Análisis de Causa Raíz aplicado a fallas en sellos mecánicos de bombas
Articulo19 de noviembre de 2019
Resumen
El propósito de este artículo es exponer, en forma sencilla, un proceso de análisis de falla disciplinado (ACR) a través del entendimiento de hasta dónde debemos extender o definir los límites de control del análisis, con la finalidad de abarcar los elementos necesarios para lograr las acciones correctivas que eliminen el problema que originó la falla o lo lleve a niveles tolerables en función de sus consecuencias.
Palabras claves: Falla, Modo y Mecanismo de Falla, Evento, Hecho, Hipótesis, Causa Raíz.
1. Bombas. Fallas frecuentes
La bomba es una máquina “generadora” que absorbe energía mecánica proveniente de un motor eléctrico, térmico u otros, transmitiéndola a un fluido y transformándola en energía hidráulica, que a su vez, permite que el fluido pueda ser transportado de un lugar a otro, a un mismo nivel o a diferentes niveles y a diferentes velocidades, presiones y caudales.
Las fallas en las bombas son frecuentemente ocasionadas por los ingenieros y operadores de la planta que no reconocen las limitaciones inherentes de capacidad en las bombas. Cuando se opera una bomba con flujo alejado de su Punto de Máxima Eficiencia (B.E.P., siglas en inglés), se producen anomalías hidráulicas en la carcasa y el impulsor. Estas anomalías, que ocurren en todas las bombas, pueden ocasionar inestabilidad hidráulica, impulsos de vibración, y flexiones del eje, trayendo como resultado desgaste acelerados, fallas prematuras y frecuentes de impulsores, cojinetes y sellos; los cuales, actúan bajo estas condiciones como fusibles mecánicos, siendo el resultado final de una autorcadena de acontecimientos. Por lo que, idealmente, el punto de diseño y de operación deben mantenerse cercanos al Punto de Mejor Eficiencia (B.E.P.). Ver fig. 1.

Fuente: El autor
Dentro de las fallas frecuentes en bombas se pueden distinguir tres tipos de problemas: hidráulicos inherentes al sistema, hidráulicos inherentes a la bomba y problemas mecánicos.
Los problemas hidráulicos inherentes al sistema son el resultado de fallas en el diseño, procedimientos deficientes de instalación y colocación incorrecta de la tubería.
Los problemas hidráulicos inherentes a la bomba surgen cuando esta no puede funcionar de acuerdo con las especificaciones de capacidad, carga y eficiencia.
En cuanto a los problemas mecánicos, estos se refieren a desperfectos mecánicos, que se manifiestan mediante síntomas como ruido, vibraciones, sobrecalentamiento y pueden llevar a originar problemas de mal funcionamiento hidráulico.
Algunos de los eventos típicos que evidencian las fallas en las bombas rotativas son:
- No entrega líquido.
- Entrega menos liquido del esperado.
- Pierde ceba después del arranque. - No levanta presión.
- Consume demasiada potencia.
- Presenta excesivo ruido.
- Presenta excesiva vibración.
- Presenta alta temperatura en la zona de cojinetes y sellos.
- Presenta excesiva fuga por empaques o sellos mecánicos.
Estos eventos, que reflejan un mal funcionamiento en la bomba, llaman nuestra atención debido a la pérdida parcial o total de las funciones de la misma, bajo las especificaciones establecidas en su contexto operacional, tal como la pérdida de su función principal (entrega de un caudal a una presión requerida), que reflejará un impacto importante sobre el proceso; así como también, son importantes las pérdidas de otras funciones como las de contención (fugas al ambiente), que cobran vital relevancia en sistemas que manejan fluidos altamente tóxicos o volátiles y requieren especificaciones de seguridad exigentes.
2. Sellos mecánicos - Fallas prematuras
Los sellos son componentes de las bombas que evitan que un fluido escape al exterior de la misma a través de las holguras o claros entre el eje y la carcasa, controlando las emisiones dentro de los rangos de diseño establecidos. Es un elemento que requiere mucha atención en la industria química, petroquímica y refinerías, entre otras.
En la actualidad existe diversidad de sellos mecánicos que dependen de una aplicación en particular. Sin embargo, su configuración básica está dispuesta de una parte rotativa y una estacionaria, las cuales están formadas por:
a. El Cabezal del Sello: es el ensamble de varios componentes, tal como, el anillo primario (que está en contacto con el asiento, formando ambos el sellado primario), sellantes secundarios. (o’rings, cuñas, fuelles, etc.), sistema de compensación de desgaste (resortes) y sistema de arrastre (retenedores, componentes metálicos misceláneos). Este cabezal es el lado flexible del sello, que se acomoda a ligeros movimientos axiales y radiales del equipo.
b. El Asiento del Sello: es el anillo de desgaste removible en la brida si es estacionario o, en la camisa, si es rotativo.

Fuente: El autor
Estos contienen los elementos que forman:
c. El sellado primario, formado por el anillo primario y el asiento, conocido comúnmente como las caras de contacto del sello. Estas caras están fabricadas con materiales como carburo de silicio, carburo de tungsteno, carbón grafitado y cerámica (óxido de aluminio).
d. El sellado secundario, formado por los elementos los empaques (o´rings, empaques grafitados, etc.) que evitan la fuga de las partes del sello con el eje y la brida.
Teóricamente, el sello debe funcionar controlando las emisiones a la atmósfera hasta que uno de sus componentes pierda su función (falla el sellado), en el primario se desgastan y/o fracturan las caras y en el secundario se deforman, se degradan los elementos de empaques.
No obstante, en la práctica observamos que en 80% de los casos, los sellos fallan antes de cumplir con su ciclo de vida.
Las mayores causas de estas fallas prematuras son:
- Diseño y selección inadecuado del sello.
- Instalación incorrecta del sello.
- Mala operación, mantenimiento o funcionamiento inadecuado de los sistemas auxiliares del sello, tales como, lubricación, fluido amortiguador / barrera, venteos, etc.
- Problemas inherentes al sistema de bombeo, como inestabilidades hidráulicas (asociadas a diseño / selección / operación de la bomba), anomalías mecánicas (relacionadas con instalación / mantenimiento de la bomba).
- Cambios en las condiciones de servicio (Contexto Operacional), respecto a las especificadas del diseño original.
En la mayoría de los casos los usuarios o custodios centran su atención en la falla del componente -en este caso del sello mecánico- y concluyen que requieren un sello más robusto que se adapte a su condición de operación (Severa), desviada de su contexto operacional actual, lo que trae como consecuencia mayores costos en la adquisición de partes y repuestos, afectando notablemente el presupuesto de mantenimiento y logrando, solo en el mejor de los casos, prolongar la ocurrencia de la falla. Por tal motivo, debe realizarse un análisis integral del proceso para identificar aquellos factores que contribuyen a la ocurrencia de la falla.
3. Ejemplo de ACR en falla de selllos mecánicos en bombas centrífugas
El proceso de Análisis Causa Raíz persigue, no solo identificar las causas de las fallas, es también un proceso cíclico de mejora continua que busca corregir las causas de las fallas y mejorar el proceso, como se muestra en la figura No. 3:

Fuente: El autor
Desarrollemos entonces un ejemplo ACR para un caso de “Falla de una bomba centrífuga multietapas por fugas en los sellos mecánicos”, empleando un proceso disciplinado de análisis con el uso de un Árbol lógico de Fallas.
El primer paso es preparar el análisis:
• Definir el problema o evento a evitar estableciendo el Evento Tope, en este caso “Paro automático de la bomba P-102”. Es recomendable indicar si el paro fue automático (activación de una protección), manual (paro realizado por el operador) o súbito (no representado en las dos anteriores). Esto facilitará la identificación de los hechos y poder emitir hipótesis basados en los posibles mecanismos de fallo de estas.
• Estimar el impacto del evento en el negocio e identificar las oportunidades. Estableciendo los costos totales (pérdida de producción, costos de refacciones e insumos, mano de obra, servicios, etc.) de la ocurrencia o ocurrencias de este evento y su impacto en el presupuesto anual de mantenimiento y en el negocio; dando visibilidad del impacto de los eventos repetitivos o esporádicos en términos económicos.
• Recabar información del equipo y su función en el proceso. Reunir información de manuales del equipo, del sistema o planta, registros históricos de parámetros operacionales, reportes técnicos, mantenimiento predictivo, preventivo o correctivo, avisos de averías, datos de fallas, etc. Usar herramientas, tales como: Contexto Operacional, diagramas de Entrada Proceso Salida (EPS), diagramas Funcionales, etc., para procesar la información.
El segundo paso consiste en recabar la información de evento:
• Establecer el Equipo Natural de Trabajo (ENT). Es importante formar un equipo conformado por personas asociadas a la gestión del activo, de diferentes departamentos y disciplinas, para asegurar distintas visiones del evento, lo cual contribuirá a obtener una mayor perspectiva del evento, aportando una solución integral. Un ENT básico, estará formado por un Facilitador (asesor metodológico), Operador (Conocedor del funcionamiento de los equipos y su impacto en el negocio), Mantenedor (conocedor de las políticas y técnicas de mantenimiento de los equipos), Programador (visión sistémica de la actividad), Especialistas (expertos en áreas específicas como Cadena de Suministro, Calidad, SHA, Recursos Humanos, Finanzas, Mercadeo y Ventas, Proveedor de la Tecnología, entre otros).
• Levantar la información, las evidencias y la secuencia de evento utilizando herramientas como las Líneas de Tiempo, para discriminar tiempo y etapas del evento, que permitan comprender en forma deductiva el desarrollo histórico del mismo.
El tercer paso, comprende el desarrollar del árbol lógico deductivo:
• Representar la lógica del evento no deseado, donde se muestran todos los factores causales en sus tres niveles de fallas, tales como la falla física (avería de componentes), el error humano (interacción humana inadecuada) y las causas raíces (causas latentes por carencias, desviaciones u omisiones organizacionales).
En este paso, tomamos el enunciado del Evento Tope, redactado en el paso No.1, (este puede ser revisado y mejorado por el ENT), seguidamente respondiendo a la pregunta: ¿Cómo puede fallar?, describimos los Hechos (que corresponden a los modos de fallo, que evidencian la ocurrencia del evento), como por ejemplo, “atascamiento súbito, eje partido, fugas, alta vibración, alta temperatura, baja presión, etc.”. Con lo anterior enmarcamos el evento en lo que llamamos la caja superior del análisis.
Cuando tenemos múltiples Hechos, el ENT deberá soportar estos con evidencias a través de la investigación y manejo de datos reales, tales como registros de paros, reparaciones, informes de producción, etc. y entrevistas al personal involucrado con la gestión del equipo. En función de optimizar tiempo y recursos, se jerarquizan los hechos a través del uso de diversas técnicas, por ejemplo, usando estadística de fallas, registros de producción, costos, etc., y se asignan porcentajes de importancia a cada hecho, en base a un criterio acordado por el ENT, que represente las mayores consecuencias o impacto al negocio, lo cual permitirá iniciar y avanzar, con el hecho que aporte mayor influencia.
Una vez jerarquizados los hechos, iniciamos con el de mayor impacto, nuevamente empleando la pregunta ¿Cómo puede fallar? y comenzamos con el proceso de generar Hipótesis, que representen los mecanismos de fallo, como por ejemplo, “Desgaste (Erosivo, Adhesivo, Oxidación o Corrosión) o Fatiga”. Estas hipótesis deberán ser validadas a través de métodos de verificación, que confirmen o refuten su ocurrencia. Estas herramientas pueden ser entrevistas al personal, reportes de inspección directa, manejo de datos (reportes de reparaciones, calibraciones, control de calidad, etc.), uso de tecnologías de diagnósticos disponibles; tales como pruebas, ensayos y/o exámenes de laboratorio (Exámenes Métalográficos, Mecánicos y/o Químicos a componentes fallados), informes de inspecciones técnicas (Análisis de Vibración, Análisis de Aceite, Termografía, Ultrasonido, etc.). En casos complejos pueden emplearse metodologías como la de los 5 Porqué, Ishikahua, etc., para simplificarlo a niveles manejables. De esta forma se irá bajando de nivel hasta llegar a los límites de control del ENT (ver figura No. 4).

Fuente: El autor
En este punto, una vez verificadas y validadas las Hipótesis (convertidas a Hechos), se llega a un nivel donde la pregunta se transforma en: ¿Por qué falló? En este momento comenzamos a identificar la aparición de la falla física, el error humano y las causas raíces que desencadenaron los eventos que eventualmente condujeron a la falla, pudiendo introducirse durante el proceso de diseño, manufactura o uso (instalación, operación o mantenimiento), tal como se muestra en el ejemplo de la figura No. 4.
Finalmente, se establece el plan de acción, que persigue eliminar las causas raíces identificadas a través de la ejecución de las acciones. También debe establecerse un sistema de medición (KPI´s), para evaluar el logro de las acciones y, en caso de no alcanzar los objetivos esperados, se revalúa el proceso y se realizan los ajustes y las mejoras necesarias.
Debido a que pueden existir restricciones de niveles de aprobación, presupuesto, tecnología disponible, etc., que pudieran convertirse en barreras para la implementación del plan, pueden emplearse técnicas de Jerarquización de Eventos, aplicando una Matriz de Prioridades, basada en Complejidad y Consecuencias (ver figura No. 5), de tal forma de comenzar a implementar el plan, con aquellas acciones de mayores consecuencias, pero menor complejidad en su solución, para de esta forma obtener victorias tempranas que contribuirán a incentivar aprobaciones e inversiones el resto del plan.

Fuente: Curso técnicas de Análisis de fallas centradas en confiabilidad, con énfasis en causa raíz. 2005. De Engineering reliability and Management - ER&M
Cursos recomendados






%252FImagen%252FRAMPREDYC-1730060420837.webp%3Falt%3Dmedia%26token%3D2634a7f0-988e-4022-b91f-382503e6e9db&w=3840&q=75)

Conclusiones
a. Las Bombas son equipos susceptibles a cambios severos de sus condiciones de operación, tal como las inestabilidades hidráulicas que súbita o progresivamente afectarán la integridad de sus componentes mecánicos. Igualmente las desviaciones en la correcta selección, instalación y mantenimiento ocasionan problemas de origen mecánicos, donde algunos de ellos eventualmente también podrían desarrollar problemas hidráulicos.
b. En la actualidad, los sellos mecánicos son excelentes elementos de contención para evitar los escapes “no controlados” a la atmósfera en los procesos de manejo de fluidos; sin embargo, requieren de condiciones mínimas de instalación, mantenimiento y operación que garanticen la vida esperada del mismo, donde la intervención humana juega un papel pimportante.
c. El uso de procesos de análisis disciplinados como el ACR y el empleo de las tecnologías disponibles para soportar este proceso de pensamiento empleando la validación de hipótesis, contribuyen al logro de resultados exitosos en el control de fallas y la gestión del mantenimiento.
Glosario de términos
A continuación se lista un glosario de términos relevantes empleados en este documento:
• Análisis Causa Raíz (ACR): Metodología empleada para analizar e identificar las causas que provocan los eventos no deseados, contribuyendo a determinar medidas preventivas que minimicen sus consecuencias, disminuyan la probabilidad de ocurrencia o en el mejor de los casos, que el evento estudiado no se produzca de nuevo.
• Causa de Falla: La circunstancia durante el diseño, la manufactura o el uso que conlleva a una falla. Fuente: STD ISO14224.
• Causa Raíz: También conocida como causa latente, es el nivel más bajo del Análisis, donde se identifican aquellos factores que contribuyeron directamente con el problema, típicamente están representada en las carencias o deficiencias de la organización, que de no ser corregidas, el evento no deseado continuará ocurriendo.
• Consecuencia de la Falla: Es lo que experimenta el dueño de un activo como resultado de la ocurrencia de un modo de falla, manifestado en el impacto a la Seguridad, la Salud, el Ambiente, la pérdida de Producción, y/o los altos costos de Mantenimiento.
• Contexto Operacional: Es la descripción de las circunstancias específicas en las cuales opera un activo físico o sistema, está escrito en una forma narrativa que incluye la descripción exacta del activo y provee la información necesaria y con suficiente detalle sobre los factores (el entorno, la tecnología, estándares, la operación, etc.) que contribuyen e influyen en el proceso general.
• Equipo Natural de Trabajo (ENT): Conformado por un conjunto de personas de diferentes departamentos, con variadas disciplinas y funciones, buscando sinergia para lograr un objetivo en común y producir un mejor e integral resultado para la organización.
• Error Humano: También conocida como causa intermedia, es la interacción inadecuada de las personas durante su participación directa o indirecta en una actividad o proceso, que contribuye con la aparición de la falla; a veces se puede atribuir a malas prácticas de las personas involucradas.
• Evento Tope: Es el último elemento en la secuencia de la línea – tiempo. Representa al evento no deseado, que justifica económicamente el análisis y las acciones para eliminarlo.
• Falla: Es la terminación de la habilidad de un sistema/equipo/parte para realizar una función requerida. Fuente: STD ISO14224.
• Falla Física: También conocida como causa directa, son típicamente representadas por elementos, componentes o partes; que al reemplazarlos, se elimina de forma temporal el problema.
• Falla Funcional: Es la incapacidad de un elemento (o el equipo que lo contiene) para cumplir con un estándar de rendimiento especificado. Fuente: Nowlan y Heap (1960).
• Falla Potencial: Es una condición física identificable que indica que una falla funcional es inminente. Fuente: Nowlan y Heap (1960).
• Hechos: Son los modos en que se presenta la falla, es lo visible que aparece luego de la falla funcional.
• Hipótesis: Es una suposición hecha a partir de unos datos, que sirve de base para iniciar una investigación o una argumentación. Una hipótesis es un enunciado no verificado, que una vez confirmado o refutado dejará de ser hipótesis y se convertirá en hecho o no.
• Indicador Clave de Rendimiento (KPI): Los KPI (Key Performance Indicator, por sus siglas en inglés) es una medida del nivel del rendimiento de un proceso. El valor del indicador está directamente relacionado con un objetivo fijado previamente y normalmente se expresa en valores porcentuales.
• Jerarquizar: Establecer un orden de prioridad, descendente o ascendente en función de criterios basados en categorías, cualidades, características, valor, etc.
• Mecanismo de Falla: El proceso físico, químico u otro, que conlleva a una falla. Fuente: STD ISO14224.
• Modo de Falla: Un evento único, que causa una falla funcional. Fuente SAE: STD JA1011. Es el modo observado de la falla. Fuente: STD ISO14224.
Referencias
- (1) KENNERH J. MCNAUGTON. Bombas. Selección, Uso y Mantenimiento. México. McGRAW-HILL. N° 373 p. 1999.
- (2) ENGINEERING RELIABILITY AND MANAGEMENT. Fundamentos de Selección, Operación y Mantenimiento de Bombas. Curso. 2005.
- (3) ANSI/API Standard 610. Centrifugal Pumps for Petroleum, Petrochemical and Natural Gas Industries. 10th Edition. 2004.
- (4) INSTITUTO DE ENERGÍA Y TERMODINÁMICA. Curso de Bombas. Compañía de Sudamericana de Seguros S.A. Nº Pág. 8. 2002.
- (5) J.D. SUMMERS-SMITH. Mechanical Seal Practice for Improved Performance, Londres; editorial MEP, N° 216 p. 1992.
- (6) J.D. SUMMERS-SMITH. An Introductory Guide To Industrial Tribology. Londres; editorial MEP, N° 201 p. 1994.
- (7) ISO 14224. Petroleum, petrochemical and natural gas industries — Collection and exchange of reliability and maintenance data for equipment. Segunda edición 2006-12-15.
- (8) SAE JA1011. Criterios de Evaluación para Procesos de Mantenimiento Centrado en Confiabilidad. Emitida AGO1999.
- (9) SAE JA1011. Una Guía para la Norma de Mantenimiento Centrado en Confiabilidad (MCC). Emitida ENE2002.
- (1) ROBERT J. LATINO, SR. VP, RELIABILITY CENTER, INC. Calidad del Proceso y el Análisis de Causa Raíz Parte 1, 2 y 3. Reliability Center, Inc. N° pag. 7. 2001.
- (2) WOODHOUSE PARTNERSHIP LTD. Análisis Causa - Raíz. Curso. CIED. Tamare.1998.
- (3) ENGINEERING RELIABILITY AND MANAGEMENT - ER & M. Técnicas de Análisis de Falla Centradas en Confiabilidad, con Énfasis en Causa Raíz. Curso. 2005.
Autor: Ing./MSc. Tibaldo Alfredo Díaz Molina
Venezuela
Especialista en Ingeniería de Mantenimiento, Confiabilidad Operacional y Gestión de Activos
Correo: tibaldodiaz@gmail.com
Síntesis curricular del autor:
Técnico Superior Universitario e Ingeniero Mecánico con Maestría en Gerencia de Empresas y 30 años de experiencia en Ingeniería de Mantenimiento, Confiabilidad Operacional y Gestión de Activos, en la industria del petrolera y minera. Consultor y facilitador acreditado como Agente Capacitador Externo, por la STPS de México y Certificado por COMPECER en gestión de mantenimiento, análisis de riesgo y análisis causa raíz.
Dinos qué te ha parecido el artículo
Artículos recomendados
El monitoreo de condición como generador de conocimientos de la Gestión de Activos

Certificación ISO 55000

Análisis Costo Riesgo Beneficio para la selección de conductores de una Planta de Generación Eléctrica

Precursores de la ingeniería industrial

Publica tu artículo en la revista #1 de Mantenimiento Industrial
Publicar un artículo en la revista es gratis, no tiene costo.
Solo debes asegurarte que no sea un artículo comercial.
¿Qué esperas?
O envía tu artículo directo: articulos@predictiva21.com
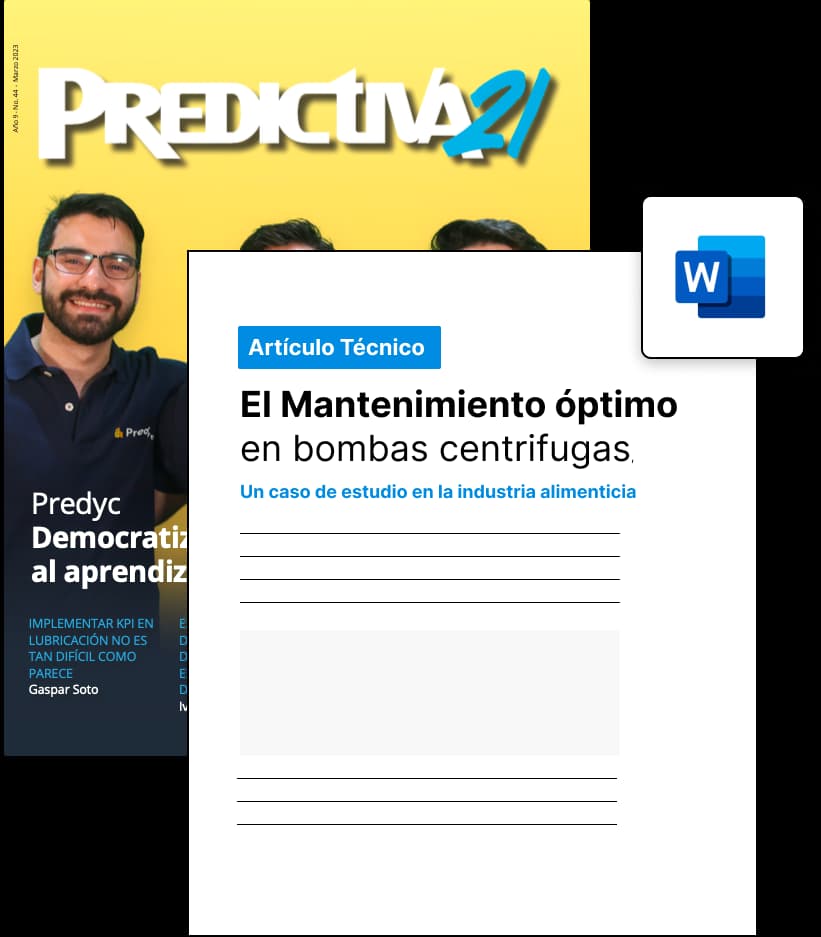
Análisis de Causa Raíz aplicado a fallas en sellos mecánicos de bombas
Articulo 19 de noviembre de 2019Resumen
El propósito de este artículo es exponer, en forma sencilla, un proceso de análisis de falla disciplinado (ACR) a través del entendimiento de hasta dónde debemos extender o definir los límites de control del análisis, con la finalidad de abarcar los elementos necesarios para lograr las acciones correctivas que eliminen el problema que originó la falla o lo lleve a niveles tolerables en función de sus consecuencias.
Palabras claves: Falla, Modo y Mecanismo de Falla, Evento, Hecho, Hipótesis, Causa Raíz.
1. Bombas. Fallas frecuentes
La bomba es una máquina “generadora” que absorbe energía mecánica proveniente de un motor eléctrico, térmico u otros, transmitiéndola a un fluido y transformándola en energía hidráulica, que a su vez, permite que el fluido pueda ser transportado de un lugar a otro, a un mismo nivel o a diferentes niveles y a diferentes velocidades, presiones y caudales.
Las fallas en las bombas son frecuentemente ocasionadas por los ingenieros y operadores de la planta que no reconocen las limitaciones inherentes de capacidad en las bombas. Cuando se opera una bomba con flujo alejado de su Punto de Máxima Eficiencia (B.E.P., siglas en inglés), se producen anomalías hidráulicas en la carcasa y el impulsor. Estas anomalías, que ocurren en todas las bombas, pueden ocasionar inestabilidad hidráulica, impulsos de vibración, y flexiones del eje, trayendo como resultado desgaste acelerados, fallas prematuras y frecuentes de impulsores, cojinetes y sellos; los cuales, actúan bajo estas condiciones como fusibles mecánicos, siendo el resultado final de una autorcadena de acontecimientos. Por lo que, idealmente, el punto de diseño y de operación deben mantenerse cercanos al Punto de Mejor Eficiencia (B.E.P.). Ver fig. 1.

Fuente: El autor
Dentro de las fallas frecuentes en bombas se pueden distinguir tres tipos de problemas: hidráulicos inherentes al sistema, hidráulicos inherentes a la bomba y problemas mecánicos.
Los problemas hidráulicos inherentes al sistema son el resultado de fallas en el diseño, procedimientos deficientes de instalación y colocación incorrecta de la tubería.
Los problemas hidráulicos inherentes a la bomba surgen cuando esta no puede funcionar de acuerdo con las especificaciones de capacidad, carga y eficiencia.
En cuanto a los problemas mecánicos, estos se refieren a desperfectos mecánicos, que se manifiestan mediante síntomas como ruido, vibraciones, sobrecalentamiento y pueden llevar a originar problemas de mal funcionamiento hidráulico.
Algunos de los eventos típicos que evidencian las fallas en las bombas rotativas son:
- No entrega líquido.
- Entrega menos liquido del esperado.
- Pierde ceba después del arranque. - No levanta presión.
- Consume demasiada potencia.
- Presenta excesivo ruido.
- Presenta excesiva vibración.
- Presenta alta temperatura en la zona de cojinetes y sellos.
- Presenta excesiva fuga por empaques o sellos mecánicos.
Estos eventos, que reflejan un mal funcionamiento en la bomba, llaman nuestra atención debido a la pérdida parcial o total de las funciones de la misma, bajo las especificaciones establecidas en su contexto operacional, tal como la pérdida de su función principal (entrega de un caudal a una presión requerida), que reflejará un impacto importante sobre el proceso; así como también, son importantes las pérdidas de otras funciones como las de contención (fugas al ambiente), que cobran vital relevancia en sistemas que manejan fluidos altamente tóxicos o volátiles y requieren especificaciones de seguridad exigentes.
2. Sellos mecánicos - Fallas prematuras
Los sellos son componentes de las bombas que evitan que un fluido escape al exterior de la misma a través de las holguras o claros entre el eje y la carcasa, controlando las emisiones dentro de los rangos de diseño establecidos. Es un elemento que requiere mucha atención en la industria química, petroquímica y refinerías, entre otras.
En la actualidad existe diversidad de sellos mecánicos que dependen de una aplicación en particular. Sin embargo, su configuración básica está dispuesta de una parte rotativa y una estacionaria, las cuales están formadas por:
a. El Cabezal del Sello: es el ensamble de varios componentes, tal como, el anillo primario (que está en contacto con el asiento, formando ambos el sellado primario), sellantes secundarios. (o’rings, cuñas, fuelles, etc.), sistema de compensación de desgaste (resortes) y sistema de arrastre (retenedores, componentes metálicos misceláneos). Este cabezal es el lado flexible del sello, que se acomoda a ligeros movimientos axiales y radiales del equipo.
b. El Asiento del Sello: es el anillo de desgaste removible en la brida si es estacionario o, en la camisa, si es rotativo.

Fuente: El autor
Estos contienen los elementos que forman:
c. El sellado primario, formado por el anillo primario y el asiento, conocido comúnmente como las caras de contacto del sello. Estas caras están fabricadas con materiales como carburo de silicio, carburo de tungsteno, carbón grafitado y cerámica (óxido de aluminio).
d. El sellado secundario, formado por los elementos los empaques (o´rings, empaques grafitados, etc.) que evitan la fuga de las partes del sello con el eje y la brida.
Teóricamente, el sello debe funcionar controlando las emisiones a la atmósfera hasta que uno de sus componentes pierda su función (falla el sellado), en el primario se desgastan y/o fracturan las caras y en el secundario se deforman, se degradan los elementos de empaques.
No obstante, en la práctica observamos que en 80% de los casos, los sellos fallan antes de cumplir con su ciclo de vida.
Las mayores causas de estas fallas prematuras son:
- Diseño y selección inadecuado del sello.
- Instalación incorrecta del sello.
- Mala operación, mantenimiento o funcionamiento inadecuado de los sistemas auxiliares del sello, tales como, lubricación, fluido amortiguador / barrera, venteos, etc.
- Problemas inherentes al sistema de bombeo, como inestabilidades hidráulicas (asociadas a diseño / selección / operación de la bomba), anomalías mecánicas (relacionadas con instalación / mantenimiento de la bomba).
- Cambios en las condiciones de servicio (Contexto Operacional), respecto a las especificadas del diseño original.
En la mayoría de los casos los usuarios o custodios centran su atención en la falla del componente -en este caso del sello mecánico- y concluyen que requieren un sello más robusto que se adapte a su condición de operación (Severa), desviada de su contexto operacional actual, lo que trae como consecuencia mayores costos en la adquisición de partes y repuestos, afectando notablemente el presupuesto de mantenimiento y logrando, solo en el mejor de los casos, prolongar la ocurrencia de la falla. Por tal motivo, debe realizarse un análisis integral del proceso para identificar aquellos factores que contribuyen a la ocurrencia de la falla.
3. Ejemplo de ACR en falla de selllos mecánicos en bombas centrífugas
El proceso de Análisis Causa Raíz persigue, no solo identificar las causas de las fallas, es también un proceso cíclico de mejora continua que busca corregir las causas de las fallas y mejorar el proceso, como se muestra en la figura No. 3:

Fuente: El autor
Desarrollemos entonces un ejemplo ACR para un caso de “Falla de una bomba centrífuga multietapas por fugas en los sellos mecánicos”, empleando un proceso disciplinado de análisis con el uso de un Árbol lógico de Fallas.
El primer paso es preparar el análisis:
• Definir el problema o evento a evitar estableciendo el Evento Tope, en este caso “Paro automático de la bomba P-102”. Es recomendable indicar si el paro fue automático (activación de una protección), manual (paro realizado por el operador) o súbito (no representado en las dos anteriores). Esto facilitará la identificación de los hechos y poder emitir hipótesis basados en los posibles mecanismos de fallo de estas.
• Estimar el impacto del evento en el negocio e identificar las oportunidades. Estableciendo los costos totales (pérdida de producción, costos de refacciones e insumos, mano de obra, servicios, etc.) de la ocurrencia o ocurrencias de este evento y su impacto en el presupuesto anual de mantenimiento y en el negocio; dando visibilidad del impacto de los eventos repetitivos o esporádicos en términos económicos.
• Recabar información del equipo y su función en el proceso. Reunir información de manuales del equipo, del sistema o planta, registros históricos de parámetros operacionales, reportes técnicos, mantenimiento predictivo, preventivo o correctivo, avisos de averías, datos de fallas, etc. Usar herramientas, tales como: Contexto Operacional, diagramas de Entrada Proceso Salida (EPS), diagramas Funcionales, etc., para procesar la información.
El segundo paso consiste en recabar la información de evento:
• Establecer el Equipo Natural de Trabajo (ENT). Es importante formar un equipo conformado por personas asociadas a la gestión del activo, de diferentes departamentos y disciplinas, para asegurar distintas visiones del evento, lo cual contribuirá a obtener una mayor perspectiva del evento, aportando una solución integral. Un ENT básico, estará formado por un Facilitador (asesor metodológico), Operador (Conocedor del funcionamiento de los equipos y su impacto en el negocio), Mantenedor (conocedor de las políticas y técnicas de mantenimiento de los equipos), Programador (visión sistémica de la actividad), Especialistas (expertos en áreas específicas como Cadena de Suministro, Calidad, SHA, Recursos Humanos, Finanzas, Mercadeo y Ventas, Proveedor de la Tecnología, entre otros).
• Levantar la información, las evidencias y la secuencia de evento utilizando herramientas como las Líneas de Tiempo, para discriminar tiempo y etapas del evento, que permitan comprender en forma deductiva el desarrollo histórico del mismo.
El tercer paso, comprende el desarrollar del árbol lógico deductivo:
• Representar la lógica del evento no deseado, donde se muestran todos los factores causales en sus tres niveles de fallas, tales como la falla física (avería de componentes), el error humano (interacción humana inadecuada) y las causas raíces (causas latentes por carencias, desviaciones u omisiones organizacionales).
En este paso, tomamos el enunciado del Evento Tope, redactado en el paso No.1, (este puede ser revisado y mejorado por el ENT), seguidamente respondiendo a la pregunta: ¿Cómo puede fallar?, describimos los Hechos (que corresponden a los modos de fallo, que evidencian la ocurrencia del evento), como por ejemplo, “atascamiento súbito, eje partido, fugas, alta vibración, alta temperatura, baja presión, etc.”. Con lo anterior enmarcamos el evento en lo que llamamos la caja superior del análisis.
Cuando tenemos múltiples Hechos, el ENT deberá soportar estos con evidencias a través de la investigación y manejo de datos reales, tales como registros de paros, reparaciones, informes de producción, etc. y entrevistas al personal involucrado con la gestión del equipo. En función de optimizar tiempo y recursos, se jerarquizan los hechos a través del uso de diversas técnicas, por ejemplo, usando estadística de fallas, registros de producción, costos, etc., y se asignan porcentajes de importancia a cada hecho, en base a un criterio acordado por el ENT, que represente las mayores consecuencias o impacto al negocio, lo cual permitirá iniciar y avanzar, con el hecho que aporte mayor influencia.
Una vez jerarquizados los hechos, iniciamos con el de mayor impacto, nuevamente empleando la pregunta ¿Cómo puede fallar? y comenzamos con el proceso de generar Hipótesis, que representen los mecanismos de fallo, como por ejemplo, “Desgaste (Erosivo, Adhesivo, Oxidación o Corrosión) o Fatiga”. Estas hipótesis deberán ser validadas a través de métodos de verificación, que confirmen o refuten su ocurrencia. Estas herramientas pueden ser entrevistas al personal, reportes de inspección directa, manejo de datos (reportes de reparaciones, calibraciones, control de calidad, etc.), uso de tecnologías de diagnósticos disponibles; tales como pruebas, ensayos y/o exámenes de laboratorio (Exámenes Métalográficos, Mecánicos y/o Químicos a componentes fallados), informes de inspecciones técnicas (Análisis de Vibración, Análisis de Aceite, Termografía, Ultrasonido, etc.). En casos complejos pueden emplearse metodologías como la de los 5 Porqué, Ishikahua, etc., para simplificarlo a niveles manejables. De esta forma se irá bajando de nivel hasta llegar a los límites de control del ENT (ver figura No. 4).

Fuente: El autor
En este punto, una vez verificadas y validadas las Hipótesis (convertidas a Hechos), se llega a un nivel donde la pregunta se transforma en: ¿Por qué falló? En este momento comenzamos a identificar la aparición de la falla física, el error humano y las causas raíces que desencadenaron los eventos que eventualmente condujeron a la falla, pudiendo introducirse durante el proceso de diseño, manufactura o uso (instalación, operación o mantenimiento), tal como se muestra en el ejemplo de la figura No. 4.
Finalmente, se establece el plan de acción, que persigue eliminar las causas raíces identificadas a través de la ejecución de las acciones. También debe establecerse un sistema de medición (KPI´s), para evaluar el logro de las acciones y, en caso de no alcanzar los objetivos esperados, se revalúa el proceso y se realizan los ajustes y las mejoras necesarias.
Debido a que pueden existir restricciones de niveles de aprobación, presupuesto, tecnología disponible, etc., que pudieran convertirse en barreras para la implementación del plan, pueden emplearse técnicas de Jerarquización de Eventos, aplicando una Matriz de Prioridades, basada en Complejidad y Consecuencias (ver figura No. 5), de tal forma de comenzar a implementar el plan, con aquellas acciones de mayores consecuencias, pero menor complejidad en su solución, para de esta forma obtener victorias tempranas que contribuirán a incentivar aprobaciones e inversiones el resto del plan.

Fuente: Curso técnicas de Análisis de fallas centradas en confiabilidad, con énfasis en causa raíz. 2005. De Engineering reliability and Management - ER&M
Cursos recomendados






%252FImagen%252FRAMPREDYC-1730060420837.webp%3Falt%3Dmedia%26token%3D2634a7f0-988e-4022-b91f-382503e6e9db&w=3840&q=75)

Conclusiones
a. Las Bombas son equipos susceptibles a cambios severos de sus condiciones de operación, tal como las inestabilidades hidráulicas que súbita o progresivamente afectarán la integridad de sus componentes mecánicos. Igualmente las desviaciones en la correcta selección, instalación y mantenimiento ocasionan problemas de origen mecánicos, donde algunos de ellos eventualmente también podrían desarrollar problemas hidráulicos.
b. En la actualidad, los sellos mecánicos son excelentes elementos de contención para evitar los escapes “no controlados” a la atmósfera en los procesos de manejo de fluidos; sin embargo, requieren de condiciones mínimas de instalación, mantenimiento y operación que garanticen la vida esperada del mismo, donde la intervención humana juega un papel pimportante.
c. El uso de procesos de análisis disciplinados como el ACR y el empleo de las tecnologías disponibles para soportar este proceso de pensamiento empleando la validación de hipótesis, contribuyen al logro de resultados exitosos en el control de fallas y la gestión del mantenimiento.
Glosario de términos
A continuación se lista un glosario de términos relevantes empleados en este documento:
• Análisis Causa Raíz (ACR): Metodología empleada para analizar e identificar las causas que provocan los eventos no deseados, contribuyendo a determinar medidas preventivas que minimicen sus consecuencias, disminuyan la probabilidad de ocurrencia o en el mejor de los casos, que el evento estudiado no se produzca de nuevo.
• Causa de Falla: La circunstancia durante el diseño, la manufactura o el uso que conlleva a una falla. Fuente: STD ISO14224.
• Causa Raíz: También conocida como causa latente, es el nivel más bajo del Análisis, donde se identifican aquellos factores que contribuyeron directamente con el problema, típicamente están representada en las carencias o deficiencias de la organización, que de no ser corregidas, el evento no deseado continuará ocurriendo.
• Consecuencia de la Falla: Es lo que experimenta el dueño de un activo como resultado de la ocurrencia de un modo de falla, manifestado en el impacto a la Seguridad, la Salud, el Ambiente, la pérdida de Producción, y/o los altos costos de Mantenimiento.
• Contexto Operacional: Es la descripción de las circunstancias específicas en las cuales opera un activo físico o sistema, está escrito en una forma narrativa que incluye la descripción exacta del activo y provee la información necesaria y con suficiente detalle sobre los factores (el entorno, la tecnología, estándares, la operación, etc.) que contribuyen e influyen en el proceso general.
• Equipo Natural de Trabajo (ENT): Conformado por un conjunto de personas de diferentes departamentos, con variadas disciplinas y funciones, buscando sinergia para lograr un objetivo en común y producir un mejor e integral resultado para la organización.
• Error Humano: También conocida como causa intermedia, es la interacción inadecuada de las personas durante su participación directa o indirecta en una actividad o proceso, que contribuye con la aparición de la falla; a veces se puede atribuir a malas prácticas de las personas involucradas.
• Evento Tope: Es el último elemento en la secuencia de la línea – tiempo. Representa al evento no deseado, que justifica económicamente el análisis y las acciones para eliminarlo.
• Falla: Es la terminación de la habilidad de un sistema/equipo/parte para realizar una función requerida. Fuente: STD ISO14224.
• Falla Física: También conocida como causa directa, son típicamente representadas por elementos, componentes o partes; que al reemplazarlos, se elimina de forma temporal el problema.
• Falla Funcional: Es la incapacidad de un elemento (o el equipo que lo contiene) para cumplir con un estándar de rendimiento especificado. Fuente: Nowlan y Heap (1960).
• Falla Potencial: Es una condición física identificable que indica que una falla funcional es inminente. Fuente: Nowlan y Heap (1960).
• Hechos: Son los modos en que se presenta la falla, es lo visible que aparece luego de la falla funcional.
• Hipótesis: Es una suposición hecha a partir de unos datos, que sirve de base para iniciar una investigación o una argumentación. Una hipótesis es un enunciado no verificado, que una vez confirmado o refutado dejará de ser hipótesis y se convertirá en hecho o no.
• Indicador Clave de Rendimiento (KPI): Los KPI (Key Performance Indicator, por sus siglas en inglés) es una medida del nivel del rendimiento de un proceso. El valor del indicador está directamente relacionado con un objetivo fijado previamente y normalmente se expresa en valores porcentuales.
• Jerarquizar: Establecer un orden de prioridad, descendente o ascendente en función de criterios basados en categorías, cualidades, características, valor, etc.
• Mecanismo de Falla: El proceso físico, químico u otro, que conlleva a una falla. Fuente: STD ISO14224.
• Modo de Falla: Un evento único, que causa una falla funcional. Fuente SAE: STD JA1011. Es el modo observado de la falla. Fuente: STD ISO14224.
Referencias
- (1) KENNERH J. MCNAUGTON. Bombas. Selección, Uso y Mantenimiento. México. McGRAW-HILL. N° 373 p. 1999.
- (2) ENGINEERING RELIABILITY AND MANAGEMENT. Fundamentos de Selección, Operación y Mantenimiento de Bombas. Curso. 2005.
- (3) ANSI/API Standard 610. Centrifugal Pumps for Petroleum, Petrochemical and Natural Gas Industries. 10th Edition. 2004.
- (4) INSTITUTO DE ENERGÍA Y TERMODINÁMICA. Curso de Bombas. Compañía de Sudamericana de Seguros S.A. Nº Pág. 8. 2002.
- (5) J.D. SUMMERS-SMITH. Mechanical Seal Practice for Improved Performance, Londres; editorial MEP, N° 216 p. 1992.
- (6) J.D. SUMMERS-SMITH. An Introductory Guide To Industrial Tribology. Londres; editorial MEP, N° 201 p. 1994.
- (7) ISO 14224. Petroleum, petrochemical and natural gas industries — Collection and exchange of reliability and maintenance data for equipment. Segunda edición 2006-12-15.
- (8) SAE JA1011. Criterios de Evaluación para Procesos de Mantenimiento Centrado en Confiabilidad. Emitida AGO1999.
- (9) SAE JA1011. Una Guía para la Norma de Mantenimiento Centrado en Confiabilidad (MCC). Emitida ENE2002.
- (1) ROBERT J. LATINO, SR. VP, RELIABILITY CENTER, INC. Calidad del Proceso y el Análisis de Causa Raíz Parte 1, 2 y 3. Reliability Center, Inc. N° pag. 7. 2001.
- (2) WOODHOUSE PARTNERSHIP LTD. Análisis Causa - Raíz. Curso. CIED. Tamare.1998.
- (3) ENGINEERING RELIABILITY AND MANAGEMENT - ER & M. Técnicas de Análisis de Falla Centradas en Confiabilidad, con Énfasis en Causa Raíz. Curso. 2005.
Autor: Ing./MSc. Tibaldo Alfredo Díaz Molina
Venezuela
Especialista en Ingeniería de Mantenimiento, Confiabilidad Operacional y Gestión de Activos
Correo: tibaldodiaz@gmail.com
Síntesis curricular del autor:
Técnico Superior Universitario e Ingeniero Mecánico con Maestría en Gerencia de Empresas y 30 años de experiencia en Ingeniería de Mantenimiento, Confiabilidad Operacional y Gestión de Activos, en la industria del petrolera y minera. Consultor y facilitador acreditado como Agente Capacitador Externo, por la STPS de México y Certificado por COMPECER en gestión de mantenimiento, análisis de riesgo y análisis causa raíz.
Dinos qué te ha parecido el artículo
Artículos recomendados
TPM e Industria 4.0 ¿Cómo las mejores prácticas de Mantenimiento se alinean con el creciente entorno de Industria 4.0?

6.1 Las Siete Preguntas Básicas del M.C.C

Probar, Detectar y Aislar – Aplicado al Mantenimiento. (Aplicación del Método recomendado por la OMS para la pandemia de COVID-19 “Probar, Detectar y Aislar” al mantenimiento).

Introducción a la gestión de inventarios

Publica tu artículo en la revista #1 de Mantenimiento Industrial
Publicar un artículo en la revista es gratis, no tiene costo.
Solo debes asegurarte que no sea un artículo comercial.
¿Qué esperas?
O envía tu artículo directo: articulos@predictiva21.com
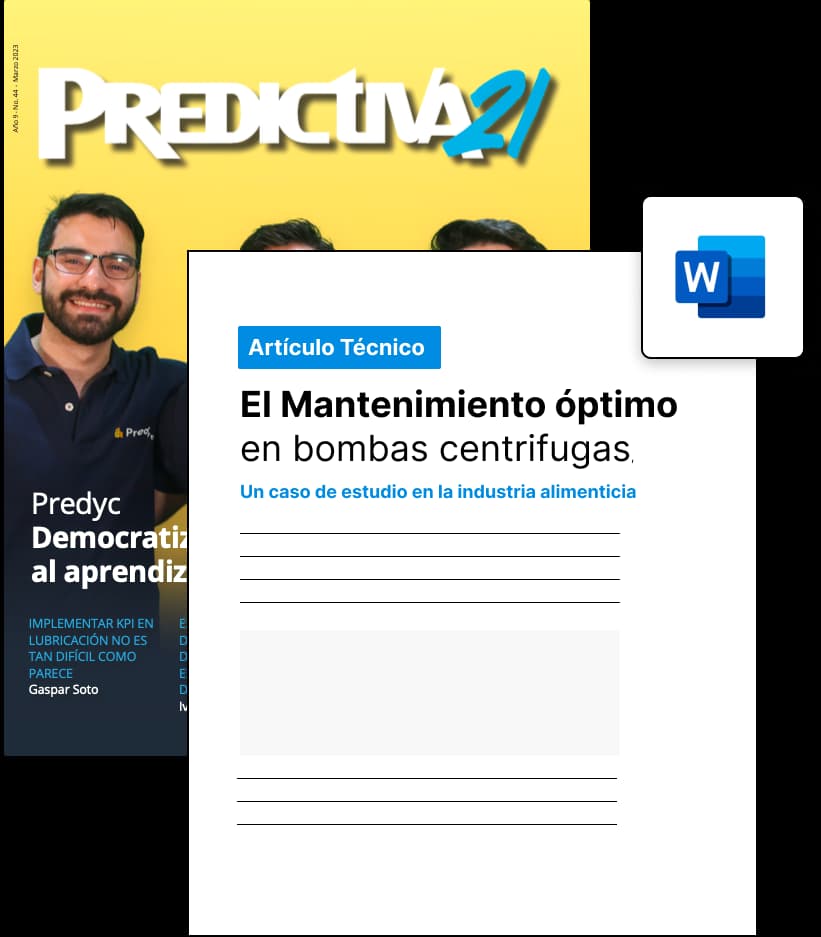