El mantenimiento y su evolución
Articulo12 de agosto de 2020
A principios del siglo XIX, luego de iniciada la Revolución Industrial, se comenzó a implementar el mantenimiento industrial toda vez que requería mejorar la producción de bienes y servicios- Con el tiempo, se fueron especializando los procesos y capacitando al personal hasta llegar a lo que conocemos hoy como uno de los mayores beneficios de la industria.
El mantenimiento industrial es aquel conjunto de medidas de carácter técnico organizativo, que pueden ser o no elaboradas previamente, que tiene como propósito sostener la funcionalidad de los equipos y garantizar un estado óptimo de las máquinas a través del tiempo.
El mantenimiento en el tiempo
- Desde el inicio de las máquinas, se hizo un mantenimiento correctivo total. En él se espera que se origine alguna avería para proceder a repararla. Los costos de mantenimiento resultaban altos por el largo tiempo de paro que se empleaba para solucionar el problema
- Durante la Primera Guerra Mundial se capacitó al personal de mantenimiento correctivo enviándolos a los laboratorios de prevención para evitar fallas. Dieron origen a los departamentos de mantenimiento preventivo.
- Con la Segunda Guerra Mundial se sistematizan los trabajos de mantenimiento preventivo.

- En 1946 es creada la Sociedad Americana de Control de Calidad.
- 1950. William Edward Deming Aplica en la industria japonesa el Control Estadístico de Calidad, donde el criterio de la empresa comienza con el proveedor y termina en el cliente. Se creó al mantenimiento productivo para obtener calidad y cantidad de producto, al tiempo de cuidar las máquinas.
- 1960. La necesidad de mantener naves en vuelo generó el mantenimiento enfocado en la confiabilidad.
- 1970. Se crea el Software Sistema Computarizado para la administración de Mantenimiento, CMMS, centrado en resolver la administración del área de mantenimiento.
- 1971. Seiichi Nakajima crea el Mantenimiento Productivo Total, involucrando a todo el personal de la empresa en le ejecución de todo tipo de mantenimiento, apoyado en los círculos de calidad.
- 1980. El Mantenimiento Centrado en la Confiabilidad fue modificado hacia la Optimización del Mantenimiento Planificado (PMO). Enfoque hacia la confiabilidad = RCM Enfoque hacia los costos = PMO.
- Desde 2005 se maneja la filosofía de la conservación (preservación y mantenimiento.
La gestión de mantenimiento
La gestión de mantenimiento garantiza la continuidad de la actividad operativa, evitando rupturas en el proceso como consecuencia de averías de máquinas y equipos. Un mantenimiento eficaz es uno de los elementos más importantes para el logro de la competitividad y operatividad empresarial en el actual marco de competencia global.
Describe la gestión exitosa y eficaz de los problemas de mantenimiento que participan en el mantenimiento, el funcionamiento y la productividad de una fábrica, instalación o planta de fabricación. Las principales áreas de enfoque de gestión de mantenimiento incluyen operaciones de producción, control ambiental y ecológico, control de inventario, control de calidad y opciones de outsourcing.
Realizar una correcta Gestión del Mantenimiento, es un claro indicador de beneficios para los resultados globales de las pequeñas, medianas y grandes compañías. El Mantenimiento industrial se tiene que valorar como una inversión, que genera beneficios y no como un gasto.
Los costos de Mantenimiento Industrial pueden llegar a alcanzar entre un 30 y 60 % de los costos operativos y es por ello que su actuación en la Industria tiene una incidencia notable sobre los resultados económicos de las compañías, haciendo necesario la correcta planificación y organización de su gestión.
Objetivos del mantenimiento
El objetivo general del mantenimiento es garantizar la producción necesaria en el momento justo, con el mínimo costo integral. El costo integral abarca además del mantenimiento de las máquinas, aspectos como el medio ambiente, el ahorro de energía, la seguridad y la calidad.
Los Objetivos concretos del mantenimiento pueden variar de acuerdo al tipo de industria. Estableciendo tareas de corto, mediano y largo plazo para lograr cumplir con todos de manera simultánea será llegar a la calidad total de mantenimiento.
Costos mínimos:
- Asegurar la máxima productividad de la nómina de mantenimiento.
- Reducir al mínimo el mantenimiento correctivo.
- Minimizar el stock inactivo en almacén.
- Extender la vida útil y productiva de las máquinas.
- Controlar el rendimiento energético de las máquinas.
- Evitar y controlar fugas de vapor, aire presurizado y demás formas de energía.
Máxima producción:
- Asegurar máxima disponibilidad de las máquinas.
- Reparar fallas en el menor tiempo posible con el menor costo.
Calidad:
- Eliminar desperfectos de las máquinas que afectan la calidad de los productos.
- Asegurar que los equipos que controlan la calidad de producto funcionen perfectamente.
Higiene y seguridad laboral:
- Mantener las protecciones de seguridad de los equipos.
- Capacitar al personal en la prevención de accidentes.
Conservación del medio ambiente:
- Controlar fugas y derrames de materiales peligrosos al momento de realizar trabajos.
- Evitar fugas de agua y desperdicios de energía eléctrica.
Mantenimiento Productivo Total
El TPM (Mantenimiento Productivo Total) surgió en Japón gracias a los esfuerzos del Japan Institute of Plant Maintenance (JIPM) como un sistema destinado a lograr la eliminación de las llamadas <seis grandes pérdidas> de los equipos, con el objetivo de facilitar la implantación de la forma de trabajo “Just in Time” o “justo a tiempo”. Es una filosofía de mantenimiento cuyo objetivo es eliminar las pérdidas en producción debidas al estado de los equipos, o en otras palabras, mantener los equipos en disposición para producir a su capacidad máxima productos de la calidad esperada, sin paradas no programadas. Esto supone:
- Cero averías.
- Cero tiempos muertos.
- Cero defectos achacables a un mal estado de los equipos.
- Sin pérdidas de rendimiento o de capacidad productiva debidos al estos de los equipos.
TPM emergió como una necesidad de integrar el departamento de mantenimiento y el de operación o producción para mejorar la productividad y la disponibilidad. En una empresa en la que TPM se ha implantado toda la organización trabaja en el mantenimiento y en la mejora de los equipos. Se basa en cinco principios fundamentales:
- Participación de todo el personal. Incluir a todos y cada uno de ellos permite garantizar el éxito del objetivo.
- Creación de una cultura corporativa orientada a la obtención de la máxima eficacia en el sistema de producción y gestión de los equipos y maquinarias.
- Implantación de un sistema de gestión de las plantas productivas para facilitar la eliminación de las pérdidas antes de que se produzcan.
- Implantación del mantenimiento preventivo como medio básico para alcanzar el objetivo de cero pérdidas mediante actividades integradas en pequeños grupos de trabajo y apoyado en el soporte que proporciona el mantenimiento autónomo.
- Aplicación de los sistemas de gestión de todos los aspectos de la producción, incluyendo diseño y desarrollo, ventas y dirección.
Cursos recomendados






%252FImagen%252FRAMPREDYC-1730060420837.webp%3Falt%3Dmedia%26token%3D2634a7f0-988e-4022-b91f-382503e6e9db&w=3840&q=75)

Las seis grandes pérdidas
Desde la filosofía del TPM se considera que una máquina parada para efectuar un cambio, una máquina averiada, una máquina que no trabaja al 100% de su capacidad o que fabrica productos defectuosos produce pérdidas a la empresa. TPM identifica seis fuentes de pérdidas que reducen la efectividad por interferir con la producción:
- Fallos del equipo, que producen pérdidas de tiempo inesperadas.
- Puesta a punto y ajustes de las máquinas (o tiempos muertos) que producen pérdidas de tiempo al iniciar una nueva operación u otra etapa de ella. Por ejemplo, al inicio en la mañana, al cambiar de lugar de trabajo, al cambiar una matriz o matriz, o al hacer un ajuste.
- Marchas en vacío, esperas y detenciones menores (averías menores) durante la operación normal que producen pérdidas de tiempo, ya sea por problemas en la instrumentación, pequeñas obstrucciones, etc.
- Velocidad de operación reducida (el equipo no funciona a su capacidad máxima), que produce pérdidas productivas al no obtenerse la velocidad de diseño del proceso.
- Defectos en el proceso, que producen pérdidas productivas al tener que rehacer partes de él, reprocesar productos defectuosos o completar actividades no terminadas.
- Pérdidas de tiempo propias de la puesta en marcha de un proceso nuevo, marcha en vacío, periodo de prueba, etc.
El análisis cuidadoso de cada una de estas causas de baja productividad lleva a encontrar las soluciones para eliminarlas y los medios para implementar estas últimas. Es fundamental que el análisis sea hecho en conjunto por el personal de producción y el de mantenimiento, porque los problemas que causan la baja productividad son de ambos tipos y las soluciones deben ser adoptadas en forma integral para que tengan éxito.
Involucrar al operador en tareas de mantenimiento logra que éste comprenda mejor la máquina e instalaciones que opera, sus características y capacidades, su nivel de criticidad; ayuda al trabajo en grupo, y facilita compartir experiencias y aprendizajes mutuos; y con todo esto, se mejora la motivación del personal.
Existe una diferencia fundamental entre la filosofía del TPM y la del RCM: mientras que en la primera son las personas y la organización el centro del proceso, es en estos dos factores en los que está basado, en el RCM el mantenimiento se basa en el análisis de fallos, y en las medidas preventivas que se adoptarán para evitarlos, y no tanto en las personas.
¿Qué espacio ocupará el mantenimiento en la industria 4.0?
Estamos entrando a una nueva revolución tecnológica. ¿Qué papel tendrá el mantenimiento en innovaciones como la inteligencia artificial, la fabricación aditiva, la conectividad, la robótica autónoma o incluso la simulación y la realidad aumentada, el big data, el cloud computing, la ciberseguridad?
Los aspectos de la Industria 4.0 incluyen los siguientes elementos físicos:
La fabricación aditiva
Los makers. Gracias a la impresión 3D, en breve podremos fabricar nuestros propios componentes (al menos, eso se especula). Quizás en un futuro más lejano, incluso se podrán fabricar mecanismos enteros. Como sabemos, uno de los ocho pilares del TPM es el control previo. Hay que estudiar el estado original de la maquinaria y sus componentes para detectar y prever fallos futuros. Cuando estos equipos vienen con la firma de un fabricante, existe una garantía. ¿Qué ocurrirá si cualquiera puede “imprimirse” sus propias piezas? ¡O incluso sus propias máquinas!
Conectividad
Ya sabemos que en las fases de implantación del TPM es importante formar nuestro equipo humano e integrar a los operarios en las propias tareas de mantenimiento. La conectividad y la integración de sistemas (existen dos modalidades, vertical u horizontal) no nos queda tan lejos. Ante un escenario de integración física-digital habrá que redoblar esfuerzos en la formación de los operarios para que ejecuten tareas de mantenimiento físico y digital.
Robótica autónoma
En este campo la pregunta es: ¿Los robots autónomos también realizarán tareas de mantenimiento de forma autónoma? Y ante las dos posibles respuestas, se abren otras preguntas igual de millonarias. En el caso de un “sí”: ¿confiaremos plenamente en la capacidad de los robots industriales para auto-mantenerse?. En el caso que sea un “no”: ¿acabaremos siendo sus médicos y sus mecánicos? Puede que el futuro de los operarios sea la supervisión y el mantenimiento y poco más- ¿Nos asusta este futuro? ¿O es un alivio? Da que pensar…
La simulación y la realidad aumentada
Para finalizar… un poco más de ciencia-ficción. El campo de la simulación y la realidad aumentada se circunscribe (por ahora) a la proyección de prototipos, ensayos, pruebas teóricas, etc. Algunas (grandes) empresas ya cuentan con tecnología de simulación para facilitar la colaboración entre las plantas y procesos físicos y los digitales, entre la producción real y la virtual. En algunas otras, la simulación forma parte ya de la formación de los operarios. Y es una ayuda muy efectiva que agiliza la instrucción en el manejo de maquinaria de forma sorprendente.
Sin embargo, ¿podremos integrar no solo el funcionamiento de toda una planta sino también las tareas de mantenimiento en las simulaciones de rendimiento? La cantidad de factores a tener en cuenta es ingente. ¿Simularemos el comportamiento de las grasas, aerosoles y lubricantes? ¿Podremos incorporar factores externos, medioambientales, situaciones excepcionales, sucesos imprevistos o incluso fallos humanos?
De ser así, gracias a la Industria 4.0 el salto del mantenimiento industrial será gigantesco y el ahorro de costos, monumental. Bueno… por algo lo llaman revolución, ¿verdad?
Referencias
- https://www.lifeder.com/evolucion-mantenimiento-industrial
- https://www.valborsoluciones.com/mantenimiento/objetivo-mantenimiento-industrial/
- http://mantenimientopetroquimica.com/tpm.html
- https://mantenimiento.win/mantenimiento-productivo-total/
Autor: Irene González
Correo: irene.gonzalez@predictiva21.com
Dinos qué te ha parecido el artículo
Artículos recomendados
Confiabilidad: Descubre en qué consiste

¿Usted es un Baby Boomer, Generación X o Millenial?

Lubricación

La Gestión de Activos como Política

Publica tu artículo en la revista #1 de Mantenimiento Industrial
Publicar un artículo en la revista es gratis, no tiene costo.
Solo debes asegurarte que no sea un artículo comercial.
¿Qué esperas?
O envía tu artículo directo: articulos@predictiva21.com
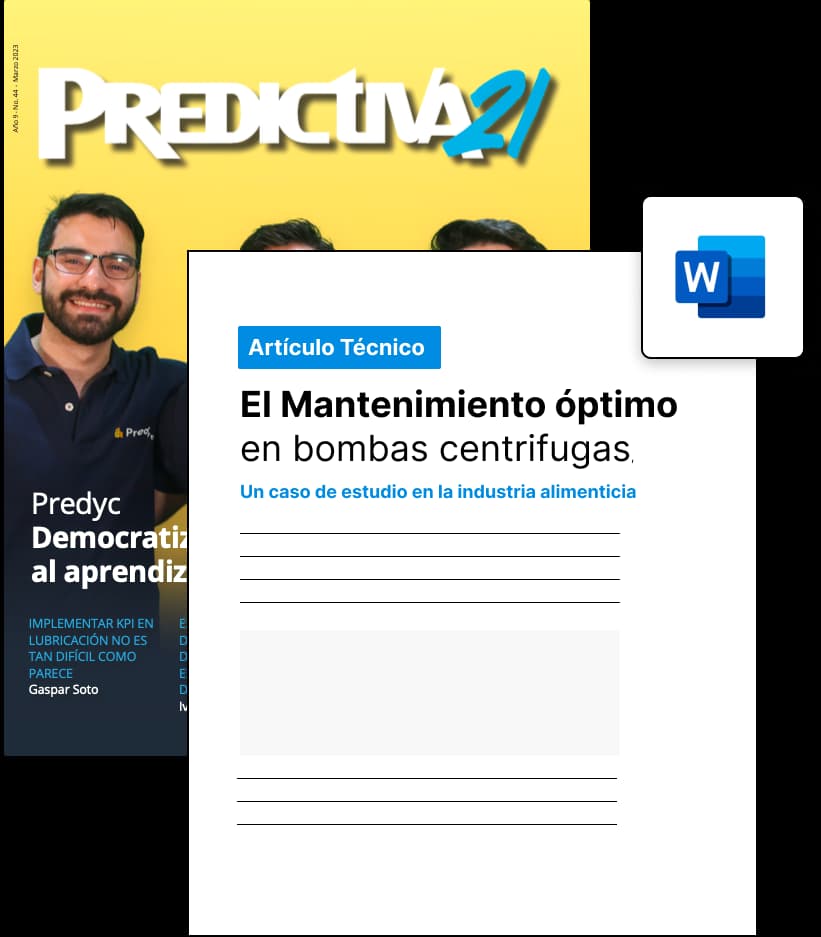
El mantenimiento y su evolución
Articulo 12 de agosto de 2020A principios del siglo XIX, luego de iniciada la Revolución Industrial, se comenzó a implementar el mantenimiento industrial toda vez que requería mejorar la producción de bienes y servicios- Con el tiempo, se fueron especializando los procesos y capacitando al personal hasta llegar a lo que conocemos hoy como uno de los mayores beneficios de la industria.
El mantenimiento industrial es aquel conjunto de medidas de carácter técnico organizativo, que pueden ser o no elaboradas previamente, que tiene como propósito sostener la funcionalidad de los equipos y garantizar un estado óptimo de las máquinas a través del tiempo.
El mantenimiento en el tiempo
- Desde el inicio de las máquinas, se hizo un mantenimiento correctivo total. En él se espera que se origine alguna avería para proceder a repararla. Los costos de mantenimiento resultaban altos por el largo tiempo de paro que se empleaba para solucionar el problema
- Durante la Primera Guerra Mundial se capacitó al personal de mantenimiento correctivo enviándolos a los laboratorios de prevención para evitar fallas. Dieron origen a los departamentos de mantenimiento preventivo.
- Con la Segunda Guerra Mundial se sistematizan los trabajos de mantenimiento preventivo.

- En 1946 es creada la Sociedad Americana de Control de Calidad.
- 1950. William Edward Deming Aplica en la industria japonesa el Control Estadístico de Calidad, donde el criterio de la empresa comienza con el proveedor y termina en el cliente. Se creó al mantenimiento productivo para obtener calidad y cantidad de producto, al tiempo de cuidar las máquinas.
- 1960. La necesidad de mantener naves en vuelo generó el mantenimiento enfocado en la confiabilidad.
- 1970. Se crea el Software Sistema Computarizado para la administración de Mantenimiento, CMMS, centrado en resolver la administración del área de mantenimiento.
- 1971. Seiichi Nakajima crea el Mantenimiento Productivo Total, involucrando a todo el personal de la empresa en le ejecución de todo tipo de mantenimiento, apoyado en los círculos de calidad.
- 1980. El Mantenimiento Centrado en la Confiabilidad fue modificado hacia la Optimización del Mantenimiento Planificado (PMO). Enfoque hacia la confiabilidad = RCM Enfoque hacia los costos = PMO.
- Desde 2005 se maneja la filosofía de la conservación (preservación y mantenimiento.
La gestión de mantenimiento
La gestión de mantenimiento garantiza la continuidad de la actividad operativa, evitando rupturas en el proceso como consecuencia de averías de máquinas y equipos. Un mantenimiento eficaz es uno de los elementos más importantes para el logro de la competitividad y operatividad empresarial en el actual marco de competencia global.
Describe la gestión exitosa y eficaz de los problemas de mantenimiento que participan en el mantenimiento, el funcionamiento y la productividad de una fábrica, instalación o planta de fabricación. Las principales áreas de enfoque de gestión de mantenimiento incluyen operaciones de producción, control ambiental y ecológico, control de inventario, control de calidad y opciones de outsourcing.
Realizar una correcta Gestión del Mantenimiento, es un claro indicador de beneficios para los resultados globales de las pequeñas, medianas y grandes compañías. El Mantenimiento industrial se tiene que valorar como una inversión, que genera beneficios y no como un gasto.
Los costos de Mantenimiento Industrial pueden llegar a alcanzar entre un 30 y 60 % de los costos operativos y es por ello que su actuación en la Industria tiene una incidencia notable sobre los resultados económicos de las compañías, haciendo necesario la correcta planificación y organización de su gestión.
Objetivos del mantenimiento
El objetivo general del mantenimiento es garantizar la producción necesaria en el momento justo, con el mínimo costo integral. El costo integral abarca además del mantenimiento de las máquinas, aspectos como el medio ambiente, el ahorro de energía, la seguridad y la calidad.
Los Objetivos concretos del mantenimiento pueden variar de acuerdo al tipo de industria. Estableciendo tareas de corto, mediano y largo plazo para lograr cumplir con todos de manera simultánea será llegar a la calidad total de mantenimiento.
Costos mínimos:
- Asegurar la máxima productividad de la nómina de mantenimiento.
- Reducir al mínimo el mantenimiento correctivo.
- Minimizar el stock inactivo en almacén.
- Extender la vida útil y productiva de las máquinas.
- Controlar el rendimiento energético de las máquinas.
- Evitar y controlar fugas de vapor, aire presurizado y demás formas de energía.
Máxima producción:
- Asegurar máxima disponibilidad de las máquinas.
- Reparar fallas en el menor tiempo posible con el menor costo.
Calidad:
- Eliminar desperfectos de las máquinas que afectan la calidad de los productos.
- Asegurar que los equipos que controlan la calidad de producto funcionen perfectamente.
Higiene y seguridad laboral:
- Mantener las protecciones de seguridad de los equipos.
- Capacitar al personal en la prevención de accidentes.
Conservación del medio ambiente:
- Controlar fugas y derrames de materiales peligrosos al momento de realizar trabajos.
- Evitar fugas de agua y desperdicios de energía eléctrica.
Mantenimiento Productivo Total
El TPM (Mantenimiento Productivo Total) surgió en Japón gracias a los esfuerzos del Japan Institute of Plant Maintenance (JIPM) como un sistema destinado a lograr la eliminación de las llamadas <seis grandes pérdidas> de los equipos, con el objetivo de facilitar la implantación de la forma de trabajo “Just in Time” o “justo a tiempo”. Es una filosofía de mantenimiento cuyo objetivo es eliminar las pérdidas en producción debidas al estado de los equipos, o en otras palabras, mantener los equipos en disposición para producir a su capacidad máxima productos de la calidad esperada, sin paradas no programadas. Esto supone:
- Cero averías.
- Cero tiempos muertos.
- Cero defectos achacables a un mal estado de los equipos.
- Sin pérdidas de rendimiento o de capacidad productiva debidos al estos de los equipos.
TPM emergió como una necesidad de integrar el departamento de mantenimiento y el de operación o producción para mejorar la productividad y la disponibilidad. En una empresa en la que TPM se ha implantado toda la organización trabaja en el mantenimiento y en la mejora de los equipos. Se basa en cinco principios fundamentales:
- Participación de todo el personal. Incluir a todos y cada uno de ellos permite garantizar el éxito del objetivo.
- Creación de una cultura corporativa orientada a la obtención de la máxima eficacia en el sistema de producción y gestión de los equipos y maquinarias.
- Implantación de un sistema de gestión de las plantas productivas para facilitar la eliminación de las pérdidas antes de que se produzcan.
- Implantación del mantenimiento preventivo como medio básico para alcanzar el objetivo de cero pérdidas mediante actividades integradas en pequeños grupos de trabajo y apoyado en el soporte que proporciona el mantenimiento autónomo.
- Aplicación de los sistemas de gestión de todos los aspectos de la producción, incluyendo diseño y desarrollo, ventas y dirección.
Cursos recomendados






%252FImagen%252FRAMPREDYC-1730060420837.webp%3Falt%3Dmedia%26token%3D2634a7f0-988e-4022-b91f-382503e6e9db&w=3840&q=75)

Las seis grandes pérdidas
Desde la filosofía del TPM se considera que una máquina parada para efectuar un cambio, una máquina averiada, una máquina que no trabaja al 100% de su capacidad o que fabrica productos defectuosos produce pérdidas a la empresa. TPM identifica seis fuentes de pérdidas que reducen la efectividad por interferir con la producción:
- Fallos del equipo, que producen pérdidas de tiempo inesperadas.
- Puesta a punto y ajustes de las máquinas (o tiempos muertos) que producen pérdidas de tiempo al iniciar una nueva operación u otra etapa de ella. Por ejemplo, al inicio en la mañana, al cambiar de lugar de trabajo, al cambiar una matriz o matriz, o al hacer un ajuste.
- Marchas en vacío, esperas y detenciones menores (averías menores) durante la operación normal que producen pérdidas de tiempo, ya sea por problemas en la instrumentación, pequeñas obstrucciones, etc.
- Velocidad de operación reducida (el equipo no funciona a su capacidad máxima), que produce pérdidas productivas al no obtenerse la velocidad de diseño del proceso.
- Defectos en el proceso, que producen pérdidas productivas al tener que rehacer partes de él, reprocesar productos defectuosos o completar actividades no terminadas.
- Pérdidas de tiempo propias de la puesta en marcha de un proceso nuevo, marcha en vacío, periodo de prueba, etc.
El análisis cuidadoso de cada una de estas causas de baja productividad lleva a encontrar las soluciones para eliminarlas y los medios para implementar estas últimas. Es fundamental que el análisis sea hecho en conjunto por el personal de producción y el de mantenimiento, porque los problemas que causan la baja productividad son de ambos tipos y las soluciones deben ser adoptadas en forma integral para que tengan éxito.
Involucrar al operador en tareas de mantenimiento logra que éste comprenda mejor la máquina e instalaciones que opera, sus características y capacidades, su nivel de criticidad; ayuda al trabajo en grupo, y facilita compartir experiencias y aprendizajes mutuos; y con todo esto, se mejora la motivación del personal.
Existe una diferencia fundamental entre la filosofía del TPM y la del RCM: mientras que en la primera son las personas y la organización el centro del proceso, es en estos dos factores en los que está basado, en el RCM el mantenimiento se basa en el análisis de fallos, y en las medidas preventivas que se adoptarán para evitarlos, y no tanto en las personas.
¿Qué espacio ocupará el mantenimiento en la industria 4.0?
Estamos entrando a una nueva revolución tecnológica. ¿Qué papel tendrá el mantenimiento en innovaciones como la inteligencia artificial, la fabricación aditiva, la conectividad, la robótica autónoma o incluso la simulación y la realidad aumentada, el big data, el cloud computing, la ciberseguridad?
Los aspectos de la Industria 4.0 incluyen los siguientes elementos físicos:
La fabricación aditiva
Los makers. Gracias a la impresión 3D, en breve podremos fabricar nuestros propios componentes (al menos, eso se especula). Quizás en un futuro más lejano, incluso se podrán fabricar mecanismos enteros. Como sabemos, uno de los ocho pilares del TPM es el control previo. Hay que estudiar el estado original de la maquinaria y sus componentes para detectar y prever fallos futuros. Cuando estos equipos vienen con la firma de un fabricante, existe una garantía. ¿Qué ocurrirá si cualquiera puede “imprimirse” sus propias piezas? ¡O incluso sus propias máquinas!
Conectividad
Ya sabemos que en las fases de implantación del TPM es importante formar nuestro equipo humano e integrar a los operarios en las propias tareas de mantenimiento. La conectividad y la integración de sistemas (existen dos modalidades, vertical u horizontal) no nos queda tan lejos. Ante un escenario de integración física-digital habrá que redoblar esfuerzos en la formación de los operarios para que ejecuten tareas de mantenimiento físico y digital.
Robótica autónoma
En este campo la pregunta es: ¿Los robots autónomos también realizarán tareas de mantenimiento de forma autónoma? Y ante las dos posibles respuestas, se abren otras preguntas igual de millonarias. En el caso de un “sí”: ¿confiaremos plenamente en la capacidad de los robots industriales para auto-mantenerse?. En el caso que sea un “no”: ¿acabaremos siendo sus médicos y sus mecánicos? Puede que el futuro de los operarios sea la supervisión y el mantenimiento y poco más- ¿Nos asusta este futuro? ¿O es un alivio? Da que pensar…
La simulación y la realidad aumentada
Para finalizar… un poco más de ciencia-ficción. El campo de la simulación y la realidad aumentada se circunscribe (por ahora) a la proyección de prototipos, ensayos, pruebas teóricas, etc. Algunas (grandes) empresas ya cuentan con tecnología de simulación para facilitar la colaboración entre las plantas y procesos físicos y los digitales, entre la producción real y la virtual. En algunas otras, la simulación forma parte ya de la formación de los operarios. Y es una ayuda muy efectiva que agiliza la instrucción en el manejo de maquinaria de forma sorprendente.
Sin embargo, ¿podremos integrar no solo el funcionamiento de toda una planta sino también las tareas de mantenimiento en las simulaciones de rendimiento? La cantidad de factores a tener en cuenta es ingente. ¿Simularemos el comportamiento de las grasas, aerosoles y lubricantes? ¿Podremos incorporar factores externos, medioambientales, situaciones excepcionales, sucesos imprevistos o incluso fallos humanos?
De ser así, gracias a la Industria 4.0 el salto del mantenimiento industrial será gigantesco y el ahorro de costos, monumental. Bueno… por algo lo llaman revolución, ¿verdad?
Referencias
- https://www.lifeder.com/evolucion-mantenimiento-industrial
- https://www.valborsoluciones.com/mantenimiento/objetivo-mantenimiento-industrial/
- http://mantenimientopetroquimica.com/tpm.html
- https://mantenimiento.win/mantenimiento-productivo-total/
Autor: Irene González
Correo: irene.gonzalez@predictiva21.com
Dinos qué te ha parecido el artículo
Artículos recomendados
Plant

Regulación de carga en motores de combustible pesado (Hfo), para determinar una operación eficiente con respecto al consumo específico de combustible.

Descubre las mejores prácticas de mantenimiento industrial

Entrevista a Fracttal

Publica tu artículo en la revista #1 de Mantenimiento Industrial
Publicar un artículo en la revista es gratis, no tiene costo.
Solo debes asegurarte que no sea un artículo comercial.
¿Qué esperas?
O envía tu artículo directo: articulos@predictiva21.com
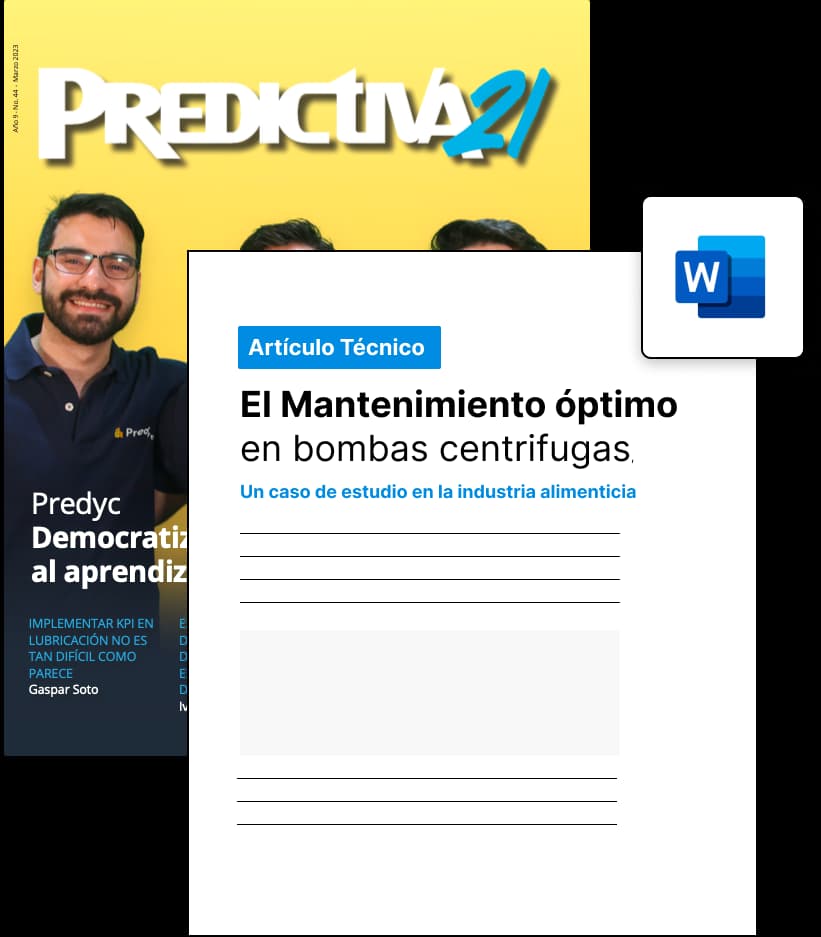