Practical Application of the Bayes Theorem for the Estimation of Availability in Industrial Assets
Articulo18 de marzo de 2020
During the development of any engineering study on reliability, one of the key activities for them to be performed effectively is the estimation of the failure and repair rate of an asset, which are meant to model statistically the availability of an asset through mathematical functions known as probability distributions, with the study of operation times and out-of-service times (see Fig. 1).


Whereas for repairable systems:
- Average Time of Operation = Mean Time Between Failures (MTBF)
- Average Time out of service = Mean Time to Repair (MTTR)
In this sense, an incorrect estimation of these values would negatively affect the results obtained in the studies performed, since we would be estimating based on an unreal behavior of the asset.
It’s important to emphasize that the failure and repair rates can be estimated through sources of different nature, be it generic or specific, that is, we can calculate them using the register of failures and repair of the asset itself or using the generic databases such as OREDA, IEE 497, PARLOC, EXIDA, among others, and even using the opinion of experts in an adequate way, trying to eliminate subjectivity, it’s an excellent source of information.
In this vein, Yañez and others, 2007, proposes the use of Bayes theorem to estimate failure rates and repair equipment. The author notes that this Theorem, "allows the combination of structured and mathematically supported form of the experience of others (prior knowledge) with experience (evidence), thereby obtaining more representative combination rates flaws operational reality the process under analysis (improved or updated knowledge)."
In this article we intend to show in a practical way and structured application of Bayes' theorem in the estimation of the availability of two turbo-generators and power generation system via Monte Carlo simulation.
Then, the estimation procedure thereof is shown.
Revision of the failure data
First, a revision of the failure data associated to the turbo generators was performed. In it, there was evidence that the record doesn’t separate the failures associated to the turbine from those of the generator, as required by the ISO 14224:2006 standards. This leads to the analysis of the turbo generation as a whole.
Hence, a summary of the operation times and out of service time from each turbo generator unit is shown. We should remark that each of the times was altered with the purpose of keeping their confidentiality.


Actualization of failure rate (Theorem of Bayes)
Next, based on the previous data and with the purpose of improving the times between the failure and the times of repair, the Theorem of Bayes was applied to reliability studies, proposed by Yañez (2007). Since, as mentioned before, it allows obtaining failure rates more adjusted to the operational reality of the asset, by means of combining the experience of others (use of generic data) with your own experience (failure register). See Fig.2.

Regarding generic data, information supplied by the Offshore Reliability Data (OREDA, 2009) was used, which is a complete database containing reliability and maintenance data from exploration and production equipment in the oil and gas industry. From it, all the failure modes downloaded from the database were used, either for the turbine and the generator as well.

From the Failure Register, the following data is obtained for the Turbogenerator TG-100:

Such data are substituted in the Equation 2, from the model:

The following data were obtained:

Likewise, the improved failure rate from the TG-101 turbo generator was estimated, obtaining the following historical data:

Substituting such data in Equation 2, the following data were obtained:

Cursos recomendados






%252FImagen%252FRAMPREDYC-1730060420837.webp%3Falt%3Dmedia%26token%3D2634a7f0-988e-4022-b91f-382503e6e9db&w=3840&q=75)

Modeling block diagram
From the information of improved failure rates, the Reliability Block Diagrams (RBD) were obtained, with the purpose of representing the architecture and operational philosophy of the generation system.
Thus, the RAPTOR 7 tool from ARINC was used, which allows modeling complex systems considering the operational philosophy and the times of failure and repair. Here, the operational philosophy of the turbo generator units in regular operations conditions appears under the philosophy k of n, 1 of 2, that is, one operating turbo generator and the other as a backup, which only starts to function in case of a programmed stop or failure from the other turbo generator. Also, the TG-101 generator is installed to operate only in case of the TG-100 turbo generator is out of service.
Hence, the proposed block diagram:

It´s important to emphasize that, with the purpose of simulating the real operational conditions and maintenance of equipment, programmed stops were considered for maintenance every 1,000 hours of operation, with a minimum duration of 72 hours, a maximum of 192 hours and an average of 168 hours.
Montecarlo simulation to estimate availability
After that, a simulation of the reliability block diagram (RBD) was performed using the Montecarlo simulation, which allows reducing the uncertainty in this kind of analysis.
The simulation of results for 50 iterations in the following 10 years of operations is presented in Table 4:


Likewise, in Figure 5, the results shown RAM parameters for year 10.

Discussion of results
From the simulation of results, we conclude:
- The annual availability for the turbogeneration system for year 10 is 99.79%, with a minimum of 99.68% and a maximum of 99.89%.
- The stochastic profile shows that the availability values of the system are above the international standards, since throughout the time, the availability will remain above 99%.
- The mean time between failures of the system is 1638.30 with a standard deviation of 571.52.
- The mean time to repair of the system is 3.23 hours, with a minimum of 2.38 hours and a maximum of 4.66 hours.
- Regarding the number of failures for the next 10 years, there is a minimum of 25 failures, a maximum of 101 and an average of 59 failures.
It´s important to emphasize that the results obtained must be updated with the enrichment of the failure register and repair of assets, since the estimated rates would come closer to their operational reality.
References
-Yañez Medardo, y Otros. (2007) "Confiabilidad Integral, Un Enfoque Práctico", Tomo II, Metodologías. R2M.
-ISO 14224. Industrias de petróleo y gas natural - Recolección e intercambio de datos de confiabilidad y mantenimiento de equipos, 2006.
-Ebeling, Charles. (2009) "An Introduction to Reliability and Maintainability Engineering". Waveland.
-O’Connor, Andrew. (2011) "Probability Distributions used in Reliability Engineering ". University of Maryland 2009.
Author: MSc. Osberto Díaz
Dinos qué te ha parecido el artículo
Artículos recomendados
Técnicas de mantenimiento predictivo

9.2 Mantenimiento Predictivo y Monitoreo según condición

¿Es el Mantenimiento Centrado en Confiabilidad una tarea fácil?

Hablemos de Mantenimiento Productivo Total

Publica tu artículo en la revista #1 de Mantenimiento Industrial
Publicar un artículo en la revista es gratis, no tiene costo.
Solo debes asegurarte que no sea un artículo comercial.
¿Qué esperas?
O envía tu artículo directo: articulos@predictiva21.com
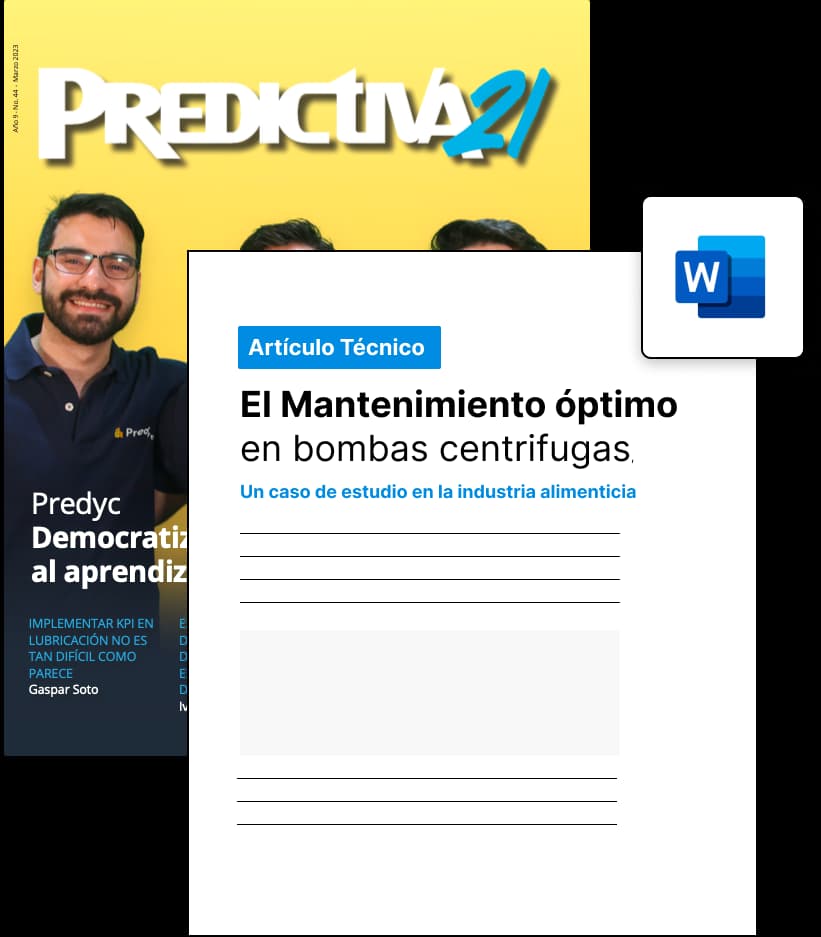
Practical Application of the Bayes Theorem for the Estimation of Availability in Industrial Assets
Articulo 18 de marzo de 2020During the development of any engineering study on reliability, one of the key activities for them to be performed effectively is the estimation of the failure and repair rate of an asset, which are meant to model statistically the availability of an asset through mathematical functions known as probability distributions, with the study of operation times and out-of-service times (see Fig. 1).


Whereas for repairable systems:
- Average Time of Operation = Mean Time Between Failures (MTBF)
- Average Time out of service = Mean Time to Repair (MTTR)
In this sense, an incorrect estimation of these values would negatively affect the results obtained in the studies performed, since we would be estimating based on an unreal behavior of the asset.
It’s important to emphasize that the failure and repair rates can be estimated through sources of different nature, be it generic or specific, that is, we can calculate them using the register of failures and repair of the asset itself or using the generic databases such as OREDA, IEE 497, PARLOC, EXIDA, among others, and even using the opinion of experts in an adequate way, trying to eliminate subjectivity, it’s an excellent source of information.
In this vein, Yañez and others, 2007, proposes the use of Bayes theorem to estimate failure rates and repair equipment. The author notes that this Theorem, "allows the combination of structured and mathematically supported form of the experience of others (prior knowledge) with experience (evidence), thereby obtaining more representative combination rates flaws operational reality the process under analysis (improved or updated knowledge)."
In this article we intend to show in a practical way and structured application of Bayes' theorem in the estimation of the availability of two turbo-generators and power generation system via Monte Carlo simulation.
Then, the estimation procedure thereof is shown.
Revision of the failure data
First, a revision of the failure data associated to the turbo generators was performed. In it, there was evidence that the record doesn’t separate the failures associated to the turbine from those of the generator, as required by the ISO 14224:2006 standards. This leads to the analysis of the turbo generation as a whole.
Hence, a summary of the operation times and out of service time from each turbo generator unit is shown. We should remark that each of the times was altered with the purpose of keeping their confidentiality.


Actualization of failure rate (Theorem of Bayes)
Next, based on the previous data and with the purpose of improving the times between the failure and the times of repair, the Theorem of Bayes was applied to reliability studies, proposed by Yañez (2007). Since, as mentioned before, it allows obtaining failure rates more adjusted to the operational reality of the asset, by means of combining the experience of others (use of generic data) with your own experience (failure register). See Fig.2.

Regarding generic data, information supplied by the Offshore Reliability Data (OREDA, 2009) was used, which is a complete database containing reliability and maintenance data from exploration and production equipment in the oil and gas industry. From it, all the failure modes downloaded from the database were used, either for the turbine and the generator as well.

From the Failure Register, the following data is obtained for the Turbogenerator TG-100:

Such data are substituted in the Equation 2, from the model:

The following data were obtained:

Likewise, the improved failure rate from the TG-101 turbo generator was estimated, obtaining the following historical data:

Substituting such data in Equation 2, the following data were obtained:

Cursos recomendados






%252FImagen%252FRAMPREDYC-1730060420837.webp%3Falt%3Dmedia%26token%3D2634a7f0-988e-4022-b91f-382503e6e9db&w=3840&q=75)

Modeling block diagram
From the information of improved failure rates, the Reliability Block Diagrams (RBD) were obtained, with the purpose of representing the architecture and operational philosophy of the generation system.
Thus, the RAPTOR 7 tool from ARINC was used, which allows modeling complex systems considering the operational philosophy and the times of failure and repair. Here, the operational philosophy of the turbo generator units in regular operations conditions appears under the philosophy k of n, 1 of 2, that is, one operating turbo generator and the other as a backup, which only starts to function in case of a programmed stop or failure from the other turbo generator. Also, the TG-101 generator is installed to operate only in case of the TG-100 turbo generator is out of service.
Hence, the proposed block diagram:

It´s important to emphasize that, with the purpose of simulating the real operational conditions and maintenance of equipment, programmed stops were considered for maintenance every 1,000 hours of operation, with a minimum duration of 72 hours, a maximum of 192 hours and an average of 168 hours.
Montecarlo simulation to estimate availability
After that, a simulation of the reliability block diagram (RBD) was performed using the Montecarlo simulation, which allows reducing the uncertainty in this kind of analysis.
The simulation of results for 50 iterations in the following 10 years of operations is presented in Table 4:


Likewise, in Figure 5, the results shown RAM parameters for year 10.

Discussion of results
From the simulation of results, we conclude:
- The annual availability for the turbogeneration system for year 10 is 99.79%, with a minimum of 99.68% and a maximum of 99.89%.
- The stochastic profile shows that the availability values of the system are above the international standards, since throughout the time, the availability will remain above 99%.
- The mean time between failures of the system is 1638.30 with a standard deviation of 571.52.
- The mean time to repair of the system is 3.23 hours, with a minimum of 2.38 hours and a maximum of 4.66 hours.
- Regarding the number of failures for the next 10 years, there is a minimum of 25 failures, a maximum of 101 and an average of 59 failures.
It´s important to emphasize that the results obtained must be updated with the enrichment of the failure register and repair of assets, since the estimated rates would come closer to their operational reality.
References
-Yañez Medardo, y Otros. (2007) "Confiabilidad Integral, Un Enfoque Práctico", Tomo II, Metodologías. R2M.
-ISO 14224. Industrias de petróleo y gas natural - Recolección e intercambio de datos de confiabilidad y mantenimiento de equipos, 2006.
-Ebeling, Charles. (2009) "An Introduction to Reliability and Maintainability Engineering". Waveland.
-O’Connor, Andrew. (2011) "Probability Distributions used in Reliability Engineering ". University of Maryland 2009.
Author: MSc. Osberto Díaz
Dinos qué te ha parecido el artículo
Artículos recomendados
¿Qué es la gestión de riesgos empresariales?

La otra visión de la Confiabilidad Operacional

Entrevista a Annalisa Ferrari

Optimización de Inventarios de Partes y Repuestos para el Mantenimiento (II Parte)

Publica tu artículo en la revista #1 de Mantenimiento Industrial
Publicar un artículo en la revista es gratis, no tiene costo.
Solo debes asegurarte que no sea un artículo comercial.
¿Qué esperas?
O envía tu artículo directo: articulos@predictiva21.com
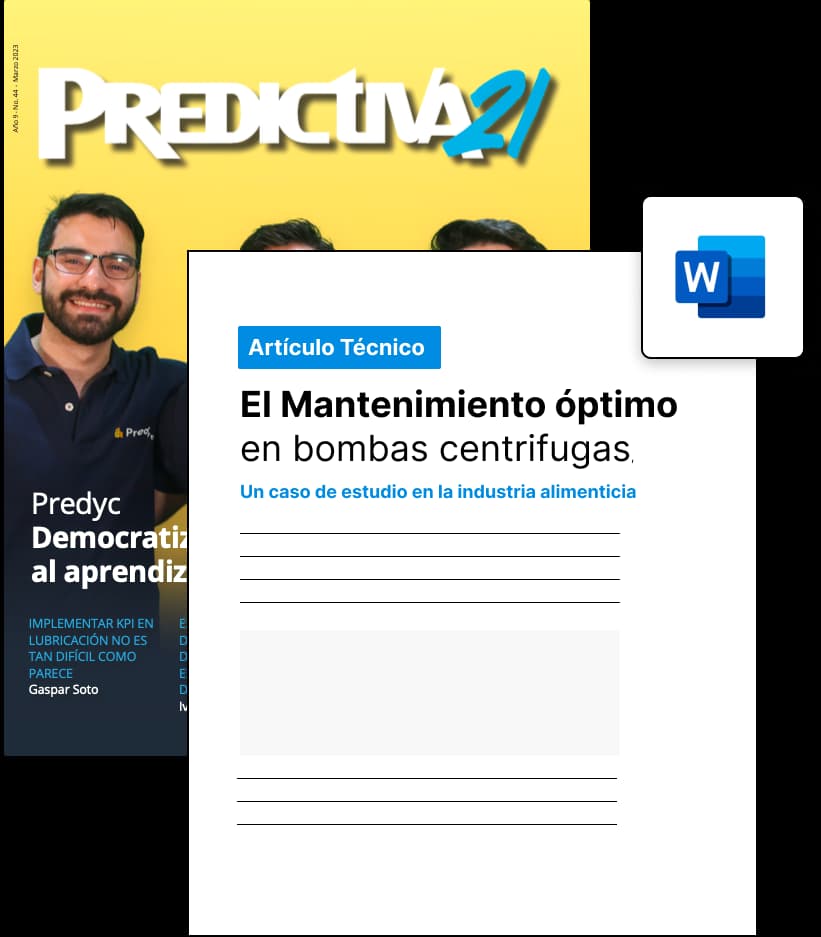