Aplicación de la Tecnología de Inspección Basada en Riesgo (IBR) para la Generación de Planes Óptimos de Inspección a Equipos Estáticos en la Industria del Petróleo y Gas
Articulo22 de enero de 2020
Introducción
En el mundo industrial una de las mayores preocupaciones recae sobre el diseño, selección y determinación de una adecuada política y estrategia de mantenimiento e inspección de los equipos estáticos, ya que estos tienen como riesgo la posibilidad de presentar una fuga externa del producto manejado y las consecuencias asociadas a la misma; como parada de alguna línea productiva, costos asociados a daños ambientales ocasionados, pérdidas de productos, mantenimiento o cambio de la estructura dañada, además de comprometer la seguridad del personal que labora en las cercanías del equipo o tubería, es por esto que a fin de reducir los niveles de riesgos asociados y costos operacionales, se hace necesario implementar metodologías y técnicas que permiten controlar, optimizar, prevenir y predecir la ocurrencia de falla en equipos estáticos; debido a esta situación actualmente se está implementando una Tecnología de Inspección Basada en Riesgo (IBR) para la Generación de Planes Óptimos de Inspección a Equipos Estáticos, basados en estándares internacionales como la práctica recomendada API-RP-580 y 581, y el uso de normas, estándares y prácticas recomendadas API como las 353, 570, 571, 574, 579, 650, 653, 1160 y ASME B31.3, 31.4, 31.8 y 31.8S, adicionalmente otros estándares de empresas del Medio Oriente (Arabia Saudita).
Esta metodología se aplica a equipos estáticos como circuitos de tuberías, recipientes a presión, intercambiadores, torres, y tanques de almacenamiento, cuyo objetivo es definir los niveles de riesgo de cada equipo, basados en la caracterización de la condición actual, mecanismos de degradación o deterioro, características de diseño, condiciones de operación, calidad y efectividad de las actividades de mantenimiento e inspección y las políticas gerenciales, así como las consecuencias asociadas a las potenciales fallas. Una vez definida la jerarquización de los equipos o tuberías de acuerdo a su nivel de riesgo, se determinan las actividades de inspección y frecuencias o fechas de ejecución, considerando los mecanismos de deterioro presentes y como punto final se realiza una optimización del programa de inspección en marcha OSI, lo cual permite determinar la cantidad requerida de puntos de inspección para cada equipo o circuito de tuberías.
Antecedentes
El presente estudio resume el resultado de la aplicación de la Tecnología de Inspección Basada en Riesgo (IBR) a instalaciones costa afuera (Off-Shore) y Costa Dentro “On-Shore” en diferentes empresas del ramo de la industria del Petróleo y Gas en países como Venezuela, México, Colombia y Arabia Saudita.
Originalmente estas instalaciones tenían planes de inspección para sus equipos estáticos, desarrollados sobre estudios y criterios tradicionales, así como también basados en experiencias de expertos conocedores del desempeño de equipos estáticos o de mecanismos de deterioro presentes en estos procesos productivos; dada esta oportunidad de mejora se decidió aplicar esta metodología o Técnica de Inspección Basada en Riesgo, lográndose el desarrollo y optimización de nuevos Planes y puntos de Inspección, adecuados a la condición actual, mecanismos de deterioro y nivel de riesgo actual; esto a su vez permitió la reducción del nivel de riesgo general de las instalaciones y de sus equipos.
Marco Conceptual
Definición de Riesgo
El riesgo es un término de naturaleza probabilística, que se define como “egresos o pérdidas probables consecuencia de la posible ocurrencia de un evento no deseado o falla”. En este simple pero poderoso concepto coexiste la posibilidad de que un evento o aseveración se haga realidad o se satisfaga, con las consecuencias de que ello ocurra. Matemáticamente el riesgo asociado a una decisión o evento viene dado por la expresión universal:
Riesgo(t) = Prob. de Falla(t) x Consecuencias
Ecuación 1
Basados en esta ecuación, se puede observar que el nivel de riesgo puede ser variable, de acuerdo a una disminución o incremento de la frecuencia de falla, o disminuyendo o incrementando las consecuencias. Es importante resaltar que de acuerdo a la experiencia sobre la determinación del riego, las acciones dirigidas a disminuir la frecuencia de ocurrencia de fallas son más factibles que las dirigidas a disminuir las consecuencias ya que esta ultimas involucran mayores inversiones o esfuerzos y decisiones de altos niveles gerenciales.
El análisis de la ecuación de riesgo, permite entender el poder de esta figura de mérito o indicador para el diagnóstico de situaciones y la toma de decisiones. A través de este indicador, pueden compararse situaciones y escenarios que bajo una perspectiva cotidiana resultarían disímiles, pero bajo ciertas circunstancias deben evaluarse y considerarlas en un proceso de toma de decisiones. Por ejemplo, podría utilizarse para discernir entre una acción de mantenimiento a equipos estáticos con frecuencias de fallas bajas pero con consecuencias tradicionalmente muy altas.
Inspección Basada en Riesgos
La Inspección Basada en Riesgos es una metodología sistemática que se apoya en las normas o estándares internacionales como API RP 580/581/571, cuyo objetivo es definir los planes de inspección basados en la caracterización probabilística del deterioro y el modelaje probabilístico de la consecuencia de una falla (caracterización del riesgo).
Esta metodología se enfoca en el estudio del deterioro de la pared de un contenedor de fluido que puede resultar en la pérdida de la función de contención del fluido presurizado, es decir, en una fuga de producto al medio ambiente.
Como todos los análisis de riesgo, el IBR implica el cálculo de probabilidades de falla y modelaje de las consecuencias de la misma. Para el cálculo de las probabilidades de falla, el IBR provee una metodología que considera los siguientes criterios:
- Espesor remanente.
- Tasa de corrosión.
- Calidad / frecuencia de inspección.
Para el modelaje de las consecuencias, la metodología IBR considera los siguientes criterios:
- Tipo de fluido.
- Sistemas de mitigación existentes.
- Inventario de producto (volumen).
A continuación se muestra un esquema general de la Metodología de Inspección Basada en Riesgo:

La siguiente figura muestra los diferente aspectos que son tomados en cuenta para la caracterización del riesgo en los estudios de IBR.

En la metodología de IBR se utiliza una matriz de 5 x 5 que gráficamente permite la ubicación del nivel de riesgo de los equipos analizados. Esta matriz presenta cuatro niveles de clasificación de riesgo que son: riesgo bajo representado típicamente en color blanco o verde, riesgo medio presentado en amarillo, riesgo medio – alto graficado en naranja y alto riesgo mostrado en rojo.

El producto de los valores de la probabilidad de falla y consecuencias permite determinar el nivel de riesgo asociado a cada equipo o circuito de tubería. Con estos resultados se puede construir una lista jerarquizada de equipos basada en el riesgo calculado, la cual es usada para la optimización de los planes de inspección. Una vez obtenido los niveles de riesgo de los equipos y circuitos de tuberías se procede a diseñar los planes de inspección así como la optimización de los puntos de inspección del Plan de Inspección en marcha.
Metodología y Aplicación
A continuación se define y desarrollan cada uno de los pasos de la metodología “Tecnología de Inspección Basada en Riesgo (IBR) para la Generación de Planes Óptimos de Inspección a Equipos Estáticos”:
Definición del sistemas o equipos a aplicar la metodologia
Consiste en la delimitación o selección de los sistemas, subsistemas y equipos o circuitos de tuberías a los cuales se les aplicara la metodología de inspección basada en riesgo.
Recolección de la información técnica requerida para el desarrollo del estudio
En esta etapa se obtendrá, capturará y evaluará los datos técnicos e información necesaria para poder establecer la base del análisis necesaria a fin de desarrollar el mapeo de riesgos y el Plan de Inspección basado en riesgo (IBR). Se tomara en consideración la información relativa al diseño, fabricación, instalación, operación y mantenimiento de los equipos y componentes de la instalación. Así como la información disponible en cuanto a los antecedentes de registros de inspección.
Para organizar toda esta información técnica, se dispone de bases de datos o “Spreadsheet” que permite descargar toda la información requerida por los software para determinar los niveles de riesgo de los equipos y circuitos de tuberías y así como también para mantener un registro de las fuentes consultadas. La revisión y captura de datos es una etapa en la que es susceptible introducir errores, por lo que se cuentan con losprocedimientos de aseguramiento de calidad necesarios para esta etapa.
A continuación se lista las fuentes de información más importante para el desarrollo de este estudio:
- Diagramas de flujo de proceso (DFP’s o PFD’s).
- Diagramas de tubería e instrumentación (DTI’s o P&ID).
- Planos Generales de la Plataforma (Plot Plans).
- Historia y registro de las inspecciones realizadas a los equipos y tuberías.
- Caracterización del fluido o fluidos de los sistemas.
- Hojas de especificación de equipos.
- Hojas de seguridad de las substancias de proceso.
- Bitácora o Reportes de mantenimiento.
- Estudios previos de Riesgo.
- Cualquier otra información técnica que contribuya al desarrollo del estudio.
En la siguiente imagen se muestra un ejemplo de una base de Datos o Spreadsheet, donde es descargada toda la información técnica requerida para el desarrollo del estudio de IBR, de acuerdo a la Tecnología de Inspección Basada en Riesgo (IBR) para la Generación de Planes Óptimos de Inspección a Equipos Estáticos.

Sistematización de la instalación
El proceso de sistematización de una planta, consiste en la división de una instalación o complejo en unidades menores de proceso que faciliten su análisis y evaluación. La unidad de estudio será el equipo o circuito de tubería de proceso. La sistematización se debe realizar tomando en cuenta los siguientes 2 conceptos:
Grupos de inventario
Se define como un grupo de equipos que pueden ser aislados remotamente o no mediante válvulas. Se asume que el inventario total de todo el grupo de inventario está potencialmente disponible para fugar. El concepto del grupo del inventario se utiliza en el cálculo para determinar el área de consecuencias.
Esta metodología busca determinar el máximo inventario disponible para fugar en caso de una falla. Se asume que todo el inventario del grupo está disponible para fugar por cualquiera de los equipos que lo integran en caso de que se presente una fuga de material. En el siguiente figura se muestra un ejemplo del establecimiento de un grupo de inventario.


- Se deberá asumir como dueño del grupo de inventario el equipo estático de mayor relevancia que corresponda.
- Los sistemas de líneas, filtros pequeños generalmente formarán parte de un grupo de inventario nunca generaran nombres del grupo, a excepción de líneas o cabezales principales.
- Los elementos que definirán los límites de los equipos preferiblemente serán, válvulas de bloqueo automáticas, válvulas de bloqueo manuales, válvulas de seguridad y en última instancia válvulas unidireccionales.
Lazos de corrosión
Otro de los criterios principales e indispensables para la conformación de los equipos o circuitos es el de lazos de corrosión, el cual por definición establece que los equipos asociados a un mismo lazo de corrosión presentan materiales, condiciones operacionales y mecanismos de deterioro similares. En el siguiente figura se muestra un ejemplo del establecimiento de un lazo de corrosión.

A continuación se mencionan algunas de las consideraciones para definir o determinar los lazos de corrosión:
- Tipo de componente, ya sea equipo de proceso circuito de tubería.
- Condiciones de operación.
- Tipo de servicio de circuito y/o equipo.
- Materiales de construcción.
- Localización de válvulas de corte o aislamiento.
- Composición química de la sustancia manejada.
- Aislamiento térmico.
En la etapa de diseño de los Lazos de Corrosion se deben identificar y evaluar los mecanismos de daño presentes en los equipos y circuitos de tuberías, para ello es importante apoyarse en la Norma API 571, que nos permite evaluar todos las Variables o Drivers que nos ayudan a establecer si un mecanismo está presente o no. Con la sistematización, cada equipo o circuito de tubería es entonces la unidad de estudio de riesgo y le corresponde un plan de inspección en particular, dependiendo del número y tipo de mecanismos de daño que éste pueda tener. Estos elementos son tratados de manera individual, de modo que cada uno recibe un trato particular y específico.
Otro aspecto importante durante el proceso de sistematización es el establecimiento de una taxonomía para mantener una estructura reproducible, confiable y ordenada que permita identificar a cada uno de los lazos y grupos de inventarios que se han clasificado y numerado de acuerdo a una taxonomía específica para cada caso. Esta taxonomía deberá poseer la siguiente estructura recomendada:
- Nivel 1» Iniciales IBR, para hacer referencia a un estudio de inspección basada en riesgo.
- Nivel 2 » Iniciales para identificar el tipo de la instalación.
- Nivel 3 » Iniciales para identificar el nombre de la instalación.
- Nivel 4 » Identificación para el nombre de la planta.
- Nivel 5 » Tipo de componente, “c” para circuito de tubería y “e” para equipo de proceso.
- Nivel 6 » Iniciales para el tipo de servicio del circuito de tubería o equipo de proceso.
- Nivel 7 » Número consecutivo para cada nodo.
Validación de la información
Es beneficioso para la calidad de un análisis del IBR y de cualquier estudio asegurar que los datos estén actualizados y validados por personas capacitadas en las áreas específicas.
La necesidad de garantizar la información es múltiple, dado que existen documentos, diagramas y planos no actualizados que no reflejan la realidad de la instalación, la falta de trazabilidad de las inspecciones, errores de los inspectores y muchas otras fuentes que pueden afectar negativamente la exactitud de los resultados de este tipo de estudio.
Es por ello que se requiere emplearse esfuerzos orientados a reducir estas fuentes de error, por lo que se ejecutan las siguientes acciones:
- Confrontación física de los diagramas y dibujos.
- Reuniones de validación con los expertos de cada área.
- Comparación entre las magnitudes de las velocidades de deterioro registradas con base en las inspecciones y las esperadas o registradas en la bibliografía o en Instalaciones similares.
- Verificación de las variables operacionales en los cuartos de control.
La actualización de la información se limita a considerar todas las líneas y equipos existentes en las instalaciones y descartar aquellos que han sido retirados de servicio, con el fin de generar los planes de inspección y acciones de mantenimiento acordes a la realidad operacional y evitando generar planes y acciones no necesarias así como el almacenamiento de datos confiables.
Identificación y evaluación de los mecanismos de daño
Para analizar el efecto del daño producido durante la operación y la inspección en la probabilidad de la detección de los defectos o fallas se ejecutan los siguientes pasos:
- Se determina la velocidad y severidad del daño.
- Se determina el nivel de confianza en la severidad de los daños.
- Se determina la eficacia de los programas de inspección.
- Se calcula el efecto del programa de inspección en el mejoramiento del nivel de determinación de los daños.
- Se calcula la probabilidad que un nivel dado de daño excederá la tolerancia del daño del equipo resultando en una falla.
- Se calculan los factores de daño.
- Se calcula el factor de daño total para todos los mecanismos de daño.
Análisis de riesgo
Este análisis está dirigido a equipos, circuitos de tuberías y válvulas, el cual permite determinar el riesgo de acuerdo al estándar de API 581 2DA EDICION SEP-2008. Este riesgo individual permite la planificación de actividades que están dirigidas a la detección de mecanismos específicos de daño.
Este análisis de riesgo se utiliza para obtener una calificación de riesgo de cada equipo de una forma determinística y considerando los criterios de aceptación de riesgos y plan de inspección requerido.
Este nivel de análisis se centra en la estimación de los factores que modifican la frecuencia de fallas y las zonas afectadas por la posible aparición de producto liberado al medio ambiente, como resultado de la pérdida de contención del equipo.
El análisis determina primero un factor que representa la probabilidad de la falla y posteriormente permite valorar un factor para las consecuencias. Ambos se combinan en una matriz de riesgo para establecer el nivel de riesgo del equipo o circuito de tuberías. Los pasos a seguir en el análisis de riesgo son:
Determinación de la Probabilidad de Falla
Frecuencia de falla para cada equipo para circuitos de tuberías, tanques, recipientes a presión e intercambiadores:
Para el cálculo del valor de la frecuencia de falla, se tomará el producto de la frecuencia de falla genérica por el factor de daño, y por el factor del sistema gerencial, según la ecuación 1. De la sección 4 de la práctica recomendada API 581 “RISK BASED INSPECTION TECHNOLOGY”. La frecuencia de falla, es expresada en términos de eventos por año, (eventos/año) como:

Frecuencia de falla genérica
La metodología IBR requiere el uso de la frecuencia de falla genérica, al comienzo del análisis de la probabilidad. La fuente de los datos debe ser elegida de manera que represente las plantas o equipos similares al equipo que es modelado.
La base de datos de las frecuencias de fallas genéricas se basa en una compilación de expedientes disponibles de las historias de la falla de equipos estáticos en operación en diversas plantas petroleras. Las frecuencias de falla genéricas se han desarrollado para cada tipo de equipo y cada diámetro de tubería. Las genéricas son obtenidas para cada tipo de nodo analizado y sus correspondientes modos de falla (fuga ¼”, 1”, 4” y ruptura).
En caso que no se tenga evidencia de fallas en las instalaciones objeto de estudio se recurrirá a la información genérica presentada en la tabla 4.1 “Suggested Component Generic Failure Frequencies, del API RP 581, Second Edition, Septiembre 2008, la cual se muestra a continuación.

En los casos donde se disponga de suficientes datos para un equipo dado, la frecuencia de falla real se podría calcular del historial de fallas observadas reales. Incluso si ninguna falla ha ocurrido en un equipo, se sabe por experiencia que la probabilidad verdadera de la falla es mayor de cero, y que el equipo no ha funcionado suficiente tiempo para experimentar una falla. Las frecuencias de falla genéricas se construyen usando datos históricos de todas las plantas dentro de una compañía o de varias plantas dentro de una industria.
Factor de Daño
Son los métodos sistemáticos usados para determinar el efecto de los mecanismos específicos de daño, que afectan la probabilidad de la falla de cada equipo. Estos sub-factores tienen cuatro funciones:
- Mapear los mecanismos de los daños bajo condiciones de funcionamiento normales y extremas.
- Establecer una tasa de daño en las condiciones en las que está operando el equipo.
- Cuantificar la eficacia del programa de inspección.
- Calcular el factor de modificación de la frecuencia genérica.
Estas diferencias son tratadas creando un factor de daño separado para cada mecanismo de deterioro. Para algunos de estos mecanismos, el índice del daño puede ser significativamente mayor a condiciones extremas diferentes a las condiciones normales de operación, tales como variaciones de la temperatura o cambios anormales en las concentraciones de un contaminante particular. Estas condiciones ocurren a menudo durante periodos de cambios operacionales o en los arranques y las paradas de proceso. El factor de daño considera tales condiciones y modifica la frecuencia de la falla.
Los factores de daño se evalúan en dos categorías de la información:
- Índice del daño del material de acuerdo a los materiales de construcción y su eficacia bajo las condiciones en las que opera.
- Efectividad del programa de inspección para identificar los mecanismos de daño activos.
Cursos recomendados




%252FImagen%252FRAMPREDYC-1730060420837.webp%3Falt%3Dmedia%26token%3D2634a7f0-988e-4022-b91f-382503e6e9db&w=3840&q=75)



Identificación y evaluación de los mecanismos de daño
Para analizar el efecto del daño producido en servicio y la inspección en la probabilidad de la falla se deben ejecutar los siguientes pasos:
- Determinar la velocidad y severidad del daño.
- Determinar el nivel de confianza en la severidad de los daños.
- Determinar la eficacia de los programas de inspección.
- Calcular el efecto del programa de inspección en el mejoramiento del nivel de determinación de los daños.
- Calcular la probabilidad de que un nivel dado de daño excederá la tolerancia del daño del equipo resultando en una falla.
- Calcular los factores de daño.
- Calcular el factor de daño total para todos los mecanismos de daño.
Para los mecanismos de deterioro, los factores de daño establecidos en API RP 581 son los siguientes:
- Adelgazamiento por corrosión/erosión (Presencia de revestimientos internos).
- Agrietamiento por corrosión bajo esfuerzos, SCC (Stress Corrosion Cracking).
- Daño externo.
- Ataque por hidrógeno a alta temperatura, HTHA.
- Fractura frágil.
- Fatiga mecánica, entre otros.
Considerando los mecanismos de daño o de deterioro, se realiza la valoración del daño que puede presentarse en los diferentes equipos, dada la posible existencia de los diferentes mecanismos de daño. Los factores específicos de daño se pueden consultar en la parte 2 del API RP 581, donde se establece la correspondiente evaluación de cada mecanismo que pueda estar presente en el equipo.
Si más de uno de los tipos generales de daño está potencialmente presente, los factores de daño individuales deben ser sumados, tal como se indica en la ecuación 2:

Se desarrollara el flujograma de toma de decisiones, y la información de proceso y mantenimiento, empleada para determinar el tipo de mecanismo de daño presente en cada equipo. Los aspectos teóricos y detalles de cada mecanismo de daño están especificados en la práctica recomendada API-571 “DAMAGE MECHANISMS AFFECTING FIXED EQUIPMENT IN THE REFINING INDUSTRY”.
Cuantificación de la eficacia del programa de inspección
Se determinan que técnicas de inspección son más recomendables con respecto a los mecanismos de daño identificados y a la efectividad de la inspección como medida de la capacidad de cada técnica de inspección o ensayo no destructivo, para detectar el mecanismo de daño que se puede presentar. Para fines de la presente metodología la efectividad de la inspección consiste de cinco categorías, las se indican en la siguiente tabla:

Factor del Sistema Gerencial
Para la evaluación del sistema gerencial de seguridad de proceso, se seguirá los pasos del anexo 2.a. del API 581 que evalúa los siguientes parámetros:
- Liderazgo y administración.
- Información de seguridad de procesos.
- Análisis de peligros de proceso.
- Manejo del cambio.
- Procedimientos operacionales.
- Prácticas de trabajo seguro.
- Entrenamiento.
- Integridad mecánica.
- Revisión de seguridad pre-arranque.
- Respuesta a emergencias.
- Investigación de incidentes.
- Contratistas.
- Auditorias.
Los resultados de este análisis serán presentados en un gráfico tipo “araña” similar al que se muestra en la siguiente figura:

Cálculo de consecuencias económicas por fuego y explosión, toxicidad, sustancias no inflamables no tóxicas
Para la realización de esta evaluación se deberá evaluar el área de afectación junto con el costo de los equipos y su costo de reparación, que se verán afectados dentro de esta área. Para el caso de daños al personal se evalúa de la misma manera con la densidad poblacional que se puede ver afectada por esta área de afectación.
Cálculo de consecuencias económicas por pérdidas de producción
Las consecuencias económicas por pérdidas de producción son estimadas empleando la tabla 5.17 – ESTIMATED EQUIPMENT OUTAGE DE LA NORMA API 581.
Cálculo de consecuencias ambientales
La evaluación de consecuencias ambientales es empleada para estimar los posibles efectos por la ocurrencia de un derrame al mar. Estos son evaluados en función del volumen derramado por su costo, expresado en unidades económicas por evento, ver ecuación (3):
Volumen derramado x costo del producto = $ / evento
Ecuación 3
Cálculo de consecuencias totales
Las consecuencias totales, son definidas como la sumatoria de cada una de las consecuencias, expresadas en unidades económicas por evento, ver ecuación (4):

Estimación del Riesgo y Jerarquización de Equipos en la Matriz de Riesgo
En este paso final se determina gráficamente, la ubicación del nivel de riesgo de los equipos analizados en una matriz de riesgo (API 581) de 5 x 5, que presenta cuatro niveles de clasificación de riesgo que son: riesgo bajo, riesgo medio, riesgo medio alto y alto riesgo, tal y como se muestra en la figura 9:

En la matriz de la Práctica API RP 581 se muestra una escala del 1 al 5 para la probabilidad de falla, esta escala indica que los equipos que estén en las categorías 1, 2, 3 y 4 tendrán una probabilidad de falla igual o menor a 1, 10, 100 y 1.000 veces la probabilidad de falla genérica de la base de datos mundial, respectivamente, mientras que los que estén en la 5 tendrán una probabilidad de falla mayor a 10.000 veces la probabilidad de falla genérica.
Como resultado se genera la matriz de riesgo de la metodología IBR. Para mostrar la ubicación de los diferentes equipos en las regiones de la matriz donde se consideran la categoría de frecuencia de falla y la categoría de consecuencia de falla, de acuerdo a las magnitudes expresadas en el análisis de riesgo por equipo. El riesgo determinado es relativo a todos los nodos evaluados en la instalación, considerando como indicador del riesgo, el riesgo financiero, en términos monetarios ($)/año.
El riesgo es determinado considerando todos los escenarios de falla (fuga ¼”, 1”, 4” y ruptura), así como las diferentes categorías de consecuencia consideradas (perdidas de producción, daños al equipo, daños por fuego y explosión, ambientales, etc.).
En la siguiente figura se muestra un ejemplo de los resultados de un estudio de IBR, en donde se puede visualizar la distribución de la cantidad de equipos de acuerdo a sus niveles de riesgo:

Diseño de los Planes de Inspección
Una vez identificados los factores de daño de cada equipo podrá identificarse cuál es la influencia de cada uno de ellos en la probabilidad de falla, así como el efecto del alcance de las actividades de inspección adecuadas en la probabilidad de detectar la manifestación del daño. Para ello, en el capítulo 9 del API Pub 581, se especifican las actividades de inspección, su alcance y frecuencias de aplicación de acuerdo a los mecanismos de deterioro presentes y su crecimiento en el tiempo.
El propósito de un plan de inspección es definir las actividades necesarias para detectar el deterioro en servicio de los equipos antes de que se produzcan las fallas. Adicionalmente se identifican actividades de mantenimiento u otras acciones de mitigación de riesgo que puedan ser aplicadas.
La concepción de una estrategia de reducción de riesgo de equipos estáticos a través de la metodología inspección basada en riesgo, sólo surtirá efecto si las actividades que han sido identificadas como las de mejor efecto de reducción de riesgo, son aplicadas en los activos. Para lo cual se recomienda establecer un mecanismo de control de las recomendaciones derivadas de los análisis a fin de garantizar su cumplimiento.

Optimización de los programas de inspección en marcha (OSI optimization)
Una vez desarrollado los planes de inspección para cada uno de los equipos o tuberías, el siguiente paso es la optimización del Programa de Inspección en Marcha (OSI Optimization), el cual consiste en determinar la cantidad exacta de puntos de inspección (CML’s) para cada equipo, de acuerdo a los mecanismos de deterioro presentes y niveles de riesgo. Este proceso se realiza de acuerdo a las normativas internacionales de referencia de empresas del Medio Oriente – Arabia Saudita. A continuación se muestra la tabla de referencia que es empleada para realizar esta optimización del programa de Inspección en Marcha.

Análisis de resultados
Como producto de las experiencias obtenidas durante el desarrollo de los diferentes estudios de IBR, se muestra a continuación los diferentes productos y resultados obtenidos mediante los programas computacionales empleados en estos estudios de Inspección Basada en Riesgo:
En la siguiente gráfica se muestra el resultado del análisis de riesgo, en donde se puede observar la jerarquización de la cantidad de equipos y tuberías, distribuidos en la Matriz de acuerdo a su nivel de riesgo, también puede observarse una proyección de la distribución de los niveles de riesgo de los equipos si el plan de inspección es implementado y por último la distribución de los equipos de acuerdo a su nivel de riesgo si el plan de inspección recomendado no es implantando, lo que permite y facilita la toma de decisiones para la ejecución e implementación de los planes y programas de inspección resultantes de la aplicación de la Tecnología de Inspección Basada en Riesgo para Equipos Estáticos.



En la siguiente tabla se muestra la distribución porcentual de los niveles de riesgo de los equipos, así como el efecto de la ejecución o no del plan de inspección recomendado por este estudio.

En la siguiente gráfica se muestra un caso específico de la evaluación de riesgo de Tanques de Almacenamiento, en donde se pudo visualizar los niveles de riesgo financieros de estos equipos y su ubicación de acuerdo al límite de riesgo aceptable para la organización.

En la siguiente gráfica se muestra un caso específico de la evaluación de riesgo de Tanques de Almacenamiento, en donde se pudo visualizar los niveles de riesgo financieros de estos equipos y su ubicación de acuerdo al límite de riesgo aceptable para la organización.

En la siguiente tabla se muestra el listado de Planes de Inspección, así como las técnicas de inspección, próximas fechas de inspección, riesgo financiero para cada equipo, etc.:

Esta tabla muestra los beneficios económicos obtenidos por la reducción del riesgo de la planta y de sus equipos por la ejecución del plan de inspección recomendado:

Por último en la siguiente tabla se muestra los resultados de la Optimización del Programa de Inspección en Marcha (OSI Optimization):

Casos de éxito
A continuación se muestra un listado de los proyectos desarrollados con la aplicación de las bases conceptuales de la Tecnología Inspección Basada en Riesgo (IBR) para la Generación de Planes Óptimos de Inspección a Equipos Estáticos de una Instalación Petrolera: 1. Inspección Basada en Riesgos en una planta de tratamiento y acondicionamiento de Gas Natural, Arabia Saudita, (adjudicado en proceso de contratación) 2. Inspección Basada en Riesgos una planta de fraccionamiento de NGL, Arabia Saudita, (en ejecución) 3. Inspección Basada en Riesgo de ocho patios de tanques para el almacenamiento de productos de Hidrocarburos (64 tanques y 4 esferas), Arabia Saudita, 2013 4. Inspección Basada en Riesgos tres (3) plantas de procesos, Arabia Saudita, 2012. 5. Inspección basada en Riesgo para una planta de compresión de gas natural la empresa Repsol. Repsol. Venezuela. 2011. 6. Inspección basada en riesgo para ductos y oleoductos de la empresa Repsol. Venezuela. 2011. 7. Elaboración de Planes de Inspección Basado en Riesgo (IBR) para Circuitos de Tuberías Recipientes a Presión de las planta Carrasco, CHACO, Bolivia, 2008 8. Elaboración de Planes de Inspección Basada en Riesgo (IBR) para Circuitos de Tuberías y Recipientes a Presión de las planta La Vertiente, BG, Bolivia 2008 9. Inspección Basada en Riesgo de las plataformas costa afuera Akal C7 y C8, Pemex, México, 2007 10. Elaboración de Planes de Inspección Basada en Riesgo para la plataforma costa afuera MPP, Shell, 2006 11. Desarrollo de una herramienta de integridad que utiliza los modelos de las normas API-RP-570, ASME-31G, Shell-92 y BOI, Shell, Venezuela, 2006 12. Elaboración de guías y Capacitación en la Aplicación de Metodologías de Confiabilidad: Mantenimiento Centrado en Confiabilidad (MCC), Análisis de Criticidad (AC), Análisis Causa Raíz (ACR), Inspección Basada en Riesgo (IBR), Vida Útil Remanente (VUR), Redimensionamiento de Instalaciones (RI), PEMEX – México. Realizado con el IMP. 2006. 13. Estudio Inspección Basada en Riesgo (IBR) para las Plataformas costa afuera: Nohoch-A1 y Nohoch-Enlace, PEMEX, México, 2005 14. Determinación del periodo de inspección basado en Riesgo (IBR) para la Terminal Marítima Dos Bocas, PEMEX, México, 2005.
Conclusiones
- La Tecnología de Inspección Basada en Riesgo (IBR), permite determinar los niveles de riesgo de los equipos y circuitos de tuberías, así como evaluar las posibilidades de reducción de riesgo de los mismos y así como también determinar los beneficios económicos de la implementación de los Planes de Inspección recomendados en estos estudios.
- Esta metodología permite el direccionamiento de los recursos a las áreas, plantas, sistemas o equipos en donde se encuentra los mayores niveles de riesgo de la planta.
- Esta metodología permite integrar las evaluaciones económicas en conjunto con los análisis de riesgos de los equipos evaluados en estos estudios, facilitando así la toma de decisiones para determinar la mejor estrategia de inspección de los equipos.
- Esta metodología tiene las facilidades de realizar estudios de Análisis Costo Riesgo Beneficio para aplicaciones específicas como tanques, etc.
- Como aspecto innovador con estos estudios se logran optimizar los programas de inspección en marcha y así determinar la cantidad de puntos de inspección requeridos para cada equipo o circuito de tubería.
Recomendaciones
Tomando en consideración las conclusiones generadas sobre la aplicación de la Tecnología de Inspección Basada en Riesgo (IBR) para la Generación de Planes Óptimos de Inspección a Equipos Estáticos en la Industria del Petróleo y Gas, tenemos:
- Implantar esta metodología como herramienta en la optimización de planes de inspección y mantenimiento de equipos estáticos, así como la optimización del Programa de Inspección en Marcha.
- Capacitar al personal encargado de la administración y cuidado de los equipos estáticos en la implementación de esta metodología de Diseño de Planes de Inspección Basada en Riesgo.
- Divulgar la metodología empleada para mejorar la toma de decisiones al momento de seleccionar estrategias de inspección y mantenimiento en equipos estáticos.
- Publicar este artículo en revistas de interés sobre el tema, así como su presentación en jornadas de Ingeniería de Confiabilidad, de Integridad Mecánica, etc.
Nomenclatura
CML: Localización de Monitoreo de Condición (“Condition Monitoring Location”).
DFP: Diagrama de Flujo de Procesos (PFD: “Proccess Flow Diagram”).
DTI: Diagrama de Tubería e Instrumentación (PID: “Process and Instrumentation Diagram”).
IBR: Inspección Basada en Riesgo.
MCC: Mantenimiento Centrado en Confiabilidad.
OSI: Inspección en Marcha (“On Stream Inspection”).
PLG: Plano de Localización General.
TML: Localización de Monitoreo de Espesor (“Thickness Monitoring Location”).
Referencias
- (1) Yañez, M., Gómez de la Vega, H; Valbuena, G.; “Ingeniería de Confiabilidad y Análisis Probabilística de Riesgo”. Reliability and Risk Management, S.A; 2004.
- (2) Materán, E.; “Modelo para el Proceso de Toma de Decisiones Basado en el Análisis de Costos del Ciclo de Vida Para Proyectos de Mantenimiento de Equipos Estáticos”.
- (3) Riddell, H.; “Training Manual For Life – Cycle Costing”. England. The Woodhouse Partnership. 1999.
- (4) Roush M.; Webb W., “Applied Reliability Engineering”, vol I, The Center for Reliability Engineering, University of Maryland. College Park. 1999.
- (5) Medardo Y.; Perdomo L. “Ingeniería de Confiabilidad; Pilar Fundamental del Mantenimiento”, 2001.
- (6) API-510. Pressure Vessel Inspection Code: Maintenance Inspection, Rating, Repair, And Alteration.
- (7) API-RP-580. Risk-Based Inspection.
- (8) API-581. Risk-Based Inspection Base Resource Document.
- (9) ASME Secc. VIII Div. I. Boiler And Pressure Vessel Code.
- (10) ASME B31.3 Process Piping.
- (11) ASME B31.G Manual For Determining The Remaining Strength Of Corroded Pipelines.
- (12) ASME B31.4 Pipeline Transportation System For Liquid Hydrocarbons And Other Liquids.
- (13) ASME B31.8 Gas Transmission And Distribution Piping System.
- (14) ASME B31.8S. Supplement to B31.8 on Managing System Integrity of Gas Pipeline.
- (15) API-570 Piping Inspection Code Inspection, Repair, Alteration, And Rerating Of In-Service Piping Systems.
- (16) API-571. Damage Mechanisms Affecting Fixed Equipment in the Refining Industry.
- (17) Recommended Practice DNV-RP-G101. Risk Based Inspection Of Offshore Topsides Static Mechanical Equipment.
- (18) API-574. Inspection Practices for Piping System Components.
- (19) API 579. Fitness-for-Service.
- (20) API 650. Welded Steel Tanks for Oil Storage.
- (21) API 653. Tank Inspection, Repair, Alteration and Reconstruction.
- (22) API 1160. MANAGING SYSTEM INTEGRITY FOR HAZARDOUS LIQUID PIPELINES.
- (23) STANDARES O NORMAS DE EMPRESAS DEL MEDIO ORIENTE – ARABIA SAUDITA.
Autores:
Materán L. Elisaúl de J.
Rojas M. Elimar A.
Gutierrez U. Edwin E.
Hernandez M, José A.
Dinos qué te ha parecido el artículo
Artículos recomendados
Precursores de la ingeniería industrial

1.1 Introducción

Caso Real: ¿Cómo afecta la Desalineación al funcionamiento de un motor eléctrico?

MODELO DE GESTIÓN PARA FLOTA VEHICULAR EN TRANSPORTE DE CARGA TERRESTRE

Publica tu artículo en la revista #1 de Mantenimiento Industrial
Publicar un artículo en la revista es gratis, no tiene costo.
Solo debes asegurarte que no sea un artículo comercial.
¿Qué esperas?
O envía tu artículo directo: articulos@predictiva21.com
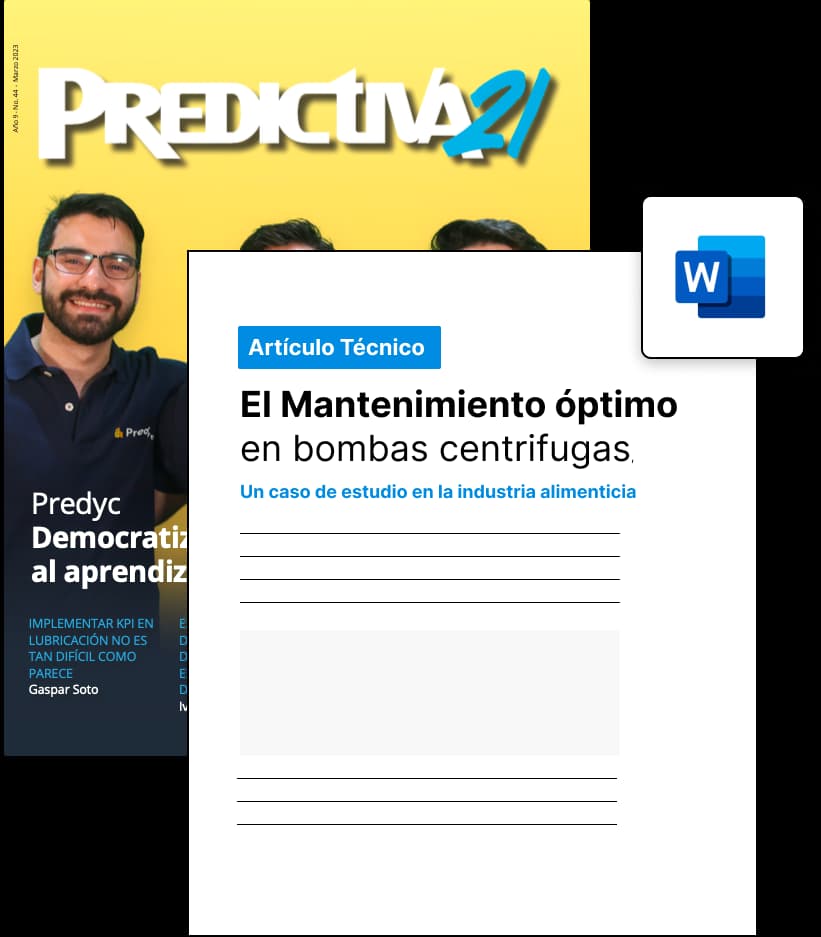
Aplicación de la Tecnología de Inspección Basada en Riesgo (IBR) para la Generación de Planes Óptimos de Inspección a Equipos Estáticos en la Industria del Petróleo y Gas
Articulo 22 de enero de 2020Introducción
En el mundo industrial una de las mayores preocupaciones recae sobre el diseño, selección y determinación de una adecuada política y estrategia de mantenimiento e inspección de los equipos estáticos, ya que estos tienen como riesgo la posibilidad de presentar una fuga externa del producto manejado y las consecuencias asociadas a la misma; como parada de alguna línea productiva, costos asociados a daños ambientales ocasionados, pérdidas de productos, mantenimiento o cambio de la estructura dañada, además de comprometer la seguridad del personal que labora en las cercanías del equipo o tubería, es por esto que a fin de reducir los niveles de riesgos asociados y costos operacionales, se hace necesario implementar metodologías y técnicas que permiten controlar, optimizar, prevenir y predecir la ocurrencia de falla en equipos estáticos; debido a esta situación actualmente se está implementando una Tecnología de Inspección Basada en Riesgo (IBR) para la Generación de Planes Óptimos de Inspección a Equipos Estáticos, basados en estándares internacionales como la práctica recomendada API-RP-580 y 581, y el uso de normas, estándares y prácticas recomendadas API como las 353, 570, 571, 574, 579, 650, 653, 1160 y ASME B31.3, 31.4, 31.8 y 31.8S, adicionalmente otros estándares de empresas del Medio Oriente (Arabia Saudita).
Esta metodología se aplica a equipos estáticos como circuitos de tuberías, recipientes a presión, intercambiadores, torres, y tanques de almacenamiento, cuyo objetivo es definir los niveles de riesgo de cada equipo, basados en la caracterización de la condición actual, mecanismos de degradación o deterioro, características de diseño, condiciones de operación, calidad y efectividad de las actividades de mantenimiento e inspección y las políticas gerenciales, así como las consecuencias asociadas a las potenciales fallas. Una vez definida la jerarquización de los equipos o tuberías de acuerdo a su nivel de riesgo, se determinan las actividades de inspección y frecuencias o fechas de ejecución, considerando los mecanismos de deterioro presentes y como punto final se realiza una optimización del programa de inspección en marcha OSI, lo cual permite determinar la cantidad requerida de puntos de inspección para cada equipo o circuito de tuberías.
Antecedentes
El presente estudio resume el resultado de la aplicación de la Tecnología de Inspección Basada en Riesgo (IBR) a instalaciones costa afuera (Off-Shore) y Costa Dentro “On-Shore” en diferentes empresas del ramo de la industria del Petróleo y Gas en países como Venezuela, México, Colombia y Arabia Saudita.
Originalmente estas instalaciones tenían planes de inspección para sus equipos estáticos, desarrollados sobre estudios y criterios tradicionales, así como también basados en experiencias de expertos conocedores del desempeño de equipos estáticos o de mecanismos de deterioro presentes en estos procesos productivos; dada esta oportunidad de mejora se decidió aplicar esta metodología o Técnica de Inspección Basada en Riesgo, lográndose el desarrollo y optimización de nuevos Planes y puntos de Inspección, adecuados a la condición actual, mecanismos de deterioro y nivel de riesgo actual; esto a su vez permitió la reducción del nivel de riesgo general de las instalaciones y de sus equipos.
Marco Conceptual
Definición de Riesgo
El riesgo es un término de naturaleza probabilística, que se define como “egresos o pérdidas probables consecuencia de la posible ocurrencia de un evento no deseado o falla”. En este simple pero poderoso concepto coexiste la posibilidad de que un evento o aseveración se haga realidad o se satisfaga, con las consecuencias de que ello ocurra. Matemáticamente el riesgo asociado a una decisión o evento viene dado por la expresión universal:
Riesgo(t) = Prob. de Falla(t) x Consecuencias
Ecuación 1
Basados en esta ecuación, se puede observar que el nivel de riesgo puede ser variable, de acuerdo a una disminución o incremento de la frecuencia de falla, o disminuyendo o incrementando las consecuencias. Es importante resaltar que de acuerdo a la experiencia sobre la determinación del riego, las acciones dirigidas a disminuir la frecuencia de ocurrencia de fallas son más factibles que las dirigidas a disminuir las consecuencias ya que esta ultimas involucran mayores inversiones o esfuerzos y decisiones de altos niveles gerenciales.
El análisis de la ecuación de riesgo, permite entender el poder de esta figura de mérito o indicador para el diagnóstico de situaciones y la toma de decisiones. A través de este indicador, pueden compararse situaciones y escenarios que bajo una perspectiva cotidiana resultarían disímiles, pero bajo ciertas circunstancias deben evaluarse y considerarlas en un proceso de toma de decisiones. Por ejemplo, podría utilizarse para discernir entre una acción de mantenimiento a equipos estáticos con frecuencias de fallas bajas pero con consecuencias tradicionalmente muy altas.
Inspección Basada en Riesgos
La Inspección Basada en Riesgos es una metodología sistemática que se apoya en las normas o estándares internacionales como API RP 580/581/571, cuyo objetivo es definir los planes de inspección basados en la caracterización probabilística del deterioro y el modelaje probabilístico de la consecuencia de una falla (caracterización del riesgo).
Esta metodología se enfoca en el estudio del deterioro de la pared de un contenedor de fluido que puede resultar en la pérdida de la función de contención del fluido presurizado, es decir, en una fuga de producto al medio ambiente.
Como todos los análisis de riesgo, el IBR implica el cálculo de probabilidades de falla y modelaje de las consecuencias de la misma. Para el cálculo de las probabilidades de falla, el IBR provee una metodología que considera los siguientes criterios:
- Espesor remanente.
- Tasa de corrosión.
- Calidad / frecuencia de inspección.
Para el modelaje de las consecuencias, la metodología IBR considera los siguientes criterios:
- Tipo de fluido.
- Sistemas de mitigación existentes.
- Inventario de producto (volumen).
A continuación se muestra un esquema general de la Metodología de Inspección Basada en Riesgo:

La siguiente figura muestra los diferente aspectos que son tomados en cuenta para la caracterización del riesgo en los estudios de IBR.

En la metodología de IBR se utiliza una matriz de 5 x 5 que gráficamente permite la ubicación del nivel de riesgo de los equipos analizados. Esta matriz presenta cuatro niveles de clasificación de riesgo que son: riesgo bajo representado típicamente en color blanco o verde, riesgo medio presentado en amarillo, riesgo medio – alto graficado en naranja y alto riesgo mostrado en rojo.

El producto de los valores de la probabilidad de falla y consecuencias permite determinar el nivel de riesgo asociado a cada equipo o circuito de tubería. Con estos resultados se puede construir una lista jerarquizada de equipos basada en el riesgo calculado, la cual es usada para la optimización de los planes de inspección. Una vez obtenido los niveles de riesgo de los equipos y circuitos de tuberías se procede a diseñar los planes de inspección así como la optimización de los puntos de inspección del Plan de Inspección en marcha.
Metodología y Aplicación
A continuación se define y desarrollan cada uno de los pasos de la metodología “Tecnología de Inspección Basada en Riesgo (IBR) para la Generación de Planes Óptimos de Inspección a Equipos Estáticos”:
Definición del sistemas o equipos a aplicar la metodologia
Consiste en la delimitación o selección de los sistemas, subsistemas y equipos o circuitos de tuberías a los cuales se les aplicara la metodología de inspección basada en riesgo.
Recolección de la información técnica requerida para el desarrollo del estudio
En esta etapa se obtendrá, capturará y evaluará los datos técnicos e información necesaria para poder establecer la base del análisis necesaria a fin de desarrollar el mapeo de riesgos y el Plan de Inspección basado en riesgo (IBR). Se tomara en consideración la información relativa al diseño, fabricación, instalación, operación y mantenimiento de los equipos y componentes de la instalación. Así como la información disponible en cuanto a los antecedentes de registros de inspección.
Para organizar toda esta información técnica, se dispone de bases de datos o “Spreadsheet” que permite descargar toda la información requerida por los software para determinar los niveles de riesgo de los equipos y circuitos de tuberías y así como también para mantener un registro de las fuentes consultadas. La revisión y captura de datos es una etapa en la que es susceptible introducir errores, por lo que se cuentan con losprocedimientos de aseguramiento de calidad necesarios para esta etapa.
A continuación se lista las fuentes de información más importante para el desarrollo de este estudio:
- Diagramas de flujo de proceso (DFP’s o PFD’s).
- Diagramas de tubería e instrumentación (DTI’s o P&ID).
- Planos Generales de la Plataforma (Plot Plans).
- Historia y registro de las inspecciones realizadas a los equipos y tuberías.
- Caracterización del fluido o fluidos de los sistemas.
- Hojas de especificación de equipos.
- Hojas de seguridad de las substancias de proceso.
- Bitácora o Reportes de mantenimiento.
- Estudios previos de Riesgo.
- Cualquier otra información técnica que contribuya al desarrollo del estudio.
En la siguiente imagen se muestra un ejemplo de una base de Datos o Spreadsheet, donde es descargada toda la información técnica requerida para el desarrollo del estudio de IBR, de acuerdo a la Tecnología de Inspección Basada en Riesgo (IBR) para la Generación de Planes Óptimos de Inspección a Equipos Estáticos.

Sistematización de la instalación
El proceso de sistematización de una planta, consiste en la división de una instalación o complejo en unidades menores de proceso que faciliten su análisis y evaluación. La unidad de estudio será el equipo o circuito de tubería de proceso. La sistematización se debe realizar tomando en cuenta los siguientes 2 conceptos:
Grupos de inventario
Se define como un grupo de equipos que pueden ser aislados remotamente o no mediante válvulas. Se asume que el inventario total de todo el grupo de inventario está potencialmente disponible para fugar. El concepto del grupo del inventario se utiliza en el cálculo para determinar el área de consecuencias.
Esta metodología busca determinar el máximo inventario disponible para fugar en caso de una falla. Se asume que todo el inventario del grupo está disponible para fugar por cualquiera de los equipos que lo integran en caso de que se presente una fuga de material. En el siguiente figura se muestra un ejemplo del establecimiento de un grupo de inventario.


- Se deberá asumir como dueño del grupo de inventario el equipo estático de mayor relevancia que corresponda.
- Los sistemas de líneas, filtros pequeños generalmente formarán parte de un grupo de inventario nunca generaran nombres del grupo, a excepción de líneas o cabezales principales.
- Los elementos que definirán los límites de los equipos preferiblemente serán, válvulas de bloqueo automáticas, válvulas de bloqueo manuales, válvulas de seguridad y en última instancia válvulas unidireccionales.
Lazos de corrosión
Otro de los criterios principales e indispensables para la conformación de los equipos o circuitos es el de lazos de corrosión, el cual por definición establece que los equipos asociados a un mismo lazo de corrosión presentan materiales, condiciones operacionales y mecanismos de deterioro similares. En el siguiente figura se muestra un ejemplo del establecimiento de un lazo de corrosión.

A continuación se mencionan algunas de las consideraciones para definir o determinar los lazos de corrosión:
- Tipo de componente, ya sea equipo de proceso circuito de tubería.
- Condiciones de operación.
- Tipo de servicio de circuito y/o equipo.
- Materiales de construcción.
- Localización de válvulas de corte o aislamiento.
- Composición química de la sustancia manejada.
- Aislamiento térmico.
En la etapa de diseño de los Lazos de Corrosion se deben identificar y evaluar los mecanismos de daño presentes en los equipos y circuitos de tuberías, para ello es importante apoyarse en la Norma API 571, que nos permite evaluar todos las Variables o Drivers que nos ayudan a establecer si un mecanismo está presente o no. Con la sistematización, cada equipo o circuito de tubería es entonces la unidad de estudio de riesgo y le corresponde un plan de inspección en particular, dependiendo del número y tipo de mecanismos de daño que éste pueda tener. Estos elementos son tratados de manera individual, de modo que cada uno recibe un trato particular y específico.
Otro aspecto importante durante el proceso de sistematización es el establecimiento de una taxonomía para mantener una estructura reproducible, confiable y ordenada que permita identificar a cada uno de los lazos y grupos de inventarios que se han clasificado y numerado de acuerdo a una taxonomía específica para cada caso. Esta taxonomía deberá poseer la siguiente estructura recomendada:
- Nivel 1» Iniciales IBR, para hacer referencia a un estudio de inspección basada en riesgo.
- Nivel 2 » Iniciales para identificar el tipo de la instalación.
- Nivel 3 » Iniciales para identificar el nombre de la instalación.
- Nivel 4 » Identificación para el nombre de la planta.
- Nivel 5 » Tipo de componente, “c” para circuito de tubería y “e” para equipo de proceso.
- Nivel 6 » Iniciales para el tipo de servicio del circuito de tubería o equipo de proceso.
- Nivel 7 » Número consecutivo para cada nodo.
Validación de la información
Es beneficioso para la calidad de un análisis del IBR y de cualquier estudio asegurar que los datos estén actualizados y validados por personas capacitadas en las áreas específicas.
La necesidad de garantizar la información es múltiple, dado que existen documentos, diagramas y planos no actualizados que no reflejan la realidad de la instalación, la falta de trazabilidad de las inspecciones, errores de los inspectores y muchas otras fuentes que pueden afectar negativamente la exactitud de los resultados de este tipo de estudio.
Es por ello que se requiere emplearse esfuerzos orientados a reducir estas fuentes de error, por lo que se ejecutan las siguientes acciones:
- Confrontación física de los diagramas y dibujos.
- Reuniones de validación con los expertos de cada área.
- Comparación entre las magnitudes de las velocidades de deterioro registradas con base en las inspecciones y las esperadas o registradas en la bibliografía o en Instalaciones similares.
- Verificación de las variables operacionales en los cuartos de control.
La actualización de la información se limita a considerar todas las líneas y equipos existentes en las instalaciones y descartar aquellos que han sido retirados de servicio, con el fin de generar los planes de inspección y acciones de mantenimiento acordes a la realidad operacional y evitando generar planes y acciones no necesarias así como el almacenamiento de datos confiables.
Identificación y evaluación de los mecanismos de daño
Para analizar el efecto del daño producido durante la operación y la inspección en la probabilidad de la detección de los defectos o fallas se ejecutan los siguientes pasos:
- Se determina la velocidad y severidad del daño.
- Se determina el nivel de confianza en la severidad de los daños.
- Se determina la eficacia de los programas de inspección.
- Se calcula el efecto del programa de inspección en el mejoramiento del nivel de determinación de los daños.
- Se calcula la probabilidad que un nivel dado de daño excederá la tolerancia del daño del equipo resultando en una falla.
- Se calculan los factores de daño.
- Se calcula el factor de daño total para todos los mecanismos de daño.
Análisis de riesgo
Este análisis está dirigido a equipos, circuitos de tuberías y válvulas, el cual permite determinar el riesgo de acuerdo al estándar de API 581 2DA EDICION SEP-2008. Este riesgo individual permite la planificación de actividades que están dirigidas a la detección de mecanismos específicos de daño.
Este análisis de riesgo se utiliza para obtener una calificación de riesgo de cada equipo de una forma determinística y considerando los criterios de aceptación de riesgos y plan de inspección requerido.
Este nivel de análisis se centra en la estimación de los factores que modifican la frecuencia de fallas y las zonas afectadas por la posible aparición de producto liberado al medio ambiente, como resultado de la pérdida de contención del equipo.
El análisis determina primero un factor que representa la probabilidad de la falla y posteriormente permite valorar un factor para las consecuencias. Ambos se combinan en una matriz de riesgo para establecer el nivel de riesgo del equipo o circuito de tuberías. Los pasos a seguir en el análisis de riesgo son:
Determinación de la Probabilidad de Falla
Frecuencia de falla para cada equipo para circuitos de tuberías, tanques, recipientes a presión e intercambiadores:
Para el cálculo del valor de la frecuencia de falla, se tomará el producto de la frecuencia de falla genérica por el factor de daño, y por el factor del sistema gerencial, según la ecuación 1. De la sección 4 de la práctica recomendada API 581 “RISK BASED INSPECTION TECHNOLOGY”. La frecuencia de falla, es expresada en términos de eventos por año, (eventos/año) como:

Frecuencia de falla genérica
La metodología IBR requiere el uso de la frecuencia de falla genérica, al comienzo del análisis de la probabilidad. La fuente de los datos debe ser elegida de manera que represente las plantas o equipos similares al equipo que es modelado.
La base de datos de las frecuencias de fallas genéricas se basa en una compilación de expedientes disponibles de las historias de la falla de equipos estáticos en operación en diversas plantas petroleras. Las frecuencias de falla genéricas se han desarrollado para cada tipo de equipo y cada diámetro de tubería. Las genéricas son obtenidas para cada tipo de nodo analizado y sus correspondientes modos de falla (fuga ¼”, 1”, 4” y ruptura).
En caso que no se tenga evidencia de fallas en las instalaciones objeto de estudio se recurrirá a la información genérica presentada en la tabla 4.1 “Suggested Component Generic Failure Frequencies, del API RP 581, Second Edition, Septiembre 2008, la cual se muestra a continuación.

En los casos donde se disponga de suficientes datos para un equipo dado, la frecuencia de falla real se podría calcular del historial de fallas observadas reales. Incluso si ninguna falla ha ocurrido en un equipo, se sabe por experiencia que la probabilidad verdadera de la falla es mayor de cero, y que el equipo no ha funcionado suficiente tiempo para experimentar una falla. Las frecuencias de falla genéricas se construyen usando datos históricos de todas las plantas dentro de una compañía o de varias plantas dentro de una industria.
Factor de Daño
Son los métodos sistemáticos usados para determinar el efecto de los mecanismos específicos de daño, que afectan la probabilidad de la falla de cada equipo. Estos sub-factores tienen cuatro funciones:
- Mapear los mecanismos de los daños bajo condiciones de funcionamiento normales y extremas.
- Establecer una tasa de daño en las condiciones en las que está operando el equipo.
- Cuantificar la eficacia del programa de inspección.
- Calcular el factor de modificación de la frecuencia genérica.
Estas diferencias son tratadas creando un factor de daño separado para cada mecanismo de deterioro. Para algunos de estos mecanismos, el índice del daño puede ser significativamente mayor a condiciones extremas diferentes a las condiciones normales de operación, tales como variaciones de la temperatura o cambios anormales en las concentraciones de un contaminante particular. Estas condiciones ocurren a menudo durante periodos de cambios operacionales o en los arranques y las paradas de proceso. El factor de daño considera tales condiciones y modifica la frecuencia de la falla.
Los factores de daño se evalúan en dos categorías de la información:
- Índice del daño del material de acuerdo a los materiales de construcción y su eficacia bajo las condiciones en las que opera.
- Efectividad del programa de inspección para identificar los mecanismos de daño activos.
Cursos recomendados




%252FImagen%252FRAMPREDYC-1730060420837.webp%3Falt%3Dmedia%26token%3D2634a7f0-988e-4022-b91f-382503e6e9db&w=3840&q=75)



Identificación y evaluación de los mecanismos de daño
Para analizar el efecto del daño producido en servicio y la inspección en la probabilidad de la falla se deben ejecutar los siguientes pasos:
- Determinar la velocidad y severidad del daño.
- Determinar el nivel de confianza en la severidad de los daños.
- Determinar la eficacia de los programas de inspección.
- Calcular el efecto del programa de inspección en el mejoramiento del nivel de determinación de los daños.
- Calcular la probabilidad de que un nivel dado de daño excederá la tolerancia del daño del equipo resultando en una falla.
- Calcular los factores de daño.
- Calcular el factor de daño total para todos los mecanismos de daño.
Para los mecanismos de deterioro, los factores de daño establecidos en API RP 581 son los siguientes:
- Adelgazamiento por corrosión/erosión (Presencia de revestimientos internos).
- Agrietamiento por corrosión bajo esfuerzos, SCC (Stress Corrosion Cracking).
- Daño externo.
- Ataque por hidrógeno a alta temperatura, HTHA.
- Fractura frágil.
- Fatiga mecánica, entre otros.
Considerando los mecanismos de daño o de deterioro, se realiza la valoración del daño que puede presentarse en los diferentes equipos, dada la posible existencia de los diferentes mecanismos de daño. Los factores específicos de daño se pueden consultar en la parte 2 del API RP 581, donde se establece la correspondiente evaluación de cada mecanismo que pueda estar presente en el equipo.
Si más de uno de los tipos generales de daño está potencialmente presente, los factores de daño individuales deben ser sumados, tal como se indica en la ecuación 2:

Se desarrollara el flujograma de toma de decisiones, y la información de proceso y mantenimiento, empleada para determinar el tipo de mecanismo de daño presente en cada equipo. Los aspectos teóricos y detalles de cada mecanismo de daño están especificados en la práctica recomendada API-571 “DAMAGE MECHANISMS AFFECTING FIXED EQUIPMENT IN THE REFINING INDUSTRY”.
Cuantificación de la eficacia del programa de inspección
Se determinan que técnicas de inspección son más recomendables con respecto a los mecanismos de daño identificados y a la efectividad de la inspección como medida de la capacidad de cada técnica de inspección o ensayo no destructivo, para detectar el mecanismo de daño que se puede presentar. Para fines de la presente metodología la efectividad de la inspección consiste de cinco categorías, las se indican en la siguiente tabla:

Factor del Sistema Gerencial
Para la evaluación del sistema gerencial de seguridad de proceso, se seguirá los pasos del anexo 2.a. del API 581 que evalúa los siguientes parámetros:
- Liderazgo y administración.
- Información de seguridad de procesos.
- Análisis de peligros de proceso.
- Manejo del cambio.
- Procedimientos operacionales.
- Prácticas de trabajo seguro.
- Entrenamiento.
- Integridad mecánica.
- Revisión de seguridad pre-arranque.
- Respuesta a emergencias.
- Investigación de incidentes.
- Contratistas.
- Auditorias.
Los resultados de este análisis serán presentados en un gráfico tipo “araña” similar al que se muestra en la siguiente figura:

Cálculo de consecuencias económicas por fuego y explosión, toxicidad, sustancias no inflamables no tóxicas
Para la realización de esta evaluación se deberá evaluar el área de afectación junto con el costo de los equipos y su costo de reparación, que se verán afectados dentro de esta área. Para el caso de daños al personal se evalúa de la misma manera con la densidad poblacional que se puede ver afectada por esta área de afectación.
Cálculo de consecuencias económicas por pérdidas de producción
Las consecuencias económicas por pérdidas de producción son estimadas empleando la tabla 5.17 – ESTIMATED EQUIPMENT OUTAGE DE LA NORMA API 581.
Cálculo de consecuencias ambientales
La evaluación de consecuencias ambientales es empleada para estimar los posibles efectos por la ocurrencia de un derrame al mar. Estos son evaluados en función del volumen derramado por su costo, expresado en unidades económicas por evento, ver ecuación (3):
Volumen derramado x costo del producto = $ / evento
Ecuación 3
Cálculo de consecuencias totales
Las consecuencias totales, son definidas como la sumatoria de cada una de las consecuencias, expresadas en unidades económicas por evento, ver ecuación (4):

Estimación del Riesgo y Jerarquización de Equipos en la Matriz de Riesgo
En este paso final se determina gráficamente, la ubicación del nivel de riesgo de los equipos analizados en una matriz de riesgo (API 581) de 5 x 5, que presenta cuatro niveles de clasificación de riesgo que son: riesgo bajo, riesgo medio, riesgo medio alto y alto riesgo, tal y como se muestra en la figura 9:

En la matriz de la Práctica API RP 581 se muestra una escala del 1 al 5 para la probabilidad de falla, esta escala indica que los equipos que estén en las categorías 1, 2, 3 y 4 tendrán una probabilidad de falla igual o menor a 1, 10, 100 y 1.000 veces la probabilidad de falla genérica de la base de datos mundial, respectivamente, mientras que los que estén en la 5 tendrán una probabilidad de falla mayor a 10.000 veces la probabilidad de falla genérica.
Como resultado se genera la matriz de riesgo de la metodología IBR. Para mostrar la ubicación de los diferentes equipos en las regiones de la matriz donde se consideran la categoría de frecuencia de falla y la categoría de consecuencia de falla, de acuerdo a las magnitudes expresadas en el análisis de riesgo por equipo. El riesgo determinado es relativo a todos los nodos evaluados en la instalación, considerando como indicador del riesgo, el riesgo financiero, en términos monetarios ($)/año.
El riesgo es determinado considerando todos los escenarios de falla (fuga ¼”, 1”, 4” y ruptura), así como las diferentes categorías de consecuencia consideradas (perdidas de producción, daños al equipo, daños por fuego y explosión, ambientales, etc.).
En la siguiente figura se muestra un ejemplo de los resultados de un estudio de IBR, en donde se puede visualizar la distribución de la cantidad de equipos de acuerdo a sus niveles de riesgo:

Diseño de los Planes de Inspección
Una vez identificados los factores de daño de cada equipo podrá identificarse cuál es la influencia de cada uno de ellos en la probabilidad de falla, así como el efecto del alcance de las actividades de inspección adecuadas en la probabilidad de detectar la manifestación del daño. Para ello, en el capítulo 9 del API Pub 581, se especifican las actividades de inspección, su alcance y frecuencias de aplicación de acuerdo a los mecanismos de deterioro presentes y su crecimiento en el tiempo.
El propósito de un plan de inspección es definir las actividades necesarias para detectar el deterioro en servicio de los equipos antes de que se produzcan las fallas. Adicionalmente se identifican actividades de mantenimiento u otras acciones de mitigación de riesgo que puedan ser aplicadas.
La concepción de una estrategia de reducción de riesgo de equipos estáticos a través de la metodología inspección basada en riesgo, sólo surtirá efecto si las actividades que han sido identificadas como las de mejor efecto de reducción de riesgo, son aplicadas en los activos. Para lo cual se recomienda establecer un mecanismo de control de las recomendaciones derivadas de los análisis a fin de garantizar su cumplimiento.

Optimización de los programas de inspección en marcha (OSI optimization)
Una vez desarrollado los planes de inspección para cada uno de los equipos o tuberías, el siguiente paso es la optimización del Programa de Inspección en Marcha (OSI Optimization), el cual consiste en determinar la cantidad exacta de puntos de inspección (CML’s) para cada equipo, de acuerdo a los mecanismos de deterioro presentes y niveles de riesgo. Este proceso se realiza de acuerdo a las normativas internacionales de referencia de empresas del Medio Oriente – Arabia Saudita. A continuación se muestra la tabla de referencia que es empleada para realizar esta optimización del programa de Inspección en Marcha.

Análisis de resultados
Como producto de las experiencias obtenidas durante el desarrollo de los diferentes estudios de IBR, se muestra a continuación los diferentes productos y resultados obtenidos mediante los programas computacionales empleados en estos estudios de Inspección Basada en Riesgo:
En la siguiente gráfica se muestra el resultado del análisis de riesgo, en donde se puede observar la jerarquización de la cantidad de equipos y tuberías, distribuidos en la Matriz de acuerdo a su nivel de riesgo, también puede observarse una proyección de la distribución de los niveles de riesgo de los equipos si el plan de inspección es implementado y por último la distribución de los equipos de acuerdo a su nivel de riesgo si el plan de inspección recomendado no es implantando, lo que permite y facilita la toma de decisiones para la ejecución e implementación de los planes y programas de inspección resultantes de la aplicación de la Tecnología de Inspección Basada en Riesgo para Equipos Estáticos.



En la siguiente tabla se muestra la distribución porcentual de los niveles de riesgo de los equipos, así como el efecto de la ejecución o no del plan de inspección recomendado por este estudio.

En la siguiente gráfica se muestra un caso específico de la evaluación de riesgo de Tanques de Almacenamiento, en donde se pudo visualizar los niveles de riesgo financieros de estos equipos y su ubicación de acuerdo al límite de riesgo aceptable para la organización.

En la siguiente gráfica se muestra un caso específico de la evaluación de riesgo de Tanques de Almacenamiento, en donde se pudo visualizar los niveles de riesgo financieros de estos equipos y su ubicación de acuerdo al límite de riesgo aceptable para la organización.

En la siguiente tabla se muestra el listado de Planes de Inspección, así como las técnicas de inspección, próximas fechas de inspección, riesgo financiero para cada equipo, etc.:

Esta tabla muestra los beneficios económicos obtenidos por la reducción del riesgo de la planta y de sus equipos por la ejecución del plan de inspección recomendado:

Por último en la siguiente tabla se muestra los resultados de la Optimización del Programa de Inspección en Marcha (OSI Optimization):

Casos de éxito
A continuación se muestra un listado de los proyectos desarrollados con la aplicación de las bases conceptuales de la Tecnología Inspección Basada en Riesgo (IBR) para la Generación de Planes Óptimos de Inspección a Equipos Estáticos de una Instalación Petrolera: 1. Inspección Basada en Riesgos en una planta de tratamiento y acondicionamiento de Gas Natural, Arabia Saudita, (adjudicado en proceso de contratación) 2. Inspección Basada en Riesgos una planta de fraccionamiento de NGL, Arabia Saudita, (en ejecución) 3. Inspección Basada en Riesgo de ocho patios de tanques para el almacenamiento de productos de Hidrocarburos (64 tanques y 4 esferas), Arabia Saudita, 2013 4. Inspección Basada en Riesgos tres (3) plantas de procesos, Arabia Saudita, 2012. 5. Inspección basada en Riesgo para una planta de compresión de gas natural la empresa Repsol. Repsol. Venezuela. 2011. 6. Inspección basada en riesgo para ductos y oleoductos de la empresa Repsol. Venezuela. 2011. 7. Elaboración de Planes de Inspección Basado en Riesgo (IBR) para Circuitos de Tuberías Recipientes a Presión de las planta Carrasco, CHACO, Bolivia, 2008 8. Elaboración de Planes de Inspección Basada en Riesgo (IBR) para Circuitos de Tuberías y Recipientes a Presión de las planta La Vertiente, BG, Bolivia 2008 9. Inspección Basada en Riesgo de las plataformas costa afuera Akal C7 y C8, Pemex, México, 2007 10. Elaboración de Planes de Inspección Basada en Riesgo para la plataforma costa afuera MPP, Shell, 2006 11. Desarrollo de una herramienta de integridad que utiliza los modelos de las normas API-RP-570, ASME-31G, Shell-92 y BOI, Shell, Venezuela, 2006 12. Elaboración de guías y Capacitación en la Aplicación de Metodologías de Confiabilidad: Mantenimiento Centrado en Confiabilidad (MCC), Análisis de Criticidad (AC), Análisis Causa Raíz (ACR), Inspección Basada en Riesgo (IBR), Vida Útil Remanente (VUR), Redimensionamiento de Instalaciones (RI), PEMEX – México. Realizado con el IMP. 2006. 13. Estudio Inspección Basada en Riesgo (IBR) para las Plataformas costa afuera: Nohoch-A1 y Nohoch-Enlace, PEMEX, México, 2005 14. Determinación del periodo de inspección basado en Riesgo (IBR) para la Terminal Marítima Dos Bocas, PEMEX, México, 2005.
Conclusiones
- La Tecnología de Inspección Basada en Riesgo (IBR), permite determinar los niveles de riesgo de los equipos y circuitos de tuberías, así como evaluar las posibilidades de reducción de riesgo de los mismos y así como también determinar los beneficios económicos de la implementación de los Planes de Inspección recomendados en estos estudios.
- Esta metodología permite el direccionamiento de los recursos a las áreas, plantas, sistemas o equipos en donde se encuentra los mayores niveles de riesgo de la planta.
- Esta metodología permite integrar las evaluaciones económicas en conjunto con los análisis de riesgos de los equipos evaluados en estos estudios, facilitando así la toma de decisiones para determinar la mejor estrategia de inspección de los equipos.
- Esta metodología tiene las facilidades de realizar estudios de Análisis Costo Riesgo Beneficio para aplicaciones específicas como tanques, etc.
- Como aspecto innovador con estos estudios se logran optimizar los programas de inspección en marcha y así determinar la cantidad de puntos de inspección requeridos para cada equipo o circuito de tubería.
Recomendaciones
Tomando en consideración las conclusiones generadas sobre la aplicación de la Tecnología de Inspección Basada en Riesgo (IBR) para la Generación de Planes Óptimos de Inspección a Equipos Estáticos en la Industria del Petróleo y Gas, tenemos:
- Implantar esta metodología como herramienta en la optimización de planes de inspección y mantenimiento de equipos estáticos, así como la optimización del Programa de Inspección en Marcha.
- Capacitar al personal encargado de la administración y cuidado de los equipos estáticos en la implementación de esta metodología de Diseño de Planes de Inspección Basada en Riesgo.
- Divulgar la metodología empleada para mejorar la toma de decisiones al momento de seleccionar estrategias de inspección y mantenimiento en equipos estáticos.
- Publicar este artículo en revistas de interés sobre el tema, así como su presentación en jornadas de Ingeniería de Confiabilidad, de Integridad Mecánica, etc.
Nomenclatura
CML: Localización de Monitoreo de Condición (“Condition Monitoring Location”).
DFP: Diagrama de Flujo de Procesos (PFD: “Proccess Flow Diagram”).
DTI: Diagrama de Tubería e Instrumentación (PID: “Process and Instrumentation Diagram”).
IBR: Inspección Basada en Riesgo.
MCC: Mantenimiento Centrado en Confiabilidad.
OSI: Inspección en Marcha (“On Stream Inspection”).
PLG: Plano de Localización General.
TML: Localización de Monitoreo de Espesor (“Thickness Monitoring Location”).
Referencias
- (1) Yañez, M., Gómez de la Vega, H; Valbuena, G.; “Ingeniería de Confiabilidad y Análisis Probabilística de Riesgo”. Reliability and Risk Management, S.A; 2004.
- (2) Materán, E.; “Modelo para el Proceso de Toma de Decisiones Basado en el Análisis de Costos del Ciclo de Vida Para Proyectos de Mantenimiento de Equipos Estáticos”.
- (3) Riddell, H.; “Training Manual For Life – Cycle Costing”. England. The Woodhouse Partnership. 1999.
- (4) Roush M.; Webb W., “Applied Reliability Engineering”, vol I, The Center for Reliability Engineering, University of Maryland. College Park. 1999.
- (5) Medardo Y.; Perdomo L. “Ingeniería de Confiabilidad; Pilar Fundamental del Mantenimiento”, 2001.
- (6) API-510. Pressure Vessel Inspection Code: Maintenance Inspection, Rating, Repair, And Alteration.
- (7) API-RP-580. Risk-Based Inspection.
- (8) API-581. Risk-Based Inspection Base Resource Document.
- (9) ASME Secc. VIII Div. I. Boiler And Pressure Vessel Code.
- (10) ASME B31.3 Process Piping.
- (11) ASME B31.G Manual For Determining The Remaining Strength Of Corroded Pipelines.
- (12) ASME B31.4 Pipeline Transportation System For Liquid Hydrocarbons And Other Liquids.
- (13) ASME B31.8 Gas Transmission And Distribution Piping System.
- (14) ASME B31.8S. Supplement to B31.8 on Managing System Integrity of Gas Pipeline.
- (15) API-570 Piping Inspection Code Inspection, Repair, Alteration, And Rerating Of In-Service Piping Systems.
- (16) API-571. Damage Mechanisms Affecting Fixed Equipment in the Refining Industry.
- (17) Recommended Practice DNV-RP-G101. Risk Based Inspection Of Offshore Topsides Static Mechanical Equipment.
- (18) API-574. Inspection Practices for Piping System Components.
- (19) API 579. Fitness-for-Service.
- (20) API 650. Welded Steel Tanks for Oil Storage.
- (21) API 653. Tank Inspection, Repair, Alteration and Reconstruction.
- (22) API 1160. MANAGING SYSTEM INTEGRITY FOR HAZARDOUS LIQUID PIPELINES.
- (23) STANDARES O NORMAS DE EMPRESAS DEL MEDIO ORIENTE – ARABIA SAUDITA.
Autores:
Materán L. Elisaúl de J.
Rojas M. Elimar A.
Gutierrez U. Edwin E.
Hernandez M, José A.
Dinos qué te ha parecido el artículo
Artículos recomendados
Análisis de Grasa y Ultrasonido para Rodamientos

Green Maintenance o Mantenimiento Sustentable en Empresas de Oil & Gas

La Terotecnología (Con la Terotecnología desde la Pas 55 hasta la ISO 55000) III Parte

La Serie de Normas ISO 55000, Herramienta para la Gestión de Activos

Publica tu artículo en la revista #1 de Mantenimiento Industrial
Publicar un artículo en la revista es gratis, no tiene costo.
Solo debes asegurarte que no sea un artículo comercial.
¿Qué esperas?
O envía tu artículo directo: articulos@predictiva21.com
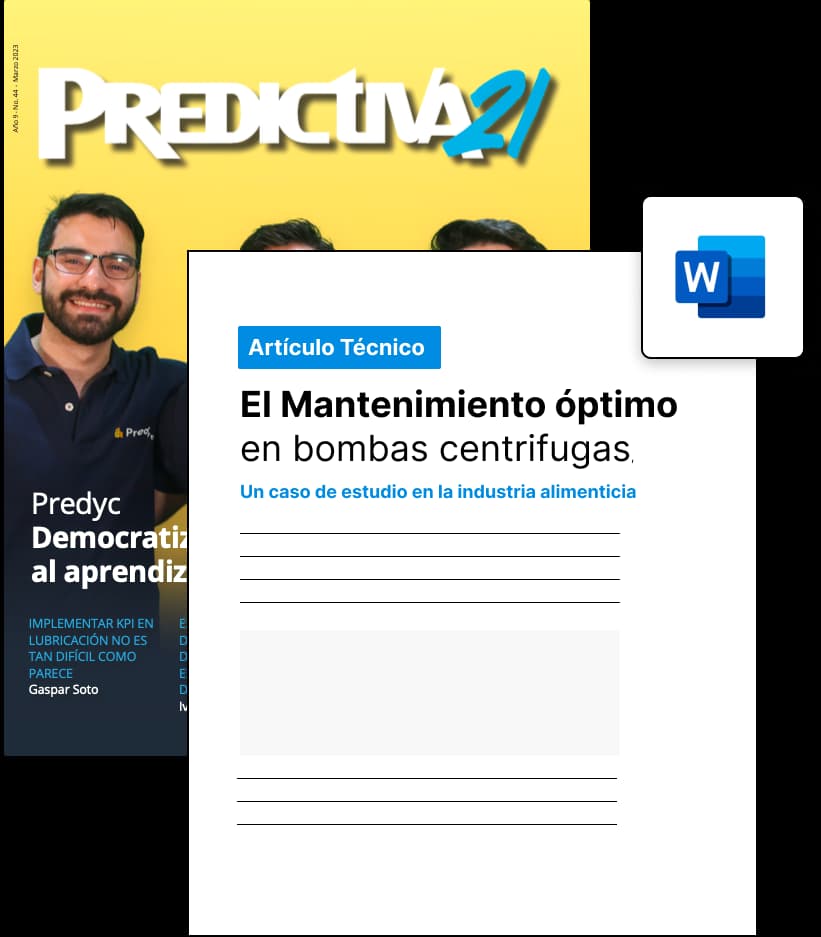