Inspección vídeo endoscopica: Estrategia útil del monitoreo basado en condición
Articulo18 de abril de 2019
En alguna oportunidad cuando hemos visitado al médico, este nos ha recomendado efectuar una vídeo endoscopia por presentar algunos síntomas como dolores estomacales, o solo para verificar algún daño asociado a las vías digestivas. Igualmente ocurre con las maquinas. Por ejemplo: en las turbinas industriales o areoderivativas cuando presentan alta temperatura de gases de escapes, baja presión de descarga del compresor axial, aumento en los niveles de vibración o en algunas ocasiones por fallas en modelos similares a determinadas horas de operación; se planifica una video endoscopia destinada a verificar las condiciones de sus componentes internos y de allí anticiparse a fallas mayores que conduzcan a incrementar los costos de operación y mantenimiento de la instalación.
Objetivo de la Video Endoscopia
Anteriormente, para determinas las condiciones físicas (grietas superficiales, defectos de soldadura, corrosión, desgaste, fatiga etc.) de los componentes internos de una turbina a gas o vapor, había que realizar desmontajes de algunos de estos componentes como la parte superior de la carcasa de los compresores axiales o la cámara de combustión de las turbinas, lo que conllevaban a demasiadas horas fuera de servicios de estos equipos, impactando la productividad de la instalación. Ya por los años 80’s comenzó a implementarse esta técnica con la aparición del boroscopio (flexible) y baroscopio (rígido), lo que permitía reducir los tiempos de paradas de la máquina. Aunque algunas turbinas no contaban con los puertos de inspección para tal fin, solo con retirar algunas partes como las bujías de la cámara de combustión, cesto de combustión o parte del múltiple de gas combustible era posible observar las partes más críticas y adicionalmente llevar registro de lo detectado, ya que estos equipos se podían conectar a una cámara fotográfica o cámara de video.
En el mercado actualmente existe una gama de equipos de video endoscopia, desde los más sofisticados y costosos hasta los más simples; sin embargo, la base de estos consisten en transmitir una luz blanca de gran intensidad proveniente de una fuente de luz (fuente de poder) y conectada a través de cable de fibra flexible a un broscopio (dispositivo flexible) o a un boroscopio (dispositivo rígido) de acuerdo al acceso a la parte inspeccionada, que para el caso de la turbinas, ya los fabricantes los tienen establecidos de acuerdo a su diseño y/o modelo.

(Fuente: Videoscopio IV86, marca Olympus)
Uno de los puntos de interés de esta estrategia del MBC es poder cuantificar la magnitud de la falla (por ejemplo, longitud y profundidad de una grieta de un álabe de una turbina) y llevar registro que permita ajustar la frecuencia de inspección para monitorear el deterioro progresivo de la Falla Potencial (P) e intervenir el equipo antes de presentarse la ocurrencia de una Falla Funcional (F) de consecuencias de alto impacto en la producción y costos de mantenimiento.

Aunque la vídeo Endoscopia no es una técnica predictiva de monitoreo de condición en línea, al igual que el resto de las técnicas cuantitativas contribuyen a evitar Falla funcionales (F) del equipo que en general reducen los costos de mantenimiento y operación mediante el ajuste del intervalo de inspección P-F.

Aplicaciones
El uso más común del video endoscopio es para la detección de grietas, desgates y fatigas en los álabes de turbinas; sin embargo, este es útil para inspeccionar recipientes a presión, intercambiadores de calor, cilindros de potencias de motores de combustión, tuberías de succión y descarga de compresores centrífugos, etc. donde igualmente los modos de fallas observados son grietas en superficies, desgastes, defectos de soldaduras y corrosión.
En cuanto a las inspecciones video endoscópicas a turbinas (industrial o aeroderivativa), en términos generales las partes inspeccionadas son: Compresor axial, cámara de combustión, turbina de alta presión (Turbina del Compresor) y turbina de baja presión (Turbina de Potencia). En cada uno de estos componentes habrá puertos específicos de inspección dependiendo de los fabricantes. Veamos un ejemplo práctico para una inspección de una turbina industrial GE modelo MS5001 de un turbo generador de 20 MW con 42704 horas de operación y 260 arranques desde su última reparación mayor.
Compresor axial
En este modelo de turbina para visualizar los álabes de 1era y 2da etapa (rotor / estator) y los inlet guide vanes (IGVs), hay que hacerlo a través del ducto de succión. Las siguientes figuras muestran un álabe de 1era etapa (rotor) con pérdida de material producto de algún impacto con un objeto desconocido y algunos inlet guide vanes (IGV`s) con presencia de sucio adherido en las paredes.

(Fuente: EYM solutions, Maturín)

(Fuente: EYM solutions, Maturín)
Cámara de Combustión
Dado que es el componente de la turbina donde se generan las altas temperaturas, atención especial a cada una de las partes que la conforman: cestos combustores, boquillas de gas combustibles, tubos cruza llamas, piezas de transición, etc.
En la turbina inspeccionada (GE MS5001) para revisar las partes calientes hay que retirar las boquillas de gas combustibles para introducir el boroscopio, en este caso se retiraron las correspondientes a los puntos 0, 90, 180 y 270º. En las siguientes figuras se muestran los detalles más críticos como son: Tubo cruza llama y piezas de transición con color rojizo característico de altas temperaturas.

(Fuente: EYM Solutions, Maturin)

(Fuente: EYM Solutions, Maturín)
Cursos recomendados






%252FImagen%252FRAMPREDYC-1730060420837.webp%3Falt%3Dmedia%26token%3D2634a7f0-988e-4022-b91f-382503e6e9db&w=3840&q=75)

Turbina de Alta Presión (Turbina del Compresor)
Para inspeccionar los álabes de 1era etapa (estator/rotor) en este modelo de turbina, se efectúa a través de los cestos combustores, es decir, llegar con el boroscopio por medio de la cámara de combustión, donde se pueden visualizar primeramente los alabes estacionarios correspondientes a cada sección del cesto combustor y luego girando el compresor axial lentamente (por medio del arrancador) se podrán inspeccionar los álabes rotativos de la misma. Las gráficas a continuación muestran los detalles más críticos en estos componentes como: álabes del estator de 1era etapa con ligeras grietas a nivel de los orificios de enfriamiento, álabes del rotor de la 1era etapa con pérdida de material en el borde de ataque y bloques térmicos 1 era etapa con excesivo desgaste y efectos de altas temperaturas.

(Fuente: EYM Solutions, Maturín)

(Fuente: EYM Solutions, Maturín)

(Fuente: EYM Solutions, Maturín)
Turbina de Baja Presión (Turbina de Potencia)
Este modelo de turbina, contempla dos puertos de inspección para visualizar las condiciones de los componentes internos de esta sección, el primero para visualizar los álabes de 1era etapa (rotor/ estor) de la turbina de baja, y con el que se puede también observar los álabes rotativos de la 2da etapa de la turbina de alta presión. Un segundo puerto de inspección para observar los álabes de 2da etapa (estator/rotor) de la turbina de baja. En la siguiente figura se muestra un álabe del estator de la 2da etapa de la turbina de baja, con grieta que se extiende a través del borde.

(Fuente: EYM Solutions, Maturín)
Análisis de los Resultados
Una vez finalizada la inspección y cuando no se evidencian daños considerables en áreas acríticas que ameriten una intervención inmediata del equipo para realizar las reparaciones que correspondan, es muy importante evaluar la información con todos los registros obtenidos y con datos históricos de la máquina, tanto de inspecciones anteriores como con los registros de los parámetros operacionales, para analizarlos conjuntamente con un equipo de trabajo donde estén incluidos especialistas del departamento de ingeniería, mantenimiento y operación para determinar las acciones a seguir de tal forma de evitar una falla funcional (F) con consecuencias de gran impacto en los costos de operación y mantenimiento de la instalación.
Autor: Pedro Antonio Navas
Correo: pnava4@hotmail.com
Dinos qué te ha parecido el artículo
Artículos recomendados
Iso 55000: norma de activos físicos

Descubre los motores diésel y su mantenimiento

¿Por qué implementar S&OP en nuestros Negocios, y no morir en el intento?

Gestión de Estrategia de Activos: Realizar Valor - Mejorar Desempeño

Publica tu artículo en la revista #1 de Mantenimiento Industrial
Publicar un artículo en la revista es gratis, no tiene costo.
Solo debes asegurarte que no sea un artículo comercial.
¿Qué esperas?
O envía tu artículo directo: articulos@predictiva21.com
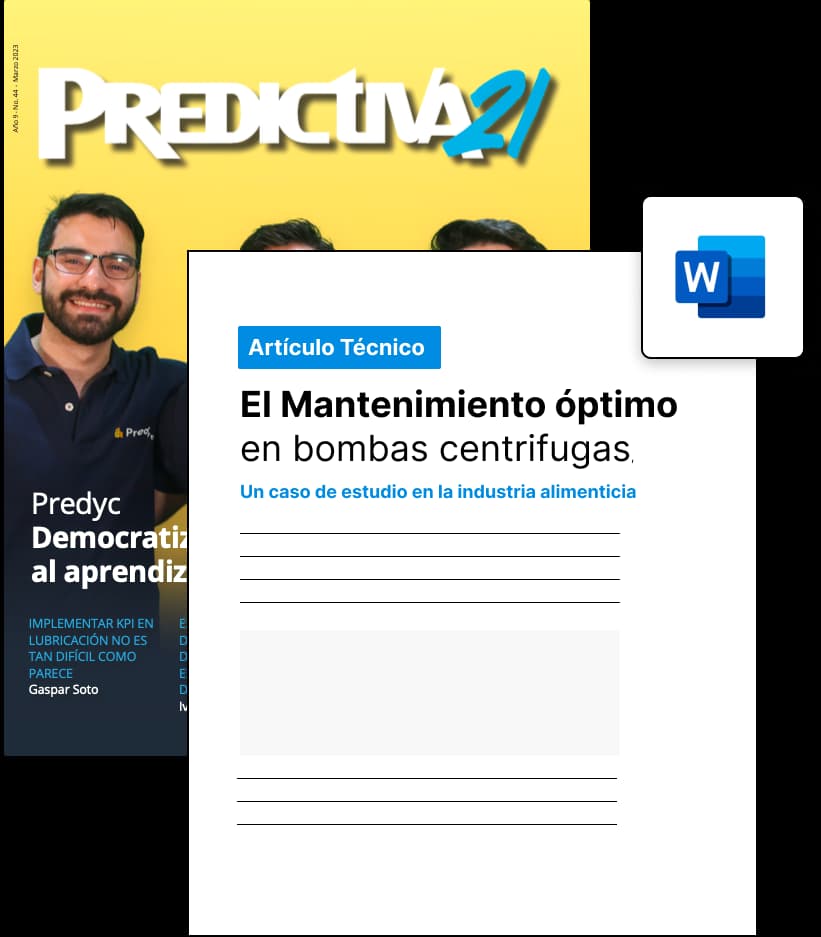
Inspección vídeo endoscopica: Estrategia útil del monitoreo basado en condición
Articulo 18 de abril de 2019En alguna oportunidad cuando hemos visitado al médico, este nos ha recomendado efectuar una vídeo endoscopia por presentar algunos síntomas como dolores estomacales, o solo para verificar algún daño asociado a las vías digestivas. Igualmente ocurre con las maquinas. Por ejemplo: en las turbinas industriales o areoderivativas cuando presentan alta temperatura de gases de escapes, baja presión de descarga del compresor axial, aumento en los niveles de vibración o en algunas ocasiones por fallas en modelos similares a determinadas horas de operación; se planifica una video endoscopia destinada a verificar las condiciones de sus componentes internos y de allí anticiparse a fallas mayores que conduzcan a incrementar los costos de operación y mantenimiento de la instalación.
Objetivo de la Video Endoscopia
Anteriormente, para determinas las condiciones físicas (grietas superficiales, defectos de soldadura, corrosión, desgaste, fatiga etc.) de los componentes internos de una turbina a gas o vapor, había que realizar desmontajes de algunos de estos componentes como la parte superior de la carcasa de los compresores axiales o la cámara de combustión de las turbinas, lo que conllevaban a demasiadas horas fuera de servicios de estos equipos, impactando la productividad de la instalación. Ya por los años 80’s comenzó a implementarse esta técnica con la aparición del boroscopio (flexible) y baroscopio (rígido), lo que permitía reducir los tiempos de paradas de la máquina. Aunque algunas turbinas no contaban con los puertos de inspección para tal fin, solo con retirar algunas partes como las bujías de la cámara de combustión, cesto de combustión o parte del múltiple de gas combustible era posible observar las partes más críticas y adicionalmente llevar registro de lo detectado, ya que estos equipos se podían conectar a una cámara fotográfica o cámara de video.
En el mercado actualmente existe una gama de equipos de video endoscopia, desde los más sofisticados y costosos hasta los más simples; sin embargo, la base de estos consisten en transmitir una luz blanca de gran intensidad proveniente de una fuente de luz (fuente de poder) y conectada a través de cable de fibra flexible a un broscopio (dispositivo flexible) o a un boroscopio (dispositivo rígido) de acuerdo al acceso a la parte inspeccionada, que para el caso de la turbinas, ya los fabricantes los tienen establecidos de acuerdo a su diseño y/o modelo.

(Fuente: Videoscopio IV86, marca Olympus)
Uno de los puntos de interés de esta estrategia del MBC es poder cuantificar la magnitud de la falla (por ejemplo, longitud y profundidad de una grieta de un álabe de una turbina) y llevar registro que permita ajustar la frecuencia de inspección para monitorear el deterioro progresivo de la Falla Potencial (P) e intervenir el equipo antes de presentarse la ocurrencia de una Falla Funcional (F) de consecuencias de alto impacto en la producción y costos de mantenimiento.

Aunque la vídeo Endoscopia no es una técnica predictiva de monitoreo de condición en línea, al igual que el resto de las técnicas cuantitativas contribuyen a evitar Falla funcionales (F) del equipo que en general reducen los costos de mantenimiento y operación mediante el ajuste del intervalo de inspección P-F.

Aplicaciones
El uso más común del video endoscopio es para la detección de grietas, desgates y fatigas en los álabes de turbinas; sin embargo, este es útil para inspeccionar recipientes a presión, intercambiadores de calor, cilindros de potencias de motores de combustión, tuberías de succión y descarga de compresores centrífugos, etc. donde igualmente los modos de fallas observados son grietas en superficies, desgastes, defectos de soldaduras y corrosión.
En cuanto a las inspecciones video endoscópicas a turbinas (industrial o aeroderivativa), en términos generales las partes inspeccionadas son: Compresor axial, cámara de combustión, turbina de alta presión (Turbina del Compresor) y turbina de baja presión (Turbina de Potencia). En cada uno de estos componentes habrá puertos específicos de inspección dependiendo de los fabricantes. Veamos un ejemplo práctico para una inspección de una turbina industrial GE modelo MS5001 de un turbo generador de 20 MW con 42704 horas de operación y 260 arranques desde su última reparación mayor.
Compresor axial
En este modelo de turbina para visualizar los álabes de 1era y 2da etapa (rotor / estator) y los inlet guide vanes (IGVs), hay que hacerlo a través del ducto de succión. Las siguientes figuras muestran un álabe de 1era etapa (rotor) con pérdida de material producto de algún impacto con un objeto desconocido y algunos inlet guide vanes (IGV`s) con presencia de sucio adherido en las paredes.

(Fuente: EYM solutions, Maturín)

(Fuente: EYM solutions, Maturín)
Cámara de Combustión
Dado que es el componente de la turbina donde se generan las altas temperaturas, atención especial a cada una de las partes que la conforman: cestos combustores, boquillas de gas combustibles, tubos cruza llamas, piezas de transición, etc.
En la turbina inspeccionada (GE MS5001) para revisar las partes calientes hay que retirar las boquillas de gas combustibles para introducir el boroscopio, en este caso se retiraron las correspondientes a los puntos 0, 90, 180 y 270º. En las siguientes figuras se muestran los detalles más críticos como son: Tubo cruza llama y piezas de transición con color rojizo característico de altas temperaturas.

(Fuente: EYM Solutions, Maturin)

(Fuente: EYM Solutions, Maturín)
Cursos recomendados






%252FImagen%252FRAMPREDYC-1730060420837.webp%3Falt%3Dmedia%26token%3D2634a7f0-988e-4022-b91f-382503e6e9db&w=3840&q=75)

Turbina de Alta Presión (Turbina del Compresor)
Para inspeccionar los álabes de 1era etapa (estator/rotor) en este modelo de turbina, se efectúa a través de los cestos combustores, es decir, llegar con el boroscopio por medio de la cámara de combustión, donde se pueden visualizar primeramente los alabes estacionarios correspondientes a cada sección del cesto combustor y luego girando el compresor axial lentamente (por medio del arrancador) se podrán inspeccionar los álabes rotativos de la misma. Las gráficas a continuación muestran los detalles más críticos en estos componentes como: álabes del estator de 1era etapa con ligeras grietas a nivel de los orificios de enfriamiento, álabes del rotor de la 1era etapa con pérdida de material en el borde de ataque y bloques térmicos 1 era etapa con excesivo desgaste y efectos de altas temperaturas.

(Fuente: EYM Solutions, Maturín)

(Fuente: EYM Solutions, Maturín)

(Fuente: EYM Solutions, Maturín)
Turbina de Baja Presión (Turbina de Potencia)
Este modelo de turbina, contempla dos puertos de inspección para visualizar las condiciones de los componentes internos de esta sección, el primero para visualizar los álabes de 1era etapa (rotor/ estor) de la turbina de baja, y con el que se puede también observar los álabes rotativos de la 2da etapa de la turbina de alta presión. Un segundo puerto de inspección para observar los álabes de 2da etapa (estator/rotor) de la turbina de baja. En la siguiente figura se muestra un álabe del estator de la 2da etapa de la turbina de baja, con grieta que se extiende a través del borde.

(Fuente: EYM Solutions, Maturín)
Análisis de los Resultados
Una vez finalizada la inspección y cuando no se evidencian daños considerables en áreas acríticas que ameriten una intervención inmediata del equipo para realizar las reparaciones que correspondan, es muy importante evaluar la información con todos los registros obtenidos y con datos históricos de la máquina, tanto de inspecciones anteriores como con los registros de los parámetros operacionales, para analizarlos conjuntamente con un equipo de trabajo donde estén incluidos especialistas del departamento de ingeniería, mantenimiento y operación para determinar las acciones a seguir de tal forma de evitar una falla funcional (F) con consecuencias de gran impacto en los costos de operación y mantenimiento de la instalación.
Autor: Pedro Antonio Navas
Correo: pnava4@hotmail.com
Dinos qué te ha parecido el artículo
Artículos recomendados
Congreso de mantenimiento

Uso y abuso del concepto “Creación de valor desde la gestión de mantenimiento”

La Orden de Trabajo

Mantenimiento programado

Publica tu artículo en la revista #1 de Mantenimiento Industrial
Publicar un artículo en la revista es gratis, no tiene costo.
Solo debes asegurarte que no sea un artículo comercial.
¿Qué esperas?
O envía tu artículo directo: articulos@predictiva21.com
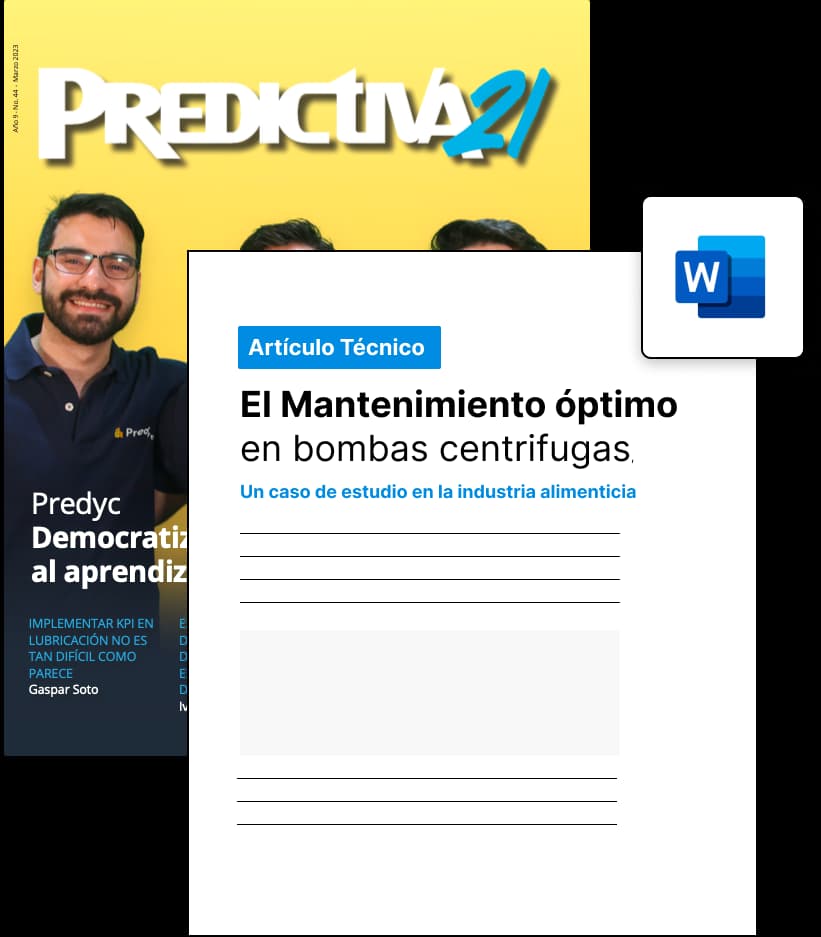