16.3.- Otras Consideraciones
Articulo7 de septiembre de 2021
En servicios que quedan fuera de las recomendaciones del API 610/ISO 13709 la responsabilidad por la selección de los materiales de construcción de las bombas no debe quedar completamente en manos del fabricante del equipo. Lo más recomendable en esos casos y cuando se deben usar materiales fuera de la cobertura de las normas es solicitar al fabricante que demuestre la viabilidad del material en el servicio propuesto mediante un listado de referencias donde, se indique los equipos que están siendo aplicados en servicios similares, el tiempo de servicio, las condiciones de operación y las capacidades.
En servicios de bombeo de petróleo, algunos especialistas recomiendan aceros aleados o inoxidables cuando para estos servicios no es requerido un material de este nivel de calidad. Para servicios de bombeo de crudo en rangos de mediana y alta energía se debe solicitar un casco de fundición de acero con componentes en rotativos en hierro fundido o en acero, tanto para lograr un buen nivel de costos de inversión inicial como para obtener la mantenibilidad y reparabilidad aceptable de los componentes de la bomba.
En la nomenclatura del API 610/ISO 13709 corresponde a los códigos S-1 y S-4; donde en la clase de materiales S-1 la carcasa y el eje son de acero al carbono y los impulsores de fundición de acero, en la clase de materiales S-4 la carcasa, los impulsores y el eje son de acero al carbono. Se debe tener cuidado en la selección de los materiales cuando se usan combinaciones fuera de lo establecido en las normas, así como en los acabados finales y holguras de rodaje para evitar agarrotamiento o “galling”.
Los fabricantes ofrecerán los materiales económicos para los servicios solicitados como carcasas de fundición de hierro o hierro nodular, el cual se puede aplicar en la gran mayoría de los servicios del área de producción y transporte de hidrocarburos, sin embargo, son materiales más difíciles de trabajar y de reacondicionar que el acero al carbono, adicional a que la ganancia en costos de inversión no son significativas.
Uno de los servicios con mayor complejidad desde el punto de vista de los materiales son los servicios para bombeo de agua salada, agua de mar o agua de formación, en estos servicios no es posible la utilización de aceros al carbono porque las tasas de corrosión y erosión son muy altas causando la perdida de los equipos en plazos muy cortos.
En ambientes donde existen cloruros como es el caso del agua de mar y agua de producción, los aceros inoxidables austeníticos de la serie 300 son sensibles y propensos a ser atacados por SCC (stress corrosion cracking), algunas soluciones dadas por fabricantes de bombas cubrir las superficies hidráulicas de las bombas de acero inoxidable austeniticas con pinturas y recubrimientos especiales para evitar el contacto del agua con el acero, sin embargo estas pinturas y recubrimientos con el uso se degradan o dañan dando pie al inicio de los ataques a estos aceros.
En algunas instalaciones marinas se utilizó para inyección de agua salada y de producción Nikel-Aluminum Bronce(NAB) que es resistente a la corrosión por picaduras e inter-granular en presencia de cloruros. Los mayores problemas observados en bombas multietapas que operaban a más de 69 bar (1000 psi) fue erosión en las carcasas a nivel de las conexiones inter-etapas, donde se formaron unos pequeños caminos que comunican las áreas inter-etapas deteriorando el rendimiento de las bombas.
En aplicaciones más recientes a partir de finales de los años 90 se ha generalizado el uso de los aceros Duplex en servicios, debido básicamente al éxito logrado con estos aceros en las instalaciones petroleras del Mar del Norte donde se están aplicando desde los años 80. Los aceros Duplexs se fabrican desde los años 30 del sigloXX, pero su uso estaba limitado a aplicaciones muy específicas debido a los reiterados problemas observados con la reparabilidad y soldabilidad de estos aceros.
Desde finales de los años 60 el uso de los aceros Duplex se extendió debido a la mejora de los procesos de fundición que permitieron la adición de mayores cantidades de nitrógeno a las aleaciones inoxidable lo cual estabiliza la Austenita y reduce la formación de fases intermedias.
Estos aceros están compuestos una mezcla proporcional de Austenita y Ferrita que constituye una estructura doble en la aleación. Los aceros Duplexs tienen mayor resistencia mecánica que los aceros Austeniticos tradicionales y alta resistencia a la corrosión por picaduras, a la corrosión inter-granular y a la corrosión por ataque de cloruros. Su principal debilidad es la tendencia a formar fases inter-metálicas cuando son sometidos a altas temperatura, lo cual da como resultado la fragilización de la aleación.
En la Industria Petroquímica se ha generalizado en algunas aplicaciones específicas, como es el caso del bombeo de fluidos ácidos o alcalinos, el uso de bombas centrífugas fabricadas con materiales no metálicos como el caso de los compuestos epóxidos reforzados con fibra de vidrio y los termoplásticos, estos materiales no están considerados ni en API 610 ni en la norma ASME B73.1.
Estos compuestos pueden ser modelados y reforzados con armazones metálicas para mejorar su resistencia y capacidad para soportar carga. La capacidad de los materiales no metálicos para soportar carga es muy variable va a depender de una serie de factores como son la calidad de la fabricación, el tipo de material, cuales son los refuerzos estructurales etc. Los compuestos no metálicos tienen mejor comportamiento a la abrasión que el acero inoxidable debido a que por la conformación de su superficie tienen menor coeficiente de fricción, además el óxido que recubre y protege el acero inoxidable es continuamente removido por los abrasivos.
Una limitación importante de los materiales no metálicos es su relativamente poca resistencia a altas temperatura, la mayoría de los materiales no metálicos usados en estas aplicaciones resisten temperaturas entre 60 y 120 °C (140 y 250 °F).
Los termoplásticos más usa son el PVC y el CPVC que tienen buenas propiedades para resistir corrosión por acido, por productos alcalinos, sales disueltas y muchos otros químicos. Tiene limitaciones para manejar solventes y aromáticos. El CPVC tiene mejor comportamiento que el PVC para manejar líquidos corrosivos calientes.
El polipropileno (PP) tiene baja Gravedad Específica (0,91), pero posee buena resistencia a los solventes, a los ácidos y los productos alcalinos.
Otro producto usado es el PTFE (politetrafluoroetileno) es uno de los productos que tiene mayor resistencia a la temperatura 260 °C (500 °F), su mayor desventaja es que comparado con otros materiales no metálicos posee baja resistencia a la abrasión y a los esfuerzos por tensión.
Dinos qué te ha parecido el artículo
Artículos recomendados
Investigación de Fallas, Reparación y Remedio Operativo Mínimo. Bomba de Alto Rendimiento

Aplicación del Mantenimiento Centrado en Confiabilidad al Brazo de Carga de Amoniaco
-1749059308029.png%3Falt%3Dmedia%26token%3D863bb934-1d7e-476d-b14e-ff12b481e413&w=256&q=75)
Comportamiento típico de los inventarios para mantenimiento

Planificación de mantenimiento industrial: ventajas

Publica tu artículo en la revista #1 de Mantenimiento Industrial
Publicar un artículo en la revista es gratis, no tiene costo.
Solo debes asegurarte que no sea un artículo comercial.
¿Qué esperas?
O envía tu artículo directo: articulos@predictiva21.com
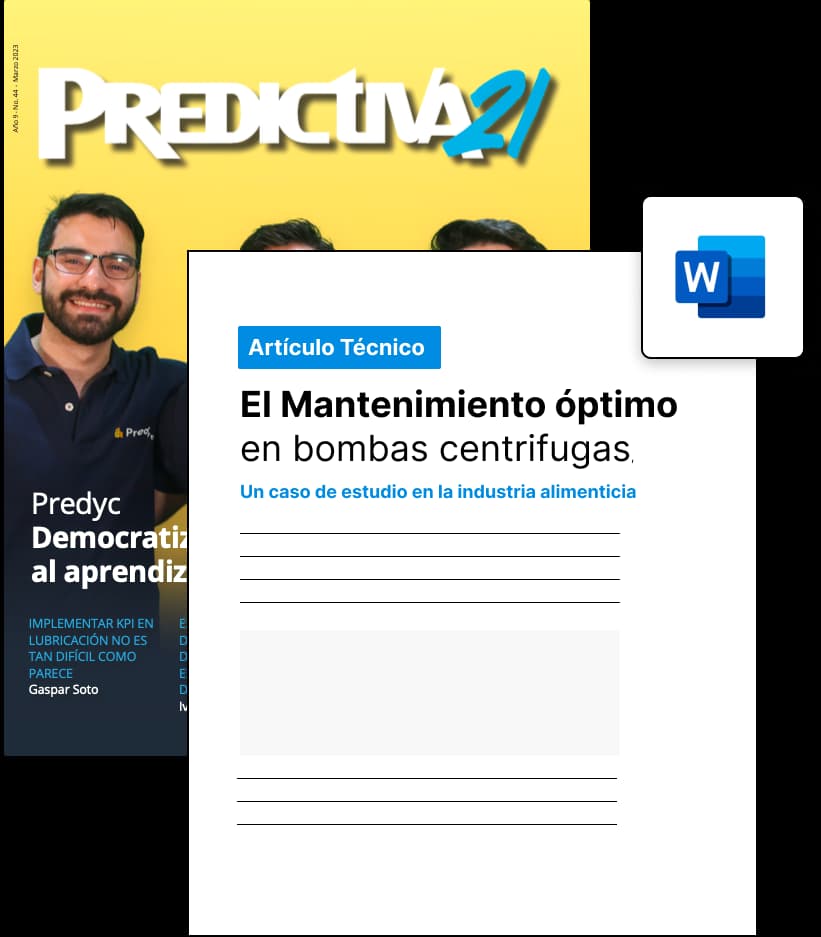
16.3.- Otras Consideraciones
Articulo 7 de septiembre de 2021En servicios que quedan fuera de las recomendaciones del API 610/ISO 13709 la responsabilidad por la selección de los materiales de construcción de las bombas no debe quedar completamente en manos del fabricante del equipo. Lo más recomendable en esos casos y cuando se deben usar materiales fuera de la cobertura de las normas es solicitar al fabricante que demuestre la viabilidad del material en el servicio propuesto mediante un listado de referencias donde, se indique los equipos que están siendo aplicados en servicios similares, el tiempo de servicio, las condiciones de operación y las capacidades.
En servicios de bombeo de petróleo, algunos especialistas recomiendan aceros aleados o inoxidables cuando para estos servicios no es requerido un material de este nivel de calidad. Para servicios de bombeo de crudo en rangos de mediana y alta energía se debe solicitar un casco de fundición de acero con componentes en rotativos en hierro fundido o en acero, tanto para lograr un buen nivel de costos de inversión inicial como para obtener la mantenibilidad y reparabilidad aceptable de los componentes de la bomba.
En la nomenclatura del API 610/ISO 13709 corresponde a los códigos S-1 y S-4; donde en la clase de materiales S-1 la carcasa y el eje son de acero al carbono y los impulsores de fundición de acero, en la clase de materiales S-4 la carcasa, los impulsores y el eje son de acero al carbono. Se debe tener cuidado en la selección de los materiales cuando se usan combinaciones fuera de lo establecido en las normas, así como en los acabados finales y holguras de rodaje para evitar agarrotamiento o “galling”.
Los fabricantes ofrecerán los materiales económicos para los servicios solicitados como carcasas de fundición de hierro o hierro nodular, el cual se puede aplicar en la gran mayoría de los servicios del área de producción y transporte de hidrocarburos, sin embargo, son materiales más difíciles de trabajar y de reacondicionar que el acero al carbono, adicional a que la ganancia en costos de inversión no son significativas.
Uno de los servicios con mayor complejidad desde el punto de vista de los materiales son los servicios para bombeo de agua salada, agua de mar o agua de formación, en estos servicios no es posible la utilización de aceros al carbono porque las tasas de corrosión y erosión son muy altas causando la perdida de los equipos en plazos muy cortos.
En ambientes donde existen cloruros como es el caso del agua de mar y agua de producción, los aceros inoxidables austeníticos de la serie 300 son sensibles y propensos a ser atacados por SCC (stress corrosion cracking), algunas soluciones dadas por fabricantes de bombas cubrir las superficies hidráulicas de las bombas de acero inoxidable austeniticas con pinturas y recubrimientos especiales para evitar el contacto del agua con el acero, sin embargo estas pinturas y recubrimientos con el uso se degradan o dañan dando pie al inicio de los ataques a estos aceros.
En algunas instalaciones marinas se utilizó para inyección de agua salada y de producción Nikel-Aluminum Bronce(NAB) que es resistente a la corrosión por picaduras e inter-granular en presencia de cloruros. Los mayores problemas observados en bombas multietapas que operaban a más de 69 bar (1000 psi) fue erosión en las carcasas a nivel de las conexiones inter-etapas, donde se formaron unos pequeños caminos que comunican las áreas inter-etapas deteriorando el rendimiento de las bombas.
En aplicaciones más recientes a partir de finales de los años 90 se ha generalizado el uso de los aceros Duplex en servicios, debido básicamente al éxito logrado con estos aceros en las instalaciones petroleras del Mar del Norte donde se están aplicando desde los años 80. Los aceros Duplexs se fabrican desde los años 30 del sigloXX, pero su uso estaba limitado a aplicaciones muy específicas debido a los reiterados problemas observados con la reparabilidad y soldabilidad de estos aceros.
Desde finales de los años 60 el uso de los aceros Duplex se extendió debido a la mejora de los procesos de fundición que permitieron la adición de mayores cantidades de nitrógeno a las aleaciones inoxidable lo cual estabiliza la Austenita y reduce la formación de fases intermedias.
Estos aceros están compuestos una mezcla proporcional de Austenita y Ferrita que constituye una estructura doble en la aleación. Los aceros Duplexs tienen mayor resistencia mecánica que los aceros Austeniticos tradicionales y alta resistencia a la corrosión por picaduras, a la corrosión inter-granular y a la corrosión por ataque de cloruros. Su principal debilidad es la tendencia a formar fases inter-metálicas cuando son sometidos a altas temperatura, lo cual da como resultado la fragilización de la aleación.
En la Industria Petroquímica se ha generalizado en algunas aplicaciones específicas, como es el caso del bombeo de fluidos ácidos o alcalinos, el uso de bombas centrífugas fabricadas con materiales no metálicos como el caso de los compuestos epóxidos reforzados con fibra de vidrio y los termoplásticos, estos materiales no están considerados ni en API 610 ni en la norma ASME B73.1.
Estos compuestos pueden ser modelados y reforzados con armazones metálicas para mejorar su resistencia y capacidad para soportar carga. La capacidad de los materiales no metálicos para soportar carga es muy variable va a depender de una serie de factores como son la calidad de la fabricación, el tipo de material, cuales son los refuerzos estructurales etc. Los compuestos no metálicos tienen mejor comportamiento a la abrasión que el acero inoxidable debido a que por la conformación de su superficie tienen menor coeficiente de fricción, además el óxido que recubre y protege el acero inoxidable es continuamente removido por los abrasivos.
Una limitación importante de los materiales no metálicos es su relativamente poca resistencia a altas temperatura, la mayoría de los materiales no metálicos usados en estas aplicaciones resisten temperaturas entre 60 y 120 °C (140 y 250 °F).
Los termoplásticos más usa son el PVC y el CPVC que tienen buenas propiedades para resistir corrosión por acido, por productos alcalinos, sales disueltas y muchos otros químicos. Tiene limitaciones para manejar solventes y aromáticos. El CPVC tiene mejor comportamiento que el PVC para manejar líquidos corrosivos calientes.
El polipropileno (PP) tiene baja Gravedad Específica (0,91), pero posee buena resistencia a los solventes, a los ácidos y los productos alcalinos.
Otro producto usado es el PTFE (politetrafluoroetileno) es uno de los productos que tiene mayor resistencia a la temperatura 260 °C (500 °F), su mayor desventaja es que comparado con otros materiales no metálicos posee baja resistencia a la abrasión y a los esfuerzos por tensión.
Dinos qué te ha parecido el artículo
Artículos recomendados
6.1 Las Siete Preguntas Básicas del M.C.C

8 pasos para un plan de Mantenimiento eléctrico

Entrevista Angeles Ysidro

Curso de planificación en mantenimiento

Publica tu artículo en la revista #1 de Mantenimiento Industrial
Publicar un artículo en la revista es gratis, no tiene costo.
Solo debes asegurarte que no sea un artículo comercial.
¿Qué esperas?
O envía tu artículo directo: articulos@predictiva21.com
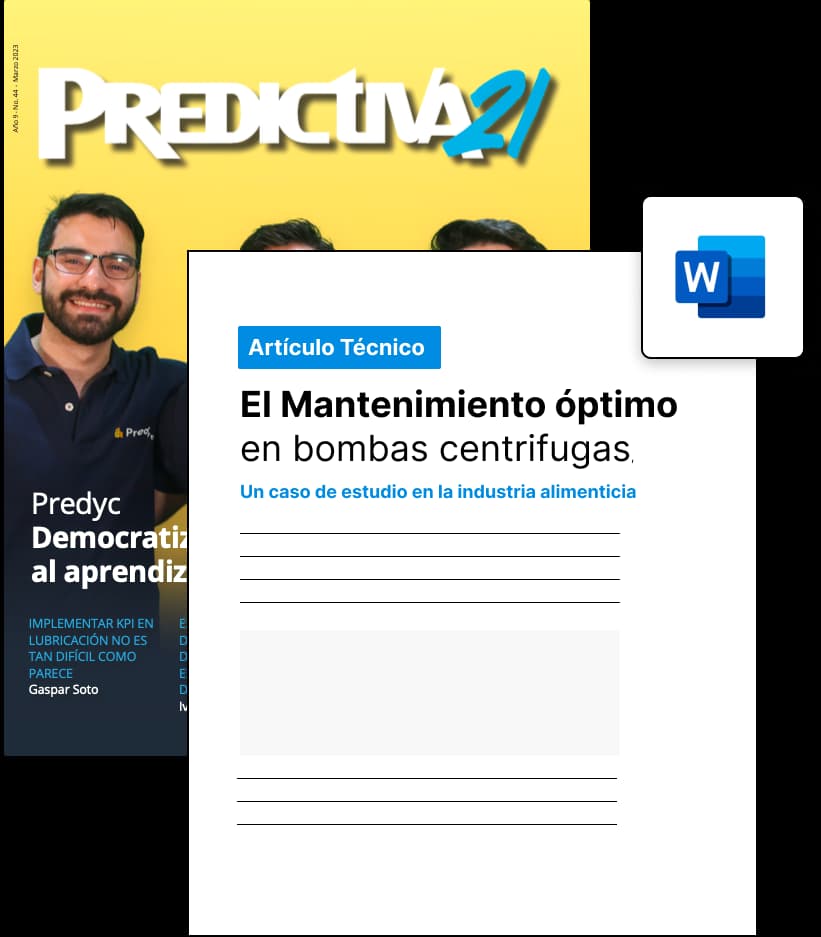