos una elevación de la temperatura de operación del cojinete, reducción de la vida de los cojinetes y hasta fallas.
En algunas situaciones los anillos pueden dislocarse de las ranuras que los contienen a causa de vibración excesiva, bajo nivel de aceite en la cajera de cojinetes o deformación del mismo anillo, por esta razón se le colocan guías y topes en la cajera que obligan a los anillos a regresar a sus ranuras de trabajo. Las cajas de cojinetes para este sistema de lubricación tienen ventanas de inspección para verificar el funcionamiento del anillo de aceite y si los anillos están posicionados adecuadamente.
Cursos recomendados
-1730145694747.webp%3Falt%3Dmedia%26token%3D719f647e-063f-47e9-a9f4-c3b59cb3a8ab&w=3840&q=75)



%252FImagen%252Frcm-1730083250826.webp%3Falt%3Dmedia%26token%3D3775356a-7b11-4c44-b21f-45b3409fb9ed&w=3840&q=75)

%252FImagen%252FRAMPREDYC-1730060420837.webp%3Falt%3Dmedia%26token%3D2634a7f0-988e-4022-b91f-382503e6e9db&w=3840&q=75)

13.3.6.- Sistema de Lubricación Forzada
Para bombas centrífugas de altas cargas, alta energía y altas velocidades que por lo general son equipadas con cojinetes de empuje planos se debe aplicar un sistema de lubricación forzada, donde tanto el cojinete de empuje como los cojinetes radiales son alimentados por este sistema de lubricación. Estos sistemas de lubricación están en la clasificación de los sistemas hidrostáticos, donde la generación de la película de lubricación es ayudada por el suministro del lubricante a una determinada presión suministrada por una bomba externa.
Debido a los niveles de energía que manejan este tipo de bombas la película de lubricación ejerce también una función en la rotodinámica al estabilizar el rotor de la bomba donde es un pilar fundamental en la estabilidad del rotor. LaFigura N° 13-12 muestra el arreglo típico de una caja de cojinetes para el uso de la lubricación forzada.

Fuente:Pump HandBook-Igor J. Karassik, Joseph P. Messina, Paul Cooper, Charles C. Heald-McGraw Hill-Third Edition-2001.
En el diagrama es posible observar la bomba de lubricación principal que es accionada por el eje de la bomba centrífuga. Estas bombas son de tornillos o de engranajes. En el diagrama también son presentados los cojinetes radiales planos y los cojinetes de empuje de zapatas pivotantes.
Existen varios arreglos ya estandarizados a nivel industrial para los sistemas de lubricación forzada para bomba centrífugas, el más usado en la Industria Petrolera es el recomendado en el API 610/ISO 13709 11ava Edición, en el anexo B, “Cooling water and lubrication system schematics”, específicamente en la figura B.8 y la tabla B.1.
En el API se pide que el sistema de lubricación forzada debe cumplir también con los lineamientos de la ISO 10438-3“Petroleum, petrochemical and natural gas industries – Lubrication, shaft-sealing and control-oil systems and auxiliaries -Part 3: General-purpose oil Systems”. En esta norma se profundiza en las características constructivas del sistema de lubricación. En la figura B.10 se indica en un esquemático los principales componentes del sistema de lubricación y en la tabla B.1 se indican cuales elementos son opcionales y cuáles deben ser adicionados a las recomendaciones de la norma la ISO 10438-3.
Las exigencias de la ISO 10438-3 son bastante completas e intentan dar características de robustez al sistema de lubricación, esta norma es idéntica a la norma API 614“Lubrication, Shaft-sealing and Oil-control Systems and Auxiliaries”, la cual era usada como referencia hasta la 8va edición del API 610.
El direccionamiento básico del API 610 y de la norma ISO 10438-3 indican que el sistema debe tener un tanque de almacenamiento de aceite, una bomba de aceite lubricante accionada por la bomba centrífuga, una bomba auxiliar accionada con motor eléctrico, un enfriador para el aceite, un sistema de filtros dobles o “duplex”. La instrumentación para control y seguridad incluye una válvula de seguridad y de retención para cada bomba, interruptores de presión, indicadores de nivel del tanque, indicadores de presión e indicadores de temperatura.
El tanque de almacenamiento debe ser fabricado en acero inoxidable austenítico, con un tiempo de retención de al menos tres minutos, equipado con un indicador de nivel protegido o blindado preferiblemente del mismo material de fabricación del tanque. Para facilitar el flujo a través del tanque y dar garantía de suficiente tiempo de circulación y retención se deben colocar deflectores y pantallas dentro del tanque.
El fondo del tanque debe ser construido con una inclinación de 20 mm/m (0,25 pulgada/pie), además debe estar equipado con drenaje, respiradero protegido con maya y elemento de filtración para prevenir la ingestión de humedad y partículas extrañas. Los tanques para suministro de aceite de emergencia o “run down tank” pueden ser especificados para este tipo de sistemas, sin embargo, no están indicados como equipo obligatorio.
Este sistema de lubricación forzada incluye al menos dos bombas para la circulación del aceite una principal accionada por el eje de la bomba y una auxiliar generalmente accionada por motores eléctricos, la cual asegura un suministro continuo de aceite lubricante en caso de falla de la bomba principal. La bomba principal es de desplazamiento positivo y está instalada en el eje de la bomba a la cual lubrica. Los tipos de bomba más usados son las de engranajes y las de tornillos. Para velocidades menores a 1.800 RPM las bombas de engranajes ofrecen buen rendimiento, para velocidades mayores la mejor selección son las bombas de tornillos. El API 610 manifiesta que a nivel de industria los aceites lubricantes más usado tiene viscosidades ISO VG de entre 32 y 68.
La norma exige que los filtros deben ser dobles o “duplex”, con cartuchos reemplazables, resistentes a la corrosión un micronaje de 10mm, equipados con válvulas de transferencia para hacer el cambio de filtro sin parar el proceso. El sistema de filtrado no debe tener derivación o “Bypass” automático en caso de ensuciamiento del filtro. Para acompañar e indicar el ensuciamiento del filtro la norma recomienda instalar un indicador de presión diferencial.
La tubería tanto de circulación como de retorno de aceite debe ser tuberías sin costura, fabricada en acero inoxidable 304, 316 o equivalente.
Los enfriadores deben ser capaces de mantener la temperatura del aceite en 50 °C (120 °F), adicionalmente indica que si es especificado el arreglo de enfriadores puede ser doble. Haciendo la acotación que cada enfriador debe tener capacidad para trabajar con la carga térmica total del sistema. La Figura N. 13-13 muestra como es arreglo de un sistema de lubricación construido bajo las especificaciones del API 610/ISO 13709.
Tanto la bomba principal como la bomba auxiliar poseen válvulas de alivio o de seguridad que descargan al tanque principal. El sistema estándar está equipado con indicadores de presión, indicadores de flujo (sobre todo en la línea de drenaje). Por lo general tiene alarma por alta presión diferencial de los filtros, por baja presión de aceite lubricante y finalmente paro por baja presión de aceite.

Fuente:PUMP MAINTENANCE HANDBOOK,Lubrication Systemsfor RotatingEquipment, BY SCOTT HANSEN AND SAM HOPKINS
En el 95% de las aplicaciones típicas de la Industria Petrolera donde es necesario un sistema de lubricación forzada para bombas centrífugas es suficiente con la utilización del arreglo recomendado por el API 610/ISO 13709 y la ISO 10438-3.
13.3.7.- Lubricación por Neblina
La Lubricación por Neblina o “Oil Mist” es un sistema de lubricación en la cual se utiliza una mezcla de aire y aceite a presión que se inyecta como un aerosol directamente en el interior de la caja de cojinetes. Los sistemas de Lubricación por Neblina o “Oil Mist” fueron desarrollados en Europa en la década de los años 30 del siglo XX, para lubricar los molinos giratorios de alta velocidad utilizados en las siderurgias y procesadoras de metales. Estos molinos eran difíciles de lubricar con grasa, ya que la grasa se centrifugaba o con aceite ya que los molinos se recalentaban con la fricción y degradaban el aceite lubricante a un ritmo mayor al esperado.
Los sistemas de Lubricación por Neblina se han popularizado desde mediado de loa años 50 del siglo XX, debido a que representan un buen balance entre los costos de inversión, los costos de mantenimiento y la efectividad del sistema.
El sistema de Lubricación por Neblina consiste en una unidad generadora de Neblina con compresor de aire (en la actualidad se generalizó el uso del aire de instrumentos de las plantas), filtros, tanques de aceite, tuberías para transportar la neblina, instrumentación, reclasificadores, boquillas de distribución y bombas auxiliares. De la unidad generadora de neblina parten las tuberías para la distribución de la neblina y llegan las tuberías de retorno del aceite condensado.
En la década de los años ochenta se generalizó el uso de los recursos de aire de instrumento centralizado disponible en las plantas de procesos, logrando el reemplazo de los compresores dedicados para cada generador de neblina. Esta sustitución solo es posible en plantas donde el aire para instrumentos o servicios esté disponible, en sistemas para plantas pequeñas o sistemas aislados se continúa utilizando el compresor como parte del sistema de generación de neblina.
En los desarrollos iniciales de los generadores de neblina los compresores representaban el punto débil del sistema causando el paro de los sistemas si su confiabilidad era baja o la política de mantenimiento inadecuada, lo que dio una reputación con opiniones divididas entre los usuarios. La figura 13-14 muestra una consola de Lubricación por Neblina con las tuberías de distribución y colector ecológico.

Fuente:www.oilmistinstitute.com/imagens/image/….
La neblina lubricante es la dispersión de pequeñísimas gotas con tamaño de 1 a 3μm (entre 4×10-4 y 12×10-3pulgadas) suspendidas en el aire en una relación aire-aceite de 200.000 a 1. Esta relación aire-aceite hace que la mezcla se encuentre por debajo de los límites de inflamabilidad.
El sistema tiene muchas ventajas que favorecen su uso. Una sola consola puede atender un número importante de equipos, como por ejemplo en el área de proceso de una planta química o una refinería una consola puede generar la neblina lubricante para todas las bombas del sistema, incluyendo los motores eléctricos, turbinas a vapor (pequeñas) y cajas de engranajes.
Una desventaja evidente es que si falla el sistema de generación de Neblina afecta a una población importante de equipos, sin embargo, la disponibilidad de los sistemas que no tienen compresores de aire (los sistemas que usan el aire del sistema general de aire de instrumentos) es altísima, complementada con el uso de sistemas de redundantes. Por ejemplo, las consolas tienen dos tanques de aceite uno principal y otro auxiliar para facilitar el mantenimiento del tanque principal sin necesidad de parar la unidad, además que los sistemas de aire centrales permiten la continuidad de operación del sistema durante varios minutos luego de un paro del sistema, debido a los volúmenes de neblina y de aire contenidos en las tuberías.
Las gotas o la mezcla aire-aceite generadas por el sistema de Lubricación por Neblina son transportadas por un sistema de tuberías a los puntos de lubricación. Las tuberías principales por lo general son de dos (2) pulgadas de diámetro, fabricadas normalmente con hierro galvanizado, roscadas y unidas con conexiones en T donde se colocan los ramales de distribución que son de ¾ de pulgada de diámetro.
Las tuberías finalizan en la proximidad de los equipos a lubricar, en un múltiple donde se fijan las tuberías de acero inoxidable y los reclasificadores que llevan la neblina a las cajas de cojinetes. Los reclasificadores son unas boquillas que regulan el flujo de Neblina a cada cojinete, este volumen va a depender de las características y diámetro de la boquilla de cada reclasificador y de las necesidades de aceite de cada punto de lubricación.La figura N° 13-15 muestra el esquema de cómo sería el arreglo de tuberías para transportar la neblina a los equipos a lubricar.
La instalación del sistema de Lubricación por Neblina es crítico respecto a otros elementos del sistema. Si el sistema de distribución no es instalado correctamente y/o las juntas no están suficientemente ajustadas se propician las fugas y perdidas de fluidos en las tuberías de neblina, el gradiente de inclinación y los soportes para sostener las tuberías también son determinantes para el buen funcionamiento. La inclinación para ayudar al desplazamiento de la neblina y los soportes evitan deformaciones y la flexión en los tubos que favorecen la formación de bolsas de aceite lubricante que interrumpen el flujo de la neblina.

Fuente:www.machinerylubrication.com/read/326/……
El sistema de Lubricación por Neblina posee multipuntos de inyección que trabajan a baja presión, por el orden de 5 kPa (20 pulgadas de H2O). La presión positiva en la cajera de cojinetes evita la entrada de humedad y garantiza la impregnación de los cojinetes con la neblina de aceite.
El sistema provee venteos en la parte posterior de los cojinetes con lo que se garantiza que el aceite pase a través de todos los cojinetes. Un drenaje en el fondo de la caja de cojinetes permite drenar el aceite que se va condensando. La figura N° 13-16 muestra como es el flujo de Neblina en la caja de cojinetes de una bomba API 610.
El sistema de Lubricación por Neblina no es un sistema obligatorio en lo referente a las normas API 610/ISO 13709 y la ASME B73.1. Ambas normas dejan al usuario en libertad de especificar el sistema si lo considera necesario, solamente el API 610 establece unos cuidados específicos para reducir la temperatura a nivel de los cojinetes para servicios a altas temperaturas, específicamente cuando la temperatura superar los 300 °C (570 °F).

Fuente:www.reliability web/…../0609/lubrication.jpg
Entre las principales ventajas de este sistema está que crea en el interior de la caja de cojinetes un ambiente libre de contaminación y con una Neblina de aceite que permite retirar calor de los cojinetes.
Por las características del diseño los sistemas de Lubricación por Neblina utilizan menos aceite que los sistemas convencionales. Un estudio realizado en el estado Norte Americano de Texas determinó que es posible extender la vida de loscojinetes hasta en tres veces más que la vida esperada con los sistemas tradicionales.
La discusión entre los usuarios actuales es que estos sistemas requieren más atención que un sistema tradicional, sin embargo, la tecnología de Lubricación por Neblina de aceite o “Oil Mist” es madura y depurada. Los sistemas de Lubricación por Neblina de aceite o “Oil Mist” actuales poseen alarmas, instrumentos de control y otros recursos que minimizan las paradas imprevistas y la falla de los sistemas.
Existen esencialmente dos tipos de sistemas para la Lubricación por Neblina de aceite:
- El sistema de Neblina Pura o “Pure Mist”.
- El sistema de Neblina por Purga o “Purge Mist”.
13.3.7.1.- Lubricación por Neblina Pura o “Pure Mist”
El sistema de Lubricación por Neblina Pura o “Pure Mist” es el sistema de Lubricación por Neblina más usado es aplicado fundamentalmente a bombas equipadas con cojinetes antifricción. El sistema consiste en el suministro de neblina lubricante directamente a los cojinetes, es decir que no se mantiene un nivel de aceite en las cajeras de cojinetes, también son eliminados los anillos de lubricación, los lubricadores (botellas para mantener el nivel de aceite) y los deflectores de aceite. El aceite entra a la cajera de cojinetes, lubrica los cojinetes, luego se condensa en la cajera y es drenado por el fondo de la cajera al colector ecológico.
La Figura N° 13-17 muestra el diagrama de una bomba de succión frontal equipada con un sistema de Lubricación por Neblina Pura.

Fuente:Centrifugal Pump Handbook_Antifriction Bearings in Centrifugal Pumps_By Ed Nelson.
El sistema de Lubricación por Neblina Pura favorece el mantenimiento de las propiedades del aceite lubricante prolongando su vida útil, ya que, al limitar la exposición del aceite a las altas temperaturas relativas a periodos muy cortos de tiempo, lo que desacelera la pérdida de las propiedades y la oxidación del aceite.
Para el suministro de la neblina lubricadora a las cajeras de los cojinetes se deriva la línea de lubricación del múltiple hasta los reclasificadores instalados en cada cojinete. Los reclasificadores son boquillas de acero inoxidable que están dimensionadas para suministrar diferentes cantidades de neblina a las cajeras de cojinetes y de esta manera satisfacer las necesidades de neblina de cada cojinete. Para recoger el aceite que se condensa y que es drenado de la cajera de cojinetes se instala una botella o recipiente ecológico en el drenaje.
La figura 13-18 muestra una bomba centrífuga con sus conexiones para Lubricación por Neblina Pura.

Fuente:oilmistinstitute.com
En la figura 13-18 se observan los reclasificadores,el drenaje del fondo de la caja de cojinetes y el colector ecológico. La Lubricación por Neblina Pura es ampliamente usada para preservar equipos fuera de servicio como es el caso de los equipos que necesitan ser almacenados por largos periodos a la espera de ser instalados en alguna planta de procesos o refinería en construcción. También esta situación se presenta cuando una planta es retirada de servicio temporalmente por no necesitarse o para realizar reparaciones mayores y prolongadas en algunos equipos principales.
De hecho, algunas normas y prácticas de ingeniería como la API RP 686 en la sección 3.2.3 “General Instructions-Jobsite Protection”da como una opción válida el uso del “Oil Mist” en proyectos de cierta magnitud cuando más de 10 piezas deben estar almacenadas por más de seis meses esperando su instalación.
La figura 13-19 muestra como ejemplo de cómo puede ser instalado el sistema de Neblina pura en una bomba almacenada.

Fuente:oilmistinstitute.com
Como se observa en la figura 12-19 el sistema es muy sencillo de instalar en una bomba que se encuentra almacenada, ya que no es necesario desmontar el equipo lo que en algunos casos origina problemas debido a complicaciones con la reinstalación de las piezas y perdida de componentes, adicionalmente los equipos a preservar con esta técnica no requieren ser preparados especialmente por ejemplo llenar las cajas de cojinetes y carcasas con aceite anticorrosivo u otro tipo de fluido de preservación. Estos dos aspectos permiten que el equipo almacenado esté listo para su instalación inmediata sin necesidad de preparación adicional.
13.3.7.2.- Lubricación por Neblina por Purga o “Purge Mist”
En los sistemas de Lubricación por Neblina de Purga al igual que en los sistemas de Niebla Pura o “Pure Mist” se inyecta la Niebla lubricante por medio de boquillas o reclasificadores a los cojinetes. La diferencia que tiene este método con el de del Lubricación con Neblina Pura es que se mantiene el nivel de aceite en la cajera de cojinetes, así como los deflectores, los lubricadores y anillos de lubricación.
Este arreglo es comúnmente usado en bombas que están equipadas con cojinetes de deslizamiento o planos y en equipos dotados con cojinetes de rodamientos donde es difícil lubricarlos apropiadamente. Este flujo de aceite adicional no puede ser suministrado por ninguno de los arreglos de boquillas y de conexiones del sistema de Lubricación por Niebla Pura por esta razón se mantienen el nivel de aceite, los anillos de lubricación y el nivel de aceite para aumentar el flujo de aceite lubricante hacia los cojinetes.
La figura N° 13-20 muestra el diagrama de una bomba de succión frontal equipada con un sistema de Lubricación por Neblina de Purga o “Purge Mist”, allí es posible observar que se mantiene el nivel de aceite en la caja de cojinetes de la bomba, así como el deflector para el salpicado.

Fuente:Centrifugal Pump Handbook_Antifriction Bearings in Centrifugal Pumps_By Ed Nelson.
En la experiencia industrial este sistema de Lubricación por Neblina de Purga requiere bastante atención por parte del mantenimiento, debido a que por no ser vital la neblina para el funcionamiento de los cojinetes es descuidado por los operarios y mantenedores, ya que se mantiene el nivel de aceite en las cajeras; así como los anillos y deflectores, el mal funcionamiento del sistema de “Oil Mist” no genera una falla inmediata, pero desvirtúa el sentido de su utilización y elimina las posibles ventajas que significa su uso.
Tanto el ASME B73.1 como el API 610/ISO 13709 especifican la lubricación por aceite como el sistema preferencial de lubricación. El ASME B73.1 en la sección 4.7.5 Lubrication, indica que la lubricación por aceite es la lubricación estándar para las bombas fabricadas siguiendo esta norma principalmente el método de lubricación por baño de aceite, sin embargo, deja abiertaopciones para el uso de otros métodos de lubricación como la lubricación por Neblina de Aceite o “Oil Mist” y hasta lubricación por grasa.
En el API 610/ISO 13709 11ava edición en el capítulo 6.11. se indica que los cojinetes y las cajeras de cojinetes deben ser diseñadas para ser lubricadas con aceite mineral a menos que expresamente se indique lo contrario. Indicando también que si también es solicitado se deben dejar las previsiones para la instalación de sistemas de lubricación por niebla o de “Oil Mist”.
Los aceites minerales básicos son producidos a partir de la destilación del petróleo crudo, tomando como materia prima el residuo largo del proceso de destilación. En la destilación, el petróleo es separado en diferentes componentes usando para ello un calentamiento inicial en hornos que lleva al petróleo a varios cientos de grados de temperatura, lo que facilita la separación de los diferentes componentes que lo forman. El petróleo luego es bombeado a una torre de destilación atmosférica, que es la etapa inicial del proceso de destilación en las refinerías convencionales.
En este proceso de destilación los componentes más livianos son captados en el tope de la torre para producir gasolina y nafta, los componentes medianos son captados en las bandejas intermedias para producir diesel y gasóleo, el fondo de la torre es la fracción más pesada es calentado en hornos y bombeado a las torres de destilación al vacío.
El lubricante base es captado en las bandejas intermedias de la torre de destilación al vacío. Este lubricante base es tratado para retirar componentes indeseables como es el asfalto, después es hidrogenado para completar las cadenas de hidrocarburos y para homogenizarlo. Las tres clases básicas de aceites lubricantes minerales son:
- Los aceites Parafínicos, que representan más del 90% de las bases de aceites lubricantes derivados del petróleo que son producidas.
- Los aceites Neftánicos.
- Los aceites Aromáticos.
Los grados de los aceites lubricantes aplicados a nivel industrial son definidos por la ISO, designados como ISOVG (ISO Viscosity Grade). La ISO establece 18 grados de viscosidad para los aceites lubricantes industriales comprendidos entre 2 y 1500 cST referidos a una temperatura de 40 ºC (104 ºF). Esta clasificación no especifica la calidad del aceite, solamente establece la viscosidad cinemática correspondiente a cada grado para la temperatura de 40 ºC (104 ºF).
En las bombas centrífugas se utilizan principalmente los aceites lubricantes grados ISOVG 32 (viscosidad cinemática entre 28,8 y 35,20 SSU, equivalente a 1,5 a 2,56 cST), ISOVG 46 (viscosidad cinemática entre 41,40 y 50,60 SSU, equivalente a 4,30 a 7,40 cST), y el ISOVG 68 (viscosidad cinemática entre 61,2 y 74,8 SSU, equivalente a 10,3 a 14 cST).
Dinos qué te ha parecido el artículo
Artículos recomendados
2.3. Selección del Software de Mantenimiento

Estadísticas prácticas no paramétricas

2.- Partes de una Bomba Centrífuga

13.1.- Tipos de Lubricación

Publica tu artículo en la revista #1 de Mantenimiento Industrial
Publicar un artículo en la revista es gratis, no tiene costo.
Solo debes asegurarte que no sea un artículo comercial.
¿Qué esperas?
O envía tu artículo directo: articulos@predictiva21.com
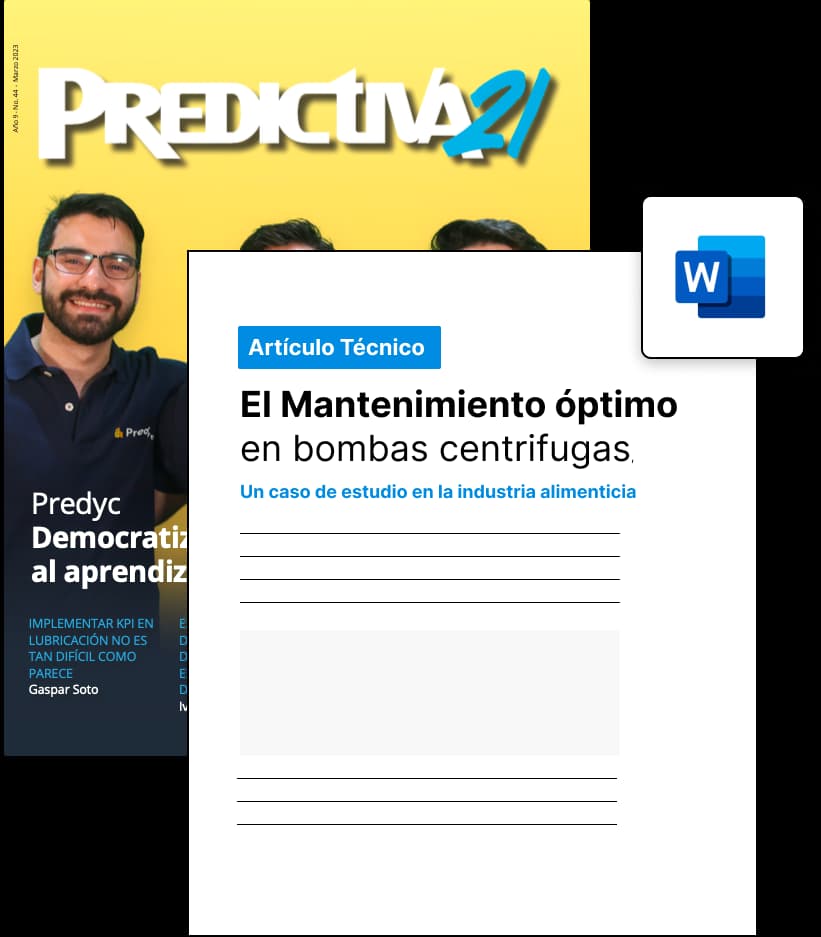