8.4. La Mudanza de Enfoque del Mantenimiento
Libros31 de agosto de 2020
El éxito de una compañía es, en gran parte, debido a la buena cooperación entre clientes y proveedores, sean internos o externos. Los roces crean costos y consumen tiempo y energía. La gestión dinámica del mantenimiento implica administración de las interfaces con otras divisiones corporativas.
La coordinación entre los subsistemas de: planificación de la producción, de la estrategia del mantenimiento, de la adquisición de repuestos, de la programación de servicios y del flujo de informaciones, elimina el conflicto de metas.
Altas disponibilidades e índices de utilización, aumento de la confiabilidad, bajo costo de producción como resultado de mantenimiento optimizado, gestión de repuestos y alta calidad de productos, son metas que pueden ser alcanzadas solamente cuando operación y mantenimiento trabajan juntos.
La no modernización de las empresas genera costos indirectos relacionados con (59):
- Pérdida continua de la competitividad, ya que los parámetros de medición están cambiando (lamentablemente este hecho no es fácil de cuantificar);
- A medida que pasa el tiempo, se vuelve más difícil enfrentar los cambios tecnológicos exigidos por la modernización;
- Se pierde el sentido de urgencia que requiere la gestión en un ambiente mutante y ultra competitivo.
Y las nuevas tecnologías están exigiendo (59):
- Personal preparado;
- Nuevos procedimientos;
- Cambio de paradigmas;
- Aprendizaje continuo;
- Nuevos enfoques de supervisión;
- Liderazgo basado en el conocimiento;
- Conversión de trabajadores manuales en trabajadores con conocimiento.
Para enfrentar la modernización se debe(59):
- Crear una verdadera cultura innovadora en el interior de la empresa;
- Motivar el perfeccionamiento continuo;
- Utilizar el "benchmark" de manera inteligente;
- Crear visiones tecnológicas adecuadas a la realidad;
- Visitar y conocer otras realidades;
- Estimular el cambio;
- Crear el espirito crítico.
Los cambios ocurren de forma cada vez más rápida, y el no seguimiento a estos, puede llevar a una empresa a quedar rezagada con relación a sus competidores - Figura 69 (59)

Áreas de cambio exitosas tuvieron su evolución de mantenimiento no-planificado hacia el mantenimiento estratégico(7).
Los expertos en mantenimiento son repetidamente confrontados respecto a: ¿cual es el método de mantenimiento más eficaz?. La respuesta es la combinación correcta de todos los métodos disponibles, o sea, mantenimiento por ruptura, mantenimiento basado en el uso y mantenimiento basado en la condición - Figura 70(5)
En la evaluación del punto óptimo de mantenimiento, se constata que el costo total del mantenimiento es influido por el costo de mantenimiento regular (costo de reparación) y por el costo de la falla (pérdida de producción). De esta manera, la estrategia óptima de mantenimiento, es aquella que minimiza el efecto conjunto de los componentes del costo, o sea, identifica el punto, donde el costo de reparación es aún menor que el costo de la pérdida de producción.
El mantenimiento planificado alcanza reducciones de costos a través de: la eliminación de desperdicios, del establecimiento de estrategias por equipo y del aumento de la capacidad, disponibilidad y confiabilidad de los equipos.
La previsibilidad y el impacto de las fallas sobre el negocio, apuntan hacia el tipo de estrategia a ser adoptada, según la importancia de las varias unidades de la planta.

Son consideradas, en el árbol de decisiones para la selección del correcto "mix de los métodos", factores como: la utilización deseada, si el proceso de producción es continuo o intermitente, calidad del producto, requisitos de seguridad, proyecto / configuración de la unidad de la planta y efectividad de los costos, previsibilidad de falla, tiempos medios entre falla y tiempos medios para reparaciones etc.
La planificación de mantenimiento es compuesta por una serie de actividades, siendo las principales etapas del proceso: enfocar el esfuerzo, desarrollar los planes e implantarlos. El resultado de esta planificación, deberá ser una serie coherente de estrategias de mantenimiento, continuamente monitoreadas y ajustadas, con el objetivo de minimizar los costos totales.
Son características de un mantenimiento óptimo:
- Enfocar las habilidades del mantenimiento departamental, en la planificación y control del mantenimiento y no en la reparación de rupturas y mejoras de equipos;
- Realizar trabajo de mantenimiento de acuerdo con planes documentados y estandarizados, tareas programadas y solicitudes de trabajo;
- Realizar mantenimiento preventivo de acuerdo con el programa (no dejar los trabajos para después);
- Documentar y analizar el historial de mantenimiento y rupturas, buscando asegurar que los índices de falla sean optimizados y los costos totales minimizados, medir y mejorar la productividad del personal e identificar oportunidades de mejora;
- Desarrollar los sistemas inteligentes necesarios para promover las acciones indicadas por el mantenimiento basado en la condición y, de esta manera capturar el conocimiento actual y futuro.
Cursos recomendados






%252FImagen%252FRAMPREDYC-1730060420837.webp%3Falt%3Dmedia%26token%3D2634a7f0-988e-4022-b91f-382503e6e9db&w=3840&q=75)

Referencias
- (5) Maintenance as a Corpotate Strategy. Andrew P. Ginder. AIPE Facilities – January/February 1996
- (7) Manutenção por estratégia – Visão do futuro. Silvio Miranda. Revista de Ensino de Engenharia – ABENGE – Nº 12 – Jul/95
- (59) Modernización de plantas industriales. Moises Saravia R. 4o Congreso Argentino de Mantenimiento – 1977
Autor: Lourival Augusto Tavares
Brasil
Consultor en Ingeniería de Mantenimiento
Empresa: Director nacional de ABRAMAN (Asociación Brasileña de Mantenimiento) en dos mandatos.
Correo: l.tavares@mandic.com.br
Ingeniero Electricista, formado por la Escuela Federal de Ingeniería de Rio de Janeiro, en el año de 1967. Past-Presidente del Comité Panamericano de Ingeniería de Mantenimiento. Supervisor de Mantenimiento en FURNAS – Centrales Eléctricas S.A. durante 23 años. Fue el jefe de la Asesoría Técnica de Apoyo en ITAIPU Binacional. Reconocido como “notorio saber” en mantenimiento por la Universidad Federal de Rio de Janeiro y por la Universidad Federal de Paraíba.
Dinos qué te ha parecido el artículo
Artículos recomendados
Diseño óptimo de experimentos: un enfoque de estudio de caso

Análisis de fallas: una guía práctica para fabricantes de componentes y sistemas electrónicos

Manual de análisis de causa raíz: una guía para la investigación de incidentes eficiente y eficaz

2.4. Conceptos Básicos

Publica tu artículo en la revista #1 de Mantenimiento Industrial
Publicar un artículo en la revista es gratis, no tiene costo.
Solo debes asegurarte que no sea un artículo comercial.
¿Qué esperas?
O envía tu artículo directo: articulos@predictiva21.com
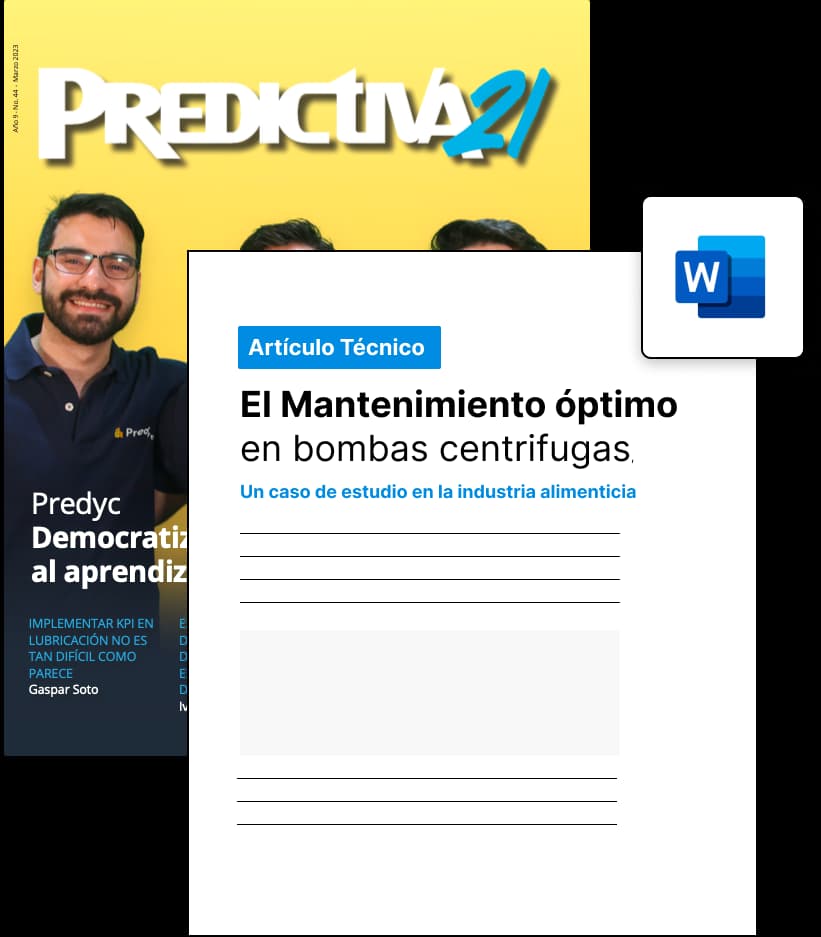
8.4. La Mudanza de Enfoque del Mantenimiento
Libros 31 de agosto de 2020El éxito de una compañía es, en gran parte, debido a la buena cooperación entre clientes y proveedores, sean internos o externos. Los roces crean costos y consumen tiempo y energía. La gestión dinámica del mantenimiento implica administración de las interfaces con otras divisiones corporativas.
La coordinación entre los subsistemas de: planificación de la producción, de la estrategia del mantenimiento, de la adquisición de repuestos, de la programación de servicios y del flujo de informaciones, elimina el conflicto de metas.
Altas disponibilidades e índices de utilización, aumento de la confiabilidad, bajo costo de producción como resultado de mantenimiento optimizado, gestión de repuestos y alta calidad de productos, son metas que pueden ser alcanzadas solamente cuando operación y mantenimiento trabajan juntos.
La no modernización de las empresas genera costos indirectos relacionados con (59):
- Pérdida continua de la competitividad, ya que los parámetros de medición están cambiando (lamentablemente este hecho no es fácil de cuantificar);
- A medida que pasa el tiempo, se vuelve más difícil enfrentar los cambios tecnológicos exigidos por la modernización;
- Se pierde el sentido de urgencia que requiere la gestión en un ambiente mutante y ultra competitivo.
Y las nuevas tecnologías están exigiendo (59):
- Personal preparado;
- Nuevos procedimientos;
- Cambio de paradigmas;
- Aprendizaje continuo;
- Nuevos enfoques de supervisión;
- Liderazgo basado en el conocimiento;
- Conversión de trabajadores manuales en trabajadores con conocimiento.
Para enfrentar la modernización se debe(59):
- Crear una verdadera cultura innovadora en el interior de la empresa;
- Motivar el perfeccionamiento continuo;
- Utilizar el "benchmark" de manera inteligente;
- Crear visiones tecnológicas adecuadas a la realidad;
- Visitar y conocer otras realidades;
- Estimular el cambio;
- Crear el espirito crítico.
Los cambios ocurren de forma cada vez más rápida, y el no seguimiento a estos, puede llevar a una empresa a quedar rezagada con relación a sus competidores - Figura 69 (59)

Áreas de cambio exitosas tuvieron su evolución de mantenimiento no-planificado hacia el mantenimiento estratégico(7).
Los expertos en mantenimiento son repetidamente confrontados respecto a: ¿cual es el método de mantenimiento más eficaz?. La respuesta es la combinación correcta de todos los métodos disponibles, o sea, mantenimiento por ruptura, mantenimiento basado en el uso y mantenimiento basado en la condición - Figura 70(5)
En la evaluación del punto óptimo de mantenimiento, se constata que el costo total del mantenimiento es influido por el costo de mantenimiento regular (costo de reparación) y por el costo de la falla (pérdida de producción). De esta manera, la estrategia óptima de mantenimiento, es aquella que minimiza el efecto conjunto de los componentes del costo, o sea, identifica el punto, donde el costo de reparación es aún menor que el costo de la pérdida de producción.
El mantenimiento planificado alcanza reducciones de costos a través de: la eliminación de desperdicios, del establecimiento de estrategias por equipo y del aumento de la capacidad, disponibilidad y confiabilidad de los equipos.
La previsibilidad y el impacto de las fallas sobre el negocio, apuntan hacia el tipo de estrategia a ser adoptada, según la importancia de las varias unidades de la planta.

Son consideradas, en el árbol de decisiones para la selección del correcto "mix de los métodos", factores como: la utilización deseada, si el proceso de producción es continuo o intermitente, calidad del producto, requisitos de seguridad, proyecto / configuración de la unidad de la planta y efectividad de los costos, previsibilidad de falla, tiempos medios entre falla y tiempos medios para reparaciones etc.
La planificación de mantenimiento es compuesta por una serie de actividades, siendo las principales etapas del proceso: enfocar el esfuerzo, desarrollar los planes e implantarlos. El resultado de esta planificación, deberá ser una serie coherente de estrategias de mantenimiento, continuamente monitoreadas y ajustadas, con el objetivo de minimizar los costos totales.
Son características de un mantenimiento óptimo:
- Enfocar las habilidades del mantenimiento departamental, en la planificación y control del mantenimiento y no en la reparación de rupturas y mejoras de equipos;
- Realizar trabajo de mantenimiento de acuerdo con planes documentados y estandarizados, tareas programadas y solicitudes de trabajo;
- Realizar mantenimiento preventivo de acuerdo con el programa (no dejar los trabajos para después);
- Documentar y analizar el historial de mantenimiento y rupturas, buscando asegurar que los índices de falla sean optimizados y los costos totales minimizados, medir y mejorar la productividad del personal e identificar oportunidades de mejora;
- Desarrollar los sistemas inteligentes necesarios para promover las acciones indicadas por el mantenimiento basado en la condición y, de esta manera capturar el conocimiento actual y futuro.
Cursos recomendados






%252FImagen%252FRAMPREDYC-1730060420837.webp%3Falt%3Dmedia%26token%3D2634a7f0-988e-4022-b91f-382503e6e9db&w=3840&q=75)

Referencias
- (5) Maintenance as a Corpotate Strategy. Andrew P. Ginder. AIPE Facilities – January/February 1996
- (7) Manutenção por estratégia – Visão do futuro. Silvio Miranda. Revista de Ensino de Engenharia – ABENGE – Nº 12 – Jul/95
- (59) Modernización de plantas industriales. Moises Saravia R. 4o Congreso Argentino de Mantenimiento – 1977
Autor: Lourival Augusto Tavares
Brasil
Consultor en Ingeniería de Mantenimiento
Empresa: Director nacional de ABRAMAN (Asociación Brasileña de Mantenimiento) en dos mandatos.
Correo: l.tavares@mandic.com.br
Ingeniero Electricista, formado por la Escuela Federal de Ingeniería de Rio de Janeiro, en el año de 1967. Past-Presidente del Comité Panamericano de Ingeniería de Mantenimiento. Supervisor de Mantenimiento en FURNAS – Centrales Eléctricas S.A. durante 23 años. Fue el jefe de la Asesoría Técnica de Apoyo en ITAIPU Binacional. Reconocido como “notorio saber” en mantenimiento por la Universidad Federal de Rio de Janeiro y por la Universidad Federal de Paraíba.
Dinos qué te ha parecido el artículo
Artículos recomendados
Lo que todo ingeniero debe saber sobre ingeniería y gestión de riesgos

2.2.- Eje

8.3. Estrategias de Gestión de Proceso

Ingeniería, teoría y práctica de Confiabilidad de sistemas de telecomunicaciones

Publica tu artículo en la revista #1 de Mantenimiento Industrial
Publicar un artículo en la revista es gratis, no tiene costo.
Solo debes asegurarte que no sea un artículo comercial.
¿Qué esperas?
O envía tu artículo directo: articulos@predictiva21.com
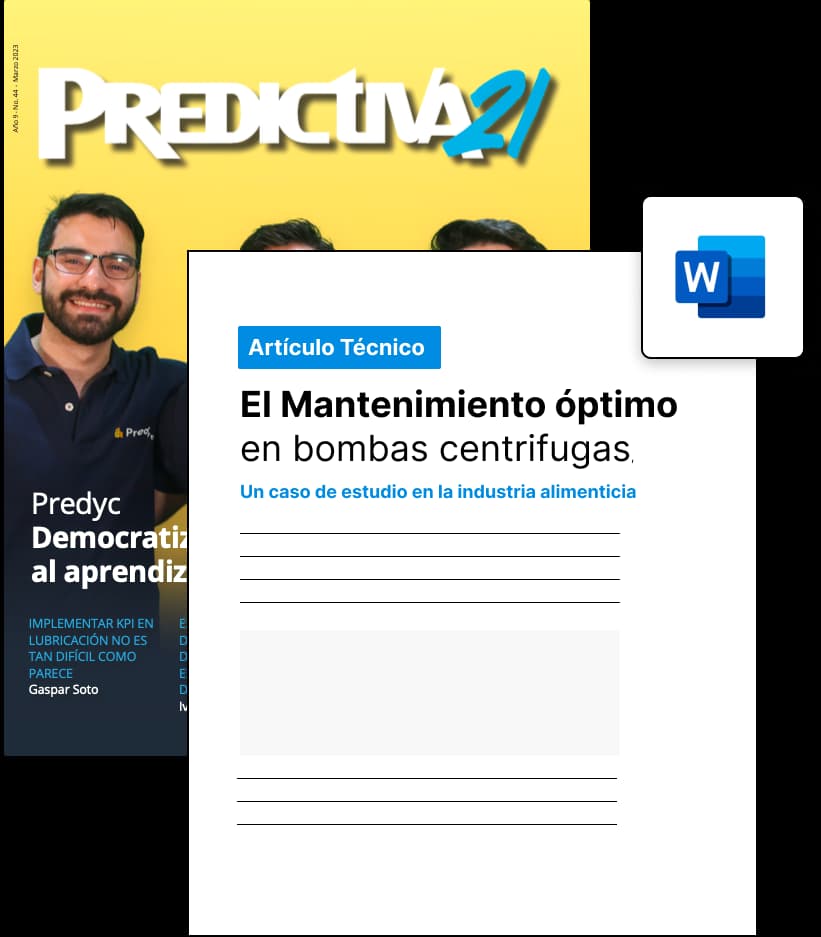