Análisis RAM de Planta de inyección de agua de la industria petrolera
Articulo22 de marzo de 2019
Dentro de las herramientas de confiabilidad, los análisis de parámetros de mantenimiento o RAM por sus siglas en inglés, han tenido gran relevancia a la hora estimar el comportamiento de los activos industriales o ISED (Instalaciones, sistemas, equipos y dispositivos), ante los movimientos naturales de sus ciclos de vida y la interacción de estos en cada fase. A continuación, se expresa la aplicación de este estudio a una planta de inyección de agua de la industria petrolera, misma conformada por seis (06) trenes de inyección. En la actualidad está presenta desviaciones significativas ante los esquemas y planes operaciones estimados, teniendo la necesidad de identificar los factores incidentes y la afectación de estos en escenarios futuros.
Contexto operacional y escenario actual
La Planta tiene como función principal inyectar de 600 - 842 mil barriles de agua al día (MBPD) a una presión comprendida entre 3800 – 4300 PSIG. El proceso consiste en cuatro (04) turbo-bombas y dos (02) moto-bombas centrifugas multietapas, en este escenario se deja en reserva las dos (02) motobombas para respaldo operacional.
Sin embargo, bajo este esquema la planta no ha obtenido los resultados esperados por la organización, al tener desviaciones, impidiendo lograr los objetivos de producción de la organización debido a la incidencia de números eventos tanto inminentes (fallas) como ajenos (factores o fallos externos) muchos de estos últimos debido a cortes eléctricos no programados por parte del suministro nacional.
Hipótesis
Las observaciones iniciales sobre el escenario de estudio se prevé que las desviaciones se deben a:
- Altos tiempos fuera de Servicio de los ISED a causa de fallas inherente.
- Altos tiempos fuera de Servicio de los ISED a causa de eventos Externos.
- Altos tiempos fuera de servicio de los ISED a causa de una combinación de fallos internos y externos.
Análisis
La información registrada en la bitácora de mantenimiento y operaciones de la planta además la validación de esta se cortejo a través de un Equipo natural de Trabajo, esta data fue el punto de partida para estimar el comportamiento de los ISED de la planta, permitiendo verificar el desarrollo de disponibilidad de la planta (ver figura N°1), lo que verificó la existencia de las desviaciones previamente indicadas.

Este análisis inicial, demostró que las fallas externas representan el 3% del tiempo total fuera de servicio registrado representado en la Figura N°2, mientras que el tren N°5 posee el 66% de este tiempo, por lo que la unidad N°5 estuvo alrededor del 50% del tiempo calendario fuera de servicio. Sin embargo, cabe destacar que esta unidad al igual que la N°6 son de respaldo operacional, por lo que la afectación está asociada a la incidencia de los otros trenes cuando fallan.

En función a la información obtenida se diseñaron los diagramas de bloque en el sistema Raptor 7.0, como se muestra en la Figura N°3. En esta ocasión, se modelaron los subsistemas que conforman cada tren, según lo indicado por la Norma ISO 14224-2016.
Se modelaron en cada Subsistema las distribuciones estadísticas correspondientes para los tiempos fuera de servicio y tiempos entre falla. Además, se incluyeron las fallas externas dentro del modelo para determinar la incidencia en el comportamiento global.
Además de incluir las actividades de mantenimiento preventivo de las unidades que inciden en la operación de las mismas.

Con el horizonte de simulación estimado de seis años, (correspondiente a las metas operaciones y al ciclo de mantenimiento) se obtuvo el perfil estocástico del comportamiento global, como se muestra en la figura N°4.

La figura N°4, presenta que el comportamiento actual ligeramente incumple las metas establecidas con respecto a la disponibilidad, para la obtención de los principales subsistemas causantes de esta desviación se realizó un tratamiento ABC de clasificación en función de indisponibilidad. Como se muestra en la figura N°5.

Así como se contempló en análisis iniciales el tren N°5, causa la mayor indisponibilidad al sistema, logrando que pese a que la configuración actual es de 4/6, se comporte como si este tren no existirá y en consecuencia el sistema se desempeñe casi a la par de un sistema 4/5, esto pudiese ser previsivo para el incremento de capacidad en escenarios futuros en función de los requerimientos operacionales, sin embargo el comportamiento complementario de los demás trenes inciden en la disponibilidad global siendo el orden el mostrado a continuación:
- Booster de R5.
- Sistema de monitoreo y control de Motor eléctrico de R5.
- Sistema de bombeo de R4.
- Sistema de Transmisión de potencia de R6.
- Sistema de Lubricación de R5.
- Sistema de bombeo de R1.
- Sistema de bombeo de R6.
- Sistema de Lubricación de R2.
Nótese que las fallas externas no entran dentro de las principales causas de indisponibilidad.
Cursos recomendados






%252FImagen%252FRAMPREDYC-1730060420837.webp%3Falt%3Dmedia%26token%3D2634a7f0-988e-4022-b91f-382503e6e9db&w=3840&q=75)

Conclusiones
- Las fallas inherente los subsistemas de Tren N°5 y los altos tiempos fuera de servicio asociados, son los principales elementos causantes de las desviación.
- Las fallas externas no representa mayor incidencia en el cumplimiento de las metas, por lo que generar acciones de mitigación estarían sobre valoradas.
- La afectación de la indisponibilidad de los trenes de contingencia ocasiona que la ocurrencia de eventos en los trenes principales afecte de forma directa el comportamiento global.
- Las afectaciones de las fallas están dadas por los altos tiempos fuera de servicio, y no por la frecuencia de ocurrencia de las mismas.
Recomendaciones
- Determinar acciones de mantenimiento para los elementos de mayor incidencia dentro del esquema operativo que garanticen la función.
- No generar en esta etapa acciones de mantenimiento para las causas externas que afectan la disponibilidad de los equipos.
- Reevaluar los parámetros de mantenimiento una vez lograda la implementación de las actividades de mantenimiento.
- Garantizar la atención de los trenes en la ocurrencia de fallas, con los debidos procedimientos que garanticen la reducción inminente del tiempo fuera de servicio de las unidades principalmente en las unidades de respaldo.
Referencias
- Mataix, C. (2000). Turbomáquinas térmicas. Editorial Dossat s.a., Madrid, España.
- Norma PDVSA MM-01-01-02, (2010). Indicadores de gestión del proceso de mantenimiento, PDVSA Venezuela
- Gómez, H., Medina N. y Yáñez M. (2008). Análisis de Confiabilidad, Disponibilidad y Mantenibilidad en Sistemas Productivos, Reliability and Risk Management S.A. Maracaibo
- Gutiérrez E.; Agüero M., Calixto I. (2007). Análisis integral de criticidad de Activos, R2M, Artículo técnico
- ISO 14224 (2016). Petroleum, petrochemical and natural gas industries—Collection and exchange of reliability and maintenance data for equipment
- Navidi W. Estadistica para ingenieros, Editorial Mc Graw Hill, Mexico.
Autor: Msc. Esp. Ing. Luigi Anthony Rondón
Correo: luigiRondon1387@gmail.com / luigi_1387@hotmail.com
Dinos qué te ha parecido el artículo
Artículos recomendados
Revisión del estándar ISO 12669 para establecer el nivel requerido de limpieza (RCL) de aceites hidráulicos

Confiabilidad Organizacional: BEPRO - Método para mejorar los procesos que afectan a la Confiabilidad Operacional

Mantenimiento; ¿costos, gastos o inversión?

Diplomado en gestión de activos y mantenimiento

Publica tu artículo en la revista #1 de Mantenimiento Industrial
Publicar un artículo en la revista es gratis, no tiene costo.
Solo debes asegurarte que no sea un artículo comercial.
¿Qué esperas?
O envía tu artículo directo: articulos@predictiva21.com
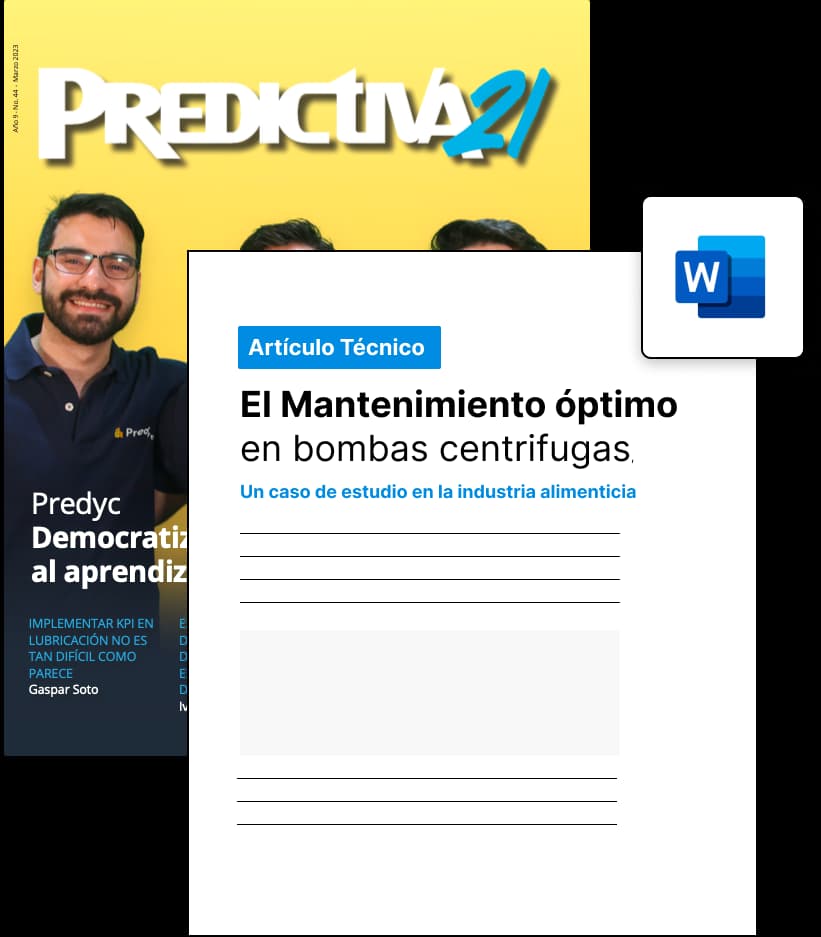
Análisis RAM de Planta de inyección de agua de la industria petrolera
Articulo 22 de marzo de 2019Dentro de las herramientas de confiabilidad, los análisis de parámetros de mantenimiento o RAM por sus siglas en inglés, han tenido gran relevancia a la hora estimar el comportamiento de los activos industriales o ISED (Instalaciones, sistemas, equipos y dispositivos), ante los movimientos naturales de sus ciclos de vida y la interacción de estos en cada fase. A continuación, se expresa la aplicación de este estudio a una planta de inyección de agua de la industria petrolera, misma conformada por seis (06) trenes de inyección. En la actualidad está presenta desviaciones significativas ante los esquemas y planes operaciones estimados, teniendo la necesidad de identificar los factores incidentes y la afectación de estos en escenarios futuros.
Contexto operacional y escenario actual
La Planta tiene como función principal inyectar de 600 - 842 mil barriles de agua al día (MBPD) a una presión comprendida entre 3800 – 4300 PSIG. El proceso consiste en cuatro (04) turbo-bombas y dos (02) moto-bombas centrifugas multietapas, en este escenario se deja en reserva las dos (02) motobombas para respaldo operacional.
Sin embargo, bajo este esquema la planta no ha obtenido los resultados esperados por la organización, al tener desviaciones, impidiendo lograr los objetivos de producción de la organización debido a la incidencia de números eventos tanto inminentes (fallas) como ajenos (factores o fallos externos) muchos de estos últimos debido a cortes eléctricos no programados por parte del suministro nacional.
Hipótesis
Las observaciones iniciales sobre el escenario de estudio se prevé que las desviaciones se deben a:
- Altos tiempos fuera de Servicio de los ISED a causa de fallas inherente.
- Altos tiempos fuera de Servicio de los ISED a causa de eventos Externos.
- Altos tiempos fuera de servicio de los ISED a causa de una combinación de fallos internos y externos.
Análisis
La información registrada en la bitácora de mantenimiento y operaciones de la planta además la validación de esta se cortejo a través de un Equipo natural de Trabajo, esta data fue el punto de partida para estimar el comportamiento de los ISED de la planta, permitiendo verificar el desarrollo de disponibilidad de la planta (ver figura N°1), lo que verificó la existencia de las desviaciones previamente indicadas.

Este análisis inicial, demostró que las fallas externas representan el 3% del tiempo total fuera de servicio registrado representado en la Figura N°2, mientras que el tren N°5 posee el 66% de este tiempo, por lo que la unidad N°5 estuvo alrededor del 50% del tiempo calendario fuera de servicio. Sin embargo, cabe destacar que esta unidad al igual que la N°6 son de respaldo operacional, por lo que la afectación está asociada a la incidencia de los otros trenes cuando fallan.

En función a la información obtenida se diseñaron los diagramas de bloque en el sistema Raptor 7.0, como se muestra en la Figura N°3. En esta ocasión, se modelaron los subsistemas que conforman cada tren, según lo indicado por la Norma ISO 14224-2016.
Se modelaron en cada Subsistema las distribuciones estadísticas correspondientes para los tiempos fuera de servicio y tiempos entre falla. Además, se incluyeron las fallas externas dentro del modelo para determinar la incidencia en el comportamiento global.
Además de incluir las actividades de mantenimiento preventivo de las unidades que inciden en la operación de las mismas.

Con el horizonte de simulación estimado de seis años, (correspondiente a las metas operaciones y al ciclo de mantenimiento) se obtuvo el perfil estocástico del comportamiento global, como se muestra en la figura N°4.

La figura N°4, presenta que el comportamiento actual ligeramente incumple las metas establecidas con respecto a la disponibilidad, para la obtención de los principales subsistemas causantes de esta desviación se realizó un tratamiento ABC de clasificación en función de indisponibilidad. Como se muestra en la figura N°5.

Así como se contempló en análisis iniciales el tren N°5, causa la mayor indisponibilidad al sistema, logrando que pese a que la configuración actual es de 4/6, se comporte como si este tren no existirá y en consecuencia el sistema se desempeñe casi a la par de un sistema 4/5, esto pudiese ser previsivo para el incremento de capacidad en escenarios futuros en función de los requerimientos operacionales, sin embargo el comportamiento complementario de los demás trenes inciden en la disponibilidad global siendo el orden el mostrado a continuación:
- Booster de R5.
- Sistema de monitoreo y control de Motor eléctrico de R5.
- Sistema de bombeo de R4.
- Sistema de Transmisión de potencia de R6.
- Sistema de Lubricación de R5.
- Sistema de bombeo de R1.
- Sistema de bombeo de R6.
- Sistema de Lubricación de R2.
Nótese que las fallas externas no entran dentro de las principales causas de indisponibilidad.
Cursos recomendados






%252FImagen%252FRAMPREDYC-1730060420837.webp%3Falt%3Dmedia%26token%3D2634a7f0-988e-4022-b91f-382503e6e9db&w=3840&q=75)

Conclusiones
- Las fallas inherente los subsistemas de Tren N°5 y los altos tiempos fuera de servicio asociados, son los principales elementos causantes de las desviación.
- Las fallas externas no representa mayor incidencia en el cumplimiento de las metas, por lo que generar acciones de mitigación estarían sobre valoradas.
- La afectación de la indisponibilidad de los trenes de contingencia ocasiona que la ocurrencia de eventos en los trenes principales afecte de forma directa el comportamiento global.
- Las afectaciones de las fallas están dadas por los altos tiempos fuera de servicio, y no por la frecuencia de ocurrencia de las mismas.
Recomendaciones
- Determinar acciones de mantenimiento para los elementos de mayor incidencia dentro del esquema operativo que garanticen la función.
- No generar en esta etapa acciones de mantenimiento para las causas externas que afectan la disponibilidad de los equipos.
- Reevaluar los parámetros de mantenimiento una vez lograda la implementación de las actividades de mantenimiento.
- Garantizar la atención de los trenes en la ocurrencia de fallas, con los debidos procedimientos que garanticen la reducción inminente del tiempo fuera de servicio de las unidades principalmente en las unidades de respaldo.
Referencias
- Mataix, C. (2000). Turbomáquinas térmicas. Editorial Dossat s.a., Madrid, España.
- Norma PDVSA MM-01-01-02, (2010). Indicadores de gestión del proceso de mantenimiento, PDVSA Venezuela
- Gómez, H., Medina N. y Yáñez M. (2008). Análisis de Confiabilidad, Disponibilidad y Mantenibilidad en Sistemas Productivos, Reliability and Risk Management S.A. Maracaibo
- Gutiérrez E.; Agüero M., Calixto I. (2007). Análisis integral de criticidad de Activos, R2M, Artículo técnico
- ISO 14224 (2016). Petroleum, petrochemical and natural gas industries—Collection and exchange of reliability and maintenance data for equipment
- Navidi W. Estadistica para ingenieros, Editorial Mc Graw Hill, Mexico.
Autor: Msc. Esp. Ing. Luigi Anthony Rondón
Correo: luigiRondon1387@gmail.com / luigi_1387@hotmail.com
Dinos qué te ha parecido el artículo
Artículos recomendados
Optimización de Inventarios de Partes y Repuestos para el Mantenimiento (II Parte)

Hablemos de Confiabilidad, Disponibilidad, Mantenibilidad, Seguridad y Riesgo de Activos

Educación Formal para el Mantenimiento

El mantenimiento y su evolución

Publica tu artículo en la revista #1 de Mantenimiento Industrial
Publicar un artículo en la revista es gratis, no tiene costo.
Solo debes asegurarte que no sea un artículo comercial.
¿Qué esperas?
O envía tu artículo directo: articulos@predictiva21.com
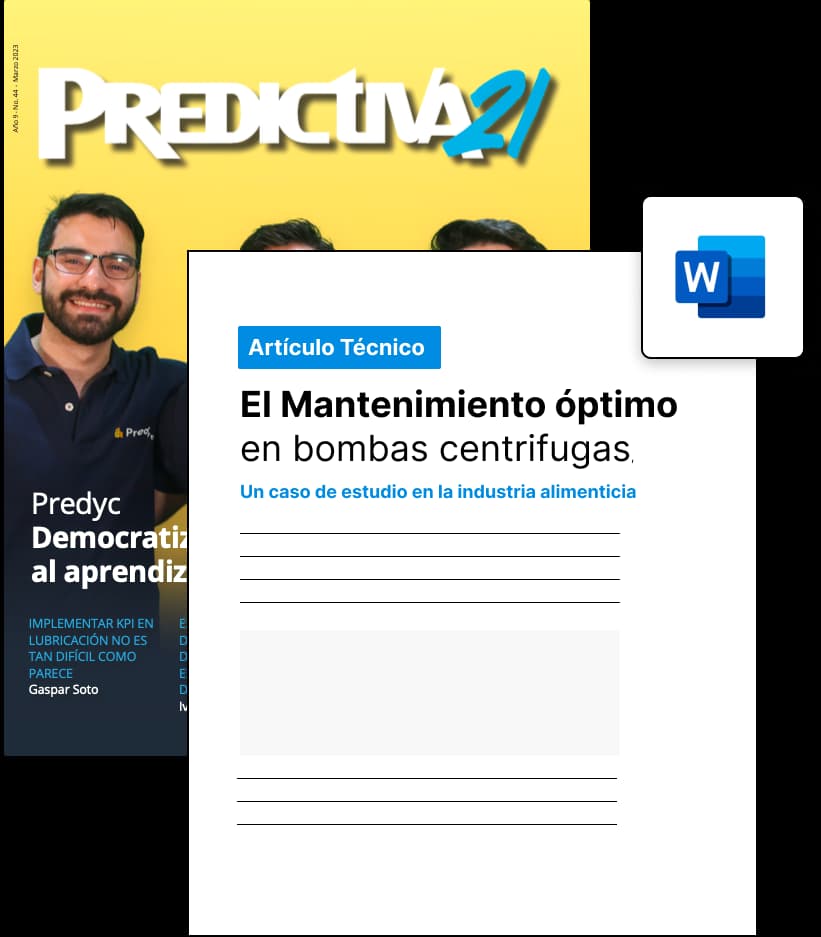