Caso Práctico: “Desbalance Resistivo en conexiones eléctricas de un motor eléctrico”
Articulo19 de agosto de 2019
El motor eléctrico es la máquina eléctrica rotativa con mayor presencia en la industria y en conjunto con una bomba u otra máquina, mueven una carga que da origen a un producto final.
No es extraño que un motor eléctrico sea parte de un sistema crítico, por tanto dotar al sistema de disponibilidad a través de una alta confiabilidad, debe ser una función que el motor eléctrico también debe cumplir.
Es habitual medir la resistencia de aislamiento de un motor eléctrico y si su valor está de acuerdo al estándar, se pone en servicio. Sin embargo, al poco tiempo de funcionamiento empieza a presentar problemas hasta fallar afectando la disponibilidad del sistema generando costos de ineficiencia.
Es habitual medir la resistencia de aislamiento de un motor eléctrico y si su valor está de acuerdo al estándar, se pone en servicio. Sin embargo, al poco tiempo de funcionamiento empieza a presentar problemas hasta fallar afectando la disponibilidad del sistema generando costos de ineficiencia.
El caso que se presenta a continuación pudo haber sido uno de esos, si no es porque aplicaron pruebas adicionales que permitieron evidenciar el problema.
Análisis estático de motores eléctricos
El análisis estático de motores eléctricos consiste en efectuar una serie de mediciones eléctricas al motor cuando está detenido. Entre estas mediciones se encuentran:
- Resistencia de aislamiento a tierra.
- Capacitancia a tierra.
- Indice de polarización (IP).
- Indice de absorción (DAR).
- Resistencia eléctrica entre bobinas.
- Inductancia entre bobinas.
Estas mediciones permiten efectuar un análisis más completo de un motor eléctrico, lo cual ayuda al analista a mejorar sustancialmente el diagnóstico del motor y así, poder evitar fallas inesperadas.
Las seis zonas de falla
PDMA Corporations, desarrolló el concepto de las 6 zonas de falla de un motor, las que se muestran a continuación:
Las seis zonas eléctricas de falla:
- Calidad de la Alimentacion
- Circuito de potencia
- Aislamiento
- Estator
- Rotor
- Entrehierro
La zona de falla afectada
La zona de falla en donde se detectó el problema corresponde al circuito de potencia y el cual se define como:
El circuito de potencia: Se refiere a todos los conductores y conexiones que existen desde el punto donde se realice la prueba hasta los bornes terminales del motor. Esto puede incluir interruptores, fusibles, contactores, protecciones contra sobrecarga, seccionadores y bornas.
El problema detectado
Durante el mantenimiento mayor de una planta de proceso, correspondía realizar el mantenimiento preventivo de un motor eléctrico de 380 (V), 50 HP y 2965 RPM que forma parte del conjunto bomba de carga a una planta de proceso.
Una vez entregado el motor por la empresa mantenedora y antes de realizar el montaje en planta, se realizó con el instrumento MCE Max de PDMA el test denominado AC Auto, el cual realiza de forma automática la medición de resistencia e inductancia de bobinas, curva tiempo resistencia, IP, DAR, resistencia de aislamiento a tierra y capacitancia a tierra.
La medición se realizó en los cables terminales de la caja de conexiones del motor, la imagen 1 muestra el punto de conexión.

Al efectuar el análisis de la medición se detectó un aumento de resistencia en la fase 3 provocando un desbalance resistivo anormal de un 18.31%. La IEEE Std 1415™ 2006 en el punto 4.3.40 establece que el desbalance resistivo debe estar entre un 3% y un 5% de la resistencia promedio, cualquier valor sobre debe ser investigado. Sin embargo, la IEEE Std 1068™ 2015 indica que el desbalance resistivos no podrá ser superior a un 1% después que un motor ha sido sometido a mantención. PDMA Corporations, recomienda que el desbalance resistivo para motores nuevos o rebobinados debe ser inferior a un 1% y para motores en servicio debe ser menor a un 3%. La imagen N° 2 muestra el reporte de medición.

Al revisar los cables de conexión, se evidenció que entre los cables de las bobinas del motor y los cables de conexión a la fuente de alimentación existía un manguito de conexión, ver imagen N° 1.
Con el objeto de descartar que el problema no estuviese en la conexión que ejerce el manguito entre ambos cables, se midió nuevamente la resistencia de las bobinas conectando el instrumento sobre el manguito de conexión de las tres fases, ver imagen N° 3.
El reporte de la medición 2, indica que la resistencia de la fase 3 y el desbalance resistivo todavía siguen elevados, ver imagen N° 4.


Con la idea de detectar cual era el problema que provocaba la alta resistencia en la fase 3, se procedió a retirar el manguito de conexión. En el retiro se evidenció que existía una conexión deficiente entre el manguito y el cable de la bobina 3, provocado por el no retiro del barniz aislante del conductor de la bobina, ver imagen N° 5.

En la imagen 5, se aprecia que la conexión entre la bobina del motor y el cable de conexión a la fuente de alimentación, se realizaba solo por el contacto entre las puntas sin aislamiento de ambos conductores.
Se retira el barniz aislante de los cables de conexión de la fase 3 del motor, se unen y se efectúa una nueva medición, ver imagen N° 6.

Esta vez, la resistencia de la fase 3 disminuye y también el desbalance resistivo a un 9.86%, pero todavía está por sobre el máximo aceptable, ver imagen N° 7.

Para asegurar que el alto desbalance resistivo tenía como causa una de ciencia en la conexión de la fase 3, se efectúa una cuarta medición, pero esta vez, se mejora la conexión instalando una prensa partida, ver imagen N° 8.

Esta vez, la resistencia y el desbalance resistivo de la fase 3 disminuyen. El desbalance resistivo lo hizo de un 9.85% a un 3.07%, valor que esta cercano al máximo recomendado, ver imagen N° 9.

Con la última medición se comprueba que el problema de desbalance resistivo tenía como causa una de ciencia en la conexión eléctrica de la fase 3 del motor. Finalmente, se decidió instalar una bornera de conexiones en el motor, para efectuar una conexión óptima de los cables de fuerza con las bobinas del motor. La imagen N° 10 muestra la bornera de conexiones instalada.

Instalada la bornera de conexiones, se efectúa la quinta medición y se comprueba que la resistencia de la fase 3 disminuye a valores muy similares de las otras dos fases, a su vez, el desbalance resistivo dismiuyó de 3.07% a un 0.89%, valor que está muy por debajo del 1% recomendado, ver imagen N° 11.

Cursos recomendados






%252FImagen%252FRAMPREDYC-1730060420837.webp%3Falt%3Dmedia%26token%3D2634a7f0-988e-4022-b91f-382503e6e9db&w=3840&q=75)

Conclusiones
- En función a los resultados del análisis y a la evidencia presentada, se concluye que el elevado desbalance resistivo que presentaba el motor, fue provocado por una de ciencia en la conexión eléctrica entre las bobinas del motor y los cables de conexión a la línea de fuerza.
- Aplicar una tensión a un motor con desbalance resistivo, dará origen a corrientes de secuencia negativa. Estas corrientes causan calentamiento en los bobinados del motor. Es así como un desbalance de tensión de un 3.5% provocará un aumento de la temperatura en el motor de un 25%. También, la conexión con mayor resistencia dará origen a una anomalía térmica provocando una elevación de T° de la conexión, la que afecta al material aislante pudiendo provocarse un cortocircuito a tierra en la caja de conexiones del motor.
Recomendaciones
- La simple medición de la resistencia de aislamiento en un motor, no es su ciente para indicar la condición del mismo, sino, que es necesaria la medición de una serie de variables que en conjunto permiten hacer un diagnóstico con mayor confiabilidad del motor. Hoy en día la tecnología permite que con un solo click se puedan medir todas las variables de una sola vez, además de su registro para un análisis de tendencia.
- Considere siempre que debe proveer al analista la instrumentación y capacitación adecuada, y la oportunidad de medición. Cada medición que se realice mejora la curva de aprendizaje del analista, hasta convertirse en un experto.
Estándares aplicables
- IEEE Std 1415™-2006, IEEE Guide for Induction Machinery Maintenance Testing and Failure Analysis.
- IEEE Std 1068™-2015, IEEE Standard for the Repair and Rewinding of AC Electric Motors in the Petroleum, Chemical, and Process Industries.
Autor: Jaime Zamora C.
Ingeniero Eléctrico
Diplomado en Gestión de Activos y Mantenimiento
Ingeniero de Mantención
Enap Refinerías Aconcagua
Chile
Correo: jzamora@enap.cl
Dinos qué te ha parecido el artículo
Artículos recomendados
Uso del Programa Life CPR - ComSys© para la Selección del Accionador y el Arreglo Óptimo en Plantas Compresoras de Gas (III Parte)

Desarrollando a otras: Estrategias para desarrollo de talento con enfoque de género

Desvelando el camino hacia la excelencia: Explorando el Modelo ART de transformación de Confiabilidad de Activos

Cálculo de cantidad de grasa para llenado inicial de rodamientos

Publica tu artículo en la revista #1 de Mantenimiento Industrial
Publicar un artículo en la revista es gratis, no tiene costo.
Solo debes asegurarte que no sea un artículo comercial.
¿Qué esperas?
O envía tu artículo directo: articulos@predictiva21.com
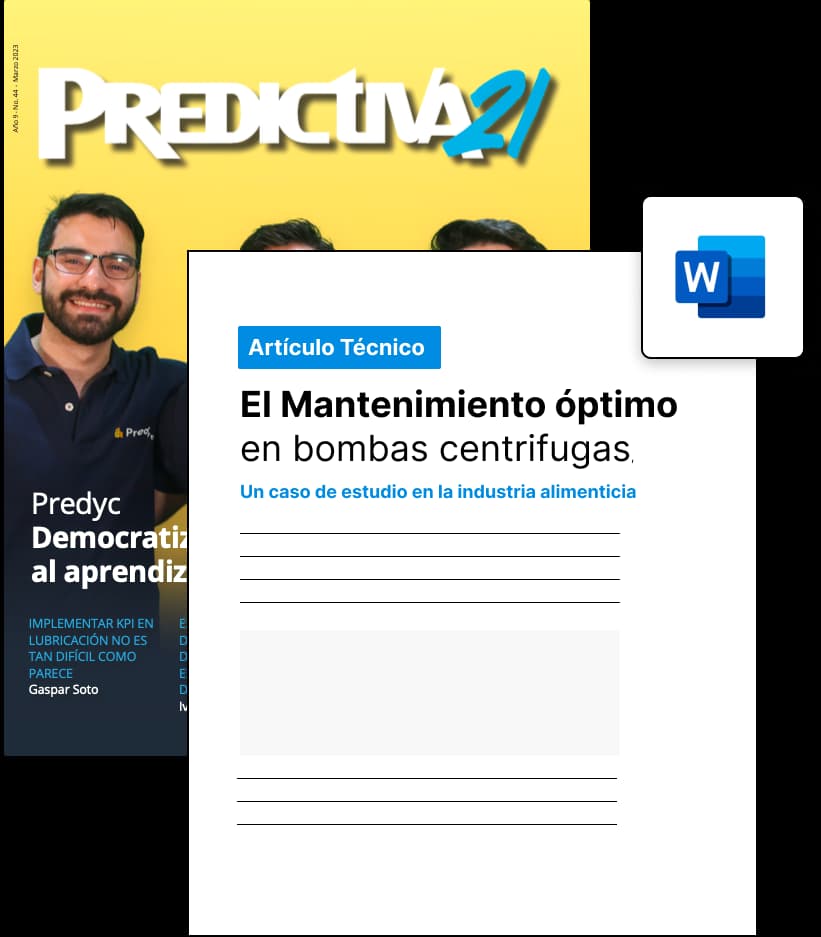
Caso Práctico: “Desbalance Resistivo en conexiones eléctricas de un motor eléctrico”
Articulo 19 de agosto de 2019El motor eléctrico es la máquina eléctrica rotativa con mayor presencia en la industria y en conjunto con una bomba u otra máquina, mueven una carga que da origen a un producto final.
No es extraño que un motor eléctrico sea parte de un sistema crítico, por tanto dotar al sistema de disponibilidad a través de una alta confiabilidad, debe ser una función que el motor eléctrico también debe cumplir.
Es habitual medir la resistencia de aislamiento de un motor eléctrico y si su valor está de acuerdo al estándar, se pone en servicio. Sin embargo, al poco tiempo de funcionamiento empieza a presentar problemas hasta fallar afectando la disponibilidad del sistema generando costos de ineficiencia.
Es habitual medir la resistencia de aislamiento de un motor eléctrico y si su valor está de acuerdo al estándar, se pone en servicio. Sin embargo, al poco tiempo de funcionamiento empieza a presentar problemas hasta fallar afectando la disponibilidad del sistema generando costos de ineficiencia.
El caso que se presenta a continuación pudo haber sido uno de esos, si no es porque aplicaron pruebas adicionales que permitieron evidenciar el problema.
Análisis estático de motores eléctricos
El análisis estático de motores eléctricos consiste en efectuar una serie de mediciones eléctricas al motor cuando está detenido. Entre estas mediciones se encuentran:
- Resistencia de aislamiento a tierra.
- Capacitancia a tierra.
- Indice de polarización (IP).
- Indice de absorción (DAR).
- Resistencia eléctrica entre bobinas.
- Inductancia entre bobinas.
Estas mediciones permiten efectuar un análisis más completo de un motor eléctrico, lo cual ayuda al analista a mejorar sustancialmente el diagnóstico del motor y así, poder evitar fallas inesperadas.
Las seis zonas de falla
PDMA Corporations, desarrolló el concepto de las 6 zonas de falla de un motor, las que se muestran a continuación:
Las seis zonas eléctricas de falla:
- Calidad de la Alimentacion
- Circuito de potencia
- Aislamiento
- Estator
- Rotor
- Entrehierro
La zona de falla afectada
La zona de falla en donde se detectó el problema corresponde al circuito de potencia y el cual se define como:
El circuito de potencia: Se refiere a todos los conductores y conexiones que existen desde el punto donde se realice la prueba hasta los bornes terminales del motor. Esto puede incluir interruptores, fusibles, contactores, protecciones contra sobrecarga, seccionadores y bornas.
El problema detectado
Durante el mantenimiento mayor de una planta de proceso, correspondía realizar el mantenimiento preventivo de un motor eléctrico de 380 (V), 50 HP y 2965 RPM que forma parte del conjunto bomba de carga a una planta de proceso.
Una vez entregado el motor por la empresa mantenedora y antes de realizar el montaje en planta, se realizó con el instrumento MCE Max de PDMA el test denominado AC Auto, el cual realiza de forma automática la medición de resistencia e inductancia de bobinas, curva tiempo resistencia, IP, DAR, resistencia de aislamiento a tierra y capacitancia a tierra.
La medición se realizó en los cables terminales de la caja de conexiones del motor, la imagen 1 muestra el punto de conexión.

Al efectuar el análisis de la medición se detectó un aumento de resistencia en la fase 3 provocando un desbalance resistivo anormal de un 18.31%. La IEEE Std 1415™ 2006 en el punto 4.3.40 establece que el desbalance resistivo debe estar entre un 3% y un 5% de la resistencia promedio, cualquier valor sobre debe ser investigado. Sin embargo, la IEEE Std 1068™ 2015 indica que el desbalance resistivos no podrá ser superior a un 1% después que un motor ha sido sometido a mantención. PDMA Corporations, recomienda que el desbalance resistivo para motores nuevos o rebobinados debe ser inferior a un 1% y para motores en servicio debe ser menor a un 3%. La imagen N° 2 muestra el reporte de medición.

Al revisar los cables de conexión, se evidenció que entre los cables de las bobinas del motor y los cables de conexión a la fuente de alimentación existía un manguito de conexión, ver imagen N° 1.
Con el objeto de descartar que el problema no estuviese en la conexión que ejerce el manguito entre ambos cables, se midió nuevamente la resistencia de las bobinas conectando el instrumento sobre el manguito de conexión de las tres fases, ver imagen N° 3.
El reporte de la medición 2, indica que la resistencia de la fase 3 y el desbalance resistivo todavía siguen elevados, ver imagen N° 4.


Con la idea de detectar cual era el problema que provocaba la alta resistencia en la fase 3, se procedió a retirar el manguito de conexión. En el retiro se evidenció que existía una conexión deficiente entre el manguito y el cable de la bobina 3, provocado por el no retiro del barniz aislante del conductor de la bobina, ver imagen N° 5.

En la imagen 5, se aprecia que la conexión entre la bobina del motor y el cable de conexión a la fuente de alimentación, se realizaba solo por el contacto entre las puntas sin aislamiento de ambos conductores.
Se retira el barniz aislante de los cables de conexión de la fase 3 del motor, se unen y se efectúa una nueva medición, ver imagen N° 6.

Esta vez, la resistencia de la fase 3 disminuye y también el desbalance resistivo a un 9.86%, pero todavía está por sobre el máximo aceptable, ver imagen N° 7.

Para asegurar que el alto desbalance resistivo tenía como causa una de ciencia en la conexión de la fase 3, se efectúa una cuarta medición, pero esta vez, se mejora la conexión instalando una prensa partida, ver imagen N° 8.

Esta vez, la resistencia y el desbalance resistivo de la fase 3 disminuyen. El desbalance resistivo lo hizo de un 9.85% a un 3.07%, valor que esta cercano al máximo recomendado, ver imagen N° 9.

Con la última medición se comprueba que el problema de desbalance resistivo tenía como causa una de ciencia en la conexión eléctrica de la fase 3 del motor. Finalmente, se decidió instalar una bornera de conexiones en el motor, para efectuar una conexión óptima de los cables de fuerza con las bobinas del motor. La imagen N° 10 muestra la bornera de conexiones instalada.

Instalada la bornera de conexiones, se efectúa la quinta medición y se comprueba que la resistencia de la fase 3 disminuye a valores muy similares de las otras dos fases, a su vez, el desbalance resistivo dismiuyó de 3.07% a un 0.89%, valor que está muy por debajo del 1% recomendado, ver imagen N° 11.

Cursos recomendados






%252FImagen%252FRAMPREDYC-1730060420837.webp%3Falt%3Dmedia%26token%3D2634a7f0-988e-4022-b91f-382503e6e9db&w=3840&q=75)

Conclusiones
- En función a los resultados del análisis y a la evidencia presentada, se concluye que el elevado desbalance resistivo que presentaba el motor, fue provocado por una de ciencia en la conexión eléctrica entre las bobinas del motor y los cables de conexión a la línea de fuerza.
- Aplicar una tensión a un motor con desbalance resistivo, dará origen a corrientes de secuencia negativa. Estas corrientes causan calentamiento en los bobinados del motor. Es así como un desbalance de tensión de un 3.5% provocará un aumento de la temperatura en el motor de un 25%. También, la conexión con mayor resistencia dará origen a una anomalía térmica provocando una elevación de T° de la conexión, la que afecta al material aislante pudiendo provocarse un cortocircuito a tierra en la caja de conexiones del motor.
Recomendaciones
- La simple medición de la resistencia de aislamiento en un motor, no es su ciente para indicar la condición del mismo, sino, que es necesaria la medición de una serie de variables que en conjunto permiten hacer un diagnóstico con mayor confiabilidad del motor. Hoy en día la tecnología permite que con un solo click se puedan medir todas las variables de una sola vez, además de su registro para un análisis de tendencia.
- Considere siempre que debe proveer al analista la instrumentación y capacitación adecuada, y la oportunidad de medición. Cada medición que se realice mejora la curva de aprendizaje del analista, hasta convertirse en un experto.
Estándares aplicables
- IEEE Std 1415™-2006, IEEE Guide for Induction Machinery Maintenance Testing and Failure Analysis.
- IEEE Std 1068™-2015, IEEE Standard for the Repair and Rewinding of AC Electric Motors in the Petroleum, Chemical, and Process Industries.
Autor: Jaime Zamora C.
Ingeniero Eléctrico
Diplomado en Gestión de Activos y Mantenimiento
Ingeniero de Mantención
Enap Refinerías Aconcagua
Chile
Correo: jzamora@enap.cl
Dinos qué te ha parecido el artículo
Artículos recomendados
Análisis Costo Riesgo Beneficio para la selección de conductores de una Planta de Generación Eléctrica

Aprovisionamiento para Garantizar la Confiabilidad de la Producción

El Ingeniero de Confiabilidad: Perfil y Habilidades

GMAO: herramienta de gestión de mantenimiento

Publica tu artículo en la revista #1 de Mantenimiento Industrial
Publicar un artículo en la revista es gratis, no tiene costo.
Solo debes asegurarte que no sea un artículo comercial.
¿Qué esperas?
O envía tu artículo directo: articulos@predictiva21.com
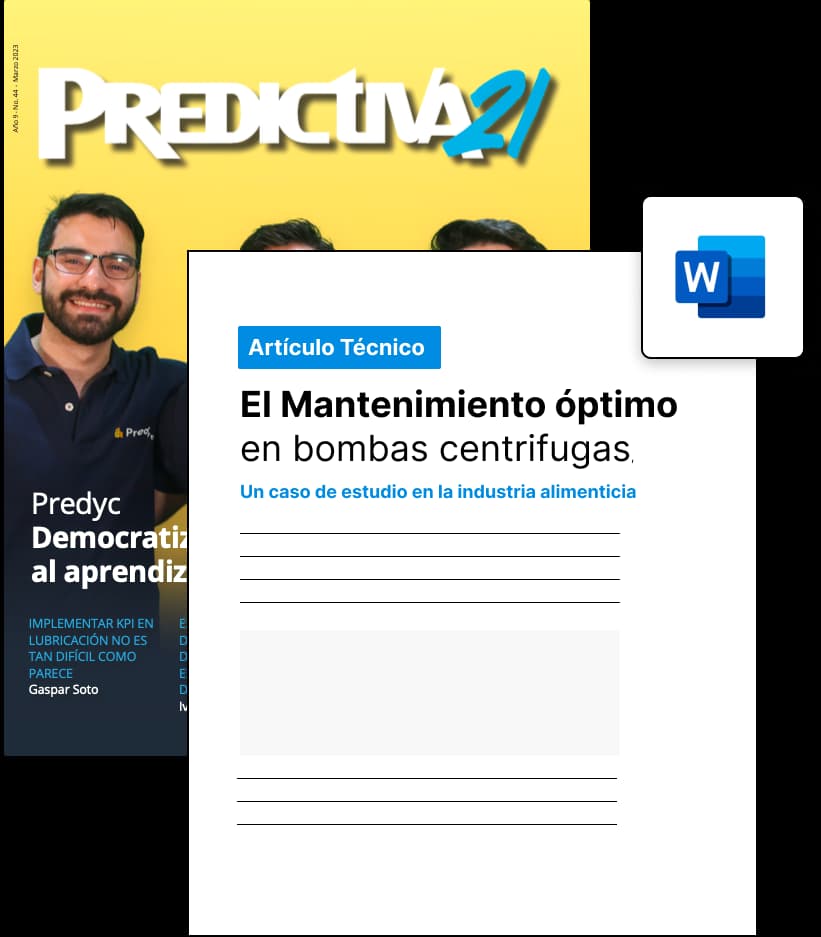