Evaluación de la Base de Datos de Mantenimiento
Articulo23 de marzo de 2020
El presente trabajo fue presentado durante el 6to Congreso Uruguayo de Mantenimiento, URUMAN 2010, teniendo como tema central la identificación del Mantenimiento Clase Mundial.
El trabajo inicia con dos interrogantes básicas:
- ¿Cuál es la META del Mantenimiento el día de hoy?
- ¿Cómo se puede identificar un “Mantenimiento Clase Mundial”?
La respuesta a la primera pregunta es: “La GENERACIÓN DE ROI (Retorno sobre la inversión)” y como respuesta a la segunda: “El que genera el ROI”:
Veamos algunos ejemplos:
De las dos fábricas de IMPSA en Argentina, la mayor unidad productiva se llama “Nave I” debido a sus características y dimensiones (225 metros de largo, 33 metros de ancho y 35 metros de altura). Incluye un moderno centro de mecánico fabricado por la Ingersoll Milling Machine Company, constituido por un torno vertical combinado con un pórtico móvil y una columna de torneado independiente, lo que permite la producción de piezas de turbinas y generadores de hasta 18 metros (59 pies) de diámetro, 6 metros (20 pies) de altura y 500 toneladas de peso.
En el sitio de UOL “Economía & Negocios” del 30 de agosto de 2010 se divulgó que “Industrias Argentinas Pescarmona - IMPSA” vendió generadores eólicos a empresas brasileñas por valor superior a USD 730.000.000,00.
Estos generadores son producidos justamente en el torno arriba indicado. Si consideramos que para fabricarlos se utilizará el torno por 6 meses con una carga mensual de 176 horas, el torno genera valor por USD 230.429,00 por hora. Esto significa que, si la confiabilidad de este torno no es 100%, o sea, que se detiene durante el proceso, la empresa tendría una pérdida directa de 3.840 dólares por minuto además de los gastos indirectos de pérdida de calidad, costo para reajustar la máquina, etc.
Otro ejemplo:
En el sur de Brasil una empresa de madera llamada Berneck, con poco más de 50 años (1952), logró resultados espectaculares de eficiencia en uno de sus procesos por la implementación, tres años atrás, del PCM (Planificación y Control de Mantenimiento). El resultado está siendo tan evidente que esta empresa, desde el inicio del 2010, está extendiendo las actividades del PCM en sus otras áreas de proceso.
Para lograr estos resultados el jefe del PCM, Felipe Hannemann, participó en cuatro cursos especializados en Gestión de Mantenimiento, empezando por aquél que trata de Bases de Datos e implementó todos los conceptos adquiridos con el auxilio de un equipo muy calificado, el apoyo de la jefatura general de mantenimiento y del gerente de la planta.
Recién el PCM está extendiendo sus actividades con la introducción de la Ingeniería de Mantenimiento que ya está formada, en este momento, con un ingeniero que empezó a contar con informes conseguidos a través de índices y consultas al historial para la generación de recomendaciones.
El trabajo desarrollado por el PCM incluye la organización de manuales, normas y procedimientos necesarios para operar y mantener toda la planta.
Para viabilizar la evaluación del Retorno Sobre la Inversión (ROI) por el mantenimiento es necesario que exista una efectiva gestión (toma de decisiones), hecha a partir de las recomendaciones del análisis de los informes (índices y consultas) adecuados a cada nivel, generados a partir de archivos consolidados, tratados por un eficiente Sistema que procese datos completos y confiables de todas las intervenciones controladas.
Si la información no es COMPLETA y CONFIABLE no se lograrán archivos consolidados que, en consecuencia, no irán a generar los informes para ser analizados y de esta forma la gestión quedará restringida a la experiencia de los gerentes en los tres niveles: estratégico, táctico y operacional.
Recomiendo que el análisis de los informes sea hecho a través de un órgano de asesoramiento, llamado “Ingeniería de Mantenimiento” que debe ser compuesto por personal con experiencia de planta, capacitación adecuada para interpretar los indicadores y espíritu pionero, o sea, buena intuición, coraje para enfrentar desafíos, persistencia y alineación a la misión y visión de la empresa. Además, el personal de este órgano también debe estar calificado para investigaciones de causa raíz de fallas, con el auxilio de la base de datos para obtener la información específica de lo que desea analizar.
La calificación de este personal también debe involucrar estudios económicos, de eficiencia de máquinas y de productividad humana, utilizando técnicas comprobadas y eficaces para estos tipos de evaluaciones. Sin embargo, todo el proceso de análisis debe ser complementado con tormentas de ideas, involucrando los niveles de supervisión de planta tanto de mantenimiento como operación, logística, calidad, seguridad y medio ambiente para, entonces, generar las recomendaciones que serían aplicadas gracias a su factibilidad por los gerentes, dando como resultado el ROI.
Como ya he indicado, para que la Ingeniería de Mantenimiento pueda desarrollar su trabajo de análisis es necesario que se cuente con una Base de Datos completa y confiable de todas las invenciones realizadas. Así, es recomendable que la empresa tenga un órgano que se encargue de este trabajo. Este órgano lo identifico como PCM - Planificación y Control de Mantenimiento que establece todos los estándares para garantizar uniformidad y consistencia de la información además de los procedimientos para las intervenciones programadas y no-programadas y, en conjunto con el área de TI, desarrolle (o adquiera y haga las adecuaciones necesarias) el Sistema para almacenar y tratar la información generada en campo.
Cuando sea posible, recomiendo que el PCM tenga un área de digitalización de OT’s para que no tengan que hacerlo los ejecutantes o supervisores además de garantizar la perfecta estandarización de la información, particularmente la relacionada con el código de ocurrencias.
Otra alternativa muy útil es la utilización de colectores de datos o palm-tops para generación y recolección de datos de las OT’s conforme se aplica en Berneck, la empresa que estoy utilizando en este trabajo como referencia. Para garantizar la confiabilidad de estos datos, es fundamental que se trabaje bajo conceptos universales y estandarizados, bien difundidos y reconocidos por todos los involucrados. Dentro de este enfoque, recomiendo utilizar los conceptos presentados en la sección “definiciones” del sitio www.copiman.org. En esta sección del sitio encontrarán la terminología universal de mantenimiento además de las indicaciones de subdivisión de la importancia operacional de los equipos (clase o criticidad) y de las prioridades.
Además, de lo ya indicado, los datos deben ser codificados utilizando tablas que irán a garantizar la estandarización de los registros.
Dentro de los códigos más utilizados se encuentra el que identifica la posición y función operacional del equipo (código de equipo también llamado “tag”) que comúnmente es formado por las tablas de “tipo de equipo” y “sistema operacional” que pueden estar asociados a la “localización física del equipo en la planta”, la propia “planta”, la “clase” y algún otro registro considerado importante para la empresa como, por ejemplo, las partes (o componentes) de los equipos.
Otro código muy utilizado es el que identifica un suceso formado por la “causa” que generó el suceso, el “efecto” que identifica como este suceso se expuso y la “acción” que identifica lo que se hizo para eliminar el suceso. Para que la tabla de “acción” no quede muy larga puede ser dividida en “acción - verbo” y “acción - complemento”.
Toda base de datos debe empezar por la identificación del ítem (equipo o activo) que llamo “catastro”, donde se debe colocar la mayor cantidad de información de forma que no solo sea útil para mantenimiento sino también para operación, ingeniería, patrimonio o cualquier otra área de la empresa que necesite hacer consultas de este tipo de información.
Normalmente en un catastro se puede identificar un conjunto de datos que se aplican a cualquier tipo de equipo, que llamo de “datos generales” o “datos administrativos” y otro que depende del tipo de equipo que llamo “datos específicos” o “datos técnicos”. Además, se puede distinguir los datos que son comunes para equipos iguales que llamo datos de “familia”, de los datos que pueden ser diferentes para equipos iguales. La asociación de los datos comunes a equipos iguales se hace a través de un “código de familia” que también sirve para asociar el sistema de mantenimiento con los sistemas de materiales y el archivo técnico.
Cuando se hace la asociación del “código de familia” con el archivo técnico se puede buscar los manuales, dibujos, fotos y videos directamente en el archivo técnico desde el cual estén digitalizados.
Dentro de los datos que son diferentes para equipos iguales, que llamo “datos exclusivos”, se encuentra el código de equipo, o código operacional, o “tag”, la fecha de inicio de operación y el costo de adquisición.
Al elaborar el catastro se debe buscar relacionar todos los repuestos específicos y no específicos con las familias de los equipos, particularmente los de “Clase A” (fundamentales al proceso) de tal forma que ayude a reducir pérdida de tiempo durante una intervención programada o no programada. En la empresa que estamos utilizando como ejemplo, todos los equipos (ítems o activos) están identificados a través de su “tag” y su número individual que se puede leer utilizando una palm, pues están identificados por un código “2D”. Cuando se empezó a codificar los equipos se aplicaron tarjetas con códigos de barras que lastimosamente no logró éxito, debido a que al ensuciarse o dañarse generaba dificultades de lectura. Los actuales códigos “2D” eliminaran este problema de daño.
La figura siguiente muestra una etiqueta colocada en un equipo con el código “2D” que identifica el mismo “tag” que aparece escrito en numeral. En este caso, por ser un equipo “Clase A” también aparecen en “2D” los códigos de los repuestos asociados a este equipo.

Entre más tablas se utilicen en un proceso de catastro menor es la posibilidad de error de digitalización. Además, se logran estándares de registro y rapidez en el registro y búsqueda de información (filtro) en el proceso de análisis de historial de equipo (o activo).
Una vez identificados los equipos se puede pasar a segunda etapa del proceso de formación de base de datos que es la “planificación”, donde se va responder los 4W y el H:
- “Why” = ¿por qué? = ¿por qué intervenir?
- “Where” = ¿en qué parte? = ¿en cuál equipo o parte (componente) intervenir?
- “What” = ¿qué? = ¿qué tipo de intervención?
- “Who” = ¿quién? = ¿quién va intervenir? (¿cuál órgano o sector?)
- “How” = Cómo = ¿cómo se hará el servicio? = ¿cuáles recomendaciones de seguridad y cuáles procedimientos?
Las recomendaciones de seguridad deben ser establecidas junto con el área de seguridad industrial y tienen como objetivo evitar que el mantenedor cometa actos inseguros o trabaje bajo condiciones inseguras, para de esta forma eliminar los accidentes. Deben ser escritas de forma objetiva, por conjunto de funcionalidades de equipos, en pocas líneas ya que deberá ser registrada en la OT, y de fácil entendimiento. Obviamente estarán contenidas en esas recomendaciones los equipos de protección individual necesarios a cada tipo de servicio.
Las instrucciones de mantenimiento son formadas por un conjunto de tareas adecuadas a cada tipo de intervención, por cada tipo de equipo y por cada sector (órgano responsable por el mantenimiento) y son escritas a partir de experiencia propia, recomendaciones de los fabricantes y, eventualmente alguna bibliografía o archivo digital especializado. Al establecer las tareas se debe estimar el tiempo necesario para ejecutarlas, llamado “tiempo patrón”, dato fundamental para el cálculo de backlog.
Algunas tareas de instrucción de mantenimiento pueden hacer referencia a registros de medición. Por lo tanto, se debe proyectar un archivo para las distintas mediciones hechas por tipo de equipo de forma que puedan servir para evaluar las pérdidas de características operacionales del equipo (degeneración) y, a través del análisis predictivo determinar el momento más adecuado para corrección de las variables que queden fuera de los límites de funcionamiento adecuados.
Al identificar ¿cuándo será realizado el servicio? (la 5a W = “When”) la planificación se convierte en “programación”, que puede ser establecida por unidad de tiempo “calendario” (día, semana o mes), o “no-calendario” (horas de funcionamiento, kilómetros recorridos, número de operaciones o número de piezas fabricadas).
Obviamente que no todas las actividades planificadas necesitan ser programadas. Se puede planificar una intervención y nunca ser realizada. Sin embargo, es muy importante tener las cosas planificadas para que en caso de ser necesaria una intervención evitar paros largos, compras de repuestos de última hora, pago de horas extras, daños al medio ambiente y riesgo a la seguridad humana.
Las programaciones de mantenimiento pueden generar tres tipos de Órdenes de Trabajo: OT de Ruta, para actividades de corto plazo y corta duración (diaria, semanal, quincenal, mensual, a cada 100 horas, a cada 200 horas y a cada 500 horas).
OT Sistemática (en vía de desaparición, pues deberá ser reemplazada por la OT basada en condición) para actividades de mediano plazo (trimestral, semestral, anual, a cada 1.000 horas; a cada 2.000 horas y a cada 5.000 horas) y OT de Grandes Paros (o de Oportunidad) para actividades de largo plazo y larga duración (cada dos o tres años, cada 20.000 horas o cada 50.000 horas).
Las programaciones deben contener plazos para que, una vez generada la OT estas sean ejecutadas. Algunos llaman a estos plazos (y lo miden a través de indicador propio) de “adherencia” a la programación. Yo llamo a esto plazo de conformidad. Son porcentuales sobre la programación para tolerancia o para suspensión de una OT. Normalmente los plazos de tolerancia están relacionados con la Clase del equipo y los plazos de suspensión están relacionados con la periodicidad de la intervención.
Por ejemplo, si un equipo es Clase A, la tolerancia para ejecución del mantenimiento debería ser igual a su propia “fecha” programada, o sea, si la programación es por unidad calendario semana y si el mantenimiento está previsto para la semana 15, la tolerancia sería la misma semana 15, lo que significa que si el servicio no se ejecuta en esta semana la OT ya está “no-conforme”. Sin embargo, si es un equipo Clase B se podría dar una tolerancia para la “fecha + 1” (o “fecha + 2”) que, en nuestro ejemplo significaría que el mantenimiento se podría realizar entre la semana 14 y 16. Si el equipo es Clase C se podría considerar como tolerancia la “fecha + 4” o sea, el servicio podría ser realizado entre la semana 11 y la semana 19.
En cuanto a una suspensión, seria aguardar, por ejemplo, 50% del periodo para que la OT sea cancelada. Y debe generar un informe para el Gerente, pues no se espera que esto ocurra. La suspensión de una OT debe ocurrir para periodos superiores a un mes y antes de cancelar, el área debe recibir un aviso con anticipación, de que esto va ocurrir.
Finalmente recomiendo que la planificación contenga todos los recursos humanos, de máquinas y herramientas, de lubricantes y de repuestos, que se presupuesta serán necesarios para realización del servicio. Esta previsión tiene dos objetivos: evitar interrupciones del trabajo (llamado “horas de espera” o “horas de demora”) y facilitar el establecimiento de los niveles de stock y de los plazos de compra o reposición de repuestos y lubricantes además que, si es necesario, facilitar la previsión de alquiler de máquinas o herramientas especiales para algunos servicios, así como la subcontratación de mano de obra.
La planificación y la programación irán permitiendo la generación de las OT’s que, a su vez, al ser ejecutadas alimentarán la base de datos con la información complementaria. A esta tercera etapa la llamo de “historial” o “recolección de datos”.
Para las actividades programadas (rutas y sistemáticas) normalmente la recolección de datos se resume en la indicación de que el servicio previsto se realizó conforme y, eventualmente, si se hizo algo que no estaba previsto.
Para las actividades no-programadas (reparación de defectos, predictiva y correctiva) se debe registrar la ocurrencia a través de sus tres elementos principales arriba indicados, o sea: la “causa”, el “efecto” y la “acción” (que puede ser compuesta por dos tablas: acción verbo y acción complemento).
Además, se debe recolectar los datos relacionados con la cantidad de horas/hombre utilizados, material utilizado y medidas hechas.
En la empresa en la cual estoy utilizando como ejemplo, todo esto se hace utilizando una palm-top, lo que brinda la facilidad de leer informaciones del equipo (y repuestos) con el código 2D.

Los resultados logrados por el PCM en Berneck han sido:
- Reducción en un 10% del tiempo de diligenciamiento en papel, lo que equivale, en el caso de lubricación, a bajar de TRES a UNO los lubricadores por el diligenciamiento para abrir y cerrar OT’s de Ruta.
- Reducción de impresión de más de 4.000 hojas de papel A4 por mes.
- Eliminación de extravíos de órdenes de trabajo, pues estas no son impresas.
- Por serie en forma de check-list estas OT’s tardarían mucho más tiempo para ser bajadas. Más de 1600 horas por mes para apunte/cierre manual del servicio realizado (esto representaría diez personas de más para este trabajo que hoy es hecho con tres personas).
- Identificación del equipo con código 2D, eliminando la digitación del TAG en la hoja de la inspección, lubricación o mantenimiento.
- Para equipos criticidad “A”, la identificación de los repuestos está en el mismo equipo bajo forma de placa con código 2D.
En Berneck el PCM logró mucho éxito en su trabajo frente al proceso de MDF (paneles de fibra de mediana densidad). En consecuencia, la empresa determinó que se ampliase su acción al área de MDP (paneles de partículas de mediana densidad) a partir de enero de 2010. El resultado, como se muestra en la tabla y gráfica siguiente, es que en 9 meses Felipe y su equipo ya lograron un aumento de disponibilidad superior a 5% lo que significa una ganancia superior a USD 1.500.000,00.

Una forma de evaluar cómo está la Base de Datos en una empresa es hacer la consulta a los Supervisores de Operación y Mantenimiento a través de una encuesta donde se solicita a cada uno que califique de 0 al 100% cómo ve la aplicación y la utilización de cada uno de los datos existentes.
Durante el 6º Congreso Uruguayo de Mantenimiento se entregó a cada participante una encuesta con 40 tipos de registros que componen una Base de Datos.
Aunque la encuesta no fue respondida por todos los participantes del evento, se procesó aquella la información utilizando la técnica de evaluación del Radar y Espiral mostrando un resultado muy parecido con las evaluaciones que hemos obtenido en algunas empresas.


Autor: Lourival Augusto Tavares
Consultor en Ingeniería de Mantenimiento
Congreso Uruguayo de Mantenimiento - URUMAN - 12 al 14 oct. 2010
Dinos qué te ha parecido el artículo
Artículos recomendados
Importancia del mantenimiento

Cursos de mantenimiento preventivo y correctivo

Condition Monitoring & Matters of the Heart: Listen to doctor Bob and make like Larry

¿Es el Mantenimiento Centrado en Confiabilidad una tarea fácil?

Publica tu artículo en la revista #1 de Mantenimiento Industrial
Publicar un artículo en la revista es gratis, no tiene costo.
Solo debes asegurarte que no sea un artículo comercial.
¿Qué esperas?
O envía tu artículo directo: articulos@predictiva21.com
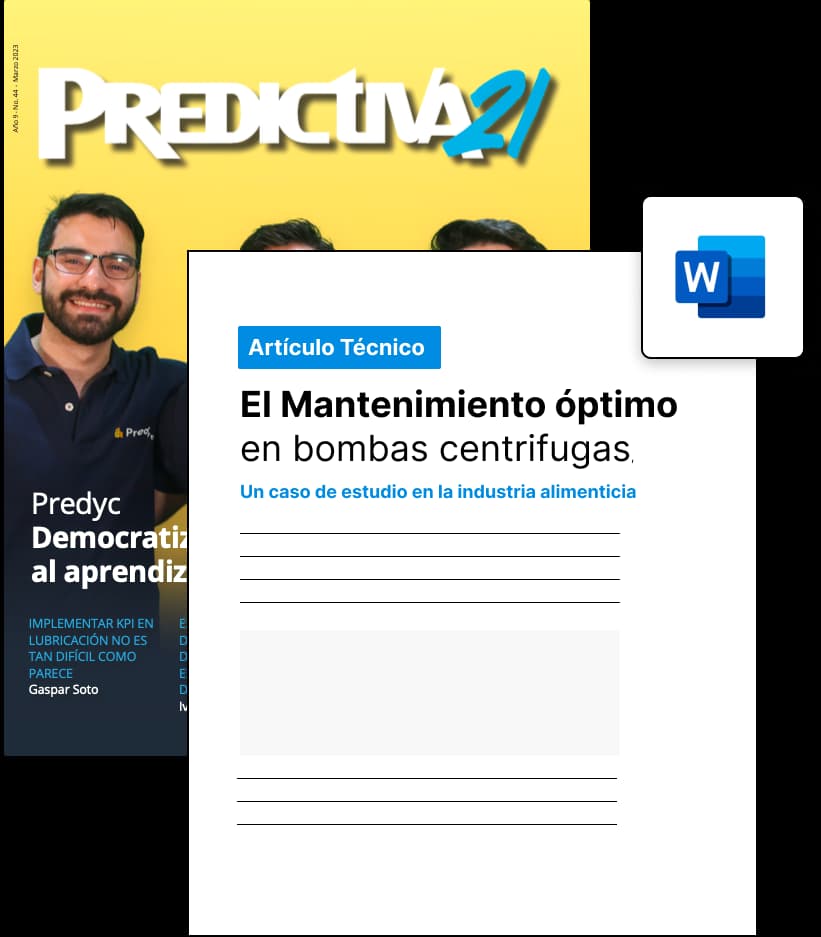
Evaluación de la Base de Datos de Mantenimiento
Articulo 23 de marzo de 2020El presente trabajo fue presentado durante el 6to Congreso Uruguayo de Mantenimiento, URUMAN 2010, teniendo como tema central la identificación del Mantenimiento Clase Mundial.
El trabajo inicia con dos interrogantes básicas:
- ¿Cuál es la META del Mantenimiento el día de hoy?
- ¿Cómo se puede identificar un “Mantenimiento Clase Mundial”?
La respuesta a la primera pregunta es: “La GENERACIÓN DE ROI (Retorno sobre la inversión)” y como respuesta a la segunda: “El que genera el ROI”:
Veamos algunos ejemplos:
De las dos fábricas de IMPSA en Argentina, la mayor unidad productiva se llama “Nave I” debido a sus características y dimensiones (225 metros de largo, 33 metros de ancho y 35 metros de altura). Incluye un moderno centro de mecánico fabricado por la Ingersoll Milling Machine Company, constituido por un torno vertical combinado con un pórtico móvil y una columna de torneado independiente, lo que permite la producción de piezas de turbinas y generadores de hasta 18 metros (59 pies) de diámetro, 6 metros (20 pies) de altura y 500 toneladas de peso.
En el sitio de UOL “Economía & Negocios” del 30 de agosto de 2010 se divulgó que “Industrias Argentinas Pescarmona - IMPSA” vendió generadores eólicos a empresas brasileñas por valor superior a USD 730.000.000,00.
Estos generadores son producidos justamente en el torno arriba indicado. Si consideramos que para fabricarlos se utilizará el torno por 6 meses con una carga mensual de 176 horas, el torno genera valor por USD 230.429,00 por hora. Esto significa que, si la confiabilidad de este torno no es 100%, o sea, que se detiene durante el proceso, la empresa tendría una pérdida directa de 3.840 dólares por minuto además de los gastos indirectos de pérdida de calidad, costo para reajustar la máquina, etc.
Otro ejemplo:
En el sur de Brasil una empresa de madera llamada Berneck, con poco más de 50 años (1952), logró resultados espectaculares de eficiencia en uno de sus procesos por la implementación, tres años atrás, del PCM (Planificación y Control de Mantenimiento). El resultado está siendo tan evidente que esta empresa, desde el inicio del 2010, está extendiendo las actividades del PCM en sus otras áreas de proceso.
Para lograr estos resultados el jefe del PCM, Felipe Hannemann, participó en cuatro cursos especializados en Gestión de Mantenimiento, empezando por aquél que trata de Bases de Datos e implementó todos los conceptos adquiridos con el auxilio de un equipo muy calificado, el apoyo de la jefatura general de mantenimiento y del gerente de la planta.
Recién el PCM está extendiendo sus actividades con la introducción de la Ingeniería de Mantenimiento que ya está formada, en este momento, con un ingeniero que empezó a contar con informes conseguidos a través de índices y consultas al historial para la generación de recomendaciones.
El trabajo desarrollado por el PCM incluye la organización de manuales, normas y procedimientos necesarios para operar y mantener toda la planta.
Para viabilizar la evaluación del Retorno Sobre la Inversión (ROI) por el mantenimiento es necesario que exista una efectiva gestión (toma de decisiones), hecha a partir de las recomendaciones del análisis de los informes (índices y consultas) adecuados a cada nivel, generados a partir de archivos consolidados, tratados por un eficiente Sistema que procese datos completos y confiables de todas las intervenciones controladas.
Si la información no es COMPLETA y CONFIABLE no se lograrán archivos consolidados que, en consecuencia, no irán a generar los informes para ser analizados y de esta forma la gestión quedará restringida a la experiencia de los gerentes en los tres niveles: estratégico, táctico y operacional.
Recomiendo que el análisis de los informes sea hecho a través de un órgano de asesoramiento, llamado “Ingeniería de Mantenimiento” que debe ser compuesto por personal con experiencia de planta, capacitación adecuada para interpretar los indicadores y espíritu pionero, o sea, buena intuición, coraje para enfrentar desafíos, persistencia y alineación a la misión y visión de la empresa. Además, el personal de este órgano también debe estar calificado para investigaciones de causa raíz de fallas, con el auxilio de la base de datos para obtener la información específica de lo que desea analizar.
La calificación de este personal también debe involucrar estudios económicos, de eficiencia de máquinas y de productividad humana, utilizando técnicas comprobadas y eficaces para estos tipos de evaluaciones. Sin embargo, todo el proceso de análisis debe ser complementado con tormentas de ideas, involucrando los niveles de supervisión de planta tanto de mantenimiento como operación, logística, calidad, seguridad y medio ambiente para, entonces, generar las recomendaciones que serían aplicadas gracias a su factibilidad por los gerentes, dando como resultado el ROI.
Como ya he indicado, para que la Ingeniería de Mantenimiento pueda desarrollar su trabajo de análisis es necesario que se cuente con una Base de Datos completa y confiable de todas las invenciones realizadas. Así, es recomendable que la empresa tenga un órgano que se encargue de este trabajo. Este órgano lo identifico como PCM - Planificación y Control de Mantenimiento que establece todos los estándares para garantizar uniformidad y consistencia de la información además de los procedimientos para las intervenciones programadas y no-programadas y, en conjunto con el área de TI, desarrolle (o adquiera y haga las adecuaciones necesarias) el Sistema para almacenar y tratar la información generada en campo.
Cuando sea posible, recomiendo que el PCM tenga un área de digitalización de OT’s para que no tengan que hacerlo los ejecutantes o supervisores además de garantizar la perfecta estandarización de la información, particularmente la relacionada con el código de ocurrencias.
Otra alternativa muy útil es la utilización de colectores de datos o palm-tops para generación y recolección de datos de las OT’s conforme se aplica en Berneck, la empresa que estoy utilizando en este trabajo como referencia. Para garantizar la confiabilidad de estos datos, es fundamental que se trabaje bajo conceptos universales y estandarizados, bien difundidos y reconocidos por todos los involucrados. Dentro de este enfoque, recomiendo utilizar los conceptos presentados en la sección “definiciones” del sitio www.copiman.org. En esta sección del sitio encontrarán la terminología universal de mantenimiento además de las indicaciones de subdivisión de la importancia operacional de los equipos (clase o criticidad) y de las prioridades.
Además, de lo ya indicado, los datos deben ser codificados utilizando tablas que irán a garantizar la estandarización de los registros.
Dentro de los códigos más utilizados se encuentra el que identifica la posición y función operacional del equipo (código de equipo también llamado “tag”) que comúnmente es formado por las tablas de “tipo de equipo” y “sistema operacional” que pueden estar asociados a la “localización física del equipo en la planta”, la propia “planta”, la “clase” y algún otro registro considerado importante para la empresa como, por ejemplo, las partes (o componentes) de los equipos.
Otro código muy utilizado es el que identifica un suceso formado por la “causa” que generó el suceso, el “efecto” que identifica como este suceso se expuso y la “acción” que identifica lo que se hizo para eliminar el suceso. Para que la tabla de “acción” no quede muy larga puede ser dividida en “acción - verbo” y “acción - complemento”.
Toda base de datos debe empezar por la identificación del ítem (equipo o activo) que llamo “catastro”, donde se debe colocar la mayor cantidad de información de forma que no solo sea útil para mantenimiento sino también para operación, ingeniería, patrimonio o cualquier otra área de la empresa que necesite hacer consultas de este tipo de información.
Normalmente en un catastro se puede identificar un conjunto de datos que se aplican a cualquier tipo de equipo, que llamo de “datos generales” o “datos administrativos” y otro que depende del tipo de equipo que llamo “datos específicos” o “datos técnicos”. Además, se puede distinguir los datos que son comunes para equipos iguales que llamo datos de “familia”, de los datos que pueden ser diferentes para equipos iguales. La asociación de los datos comunes a equipos iguales se hace a través de un “código de familia” que también sirve para asociar el sistema de mantenimiento con los sistemas de materiales y el archivo técnico.
Cuando se hace la asociación del “código de familia” con el archivo técnico se puede buscar los manuales, dibujos, fotos y videos directamente en el archivo técnico desde el cual estén digitalizados.
Dentro de los datos que son diferentes para equipos iguales, que llamo “datos exclusivos”, se encuentra el código de equipo, o código operacional, o “tag”, la fecha de inicio de operación y el costo de adquisición.
Al elaborar el catastro se debe buscar relacionar todos los repuestos específicos y no específicos con las familias de los equipos, particularmente los de “Clase A” (fundamentales al proceso) de tal forma que ayude a reducir pérdida de tiempo durante una intervención programada o no programada. En la empresa que estamos utilizando como ejemplo, todos los equipos (ítems o activos) están identificados a través de su “tag” y su número individual que se puede leer utilizando una palm, pues están identificados por un código “2D”. Cuando se empezó a codificar los equipos se aplicaron tarjetas con códigos de barras que lastimosamente no logró éxito, debido a que al ensuciarse o dañarse generaba dificultades de lectura. Los actuales códigos “2D” eliminaran este problema de daño.
La figura siguiente muestra una etiqueta colocada en un equipo con el código “2D” que identifica el mismo “tag” que aparece escrito en numeral. En este caso, por ser un equipo “Clase A” también aparecen en “2D” los códigos de los repuestos asociados a este equipo.

Entre más tablas se utilicen en un proceso de catastro menor es la posibilidad de error de digitalización. Además, se logran estándares de registro y rapidez en el registro y búsqueda de información (filtro) en el proceso de análisis de historial de equipo (o activo).
Una vez identificados los equipos se puede pasar a segunda etapa del proceso de formación de base de datos que es la “planificación”, donde se va responder los 4W y el H:
- “Why” = ¿por qué? = ¿por qué intervenir?
- “Where” = ¿en qué parte? = ¿en cuál equipo o parte (componente) intervenir?
- “What” = ¿qué? = ¿qué tipo de intervención?
- “Who” = ¿quién? = ¿quién va intervenir? (¿cuál órgano o sector?)
- “How” = Cómo = ¿cómo se hará el servicio? = ¿cuáles recomendaciones de seguridad y cuáles procedimientos?
Las recomendaciones de seguridad deben ser establecidas junto con el área de seguridad industrial y tienen como objetivo evitar que el mantenedor cometa actos inseguros o trabaje bajo condiciones inseguras, para de esta forma eliminar los accidentes. Deben ser escritas de forma objetiva, por conjunto de funcionalidades de equipos, en pocas líneas ya que deberá ser registrada en la OT, y de fácil entendimiento. Obviamente estarán contenidas en esas recomendaciones los equipos de protección individual necesarios a cada tipo de servicio.
Las instrucciones de mantenimiento son formadas por un conjunto de tareas adecuadas a cada tipo de intervención, por cada tipo de equipo y por cada sector (órgano responsable por el mantenimiento) y son escritas a partir de experiencia propia, recomendaciones de los fabricantes y, eventualmente alguna bibliografía o archivo digital especializado. Al establecer las tareas se debe estimar el tiempo necesario para ejecutarlas, llamado “tiempo patrón”, dato fundamental para el cálculo de backlog.
Algunas tareas de instrucción de mantenimiento pueden hacer referencia a registros de medición. Por lo tanto, se debe proyectar un archivo para las distintas mediciones hechas por tipo de equipo de forma que puedan servir para evaluar las pérdidas de características operacionales del equipo (degeneración) y, a través del análisis predictivo determinar el momento más adecuado para corrección de las variables que queden fuera de los límites de funcionamiento adecuados.
Al identificar ¿cuándo será realizado el servicio? (la 5a W = “When”) la planificación se convierte en “programación”, que puede ser establecida por unidad de tiempo “calendario” (día, semana o mes), o “no-calendario” (horas de funcionamiento, kilómetros recorridos, número de operaciones o número de piezas fabricadas).
Obviamente que no todas las actividades planificadas necesitan ser programadas. Se puede planificar una intervención y nunca ser realizada. Sin embargo, es muy importante tener las cosas planificadas para que en caso de ser necesaria una intervención evitar paros largos, compras de repuestos de última hora, pago de horas extras, daños al medio ambiente y riesgo a la seguridad humana.
Las programaciones de mantenimiento pueden generar tres tipos de Órdenes de Trabajo: OT de Ruta, para actividades de corto plazo y corta duración (diaria, semanal, quincenal, mensual, a cada 100 horas, a cada 200 horas y a cada 500 horas).
OT Sistemática (en vía de desaparición, pues deberá ser reemplazada por la OT basada en condición) para actividades de mediano plazo (trimestral, semestral, anual, a cada 1.000 horas; a cada 2.000 horas y a cada 5.000 horas) y OT de Grandes Paros (o de Oportunidad) para actividades de largo plazo y larga duración (cada dos o tres años, cada 20.000 horas o cada 50.000 horas).
Las programaciones deben contener plazos para que, una vez generada la OT estas sean ejecutadas. Algunos llaman a estos plazos (y lo miden a través de indicador propio) de “adherencia” a la programación. Yo llamo a esto plazo de conformidad. Son porcentuales sobre la programación para tolerancia o para suspensión de una OT. Normalmente los plazos de tolerancia están relacionados con la Clase del equipo y los plazos de suspensión están relacionados con la periodicidad de la intervención.
Por ejemplo, si un equipo es Clase A, la tolerancia para ejecución del mantenimiento debería ser igual a su propia “fecha” programada, o sea, si la programación es por unidad calendario semana y si el mantenimiento está previsto para la semana 15, la tolerancia sería la misma semana 15, lo que significa que si el servicio no se ejecuta en esta semana la OT ya está “no-conforme”. Sin embargo, si es un equipo Clase B se podría dar una tolerancia para la “fecha + 1” (o “fecha + 2”) que, en nuestro ejemplo significaría que el mantenimiento se podría realizar entre la semana 14 y 16. Si el equipo es Clase C se podría considerar como tolerancia la “fecha + 4” o sea, el servicio podría ser realizado entre la semana 11 y la semana 19.
En cuanto a una suspensión, seria aguardar, por ejemplo, 50% del periodo para que la OT sea cancelada. Y debe generar un informe para el Gerente, pues no se espera que esto ocurra. La suspensión de una OT debe ocurrir para periodos superiores a un mes y antes de cancelar, el área debe recibir un aviso con anticipación, de que esto va ocurrir.
Finalmente recomiendo que la planificación contenga todos los recursos humanos, de máquinas y herramientas, de lubricantes y de repuestos, que se presupuesta serán necesarios para realización del servicio. Esta previsión tiene dos objetivos: evitar interrupciones del trabajo (llamado “horas de espera” o “horas de demora”) y facilitar el establecimiento de los niveles de stock y de los plazos de compra o reposición de repuestos y lubricantes además que, si es necesario, facilitar la previsión de alquiler de máquinas o herramientas especiales para algunos servicios, así como la subcontratación de mano de obra.
La planificación y la programación irán permitiendo la generación de las OT’s que, a su vez, al ser ejecutadas alimentarán la base de datos con la información complementaria. A esta tercera etapa la llamo de “historial” o “recolección de datos”.
Para las actividades programadas (rutas y sistemáticas) normalmente la recolección de datos se resume en la indicación de que el servicio previsto se realizó conforme y, eventualmente, si se hizo algo que no estaba previsto.
Para las actividades no-programadas (reparación de defectos, predictiva y correctiva) se debe registrar la ocurrencia a través de sus tres elementos principales arriba indicados, o sea: la “causa”, el “efecto” y la “acción” (que puede ser compuesta por dos tablas: acción verbo y acción complemento).
Además, se debe recolectar los datos relacionados con la cantidad de horas/hombre utilizados, material utilizado y medidas hechas.
En la empresa en la cual estoy utilizando como ejemplo, todo esto se hace utilizando una palm-top, lo que brinda la facilidad de leer informaciones del equipo (y repuestos) con el código 2D.

Los resultados logrados por el PCM en Berneck han sido:
- Reducción en un 10% del tiempo de diligenciamiento en papel, lo que equivale, en el caso de lubricación, a bajar de TRES a UNO los lubricadores por el diligenciamiento para abrir y cerrar OT’s de Ruta.
- Reducción de impresión de más de 4.000 hojas de papel A4 por mes.
- Eliminación de extravíos de órdenes de trabajo, pues estas no son impresas.
- Por serie en forma de check-list estas OT’s tardarían mucho más tiempo para ser bajadas. Más de 1600 horas por mes para apunte/cierre manual del servicio realizado (esto representaría diez personas de más para este trabajo que hoy es hecho con tres personas).
- Identificación del equipo con código 2D, eliminando la digitación del TAG en la hoja de la inspección, lubricación o mantenimiento.
- Para equipos criticidad “A”, la identificación de los repuestos está en el mismo equipo bajo forma de placa con código 2D.
En Berneck el PCM logró mucho éxito en su trabajo frente al proceso de MDF (paneles de fibra de mediana densidad). En consecuencia, la empresa determinó que se ampliase su acción al área de MDP (paneles de partículas de mediana densidad) a partir de enero de 2010. El resultado, como se muestra en la tabla y gráfica siguiente, es que en 9 meses Felipe y su equipo ya lograron un aumento de disponibilidad superior a 5% lo que significa una ganancia superior a USD 1.500.000,00.

Una forma de evaluar cómo está la Base de Datos en una empresa es hacer la consulta a los Supervisores de Operación y Mantenimiento a través de una encuesta donde se solicita a cada uno que califique de 0 al 100% cómo ve la aplicación y la utilización de cada uno de los datos existentes.
Durante el 6º Congreso Uruguayo de Mantenimiento se entregó a cada participante una encuesta con 40 tipos de registros que componen una Base de Datos.
Aunque la encuesta no fue respondida por todos los participantes del evento, se procesó aquella la información utilizando la técnica de evaluación del Radar y Espiral mostrando un resultado muy parecido con las evaluaciones que hemos obtenido en algunas empresas.


Autor: Lourival Augusto Tavares
Consultor en Ingeniería de Mantenimiento
Congreso Uruguayo de Mantenimiento - URUMAN - 12 al 14 oct. 2010
Dinos qué te ha parecido el artículo
Artículos recomendados
8.3 Filosofía del TPM

Aplicaciones mecánicas de la Termografía

Advantages & disdvantages using active magnetic bearings vs gas/air barings vs lube oil bearings in turbomachinery

Fracttal cierra inversión de US$ 5.3 millones para transformar el mantenimiento del futuro

Publica tu artículo en la revista #1 de Mantenimiento Industrial
Publicar un artículo en la revista es gratis, no tiene costo.
Solo debes asegurarte que no sea un artículo comercial.
¿Qué esperas?
O envía tu artículo directo: articulos@predictiva21.com
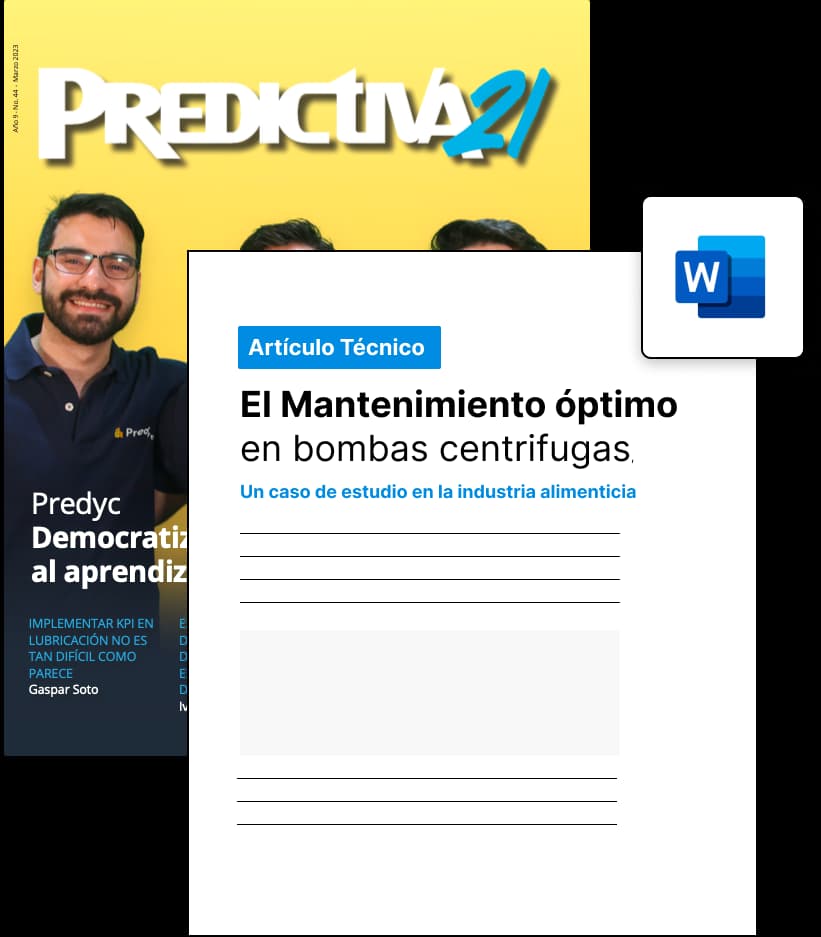