El Principio de Pareto y los “Malos Actores”
Articulo17 de junio de 2019
Es ampliamente conocido el uso de los diagramas de Pareto como herramienta de mejora en operaciones y mantenimiento, pero su uso no está circunscrito a estas áreas, es una herramienta de uso general.
Haciendo un poco de historia, el Principio de Pareto que da origen a los diagramas respectivos está basado en el fenómeno observado por el economista italiano Vilfredo Federico Damaso Pareto, quien en 1906 hizo la famosa observación de que el 20% de la población poseía el 80% de la propiedad en Italia. Si Pareto hubiera vivido en nuestros tiempos la observación. Si Pareto hubiera vivido en nuestros tiempos la observación le hubiera conducido quizás a establecer una proporción diferente de este porcentaje. (Según el informe OXFAM del 2015 el 1% de la población mundial acumula el 50% de la riqueza y el otro 50% se distribuye entre el 99% restante de la población, pero ese es otro tema).

(1848 – 1923)

Es interesante mencionar que allá por el año 2003 hubo una propuesta de renombrar este principio como “Principio de Juran”, iniciativa que partió de la American Society for Quality (ASQ), dado que fue en 1937, Joseph Juran quien dio a conocer el principio, tal como lo relató Luis Felipe Sexto en su artículo “¿Fin del Principio de Pareto?”. Esta iniciativa, como podemos comprobarlo, quedó en el olvido.
El principio de Pareto expone que existen usualmente unos cuantos contribuidores que son responsables de la mayor porción de problemas que están siendo investigados. Los otros contribuidores son típicamente responsables por una parte relativamente pequeña de los problemas.
Esto es frecuentemente fijado por la regla del 80/20, que dice que 80% de los problemas bajo investigación son causados por sólo el 20% de los contribuidores.
El proceso usual para construir un Diagrama de Pareto comprende cuatro pasos:
- Determinar cuáles son los contribuidores del problema que está siendo investigado.
- Determinar el nivel de contribución de cada contribuidor del problema.
- Dibujar un diagrama de barras de estos resultados.
- Agregar una línea mostrando el porcentaje acumulativo logrado por la sumatoria de cada contribuidor adicional.
Los principales contribuidores son denominados como los “pocos vitales” y los contribuidores menores como los “muchos triviales”.
También es frecuente a los “pocos vitales” denominarlos como los “top ten” o los “malos actores” siendo esta última la denominación que se ha convertido en la más usada, incluyendo a los anglófilos que se refieren a los “bad actors”. El término no alude a actores de películas serie B, a aquellos que nunca serán nominados y por lo tanto jamás ganarán un premio de la Academia, o a los que militan en las listas de los premios “Razzi” a las malas actuaciones.
Uno de los motivos para producir este artículo fueron tres eventos recientes, donde fue abordado el tema de los “malos actores”. En la primera de ellas en una reunión con la presencia de personal de operaciones, mantenimiento y contratista de mantenimiento, una lista de malos actores había sido propuesta sin un criterio de nido y basado en las apreciaciones personales de algunos de los asistentes. Una de las confusiones que pude percibir fue la de mezclar equipos críticos con malos actores. Para algunos de los asistentes un equipo de criticidad alta era un “mal actor” per se, otros apelaban a la forma en que este equipo afectaba la capacidad operativa de la sección de la planta a su cargo. También fue mencionada la frecuencia de las fallas de un equipo.
La segunda ocasión sucedió en otra reunión donde se nos informaba que el cliente de un servicio de mantenimiento solicitaba al contratista el reporte de los “malos actores”. ¿Cuál era el criterio?, de forma muy gaseosa se informaba que un bajo MTBF era el criterio para clasificar a un “mal actor”.
Finalmente, el tercer evento, se presentó cuando el área de confiabilidad de una planta presentó su lista de “malos actores” basados en el costo de mantenimiento, lo cual parecería bastante adecuado. Pero estos costos incluían los costos de mantenimientos preventivos y correctivos de los equipos, por lo cual mostraba una imagen errónea de los “malos actores”, puesto que los gastos del principal “mal actor” estaban compuestos de un 90% de gastos en mantenimiento preventivo. Si solo se consideraban eventos de mantenimiento correctivo el ranking variaba marcadamente. Esto ocasionaba que se prestara atención a “malos actores” que no lo eran en realidad.
¿Cuáles deben ser los criterios para elegir a los “malos actores”?. Anthony Smith en su libro “RCM - Gateway to World Class Maintenance” (RCM – Puerta al Mantenimiento de Clase Mundial) precisa tres criterios:
1. El costo del mantenimiento correctivo acumulado por el equipo en el período reciente de dos años.
El siguiente es un ejemplo de un diagrama de Pareto construido en base al costo del mantenimiento correctivo de los componentes de una flota de tractores (Ver figuras 1 y 2).


2. El número de eventos de mantenimiento correctivo ejecutados en el activo en el período reciente de dos años.
La figura presentada a continuación muestra un diagrama de Pareto por número de eventos para un conjunto de compresores reciprocantes de gas, donde se han agrupado las fallas por el modo de falla según ISO 14224:2006 para un período de 12 meses (Ver figura 3).

3. El número de horas atribuidas a paradas de planta en el período reciente de dos años.
La figura siguiente muestra un diagrama de Pareto por horas de parada de planta para un conjunto de compresores reciprocantes de gas, donde se han agrupado las fallas por el modo de falla según ISO 14224:2006 para un período de 12 meses (Ver Figura 4).

Con las capacidades actuales de procesamiento de información no deberíamos tener problemas para llevar los tres cómputos.
Usar solo el costo del mantenimiento correctivo deja de lado el impacto de la falla del equipo en la producción. En mi experiencia profesional me he topado con casos en los cuales el costo de los trabajos de mantenimiento correctivo es muy inferior al de los costos de la parada de planta ocasionada. En uno de ellos, el costo del mantenimiento correctivo estuvo en el orden de US$ 25 000 pero el costo de la producción no realizada alcanzó los US$ 1 200 000, es decir fue 48 veces el costo del correctivo. Esto podría detectarse usando un Pareto de horas de parada ocasionada por los activos.
Finalmente, un Pareto con malos actores por número de eventos, puede ayudarnos a identificar tareas recurrentes que pueden no ser de forma individual un mal actor, pero la acumulación de eventos similares y los recursos que deben de ser distraídos de otras tareas pueden convertirse en significativos para la distribución de recursos de personal, tomando en cuenta el tiempo de la tarea en sí como los tiempos administrativos por obtención de permisos de trabajos y otros asuntos de seguridad en el trabajo.
Lo recomendable es que nuestra organización desarrolle un documento que establezca los criterios que definirán los “malos actores” de nuestros Paretos, cuya eliminación contribuya al logro de los objetivos organizacionales.
Finalmente les dejo una idea para discutir. Leyendo el libro de Daniel Denett, “Intuition Pumps And Other Tools for Thinking”, encontré la “Ley de Sturgeon” que en inglés es expresada como “ninety percent of everything is crap”, (“noventa por ciento de todo es basura”) que alude a que el 90% de la producción literaria de ciencia ficción es de bajísima calidad. Ya hay quienes proponen extender esta ley a otros campos del quehacer de la humanidad.
Cursos recomendados




%252FImagen%252FRAMPREDYC-1730060420837.webp%3Falt%3Dmedia%26token%3D2634a7f0-988e-4022-b91f-382503e6e9db&w=3840&q=75)



Referencias
- Riqueza: Tenerlo todo y querer más, Oxfam International, Oxfam GB, 2015
- RCM--Gateway to World Class Maintenance by Anthony M. Smith and Glenn R. Hinchcli e, Butterworth-Heinemann; 2003
- Intuition Pumps And Other Tools for Thinking, Daniel Denett, W. W. Norton & Company, 2014Autor: Víctor D. Manríquez, CMRP Ingeniero Mecánico. Mag. Energías Renovables Líder de Confiabilidad CBI Peruana SAC Docente IPEMAN vmanriquez62@yahoo.es Perú
Autor: Víctor D. Manríquez
CMRP Ingeniero Mecánico.
Mag. Energías Renovables
Líder de Confiabilidad
CBI Peruana SAC
Docente IPEMAN
Perú
Correo: vmanriquez62@yahoo.es
Dinos qué te ha parecido el artículo
Artículos recomendados
Curso TPM y lo que aprenderás en uno

¿Qué es la transformación digital para el Mantenimiento Predictivo?

Propuesta de adopción de modelos de optimización de alcance, duración y costo en paradas de planta

Termografía I

Publica tu artículo en la revista #1 de Mantenimiento Industrial
Publicar un artículo en la revista es gratis, no tiene costo.
Solo debes asegurarte que no sea un artículo comercial.
¿Qué esperas?
O envía tu artículo directo: articulos@predictiva21.com
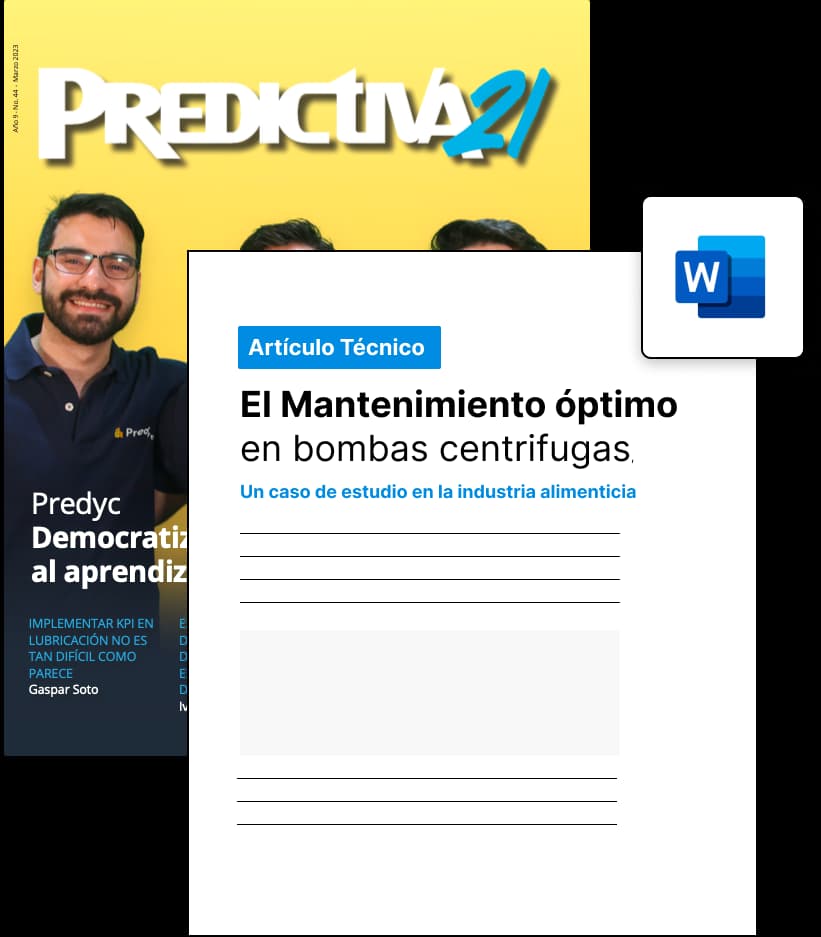
El Principio de Pareto y los “Malos Actores”
Articulo 17 de junio de 2019Es ampliamente conocido el uso de los diagramas de Pareto como herramienta de mejora en operaciones y mantenimiento, pero su uso no está circunscrito a estas áreas, es una herramienta de uso general.
Haciendo un poco de historia, el Principio de Pareto que da origen a los diagramas respectivos está basado en el fenómeno observado por el economista italiano Vilfredo Federico Damaso Pareto, quien en 1906 hizo la famosa observación de que el 20% de la población poseía el 80% de la propiedad en Italia. Si Pareto hubiera vivido en nuestros tiempos la observación. Si Pareto hubiera vivido en nuestros tiempos la observación le hubiera conducido quizás a establecer una proporción diferente de este porcentaje. (Según el informe OXFAM del 2015 el 1% de la población mundial acumula el 50% de la riqueza y el otro 50% se distribuye entre el 99% restante de la población, pero ese es otro tema).

(1848 – 1923)

Es interesante mencionar que allá por el año 2003 hubo una propuesta de renombrar este principio como “Principio de Juran”, iniciativa que partió de la American Society for Quality (ASQ), dado que fue en 1937, Joseph Juran quien dio a conocer el principio, tal como lo relató Luis Felipe Sexto en su artículo “¿Fin del Principio de Pareto?”. Esta iniciativa, como podemos comprobarlo, quedó en el olvido.
El principio de Pareto expone que existen usualmente unos cuantos contribuidores que son responsables de la mayor porción de problemas que están siendo investigados. Los otros contribuidores son típicamente responsables por una parte relativamente pequeña de los problemas.
Esto es frecuentemente fijado por la regla del 80/20, que dice que 80% de los problemas bajo investigación son causados por sólo el 20% de los contribuidores.
El proceso usual para construir un Diagrama de Pareto comprende cuatro pasos:
- Determinar cuáles son los contribuidores del problema que está siendo investigado.
- Determinar el nivel de contribución de cada contribuidor del problema.
- Dibujar un diagrama de barras de estos resultados.
- Agregar una línea mostrando el porcentaje acumulativo logrado por la sumatoria de cada contribuidor adicional.
Los principales contribuidores son denominados como los “pocos vitales” y los contribuidores menores como los “muchos triviales”.
También es frecuente a los “pocos vitales” denominarlos como los “top ten” o los “malos actores” siendo esta última la denominación que se ha convertido en la más usada, incluyendo a los anglófilos que se refieren a los “bad actors”. El término no alude a actores de películas serie B, a aquellos que nunca serán nominados y por lo tanto jamás ganarán un premio de la Academia, o a los que militan en las listas de los premios “Razzi” a las malas actuaciones.
Uno de los motivos para producir este artículo fueron tres eventos recientes, donde fue abordado el tema de los “malos actores”. En la primera de ellas en una reunión con la presencia de personal de operaciones, mantenimiento y contratista de mantenimiento, una lista de malos actores había sido propuesta sin un criterio de nido y basado en las apreciaciones personales de algunos de los asistentes. Una de las confusiones que pude percibir fue la de mezclar equipos críticos con malos actores. Para algunos de los asistentes un equipo de criticidad alta era un “mal actor” per se, otros apelaban a la forma en que este equipo afectaba la capacidad operativa de la sección de la planta a su cargo. También fue mencionada la frecuencia de las fallas de un equipo.
La segunda ocasión sucedió en otra reunión donde se nos informaba que el cliente de un servicio de mantenimiento solicitaba al contratista el reporte de los “malos actores”. ¿Cuál era el criterio?, de forma muy gaseosa se informaba que un bajo MTBF era el criterio para clasificar a un “mal actor”.
Finalmente, el tercer evento, se presentó cuando el área de confiabilidad de una planta presentó su lista de “malos actores” basados en el costo de mantenimiento, lo cual parecería bastante adecuado. Pero estos costos incluían los costos de mantenimientos preventivos y correctivos de los equipos, por lo cual mostraba una imagen errónea de los “malos actores”, puesto que los gastos del principal “mal actor” estaban compuestos de un 90% de gastos en mantenimiento preventivo. Si solo se consideraban eventos de mantenimiento correctivo el ranking variaba marcadamente. Esto ocasionaba que se prestara atención a “malos actores” que no lo eran en realidad.
¿Cuáles deben ser los criterios para elegir a los “malos actores”?. Anthony Smith en su libro “RCM - Gateway to World Class Maintenance” (RCM – Puerta al Mantenimiento de Clase Mundial) precisa tres criterios:
1. El costo del mantenimiento correctivo acumulado por el equipo en el período reciente de dos años.
El siguiente es un ejemplo de un diagrama de Pareto construido en base al costo del mantenimiento correctivo de los componentes de una flota de tractores (Ver figuras 1 y 2).


2. El número de eventos de mantenimiento correctivo ejecutados en el activo en el período reciente de dos años.
La figura presentada a continuación muestra un diagrama de Pareto por número de eventos para un conjunto de compresores reciprocantes de gas, donde se han agrupado las fallas por el modo de falla según ISO 14224:2006 para un período de 12 meses (Ver figura 3).

3. El número de horas atribuidas a paradas de planta en el período reciente de dos años.
La figura siguiente muestra un diagrama de Pareto por horas de parada de planta para un conjunto de compresores reciprocantes de gas, donde se han agrupado las fallas por el modo de falla según ISO 14224:2006 para un período de 12 meses (Ver Figura 4).

Con las capacidades actuales de procesamiento de información no deberíamos tener problemas para llevar los tres cómputos.
Usar solo el costo del mantenimiento correctivo deja de lado el impacto de la falla del equipo en la producción. En mi experiencia profesional me he topado con casos en los cuales el costo de los trabajos de mantenimiento correctivo es muy inferior al de los costos de la parada de planta ocasionada. En uno de ellos, el costo del mantenimiento correctivo estuvo en el orden de US$ 25 000 pero el costo de la producción no realizada alcanzó los US$ 1 200 000, es decir fue 48 veces el costo del correctivo. Esto podría detectarse usando un Pareto de horas de parada ocasionada por los activos.
Finalmente, un Pareto con malos actores por número de eventos, puede ayudarnos a identificar tareas recurrentes que pueden no ser de forma individual un mal actor, pero la acumulación de eventos similares y los recursos que deben de ser distraídos de otras tareas pueden convertirse en significativos para la distribución de recursos de personal, tomando en cuenta el tiempo de la tarea en sí como los tiempos administrativos por obtención de permisos de trabajos y otros asuntos de seguridad en el trabajo.
Lo recomendable es que nuestra organización desarrolle un documento que establezca los criterios que definirán los “malos actores” de nuestros Paretos, cuya eliminación contribuya al logro de los objetivos organizacionales.
Finalmente les dejo una idea para discutir. Leyendo el libro de Daniel Denett, “Intuition Pumps And Other Tools for Thinking”, encontré la “Ley de Sturgeon” que en inglés es expresada como “ninety percent of everything is crap”, (“noventa por ciento de todo es basura”) que alude a que el 90% de la producción literaria de ciencia ficción es de bajísima calidad. Ya hay quienes proponen extender esta ley a otros campos del quehacer de la humanidad.
Cursos recomendados




%252FImagen%252FRAMPREDYC-1730060420837.webp%3Falt%3Dmedia%26token%3D2634a7f0-988e-4022-b91f-382503e6e9db&w=3840&q=75)



Referencias
- Riqueza: Tenerlo todo y querer más, Oxfam International, Oxfam GB, 2015
- RCM--Gateway to World Class Maintenance by Anthony M. Smith and Glenn R. Hinchcli e, Butterworth-Heinemann; 2003
- Intuition Pumps And Other Tools for Thinking, Daniel Denett, W. W. Norton & Company, 2014Autor: Víctor D. Manríquez, CMRP Ingeniero Mecánico. Mag. Energías Renovables Líder de Confiabilidad CBI Peruana SAC Docente IPEMAN vmanriquez62@yahoo.es Perú
Autor: Víctor D. Manríquez
CMRP Ingeniero Mecánico.
Mag. Energías Renovables
Líder de Confiabilidad
CBI Peruana SAC
Docente IPEMAN
Perú
Correo: vmanriquez62@yahoo.es
Dinos qué te ha parecido el artículo
Artículos recomendados
Serie: “Confiabilidad en Sistemas de misión Critica: Empezar por el Principio”. Sistemas de Puesta a Tierra (II Parte)

¿Cómo implementar de manera estratégica energías renovables en la Industria?

Uso y abuso del concepto “Creación de valor desde la gestión de mantenimiento”

Mantenimiento industrial

Publica tu artículo en la revista #1 de Mantenimiento Industrial
Publicar un artículo en la revista es gratis, no tiene costo.
Solo debes asegurarte que no sea un artículo comercial.
¿Qué esperas?
O envía tu artículo directo: articulos@predictiva21.com
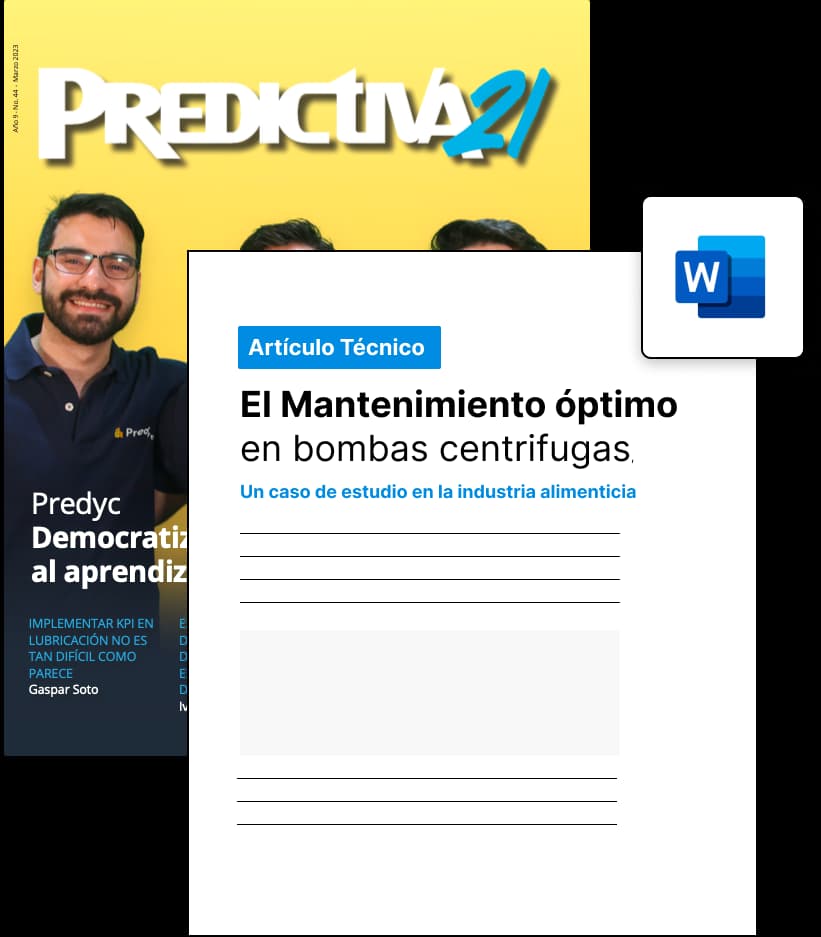