Propuesta de adopción de modelos de optimización de alcance, duración y costo en paradas de planta
Articulo22 de junio de 2022
Proposal for the adoption of scope, duration and cost optimization models in turnaround
Resumen
Las paradas de planta (mantenimiento mayor) en las refinerías de petróleo son actividades de alto impacto para el negocio, su gestión adecuada es relevante para obtener los resultados esperados y por tanto la industria ha adoptado metodologías, métodos, herramientas y buenas prácticas para mejorar su gestión, muchas de estas, provenientes de la gestión de proyectos. En este artículo se proponen algunas buenas prácticas de la industria, en el marco de la gestión de proyectos, para mejorar el desempeño de las paradas de planta (mantenimiento mayor), específicamente los asociados a la gestión de la triple restricción clásica: alcance, duración y costo.
Se realiza una revisión de los resultados históricos de paradas de planta en la organización (premisas vs. resultados finales); como también el referenciamiento internacional con refinerías similares que también participan de estos estudios en el área de la costa del golfo. Se utilizan listas de verificación de cumplimiento para validar el desempeño de las áreas de gestión frente a los resultados del mantenimiento de dos eventos ejecutados en 2021.
Se exploran los factores de éxito de una parada de planta asociados al cumplimiento de las premisas definidas de alcance, duración y costo, identificando como variables incidentes principales para su desempeño, la calidad de la planificación y la materialización de trabajos emergentes como catalizadores del incremento en alcance, duración y costo.
A partir de la data analizada se relacionó el efecto de las desviaciones con la baja gestión en el enfoque organizacional y a la necesidad de formas diferentes de abordarlos, y de allí surge la propuesta de adopción de buenas prácticas tendientes a la optimización. La propuesta presenta dos enfoques, el primero, abordando temática organizacional: creación de una PMO de apoyo; y un segundo enfoque asociado a la incorporación de buenas prácticas y herramientas específicas que mejoren el desempeño, tales como la definición de alcance bajo RBWS, la gestión de duración bajo cadena crítica y la gestión de estimación de costo bajo buenas prácticas de la AACE, entre otras, todas bajo un contexto de gestión del riesgo.
Palabras Clave
Parada de Planta, PMO, Triple Restricción, Gestión del Riesgo, RBWS, CCPM.
Abstract
Plant shutdowns (turnaround) in oil & gas refineries are activities with a high impact for the business, their proper management is relevant to obtain the expected results and therefore the industry has adopted methodologies, methods, tools, and good practices to improve their performance management, many of these, coming from project management. This article proposes some good industry practices, within the framework of project management, to improve the performance of plant shutdowns (major maintenance), specifically those associated with the management of the classic triple constraint: scope, duration, and cost.
A review of the historical results of turnaround in the organization (premises vs. results) is carried out; as well as international benchmarking with similar refineries that also participate in these studies in the Gulf Coast area. Compliance checklists are used to validate the performance of the management areas against the maintenance results of two events executed in 2021.
The success factors of a turnaround associated with compliance with the defined premises of scope, duration and cost are explored, identifying as main incident variables for its performance, the quality of planning and the materialization of emerging works as catalysts for the increase in production. scope, duration, and cost.
From the data analyzed, the effect of the deviations was related to poor management in the organizational approach and the need for different ways to address them, and from there the proposal for the adoption of good practices aimed at optimization arises. The proposal presents two approaches, the first, addressing organizational issues: creation of a support PMO; and a second approach associated with the incorporation of good practices and specific tools that improve performance, such as scope definition under RBWS, duration management under critical chain and cost estimation management under good practices of the AACE, among others. others, all in a risk management context.
Key words
Turnaround, PMO, Triple Constraint; Risk Management, RBWS, CCPM.
I. Introducción
Una parada de planta (mantenimiento mayor) es un evento de impacto superlativo sobre los resultados del negocio de refinación y de manera general sobre la organización y, por tanto, se consideran factores determinantes de este impacto aspectos como: el alcance, la duración, y el costo, ente otros.
Así pues, una gestión adecuada sobre estos aspectos influenciará positivamente los resultados de la organización, desde la disponibilidad operacional, pasando por la confiabilidad de sus activos y finalmente su impacto positivo en la producción y los resultados económicos del negocio. Para efectos de este artículo, se usará de manera intercambiable el termino mantenimiento mayor y parada de planta como equivalentes.
En algunas organizaciones, las paradas de planta son consideradas como un proyecto, desde la perspectiva de su gestión, sin embargo, existen otras corrientes que discrepan de esta definición, no obstante, para efectos de este artículo, se acepta que una parada de planta obedece, de manera general, a la definición de lo que es un proyecto de acuerdo con el Project Manegement Institute (PMI) en su guía PMBOK, en su sexta edición [1].
En este orden de ideas, es importante reconocer que la relación existente entre la gestión de activos industriales y la gestión de proyectos, presentan diversos puntos en común lo que acentúa la posibilidad de hacer uso de algunas de sus metodologías, herramientas, procesos, estándares y buenas prácticas entre ambos.
Por su definición, bajo la norma internacional ISO 55000 – Gestión de Activos – Aspectos generales, principios y terminología: “Un sistema de gestión de activos es un conjunto de elementos de una organización interrelacionados y que interactúan cuya función es establecer la política y los objetivos de la gestión de activos y los procesos necesarios para alcanzar dichos objetivos” [2].
Puntualmente para la organización base de este artículo, la gestión de activos industriales tiene como propósito incidir en el ciclo de vida del activo, primando la perspectiva de la confiabilidad operacional, la administración rentable y gerenciamiento del riesgo mediante la aplicación de las mejores prácticas integradas existentes, garantizando la integridad de las personas, el medio ambiente, la infraestructura, en armonía con el entorno y la continuidad de las operaciones, bajo criterios de eficiencia, eficacia y efectividad [3].
Para el modelo de la organización el ciclo de vida del activo se desarrolla a través de diferentes fases (5): a) Incorporación, b) Operación de Mantenimiento, c) Operación Estructurada, d) Optimización del Activo y e) Desincorporación. Dentro de la fase de operación de mantenimiento (rutinario y mayor), se encuentra circunscrito el proceso de mantenimiento mayor también conocido como parada de planta, y que es objetivo en este artículo.
Por otra parte, la gestión de proyectos puede entenderse como un conjunto de metodologías, herramientas, estándares, entre otros, con el propósito de crear un producto, servicio, o resultado único [1]. Bajo este contexto es importante comprender que todo proyecto o la gestión de este viene limitado por restricciones inherentes como suelen ser, el alcance, la duración, el costo, entre otros, lo cual es denominado bajo el PMBOK como la triple restricción.
Es importante aclarar que existen múltiples interpretaciones asociadas a este concepto que consideran no solo estos tres factores, sino que incluye otros como: calidad, riesgos, interesados, etc., y tiende a denominarse múltiple restricción. Si bien la múltiple restricción es un concepto ampliado, para los efectos de este artículo, el enfoque será sobre la triple restricción original.
Ahora bien, aceptando que una parada de planta posee las características de un proyecto, se puede evidenciar que la gestión de estos tipos de mantenimiento se enmarca en modelos que claramente difieren de una organización a otra debido fundamentalmente a su naturaleza, a su frecuencia o a su alcance, es decir, la manera como se gestiona una parada de planta obedece fundamentalmente a las necesidades y requerimientos propios de cada organización.
No obstante, esas diferencias, la mayoría de estos modelos converge en aspectos tales como: un inicio, la planificación, la ejecución, monitoreo y control, y el cierre. El modelo por considerar en este artículo [3] está orientado en gran medida en las áreas de gestión (conocimiento) manifestadas por el PMI en su guía PMBOK.
Las mejores prácticas de la industria y los datos de referenciamiento consultados, plantean cifras inquietantes que deben ser gestionados por su impacto negativo en los resultados de las paradas de planta: desviaciones en el alcance, debido a incremento de este, con valores por encima de un 15% al planeado; en duración, debido a extensión del mantenimiento, del orden del 10% al planeado; y en costo por encima del 25%, debido a las desviaciones precedentes [4].
Estas cifras generales de la industria muestran como un factor potencial de mejora disminuir estas desviaciones a través de diversos métodos. En este sentido, este articulo presenta un análisis y diagnóstico de los resultados obtenidos en un conjunto de paradas de planta como también datos de referenciamiento de la industria, construido alrededor de resultados históricos recientes.
Para este análisis y diagnostico partimos de la premisa de optimizar a través del uso de metodologías conocidas y probadas bajo los estrictos estándares internacionales que rigen el que hacer de la organización, considerando como factor de éxito de la parada de planta, el cumplimiento de los objetivos planificados en alcance, duración y costo.
Así pues, a través de proponer métodos que integren la gestión de la parada de planta, se pretende identificar e incidir positivamente en los tres aspectos focales de alcance, duración y costo de esta, a través de la potenciación de los factores internos de la organización. Para esto se propone un referenciamiento interno y externo del proceso de parada de planta (mantenimiento mayor), con énfasis en su fase de planificación y su impacto final en el resultado y cumplimiento de las premisas de este.
II. Contexto del proceso de mantenimiento mayor (parada de planta) en la organización
A continuación, se desarrolla una descripción del proceso de mantenimiento mayor (parada de planta) en la organización, considerando sus objetivos y metas (premisas); siguiendo por un entendimiento de la manera actual en que se desarrollan los aspectos del alcance, la duración y el costo de cada parada de planta; como también, un repaso sobre la manera en que se aborda la planificación de las paradas de planta y finalmente describiendo el contexto organizacional actual.
Proceso de mantenimiento mayor (parada de planta)
El proceso de mantenimiento mayor (parada de planta) considerado en este artículo es el adoptado por la organización [3], el cual está en vigencia desde hace más de 25 años y fue un modelo transferido por buenas prácticas y convenios realizados con referentes internacionales del negocio oil & gas.
El objetivo del proceso es: “Llevar a cabo la reparación programada de una unidad productiva para mejorar la confiabilidad y disponibilidad de los equipos que la compone en su ciclo de corrida, cumpliendo eficiencia, eficacia y efectividad, asegurando la integridad de las personas, el medio ambiente, la infraestructura, la armonía con el entorno” [3].
Si bien el objetivo de un mantenimiento mayor (parada de planta) se describe claramente en el párrafo anterior, es muy importante comprender algunas de las razones principales por las que se incurre en estas actividades de mantenimiento.
En principio se debe considerar que un mantenimiento mayor (parada de planta) corresponde a una seria de actividades que de no estar la planta fuera de servicio, no se podrían ejecutar y habitualmente corresponden a actividades como cambio de partes, piezas, repuestos o de componentes que superan su ciclo de vida, que han sufrido obsolescencia o mal funcionamiento, para inspeccionar los equipos, también para gestionar cambios en las unidades a través de proyectos de mejora, modificación y/o corrección de fallas, sin olvidar el cumplimiento de regulaciones y contratos de licenciamiento, etc.
Considerando lo anterior, se puede entender bajo el criterio de definición que “un mantenimiento mayor es el que se hace a la unidad operativa (sistema de activos industriales), cuando esta se encuentra fuera de servicio, después de haber cumplido su ciclo de corrida definida a partir de las metodologías de confiabilidad (RCM, RBI, IPF, entre otras).
Adicionalmente, este mantenimiento debe cumplir las fechas establecidas en el plan de hitos de los mantenimientos mayores, y cumplir cada una de las fases descritas en este proceso: Planear actividades de largo plazo, Precisar el alcance del mantenimiento mayor, Planificación del mantenimiento mayor, Realizar actividades de alistamiento, Ejecutar el mantenimiento mayor, Cerrar el mantenimiento mayor” [3].

La figura 1 describe la relación entre las fases del mantenimiento mayor de la organización y los procesos de gestión o áreas del conocimiento necesarios y considerados para gestionarlo. Igualmente muestra una línea de tiempo donde se recomienda iniciar y finalizar de cada una de las fases del proceso (desde 30 meses antes hasta 4 meses después de la ejecución), como también los hitos principales de inicio y cierre de cada una de ellas.
Cada una de las fases descritas y representadas en la figura 1 anterior, se gestionan a través de diferentes áreas del conocimiento que coinciden en su mayoría con las áreas de gestión referenciadas en el PMBOK del PMI. Esto es importante ya que permite establecer un relacionamiento entre el impacto de las áreas de gestión y cada una de las fases del mantenimiento mayor, eso sí, tomando como referencia el criterio base de las premisas del mantenimiento enfocadas en el alcance, la duración y el costo.
Las entradas de las diferentes fases obedecen a hitos bien definidos del proceso y son determinantes para el éxito de la parada de planta, entre otros son: Premisas del mantenimiento, Congelamiento de alcance, Paquetes de Trabajo (Planificación / Programación), Talleres de Alistamiento, Ejecución, Corrida de desempeño, Informe final.
Objetivos y metas de una parada de planta
Las premisas de la parada de planta consisten en la definición de los objetivos y metas a través de un documento con los lineamientos para el alcance, la duración, el costo, el desempeño HSE, de calidad, y productividad durante la ejecución de la parada, como también la eficiencia y la confiabilidad esperada para l la planta intervenida, los niveles de riesgo aceptados, entre otros. En dicho documento se establecen las métricas necesarias para validar el éxito del mantenimiento mayor y contra esta línea base se realizan las comparaciones del desempeño del mantenimiento.
Como característica clave, las premisas deben ser un documento validado y aprobado oportunamente por todos los interesados requeridos y sustentado en los niveles necesarios, en resumen, es el compromiso entre las partes para el mantenimiento mayor bajo el cual se cobijan el negocio, su estrategia y los aspectos particulares del mantenimiento mayor y es validado y aprobado por los niveles superiores de la organización.
Alcance de una parada de planta
El alcance para una parada de planta surge de diferentes escenarios, requerimiento y necesidades como se describió previamente. Sin embargo, no todo el alcance “propuesto” es incluido finalmente. Previo a su precisión, se realizan diversos talleres de revisión y validación bajo las metodologías propias y derivando finalmente en lo que se denomina el alcance congelado, o en otros referenciamientos como la lista de trabajos (work list).
El alcance congelado es un registro que corresponde al listado priorizado de ordenes de mantenimiento (CMMS), donde se identifican los activos industriales a intervenir durante el mantenimiento mayor con un alcance definido, así como las que fueron removidas del alcance (taller de cuestionamiento), diferidas a otro mantenimiento mayor o redireccionadas a mantenimiento rutinario, todo esto con el fin de garantizar la confiabilidad mecánica y operación de las plantas. Este listado esta priorizado bajo los criterios de Factor de riesgo (Factor J) – Valoración RAM (metodologías trasferidas por Shell Global Solution).
De manera general se puede encontrar tres tipos de alcances durante el ciclo de un mantenimiento mayor. El que se denomina alcance conocido, asociado al alcance precisado y congelado, también llamado original; el alcance de previsión, el cual es una estimación probable de su ocurrencia y de sus cantidades (podría o no materializarse o ser en una cantidad mayor o menor del estimado); y finalmente el alcance emergente que puede surgir antes de la ejecución, pero que surge en mayor medida durante la ejecución una vez abiertos e inspeccionados los equipos intervenidos.
El impacto de los alcances de previsión y en especial el emergente, son considerables en términos del riesgo de mayor duración, costo y por tanto la afectación del mantenimiento integral. Pero, de otra parte, es probable que este alcance emergente sea indispensable para garantizar la integridad, confiabilidad y finalmente la disponibilidad del activo, por tanto, cada caso y cada alcance emergente debe ser evaluado y cuestionado bajo las metodologías establecidas para este fin y así tomar la decisión óptima para cada caso.
Duración de una parada de planta
La duración de una parada de planta está supeditada a su alcance, al proceso de planificación y a la optimización de la programación. La principal salida de esta fase del proceso es el programa detallado de trabajo y la(s) ruta(s) critica(s) derivadas de la programación de actividades, entendiéndose por ruta critica el camino o el conjunto de actividades con mayor duración del mantenimiento y por tanto con una holgura cero. Así pues, estas rutas criticas establecen la duración nominal del mantenimiento mayor.
Es importante reconocer que existen múltiples métodos para gestionar el cronograma y su duración, como por ejemplo el método CPM (Critical Path Method), anteriormente descrito; el método PERT (Program Evaluation and Review Techniques) Técnica de Revisión y Evaluación de Programas; el de Cadena Critica, entre otros.
La principal diferencia entre PERT y CPM radica en que el diagrama de PERT se utiliza, generalmente, al necesitarse determinar el tiempo necesario para la finalización de un proyecto, en contraste con el CPM que se utiliza en proyectos con características predecibles. En otras palabras, los diagramas de PERT son un método para planificar y gestionar el tiempo, mientras que el CPM se encamina más para controlar costos y tiempo [5].
El programa detallado de trabajo vincula una secuencia lógica con unas duraciones y recursos necesarios, como también la interrelación entre ellos. La gestión del cronograma es realizada a través de aplicativos informáticos especializados como Primavera P6, Microsoft Project, ente otros.
Es importante comprender que la duración es sensible a los cambios de alcance y esto mismo deriva en posibles impactos en los costos del mantenimiento mayor. La gestión de la duración del mantenimiento mayor no solo obedece al monitoreo y control del cronograma, sino más bien a la integración y la relación entre el alcance, duración y costo (triple restricción clásica).
Costos de una parada de planta
Si hay un factor relevante en el desempeño de una parada de planta se puede resumir en el costo de esta. Esta afirmación se fundamenta en que cualquier otra de las restricciones contempladas (alcance y/o duración), dan como resultado una desviación sobre el costo del mantenimiento.
El proceso de costeo de una parada de planta se inicia en fases tempranas del mismo ya que debe surtir diferentes etapas y momentos de acuerdo con el plan de hitos establecido, por ejemplo, las compras de muy largo plazo, la solitud del presupuesto plurianual, etc.
La gestión de costos es un proceso gradual que considera una progresión, especialmente en su precisión asociada, la cual en la medida que avanza el proceso de mantenimiento mayor, ofrece mayor certeza y detalle para realizar las estimaciones respectivas. Un ejemplo de esto es que para la fase de largo plazo el presupuesto tiene una precisión de +/- 50%, en la de planificación detallada del +/- 30% y para la ejecución está en el orden del +/-10%.
Teniendo en cuanta esto, dentro del proceso de mantenimiento mayor se siguen las diferentes etapas para gestionar los costos: planificar, estimar, determinar presupuesto, controlar costos, nótese que son los mismos procesos sugeridos por la guía del PMBOK.
Durante la ejecución del mantenimiento mayor, los costos se gestionan bajo los parámetros del monitoreo y control, haciendo uso de herramientas como la línea base de costos, el valor ganado, análisis de tendencias, de variación, etc.
Como fue tratado en el apartado de alcance, la influencia de este sobre los costos es preponderante, y su gestión resulta prioritaria para mantener el presupuesto alineado con las metas y objetivos especificados en las premisas. Por tanto, recordando que el presupuesto debe responder por el alcance conocido, el de previsión y el emergente y ya que estos tipos de alcance tiene momentos del tiempo particulares, resulta ser un factor para considerar en la estimación y presupuestación de los costos del mantenimiento (variación de la precisión en función de las fases del mantenimiento mayor).
En resumen y utilizando las expresiones acuñadas en la gestión del riesgo, aparecen de manera general dos grupos de alcances para desarrollar la estimación de costos, los conocidos-desconocidos: incluyen el alcance conocido y los trabajos emergentes previos a la ejecución y los desconocidos-desconocidos: los cueles incluyen el trabajo emergente identificado durante la ejecución y producto de la inspección detallada de los equipos y que corresponde a trabajos que no pudiesen ser previstos hasta no abrir e inspeccionar.
Planificación de una parada de planta
Dentro de las fases del proceso de mantenimiento mayor (parada de planta), indudablemente el corazón de este se halla en la planificación, entendida esta, bajo el contexto del mantenimiento mayor, como las actividades de planeación necesarias para asegurar la ejecución del mantenimiento, e incluye entre otros, la planeación detallada de la ejecución, la logística, el plan de contratación y compras, etc.
Los principales hitos que se deben desarrollar en esta fase son: elaborar y consolidar programas y paquetes de trabajo; realizar talleres de cuestionamiento de ruta crítica; definir estrategia de ejecución; planear ordenes de trabajo; compras y contratos; revisión de alistamiento; entre otros.
La entrada principal para esta fase del mantenimiento mayor es el alcance congelado y su principal salida es el taller de revisión del alistamiento. El entregable principal son los paquetes de trabajo, y el programa detallado de trabajo.
Para el análisis y diagnóstico de este artículo, se tendrá como unidad de gestión comparable los paquetes de trabajo y su efecto sobre las premisas del mantenimiento mayor: alcance, duración y costo.
Un paquete de trabajo es un conjunto de entregables producto de la planificación, el cual incorpora todo lo necesario para ejecutar la acción de mantenimiento. Incluye desde la gestión a través del CMMS de la organización de las ordenes de mantenimiento, gestión de materiales y repuestos, planos, referencias técnicas, controles de calidad, procedimientos específicos, planes de izaje etc.
En la planificación hay dos factores relevantes que se deben destacar, el primero asociado a estimaciones (personas, equipos, materiales, herramientas, duración de actividades, etc.) y el segundo asociado a la programación y a dar la secuencia lógica de las actividades y la optimización de los recursos estimados (histogramas).
Para efectos de estimaciones, se incorporan buenas prácticas de la industria a nivel internacional como el uso de normas labor (estudios de actividades y sus duraciones y recursos medidos en diferentes organizaciones a nivel mundial); el juicio de expertos; históricos de mantenimiento. Por otra parte, para la gestión del cronograma, se realiza la integración de las estimaciones y su secuencia lógica en el cronograma y se realizan talleres de optimización del alcance donde se identifican, gestionan y optimizan las actividades y su secuencia, los recursos (nivelaciones) arrojando la duración final esperada.
Teniendo en cuanta lo anterior, se pone de manifiesto la relevancia de esta fase y su impacto sobre la triple restricción original tomada como referencia para este artículo.
Marco contextual de una parada de planta en la organización
En la actualidad, la gestión de un mantenimiento mayor (parada de planta) obedece a varios esfuerzos relativamente aislados ya que de acuerdo con la estructura orgánica y la naturaleza del proceso (frecuencia), la asignación de recursos para su gestión (en algunos casos de más de 24 meses previos a la ejecución), requiere que se asignen Lideres de Parada (Gerentes de Proyecto), Planeadores, etc. a múltiples y simultáneos eventos. Igualmente, si bien el proceso está claramente establecido, maduro y en realimentación de mejora continua, se observan adaptaciones no convenientes como el uso de plantillas y formatos diferentes, el uso de repositorios documentales diversos, rigurosidad y competencia en el desarrollo de los talleres que soportan el proceso (cuestionamiento del alcance, optimización del alcance, alistamiento, etc.), etc.
Es claro que estas variaciones podrían obedecer más a la forma que al fondo, pero finalmente el efecto sobre los resultados podría ser básicamente en optimización. Por otra parte, los hechos particulares descritos, se potencian al ser dos refinerías de características diferentes que aplican el mismo proceso y además con estrategias que obedecen en algunos momentos a condiciones puntuales de mercado o estrategia. Es importante aclarar, que actualmente existe un proceso de alineación estratégica que busca integrar las dos refinerías y transferir las mejores prácticas entre sí y ser adecuadamente gestionadas desde lo operacional, la gestión de activos, y de resultados del negocio.
Actualmente para la planificación de la para de planta, se cuenta con una unidad integral y centralizada de planificación que posee profesionales divididos por especialidades y coordinados a través de un líder de planificación. Esta unidad recibe las solicitudes de planificación, las gestiona bajo los entregables establecidos para las mismas y finalmente entrega unos paquetes de trabajo con todo lo requerido para la ejecución de la parada de planta y un plan detallado de trabajo.
III. Revisión de resultados de la gestión del mantenimiento mayor (parada de planta) en eventos de la organización y de referenciamiento
Durante el año 2021 se ejecutaron varias paradas de planta a diversas unidades de proceso de la refinería, de los cuales se seleccionó dos eventos particulares que se consideran dentro del alcance de este artículo.
A estos dos eventos se les realizó un análisis y diagnóstico de los resultados obtenidos (comparativamente con las premisas) [6], y, además, a través de referenciamiento, principalmente con los estudios internacionales sobre confiabilidad y mantenimiento (RAM) de Solomon Inc. [4, 7, 8, 9, 10, 11].
Los eventos considerados corresponden a unidades de proceso principales, las cuales se interviene por bloques operacionales relacionados, los cuales están conformados por un total de 5 plantas intervenidas. Estos mantenimientos cumplieron el proceso completo de las 6 fases en los tiempos establecidos y cumpliendo los hitos definidos para cada fase.
Premisas de la parada de planta
Para los eventos constituyentes de este artículo, fueron establecidas unas premisas, las cuales surtieron el proceso de validación por la línea organizacional responsable. Las premisas integraron y alinearon el negocio, la estrategia y los factores particulares de los eventos.
Así pues, se extractan de estas premisas las referentes a las metas del alcance, la duración y el costo de los mantenimientos mayores.
Los valores referenciados en las premisas como desviación permisible y valores de referenciamiento se muestran en la tabla 1.

Cursos recomendados




%252FImagen%252FRAMPREDYC-1730060420837.webp%3Falt%3Dmedia%26token%3D2634a7f0-988e-4022-b91f-382503e6e9db&w=3840&q=75)



Resultados de los eventos de parada de planta 2021
Los resultados analizados en este artículo se centran en las desviaciones frente a las premisas establecidas para el alcance, la duración y el costo de los mantenimientos mayores.

Claramente se observa una desviación en el alcance, la duración y el costo de los eventos. El análisis y propuesta serán desarrollados a continuación de manera independiente para cada factor y finalmente se realizará la integración de las diferentes causalidades y efectos encontrados y la propuesta de optimización.
Mediante el uso de listas de verificación de cumplimiento para cada una de las áreas de gestión del mantenimiento mayor, se realizó una valoración y ponderación de dicho cumplimiento siendo 5 el máximo resultado posible (100% de cumplimiento) y 1 el mínimo resultado posible (0% de cumplimiento). Igualmente se estableció una valoración cualitativa como se describe a continuación.



De acuerdo con los resultados presentados en la figura 3, se establecen las áreas de gestión del mantenimiento mayor con un menor desempeño la definición & optimización del alcance; el proceso de planificación; Presupuesto, estimación & control de costos y en menor medida la gestión de la calidad y la gestión de riesgos.

Se infiere que el costo representa el mayor impacto y su relación con la definición del alcance, la gestión de la duración representa una oportunidad de optimización.
Ahora bien, los resultados analizados muestran que el proceso de planificación tiene un desempeño con cumplimiento medio y por tanto requiere un análisis más detallado.
El modelo de planificación actualmente empleado utiliza tres esquemas de planificación: cien por ciento la organización; cien por ciento aliados y finalmente mixtas. Este análisis se realizará bajo el criterio de una planificación 100% de la organización.
Si bien existen unos modelos generales para la elaboración, la completitud y calidad de los paquetes de trabajo, se ha identifico variaciones considerables entre las planificaciones y entre los eventos, además, también existen variaciones dependiendo del esquema de planificación.

La tabla 3 representa que los esquemas de planificación inciden en la calidad de los entregables, también se infiere que las principales brechas del paquete de trabajo se encuentran en las estimaciones y la información técnica mínima requerida. En resume, la calidad de cumplimiento de los paquetes de trabajo está en promedio 90% bajo los tres esquemas.
En la tabla 4 se presenta una comparación histórica entre los resultados de los mantenimientos mayores en los últimos años, relacionando las premisas comprometidas para estas y los resultados reales obtenidos.
En este sentido, se observa una desviación importante en los resultados comprometidos en las premisas de cada evento, y su bajo nivel de cumplimiento. Los datos con los que se cuenta demuestran principalmente desviaciones asociadas a trabajos emergentes y contingentes que afectan drásticamente los valores de alcance, duración y costo. Esto nos lleva a considerar la necesidad de revisar la calidad de cumplimiento de la planificación, como uno de los factores influyentes en las desviaciones a las premisas comprometidas.


Desde el punto de vista de la calidad de la planificación, específicamente lo asociado a mayor alcance, se debe analizar el contexto bajo las siguientes condiciones. La primera, asociada a la planificación, es determinar la calidad de esta, lo cual incluye básicamente constatar si lo planeado fue suficiente para cumplir el alcance o hay alguna desviación que haya generado la necesidad de realizar más trabajo no planeado.
Como segunda medida, es probable que la desviación de alcance sea consecuencia del estado natural de deterior del equipo o que solo fue posible evidenciarlo una vez abierto e inspeccionado. Este factor se sale del análisis que se pretende, ya que el mismo no pudiese determinarse previamente. Sin embargo, presenta un alto impacto sobre los costos y la duración del mantenimiento.
Por tanto, se requiere establecer un indicador de cumplimiento de los paquetes de trabajo planificados. Este indicador debe permitir visualizar las diferentes condiciones adoptadas desde el congelamiento del alcance y de la planificación en sí mismas. Esta es la principal variable de comparación con el criterio de éxito, que se define como el cumplimiento de las premisas comprometidas.
Continuando con el diagnostico, se presenta una comparación general de cumplimento de las fases del proceso para eventos históricos ejecutados que permiten visualizar los puntos focales de atención para obtener los resultados positivos que busca la organización.
De las fases de un mantenimiento mayor, las desviaciones más representativas se encuentran fundamentalmente en la de planificación y de allí se deriva específicamente el impacto de los paquetes de trabajo como unidades de comparación de éxito. Es decir, como las unidades mínimas de trabajo completadas y planificadas y que son la base para las estimaciones de duración y costo. Así pues, se establece dentro de este diagnóstico una relación entre la calidad de la planificación (paquetes de trabajo), su implementación y uso.
En resumen, para una parada de planta, la cual muestra desviaciones al cumplimiento de sus premisas, y enfocándonos solamente en el efecto de la planificación sobre ellas, se correlaciona inicialmente que la calidad de la planificación (uso de estándares, coherencia y uniformidad), podrían incrementar la probabilidad de éxito y cumplimento de las premisas comprometidas en el evento. De esto, se deriva la promesa de valor esperada, en una estandarización que promueva su cumplimiento y uso.
IV. Propuesta de optimización
Si bien la implementación de modelos de optimización surte diferentes aspectos asociados a la estrategia organizacional y la manera de abordar las necesidades propias de su gestión de proyectos, existen modelos propuestos que, de manera general, describen la manera como se adoptan desde la evolución de la madurez organizacional y la gobernanza de esta.
La propuesta derivada de este análisis subyace en un enfoque que, en primera instancia, está asociado al modelo organizacional (la forma de hacer las cosas) y el siguiente enfoque es la incorporación y/o mejora de técnicas y herramientas propias para gestionar los diferentes aspectos de alcance, duración y costo.
Enfoque 1: del modelo organizacional – Implementación de una Oficina de Proyectos PMO
La planificación en una parada de planta ejerce un gran impacto en los resultados de esta. En este sentido, ordenar, organizar, estandarizar este proceso, es una alternativa de mejora continua que ofrece ventajas claras en dicha optimización.
En esta primera parte de la propuesta de optimización, se pretende establecer los posibles lineamientos y beneficios que podría generar la implementación de una Project Management Office – PMO de Apoyo para la gestión del mantenimiento mayor (Parada de Planta), en función de la literatura y definiciones consultadas.
De acuerdo con el PMBOK en su sexta edición, una Project Management Office – PMO es una estructura de gestión que estandariza los procesos de gobernanza relacionados con el proyecto y facilita el intercambio de recursos, metodologías, herramientas y técnicas [1].
En este sentido, y haciendo un paralelo a la estructura actual de gestión de un mantenimiento mayor en la organización, se tienen recursos diseminados, metodologías combinadas y uso indiscriminado de herramientas y técnicas en función de las necesidades de cada líder de parada (gerente de proyecto) y por tanto surge la oportunidad de integrar, a través de una PMO de Apoyo, las ventajas inherentes a esta estructura con vista a incrementar la eficiencia y eficacia de los resultados de los mantenimientos mayores y por ende en los resultados sobre el negocio de refinación.
Si bien determinar el impacto del valor generado por una PMO representa un desafío importante en sí mismo, es claro que desde la perspectiva del objetivo de este artículo se podrá obtener una primera aproximación de este impacto en términos del uso de los beneficios de esta estructura mas no de la eficiencia y eficacia en los resultados de la gestión de un mantenimiento mayor, este complemento será desarrollado en posteriores estudios utilizando mediciones significativas de la relación directa de las variables del proceso sobre los resultados [12].
Dentro de este artículo, se permeará la visión del PMI en su modelo, sin desconocer la existencia de otros modelos importantes [13,14], por tanto, se adopta que existen varios tipos de PMO y que cada una varía en función del grado de control e influencia que ejerce sobre los proyectos: de apoyo, de control y directiva.
Siguiendo la revisión de la literatura realizada, por su definición, por su alcance y beneficios, para el caso de los mantenimientos mayores, una PMO de Apoyo cubrirá de manera general los aspectos de mejora identificados previamente.
Una PMO de Apoyo, de acuerdo con la definición del PMBOK, es la que desempeña un rol consultivo para los proyectos (mantenimientos mayores), suministrando plantillas, mejores prácticas, capacitación, acceso a la información y lecciones aprendidas de otros proyectos.
Amendola plantea la gestión de paradas de planta mediante una PMO, pero complementado la gestión de la parada de planta desde el modelo: Risk-oriented Project life-cycle [15], el cual difiere en algunos aspectos al modelo de la organización estudiada. sin embargo, coincide en la búsqueda de nuevas formas de dirección y gestión de las paradas de plata con el objetivo final de recuperar la integridad, la confiabilidad y disponibilidad de los activos.
Por otro lado, es importante reconocer que la implementación y uso de una PMO de Apoyo en sí misma no garantiza la obtención de los beneficios esperados, ya que también los resultados estarán enmarcados en cómo sobre la organización influye su cultura organizacional, su madurez, la gobernanza, entre otros aspectos limitantes [16, 17].
El otro aspecto para considerar es la medición de variables de desempeño que contrasten la generación de valor de la implementación de una PMO en la gestión de mantenimiento mayor. Estas mediciones en diferentes referencias consultadas establecen métodos cualitativos y cuantitativos, con resultados disimiles, sin embargo, aportan una contribución a los aspectos particulares que debe desarrollar cada organización en sus métricas y así poder referenciarse y determinar los beneficios obtenidos.
Enfoque 2: Incorporación de buenas practicas
Optimización del Alcance en una parada de planta
La definición del alcance es la entrada determinante para los demás factores acá contemplados y por tanto requiere una especial atención.
Dentro de las buenas prácticas de la industria y considerándola como una alternativa complementaria a los talleres de cuestionamiento del alcance que se desarrollan habitualmente en el proceso, se propone el uso de la optimización del alcance basado en riesgo – Risk based work scope optimization y sus siglas en ingles RBWS [18, 19, 20]. Igualmente, buscando mayor eficiencia y efectividad en la definición de los alcances, se propone restructurar la estrategia de RBI – Risk Based Inspection [21, 22]. que se emplea actualmente.
Para la optimización del alcance basado en riesgo – RBWS, se debe entender su alcance y limitaciones. La metodología RBWS proporciona una base rigurosa para justificar la inclusión o el rechazo de elementos de la lista de trabajo (alcance propuesto), si estos no mitigan los riesgos o no satisfacen los criterios de costo/beneficio que se establecen para la evaluación, los cuales son definidos por la organización (apetito al riesgo).
La aplicación de la toma de decisiones basada en el riesgo – RBWS, elimina discrecionalmente las tareas del mantenimiento mayor y retiene tareas que mitigan los riesgos inaceptables o que proporcionarían un beneficio desde un punto de vista financiero. El resultado de una evaluación de RBWS genera un alcance de trabajo más estricto que conduce a una reducción significativa en la duración y los costos del mantenimiento mayor. La aplicación de la metodología aplica para todos los tipos de equipos principales (equipos estáticos, tuberías, equipos rotativos, instrumentos, electricidad, calentadores, sistemas de TEA, etc.) programados para un mantenimiento mayor.
La metodología RBWS, cuando se usa con equipos estáticos, utiliza datos de inspección basada en riesgos (RBI), cuando es necesario, para validar o rechazar tareas del mantenimiento mayor que están incluidas en la lista de trabajo. Las evaluaciones de RBI se enfocan en la integridad del equipo y la pérdida de contención, mientras que la metodología RBWS complementa estas evaluaciones con la consideración de fallas y consecuencias en los componentes internos de los recipientes a presión que pueden causar una parada no programada y un impacto en la integridad y confiabilidad del equipo.
Alineado con lo anterior, en cuanto a la restructuración de la estrategia en la aplicación de la practica recomendada de API 580, inspección basada en riesgo – RBI, es importante definir de manera general lo que esta metodología considera y aporta al proceso.
La metodología Inspección Basada en Riesgo está fundamentada en las practicas recomendadas API RP-580 y API PUB-581 y su premisa es caracterizar el riesgo asociado a los equipos estáticos (intercambiadores de calor, recipientes a presión, tuberías, etc.) bajo un lazo común de corrosión (mecanismos de daño y modos de falla), usando el análisis del comportamiento histórico de: las fallas, modos de degradación o deterioro, características de diseño, condiciones de operación, mantenimiento, inspección y políticas organizacionales, considerando simultáneamente la calidad y efectividad de la inspección realizada, así como las consecuencias asociadas a las fallas potenciales [21, 22]..
El objetivo fundamental del RBI es definir planes de inspección basados en la caracterización probabilística del deterioro y el modelamiento probabilístico de la consecuencia de una falla (caracterización del riesgo) [21, 22].
Existe una “Metodología RBI mejorada para la Integridad Mecánica de Activos” se basa en la integración de las metodologías de Inspección Basada en Riesgos, “Valoración del Riesgo por Corrosión” (VRC)”, Integridad Mecánica (IM) y modelamiento probabilístico del deterioro, lo cual permite ampliar el espectro de cobertura de mecanismos de deterioro considerados en el enfoque clásico del RBI [23, 24].
El mayor impacto que puede ofrecer el RBI es el asociado a los trabajos emergentes, en especial los generados durante la apertura e inspección de equipos. Si se considera el alcance emergente bajo estas características, se podría dividir este en alcance previsible y alcance imprevisible, ambas circunstancias asociadas a la predictibilidad que a su vez depende de la frecuencia y alcance de las inspecciones, de las violaciones a las ventanas operativas (API RP584), al estado de las corridas (ejecución de la corrida de desempeño), etc. Finalmente, realizando el seguimiento detallado de estas, se podrá tener mayor control sobre los mecanismos de daño, los modos de falla y la probabilidad de falla asociados y por tanto optimizar alcances a través de la anticipación.
Optimización de la duración de una parada de planta
En cuanto a la duración, la propuesta se enfoca en adoptar complementariamente a los métodos tradicionales de CPM/PERT, el método de la cadena critica (CCPM), pero con el valor añadido del análisis de riesgo simultaneo [25, 26, 27].
La cadena crítica (CCPM), está basada en la teoría de las restricciones que tiene por objetivo identificar la causa principal de los problemas (cuellos de botella) y poder ser corregidos y así optimizar la manera de gestionar las duraciones, estableciendo de manifiesto lo más eficaz en la ejecución a la vez que se minimiza el uso de recursos disponibles.
Por tanto, el método CCPM puede definir la duración mínima en que el mantenimiento puede finalizar e impone las restricciones que logran no perder la alineación con esa secuencia de actividades de menor duración. De esta forma, se evitan los obstáculos que, con mayor frecuencia, pueden conducir un mantenimiento al fracaso o al bajo desempeño.
La metodología se compone de cinco pasos [25]:
- Identificar las restricciones del sistema.
- Diferenciar las restricciones físicas de las organizacionales para, por ejemplo, diferenciar entre las limitaciones de recursos materiales y entre las reglas empresariales.
- Superar las restricciones del sistema: Los esfuerzos deben centrarse en aquellas tareas que formen parte de la cadena crítica, que son las que determinarán la finalización del proyecto.
- Subordinar todas las demás tareas a la decisión tomada en la cadena crítica.
- Si se rompe una restricción, no volver a la rutina y regresar al primer paso.
Optimización del costo de una parada de planta
Asociado al costo, las buenas prácticas complementarias sugeridas pasan por dos acciones. La primera relacionada con las estimaciones y la segunda asociada al control del presupuesto [28, 29].
Complementario a los métodos y técnicas de estimaciones actualmente utilizados, se sugiere el uso de prácticas recomendadas como las de la AACE (American Association of Cost Engineering), tales como AACE RP112R-20, “Cost Estimate Classification System – As Applied in Maintenance Turnarounds for the Process”. Las estimaciones deben ser debidamente soportadas con su respectivo BOE (Basis of Estimate) que no es otra cosa que unas premisas y detalles de la manera como se realizó la estimación. Igualmente, importante es tener estandarizada la EDT, tanto de programación, como riesgos y obviamente costos.
De manera general una buena estrategia de estimación de costos debe incluir la mejora en los procesos de estimación (procesos conocidos y trazables); la competencia del personal estimador y el uso de tecnología que permite gestionar las estimaciones más eficientemente y lograr una línea base de costos confiable y estructurada.
Por otra parte, lo relacionado al control de costos de la parada de planta, surge como herramienta el uso del valor ganado – “cantidad de trabajo ejecutado a la fecha, expresado en términos del presupuesto autorizado para ese trabajo” [1]. Usar el valor ganado involucra tanto las áreas de planificación, de programación, costos y dirección. En resume es una técnica que permite cierto control y seguimiento a la interrelación del cronograma y el presupuesto y proporciona información muy útil para la toma oportuna de decisiones. No obstante, también hay que reconocer las limitaciones (meramente operativas) de esta técnica y los niveles de confiabilidad de la información con la cual se constituye.
Es evidente, que lo descrito en los párrafos anteriores corresponde a la preparación previa de la parada de planta y si bien el control de costos se materializa principalmente en la ejecución, es vital comprender que dentro de los resultados que se pretende impactar para optimizar los costos obedece a la gestión de su principal enemigo: el trabajo emergente. En ese orden de ideas, se relacionan estrechamente las tareas descritas en la optimización del alcance, relacionado al RBI y al control de ventanas operativas, como también a la anticipación de mecanismos de daño y modos de falla.
V. Conclusión
La gestión de un mantenimiento mayor (parada de planta) puede aceptarse como un proyecto y por tanto puede hacer uso de las diferentes metodologías, métodos, técnicas, herramientas, buenas prácticas que dicha gestión ofrece bajo los diferentes aspectos considerados. Así pues, entendiendo el impacto de un mantenimiento mayor sobre los resultados del negocio de refinación, se hace evidente que la adecuada gestión de este puede incidir positivamente en aspectos como: alcance, duración, costo, calidad, riesgos, seguridad, etc.
La mejora continua y la adopción de diversas metodologías, métodos, técnicas, herramientas, buenas prácticas, etc. para obtener los resultados esperados en un mantenimiento mayor, permite inferir que reconociendo las falencias actuales del proceso adoptado y desarrollado en la organización, una gestión del mantenimiento a través de una PMO de Apoyo, podría brindar los beneficios, al menos desde la perspectiva de la literatura consultada: integrar y apoyar a gestión a través del suministro de buenas prácticas, capacitación, acceso a la información, plantillas, lecciones aprendidas, etc.
Sin embargo, también es claro que la dificultad inherente a la medición de beneficios entregados por una PMO de apoyo limita los resultados y hace necesario establecer un marco particular para el análisis dependiendo de cada organización y sus expectativas.
La propuesta de optimización sugiere dos enfoques integrados, por una parte, está la estructura o modelo organizacional sugerido (PMO de apoyo) y, por otra parte, la incorporación y/o mejoras de buenas prácticas, técnicas, métodos y herramientas.
Un factor común en el desarrollo de los enfoques propuestos es la gestión del riesgo, la cual está presente en todas las propuestas desarrolladas y ofrece un complemento en la identificación y evaluación de los riesgos para permitir que estos se entiendan claramente y se gestionen de manera efectiva. El aspecto vinculante para la identificación/evaluación de riesgos con su gestión es la comprensión detallada de cada riesgo. Estas técnicas de identificación, sin embargo, tienden a producir una lista no estructurada de riesgos que frecuentemente no ayuda a determinar dónde centrar la atención de la gestión de riesgos.
De alguna manera, la evaluación cualitativa de riesgos puede ayudar a priorizar sistemáticamente los riesgos identificados a raves de estimar la probabilidad y los impactos, exponiendo así los riesgos más significativos; pero esto trata los riesgos de uno en uno y no como un conjunto interactivo e interrelacionado y por tanto no considera los posibles patrones de exposición al riesgo subyacentes, por lo que tampoco proporciona una comprensión general del riesgo que enfrenta el mantenimiento en su conjunto. Por ello, el paso significativamente lógico, es mudar y complementar el análisis cuantitativo con las técnicas cuantitativas y asociadas a la visualización de riesgos integrales.
Es posible a través de las buenas prácticas y/o de herramientas particulares, acompañado de una fuerte disciplina, incidir positivamente en el alcance, la duración y el costo de una parada de planta. Las desviaciones que usualmente se describen frente a las premisas y el referenciamiento, obedecen en gran medida a una baja o pobre definición de alcances y/o a trabajo emergente mal gestionado (identificación inoportuna). Evidentemente, la condición antes descrita guarda una fuerte relación con la calidad y oportunidad de gestión de los entregables principales de la planificación: que son los paquetes de trabajo y el programa detallado de trabajo.
Un detalle relevante para considerar es mejorar la capacidad de anticipación a los alcances emergentes, en especial los definidos como desconocidos y que requieren los equipos abiertos e inspeccionados. La manera de gestionar los alcances a través del RBI y siendo muy disciplinados con el cumplimiento de las ventanas operativas específicas de cada planta, ofrece una oportunidad de anticipación a los probables mecanismos de daño o modos de falla inducidos por la operación y que usualmente se evidencian una vez abiertos los equipo pero que podrían diagnosticarse frente a las variaciones identificadas en las violaciones de las ventanas operativas (cambio de variables en operación).
Esto requiere un reporte y seguimiento oportuno para así constituir una extensión de la inspección previa a la parada, conociendo los probables efectos de dichas violaciones operacionales sobre los mecanismos de daño esperados.
En resumen, un marco organizacional favorable y que integre efectivamente los requerimientos, considerando el que y el cómo, apoyado en una fuerte disciplina de cumplimiento del proceso a través de la implantación y uso de buenas prácticas, como las sugeridas en este artículo, podrán tener un alto impacto positivo en los resultados del mantenimiento mayor y del negocio de refinación en general (alineación estratégica).
Para validar estos resultados y los enfoques sugeridos, es necesario realizar investigaciones más profundas y desarrollar técnicas de investigación que modelen el impacto (generación de valor) del uso de una PMO de apoyo para la gestión del mantenimiento mayor, junto con la implementación de las buenas prácticas acá sugeridas y su impacto en los objetivos y metas del mantenimiento mayor: alcance, duración y costo. Ese estudio deberá construirse alrededor de los resultados de los mantenimientos mayores históricos, frente a pilotos propuestos para los desarrollos bajo el nuevo modelo.
Referencias
[1] Project Management Institute. (2017). A guide to the Project Management Body of Knowledge (PMBOK guide) (6th ed.). Project Management Institute.[2] Serie ISO 55000/1/2 Gestión de activos[3] Ecopetrol S.A., RFN-G-5127 Guía gestión de mantenimiento mayor. Ecopetrol S.A. 2019.[4] Solomon Inc. International, “Worldwide fuels refinery performance analysis for operating year 2018”.[5] Lucidchart – Diagrama de PERT: Definición y cómo hacerlo: https://www.lucidchart.com/[6] Ecopetrol S.A. Informes de cierre de paradas de planta 2021, Informe presentado a la junta directiva – Refineria de Cartagena.[7] Solomon Inc. International Study of Plant Reliability and Maintenance Effectiveness Performance Analysis (RAM Study) 2018.[8] Solomon (2017). Achieving World’s Best Refinery Status. [9] IPA. (2011) ‘IPA’s Turnaround Evaluations’ [10] A. Poling, “Reliability and maintenance: the path to world class performance”, Hydrocarbon Processing, Dec 2012.[11] J. Stroup, “What characteristics define the world´s best refineries?”, Hydrocarbon Processing, May 2014.[12] V. Juhani, C. Arndt, J.P. Bergman,J. Hallikas, and J. Kaaja, “Impact of the PMPs roles on project performance”, International Journal of Information Technology Project Management, vol. 9, Issue 4, October-December 2018 [13] J. Valdés. “La PMO ágil: un enfoque súper rápido para crear una PMO efective para su organización = The agile PMO: a super fast approach to create an effective PMO for an organization”. Paper presented at PMI® Global Congress 2008—Latin America, São Paulo, Brazil. Newtown Square, PA: Project Management Institute.[14] T. Le Dinh, T. Ho Van, T. Nomo. “A framework for knowledge management in Project management office”. The Journal of Modern Project Management, January-April 2016.[15] L. Amendola. “Gestion de las paradas de planta mediante Project portafolio management office”[16] E. Too, P. Weaver, “The management of project management: a conceptual framework for project governance”, International Journal of Project Management, 32 (2014) 1382-1394.[17] M. Parchami Jalal, S. Matin Koosha, “Identifying organizational variables affecting project management office characteristics and analyzing their correlations in the Irani project-oriented organizations of the construction industry”, International Journal of Project Management, 33 (2015) 458-466[18] A. Radhakrishnan, “Risk Based Work Selection (RBWS) – An Essential Step for Turnaround Work Scope Optimization”, Inspectioneering, October 2019.[19] A. Radhakrishnan, “Risk Based Work Selection (RBWS) – A Focused Process for Achieving Turnaround”, Inspectioneering, September 2019.[20] A. Radhakrishnan, “Risk Based Work Selection (RBWS) – An Essential Step for Turnaround Work Scope Optimization in Refining”, Becht, December 2016.[21] American Petroleum Institute, “Recommended Practice: Risk Based Inspection – API 580”, API, November 2016.[22] American Petroleum Institute, “Recommended Practice: Risk Based Inspection Methodology – API 581”, API, November 2019.[23] F. Elfeituri, S. Elemnifi, “Optimizing turnaround maintenance performance”, PPCOE 2007, October 2007.[24] R. Vichich, “Turnaround excellence – key success factors”, AIChE 2012, April 2012.[25] E. Goldratt, “Cadena Critica”, Granica 2008.[26] M. Bevilacqua, F. Ciarapica, G. Giacchetta, “Critical chain and risk analysis applied to high-risk industry maintenance: A case study”, International Journal of Project Management 27 (2009) 419-432.[27] O. Zwikael, R. Dutt Pathak, G. Singh, S. Ahmed, “The moderating effect of risk on the relationship between planning and success”, International Journal of Project Management 32 (2014) 435-441.[28] AACE RP112R-20, “Cost Estimate Classification System – As Applied in Maintenance Turnarounds for the Process”, AACE, 2020.[29] G. Lawrence, “Cost Estimating for turnarounds”, Petroleum Technology Quarterly Q1 2012.[30] R. Gort, Huw Morgan, (2003). Guía para el Gerenciamiento de Paradas de Planta. Shell Global Solutions International B.V., La Haya.[31] Pockarel, S & Jiao, J.R. (2008) ‘Turnaround maintenance management in a processing industry: A case study’, Journal of Quality in Maintenance Engineering, vol. 14, no. 2, pp. 109-122.Autor
Jaime Andrés Trujillo Duque.
Ingeniero de Materiales, Universidad del Valle; Especialista en Gerencia de Mantenimiento, Universidad Tecnológica de Bolívar; En curso Maestría en Gerencia de Proyectos, Universidad Tecnológica de Bolívar.
jatrujillo@utb.edu.co – ORCID: 0000-0003-3523-423X.
Planeador y Programador Integral de Mantenimiento, Departamento de Paradas de Planta, Refinería de Cartagena – Ecopetrol S.A., Colombia.
jaime.trujillodu@ecopetrol.com.co.
Con 18 años de experiencia en el sector Oil & Gas en proyectos de construcción y en mantenimiento de plantas y equipos mayores, actualmente Líder de Mantenimiento de Calderas y TEA en la Refinería de Cartagena.
Dinos qué te ha parecido el artículo
Artículos recomendados
Aplicación del estándar API 650 a un activo físico instalado en la industria petroquímica: Caso de estudio basado en el Apéndice “F”

Curso SAP

La Ingeniería Industrial - ¡Conócela!

Investigación de Fallas, Reparación y Remedio Operativo Mínimo. Bomba de Alto Rendimiento

Publica tu artículo en la revista #1 de Mantenimiento Industrial
Publicar un artículo en la revista es gratis, no tiene costo.
Solo debes asegurarte que no sea un artículo comercial.
¿Qué esperas?
O envía tu artículo directo: articulos@predictiva21.com
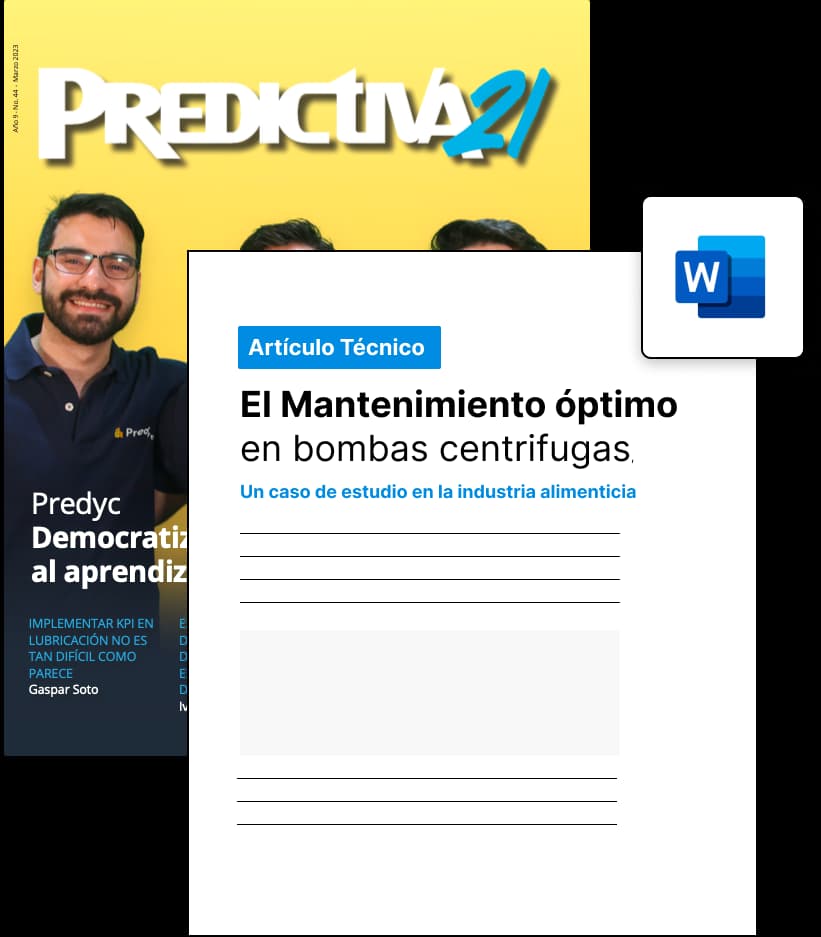
Propuesta de adopción de modelos de optimización de alcance, duración y costo en paradas de planta
Articulo 22 de junio de 2022Proposal for the adoption of scope, duration and cost optimization models in turnaround
Resumen
Las paradas de planta (mantenimiento mayor) en las refinerías de petróleo son actividades de alto impacto para el negocio, su gestión adecuada es relevante para obtener los resultados esperados y por tanto la industria ha adoptado metodologías, métodos, herramientas y buenas prácticas para mejorar su gestión, muchas de estas, provenientes de la gestión de proyectos. En este artículo se proponen algunas buenas prácticas de la industria, en el marco de la gestión de proyectos, para mejorar el desempeño de las paradas de planta (mantenimiento mayor), específicamente los asociados a la gestión de la triple restricción clásica: alcance, duración y costo.
Se realiza una revisión de los resultados históricos de paradas de planta en la organización (premisas vs. resultados finales); como también el referenciamiento internacional con refinerías similares que también participan de estos estudios en el área de la costa del golfo. Se utilizan listas de verificación de cumplimiento para validar el desempeño de las áreas de gestión frente a los resultados del mantenimiento de dos eventos ejecutados en 2021.
Se exploran los factores de éxito de una parada de planta asociados al cumplimiento de las premisas definidas de alcance, duración y costo, identificando como variables incidentes principales para su desempeño, la calidad de la planificación y la materialización de trabajos emergentes como catalizadores del incremento en alcance, duración y costo.
A partir de la data analizada se relacionó el efecto de las desviaciones con la baja gestión en el enfoque organizacional y a la necesidad de formas diferentes de abordarlos, y de allí surge la propuesta de adopción de buenas prácticas tendientes a la optimización. La propuesta presenta dos enfoques, el primero, abordando temática organizacional: creación de una PMO de apoyo; y un segundo enfoque asociado a la incorporación de buenas prácticas y herramientas específicas que mejoren el desempeño, tales como la definición de alcance bajo RBWS, la gestión de duración bajo cadena crítica y la gestión de estimación de costo bajo buenas prácticas de la AACE, entre otras, todas bajo un contexto de gestión del riesgo.
Palabras Clave
Parada de Planta, PMO, Triple Restricción, Gestión del Riesgo, RBWS, CCPM.
Abstract
Plant shutdowns (turnaround) in oil & gas refineries are activities with a high impact for the business, their proper management is relevant to obtain the expected results and therefore the industry has adopted methodologies, methods, tools, and good practices to improve their performance management, many of these, coming from project management. This article proposes some good industry practices, within the framework of project management, to improve the performance of plant shutdowns (major maintenance), specifically those associated with the management of the classic triple constraint: scope, duration, and cost.
A review of the historical results of turnaround in the organization (premises vs. results) is carried out; as well as international benchmarking with similar refineries that also participate in these studies in the Gulf Coast area. Compliance checklists are used to validate the performance of the management areas against the maintenance results of two events executed in 2021.
The success factors of a turnaround associated with compliance with the defined premises of scope, duration and cost are explored, identifying as main incident variables for its performance, the quality of planning and the materialization of emerging works as catalysts for the increase in production. scope, duration, and cost.
From the data analyzed, the effect of the deviations was related to poor management in the organizational approach and the need for different ways to address them, and from there the proposal for the adoption of good practices aimed at optimization arises. The proposal presents two approaches, the first, addressing organizational issues: creation of a support PMO; and a second approach associated with the incorporation of good practices and specific tools that improve performance, such as scope definition under RBWS, duration management under critical chain and cost estimation management under good practices of the AACE, among others. others, all in a risk management context.
Key words
Turnaround, PMO, Triple Constraint; Risk Management, RBWS, CCPM.
I. Introducción
Una parada de planta (mantenimiento mayor) es un evento de impacto superlativo sobre los resultados del negocio de refinación y de manera general sobre la organización y, por tanto, se consideran factores determinantes de este impacto aspectos como: el alcance, la duración, y el costo, ente otros.
Así pues, una gestión adecuada sobre estos aspectos influenciará positivamente los resultados de la organización, desde la disponibilidad operacional, pasando por la confiabilidad de sus activos y finalmente su impacto positivo en la producción y los resultados económicos del negocio. Para efectos de este artículo, se usará de manera intercambiable el termino mantenimiento mayor y parada de planta como equivalentes.
En algunas organizaciones, las paradas de planta son consideradas como un proyecto, desde la perspectiva de su gestión, sin embargo, existen otras corrientes que discrepan de esta definición, no obstante, para efectos de este artículo, se acepta que una parada de planta obedece, de manera general, a la definición de lo que es un proyecto de acuerdo con el Project Manegement Institute (PMI) en su guía PMBOK, en su sexta edición [1].
En este orden de ideas, es importante reconocer que la relación existente entre la gestión de activos industriales y la gestión de proyectos, presentan diversos puntos en común lo que acentúa la posibilidad de hacer uso de algunas de sus metodologías, herramientas, procesos, estándares y buenas prácticas entre ambos.
Por su definición, bajo la norma internacional ISO 55000 – Gestión de Activos – Aspectos generales, principios y terminología: “Un sistema de gestión de activos es un conjunto de elementos de una organización interrelacionados y que interactúan cuya función es establecer la política y los objetivos de la gestión de activos y los procesos necesarios para alcanzar dichos objetivos” [2].
Puntualmente para la organización base de este artículo, la gestión de activos industriales tiene como propósito incidir en el ciclo de vida del activo, primando la perspectiva de la confiabilidad operacional, la administración rentable y gerenciamiento del riesgo mediante la aplicación de las mejores prácticas integradas existentes, garantizando la integridad de las personas, el medio ambiente, la infraestructura, en armonía con el entorno y la continuidad de las operaciones, bajo criterios de eficiencia, eficacia y efectividad [3].
Para el modelo de la organización el ciclo de vida del activo se desarrolla a través de diferentes fases (5): a) Incorporación, b) Operación de Mantenimiento, c) Operación Estructurada, d) Optimización del Activo y e) Desincorporación. Dentro de la fase de operación de mantenimiento (rutinario y mayor), se encuentra circunscrito el proceso de mantenimiento mayor también conocido como parada de planta, y que es objetivo en este artículo.
Por otra parte, la gestión de proyectos puede entenderse como un conjunto de metodologías, herramientas, estándares, entre otros, con el propósito de crear un producto, servicio, o resultado único [1]. Bajo este contexto es importante comprender que todo proyecto o la gestión de este viene limitado por restricciones inherentes como suelen ser, el alcance, la duración, el costo, entre otros, lo cual es denominado bajo el PMBOK como la triple restricción.
Es importante aclarar que existen múltiples interpretaciones asociadas a este concepto que consideran no solo estos tres factores, sino que incluye otros como: calidad, riesgos, interesados, etc., y tiende a denominarse múltiple restricción. Si bien la múltiple restricción es un concepto ampliado, para los efectos de este artículo, el enfoque será sobre la triple restricción original.
Ahora bien, aceptando que una parada de planta posee las características de un proyecto, se puede evidenciar que la gestión de estos tipos de mantenimiento se enmarca en modelos que claramente difieren de una organización a otra debido fundamentalmente a su naturaleza, a su frecuencia o a su alcance, es decir, la manera como se gestiona una parada de planta obedece fundamentalmente a las necesidades y requerimientos propios de cada organización.
No obstante, esas diferencias, la mayoría de estos modelos converge en aspectos tales como: un inicio, la planificación, la ejecución, monitoreo y control, y el cierre. El modelo por considerar en este artículo [3] está orientado en gran medida en las áreas de gestión (conocimiento) manifestadas por el PMI en su guía PMBOK.
Las mejores prácticas de la industria y los datos de referenciamiento consultados, plantean cifras inquietantes que deben ser gestionados por su impacto negativo en los resultados de las paradas de planta: desviaciones en el alcance, debido a incremento de este, con valores por encima de un 15% al planeado; en duración, debido a extensión del mantenimiento, del orden del 10% al planeado; y en costo por encima del 25%, debido a las desviaciones precedentes [4].
Estas cifras generales de la industria muestran como un factor potencial de mejora disminuir estas desviaciones a través de diversos métodos. En este sentido, este articulo presenta un análisis y diagnóstico de los resultados obtenidos en un conjunto de paradas de planta como también datos de referenciamiento de la industria, construido alrededor de resultados históricos recientes.
Para este análisis y diagnostico partimos de la premisa de optimizar a través del uso de metodologías conocidas y probadas bajo los estrictos estándares internacionales que rigen el que hacer de la organización, considerando como factor de éxito de la parada de planta, el cumplimiento de los objetivos planificados en alcance, duración y costo.
Así pues, a través de proponer métodos que integren la gestión de la parada de planta, se pretende identificar e incidir positivamente en los tres aspectos focales de alcance, duración y costo de esta, a través de la potenciación de los factores internos de la organización. Para esto se propone un referenciamiento interno y externo del proceso de parada de planta (mantenimiento mayor), con énfasis en su fase de planificación y su impacto final en el resultado y cumplimiento de las premisas de este.
II. Contexto del proceso de mantenimiento mayor (parada de planta) en la organización
A continuación, se desarrolla una descripción del proceso de mantenimiento mayor (parada de planta) en la organización, considerando sus objetivos y metas (premisas); siguiendo por un entendimiento de la manera actual en que se desarrollan los aspectos del alcance, la duración y el costo de cada parada de planta; como también, un repaso sobre la manera en que se aborda la planificación de las paradas de planta y finalmente describiendo el contexto organizacional actual.
Proceso de mantenimiento mayor (parada de planta)
El proceso de mantenimiento mayor (parada de planta) considerado en este artículo es el adoptado por la organización [3], el cual está en vigencia desde hace más de 25 años y fue un modelo transferido por buenas prácticas y convenios realizados con referentes internacionales del negocio oil & gas.
El objetivo del proceso es: “Llevar a cabo la reparación programada de una unidad productiva para mejorar la confiabilidad y disponibilidad de los equipos que la compone en su ciclo de corrida, cumpliendo eficiencia, eficacia y efectividad, asegurando la integridad de las personas, el medio ambiente, la infraestructura, la armonía con el entorno” [3].
Si bien el objetivo de un mantenimiento mayor (parada de planta) se describe claramente en el párrafo anterior, es muy importante comprender algunas de las razones principales por las que se incurre en estas actividades de mantenimiento.
En principio se debe considerar que un mantenimiento mayor (parada de planta) corresponde a una seria de actividades que de no estar la planta fuera de servicio, no se podrían ejecutar y habitualmente corresponden a actividades como cambio de partes, piezas, repuestos o de componentes que superan su ciclo de vida, que han sufrido obsolescencia o mal funcionamiento, para inspeccionar los equipos, también para gestionar cambios en las unidades a través de proyectos de mejora, modificación y/o corrección de fallas, sin olvidar el cumplimiento de regulaciones y contratos de licenciamiento, etc.
Considerando lo anterior, se puede entender bajo el criterio de definición que “un mantenimiento mayor es el que se hace a la unidad operativa (sistema de activos industriales), cuando esta se encuentra fuera de servicio, después de haber cumplido su ciclo de corrida definida a partir de las metodologías de confiabilidad (RCM, RBI, IPF, entre otras).
Adicionalmente, este mantenimiento debe cumplir las fechas establecidas en el plan de hitos de los mantenimientos mayores, y cumplir cada una de las fases descritas en este proceso: Planear actividades de largo plazo, Precisar el alcance del mantenimiento mayor, Planificación del mantenimiento mayor, Realizar actividades de alistamiento, Ejecutar el mantenimiento mayor, Cerrar el mantenimiento mayor” [3].

La figura 1 describe la relación entre las fases del mantenimiento mayor de la organización y los procesos de gestión o áreas del conocimiento necesarios y considerados para gestionarlo. Igualmente muestra una línea de tiempo donde se recomienda iniciar y finalizar de cada una de las fases del proceso (desde 30 meses antes hasta 4 meses después de la ejecución), como también los hitos principales de inicio y cierre de cada una de ellas.
Cada una de las fases descritas y representadas en la figura 1 anterior, se gestionan a través de diferentes áreas del conocimiento que coinciden en su mayoría con las áreas de gestión referenciadas en el PMBOK del PMI. Esto es importante ya que permite establecer un relacionamiento entre el impacto de las áreas de gestión y cada una de las fases del mantenimiento mayor, eso sí, tomando como referencia el criterio base de las premisas del mantenimiento enfocadas en el alcance, la duración y el costo.
Las entradas de las diferentes fases obedecen a hitos bien definidos del proceso y son determinantes para el éxito de la parada de planta, entre otros son: Premisas del mantenimiento, Congelamiento de alcance, Paquetes de Trabajo (Planificación / Programación), Talleres de Alistamiento, Ejecución, Corrida de desempeño, Informe final.
Objetivos y metas de una parada de planta
Las premisas de la parada de planta consisten en la definición de los objetivos y metas a través de un documento con los lineamientos para el alcance, la duración, el costo, el desempeño HSE, de calidad, y productividad durante la ejecución de la parada, como también la eficiencia y la confiabilidad esperada para l la planta intervenida, los niveles de riesgo aceptados, entre otros. En dicho documento se establecen las métricas necesarias para validar el éxito del mantenimiento mayor y contra esta línea base se realizan las comparaciones del desempeño del mantenimiento.
Como característica clave, las premisas deben ser un documento validado y aprobado oportunamente por todos los interesados requeridos y sustentado en los niveles necesarios, en resumen, es el compromiso entre las partes para el mantenimiento mayor bajo el cual se cobijan el negocio, su estrategia y los aspectos particulares del mantenimiento mayor y es validado y aprobado por los niveles superiores de la organización.
Alcance de una parada de planta
El alcance para una parada de planta surge de diferentes escenarios, requerimiento y necesidades como se describió previamente. Sin embargo, no todo el alcance “propuesto” es incluido finalmente. Previo a su precisión, se realizan diversos talleres de revisión y validación bajo las metodologías propias y derivando finalmente en lo que se denomina el alcance congelado, o en otros referenciamientos como la lista de trabajos (work list).
El alcance congelado es un registro que corresponde al listado priorizado de ordenes de mantenimiento (CMMS), donde se identifican los activos industriales a intervenir durante el mantenimiento mayor con un alcance definido, así como las que fueron removidas del alcance (taller de cuestionamiento), diferidas a otro mantenimiento mayor o redireccionadas a mantenimiento rutinario, todo esto con el fin de garantizar la confiabilidad mecánica y operación de las plantas. Este listado esta priorizado bajo los criterios de Factor de riesgo (Factor J) – Valoración RAM (metodologías trasferidas por Shell Global Solution).
De manera general se puede encontrar tres tipos de alcances durante el ciclo de un mantenimiento mayor. El que se denomina alcance conocido, asociado al alcance precisado y congelado, también llamado original; el alcance de previsión, el cual es una estimación probable de su ocurrencia y de sus cantidades (podría o no materializarse o ser en una cantidad mayor o menor del estimado); y finalmente el alcance emergente que puede surgir antes de la ejecución, pero que surge en mayor medida durante la ejecución una vez abiertos e inspeccionados los equipos intervenidos.
El impacto de los alcances de previsión y en especial el emergente, son considerables en términos del riesgo de mayor duración, costo y por tanto la afectación del mantenimiento integral. Pero, de otra parte, es probable que este alcance emergente sea indispensable para garantizar la integridad, confiabilidad y finalmente la disponibilidad del activo, por tanto, cada caso y cada alcance emergente debe ser evaluado y cuestionado bajo las metodologías establecidas para este fin y así tomar la decisión óptima para cada caso.
Duración de una parada de planta
La duración de una parada de planta está supeditada a su alcance, al proceso de planificación y a la optimización de la programación. La principal salida de esta fase del proceso es el programa detallado de trabajo y la(s) ruta(s) critica(s) derivadas de la programación de actividades, entendiéndose por ruta critica el camino o el conjunto de actividades con mayor duración del mantenimiento y por tanto con una holgura cero. Así pues, estas rutas criticas establecen la duración nominal del mantenimiento mayor.
Es importante reconocer que existen múltiples métodos para gestionar el cronograma y su duración, como por ejemplo el método CPM (Critical Path Method), anteriormente descrito; el método PERT (Program Evaluation and Review Techniques) Técnica de Revisión y Evaluación de Programas; el de Cadena Critica, entre otros.
La principal diferencia entre PERT y CPM radica en que el diagrama de PERT se utiliza, generalmente, al necesitarse determinar el tiempo necesario para la finalización de un proyecto, en contraste con el CPM que se utiliza en proyectos con características predecibles. En otras palabras, los diagramas de PERT son un método para planificar y gestionar el tiempo, mientras que el CPM se encamina más para controlar costos y tiempo [5].
El programa detallado de trabajo vincula una secuencia lógica con unas duraciones y recursos necesarios, como también la interrelación entre ellos. La gestión del cronograma es realizada a través de aplicativos informáticos especializados como Primavera P6, Microsoft Project, ente otros.
Es importante comprender que la duración es sensible a los cambios de alcance y esto mismo deriva en posibles impactos en los costos del mantenimiento mayor. La gestión de la duración del mantenimiento mayor no solo obedece al monitoreo y control del cronograma, sino más bien a la integración y la relación entre el alcance, duración y costo (triple restricción clásica).
Costos de una parada de planta
Si hay un factor relevante en el desempeño de una parada de planta se puede resumir en el costo de esta. Esta afirmación se fundamenta en que cualquier otra de las restricciones contempladas (alcance y/o duración), dan como resultado una desviación sobre el costo del mantenimiento.
El proceso de costeo de una parada de planta se inicia en fases tempranas del mismo ya que debe surtir diferentes etapas y momentos de acuerdo con el plan de hitos establecido, por ejemplo, las compras de muy largo plazo, la solitud del presupuesto plurianual, etc.
La gestión de costos es un proceso gradual que considera una progresión, especialmente en su precisión asociada, la cual en la medida que avanza el proceso de mantenimiento mayor, ofrece mayor certeza y detalle para realizar las estimaciones respectivas. Un ejemplo de esto es que para la fase de largo plazo el presupuesto tiene una precisión de +/- 50%, en la de planificación detallada del +/- 30% y para la ejecución está en el orden del +/-10%.
Teniendo en cuanta esto, dentro del proceso de mantenimiento mayor se siguen las diferentes etapas para gestionar los costos: planificar, estimar, determinar presupuesto, controlar costos, nótese que son los mismos procesos sugeridos por la guía del PMBOK.
Durante la ejecución del mantenimiento mayor, los costos se gestionan bajo los parámetros del monitoreo y control, haciendo uso de herramientas como la línea base de costos, el valor ganado, análisis de tendencias, de variación, etc.
Como fue tratado en el apartado de alcance, la influencia de este sobre los costos es preponderante, y su gestión resulta prioritaria para mantener el presupuesto alineado con las metas y objetivos especificados en las premisas. Por tanto, recordando que el presupuesto debe responder por el alcance conocido, el de previsión y el emergente y ya que estos tipos de alcance tiene momentos del tiempo particulares, resulta ser un factor para considerar en la estimación y presupuestación de los costos del mantenimiento (variación de la precisión en función de las fases del mantenimiento mayor).
En resumen y utilizando las expresiones acuñadas en la gestión del riesgo, aparecen de manera general dos grupos de alcances para desarrollar la estimación de costos, los conocidos-desconocidos: incluyen el alcance conocido y los trabajos emergentes previos a la ejecución y los desconocidos-desconocidos: los cueles incluyen el trabajo emergente identificado durante la ejecución y producto de la inspección detallada de los equipos y que corresponde a trabajos que no pudiesen ser previstos hasta no abrir e inspeccionar.
Planificación de una parada de planta
Dentro de las fases del proceso de mantenimiento mayor (parada de planta), indudablemente el corazón de este se halla en la planificación, entendida esta, bajo el contexto del mantenimiento mayor, como las actividades de planeación necesarias para asegurar la ejecución del mantenimiento, e incluye entre otros, la planeación detallada de la ejecución, la logística, el plan de contratación y compras, etc.
Los principales hitos que se deben desarrollar en esta fase son: elaborar y consolidar programas y paquetes de trabajo; realizar talleres de cuestionamiento de ruta crítica; definir estrategia de ejecución; planear ordenes de trabajo; compras y contratos; revisión de alistamiento; entre otros.
La entrada principal para esta fase del mantenimiento mayor es el alcance congelado y su principal salida es el taller de revisión del alistamiento. El entregable principal son los paquetes de trabajo, y el programa detallado de trabajo.
Para el análisis y diagnóstico de este artículo, se tendrá como unidad de gestión comparable los paquetes de trabajo y su efecto sobre las premisas del mantenimiento mayor: alcance, duración y costo.
Un paquete de trabajo es un conjunto de entregables producto de la planificación, el cual incorpora todo lo necesario para ejecutar la acción de mantenimiento. Incluye desde la gestión a través del CMMS de la organización de las ordenes de mantenimiento, gestión de materiales y repuestos, planos, referencias técnicas, controles de calidad, procedimientos específicos, planes de izaje etc.
En la planificación hay dos factores relevantes que se deben destacar, el primero asociado a estimaciones (personas, equipos, materiales, herramientas, duración de actividades, etc.) y el segundo asociado a la programación y a dar la secuencia lógica de las actividades y la optimización de los recursos estimados (histogramas).
Para efectos de estimaciones, se incorporan buenas prácticas de la industria a nivel internacional como el uso de normas labor (estudios de actividades y sus duraciones y recursos medidos en diferentes organizaciones a nivel mundial); el juicio de expertos; históricos de mantenimiento. Por otra parte, para la gestión del cronograma, se realiza la integración de las estimaciones y su secuencia lógica en el cronograma y se realizan talleres de optimización del alcance donde se identifican, gestionan y optimizan las actividades y su secuencia, los recursos (nivelaciones) arrojando la duración final esperada.
Teniendo en cuanta lo anterior, se pone de manifiesto la relevancia de esta fase y su impacto sobre la triple restricción original tomada como referencia para este artículo.
Marco contextual de una parada de planta en la organización
En la actualidad, la gestión de un mantenimiento mayor (parada de planta) obedece a varios esfuerzos relativamente aislados ya que de acuerdo con la estructura orgánica y la naturaleza del proceso (frecuencia), la asignación de recursos para su gestión (en algunos casos de más de 24 meses previos a la ejecución), requiere que se asignen Lideres de Parada (Gerentes de Proyecto), Planeadores, etc. a múltiples y simultáneos eventos. Igualmente, si bien el proceso está claramente establecido, maduro y en realimentación de mejora continua, se observan adaptaciones no convenientes como el uso de plantillas y formatos diferentes, el uso de repositorios documentales diversos, rigurosidad y competencia en el desarrollo de los talleres que soportan el proceso (cuestionamiento del alcance, optimización del alcance, alistamiento, etc.), etc.
Es claro que estas variaciones podrían obedecer más a la forma que al fondo, pero finalmente el efecto sobre los resultados podría ser básicamente en optimización. Por otra parte, los hechos particulares descritos, se potencian al ser dos refinerías de características diferentes que aplican el mismo proceso y además con estrategias que obedecen en algunos momentos a condiciones puntuales de mercado o estrategia. Es importante aclarar, que actualmente existe un proceso de alineación estratégica que busca integrar las dos refinerías y transferir las mejores prácticas entre sí y ser adecuadamente gestionadas desde lo operacional, la gestión de activos, y de resultados del negocio.
Actualmente para la planificación de la para de planta, se cuenta con una unidad integral y centralizada de planificación que posee profesionales divididos por especialidades y coordinados a través de un líder de planificación. Esta unidad recibe las solicitudes de planificación, las gestiona bajo los entregables establecidos para las mismas y finalmente entrega unos paquetes de trabajo con todo lo requerido para la ejecución de la parada de planta y un plan detallado de trabajo.
III. Revisión de resultados de la gestión del mantenimiento mayor (parada de planta) en eventos de la organización y de referenciamiento
Durante el año 2021 se ejecutaron varias paradas de planta a diversas unidades de proceso de la refinería, de los cuales se seleccionó dos eventos particulares que se consideran dentro del alcance de este artículo.
A estos dos eventos se les realizó un análisis y diagnóstico de los resultados obtenidos (comparativamente con las premisas) [6], y, además, a través de referenciamiento, principalmente con los estudios internacionales sobre confiabilidad y mantenimiento (RAM) de Solomon Inc. [4, 7, 8, 9, 10, 11].
Los eventos considerados corresponden a unidades de proceso principales, las cuales se interviene por bloques operacionales relacionados, los cuales están conformados por un total de 5 plantas intervenidas. Estos mantenimientos cumplieron el proceso completo de las 6 fases en los tiempos establecidos y cumpliendo los hitos definidos para cada fase.
Premisas de la parada de planta
Para los eventos constituyentes de este artículo, fueron establecidas unas premisas, las cuales surtieron el proceso de validación por la línea organizacional responsable. Las premisas integraron y alinearon el negocio, la estrategia y los factores particulares de los eventos.
Así pues, se extractan de estas premisas las referentes a las metas del alcance, la duración y el costo de los mantenimientos mayores.
Los valores referenciados en las premisas como desviación permisible y valores de referenciamiento se muestran en la tabla 1.

Cursos recomendados




%252FImagen%252FRAMPREDYC-1730060420837.webp%3Falt%3Dmedia%26token%3D2634a7f0-988e-4022-b91f-382503e6e9db&w=3840&q=75)



Resultados de los eventos de parada de planta 2021
Los resultados analizados en este artículo se centran en las desviaciones frente a las premisas establecidas para el alcance, la duración y el costo de los mantenimientos mayores.

Claramente se observa una desviación en el alcance, la duración y el costo de los eventos. El análisis y propuesta serán desarrollados a continuación de manera independiente para cada factor y finalmente se realizará la integración de las diferentes causalidades y efectos encontrados y la propuesta de optimización.
Mediante el uso de listas de verificación de cumplimiento para cada una de las áreas de gestión del mantenimiento mayor, se realizó una valoración y ponderación de dicho cumplimiento siendo 5 el máximo resultado posible (100% de cumplimiento) y 1 el mínimo resultado posible (0% de cumplimiento). Igualmente se estableció una valoración cualitativa como se describe a continuación.



De acuerdo con los resultados presentados en la figura 3, se establecen las áreas de gestión del mantenimiento mayor con un menor desempeño la definición & optimización del alcance; el proceso de planificación; Presupuesto, estimación & control de costos y en menor medida la gestión de la calidad y la gestión de riesgos.

Se infiere que el costo representa el mayor impacto y su relación con la definición del alcance, la gestión de la duración representa una oportunidad de optimización.
Ahora bien, los resultados analizados muestran que el proceso de planificación tiene un desempeño con cumplimiento medio y por tanto requiere un análisis más detallado.
El modelo de planificación actualmente empleado utiliza tres esquemas de planificación: cien por ciento la organización; cien por ciento aliados y finalmente mixtas. Este análisis se realizará bajo el criterio de una planificación 100% de la organización.
Si bien existen unos modelos generales para la elaboración, la completitud y calidad de los paquetes de trabajo, se ha identifico variaciones considerables entre las planificaciones y entre los eventos, además, también existen variaciones dependiendo del esquema de planificación.

La tabla 3 representa que los esquemas de planificación inciden en la calidad de los entregables, también se infiere que las principales brechas del paquete de trabajo se encuentran en las estimaciones y la información técnica mínima requerida. En resume, la calidad de cumplimiento de los paquetes de trabajo está en promedio 90% bajo los tres esquemas.
En la tabla 4 se presenta una comparación histórica entre los resultados de los mantenimientos mayores en los últimos años, relacionando las premisas comprometidas para estas y los resultados reales obtenidos.
En este sentido, se observa una desviación importante en los resultados comprometidos en las premisas de cada evento, y su bajo nivel de cumplimiento. Los datos con los que se cuenta demuestran principalmente desviaciones asociadas a trabajos emergentes y contingentes que afectan drásticamente los valores de alcance, duración y costo. Esto nos lleva a considerar la necesidad de revisar la calidad de cumplimiento de la planificación, como uno de los factores influyentes en las desviaciones a las premisas comprometidas.


Desde el punto de vista de la calidad de la planificación, específicamente lo asociado a mayor alcance, se debe analizar el contexto bajo las siguientes condiciones. La primera, asociada a la planificación, es determinar la calidad de esta, lo cual incluye básicamente constatar si lo planeado fue suficiente para cumplir el alcance o hay alguna desviación que haya generado la necesidad de realizar más trabajo no planeado.
Como segunda medida, es probable que la desviación de alcance sea consecuencia del estado natural de deterior del equipo o que solo fue posible evidenciarlo una vez abierto e inspeccionado. Este factor se sale del análisis que se pretende, ya que el mismo no pudiese determinarse previamente. Sin embargo, presenta un alto impacto sobre los costos y la duración del mantenimiento.
Por tanto, se requiere establecer un indicador de cumplimiento de los paquetes de trabajo planificados. Este indicador debe permitir visualizar las diferentes condiciones adoptadas desde el congelamiento del alcance y de la planificación en sí mismas. Esta es la principal variable de comparación con el criterio de éxito, que se define como el cumplimiento de las premisas comprometidas.
Continuando con el diagnostico, se presenta una comparación general de cumplimento de las fases del proceso para eventos históricos ejecutados que permiten visualizar los puntos focales de atención para obtener los resultados positivos que busca la organización.
De las fases de un mantenimiento mayor, las desviaciones más representativas se encuentran fundamentalmente en la de planificación y de allí se deriva específicamente el impacto de los paquetes de trabajo como unidades de comparación de éxito. Es decir, como las unidades mínimas de trabajo completadas y planificadas y que son la base para las estimaciones de duración y costo. Así pues, se establece dentro de este diagnóstico una relación entre la calidad de la planificación (paquetes de trabajo), su implementación y uso.
En resumen, para una parada de planta, la cual muestra desviaciones al cumplimiento de sus premisas, y enfocándonos solamente en el efecto de la planificación sobre ellas, se correlaciona inicialmente que la calidad de la planificación (uso de estándares, coherencia y uniformidad), podrían incrementar la probabilidad de éxito y cumplimento de las premisas comprometidas en el evento. De esto, se deriva la promesa de valor esperada, en una estandarización que promueva su cumplimiento y uso.
IV. Propuesta de optimización
Si bien la implementación de modelos de optimización surte diferentes aspectos asociados a la estrategia organizacional y la manera de abordar las necesidades propias de su gestión de proyectos, existen modelos propuestos que, de manera general, describen la manera como se adoptan desde la evolución de la madurez organizacional y la gobernanza de esta.
La propuesta derivada de este análisis subyace en un enfoque que, en primera instancia, está asociado al modelo organizacional (la forma de hacer las cosas) y el siguiente enfoque es la incorporación y/o mejora de técnicas y herramientas propias para gestionar los diferentes aspectos de alcance, duración y costo.
Enfoque 1: del modelo organizacional – Implementación de una Oficina de Proyectos PMO
La planificación en una parada de planta ejerce un gran impacto en los resultados de esta. En este sentido, ordenar, organizar, estandarizar este proceso, es una alternativa de mejora continua que ofrece ventajas claras en dicha optimización.
En esta primera parte de la propuesta de optimización, se pretende establecer los posibles lineamientos y beneficios que podría generar la implementación de una Project Management Office – PMO de Apoyo para la gestión del mantenimiento mayor (Parada de Planta), en función de la literatura y definiciones consultadas.
De acuerdo con el PMBOK en su sexta edición, una Project Management Office – PMO es una estructura de gestión que estandariza los procesos de gobernanza relacionados con el proyecto y facilita el intercambio de recursos, metodologías, herramientas y técnicas [1].
En este sentido, y haciendo un paralelo a la estructura actual de gestión de un mantenimiento mayor en la organización, se tienen recursos diseminados, metodologías combinadas y uso indiscriminado de herramientas y técnicas en función de las necesidades de cada líder de parada (gerente de proyecto) y por tanto surge la oportunidad de integrar, a través de una PMO de Apoyo, las ventajas inherentes a esta estructura con vista a incrementar la eficiencia y eficacia de los resultados de los mantenimientos mayores y por ende en los resultados sobre el negocio de refinación.
Si bien determinar el impacto del valor generado por una PMO representa un desafío importante en sí mismo, es claro que desde la perspectiva del objetivo de este artículo se podrá obtener una primera aproximación de este impacto en términos del uso de los beneficios de esta estructura mas no de la eficiencia y eficacia en los resultados de la gestión de un mantenimiento mayor, este complemento será desarrollado en posteriores estudios utilizando mediciones significativas de la relación directa de las variables del proceso sobre los resultados [12].
Dentro de este artículo, se permeará la visión del PMI en su modelo, sin desconocer la existencia de otros modelos importantes [13,14], por tanto, se adopta que existen varios tipos de PMO y que cada una varía en función del grado de control e influencia que ejerce sobre los proyectos: de apoyo, de control y directiva.
Siguiendo la revisión de la literatura realizada, por su definición, por su alcance y beneficios, para el caso de los mantenimientos mayores, una PMO de Apoyo cubrirá de manera general los aspectos de mejora identificados previamente.
Una PMO de Apoyo, de acuerdo con la definición del PMBOK, es la que desempeña un rol consultivo para los proyectos (mantenimientos mayores), suministrando plantillas, mejores prácticas, capacitación, acceso a la información y lecciones aprendidas de otros proyectos.
Amendola plantea la gestión de paradas de planta mediante una PMO, pero complementado la gestión de la parada de planta desde el modelo: Risk-oriented Project life-cycle [15], el cual difiere en algunos aspectos al modelo de la organización estudiada. sin embargo, coincide en la búsqueda de nuevas formas de dirección y gestión de las paradas de plata con el objetivo final de recuperar la integridad, la confiabilidad y disponibilidad de los activos.
Por otro lado, es importante reconocer que la implementación y uso de una PMO de Apoyo en sí misma no garantiza la obtención de los beneficios esperados, ya que también los resultados estarán enmarcados en cómo sobre la organización influye su cultura organizacional, su madurez, la gobernanza, entre otros aspectos limitantes [16, 17].
El otro aspecto para considerar es la medición de variables de desempeño que contrasten la generación de valor de la implementación de una PMO en la gestión de mantenimiento mayor. Estas mediciones en diferentes referencias consultadas establecen métodos cualitativos y cuantitativos, con resultados disimiles, sin embargo, aportan una contribución a los aspectos particulares que debe desarrollar cada organización en sus métricas y así poder referenciarse y determinar los beneficios obtenidos.
Enfoque 2: Incorporación de buenas practicas
Optimización del Alcance en una parada de planta
La definición del alcance es la entrada determinante para los demás factores acá contemplados y por tanto requiere una especial atención.
Dentro de las buenas prácticas de la industria y considerándola como una alternativa complementaria a los talleres de cuestionamiento del alcance que se desarrollan habitualmente en el proceso, se propone el uso de la optimización del alcance basado en riesgo – Risk based work scope optimization y sus siglas en ingles RBWS [18, 19, 20]. Igualmente, buscando mayor eficiencia y efectividad en la definición de los alcances, se propone restructurar la estrategia de RBI – Risk Based Inspection [21, 22]. que se emplea actualmente.
Para la optimización del alcance basado en riesgo – RBWS, se debe entender su alcance y limitaciones. La metodología RBWS proporciona una base rigurosa para justificar la inclusión o el rechazo de elementos de la lista de trabajo (alcance propuesto), si estos no mitigan los riesgos o no satisfacen los criterios de costo/beneficio que se establecen para la evaluación, los cuales son definidos por la organización (apetito al riesgo).
La aplicación de la toma de decisiones basada en el riesgo – RBWS, elimina discrecionalmente las tareas del mantenimiento mayor y retiene tareas que mitigan los riesgos inaceptables o que proporcionarían un beneficio desde un punto de vista financiero. El resultado de una evaluación de RBWS genera un alcance de trabajo más estricto que conduce a una reducción significativa en la duración y los costos del mantenimiento mayor. La aplicación de la metodología aplica para todos los tipos de equipos principales (equipos estáticos, tuberías, equipos rotativos, instrumentos, electricidad, calentadores, sistemas de TEA, etc.) programados para un mantenimiento mayor.
La metodología RBWS, cuando se usa con equipos estáticos, utiliza datos de inspección basada en riesgos (RBI), cuando es necesario, para validar o rechazar tareas del mantenimiento mayor que están incluidas en la lista de trabajo. Las evaluaciones de RBI se enfocan en la integridad del equipo y la pérdida de contención, mientras que la metodología RBWS complementa estas evaluaciones con la consideración de fallas y consecuencias en los componentes internos de los recipientes a presión que pueden causar una parada no programada y un impacto en la integridad y confiabilidad del equipo.
Alineado con lo anterior, en cuanto a la restructuración de la estrategia en la aplicación de la practica recomendada de API 580, inspección basada en riesgo – RBI, es importante definir de manera general lo que esta metodología considera y aporta al proceso.
La metodología Inspección Basada en Riesgo está fundamentada en las practicas recomendadas API RP-580 y API PUB-581 y su premisa es caracterizar el riesgo asociado a los equipos estáticos (intercambiadores de calor, recipientes a presión, tuberías, etc.) bajo un lazo común de corrosión (mecanismos de daño y modos de falla), usando el análisis del comportamiento histórico de: las fallas, modos de degradación o deterioro, características de diseño, condiciones de operación, mantenimiento, inspección y políticas organizacionales, considerando simultáneamente la calidad y efectividad de la inspección realizada, así como las consecuencias asociadas a las fallas potenciales [21, 22]..
El objetivo fundamental del RBI es definir planes de inspección basados en la caracterización probabilística del deterioro y el modelamiento probabilístico de la consecuencia de una falla (caracterización del riesgo) [21, 22].
Existe una “Metodología RBI mejorada para la Integridad Mecánica de Activos” se basa en la integración de las metodologías de Inspección Basada en Riesgos, “Valoración del Riesgo por Corrosión” (VRC)”, Integridad Mecánica (IM) y modelamiento probabilístico del deterioro, lo cual permite ampliar el espectro de cobertura de mecanismos de deterioro considerados en el enfoque clásico del RBI [23, 24].
El mayor impacto que puede ofrecer el RBI es el asociado a los trabajos emergentes, en especial los generados durante la apertura e inspección de equipos. Si se considera el alcance emergente bajo estas características, se podría dividir este en alcance previsible y alcance imprevisible, ambas circunstancias asociadas a la predictibilidad que a su vez depende de la frecuencia y alcance de las inspecciones, de las violaciones a las ventanas operativas (API RP584), al estado de las corridas (ejecución de la corrida de desempeño), etc. Finalmente, realizando el seguimiento detallado de estas, se podrá tener mayor control sobre los mecanismos de daño, los modos de falla y la probabilidad de falla asociados y por tanto optimizar alcances a través de la anticipación.
Optimización de la duración de una parada de planta
En cuanto a la duración, la propuesta se enfoca en adoptar complementariamente a los métodos tradicionales de CPM/PERT, el método de la cadena critica (CCPM), pero con el valor añadido del análisis de riesgo simultaneo [25, 26, 27].
La cadena crítica (CCPM), está basada en la teoría de las restricciones que tiene por objetivo identificar la causa principal de los problemas (cuellos de botella) y poder ser corregidos y así optimizar la manera de gestionar las duraciones, estableciendo de manifiesto lo más eficaz en la ejecución a la vez que se minimiza el uso de recursos disponibles.
Por tanto, el método CCPM puede definir la duración mínima en que el mantenimiento puede finalizar e impone las restricciones que logran no perder la alineación con esa secuencia de actividades de menor duración. De esta forma, se evitan los obstáculos que, con mayor frecuencia, pueden conducir un mantenimiento al fracaso o al bajo desempeño.
La metodología se compone de cinco pasos [25]:
- Identificar las restricciones del sistema.
- Diferenciar las restricciones físicas de las organizacionales para, por ejemplo, diferenciar entre las limitaciones de recursos materiales y entre las reglas empresariales.
- Superar las restricciones del sistema: Los esfuerzos deben centrarse en aquellas tareas que formen parte de la cadena crítica, que son las que determinarán la finalización del proyecto.
- Subordinar todas las demás tareas a la decisión tomada en la cadena crítica.
- Si se rompe una restricción, no volver a la rutina y regresar al primer paso.
Optimización del costo de una parada de planta
Asociado al costo, las buenas prácticas complementarias sugeridas pasan por dos acciones. La primera relacionada con las estimaciones y la segunda asociada al control del presupuesto [28, 29].
Complementario a los métodos y técnicas de estimaciones actualmente utilizados, se sugiere el uso de prácticas recomendadas como las de la AACE (American Association of Cost Engineering), tales como AACE RP112R-20, “Cost Estimate Classification System – As Applied in Maintenance Turnarounds for the Process”. Las estimaciones deben ser debidamente soportadas con su respectivo BOE (Basis of Estimate) que no es otra cosa que unas premisas y detalles de la manera como se realizó la estimación. Igualmente, importante es tener estandarizada la EDT, tanto de programación, como riesgos y obviamente costos.
De manera general una buena estrategia de estimación de costos debe incluir la mejora en los procesos de estimación (procesos conocidos y trazables); la competencia del personal estimador y el uso de tecnología que permite gestionar las estimaciones más eficientemente y lograr una línea base de costos confiable y estructurada.
Por otra parte, lo relacionado al control de costos de la parada de planta, surge como herramienta el uso del valor ganado – “cantidad de trabajo ejecutado a la fecha, expresado en términos del presupuesto autorizado para ese trabajo” [1]. Usar el valor ganado involucra tanto las áreas de planificación, de programación, costos y dirección. En resume es una técnica que permite cierto control y seguimiento a la interrelación del cronograma y el presupuesto y proporciona información muy útil para la toma oportuna de decisiones. No obstante, también hay que reconocer las limitaciones (meramente operativas) de esta técnica y los niveles de confiabilidad de la información con la cual se constituye.
Es evidente, que lo descrito en los párrafos anteriores corresponde a la preparación previa de la parada de planta y si bien el control de costos se materializa principalmente en la ejecución, es vital comprender que dentro de los resultados que se pretende impactar para optimizar los costos obedece a la gestión de su principal enemigo: el trabajo emergente. En ese orden de ideas, se relacionan estrechamente las tareas descritas en la optimización del alcance, relacionado al RBI y al control de ventanas operativas, como también a la anticipación de mecanismos de daño y modos de falla.
V. Conclusión
La gestión de un mantenimiento mayor (parada de planta) puede aceptarse como un proyecto y por tanto puede hacer uso de las diferentes metodologías, métodos, técnicas, herramientas, buenas prácticas que dicha gestión ofrece bajo los diferentes aspectos considerados. Así pues, entendiendo el impacto de un mantenimiento mayor sobre los resultados del negocio de refinación, se hace evidente que la adecuada gestión de este puede incidir positivamente en aspectos como: alcance, duración, costo, calidad, riesgos, seguridad, etc.
La mejora continua y la adopción de diversas metodologías, métodos, técnicas, herramientas, buenas prácticas, etc. para obtener los resultados esperados en un mantenimiento mayor, permite inferir que reconociendo las falencias actuales del proceso adoptado y desarrollado en la organización, una gestión del mantenimiento a través de una PMO de Apoyo, podría brindar los beneficios, al menos desde la perspectiva de la literatura consultada: integrar y apoyar a gestión a través del suministro de buenas prácticas, capacitación, acceso a la información, plantillas, lecciones aprendidas, etc.
Sin embargo, también es claro que la dificultad inherente a la medición de beneficios entregados por una PMO de apoyo limita los resultados y hace necesario establecer un marco particular para el análisis dependiendo de cada organización y sus expectativas.
La propuesta de optimización sugiere dos enfoques integrados, por una parte, está la estructura o modelo organizacional sugerido (PMO de apoyo) y, por otra parte, la incorporación y/o mejoras de buenas prácticas, técnicas, métodos y herramientas.
Un factor común en el desarrollo de los enfoques propuestos es la gestión del riesgo, la cual está presente en todas las propuestas desarrolladas y ofrece un complemento en la identificación y evaluación de los riesgos para permitir que estos se entiendan claramente y se gestionen de manera efectiva. El aspecto vinculante para la identificación/evaluación de riesgos con su gestión es la comprensión detallada de cada riesgo. Estas técnicas de identificación, sin embargo, tienden a producir una lista no estructurada de riesgos que frecuentemente no ayuda a determinar dónde centrar la atención de la gestión de riesgos.
De alguna manera, la evaluación cualitativa de riesgos puede ayudar a priorizar sistemáticamente los riesgos identificados a raves de estimar la probabilidad y los impactos, exponiendo así los riesgos más significativos; pero esto trata los riesgos de uno en uno y no como un conjunto interactivo e interrelacionado y por tanto no considera los posibles patrones de exposición al riesgo subyacentes, por lo que tampoco proporciona una comprensión general del riesgo que enfrenta el mantenimiento en su conjunto. Por ello, el paso significativamente lógico, es mudar y complementar el análisis cuantitativo con las técnicas cuantitativas y asociadas a la visualización de riesgos integrales.
Es posible a través de las buenas prácticas y/o de herramientas particulares, acompañado de una fuerte disciplina, incidir positivamente en el alcance, la duración y el costo de una parada de planta. Las desviaciones que usualmente se describen frente a las premisas y el referenciamiento, obedecen en gran medida a una baja o pobre definición de alcances y/o a trabajo emergente mal gestionado (identificación inoportuna). Evidentemente, la condición antes descrita guarda una fuerte relación con la calidad y oportunidad de gestión de los entregables principales de la planificación: que son los paquetes de trabajo y el programa detallado de trabajo.
Un detalle relevante para considerar es mejorar la capacidad de anticipación a los alcances emergentes, en especial los definidos como desconocidos y que requieren los equipos abiertos e inspeccionados. La manera de gestionar los alcances a través del RBI y siendo muy disciplinados con el cumplimiento de las ventanas operativas específicas de cada planta, ofrece una oportunidad de anticipación a los probables mecanismos de daño o modos de falla inducidos por la operación y que usualmente se evidencian una vez abiertos los equipo pero que podrían diagnosticarse frente a las variaciones identificadas en las violaciones de las ventanas operativas (cambio de variables en operación).
Esto requiere un reporte y seguimiento oportuno para así constituir una extensión de la inspección previa a la parada, conociendo los probables efectos de dichas violaciones operacionales sobre los mecanismos de daño esperados.
En resumen, un marco organizacional favorable y que integre efectivamente los requerimientos, considerando el que y el cómo, apoyado en una fuerte disciplina de cumplimiento del proceso a través de la implantación y uso de buenas prácticas, como las sugeridas en este artículo, podrán tener un alto impacto positivo en los resultados del mantenimiento mayor y del negocio de refinación en general (alineación estratégica).
Para validar estos resultados y los enfoques sugeridos, es necesario realizar investigaciones más profundas y desarrollar técnicas de investigación que modelen el impacto (generación de valor) del uso de una PMO de apoyo para la gestión del mantenimiento mayor, junto con la implementación de las buenas prácticas acá sugeridas y su impacto en los objetivos y metas del mantenimiento mayor: alcance, duración y costo. Ese estudio deberá construirse alrededor de los resultados de los mantenimientos mayores históricos, frente a pilotos propuestos para los desarrollos bajo el nuevo modelo.
Referencias
[1] Project Management Institute. (2017). A guide to the Project Management Body of Knowledge (PMBOK guide) (6th ed.). Project Management Institute.[2] Serie ISO 55000/1/2 Gestión de activos[3] Ecopetrol S.A., RFN-G-5127 Guía gestión de mantenimiento mayor. Ecopetrol S.A. 2019.[4] Solomon Inc. International, “Worldwide fuels refinery performance analysis for operating year 2018”.[5] Lucidchart – Diagrama de PERT: Definición y cómo hacerlo: https://www.lucidchart.com/[6] Ecopetrol S.A. Informes de cierre de paradas de planta 2021, Informe presentado a la junta directiva – Refineria de Cartagena.[7] Solomon Inc. International Study of Plant Reliability and Maintenance Effectiveness Performance Analysis (RAM Study) 2018.[8] Solomon (2017). Achieving World’s Best Refinery Status. [9] IPA. (2011) ‘IPA’s Turnaround Evaluations’ [10] A. Poling, “Reliability and maintenance: the path to world class performance”, Hydrocarbon Processing, Dec 2012.[11] J. Stroup, “What characteristics define the world´s best refineries?”, Hydrocarbon Processing, May 2014.[12] V. Juhani, C. Arndt, J.P. Bergman,J. Hallikas, and J. Kaaja, “Impact of the PMPs roles on project performance”, International Journal of Information Technology Project Management, vol. 9, Issue 4, October-December 2018 [13] J. Valdés. “La PMO ágil: un enfoque súper rápido para crear una PMO efective para su organización = The agile PMO: a super fast approach to create an effective PMO for an organization”. Paper presented at PMI® Global Congress 2008—Latin America, São Paulo, Brazil. Newtown Square, PA: Project Management Institute.[14] T. Le Dinh, T. Ho Van, T. Nomo. “A framework for knowledge management in Project management office”. The Journal of Modern Project Management, January-April 2016.[15] L. Amendola. “Gestion de las paradas de planta mediante Project portafolio management office”[16] E. Too, P. Weaver, “The management of project management: a conceptual framework for project governance”, International Journal of Project Management, 32 (2014) 1382-1394.[17] M. Parchami Jalal, S. Matin Koosha, “Identifying organizational variables affecting project management office characteristics and analyzing their correlations in the Irani project-oriented organizations of the construction industry”, International Journal of Project Management, 33 (2015) 458-466[18] A. Radhakrishnan, “Risk Based Work Selection (RBWS) – An Essential Step for Turnaround Work Scope Optimization”, Inspectioneering, October 2019.[19] A. Radhakrishnan, “Risk Based Work Selection (RBWS) – A Focused Process for Achieving Turnaround”, Inspectioneering, September 2019.[20] A. Radhakrishnan, “Risk Based Work Selection (RBWS) – An Essential Step for Turnaround Work Scope Optimization in Refining”, Becht, December 2016.[21] American Petroleum Institute, “Recommended Practice: Risk Based Inspection – API 580”, API, November 2016.[22] American Petroleum Institute, “Recommended Practice: Risk Based Inspection Methodology – API 581”, API, November 2019.[23] F. Elfeituri, S. Elemnifi, “Optimizing turnaround maintenance performance”, PPCOE 2007, October 2007.[24] R. Vichich, “Turnaround excellence – key success factors”, AIChE 2012, April 2012.[25] E. Goldratt, “Cadena Critica”, Granica 2008.[26] M. Bevilacqua, F. Ciarapica, G. Giacchetta, “Critical chain and risk analysis applied to high-risk industry maintenance: A case study”, International Journal of Project Management 27 (2009) 419-432.[27] O. Zwikael, R. Dutt Pathak, G. Singh, S. Ahmed, “The moderating effect of risk on the relationship between planning and success”, International Journal of Project Management 32 (2014) 435-441.[28] AACE RP112R-20, “Cost Estimate Classification System – As Applied in Maintenance Turnarounds for the Process”, AACE, 2020.[29] G. Lawrence, “Cost Estimating for turnarounds”, Petroleum Technology Quarterly Q1 2012.[30] R. Gort, Huw Morgan, (2003). Guía para el Gerenciamiento de Paradas de Planta. Shell Global Solutions International B.V., La Haya.[31] Pockarel, S & Jiao, J.R. (2008) ‘Turnaround maintenance management in a processing industry: A case study’, Journal of Quality in Maintenance Engineering, vol. 14, no. 2, pp. 109-122.Autor
Jaime Andrés Trujillo Duque.
Ingeniero de Materiales, Universidad del Valle; Especialista en Gerencia de Mantenimiento, Universidad Tecnológica de Bolívar; En curso Maestría en Gerencia de Proyectos, Universidad Tecnológica de Bolívar.
jatrujillo@utb.edu.co – ORCID: 0000-0003-3523-423X.
Planeador y Programador Integral de Mantenimiento, Departamento de Paradas de Planta, Refinería de Cartagena – Ecopetrol S.A., Colombia.
jaime.trujillodu@ecopetrol.com.co.
Con 18 años de experiencia en el sector Oil & Gas en proyectos de construcción y en mantenimiento de plantas y equipos mayores, actualmente Líder de Mantenimiento de Calderas y TEA en la Refinería de Cartagena.
Dinos qué te ha parecido el artículo
Artículos recomendados
Análisis de datos: esencial para la toma de decisiones

Modelamiento de Confiabilidad Utilizando MINITAB Como Herramienta de Análisis

SEPMAN 2021

Vehículos eléctricos: descubre su mantenimiento y cómo funcionan

Publica tu artículo en la revista #1 de Mantenimiento Industrial
Publicar un artículo en la revista es gratis, no tiene costo.
Solo debes asegurarte que no sea un artículo comercial.
¿Qué esperas?
O envía tu artículo directo: articulos@predictiva21.com
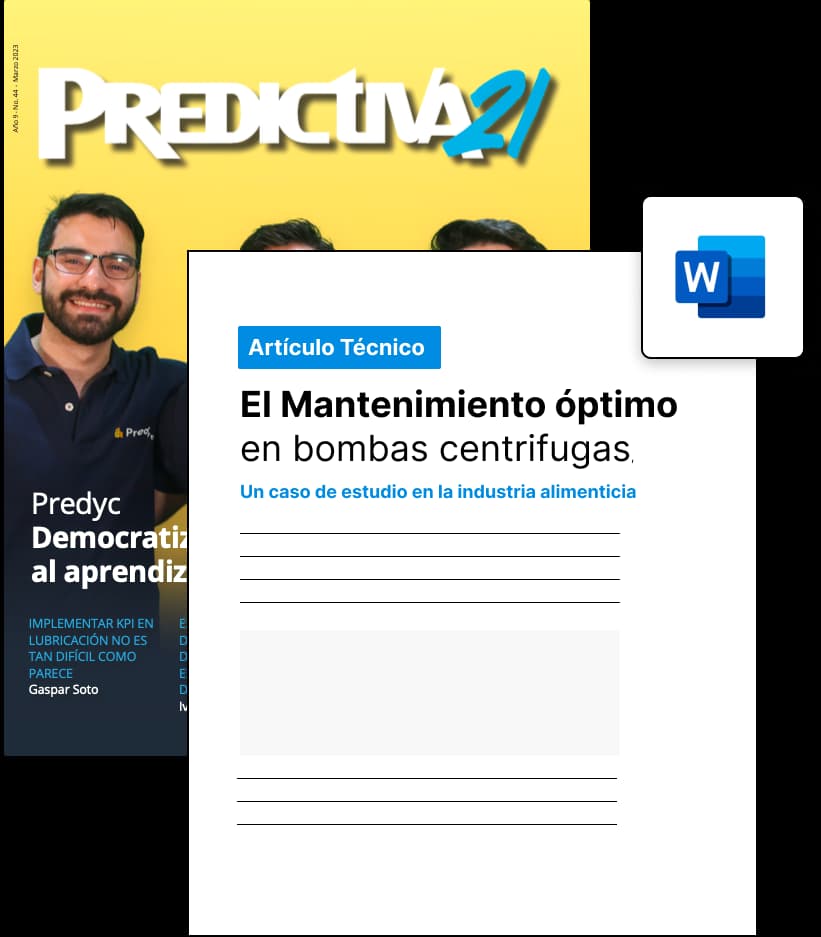