Transformando el Monitoreo de Turbomáquinas, nuevas perspectivas desde la Gestión de Activos
Articulo15 de febrero de 2024
En este artículo se invita a una discusión en relación a la estrategia que históricamente se ha usado para el monitoreo de turbomáquinas y como la toma de decisiones en la gestión de este tipo de activos nos invita a replantear aspectos claves en la búsqueda de disminuir la incertidumbre en estos activos, desde su concepción hasta su desincorporación, a partir de la generación de información basada en la captura de datos mediante diferentes técnicas de monitoreo y diagnóstico.
Antes debemos analizar donde radica la criticidad de este tipo de activos y hay 2 factores fundamentales, el primero el impacto sobre la calidad de vida del ser humano y el desarrollo de la sociedad, ya que este tipo de máquinas son muy usadas para la generación de energía eléctrica, como mecanismo de propulsión y para trasegar fluidos, el segundo su costo elevado en sus cuatro etapas del ciclo de vida: adquisición, montaje y comisionamiento, mantenimiento y operación, renovación o disposición.
Los casos prácticos que serán citados en este espacio se enfocan en aplicaciones para la generación de energía eléctrica, ya que en las últimas dos décadas se ha presentado un aumento de más del 100% en la generación mundial, figura 1, en donde un porcentaje importante de la generación proviene de fuentes que involucran turbomáquinas en su proceso, figura 2.

Figura 1. Tendencia de la generación mundial durante 1990 - 2021 – GWh. Tomado IEA data1

Figura 2. Tendencia de la distribución de la generación mundial durante 1990 - 2021 – GWh. Tomado IEA data1
Volviendo a la historia del monitoreo de las turbomáquinas, debemos ir al año 1965 cuando se implementó por primera vez de manera exitosa la tecnología de corrientes de Eddy en sensores de desplazamiento sin contacto, los cuales están diseñados para medir distancias diminutas, entre la punta del sensor y una superficie conductora, como un eje rotativo, que permite cuantificar desplazamientos sumamente pequeños, generalmente del orden de unos pocos micrones.
Este hecho genera un gran impacto, ya que permite a las industrias con turbomáquinas implementar sensores para medir de manera directa el desplazamiento del eje, el cual suele ser el componente hacia donde se transmiten las cargas dinámicas producto de la operación; y de medirse solo la vibración en carcasa, se perdería información relevante, ya que al ser máquinas que usualmente trabajan con cojinetes hidrodinámicos, las características de la película de lubricación amortiguan y no transmiten de manera adecuada la vibración del eje a la carcasa. Como resultado, se establece la medición con sensores de proximidad como un método más preciso para determinar el estado de este tipo de máquinas e inicia la era de los sistemas de protección.
En 1970, el American Petroleum Institute definió la sonda de proximidad como el dispositivo de medición para evaluar la vibración aceptable del eje y en 1976 publicó la primera versión del estándar API 670 - Machinery Protection Systems, como una guía para el diseño, instalación, configuración y mantenimiento de sistemas de protección de maquinaria utilizados en la industria.

Figura 3. Sonda de proximidad
En definitiva, el desarrollo para la medición de la vibración del eje, utilizando sondas de proximidad, se convirtió en el estándar de la industria para las pruebas de aceptación de turbo maquinaria y su protección en etapa de operación, consolidando este método como el idóneo para evaluar la vibración y la condición mecánica general en maquinaria rotativa crítica como turbinas, compresores, bombas, motores eléctricos, generadores y otros equipos rotativos2.
Sin embargo, en las últimas décadas este se ha convertido casi en el único método aplicado en turbo maquinaria para determinar su condición y solo las organizaciones con un mayor nivel de madurez en la gestión de activos, involucran elementos claves como medición de vibración sobre carcasa, herramientas de diagnóstico especiales como son los estudios de análisis rotodinámico y de Operational Deflection Shape (ODS); así como la integración de variables de proceso.
La experiencia nos ha mostrado que cuando la estrategia de monitoreo solo está basada en sistemas de medición y protección por sondas de proximidad, se vuelve insuficiente para una gestión de activos idónea, ya que desde la concepción del proyecto no se involucran aspectos relevantes que luego serán claves en la puesta en marcha, operación y mantenimiento, impactando en la confiabilidad, los costos, la gestión del inventario de repuestos y el nivel de incertidumbre en la toma de decisiones, por eso enunciaremos 3 casos que nos ayudarán a comprender lo expuesto.
Turbogenerador de condensación de 62 mw con eventos repetitivos de inestabilidad dinámica no determinística - Caso 1
Este caso se trata de un turbogenerador cuya dificultad radicaba en la ocurrencia de eventos, aparentemente aleatorios, en los que había incrementos de vibración hasta niveles de alarma del sistema de protección; que luego disminuían y se regresaba a una relativa estabilidad operativa sin que hubiese una causa aparente. El personal de operación sostenía que tales eventos eran más probables ante cambios de carga; pero que ello no era determinístico.

Ante tal panorama, se plantearon pruebas diagnóstico apuntando a identificar la causa de los eventos y en general a describir la condición de salud de la máquina a partir de sus señales de vibración. Esto, con el objetivo de dar luces para una asertiva planeación, programación y ejecución de las intervenciones de mantenimiento mayor que se tenían previstas para dentro de 4 meses. En ese sentido, se adquirieron señales de vibración relativa de los proximitores del sistema de protección, durante reducción de carga, parada y arranque de la turbina, la sincronización y el incremento de carga a su valor nominal.

A partir del análisis de órbitas, formas de onda y firmas espectrales, se logró identificar un fenómeno de remolino de aceite (Oil whirl), que en este caso consistía en inestabilidad de la película lubricante que soporta la rotación del eje dentro de los cojinetes, atribuido a altas holguras radiales como producto de desgaste. Así, ante cambios de carga o alguna variación en las fuerzas operativas, la película hidrodinámica de aceite en ciertos casos no lograba mantener su estabilidad y se generaban desplazamientos erráticos del eje, que eran registrados como altas vibraciones. Luego, una vez la película lograba estabilizarse, se reducían las vibraciones a niveles normales de operación. A partir de esta conclusión, se recomendó al personal operador establecer la práctica de solo realizar variaciones suaves cuando se requiriera cambiar carga de generación para gestionar el riesgo y mantener la máquina operativa hasta el mantenimiento mayor. Por otro lado, también lograron gestionar la adquisición oportuna de repuestos y realizar una correcta planificación de la intervención de cambio de cojinetes; de manera que se optimizaron tiempos de ejecución, la máquina regresó a generación en el tiempo planeado y con una operación con mayor confiabilidad.

Este caso pone en evidencia que el enfoque de registro de amplitudes de vibraciones a través del sistema de protección, es insuficiente a la hora de brindar información valiosa para la adecuada gestión de la operación y la toma de decisiones asertivas de mantenimiento, que busquen la operación confiable y segura de la turbomaquinaria.
Turbogenerador de extracción de 46 mw con dos eventos recientes de falla en álabes-Caso 2
Este caso obedece a una turbina de vapor de cogeneración de un Ingenio azucarero, cuya situación problema obedece la ocurrencia de fallas por desprendimiento de álabe en una de las ruedas de la turbina. Con estas fallas, no solo se generaron indisponibilidades, con las implicaciones técnicas y económicas que ello contrae, sino que también se hizo evidente la nula efectividad del sistema de protección por vibraciones ante este tipo de fallas. Toda vez que previo la ocurrencia, no se registró ningún tipo de señal de alerta; e incluso, solo unos segundos después del desprendimiento del álabe, se alcanzó el disparo por vibraciones debido al efecto de desbalance.


Posterior a la reparación del primer evento de falla, se acompañó el arranque de la máquina con un análisis integral de vibraciones, que incluyó vibraciones relativas desde los proximitores del sistema de protección y vibraciones absolutas registradas a través de acelerómetros instalados temporalmente sobre carcasa de los cojinetes. Esto, con el objetivo de tener una mirada amplia sobre la condición de la máquina, que incluyera las vibraciones en bajas y medias frecuencias en las variables desplazamiento y velocidad; y vibraciones en alta frecuencia en la variable aceleración. En la medición se identificó una excitación espectral de alta frecuencia del pico de 95 veces la frecuencia rotacional (95X), que corresponde a la frecuencia de paso de álabes (BPF) de una rueda de la turbina; su amplitud en ese momento era de 1.5 G’s-rms. Ante ello, se reportó a personal a cargo sobre posible irregularidad del flujo de vapor a través de los álabes; y se recomendó monitoreo.
Con lo anterior, la máquina continuó la operación durante alrededor de 10 meses, cuando se realizó un nuevo análisis de vibraciones. En este se identificó que persistía la excitación de alta frecuencia, con incremento significativo en su amplitud, del orden del 193%, alcanzando niveles de 4.4 G’s-rms. Esa vez se generó una alerta al personal a cargo, sobre el incremento en el riesgo que significaba este importante cambio en las vibraciones de alta frecuencia. El operador de la máquina transfirió esta inquietud al fabricante, sin hubiese una respuesta de alarma o que indicase la necesidad de alguna intervención. Alrededor de dos meses después de generada la alarma, se presentó un nuevo evento de desprendimiento de álabe, con la misma secuencia de eventos presenciada en la primera falla.
Posterior a la reparación, se hizo un nuevo acompañamiento en el arranque; en el cual, se identificó que se mantenía la presencia del pico de frecuencia de paso de álabes con una amplitud que se había reducido en un 75%, alcanzando 1.1 G’s-rms. Lo anterior plantea que existiría una relación directa entre la amplitud de este pico, con la degradación de la condición de integridad y el riesgo de falla en los álabes. Este caso evidencia que para protección ante eventos potenciales de falla o que comprometan la integridad en turbomáquinas, las vibraciones relativas no son suficientes, como señales que generen una alarma o detonen una parada de protección. Además, su registros no generan información suficiente, al momento de construir diagnósticos predictivos y/o un eventual análisis de causa-raíz.
Así, este caso presenta solo un ejemplo de todos los que pudiese haber, en donde la integración entre vibraciones absolutas con relativas son un requisito para el diagnóstico oportuno de patologías de falla y una mejora sustancial del esquema de protección de la turbomaquinaria.
Turbogenerador de contrapresión de 27 mw con inestabilidad dinámica al paso por la velocidad crítica en arranque posterior a intervención de mantenimiento mayor- Caso 3
Este caso corresponde a un conjunto turbina, caja reductora y generador, que conforman la unidad de cogeneración de un Ingenio azucarero y cuya dificultad obedeció a la imposibilidad de arrancarlo y ponerlo en operación luego de una intervención mayor de mantenimiento. Esta imposibilidad se debía a que las vibraciones en la turbina alcanzaban niveles de disparo al acercarse a su primera velocidad crítica. Esto supuso un problema importante para el personal a cargo; toda vez que se venía de un tiempo de indisponibilidad relativamente largo y las expectativas estaban en lograr una mejor condición operativa.


En este caso, se realizó acompañamiento con análisis integral de vibraciones, relativas y absolutas, durante un intento de arranque de la máquina; encontrando que efectivamente ocurrían altos niveles vibratorios con excitación fundamental de la frecuencia de giro de la turbina, lo cual contrastaba con el hecho de que se había garantizado un adecuado balance rotacional del rotor; por lo que se planteó integrar herramientas de diagnóstico especiales como un estudio ODS (Operational Deflection Shape). A través del cual se buscó entender el patrón de vibraciones de todo el conjunto, no solo los apoyos de la máquina, sino también del sistema de suportación, incluyendo la base civil, el grouting y el sistema de anclaje.
A través del estudio de ODS se logró identificar un patrón de deflexiones del Grouting con diferencias de fase significativas y sin que se siguiese una secuencia específica; sino que éstas eran de cierto carácter errático. Este patrón indicaba que la suportación no estaba absorbiendo adecuadamente las cargas dinámicas de operación que se transfieren a través de los elementos de anclaje a base.

Ello se produce, sea por un inadecuado anclaje o rigidez insuficiente en la suportación. Al revisar las condiciones que habían cambiado en la suportación durante el mantenimiento y verificar que los elementos de anclaje estaban en buen estado; se señaló el proceso de fraguado como la causa potencial de una disminución en la rigidez del grouting. Al verificar la consistencia, se logró identificar la existencia de burbujas de aire en el Grouting, como producto de un fraguado inefectivo del material; con lo cual se generaron discontinuidades que se traducían en insuficiente rigidez estructural para la absorción de las cargas dinámicas y su correspondiente transmisión a base.
Así, este caso muestra como las herramientas de diagnóstico predictivo como el estudio Operational Deflection Shape o de formas de deflexión operacional (ODS) se postula como un requisito para propender y asegurar la confiabilidad operativa de la turbomaquinaria durante las diferentes etapas de ciclo de vida, como lo son durante el montaje y comisionamiento inicial; así como de manera posterior a intervenciones de mantenimiento mayor.
Por lo anterior es fundamental partir desde tres definiciones que serán claves para las Conclusiones de este artículo y que están estrechamente ligados con la definición de la estrategia para gestionar activos:

Si nos remitimos nuevamente a los casos expuestos, está claro que una estrategia basada en medición y protección con sensores de proximidad, no fue suficiente para determinar el estado de los sistemas y sus componentes, lo que exigió involucrar otras herramientas que al integrarse permitieron llegar a un diagnóstico consolidado y asertivo, lo que conllevó a una toma de decisiones informada por parte de la organización.
Las conclusiones acá presentadas, figura 4, nacen de nuestra experiencia en múltiples análisis complejos de turbomaquinaria, que normalmente son solicitados como consecuencia de operaciones atípicas, afectaciones en la capacidad de generación y como condición más crítica por impacto en la disponibilidad del activo, es por esto que buscamos que la estrategia de monitoreo de condición sea alineada desde la concepción de la turbomáquina, ya que esto permitirá identificar de manera oportuna aspectos relevantes que impactaran en como los datos adquiridos desembocan en decisiones oportunas e informadas.

Figura 4. Alineación de estrategias CBM con el ciclo de vida.
Aunque muchos de los conceptos acá tratados, no son nuevos y su desarrollo se remonta a varias décadas atrás, la realidad es que aún tenemos oportunidades de mejora que nos acerquen a una estrategia más sólida, involucrando aspectos técnicos, tecnológicos, normativos y culturales, que soporten la generación de conocimiento sobre activos tan críticos como las turbomáquinas, que conlleve a la toma de decisiones que soporten al negocio.
"El centro de una sociedad, economía y comunidad moderna, no es la tecnología, es la información."
Bibliografía:
UNE-ISO 5500 Gestión de activos - Aspectos generales, principios y terminología
ISO 9000:2015, Sistemas de gestión de la calidad. Fundamentos y vocabulario
ISO 17359, Condition monitoring and diagnostics of machines. General guidelines
API STANDARD 670, Machinery Protection Systems
Autores
Maria Alejandra Martínez Delgado, CMRP, CGMC, IAM CERTIFICATE
Ingeniera Mecánica, emprendedora y apasionada por la confiabilidad, certificada como Líder AMP Strategic ISO 55000, profesional IAM, Profesional CMRP y Gestor de Mantenimiento y Confiabilidad ACIEM – CGMC, miembro y Chair del comité SMRP LATAM, con más de 10 años de experiencia en el sector industrial en diferentes países de Latinoamérica, fundadora de la compañía IDC Ingeniería de Confiablidad, conferencista, docente y consultora en proyectos de comisionamiento y puesta en marcha de plantas industriales, implementación de estrategias mantenimiento, confiabilidad y gestión de activos alineados a los fundamentos de la Industria 4.0.
Juan Camilo Urango Peréz
Ingeniero Mecánico de la Facultad de Minas de la Universidad Nacional de Colombia, cursando maestría en Ingeniería Mecánica de esta misma facultad, analista de vibraciones ISO CAT II, con amplia formación en mantenimiento industrial, confiabilidad y gestión de activos. Liderazgo en implementación de estrategias de monitoreo de condición integrando elementos de la industria 4.0, análisis rotodinámicos en turbomaquinaria y análisis de causa raíz en eventos de alta complejidad, en países de centro américa y Colombia.
Dinos qué te ha parecido el artículo
Artículos recomendados
La Actitud y Aptitud del Mantenimiento

19.1.- Como se Miden las Vibraciones y Como son Interpretadas

Uso del análisis de vibraciones en el mantenimiento Predictivo de maquinas rotantes

Tipos de mantenimiento preventivo

Publica tu artículo en la revista #1 de Mantenimiento Industrial
Publicar un artículo en la revista es gratis, no tiene costo.
Solo debes asegurarte que no sea un artículo comercial.
¿Qué esperas?
O envía tu artículo directo: articulos@predictiva21.com
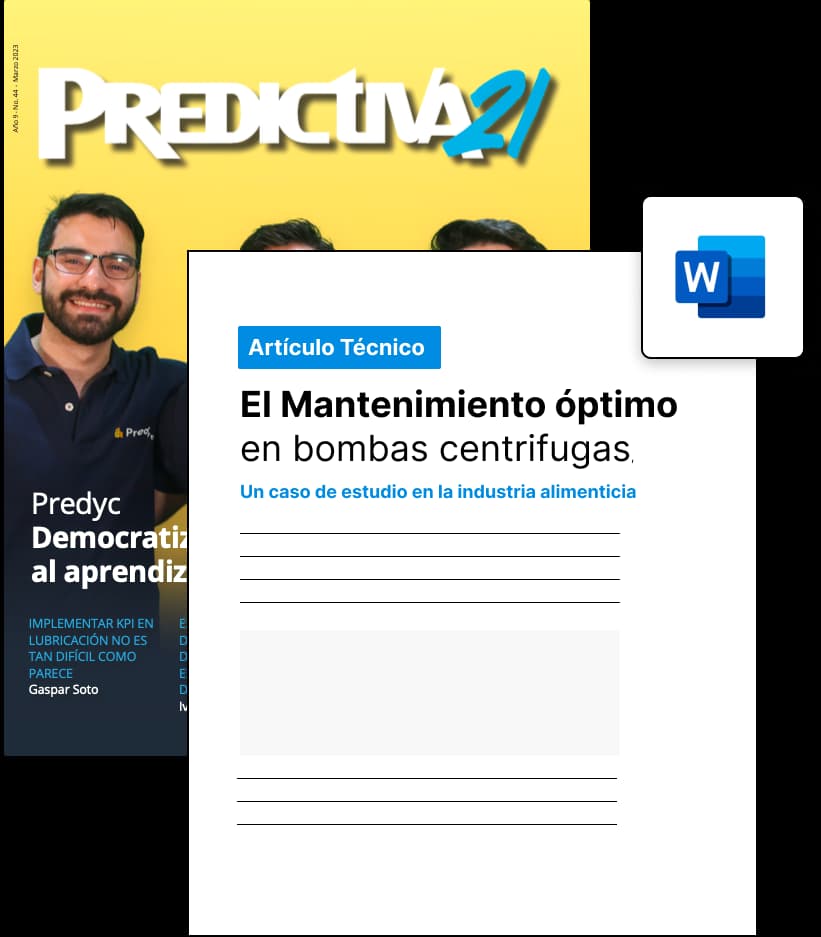
Transformando el Monitoreo de Turbomáquinas, nuevas perspectivas desde la Gestión de Activos
Articulo 15 de febrero de 2024En este artículo se invita a una discusión en relación a la estrategia que históricamente se ha usado para el monitoreo de turbomáquinas y como la toma de decisiones en la gestión de este tipo de activos nos invita a replantear aspectos claves en la búsqueda de disminuir la incertidumbre en estos activos, desde su concepción hasta su desincorporación, a partir de la generación de información basada en la captura de datos mediante diferentes técnicas de monitoreo y diagnóstico.
Antes debemos analizar donde radica la criticidad de este tipo de activos y hay 2 factores fundamentales, el primero el impacto sobre la calidad de vida del ser humano y el desarrollo de la sociedad, ya que este tipo de máquinas son muy usadas para la generación de energía eléctrica, como mecanismo de propulsión y para trasegar fluidos, el segundo su costo elevado en sus cuatro etapas del ciclo de vida: adquisición, montaje y comisionamiento, mantenimiento y operación, renovación o disposición.
Los casos prácticos que serán citados en este espacio se enfocan en aplicaciones para la generación de energía eléctrica, ya que en las últimas dos décadas se ha presentado un aumento de más del 100% en la generación mundial, figura 1, en donde un porcentaje importante de la generación proviene de fuentes que involucran turbomáquinas en su proceso, figura 2.

Figura 1. Tendencia de la generación mundial durante 1990 - 2021 – GWh. Tomado IEA data1

Figura 2. Tendencia de la distribución de la generación mundial durante 1990 - 2021 – GWh. Tomado IEA data1
Volviendo a la historia del monitoreo de las turbomáquinas, debemos ir al año 1965 cuando se implementó por primera vez de manera exitosa la tecnología de corrientes de Eddy en sensores de desplazamiento sin contacto, los cuales están diseñados para medir distancias diminutas, entre la punta del sensor y una superficie conductora, como un eje rotativo, que permite cuantificar desplazamientos sumamente pequeños, generalmente del orden de unos pocos micrones.
Este hecho genera un gran impacto, ya que permite a las industrias con turbomáquinas implementar sensores para medir de manera directa el desplazamiento del eje, el cual suele ser el componente hacia donde se transmiten las cargas dinámicas producto de la operación; y de medirse solo la vibración en carcasa, se perdería información relevante, ya que al ser máquinas que usualmente trabajan con cojinetes hidrodinámicos, las características de la película de lubricación amortiguan y no transmiten de manera adecuada la vibración del eje a la carcasa. Como resultado, se establece la medición con sensores de proximidad como un método más preciso para determinar el estado de este tipo de máquinas e inicia la era de los sistemas de protección.
En 1970, el American Petroleum Institute definió la sonda de proximidad como el dispositivo de medición para evaluar la vibración aceptable del eje y en 1976 publicó la primera versión del estándar API 670 - Machinery Protection Systems, como una guía para el diseño, instalación, configuración y mantenimiento de sistemas de protección de maquinaria utilizados en la industria.

Figura 3. Sonda de proximidad
En definitiva, el desarrollo para la medición de la vibración del eje, utilizando sondas de proximidad, se convirtió en el estándar de la industria para las pruebas de aceptación de turbo maquinaria y su protección en etapa de operación, consolidando este método como el idóneo para evaluar la vibración y la condición mecánica general en maquinaria rotativa crítica como turbinas, compresores, bombas, motores eléctricos, generadores y otros equipos rotativos2.
Sin embargo, en las últimas décadas este se ha convertido casi en el único método aplicado en turbo maquinaria para determinar su condición y solo las organizaciones con un mayor nivel de madurez en la gestión de activos, involucran elementos claves como medición de vibración sobre carcasa, herramientas de diagnóstico especiales como son los estudios de análisis rotodinámico y de Operational Deflection Shape (ODS); así como la integración de variables de proceso.
La experiencia nos ha mostrado que cuando la estrategia de monitoreo solo está basada en sistemas de medición y protección por sondas de proximidad, se vuelve insuficiente para una gestión de activos idónea, ya que desde la concepción del proyecto no se involucran aspectos relevantes que luego serán claves en la puesta en marcha, operación y mantenimiento, impactando en la confiabilidad, los costos, la gestión del inventario de repuestos y el nivel de incertidumbre en la toma de decisiones, por eso enunciaremos 3 casos que nos ayudarán a comprender lo expuesto.
Turbogenerador de condensación de 62 mw con eventos repetitivos de inestabilidad dinámica no determinística - Caso 1
Este caso se trata de un turbogenerador cuya dificultad radicaba en la ocurrencia de eventos, aparentemente aleatorios, en los que había incrementos de vibración hasta niveles de alarma del sistema de protección; que luego disminuían y se regresaba a una relativa estabilidad operativa sin que hubiese una causa aparente. El personal de operación sostenía que tales eventos eran más probables ante cambios de carga; pero que ello no era determinístico.

Ante tal panorama, se plantearon pruebas diagnóstico apuntando a identificar la causa de los eventos y en general a describir la condición de salud de la máquina a partir de sus señales de vibración. Esto, con el objetivo de dar luces para una asertiva planeación, programación y ejecución de las intervenciones de mantenimiento mayor que se tenían previstas para dentro de 4 meses. En ese sentido, se adquirieron señales de vibración relativa de los proximitores del sistema de protección, durante reducción de carga, parada y arranque de la turbina, la sincronización y el incremento de carga a su valor nominal.

A partir del análisis de órbitas, formas de onda y firmas espectrales, se logró identificar un fenómeno de remolino de aceite (Oil whirl), que en este caso consistía en inestabilidad de la película lubricante que soporta la rotación del eje dentro de los cojinetes, atribuido a altas holguras radiales como producto de desgaste. Así, ante cambios de carga o alguna variación en las fuerzas operativas, la película hidrodinámica de aceite en ciertos casos no lograba mantener su estabilidad y se generaban desplazamientos erráticos del eje, que eran registrados como altas vibraciones. Luego, una vez la película lograba estabilizarse, se reducían las vibraciones a niveles normales de operación. A partir de esta conclusión, se recomendó al personal operador establecer la práctica de solo realizar variaciones suaves cuando se requiriera cambiar carga de generación para gestionar el riesgo y mantener la máquina operativa hasta el mantenimiento mayor. Por otro lado, también lograron gestionar la adquisición oportuna de repuestos y realizar una correcta planificación de la intervención de cambio de cojinetes; de manera que se optimizaron tiempos de ejecución, la máquina regresó a generación en el tiempo planeado y con una operación con mayor confiabilidad.

Este caso pone en evidencia que el enfoque de registro de amplitudes de vibraciones a través del sistema de protección, es insuficiente a la hora de brindar información valiosa para la adecuada gestión de la operación y la toma de decisiones asertivas de mantenimiento, que busquen la operación confiable y segura de la turbomaquinaria.
Turbogenerador de extracción de 46 mw con dos eventos recientes de falla en álabes-Caso 2
Este caso obedece a una turbina de vapor de cogeneración de un Ingenio azucarero, cuya situación problema obedece la ocurrencia de fallas por desprendimiento de álabe en una de las ruedas de la turbina. Con estas fallas, no solo se generaron indisponibilidades, con las implicaciones técnicas y económicas que ello contrae, sino que también se hizo evidente la nula efectividad del sistema de protección por vibraciones ante este tipo de fallas. Toda vez que previo la ocurrencia, no se registró ningún tipo de señal de alerta; e incluso, solo unos segundos después del desprendimiento del álabe, se alcanzó el disparo por vibraciones debido al efecto de desbalance.


Posterior a la reparación del primer evento de falla, se acompañó el arranque de la máquina con un análisis integral de vibraciones, que incluyó vibraciones relativas desde los proximitores del sistema de protección y vibraciones absolutas registradas a través de acelerómetros instalados temporalmente sobre carcasa de los cojinetes. Esto, con el objetivo de tener una mirada amplia sobre la condición de la máquina, que incluyera las vibraciones en bajas y medias frecuencias en las variables desplazamiento y velocidad; y vibraciones en alta frecuencia en la variable aceleración. En la medición se identificó una excitación espectral de alta frecuencia del pico de 95 veces la frecuencia rotacional (95X), que corresponde a la frecuencia de paso de álabes (BPF) de una rueda de la turbina; su amplitud en ese momento era de 1.5 G’s-rms. Ante ello, se reportó a personal a cargo sobre posible irregularidad del flujo de vapor a través de los álabes; y se recomendó monitoreo.
Con lo anterior, la máquina continuó la operación durante alrededor de 10 meses, cuando se realizó un nuevo análisis de vibraciones. En este se identificó que persistía la excitación de alta frecuencia, con incremento significativo en su amplitud, del orden del 193%, alcanzando niveles de 4.4 G’s-rms. Esa vez se generó una alerta al personal a cargo, sobre el incremento en el riesgo que significaba este importante cambio en las vibraciones de alta frecuencia. El operador de la máquina transfirió esta inquietud al fabricante, sin hubiese una respuesta de alarma o que indicase la necesidad de alguna intervención. Alrededor de dos meses después de generada la alarma, se presentó un nuevo evento de desprendimiento de álabe, con la misma secuencia de eventos presenciada en la primera falla.
Posterior a la reparación, se hizo un nuevo acompañamiento en el arranque; en el cual, se identificó que se mantenía la presencia del pico de frecuencia de paso de álabes con una amplitud que se había reducido en un 75%, alcanzando 1.1 G’s-rms. Lo anterior plantea que existiría una relación directa entre la amplitud de este pico, con la degradación de la condición de integridad y el riesgo de falla en los álabes. Este caso evidencia que para protección ante eventos potenciales de falla o que comprometan la integridad en turbomáquinas, las vibraciones relativas no son suficientes, como señales que generen una alarma o detonen una parada de protección. Además, su registros no generan información suficiente, al momento de construir diagnósticos predictivos y/o un eventual análisis de causa-raíz.
Así, este caso presenta solo un ejemplo de todos los que pudiese haber, en donde la integración entre vibraciones absolutas con relativas son un requisito para el diagnóstico oportuno de patologías de falla y una mejora sustancial del esquema de protección de la turbomaquinaria.
Turbogenerador de contrapresión de 27 mw con inestabilidad dinámica al paso por la velocidad crítica en arranque posterior a intervención de mantenimiento mayor- Caso 3
Este caso corresponde a un conjunto turbina, caja reductora y generador, que conforman la unidad de cogeneración de un Ingenio azucarero y cuya dificultad obedeció a la imposibilidad de arrancarlo y ponerlo en operación luego de una intervención mayor de mantenimiento. Esta imposibilidad se debía a que las vibraciones en la turbina alcanzaban niveles de disparo al acercarse a su primera velocidad crítica. Esto supuso un problema importante para el personal a cargo; toda vez que se venía de un tiempo de indisponibilidad relativamente largo y las expectativas estaban en lograr una mejor condición operativa.


En este caso, se realizó acompañamiento con análisis integral de vibraciones, relativas y absolutas, durante un intento de arranque de la máquina; encontrando que efectivamente ocurrían altos niveles vibratorios con excitación fundamental de la frecuencia de giro de la turbina, lo cual contrastaba con el hecho de que se había garantizado un adecuado balance rotacional del rotor; por lo que se planteó integrar herramientas de diagnóstico especiales como un estudio ODS (Operational Deflection Shape). A través del cual se buscó entender el patrón de vibraciones de todo el conjunto, no solo los apoyos de la máquina, sino también del sistema de suportación, incluyendo la base civil, el grouting y el sistema de anclaje.
A través del estudio de ODS se logró identificar un patrón de deflexiones del Grouting con diferencias de fase significativas y sin que se siguiese una secuencia específica; sino que éstas eran de cierto carácter errático. Este patrón indicaba que la suportación no estaba absorbiendo adecuadamente las cargas dinámicas de operación que se transfieren a través de los elementos de anclaje a base.

Ello se produce, sea por un inadecuado anclaje o rigidez insuficiente en la suportación. Al revisar las condiciones que habían cambiado en la suportación durante el mantenimiento y verificar que los elementos de anclaje estaban en buen estado; se señaló el proceso de fraguado como la causa potencial de una disminución en la rigidez del grouting. Al verificar la consistencia, se logró identificar la existencia de burbujas de aire en el Grouting, como producto de un fraguado inefectivo del material; con lo cual se generaron discontinuidades que se traducían en insuficiente rigidez estructural para la absorción de las cargas dinámicas y su correspondiente transmisión a base.
Así, este caso muestra como las herramientas de diagnóstico predictivo como el estudio Operational Deflection Shape o de formas de deflexión operacional (ODS) se postula como un requisito para propender y asegurar la confiabilidad operativa de la turbomaquinaria durante las diferentes etapas de ciclo de vida, como lo son durante el montaje y comisionamiento inicial; así como de manera posterior a intervenciones de mantenimiento mayor.
Por lo anterior es fundamental partir desde tres definiciones que serán claves para las Conclusiones de este artículo y que están estrechamente ligados con la definición de la estrategia para gestionar activos:

Si nos remitimos nuevamente a los casos expuestos, está claro que una estrategia basada en medición y protección con sensores de proximidad, no fue suficiente para determinar el estado de los sistemas y sus componentes, lo que exigió involucrar otras herramientas que al integrarse permitieron llegar a un diagnóstico consolidado y asertivo, lo que conllevó a una toma de decisiones informada por parte de la organización.
Las conclusiones acá presentadas, figura 4, nacen de nuestra experiencia en múltiples análisis complejos de turbomaquinaria, que normalmente son solicitados como consecuencia de operaciones atípicas, afectaciones en la capacidad de generación y como condición más crítica por impacto en la disponibilidad del activo, es por esto que buscamos que la estrategia de monitoreo de condición sea alineada desde la concepción de la turbomáquina, ya que esto permitirá identificar de manera oportuna aspectos relevantes que impactaran en como los datos adquiridos desembocan en decisiones oportunas e informadas.

Figura 4. Alineación de estrategias CBM con el ciclo de vida.
Aunque muchos de los conceptos acá tratados, no son nuevos y su desarrollo se remonta a varias décadas atrás, la realidad es que aún tenemos oportunidades de mejora que nos acerquen a una estrategia más sólida, involucrando aspectos técnicos, tecnológicos, normativos y culturales, que soporten la generación de conocimiento sobre activos tan críticos como las turbomáquinas, que conlleve a la toma de decisiones que soporten al negocio.
"El centro de una sociedad, economía y comunidad moderna, no es la tecnología, es la información."
Bibliografía:
UNE-ISO 5500 Gestión de activos - Aspectos generales, principios y terminología
ISO 9000:2015, Sistemas de gestión de la calidad. Fundamentos y vocabulario
ISO 17359, Condition monitoring and diagnostics of machines. General guidelines
API STANDARD 670, Machinery Protection Systems
Autores
Maria Alejandra Martínez Delgado, CMRP, CGMC, IAM CERTIFICATE
Ingeniera Mecánica, emprendedora y apasionada por la confiabilidad, certificada como Líder AMP Strategic ISO 55000, profesional IAM, Profesional CMRP y Gestor de Mantenimiento y Confiabilidad ACIEM – CGMC, miembro y Chair del comité SMRP LATAM, con más de 10 años de experiencia en el sector industrial en diferentes países de Latinoamérica, fundadora de la compañía IDC Ingeniería de Confiablidad, conferencista, docente y consultora en proyectos de comisionamiento y puesta en marcha de plantas industriales, implementación de estrategias mantenimiento, confiabilidad y gestión de activos alineados a los fundamentos de la Industria 4.0.
Juan Camilo Urango Peréz
Ingeniero Mecánico de la Facultad de Minas de la Universidad Nacional de Colombia, cursando maestría en Ingeniería Mecánica de esta misma facultad, analista de vibraciones ISO CAT II, con amplia formación en mantenimiento industrial, confiabilidad y gestión de activos. Liderazgo en implementación de estrategias de monitoreo de condición integrando elementos de la industria 4.0, análisis rotodinámicos en turbomaquinaria y análisis de causa raíz en eventos de alta complejidad, en países de centro américa y Colombia.
Dinos qué te ha parecido el artículo
Artículos recomendados
6 Errores a evitar con el software de gestión de activos (EAM)

Las Revoluciones Industriales en el Mundo (II Parte)

El CEO de Emerson, David N. Farr, se jubila

Metodología Propuesta para Toma de Decisión de Inspección de Líneas de Flujo de Crudo Basado en Modelos Estadísticos de Criticidad

Publica tu artículo en la revista #1 de Mantenimiento Industrial
Publicar un artículo en la revista es gratis, no tiene costo.
Solo debes asegurarte que no sea un artículo comercial.
¿Qué esperas?
O envía tu artículo directo: articulos@predictiva21.com
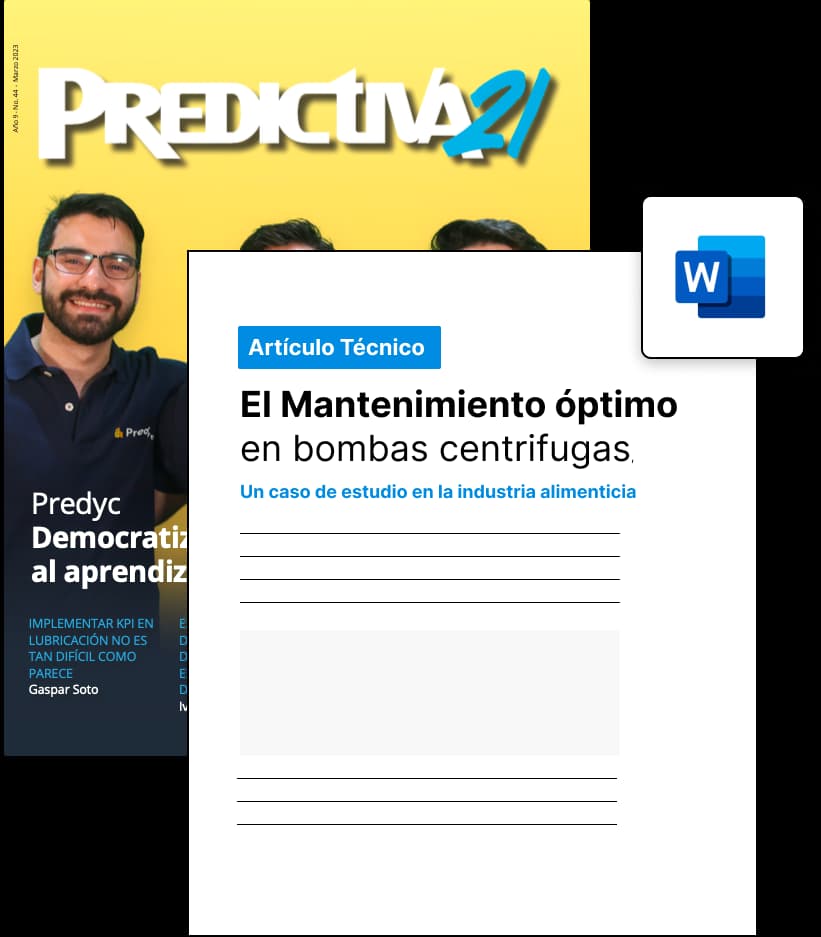