Calibración de válvulas en Motores Diésel de velocidad media
Articulo12 de junio de 2019
De acuerdo con los programas de mantenimiento preventivo de las unidades de combustión interna diésel en centrales eléctricas, independientemente de las marcas o modelos de las unidades de combustión interna, una de las tareas del plan de mantenimiento es la calibración de válvulas del motor.
En las unidades de generación eléctrica (y en el equipo o road), la referencia para la ejecución de los diferentes planes de mantenimiento preventivo esta dado en función de las horas de operación del motor.
Objetivo
Determinar el procedimiento técnico correspondiente a la calibración de válvulas de un motor, utilizando equipos de medición y comprobación. La herramienta seleccionada es el dial indicador. Esto permitirá además mantener un archivo documentado de la variación del claro de válvulas acorde con las horas de operación de los cabezotes. En la figura 1 se puede apreciar el dial, herramienta de precisión. Como parte fundamental del presente artículo, buscamos demostrar la importancia de utilizar equipos de comprobación.

Definiciones
Antes de proceder a la explicación del tema, deberemos presentar la terminología a utilizar, a fin de estandarizar conceptos:
Calibración de válvulas: Procedimiento utilizado en los motores de combustión interna, y que sirve para asegurar que las válvulas del motor se cierren completamente cuando el grado de dilatación térmica de los materiales ha sido alcanzado. Esta medida está determinada por el fabricante del equipo y debe controlarse periódicamente. Es una tarea requerida por el programa de mantenimiento y se realiza cada cierto número horas de operación o en caso de desmontaje de partes relacionadas.
El método más común utilizado en los motores es tornillo-contratuerca.
Válvulas del cabezote de motor diesel: Elementos de construcción mecánica que permiten el ingreso del aire a la cámara de combustión (válvulas de admisión) y la salida de los gases resultantes de la combustión producida (válvulas de escape).
TDC: Por sus siglas en inglés, Top Dead Center, y se refiere al momento de giro del cigüeñal y su conjunto biela- pistón, en el que el movimiento alternativo de este llega a su parte más alta y cambia de dirección.
BDC: Bottom Dead Center, es la posición contraria a la anterior, y es el momento en el que el pistón del motor llega a la parte más baja de su recorrido en el cilindro para iniciar su movimiento ascendente (hacia el TDC).
Cabezote: Componente que constituye la parte alta del motor y determina uno de los límites que forman la cámara de combustión. Está compuesto por las válvulas, balancines, inyector de combustible y ductos de lubricación, entre otros.
Ciclo del motor diesel: Eventos ocurridos durante la operación del motor y que están determinados por el fabricante del motor. Para información general estos son: admisión, compresión; combustión y escape.
Sincronización del motor: Es un estado determinado por el fabricante y define la correcta operación del mismo. Debe mantenerse siempre en las condiciones originales, para que los trabajos conexos, no tengan margen de error.
Árbol de levas: Elemento mecánico que compone el sistema de distribución del motor y que en conjunto con el resto de partes determina la correcta puesta a punto.
Designación de los cilindros: De acuerdo con las normas ISO 1204 y DIN 6265, la designación de los cilindros empieza por el lado de accionamiento. En un motor en V, los cilindros del lado izquierdo, vistos desde el extremo de accionamiento, se denominan A1, A2, etc., y los del bloque derecho, B1, B2, etc.
Giro del motor: Puede ser CW o CCW.
Marcas del volante: Son marcaciones realizadas en el volante del motor que determinan gráficamente el TDC para cada cilindro.
Orden de encendido: Secuencia que determina el ciclo de la combustión en cada uno de los cilindros del motor. Responde a las características del diseño del motor, y está registrado en el manual de instrucciones de cada fabricante.
Cursos recomendados






%252FImagen%252FRAMPREDYC-1730060420837.webp%3Falt%3Dmedia%26token%3D2634a7f0-988e-4022-b91f-382503e6e9db&w=3840&q=75)

Procedimiento
De acuerdo con las especificaciones de los manuales de instrucciones del motor diesel, el procedimiento respectivo esta descrito en el respectivo manual de mantenimiento OEM (Original Equipement Manufacturer) del motor. En algunos casos, se recomendará el uso de ciertas herramientas específicas para cada fabricante, ya sea para control o modificación de la calibración de válvulas. De manera adicional, en el referido documento se encontrará el valor del claro de válvulas que se deberá mantener.
Como se aprecia en la figura siguiente y que corresponde a un ejemplo real, está determinado un valor específico, que debe ser alcanzado con el mayor grado de precisión posible.

Es muy importante hacer notar, además, que las tareas relacionadas con el plan de mantenimiento deberán ser ejecutados por técnicos calificados y certificados con la finalidad de preservar el equipo y la integridad de las personas.
Una vez que se procede con la ejecución de los pasos indicados en el documento técnico que guía las labores respectivas, se procede a instalar el reloj indicador, y en base a la indicación específica, se procede a determinar el claro de válvulas correspondiente, tanto para admisión como para escape.
La importancia de utilizar este equipo, que se puede apreciar en la figura 3, radica en el hecho que este dispositivo mide desplazamiento lineal, logrando así determinar la holgura de manera directa y precisa, y no en base a la apreciación individual de cada técnico cuando se usa el método de galgas.

Conclusiones
Con el procedimiento de calibración de válvulas de admisión y escape con dial indicador, se llega a determinar las siguientes definiciones:
- El método de calibración de válvulas con reloj indicador es más preciso con relación al método de galgas.
- Una vez determinado de la manera correcta el espacio entre balancín y horquilla, bastara con instalar el comparador, para saber si la holgura de válvulas es la adecuada. De esta manera, se optimiza el tiempo requerido para completar esta tarea, cambiando de manera esencial el procedimiento.
- Un reloj indicador mide movimiento vertical, de tal manera que con el uso de este método, el claro de válvulas se determina de manera cuantificable y no está sujeto al criterio del operador (persona a cargo de la ejecución de la tarea).
Existen además en el mercado, modelos e indicadores de carátula con versiones electrónicas equipadas con señal bluetooth, lo cual permite inclusive llevar en tiempo real el historial de cada calibración realizada, para poder determinar tendencias y evolución en cada uno de los cabezotes trabajados.
Autor: Martin Cevallos
Manager de LubriCenter H.A.
Correo: martinic35@hotmail.com
Dinos qué te ha parecido el artículo
Artículos recomendados
3.1 Equipos naturales de trabajo

Repercusión de la depresión en Confiabilidad Humana

Curso de mantención industrial: ¿Qué es? ¡Descúbrelo!

La Confiabilidad: La Lucha del Bien Contra el Mal

Publica tu artículo en la revista #1 de Mantenimiento Industrial
Publicar un artículo en la revista es gratis, no tiene costo.
Solo debes asegurarte que no sea un artículo comercial.
¿Qué esperas?
O envía tu artículo directo: articulos@predictiva21.com
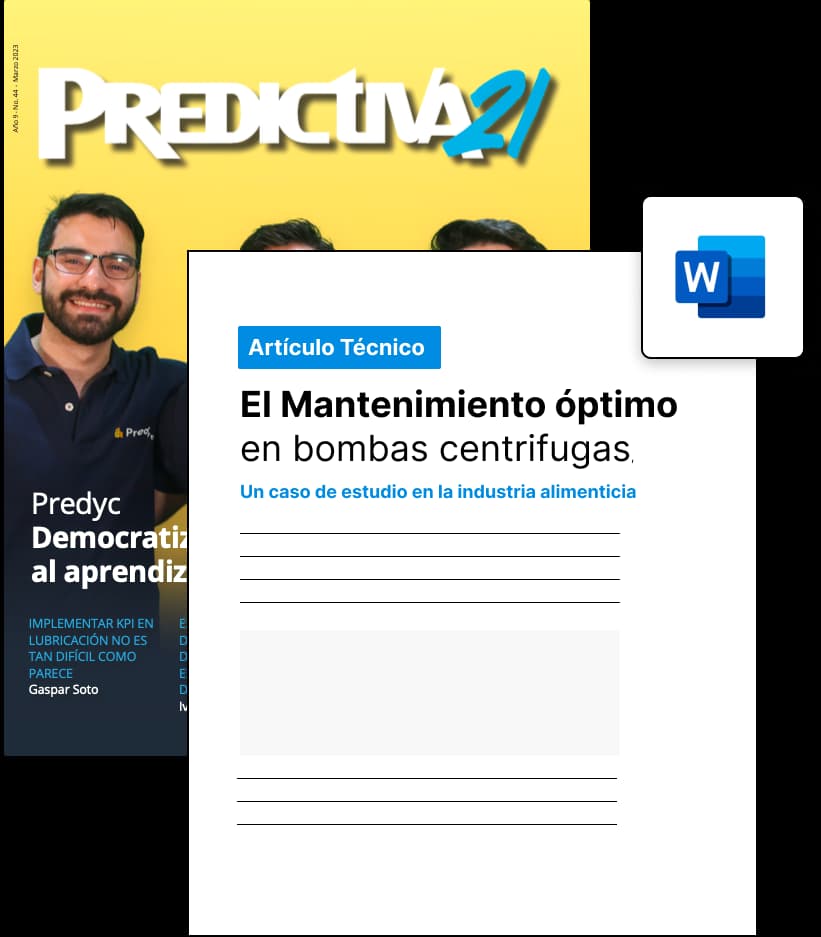
Calibración de válvulas en Motores Diésel de velocidad media
Articulo 12 de junio de 2019De acuerdo con los programas de mantenimiento preventivo de las unidades de combustión interna diésel en centrales eléctricas, independientemente de las marcas o modelos de las unidades de combustión interna, una de las tareas del plan de mantenimiento es la calibración de válvulas del motor.
En las unidades de generación eléctrica (y en el equipo o road), la referencia para la ejecución de los diferentes planes de mantenimiento preventivo esta dado en función de las horas de operación del motor.
Objetivo
Determinar el procedimiento técnico correspondiente a la calibración de válvulas de un motor, utilizando equipos de medición y comprobación. La herramienta seleccionada es el dial indicador. Esto permitirá además mantener un archivo documentado de la variación del claro de válvulas acorde con las horas de operación de los cabezotes. En la figura 1 se puede apreciar el dial, herramienta de precisión. Como parte fundamental del presente artículo, buscamos demostrar la importancia de utilizar equipos de comprobación.

Definiciones
Antes de proceder a la explicación del tema, deberemos presentar la terminología a utilizar, a fin de estandarizar conceptos:
Calibración de válvulas: Procedimiento utilizado en los motores de combustión interna, y que sirve para asegurar que las válvulas del motor se cierren completamente cuando el grado de dilatación térmica de los materiales ha sido alcanzado. Esta medida está determinada por el fabricante del equipo y debe controlarse periódicamente. Es una tarea requerida por el programa de mantenimiento y se realiza cada cierto número horas de operación o en caso de desmontaje de partes relacionadas.
El método más común utilizado en los motores es tornillo-contratuerca.
Válvulas del cabezote de motor diesel: Elementos de construcción mecánica que permiten el ingreso del aire a la cámara de combustión (válvulas de admisión) y la salida de los gases resultantes de la combustión producida (válvulas de escape).
TDC: Por sus siglas en inglés, Top Dead Center, y se refiere al momento de giro del cigüeñal y su conjunto biela- pistón, en el que el movimiento alternativo de este llega a su parte más alta y cambia de dirección.
BDC: Bottom Dead Center, es la posición contraria a la anterior, y es el momento en el que el pistón del motor llega a la parte más baja de su recorrido en el cilindro para iniciar su movimiento ascendente (hacia el TDC).
Cabezote: Componente que constituye la parte alta del motor y determina uno de los límites que forman la cámara de combustión. Está compuesto por las válvulas, balancines, inyector de combustible y ductos de lubricación, entre otros.
Ciclo del motor diesel: Eventos ocurridos durante la operación del motor y que están determinados por el fabricante del motor. Para información general estos son: admisión, compresión; combustión y escape.
Sincronización del motor: Es un estado determinado por el fabricante y define la correcta operación del mismo. Debe mantenerse siempre en las condiciones originales, para que los trabajos conexos, no tengan margen de error.
Árbol de levas: Elemento mecánico que compone el sistema de distribución del motor y que en conjunto con el resto de partes determina la correcta puesta a punto.
Designación de los cilindros: De acuerdo con las normas ISO 1204 y DIN 6265, la designación de los cilindros empieza por el lado de accionamiento. En un motor en V, los cilindros del lado izquierdo, vistos desde el extremo de accionamiento, se denominan A1, A2, etc., y los del bloque derecho, B1, B2, etc.
Giro del motor: Puede ser CW o CCW.
Marcas del volante: Son marcaciones realizadas en el volante del motor que determinan gráficamente el TDC para cada cilindro.
Orden de encendido: Secuencia que determina el ciclo de la combustión en cada uno de los cilindros del motor. Responde a las características del diseño del motor, y está registrado en el manual de instrucciones de cada fabricante.
Cursos recomendados






%252FImagen%252FRAMPREDYC-1730060420837.webp%3Falt%3Dmedia%26token%3D2634a7f0-988e-4022-b91f-382503e6e9db&w=3840&q=75)

Procedimiento
De acuerdo con las especificaciones de los manuales de instrucciones del motor diesel, el procedimiento respectivo esta descrito en el respectivo manual de mantenimiento OEM (Original Equipement Manufacturer) del motor. En algunos casos, se recomendará el uso de ciertas herramientas específicas para cada fabricante, ya sea para control o modificación de la calibración de válvulas. De manera adicional, en el referido documento se encontrará el valor del claro de válvulas que se deberá mantener.
Como se aprecia en la figura siguiente y que corresponde a un ejemplo real, está determinado un valor específico, que debe ser alcanzado con el mayor grado de precisión posible.

Es muy importante hacer notar, además, que las tareas relacionadas con el plan de mantenimiento deberán ser ejecutados por técnicos calificados y certificados con la finalidad de preservar el equipo y la integridad de las personas.
Una vez que se procede con la ejecución de los pasos indicados en el documento técnico que guía las labores respectivas, se procede a instalar el reloj indicador, y en base a la indicación específica, se procede a determinar el claro de válvulas correspondiente, tanto para admisión como para escape.
La importancia de utilizar este equipo, que se puede apreciar en la figura 3, radica en el hecho que este dispositivo mide desplazamiento lineal, logrando así determinar la holgura de manera directa y precisa, y no en base a la apreciación individual de cada técnico cuando se usa el método de galgas.

Conclusiones
Con el procedimiento de calibración de válvulas de admisión y escape con dial indicador, se llega a determinar las siguientes definiciones:
- El método de calibración de válvulas con reloj indicador es más preciso con relación al método de galgas.
- Una vez determinado de la manera correcta el espacio entre balancín y horquilla, bastara con instalar el comparador, para saber si la holgura de válvulas es la adecuada. De esta manera, se optimiza el tiempo requerido para completar esta tarea, cambiando de manera esencial el procedimiento.
- Un reloj indicador mide movimiento vertical, de tal manera que con el uso de este método, el claro de válvulas se determina de manera cuantificable y no está sujeto al criterio del operador (persona a cargo de la ejecución de la tarea).
Existen además en el mercado, modelos e indicadores de carátula con versiones electrónicas equipadas con señal bluetooth, lo cual permite inclusive llevar en tiempo real el historial de cada calibración realizada, para poder determinar tendencias y evolución en cada uno de los cabezotes trabajados.
Autor: Martin Cevallos
Manager de LubriCenter H.A.
Correo: martinic35@hotmail.com
Dinos qué te ha parecido el artículo
Artículos recomendados
19.2.- ¿Qué Dicen el ASME B73.1 y el API 610 Sobre Vibración?

Innovación y crecimiento potencial energía renovable desde el mantenimiento.

Entrevista Angeles Ysidro

La Ingeniería Industrial - ¡Conócela!

Publica tu artículo en la revista #1 de Mantenimiento Industrial
Publicar un artículo en la revista es gratis, no tiene costo.
Solo debes asegurarte que no sea un artículo comercial.
¿Qué esperas?
O envía tu artículo directo: articulos@predictiva21.com
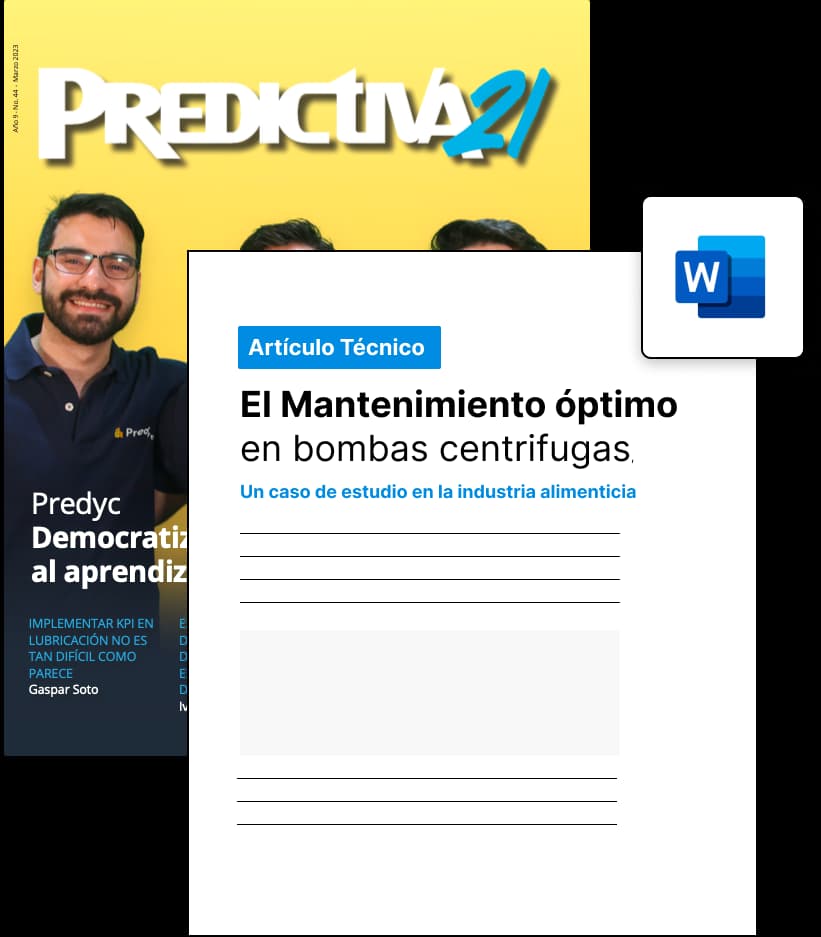