Uso y aplicación de la Prueba de Gota
Articulo20 de noviembre de 2019
La prueba de la gota de lubricante sobre papel filtro es una técnica que data del siglo XIX. En el área científica se le conoce como cromatografía plana en papel filtro y es usada para identificar la condición y degradación de lubricantes para motores de combustión interna a diésel, gasolina y gas. Es una prueba cualitativa que consiste en la separación por su peso molecular de los compuestos que se encuentran suspendidos y diluidos en el lubricante, a través de la capilaridad y uniformidad del papel Whatman #4. Por medio de esta prueba se separan los productos de degradación del lubricante (barniz, lacas, lodos) y contaminantes (hollín, anticongelante y combustible).
Al colocar sobre el papel el lubricante, este se desplaza por capilaridad de manera circular. Los compuestos más ligeros (como el combustible) viajarán más rápido, mientras que los más pesados (como el hollín y los productos de degradación) irán más lentos. Esto hace que el círculo que genera la gota tenga características muy específicas que permiten identificar de manera visual la presencia de condiciones anormales. Esta es una prueba cualitativa, por lo tanto, sirve solo para detectar una condición normal o anormal por apreciación visual. Con el tiempo y suficiente práctica podrá desarrollar sus habilidades de interpretación para identificar diferentes condiciones del lubricante.
¿Por qué es importante efectuar la prueba de la gota? Cada una de las condiciones identificadas por la prueba de la gota indican modos de falla diferentes que merecen ser investigados, ya que pueden causar severos daños a la maquinaria y acelerar la degradación del lubricante. Entre las condiciones que se detectan con esta prueba están las siguientes:
Hollín
El hollín es 98% carbón y sus partículas tienen forma casi esférica con tamaños que van desde 0.01 hasta 0.05 micrones. Estas partículas, mientras permanezcan pequeñas, no ponen en peligro los diferentes componentes del motor. Sin embargo, con el tiempo y el agotamiento de los aditivos del lubricante, estas tienden a aglomerarse y crecer en tamaño. Al no poder ser manejadas por el lubricante, estas partículas producen incremento en la viscosidad del lubricante y depósitos en el motor. Adicionalmente, al tratarse de carbón y crecer en tamaño, ocasiona desgaste abrasivo, principalmente en zonas donde la lubricación es a película límite. El aditivo dispersante en el lubricante se encarga de mantener el hollín finamente disperso, evitando su crecimiento y aglomeración. Excesivas cantidades de hollín agotan rápidamente la capacidad dispersante del lubricante formando lo que normalmente se conoce como lodos. A medida que se consume el dispersante, las partículas de hollín comienzan a aglomerarse y a depositarse sobre las superficies del motor impidiendo una correcta lubricación y flujo de aceite a través del filtro. Excesivas cantidades de hollín incrementan la viscosidad del lubricante ocasionando un mayor desgaste, al afectar el desempeño del antidesgaste, generando una falla prematura del motor.
El uso de motores con recirculación de gases de escape (EGR) ha incrementado el nivel de hollín en el lubricante, por lo que se han generado nuevos niveles de desempeño a fin de que estos lubricantes puedan manejar mayores concentraciones de hollín sin afectar sus propiedades y la protección de los motores.
Detección de hollín
La prueba de gota puede evaluar tanto la concentración de hollín en el lubricante como su estado de dispersión. La gota se inspecciona colocándola sobre una tableta de luz blanca, la cual permite que las condiciones de inspección sean consistentes.
Concentración o carga de hollín
La concentración de hollín en el lubricante depende de la condición del sistema de combustión, la condición del filtro de aire, de las condiciones y estilo de operación y del tiempo que el lubricante ha trabajado en el motor. Cuando un motor opera en condiciones anormales, con filtro de aire saturado, se ha excedido el tiempo de cambio de lubricante o es operado de manera incorrecta, la generación y la concentración de hollín en el lubricante será mayor.
Una gota grande y traslúcida o de tono ligeramente obscuro significa que la concentración de hollín es baja. Una alta concentración de hollín en el lubricante se observará en una gota obscura, no traslúcida. Mientras más obscura la gota, mayor será la concentración de hollín en el lubricante.

Fuente: El autor
Dispersión de hollín o dispersancia
El hollín en el lubricante puede estar disperso o aglomerado, lo que depende de la capacidad del lubricante para mantenerlo en suspensión. Cuando el hollín está disperso, significa que el aditivo del lubricante está haciendo su trabajo y mantiene las partículas de hollín finamente separadas. Al agotarse este aditivo, las partículas de hollín se aglomeran y crecen en tamaño y peso. La prueba de gota es la única técnica existente para identificar esta condición del lubricante.
Al efectuar la prueba de la gota y diseminarse el aceite sobre el papel Whatman, las partículas de hollín dispersas en el lubricante viajarán fácilmente con el básico lubricante y formarán un círculo grande y uniforme, un poco traslúcido o de tonalidad ligeramente obscura, dependiendo de la concentración de hollín. Cuando las partículas de hollín están aglomeradas, se observará un círculo con un diámetro más pequeño y un color más obscuro. Esto se considera una condición anormal que debe ser notificada e investigada.

Combustible
La contaminación o dilución con combustible es un fenómeno que se presenta en los motores de combustión interna en los cuales el combustible no quemado (diésel, gasolina, condensados del gas natural o LP) se acumulan en el cárter del motor. Una mezcla aire/combustible excesivamente rica o una combustión incompleta, ocasionan que cierta cantidad de combustible pase a través del sistema anillos/pistón/cilindros diluyendo el aceite del motor. Esta situación es más común en motores donde el combustible es inyectado a elevadas presiones, pasando a través de los anillos hacia el cárter del motor, incrementando el desgaste a causa de la dilución del lubricante y pérdida de la película.
Dado que los componentes menos volátiles del combustible tienen una elevada tendencia a condensarse, el nivel de dilución del lubricante está directamente relacionado con la volatilidad del combustible. Los combustibles con puntos finales de destilación muy elevados contienen una gran cantidad de compuestos poco volátiles que serán difíciles de quemar durante el proceso de combustión. Esto traerá como consecuencia una elevada dilución y una pérdida sustancial en la viscosidad del lubricante, lo que no permitirá la formación de una película de lubricante adecuada que mantenga las superficies separadas, incrementando el desgaste de los componentes del motor.
Un lubricante con una viscosidad baja como consecuencia de una contaminación con combustible no estará en capacidad de mantener separadas las superficies en movimiento, provocando el contacto metal-metal con el consiguiente desgaste de los componentes del motor.
Cursos recomendados




%252FImagen%252FRAMPREDYC-1730060420837.webp%3Falt%3Dmedia%26token%3D2634a7f0-988e-4022-b91f-382503e6e9db&w=3840&q=75)



Detección de combustible en el lubricante
El combustible es más ligero que el lubricante, por lo tanto, en caso de estar presente en el lubricante, viajará más rápido y se situará en la parte externa o borde de la circunferencia de la gota de aceite.
Para identificar la presencia de combustible, el papel con la gota de aceite debe colocarse bajo la lámpara de luz ultravioleta en una habitación con poca luz para evitar interferencia en la inspección. Los aromáticos contenidos en el combustible poseen características de fluorescencia cuando son inspeccionados bajo la luz ultravioleta. Un círculo fluorescente en el exterior de la gota de lubricante nos indicará la presencia de combustible.

Fuente: El autor
Anticongelante (glicol)
El anticongelante protege al motor del congelamiento y a sus componentes de la corrosión; al mismo tiempo juega un papel importante en el balance energético de los motores, eliminando el calor. En motores diésel de servicio severo, solo un tercio del total de la energía producida es utilizado para mover el vehículo. Un tercio de la energía se va en los gases de escape y el tercio remanente se elimina del motor a través del refrigerante. Este calor eliminado proporciona el balance adecuado en el total del calor generado por el motor para asegurar su correcto funcionamiento. Un sobrecalentamiento puede dar como resultado la degradación acelerada del lubricante y posteriormente del propio motor.
La contaminación del lubricante con el anticongelante expone al motor a una mezcla de sustancias químicas muy poderosas y venenosas. Al igual que otros contaminantes peligrosos, como las partículas y la humedad, el potencial destructivo del anticongelante puede progresar hasta lograr una falla masiva del motor en un corto intervalo de tiempo.
El principal componente del anticongelante es el glicol, en forma de etilén glicol o propilén glicol, mezclado 50/50 con agua para formar un líquido refrigerante para transferir calor, elevar el punto de ebullición del agua (107 °C) y disminuir el punto de congelación (-35 °C).
Detección de anticongelante
El anticongelante de los motores de combustión interna es una mezcla de agua y algún tipo de glicol. Cuando hay una fuga de anticongelante hacia el lubricante de motor, normalmente el agua se evapora por las temperaturas de operación, pero el glicol reacciona con los aditivos del lubricante, destruyendo su capacidad dispersante. El hollín que se encontraba disperso se aglomera y forma una pasta gelatinosa, la cual, por su peso, se queda en el centro de la gota. El lubricante trata de salir por capilaridad, pero el hollín aglomerado lo obstaculiza. Eso hace que se genere una mancha deforme (no circular) y que en el centro de la gota quede una concentración de apariencia pastosa negra. Se apreciará un halo transparente circular que corresponde al básico lubricante.
En la gota de aceite se observará un depósito pegajoso tipo mayonesa negra en el centro de la gota, con una coloración verduzca, rojiza, dependiendo del color del anticongelante utilizado.

Fuente: El autor
Autor: Roberto Trujillo Corona
Empresa: Noria Latín América
Dinos qué te ha parecido el artículo
Artículos recomendados
5 Prácticas de Lubricación para mejorar el desempeño de sus Sistemas Hidráulicos

Mantenimiento industrial

Mantenimiento preventivo

Tolerancias en rodamientos

Publica tu artículo en la revista #1 de Mantenimiento Industrial
Publicar un artículo en la revista es gratis, no tiene costo.
Solo debes asegurarte que no sea un artículo comercial.
¿Qué esperas?
O envía tu artículo directo: articulos@predictiva21.com
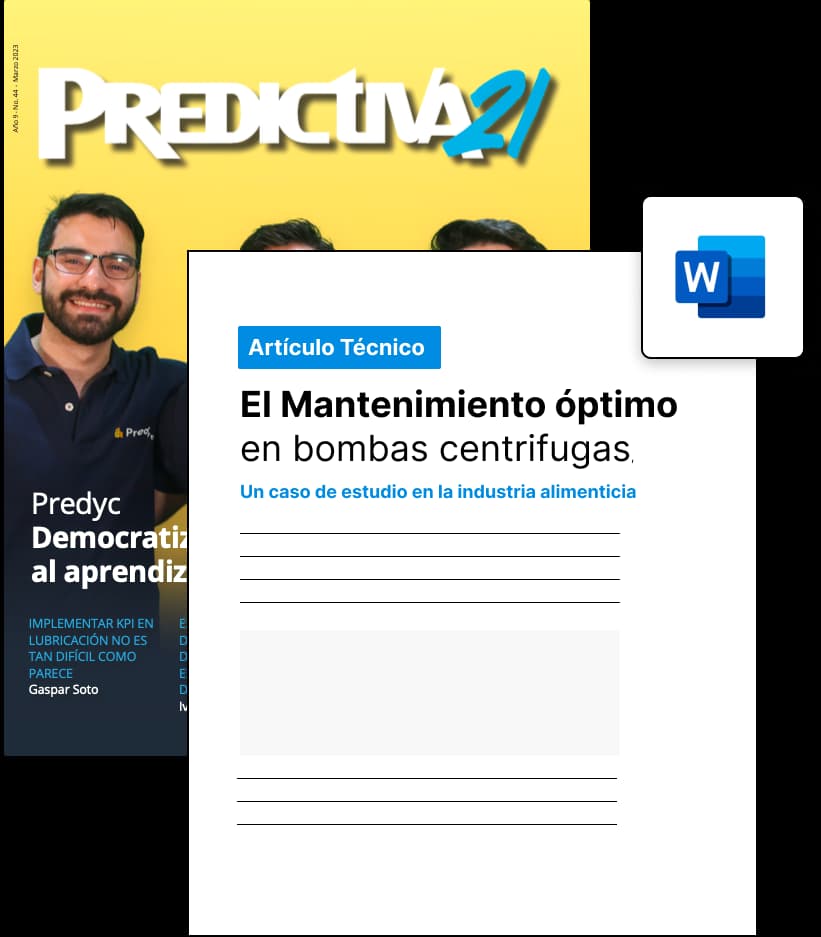
Uso y aplicación de la Prueba de Gota
Articulo 20 de noviembre de 2019La prueba de la gota de lubricante sobre papel filtro es una técnica que data del siglo XIX. En el área científica se le conoce como cromatografía plana en papel filtro y es usada para identificar la condición y degradación de lubricantes para motores de combustión interna a diésel, gasolina y gas. Es una prueba cualitativa que consiste en la separación por su peso molecular de los compuestos que se encuentran suspendidos y diluidos en el lubricante, a través de la capilaridad y uniformidad del papel Whatman #4. Por medio de esta prueba se separan los productos de degradación del lubricante (barniz, lacas, lodos) y contaminantes (hollín, anticongelante y combustible).
Al colocar sobre el papel el lubricante, este se desplaza por capilaridad de manera circular. Los compuestos más ligeros (como el combustible) viajarán más rápido, mientras que los más pesados (como el hollín y los productos de degradación) irán más lentos. Esto hace que el círculo que genera la gota tenga características muy específicas que permiten identificar de manera visual la presencia de condiciones anormales. Esta es una prueba cualitativa, por lo tanto, sirve solo para detectar una condición normal o anormal por apreciación visual. Con el tiempo y suficiente práctica podrá desarrollar sus habilidades de interpretación para identificar diferentes condiciones del lubricante.
¿Por qué es importante efectuar la prueba de la gota? Cada una de las condiciones identificadas por la prueba de la gota indican modos de falla diferentes que merecen ser investigados, ya que pueden causar severos daños a la maquinaria y acelerar la degradación del lubricante. Entre las condiciones que se detectan con esta prueba están las siguientes:
Hollín
El hollín es 98% carbón y sus partículas tienen forma casi esférica con tamaños que van desde 0.01 hasta 0.05 micrones. Estas partículas, mientras permanezcan pequeñas, no ponen en peligro los diferentes componentes del motor. Sin embargo, con el tiempo y el agotamiento de los aditivos del lubricante, estas tienden a aglomerarse y crecer en tamaño. Al no poder ser manejadas por el lubricante, estas partículas producen incremento en la viscosidad del lubricante y depósitos en el motor. Adicionalmente, al tratarse de carbón y crecer en tamaño, ocasiona desgaste abrasivo, principalmente en zonas donde la lubricación es a película límite. El aditivo dispersante en el lubricante se encarga de mantener el hollín finamente disperso, evitando su crecimiento y aglomeración. Excesivas cantidades de hollín agotan rápidamente la capacidad dispersante del lubricante formando lo que normalmente se conoce como lodos. A medida que se consume el dispersante, las partículas de hollín comienzan a aglomerarse y a depositarse sobre las superficies del motor impidiendo una correcta lubricación y flujo de aceite a través del filtro. Excesivas cantidades de hollín incrementan la viscosidad del lubricante ocasionando un mayor desgaste, al afectar el desempeño del antidesgaste, generando una falla prematura del motor.
El uso de motores con recirculación de gases de escape (EGR) ha incrementado el nivel de hollín en el lubricante, por lo que se han generado nuevos niveles de desempeño a fin de que estos lubricantes puedan manejar mayores concentraciones de hollín sin afectar sus propiedades y la protección de los motores.
Detección de hollín
La prueba de gota puede evaluar tanto la concentración de hollín en el lubricante como su estado de dispersión. La gota se inspecciona colocándola sobre una tableta de luz blanca, la cual permite que las condiciones de inspección sean consistentes.
Concentración o carga de hollín
La concentración de hollín en el lubricante depende de la condición del sistema de combustión, la condición del filtro de aire, de las condiciones y estilo de operación y del tiempo que el lubricante ha trabajado en el motor. Cuando un motor opera en condiciones anormales, con filtro de aire saturado, se ha excedido el tiempo de cambio de lubricante o es operado de manera incorrecta, la generación y la concentración de hollín en el lubricante será mayor.
Una gota grande y traslúcida o de tono ligeramente obscuro significa que la concentración de hollín es baja. Una alta concentración de hollín en el lubricante se observará en una gota obscura, no traslúcida. Mientras más obscura la gota, mayor será la concentración de hollín en el lubricante.

Fuente: El autor
Dispersión de hollín o dispersancia
El hollín en el lubricante puede estar disperso o aglomerado, lo que depende de la capacidad del lubricante para mantenerlo en suspensión. Cuando el hollín está disperso, significa que el aditivo del lubricante está haciendo su trabajo y mantiene las partículas de hollín finamente separadas. Al agotarse este aditivo, las partículas de hollín se aglomeran y crecen en tamaño y peso. La prueba de gota es la única técnica existente para identificar esta condición del lubricante.
Al efectuar la prueba de la gota y diseminarse el aceite sobre el papel Whatman, las partículas de hollín dispersas en el lubricante viajarán fácilmente con el básico lubricante y formarán un círculo grande y uniforme, un poco traslúcido o de tonalidad ligeramente obscura, dependiendo de la concentración de hollín. Cuando las partículas de hollín están aglomeradas, se observará un círculo con un diámetro más pequeño y un color más obscuro. Esto se considera una condición anormal que debe ser notificada e investigada.

Combustible
La contaminación o dilución con combustible es un fenómeno que se presenta en los motores de combustión interna en los cuales el combustible no quemado (diésel, gasolina, condensados del gas natural o LP) se acumulan en el cárter del motor. Una mezcla aire/combustible excesivamente rica o una combustión incompleta, ocasionan que cierta cantidad de combustible pase a través del sistema anillos/pistón/cilindros diluyendo el aceite del motor. Esta situación es más común en motores donde el combustible es inyectado a elevadas presiones, pasando a través de los anillos hacia el cárter del motor, incrementando el desgaste a causa de la dilución del lubricante y pérdida de la película.
Dado que los componentes menos volátiles del combustible tienen una elevada tendencia a condensarse, el nivel de dilución del lubricante está directamente relacionado con la volatilidad del combustible. Los combustibles con puntos finales de destilación muy elevados contienen una gran cantidad de compuestos poco volátiles que serán difíciles de quemar durante el proceso de combustión. Esto traerá como consecuencia una elevada dilución y una pérdida sustancial en la viscosidad del lubricante, lo que no permitirá la formación de una película de lubricante adecuada que mantenga las superficies separadas, incrementando el desgaste de los componentes del motor.
Un lubricante con una viscosidad baja como consecuencia de una contaminación con combustible no estará en capacidad de mantener separadas las superficies en movimiento, provocando el contacto metal-metal con el consiguiente desgaste de los componentes del motor.
Cursos recomendados




%252FImagen%252FRAMPREDYC-1730060420837.webp%3Falt%3Dmedia%26token%3D2634a7f0-988e-4022-b91f-382503e6e9db&w=3840&q=75)



Detección de combustible en el lubricante
El combustible es más ligero que el lubricante, por lo tanto, en caso de estar presente en el lubricante, viajará más rápido y se situará en la parte externa o borde de la circunferencia de la gota de aceite.
Para identificar la presencia de combustible, el papel con la gota de aceite debe colocarse bajo la lámpara de luz ultravioleta en una habitación con poca luz para evitar interferencia en la inspección. Los aromáticos contenidos en el combustible poseen características de fluorescencia cuando son inspeccionados bajo la luz ultravioleta. Un círculo fluorescente en el exterior de la gota de lubricante nos indicará la presencia de combustible.

Fuente: El autor
Anticongelante (glicol)
El anticongelante protege al motor del congelamiento y a sus componentes de la corrosión; al mismo tiempo juega un papel importante en el balance energético de los motores, eliminando el calor. En motores diésel de servicio severo, solo un tercio del total de la energía producida es utilizado para mover el vehículo. Un tercio de la energía se va en los gases de escape y el tercio remanente se elimina del motor a través del refrigerante. Este calor eliminado proporciona el balance adecuado en el total del calor generado por el motor para asegurar su correcto funcionamiento. Un sobrecalentamiento puede dar como resultado la degradación acelerada del lubricante y posteriormente del propio motor.
La contaminación del lubricante con el anticongelante expone al motor a una mezcla de sustancias químicas muy poderosas y venenosas. Al igual que otros contaminantes peligrosos, como las partículas y la humedad, el potencial destructivo del anticongelante puede progresar hasta lograr una falla masiva del motor en un corto intervalo de tiempo.
El principal componente del anticongelante es el glicol, en forma de etilén glicol o propilén glicol, mezclado 50/50 con agua para formar un líquido refrigerante para transferir calor, elevar el punto de ebullición del agua (107 °C) y disminuir el punto de congelación (-35 °C).
Detección de anticongelante
El anticongelante de los motores de combustión interna es una mezcla de agua y algún tipo de glicol. Cuando hay una fuga de anticongelante hacia el lubricante de motor, normalmente el agua se evapora por las temperaturas de operación, pero el glicol reacciona con los aditivos del lubricante, destruyendo su capacidad dispersante. El hollín que se encontraba disperso se aglomera y forma una pasta gelatinosa, la cual, por su peso, se queda en el centro de la gota. El lubricante trata de salir por capilaridad, pero el hollín aglomerado lo obstaculiza. Eso hace que se genere una mancha deforme (no circular) y que en el centro de la gota quede una concentración de apariencia pastosa negra. Se apreciará un halo transparente circular que corresponde al básico lubricante.
En la gota de aceite se observará un depósito pegajoso tipo mayonesa negra en el centro de la gota, con una coloración verduzca, rojiza, dependiendo del color del anticongelante utilizado.

Fuente: El autor
Autor: Roberto Trujillo Corona
Empresa: Noria Latín América
Dinos qué te ha parecido el artículo
Artículos recomendados
Cursos de mantenimiento preventivo: ¿Por qué deberías tomarlos?

8.8 Aplicación de Conceptos de las Cinco "S"

Detergencia en los aceites lubricantes de motores de combustión

Lanzamiento del nuevo libro "Cases on Optimizing the Asset Management Process"

Publica tu artículo en la revista #1 de Mantenimiento Industrial
Publicar un artículo en la revista es gratis, no tiene costo.
Solo debes asegurarte que no sea un artículo comercial.
¿Qué esperas?
O envía tu artículo directo: articulos@predictiva21.com
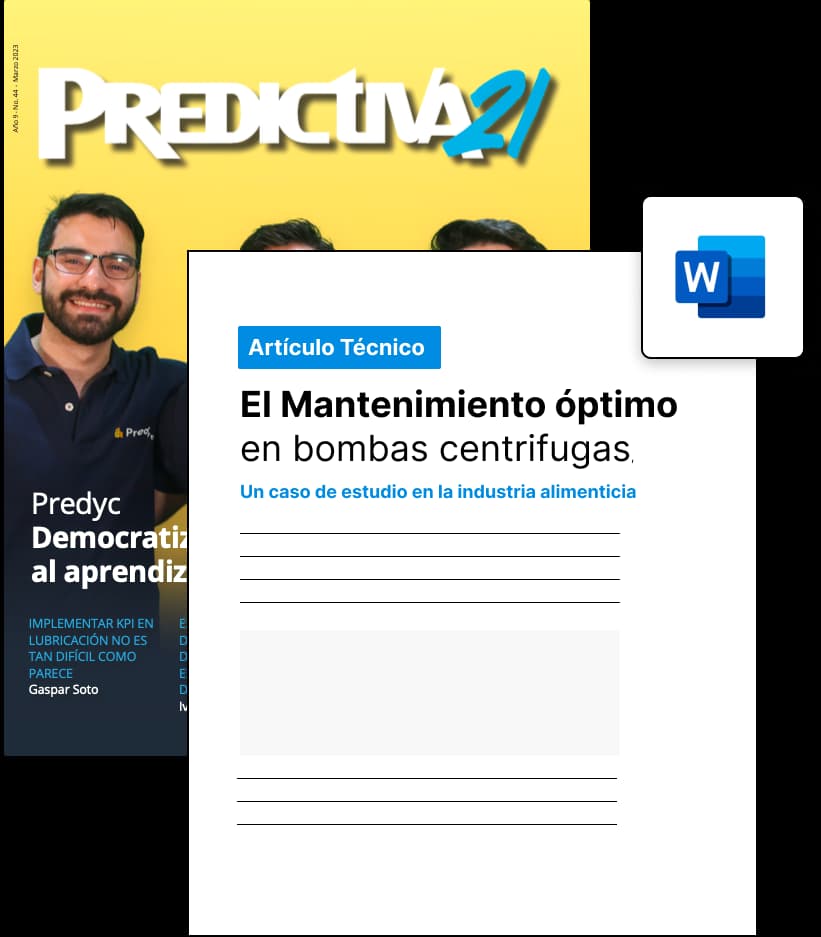