Más allá de la curva P-F
Articulo6 de noviembre de 2019
Introducción
Muchos autores incluyen en sus libros y artículos de revistas diferentes maneras en las que la curva P-F puede ser utilizada en el campo del mantenimiento industrial. Pocos gestores de mantenimiento logran entender con claridad lo valiosa que es la interpretación de esta gráfica en el camino hacia la proactividad y el aseguramiento de la confiabilidad operativa de las plantas industriales.
Esta curva nos debe llevar a comprender que la confiabilidad del mantenimiento se logra saltando del punto F (fallas funcionales) al punto P (fallas potenciales) hasta una zona de proactividad donde diseñamos diferentes mecanismos que nos permitan hacer un mantenimiento de precisión, sin desperdicios, con el mínimo de defectos posibles y que nos permita sobre todo anticiparnos a la falla de la máquina.
Es decir, el gestor de mantenimiento debe buscar los mecanismos probados y no probados que le permitan estar lo más a la izquierda posible en la curva, en una zona segura y a la vez eficiente.

Contenido
Durante más de trece años de trabajar en la ingeniería del mantenimiento he tenido la oportunidad de pasar por todas las etapas de la curva P-F: la del mantenimiento reactivo, es decir actuar hasta cuando el equipo falla. La del mantenimiento preventivo, cambiando los repuestos e interviniendo los equipos con una frecuencia definida. Hasta llegar al mantenimiento predictivo aplicando las técnicas de monitoreo de condición y ensayos no destructivos. Ahora viviendo el modo proactivo en el que he encontrando de manera fascinante el camino hacia la que podríamos llamar “Confiabilidad”.
Este camino implica plantear una estrategia que nos permita de una forma ordenada ir paso a paso escalando desde el punto F al punto P.
En cada etapa hay dificultades culturales, resistencia al cambio, fracasos y lo importante será tener claro el objetivo para seguir adelante rompiendo estas barreras.
Vivir en un completo estado de mantenimiento reactivo es estresante y muy costoso, es desgastante y existe el riesgo que nos acostumbremos a vivir de esa manera creyendo que es lo normal y que todas las labores de mantenimiento que hacemos son las correctas. Definitivamente no podemos dar confiabilidad cuando la mayor parte del mantenimiento que realizamos es de este tipo.
En el mantenimiento preventivo las labores son más coordinadas, se genera mucha labor de planificación, es la base de todo proceso de mantenimiento y confiabilidad. Es una etapa difícil porque las fallas seguirán ocurriendo y muchas veces tendrá que reprogramar su mantenimiento, habrá constantes discusiones con el equipo de producción ya que ellos querrán producir y usted mantener el equipo.
La efectividad del mantenimiento se empieza a sentir con la implementación del mantenimiento predictivo, quizá iniciar con rutas de inspección no muy sofisticadas, viendo, oyendo, sintiendo, oliendo, anotando las anormalidades que identifique en los equipos y máquinas para coordinar su corrección.
Se dibujará en usted una sonrisa cuando sienta la genialidad de detectar el inicio de una falla cuando ningún humano era capaz de hacerlo, pero para esto previamente habrá tenido que justificar la implementación del sistema predictivo ya sea propio o subcontratado. La detección temprana de las fallas o defectos se logra utilizando técnicas de monitoreo de condición y evaluación de elementos de las máquinas: ultrasonidos, termografía, análisis de vibraciones, análisis de aceites y ensayos no destructivos, son las técnicas más utilizadas.
Habiendo pasado por dichas etapas podemos iniciar la optimización de las mismas ya que siempre habrá un porcentaje de cada una en nuestro esquema de mantenimiento. A esta optimización se le llama mantenimiento proactivo o de confiabilidad. Consistirá entonces en minimizar el mantenimiento reactivo, optimizar el preventivo y enfocar el mantenimiento predictivo al monitoreo por condición basado en el riesgo y criticidad de las máquinas.
Si trazamos sobre la curva P-F una gráfica de costos de mantenimiento, podemos observar que los costos más bajos se obtienen en el mantenimiento proactivo o de confiabilidad y los costos más elevados se registran cuando vivimos en un modo de mantenimiento reactivo. Está comprobado que pasar de un mantenimiento totalmente reactivo a un mantenimiento proactivo puede significar un ahorro en costos de mantenimiento hasta de 30%, que puede ser insignificante comparado con los beneficios que se obtendrán en la operación.
El identificar la falla cuando aún es potencial (punto P) sin llegar a funcional (punto F) nos da muchas ventajas porque nos permite planificar los repuestos, la mano de obra, informar oportunamente a producción para hacer la intervención del equipo en un periodo de poca demanda, con inventarios suficientes y con la debida coordinación de las diferentes áreas involucradas. Para lograr la proactividad necesitamos implementar inicialmente el mantenimiento preventivo y predictivo, es como una caja de cambios mecánica en la que los cambios tienen que ir de uno en uno y de forma secuencial, el no hacerlo de esta manera nos puede hacer perder la potencia y tener que regresar a una relación donde incluso se puede detener la máquina.
Tener el mapa bien trazado en el tiempo y con objetivos claros debe ser la clave. Las empresas que cuentan con un mantenimiento de clase mundial han llegado a tener menos de un 10% de mantenimiento no planeado, este debe ser uno de los objetivos en su planta.
Cursos recomendados






%252FImagen%252FRAMPREDYC-1730060420837.webp%3Falt%3Dmedia%26token%3D2634a7f0-988e-4022-b91f-382503e6e9db&w=3840&q=75)

Resumen:
Se debe trazar un plan estratégico que puede implicar meses o años que nos permita pasar de tener un alto porcentaje de mantenimiento reactivo a un mantenimiento mayormente proactivo, que alcance indicadores de clase mundial y que de confiabilidad a la operación de los activos.
El camino es arduo y complejo, pero es alcanzable. Muchas industrias lo han logrado a nivel mundial, necesitando para ello inversión, perseverancia, estrategia y cambios de cultura organizacional.
Las recompensas de alcanzar un mantenimiento proactivo se verán reflejadas en una reducción de los costos de mantenimiento y operación, mejora en la disponibilidad de las maquinas, que produzcan como mínimo la cantidad de unidades para la que fueron diseñadas y que las pérdidas por calidad sean mínimas.

mantenimiento proactivo
Autor: Víctor Blanco
Dinos qué te ha parecido el artículo
Artículos recomendados
20.5.- Bomba Vertical Tipo Turbina

Formación en ingeniería industrial y sus ramas

Experiencias en el desarrollo de Análisis de Confiabilidad, Disponibilidad y Mantenibilidad (Análisis RAM).

Fundamentos de funcionamiento de rodamientos

Publica tu artículo en la revista #1 de Mantenimiento Industrial
Publicar un artículo en la revista es gratis, no tiene costo.
Solo debes asegurarte que no sea un artículo comercial.
¿Qué esperas?
O envía tu artículo directo: articulos@predictiva21.com
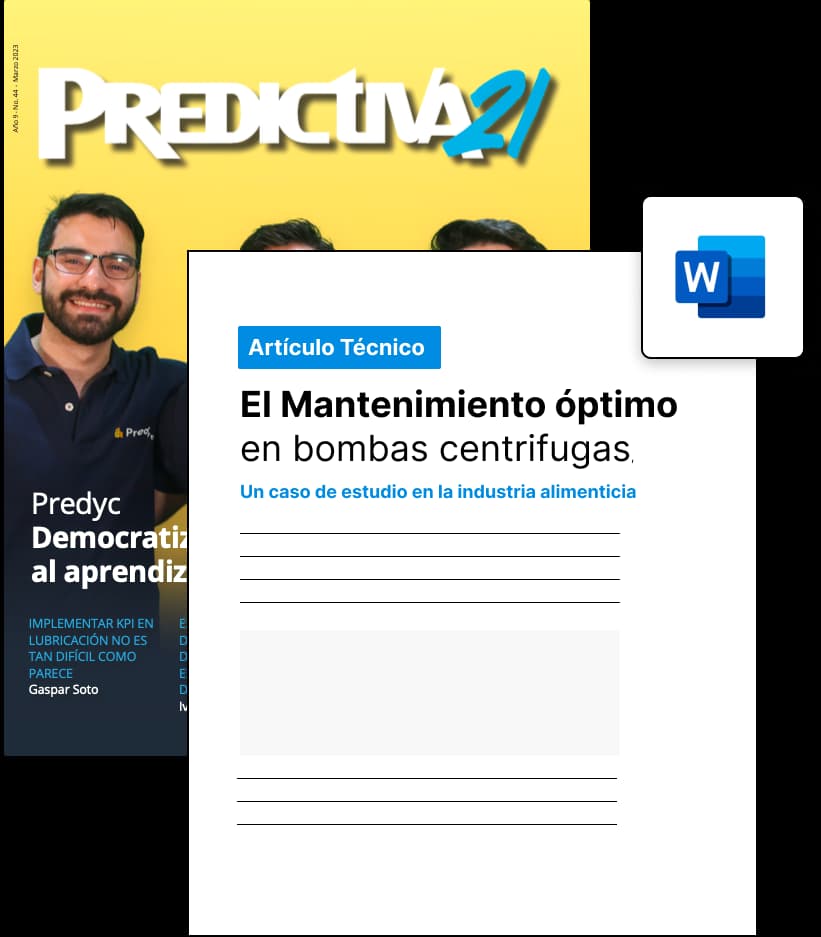
Más allá de la curva P-F
Articulo 6 de noviembre de 2019Introducción
Muchos autores incluyen en sus libros y artículos de revistas diferentes maneras en las que la curva P-F puede ser utilizada en el campo del mantenimiento industrial. Pocos gestores de mantenimiento logran entender con claridad lo valiosa que es la interpretación de esta gráfica en el camino hacia la proactividad y el aseguramiento de la confiabilidad operativa de las plantas industriales.
Esta curva nos debe llevar a comprender que la confiabilidad del mantenimiento se logra saltando del punto F (fallas funcionales) al punto P (fallas potenciales) hasta una zona de proactividad donde diseñamos diferentes mecanismos que nos permitan hacer un mantenimiento de precisión, sin desperdicios, con el mínimo de defectos posibles y que nos permita sobre todo anticiparnos a la falla de la máquina.
Es decir, el gestor de mantenimiento debe buscar los mecanismos probados y no probados que le permitan estar lo más a la izquierda posible en la curva, en una zona segura y a la vez eficiente.

Contenido
Durante más de trece años de trabajar en la ingeniería del mantenimiento he tenido la oportunidad de pasar por todas las etapas de la curva P-F: la del mantenimiento reactivo, es decir actuar hasta cuando el equipo falla. La del mantenimiento preventivo, cambiando los repuestos e interviniendo los equipos con una frecuencia definida. Hasta llegar al mantenimiento predictivo aplicando las técnicas de monitoreo de condición y ensayos no destructivos. Ahora viviendo el modo proactivo en el que he encontrando de manera fascinante el camino hacia la que podríamos llamar “Confiabilidad”.
Este camino implica plantear una estrategia que nos permita de una forma ordenada ir paso a paso escalando desde el punto F al punto P.
En cada etapa hay dificultades culturales, resistencia al cambio, fracasos y lo importante será tener claro el objetivo para seguir adelante rompiendo estas barreras.
Vivir en un completo estado de mantenimiento reactivo es estresante y muy costoso, es desgastante y existe el riesgo que nos acostumbremos a vivir de esa manera creyendo que es lo normal y que todas las labores de mantenimiento que hacemos son las correctas. Definitivamente no podemos dar confiabilidad cuando la mayor parte del mantenimiento que realizamos es de este tipo.
En el mantenimiento preventivo las labores son más coordinadas, se genera mucha labor de planificación, es la base de todo proceso de mantenimiento y confiabilidad. Es una etapa difícil porque las fallas seguirán ocurriendo y muchas veces tendrá que reprogramar su mantenimiento, habrá constantes discusiones con el equipo de producción ya que ellos querrán producir y usted mantener el equipo.
La efectividad del mantenimiento se empieza a sentir con la implementación del mantenimiento predictivo, quizá iniciar con rutas de inspección no muy sofisticadas, viendo, oyendo, sintiendo, oliendo, anotando las anormalidades que identifique en los equipos y máquinas para coordinar su corrección.
Se dibujará en usted una sonrisa cuando sienta la genialidad de detectar el inicio de una falla cuando ningún humano era capaz de hacerlo, pero para esto previamente habrá tenido que justificar la implementación del sistema predictivo ya sea propio o subcontratado. La detección temprana de las fallas o defectos se logra utilizando técnicas de monitoreo de condición y evaluación de elementos de las máquinas: ultrasonidos, termografía, análisis de vibraciones, análisis de aceites y ensayos no destructivos, son las técnicas más utilizadas.
Habiendo pasado por dichas etapas podemos iniciar la optimización de las mismas ya que siempre habrá un porcentaje de cada una en nuestro esquema de mantenimiento. A esta optimización se le llama mantenimiento proactivo o de confiabilidad. Consistirá entonces en minimizar el mantenimiento reactivo, optimizar el preventivo y enfocar el mantenimiento predictivo al monitoreo por condición basado en el riesgo y criticidad de las máquinas.
Si trazamos sobre la curva P-F una gráfica de costos de mantenimiento, podemos observar que los costos más bajos se obtienen en el mantenimiento proactivo o de confiabilidad y los costos más elevados se registran cuando vivimos en un modo de mantenimiento reactivo. Está comprobado que pasar de un mantenimiento totalmente reactivo a un mantenimiento proactivo puede significar un ahorro en costos de mantenimiento hasta de 30%, que puede ser insignificante comparado con los beneficios que se obtendrán en la operación.
El identificar la falla cuando aún es potencial (punto P) sin llegar a funcional (punto F) nos da muchas ventajas porque nos permite planificar los repuestos, la mano de obra, informar oportunamente a producción para hacer la intervención del equipo en un periodo de poca demanda, con inventarios suficientes y con la debida coordinación de las diferentes áreas involucradas. Para lograr la proactividad necesitamos implementar inicialmente el mantenimiento preventivo y predictivo, es como una caja de cambios mecánica en la que los cambios tienen que ir de uno en uno y de forma secuencial, el no hacerlo de esta manera nos puede hacer perder la potencia y tener que regresar a una relación donde incluso se puede detener la máquina.
Tener el mapa bien trazado en el tiempo y con objetivos claros debe ser la clave. Las empresas que cuentan con un mantenimiento de clase mundial han llegado a tener menos de un 10% de mantenimiento no planeado, este debe ser uno de los objetivos en su planta.
Cursos recomendados






%252FImagen%252FRAMPREDYC-1730060420837.webp%3Falt%3Dmedia%26token%3D2634a7f0-988e-4022-b91f-382503e6e9db&w=3840&q=75)

Resumen:
Se debe trazar un plan estratégico que puede implicar meses o años que nos permita pasar de tener un alto porcentaje de mantenimiento reactivo a un mantenimiento mayormente proactivo, que alcance indicadores de clase mundial y que de confiabilidad a la operación de los activos.
El camino es arduo y complejo, pero es alcanzable. Muchas industrias lo han logrado a nivel mundial, necesitando para ello inversión, perseverancia, estrategia y cambios de cultura organizacional.
Las recompensas de alcanzar un mantenimiento proactivo se verán reflejadas en una reducción de los costos de mantenimiento y operación, mejora en la disponibilidad de las maquinas, que produzcan como mínimo la cantidad de unidades para la que fueron diseñadas y que las pérdidas por calidad sean mínimas.

mantenimiento proactivo
Autor: Víctor Blanco
Dinos qué te ha parecido el artículo
Artículos recomendados
Tipos de mantenimiento

La Otra Visión de la Confiabilidad Operacional

Lourival Tavares, pasión por el Mantenimiento

Redes de conocimiento AMGA

Publica tu artículo en la revista #1 de Mantenimiento Industrial
Publicar un artículo en la revista es gratis, no tiene costo.
Solo debes asegurarte que no sea un artículo comercial.
¿Qué esperas?
O envía tu artículo directo: articulos@predictiva21.com
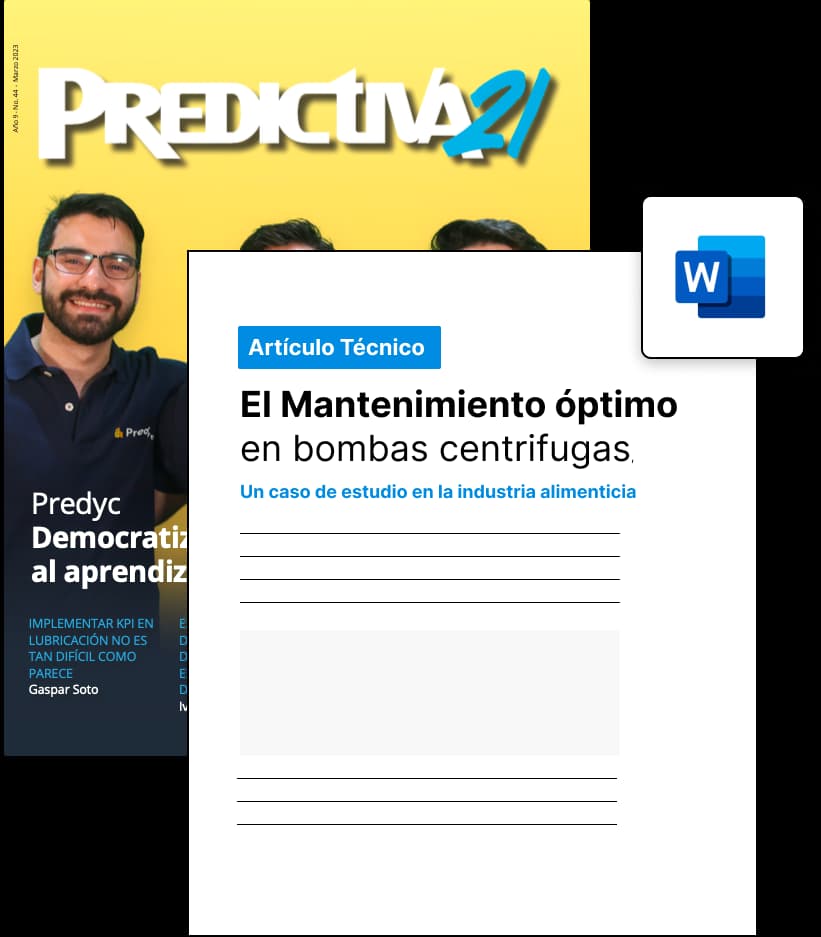