Del Invento de la Rueda a la Formula 1
Articulo30 de enero de 2020
En los Congresos Internacionales de los últimos años, por lo menos unos 50% de las Conferencias tratan de Gestión de Activos, una vez que, con la evolución tecnológica, la globalización y la competitividad, cada vez más las empresas deben buscar ser más eficientes y eficaces manteniendo un alto nivel de calidad, tiempos de entrega adecuados, eliminación de riesgos de accidentes y de contaminación.
En este año 2014 vamos tener aprobada la nueva norma internacional ISO 55000 que reglamenta procedimientos para el tema donde destacamos algunos conceptos importantes (1):
“Gestión de Activos: Actividad corporativa organizada que busca la generación de valores por los activos”
“Actividad también se refiere a la aplicación de elementos del Sistema de Gestión de Activos”
“El término Actividad corporativa tiene un significado amplio y puede incluir, por ejemplo, los planes y sus aplicaciones”
“La generación de valores normalmente involucrará el balance entre costos, riesgos, oportunidades y beneficios de mejoría de desempeño”
“Los valores pueden ser tangibles e intangibles, financieros o no-financieros e incluyen consideraciones de riesgo y confiabilidad”
“Vida del Activo: Período desde su concepción hasta su descarte”
“Costo de Ciclo de Vida: Las etapas que involucran la gestión de costos en la vida de un activo”
Además, esta misma norma indica que:
“La Gestión de Activos involucra el equilibrio de costos, oportunidades y riesgos a través del desempeño deseado, para lograr los objetivos organizacionales. El equilibrio debe ser considerado en diferentes marcos de tiempo.”
“La gestión de activos orienta a una organización para examinar la necesidad y el rendimiento de los activos y sus sistemas, en diferentes niveles. Además, orienta la aplicación de los enfoques analíticos a la gestión de activos en las diferentes etapas de su Ciclo de Vida (el cual puede comenzar con la concepción de la necesidad del activo hasta su desactivación e incluye el manejo de cualquier posible eliminación de los pasivos innecesarios)”
Donde, se destaca el texto:
“En las diferentes etapas de su Ciclo de Vida (el cual puede comenzar con la concepción de la necesidad del activo hasta su desactivación e incluye el manejo de cualquier posible eliminación de los pasivos innecesarios)”
Lo que refuerza la condición de búsqueda permanente de acciones que generen valores, eliminando los desperdicios de insumos, tiempos e improductividades de forma que permita que la empresa siga progresando, aun cuando las condiciones de mercado sean desfavorables.
Por lo tanto, la Gestión de Activos no involucra solamente el mantenimiento, sino también a toda la corporación. Además, que el término “activos” no se refiere solamente a los “activos físicos” y si a todo tipo de activo como el capital humano, los estándares, los procedimientos etc., donde se considera que la función mantenimiento pasa a ser la más indicada para hacer la coordinación del proyecto, que debe estar orientado para los enfoques financiero y estratégico.
Presentamos, a continuación, un recorrido en algunos hechos de procedimientos, técnicas, métodos, propuestas y situaciones que nos conllevan a la aplicación de la Gestión de Activos hasta el día de hoy (y que justifican el título de este trabajo).
Se puede decir que todo empieza con la primera revolución industrial (2). En el Siglo XIX con la mecanización de las industrias surge la necesidad de las primeras reparaciones.
Hasta 1914 las máquinas eran robustas y superdimensionadas y el mantenimiento tenía importancia secundaria y era ejecutado por el mismo efectivo de operación. Con el advenimiento de la Primera Guerra Mundial y la implantación de la producción en serie instituida por Ford, las fábricas pasan a establecer programas mínimos de producción y, en consecuencia, sintieron la necesidad de crear equipos que pudiesen efectuar reparaciones en máquinas en el menor tiempo posible. Así, surgió un órgano subordinado a operación, cuyo objetivo básico era de ejecución de mantenimiento, hoy día conocido como correctivo.
Esta situación se mantuvo hasta la década de 1940, cuando, en función de la Segunda Guerra Mundial y la necesidad de aumentar la rapidez de producción, la alta administración pasó a preocuparse, no solamente de corregir fallas sino también de evitar que las mismas ocurriesen, razón por la cual el personal técnico de mantenimiento pasó a desarrollar el proceso de Prevención de averías (basada en el tiempo y de acuerdo con las recomendaciones de los fabricantes) que, juntamente con la Corrección, completaban el cuadro general de mantenimiento.
En los años 50, con el desarrollo de la industria para satisfacer los esfuerzos de la posguerra, la evolución de la aviación comercial y de la industria electrónica, los Gerentes de Mantenimiento observaron que, en muchos casos, el tiempo empleado para diagnosticar las fallas era mayor que el tiempo empleado en la ejecución de la reparación y seleccionaron grupos de especialistas para conformar un órgano asesor que se llamó PCM - Planificación y Control de Mantenimiento. En este mismo periodo se desarrolla el Análisis FODA (3).

La tecnología de información vigente estaba basada en los gigantescos mainframes que rodaban los primeros sistemas de control de estoques - actividad pionera de inserción entre gestión y tecnología. La automatización era cara y lenta (aunque demandaba menos tiempo que los procesos manuales), y para pocos (4).
En 1960 la IATA (International Air Transport Association) teniendo en cuenta que las acciones preventivas tradicionales no garantizaban la seguridad de los vuelos, empieza a desarrollar los conceptos del Mantenimiento Centrado en la Confiabilidad (5).
En la segunda mitad de los 60 y a lo largo de los 70, con la difusión de las computadoras, el fortalecimiento de las Asociaciones Nacionales de Mantenimiento, creadas al final del periodo anterior y la sofisticación de los instrumentos de protección y medición, el PCM pasa a contar con un área especializada en análisis, la Ingeniería de Mantenimiento, que pasó a calcular y analizar los Indicadores de Mantenimiento. Además, aparecen en este periodo los CMMS (Sistema Computarizado para la Administración del Mantenimiento que ha evolucionado a los actuales EAM (Sistemas de Administración de Activos de la Empresa).
Aparecen los MRP’s (Material Requirement Planning - “Planeamiento de las Requisiciones de Materiales”), antecesores de los Sistemas ERP (Enterprise Resource Planning).
Se pasa a desarrollar criterios de predicción o previsión de fallas, con el objetivo de optimizar el desempeño de los grupos de ejecución del mantenimiento. Esos criterios, conocidos como Mantenimiento Predictivo o Previsivo, fueron asociados a métodos de planificación y control de mantenimiento automatizados, reduciendo las tareas burocráticas de los ejecutantes del mantenimiento.
En este mismo periodo aparecen el TPM (Mantenimiento Productivo Total - 1971) donde se implementa el llamado “mantenimiento autónomo”, o sea, algunas actividades de mantenimiento pasan a ser desarrolladas por el operador.
En 1980 las plantas generadoras de electricidad que funcionan con energía nuclear y el Instituto para la Investigación de la Energía Eléctrica, con el objetivo de abatir costos (más que mejorar la calidad del producto) modifica el Mantenimiento Centrado en la Confiabilidad en forma tan profunda que ha dado lugar a la Optimización del Mantenimiento Planificado (PMO).
En 1982 hay un estancamiento de la producción (tasas negativas en Gran Bretaña y en los países europeos), aumento espectacular del desempleo, (Estados Unidos registra en un solo mes medio millón de desempleados más), la producción industrial cae en Gran Bretaña al nivel de 1967 y, por primera vez desde 1945, el comercio mundial cae durante 2 años consecutivos. Se producen cierres de empresas y despidos masivos a un nivel jamás visto desde la depresión de 1929. Comienza a desarrollarse una tendencia que va a continuar creciendo desde entonces. Regiones enteras de rancia tradición industrial ven el cierre sistemático de fábricas y pozos mineros y el paro se dispara hasta índices del 30% (6). En la búsqueda de reducción de gastos se dejó de hacer mantenimiento y la consecuencia fue el aumento de pérdidas de patrimonio y aumento de accidentes.
Inicio de las redes de computadoras conectadas a servidores - más baratos y fáciles de usar que los mainframes. El MRP se transforma en MRP II (Manufacturing Resource Planning), que pasó a controlar también otras actividades como mano de obra y maquinaria. Nacía el ERP (Enterprise Resource Planning) (4).
En 1986, se desarrolla en Estados Unidos la metodología de evaluación por el Radar que tiene como principales ventajas la simplicidad de aplicación y la posibilidad de obtener de los operadores y mantenedores la identificación de puntos fuertes y debilidades de la empresa.
En 1988 Taiichi Ohno (ingeniero chino, jefe de Toyota Motors Company), divulga los conceptos del TPS en la publicación “Toyota production system: beyond large-scale production, Productivity press” donde indica: “Los valores sociales han cambiado. Ahora bien, no podemos vender nuestros productos a no ser que nos ubiquemos dentro de los corazones de nuestros consumidores, cada uno de los cuales tiene conceptos y gustos diferentes. Hoy en día, el mundo industrial se vio obligado a dominar de verdad el sistema de producción múltiple, en pequeñas cantidades” (7).

En 1990 se crea la “North American Maintenance Excellence Award (EEUU)” cuyo objetivo es impulsar la calidad y competencia en el uso de las “mejores prácticas” y la identificación de las empresas líderes; así como la divulgación y el intercambio de las mejores prácticas, estrategias y beneficios derivados de la implementación (8).
- 01) Trabajo en equipo.
- 02) Contratistas orientadas a la productividad.
- 03) Integración con proveedores de materiales y servicios.
- 04) Apoyo y visión de la dirección.
- 05) Planificación y programación proactiva.
- 06) Mejoramiento continuo.
- 07) Gestión disciplinada de stock de materiales.
- 08) Integración de sistemas.
- 09) Gestión de paradas de planta.
- 10) Producción basada en confiabilidad.
En 1991 Dupont presenta su propuesta de evaluación del Grado de Madurez de la empresa que, saliendo del nivel “Tradicional” se pasa al nivel “Transición” y se alcanza el nivel “Clase Mundial”. Esta propuesta fue sucedida por la evaluación de McKinsey en 1995 donde se amplía de tres a doce pilares con cinco niveles en cada uno y, en 2000, por Tompkins Associates Inc. con siete pilares y cinco niveles en cada uno. En 1993 una nueva forma de gestionar era requerida y así nace el Institute of Asset Management (IAM), agrupando diversas empresas interesadas en compartir experiencias y mejores prácticas. Este instituto establece nuevas prácticas llamadas de Gestión de Activos que trajeron una revolución en el Reino Unido, Australia y Nueva Zelandia que, dos años después, ya tenían un grupo de compañías de estos países asociados al Instituto (8).
En 1998 se establece para diferentes mercados e industrias, la necesidad de crear las bases sólidas para el Asset Management y, en el 2003, se establece el comité de British Standard en Asset Management, que en mayo 2004 publican las especificaciones British Standard PAS 55 apoyada en las normas ISO 9000, ISO 14000 y OSHA 18000 (8). Los CMMS evolucionan a los EAM.
En 2005 se incorpora el mantenimiento en la filosofía FEL (Front End Loading), también conocida como “Planeamiento Preproyecto (PPP) o “Ingeniería Final del Inicio del Proyecto” (FEED) que es un método de desarrollo de proyectos de capital (9).
En 2008 la gran aceptación de PAS 55 plantea la generación de otra norma ISO que considera todo lo que se ha venido haciendo hasta entonces, pero de una forma más sistémica (8).

En el 10 de agosto de 2010 el comité técnico de ISO decide por la creación de un Estándar Internacional para la gestión de activos basado en el documento de la PAS55 - La ISO 55000 (8). Hoy en día, el reto es rentabilizar el negocio con sustentabilidad haciendo que la gestión de activos físicos sea considerada como un negocio conduce a la aplicación de la ISO 55000 como guía para lograrlo.
Cursos recomendados






%252FImagen%252FRAMPREDYC-1730060420837.webp%3Falt%3Dmedia%26token%3D2634a7f0-988e-4022-b91f-382503e6e9db&w=3840&q=75)

Referencias
- -Asset Performance Management Industry Trends Paul R. Casto - Meridiun. 28o Congresso Brasileiro de Manutenção - Setembro 2013
- -Mantenimiento Centrado en el Negocio. Lourival Augusto Tavares, Marco Antonio Calixto, Paulo Roberto Poydo y João Esmeraldo Silva. Noria Latinoamerica - www.noria.com.mx.
- -Significado de SWOT. www.significados.com.br
- -Sistema Integrado de Gestão Empresarial. Wilkepedia - Enciclopedia Libre.
- -Evolución del mantenimiento. Yrmeric Gonzalez Blog mantenimiento 1. http://ugmamantenimiento12011.blogspot.com.br/2011/10 /evolucion-del-mantenimiento.html.
- -Crisis económica (II) - Los años 80 - Treinta años de crisis abierta del capitalismo. Revista Internacional el abril 17, 1999. http://es.internationalism.org/rint97-crisis#_ftn1
- -Sistema Toyota de Produção. Wilkepedia - Enciclopedia Libre.
- -Pilares que sustentan la gestión de activos físicos Luis Amendola. Congreso Brasileño de Mantenimiento. Septiembre 2013
- -Metodologia FEL - Metodo dos Portões. Rodolfo Stonner. Blogtek.com. http://blogtek.com.br/metodologia-fel-%e2%80%93-metod o-dos-portoes/
Autor: Alexandre Dias Tavares
Dinos qué te ha parecido el artículo
Artículos recomendados
El valor del Mantenimiento Predictivo

Uso de la psicología del comportamiento en Reportes de Mantenimiento basado en Condición para hacerlos más efectivos

Refinería Dos Bocas, una obra en medio de la polémica

Ultrasonido

Publica tu artículo en la revista #1 de Mantenimiento Industrial
Publicar un artículo en la revista es gratis, no tiene costo.
Solo debes asegurarte que no sea un artículo comercial.
¿Qué esperas?
O envía tu artículo directo: articulos@predictiva21.com
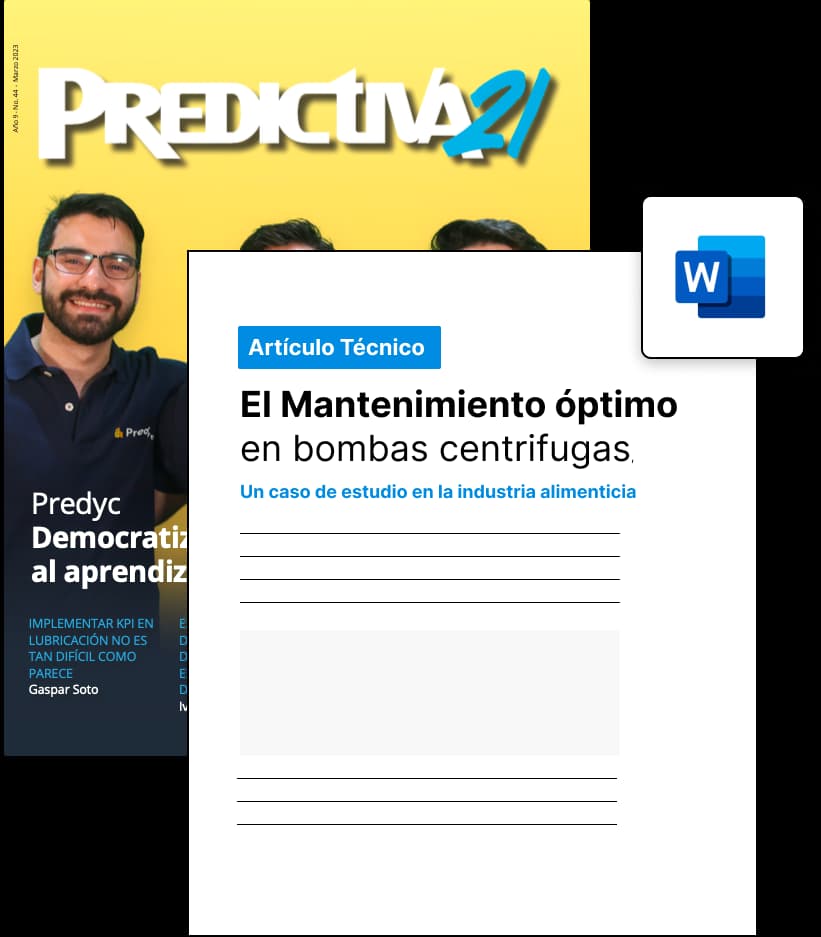
Del Invento de la Rueda a la Formula 1
Articulo 30 de enero de 2020En los Congresos Internacionales de los últimos años, por lo menos unos 50% de las Conferencias tratan de Gestión de Activos, una vez que, con la evolución tecnológica, la globalización y la competitividad, cada vez más las empresas deben buscar ser más eficientes y eficaces manteniendo un alto nivel de calidad, tiempos de entrega adecuados, eliminación de riesgos de accidentes y de contaminación.
En este año 2014 vamos tener aprobada la nueva norma internacional ISO 55000 que reglamenta procedimientos para el tema donde destacamos algunos conceptos importantes (1):
“Gestión de Activos: Actividad corporativa organizada que busca la generación de valores por los activos”
“Actividad también se refiere a la aplicación de elementos del Sistema de Gestión de Activos”
“El término Actividad corporativa tiene un significado amplio y puede incluir, por ejemplo, los planes y sus aplicaciones”
“La generación de valores normalmente involucrará el balance entre costos, riesgos, oportunidades y beneficios de mejoría de desempeño”
“Los valores pueden ser tangibles e intangibles, financieros o no-financieros e incluyen consideraciones de riesgo y confiabilidad”
“Vida del Activo: Período desde su concepción hasta su descarte”
“Costo de Ciclo de Vida: Las etapas que involucran la gestión de costos en la vida de un activo”
Además, esta misma norma indica que:
“La Gestión de Activos involucra el equilibrio de costos, oportunidades y riesgos a través del desempeño deseado, para lograr los objetivos organizacionales. El equilibrio debe ser considerado en diferentes marcos de tiempo.”
“La gestión de activos orienta a una organización para examinar la necesidad y el rendimiento de los activos y sus sistemas, en diferentes niveles. Además, orienta la aplicación de los enfoques analíticos a la gestión de activos en las diferentes etapas de su Ciclo de Vida (el cual puede comenzar con la concepción de la necesidad del activo hasta su desactivación e incluye el manejo de cualquier posible eliminación de los pasivos innecesarios)”
Donde, se destaca el texto:
“En las diferentes etapas de su Ciclo de Vida (el cual puede comenzar con la concepción de la necesidad del activo hasta su desactivación e incluye el manejo de cualquier posible eliminación de los pasivos innecesarios)”
Lo que refuerza la condición de búsqueda permanente de acciones que generen valores, eliminando los desperdicios de insumos, tiempos e improductividades de forma que permita que la empresa siga progresando, aun cuando las condiciones de mercado sean desfavorables.
Por lo tanto, la Gestión de Activos no involucra solamente el mantenimiento, sino también a toda la corporación. Además, que el término “activos” no se refiere solamente a los “activos físicos” y si a todo tipo de activo como el capital humano, los estándares, los procedimientos etc., donde se considera que la función mantenimiento pasa a ser la más indicada para hacer la coordinación del proyecto, que debe estar orientado para los enfoques financiero y estratégico.
Presentamos, a continuación, un recorrido en algunos hechos de procedimientos, técnicas, métodos, propuestas y situaciones que nos conllevan a la aplicación de la Gestión de Activos hasta el día de hoy (y que justifican el título de este trabajo).
Se puede decir que todo empieza con la primera revolución industrial (2). En el Siglo XIX con la mecanización de las industrias surge la necesidad de las primeras reparaciones.
Hasta 1914 las máquinas eran robustas y superdimensionadas y el mantenimiento tenía importancia secundaria y era ejecutado por el mismo efectivo de operación. Con el advenimiento de la Primera Guerra Mundial y la implantación de la producción en serie instituida por Ford, las fábricas pasan a establecer programas mínimos de producción y, en consecuencia, sintieron la necesidad de crear equipos que pudiesen efectuar reparaciones en máquinas en el menor tiempo posible. Así, surgió un órgano subordinado a operación, cuyo objetivo básico era de ejecución de mantenimiento, hoy día conocido como correctivo.
Esta situación se mantuvo hasta la década de 1940, cuando, en función de la Segunda Guerra Mundial y la necesidad de aumentar la rapidez de producción, la alta administración pasó a preocuparse, no solamente de corregir fallas sino también de evitar que las mismas ocurriesen, razón por la cual el personal técnico de mantenimiento pasó a desarrollar el proceso de Prevención de averías (basada en el tiempo y de acuerdo con las recomendaciones de los fabricantes) que, juntamente con la Corrección, completaban el cuadro general de mantenimiento.
En los años 50, con el desarrollo de la industria para satisfacer los esfuerzos de la posguerra, la evolución de la aviación comercial y de la industria electrónica, los Gerentes de Mantenimiento observaron que, en muchos casos, el tiempo empleado para diagnosticar las fallas era mayor que el tiempo empleado en la ejecución de la reparación y seleccionaron grupos de especialistas para conformar un órgano asesor que se llamó PCM - Planificación y Control de Mantenimiento. En este mismo periodo se desarrolla el Análisis FODA (3).

La tecnología de información vigente estaba basada en los gigantescos mainframes que rodaban los primeros sistemas de control de estoques - actividad pionera de inserción entre gestión y tecnología. La automatización era cara y lenta (aunque demandaba menos tiempo que los procesos manuales), y para pocos (4).
En 1960 la IATA (International Air Transport Association) teniendo en cuenta que las acciones preventivas tradicionales no garantizaban la seguridad de los vuelos, empieza a desarrollar los conceptos del Mantenimiento Centrado en la Confiabilidad (5).
En la segunda mitad de los 60 y a lo largo de los 70, con la difusión de las computadoras, el fortalecimiento de las Asociaciones Nacionales de Mantenimiento, creadas al final del periodo anterior y la sofisticación de los instrumentos de protección y medición, el PCM pasa a contar con un área especializada en análisis, la Ingeniería de Mantenimiento, que pasó a calcular y analizar los Indicadores de Mantenimiento. Además, aparecen en este periodo los CMMS (Sistema Computarizado para la Administración del Mantenimiento que ha evolucionado a los actuales EAM (Sistemas de Administración de Activos de la Empresa).
Aparecen los MRP’s (Material Requirement Planning - “Planeamiento de las Requisiciones de Materiales”), antecesores de los Sistemas ERP (Enterprise Resource Planning).
Se pasa a desarrollar criterios de predicción o previsión de fallas, con el objetivo de optimizar el desempeño de los grupos de ejecución del mantenimiento. Esos criterios, conocidos como Mantenimiento Predictivo o Previsivo, fueron asociados a métodos de planificación y control de mantenimiento automatizados, reduciendo las tareas burocráticas de los ejecutantes del mantenimiento.
En este mismo periodo aparecen el TPM (Mantenimiento Productivo Total - 1971) donde se implementa el llamado “mantenimiento autónomo”, o sea, algunas actividades de mantenimiento pasan a ser desarrolladas por el operador.
En 1980 las plantas generadoras de electricidad que funcionan con energía nuclear y el Instituto para la Investigación de la Energía Eléctrica, con el objetivo de abatir costos (más que mejorar la calidad del producto) modifica el Mantenimiento Centrado en la Confiabilidad en forma tan profunda que ha dado lugar a la Optimización del Mantenimiento Planificado (PMO).
En 1982 hay un estancamiento de la producción (tasas negativas en Gran Bretaña y en los países europeos), aumento espectacular del desempleo, (Estados Unidos registra en un solo mes medio millón de desempleados más), la producción industrial cae en Gran Bretaña al nivel de 1967 y, por primera vez desde 1945, el comercio mundial cae durante 2 años consecutivos. Se producen cierres de empresas y despidos masivos a un nivel jamás visto desde la depresión de 1929. Comienza a desarrollarse una tendencia que va a continuar creciendo desde entonces. Regiones enteras de rancia tradición industrial ven el cierre sistemático de fábricas y pozos mineros y el paro se dispara hasta índices del 30% (6). En la búsqueda de reducción de gastos se dejó de hacer mantenimiento y la consecuencia fue el aumento de pérdidas de patrimonio y aumento de accidentes.
Inicio de las redes de computadoras conectadas a servidores - más baratos y fáciles de usar que los mainframes. El MRP se transforma en MRP II (Manufacturing Resource Planning), que pasó a controlar también otras actividades como mano de obra y maquinaria. Nacía el ERP (Enterprise Resource Planning) (4).
En 1986, se desarrolla en Estados Unidos la metodología de evaluación por el Radar que tiene como principales ventajas la simplicidad de aplicación y la posibilidad de obtener de los operadores y mantenedores la identificación de puntos fuertes y debilidades de la empresa.
En 1988 Taiichi Ohno (ingeniero chino, jefe de Toyota Motors Company), divulga los conceptos del TPS en la publicación “Toyota production system: beyond large-scale production, Productivity press” donde indica: “Los valores sociales han cambiado. Ahora bien, no podemos vender nuestros productos a no ser que nos ubiquemos dentro de los corazones de nuestros consumidores, cada uno de los cuales tiene conceptos y gustos diferentes. Hoy en día, el mundo industrial se vio obligado a dominar de verdad el sistema de producción múltiple, en pequeñas cantidades” (7).

En 1990 se crea la “North American Maintenance Excellence Award (EEUU)” cuyo objetivo es impulsar la calidad y competencia en el uso de las “mejores prácticas” y la identificación de las empresas líderes; así como la divulgación y el intercambio de las mejores prácticas, estrategias y beneficios derivados de la implementación (8).
- 01) Trabajo en equipo.
- 02) Contratistas orientadas a la productividad.
- 03) Integración con proveedores de materiales y servicios.
- 04) Apoyo y visión de la dirección.
- 05) Planificación y programación proactiva.
- 06) Mejoramiento continuo.
- 07) Gestión disciplinada de stock de materiales.
- 08) Integración de sistemas.
- 09) Gestión de paradas de planta.
- 10) Producción basada en confiabilidad.
En 1991 Dupont presenta su propuesta de evaluación del Grado de Madurez de la empresa que, saliendo del nivel “Tradicional” se pasa al nivel “Transición” y se alcanza el nivel “Clase Mundial”. Esta propuesta fue sucedida por la evaluación de McKinsey en 1995 donde se amplía de tres a doce pilares con cinco niveles en cada uno y, en 2000, por Tompkins Associates Inc. con siete pilares y cinco niveles en cada uno. En 1993 una nueva forma de gestionar era requerida y así nace el Institute of Asset Management (IAM), agrupando diversas empresas interesadas en compartir experiencias y mejores prácticas. Este instituto establece nuevas prácticas llamadas de Gestión de Activos que trajeron una revolución en el Reino Unido, Australia y Nueva Zelandia que, dos años después, ya tenían un grupo de compañías de estos países asociados al Instituto (8).
En 1998 se establece para diferentes mercados e industrias, la necesidad de crear las bases sólidas para el Asset Management y, en el 2003, se establece el comité de British Standard en Asset Management, que en mayo 2004 publican las especificaciones British Standard PAS 55 apoyada en las normas ISO 9000, ISO 14000 y OSHA 18000 (8). Los CMMS evolucionan a los EAM.
En 2005 se incorpora el mantenimiento en la filosofía FEL (Front End Loading), también conocida como “Planeamiento Preproyecto (PPP) o “Ingeniería Final del Inicio del Proyecto” (FEED) que es un método de desarrollo de proyectos de capital (9).
En 2008 la gran aceptación de PAS 55 plantea la generación de otra norma ISO que considera todo lo que se ha venido haciendo hasta entonces, pero de una forma más sistémica (8).

En el 10 de agosto de 2010 el comité técnico de ISO decide por la creación de un Estándar Internacional para la gestión de activos basado en el documento de la PAS55 - La ISO 55000 (8). Hoy en día, el reto es rentabilizar el negocio con sustentabilidad haciendo que la gestión de activos físicos sea considerada como un negocio conduce a la aplicación de la ISO 55000 como guía para lograrlo.
Cursos recomendados






%252FImagen%252FRAMPREDYC-1730060420837.webp%3Falt%3Dmedia%26token%3D2634a7f0-988e-4022-b91f-382503e6e9db&w=3840&q=75)

Referencias
- -Asset Performance Management Industry Trends Paul R. Casto - Meridiun. 28o Congresso Brasileiro de Manutenção - Setembro 2013
- -Mantenimiento Centrado en el Negocio. Lourival Augusto Tavares, Marco Antonio Calixto, Paulo Roberto Poydo y João Esmeraldo Silva. Noria Latinoamerica - www.noria.com.mx.
- -Significado de SWOT. www.significados.com.br
- -Sistema Integrado de Gestão Empresarial. Wilkepedia - Enciclopedia Libre.
- -Evolución del mantenimiento. Yrmeric Gonzalez Blog mantenimiento 1. http://ugmamantenimiento12011.blogspot.com.br/2011/10 /evolucion-del-mantenimiento.html.
- -Crisis económica (II) - Los años 80 - Treinta años de crisis abierta del capitalismo. Revista Internacional el abril 17, 1999. http://es.internationalism.org/rint97-crisis#_ftn1
- -Sistema Toyota de Produção. Wilkepedia - Enciclopedia Libre.
- -Pilares que sustentan la gestión de activos físicos Luis Amendola. Congreso Brasileño de Mantenimiento. Septiembre 2013
- -Metodologia FEL - Metodo dos Portões. Rodolfo Stonner. Blogtek.com. http://blogtek.com.br/metodologia-fel-%e2%80%93-metod o-dos-portoes/
Autor: Alexandre Dias Tavares
Dinos qué te ha parecido el artículo
Artículos recomendados
Jefe de mantenimiento

La termografía y el mantenimiento predictivo

Aplicación del estándar API 581 a un activo físico instalado en la industria petroquímica: Caso de estudio basado en Métodos y Normas Vigentes

La Efectividad de las actividades de Mantenimiento

Publica tu artículo en la revista #1 de Mantenimiento Industrial
Publicar un artículo en la revista es gratis, no tiene costo.
Solo debes asegurarte que no sea un artículo comercial.
¿Qué esperas?
O envía tu artículo directo: articulos@predictiva21.com
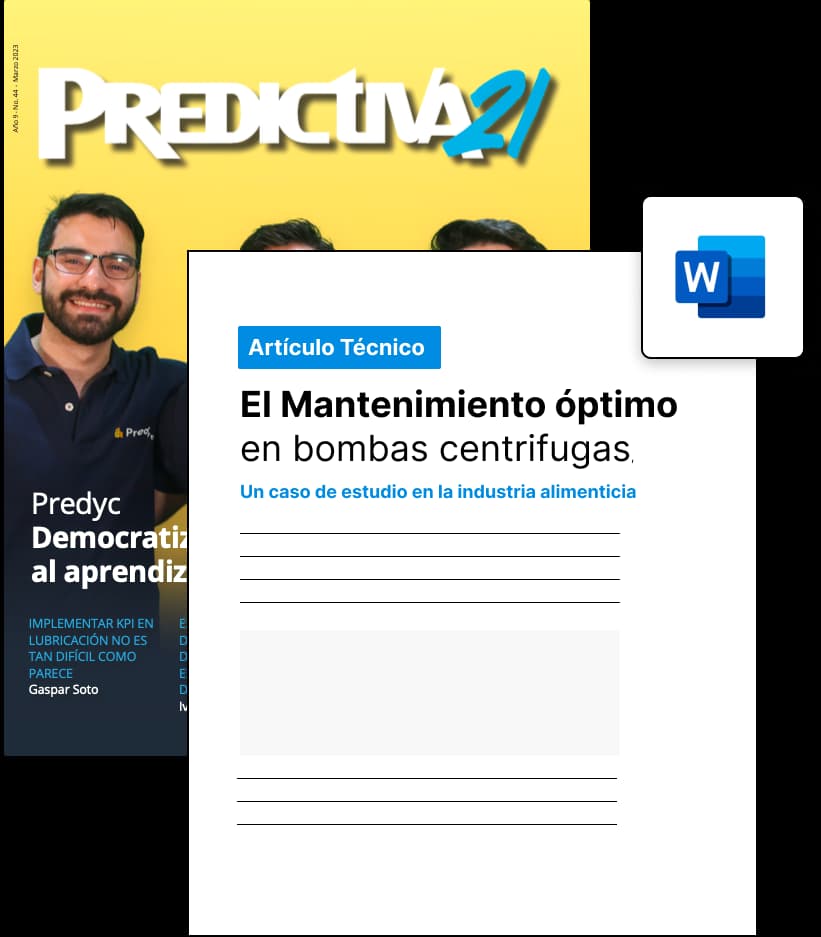