La Gerencia del Combustible como Elemento Clave en Centrales Térmicas a Vapor
Articulo29 de abril de 2020
En todas las Centrales Térmicas a Vapor (ver fig.1), se transforma la energía química de un combustible (gas natural, fuel número 6, fuel número 2, y carbón entre otros) en energía eléctrica, es decir se transforman los Btu del combustible, en kWh. Asociados a estos procesos de conversión, están las perdidas, que no son más que la energía que no se aprovecha, estas pérdidas pueden ser propias, producto de las ineficiencias por diseño de los equipos o consecuencias de la forma como se operen las unidades. En Las Centrales Térmicas a Vapor, para medir la relación entre la energía introducida y la energía aprovechada, se usa una variable denominada Eficiencia de la Planta. Esta Eficiencia también puede ser expresada a través de otra variable denominada Heat Rate, variable que nos indica cuanta cantidad de combustible en términos de energía se necesita para generar un kWh a un determinado poder calorífico.

Los altos costos de los combustibles a nivel mundial y la aparición de los mercados desregulados en muchos países, han llevado a las Empresas de Generación de Energía Eléctrica con Plantas Térmicas a Vapor, a Gerenciar sus costos por concepto de combustible y esto se debe principalmente a que uno de los factores que más afecta el costo de producción ($/kWh) lo constituye el precio del combustible. Como puede verse en la fig. 2 en algunas Plantas este costo puede llegar a representar hasta un 85% del costo total de producción.

Este trabajo se concentra en el proyecto la Gerencia del Combustible y en el mismo se presenta una lista de verificación que incluye los siguientes puntos:
- Identificar las variables que afectan el Heat Rate de las unidades de generación.
- Determinar la Capacidad Técnica del Personal de operadores y mantenedores en los procesos de las unidades de generación.
- Conocer el estado de equipos instalados para la medición del Heat Rate.
- Contar con las pruebas de Eficiencia y de Heat Balance de diseño de las unidades de generación.
La Experiencia a nivel de las principales Centrales Térmicas de Generación de Energía Eléctrica nos conduce a que los principales factores que afectan el Heat Rate de sus unidades son:
- Factor de Capacidad de la Planta.
- Exceso de Oxígeno en la Caldera (alto o bajo).
- Temperatura y Presión del Vapor Principal y Recalentado.
- Presión de escape del Condensador.
- Precalentadores de Agua de Alimentación.
- Pureza de Hidrógeno en el Generador.
- Resistencias Térmicas en Superficies de Transferencias de Calor.
- Estado de la Instrumentación.
- Fugas de Agua y Vapor.
- Calibración de los elementos de medición de combustible.
- Habilidades y Conocimientos del personal de la Planta.
Monitoreo en tiempo real del Heat Rate
La centralización en computadoras de las señales de la energía generada de cada unidad, así como también del flujo de combustible y el poder calórico (solo gas natural) permiten mediante un algoritmo matemático, Ec. 1 calcular y mostrar en tiempo real el Heat Rate de cada unidad. Esta información les permite a los operadores de unidad realizar los ajustes y operaciones necesarias a fin de optimizar el consumo de combustible y de esta manera reducir las pérdidas. Otra bondad que ofrece este sistema, es la de facilitar la realización de un despacho económico de carga con las diferentes unidades de generación en línea, ya que al conocer en tiempo real las eficiencias de las máquinas los operadores pueden efectuar variaciones en la carga de las unidades para obtener el mejor valor de eficiencia del conjunto, y de esta manera se puede suplir la demanda de energía eficientemente. En la Fig. 3 se muestra un diagrama esquemático del sistema.
Heat Rate (Btu/kWh) = V*HHV/EG (1)
Donde el Heat Rate es la relación entre la energía de entrada y la energía de salida.
V. = Volumen o masa de Combustible (Ft3 o Lbm).
HHV. = Poder Calorífico Alto. (Btu/ Ft3 o Btu/ Lbm).
EG. = Energía Generada (kWh) = Pi * FC*.
Pi. = Potencia Instalada de la Unidad KW.
FC = Factor de Capacidad de la Unidad %.
HP = Número de horas del período considerado.

Porcentaje de variación de los valores de heat rate por variable operativa
En pruebas realizadas en Centrales Térmicas a vapor durante su operación se ha podido observar mediante la medición del heat rate en tiempo real como se afecta la eficiencia de una maquina al operarla fuera de sus parámetros operativos de diseño. En la fig. 4 se presenta la data obtenida.

Desviaciones en la medición del combustible
En todas las Centrales Energéticas, los responsables de para la recepción del combustible llegan un control estricto de lo facturado y lo recibido ya que cualquier variación será cargada a las unidades bien sea por mejora en la eficiencia o por disminución de la misma. En las plantas que queman gas natural se instalan estaciones de medición espejo, es decir equipos de medición de iguales características a la del suplidor de gas con la finalidad de poder llevar un mejor control de lo facturado por el suplidor. Algunas plantas solo permiten variaciones hasta un 2%. Para el cálculo del volumen suministrado, se utiliza la metodología de corregir el volumen por el factor resultante de dividir el poder calorífico promedio del gas suministrado por el poder calorífico del gas contractual. de En el caso de las plantas que queman fuel oil, el control se hace cuando termina el proceso de bombeo hacia los tanques de almacenamiento y es allí cuando se toman muestras para medir el poder calorífico, temperatura del combustible, grados api y volumen despachado y una vez comparado con las especificaciones del combustible contratado se procede a certificar dicho combustible.
Carga de la unidad
Como puede verse en la Fig. 5, el heat rate de las centrales térmicas a vapor típica, se ve afectado en cargas inferiores al 75 % y mayores a 85%. Es por ello que se hace necesario efectuar pruebas de Heat Balance y de Eficiencia a diferentes porcentajes de carga (50,75,85 y 100%) de cada unidad de generación y comparar los valores obtenidos con los valores de diseño. Con estas pruebas, se puede determinar el estado operativo de los diferentes equipos de las unidades de generación.
Con toda la data obtenida se pueden realizar las acciones correctivas pertinentes, con la finalidad de llevar las máquinas a su valor de diseño, mejorando así el consumo de combustible. Es recomendable que estas pruebas sean realizadas trimestralmente y una semana antes de cada parada para mantenimiento. Los reportes de las pruebas de heat balance y de eficiencia son utilizados como material de soporte para pruebas futuras.

Porcentaje exceso de oxigeno
Cuando hablamos del % de exceso de oxígeno, nos referimos a la cantidad de aire en exceso que debemos suministrar al generador de vapor para producir una combustión completa y de esta manera evitar botar combustible por la chimenea a través del CO. Hoy en día las unidades modernas y algunas unidades repotenciadas utilizan varios analizadores de oxígeno en los gases de salida hacia la chimenea y además medidores de opacidad. Esto permite de acuerdo a los valores especificados por el fabricante del generador de vapor hacer los ajustes correspondientes. Como podemos ver en las ecuaciones siguientes usando como combustible el metano, en todo proceso de combustión completa se genera dióxido de carbono más agua y en toda combustión incompleta se genera monóxido de carbono más agua.


Cursos recomendados




%252FImagen%252FRAMPREDYC-1730060420837.webp%3Falt%3Dmedia%26token%3D2634a7f0-988e-4022-b91f-382503e6e9db&w=3840&q=75)



Presión de escape del generador
Mejorando la presión de escape del condensador, se logra mejorar la eficiencia de la turbina y por ende la eficiencia del ciclo. En la fig. 6 se puede observar como un aumento de 20 mmHg en la presión de escape en el condensador de una máquina, puede causar un incremento del Heat Rate hasta de un 5 %, lo que es equivalente a un aumento del consumo de combustible en ese mismo orden.
El aumento en la presión de escape del condensador es evitado o corregido por medio de un plan de limpieza de los tubos, a través de maniobras operativas, y ajustes en el sistema de agua de refrigeración.

Precalentadores de agua de alimentación
Manteniendo en servicio continuo los precalentadores de agua de alimentación, asegurarse que sus drenajes no sean conducidos al condensador y que las válvulas controladoras de nivel funcionen bien, permite reducir el consumo de combustible. Teniendo en servicio estos precalentadores de una manera eficiente se logra que el agua de alimentación llegue más caliente al generador de vapor con lo cual reduce el consumo de combustible. Existen unidades que derratean la capacidad de la unidad hasta un 15 % de su potencia nominal cuando sacan fuera de servicio los precalentadores de alta presión. Esto se hace para proteger al generador de vapor. En la fig. 7 podemos ver un esquema típico de estos equipos y el balance energético.

Control de la pureza de hidrógeno
Mantener la pureza de hidrógeno para el enfriamiento en los generadores eléctricos por encima del 98%, reduce la pérdida de potencia como producto de la fricción dentro del generador por el aumento de densidad del gas. En la fig. 8 se puede observar que con una variación de un 5% en la pureza de hidrógeno por debajo de la pureza normal de operación en un generador eléctrico que opera con una presión de Hidrógeno de 60 lbf/in2 puede ocasionar una pérdida de potencia hasta de 1700 kW. Es por ello que se disponer de medidores de pureza en línea con alarmas que se activen cuando la presión llegue al valor seteado.

Conclusiones
• El monitoreo en tiempo real del Heat Rate, permite la inmediata corrección de cualquier anormalidad que pudiera afectar esta variable y proporciona un método adicional para mejorar la eficiencia de la Planta. La habilidad para corregir rápidamente una condición fuera de rango puede proveer una operación más eficiente de la unidad, con un mínimo de perdidas debido a la condición de ineficiencia observada. Adicionalmente este sistema hace posible el monitorear las condiciones de los parámetros de las unidades y tomar acciones correctivas rápidamente.
• Dentro de los elementos que afectan más la eficiencia de la unidad, se identificó la variable exceso de oxígeno como la más influyente; en pruebas de combustión realizadas en las diferentes calderas se pudo observar que el exceso de oxígeno puede ocasionar variaciones en el consumo de combustible hasta de un 10%.
• La optimización de los costos de producción de la energía generada, como producto de una mejora en el consumo de combustible, permite alcanzar precios competitivos dentro de mercados desregulados.
• Toda variable que pueda ser cuantificada, puede ser Gerenciada.
• El costo de un proyecto para la medición del Heat Rate en tiempo real incluyendo, computadoras, medidores de energía generada, calorímetro, medidores de flujos de combustibles e instalación, puede estar aproximadamente en unos 200.000 $.
• En la tabla número 1 se muestran los incrementos anualizados en dólares para una unidad de 400.000 KW, que tiene un Heat Rate de diseño de 9.800 Btu/kWh (poder calorífico alto) y que opera con un factor de capacidad de 75%. En esta tabla se puede observar que con una variación del Heat Rate del 1 % y con un costo de la energía de 1$/MM Btu el costo anual por concepto de combustible se incrementa en 257.544,00. Esto nos dice que un proyecto como este, tiene un retorno de la inversión en menos de un año.
La ecuación número 2 muestra como calcular el incremento de costo.
IC = EG x (HRa – HRd) x CE (2)
Donde IC es el Incremento del costo de combustible:
EG = Pi *CF*HP= Energía Generada (kWh).
CF = Factor de Capacidad (%).
HRa= Heat Rate Actual (Btu/kWh).
HRd= Heat Rate de Diseño (Btu/kWh).
CE = Costo de la Energía ($/MMBtu).
Pi = Potencia Instalada (kW).
HP = Número de horas del periodo considerado.

Referencias
- 1. Lou B. Mehl & Thomas R. White. Sargent & Laundy Chicago, Illinois. “Option to Reduce the Operating Costs at Fossil Power Stations.
- 2. Handbook for Thermal and Nuclear Power Engineering Society.
- 3. Experiencias del Autor.
Autor: Alberto Fuentes Ingeniero Mecánico
Universidad Central de Venezuela
32 años en el área de plantas térmicas de generación
Dinos qué te ha parecido el artículo
Artículos recomendados
Planificación de mantenimiento mecánico

Congreso PRECONLUB 2021 de Grupo TECHGNOSIS

17.3.- Control por Variación de Velocidad

El mantenimiento predictivo: usando herramientas modernas

Publica tu artículo en la revista #1 de Mantenimiento Industrial
Publicar un artículo en la revista es gratis, no tiene costo.
Solo debes asegurarte que no sea un artículo comercial.
¿Qué esperas?
O envía tu artículo directo: articulos@predictiva21.com
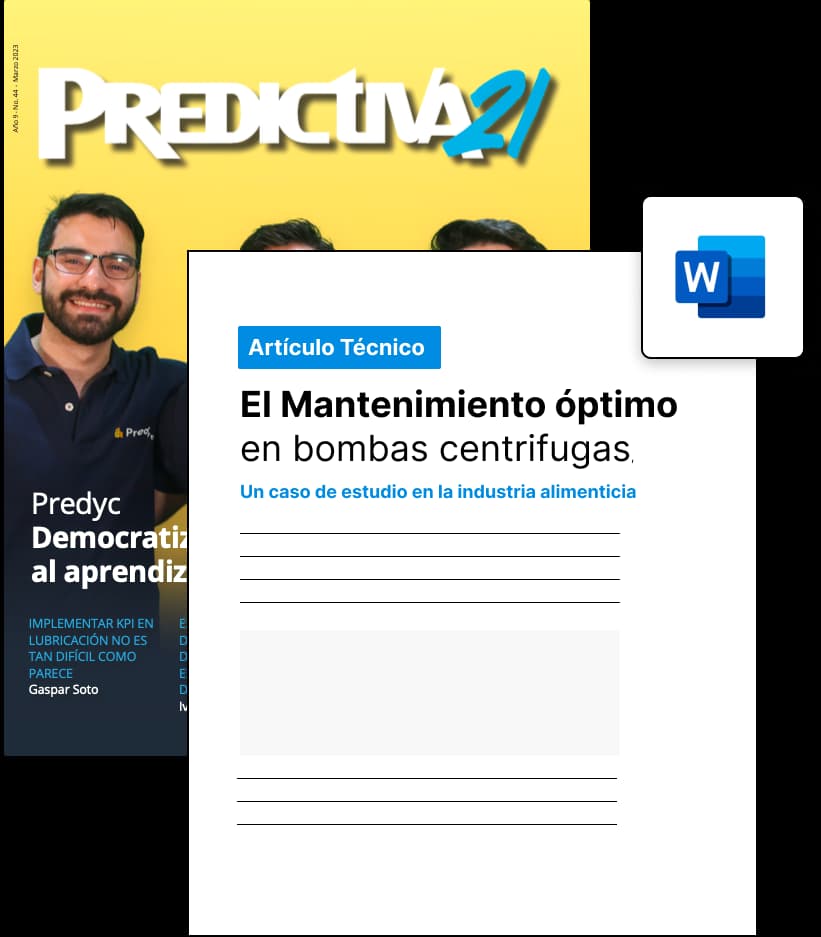
La Gerencia del Combustible como Elemento Clave en Centrales Térmicas a Vapor
Articulo 29 de abril de 2020En todas las Centrales Térmicas a Vapor (ver fig.1), se transforma la energía química de un combustible (gas natural, fuel número 6, fuel número 2, y carbón entre otros) en energía eléctrica, es decir se transforman los Btu del combustible, en kWh. Asociados a estos procesos de conversión, están las perdidas, que no son más que la energía que no se aprovecha, estas pérdidas pueden ser propias, producto de las ineficiencias por diseño de los equipos o consecuencias de la forma como se operen las unidades. En Las Centrales Térmicas a Vapor, para medir la relación entre la energía introducida y la energía aprovechada, se usa una variable denominada Eficiencia de la Planta. Esta Eficiencia también puede ser expresada a través de otra variable denominada Heat Rate, variable que nos indica cuanta cantidad de combustible en términos de energía se necesita para generar un kWh a un determinado poder calorífico.

Los altos costos de los combustibles a nivel mundial y la aparición de los mercados desregulados en muchos países, han llevado a las Empresas de Generación de Energía Eléctrica con Plantas Térmicas a Vapor, a Gerenciar sus costos por concepto de combustible y esto se debe principalmente a que uno de los factores que más afecta el costo de producción ($/kWh) lo constituye el precio del combustible. Como puede verse en la fig. 2 en algunas Plantas este costo puede llegar a representar hasta un 85% del costo total de producción.

Este trabajo se concentra en el proyecto la Gerencia del Combustible y en el mismo se presenta una lista de verificación que incluye los siguientes puntos:
- Identificar las variables que afectan el Heat Rate de las unidades de generación.
- Determinar la Capacidad Técnica del Personal de operadores y mantenedores en los procesos de las unidades de generación.
- Conocer el estado de equipos instalados para la medición del Heat Rate.
- Contar con las pruebas de Eficiencia y de Heat Balance de diseño de las unidades de generación.
La Experiencia a nivel de las principales Centrales Térmicas de Generación de Energía Eléctrica nos conduce a que los principales factores que afectan el Heat Rate de sus unidades son:
- Factor de Capacidad de la Planta.
- Exceso de Oxígeno en la Caldera (alto o bajo).
- Temperatura y Presión del Vapor Principal y Recalentado.
- Presión de escape del Condensador.
- Precalentadores de Agua de Alimentación.
- Pureza de Hidrógeno en el Generador.
- Resistencias Térmicas en Superficies de Transferencias de Calor.
- Estado de la Instrumentación.
- Fugas de Agua y Vapor.
- Calibración de los elementos de medición de combustible.
- Habilidades y Conocimientos del personal de la Planta.
Monitoreo en tiempo real del Heat Rate
La centralización en computadoras de las señales de la energía generada de cada unidad, así como también del flujo de combustible y el poder calórico (solo gas natural) permiten mediante un algoritmo matemático, Ec. 1 calcular y mostrar en tiempo real el Heat Rate de cada unidad. Esta información les permite a los operadores de unidad realizar los ajustes y operaciones necesarias a fin de optimizar el consumo de combustible y de esta manera reducir las pérdidas. Otra bondad que ofrece este sistema, es la de facilitar la realización de un despacho económico de carga con las diferentes unidades de generación en línea, ya que al conocer en tiempo real las eficiencias de las máquinas los operadores pueden efectuar variaciones en la carga de las unidades para obtener el mejor valor de eficiencia del conjunto, y de esta manera se puede suplir la demanda de energía eficientemente. En la Fig. 3 se muestra un diagrama esquemático del sistema.
Heat Rate (Btu/kWh) = V*HHV/EG (1)
Donde el Heat Rate es la relación entre la energía de entrada y la energía de salida.
V. = Volumen o masa de Combustible (Ft3 o Lbm).
HHV. = Poder Calorífico Alto. (Btu/ Ft3 o Btu/ Lbm).
EG. = Energía Generada (kWh) = Pi * FC*.
Pi. = Potencia Instalada de la Unidad KW.
FC = Factor de Capacidad de la Unidad %.
HP = Número de horas del período considerado.

Porcentaje de variación de los valores de heat rate por variable operativa
En pruebas realizadas en Centrales Térmicas a vapor durante su operación se ha podido observar mediante la medición del heat rate en tiempo real como se afecta la eficiencia de una maquina al operarla fuera de sus parámetros operativos de diseño. En la fig. 4 se presenta la data obtenida.

Desviaciones en la medición del combustible
En todas las Centrales Energéticas, los responsables de para la recepción del combustible llegan un control estricto de lo facturado y lo recibido ya que cualquier variación será cargada a las unidades bien sea por mejora en la eficiencia o por disminución de la misma. En las plantas que queman gas natural se instalan estaciones de medición espejo, es decir equipos de medición de iguales características a la del suplidor de gas con la finalidad de poder llevar un mejor control de lo facturado por el suplidor. Algunas plantas solo permiten variaciones hasta un 2%. Para el cálculo del volumen suministrado, se utiliza la metodología de corregir el volumen por el factor resultante de dividir el poder calorífico promedio del gas suministrado por el poder calorífico del gas contractual. de En el caso de las plantas que queman fuel oil, el control se hace cuando termina el proceso de bombeo hacia los tanques de almacenamiento y es allí cuando se toman muestras para medir el poder calorífico, temperatura del combustible, grados api y volumen despachado y una vez comparado con las especificaciones del combustible contratado se procede a certificar dicho combustible.
Carga de la unidad
Como puede verse en la Fig. 5, el heat rate de las centrales térmicas a vapor típica, se ve afectado en cargas inferiores al 75 % y mayores a 85%. Es por ello que se hace necesario efectuar pruebas de Heat Balance y de Eficiencia a diferentes porcentajes de carga (50,75,85 y 100%) de cada unidad de generación y comparar los valores obtenidos con los valores de diseño. Con estas pruebas, se puede determinar el estado operativo de los diferentes equipos de las unidades de generación.
Con toda la data obtenida se pueden realizar las acciones correctivas pertinentes, con la finalidad de llevar las máquinas a su valor de diseño, mejorando así el consumo de combustible. Es recomendable que estas pruebas sean realizadas trimestralmente y una semana antes de cada parada para mantenimiento. Los reportes de las pruebas de heat balance y de eficiencia son utilizados como material de soporte para pruebas futuras.

Porcentaje exceso de oxigeno
Cuando hablamos del % de exceso de oxígeno, nos referimos a la cantidad de aire en exceso que debemos suministrar al generador de vapor para producir una combustión completa y de esta manera evitar botar combustible por la chimenea a través del CO. Hoy en día las unidades modernas y algunas unidades repotenciadas utilizan varios analizadores de oxígeno en los gases de salida hacia la chimenea y además medidores de opacidad. Esto permite de acuerdo a los valores especificados por el fabricante del generador de vapor hacer los ajustes correspondientes. Como podemos ver en las ecuaciones siguientes usando como combustible el metano, en todo proceso de combustión completa se genera dióxido de carbono más agua y en toda combustión incompleta se genera monóxido de carbono más agua.


Cursos recomendados




%252FImagen%252FRAMPREDYC-1730060420837.webp%3Falt%3Dmedia%26token%3D2634a7f0-988e-4022-b91f-382503e6e9db&w=3840&q=75)



Presión de escape del generador
Mejorando la presión de escape del condensador, se logra mejorar la eficiencia de la turbina y por ende la eficiencia del ciclo. En la fig. 6 se puede observar como un aumento de 20 mmHg en la presión de escape en el condensador de una máquina, puede causar un incremento del Heat Rate hasta de un 5 %, lo que es equivalente a un aumento del consumo de combustible en ese mismo orden.
El aumento en la presión de escape del condensador es evitado o corregido por medio de un plan de limpieza de los tubos, a través de maniobras operativas, y ajustes en el sistema de agua de refrigeración.

Precalentadores de agua de alimentación
Manteniendo en servicio continuo los precalentadores de agua de alimentación, asegurarse que sus drenajes no sean conducidos al condensador y que las válvulas controladoras de nivel funcionen bien, permite reducir el consumo de combustible. Teniendo en servicio estos precalentadores de una manera eficiente se logra que el agua de alimentación llegue más caliente al generador de vapor con lo cual reduce el consumo de combustible. Existen unidades que derratean la capacidad de la unidad hasta un 15 % de su potencia nominal cuando sacan fuera de servicio los precalentadores de alta presión. Esto se hace para proteger al generador de vapor. En la fig. 7 podemos ver un esquema típico de estos equipos y el balance energético.

Control de la pureza de hidrógeno
Mantener la pureza de hidrógeno para el enfriamiento en los generadores eléctricos por encima del 98%, reduce la pérdida de potencia como producto de la fricción dentro del generador por el aumento de densidad del gas. En la fig. 8 se puede observar que con una variación de un 5% en la pureza de hidrógeno por debajo de la pureza normal de operación en un generador eléctrico que opera con una presión de Hidrógeno de 60 lbf/in2 puede ocasionar una pérdida de potencia hasta de 1700 kW. Es por ello que se disponer de medidores de pureza en línea con alarmas que se activen cuando la presión llegue al valor seteado.

Conclusiones
• El monitoreo en tiempo real del Heat Rate, permite la inmediata corrección de cualquier anormalidad que pudiera afectar esta variable y proporciona un método adicional para mejorar la eficiencia de la Planta. La habilidad para corregir rápidamente una condición fuera de rango puede proveer una operación más eficiente de la unidad, con un mínimo de perdidas debido a la condición de ineficiencia observada. Adicionalmente este sistema hace posible el monitorear las condiciones de los parámetros de las unidades y tomar acciones correctivas rápidamente.
• Dentro de los elementos que afectan más la eficiencia de la unidad, se identificó la variable exceso de oxígeno como la más influyente; en pruebas de combustión realizadas en las diferentes calderas se pudo observar que el exceso de oxígeno puede ocasionar variaciones en el consumo de combustible hasta de un 10%.
• La optimización de los costos de producción de la energía generada, como producto de una mejora en el consumo de combustible, permite alcanzar precios competitivos dentro de mercados desregulados.
• Toda variable que pueda ser cuantificada, puede ser Gerenciada.
• El costo de un proyecto para la medición del Heat Rate en tiempo real incluyendo, computadoras, medidores de energía generada, calorímetro, medidores de flujos de combustibles e instalación, puede estar aproximadamente en unos 200.000 $.
• En la tabla número 1 se muestran los incrementos anualizados en dólares para una unidad de 400.000 KW, que tiene un Heat Rate de diseño de 9.800 Btu/kWh (poder calorífico alto) y que opera con un factor de capacidad de 75%. En esta tabla se puede observar que con una variación del Heat Rate del 1 % y con un costo de la energía de 1$/MM Btu el costo anual por concepto de combustible se incrementa en 257.544,00. Esto nos dice que un proyecto como este, tiene un retorno de la inversión en menos de un año.
La ecuación número 2 muestra como calcular el incremento de costo.
IC = EG x (HRa – HRd) x CE (2)
Donde IC es el Incremento del costo de combustible:
EG = Pi *CF*HP= Energía Generada (kWh).
CF = Factor de Capacidad (%).
HRa= Heat Rate Actual (Btu/kWh).
HRd= Heat Rate de Diseño (Btu/kWh).
CE = Costo de la Energía ($/MMBtu).
Pi = Potencia Instalada (kW).
HP = Número de horas del periodo considerado.

Referencias
- 1. Lou B. Mehl & Thomas R. White. Sargent & Laundy Chicago, Illinois. “Option to Reduce the Operating Costs at Fossil Power Stations.
- 2. Handbook for Thermal and Nuclear Power Engineering Society.
- 3. Experiencias del Autor.
Autor: Alberto Fuentes Ingeniero Mecánico
Universidad Central de Venezuela
32 años en el área de plantas térmicas de generación
Dinos qué te ha parecido el artículo
Artículos recomendados
Tribología Centrada en Confiabilidad

La satanización del Mantenimiento Correctivo

El mantenimiento predictivo: usando herramientas modernas

El modelo de gestión CBM y el estándar iso-17359

Publica tu artículo en la revista #1 de Mantenimiento Industrial
Publicar un artículo en la revista es gratis, no tiene costo.
Solo debes asegurarte que no sea un artículo comercial.
¿Qué esperas?
O envía tu artículo directo: articulos@predictiva21.com
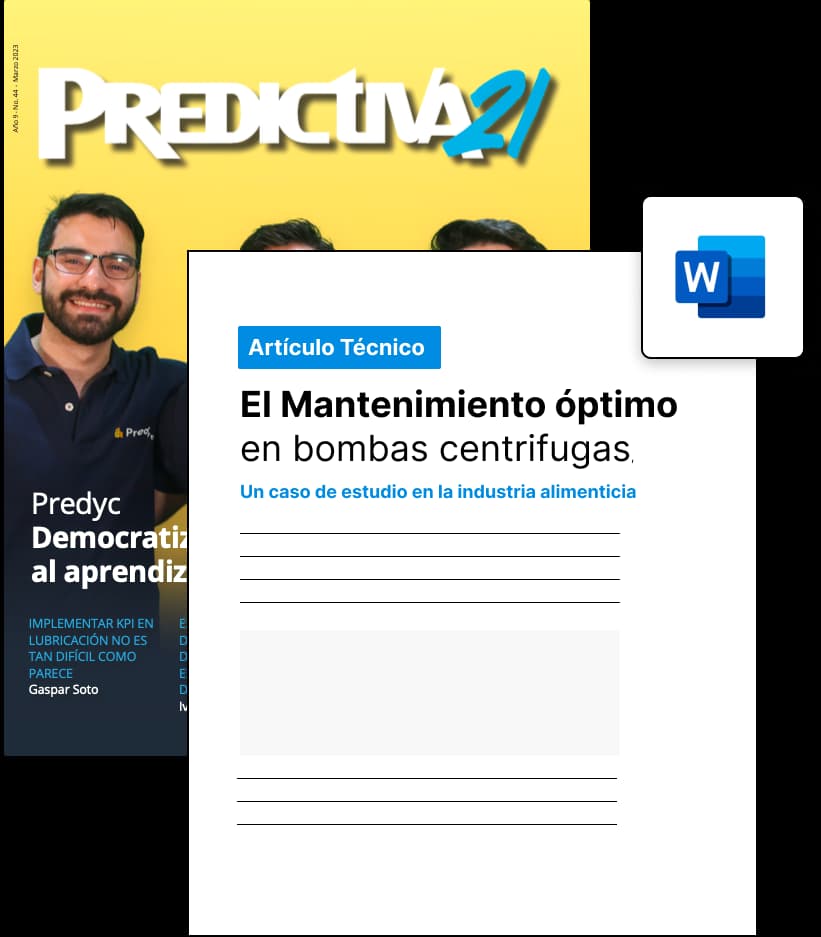