Understanding and implementing Maintenance Excellence
Articulo23 de octubre de 2019
Introductión
Modern industry is at a crossroads in today’s world. Management is driven to reduce costs and provide higher productivity. Yet, management in many cases does not have the correct information required to make long-term cost effective decisions with regards to the maintenance of the facilities, buildings, infrastructure, utilities, and assets that make parts that make up the final product. This paper will focus around large industry, which uses high technology machine tools. The principals discussed here however will apply to any business of any size. The key is to understand what Maintenance Excellence is, and how to apply the principals. You need to understand that Maintenance Excellence for one company may not be the same for another. This sounds like achieving Maintenance Excellence is a moving target and in reality this is a true statement.
Each business is different with different ways of producing products and making profits. Because of this, you will need to understand the basic principals of achieving Maintenance Excellence. Understanding all the aspects of achieving Maintenance Excellence is a tough task, but smart management can set goals and reach those goals in incremental fashion. A little at a time, a company can achieve Maintenance Excellence. The subjects covered in this presentation are the basic building blocks, and as with any effort to reach true World Class status, the most important building blocks are the foundation blocks, for if these are weak, the rest of the effort will crumble.
Problems
Large industrial manufacturing is driven from a culture established more than 50 years ago. Too many old ways are still in place, and companies need to break free of that mold if they want to exist and compete, but especially if they wish to achieve World Class Maintenance Excellence. The business world today is a global a air and this alone assures companies that they need to change their thinking to stay in business.
“Reduce Overhead First” thinking is firmly established in the old culture, and to change this thinking will require showing and proving the value of an overhead organization, primarily a Facilities Organization. To change culture takes time and patience, both of which are probably in short supply in today’s environment. To counter the environment, you will need to have change agents in place. What is a change agent? These are people who drive the changes to processes and cultures engrained in the current environment. Change agents are people who have a talent for understanding that change is inevitable and will happen whether in an organized manner or not. These are people who are very good under pressure and scrutiny, and who believe in the changes they are working to achieve. These people understand that culture changes are slow, yet process changes can be very fast. These are people who believe in the changes that they are helping to drive. One absolute fact about change is that it will happen. The key is to be in control of the changes by having a plan.
Understanding how to show a maintenance department’s value. This will always be a continual challenge for management in a maintenance organization. If the services your team provides to Operations simply suck up money with no real value shown in return, you will never fully achieve Maintenance Excellence. The real question is how do you show value. If your services in no way provide a dollar input to the company bottom line, how is it possible to show your true value to your customer? The key to this is in knowing your company’s operation and how your company makes profit. It all comes down to a common denominator, dollars. If you know for example, that a machine tool needs to operate reliably for a set number of hours each day to produce a set amount of parts, and you know the cost of the operation to produce these parts, then one way to show value is to show management the cost to the company for machine failures during the part run periods.
Let us say that an asset “cuts chips” for 60% of a 24 hour period. That equates to 14.4 hours of actual Economic Value Added time. The balance of the 24 hours (9.6) is used for machine and tool set up time, lunches, breaks, shift schedules, etc. If the asset fails during a cutting period, then it will immediately begin to cost your operations money in lost productivity, upstream process backup of inventory, downstream process delays to finished product, asset operator labor to rework the part, operator labor lost to machine downtime during the failure, maintenance labor to perform reactive failure corrections, and so on and on. An average rule of thumb is that reactive maintenance work costs you four times as much as planned work. If you know these things, you are on the way to showing the value of a maintenance organization because you will be able to show in dollars and cents the costs of asset failures to the company.
This is only one way to show value. There are many ways, but those are dependant on knowing how your business operates. To have the ability to really show value, will require you to embrace the seven basic foundation principals of Maintenance Excellence. Understanding these basic principals and how to implement them is important, but sustaining them is critical. Once the basic foundation principals are in place and effective, you will be able to institute the Advanced Maintenance Excellence principals. You will find that just getting the foundation principals in place will be a major culture change, but it is essential these be in place before moving to the advanced principals.
Recommendations
Institute the Seven Foundation Principals of World Class Maintenance Excellence.
• Identification of all work. All work must be identified and input to a CMMS system. Work that is performed but not tracked is lost. Even though the work was important and time and resources were expended, you won’t be able to account for that work and thus your maintenance organization will not get credit for their efforts.
• Prioritization of all work. All work that is submitted must be assigned a priority. There are many ways of doing this but it is much easier if you stay simple. For example, Priority 1 work would be the highest level of reactive work that would be started in a 0-24 hour time range. Priority 2 work would be reactive that could be started in a 2 –7 day time range. Priority 3 work is all planned work and can be started in a range of 8-28 days. These simple priorities should be assigned by whoever identifies the work. By taking this approach, it will make it easier to chart the work for reference. World Class companies perform at 80% planned activities or better, with 20% or less in reactive work. Reactive work usually costs the company four times the cost of planned work, therefore being able to show this helps you to show your value.
• Planning and Scheduling of all work other than reactive. All work that is non reactive should be planned and scheduled. This function allows for resources to be matched to production windows of opportunity. Parts and supplies, tools, and all resources other than manpower should be planned to a specific job. Your technicians don’t need to be running for parts or searching for tools and prints because that is draining and wasting their expertise. Making the most of this will greatly help in showing value.
• Managing workloads. If you are planning and scheduling all of your planned activities, you will be able to begin managing your true workloads and your manpower resources much more effectively. There will be less scrambling to get techs to jobs. You will be able to level load your PM work across a given timeframe and adjust resources accordingly. This gives you the ability to reduce costs by simple work management activities.
• Work Execution. Work that is committed and planned must be executed. If you’ve got production committal to release an asset for work, your team must be there to perform. Otherwise you will lose credibility and it’s all down hill from there.
• Variances in work processes. Give your techs the ability to list what problems they encounter on any job. These are variances. Be able to collect and take actions to correct these problems.
• Measuring Key Process Indicators. Having a documented maintenance process allows you to measure key points within the process that allow you to gage its health. Key Process Indicators are a way to show the value of the process and the value of the maintenance organization.
• Institute the Advanced Principals of World Class Maintenance Excellence only after the foundation is solid. The focus of this paper is based on the seven foundation principals. The basics of advanced implementation revolve around these issues:
- Instituting Reliability in Assets and Processes.
- Understanding Reliability in context to Maintenance.
- Understand that to improve Reliability in assets is different than improving Reliability in Processes.
The following are some examples of what a World Class Company with Maintenance Excellence implemented would reflect:
- Specify, design and buy assets based on life cycle cost (LCC) instead of lowest cost to buy.
- A management team focusing on the same results.
- There is a documented reliability and maintenance policy that includes a 3 to 5 year improvement plan.
- High level of planning and scheduling.
- Correct prioritization of work.
- Preventive Maintenance/Essential Care and Condition Monitoring content is right.
- PM execution is 100%.
- 85% of spare parts and materials are delivered to the job site.
- Service level is 97% for the spare parts stores.
- The technical database is 95% correct.
- Basics of Maintenance are instituted:
- 1. Balancing.
- 2. Cleaning of components.
- 3. Lubrication.
- 4. Alignment.
- Operations Practices Safety Standards are high.
- Individual training plans are developed and used.
- Craftspeople have a high level of skills and front line supervision adjusts its management style accordingly.
Cursos recomendados






%252FImagen%252FRAMPREDYC-1730060420837.webp%3Falt%3Dmedia%26token%3D2634a7f0-988e-4022-b91f-382503e6e9db&w=3840&q=75)

Conclusión
- Understanding where your business is today.
- What you need to do to change culture.
- How implementing the seven basic principals begin to drive Maintenance Excellence.
- Executing the plan to achieve Maintenance Excellence.
- Plan - Create a plan.
- Do - Execute the plan.
- Check - Evaluate the execution of the plan.
- Act - Take corrective actions where needed.
I believe you understand that there is no simple, easy method of reaching Maintenance Excellence. Each company is different with different management styles and business goals. This paper only gives you a little insight on what it will take to show your value as a maintenance organization. True Maintenance Excellence is something that can only be achieved with hard work, but it is not easy and it can be a moving target. If you truly believe that becoming a valued overhead organization is critical, then you will understand that in order to achieve it means hard work, lots of changes, and dedication. These basic seven foundation principals are a required component of Maintenance Excellence, and yet these seven are only the foundation blocks. These are only the start of the journey. If you can institute these seven basic principals, you will have taken the first seven steps to Maintenance Excellence. Good Luck on your journey.
Author: Kenneth D. Peoples
Reliability Engineering
Predictive Technologies Manager
The Boeing Commercial Airplane Company
Wichita Division Work Place Services
Email: kenneth.d.peoples@boeing.com
Dinos qué te ha parecido el artículo
Artículos recomendados
Influencia de los parámetros pasivos de vibración en el comportamiento dinámico de equipos

Detección temperatura anormal por daños en el asiento de la válvula compresora interna de cuarta etapa, compresor dresser rand

Aprender Mantenimiento Industrial

Mantenimiento Industrial para afrontar la Crisis

Publica tu artículo en la revista #1 de Mantenimiento Industrial
Publicar un artículo en la revista es gratis, no tiene costo.
Solo debes asegurarte que no sea un artículo comercial.
¿Qué esperas?
O envía tu artículo directo: articulos@predictiva21.com
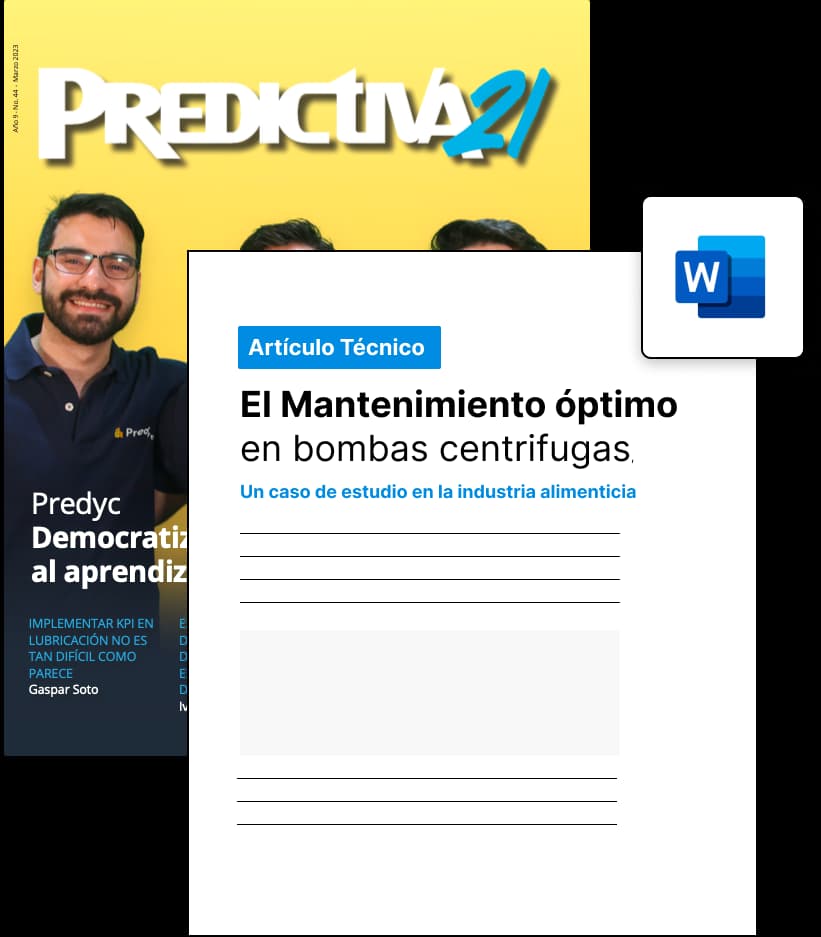
Understanding and implementing Maintenance Excellence
Articulo 23 de octubre de 2019Introductión
Modern industry is at a crossroads in today’s world. Management is driven to reduce costs and provide higher productivity. Yet, management in many cases does not have the correct information required to make long-term cost effective decisions with regards to the maintenance of the facilities, buildings, infrastructure, utilities, and assets that make parts that make up the final product. This paper will focus around large industry, which uses high technology machine tools. The principals discussed here however will apply to any business of any size. The key is to understand what Maintenance Excellence is, and how to apply the principals. You need to understand that Maintenance Excellence for one company may not be the same for another. This sounds like achieving Maintenance Excellence is a moving target and in reality this is a true statement.
Each business is different with different ways of producing products and making profits. Because of this, you will need to understand the basic principals of achieving Maintenance Excellence. Understanding all the aspects of achieving Maintenance Excellence is a tough task, but smart management can set goals and reach those goals in incremental fashion. A little at a time, a company can achieve Maintenance Excellence. The subjects covered in this presentation are the basic building blocks, and as with any effort to reach true World Class status, the most important building blocks are the foundation blocks, for if these are weak, the rest of the effort will crumble.
Problems
Large industrial manufacturing is driven from a culture established more than 50 years ago. Too many old ways are still in place, and companies need to break free of that mold if they want to exist and compete, but especially if they wish to achieve World Class Maintenance Excellence. The business world today is a global a air and this alone assures companies that they need to change their thinking to stay in business.
“Reduce Overhead First” thinking is firmly established in the old culture, and to change this thinking will require showing and proving the value of an overhead organization, primarily a Facilities Organization. To change culture takes time and patience, both of which are probably in short supply in today’s environment. To counter the environment, you will need to have change agents in place. What is a change agent? These are people who drive the changes to processes and cultures engrained in the current environment. Change agents are people who have a talent for understanding that change is inevitable and will happen whether in an organized manner or not. These are people who are very good under pressure and scrutiny, and who believe in the changes they are working to achieve. These people understand that culture changes are slow, yet process changes can be very fast. These are people who believe in the changes that they are helping to drive. One absolute fact about change is that it will happen. The key is to be in control of the changes by having a plan.
Understanding how to show a maintenance department’s value. This will always be a continual challenge for management in a maintenance organization. If the services your team provides to Operations simply suck up money with no real value shown in return, you will never fully achieve Maintenance Excellence. The real question is how do you show value. If your services in no way provide a dollar input to the company bottom line, how is it possible to show your true value to your customer? The key to this is in knowing your company’s operation and how your company makes profit. It all comes down to a common denominator, dollars. If you know for example, that a machine tool needs to operate reliably for a set number of hours each day to produce a set amount of parts, and you know the cost of the operation to produce these parts, then one way to show value is to show management the cost to the company for machine failures during the part run periods.
Let us say that an asset “cuts chips” for 60% of a 24 hour period. That equates to 14.4 hours of actual Economic Value Added time. The balance of the 24 hours (9.6) is used for machine and tool set up time, lunches, breaks, shift schedules, etc. If the asset fails during a cutting period, then it will immediately begin to cost your operations money in lost productivity, upstream process backup of inventory, downstream process delays to finished product, asset operator labor to rework the part, operator labor lost to machine downtime during the failure, maintenance labor to perform reactive failure corrections, and so on and on. An average rule of thumb is that reactive maintenance work costs you four times as much as planned work. If you know these things, you are on the way to showing the value of a maintenance organization because you will be able to show in dollars and cents the costs of asset failures to the company.
This is only one way to show value. There are many ways, but those are dependant on knowing how your business operates. To have the ability to really show value, will require you to embrace the seven basic foundation principals of Maintenance Excellence. Understanding these basic principals and how to implement them is important, but sustaining them is critical. Once the basic foundation principals are in place and effective, you will be able to institute the Advanced Maintenance Excellence principals. You will find that just getting the foundation principals in place will be a major culture change, but it is essential these be in place before moving to the advanced principals.
Recommendations
Institute the Seven Foundation Principals of World Class Maintenance Excellence.
• Identification of all work. All work must be identified and input to a CMMS system. Work that is performed but not tracked is lost. Even though the work was important and time and resources were expended, you won’t be able to account for that work and thus your maintenance organization will not get credit for their efforts.
• Prioritization of all work. All work that is submitted must be assigned a priority. There are many ways of doing this but it is much easier if you stay simple. For example, Priority 1 work would be the highest level of reactive work that would be started in a 0-24 hour time range. Priority 2 work would be reactive that could be started in a 2 –7 day time range. Priority 3 work is all planned work and can be started in a range of 8-28 days. These simple priorities should be assigned by whoever identifies the work. By taking this approach, it will make it easier to chart the work for reference. World Class companies perform at 80% planned activities or better, with 20% or less in reactive work. Reactive work usually costs the company four times the cost of planned work, therefore being able to show this helps you to show your value.
• Planning and Scheduling of all work other than reactive. All work that is non reactive should be planned and scheduled. This function allows for resources to be matched to production windows of opportunity. Parts and supplies, tools, and all resources other than manpower should be planned to a specific job. Your technicians don’t need to be running for parts or searching for tools and prints because that is draining and wasting their expertise. Making the most of this will greatly help in showing value.
• Managing workloads. If you are planning and scheduling all of your planned activities, you will be able to begin managing your true workloads and your manpower resources much more effectively. There will be less scrambling to get techs to jobs. You will be able to level load your PM work across a given timeframe and adjust resources accordingly. This gives you the ability to reduce costs by simple work management activities.
• Work Execution. Work that is committed and planned must be executed. If you’ve got production committal to release an asset for work, your team must be there to perform. Otherwise you will lose credibility and it’s all down hill from there.
• Variances in work processes. Give your techs the ability to list what problems they encounter on any job. These are variances. Be able to collect and take actions to correct these problems.
• Measuring Key Process Indicators. Having a documented maintenance process allows you to measure key points within the process that allow you to gage its health. Key Process Indicators are a way to show the value of the process and the value of the maintenance organization.
• Institute the Advanced Principals of World Class Maintenance Excellence only after the foundation is solid. The focus of this paper is based on the seven foundation principals. The basics of advanced implementation revolve around these issues:
- Instituting Reliability in Assets and Processes.
- Understanding Reliability in context to Maintenance.
- Understand that to improve Reliability in assets is different than improving Reliability in Processes.
The following are some examples of what a World Class Company with Maintenance Excellence implemented would reflect:
- Specify, design and buy assets based on life cycle cost (LCC) instead of lowest cost to buy.
- A management team focusing on the same results.
- There is a documented reliability and maintenance policy that includes a 3 to 5 year improvement plan.
- High level of planning and scheduling.
- Correct prioritization of work.
- Preventive Maintenance/Essential Care and Condition Monitoring content is right.
- PM execution is 100%.
- 85% of spare parts and materials are delivered to the job site.
- Service level is 97% for the spare parts stores.
- The technical database is 95% correct.
- Basics of Maintenance are instituted:
- 1. Balancing.
- 2. Cleaning of components.
- 3. Lubrication.
- 4. Alignment.
- Operations Practices Safety Standards are high.
- Individual training plans are developed and used.
- Craftspeople have a high level of skills and front line supervision adjusts its management style accordingly.
Cursos recomendados






%252FImagen%252FRAMPREDYC-1730060420837.webp%3Falt%3Dmedia%26token%3D2634a7f0-988e-4022-b91f-382503e6e9db&w=3840&q=75)

Conclusión
- Understanding where your business is today.
- What you need to do to change culture.
- How implementing the seven basic principals begin to drive Maintenance Excellence.
- Executing the plan to achieve Maintenance Excellence.
- Plan - Create a plan.
- Do - Execute the plan.
- Check - Evaluate the execution of the plan.
- Act - Take corrective actions where needed.
I believe you understand that there is no simple, easy method of reaching Maintenance Excellence. Each company is different with different management styles and business goals. This paper only gives you a little insight on what it will take to show your value as a maintenance organization. True Maintenance Excellence is something that can only be achieved with hard work, but it is not easy and it can be a moving target. If you truly believe that becoming a valued overhead organization is critical, then you will understand that in order to achieve it means hard work, lots of changes, and dedication. These basic seven foundation principals are a required component of Maintenance Excellence, and yet these seven are only the foundation blocks. These are only the start of the journey. If you can institute these seven basic principals, you will have taken the first seven steps to Maintenance Excellence. Good Luck on your journey.
Author: Kenneth D. Peoples
Reliability Engineering
Predictive Technologies Manager
The Boeing Commercial Airplane Company
Wichita Division Work Place Services
Email: kenneth.d.peoples@boeing.com
Dinos qué te ha parecido el artículo
Artículos recomendados
¿En qué consiste una academia de mantenimiento?

Importancia del mantenimiento

Cálculo de frecuencia de muestreo en análisis de aceites y otras tecnologías predictivas

Criterios de aceptación de niveles de Vibración en Compresores Reciprocantes

Publica tu artículo en la revista #1 de Mantenimiento Industrial
Publicar un artículo en la revista es gratis, no tiene costo.
Solo debes asegurarte que no sea un artículo comercial.
¿Qué esperas?
O envía tu artículo directo: articulos@predictiva21.com
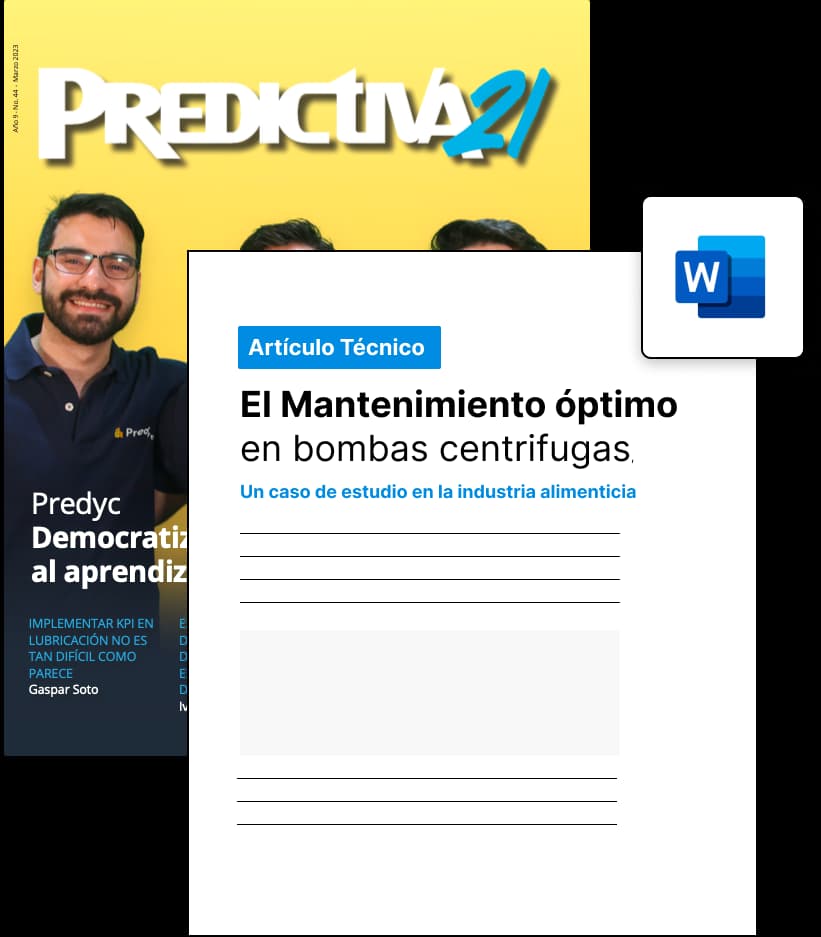