Aplicación de Metodología para Análisis de Modos y Efectos de Falla para Reducción en Tiempos de Paradas de Planta por Fallas Repetitivas
Articulo24 de abril de 2019
Las líneas de producción de la mayoría de las empresas tienen como objetivo cumplir mínimo el 90% de la producción programada. Este margen indica que debemos tener el mínimo de paradas por causas técnicas, para el cumplimiento de estos planes, es fundamental el rol del departamento de mantenimiento e ingeniería y más aún el análisis correcto de cada eventualidad para así disminuir al mínimo su ocurrencia, disminuyendo los tiempos de parada de planta y los costos de ineficiencia. La planta se hace más segura y garantiza la inocuidad de los alimentos producidos a nuestros clientes.
Las empresas de productos de consumo masivo son más propensas a paradas técnicas en especial las que cuentan con líneas de producción en serie, logrando una alta criticidad operacional en todo momento. Todas las unidades de negocio son independientes y se rentabilizan por sí solas, siendo todas en procesos continuos. En la Figura N°1 se observa línea de Pan especial, donde se elabora y comercializan 7 formatos distintos.

Las fabricas panificadoras de alto nivel de automatización, son un claro ejemplo de los arreglos de equipos en serie, esto di culta un poco el análisis correcto de fallas ya que un funcionamiento anormal en cualquier punto de la línea, la detiene por completo, esta situación puede generar las siguientes desventajas:
- Análisis incorrecto de la raíz real de las fallas.
- Alto nivel de mermas.
- Baja rentabilidad del negocio.
- Productos de baja calidad para nuestros clientes.
- Tratamiento incorrecto de las paradas técnicas por tiempo insuficiente para la realización de análisis, y tratar de poner las líneas en funcionamiento en el menor tiempo posible.
- Diferenciar el tipo de falla presentada, si es por mantenimiento, operación, control de calidad etc.
Tomaremos un ejemplo real de la manera correcta de realizar un análisis de modo y efectos de falla de una situación real. (AMEF)
Empresa donde se realizará el análisis: Latín American Foods S.A, Ubicada en Santiago de Chile. Equipo a realizar: Desmoldeador L3 (Pan Especial). Latín American Foods S.A. es una Empresa de panadería industrial donde se cuentan con 5 unidades de negocio principales: Marraquetas, Hallullas, Pan especial, Pizzas y Pastelería. Los capitales son chilenos.
La línea de pan especial produce 14.000 unidades panificadoras por hora, siendo sus principales productos, pan de hot dog, hamburguesa, baguette, chocoso, entre otros. Esta línea en particular cuenta con un equipo que se encarga de sacar (sistema de vacío) el pan que viene de las bandejas de 16 unidades. El producto viene de un sistema de cocción en horno de módulos continuo y su fabricante es Mondial Forni. En resumen, el equipo de análisis es el desmoldeador automático de pan el cual se muestra en la figura número 4 y sus especificaciones técnicas son las siguientes:

Datos técnicos:
- Masa: 2250 kg.
- Tensión: 400 V 3 F + N + T.
- Potencia absorbida nominal: 46,5 kW.
- Consumo de aire:20 Nl/min.
- Presión de funcionamiento: 6 bar (90 psi).
- El nivel de presión acústica ponderada A de la máquina es inferior a 90º dB (A).
- Grupos o conjuntos que lo integran:
- Motorización vertical.
- Grupo de tratamiento de aire.
- Motorización de rotación cabeza.
- Motorización longitudinal.
- Estación de aspiración.
- Cabeza de toma de productos.
- Teclado de mando.
- Tablero eléctrico.


El primer paso para un análisis de modo y efecto de falla es definir el propósito del equipo en cuestión, en este caso el desmoldeador de vacío automático.
Propósito:
Para realizar el proceso de empaquetado de pan este debe estar a una temperatura ambiente, para lograr esta condición se debe sacar la bandeja en que se hornea, objetivo del desmoldeador. La bandeja sigue su línea a un proceso de lavado y el producto sigue hacia las espiras industriales de enfriamiento y congelado tal como se muestra en la figura N°5.

Función principal:
- Retirar el pan de las bandejas que provienen del horno Mondial Forni, mediante sistema de vacío, por medio de ventosas.
- Colocarlo en el transportador hacia cámara de enfriamiento.
Se debe realizar un diagrama EPS (Entrada-Proceso-Salida), para definir la entrada y salida que se espera del proceso, en la figura Nº 6 se muestra el diagrama EPS de nuestro proceso.
Luego de este diagrama se procede a realizar el diagrama funcional del equipo, el cual se muestra en la figura Nº 6.

Una vez realizado el diagrama funcional se procede a iniciar la elaboración del AMEF como tal teniendo claro las siguientes definiciones.
- Componentes: Partes o piezas del equipo.
- Función: Actividad para la cual el equipo fue diseñada.
- Falla Funcional: sucede cuando el sistema opera por fuera de parámetros normales o deseados.
- Modo de falla: es una causa de falla o una posible manera en la que un sistema puede fallar.
En la imagen número 7 se muestra un ejemplo de cómo analizar el modo de falla de uno de los conjuntos pertenecientes al equipo estudiado.
Basado en la imagen número 8, una vez tenemos los modos de falla, suponemos que el modo en que fallo el equipo fue por los rodamientos dañados, y realizamos un análisis ¿Por qué la maquina no está desmoldando el pan? Por qué el desmoldeador no se está moviendo de manera vertical, ¿Por qué no se está moviendo de manera vertical? Por qué fallaron los rodamientos lineales, ¿Por qué fallaron los rodamientos lineales? Se encontraban secos y se desarmaron, ¿Por qué se encontraban secos? Por qué no se lubricaron. Acá tenemos un claro ejemplo que la falla fue por lubricación, ósea que debemos verificar si tienen un plan de lubricación creado o de ser así que su frecuencia sea la adecuada.
Este análisis lo podemos realizar independientemente cual fuese la parte objeto por la que se detuvo el equipo, por eso la importancia de considerarlos todos en la planilla del AMEF.
Ventajas del AMEF:
- Identificar las posibles fallas en un proceso o sistema.
- Conocer a fondo el proceso o el sistema.
- Identificar las causas posibles de las fallas.
- Identificar los tiemposóptimos de los upgrade.
- Aumentar la disponibilidad de maquinas.
- Cumplimiento del plan de negocios.
- Generación de ventaja competitiva en mejora enfocada
- Cumplimiento del EBITDA.
- Logra capacitación permanente y update en conocimiento.


Autores:
Rodrigo Gomez D.
M. SC, Ingeniero civil mecánico (U.T.F.S.M.)
Valparaíso Chile
Gerente de Mantenimiento Planta LAF.
Correo: rgomez@lafchile.com
Fabiola Vargas R.
Ingeniero Mecánico (Universidad de Carabobo)
Carabobo Venezuela
Planificador de Mantenimiento Planta LAF.
Dinos qué te ha parecido el artículo
Artículos recomendados
¿Por qué implementar S&OP en nuestros Negocios, y no morir en el intento?

¿Por que confiabilidad centrada en las personas?

Entrevista Gabriela Mejías, Directora de WIRAM LATAM

Plan de mantenimiento preventivo en Excel

Publica tu artículo en la revista #1 de Mantenimiento Industrial
Publicar un artículo en la revista es gratis, no tiene costo.
Solo debes asegurarte que no sea un artículo comercial.
¿Qué esperas?
O envía tu artículo directo: articulos@predictiva21.com
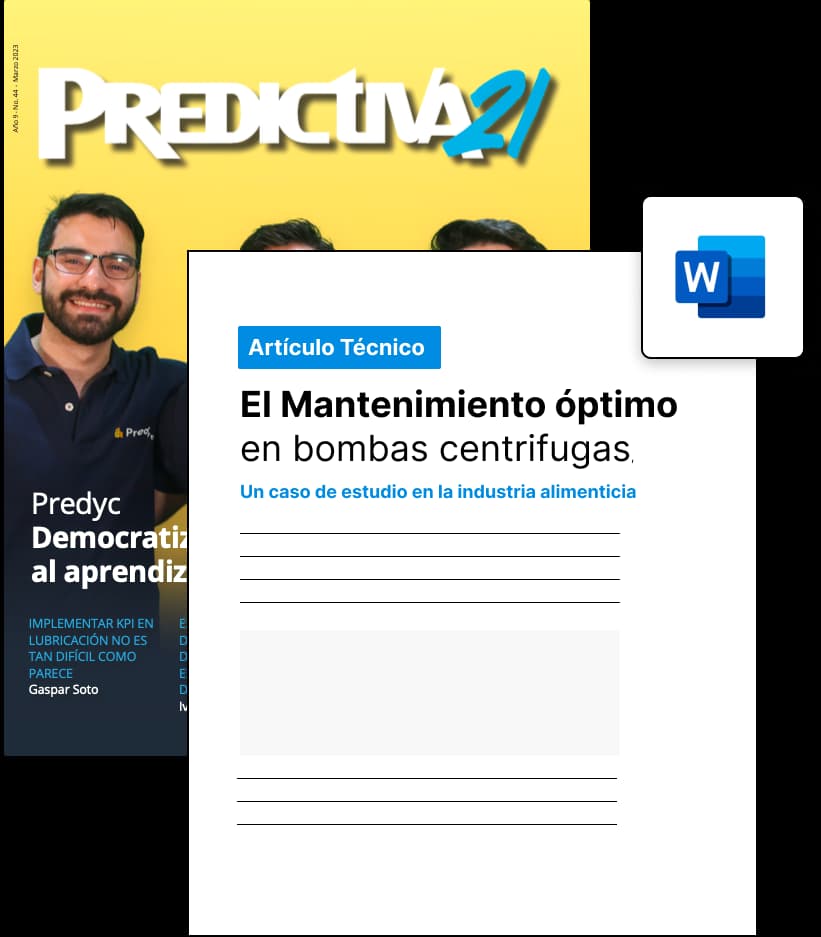
Aplicación de Metodología para Análisis de Modos y Efectos de Falla para Reducción en Tiempos de Paradas de Planta por Fallas Repetitivas
Articulo 24 de abril de 2019Las líneas de producción de la mayoría de las empresas tienen como objetivo cumplir mínimo el 90% de la producción programada. Este margen indica que debemos tener el mínimo de paradas por causas técnicas, para el cumplimiento de estos planes, es fundamental el rol del departamento de mantenimiento e ingeniería y más aún el análisis correcto de cada eventualidad para así disminuir al mínimo su ocurrencia, disminuyendo los tiempos de parada de planta y los costos de ineficiencia. La planta se hace más segura y garantiza la inocuidad de los alimentos producidos a nuestros clientes.
Las empresas de productos de consumo masivo son más propensas a paradas técnicas en especial las que cuentan con líneas de producción en serie, logrando una alta criticidad operacional en todo momento. Todas las unidades de negocio son independientes y se rentabilizan por sí solas, siendo todas en procesos continuos. En la Figura N°1 se observa línea de Pan especial, donde se elabora y comercializan 7 formatos distintos.

Las fabricas panificadoras de alto nivel de automatización, son un claro ejemplo de los arreglos de equipos en serie, esto di culta un poco el análisis correcto de fallas ya que un funcionamiento anormal en cualquier punto de la línea, la detiene por completo, esta situación puede generar las siguientes desventajas:
- Análisis incorrecto de la raíz real de las fallas.
- Alto nivel de mermas.
- Baja rentabilidad del negocio.
- Productos de baja calidad para nuestros clientes.
- Tratamiento incorrecto de las paradas técnicas por tiempo insuficiente para la realización de análisis, y tratar de poner las líneas en funcionamiento en el menor tiempo posible.
- Diferenciar el tipo de falla presentada, si es por mantenimiento, operación, control de calidad etc.
Tomaremos un ejemplo real de la manera correcta de realizar un análisis de modo y efectos de falla de una situación real. (AMEF)
Empresa donde se realizará el análisis: Latín American Foods S.A, Ubicada en Santiago de Chile. Equipo a realizar: Desmoldeador L3 (Pan Especial). Latín American Foods S.A. es una Empresa de panadería industrial donde se cuentan con 5 unidades de negocio principales: Marraquetas, Hallullas, Pan especial, Pizzas y Pastelería. Los capitales son chilenos.
La línea de pan especial produce 14.000 unidades panificadoras por hora, siendo sus principales productos, pan de hot dog, hamburguesa, baguette, chocoso, entre otros. Esta línea en particular cuenta con un equipo que se encarga de sacar (sistema de vacío) el pan que viene de las bandejas de 16 unidades. El producto viene de un sistema de cocción en horno de módulos continuo y su fabricante es Mondial Forni. En resumen, el equipo de análisis es el desmoldeador automático de pan el cual se muestra en la figura número 4 y sus especificaciones técnicas son las siguientes:

Datos técnicos:
- Masa: 2250 kg.
- Tensión: 400 V 3 F + N + T.
- Potencia absorbida nominal: 46,5 kW.
- Consumo de aire:20 Nl/min.
- Presión de funcionamiento: 6 bar (90 psi).
- El nivel de presión acústica ponderada A de la máquina es inferior a 90º dB (A).
- Grupos o conjuntos que lo integran:
- Motorización vertical.
- Grupo de tratamiento de aire.
- Motorización de rotación cabeza.
- Motorización longitudinal.
- Estación de aspiración.
- Cabeza de toma de productos.
- Teclado de mando.
- Tablero eléctrico.


El primer paso para un análisis de modo y efecto de falla es definir el propósito del equipo en cuestión, en este caso el desmoldeador de vacío automático.
Propósito:
Para realizar el proceso de empaquetado de pan este debe estar a una temperatura ambiente, para lograr esta condición se debe sacar la bandeja en que se hornea, objetivo del desmoldeador. La bandeja sigue su línea a un proceso de lavado y el producto sigue hacia las espiras industriales de enfriamiento y congelado tal como se muestra en la figura N°5.

Función principal:
- Retirar el pan de las bandejas que provienen del horno Mondial Forni, mediante sistema de vacío, por medio de ventosas.
- Colocarlo en el transportador hacia cámara de enfriamiento.
Se debe realizar un diagrama EPS (Entrada-Proceso-Salida), para definir la entrada y salida que se espera del proceso, en la figura Nº 6 se muestra el diagrama EPS de nuestro proceso.
Luego de este diagrama se procede a realizar el diagrama funcional del equipo, el cual se muestra en la figura Nº 6.

Una vez realizado el diagrama funcional se procede a iniciar la elaboración del AMEF como tal teniendo claro las siguientes definiciones.
- Componentes: Partes o piezas del equipo.
- Función: Actividad para la cual el equipo fue diseñada.
- Falla Funcional: sucede cuando el sistema opera por fuera de parámetros normales o deseados.
- Modo de falla: es una causa de falla o una posible manera en la que un sistema puede fallar.
En la imagen número 7 se muestra un ejemplo de cómo analizar el modo de falla de uno de los conjuntos pertenecientes al equipo estudiado.
Basado en la imagen número 8, una vez tenemos los modos de falla, suponemos que el modo en que fallo el equipo fue por los rodamientos dañados, y realizamos un análisis ¿Por qué la maquina no está desmoldando el pan? Por qué el desmoldeador no se está moviendo de manera vertical, ¿Por qué no se está moviendo de manera vertical? Por qué fallaron los rodamientos lineales, ¿Por qué fallaron los rodamientos lineales? Se encontraban secos y se desarmaron, ¿Por qué se encontraban secos? Por qué no se lubricaron. Acá tenemos un claro ejemplo que la falla fue por lubricación, ósea que debemos verificar si tienen un plan de lubricación creado o de ser así que su frecuencia sea la adecuada.
Este análisis lo podemos realizar independientemente cual fuese la parte objeto por la que se detuvo el equipo, por eso la importancia de considerarlos todos en la planilla del AMEF.
Ventajas del AMEF:
- Identificar las posibles fallas en un proceso o sistema.
- Conocer a fondo el proceso o el sistema.
- Identificar las causas posibles de las fallas.
- Identificar los tiemposóptimos de los upgrade.
- Aumentar la disponibilidad de maquinas.
- Cumplimiento del plan de negocios.
- Generación de ventaja competitiva en mejora enfocada
- Cumplimiento del EBITDA.
- Logra capacitación permanente y update en conocimiento.


Autores:
Rodrigo Gomez D.
M. SC, Ingeniero civil mecánico (U.T.F.S.M.)
Valparaíso Chile
Gerente de Mantenimiento Planta LAF.
Correo: rgomez@lafchile.com
Fabiola Vargas R.
Ingeniero Mecánico (Universidad de Carabobo)
Carabobo Venezuela
Planificador de Mantenimiento Planta LAF.
Dinos qué te ha parecido el artículo
Artículos recomendados
El monitoreo de condición como generador de conocimientos de la Gestión de Activos

Re-evolución de la naturaleza holística del aire

Programación del mantenimiento preventivo

El Podcast de Mantenimiento 4.0, el formato que muchos prefieren.

Publica tu artículo en la revista #1 de Mantenimiento Industrial
Publicar un artículo en la revista es gratis, no tiene costo.
Solo debes asegurarte que no sea un artículo comercial.
¿Qué esperas?
O envía tu artículo directo: articulos@predictiva21.com
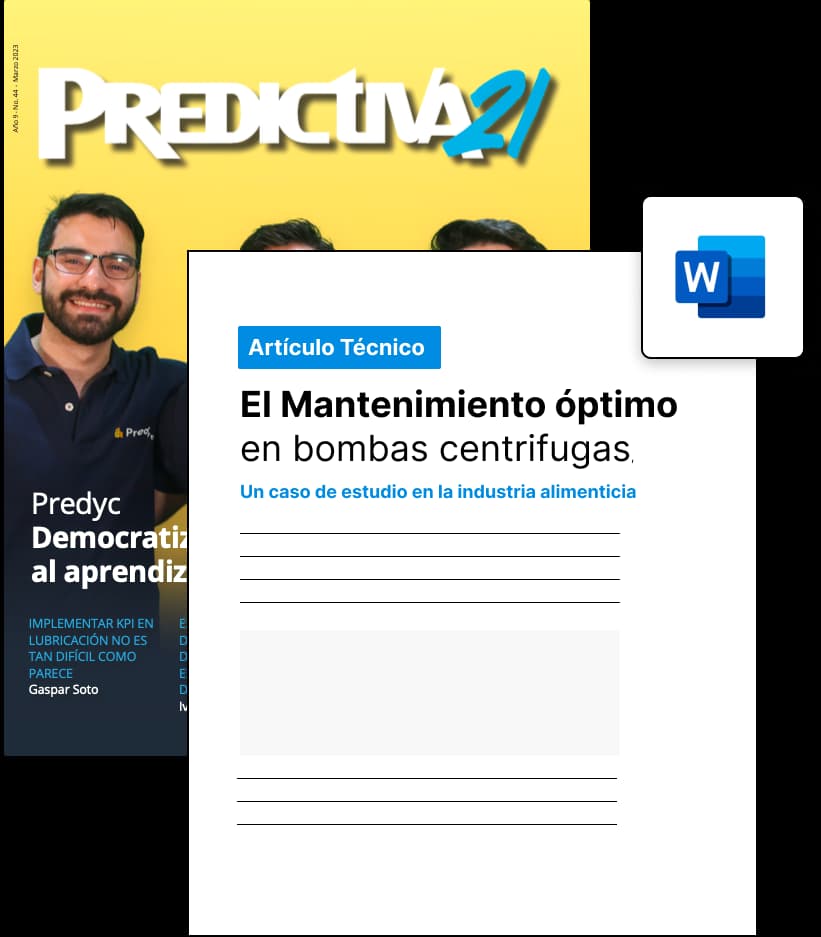