El valor del Mantenimiento Predictivo
Articulo25 de mayo de 2019
El concepto de mantenimiento ha evolucionado mucho en los últimos años, y esta tendencia ha sido y es manejada por estudiantes de mantenimiento, con el fin de explotar cada vez más las posibilidades de mejoras en los procesos industriales. Sin embargo, cada vez encontramos más aspectos de relevancia dignos de ser reevaluados, y que nos hacen reflexionar sobre si estamos utilizando las mejores prácticas. Este hecho refuerza la ideología personal de que nada de lo que tengo es tan bueno que no se puede mejorar, ya sea de procesos, diseño, procedimiento o incluso una simple buena práctica de mantenimiento.
La estrategia de gestión de activos trata de optimizar el negocio y la reducción de costes en todas las áreas. En general, el precio final de un producto, o incluso un servicio, se cuantifica en términos de cómo utiliza los recursos, materias primas y mano de obra para producir, así como los gastos financieros, logística, distribución, y también los costos para mantener la línea de producción. Por lo tanto, hay quienes dependen en casi su totalidad del mercado externo, lo que restringe a un menor número de acciones la estrategia de negocio, pero la mano de obra y mantenimiento de los activos físicos de la empresa están totalmente influidos por éste. Por lo tanto, la estrategia para reducir los costos de permanecer disponible para producir en la planta ha sido, durante muchos años, más conveniente para aumentar los beneficios y mejorar los resultados operativos.
Ideológicamente, no es posible comprar materias primas más baratas y reducir el precio pagado para llevar el producto al cliente, lo mejor es asegurarse de que la planta tenga un alto rendimiento a bajo costo. Históricamente, el control de mantenimiento parece haber sido iniciado por la gestión de los costes. En la era de Taylor, ya se empiezan a enfocar las tareas que buscan una mayor eciencia de las actividades, con el objetivo de fomentar la optimización de tareas para reducir el esfuerzo y el tiempo a n de aumentar la rentabilidad. El principio de contabilidad en las empresas siempre nos llevó a dirigir la ideología para la producción, pero se puede utilizar de la misma manera en el mantenimiento, con el n de optimizar las actividades para reducir el gasto.
En este contexto, la evolución de las estrategias de mantenimiento está caminando, junto con la reducción de sus costes. Durante el período de 1920 a 1940 se impuso el mantenimiento correctivo en instalaciones industriales, que tenía una alta cantidad asignada en el costo de mantenimiento. Con los años, el mantenimiento preventivo comenzó a ganar espacio, y los costes empezaban a caer, y luego inmediatamente comenzó un enfoque preventivo con el uso de la evaluación del estado de la máquina, el mantenimiento predictivo o condicional. Para la época, se percibía el mantenimiento como una actividad de alto coste, aplicable sólo a pocos equipos de la planta, con alta importancia para el proceso productivo, y sólo en las empresas con mayor capital. Sin embargo, en los últimos años este punto de vista fue cambiando a medida que el servicio comenzó a ser estudiado, llegando a la conclusión de que cuanto más estratégica la tarea de mantenimiento, menor será el costo de esta actividad. La figura 01 ilustra un autor brasileño de renombre, Alan Kardec, que demuestra gráficamente esta idea con referencia al valor y resultados para la empresa.

Con los años el mantenimiento predictivo comenzó a ser aplicado cada vez más en las empresas. A esto se sumó el hecho de la evolución misma del concepto del mantenimiento como centro de costos. Con la revolución digital, los costos de esta actividad se redujeron considerablemente, pues el precio de las herramientas digitales lo hizo mucho más accesible. Las herramientas analógicas que se utilizaron en los años 30´s y 40´s eran muy costosas, difíciles de manipular (debido a su tamaño) y mucho más lentas o limitadas para cierto tipo de aplicaciones. Los ordenadores portátiles y los microprocesadores no tenían la capacidad de procesamiento de información de trabajo, el volumen de datos generados era mucho menor que el de hoy en día, y el tamaño de las máquinas utilizadas para estos propósitos eran muy grandes. Con la reducción de los elementos y costos que intervienen en la ejecución del mantenimiento predictivo, muchas empresas han entrado en el campo de la externalización de estas actividades, el aumento de la oferta de este tipo de servicios, y cómo las pequeñas empresas tienen costos más bajos que medianas y grandes. Pioneras como SKF, Bruel y 01dB, comenzaron a cobrar precios mucho más bajos. Luego, alrededor de los años 90 las empresas comenzaron a innovar, cambiando la forma de vender esta estrategia de mantenimiento, haciendo contratos de desempeño centrada en los resultados, uniendo los servicios predictivos en el mismo paquete que los de lubricación, reparaciones o la entrega de los rodamientos. La estrategia estuvo orientada a valorar la predicción, lo que a su vez elevó el valor y el costo de esta actividad.
Siguiendo esta línea de tiempo descrito para el mantenimiento predictivo, se puede entender por qué tenía fama de mantenimiento caro, una idea que aún persiste. Esta es una visión muy equivocada de predicción, porque hoy en día el dinero es muy atractivo. Incluso en los viejos tiempos, cuando esta costaba más, la rentabilidad de la producción aplicando esta estrategia de seguimiento en las empresas demostró la valía de esta inversión. Hoy en día, el valor utilizado en la implementación de un mantenimiento predictivo se recupera en el corto plazo y se ha convertido en obligatorio para las empresas que tratan de alcanzar un nivel de clase mundial de excelencia en el servicio. La imagen que "predictivo caro" debería suprimirse, ya que no era real en el pasado y en la actualidad no tiene sentido. El retorno está garantizado..
Cursos recomendados






%252FImagen%252FRAMPREDYC-1730060420837.webp%3Falt%3Dmedia%26token%3D2634a7f0-988e-4022-b91f-382503e6e9db&w=3840&q=75)

Referencias
http://www.abraman.org.br/noticias/artigo-a-evoluc ao-do-processo-de-gestao, Alan Kardec, site da ABRAMAN, em 16/06/2015.
Autor: Ing. Franklin da Silva Nonato
Dinos qué te ha parecido el artículo
Artículos recomendados
Lazos de corrosión, como parte fundamental de la metodología de inspección basada en riesgo

Aplicaciones mecánicas de la Termografía

Cálculo de la viscosidad de aceite básico en la grasa para la lubricación de rodamientos

La termografía y el mantenimiento predictivo

Publica tu artículo en la revista #1 de Mantenimiento Industrial
Publicar un artículo en la revista es gratis, no tiene costo.
Solo debes asegurarte que no sea un artículo comercial.
¿Qué esperas?
O envía tu artículo directo: articulos@predictiva21.com
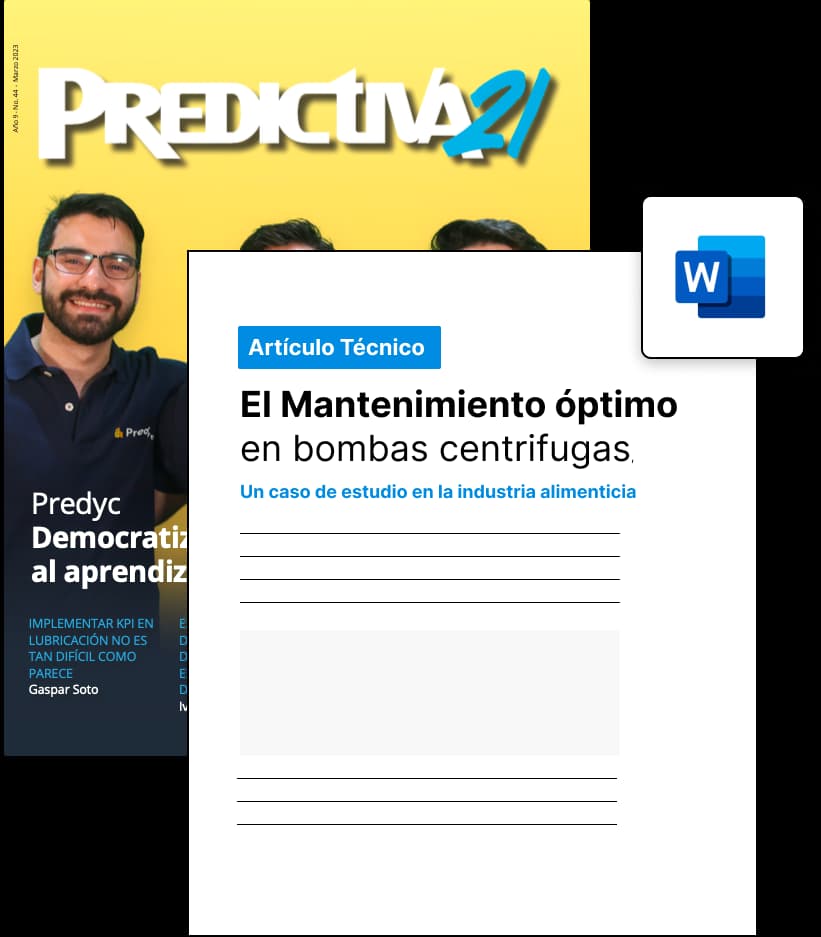
El valor del Mantenimiento Predictivo
Articulo 25 de mayo de 2019El concepto de mantenimiento ha evolucionado mucho en los últimos años, y esta tendencia ha sido y es manejada por estudiantes de mantenimiento, con el fin de explotar cada vez más las posibilidades de mejoras en los procesos industriales. Sin embargo, cada vez encontramos más aspectos de relevancia dignos de ser reevaluados, y que nos hacen reflexionar sobre si estamos utilizando las mejores prácticas. Este hecho refuerza la ideología personal de que nada de lo que tengo es tan bueno que no se puede mejorar, ya sea de procesos, diseño, procedimiento o incluso una simple buena práctica de mantenimiento.
La estrategia de gestión de activos trata de optimizar el negocio y la reducción de costes en todas las áreas. En general, el precio final de un producto, o incluso un servicio, se cuantifica en términos de cómo utiliza los recursos, materias primas y mano de obra para producir, así como los gastos financieros, logística, distribución, y también los costos para mantener la línea de producción. Por lo tanto, hay quienes dependen en casi su totalidad del mercado externo, lo que restringe a un menor número de acciones la estrategia de negocio, pero la mano de obra y mantenimiento de los activos físicos de la empresa están totalmente influidos por éste. Por lo tanto, la estrategia para reducir los costos de permanecer disponible para producir en la planta ha sido, durante muchos años, más conveniente para aumentar los beneficios y mejorar los resultados operativos.
Ideológicamente, no es posible comprar materias primas más baratas y reducir el precio pagado para llevar el producto al cliente, lo mejor es asegurarse de que la planta tenga un alto rendimiento a bajo costo. Históricamente, el control de mantenimiento parece haber sido iniciado por la gestión de los costes. En la era de Taylor, ya se empiezan a enfocar las tareas que buscan una mayor eciencia de las actividades, con el objetivo de fomentar la optimización de tareas para reducir el esfuerzo y el tiempo a n de aumentar la rentabilidad. El principio de contabilidad en las empresas siempre nos llevó a dirigir la ideología para la producción, pero se puede utilizar de la misma manera en el mantenimiento, con el n de optimizar las actividades para reducir el gasto.
En este contexto, la evolución de las estrategias de mantenimiento está caminando, junto con la reducción de sus costes. Durante el período de 1920 a 1940 se impuso el mantenimiento correctivo en instalaciones industriales, que tenía una alta cantidad asignada en el costo de mantenimiento. Con los años, el mantenimiento preventivo comenzó a ganar espacio, y los costes empezaban a caer, y luego inmediatamente comenzó un enfoque preventivo con el uso de la evaluación del estado de la máquina, el mantenimiento predictivo o condicional. Para la época, se percibía el mantenimiento como una actividad de alto coste, aplicable sólo a pocos equipos de la planta, con alta importancia para el proceso productivo, y sólo en las empresas con mayor capital. Sin embargo, en los últimos años este punto de vista fue cambiando a medida que el servicio comenzó a ser estudiado, llegando a la conclusión de que cuanto más estratégica la tarea de mantenimiento, menor será el costo de esta actividad. La figura 01 ilustra un autor brasileño de renombre, Alan Kardec, que demuestra gráficamente esta idea con referencia al valor y resultados para la empresa.

Con los años el mantenimiento predictivo comenzó a ser aplicado cada vez más en las empresas. A esto se sumó el hecho de la evolución misma del concepto del mantenimiento como centro de costos. Con la revolución digital, los costos de esta actividad se redujeron considerablemente, pues el precio de las herramientas digitales lo hizo mucho más accesible. Las herramientas analógicas que se utilizaron en los años 30´s y 40´s eran muy costosas, difíciles de manipular (debido a su tamaño) y mucho más lentas o limitadas para cierto tipo de aplicaciones. Los ordenadores portátiles y los microprocesadores no tenían la capacidad de procesamiento de información de trabajo, el volumen de datos generados era mucho menor que el de hoy en día, y el tamaño de las máquinas utilizadas para estos propósitos eran muy grandes. Con la reducción de los elementos y costos que intervienen en la ejecución del mantenimiento predictivo, muchas empresas han entrado en el campo de la externalización de estas actividades, el aumento de la oferta de este tipo de servicios, y cómo las pequeñas empresas tienen costos más bajos que medianas y grandes. Pioneras como SKF, Bruel y 01dB, comenzaron a cobrar precios mucho más bajos. Luego, alrededor de los años 90 las empresas comenzaron a innovar, cambiando la forma de vender esta estrategia de mantenimiento, haciendo contratos de desempeño centrada en los resultados, uniendo los servicios predictivos en el mismo paquete que los de lubricación, reparaciones o la entrega de los rodamientos. La estrategia estuvo orientada a valorar la predicción, lo que a su vez elevó el valor y el costo de esta actividad.
Siguiendo esta línea de tiempo descrito para el mantenimiento predictivo, se puede entender por qué tenía fama de mantenimiento caro, una idea que aún persiste. Esta es una visión muy equivocada de predicción, porque hoy en día el dinero es muy atractivo. Incluso en los viejos tiempos, cuando esta costaba más, la rentabilidad de la producción aplicando esta estrategia de seguimiento en las empresas demostró la valía de esta inversión. Hoy en día, el valor utilizado en la implementación de un mantenimiento predictivo se recupera en el corto plazo y se ha convertido en obligatorio para las empresas que tratan de alcanzar un nivel de clase mundial de excelencia en el servicio. La imagen que "predictivo caro" debería suprimirse, ya que no era real en el pasado y en la actualidad no tiene sentido. El retorno está garantizado..
Cursos recomendados






%252FImagen%252FRAMPREDYC-1730060420837.webp%3Falt%3Dmedia%26token%3D2634a7f0-988e-4022-b91f-382503e6e9db&w=3840&q=75)

Referencias
http://www.abraman.org.br/noticias/artigo-a-evoluc ao-do-processo-de-gestao, Alan Kardec, site da ABRAMAN, em 16/06/2015.
Autor: Ing. Franklin da Silva Nonato
Dinos qué te ha parecido el artículo
Artículos recomendados
El Know How y la Gestión del Activo Humano

LA OTRA VISIÓN DE LA CONFIABILIDAD OPERACIONAL

8.3 Filosofía del TPM

Alexis Lárez: Manager de Mantenimiento AEM 2020 - Rumbo al European Maintenance Manager Award EMMA 2021

Publica tu artículo en la revista #1 de Mantenimiento Industrial
Publicar un artículo en la revista es gratis, no tiene costo.
Solo debes asegurarte que no sea un artículo comercial.
¿Qué esperas?
O envía tu artículo directo: articulos@predictiva21.com
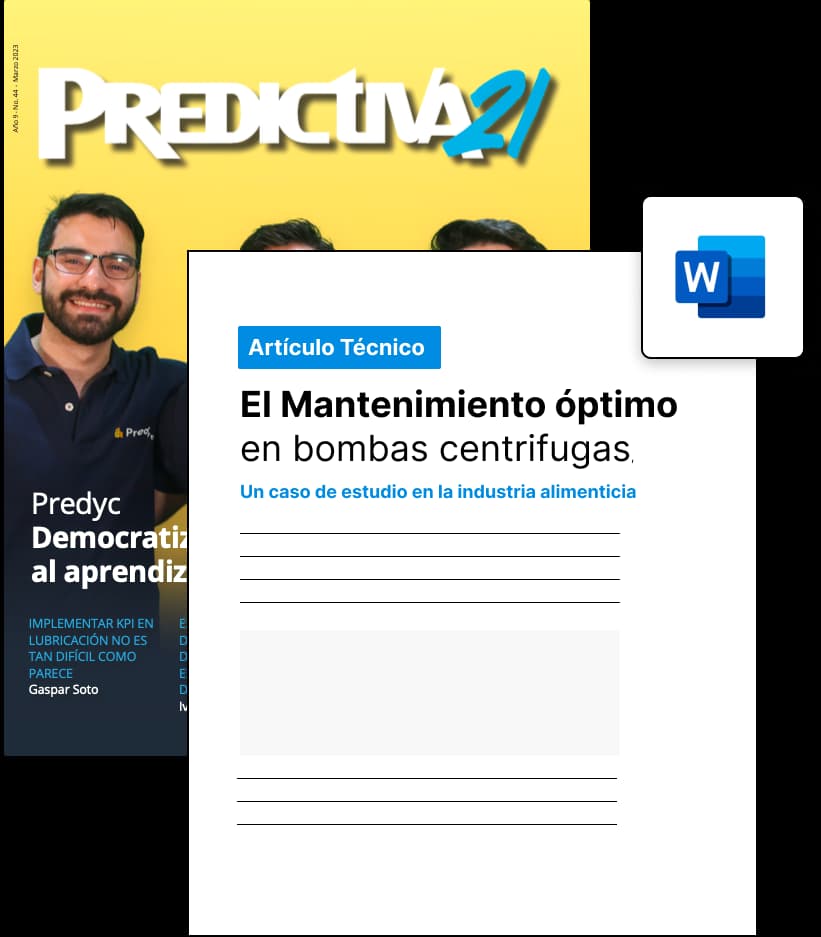