Cambios en la norma ISO 14224:2016 - Recolección e intercambio de data de confiabilidad y mantenimiento para equipos - Categorías de mantenimiento
Articulo23 de abril de 2019
Muchos en el área de mantenimiento y confiabilidad 24 estamos familiarizados con la norma ISO 142 “Petroleum, petrochemical and natural gas industries — Collection and exchange of reliability and maintenance data for equipment” – “Industrias del petróleo, petroquímica y gas natural – Recolección e intercambio de data de confiabilidad y mantenimiento para equipos”.
Quienes la consultamos, conocemos que el cuerpo de la norma es aplicable a otras industrias, mientras que la información incluida en los anexos si es mayormente aplicable a las industrias referidas en el título de la norma. Desde la primera edición de 1999 ha sido una fuente de consulta relevante en nuestro campo.
La segunda edición del 2006, fue una innovación importante y ahora luego de 10 años el Comité ISO/TC 67: Technical Committee, Materials, equipment and o shore structures for petroleum, petrochemical and natural gas industries; responsable de este estándar, publicó el pasado 15 de septiembre de 2016 la tercera versión.
¿Cuáles son los cambios principales efectuados en la norma ISO 14224:2016?
Como lo señala la norma en la página V de la introducción, los cambios principales se han dado en:
- Cláusula 3: Nuevas definiciones.
- Cláusulas 8 y 9: Cambios en figuras y tablas.
- Anexo A: Nuevas clases de equipos.
- Anexo B Nuevos modos de falla asociados y alineados.
- Anexo C: Cambios y nuevas sub cláusulas, como C.3.4 y C.7.
- Anexo E: Nuevos KPI.
- Anexo F: Alineamiento con el estándar ISO/TR 12489:2013.
Voy a referirme en este artículo a algunos de estos cambios en las Cláusulas 3, 8 y 9. Uno de ellos, es en las categorías del mantenimiento. La ISO 14224:2016 es más específica que la versión del 2006.
En la versión anterior la figura 6 Categorización del mantenimiento, nos mostraba las dos grandes categorías del mantenimiento: correctivo y preventivo y debajo de esta última tres subcategorías: Prueba e inspección, monitoreo por condición y periódico.
La Figura 6 Categorización del mantenimiento de la versión 2016 nos presenta ahora lo siguiente:
Tenemos que en la categoría del mantenimiento correctivo (2b), figuran ahora dos subcategorías, el mantenimiento correctivo diferido (4g), al que podemos identificar con el correctivo programado y el mantenimiento correctivo inmediato (4f), o emergencias, el menos apreciado y que buscamos minimizar.
Por su parte, en el lado del mantenimiento preventivo (2a), observamos primero, una división entre el mantenimiento preventivo basado en la condición (3a) y el predeterminado (3b) o periódico.
El mantenimiento preventivo basado en la condición tiene dos sub categorías, el monitoreo de condición (4b) que es nuestro mantenimiento predictivo clásico y el mantenimiento de “pruebas e inspecciones” (4a).
El mantenimiento predeterminado a su vez cuenta con tres subcategorías: Prueba periódica (4c), reemplazo programado (4d) y servicio programado (4e). Acompañan a la figura, algunas notas que refieren o clarifican algunos términos.
Particularmente, opino que la introducción y precisión de las definiciones de las categorías y subcategorías de mantenimiento, nos ayudarán a resolver dudas y zanjar discusiones de donde ubicar los tipos de mantenimiento que ejecutamos. Las definiciones de las órdenes de trabajo por las actividades de mantenimiento incluidas, podrían adecuarse a estas definiciones. Esto posteriormente se reflejará en la cantidad de órdenes de trabajo, horas hombre y costos por categoría de mantenimiento, y que serán el insumo para el cálculo de los indicadores de nuestra gestión del trabajo de mantenimiento (Pilar 5 del Cuerpo del Conocimiento de la SMRP).

Fuente: Norma ISO 14224:2016, página 42 Traducción y adaptación propia.
No perdamos de vista, que esta norma está dirigida a la gestión de la información de mantenimiento y confiabilidad con el objetivo que ésta sea suficiente y de calidad, ya que en el análisis de esta información se basarán las decisiones que tomemos. Así mismo, es pertinente recordar la importancia que la información tiene en la gestión de activos, definida en la cláusula 7.5 Requisitos de la información; de la norma ISO 55001:2014.
Echemos ahora una mirada a algunos cambios en las definiciones. La versión 2006 en 3.5, definía mantenimiento correctivo (2b) como “Mantenimiento realizado después del reconocimiento de una falla con la intención de devolver el ítem a un estado en el cual pueda ejecutar la función requerida”. La versión 2016 la reemplaza en 3.8 por la siguiente: “Mantenimiento realizado después de la detección de una falla para efectos de restablecimiento.”
Esta modificación, es consecuencia del cambio en la fuente de la definición, la norma IEC 60050 International electrotechnical vocabulary - Part 192: Dependability, que fue actualizada de la versión de 1990 a la de 2015. La nueva definición es más breve, deja de aludir a la función requerida, la cual queda implícitamente incluida al usar la palabra “restablecimiento”. La palabra en el texto original en inglés es restoration, la cual puede ser traducida por restauración o restablecimiento en nuestro idioma, me parece más apropiada la segunda.
Para el mantenimiento preventivo (2 a), en la versión del 2006 encontrábamos en 3.42: “Mantenimiento realizado a intervalos predeterminados o de acuerdo con un criterio prescrito con la intención de reducir la probabilidad de falla o la degradación del funcionamiento de un ítem.” La última versión señala en 3.78: “Mantenimiento realizado para mitigar la degradación y reducir la probabilidad de fallo”. Nuevamente la fuente de la nueva definición es la IEC 60050-192:2015. Aquí encontramos que la definición deja de lado la alusión a intervalos predeterminados o criterio prescrito, con el fin de precisar estas características en las dos subcategorías correspondientes: mantenimiento preventivo basado en la condición (3 a) y mantenimiento preventivo predeterminado (3b).
La definición de mantenimiento basado en la condición (3 a) (CBM por sus siglas en inglés), ausente en la versión del 2006, ha sido ahora incluida en 3.7 como: “mantenimiento preventivo basado en la evaluación de la condición física”.
Para el mantenimiento predeterminado, nos re ere a la definición del estándar europeo EN 13306:2010 Maintenance - Maintenance terminology: “Mantenimiento preventivo ejecutado de acuerdo con intervalos establecidos de tiempo, número de unidades o uso pero sin investigación previa de la condición”. Deja claro, la norma en esta definición, la ejecución del mantenimiento con intervalos establecidos, sin evaluar la condición. En el último nivel de categorías de mantenimiento, solo encontramos en la norma definición para 3.74 Prueba periódica: “Operación planificada realizada a intervalos de tiempo constantes con el fin de detectar potenciales fallos ocultos que pueden haberse producido entretanto.”
Finalmente, incluye la versión 2016 dos definiciones ausentes en la versión previa; en 3.76 mantenimiento planeado /mantenimiento programado /Mantenimiento preventivo planeado y en 3.77 mantenimiento predictivo (PdM) no señaladas como categorías de mantenimiento en la figura mostrada líneas arriba, pero de uso frecuente en nuestro trabajo diario.
Llegó hasta aquí con esta revisión de los términos y definiciones para las categorías o tipos de mantenimiento en la ISO 14224:2016. Esta versión tiene 280 páginas versus las 182 de la versión del 2006, así que tenemos aún mucho material por revisar. Como siempre, enfocados en que las características de la data de mantenimiento y confiabilidad que gestionamos, sean las requeridas para el análisis y toma de decisiones del negocio.
Autor: Víctor D. Manríquez
Ingeniero Mecánico
CMRP, CAMA
Mag. Energías Renovables
Consultor Senior & Docente en Mantenimiento, Confiabilidad & Gestión de Activos
Perú
Correo: vmanriquez62@yahoo.es
Dinos qué te ha parecido el artículo
Artículos recomendados
Las Revoluciones Industriales en el Mundo (II Parte)

Podcast de Gestión de Activos

Desgaste de los discos del rotor en turbinas de gas industriales: experiencia, riesgo, prevención, corrección y recomendaciones

17° Congreso Uruman 2021, Tecnología y Cultura Digital: Confiabilidad para el mundo del mañana.

Publica tu artículo en la revista #1 de Mantenimiento Industrial
Publicar un artículo en la revista es gratis, no tiene costo.
Solo debes asegurarte que no sea un artículo comercial.
¿Qué esperas?
O envía tu artículo directo: articulos@predictiva21.com
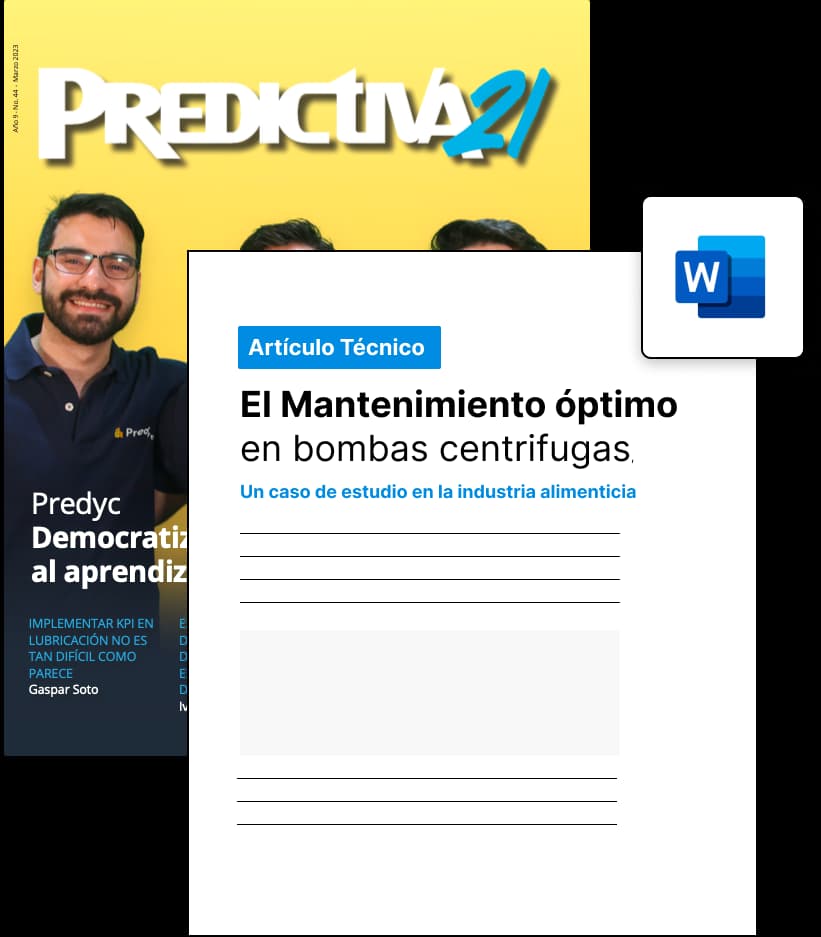
Cambios en la norma ISO 14224:2016 - Recolección e intercambio de data de confiabilidad y mantenimiento para equipos - Categorías de mantenimiento
Articulo 23 de abril de 2019Muchos en el área de mantenimiento y confiabilidad 24 estamos familiarizados con la norma ISO 142 “Petroleum, petrochemical and natural gas industries — Collection and exchange of reliability and maintenance data for equipment” – “Industrias del petróleo, petroquímica y gas natural – Recolección e intercambio de data de confiabilidad y mantenimiento para equipos”.
Quienes la consultamos, conocemos que el cuerpo de la norma es aplicable a otras industrias, mientras que la información incluida en los anexos si es mayormente aplicable a las industrias referidas en el título de la norma. Desde la primera edición de 1999 ha sido una fuente de consulta relevante en nuestro campo.
La segunda edición del 2006, fue una innovación importante y ahora luego de 10 años el Comité ISO/TC 67: Technical Committee, Materials, equipment and o shore structures for petroleum, petrochemical and natural gas industries; responsable de este estándar, publicó el pasado 15 de septiembre de 2016 la tercera versión.
¿Cuáles son los cambios principales efectuados en la norma ISO 14224:2016?
Como lo señala la norma en la página V de la introducción, los cambios principales se han dado en:
- Cláusula 3: Nuevas definiciones.
- Cláusulas 8 y 9: Cambios en figuras y tablas.
- Anexo A: Nuevas clases de equipos.
- Anexo B Nuevos modos de falla asociados y alineados.
- Anexo C: Cambios y nuevas sub cláusulas, como C.3.4 y C.7.
- Anexo E: Nuevos KPI.
- Anexo F: Alineamiento con el estándar ISO/TR 12489:2013.
Voy a referirme en este artículo a algunos de estos cambios en las Cláusulas 3, 8 y 9. Uno de ellos, es en las categorías del mantenimiento. La ISO 14224:2016 es más específica que la versión del 2006.
En la versión anterior la figura 6 Categorización del mantenimiento, nos mostraba las dos grandes categorías del mantenimiento: correctivo y preventivo y debajo de esta última tres subcategorías: Prueba e inspección, monitoreo por condición y periódico.
La Figura 6 Categorización del mantenimiento de la versión 2016 nos presenta ahora lo siguiente:
Tenemos que en la categoría del mantenimiento correctivo (2b), figuran ahora dos subcategorías, el mantenimiento correctivo diferido (4g), al que podemos identificar con el correctivo programado y el mantenimiento correctivo inmediato (4f), o emergencias, el menos apreciado y que buscamos minimizar.
Por su parte, en el lado del mantenimiento preventivo (2a), observamos primero, una división entre el mantenimiento preventivo basado en la condición (3a) y el predeterminado (3b) o periódico.
El mantenimiento preventivo basado en la condición tiene dos sub categorías, el monitoreo de condición (4b) que es nuestro mantenimiento predictivo clásico y el mantenimiento de “pruebas e inspecciones” (4a).
El mantenimiento predeterminado a su vez cuenta con tres subcategorías: Prueba periódica (4c), reemplazo programado (4d) y servicio programado (4e). Acompañan a la figura, algunas notas que refieren o clarifican algunos términos.
Particularmente, opino que la introducción y precisión de las definiciones de las categorías y subcategorías de mantenimiento, nos ayudarán a resolver dudas y zanjar discusiones de donde ubicar los tipos de mantenimiento que ejecutamos. Las definiciones de las órdenes de trabajo por las actividades de mantenimiento incluidas, podrían adecuarse a estas definiciones. Esto posteriormente se reflejará en la cantidad de órdenes de trabajo, horas hombre y costos por categoría de mantenimiento, y que serán el insumo para el cálculo de los indicadores de nuestra gestión del trabajo de mantenimiento (Pilar 5 del Cuerpo del Conocimiento de la SMRP).

Fuente: Norma ISO 14224:2016, página 42 Traducción y adaptación propia.
No perdamos de vista, que esta norma está dirigida a la gestión de la información de mantenimiento y confiabilidad con el objetivo que ésta sea suficiente y de calidad, ya que en el análisis de esta información se basarán las decisiones que tomemos. Así mismo, es pertinente recordar la importancia que la información tiene en la gestión de activos, definida en la cláusula 7.5 Requisitos de la información; de la norma ISO 55001:2014.
Echemos ahora una mirada a algunos cambios en las definiciones. La versión 2006 en 3.5, definía mantenimiento correctivo (2b) como “Mantenimiento realizado después del reconocimiento de una falla con la intención de devolver el ítem a un estado en el cual pueda ejecutar la función requerida”. La versión 2016 la reemplaza en 3.8 por la siguiente: “Mantenimiento realizado después de la detección de una falla para efectos de restablecimiento.”
Esta modificación, es consecuencia del cambio en la fuente de la definición, la norma IEC 60050 International electrotechnical vocabulary - Part 192: Dependability, que fue actualizada de la versión de 1990 a la de 2015. La nueva definición es más breve, deja de aludir a la función requerida, la cual queda implícitamente incluida al usar la palabra “restablecimiento”. La palabra en el texto original en inglés es restoration, la cual puede ser traducida por restauración o restablecimiento en nuestro idioma, me parece más apropiada la segunda.
Para el mantenimiento preventivo (2 a), en la versión del 2006 encontrábamos en 3.42: “Mantenimiento realizado a intervalos predeterminados o de acuerdo con un criterio prescrito con la intención de reducir la probabilidad de falla o la degradación del funcionamiento de un ítem.” La última versión señala en 3.78: “Mantenimiento realizado para mitigar la degradación y reducir la probabilidad de fallo”. Nuevamente la fuente de la nueva definición es la IEC 60050-192:2015. Aquí encontramos que la definición deja de lado la alusión a intervalos predeterminados o criterio prescrito, con el fin de precisar estas características en las dos subcategorías correspondientes: mantenimiento preventivo basado en la condición (3 a) y mantenimiento preventivo predeterminado (3b).
La definición de mantenimiento basado en la condición (3 a) (CBM por sus siglas en inglés), ausente en la versión del 2006, ha sido ahora incluida en 3.7 como: “mantenimiento preventivo basado en la evaluación de la condición física”.
Para el mantenimiento predeterminado, nos re ere a la definición del estándar europeo EN 13306:2010 Maintenance - Maintenance terminology: “Mantenimiento preventivo ejecutado de acuerdo con intervalos establecidos de tiempo, número de unidades o uso pero sin investigación previa de la condición”. Deja claro, la norma en esta definición, la ejecución del mantenimiento con intervalos establecidos, sin evaluar la condición. En el último nivel de categorías de mantenimiento, solo encontramos en la norma definición para 3.74 Prueba periódica: “Operación planificada realizada a intervalos de tiempo constantes con el fin de detectar potenciales fallos ocultos que pueden haberse producido entretanto.”
Finalmente, incluye la versión 2016 dos definiciones ausentes en la versión previa; en 3.76 mantenimiento planeado /mantenimiento programado /Mantenimiento preventivo planeado y en 3.77 mantenimiento predictivo (PdM) no señaladas como categorías de mantenimiento en la figura mostrada líneas arriba, pero de uso frecuente en nuestro trabajo diario.
Llegó hasta aquí con esta revisión de los términos y definiciones para las categorías o tipos de mantenimiento en la ISO 14224:2016. Esta versión tiene 280 páginas versus las 182 de la versión del 2006, así que tenemos aún mucho material por revisar. Como siempre, enfocados en que las características de la data de mantenimiento y confiabilidad que gestionamos, sean las requeridas para el análisis y toma de decisiones del negocio.
Autor: Víctor D. Manríquez
Ingeniero Mecánico
CMRP, CAMA
Mag. Energías Renovables
Consultor Senior & Docente en Mantenimiento, Confiabilidad & Gestión de Activos
Perú
Correo: vmanriquez62@yahoo.es
Dinos qué te ha parecido el artículo
Artículos recomendados
Aplicación de un Estudio RAM a un Sistema de Bombeo

Disminución de los costos por hora en neumáticos de camiones mineros

7.4 Beneficios generados por el Análisis Causa Raíz

Desafíos que enfrentan los Gerentes de Mantenimiento

Publica tu artículo en la revista #1 de Mantenimiento Industrial
Publicar un artículo en la revista es gratis, no tiene costo.
Solo debes asegurarte que no sea un artículo comercial.
¿Qué esperas?
O envía tu artículo directo: articulos@predictiva21.com
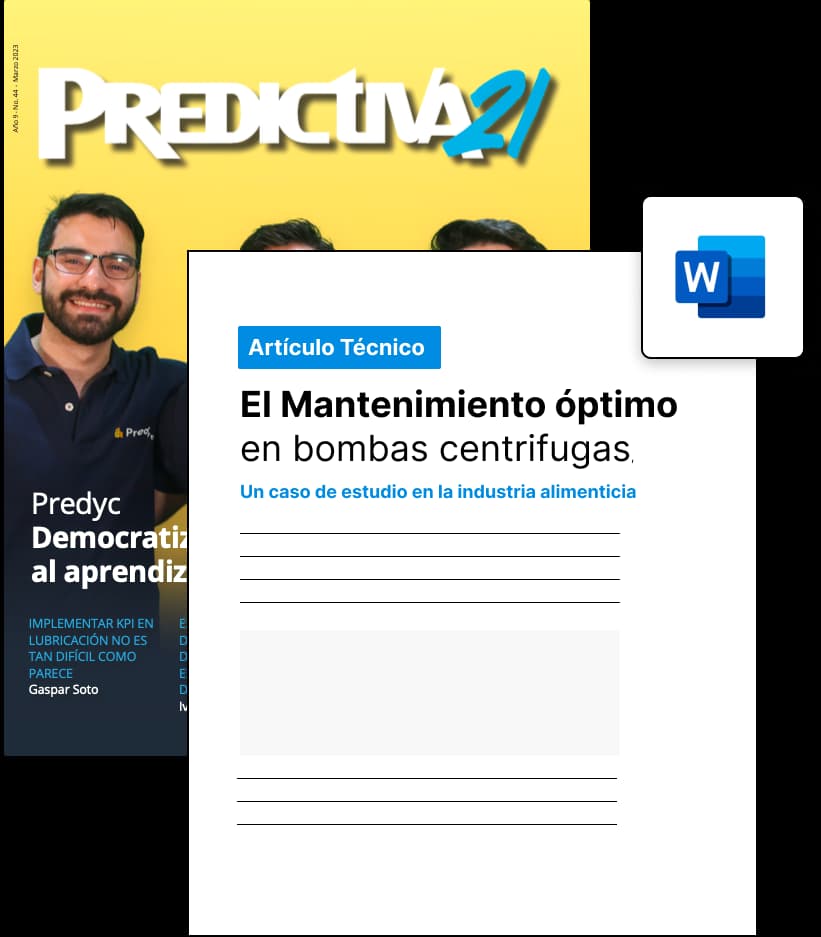