El Mantenimiento Preventivo no siempre es una Tarea Fácil
Articulo26 de mayo de 2019
Todos hablamos del Mantenimiento Preventivo como si fuese una actividad muy sencilla, pero esto está muy lejos de ser cierto. Aunque ustedes no lo crean, el rango en el cual se encuentra el Indicador de efectividad de mantenimiento preventivo oscila entre un 40 y 70 por ciento. Este es el resultado de casi 30 años de experiencia en consultoría, investigación, encuestas y de opiniones del personal que trabaja en el área de mantenimiento. Si bien es cierto que esta afirmación que hago es para empresas venezolanas, porque muchos países no tiene las complicaciones económicas y regulaciones para conseguir repuestos, también pienso que está muy cerca de la realidad, debido a trabajos que he hecho en el exterior, encontrándome situaciones que también suceden en esas plantas y que las comentaremos mas adelante. Vamos a iniciarnos con la siguiente pregunta: ¿A qué llamo Indicador de Efectividad de Trabajos Preventivos? Esto es: Cantidad de Trabajos de Mantenimiento Preventivo Ejecutados versus Cantidad de Trabajos de Mantenimiento Preventivo Programados en un período determinado, ya sea en una semana, mes, trimestre, semestre o anual. Ahora bien, veamos por qué de lo dicho anteriormente con relación a la dificultad de lograr la consecución de un alto valor de este indicador de trabajos preventivos. A continuación paso a explicarlo y quizás después de leerlo coincidan conmigo.
1. Cuando se elaboran las rutinas de mantenimiento, en éstas he encontrado que la información contenida es deficiente porque no contempla toda la documentación necesaria para construir protocolos de mantenimiento efectivos. Esto se debe principalmente a: mala estimación de los tiempos de ejecución de los trabajos preventivos, falta de materiales partes y repuestos que deben estar indicados en las rutinas, inadecuadas o falta de herramientas que son necesarias para llevar a buen término estas actividades, inadecuadas frecuencias de intervenciones preventivas, falta y confusos procedimientos para ejecutar los trabajos, y una situación sumamente marcada es la ausencia de manuales de operación y mantenimiento, despieces y planos. En otras palabras, hay una planificación inadecuada o deficiente al momento de elaborar las rutinas preventivas. Fíjense que me refiero a la planificación y no a la programación, recuerden que aquí hablamos del momento en el cual estamos, recopilando, elaborando y organizando la información a contemplar en los trabajos preventivos y que posteriormente pasarán a la etapa de programación y ejecución.
2. La organización del mantenimiento no siempre es la mejor diseñada para llevar a cabo las tareas de Planificación, Programación y Ejecución correctamente. Muchas veces tenemos una(s) persona(s) que planifica(n), programa(n) y también ejecuta(n) el mantenimiento preventivo, pero adicionalmente también lleva(n) a cabo los trabajos correctivos, Ahora les pregunto: ¿Cómo van a poder cumplir con todas las tareas preventivas si la(s) misma(s) persona(s) que está(n) involucradas en los preventivos la utilizamos para que intervengan en los trabajos correctivos tanto programados como de emergencia? Cualquier programa se verá afectado ante esta situación .
3. Muchas veces no tenemos estructurada una orden de trabajos preventivos y que según mi experiencia debe ser diferente a la de trabajos correctivos. Si entendemos que una rutina preventiva es: “hacer siempre lo mismo, con la misma frecuencia, misma cantidad y tiempo de mano de obra, mismo tiempo completo de la actividad, condiciones de seguridad, los mismos repuestos, partes y materiales, al igual que las herramientas”; las personas no logran construir la estrategia para general las órdenes de trabajos preventivos que por su volumen y frecuencia pueden convertirse en un trauma que mas adelante causa una gran frustración y en consecuencia, la posible presencia de lo que llamé en el artículo anterior de la revista “El Costo Psicológico”.
4. Para los que trabajan en el medio industrial, saben muy bien que el dueño de los equipos es la gente de operación o en menor nivel la de producción, y muchas veces cuando está programado realizar un preventivo a cualquier equipo o instalación, no es entregado al personal de mantenimiento justificando que deben sacar una producción cualquiera. Muchas veces esto se acentúa cuando no existe una verdadera comunicación o interrelación entre quien opera y quien mantiene. De igual manera, la postergación o adelanto de un trabajo preventivo a la espera de un mantenimiento correctivo programado o viceversa, también contribuye a desbalancear el BACKLOG ocasionando dificultad para aumentar el porcentaje de efectividad del mantenimiento preventivo.
5. Para el caso que nos ocupa, la dificultad que tenemos en Venezuela para obtener divisas, así como también devaluaciones continuas está mellando considerablemente la vida útil del equipamiento, debido a que, ante la falta de repuestos, partes y materiales tengamos que estar postergando los trabajos preventivos o ejecutándolos inadecuadamente. Indudablemente este escenario está afectando profundamente la producción de alimentos, bienes y servicios; y el reemplazo de los equipos por demás, se está convirtiendo en un escenario sumamente difícil. Sin temor a equivocarme, la ausencia de insumos para realizar los trabajos preventivos también afecta no solo a nuestro indicador, sino a la operación misma.
6. La ausencia de planes de adiestramiento, entrenamiento, mejoramiento profesional que son estrategias de fortalecimiento del recurso humano, muchas empresas deciden minimizarlas al momento que se ven amenazadas su estructura de costos y ganancias. Esta situación le suma un ingrediente negativo a este indicador de efectividad de trabajos preventivos.
7. La “Rotación del Personal” es una variable muy importante que igualmente afecta este indicador de trabajos preventivos. Esto se debe a que cuando existe una alta rotación por mejores beneficios de las personas que tienen el know how y el know What, saber cómo y saber qué, comienzan a irse de las empresas dejándolas a éstas en una posición sumamente delicada. Sumado a ello, si no se tiene una filosofía de mantenimiento sólida con un buen sistema de mantenimiento bien organizado, estructurado y soportado, inevitablemente el impacto negativo va ser mucho mayor. En este orden de ideas, cuando las personas llegan a una organización y sus actividades productivas son muy agresivas, tal es el caso de trabajos de minería, cuyos trabajadores están expuestos a grandes riesgos por profundidades a las cuales trabajan, duran muy pocos ocasionando así altas rotaciones. Las personas nunca aprenden ni a operar ni a mantener adecuadamente los equipos, mucho menos a planificar y programar trabajos preventivos.
8. Un control de inventarios débil y un desconocimiento de una clasificación ABC desvirtuada de una efectiva política de materiales que permita tener oportunamente en el almacén aquellos materiales partes y repuestos que son parte de un consumo rutinario, también evita alcanzar altos valores del indicador.
9. El tipo de proceso muchas veces imposibilita realizar un mantenimiento preventivo, tal es el caso de plantas de flujo continuo que durante la Ingeniería básica y de detalle se colocan equipos que forzosamente necesitan preventivos y para no pararlos tenemos que esperar una Parada de planta planificada y programada para atenderlos. Indudablemente, el mantenimiento predictivo cobra mucha fuerza en estos casos para mantener la confiabilidad operacional.
10. La ausencia de un buen software de mantenimiento que permita controlar el Backlog y a la vez balancear adecuadamente tanto la carga de trabajos de mantenimiento correctivo como de preventivo es otra situación que contribuye a que el indicador de efectividad de los trabajos preventivos sea muy débil.
11. En el artículo “La Aptitud y la Actitud hacia el mantenimiento” del cual hablamos en el volumen #3 de esta revista encontramos que hay gente que no quiere hacer mantenimiento o simplemente no quiere hacer las cosas bien. Estas personas son los que hacen ruido en una empresa y son un problema. El mantenimiento preventivo no escapa tampoco a estas situaciones.
Para concluir, quizás existan otras razones que afectan el indicador de efectividad de los trabajos preventivos, pero considero que si logramos resolver o atenuar estos escenarios, estaremos muy cerca del camino correcto para construir un Sistema de Mantenimiento de Calidad. Recuerde mi máxima:
“No se puede mantener lo que no se conoce”
Brau Clemenza
Autor: Ing. Brau Clemenza
M.Sc en Gerencia de Mantenimiento
Consultor, Profesor, Investigador y Articulista
Dinos qué te ha parecido el artículo
Artículos recomendados
El Entrenamiento como Pilar de la Operación y Mantenimiento en la Industria

Confiabilidad en el Talento Humano para Organizaciones Exitosas

Aprende qué es un plan de mantenimiento

Criterios de aceptación de niveles de Vibración en Compresores Reciprocantes

Publica tu artículo en la revista #1 de Mantenimiento Industrial
Publicar un artículo en la revista es gratis, no tiene costo.
Solo debes asegurarte que no sea un artículo comercial.
¿Qué esperas?
O envía tu artículo directo: articulos@predictiva21.com
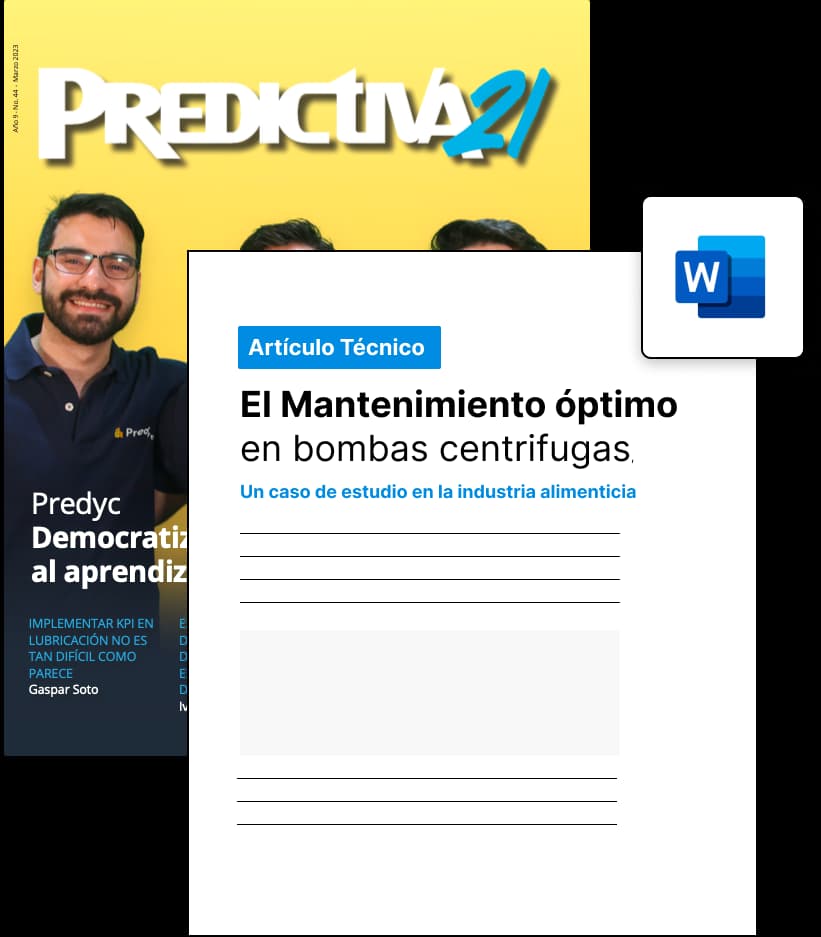
El Mantenimiento Preventivo no siempre es una Tarea Fácil
Articulo 26 de mayo de 2019Todos hablamos del Mantenimiento Preventivo como si fuese una actividad muy sencilla, pero esto está muy lejos de ser cierto. Aunque ustedes no lo crean, el rango en el cual se encuentra el Indicador de efectividad de mantenimiento preventivo oscila entre un 40 y 70 por ciento. Este es el resultado de casi 30 años de experiencia en consultoría, investigación, encuestas y de opiniones del personal que trabaja en el área de mantenimiento. Si bien es cierto que esta afirmación que hago es para empresas venezolanas, porque muchos países no tiene las complicaciones económicas y regulaciones para conseguir repuestos, también pienso que está muy cerca de la realidad, debido a trabajos que he hecho en el exterior, encontrándome situaciones que también suceden en esas plantas y que las comentaremos mas adelante. Vamos a iniciarnos con la siguiente pregunta: ¿A qué llamo Indicador de Efectividad de Trabajos Preventivos? Esto es: Cantidad de Trabajos de Mantenimiento Preventivo Ejecutados versus Cantidad de Trabajos de Mantenimiento Preventivo Programados en un período determinado, ya sea en una semana, mes, trimestre, semestre o anual. Ahora bien, veamos por qué de lo dicho anteriormente con relación a la dificultad de lograr la consecución de un alto valor de este indicador de trabajos preventivos. A continuación paso a explicarlo y quizás después de leerlo coincidan conmigo.
1. Cuando se elaboran las rutinas de mantenimiento, en éstas he encontrado que la información contenida es deficiente porque no contempla toda la documentación necesaria para construir protocolos de mantenimiento efectivos. Esto se debe principalmente a: mala estimación de los tiempos de ejecución de los trabajos preventivos, falta de materiales partes y repuestos que deben estar indicados en las rutinas, inadecuadas o falta de herramientas que son necesarias para llevar a buen término estas actividades, inadecuadas frecuencias de intervenciones preventivas, falta y confusos procedimientos para ejecutar los trabajos, y una situación sumamente marcada es la ausencia de manuales de operación y mantenimiento, despieces y planos. En otras palabras, hay una planificación inadecuada o deficiente al momento de elaborar las rutinas preventivas. Fíjense que me refiero a la planificación y no a la programación, recuerden que aquí hablamos del momento en el cual estamos, recopilando, elaborando y organizando la información a contemplar en los trabajos preventivos y que posteriormente pasarán a la etapa de programación y ejecución.
2. La organización del mantenimiento no siempre es la mejor diseñada para llevar a cabo las tareas de Planificación, Programación y Ejecución correctamente. Muchas veces tenemos una(s) persona(s) que planifica(n), programa(n) y también ejecuta(n) el mantenimiento preventivo, pero adicionalmente también lleva(n) a cabo los trabajos correctivos, Ahora les pregunto: ¿Cómo van a poder cumplir con todas las tareas preventivas si la(s) misma(s) persona(s) que está(n) involucradas en los preventivos la utilizamos para que intervengan en los trabajos correctivos tanto programados como de emergencia? Cualquier programa se verá afectado ante esta situación .
3. Muchas veces no tenemos estructurada una orden de trabajos preventivos y que según mi experiencia debe ser diferente a la de trabajos correctivos. Si entendemos que una rutina preventiva es: “hacer siempre lo mismo, con la misma frecuencia, misma cantidad y tiempo de mano de obra, mismo tiempo completo de la actividad, condiciones de seguridad, los mismos repuestos, partes y materiales, al igual que las herramientas”; las personas no logran construir la estrategia para general las órdenes de trabajos preventivos que por su volumen y frecuencia pueden convertirse en un trauma que mas adelante causa una gran frustración y en consecuencia, la posible presencia de lo que llamé en el artículo anterior de la revista “El Costo Psicológico”.
4. Para los que trabajan en el medio industrial, saben muy bien que el dueño de los equipos es la gente de operación o en menor nivel la de producción, y muchas veces cuando está programado realizar un preventivo a cualquier equipo o instalación, no es entregado al personal de mantenimiento justificando que deben sacar una producción cualquiera. Muchas veces esto se acentúa cuando no existe una verdadera comunicación o interrelación entre quien opera y quien mantiene. De igual manera, la postergación o adelanto de un trabajo preventivo a la espera de un mantenimiento correctivo programado o viceversa, también contribuye a desbalancear el BACKLOG ocasionando dificultad para aumentar el porcentaje de efectividad del mantenimiento preventivo.
5. Para el caso que nos ocupa, la dificultad que tenemos en Venezuela para obtener divisas, así como también devaluaciones continuas está mellando considerablemente la vida útil del equipamiento, debido a que, ante la falta de repuestos, partes y materiales tengamos que estar postergando los trabajos preventivos o ejecutándolos inadecuadamente. Indudablemente este escenario está afectando profundamente la producción de alimentos, bienes y servicios; y el reemplazo de los equipos por demás, se está convirtiendo en un escenario sumamente difícil. Sin temor a equivocarme, la ausencia de insumos para realizar los trabajos preventivos también afecta no solo a nuestro indicador, sino a la operación misma.
6. La ausencia de planes de adiestramiento, entrenamiento, mejoramiento profesional que son estrategias de fortalecimiento del recurso humano, muchas empresas deciden minimizarlas al momento que se ven amenazadas su estructura de costos y ganancias. Esta situación le suma un ingrediente negativo a este indicador de efectividad de trabajos preventivos.
7. La “Rotación del Personal” es una variable muy importante que igualmente afecta este indicador de trabajos preventivos. Esto se debe a que cuando existe una alta rotación por mejores beneficios de las personas que tienen el know how y el know What, saber cómo y saber qué, comienzan a irse de las empresas dejándolas a éstas en una posición sumamente delicada. Sumado a ello, si no se tiene una filosofía de mantenimiento sólida con un buen sistema de mantenimiento bien organizado, estructurado y soportado, inevitablemente el impacto negativo va ser mucho mayor. En este orden de ideas, cuando las personas llegan a una organización y sus actividades productivas son muy agresivas, tal es el caso de trabajos de minería, cuyos trabajadores están expuestos a grandes riesgos por profundidades a las cuales trabajan, duran muy pocos ocasionando así altas rotaciones. Las personas nunca aprenden ni a operar ni a mantener adecuadamente los equipos, mucho menos a planificar y programar trabajos preventivos.
8. Un control de inventarios débil y un desconocimiento de una clasificación ABC desvirtuada de una efectiva política de materiales que permita tener oportunamente en el almacén aquellos materiales partes y repuestos que son parte de un consumo rutinario, también evita alcanzar altos valores del indicador.
9. El tipo de proceso muchas veces imposibilita realizar un mantenimiento preventivo, tal es el caso de plantas de flujo continuo que durante la Ingeniería básica y de detalle se colocan equipos que forzosamente necesitan preventivos y para no pararlos tenemos que esperar una Parada de planta planificada y programada para atenderlos. Indudablemente, el mantenimiento predictivo cobra mucha fuerza en estos casos para mantener la confiabilidad operacional.
10. La ausencia de un buen software de mantenimiento que permita controlar el Backlog y a la vez balancear adecuadamente tanto la carga de trabajos de mantenimiento correctivo como de preventivo es otra situación que contribuye a que el indicador de efectividad de los trabajos preventivos sea muy débil.
11. En el artículo “La Aptitud y la Actitud hacia el mantenimiento” del cual hablamos en el volumen #3 de esta revista encontramos que hay gente que no quiere hacer mantenimiento o simplemente no quiere hacer las cosas bien. Estas personas son los que hacen ruido en una empresa y son un problema. El mantenimiento preventivo no escapa tampoco a estas situaciones.
Para concluir, quizás existan otras razones que afectan el indicador de efectividad de los trabajos preventivos, pero considero que si logramos resolver o atenuar estos escenarios, estaremos muy cerca del camino correcto para construir un Sistema de Mantenimiento de Calidad. Recuerde mi máxima:
“No se puede mantener lo que no se conoce”
Brau Clemenza
Autor: Ing. Brau Clemenza
M.Sc en Gerencia de Mantenimiento
Consultor, Profesor, Investigador y Articulista
Dinos qué te ha parecido el artículo
Artículos recomendados
Herramientas para la Auditoria y Certificación en Gestión de Activos. Pas 55 - Pam - Sam e ISO 55001

Redes de conocimiento AMGA

Modelos matemáticos de cálculo de criticidades de activos industriales

Gestión de mantenimiento de averías

Publica tu artículo en la revista #1 de Mantenimiento Industrial
Publicar un artículo en la revista es gratis, no tiene costo.
Solo debes asegurarte que no sea un artículo comercial.
¿Qué esperas?
O envía tu artículo directo: articulos@predictiva21.com
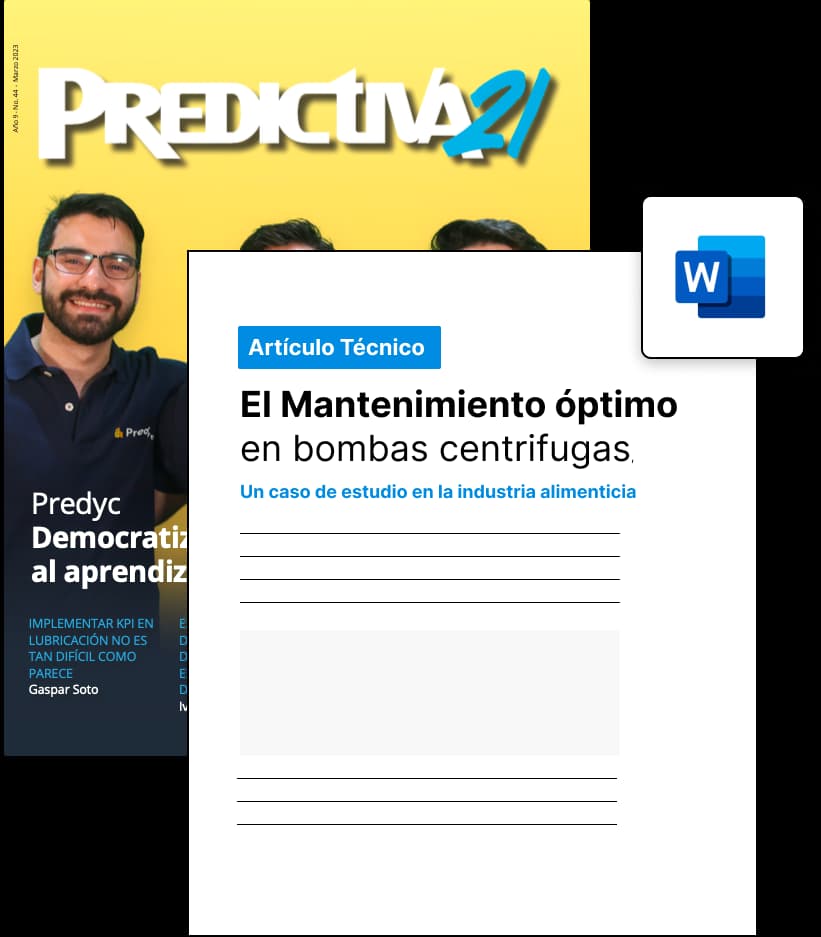