2.3.- Carcasa
Libros21 de agosto de 2021
La carcasa es el cuerpo de la bomba centrífuga, en este capítulo se hará diferencia entre el diseño externo y el diseño interno de la carcasa de las bombas centrífugas. El diseño interno de la carcasa permite capturar el líquido a alta velocidad transformando la energía cinética, que trae el fluido, en presión. Externamente las formas y elementos constructivos de las carcasas permiten soportar las fuerzas y las fuerzas generadas en el proceso de bombeo.
2.3.1.- Carcasa Interna
Los diseños de las bombas centrífugas de procesos que son usadas en la Industria Petrolera están regulados fundamentalmente por las normas API 610/ISO 13079 y por la ASME B73.1.
Las carcasas de las bombas fabricadas bajo el B73.1 manejan una presión máxima de 20 bars (300 psig) a una temperatura de 150 °C (300 °F); las bombas diseñadas siguiendo el API 610/ISO 13709 pueden trabajar con presiones de hasta 52 bars (750 psig) a una temperatura de 260 °C (500 °F). En ambos casos los diseños para presiones mayores son considerados diseños especiales.
En los diseños iniciales de las bombas centrífugas se utilizaban carcasas cuadradas, hasta que en 1839 el inventor norteamericano W. H. Andrew introdujo un modelo de carcasa tipo espiral bastante rudimentaria. Los diseños o arreglos fundamentales de las carcasas de las bombas centrífugas son la voluta y el difusor, a continuación, una breve descripción de los dos diseños de carcasa.
2.3.1.1.- Voluta
La configuración tipo voluta de la carcasa, en una bomba centrífuga, se asemeja a la forma de un espiral.
Los tres principales tipos de carcasa tipo voluta son:
- Voluta simple.
- Doble voluta.
- Voluta concéntrica.
a.- Voluta simple
Por su sencillez, la voluta simple es el tipo más común de construcción, está generalizado en las bombas de baja y media energía debido a que genera bajos costos relativos de fabricación, son relativamente sencillas de maquinar y ajustar. La figura 2-13 muestra el cuerpo de una carcasa tipo voluta simple.

Fuente:Castwel Foundry Agra, Uttar Pradesh
Este tipo de diseño de carcasa resulta práctico, debido a que la conversión de energía cinética en presión se realiza de forma eficiente. La forma en espiral de la voluta permite un incremento del área a una razón proporcional, que mantiene al líquido, que es descargado del impulsor, a una velocidad constante hasta que es difundido en la carcasa.
Clásicamente la velocidad de referencia tomada para el diseño de las volutas es la velocidad en el Punto de Mejor Eficiencia(BEP) y las velocidades en otros puntos de operación son estimadas en función de la velocidad del fluido en el BEP. En la actualidad el diseño computarizado de las bombas ha permitido modelar las velocidades del fluido en las diferentes condiciones de operación.
La figura N° 2-14 presenta el esquema de una bomba con carcasa tipo voluta mostrando las flechas orientadas radialmente que indican la dirección de las fuerzas, que el fluido está ejerciendo contra el centro de la bomba. La principal desventaja de este tipo de carcasa es que el esfuerzo radial se incrementa debido al cambio constante del área seccional de la carcasa.

Fuente:www.pumpfundamentals.com/DOUBLEVolute.pdf
En la figura 2-14 se observa que a medida que el caracol de la carcasa se aproxima a la garganta de salida las fuerzas radiales se incrementan sustancialmente. La magnitud de estas fuerzas es indicada por el tamaño de las flechas, las cuales se incrementan progresivamente al aproximarse al área de descarga.
Existen problemas asociados al desbalance de las fuerzas radiales que causan diferentes tipos de eventos. El esfuerzo radial excesivo puede causar la deflexión del eje, sobrecarga en los cojinetes radiales y axiales, daños en las caras de los sellos mecánicos, daños en las estoperas de las cajas de cojinetes y otros efectos que acortan la vida operativa de la bomba.
En las bombas de bajo caudal usadas para aplicaciones especiales, como las bombas para manejar sólidos y desechos, se acostumbra a usar carcasas de voluta simple.
b.- Doble voluta
La carcasa de doble voluta se utiliza principalmente en las bombas diseñadas siguiendo el API 610/ISO 13709 o en las bombas de gran capacidad. En las carcasas de doble voluta se incorpora una vena interna a lo largo del espiral de la carcasa. La figura N° 2-15 muestra el diagrama en corte de una bomba con carcasa de doble voluta, mostrando la vena interna y la distribución de fuerzas radiales.
Este diseño de carcasa reduce el desbalance de presiones radiales alrededor de la periferia del impulsor, mediante la división del flujo total y reducción relativa del área de la voluta, equilibrando de esta forma las fuerzas radiales cuando la bomba trabaja a caudales fuera del caudal de diseño.
Esta modificación de la voluta aumenta la vida de los cojinetes radiales, ya que reduce las fuerzas radiales transmitidas al eje entre 1/6 y 1/3 de las fuerzas observadas en bombas con voluta simple.

Fuente:www.pumpfundamentals.com/DOUBLEVolute.pdf
En el pasado la fundición de las carcasas de doble voluta en bombas de baja capacidad representaba un problema porque sé hacia muy difícil que la vena de separación que divide la voluta quedara bien fundida y sin imperfecciones. La figura 2-16 muestra una carcasa doble voluta fundida mostrando la vena de separación.
Las imperfecciones causan altas perdidas de energía en la bomba, tanto hidráulicas como por fricción. En la actualidad las técnicas de fundición se han perfeccionado y permiten un mejor control de los acabados y de las áreas de los pasajes de las volutas dobles.
La fabricación de estas carcasas resulta más costosa y se experimenta una reducción de la Eficiencia de estas bombas con respecto a las bombas de voluta simple de entre 1 y 2%, debido al incremento de la fricción en las superficies adicionales. Sin embargo, las ventajas hidráulicas superan cualquier pequeño inconveniente que se pueda observar en estas bombas, siendo ampliamente usadas en procesos y aplicaciones exigentes.

Fuente:http://www.cixihuili.com/html/product_174.html
c.- Voluta concéntrica
En contraparte a las bombas de voluta tipo espiral existen las volutas concéntricas, muy comunes en bombas de relativamente bajo costo, alto Cabezal de Descarga relativo y baja Velocidad Específica(NS). En estas bombas la carcasa es circular y mantiene una distancia fija con el diámetro exterior del impulsor. La figura 2-17 muestra el modelo de una bomba con carcasa concéntrica.

Fuente: www.gouldspumps.com/download_files/lf3196_i_FRAME/
La carcasa concéntrica es ampliamente utilizada en bombas de acero inoxidable fabricadas por estampado y cuando las carcasas son fabricadas por fundición se reduce considerablemente el trabajo de maquinado y la complejidad de los moldes. Este tipo de carcasa se aplica en bombas que acomodan impulsores de diferentes diámetros o que requieren que los pasajes de la carcasa sean maquinados en detalle, como es el caso de las bombas sanitarias, bombas criogénicas, etc.
2.3.1.2.- Fuerzas Radiales
Como fue explicado en la sección anterior que habla de las carcasas tipo voluta, en el proceso de bombeo centrífugo se generan fuerzas radiales y axiales que actúan sobre los componentes como son impulsores, sellos mecánicos, ejes, cojinetes etc. Parte del conocimiento de las bombas centrífugas es entender cómo actúan estas fuerzas en el interior de la bomba.
Una aproximación de los valores de los esfuerzos radiales en bombas de procesos es dada por la ecuación N° 2-4 de Esfuerzo Radial en una bomba centrífuga tal como sigue a continuación:
![[2-4]](/_next/image?url=https%3A%2F%2Ffirebasestorage.googleapis.com%2Fv0%2Fb%2Fpredyc2023.appspot.com%2Fo%2FArticulosP21%252F2-3-carcasa%252Fimage-137.png%3Falt%3Dmedia%26token%3D2a50bfbf-7638-4264-b03b-898f0af769c1&w=640&q=75)
F:Esfuerzo radial, en Libras.
H:CabezalDiferencial de la bomba, en Pies.
D2: Diámetro del impulsor, en Pulgadas.
B2: Ancho del impulsor en el área de descarga, en Pulgadas.
K: Constante, definida con laecuación N° 2-5
Donde K es:
![[2-5]](/_next/image?url=https%3A%2F%2Ffirebasestorage.googleapis.com%2Fv0%2Fb%2Fpredyc2023.appspot.com%2Fo%2FArticulosP21%252F2-3-carcasa%252Fimage-138.png%3Falt%3Dmedia%26token%3D9ced97a4-5037-4c5c-b747-8221997d99c2&w=640&q=75)
Q: Caudal a cualquier capacidad, en gpm.
QBEP: Caudal en el BEP,Punto de Mejor Eficiencia, en gpm.
Si observamos la figura N° 2-18 podemos ver cómo influye en el esfuerzo radial de las bombas centrífugas el operar fuera del Punto de Mejor Eficiencia(BEP).
La figura contiene el comportamiento del esfuerzo radial para diferentes diseños de carcasa tipo voluta. Como se observa en la gráfica, que es referencial, usando carcasas de doble voluta se pueden lograr reducciones del esfuerzo radial en más de un 40% cuando se opera fuera del BEP.

Fuente: Centrifugal pump user’s guidebook: problems and solutions Por S. Yedidiah Charter 10.
Cuando se tiene una voluta simple o estándar a 100% del caudal de diseño el esfuerzo radial no supera más del 20% del esfuerzo que se alcanza en el punto de cierre o “shutoff”, cuando la válvula de descarga está completamente cerrada, es allí cuando el esfuerzo radial es máximo en las carcasas tipo voluta simple o Standard.
Al desplazarse el caudal tanto a la derecha como a la izquierda del BEP, Punto de Mejor Eficiencia el esfuerzo radial aumenta considerablemente. Cuando se usa una carcasa tipo voluta, pero concéntrica el balance de las fuerzas radiales mejora considerablemente reduciendo el esfuerzo radial máximo a un 60% del esfuerzo total alcanzado con una carcasa de voluta simple en espiral.
Finalmente, con el arreglo de doble voluta las fuerzas radiales están completamente equilibradas, lo que reduce la fuerza radial máxima del equipo a un 20% del total del esfuerzo radial alcanzado en una bomba de voluta simple del tipo espiral.
Las fuerzas radiales excesivas son las principales causantes de la deflexión de los ejes por arriba de lo esperado, lo cual origina los daños prematuros de los siguientes componentes: anillos de desgaste los cuales se erosionan por roce, los cojinetes que soportan mayores fuerzas que las esperadas normalmente, los sellos mecánicos que se desgastan de forma no uniforme y son afectados por el aumento en el calor generado en las superficies de contacto y puede causarhasta la fatiga del eje cuando las fuerzas radiales son cíclicas.
Existen otros elementos del diseño de la voluta que pudiese influenciar en la fluctuación de las fuerzas radiales como por ejemplo la holgura entre el radio exterior del impulsor y la lengüeta de la voluta.
2.3.1.3.- Difusor
La construcción tipo difusor en una carcasa, es fundamentalmente una serie de alabes o paletas fijas alrededor del impulsor.
La carcasa tipo difusor trabaja de la siguiente forma: los alabes reciben el líquido descargado por el impulsor reduciéndole la velocidad, usando para ello la orientación de los ángulos de entrada y salida, esta acción convierte la energía cinética del líquido en energía de presión, adicionalmente dirigen el líquido a la boquilla de descarga.
La figura N° 2-19 muestra un diagrama de una bomba construida con una carcasa tipo difusor, donde es posible observar los alabes fijos.

Fuente:Flowserve/PROS+SE/Release 3.03a
Históricamente el primer desarrollo de carcasas tipo difusor del que se tenga conocimiento fue el patentado, en 1875, por el científico Inglés Osborne Reinold. La figura N° 2-20 muestra la fotografía de un difusor para bombas centrífugas.
El diseño de carcasa interna tipo difusor es aplicado principalmente a bombas de ingeniería donde se requiere el manejo de mayores volúmenes de fluidos con presiones medias y altas, utilizando dimensiones más reducidas a las que pudiesen resultar de utilizar una bomba con carcasa tipo voluta.

Fuente:Fotografiado por el autor.
La principal desventaja en la utilización de las bombas con difusor está en su complejidad, que incrementa los costos de fabricación.
Existe diseños de carcasa tipo difusor donde los alabes guías son variables es decir pueden ser ajustados manualmente si se prevén cambios prolongados en los regímenes de flujo. Esto es con la finalidad de permitir mayor Eficiencia y el acoplamiento con las exigencias del sistema, dando flexibilidad para operar en rangos más amplios de caudal.
2.3.2.- Interacción Carcasa – Impulsor
La interacción entre la carcasa y los impulsores en el interior de la bomba es fundamental para el comportamiento hidráulico adecuado del equipo. Para lograr un buen desempeño hidráulico se deben mantener las unas dimensiones críticas entre los impulsores y la carcasa con la finalidad de reducir los choques hidráulicos, las pulsaciones y el ruido que se genera como resultado de la conversión de la energía cinética en energía de presión. Estas dimensiones se describen a continuación.
En la figura N° 2-21 se muestran la dimensión crítica “A” o GAP “A” y la dimensión crítica “B” o GAP “B”, en la interacción carcasa- impulsor.
La dimensión “A” (GAP “A”, en la figura 2-21) es la distancia entre el tope del impulsor y la garganta de entrada a la voluta o difusor, con ella se controlan las presiones en la parte posterior del impulsor, reduciendo las fuerzas axiales. Tanto para el diseño de carcasa tipo voluta como para las carcasas tipo difusores la dimensión “A” debe estar en el orden de 1,27 mm (0,050 pulgadas).

Fuente: Reliability-Driven Pump Maintenance: by Terry Hernandez_The Pump Handbook series.
El corte de los impulsores para el ajuste del Cabezal puede traer complicaciones con la dimensión “A” generando vibraciones axiales, por lo general de alta frecuencia, los impulsores de doble succión son especialmente sensibles a problemas relacionados con el incremento de la dimensión “A”.
La dimensión “B” (GAP “B”) es la distancia entre el tope del impulsor y la lengüeta de la voluta (Cut Water) o la punta de los difusores. Con ella se controla el esfuerzo y la amplitud de los choques hidráulicos principalmente los causados por el paso de los alabes. Para las bombas con difusores la dimensión “B” debe estar entre el 4 y 12% del diámetro del impulsor, con un valor preferencial del 6% y para las bombas con voluta debe estar entre el 6 y 12%, con un valor preferencial del 10% del diámetro del impulsor.
El uso o aplicación en una bomba del diámetro más pequeño en un determinado tipo de impulsor causa el incremento de la turbulencia en el interior de la carcasa, específicamente en la entrada a la voluta o difusor propiciando la erosión y las pulsaciones. Es recomendable usar el mayor diámetro posible en los impulsores disponibles o hacer el ajuste del GAP “A” o “B” para evitar estos problemas. Una gran variedad de fallas, en los impulsores de las bombas centrífugas, están relacionadas con la incorrecta fijación de estas dimensiones.
Las pulsaciones causadas por la dimensión “A” (GAP “A”) superior al mínimo permitido, combinado con un flujo reducido en la bomba puede causar la rotura de los impulsores a nivel del borde de ataque de los alabes a la descarga.
Las pulsaciones en bombas que estén siendo operadas a bajo flujo no deben superar el 5% del Cabezal desarrollado por la bomba; en condiciones de flujo normal las pulsaciones deben ser irrelevantes. Con el incrementando del GAP “B” de 1% a 6% las pulsaciones hidráulicas se pueden reducir de entre 80 y 85%
Los efectos de la incorrecta fijación de las dimensiones “A” y “B” alcanzan también a los sellos mecánicos y los cojinetes, debido a la variación constante de las fuerzas axiales de las bombas.
2.3.2.1.- Paso de Alabe
Existe un fenómeno denominado Paso de Alabe que se presenta cuando se ajusta inadecuadamente el GAP “B”. El fenómeno ocurre cuando la holgura es inadecuada y existe mucha proximidad entre la lengüeta de entrada al canal de descarga de la bomba o “Cut Water”, y el diámetro exterior del impulsor causando el aumento de la velocidad del líquido en este punto, por balance y conservación de la energía este aumento de velocidad provoca la reducción de la presión del líquido en esta área dando como resultado una vaporización del líquido, si se alcanza la presión de vapor (HVP) de la mezcla. Es una cavitación localizada ya que inmediatamente, aguas arriba de la lengüeta, las burbujas colapsan al incrementarse la presión del sistema.
Las principales normas para las bombas centrífugas como la API 610/ISO 13709 en la sección 6 “Basic Design” en el párrafo 6.1.15 pide que se aplique esta regla, sobre todo en las bombas con Cabezales mayores a 200 m (650 pies) por etapa y de al menos 225 KW (300 HP) por etapa, con la finalidad de reducir la vibración a las frecuencias correspondiente al Paso de Alabe, “Vane Passing”. Debido a que problemas de ajuste de las dimensiones “A” y “B” en bombas de este tamaño causarían daños importantes en los sellos, cojinetes y otros componentes causado por las vibraciones y el desbalance de fuerzas axiales.
Los daños o perturbaciones causadas por este fenómeno van a depender de los niveles de energía de la bomba. Cuando se producen daños se observa desgaste de la lengüeta de descarga de la carcasa o “Cut Water”, y a nivel de impulsor se observan daños en el centro del alabe en la cara activa en el topo del impulsor.
Desde el punto de vista de las vibraciones mecánicas estas se manifiestan a una frecuencia que es el resultante de la multiplicación de la velocidad de rotación del rotor de la bomba, multiplicada por el número de alabes del impulsor incluyendo las armónicas a 2x y 3x, por ejemplo, si la bomba centrífuga tiene una velocidad de 3.600 RPM y cinco alabes en el impulsor el paso de alabe se manifiesta a 18.000 RPM con armónicas a 36.000 y 54.000 RPM. La magnitud de la vibración va a depender de los niveles de energía de la bomba y del ajuste del GAP “B”.
Cuando se va a ajustar el diámetro de un impulsor se debe realizar una evaluación del comportamiento hidráulico de la bomba antes de realizar el ajuste con la finalidad de evitar las posibles complicaciones de un ajuste inadecuado de las dimensiones “A” y “B”.
Cursos recomendados
-1730145694747.webp%3Falt%3Dmedia%26token%3D719f647e-063f-47e9-a9f4-c3b59cb3a8ab&w=3840&q=75)



%252FImagen%252Frcm-1730083250826.webp%3Falt%3Dmedia%26token%3D3775356a-7b11-4c44-b21f-45b3409fb9ed&w=3840&q=75)

%252FImagen%252FRAMPREDYC-1730060420837.webp%3Falt%3Dmedia%26token%3D2634a7f0-988e-4022-b91f-382503e6e9db&w=3840&q=75)

2.3.3.- Diseño Externo de la Carcasa
Existen diferentes formas y diseños para soportar externamente la carcasa de las bombas centrífugas, los principales son soportarla en la parte inferior o en el pie (foot mounted), montaje en la parte central o en pedestal (Center line mounted) y las bombas con carcasa en línea (inline casing).
2.3.3.1.- Montaje en el Pie
Las bombas que son montadas en el pie son las bombas generales de procesos como las fabricadas bajo la norma ASME B73.1 y corresponde a la designación OH1 en la nomenclatura del API 610. De acuerdo con el API 610 11ava edición para bombas del tipo BB1, BB2, BB3, y BB5 si la temperatura de servicio de la bomba es menor a 150 °C (300 °F) (temperatura de servicio relativamente baja) se pueden usar carcasas montadas en el pie.
Por su diseño y características estas bombas no son fabricadas para ser sometidas a grandes cargas o temperaturas. Los acabados de estas bombas son variados y dependen fundamentalmente de la complejidad de la aplicación para la cual son fabricadas, ellas no están diseñadas para soportar altos momentos torsionales y los costos relacionados con la implantación (inversión inicial) son significativamente más bajos que los costos de las bombas fabricadas siguiendo el API 610. La figura 2-22 muestra una bomba con montaje en el pie.

Fuente: SULZER PUMPS, ANSI Process Pumps CPT adventage.
2.3.3.2.- Montaje Central
Las bombas de montaje central son las fabricadas bajo la norma API 610/ISO 13709, corresponden a la designación OH2 del API 610. La figura 2-23 muestra una bomba de montaje central.

Fuente:www.sulzerpumps.com/desktopdefault.aspx
Esta configuración, de montaje central, le permite a la bomba manejar mayores temperaturas y presiones. La razón para usar un montaje central es que minimiza las distorsiones causadas por las altas temperaturas y por los esfuerzos. Las tuberías y los equipos impulsores poseen gradientes de expansión diferentes, cuando se fija la bomba en el centro, la expansión térmica de la carcasa se realiza de forma uniforme y sin interferencias.
En este diseño las aletas de fijación de la carcasa están unidas en el eje central del cuerpo de la bomba, por lo que la expansión térmica de la carcasa se produce de forma uniforme evitando de esta forma la desalineación, la distorsión de la carcasa y el exceso de esfuerzos radiales y axiales sobre los rotores.
2.3.3.3.- Montaje en Línea
En las bombas con carcasa en línea la succión y la descarga están alineadas y el cuerpo de la bomba tiene una configuración que le permite soportar un motor vertical. La figura Nº 2-24 muestra el diagrama de una bomba con montaje en línea.
El cuerpo de la bomba no posee ningún tipo de soporte para la carcasa que se fije a un “skid” de metal o base estructural y pueden ser soportadas por las tuberías que están conectadas a sus bridas.
Las bombas en línea van de capacidades y tamaños pequeños a medianos, debido a la limitación que representa el no tener un soporte firme y una base estructural. El uso de las bombas verticales en línea está muy extendido en las refinerías, plantas petroquímicas y mejoradores de petróleo debido a su capacidad para ahorrar espacio.

Fuente:www.fochpump.com/SLB-Vertical-Single-stage-Do.
La configuración de esta bomba le permite ubicar el motor en posición vertical y por no requerir estructuras para soportarlas, facilita su uso en plantas o sistemas que están saturados de equipos, donde el espacio es el principal incentivo, pudiéndose colocar varios pisos de bombas sin necesidad de bases sólidas para soportarlas.
2.3.3.4.- Montaje de Bombas Verticales
Las bombas verticales del tipo turbina deben ser montadas sobre un pedestal que permita que la columna de la bomba se sumerja en el líquido que se quiere bombear.
Los pedestales son aplicados a las bombas verticales del tipo VS1, VS2, VS6 y VS7 según la nomenclatura del API 610. El diseño del pedestal contiene un soporte para el motor que se coloca también en la posición vertical, adicionalmente cuenta con un espaciador que permite la manipulación de los acoplamientos entre la bomba y el motor. El cabezal de la bomba se soporta en una plancha metálica por lo general de acero que fija el conjunto a la base, en las aplicaciones terrestres se completa o llena esta base con “grauting” para aumentar la rigidez del sistema.
La bomba está sumergida en el líquido y lo succiona directamente de la fuente que puede ser un pozo, un tanque o una cisterna, para luego elevarlo hacia el cabezal de la bomba en el tope que es quien contiene la brida de descarga. La figura Nº 2-25 muestra el diagrama de una bomba vertical tipo turbina montada sobre un pedestal.

Fuente: Dibujado por el Autor.
2.3.4.- Interacción Carcasa – Base
Parte de la confiabilidad y disponibilidad de las bombas centrífugas depende de la durabilidad en servicio de sellos mecánicos, cojinetes y del mantenimiento de las holguras de rodaje. La prolongación de la vida operativa de estos elementos, entre otros factores, está relacionada con la base de soporte donde son instaladas las bombas centrífugas.
La función fundamental de la base de soporte (Baseplate) es mantener la alineación precisa entre la bomba y el elemento accionador sea motor eléctrico, turbina a vapor, turbina a gas o cualquier otro equipo que suministre energía mecánica a la bomba.
La máxima pregonada por los especialistas en la materia es que la base del equipo no puede ser usada como punto de anclaje de la tubería y debe tener la suficiente rigidez para evitar distorsiones.
Las dos normas de referencia para las bombas centrífugas usadas en este libro la API 610/ISO 13079 y la ASME B73.1 establecen las características básicas de las bases a usar en las bombas centrífugas.
La norma ASME B73.1 indica fundamentalmente las dimensiones de la base, con la finalidad que la base engrane con las dimensiones de las familias de bombas y con las dimensiones de los equipos impulsores. Estos equipos impulsores son principalmente los motores eléctricos (La norma hace referencia a la especificación NEMA para los motores eléctricos donde se tienen normalizadas las familias de tamaños o ‘Frames”).A parte de cumplir con las dimensiones la norma pide que la base debe ser losuficientemente rígida para limitar el desalineamiento paralelo del eje a 50mm (0,002 pulgadas) cuando el torque de placa del motor es aplicado. La figura 2-26 muestra una base ANSI típica.
En la figura se observa la bomba centrífuga accionada por un motor eléctrico instalado en una base metálica hecha con perfiles, ya le fue colocado el “grout”, no posee drenajes y deja espacios internos donde se pueden acumular líquidos que pueden propiciar corrosión. Las bases ASME B73.1 son fabricadas de diversos materiales de acero estructural, acero estampado, hierro fundido y otros materiales no metálicos.

Fuente:Fotografiado por el autor.
La norma API 610/ISO 13079 es más exigente en cuanto a los acabados y a la rigidez. Esta norma exige que la base sea construida en una pieza única, con refuerzo de acero estructural, con acabados para facilitar el anclaje del “grout”. El API también pide agujeros para permitir el vaciado del “grout”, agujeros para el venteo del aire, elementos para el izamiento de la base, elementos que permitan la nivelación, recursos para facilitar la alineación del equipo impulsor, etc.
Lafigura N° 2-27 muestra una bomba API 610/ISO 13709, montada sobre una base típica fabricada por las especificaciones del API, se puede observar el refuerzo estructural, los agujeros para colocación del “graut”, recursos para alineación, y nivelación.
Esta base debe tener pendiente para facilitar el flujo de los líquidos derramados al drenaje y debe ser de dimensiones mayores al conjunto que soporta para poder colectar los líquidos que se derraman por fugas. La soldadura debe ser corrida, no se permite la soldadura por puntos para evitar acumulación de líquidos y limitar espacios para la corrosión.

Fuente:www.pumpworks610.com/brochures/PWH-Brochure-7-6-09.pdf
En la norma API se exige una base lo suficientemente rígida para tolerar una desalineación máxima de 50mm (0,002 pulgadas). En cuanto a los esfuerzos en las boquillas (bridas de las tuberías) la norma es exigente establece los límites de las fuerzas y describe las metodologías de cómo debe ser medidos estos esfuerzos.
De hecho, hasta la sexta edición del API 610 no existía una metodología uniforme para medir los esfuerzos sobre las boquillas o bridas, dejando en manos de cada fabricante la metodología para medirlos. Luego de la implantación de la sexta edición de la norma muchas bombas aceptadas como API dejaron de serlo, debido a su falta de robustez del casco y de la base de soporte.
Como recomendaciones generales para un mejor aprovechamiento de las bases de soporte es conveniente:
- Mantener la regla de una desalineación máxima de 50mm (0,002 pulgadas).
- Para facilitar el alineamiento del conjunto impulsor se deben colocar tornillos laterales para alineación, sobre todo cuando los motores son mayores a 25 HP ya que esto facilita los trabajos de posicionamiento del motor y la alineación de los equipos.
- Establecer la bomba el equipo fijo, la bomba siempre está montada directamente sobre el pedestal de la base sin suplementos metálicos, ajustada y sincronizada a la tubería para evitar esfuerzos sobre las bridas de las bombas.
2.3.4.1.- Bases Pre – Grauteadas
En los últimos años se están usando las bases pre-grauteadas de fábrica. La expansión observada en el uso de esta solución se basa fundamentalmente en la propuesta económica que ofrece ahorros de hasta un 30% en los costos de instalación, adicionalmente elimina las burbujas de aire y las posibles cavidades que forman en el vaciado del “grout”, garantizando de esta forma la rigidez del conjunto moto-bomba, adicionalmente el curado del “grout” se realiza de forma controlada y finalmente por el proceso poco traumático de la operación se preserva la integridad las superficies de montaje (Superficies mecanizadas donde son instalados los equipos tanto los equipos impulsores como los equipos principales).
Sin embargo, en la práctica se han observado problemas con las bases pre-grauteadas que son importantes de destacar a continuación:
- Los costos de embarque se incrementan por el peso adicional del “grout” en el conjunto, se estima entre 50 y 75% mayor al de una base no pre-grauteada.
- Se han presentado complicaciones en el manejo de las bases en el campo, debido al peso adicional del “grout” que se colocó en el “skids” de la bomba, lo cual motiva la redirección de la capacidad de los equipos de izamiento utilizados para manipular el conjunto.
- Los cuidados adicionales en la manipulación pueden diluir el ahorro identificado inicialmente.
Como ejemplo tangible durante la construcción de una refinería de 280 MBD de carga, aproximadamente el 20% de las bases o “skids” pre-grauteados para equipos de bombeo resultaron deformadas en el transporte o por la manipulación en campo. Esto hizo necesario el maquinado de las superficies de montaje en sitio para lograr la plenitud y paralelismo pedido por el API 686 “Recommended Practice for Machinery Installation and Installation Desing”.
Una buena práctica cuando se usan estas bases pre-grauteadas es desmontar el equipo accionador para el transporte y para la manipulación en campo (motor eléctrico o turbina a vapor), que es más pesado que la bomba con la finalidad de aligerar el peso del conjunto. Es recomendable analizar en detalle los beneficios y desventajas del uso de sistemas pre-grateados antes de aplicarlos con la finalidad de establecer el posible ahorro real evaluando los costos adicionales por manipulación, por equipos de izamiento y por incremento de los pesos de transporte.
Dinos qué te ha parecido el artículo
Artículos recomendados
Manual de análisis de causa raíz: una guía para la investigación de incidentes eficiente y eficaz

Diseño óptimo de experimentos: un enfoque de estudio de caso

Diagnóstico de fallos y control sostenible de aerogeneradores: Estrategias robustas basadas en datos y en modelos

Índice

Publica tu artículo en la revista #1 de Mantenimiento Industrial
Publicar un artículo en la revista es gratis, no tiene costo.
Solo debes asegurarte que no sea un artículo comercial.
¿Qué esperas?
O envía tu artículo directo: articulos@predictiva21.com
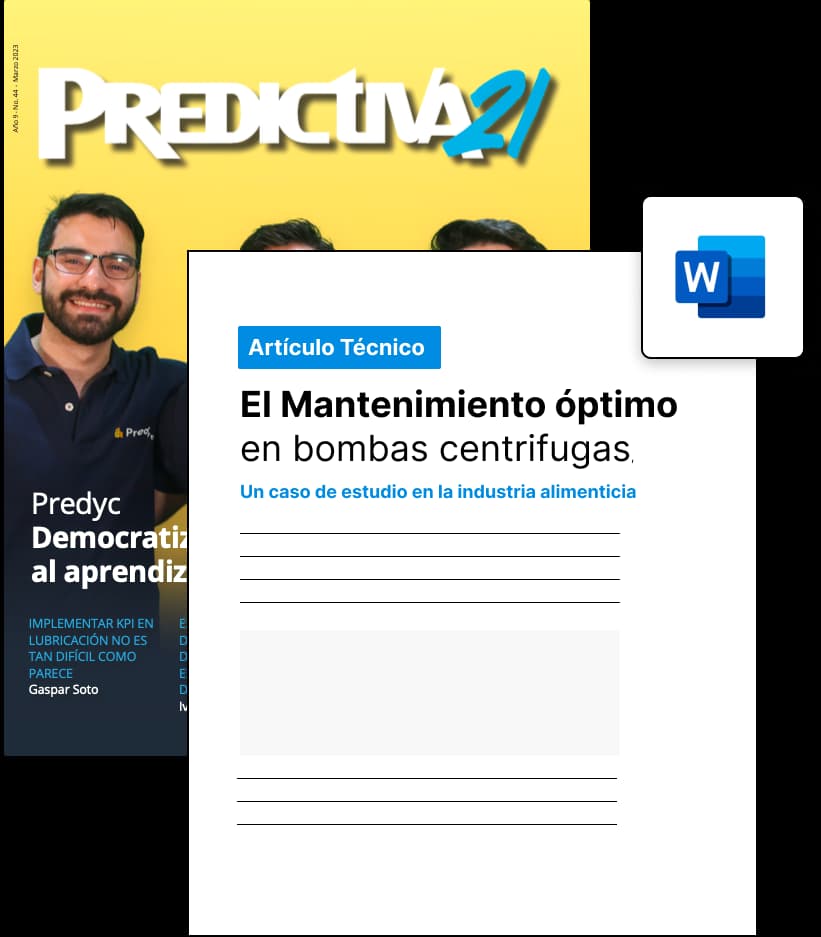
2.3.- Carcasa
Libros 21 de agosto de 2021La carcasa es el cuerpo de la bomba centrífuga, en este capítulo se hará diferencia entre el diseño externo y el diseño interno de la carcasa de las bombas centrífugas. El diseño interno de la carcasa permite capturar el líquido a alta velocidad transformando la energía cinética, que trae el fluido, en presión. Externamente las formas y elementos constructivos de las carcasas permiten soportar las fuerzas y las fuerzas generadas en el proceso de bombeo.
2.3.1.- Carcasa Interna
Los diseños de las bombas centrífugas de procesos que son usadas en la Industria Petrolera están regulados fundamentalmente por las normas API 610/ISO 13079 y por la ASME B73.1.
Las carcasas de las bombas fabricadas bajo el B73.1 manejan una presión máxima de 20 bars (300 psig) a una temperatura de 150 °C (300 °F); las bombas diseñadas siguiendo el API 610/ISO 13709 pueden trabajar con presiones de hasta 52 bars (750 psig) a una temperatura de 260 °C (500 °F). En ambos casos los diseños para presiones mayores son considerados diseños especiales.
En los diseños iniciales de las bombas centrífugas se utilizaban carcasas cuadradas, hasta que en 1839 el inventor norteamericano W. H. Andrew introdujo un modelo de carcasa tipo espiral bastante rudimentaria. Los diseños o arreglos fundamentales de las carcasas de las bombas centrífugas son la voluta y el difusor, a continuación, una breve descripción de los dos diseños de carcasa.
2.3.1.1.- Voluta
La configuración tipo voluta de la carcasa, en una bomba centrífuga, se asemeja a la forma de un espiral.
Los tres principales tipos de carcasa tipo voluta son:
- Voluta simple.
- Doble voluta.
- Voluta concéntrica.
a.- Voluta simple
Por su sencillez, la voluta simple es el tipo más común de construcción, está generalizado en las bombas de baja y media energía debido a que genera bajos costos relativos de fabricación, son relativamente sencillas de maquinar y ajustar. La figura 2-13 muestra el cuerpo de una carcasa tipo voluta simple.

Fuente:Castwel Foundry Agra, Uttar Pradesh
Este tipo de diseño de carcasa resulta práctico, debido a que la conversión de energía cinética en presión se realiza de forma eficiente. La forma en espiral de la voluta permite un incremento del área a una razón proporcional, que mantiene al líquido, que es descargado del impulsor, a una velocidad constante hasta que es difundido en la carcasa.
Clásicamente la velocidad de referencia tomada para el diseño de las volutas es la velocidad en el Punto de Mejor Eficiencia(BEP) y las velocidades en otros puntos de operación son estimadas en función de la velocidad del fluido en el BEP. En la actualidad el diseño computarizado de las bombas ha permitido modelar las velocidades del fluido en las diferentes condiciones de operación.
La figura N° 2-14 presenta el esquema de una bomba con carcasa tipo voluta mostrando las flechas orientadas radialmente que indican la dirección de las fuerzas, que el fluido está ejerciendo contra el centro de la bomba. La principal desventaja de este tipo de carcasa es que el esfuerzo radial se incrementa debido al cambio constante del área seccional de la carcasa.

Fuente:www.pumpfundamentals.com/DOUBLEVolute.pdf
En la figura 2-14 se observa que a medida que el caracol de la carcasa se aproxima a la garganta de salida las fuerzas radiales se incrementan sustancialmente. La magnitud de estas fuerzas es indicada por el tamaño de las flechas, las cuales se incrementan progresivamente al aproximarse al área de descarga.
Existen problemas asociados al desbalance de las fuerzas radiales que causan diferentes tipos de eventos. El esfuerzo radial excesivo puede causar la deflexión del eje, sobrecarga en los cojinetes radiales y axiales, daños en las caras de los sellos mecánicos, daños en las estoperas de las cajas de cojinetes y otros efectos que acortan la vida operativa de la bomba.
En las bombas de bajo caudal usadas para aplicaciones especiales, como las bombas para manejar sólidos y desechos, se acostumbra a usar carcasas de voluta simple.
b.- Doble voluta
La carcasa de doble voluta se utiliza principalmente en las bombas diseñadas siguiendo el API 610/ISO 13709 o en las bombas de gran capacidad. En las carcasas de doble voluta se incorpora una vena interna a lo largo del espiral de la carcasa. La figura N° 2-15 muestra el diagrama en corte de una bomba con carcasa de doble voluta, mostrando la vena interna y la distribución de fuerzas radiales.
Este diseño de carcasa reduce el desbalance de presiones radiales alrededor de la periferia del impulsor, mediante la división del flujo total y reducción relativa del área de la voluta, equilibrando de esta forma las fuerzas radiales cuando la bomba trabaja a caudales fuera del caudal de diseño.
Esta modificación de la voluta aumenta la vida de los cojinetes radiales, ya que reduce las fuerzas radiales transmitidas al eje entre 1/6 y 1/3 de las fuerzas observadas en bombas con voluta simple.

Fuente:www.pumpfundamentals.com/DOUBLEVolute.pdf
En el pasado la fundición de las carcasas de doble voluta en bombas de baja capacidad representaba un problema porque sé hacia muy difícil que la vena de separación que divide la voluta quedara bien fundida y sin imperfecciones. La figura 2-16 muestra una carcasa doble voluta fundida mostrando la vena de separación.
Las imperfecciones causan altas perdidas de energía en la bomba, tanto hidráulicas como por fricción. En la actualidad las técnicas de fundición se han perfeccionado y permiten un mejor control de los acabados y de las áreas de los pasajes de las volutas dobles.
La fabricación de estas carcasas resulta más costosa y se experimenta una reducción de la Eficiencia de estas bombas con respecto a las bombas de voluta simple de entre 1 y 2%, debido al incremento de la fricción en las superficies adicionales. Sin embargo, las ventajas hidráulicas superan cualquier pequeño inconveniente que se pueda observar en estas bombas, siendo ampliamente usadas en procesos y aplicaciones exigentes.

Fuente:http://www.cixihuili.com/html/product_174.html
c.- Voluta concéntrica
En contraparte a las bombas de voluta tipo espiral existen las volutas concéntricas, muy comunes en bombas de relativamente bajo costo, alto Cabezal de Descarga relativo y baja Velocidad Específica(NS). En estas bombas la carcasa es circular y mantiene una distancia fija con el diámetro exterior del impulsor. La figura 2-17 muestra el modelo de una bomba con carcasa concéntrica.

Fuente: www.gouldspumps.com/download_files/lf3196_i_FRAME/
La carcasa concéntrica es ampliamente utilizada en bombas de acero inoxidable fabricadas por estampado y cuando las carcasas son fabricadas por fundición se reduce considerablemente el trabajo de maquinado y la complejidad de los moldes. Este tipo de carcasa se aplica en bombas que acomodan impulsores de diferentes diámetros o que requieren que los pasajes de la carcasa sean maquinados en detalle, como es el caso de las bombas sanitarias, bombas criogénicas, etc.
2.3.1.2.- Fuerzas Radiales
Como fue explicado en la sección anterior que habla de las carcasas tipo voluta, en el proceso de bombeo centrífugo se generan fuerzas radiales y axiales que actúan sobre los componentes como son impulsores, sellos mecánicos, ejes, cojinetes etc. Parte del conocimiento de las bombas centrífugas es entender cómo actúan estas fuerzas en el interior de la bomba.
Una aproximación de los valores de los esfuerzos radiales en bombas de procesos es dada por la ecuación N° 2-4 de Esfuerzo Radial en una bomba centrífuga tal como sigue a continuación:
![[2-4]](/_next/image?url=https%3A%2F%2Ffirebasestorage.googleapis.com%2Fv0%2Fb%2Fpredyc2023.appspot.com%2Fo%2FArticulosP21%252F2-3-carcasa%252Fimage-137.png%3Falt%3Dmedia%26token%3D2a50bfbf-7638-4264-b03b-898f0af769c1&w=640&q=75)
F:Esfuerzo radial, en Libras.
H:CabezalDiferencial de la bomba, en Pies.
D2: Diámetro del impulsor, en Pulgadas.
B2: Ancho del impulsor en el área de descarga, en Pulgadas.
K: Constante, definida con laecuación N° 2-5
Donde K es:
![[2-5]](/_next/image?url=https%3A%2F%2Ffirebasestorage.googleapis.com%2Fv0%2Fb%2Fpredyc2023.appspot.com%2Fo%2FArticulosP21%252F2-3-carcasa%252Fimage-138.png%3Falt%3Dmedia%26token%3D9ced97a4-5037-4c5c-b747-8221997d99c2&w=640&q=75)
Q: Caudal a cualquier capacidad, en gpm.
QBEP: Caudal en el BEP,Punto de Mejor Eficiencia, en gpm.
Si observamos la figura N° 2-18 podemos ver cómo influye en el esfuerzo radial de las bombas centrífugas el operar fuera del Punto de Mejor Eficiencia(BEP).
La figura contiene el comportamiento del esfuerzo radial para diferentes diseños de carcasa tipo voluta. Como se observa en la gráfica, que es referencial, usando carcasas de doble voluta se pueden lograr reducciones del esfuerzo radial en más de un 40% cuando se opera fuera del BEP.

Fuente: Centrifugal pump user’s guidebook: problems and solutions Por S. Yedidiah Charter 10.
Cuando se tiene una voluta simple o estándar a 100% del caudal de diseño el esfuerzo radial no supera más del 20% del esfuerzo que se alcanza en el punto de cierre o “shutoff”, cuando la válvula de descarga está completamente cerrada, es allí cuando el esfuerzo radial es máximo en las carcasas tipo voluta simple o Standard.
Al desplazarse el caudal tanto a la derecha como a la izquierda del BEP, Punto de Mejor Eficiencia el esfuerzo radial aumenta considerablemente. Cuando se usa una carcasa tipo voluta, pero concéntrica el balance de las fuerzas radiales mejora considerablemente reduciendo el esfuerzo radial máximo a un 60% del esfuerzo total alcanzado con una carcasa de voluta simple en espiral.
Finalmente, con el arreglo de doble voluta las fuerzas radiales están completamente equilibradas, lo que reduce la fuerza radial máxima del equipo a un 20% del total del esfuerzo radial alcanzado en una bomba de voluta simple del tipo espiral.
Las fuerzas radiales excesivas son las principales causantes de la deflexión de los ejes por arriba de lo esperado, lo cual origina los daños prematuros de los siguientes componentes: anillos de desgaste los cuales se erosionan por roce, los cojinetes que soportan mayores fuerzas que las esperadas normalmente, los sellos mecánicos que se desgastan de forma no uniforme y son afectados por el aumento en el calor generado en las superficies de contacto y puede causarhasta la fatiga del eje cuando las fuerzas radiales son cíclicas.
Existen otros elementos del diseño de la voluta que pudiese influenciar en la fluctuación de las fuerzas radiales como por ejemplo la holgura entre el radio exterior del impulsor y la lengüeta de la voluta.
2.3.1.3.- Difusor
La construcción tipo difusor en una carcasa, es fundamentalmente una serie de alabes o paletas fijas alrededor del impulsor.
La carcasa tipo difusor trabaja de la siguiente forma: los alabes reciben el líquido descargado por el impulsor reduciéndole la velocidad, usando para ello la orientación de los ángulos de entrada y salida, esta acción convierte la energía cinética del líquido en energía de presión, adicionalmente dirigen el líquido a la boquilla de descarga.
La figura N° 2-19 muestra un diagrama de una bomba construida con una carcasa tipo difusor, donde es posible observar los alabes fijos.

Fuente:Flowserve/PROS+SE/Release 3.03a
Históricamente el primer desarrollo de carcasas tipo difusor del que se tenga conocimiento fue el patentado, en 1875, por el científico Inglés Osborne Reinold. La figura N° 2-20 muestra la fotografía de un difusor para bombas centrífugas.
El diseño de carcasa interna tipo difusor es aplicado principalmente a bombas de ingeniería donde se requiere el manejo de mayores volúmenes de fluidos con presiones medias y altas, utilizando dimensiones más reducidas a las que pudiesen resultar de utilizar una bomba con carcasa tipo voluta.

Fuente:Fotografiado por el autor.
La principal desventaja en la utilización de las bombas con difusor está en su complejidad, que incrementa los costos de fabricación.
Existe diseños de carcasa tipo difusor donde los alabes guías son variables es decir pueden ser ajustados manualmente si se prevén cambios prolongados en los regímenes de flujo. Esto es con la finalidad de permitir mayor Eficiencia y el acoplamiento con las exigencias del sistema, dando flexibilidad para operar en rangos más amplios de caudal.
2.3.2.- Interacción Carcasa – Impulsor
La interacción entre la carcasa y los impulsores en el interior de la bomba es fundamental para el comportamiento hidráulico adecuado del equipo. Para lograr un buen desempeño hidráulico se deben mantener las unas dimensiones críticas entre los impulsores y la carcasa con la finalidad de reducir los choques hidráulicos, las pulsaciones y el ruido que se genera como resultado de la conversión de la energía cinética en energía de presión. Estas dimensiones se describen a continuación.
En la figura N° 2-21 se muestran la dimensión crítica “A” o GAP “A” y la dimensión crítica “B” o GAP “B”, en la interacción carcasa- impulsor.
La dimensión “A” (GAP “A”, en la figura 2-21) es la distancia entre el tope del impulsor y la garganta de entrada a la voluta o difusor, con ella se controlan las presiones en la parte posterior del impulsor, reduciendo las fuerzas axiales. Tanto para el diseño de carcasa tipo voluta como para las carcasas tipo difusores la dimensión “A” debe estar en el orden de 1,27 mm (0,050 pulgadas).

Fuente: Reliability-Driven Pump Maintenance: by Terry Hernandez_The Pump Handbook series.
El corte de los impulsores para el ajuste del Cabezal puede traer complicaciones con la dimensión “A” generando vibraciones axiales, por lo general de alta frecuencia, los impulsores de doble succión son especialmente sensibles a problemas relacionados con el incremento de la dimensión “A”.
La dimensión “B” (GAP “B”) es la distancia entre el tope del impulsor y la lengüeta de la voluta (Cut Water) o la punta de los difusores. Con ella se controla el esfuerzo y la amplitud de los choques hidráulicos principalmente los causados por el paso de los alabes. Para las bombas con difusores la dimensión “B” debe estar entre el 4 y 12% del diámetro del impulsor, con un valor preferencial del 6% y para las bombas con voluta debe estar entre el 6 y 12%, con un valor preferencial del 10% del diámetro del impulsor.
El uso o aplicación en una bomba del diámetro más pequeño en un determinado tipo de impulsor causa el incremento de la turbulencia en el interior de la carcasa, específicamente en la entrada a la voluta o difusor propiciando la erosión y las pulsaciones. Es recomendable usar el mayor diámetro posible en los impulsores disponibles o hacer el ajuste del GAP “A” o “B” para evitar estos problemas. Una gran variedad de fallas, en los impulsores de las bombas centrífugas, están relacionadas con la incorrecta fijación de estas dimensiones.
Las pulsaciones causadas por la dimensión “A” (GAP “A”) superior al mínimo permitido, combinado con un flujo reducido en la bomba puede causar la rotura de los impulsores a nivel del borde de ataque de los alabes a la descarga.
Las pulsaciones en bombas que estén siendo operadas a bajo flujo no deben superar el 5% del Cabezal desarrollado por la bomba; en condiciones de flujo normal las pulsaciones deben ser irrelevantes. Con el incrementando del GAP “B” de 1% a 6% las pulsaciones hidráulicas se pueden reducir de entre 80 y 85%
Los efectos de la incorrecta fijación de las dimensiones “A” y “B” alcanzan también a los sellos mecánicos y los cojinetes, debido a la variación constante de las fuerzas axiales de las bombas.
2.3.2.1.- Paso de Alabe
Existe un fenómeno denominado Paso de Alabe que se presenta cuando se ajusta inadecuadamente el GAP “B”. El fenómeno ocurre cuando la holgura es inadecuada y existe mucha proximidad entre la lengüeta de entrada al canal de descarga de la bomba o “Cut Water”, y el diámetro exterior del impulsor causando el aumento de la velocidad del líquido en este punto, por balance y conservación de la energía este aumento de velocidad provoca la reducción de la presión del líquido en esta área dando como resultado una vaporización del líquido, si se alcanza la presión de vapor (HVP) de la mezcla. Es una cavitación localizada ya que inmediatamente, aguas arriba de la lengüeta, las burbujas colapsan al incrementarse la presión del sistema.
Las principales normas para las bombas centrífugas como la API 610/ISO 13709 en la sección 6 “Basic Design” en el párrafo 6.1.15 pide que se aplique esta regla, sobre todo en las bombas con Cabezales mayores a 200 m (650 pies) por etapa y de al menos 225 KW (300 HP) por etapa, con la finalidad de reducir la vibración a las frecuencias correspondiente al Paso de Alabe, “Vane Passing”. Debido a que problemas de ajuste de las dimensiones “A” y “B” en bombas de este tamaño causarían daños importantes en los sellos, cojinetes y otros componentes causado por las vibraciones y el desbalance de fuerzas axiales.
Los daños o perturbaciones causadas por este fenómeno van a depender de los niveles de energía de la bomba. Cuando se producen daños se observa desgaste de la lengüeta de descarga de la carcasa o “Cut Water”, y a nivel de impulsor se observan daños en el centro del alabe en la cara activa en el topo del impulsor.
Desde el punto de vista de las vibraciones mecánicas estas se manifiestan a una frecuencia que es el resultante de la multiplicación de la velocidad de rotación del rotor de la bomba, multiplicada por el número de alabes del impulsor incluyendo las armónicas a 2x y 3x, por ejemplo, si la bomba centrífuga tiene una velocidad de 3.600 RPM y cinco alabes en el impulsor el paso de alabe se manifiesta a 18.000 RPM con armónicas a 36.000 y 54.000 RPM. La magnitud de la vibración va a depender de los niveles de energía de la bomba y del ajuste del GAP “B”.
Cuando se va a ajustar el diámetro de un impulsor se debe realizar una evaluación del comportamiento hidráulico de la bomba antes de realizar el ajuste con la finalidad de evitar las posibles complicaciones de un ajuste inadecuado de las dimensiones “A” y “B”.
Cursos recomendados
-1730145694747.webp%3Falt%3Dmedia%26token%3D719f647e-063f-47e9-a9f4-c3b59cb3a8ab&w=3840&q=75)



%252FImagen%252Frcm-1730083250826.webp%3Falt%3Dmedia%26token%3D3775356a-7b11-4c44-b21f-45b3409fb9ed&w=3840&q=75)

%252FImagen%252FRAMPREDYC-1730060420837.webp%3Falt%3Dmedia%26token%3D2634a7f0-988e-4022-b91f-382503e6e9db&w=3840&q=75)

2.3.3.- Diseño Externo de la Carcasa
Existen diferentes formas y diseños para soportar externamente la carcasa de las bombas centrífugas, los principales son soportarla en la parte inferior o en el pie (foot mounted), montaje en la parte central o en pedestal (Center line mounted) y las bombas con carcasa en línea (inline casing).
2.3.3.1.- Montaje en el Pie
Las bombas que son montadas en el pie son las bombas generales de procesos como las fabricadas bajo la norma ASME B73.1 y corresponde a la designación OH1 en la nomenclatura del API 610. De acuerdo con el API 610 11ava edición para bombas del tipo BB1, BB2, BB3, y BB5 si la temperatura de servicio de la bomba es menor a 150 °C (300 °F) (temperatura de servicio relativamente baja) se pueden usar carcasas montadas en el pie.
Por su diseño y características estas bombas no son fabricadas para ser sometidas a grandes cargas o temperaturas. Los acabados de estas bombas son variados y dependen fundamentalmente de la complejidad de la aplicación para la cual son fabricadas, ellas no están diseñadas para soportar altos momentos torsionales y los costos relacionados con la implantación (inversión inicial) son significativamente más bajos que los costos de las bombas fabricadas siguiendo el API 610. La figura 2-22 muestra una bomba con montaje en el pie.

Fuente: SULZER PUMPS, ANSI Process Pumps CPT adventage.
2.3.3.2.- Montaje Central
Las bombas de montaje central son las fabricadas bajo la norma API 610/ISO 13709, corresponden a la designación OH2 del API 610. La figura 2-23 muestra una bomba de montaje central.

Fuente:www.sulzerpumps.com/desktopdefault.aspx
Esta configuración, de montaje central, le permite a la bomba manejar mayores temperaturas y presiones. La razón para usar un montaje central es que minimiza las distorsiones causadas por las altas temperaturas y por los esfuerzos. Las tuberías y los equipos impulsores poseen gradientes de expansión diferentes, cuando se fija la bomba en el centro, la expansión térmica de la carcasa se realiza de forma uniforme y sin interferencias.
En este diseño las aletas de fijación de la carcasa están unidas en el eje central del cuerpo de la bomba, por lo que la expansión térmica de la carcasa se produce de forma uniforme evitando de esta forma la desalineación, la distorsión de la carcasa y el exceso de esfuerzos radiales y axiales sobre los rotores.
2.3.3.3.- Montaje en Línea
En las bombas con carcasa en línea la succión y la descarga están alineadas y el cuerpo de la bomba tiene una configuración que le permite soportar un motor vertical. La figura Nº 2-24 muestra el diagrama de una bomba con montaje en línea.
El cuerpo de la bomba no posee ningún tipo de soporte para la carcasa que se fije a un “skid” de metal o base estructural y pueden ser soportadas por las tuberías que están conectadas a sus bridas.
Las bombas en línea van de capacidades y tamaños pequeños a medianos, debido a la limitación que representa el no tener un soporte firme y una base estructural. El uso de las bombas verticales en línea está muy extendido en las refinerías, plantas petroquímicas y mejoradores de petróleo debido a su capacidad para ahorrar espacio.

Fuente:www.fochpump.com/SLB-Vertical-Single-stage-Do.
La configuración de esta bomba le permite ubicar el motor en posición vertical y por no requerir estructuras para soportarlas, facilita su uso en plantas o sistemas que están saturados de equipos, donde el espacio es el principal incentivo, pudiéndose colocar varios pisos de bombas sin necesidad de bases sólidas para soportarlas.
2.3.3.4.- Montaje de Bombas Verticales
Las bombas verticales del tipo turbina deben ser montadas sobre un pedestal que permita que la columna de la bomba se sumerja en el líquido que se quiere bombear.
Los pedestales son aplicados a las bombas verticales del tipo VS1, VS2, VS6 y VS7 según la nomenclatura del API 610. El diseño del pedestal contiene un soporte para el motor que se coloca también en la posición vertical, adicionalmente cuenta con un espaciador que permite la manipulación de los acoplamientos entre la bomba y el motor. El cabezal de la bomba se soporta en una plancha metálica por lo general de acero que fija el conjunto a la base, en las aplicaciones terrestres se completa o llena esta base con “grauting” para aumentar la rigidez del sistema.
La bomba está sumergida en el líquido y lo succiona directamente de la fuente que puede ser un pozo, un tanque o una cisterna, para luego elevarlo hacia el cabezal de la bomba en el tope que es quien contiene la brida de descarga. La figura Nº 2-25 muestra el diagrama de una bomba vertical tipo turbina montada sobre un pedestal.

Fuente: Dibujado por el Autor.
2.3.4.- Interacción Carcasa – Base
Parte de la confiabilidad y disponibilidad de las bombas centrífugas depende de la durabilidad en servicio de sellos mecánicos, cojinetes y del mantenimiento de las holguras de rodaje. La prolongación de la vida operativa de estos elementos, entre otros factores, está relacionada con la base de soporte donde son instaladas las bombas centrífugas.
La función fundamental de la base de soporte (Baseplate) es mantener la alineación precisa entre la bomba y el elemento accionador sea motor eléctrico, turbina a vapor, turbina a gas o cualquier otro equipo que suministre energía mecánica a la bomba.
La máxima pregonada por los especialistas en la materia es que la base del equipo no puede ser usada como punto de anclaje de la tubería y debe tener la suficiente rigidez para evitar distorsiones.
Las dos normas de referencia para las bombas centrífugas usadas en este libro la API 610/ISO 13079 y la ASME B73.1 establecen las características básicas de las bases a usar en las bombas centrífugas.
La norma ASME B73.1 indica fundamentalmente las dimensiones de la base, con la finalidad que la base engrane con las dimensiones de las familias de bombas y con las dimensiones de los equipos impulsores. Estos equipos impulsores son principalmente los motores eléctricos (La norma hace referencia a la especificación NEMA para los motores eléctricos donde se tienen normalizadas las familias de tamaños o ‘Frames”).A parte de cumplir con las dimensiones la norma pide que la base debe ser losuficientemente rígida para limitar el desalineamiento paralelo del eje a 50mm (0,002 pulgadas) cuando el torque de placa del motor es aplicado. La figura 2-26 muestra una base ANSI típica.
En la figura se observa la bomba centrífuga accionada por un motor eléctrico instalado en una base metálica hecha con perfiles, ya le fue colocado el “grout”, no posee drenajes y deja espacios internos donde se pueden acumular líquidos que pueden propiciar corrosión. Las bases ASME B73.1 son fabricadas de diversos materiales de acero estructural, acero estampado, hierro fundido y otros materiales no metálicos.

Fuente:Fotografiado por el autor.
La norma API 610/ISO 13079 es más exigente en cuanto a los acabados y a la rigidez. Esta norma exige que la base sea construida en una pieza única, con refuerzo de acero estructural, con acabados para facilitar el anclaje del “grout”. El API también pide agujeros para permitir el vaciado del “grout”, agujeros para el venteo del aire, elementos para el izamiento de la base, elementos que permitan la nivelación, recursos para facilitar la alineación del equipo impulsor, etc.
Lafigura N° 2-27 muestra una bomba API 610/ISO 13709, montada sobre una base típica fabricada por las especificaciones del API, se puede observar el refuerzo estructural, los agujeros para colocación del “graut”, recursos para alineación, y nivelación.
Esta base debe tener pendiente para facilitar el flujo de los líquidos derramados al drenaje y debe ser de dimensiones mayores al conjunto que soporta para poder colectar los líquidos que se derraman por fugas. La soldadura debe ser corrida, no se permite la soldadura por puntos para evitar acumulación de líquidos y limitar espacios para la corrosión.

Fuente:www.pumpworks610.com/brochures/PWH-Brochure-7-6-09.pdf
En la norma API se exige una base lo suficientemente rígida para tolerar una desalineación máxima de 50mm (0,002 pulgadas). En cuanto a los esfuerzos en las boquillas (bridas de las tuberías) la norma es exigente establece los límites de las fuerzas y describe las metodologías de cómo debe ser medidos estos esfuerzos.
De hecho, hasta la sexta edición del API 610 no existía una metodología uniforme para medir los esfuerzos sobre las boquillas o bridas, dejando en manos de cada fabricante la metodología para medirlos. Luego de la implantación de la sexta edición de la norma muchas bombas aceptadas como API dejaron de serlo, debido a su falta de robustez del casco y de la base de soporte.
Como recomendaciones generales para un mejor aprovechamiento de las bases de soporte es conveniente:
- Mantener la regla de una desalineación máxima de 50mm (0,002 pulgadas).
- Para facilitar el alineamiento del conjunto impulsor se deben colocar tornillos laterales para alineación, sobre todo cuando los motores son mayores a 25 HP ya que esto facilita los trabajos de posicionamiento del motor y la alineación de los equipos.
- Establecer la bomba el equipo fijo, la bomba siempre está montada directamente sobre el pedestal de la base sin suplementos metálicos, ajustada y sincronizada a la tubería para evitar esfuerzos sobre las bridas de las bombas.
2.3.4.1.- Bases Pre – Grauteadas
En los últimos años se están usando las bases pre-grauteadas de fábrica. La expansión observada en el uso de esta solución se basa fundamentalmente en la propuesta económica que ofrece ahorros de hasta un 30% en los costos de instalación, adicionalmente elimina las burbujas de aire y las posibles cavidades que forman en el vaciado del “grout”, garantizando de esta forma la rigidez del conjunto moto-bomba, adicionalmente el curado del “grout” se realiza de forma controlada y finalmente por el proceso poco traumático de la operación se preserva la integridad las superficies de montaje (Superficies mecanizadas donde son instalados los equipos tanto los equipos impulsores como los equipos principales).
Sin embargo, en la práctica se han observado problemas con las bases pre-grauteadas que son importantes de destacar a continuación:
- Los costos de embarque se incrementan por el peso adicional del “grout” en el conjunto, se estima entre 50 y 75% mayor al de una base no pre-grauteada.
- Se han presentado complicaciones en el manejo de las bases en el campo, debido al peso adicional del “grout” que se colocó en el “skids” de la bomba, lo cual motiva la redirección de la capacidad de los equipos de izamiento utilizados para manipular el conjunto.
- Los cuidados adicionales en la manipulación pueden diluir el ahorro identificado inicialmente.
Como ejemplo tangible durante la construcción de una refinería de 280 MBD de carga, aproximadamente el 20% de las bases o “skids” pre-grauteados para equipos de bombeo resultaron deformadas en el transporte o por la manipulación en campo. Esto hizo necesario el maquinado de las superficies de montaje en sitio para lograr la plenitud y paralelismo pedido por el API 686 “Recommended Practice for Machinery Installation and Installation Desing”.
Una buena práctica cuando se usan estas bases pre-grauteadas es desmontar el equipo accionador para el transporte y para la manipulación en campo (motor eléctrico o turbina a vapor), que es más pesado que la bomba con la finalidad de aligerar el peso del conjunto. Es recomendable analizar en detalle los beneficios y desventajas del uso de sistemas pre-grateados antes de aplicarlos con la finalidad de establecer el posible ahorro real evaluando los costos adicionales por manipulación, por equipos de izamiento y por incremento de los pesos de transporte.
Dinos qué te ha parecido el artículo
Artículos recomendados
Mantenimiento Centrado en la Confiabilidad (RCM): Implementación simplificada

Ingeniería de Confiabilidad (Elsayed)

6.2.- Como se Determina el NPSHR

4.2.- Diseño Hidráulico de las Bombas Centrífugas

Publica tu artículo en la revista #1 de Mantenimiento Industrial
Publicar un artículo en la revista es gratis, no tiene costo.
Solo debes asegurarte que no sea un artículo comercial.
¿Qué esperas?
O envía tu artículo directo: articulos@predictiva21.com
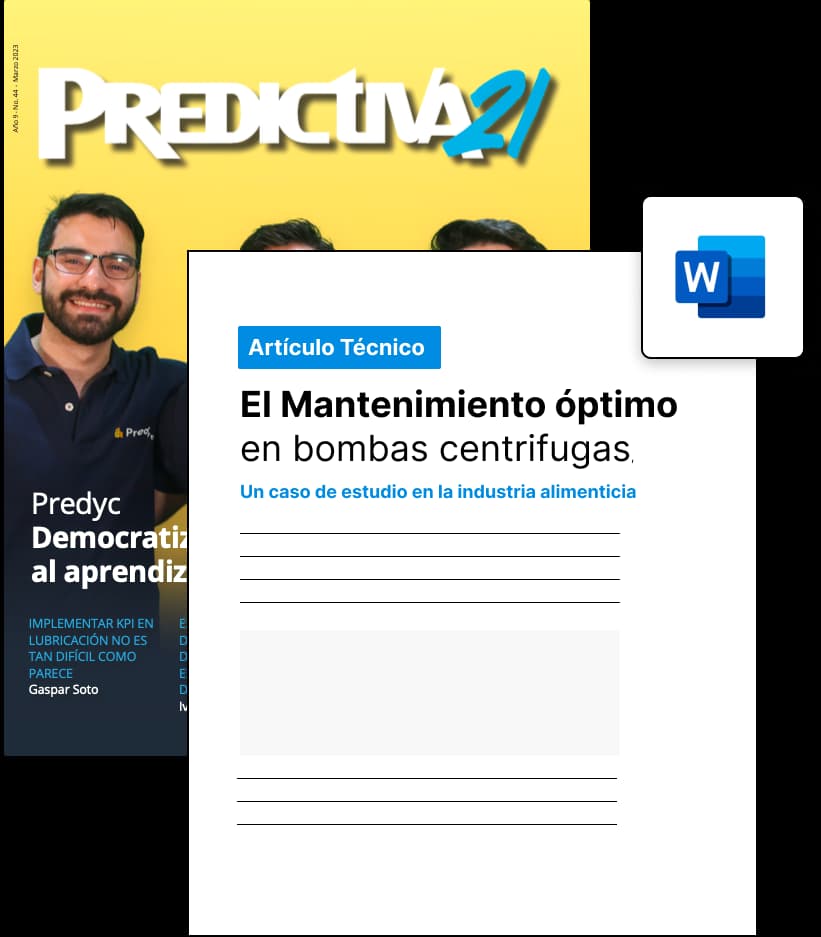