La importancia de los procedimientos en Mantenimiento
Articulo6 de noviembre de 2019
Estadísticamente se ha demostrado que un gran porcentaje de accidentes ocurren principalmente por la inobservancia de los procedimientos, falta de ellos, mala elaboración o interpretación. Muchas veces se diseñan procedimientos y la gente no los sigue. Esto se debe a cualesquiera de las siguientes razones: flojera, dificultad para entenderlos, falta de claridad, apuro, falta de interés, falta de supervisión, falta de concentración, por decir los mas comunes. Ejemplos los podemos ver cuando las personas compran un celular, muy pocas personas leen completamente el manual, porque es mas fácil preguntarle al vecino cuando hay dudas de cómo se hace una operación. Igualmente ocurre cuando adquirimos un vehículo, al principio leemos el manual, pero después ni pendiente de él.
Lo mismo se presenta cuando tomamos un avión y la aeromoza comienza con las indicaciones del uso del salvavidas y máscaras de emergencia, muy poca gente muestra interés, y si lo hace es porque existe alguna atracción por quien da las explicaciones, caso contrario, giramos la cabeza para buscar alguna revista. A la gente muchas veces le fastidia seguir procedimientos. Sarcásticamente, podemos hacer la siguiente pregunta ¿cuántas personas han leído las instrucciones de uso de un preservativo? Así podemos encontrar cualquier cantidad de ejemplos a diario; pero para el tema que nos ocupa, la manera de ver los procedimientos y su importancia también están presente al momento de realizar un trabajo de mantenimiento. Estas razones tampoco escapan a los trabajadores y que muchas veces su omisión puede ocasionar una falla o accidentes con consecuencias posiblemente irreversibles.
Cuando escribamos un procedimiento de mantenimiento, éste tiene que ser: sencillo, claro, preciso y conciso. De tal forma que no deje lugar a ambigüedades, ninguna duda y malas interpretaciones. Hay que leerlo una y otra vez, someterlo a prueba e ir corrigiéndolo hasta perfeccionarlo, como dicen los japonés POKAS-YOKE, a prueba de errores. Es mucho el tiempo que se ahorra una persona cuando existen procedimientos con estas características e indicaciones de lo que hay qué hacer y cómo hacerlo, con quién hacerlo; Con que seguridad pero sobre todo, con ellos, disminuiremos las probabilidades de accidentes que se puedan presentar, si somos responsables con su cumplimiento, y no menos importante, también son de gran ayuda para la disminución de los tiempos para intervenir el equipamiento o como decimos “TIME TO REPAIR”. Estos procedimientos debemos elaborarlos tanto para los mantenimientos correctivos como preventivo de los equipos, para estos últimos, se convierte en una herramienta poderosa al momento que estamos programando y ejecutando estos trabajos. Fíjense que me refiero al procedimiento de intervención no a los procedimientos del flujo de mantenimiento que también son muy importantes. Ahora bien, si sabemos que son intervenciones siempre repetitivas, haciendo siempre lo mismo, no debería haber ninguna desviación del tiempo, a menos que surja un imprevisto que nunca falta durante un trabajo. Imagínense, cuanta ayuda tendríamos al momento de ejecutar una Parada de Planta si tenemos procedimientos elaborados, codificados y probados. Las estimaciones de Tiempo mas Temprano para Terminar y Tiempo mas Tarde para Terminar serían mucho mas cercanos.
Para poner un ejemplo muy sencillo, observe qué significa la siguiente expresión: “BAJE EL BREAKER”. ¿Nos está diciendo que lo quite o que lo remueva? Ahora fíjense la misma instrucción “COLOQUE LA PALANCA EN LA POSICIÓN (OFF) o (0)”. Aquí no está diciendo que desergenicemos el circuito o el tablero. Recordemos que la descripción es OFF/ON para un breaker americanos y 0/1 para uno europeo. Como pueden observar la segunda expresión es mas completa. Veamos el siguiente ejemplo: “SAQUE LOS CONTACTOS Y LIMPIELOS” Les pregunto cómo los sacos y no menos importantes como los soplos. Esta instrucción no es precisa ni concreta. Como pueden ver podemos pasar mucho tiempo consiguiendo ejemplos de procedimientos mal elaborados, incompletos y sin precisión. Por tal razón la redacción y ortografía también se convierten en otro gran ingrediente al momento de escribir procedimientos de ejecución de trabajos de mantenimiento.
Autor: Brau Clemenza
Dinos qué te ha parecido el artículo
Artículos recomendados
People

El Sistema WMS: descubre su aporte a las empresas

Confiabilidad Humana y el Humano Confiable Parte II

Alexis Lárez: Manager de Mantenimiento AEM 2020 - Rumbo al European Maintenance Manager Award EMMA 2021

Publica tu artículo en la revista #1 de Mantenimiento Industrial
Publicar un artículo en la revista es gratis, no tiene costo.
Solo debes asegurarte que no sea un artículo comercial.
¿Qué esperas?
O envía tu artículo directo: articulos@predictiva21.com
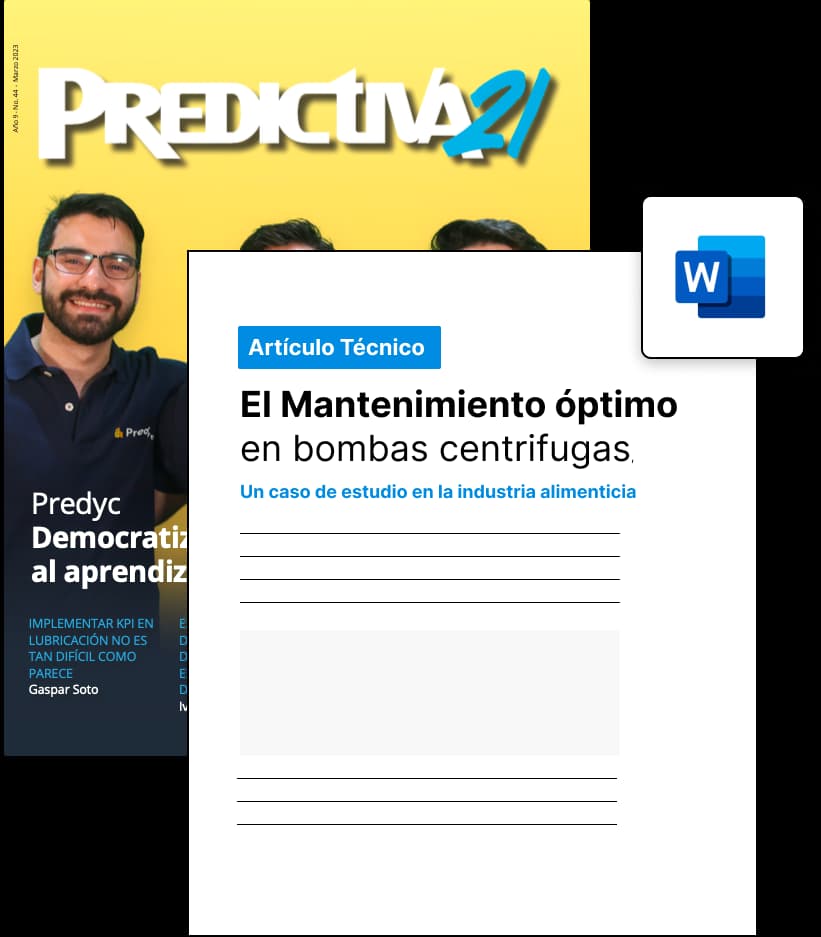
La importancia de los procedimientos en Mantenimiento
Articulo 6 de noviembre de 2019Estadísticamente se ha demostrado que un gran porcentaje de accidentes ocurren principalmente por la inobservancia de los procedimientos, falta de ellos, mala elaboración o interpretación. Muchas veces se diseñan procedimientos y la gente no los sigue. Esto se debe a cualesquiera de las siguientes razones: flojera, dificultad para entenderlos, falta de claridad, apuro, falta de interés, falta de supervisión, falta de concentración, por decir los mas comunes. Ejemplos los podemos ver cuando las personas compran un celular, muy pocas personas leen completamente el manual, porque es mas fácil preguntarle al vecino cuando hay dudas de cómo se hace una operación. Igualmente ocurre cuando adquirimos un vehículo, al principio leemos el manual, pero después ni pendiente de él.
Lo mismo se presenta cuando tomamos un avión y la aeromoza comienza con las indicaciones del uso del salvavidas y máscaras de emergencia, muy poca gente muestra interés, y si lo hace es porque existe alguna atracción por quien da las explicaciones, caso contrario, giramos la cabeza para buscar alguna revista. A la gente muchas veces le fastidia seguir procedimientos. Sarcásticamente, podemos hacer la siguiente pregunta ¿cuántas personas han leído las instrucciones de uso de un preservativo? Así podemos encontrar cualquier cantidad de ejemplos a diario; pero para el tema que nos ocupa, la manera de ver los procedimientos y su importancia también están presente al momento de realizar un trabajo de mantenimiento. Estas razones tampoco escapan a los trabajadores y que muchas veces su omisión puede ocasionar una falla o accidentes con consecuencias posiblemente irreversibles.
Cuando escribamos un procedimiento de mantenimiento, éste tiene que ser: sencillo, claro, preciso y conciso. De tal forma que no deje lugar a ambigüedades, ninguna duda y malas interpretaciones. Hay que leerlo una y otra vez, someterlo a prueba e ir corrigiéndolo hasta perfeccionarlo, como dicen los japonés POKAS-YOKE, a prueba de errores. Es mucho el tiempo que se ahorra una persona cuando existen procedimientos con estas características e indicaciones de lo que hay qué hacer y cómo hacerlo, con quién hacerlo; Con que seguridad pero sobre todo, con ellos, disminuiremos las probabilidades de accidentes que se puedan presentar, si somos responsables con su cumplimiento, y no menos importante, también son de gran ayuda para la disminución de los tiempos para intervenir el equipamiento o como decimos “TIME TO REPAIR”. Estos procedimientos debemos elaborarlos tanto para los mantenimientos correctivos como preventivo de los equipos, para estos últimos, se convierte en una herramienta poderosa al momento que estamos programando y ejecutando estos trabajos. Fíjense que me refiero al procedimiento de intervención no a los procedimientos del flujo de mantenimiento que también son muy importantes. Ahora bien, si sabemos que son intervenciones siempre repetitivas, haciendo siempre lo mismo, no debería haber ninguna desviación del tiempo, a menos que surja un imprevisto que nunca falta durante un trabajo. Imagínense, cuanta ayuda tendríamos al momento de ejecutar una Parada de Planta si tenemos procedimientos elaborados, codificados y probados. Las estimaciones de Tiempo mas Temprano para Terminar y Tiempo mas Tarde para Terminar serían mucho mas cercanos.
Para poner un ejemplo muy sencillo, observe qué significa la siguiente expresión: “BAJE EL BREAKER”. ¿Nos está diciendo que lo quite o que lo remueva? Ahora fíjense la misma instrucción “COLOQUE LA PALANCA EN LA POSICIÓN (OFF) o (0)”. Aquí no está diciendo que desergenicemos el circuito o el tablero. Recordemos que la descripción es OFF/ON para un breaker americanos y 0/1 para uno europeo. Como pueden observar la segunda expresión es mas completa. Veamos el siguiente ejemplo: “SAQUE LOS CONTACTOS Y LIMPIELOS” Les pregunto cómo los sacos y no menos importantes como los soplos. Esta instrucción no es precisa ni concreta. Como pueden ver podemos pasar mucho tiempo consiguiendo ejemplos de procedimientos mal elaborados, incompletos y sin precisión. Por tal razón la redacción y ortografía también se convierten en otro gran ingrediente al momento de escribir procedimientos de ejecución de trabajos de mantenimiento.
Autor: Brau Clemenza
Dinos qué te ha parecido el artículo
Artículos recomendados
Lubricación efectiva

Análisis de modo y efectos de falla (AMEF) en compresores reciprocantes

Repercusión de la Diabetes Mellitus en la Confiabilidad Humana

Curso Gestión de Mantenimiento Industrial

Publica tu artículo en la revista #1 de Mantenimiento Industrial
Publicar un artículo en la revista es gratis, no tiene costo.
Solo debes asegurarte que no sea un artículo comercial.
¿Qué esperas?
O envía tu artículo directo: articulos@predictiva21.com
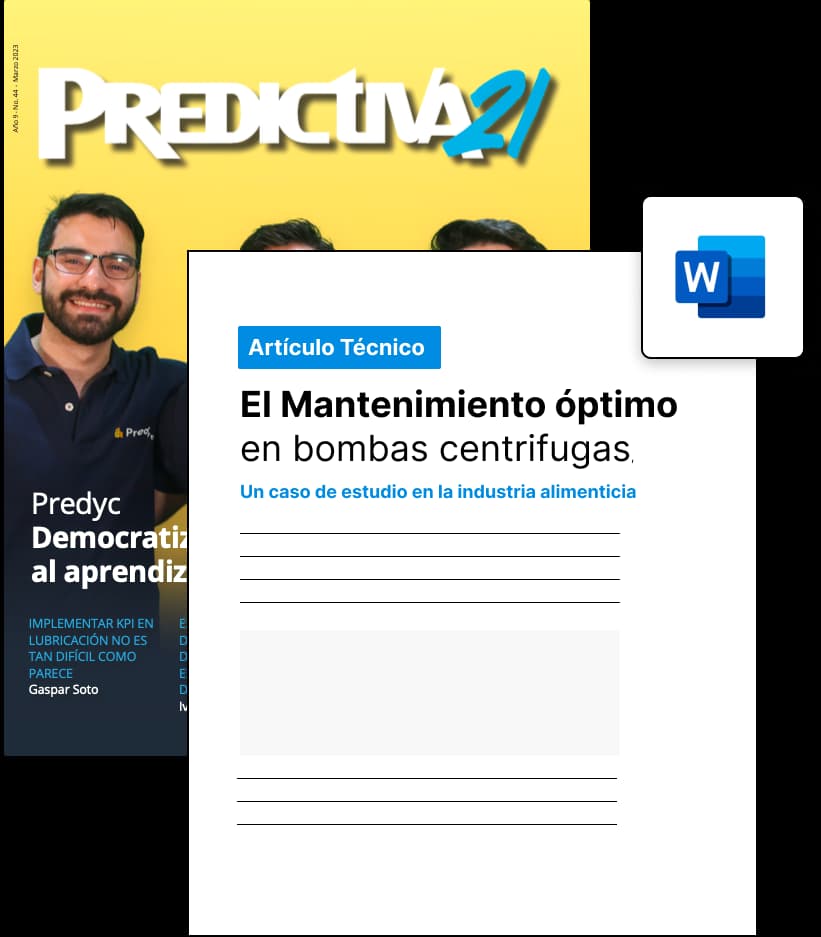