El Plan de Mejora Operativa como Metodología para detectar Áreas de Oportunidad en la Turbo Maquinaria de instalaciones Costa Afuera
Articulo15 de junio de 2020
1. Abstract
This document describes methodological aspects of the adaptation and implementation a generic operational reliability system for strategic installations to specific offshore installations. The object of study is the oil & gas technology, specifically equipment for oil pumping, gas compression and electric generation.
Such adaptation requires collecting information on failures, maintenance and operation, statistical analysis, calculation of keys performance indicators and general knowledge of asset management.
The purpose of this methodology is 1) to establish strategies for closing gaps and determining the necessary actions required to adequately implementing the system of operational reliability in the specific operational context, 2) prioritize the failures and operational impacts that generate deferred production, and 3) reduce operation and maintenance costs.
Términos generales: Contención, sustentabilidad, indicadores.
Palabras clave: Confiabilidad, gestión, desempeño, mejora operativa.
2. Introducción
El presente documento nos muestra aspectos generales sobre la adaptación y desarrollo de las acciones de un plan de mejora operativa para una instalación costa afuera. Esto tiene su origen en actividades específicas derivadas de la implementación de un sistema de confiabilidad operacional para instalaciones petroleras.
El objeto de estudio es la tecnología de estas instalaciones, específicamente los equipos de bombeo de aceite, compresión de gas y generación eléctrica, así como los equipos auxiliares/periféricos para su funcionamiento. Se requiere para ello la recopilación de información sobre fallas, mantenimiento y operación, análisis estadístico, cálculo indicador, claves de gestión, desempeño y confiabilidad y conocimientos generales de gestión de activos.
Esta metodología tiene el propósito de establecer estrategias para el cierre de brechas e implementar adecuadamente un sistema de confiabilidad operativa en un contexto dado, jerarquizar las fallas e impactos operativos que generan producción diferida, así como reducir las pérdidas y costos de operación y mantenimiento.
3. Desarrollo del plan de mejora operativa
El enfoque conceptual de desarrollo del plan de mejora operativa incluye la revisión de elementos específicos de los procesos de gestión de operación y mantenimiento, con contribución directa en los resultados de desempeño, condición dinámica actual de la turbo maquinaria y tablero de confiabilidad operacional resultante para cada tipo de equipo, como se ilustra en la figura 1.

El plan de mejora operativa genera un número de acciones específicas de contención y acciones de sustentabilidad, dirigidas a proponer una estrategia exitosa que maximice la efectividad, disminuyendo el número de fallas para obtener la confiabilidad operativa y mantenibilidad requerida, distribuidas como se presenta en la tabla 1.

La evaluación se realiza a través de los indicadores que se calcularán para los tipos de equipos y permitirá detectar desviaciones de los mismos, según su clasificación por área funcional.
3.1. Descripción de las fases del proceso para su documentación
Medir y evaluar indicadores de gestión, desempeño y confiabilidad: Analizar resultados de los indicadores correlacionarlos, jerarquizarlos y determinar los que requieren ser mejorados.
Evaluar y definir factores de desviación: Evaluar el desempeño operativo actual para identificar brechas de desempeño incluyendo la identificación de oportunidades de mejora con base al análisis estadístico de fallas, elaboración de Pareto y análisis de pérdidas de oportunidad.
Acciones específicas: proponer acciones específicas para corregir causas de las desviaciones y cerrar brechas de desempeño.
Correlacionar subelementos del sistema de confiabilidad operacional: Determinar el subelemento y herramientas necesarias que apoyarán la mejora de los factores identificados.
Priorizar acciones: Considerando el impacto en la instalación y la viabilidad de ejecución, se priorizarán las acciones a ejecutar.
Formalizar: Una vez priorizadas las acciones, se determinan responsables y fechas de cumplimiento. El mismo debe contar con evidencia documental.
Ejecutar acciones: Una vez formalizado, el documento debe difundirse, aplicarse y sus avances deben ser revisados periódicamente.
Revisión de la gestión.
3.2. Medición y cálculo de Indicadores
Posterior al cálculo y análisis de los indicadores de gestión, desempeño y confiabilidad se pretende detectar oportunidades de mejora para la turbo maquinaria de instalaciones costa afuera, en áreas funcionales como:
- Instalaciones y equipos.
- Planeación y programación.
- Operación segura.
- Mantenimiento preventivo y predictivo.
- Efectividad de programas de confiabilidad.
Las recomendaciones y conclusiones sobre la posición o valor de los indicadores del tablero (lo cual será un tema de otro artículo) se realizan a través de los análisis de predictivo realizados, los horómetros de la turbo maquinaria y la gestión del mantenimiento.
3.3. Evaluar y definir factores de desviación
Luego se identifican los factores a nivel de gente, procesos y tecnología que inciden en la desviación negativa de estos indicadores de acuerdo al análisis de información de las diferentes bases de datos utilizadas para el cálculo:
Los factores a evaluar son 12 y se describen a continuación:
•Suficiencia de competencias: Se valora si el personal demuestra ser competente para cumplir a cabalidad con las funciones de su puesto.
•Productividad del personal: Asumiendo que el personal sea suficiente y esté preparado con las competencias requeridas, se evalúan aspectos como nivel de compromiso, actitud, motivación y responsabilidad, por ello es necesario determinar todo el personal que requiera atención.
•Nivel de coordinación operativa: Se detecta el grado de coordinación, comunicación e integración entre operación y mantenimiento en diferentes ámbitos de competencia, para facilitar el logro de los objetivos y evitar afectaciones en el desempeño operativo de la instalación/ducto.
•Disponibilidad de recursos: Se evalúa la disponibilidad de recursos financieros, materiales y humanos requeridos para llevar a cabo la operación y el mantenimiento.
•Afectación por fallas recurrentes y eventos de alto impacto: Se evalúa la información de fallas de la instalación/ducto y mediante un análisis de Pareto se determina el 20% de los modos de falla de las familias de equipos principales, que representan el 80% del impacto económico en el último año (cantidad de veces que ocurre por el impacto económico cada vez que ocurre, considerando costos de operación, costos de mantenimiento y el valor de pérdidas).
•Disciplina Operativa: Se evalúa el nivel de desempeño de la disciplina operativa, es decir, el cumplimiento riguroso y continuo de todos los procedimientos e instrucciones de trabajo, tanto operativos, administrativos y de mantenimiento.
•Nivel de la planeación y programación: Se evalúa si la planeación y programación es suficiente para soportar los requerimientos de los procesos de operación y mantenimiento y cumplir con los planes y metas establecidos.
•Administración de cambios: Se evalúa la capacidad o cultura del personal en la identificación, documentación, comunicación y manejo de los cambios efectuados, tales como: modificaciones en el diseño o en el contexto o soluciones provisionales.
•Condiciones físicas de trabajo: A través de recorridos y observaciones se valora el ambiente físico bajo el cual realiza su trabajo el personal de operación y mantenimiento.
•Confiabilidad de datos: Se evalúa el nivel de utilización de las fuentes de gestión de la información, en el ámbito de competencia de cada usuario y la calidad de la información en el sistema.
•Estado de equipos: Se observan las condiciones físicas de los equipos de las instalaciones o ductos en términos de integridad y riesgo a través de inspecciones y observaciones en sitio.
•Capacidad de infraestructura productiva: Se miden casos de exceso o falta de equipos, derivado del diseño inicial y/o cambios en el contexto operacional.
3.4. Acciones específicas
• Las acciones de contención están dirigidas a reestructurar los procesos actuales de gestión de operación y mantenimiento en todas las fases de la cadena de valor ingeniería, planeación, programación y ejecución.
• Las acciones de sustentabilidad están dirigidas a sistematizar los procesos de gestión de operación y mantenimiento en todas las fases de la cadena de valor: ingeniería, planeación, programación y ejecución.
3.5. Correlacionar subelementos del sistema de confiabilidad
Los indicadores ya calculados se relacionarán con los siguientes factores para saber cuál de ellos afecta la desviación que puedan tener.
•Confiabilidad Humana: Evaluación de competencias y mecanismos de motivación al personal de la organización.
•Confiabilidad de Diseño: Análisis de costo de ciclo de vida, niveles de integridad de la seguridad, entre otros.
•Confiabilidad de proceso: Se toman en cuenta procesos de gestión de operación, así como buenas prácticas de operación, contextos operacionales actuales de las instalaciones y procedimientos operativos.
•Confiabilidad de equipos y ductos: Metodologías como: Análisis de causa raíz (ACR), mantenimiento centrado en confiabilidad (MCC), mantenimiento basado en condición (MBC).
•Proceso de mantenimiento: Buenas prácticas de mantenimiento, procesos de gestión del mantenimiento.
Cursos recomendados






%252FImagen%252FRAMPREDYC-1730060420837.webp%3Falt%3Dmedia%26token%3D2634a7f0-988e-4022-b91f-382503e6e9db&w=3840&q=75)

3.6. Priorización de listado de acciones a desarrollar
Para desarrollar la priorización de acciones generadas, es necesario valorar la viabilidad y el impacto operativo de cada una de estas, utilizando y construyendo la matriz de priorización. Para desarrollar la priorización de las acciones es necesario valorar la viabilidad de la implementación y el impacto. En la valoración se presentarán dos matrices, una para las acciones de contención y otra para las acciones de sustentabilidad, para ello se utiliza el esquema presentado en la figura 2.

3.7. Documentación para formalización del plan de mejora operativa
El plan de acciones específicas de contención y sustentabilidad para la mejora operativa debe contener la estrategia, plazo de ejecución, asignación de recursos y responsabilidades para alcanzar las metas propuestas a nivel instalación por tipo de equipos, en los indicadores de confiabilidad humana, confiabilidad de equipos, confiabilidad de diseño y confiabilidad de procesos físicos y de gestión en el corto, mediano y largo plazo. Es necesario desarrollar y documentar el plan de mejora conforme al modelo y elementos del sistema de gestión de activos propuestos en las especificaciones de la publicación PAS-55- 2:2008 del IAM-BSI, como se muestra en la figura 3.

3.8. Ejecución del plan de mejora operativa
Documentación de la implementación: Comprende la documentación de evidencias de implementación como parte del ciclo de mejora continua (ver figura 4). A través de la recopilación de información, se obtienen evidencias de cumplimiento y ejecución de las acciones emitidas y se realiza una medición de avances en la ejecución de acciones con una periodicidad constante; todo ello en un marco de entrevistas con las personas responsables de las acciones.

4. Evaluación de impactos del plan de mejora operativa y revisión de gestión
Comprende la actualización y análisis sistemático de los indicadores calculados (lo cual se debe de hacer de un modo periódico y continuo) tomando como base un análisis comparativo (antes y ahora) para la identificación de brechas, a partir de allí se hará una evaluación de acciones realizadas y no realizadas tanto con impacto en los indicadores como sin impacto en los indicadores.
Actualización de estrategias para el cierre de brechas: En este punto se revisará la vigencia de las acciones emitidas y se identificarán de acciones complementarias con la finalidad de dar continuidad a actividades propuestas anteriormente que tuvieron impacto positivo, generando así compromisos para formalizar el documento de acciones complementarias.
Informe de Revisión de Gestión: Se hace efectivo con la elaboración de un documento o reporte con una frecuencia acordada.
Comunicación de resultados: Se realiza a través de la divulgación del documento y de los resultados obtenidos a todas las personas que conforman el equipo de trabajo incluyendo a las máximas autoridades de la organización.
Todo lo comentado anteriormente lo podemos observar resumido en la figura 5.

5. Conclusiones
Esta metodología es de gran utilidad ya que nos permite, de un modo muy objetivo (siempre y cuando se cumplan los procedimientos para realizarla), establecer estrategias para el cierre de brechas y acciones necesarias que faciliten incrementar la confiabilidad de una instalación en un contexto operativo dado, lo cual nos permitirá jerarquizar las fallas e impactos operativos que generan producción diferida reduciendo así las pérdidas y costos, rompiendo los paradigmas preestablecidos por el personal de operación y mantenimiento.
Es importante indicar que durante el desarrollo de planes de mejora operativa se ha observado que, en el proceso de validación, los equipos de trabajo discriminan acciones de gran valor debido al esfuerzo que representa la ejecución de las mismas, siendo ellos los responsables de su ejecución. Al reconocer una falla en la gestión se podrían llegar a evidenciar algunas áreas de oportunidad en las competencias del personal conformado por el equipo de trabajo, proceso similar al de un juez que se juzga a sí mismo.
Finalmente, el plan de mejora operativa nos permitirá una gestión de operación y mantenimiento efectiva, así se podrá:
- Tomar decisiones más acertadas.
- Maximizar la efectividad de las acciones.
- Desarrollar actividades preventivas bajo un enfoque costo-efectivo.
6. Glosario de términos
A continuación, se listan las definiciones de los términos más importantes que se usaron a lo largo de este documento.
• Análisis Causa Raíz (ACR): Metodología usada para identificar factores causales de fallas, relacionados a gente, procesos y tecnología, con el objeto de resolver problemas.
•Análisis de desempeño: Pruebas de rendimiento en campo para la determinación del rendimiento térmico utilizado para diagnósticos y evaluaciones en la toma de decisiones de mantenimiento, optimización y dimensionamiento de la turbo maquinaria.
•Análisis del costo del ciclo de vida: Metodología que permite optimizar y maximizar la rentabilidad del proceso de producción a lo largo del ciclo de vida del activo, tomando en consideración acciones relacionadas con el mejoramiento de la confiabilidad y de la mantenibilidad de los activos (calidad del diseño, tecnología utilizada, complejidad técnica, frecuencia de fallas, manejo de inventarios, costos de mantenimiento preventivo/correctivo, costos operacionales, niveles de accesibilidad, etc.), así como el impacto sobre las posibles expectativas para extender la vida útil de los activos a costos razonables.
•Área funcional: Agrupamiento de indicadores dentro del Tablero de Confiabilidad Operacional en el cual se encuentran indicadores relacionados a un área común de atención de una instalación o de un Activo por medio de las cuales se establecen metas y objetivos.
•Ciclo de Deming: El ciclo de Deming (de Edwards Deming), también conocido como círculo PDCA (del inglés plan-do-check-act, esto es, planificar-hacer- verificar-actuar) o espiral de mejora continua, es una estrategia de mejora continua de la calidad en los cuatro pasos mencionados.
•Competencia: Conjunto de conocimientos y destrezas necesarios para el desempeño de las funciones en un puesto de trabajo.
•Confiabilidad: Se define como la probabilidad de operar sin fallas, cumpliendo la función requerida en un período determinado y bajo un contexto operacional establecido.
•Contexto operacional: Las circunstancias bajo las cuales se espera que opere un activo físico.
•Equipo de trabajo: Conjunto de personas que enfocan un esfuerzo, conocimientos, habilidades y destrezas al logro de un objetivo común, mediante la asignación de roles y responsabilidades que facilitan su funcionamiento.
•Falla de alto impacto o esporádicas: Son aquellas que ocurren ocasionalmente y se caracterizan por crear caos cuando aparecen, debido a su alto impacto en el negocio, seguridad o medio ambiente. Tienen ciertas características que son importantes: capturan la atención de todos, no ocurren con mucha frecuencia, cuestan mucho dinero, son altamente visibles y lleva tiempo para volver al estado normal.
•Falla potencial: Una condición identificable que indica que una falla funcional está a punto de ocurrir o está en proceso de ocurrir.
•Fallas recurrentes: Son fallas repetitivas o crónicas. En ocasiones resultan de bajo impacto, por lo que su efecto acumulado es desapercibido por los que operan o mantienen la instalación.
•Indicador: Es un parámetro numérico que mide el desempeño utilizando un factor crítico identificado en las personas, la organización o en los procesos respecto a los objetivos y las metas del negocio.
•Jerarquización: Ordenamiento de acuerdo a su Prioridad.
•Mantenibilidad: Se define como la probabilidad de que un componente o sistema en falla sea restaurado o reparado a una condición operativa específica en un periodo de tiempo establecido, cuando el mantenimiento es desempeñado de acuerdo con los procedimientos establecidos y se cuenta con los recursos apropiados. Es una función determinística que identifica la facilidad con la cual una actividad de mantenimiento puede ser ejecutada en un equipo, el tiempo promedio para reparar (MTTR) es un indicativo de la mantenibilidad y está en función del diseño y la tarea a efectuar, considerando siempre el uso adecuado de recursos.
•Mantenimiento centrado en confiabilidad (MCC): Es un proceso analítico y sistemático basado en el entendimiento de la función de los sistemas y las fallas funcionales.
•Mantenimiento basado en condición (MBC): Es un proceso analítico y sistemático basado en el entendimiento y la monitorización de las condiciones o estado de los diferentes elementos de un equipo para decidir el momento óptimo (más adecuado) para realizar las tareas de mantenimiento.
7. Referencias
- [1]. British Standard Institute PAS 55:2008 Gestión de Activos Parte 1, ISBN: 978-0-9563934-0-1.
- [2]. British Standard Institute PAS 55:2008 Gestión de Activos Parte 2, ISBN: 978-0-9563934-2-5.
- [3]. Deming W., Edwards. (1989)” Calidad, Productividad y Competitividad: La salida de la crisis”, Ediciones Díaz de Santos, Madrid.
- [4]. Dounce V., Enrique. (2007) “La productividad en el Mantenimiento Industrial”. Décima reimpresión. México.
- [5]. Duke, Okes (2009). “Root Cause Analysis; The Core of Problem Solving and Corrective Action”. American Society for Quality, Quality Press, Milwaukee.
- [6]. Gaither, Norman y Frazier, Grey. (2000) “Administración de Producción y Operaciones”. Cuarta Edición. Editorial Thomson. México.
- [7]. Guía Técnica para el Cálculo de Indicadores de Confiabilidad Operacional en Petróleos Mexicanos y Organismos Subsidiarios Clave DCO-SCM-GT-012.
- [8]. Guía Técnica para el Cálculo de Indicadores de Desempeño y Gestión de Mantenimiento en Pemex Exploración y Producción, Clave GG-NO-OP-0001- 2011.
- [9]. Jimeno Bernal, Jorge (2013), «Ciclo PDCA» recuperado de: http://www.pdcahome.com/5202/ciclo- pdca.
- [10]. Manual Técnico de Confiabilidad Operacional en Petróleos Mexicanos y Organismos Subsidiarios, Clave: 800-16700-DCO-SCM-MT-001.
- [11]. Manual del Sistema de Confiabilidad Operacional en Pemex Exploración y Producción, Versión 3.
- [12]. Manual CG-IE-MA-0001-2008 Criterios técnicos para clasificar los tipos de mantenimiento predictivo, preventivo y correctivo en Pemex Exploración y Producción.
- [13]. Manual de Taxonomía de equipos de Petróleos Mexicanos y Organismos Subsidiarios. Clave: 800- 16700-M-01 (última) y Clave: DCO-SCM-XP-000 (anterior).
- [14]. Muñiz, José (1998). “Fiabilidad. Teoría clásica de los Tests”. Editorial Pirámide. 5ª Edición. Madrid.
- [15]. Norma ISO 14224-2006 Petroleum and Natural Industries-Collection and Exchange of reliability and maintenance data for equipment.
- [16]. Iresson (1990). “Reliability Handbook”. Editorial John Wiley & Sons, New York.
- [17]. Delgado M., Miriam. (2009)” Sistema de Administración del Mantenimiento”. Gobierno del Estado de México. México.
- [18]. Tavares, Lourival. “Administración Moderna del Mantenimiento”. Editorial Novo Polo Publicaçoes. Brasil.
8. Anexos


Autor: MI. Remigio D. Sena Mesa
Correo: remigiosena@hotmail.com
Dinos qué te ha parecido el artículo
Artículos recomendados
Disminución de los costos por hora en neumáticos de camiones mineros

Investigación de Fallas, Reparación y Remedio Operativo Mínimo. Bomba de Alto Rendimiento

Gestión de Integridad de Activos para Infraestructuras basado en Fiabilidad e Inteligencia Artificial

Entrevista con Chris Struve

Publica tu artículo en la revista #1 de Mantenimiento Industrial
Publicar un artículo en la revista es gratis, no tiene costo.
Solo debes asegurarte que no sea un artículo comercial.
¿Qué esperas?
O envía tu artículo directo: articulos@predictiva21.com
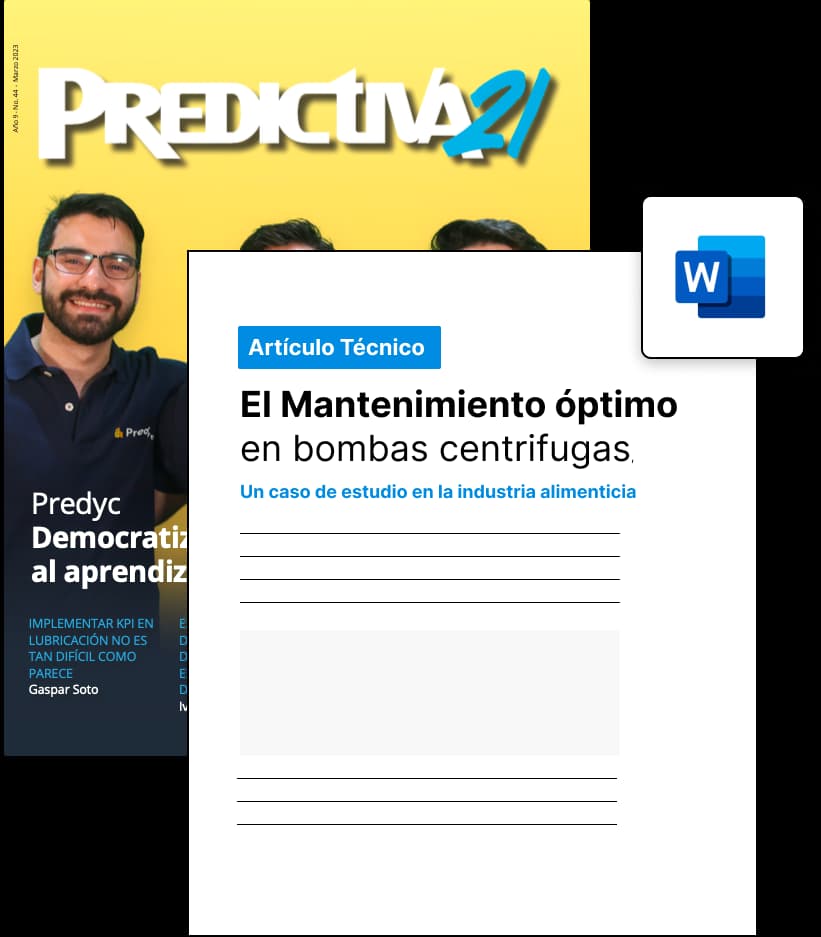
El Plan de Mejora Operativa como Metodología para detectar Áreas de Oportunidad en la Turbo Maquinaria de instalaciones Costa Afuera
Articulo 15 de junio de 20201. Abstract
This document describes methodological aspects of the adaptation and implementation a generic operational reliability system for strategic installations to specific offshore installations. The object of study is the oil & gas technology, specifically equipment for oil pumping, gas compression and electric generation.
Such adaptation requires collecting information on failures, maintenance and operation, statistical analysis, calculation of keys performance indicators and general knowledge of asset management.
The purpose of this methodology is 1) to establish strategies for closing gaps and determining the necessary actions required to adequately implementing the system of operational reliability in the specific operational context, 2) prioritize the failures and operational impacts that generate deferred production, and 3) reduce operation and maintenance costs.
Términos generales: Contención, sustentabilidad, indicadores.
Palabras clave: Confiabilidad, gestión, desempeño, mejora operativa.
2. Introducción
El presente documento nos muestra aspectos generales sobre la adaptación y desarrollo de las acciones de un plan de mejora operativa para una instalación costa afuera. Esto tiene su origen en actividades específicas derivadas de la implementación de un sistema de confiabilidad operacional para instalaciones petroleras.
El objeto de estudio es la tecnología de estas instalaciones, específicamente los equipos de bombeo de aceite, compresión de gas y generación eléctrica, así como los equipos auxiliares/periféricos para su funcionamiento. Se requiere para ello la recopilación de información sobre fallas, mantenimiento y operación, análisis estadístico, cálculo indicador, claves de gestión, desempeño y confiabilidad y conocimientos generales de gestión de activos.
Esta metodología tiene el propósito de establecer estrategias para el cierre de brechas e implementar adecuadamente un sistema de confiabilidad operativa en un contexto dado, jerarquizar las fallas e impactos operativos que generan producción diferida, así como reducir las pérdidas y costos de operación y mantenimiento.
3. Desarrollo del plan de mejora operativa
El enfoque conceptual de desarrollo del plan de mejora operativa incluye la revisión de elementos específicos de los procesos de gestión de operación y mantenimiento, con contribución directa en los resultados de desempeño, condición dinámica actual de la turbo maquinaria y tablero de confiabilidad operacional resultante para cada tipo de equipo, como se ilustra en la figura 1.

El plan de mejora operativa genera un número de acciones específicas de contención y acciones de sustentabilidad, dirigidas a proponer una estrategia exitosa que maximice la efectividad, disminuyendo el número de fallas para obtener la confiabilidad operativa y mantenibilidad requerida, distribuidas como se presenta en la tabla 1.

La evaluación se realiza a través de los indicadores que se calcularán para los tipos de equipos y permitirá detectar desviaciones de los mismos, según su clasificación por área funcional.
3.1. Descripción de las fases del proceso para su documentación
Medir y evaluar indicadores de gestión, desempeño y confiabilidad: Analizar resultados de los indicadores correlacionarlos, jerarquizarlos y determinar los que requieren ser mejorados.
Evaluar y definir factores de desviación: Evaluar el desempeño operativo actual para identificar brechas de desempeño incluyendo la identificación de oportunidades de mejora con base al análisis estadístico de fallas, elaboración de Pareto y análisis de pérdidas de oportunidad.
Acciones específicas: proponer acciones específicas para corregir causas de las desviaciones y cerrar brechas de desempeño.
Correlacionar subelementos del sistema de confiabilidad operacional: Determinar el subelemento y herramientas necesarias que apoyarán la mejora de los factores identificados.
Priorizar acciones: Considerando el impacto en la instalación y la viabilidad de ejecución, se priorizarán las acciones a ejecutar.
Formalizar: Una vez priorizadas las acciones, se determinan responsables y fechas de cumplimiento. El mismo debe contar con evidencia documental.
Ejecutar acciones: Una vez formalizado, el documento debe difundirse, aplicarse y sus avances deben ser revisados periódicamente.
Revisión de la gestión.
3.2. Medición y cálculo de Indicadores
Posterior al cálculo y análisis de los indicadores de gestión, desempeño y confiabilidad se pretende detectar oportunidades de mejora para la turbo maquinaria de instalaciones costa afuera, en áreas funcionales como:
- Instalaciones y equipos.
- Planeación y programación.
- Operación segura.
- Mantenimiento preventivo y predictivo.
- Efectividad de programas de confiabilidad.
Las recomendaciones y conclusiones sobre la posición o valor de los indicadores del tablero (lo cual será un tema de otro artículo) se realizan a través de los análisis de predictivo realizados, los horómetros de la turbo maquinaria y la gestión del mantenimiento.
3.3. Evaluar y definir factores de desviación
Luego se identifican los factores a nivel de gente, procesos y tecnología que inciden en la desviación negativa de estos indicadores de acuerdo al análisis de información de las diferentes bases de datos utilizadas para el cálculo:
Los factores a evaluar son 12 y se describen a continuación:
•Suficiencia de competencias: Se valora si el personal demuestra ser competente para cumplir a cabalidad con las funciones de su puesto.
•Productividad del personal: Asumiendo que el personal sea suficiente y esté preparado con las competencias requeridas, se evalúan aspectos como nivel de compromiso, actitud, motivación y responsabilidad, por ello es necesario determinar todo el personal que requiera atención.
•Nivel de coordinación operativa: Se detecta el grado de coordinación, comunicación e integración entre operación y mantenimiento en diferentes ámbitos de competencia, para facilitar el logro de los objetivos y evitar afectaciones en el desempeño operativo de la instalación/ducto.
•Disponibilidad de recursos: Se evalúa la disponibilidad de recursos financieros, materiales y humanos requeridos para llevar a cabo la operación y el mantenimiento.
•Afectación por fallas recurrentes y eventos de alto impacto: Se evalúa la información de fallas de la instalación/ducto y mediante un análisis de Pareto se determina el 20% de los modos de falla de las familias de equipos principales, que representan el 80% del impacto económico en el último año (cantidad de veces que ocurre por el impacto económico cada vez que ocurre, considerando costos de operación, costos de mantenimiento y el valor de pérdidas).
•Disciplina Operativa: Se evalúa el nivel de desempeño de la disciplina operativa, es decir, el cumplimiento riguroso y continuo de todos los procedimientos e instrucciones de trabajo, tanto operativos, administrativos y de mantenimiento.
•Nivel de la planeación y programación: Se evalúa si la planeación y programación es suficiente para soportar los requerimientos de los procesos de operación y mantenimiento y cumplir con los planes y metas establecidos.
•Administración de cambios: Se evalúa la capacidad o cultura del personal en la identificación, documentación, comunicación y manejo de los cambios efectuados, tales como: modificaciones en el diseño o en el contexto o soluciones provisionales.
•Condiciones físicas de trabajo: A través de recorridos y observaciones se valora el ambiente físico bajo el cual realiza su trabajo el personal de operación y mantenimiento.
•Confiabilidad de datos: Se evalúa el nivel de utilización de las fuentes de gestión de la información, en el ámbito de competencia de cada usuario y la calidad de la información en el sistema.
•Estado de equipos: Se observan las condiciones físicas de los equipos de las instalaciones o ductos en términos de integridad y riesgo a través de inspecciones y observaciones en sitio.
•Capacidad de infraestructura productiva: Se miden casos de exceso o falta de equipos, derivado del diseño inicial y/o cambios en el contexto operacional.
3.4. Acciones específicas
• Las acciones de contención están dirigidas a reestructurar los procesos actuales de gestión de operación y mantenimiento en todas las fases de la cadena de valor ingeniería, planeación, programación y ejecución.
• Las acciones de sustentabilidad están dirigidas a sistematizar los procesos de gestión de operación y mantenimiento en todas las fases de la cadena de valor: ingeniería, planeación, programación y ejecución.
3.5. Correlacionar subelementos del sistema de confiabilidad
Los indicadores ya calculados se relacionarán con los siguientes factores para saber cuál de ellos afecta la desviación que puedan tener.
•Confiabilidad Humana: Evaluación de competencias y mecanismos de motivación al personal de la organización.
•Confiabilidad de Diseño: Análisis de costo de ciclo de vida, niveles de integridad de la seguridad, entre otros.
•Confiabilidad de proceso: Se toman en cuenta procesos de gestión de operación, así como buenas prácticas de operación, contextos operacionales actuales de las instalaciones y procedimientos operativos.
•Confiabilidad de equipos y ductos: Metodologías como: Análisis de causa raíz (ACR), mantenimiento centrado en confiabilidad (MCC), mantenimiento basado en condición (MBC).
•Proceso de mantenimiento: Buenas prácticas de mantenimiento, procesos de gestión del mantenimiento.
Cursos recomendados






%252FImagen%252FRAMPREDYC-1730060420837.webp%3Falt%3Dmedia%26token%3D2634a7f0-988e-4022-b91f-382503e6e9db&w=3840&q=75)

3.6. Priorización de listado de acciones a desarrollar
Para desarrollar la priorización de acciones generadas, es necesario valorar la viabilidad y el impacto operativo de cada una de estas, utilizando y construyendo la matriz de priorización. Para desarrollar la priorización de las acciones es necesario valorar la viabilidad de la implementación y el impacto. En la valoración se presentarán dos matrices, una para las acciones de contención y otra para las acciones de sustentabilidad, para ello se utiliza el esquema presentado en la figura 2.

3.7. Documentación para formalización del plan de mejora operativa
El plan de acciones específicas de contención y sustentabilidad para la mejora operativa debe contener la estrategia, plazo de ejecución, asignación de recursos y responsabilidades para alcanzar las metas propuestas a nivel instalación por tipo de equipos, en los indicadores de confiabilidad humana, confiabilidad de equipos, confiabilidad de diseño y confiabilidad de procesos físicos y de gestión en el corto, mediano y largo plazo. Es necesario desarrollar y documentar el plan de mejora conforme al modelo y elementos del sistema de gestión de activos propuestos en las especificaciones de la publicación PAS-55- 2:2008 del IAM-BSI, como se muestra en la figura 3.

3.8. Ejecución del plan de mejora operativa
Documentación de la implementación: Comprende la documentación de evidencias de implementación como parte del ciclo de mejora continua (ver figura 4). A través de la recopilación de información, se obtienen evidencias de cumplimiento y ejecución de las acciones emitidas y se realiza una medición de avances en la ejecución de acciones con una periodicidad constante; todo ello en un marco de entrevistas con las personas responsables de las acciones.

4. Evaluación de impactos del plan de mejora operativa y revisión de gestión
Comprende la actualización y análisis sistemático de los indicadores calculados (lo cual se debe de hacer de un modo periódico y continuo) tomando como base un análisis comparativo (antes y ahora) para la identificación de brechas, a partir de allí se hará una evaluación de acciones realizadas y no realizadas tanto con impacto en los indicadores como sin impacto en los indicadores.
Actualización de estrategias para el cierre de brechas: En este punto se revisará la vigencia de las acciones emitidas y se identificarán de acciones complementarias con la finalidad de dar continuidad a actividades propuestas anteriormente que tuvieron impacto positivo, generando así compromisos para formalizar el documento de acciones complementarias.
Informe de Revisión de Gestión: Se hace efectivo con la elaboración de un documento o reporte con una frecuencia acordada.
Comunicación de resultados: Se realiza a través de la divulgación del documento y de los resultados obtenidos a todas las personas que conforman el equipo de trabajo incluyendo a las máximas autoridades de la organización.
Todo lo comentado anteriormente lo podemos observar resumido en la figura 5.

5. Conclusiones
Esta metodología es de gran utilidad ya que nos permite, de un modo muy objetivo (siempre y cuando se cumplan los procedimientos para realizarla), establecer estrategias para el cierre de brechas y acciones necesarias que faciliten incrementar la confiabilidad de una instalación en un contexto operativo dado, lo cual nos permitirá jerarquizar las fallas e impactos operativos que generan producción diferida reduciendo así las pérdidas y costos, rompiendo los paradigmas preestablecidos por el personal de operación y mantenimiento.
Es importante indicar que durante el desarrollo de planes de mejora operativa se ha observado que, en el proceso de validación, los equipos de trabajo discriminan acciones de gran valor debido al esfuerzo que representa la ejecución de las mismas, siendo ellos los responsables de su ejecución. Al reconocer una falla en la gestión se podrían llegar a evidenciar algunas áreas de oportunidad en las competencias del personal conformado por el equipo de trabajo, proceso similar al de un juez que se juzga a sí mismo.
Finalmente, el plan de mejora operativa nos permitirá una gestión de operación y mantenimiento efectiva, así se podrá:
- Tomar decisiones más acertadas.
- Maximizar la efectividad de las acciones.
- Desarrollar actividades preventivas bajo un enfoque costo-efectivo.
6. Glosario de términos
A continuación, se listan las definiciones de los términos más importantes que se usaron a lo largo de este documento.
• Análisis Causa Raíz (ACR): Metodología usada para identificar factores causales de fallas, relacionados a gente, procesos y tecnología, con el objeto de resolver problemas.
•Análisis de desempeño: Pruebas de rendimiento en campo para la determinación del rendimiento térmico utilizado para diagnósticos y evaluaciones en la toma de decisiones de mantenimiento, optimización y dimensionamiento de la turbo maquinaria.
•Análisis del costo del ciclo de vida: Metodología que permite optimizar y maximizar la rentabilidad del proceso de producción a lo largo del ciclo de vida del activo, tomando en consideración acciones relacionadas con el mejoramiento de la confiabilidad y de la mantenibilidad de los activos (calidad del diseño, tecnología utilizada, complejidad técnica, frecuencia de fallas, manejo de inventarios, costos de mantenimiento preventivo/correctivo, costos operacionales, niveles de accesibilidad, etc.), así como el impacto sobre las posibles expectativas para extender la vida útil de los activos a costos razonables.
•Área funcional: Agrupamiento de indicadores dentro del Tablero de Confiabilidad Operacional en el cual se encuentran indicadores relacionados a un área común de atención de una instalación o de un Activo por medio de las cuales se establecen metas y objetivos.
•Ciclo de Deming: El ciclo de Deming (de Edwards Deming), también conocido como círculo PDCA (del inglés plan-do-check-act, esto es, planificar-hacer- verificar-actuar) o espiral de mejora continua, es una estrategia de mejora continua de la calidad en los cuatro pasos mencionados.
•Competencia: Conjunto de conocimientos y destrezas necesarios para el desempeño de las funciones en un puesto de trabajo.
•Confiabilidad: Se define como la probabilidad de operar sin fallas, cumpliendo la función requerida en un período determinado y bajo un contexto operacional establecido.
•Contexto operacional: Las circunstancias bajo las cuales se espera que opere un activo físico.
•Equipo de trabajo: Conjunto de personas que enfocan un esfuerzo, conocimientos, habilidades y destrezas al logro de un objetivo común, mediante la asignación de roles y responsabilidades que facilitan su funcionamiento.
•Falla de alto impacto o esporádicas: Son aquellas que ocurren ocasionalmente y se caracterizan por crear caos cuando aparecen, debido a su alto impacto en el negocio, seguridad o medio ambiente. Tienen ciertas características que son importantes: capturan la atención de todos, no ocurren con mucha frecuencia, cuestan mucho dinero, son altamente visibles y lleva tiempo para volver al estado normal.
•Falla potencial: Una condición identificable que indica que una falla funcional está a punto de ocurrir o está en proceso de ocurrir.
•Fallas recurrentes: Son fallas repetitivas o crónicas. En ocasiones resultan de bajo impacto, por lo que su efecto acumulado es desapercibido por los que operan o mantienen la instalación.
•Indicador: Es un parámetro numérico que mide el desempeño utilizando un factor crítico identificado en las personas, la organización o en los procesos respecto a los objetivos y las metas del negocio.
•Jerarquización: Ordenamiento de acuerdo a su Prioridad.
•Mantenibilidad: Se define como la probabilidad de que un componente o sistema en falla sea restaurado o reparado a una condición operativa específica en un periodo de tiempo establecido, cuando el mantenimiento es desempeñado de acuerdo con los procedimientos establecidos y se cuenta con los recursos apropiados. Es una función determinística que identifica la facilidad con la cual una actividad de mantenimiento puede ser ejecutada en un equipo, el tiempo promedio para reparar (MTTR) es un indicativo de la mantenibilidad y está en función del diseño y la tarea a efectuar, considerando siempre el uso adecuado de recursos.
•Mantenimiento centrado en confiabilidad (MCC): Es un proceso analítico y sistemático basado en el entendimiento de la función de los sistemas y las fallas funcionales.
•Mantenimiento basado en condición (MBC): Es un proceso analítico y sistemático basado en el entendimiento y la monitorización de las condiciones o estado de los diferentes elementos de un equipo para decidir el momento óptimo (más adecuado) para realizar las tareas de mantenimiento.
7. Referencias
- [1]. British Standard Institute PAS 55:2008 Gestión de Activos Parte 1, ISBN: 978-0-9563934-0-1.
- [2]. British Standard Institute PAS 55:2008 Gestión de Activos Parte 2, ISBN: 978-0-9563934-2-5.
- [3]. Deming W., Edwards. (1989)” Calidad, Productividad y Competitividad: La salida de la crisis”, Ediciones Díaz de Santos, Madrid.
- [4]. Dounce V., Enrique. (2007) “La productividad en el Mantenimiento Industrial”. Décima reimpresión. México.
- [5]. Duke, Okes (2009). “Root Cause Analysis; The Core of Problem Solving and Corrective Action”. American Society for Quality, Quality Press, Milwaukee.
- [6]. Gaither, Norman y Frazier, Grey. (2000) “Administración de Producción y Operaciones”. Cuarta Edición. Editorial Thomson. México.
- [7]. Guía Técnica para el Cálculo de Indicadores de Confiabilidad Operacional en Petróleos Mexicanos y Organismos Subsidiarios Clave DCO-SCM-GT-012.
- [8]. Guía Técnica para el Cálculo de Indicadores de Desempeño y Gestión de Mantenimiento en Pemex Exploración y Producción, Clave GG-NO-OP-0001- 2011.
- [9]. Jimeno Bernal, Jorge (2013), «Ciclo PDCA» recuperado de: http://www.pdcahome.com/5202/ciclo- pdca.
- [10]. Manual Técnico de Confiabilidad Operacional en Petróleos Mexicanos y Organismos Subsidiarios, Clave: 800-16700-DCO-SCM-MT-001.
- [11]. Manual del Sistema de Confiabilidad Operacional en Pemex Exploración y Producción, Versión 3.
- [12]. Manual CG-IE-MA-0001-2008 Criterios técnicos para clasificar los tipos de mantenimiento predictivo, preventivo y correctivo en Pemex Exploración y Producción.
- [13]. Manual de Taxonomía de equipos de Petróleos Mexicanos y Organismos Subsidiarios. Clave: 800- 16700-M-01 (última) y Clave: DCO-SCM-XP-000 (anterior).
- [14]. Muñiz, José (1998). “Fiabilidad. Teoría clásica de los Tests”. Editorial Pirámide. 5ª Edición. Madrid.
- [15]. Norma ISO 14224-2006 Petroleum and Natural Industries-Collection and Exchange of reliability and maintenance data for equipment.
- [16]. Iresson (1990). “Reliability Handbook”. Editorial John Wiley & Sons, New York.
- [17]. Delgado M., Miriam. (2009)” Sistema de Administración del Mantenimiento”. Gobierno del Estado de México. México.
- [18]. Tavares, Lourival. “Administración Moderna del Mantenimiento”. Editorial Novo Polo Publicaçoes. Brasil.
8. Anexos


Autor: MI. Remigio D. Sena Mesa
Correo: remigiosena@hotmail.com
Dinos qué te ha parecido el artículo
Artículos recomendados
Congreso de Mantenimiento y Confiabilidad Latinoamérica (Perú 2019)

Vibraciones Mecánicas

Diplomado en gestión de activos y mantenimiento

Confiabilidad en el Talento Humano para Organizaciones Exitosas

Publica tu artículo en la revista #1 de Mantenimiento Industrial
Publicar un artículo en la revista es gratis, no tiene costo.
Solo debes asegurarte que no sea un artículo comercial.
¿Qué esperas?
O envía tu artículo directo: articulos@predictiva21.com
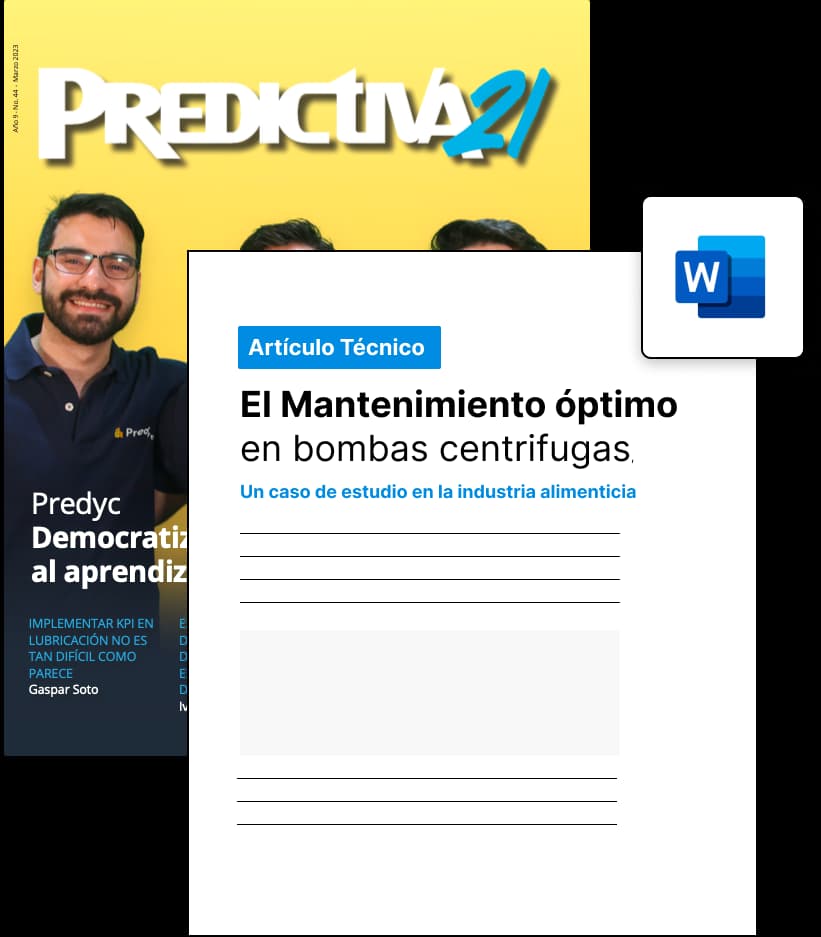