Si usted no construye su filosofía de mantenimiento, ninguna estrategia que utilice le servirá completamente
Articulo15 de agosto de 2019
La gente que está involucrada en el Mantenimiento reconoce que esta es la función más dinámica que hay en una planta, debido a que tenemos una gran cantidad de equipos por mantener, y cada uno de ellos tiene una enorme variedad de protocolos de mantenimiento. Adicionalmente a ello, requerimos de una gran cantidad de partes, materiales y repuestos para ejecutar el mantenimiento, diversidad de mano de obra; así mismo, debemos monitorear condiciones con precisión para aquellos activos críticos, controlar el Backlog.
Igualmente tenemos que planificar, programar ejecutar y registrar en los históricos que tengamos, ya sean en un software o simplemente en archivos manuales de mantenimiento. Indudablemente son demasiadas actividades que de no llevarlas correctamente, el mantenimiento dejaría de cumplir sus cometidos principales: lograr que los equipos operen la mayor cantidad de tiempo posible correctamente, menos paradas, rápidos tiempos para reparar, mayor seguridad y costos mínimos. Igualmente a todo esto se le suma, que los productos son diferentes, ubicaciones de las plantas en condiciones agresivas y un ingrediente muy importante: La Cultura de la Gente. Quizás podríamos encontrar muchas más razones que refuerzan lo que he dicho al principio de este artículo, pero pienso que son las principales.
Mi larga trayectoria por más de treinta años en el medio industrial como ingeniero de planta, gerente, consultor, investigador y profesor me ha reafirmado que “si usted no construye su propia filosofía de trabajo de mantenimiento, ninguna estrategia le servirá o simplemente no le sacará su máximo provecho”. Ahora bien, a qué me refiero con esto; la respuesta es que al igual que las personas, no hay dos iguales. Con ello quiero decir que no hay dos plantas iguales, aunque sean idénticas, y la razón radica en las personas. Quizás muchos no hayan oído hablar del psicólogo estadounidense Abraham Maslow, pero a los que sí han escuchado o leído sobre él, recordarán que fue quien desarrolló la famosa teoría de la Pirámide de Maslow y sus Jerarquía de necesidades.

Sumado a esto, tenemos la teoría de los factores Higiénicos y Motivacionales de Frederick Herzberg, que están relacionado con la satisfacción e insatisfacción. Los factores Motivacionales son los que producen satisfacción: logros, reconocimiento, independencia laboral, responsabilidad y promoción. Los factores Higiénicos son los que producen la insatisfacción: Sueldo y beneficios empresariales, política de la empresa y su organización, relaciones con los compañeros de trabajo, ambiente físico, supervisión, estatus, seguridad laboral, crecimiento, madurez, consolidación.
Muy bien, a lo mejor preguntarán, ¿Y qué tiene que ver todo esto con el mantenimiento? Pues les digo que mucho, debido a que un mantenimiento de calidad producto de su propia filosofía de trabajo está íntimamente relacionado con las personas a todos los niveles jerárquicos, desde la alta gerencia hasta el último técnico u obrero de la planta.
Ahora bien, uno de los artículos que desarrollé en esta revista, tenía que ver con La Actitud y La Aptitud de las personas hacia el mantenimiento y explicaba en su momento que había cuatro maneras de estar en el mantenimiento y era que:
- A la gente no le interesa el mantenimiento.
- La gente no sabe hacer mantenimiento.
- La gente no puede hacer mantenimiento.
- La gente no quiere hacer mantenimiento.
En ese artículo indicaba que pasaba cuando las personas se encontraban en cada uno de esos escenarios y qué debíamos hacer para dar respuesta con una salida razonable. Ustedes se preguntarán nuevamente qué tiene que ver esto con el mantenimiento; y nuevamente les digo que mucho, porque el mantenimiento gira en torno a la Actitud y Aptitudes de las personas. Imagínense todo ese cúmulo de actividades de las cuales comentamos al inicio de este artículo sino las hacemos con mucha “Disciplina, Constancia, Mística, Responsabilidad, Control y Seguimiento”; y que son el resultado de cuán bien estemos ubicados o estrechamente relacionados con la teoría de los factores y la Jerarquía de Necesidades comentadas anteriormente. Indudablemente de no profundizar en esto, estamos en el camino correcto al fracaso. “Recuerde no hay nada más peligroso para el mantenimiento que una persona confusa, desubicada, desorientada, distraída como resultado de uno o varios problemas: psíquicos, emocionales o físicos”.
Cuando me refiero a construir su filosofía de trabajo, me refiero hasta dónde quiere llegar con su mantenimiento, qué es lo que realmente le interesa y qué quiere alcanza. Tiene que ver con la planificación estratégica: dónde estamos hoy, dónde queremos estar en el futuro y el medio para hacerlo. Ese medio es su “Filosofía de Mantenimiento” para lograr lo que quiere. Es el vector que debe utilizar para llegar a su posición deseada con el mantenimiento. Es hacerse un traje a su medida.
En este sentido, cómo podemos utilizar una estrategia de: actividades predictivas, SMED, POKA YOKE, TPM, mantenimiento centrado en confiabilidad, o encaminarse a una implantación de la norma ISO 55000, etc. Si estamos o somos débiles con la condición de nuestra gente. Sé que algunas de estas estrategias de trabajos contemplan el Factor Humano, pero indudablemente tenemos que revisar en profundidad y no verlo como una simple condición para implantar cualquier estrategia de mantenimiento. Pienso que va mucho más allá, significa entender sin ningún tipo de duda que nuestro principal recurso es la gente, porque los equipos son inanimados, les damos vida cuando los operamos y mantenemos; y sin nuestra primera energía que es la gente no sería posible esta cruzada de “Construir una Filosofía de Trabajo de Mantenimiento Exitosa”.
Autor: Brau Clemenza
Consultor, Investigador, Articulista
Dinos qué te ha parecido el artículo
Artículos recomendados
Aplicación Práctica del Teorema de Bayes para la Estimación de la Disponibilidad en Activos Industriales

Entrevista Luis Felipe Sexto

Termografía

Efecto del Síndrome de Bornout en Confiabilidad Humana

Publica tu artículo en la revista #1 de Mantenimiento Industrial
Publicar un artículo en la revista es gratis, no tiene costo.
Solo debes asegurarte que no sea un artículo comercial.
¿Qué esperas?
O envía tu artículo directo: articulos@predictiva21.com
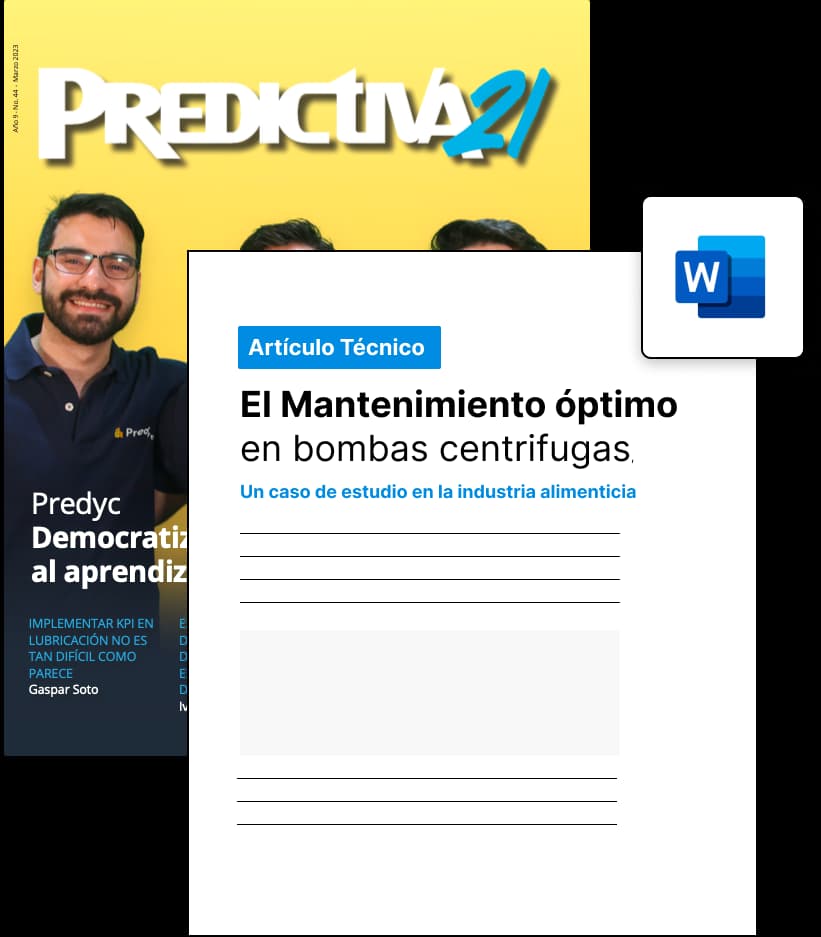
Si usted no construye su filosofía de mantenimiento, ninguna estrategia que utilice le servirá completamente
Articulo 15 de agosto de 2019La gente que está involucrada en el Mantenimiento reconoce que esta es la función más dinámica que hay en una planta, debido a que tenemos una gran cantidad de equipos por mantener, y cada uno de ellos tiene una enorme variedad de protocolos de mantenimiento. Adicionalmente a ello, requerimos de una gran cantidad de partes, materiales y repuestos para ejecutar el mantenimiento, diversidad de mano de obra; así mismo, debemos monitorear condiciones con precisión para aquellos activos críticos, controlar el Backlog.
Igualmente tenemos que planificar, programar ejecutar y registrar en los históricos que tengamos, ya sean en un software o simplemente en archivos manuales de mantenimiento. Indudablemente son demasiadas actividades que de no llevarlas correctamente, el mantenimiento dejaría de cumplir sus cometidos principales: lograr que los equipos operen la mayor cantidad de tiempo posible correctamente, menos paradas, rápidos tiempos para reparar, mayor seguridad y costos mínimos. Igualmente a todo esto se le suma, que los productos son diferentes, ubicaciones de las plantas en condiciones agresivas y un ingrediente muy importante: La Cultura de la Gente. Quizás podríamos encontrar muchas más razones que refuerzan lo que he dicho al principio de este artículo, pero pienso que son las principales.
Mi larga trayectoria por más de treinta años en el medio industrial como ingeniero de planta, gerente, consultor, investigador y profesor me ha reafirmado que “si usted no construye su propia filosofía de trabajo de mantenimiento, ninguna estrategia le servirá o simplemente no le sacará su máximo provecho”. Ahora bien, a qué me refiero con esto; la respuesta es que al igual que las personas, no hay dos iguales. Con ello quiero decir que no hay dos plantas iguales, aunque sean idénticas, y la razón radica en las personas. Quizás muchos no hayan oído hablar del psicólogo estadounidense Abraham Maslow, pero a los que sí han escuchado o leído sobre él, recordarán que fue quien desarrolló la famosa teoría de la Pirámide de Maslow y sus Jerarquía de necesidades.

Sumado a esto, tenemos la teoría de los factores Higiénicos y Motivacionales de Frederick Herzberg, que están relacionado con la satisfacción e insatisfacción. Los factores Motivacionales son los que producen satisfacción: logros, reconocimiento, independencia laboral, responsabilidad y promoción. Los factores Higiénicos son los que producen la insatisfacción: Sueldo y beneficios empresariales, política de la empresa y su organización, relaciones con los compañeros de trabajo, ambiente físico, supervisión, estatus, seguridad laboral, crecimiento, madurez, consolidación.
Muy bien, a lo mejor preguntarán, ¿Y qué tiene que ver todo esto con el mantenimiento? Pues les digo que mucho, debido a que un mantenimiento de calidad producto de su propia filosofía de trabajo está íntimamente relacionado con las personas a todos los niveles jerárquicos, desde la alta gerencia hasta el último técnico u obrero de la planta.
Ahora bien, uno de los artículos que desarrollé en esta revista, tenía que ver con La Actitud y La Aptitud de las personas hacia el mantenimiento y explicaba en su momento que había cuatro maneras de estar en el mantenimiento y era que:
- A la gente no le interesa el mantenimiento.
- La gente no sabe hacer mantenimiento.
- La gente no puede hacer mantenimiento.
- La gente no quiere hacer mantenimiento.
En ese artículo indicaba que pasaba cuando las personas se encontraban en cada uno de esos escenarios y qué debíamos hacer para dar respuesta con una salida razonable. Ustedes se preguntarán nuevamente qué tiene que ver esto con el mantenimiento; y nuevamente les digo que mucho, porque el mantenimiento gira en torno a la Actitud y Aptitudes de las personas. Imagínense todo ese cúmulo de actividades de las cuales comentamos al inicio de este artículo sino las hacemos con mucha “Disciplina, Constancia, Mística, Responsabilidad, Control y Seguimiento”; y que son el resultado de cuán bien estemos ubicados o estrechamente relacionados con la teoría de los factores y la Jerarquía de Necesidades comentadas anteriormente. Indudablemente de no profundizar en esto, estamos en el camino correcto al fracaso. “Recuerde no hay nada más peligroso para el mantenimiento que una persona confusa, desubicada, desorientada, distraída como resultado de uno o varios problemas: psíquicos, emocionales o físicos”.
Cuando me refiero a construir su filosofía de trabajo, me refiero hasta dónde quiere llegar con su mantenimiento, qué es lo que realmente le interesa y qué quiere alcanza. Tiene que ver con la planificación estratégica: dónde estamos hoy, dónde queremos estar en el futuro y el medio para hacerlo. Ese medio es su “Filosofía de Mantenimiento” para lograr lo que quiere. Es el vector que debe utilizar para llegar a su posición deseada con el mantenimiento. Es hacerse un traje a su medida.
En este sentido, cómo podemos utilizar una estrategia de: actividades predictivas, SMED, POKA YOKE, TPM, mantenimiento centrado en confiabilidad, o encaminarse a una implantación de la norma ISO 55000, etc. Si estamos o somos débiles con la condición de nuestra gente. Sé que algunas de estas estrategias de trabajos contemplan el Factor Humano, pero indudablemente tenemos que revisar en profundidad y no verlo como una simple condición para implantar cualquier estrategia de mantenimiento. Pienso que va mucho más allá, significa entender sin ningún tipo de duda que nuestro principal recurso es la gente, porque los equipos son inanimados, les damos vida cuando los operamos y mantenemos; y sin nuestra primera energía que es la gente no sería posible esta cruzada de “Construir una Filosofía de Trabajo de Mantenimiento Exitosa”.
Autor: Brau Clemenza
Consultor, Investigador, Articulista
Dinos qué te ha parecido el artículo
Artículos recomendados
¿Qué es la confiabilidad consciente?

CÓMO HACER UN PRESUPUESTO DE MANTENIMIENTO

Mantenimiento Asistido por Inteligencia Artificial, la evolución del Mantenimiento Prescriptivo

Tolerancias en rodamientos

Publica tu artículo en la revista #1 de Mantenimiento Industrial
Publicar un artículo en la revista es gratis, no tiene costo.
Solo debes asegurarte que no sea un artículo comercial.
¿Qué esperas?
O envía tu artículo directo: articulos@predictiva21.com
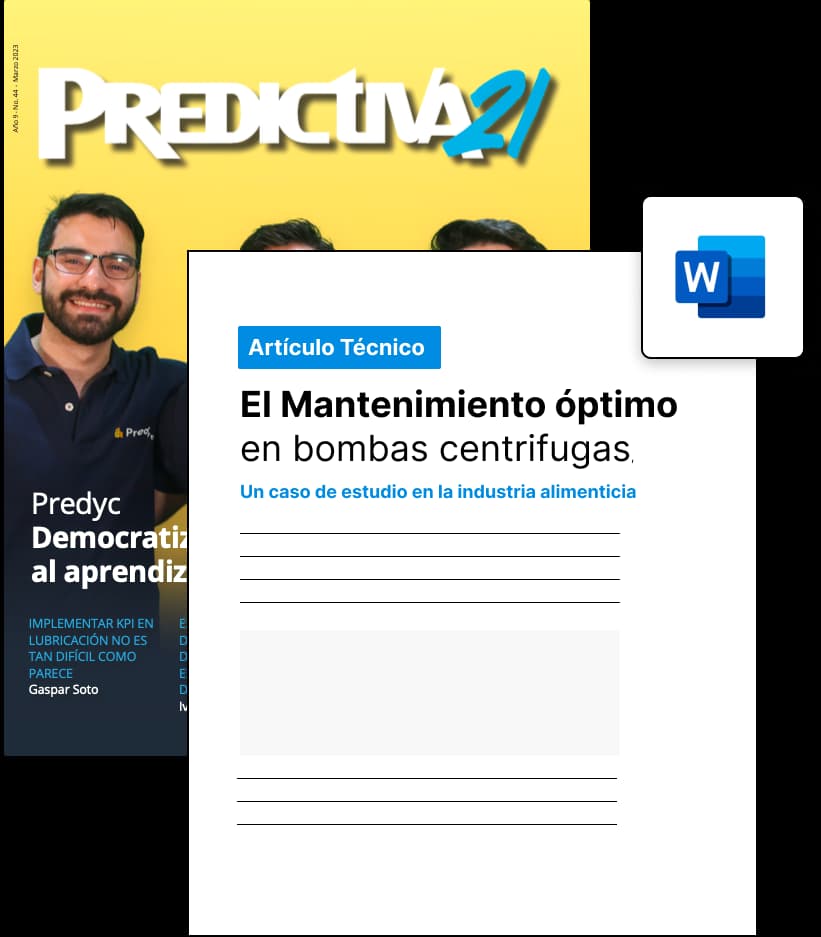