Uso del Programa Life CPR - ComSys© para la Selección del Accionador y el Arreglo Óptimo en Plantas Compresoras de Gas (II Parte)
Articulo13 de abril de 2020
Este artículo presenta el proceso de evaluación técnico económico que debe ser tomado en cuenta para la selección del tipo de accionador, el tamaño y el número óptimo de trenes en plantas compresoras de gas natural, durante la fase de conceptualización de nuevos proyectos. Técnicamente se verifica que los equipos sean capaces de satisfacer el servicio, y económicamente se jerarquizan las opciones por sus costos de ciclo de vida y las pérdidas de oportunidad causadas por los paros programados y no programados en el horizonte económico. Se introducen además las bondades del programa Life CPR – ComSys © (Life Cycle Cost, Procution and Reliability), desarrollado en Visual Basic Application, que facilita el cálculo de las variables técnicas y económicas necesarias para jerarquizar las opciones. Finalmente, se muestra un caso en el que la escogencia del arreglo fue facilitada por el uso del programa computarizado, lográndose reducir el esfuerzo y el tiempo de evaluación en un 35%.
Estimado de inversiones, costos y pérdidas
A continuación, algunas consideraciones para la estimación de las inversiones, los costos y las pérdidas de oportunidad, en el orden en que aparecen en el esquema de la Fig. 16.
Inversiones
En este trabajo definimos por estimados de inversión clase IV o V los que cumplen con las características descritas en la Tabla 1.
Los estimados clase V son suficientes para definir la factibilidad del negocio durante la Visualización del Proyecto, a fin de obtener fondos para desarrollar la Ingeniería Conceptual (Fig. 27). Usualmente se fundamentan en curvas de costos de proyectos similares, pero la limitación y dispersión de los datos en la muestra hace difícil establecer la confiabilidad del estimado.


Los estimados clase IV tienen la confiabilidad necesaria (±30%) para seleccionar la mejor opción técnica y económica durante la Ingeniería Conceptual del proyecto. El clase IV desglosa el proyecto en sus componentes más costosos (accionador, compresores, caja de engranajes, enfriadores, etc.), cuyas magnitudes se establecen con la ayuda de curvas y/o bases de costos por componente. La Fig. 28, por ejemplo, exhibe los precios de 65 modelos diferentes de turbinas en un amplio rango de potencias ISO. La curva tipo potencial corresponde al mejor ajuste de los datos. La desviación de precios entre la curva y los datos aparece en el histograma de la Fig. 29. La curva azul “tipo S” de probabilidad acumulada muestra que el precio del 90% de estas turbinas puede ser estimado por la curva con una confianza de ± 30%.


Costos energéticos
En el caso eléctrico, resultan de la multiplicación de la tarifa eléctrica por los requerimientos de potencia para la compresión. A la potencia suministrada por el motor debe agregársele las pérdidas que existan hasta el punto de fiscalización, como, por ejemplo, pérdidas en el motor, variador de frecuencia, filtros, transformadores y líneas de transmisión. La potencia requerida dependerá también del modo como se combinan los estados de los trenes, es decir, “On”, “Off y “Standby”. La Fig. 30 muestra la potencia al eje [Hp] requerida por cada tren y por el centro de compresión, para los 16 posibles modos de operación del ejemplo de la Fig. 25.

En el caso de accionadores a gas, los costos energéticos resultan de la multiplicación de la tarifa del gas por el volumen de gas combustible consumido. En el cálculo de este último intervienen, además de los requerimientos de potencia, el poder calórico del gas (LHV) y el “heat rate” de los accionadores. En el caso más general, el “heat rate” es afectado por las condiciones ambientales, las pérdidas en los ductos de entrada de aire y salida de gases, el deterioro del accionador y la operación “off design”. La Fig. 31 contiene los valores del “heat rate” en sitio [Btu/Hp-hr] y del volumen de gas combustible [MMscfd], correspondientes al ejemplo de las Fig. 25 y 30, considerando un poder calórico LHV de 1000 Btu/scf.

Alquileres de equipos y plantas
Cuando apliquen, deberán ser considerados como un costo dentro de las opciones evaluadas.
Cursos recomendados






%252FImagen%252FRAMPREDYC-1730060420837.webp%3Falt%3Dmedia%26token%3D2634a7f0-988e-4022-b91f-382503e6e9db&w=3840&q=75)

Costos de operación
Se refieren a los costos del personal, logística y administración necesarios para mantener la operación del centro de compresión. Es claro que estos no son lineales con el número de trenes. A manera de ejemplo, el personal requerido para la operación de cuatro trenes dentro de un mismo centro es muy similar al requerido para la operación de tres. Este costo se puede estimar de manera sencilla multiplicando el costo de labor directa por un factor de “overhead” que considere la labor indirecta, la logística y la administración.
Costos de mantenimiento
Se refieren a los costos del personal, logística, administración, materiales y repuestos involucrados en los mantenimientos preventivo, programado y correctivo. El mantenimiento correctivo está ligado a los indicadores de confiabilidad de los trenes, y estos a su vez a la tecnología seleccionada para el accionador y los compresores. Del mismo modo, la tecnología seleccionada determina la frecuencia y los costos de los diferentes niveles de mantenimiento programado: menor, media vida y overhaul.
Una manera simple de estimar los costos de mantenimiento programado y no programado, pero imprecisa y carente de realismo, es asumir que los mismos son constantes cada año, y que representan un porcentaje fijo de la inversión (2% al 5% por ejemplo).
Un tanto más acertado es el uso de indicadores de costo [$/Hp-hr], que toman en cuenta las horas de operación de los trenes, pero pasan por alto el aspecto cíclico de los mantenimientos programados y establecen erróneamente una dependencia lineal entre los costos de mantenimiento y el tamaño de los equipos. Es bien sabido que el costo por Hp disminuye a medida que aumenta el tamaño de los equipos. Establecer el indicador apropiado para el servicio es en si un reto. La Fig. 32 muestra un sondeo de indicadores de mantenimiento [$/Hp-hr] utilizados por diferentes fuentes, para trenes compresores accionados por motores a gas. Los indicadores en generación eléctrica se añaden como referencia. Las líneas verticales azules corresponden al rango de indicadores encontrado por el autor en 49 aplicaciones que soportan producción de petróleo en Venezuela. La distribución probabilística de los costos de esas 49 aplicaciones se incluye en la parte derecha del gráfico.

Otra forma más precisa, pero que requiere más elaboración, separa los mantenimientos programados de las fallas. Los mantenimientos programados de todos los trenes se sincronizan en la vida del proyecto, considerando las horas de operación de cada tren y las frecuencias recomendadas. A cada nivel de mantenimiento se le asigna entonces el costo que le corresponde. Los mantenimientos por fallas, aunque son de carácter aleatorio, se asocian también a las horas operadas. Este método trata en forma justa los trenes de respaldo que se encuentran en “standby”, pues estos sólo operan una fracción del año. La Fig. 33 muestra un ejemplo de un tren reciprocante accionado por un motor a gas de 2225 Hp, para el que se han definido cuatro niveles de mantenimiento con frecuencias respectivas de 1000, 4000, 8000 y 32000 hrs. En ella se cuantifican los mantenimientos por nivel en los primeros 6 años de operación, considerando las horas operadas cada año, después de descontar las horas en “standby” y en paros programados y no programados. Obsérvese como en el año 2007 sólo hay un mantenimiento programado, debido a que el tren se encuentra en “standby” casi todo el año y sólo opera 734 hrs, equivalentes a un mes.

Debe tomarse en cuenta que algunos lineamientos financieros capitalizan los mantenimientos mayores, en lugar de contabilizados como gastos. Un ejemplo son los overhauls de las turbinas a gas.
Bonos y penalizaciones
Deben considerarse cuando existan. Algunos proyectos, por ejemplo, están sujetos a bonos ó penalizaciones asociados a la cantidad de gas comprimido, o a los indicadores de disponibilidad y confiabilidad. Otros proyectos son penalizados con multas cuando ventean o queman gas porque sus trenes están fuera de servicio. La adición de bonos y penalizaciones favorece la selección de equipos confiables y, dependiendo de los montos, justifica la adición de capacidad o trenes de respaldo. La matriz de modos de la Fig. 25 sirve para cuantificar la cantidad de gas no manejado, venteado o quemado, insumo para contabilizar los bonos y penalizaciones en el flujo de caja.
Pérdida de oportunidades
Como ya se mencionó, son las mermas en los ingresos, directos e indirectos, a los que se da lugar cuando se producen paros programados y no programados. Dependiendo de la actividad que se soporte (venta de gas comprimido, inyección de gas a yacimientos, levantamiento artificial de crudo, extracción de LGN, etc.), las pérdidas de oportunidad pudieran fácilmente convertirse en el mayor de los renglones. Al igual que en el punto anterior, la matriz de modos de la Fig. 25 sirve para estimar la pérdida de oportunidades, una vez que se establezcan las correlaciones entre el gas no manejado y la merma de los productos de la actividad económica soportada.
Autor: Enrique J. González
Ingeniero Mecánico de la Universidad Simón Bolívar (1986).
Maestría en Ingeniería Mecánica en la Universidad de Texas A&M.
Dinos qué te ha parecido el artículo
Artículos recomendados
Redes de conocimiento AMGA

Vehículos eléctricos: descubre su mantenimiento y cómo funcionan

Línea del tiempo de la ingeniería industrial

Aplicación de la Tecnología de Inspección Basada en Riesgo (IBR) para la Generación de Planes Óptimos de Inspección a Equipos Estáticos en la Industria del Petróleo y Gas

Publica tu artículo en la revista #1 de Mantenimiento Industrial
Publicar un artículo en la revista es gratis, no tiene costo.
Solo debes asegurarte que no sea un artículo comercial.
¿Qué esperas?
O envía tu artículo directo: articulos@predictiva21.com
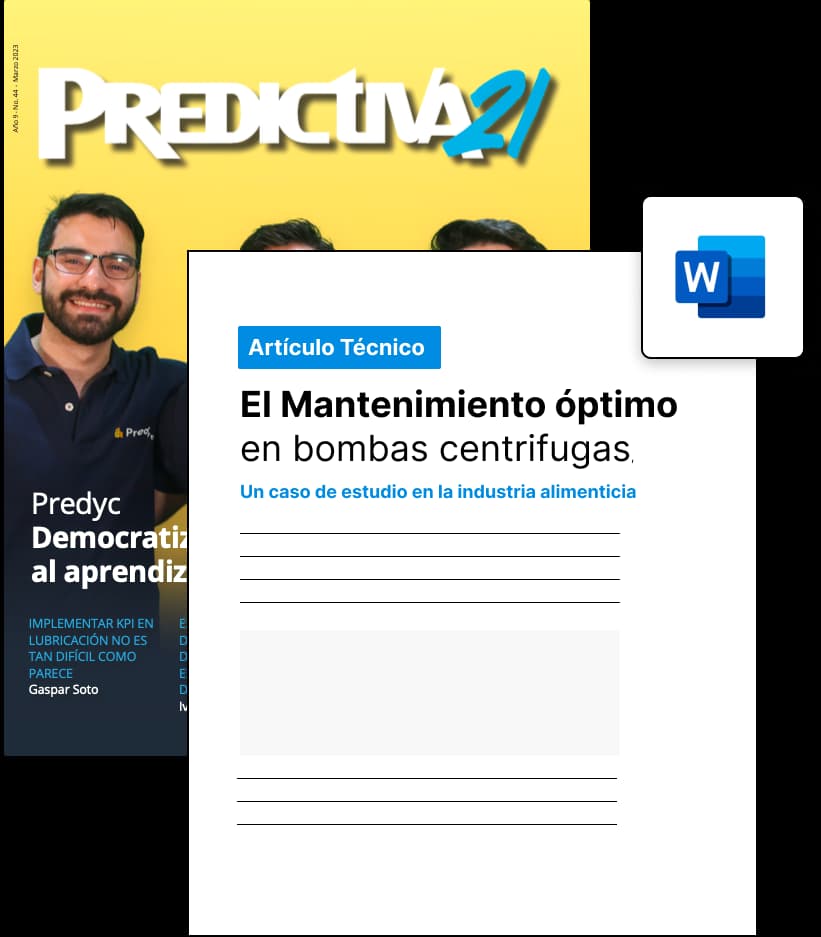
Uso del Programa Life CPR - ComSys© para la Selección del Accionador y el Arreglo Óptimo en Plantas Compresoras de Gas (II Parte)
Articulo 13 de abril de 2020Este artículo presenta el proceso de evaluación técnico económico que debe ser tomado en cuenta para la selección del tipo de accionador, el tamaño y el número óptimo de trenes en plantas compresoras de gas natural, durante la fase de conceptualización de nuevos proyectos. Técnicamente se verifica que los equipos sean capaces de satisfacer el servicio, y económicamente se jerarquizan las opciones por sus costos de ciclo de vida y las pérdidas de oportunidad causadas por los paros programados y no programados en el horizonte económico. Se introducen además las bondades del programa Life CPR – ComSys © (Life Cycle Cost, Procution and Reliability), desarrollado en Visual Basic Application, que facilita el cálculo de las variables técnicas y económicas necesarias para jerarquizar las opciones. Finalmente, se muestra un caso en el que la escogencia del arreglo fue facilitada por el uso del programa computarizado, lográndose reducir el esfuerzo y el tiempo de evaluación en un 35%.
Estimado de inversiones, costos y pérdidas
A continuación, algunas consideraciones para la estimación de las inversiones, los costos y las pérdidas de oportunidad, en el orden en que aparecen en el esquema de la Fig. 16.
Inversiones
En este trabajo definimos por estimados de inversión clase IV o V los que cumplen con las características descritas en la Tabla 1.
Los estimados clase V son suficientes para definir la factibilidad del negocio durante la Visualización del Proyecto, a fin de obtener fondos para desarrollar la Ingeniería Conceptual (Fig. 27). Usualmente se fundamentan en curvas de costos de proyectos similares, pero la limitación y dispersión de los datos en la muestra hace difícil establecer la confiabilidad del estimado.


Los estimados clase IV tienen la confiabilidad necesaria (±30%) para seleccionar la mejor opción técnica y económica durante la Ingeniería Conceptual del proyecto. El clase IV desglosa el proyecto en sus componentes más costosos (accionador, compresores, caja de engranajes, enfriadores, etc.), cuyas magnitudes se establecen con la ayuda de curvas y/o bases de costos por componente. La Fig. 28, por ejemplo, exhibe los precios de 65 modelos diferentes de turbinas en un amplio rango de potencias ISO. La curva tipo potencial corresponde al mejor ajuste de los datos. La desviación de precios entre la curva y los datos aparece en el histograma de la Fig. 29. La curva azul “tipo S” de probabilidad acumulada muestra que el precio del 90% de estas turbinas puede ser estimado por la curva con una confianza de ± 30%.


Costos energéticos
En el caso eléctrico, resultan de la multiplicación de la tarifa eléctrica por los requerimientos de potencia para la compresión. A la potencia suministrada por el motor debe agregársele las pérdidas que existan hasta el punto de fiscalización, como, por ejemplo, pérdidas en el motor, variador de frecuencia, filtros, transformadores y líneas de transmisión. La potencia requerida dependerá también del modo como se combinan los estados de los trenes, es decir, “On”, “Off y “Standby”. La Fig. 30 muestra la potencia al eje [Hp] requerida por cada tren y por el centro de compresión, para los 16 posibles modos de operación del ejemplo de la Fig. 25.

En el caso de accionadores a gas, los costos energéticos resultan de la multiplicación de la tarifa del gas por el volumen de gas combustible consumido. En el cálculo de este último intervienen, además de los requerimientos de potencia, el poder calórico del gas (LHV) y el “heat rate” de los accionadores. En el caso más general, el “heat rate” es afectado por las condiciones ambientales, las pérdidas en los ductos de entrada de aire y salida de gases, el deterioro del accionador y la operación “off design”. La Fig. 31 contiene los valores del “heat rate” en sitio [Btu/Hp-hr] y del volumen de gas combustible [MMscfd], correspondientes al ejemplo de las Fig. 25 y 30, considerando un poder calórico LHV de 1000 Btu/scf.

Alquileres de equipos y plantas
Cuando apliquen, deberán ser considerados como un costo dentro de las opciones evaluadas.
Cursos recomendados






%252FImagen%252FRAMPREDYC-1730060420837.webp%3Falt%3Dmedia%26token%3D2634a7f0-988e-4022-b91f-382503e6e9db&w=3840&q=75)

Costos de operación
Se refieren a los costos del personal, logística y administración necesarios para mantener la operación del centro de compresión. Es claro que estos no son lineales con el número de trenes. A manera de ejemplo, el personal requerido para la operación de cuatro trenes dentro de un mismo centro es muy similar al requerido para la operación de tres. Este costo se puede estimar de manera sencilla multiplicando el costo de labor directa por un factor de “overhead” que considere la labor indirecta, la logística y la administración.
Costos de mantenimiento
Se refieren a los costos del personal, logística, administración, materiales y repuestos involucrados en los mantenimientos preventivo, programado y correctivo. El mantenimiento correctivo está ligado a los indicadores de confiabilidad de los trenes, y estos a su vez a la tecnología seleccionada para el accionador y los compresores. Del mismo modo, la tecnología seleccionada determina la frecuencia y los costos de los diferentes niveles de mantenimiento programado: menor, media vida y overhaul.
Una manera simple de estimar los costos de mantenimiento programado y no programado, pero imprecisa y carente de realismo, es asumir que los mismos son constantes cada año, y que representan un porcentaje fijo de la inversión (2% al 5% por ejemplo).
Un tanto más acertado es el uso de indicadores de costo [$/Hp-hr], que toman en cuenta las horas de operación de los trenes, pero pasan por alto el aspecto cíclico de los mantenimientos programados y establecen erróneamente una dependencia lineal entre los costos de mantenimiento y el tamaño de los equipos. Es bien sabido que el costo por Hp disminuye a medida que aumenta el tamaño de los equipos. Establecer el indicador apropiado para el servicio es en si un reto. La Fig. 32 muestra un sondeo de indicadores de mantenimiento [$/Hp-hr] utilizados por diferentes fuentes, para trenes compresores accionados por motores a gas. Los indicadores en generación eléctrica se añaden como referencia. Las líneas verticales azules corresponden al rango de indicadores encontrado por el autor en 49 aplicaciones que soportan producción de petróleo en Venezuela. La distribución probabilística de los costos de esas 49 aplicaciones se incluye en la parte derecha del gráfico.

Otra forma más precisa, pero que requiere más elaboración, separa los mantenimientos programados de las fallas. Los mantenimientos programados de todos los trenes se sincronizan en la vida del proyecto, considerando las horas de operación de cada tren y las frecuencias recomendadas. A cada nivel de mantenimiento se le asigna entonces el costo que le corresponde. Los mantenimientos por fallas, aunque son de carácter aleatorio, se asocian también a las horas operadas. Este método trata en forma justa los trenes de respaldo que se encuentran en “standby”, pues estos sólo operan una fracción del año. La Fig. 33 muestra un ejemplo de un tren reciprocante accionado por un motor a gas de 2225 Hp, para el que se han definido cuatro niveles de mantenimiento con frecuencias respectivas de 1000, 4000, 8000 y 32000 hrs. En ella se cuantifican los mantenimientos por nivel en los primeros 6 años de operación, considerando las horas operadas cada año, después de descontar las horas en “standby” y en paros programados y no programados. Obsérvese como en el año 2007 sólo hay un mantenimiento programado, debido a que el tren se encuentra en “standby” casi todo el año y sólo opera 734 hrs, equivalentes a un mes.

Debe tomarse en cuenta que algunos lineamientos financieros capitalizan los mantenimientos mayores, en lugar de contabilizados como gastos. Un ejemplo son los overhauls de las turbinas a gas.
Bonos y penalizaciones
Deben considerarse cuando existan. Algunos proyectos, por ejemplo, están sujetos a bonos ó penalizaciones asociados a la cantidad de gas comprimido, o a los indicadores de disponibilidad y confiabilidad. Otros proyectos son penalizados con multas cuando ventean o queman gas porque sus trenes están fuera de servicio. La adición de bonos y penalizaciones favorece la selección de equipos confiables y, dependiendo de los montos, justifica la adición de capacidad o trenes de respaldo. La matriz de modos de la Fig. 25 sirve para cuantificar la cantidad de gas no manejado, venteado o quemado, insumo para contabilizar los bonos y penalizaciones en el flujo de caja.
Pérdida de oportunidades
Como ya se mencionó, son las mermas en los ingresos, directos e indirectos, a los que se da lugar cuando se producen paros programados y no programados. Dependiendo de la actividad que se soporte (venta de gas comprimido, inyección de gas a yacimientos, levantamiento artificial de crudo, extracción de LGN, etc.), las pérdidas de oportunidad pudieran fácilmente convertirse en el mayor de los renglones. Al igual que en el punto anterior, la matriz de modos de la Fig. 25 sirve para estimar la pérdida de oportunidades, una vez que se establezcan las correlaciones entre el gas no manejado y la merma de los productos de la actividad económica soportada.
Autor: Enrique J. González
Ingeniero Mecánico de la Universidad Simón Bolívar (1986).
Maestría en Ingeniería Mecánica en la Universidad de Texas A&M.
Dinos qué te ha parecido el artículo
Artículos recomendados
Introducción al Análisis de Fallas Múltiples

Técnico en mantenimiento

Dónde estudiar técnico en mantenimiento industrial

Certificación SMRP: descubre este importante certificado

Publica tu artículo en la revista #1 de Mantenimiento Industrial
Publicar un artículo en la revista es gratis, no tiene costo.
Solo debes asegurarte que no sea un artículo comercial.
¿Qué esperas?
O envía tu artículo directo: articulos@predictiva21.com
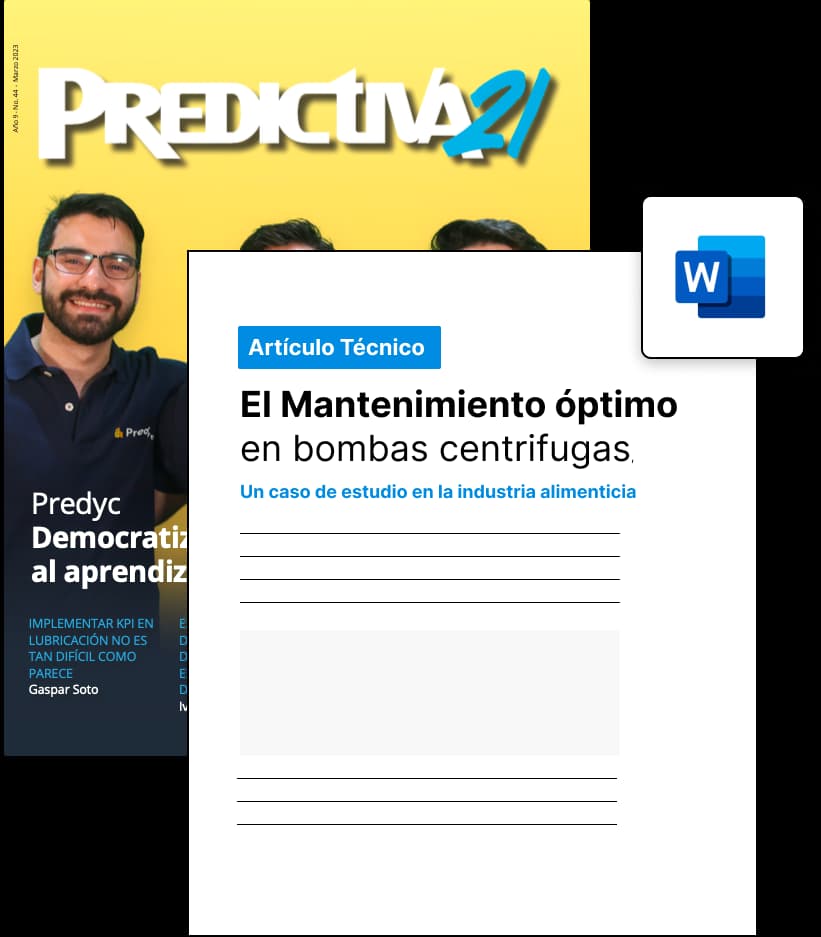