Las Revoluciones Industriales en el Mundo (II Parte)
Articulo10 de marzo de 2020
Tercera revolución industrial
Su desarrollo se sitúa Japón entre los años 1950-1971 y recordemos que éste país quedó destrozado como resultado de la guerra y fue ocupado por las fuerzas norteamericanas en septiembre de 1946 por el Comando Supremo de las Potencias Aliadas (SCAP, siglas en inglés), quien nombró al General estadounidense Douglas MacArthur como responsable de establecer un programa de desarrollo con especialistas norteamericanos para la reconstrucción de esta nación. Dentro de éstos, los más relevantes fueron: W. Edwards Deming, Walter Andrew Stewart y Joseph Moses Juran.
Desde los primeros años de su estancia en Japón se dieron a conocer con los máximos niveles industriales del país compartiendo sus conocimientos en estadística, en calidad, en grupos PM, en logística, etcétera. Empezaron en ese nivel debido a que las vivencias de los norteamericanos en el lapso de 1939 a 1945 les mostraron la incongruencia de no preparar a los propietarios y altos niveles con poder de decisión y su compromiso con el cliente. En Japón podían hacerlo porque para la Unión de Científicos e Ingenieros Japoneses (UCIJ) y los altos niveles de la industria ésta preparación realmente despertó un interés vital, además de llenar sus expectativas de un promisorio futuro próximo y casar plenamente con la idiosincrasia de su pueblo.
Sigamos los pasos del Dr. Deming durante su larga estancia por el Japón (1950 - 1980) en donde llegó a adquirir un gran reconocimiento y estimación. Los japoneses le mostraron su aprecio instituyendo en 1951 el “Premio Deming” (una medalla de plata con su efigie).
Una de sus grandes contribuciones es el “control estadístico de proceso” que facilita el diagnóstico de la calidad de funcionamiento de la máquina. Fue común que durante sus conferencias recomendara que la calidad no debiera medirse sobre el producto terminado, sino debería formar parte del proceso de producción y que ésta se detectara a través del uso frecuente de la estadística. También influía en el establecimiento de los “Grupos de trabajo”, y la aplicación de la logística.
Deming orientó a los japoneses acerca de que antes de hacer un producto, se investigara el mercado para conocer lo que éste demandaba y de ahí establecer los parámetros que regirían los procesos de producción. Deming siguió trabajando muy estrechamente con los japoneses durante treinta años a través de los cuales hizo de esa nación el emporio que actualmente es y regresó a EUA debido a la fama que en su patria adquirió gracias a las investigaciones que sobre “El milagro japonés” hizo la periodista norteamericana Clare Crawford Mason.
Seiichi Nakajima (1928)

En 1950 era un alto funcionario del Instituto Japonés de Mantenimiento de la planta (JIMP) y fue uno de los muchos industriales de alto nivel que recibieron las enseñanzas de Deming sobre el Mantenimiento Productivo Norteamericano PM y con base en sus observaciones desarrolló el Mantenimiento Productivo Total. En 1971 lo introdujo en algunas industrias japonesas iniciando con ello el boom de dicha industria y en pocos años todo el mundo apreciaba la calidad de los productos de ese país. En 1987 dirigió durante dos semanas una misión nipona a los Estados Unidos para dar a conocer su TPM ya que existían muchos industriales norteamericanos con deseos de establecerlo; este efecto se ha replicado en el ámbito mundial con muy buenos resultados. En la actualidad el TPM nos demuestra cómo todo el personal de la empresa incluyendo sus proveedores y distribuidores está involucrado en la productividad.
Concepto del mantenimiento productivo (PM)
Para 1939 las empresas tenían una organización simple, generalmente una dirección general con tres o cuatro subdirecciones o gerencias subordinadas para encargarse de las funciones primarias; producir, vender, administrar y desarrollar las finanzas. El Mantenimiento Productivo (PM) se originó en el área de Producción debido a que ya existían en ella buenos conceptos sobre la división del trabajo, la ciencia y la administración aplicadas a la industria, el uso de la estadística, la búsqueda de la calidad del producto, etcétera; pero estos conocimientos por razón natural no existían en las áreas de ventas, administración o finanzas. La figura 3 nos muestra un organigrama hipotético de una empresa norteamericana en 1950 en la que observamos que solo en la dirección de producción se tiene establecido el PM pues se suponía que solo en esta era necesaria dicha actividad.

Recordemos que desde 1919 los señores, W. Edwards Deming, Walter A. Shewhart y Joseph Juran entre otros, estuvieron directamente trabajando para las industrias norteamericanas aportando soluciones a múltiples problemas estableciendo o cambiando procesos tanto técnicos como administrativos. Cuando en 1947 dichas personas arribaron al Japón, además de su gran preparación, llegaron con la idea de que el desarrollo del personal en la industria debería ser aplicado a todos sus integrantes, con énfasis en los dueños y directores generales de las empresas. Las otras direcciones como las de finanzas, administración y ventas no vamos a considerarlas en éste subtema, puesto que el fenómeno se desarrolló solo en producción.
Cuando Nakajima en 1950 inició sus estudios de PM desde Japón, encontró que la industria americana estaba organizada de manera similar a la mostrada en la Figura 3. Ya trabajaban los supervisores y obreros con los grupos de trabajo (GTPM) y ya se empleaba normalmente la Logística. Para facilitar nuestra percepción analicemos solamente la Gerencia de Producción de la mencionada figura y desarrollemos su organigrama (ver figura 4); esto fue lo que encontró Seiichi Nakajima cuando empezó a desarrollar sus estudios del Mantenimiento Productivo norteamericano.

Concepto del mantenimiento productivo total (TPM por sus siglas en inglés)
La labor de cualquier industria es la de producir en forma conjunta como un solo equipo, como una orquesta, en donde cada dirección, gerencia, departamento, proveedor o persona, debe esforzarse en forma coordinada para obtener beneficios, para lo cual debe emplear con eficacia el capital de trabajo que integra a la empresa. Es evidente que hasta el departamento más insignificante tiene que Preservar y Mantener su propio capital de trabajo, así sean escritorios, teléfonos, equipos de cómputo, escobas, cortadoras de césped, útiles de aseo, etcétera; debido a esto los trabajos de PM tienen que estar considerados que se hacen en toda la empresa y no solo en la dirección de producción. La figura 5 nos proporciona la razón del por qué se le llama “Mantenimiento Productivo Total” ya que para obtener la calidad en toda la empresa es necesario que cada uno de sus departamentos, personas de cualquier nivel incluyendo proveedores tengan un comportamiento holístico.

En 1971, después de 20 años de esfuerzo, Nakajima puso en marcha en Japón lo que él llamó Mantenimiento Productivo Total (TPM, siglas en inglés) en el cual todos los departamentos quedaron obligados a realizar labores de PM que deben desarrollar los propios trabajadores de la empresa, esto hace necesario construir sobre el organigrama existente de la empresa y con autoridad Staff, una estructura para administrar el TPM. En la Figura 6 estamos considerando como ejemplo a la Dirección de Producción, en el entendido de que esto se repite en forma similar a las tres Direcciones restantes. La función Staff está mostrada en color verde. Es necesario aclarar que más del 90% del personal que ejecuta estas funciones es el mismo que ya pertenece a la empresa y el restante porcentaje lo ocupará nuevo personal generalmente especializado en el funcionamiento del TPM.

Con éstas ideas en mente situémonos en nuestra actualidad 2014 y vemos que a través de un poco más de treinta años las cosas han cambiado en forma exponencial.
En el TPM se considera que en toda la empresa existen activos que conservar, ya que hasta el último hombre tiene herramientas y algunos tipos de recursos a su cargo para desarrollar su trabajo; esa es la razón de ser del “Mantenimiento autónomo” pues como mencionamos, las computadoras, teléfonos, etcétera, también son activos de la empresa por lo que se espera que su costo de ciclo de vida (LCC) también produzca utilidades y deben ser atendidos desde sus primeros auxilios por el usuario. Con esto podemos concluir que lo que en 1950 se estaba haciendo solamente en las áreas de producción (PM) ahora se hace en toda la empresa (TPM).
Lo que a nuestro juicio fue el gran avance que proporcionó Nakajima a la industria mundial, es hacer del PM de un departamento de producción de una empresa que había demostrado proporcionar calidad a su producto, un TPM holístico con el cual hasta el último hombre tiene que desplegar un papel para el adecuado funcionamiento de ésta (incluyendo proveedores, clientes, usuarios etc.) y pondrá voluntariamente sus capacidades para conseguirlo, porque él a su vez se desarrolla como recurso humano de calidad.
Cursos recomendados






%252FImagen%252FRAMPREDYC-1730060420837.webp%3Falt%3Dmedia%26token%3D2634a7f0-988e-4022-b91f-382503e6e9db&w=3840&q=75)

Kaouru Ishikawa (1915-1989)

En 1947 fue otro de los industriales de alto nivel que recibieron las enseñanzas de Deming y como era un teórico de la administración, dedicó su tiempo a estudiar cómo mejorar la administración de sus industrias y la calidad de los productos japoneses, dedicándose a trabajar desde 1949 como consultor de empresas estudiando a fondo el modelo norteamericano y japonés en éstas áreas, heredando el desarrollo más importante que la industria mundial ha experimentado.
Por lo que respecta a la administración, hizo posible que los científicos descubrieran que el recurso humano es el “capital activo” más importante que existe en las empresas ya que consideró que el hombre por naturaleza es bueno y proactivo con lo que le interesa. Esto contrastaba con la forma que recomendaban los grandes industriales de Norteamerica, ya que las teorías de éstos al referirse al trabajador, eran de que debía obligársele a trabajar como un autómata; al menos estas eran las ideas que proporcionaban los trabajos de W. Taylor y Henry Fayol.
Por lo que atañe a la calidad, Ishikawua se inició con el uso de gráficas de control por muestreo y el empleo de la estadística con el concepto americano. Desarrolló un criterio muy adelantado que le permitió apoyar a su país para que perteneciera a la Internacional Standard Organización (ISO) llegando Kaoru a ser el presidente de la delegación japonesa.
Al igual que Nakajima, Ishikawua puso mucho interés en los Grupos de Trabajo PM desarrollando su propio concepto, los cuales empezaron a funcionar con muy buenos resultados en 1962, fecha en que se implantó en la Compañía de Telégrafos y Teléfonos Nippon el primer Círculo de Calidad. 17 años después se consideró que más de diez millones de trabajadores japoneses pertenecian a dichos grupos y se les llamó “Círculos de Calidad” porque estos integraron la calidad al proceso de producción.
Círculos de calidad
Se le llama círculo de calidad a un conjunto generalmente formado por cuatro a diez personas que voluntariamente contribuyen al desarrollo de la empresa en donde trabajan y en ésta labor son apoyados por la alta dirección. Los integrantes deben conocer lo mejor posible el trabajo que desarrollan en conjunto y los problemas que de éste se deriven con el objeto de reunirse preferiblemente cada semana. Debe entre ellos existir un líder, quien puede o no ser el supervisor oficial y es deseable que sea escogido por el grupo. El líder es auxiliado por la alta dirección a través de un facilitador que en nuestro caso pertenece al Comité TPM de Grupo (ver Figura 6) y el cual está muy preparado a nivel empresa en el funcionamiento de estos grupos ya que su principal labor es asegurarse que las soluciones propuestas vayan dirigidas a mejorar las condiciones de trabajo, aumentar la productividad y a producir satisfactores exigidos por el mercado al que son dirigidos.
Ishikawua recomendaba la utilización de lo que él llamó “siete herramientas básicas de la calidad”, tales como los diagramas de Pareto, de Dispersión, de Causa y efecto, etcétera; muchas de ellas fueron de su autoría.
Debemos considerar que El TPM es un sistema de administración diseñado para facilitar el desarrollo de la industria, (no solo el “mantenimiento” de sus máquinas), se apoya en la participación proactiva de todo el personal que compone la empresa incluyendo a los proveedores.
Conclusión
Espero que el estudio de éste articulo haya logrado interesar a mis lectores y los haya convencido de que el esfuerzo mundial por encontrar la forma de elaborar los miles de billones de satisfactorios o productos elaborados que exige nuestra vida en la Tierra, solo es posible a través de la efectividad de una industria mundial la cual radica en el “subsistema de productos eficientes” y no en el de “Equipos de trabajo eficientes”. Es conveniente enfatizar que aquí nos referimos a los productos que se elaboran por las empresas y no a las máquinas con las cuales se producen estos, lo que aclara “El Principio de Efectividad Industrial” que se refiere al “Equilibrio entre la calidad de la materia que integra el producto y la calidad del servicio que esta proporciona como sistema, durante su ciclo de vida útil”.

La efectividad de nuestras empresas no la vamos a conseguir nunca mientras sigamos dándole al mantenimiento un lugar equivocado. No señores. El mantenimiento desde el punto de vista ecológico es una rama de la Conservación y menciono la ecología por la razón que buscamos comprender la estructura y funcionamiento inherentes a los seres vivos en su medio ambiente, entonces debemos empezar apoyándonos en la Biología y de ahí en una de sus disciplinas; la Ecología, ya que ésta analiza los elementos naturales y humanos vinculados por la simbiosis que entre ellos existe (ríos, climas, plantas, animales, seres humanos etc.). Entre todos estos elementos el ser humano es especial porque tiene la capacidad de actuar inteligentemente para modificarlo con rapidez de acuerdo con sus intereses ya sean éstos en pro o en contra del sistema.
Una nueva materia que debe existir en nuestro plan de estudios es la “Teoría General de los Sistemas” pues estamos inmersos en un sistema cíclico y nuestro máximo interés debe ser el cómo cuidarlo.
Autor: Ing. Enrique Dounce Villanueva
Dinos qué te ha parecido el artículo
Artículos recomendados
Confiabilidad de Bombas Centrífugas

¿En qué consiste una academia de mantenimiento?

Modelo de Confiabilidad con Metodología RAM para un sistema de bombeo de agua de inyección

Administración de mantenimiento

Publica tu artículo en la revista #1 de Mantenimiento Industrial
Publicar un artículo en la revista es gratis, no tiene costo.
Solo debes asegurarte que no sea un artículo comercial.
¿Qué esperas?
O envía tu artículo directo: articulos@predictiva21.com
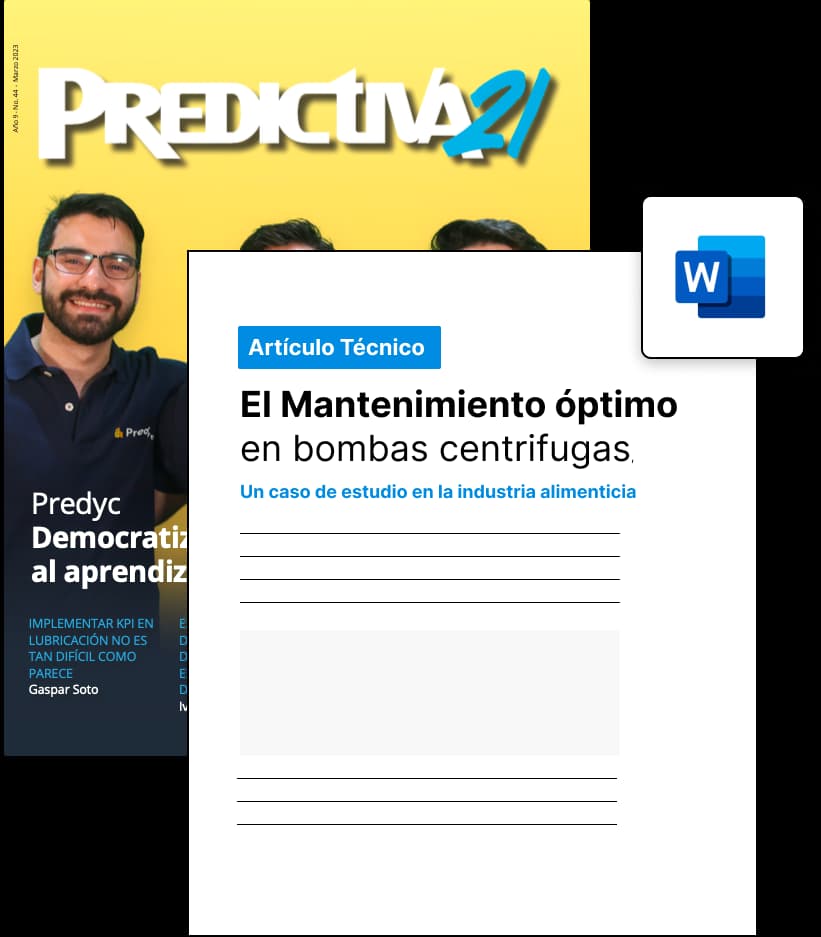
Las Revoluciones Industriales en el Mundo (II Parte)
Articulo 10 de marzo de 2020Tercera revolución industrial
Su desarrollo se sitúa Japón entre los años 1950-1971 y recordemos que éste país quedó destrozado como resultado de la guerra y fue ocupado por las fuerzas norteamericanas en septiembre de 1946 por el Comando Supremo de las Potencias Aliadas (SCAP, siglas en inglés), quien nombró al General estadounidense Douglas MacArthur como responsable de establecer un programa de desarrollo con especialistas norteamericanos para la reconstrucción de esta nación. Dentro de éstos, los más relevantes fueron: W. Edwards Deming, Walter Andrew Stewart y Joseph Moses Juran.
Desde los primeros años de su estancia en Japón se dieron a conocer con los máximos niveles industriales del país compartiendo sus conocimientos en estadística, en calidad, en grupos PM, en logística, etcétera. Empezaron en ese nivel debido a que las vivencias de los norteamericanos en el lapso de 1939 a 1945 les mostraron la incongruencia de no preparar a los propietarios y altos niveles con poder de decisión y su compromiso con el cliente. En Japón podían hacerlo porque para la Unión de Científicos e Ingenieros Japoneses (UCIJ) y los altos niveles de la industria ésta preparación realmente despertó un interés vital, además de llenar sus expectativas de un promisorio futuro próximo y casar plenamente con la idiosincrasia de su pueblo.
Sigamos los pasos del Dr. Deming durante su larga estancia por el Japón (1950 - 1980) en donde llegó a adquirir un gran reconocimiento y estimación. Los japoneses le mostraron su aprecio instituyendo en 1951 el “Premio Deming” (una medalla de plata con su efigie).
Una de sus grandes contribuciones es el “control estadístico de proceso” que facilita el diagnóstico de la calidad de funcionamiento de la máquina. Fue común que durante sus conferencias recomendara que la calidad no debiera medirse sobre el producto terminado, sino debería formar parte del proceso de producción y que ésta se detectara a través del uso frecuente de la estadística. También influía en el establecimiento de los “Grupos de trabajo”, y la aplicación de la logística.
Deming orientó a los japoneses acerca de que antes de hacer un producto, se investigara el mercado para conocer lo que éste demandaba y de ahí establecer los parámetros que regirían los procesos de producción. Deming siguió trabajando muy estrechamente con los japoneses durante treinta años a través de los cuales hizo de esa nación el emporio que actualmente es y regresó a EUA debido a la fama que en su patria adquirió gracias a las investigaciones que sobre “El milagro japonés” hizo la periodista norteamericana Clare Crawford Mason.
Seiichi Nakajima (1928)

En 1950 era un alto funcionario del Instituto Japonés de Mantenimiento de la planta (JIMP) y fue uno de los muchos industriales de alto nivel que recibieron las enseñanzas de Deming sobre el Mantenimiento Productivo Norteamericano PM y con base en sus observaciones desarrolló el Mantenimiento Productivo Total. En 1971 lo introdujo en algunas industrias japonesas iniciando con ello el boom de dicha industria y en pocos años todo el mundo apreciaba la calidad de los productos de ese país. En 1987 dirigió durante dos semanas una misión nipona a los Estados Unidos para dar a conocer su TPM ya que existían muchos industriales norteamericanos con deseos de establecerlo; este efecto se ha replicado en el ámbito mundial con muy buenos resultados. En la actualidad el TPM nos demuestra cómo todo el personal de la empresa incluyendo sus proveedores y distribuidores está involucrado en la productividad.
Concepto del mantenimiento productivo (PM)
Para 1939 las empresas tenían una organización simple, generalmente una dirección general con tres o cuatro subdirecciones o gerencias subordinadas para encargarse de las funciones primarias; producir, vender, administrar y desarrollar las finanzas. El Mantenimiento Productivo (PM) se originó en el área de Producción debido a que ya existían en ella buenos conceptos sobre la división del trabajo, la ciencia y la administración aplicadas a la industria, el uso de la estadística, la búsqueda de la calidad del producto, etcétera; pero estos conocimientos por razón natural no existían en las áreas de ventas, administración o finanzas. La figura 3 nos muestra un organigrama hipotético de una empresa norteamericana en 1950 en la que observamos que solo en la dirección de producción se tiene establecido el PM pues se suponía que solo en esta era necesaria dicha actividad.

Recordemos que desde 1919 los señores, W. Edwards Deming, Walter A. Shewhart y Joseph Juran entre otros, estuvieron directamente trabajando para las industrias norteamericanas aportando soluciones a múltiples problemas estableciendo o cambiando procesos tanto técnicos como administrativos. Cuando en 1947 dichas personas arribaron al Japón, además de su gran preparación, llegaron con la idea de que el desarrollo del personal en la industria debería ser aplicado a todos sus integrantes, con énfasis en los dueños y directores generales de las empresas. Las otras direcciones como las de finanzas, administración y ventas no vamos a considerarlas en éste subtema, puesto que el fenómeno se desarrolló solo en producción.
Cuando Nakajima en 1950 inició sus estudios de PM desde Japón, encontró que la industria americana estaba organizada de manera similar a la mostrada en la Figura 3. Ya trabajaban los supervisores y obreros con los grupos de trabajo (GTPM) y ya se empleaba normalmente la Logística. Para facilitar nuestra percepción analicemos solamente la Gerencia de Producción de la mencionada figura y desarrollemos su organigrama (ver figura 4); esto fue lo que encontró Seiichi Nakajima cuando empezó a desarrollar sus estudios del Mantenimiento Productivo norteamericano.

Concepto del mantenimiento productivo total (TPM por sus siglas en inglés)
La labor de cualquier industria es la de producir en forma conjunta como un solo equipo, como una orquesta, en donde cada dirección, gerencia, departamento, proveedor o persona, debe esforzarse en forma coordinada para obtener beneficios, para lo cual debe emplear con eficacia el capital de trabajo que integra a la empresa. Es evidente que hasta el departamento más insignificante tiene que Preservar y Mantener su propio capital de trabajo, así sean escritorios, teléfonos, equipos de cómputo, escobas, cortadoras de césped, útiles de aseo, etcétera; debido a esto los trabajos de PM tienen que estar considerados que se hacen en toda la empresa y no solo en la dirección de producción. La figura 5 nos proporciona la razón del por qué se le llama “Mantenimiento Productivo Total” ya que para obtener la calidad en toda la empresa es necesario que cada uno de sus departamentos, personas de cualquier nivel incluyendo proveedores tengan un comportamiento holístico.

En 1971, después de 20 años de esfuerzo, Nakajima puso en marcha en Japón lo que él llamó Mantenimiento Productivo Total (TPM, siglas en inglés) en el cual todos los departamentos quedaron obligados a realizar labores de PM que deben desarrollar los propios trabajadores de la empresa, esto hace necesario construir sobre el organigrama existente de la empresa y con autoridad Staff, una estructura para administrar el TPM. En la Figura 6 estamos considerando como ejemplo a la Dirección de Producción, en el entendido de que esto se repite en forma similar a las tres Direcciones restantes. La función Staff está mostrada en color verde. Es necesario aclarar que más del 90% del personal que ejecuta estas funciones es el mismo que ya pertenece a la empresa y el restante porcentaje lo ocupará nuevo personal generalmente especializado en el funcionamiento del TPM.

Con éstas ideas en mente situémonos en nuestra actualidad 2014 y vemos que a través de un poco más de treinta años las cosas han cambiado en forma exponencial.
En el TPM se considera que en toda la empresa existen activos que conservar, ya que hasta el último hombre tiene herramientas y algunos tipos de recursos a su cargo para desarrollar su trabajo; esa es la razón de ser del “Mantenimiento autónomo” pues como mencionamos, las computadoras, teléfonos, etcétera, también son activos de la empresa por lo que se espera que su costo de ciclo de vida (LCC) también produzca utilidades y deben ser atendidos desde sus primeros auxilios por el usuario. Con esto podemos concluir que lo que en 1950 se estaba haciendo solamente en las áreas de producción (PM) ahora se hace en toda la empresa (TPM).
Lo que a nuestro juicio fue el gran avance que proporcionó Nakajima a la industria mundial, es hacer del PM de un departamento de producción de una empresa que había demostrado proporcionar calidad a su producto, un TPM holístico con el cual hasta el último hombre tiene que desplegar un papel para el adecuado funcionamiento de ésta (incluyendo proveedores, clientes, usuarios etc.) y pondrá voluntariamente sus capacidades para conseguirlo, porque él a su vez se desarrolla como recurso humano de calidad.
Cursos recomendados






%252FImagen%252FRAMPREDYC-1730060420837.webp%3Falt%3Dmedia%26token%3D2634a7f0-988e-4022-b91f-382503e6e9db&w=3840&q=75)

Kaouru Ishikawa (1915-1989)

En 1947 fue otro de los industriales de alto nivel que recibieron las enseñanzas de Deming y como era un teórico de la administración, dedicó su tiempo a estudiar cómo mejorar la administración de sus industrias y la calidad de los productos japoneses, dedicándose a trabajar desde 1949 como consultor de empresas estudiando a fondo el modelo norteamericano y japonés en éstas áreas, heredando el desarrollo más importante que la industria mundial ha experimentado.
Por lo que respecta a la administración, hizo posible que los científicos descubrieran que el recurso humano es el “capital activo” más importante que existe en las empresas ya que consideró que el hombre por naturaleza es bueno y proactivo con lo que le interesa. Esto contrastaba con la forma que recomendaban los grandes industriales de Norteamerica, ya que las teorías de éstos al referirse al trabajador, eran de que debía obligársele a trabajar como un autómata; al menos estas eran las ideas que proporcionaban los trabajos de W. Taylor y Henry Fayol.
Por lo que atañe a la calidad, Ishikawua se inició con el uso de gráficas de control por muestreo y el empleo de la estadística con el concepto americano. Desarrolló un criterio muy adelantado que le permitió apoyar a su país para que perteneciera a la Internacional Standard Organización (ISO) llegando Kaoru a ser el presidente de la delegación japonesa.
Al igual que Nakajima, Ishikawua puso mucho interés en los Grupos de Trabajo PM desarrollando su propio concepto, los cuales empezaron a funcionar con muy buenos resultados en 1962, fecha en que se implantó en la Compañía de Telégrafos y Teléfonos Nippon el primer Círculo de Calidad. 17 años después se consideró que más de diez millones de trabajadores japoneses pertenecian a dichos grupos y se les llamó “Círculos de Calidad” porque estos integraron la calidad al proceso de producción.
Círculos de calidad
Se le llama círculo de calidad a un conjunto generalmente formado por cuatro a diez personas que voluntariamente contribuyen al desarrollo de la empresa en donde trabajan y en ésta labor son apoyados por la alta dirección. Los integrantes deben conocer lo mejor posible el trabajo que desarrollan en conjunto y los problemas que de éste se deriven con el objeto de reunirse preferiblemente cada semana. Debe entre ellos existir un líder, quien puede o no ser el supervisor oficial y es deseable que sea escogido por el grupo. El líder es auxiliado por la alta dirección a través de un facilitador que en nuestro caso pertenece al Comité TPM de Grupo (ver Figura 6) y el cual está muy preparado a nivel empresa en el funcionamiento de estos grupos ya que su principal labor es asegurarse que las soluciones propuestas vayan dirigidas a mejorar las condiciones de trabajo, aumentar la productividad y a producir satisfactores exigidos por el mercado al que son dirigidos.
Ishikawua recomendaba la utilización de lo que él llamó “siete herramientas básicas de la calidad”, tales como los diagramas de Pareto, de Dispersión, de Causa y efecto, etcétera; muchas de ellas fueron de su autoría.
Debemos considerar que El TPM es un sistema de administración diseñado para facilitar el desarrollo de la industria, (no solo el “mantenimiento” de sus máquinas), se apoya en la participación proactiva de todo el personal que compone la empresa incluyendo a los proveedores.
Conclusión
Espero que el estudio de éste articulo haya logrado interesar a mis lectores y los haya convencido de que el esfuerzo mundial por encontrar la forma de elaborar los miles de billones de satisfactorios o productos elaborados que exige nuestra vida en la Tierra, solo es posible a través de la efectividad de una industria mundial la cual radica en el “subsistema de productos eficientes” y no en el de “Equipos de trabajo eficientes”. Es conveniente enfatizar que aquí nos referimos a los productos que se elaboran por las empresas y no a las máquinas con las cuales se producen estos, lo que aclara “El Principio de Efectividad Industrial” que se refiere al “Equilibrio entre la calidad de la materia que integra el producto y la calidad del servicio que esta proporciona como sistema, durante su ciclo de vida útil”.

La efectividad de nuestras empresas no la vamos a conseguir nunca mientras sigamos dándole al mantenimiento un lugar equivocado. No señores. El mantenimiento desde el punto de vista ecológico es una rama de la Conservación y menciono la ecología por la razón que buscamos comprender la estructura y funcionamiento inherentes a los seres vivos en su medio ambiente, entonces debemos empezar apoyándonos en la Biología y de ahí en una de sus disciplinas; la Ecología, ya que ésta analiza los elementos naturales y humanos vinculados por la simbiosis que entre ellos existe (ríos, climas, plantas, animales, seres humanos etc.). Entre todos estos elementos el ser humano es especial porque tiene la capacidad de actuar inteligentemente para modificarlo con rapidez de acuerdo con sus intereses ya sean éstos en pro o en contra del sistema.
Una nueva materia que debe existir en nuestro plan de estudios es la “Teoría General de los Sistemas” pues estamos inmersos en un sistema cíclico y nuestro máximo interés debe ser el cómo cuidarlo.
Autor: Ing. Enrique Dounce Villanueva
Dinos qué te ha parecido el artículo
Artículos recomendados
Cursos de Mantenimiento Industrial con Certificado

Paradas de mantenimiento: pasos para realizarla

Cambios en la norma ISO 14224:2016 - Recolección e intercambio de data de confiabilidad y mantenimiento para equipos - Categorías de mantenimiento

La gente apasionada lo hace diferente

Publica tu artículo en la revista #1 de Mantenimiento Industrial
Publicar un artículo en la revista es gratis, no tiene costo.
Solo debes asegurarte que no sea un artículo comercial.
¿Qué esperas?
O envía tu artículo directo: articulos@predictiva21.com
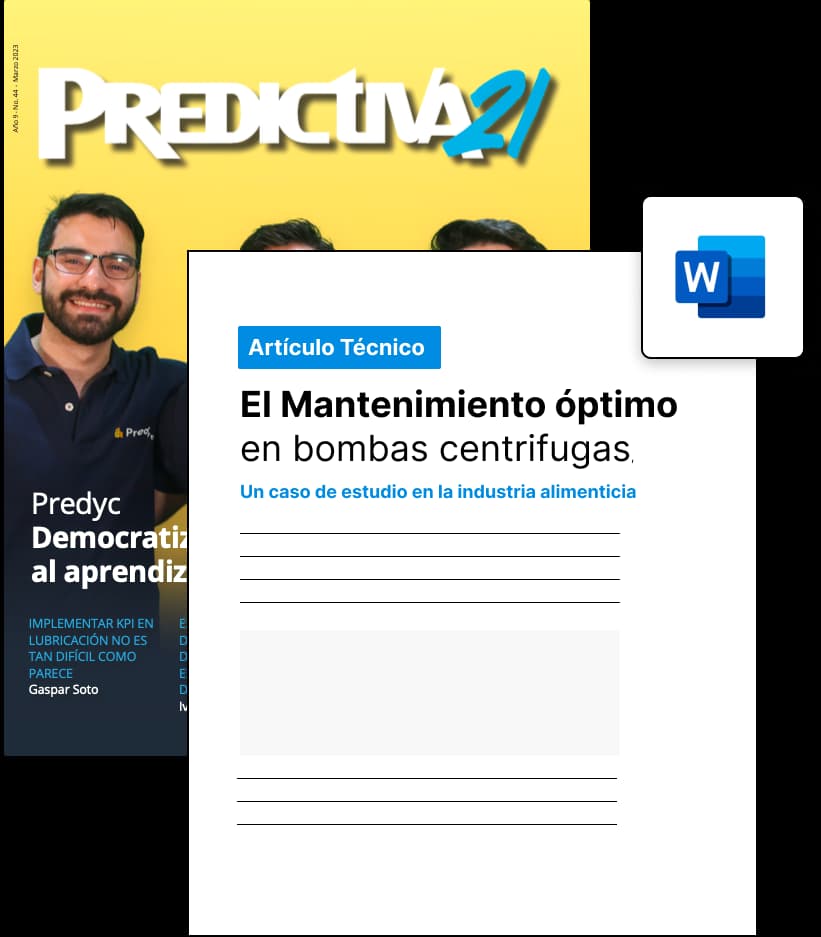