Dirección y Gestión de Paradas de Planta, Bajo los Lineamientos del PMI
Articulo3 de febrero de 2020
Una parada de planta o de mantenimiento, es un período durante el cual la planta se encuentra fuera de servicio, permitiendo efectuar tareas de mantenimiento como inspecciones, reparaciones generales, sustituciones, rediseños de máquinas (overhauls). Una parada de planta es un proyecto de ingeniería con inversión de capital, en donde se presenta una gran “oportunidad” de mejora. Lograr un conocimiento detallado del proyecto de modo de minimizar el riesgo en las fases de:
- Ingeniería conceptual.
- Ingeniería de detalle.
- Proveeduría.
- Construcción.
- Start-Up.
Es una justificación para aplicar el Estándar del PMBOK, y empezar a trabajar hacia una Gestión de Paradas de Planta con la metodología del PMBOK.
Las Paradas de Planta son comunes en las grandes plantas industriales, como la industria petrolera, petroquímica, cementera, papelera y química. En estos sectores industriales son comunes las paradas en intervalos regulares de tiempo para realizar trabajos de mantenimiento, reparaciones generales, sustituciones, rediseños de máquinas (overhauls) y nuevos proyectos, de conformidad con los requisitos de seguridad y medio ambiente.
El proceso se conoce como Parada y se inicia con la salida de operación de la planta y la desconexión de los equipos. Los proyectos, los trabajos de mantenimiento e inspecciones se pueden llevar a cabo, finalmente, la planta tiene que ser puesta en marcha hasta llegar a las condiciones normales de operación en las nuevas condiciones.
Más específicamente, durante la parada de planta los departamentos de mantenimiento sienten la mayor presión, en el sentido de que todos los ojos de la alta dirección de la empresa están sobre ellos, (Amendola, 2005).
Un retraso innecesario en la ejecución de una planificación puede extenderse a otras áreas o incluso puede parar la actividad de una empresa completa. Por estas razones es importante que las empresas tengan un sólido proceso de planificación y dirección de proyectos de paradas de planta.
Resulta interesante conjeturar por qué las paradas de planta hasta ahora han recibido relativamente poca atención, dado su impacto sobre el rendimiento de la empresa. La respuesta puede estar en el hecho de que la mayoría de las empresas están acostumbradas en su historial de mantenimiento al tiempo de inactividad, interrupciones cada vez más frecuentes a medida que las plantas crecen en infraestructura, y tal vez, incluso ahora, lo pueden considerar como un «mal necesario», (Lenahan, 1999).
En los últimos años, debido a la complejidad de las actividades que se realizan en los proyectos, y a las limitaciones tecnológicas que poseen los departamentos de mantenimiento para la manutención de estos equipos, el PM ha ganado importancia estratégica en el manejo gerencial del mantenimiento en prácticamente todas las grandes y medianas empresas.
Las técnicas del project management (PM), son aplicadas para desarrollar y completar una gran variedad de proyectos, por ejemplo; el desarrollo de nuevos productos, instalación de una nueva planta, planificación de la producción, y en general para proyectos asociados a los procesos operacionales y de mantenimiento (Pokharel & Jianxin, 2008).
En este contexto la investigación se concentra en la descripción y el desarrollo de los procesos para la dirección y gestión del proyecto de mantenimiento (Maintenance Project Management), aspecto poco tratado en la literatura teórica y práctica del mantenimiento, lo que constituye el carácter distintivo de este trabajo.
Metodología
La planificación de la parada de planta proporciona el marco de referencia para los stakeholder de la empresa puedan evaluar las necesidades del proyecto de parada de planta, identificar riesgos, definir retos y oportunidades y decidir las acciones basadas en un conjunto de valores compartidos.

Para focalizar y organizar mejor los esfuerzos, emprender las acciones de dirección y preparar el plan estratégico, se forma un equipo de trabajo constituido por todos los interesados (stakeholders) de la empresa: Operaciones, Mantenimiento, Procesos, Ingeniería de Planta, Inspección, Proyectos, entre otros, que permitirá lograr los mejores resultados de la parada y la integración del proyecto. Ver figura 4.
Fase 1 – Plan gerencial y estratégico
Se definen los objetivos y premisas de la Parada de Planta:
- 1. Alcance y restricciones.
- 2. Preparar los paquetes de trabajo.
- 3. Identificar la Pre-Parada.
- 4. Adquirir materiales y repuestos.
- 5. Definir los paquetes de trabajo de los contratistas.
- 6. Seleccionar los contratistas de la parada.
- 7. Plan integrado de Parada de Planta.
- 8. Organización de la Parada de Planta.
- 9. Crear un sitio de logística.
- 10. Plan de costos de la parada de planta.
- 11. Mantenimiento legal y permisos.
- 12. Programa de Seguridad & Salud (HSE).
- 13. Definir programa de calidad.
- 14. Resumen y manual de parada de planta.
Resumen y manual de parada de planta
Fase 2 – Proceso gerencial y aprobación de la lista de trabajo
La identificación del alcance preliminar de una parada de planta. Generalmente la organización de la parada de planta se enfoca en los puntos de la lista de trabajo “Work List”. En la Lista de Trabajo de la Parada deben utilizarse todos los elementos del alcance de trabajo originados por: Ingeniería de Procesos,Operaciones, Ingeniería/Técnico, Proyectos, de Capital, Cambios de Plantas, Inspección, HSEQ y Mantenimiento.
Fase 3 – Definición del alcance
Planificación de mediano plazo y se inicia entre 15 y 18 meses antes de apagado de la planta, este tiempo debe ajustarse a cada una de las áreas. Consiste en:
- Definir el equipo gerencial de la parada, equipo trabajo, responsabilidades, las metas.
- Desarrollar, justificar y reducir al mínimo los elementos de la lista.
- Elaborar los planes individuales de cada departamento (M & O).
- Aprobar la lista inicial, la fecha de corte y el presupuesto.
- Desarrollar y comunicar la programación de las fases de la parada.
- Solicitud de permisos trabajos de operaciones y Plan HSE.
- Listados preliminares consolidados.
- Desarrollo de ingeniería.
- Gestión Contratación y Compras de largo plazo.
- Documentación histórica.
Fase 4 – Planeación detallada
Esta fase integra todos los elementos asociados con el desarrollo de las órdenes de trabajo para establecer una programación efectiva del trabajo de la parada. Consiste en:
• Desarrollar en detalle las órdenes de trabajo planificadas con toda la información técnica pertinente y las cantidades estimadas de los trabajos.
• Desarrollar diagramas de redes lógicas y la programación de la ejecución del trabajo para cada elemento de la lista de trabajo, determinar la duración y la ruta crítica de la parada y las horas hombre requerido y la programación de turnos.
• Desarrollar el plan y las estrategias de contratación, definir todos los materiales y equipos requeridos, y el presupuesto total de la parada.
• Contar con un sistema deplanificación, programación y control que sea capaz de comunicar la información de costos, recursos, progreso y acciones correctivas requeridas para la organización.
• Responder a los cambios de alcance, así como optimizar el uso eficiente de las competencias y recursos disponibles.
Fase 5 – Desarrollo de la fase de ejecución
Esta fase integra todos los elementos asociados con la ejecución y control del trabajo de pre-parada y post-parada. Durante esta fase la fuerza hombre del contratista de mantenimiento se movilizará y apoyará al equipo gerencial de la parada y juntos ejecutarán el alcance de trabajo.
La clave de una parada exitosa está en el compromiso del equipo de gerencia de la parada y de la fuerza hombre de mantenimiento del contratista para vigilar las metas y objetivos de la misma (seguridad, calidad, costo y tiempo). La mejora continua en esta fase se alcanza a través de: suministrar información detallada a los supervisores, impartir orientaciones para la comprensión del alcance de trabajo.
Fase 6 – Desarrollo de la fase de cierre
Integra todos los elementos asociados a la preparación de un reporte formal de cierre para luego utilizarlo en el desarrollo de un plan de acción de mejoramiento continuo.
Todas las áreas del proceso Gerencial de Paradas serán revisadas para determinar la brecha entre los resultados, las metas y los objetivos establecidos para la parada.
Prácticas de la Metodología de Parada de Planta
1. Oficina Central de Parada
- Proveer los recursos y dinero para la Parada de Planta.
- Balancear las restricciones de la Parada de Planta.
- Fijar los objetivos de la Parada de Planta.
- Formulación de la política para alcanzar los objetivos de la Parada de Planta.
- Monitorear el progreso contra los objetivos.
- Modificar si es necesario las políticas o los objetivos de la Parada de Planta.
2. Roles y Responsabilidades
El personal que está involucrado en la planeación de la parada.
- Gerente de Parada de Planta.
- Coordinador de Preparación.
- Coordinador de Planificación.
- Equipo de Planeación.
- Coordinador de Logística.
- Equipo de Logística.

3. Determinar el Alcance de la Parada
Se desarrolla un plan maestro para elaborar un documento consistente y coherente que sirva de guía para la ejecución y control de la parada planta. Este proceso se repite varias veces durante la parada de planta.
El alcance del trabajo es preparado por todos los departamentos de ingeniería y revisado por los líderes de cada área (Mantenimiento, Producción, Proyectos, Construcción, HSE, Supervisores, Eléctricos, Mecánicos, Instrumentistas). Los líderes son miembros de la lista maestra de recursos de tiempo completo para la expansión del proyecto.


4. Determinar el Tiempo de la Parada
Son los procesos requeridos para asegurar que el proyecto sea completado en el tiempo ideal. Se definen, se identifican, y se documentan las actividades específicas que deben desarrollarse con el fin de cumplir con la Estructura de Descomposición del Proyecto (EDP), (Construction Extension to PMBOK, 2007).

Estructura De Descomposición Del Proyecto
La estructura de desglose de trabajo es una representación gráfica del proyecto, que desglosa el proyecto (áreas, sistema operativo) a su más bajo nivel en subproyectos, paquetes de trabajo y finalmente en actividades.
- Ingeniería constructiva de detalle.
- Gestión de compras y aprovisionamientos. Gestión de contratos.
- Fabricación y suministro (logística y tráfico hasta el lugar de los trabajos).
- Movilización en campo.
- Obra Civil, incluyendo y arquitectura y urbanización, conducciones, etc.
- Montaje mecánico (equipos, tuberías, estructuras).
- Montaje eléctrico (cableados y tendidos, montaje de equipos eléctricos: transformadores, etc.).
- Montaje de instrumentación en campo: válvulas, instrumentos, transmisores, cableado, cajas, cuadros.
- Montaje y configuración del sistema de control.
- Pre-comisionado y comisionado de sistemas, unidades.
- Puesta en marcha de la planta.
5. Planeación Detallada del Proyecto
- Establecer el plan HSE.
- Preparar, revisar y aprobar el alcance de los trabajos.
- Definir los paquetes de trabajo de la parada.
- Establecer una fecha tope de solicitudes de trabajo para realizar en la Parada.
- Planificación de las actividades y avance de la parada.
- Integrar el capital de trabajo con mantenimiento y producción en el cronograma de actividades de la parada.
- Nombramiento del equipo de dirección y coordinadores de la Parada de Planta.
- Recursos clave: Mantener la disciplina para cumplir con la Parada Planta, reuniones de control de la parada, el calendario, mantener políticas de no cambio.
- La realización de planes de contingencia para el peor de los escenarios.
6. Plan de Costos del Proyecto
Comprende la determinación de la clase y cantidad de recursos físicos que deben emplearse para desarrollar las tareas de la Parada de Planta, (Construction Extension to PMBOK, 2007).

7. Plan de Calidad del Proyecto
La gestión de la calidad de la Parada son los procesos requeridos para asegurar que la Parada de Planta satisface las necesidades para las cuales fue realizada.


8. Plan de Recursos Humanos del Proyecto
Son los procesos requeridos para usar de la manera más efectiva al personal necesario para el desarrollo de la Parada de Planta. De acuerdo al PMBOK, los procesos son:
- Planificación de la Organización.
- Adquisición de Personal.
- Desarrollo del Equipo.
- Movilización en campo.
- Dirigir al Equipo del Proyecto.
9. Plan de Comunicaciones del Proyecto
El plan de comunicación en la Parada de Planta, son los procesos requeridos para asegurar que la información fluya de una forma adecuada y sea almacenada para su uso correcto. De acuerdo al PMBOK, un plan de comunicación debe ser claro, conciso, relevante y a tiempo.
El siguiente diagrama muestras los pasos para crear un Plan de Comunicación para una Parada de Planta. Figura 8, Descripción General de las Comunicaciones en la Parada Planta, (PMBOK, 2008).

10. Plan de Administración Riesgos y Seguridad del Proyecto
Son los procesos requeridos para minimizar la posibilidad e impacto de hechos fortuitos en la parada de planta. El plan de gestión de riesgos describe como se estructura y se realiza la gestión de riesgos en el proyecto; el cual pasa a ser un subconjunto del plan de gestión del proyecto, (PMBOK, 2008).
Identificación de Riesgos: La identificación de riesgos consiste en determinar qué tipos de riesgos son los más probables y documentar las características de cada uno de ellos.
RPN= Factor detección x Impacto x Probabilidad, en donde el valor más alto de RPN, el riesgo tiene mayor relevancia, (Muiño, 2011).



El plan de HSE incluye: Fase planeación (Elaboración Plan Integral HSE), Fase de ejecución (Desarrollo e implementación del Plan HSE, Seguimiento y control del Plan HSE, Elaboración y Ejecución del Plan de desarrollo de competencias en HSE) y Fase de cierre (Lecciones aprendidas, Evaluación contratistas, Informe final HSE).
- Ejecutar el 100% del Plan de Gestión Integral HSE, Cero tolerancia al incumplimiento de las Reglas HSE.

11. Plan de Adquisiciones del Proyecto
Son los procesos requeridos para adquirir los equipos, repuestos, materiales y servicios necesarios para la parada de planta.
12. Ejecución del Proyecto Parada
El proceso de ejecución, el objetivo principal es el monitoreo y control de todas las tareas que se desarrollan durante el proyecto, se controla el cronograma y los costos de la Parada de Planta. Consiste en varios procesos claves que incluyen:
- 1. El plan está terminado y el hito que se programó está finalizado.
- 2. Desarrollar un plan de trabajos inesperados o tarde.
- 3. Desarrollar una rutina para dirección y gestión de la parada.
- 4. Trabajos que se realizan en cada turno de día.
- 5. Un procedimiento de control cambio para cada turno.
- 6. Trabajos que se realizan durante el tercer turno (turno de noche).
- 7. El control de los trabajos.
- 8. El control de costos.
- 9. Control programa diario.
- 10. Reporte diario de cada actividad.
- 11. Recuperación y la puesta en marcha de la planta.





Cursos recomendados




%252FImagen%252FRAMPREDYC-1730060420837.webp%3Falt%3Dmedia%26token%3D2634a7f0-988e-4022-b91f-382503e6e9db&w=3840&q=75)



Lecciones aprendidas y cierre de la Parada de Planta
- 1. Informe Final de Costos.
- 2. Informe Final del Cronograma.
- 3. Informe Final de Control de Calidad.
- 4. Informe Final de las Inspecciones y Especificaciones Técnicas.
- 5. Informe Final de Seguridad y Medio Ambiente.
- 6. Informe Final de la Organización del proyecto.
- 7. Informe Final Gestión Parada Planta.
- 8. Informe Final de los Contratos y Contratistas.
- 9. Informe Final de la Ejecución e Inspecciones de la Parada Planta.
- 10. Informe Final de las Herramientas disponibles que dejo la Parada.
- 11. Informe Final de la Cadena de Suministro de la Parada de Planta (Repuestos, Materiales).
- 12. Informe Final del Clima (Tiempo meteorológico).
- 13. Informe Final de las Obras, Construcción y Fabricación de la parada.
- 14. Informe Final de los Controles y Sistemas.
- 15. Informe Final fuerza laboral en la Parada.
- 16. Informe Final del Almacén y Compras.
- 17. El libro queda disponible para uso del personal interno y para el desarrollo de la siguiente Parada.
Conclusiones
La investigación aporta a los comités centrales de paradas de planta y sus líderes, una metodología que permite definir, planificar y ejecutar una parada de planta. Además la investigación da las pautas para el desarrollo del libro de lecciones aprendidas con el objetivo de idenficar y sugerir oportunidades de mejora para la siguiente parada.
De la revisión bibliográfica se puede concluir que los procesos de toma de decisiones en los Proyectos de Parada de Planta ocurren a menudo en una atmosfera de limitada racionalidad empresarial en donde los conflictos de intereses son raramente resueltos por completo, se evitan la incertidumbre, y los que toman las decisiones aprenden sobre la marcha.
Empresas que han adaptado la Guía del PMBOK, cuarta edición, han logrado excelentes resultados en la realización de sus proyectos, estos logros son presentados en el documento final de Parada de Planta en el cual realizan un benchmarking con empresas filiales, o empresas del mismo sector industrial, (IPA, 2011).
Adoptar los lineamientos del PMI para la dirección y gestión de Paradas de Planta para sectores industriales como el Petrolero, Petroquímico y Minero, ha sido un total éxito debido a la complejidad de sus proyectos y su alto costo. Este modelo de gestión de proyectos, lo están adoptando las grandes y medianas empresas de otros sectores de la economía internacional.
Las personas que dirigen y supervisan la parada planta influyen notablemente en el éxito o fracaso del proyecto. Para un proyecto de parada de planta es necesario disponer de un ambiente de trabajo y un equipo humano de alto desempeño para cumplir eficientemente con los objetivos del proyecto.
De la revisión bibliográfica y en el desarrollo del proyecto se concluye que es de suma importancia contar con herramientas informáticas o software para el desarrollo de proyectos, por la necesidad de informar a los interesados del proyecto en el escenario y tiempo adecuado, y a medida que avanza el proyecto la información se vuelve más compleja para llevarla en formatos.
Referencias
- 1. Alkemade, J, Jackson, J.A & Schroeder, B. (2011) ‘TRADE-OFF ECONOMICS IN REFINERY AND PLANT TURNAROUNDS’, AP Networks, consultado 10 agosto 2011.
- 2. Amendola, Luis. (2005) Dirección y Gestión de Paradas de Planta (The Theory of Constraints), Ediciones Espuela de Plata, España.
- 3. Amendola, Luis. (2006) Estrategias y Tácticas en la Dirección y Gestión de Proyectos, Editorial Universidad Politécnica de Valencia, España.
- 4. Amendola, L & Depool, T. (2006) ‘Mitigar los Riesgos en la Gestión de Paradas de Planta EDP”Estructura de Descomposición del Proyecto” WBS “Work Breakdown Structure” Mantenimiento’, PMM Institute for Learning, consultado 13 octubre 2011.
- 5. Amendola, L, Depool, T & Gonzáles, J.M. (2011) ‘STRATEGIC MODEL TO MANAGEMENT MULTIPROJECTS BASED ON THE CRITICAL CHAIN METODOLOGY (CCPM)’, PMM Institute for Learning, consultado 1 febrero 2012.
- 6. Amendola, Luis. (2011) ‘Metodología de Dirección y Gestión de Proyectos de Paradas de Planta de Proceso’, consultado 6 agosto 2011.
- 7. Apaolaza, U & Oyarbide, A. (2005) ‘La aportación de la Cadena Crítica frente a la gestión clásica de proyectos’, IX Congreso de Ingeniería de Organización Gijón, España.
- 8. Contruction Industry Institute. (2011) ‘Project Life Cycle Matrix’, Construction-Institute.org, consultado 5 octubre 2011.
- 9. Duffuaa, S.O & Ben Daya, M.A. (2004) ‘Turnaround maintenance in petrochemical industry: Practices and suggested improvements’, Journal of Quality in Maintenance Engineering, vol. 10, no. 3, pp. 184-190, consultado 1 agosto 2011.
- 10. Duggan, M & Blayden, R. (2001) ‘Venture maintainability: a path to project success Why are some projects less successful than others and what can we do to improve?’, Journal of Quality in Maintenance Engineering, vol. 7, no. 4, pp. 241-251, consultado 12 agosto 2011.
- 11. Ertl, B. (2011) ‘Applying PMBOK to Shutdowns, Turnarounds and Outages’, Inter Plan Systems Inc, consultado 6 agosto 2011.
- 12. Gadze, J. (2011) ‘Demo Front End Loading (FEL)’, CVPRO.com, consultado 5 octubre 2011.
- 13. García, Santiago. (2010) La Contratación del Mantenimiento Industrial, Ediciones Díaz de Santos, España.
- 14. Gonzales, Francisco Javier. 2010 Reducción de Costes y Mejora de Resultados en Mantenimiento, FC Editorial, España.
- 15. Industrial Info Resources. (2011) ‘Intelligence on Petroleum Refineries throughout Latin America’, consultado 2 diciembre 2011.
- 16. Inter Plan Systems Inc. (2011) ‘Turnaround Project Management Primer – Justification for Managing Turnarounds’, consultado 10 agosto 2011.
- 17. IPA. (2011) ‘IPA’s Turnaround Evaluations’, Ipaglobal.com, consultado 5 octubre 2011.
- 18. Jones, M. (2004) ‘The Case for Front End Loading (FEL) and Constructability Reviews’, Professional Paper Delivered to the Greater New Orleans Chapter, Project Management Institute, consultado 5 octubre 2011.
- 19. Joshi, N. (2003) ‘Benchmarking and Best Practices for Turnarounds’, IQPC Turnaround Conference, London, England.
- 20. Lenahan, Tom. (1999) Turnaround Management, Butterworth-Heinemann, Oxford.
- 21. Levitt, A & Wurtmann, B. (2008) Shutdown Risk Management, New Standard Institute, consultado 6 agosto.
- 22. McLay, John. (2011) ‘Practical Management for Plant Turnarounds’, ReliabilityWeb.com, consultado 15 agosto 2011.
- 23. Method 123. (2011) ‘Risk Management’, Method 123, consultado 3 octubre 2011.
- 24. Muiño, A. (2011) ‘Real Risk’, PMI Global Congress Proceedings, Dublin, Ireland.
- 25. Parra, M. (2011) ‘Planificación de una parada de refinería: Caso Proyecto RLP10.1b Refinería La Pampilla Perú’, Encuentro de Directores de Proyectos PMI Chapter de Madrid, consultado 5 octubre 2011.
- 26. Pockarel, S & Jiao, J.R. (2008) ‘Turnaround maintenance management in a processing industry: A case study’, Journal of Quality in Maintenance Engineering, vol. 14, no. 2, pp. 109-122, consultado 6 agosto 2011.
Autor: Nain Aguado Quintero
Ingeniero Mecánico, con especialización en diseño de maquinaria y equipo agroindustrial y MBA en Dirección
Proyectos, Universidad Viña del Mar (Chile).
Consultor en gestión de mantenimiento y conabilidad lubricación y dirección de proyectos en ABSG Colombia
Director General de LubricarOnLine.com.co.
Bogotá, Colombia
Correo: naguado@absconsulting.com
Dinos qué te ha parecido el artículo
Artículos recomendados
Generalización, Beneficios e Impacto de la Tecnología SGestMan © (II Parte)

Curso Gestión de Mantenimiento Industrial

Confiabilidad Humana y el Humano Confiable Parte II

Detergencia en los aceites lubricantes de motores de combustión

Publica tu artículo en la revista #1 de Mantenimiento Industrial
Publicar un artículo en la revista es gratis, no tiene costo.
Solo debes asegurarte que no sea un artículo comercial.
¿Qué esperas?
O envía tu artículo directo: articulos@predictiva21.com
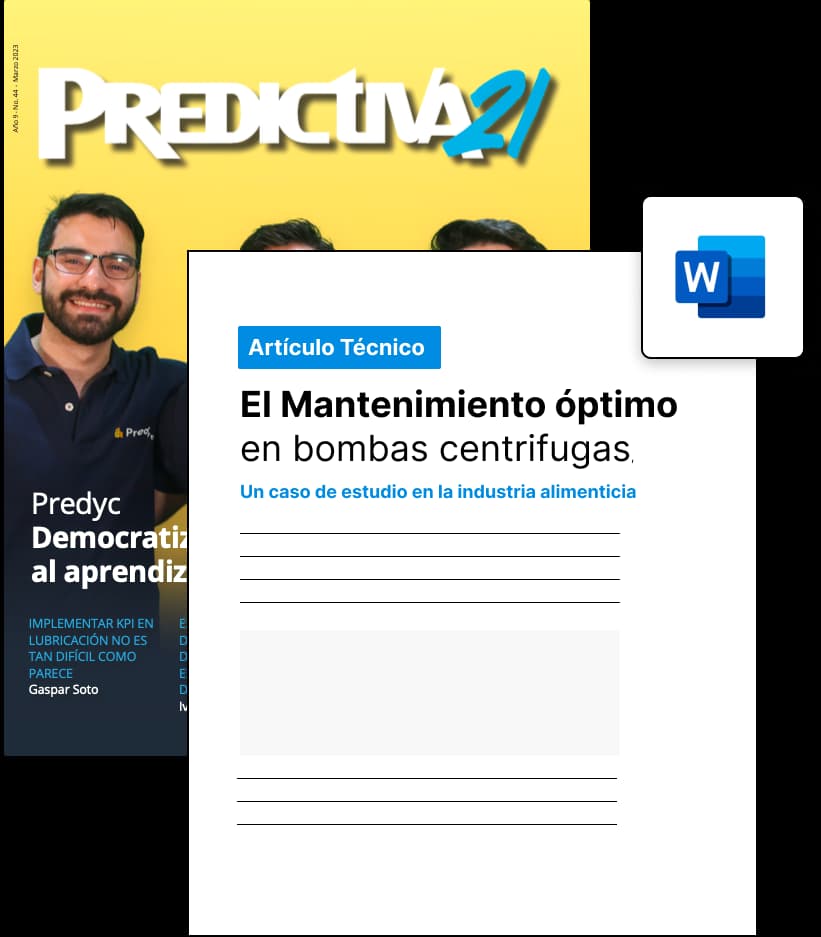
Dirección y Gestión de Paradas de Planta, Bajo los Lineamientos del PMI
Articulo 3 de febrero de 2020Una parada de planta o de mantenimiento, es un período durante el cual la planta se encuentra fuera de servicio, permitiendo efectuar tareas de mantenimiento como inspecciones, reparaciones generales, sustituciones, rediseños de máquinas (overhauls). Una parada de planta es un proyecto de ingeniería con inversión de capital, en donde se presenta una gran “oportunidad” de mejora. Lograr un conocimiento detallado del proyecto de modo de minimizar el riesgo en las fases de:
- Ingeniería conceptual.
- Ingeniería de detalle.
- Proveeduría.
- Construcción.
- Start-Up.
Es una justificación para aplicar el Estándar del PMBOK, y empezar a trabajar hacia una Gestión de Paradas de Planta con la metodología del PMBOK.
Las Paradas de Planta son comunes en las grandes plantas industriales, como la industria petrolera, petroquímica, cementera, papelera y química. En estos sectores industriales son comunes las paradas en intervalos regulares de tiempo para realizar trabajos de mantenimiento, reparaciones generales, sustituciones, rediseños de máquinas (overhauls) y nuevos proyectos, de conformidad con los requisitos de seguridad y medio ambiente.
El proceso se conoce como Parada y se inicia con la salida de operación de la planta y la desconexión de los equipos. Los proyectos, los trabajos de mantenimiento e inspecciones se pueden llevar a cabo, finalmente, la planta tiene que ser puesta en marcha hasta llegar a las condiciones normales de operación en las nuevas condiciones.
Más específicamente, durante la parada de planta los departamentos de mantenimiento sienten la mayor presión, en el sentido de que todos los ojos de la alta dirección de la empresa están sobre ellos, (Amendola, 2005).
Un retraso innecesario en la ejecución de una planificación puede extenderse a otras áreas o incluso puede parar la actividad de una empresa completa. Por estas razones es importante que las empresas tengan un sólido proceso de planificación y dirección de proyectos de paradas de planta.
Resulta interesante conjeturar por qué las paradas de planta hasta ahora han recibido relativamente poca atención, dado su impacto sobre el rendimiento de la empresa. La respuesta puede estar en el hecho de que la mayoría de las empresas están acostumbradas en su historial de mantenimiento al tiempo de inactividad, interrupciones cada vez más frecuentes a medida que las plantas crecen en infraestructura, y tal vez, incluso ahora, lo pueden considerar como un «mal necesario», (Lenahan, 1999).
En los últimos años, debido a la complejidad de las actividades que se realizan en los proyectos, y a las limitaciones tecnológicas que poseen los departamentos de mantenimiento para la manutención de estos equipos, el PM ha ganado importancia estratégica en el manejo gerencial del mantenimiento en prácticamente todas las grandes y medianas empresas.
Las técnicas del project management (PM), son aplicadas para desarrollar y completar una gran variedad de proyectos, por ejemplo; el desarrollo de nuevos productos, instalación de una nueva planta, planificación de la producción, y en general para proyectos asociados a los procesos operacionales y de mantenimiento (Pokharel & Jianxin, 2008).
En este contexto la investigación se concentra en la descripción y el desarrollo de los procesos para la dirección y gestión del proyecto de mantenimiento (Maintenance Project Management), aspecto poco tratado en la literatura teórica y práctica del mantenimiento, lo que constituye el carácter distintivo de este trabajo.
Metodología
La planificación de la parada de planta proporciona el marco de referencia para los stakeholder de la empresa puedan evaluar las necesidades del proyecto de parada de planta, identificar riesgos, definir retos y oportunidades y decidir las acciones basadas en un conjunto de valores compartidos.

Para focalizar y organizar mejor los esfuerzos, emprender las acciones de dirección y preparar el plan estratégico, se forma un equipo de trabajo constituido por todos los interesados (stakeholders) de la empresa: Operaciones, Mantenimiento, Procesos, Ingeniería de Planta, Inspección, Proyectos, entre otros, que permitirá lograr los mejores resultados de la parada y la integración del proyecto. Ver figura 4.
Fase 1 – Plan gerencial y estratégico
Se definen los objetivos y premisas de la Parada de Planta:
- 1. Alcance y restricciones.
- 2. Preparar los paquetes de trabajo.
- 3. Identificar la Pre-Parada.
- 4. Adquirir materiales y repuestos.
- 5. Definir los paquetes de trabajo de los contratistas.
- 6. Seleccionar los contratistas de la parada.
- 7. Plan integrado de Parada de Planta.
- 8. Organización de la Parada de Planta.
- 9. Crear un sitio de logística.
- 10. Plan de costos de la parada de planta.
- 11. Mantenimiento legal y permisos.
- 12. Programa de Seguridad & Salud (HSE).
- 13. Definir programa de calidad.
- 14. Resumen y manual de parada de planta.
Resumen y manual de parada de planta
Fase 2 – Proceso gerencial y aprobación de la lista de trabajo
La identificación del alcance preliminar de una parada de planta. Generalmente la organización de la parada de planta se enfoca en los puntos de la lista de trabajo “Work List”. En la Lista de Trabajo de la Parada deben utilizarse todos los elementos del alcance de trabajo originados por: Ingeniería de Procesos,Operaciones, Ingeniería/Técnico, Proyectos, de Capital, Cambios de Plantas, Inspección, HSEQ y Mantenimiento.
Fase 3 – Definición del alcance
Planificación de mediano plazo y se inicia entre 15 y 18 meses antes de apagado de la planta, este tiempo debe ajustarse a cada una de las áreas. Consiste en:
- Definir el equipo gerencial de la parada, equipo trabajo, responsabilidades, las metas.
- Desarrollar, justificar y reducir al mínimo los elementos de la lista.
- Elaborar los planes individuales de cada departamento (M & O).
- Aprobar la lista inicial, la fecha de corte y el presupuesto.
- Desarrollar y comunicar la programación de las fases de la parada.
- Solicitud de permisos trabajos de operaciones y Plan HSE.
- Listados preliminares consolidados.
- Desarrollo de ingeniería.
- Gestión Contratación y Compras de largo plazo.
- Documentación histórica.
Fase 4 – Planeación detallada
Esta fase integra todos los elementos asociados con el desarrollo de las órdenes de trabajo para establecer una programación efectiva del trabajo de la parada. Consiste en:
• Desarrollar en detalle las órdenes de trabajo planificadas con toda la información técnica pertinente y las cantidades estimadas de los trabajos.
• Desarrollar diagramas de redes lógicas y la programación de la ejecución del trabajo para cada elemento de la lista de trabajo, determinar la duración y la ruta crítica de la parada y las horas hombre requerido y la programación de turnos.
• Desarrollar el plan y las estrategias de contratación, definir todos los materiales y equipos requeridos, y el presupuesto total de la parada.
• Contar con un sistema deplanificación, programación y control que sea capaz de comunicar la información de costos, recursos, progreso y acciones correctivas requeridas para la organización.
• Responder a los cambios de alcance, así como optimizar el uso eficiente de las competencias y recursos disponibles.
Fase 5 – Desarrollo de la fase de ejecución
Esta fase integra todos los elementos asociados con la ejecución y control del trabajo de pre-parada y post-parada. Durante esta fase la fuerza hombre del contratista de mantenimiento se movilizará y apoyará al equipo gerencial de la parada y juntos ejecutarán el alcance de trabajo.
La clave de una parada exitosa está en el compromiso del equipo de gerencia de la parada y de la fuerza hombre de mantenimiento del contratista para vigilar las metas y objetivos de la misma (seguridad, calidad, costo y tiempo). La mejora continua en esta fase se alcanza a través de: suministrar información detallada a los supervisores, impartir orientaciones para la comprensión del alcance de trabajo.
Fase 6 – Desarrollo de la fase de cierre
Integra todos los elementos asociados a la preparación de un reporte formal de cierre para luego utilizarlo en el desarrollo de un plan de acción de mejoramiento continuo.
Todas las áreas del proceso Gerencial de Paradas serán revisadas para determinar la brecha entre los resultados, las metas y los objetivos establecidos para la parada.
Prácticas de la Metodología de Parada de Planta
1. Oficina Central de Parada
- Proveer los recursos y dinero para la Parada de Planta.
- Balancear las restricciones de la Parada de Planta.
- Fijar los objetivos de la Parada de Planta.
- Formulación de la política para alcanzar los objetivos de la Parada de Planta.
- Monitorear el progreso contra los objetivos.
- Modificar si es necesario las políticas o los objetivos de la Parada de Planta.
2. Roles y Responsabilidades
El personal que está involucrado en la planeación de la parada.
- Gerente de Parada de Planta.
- Coordinador de Preparación.
- Coordinador de Planificación.
- Equipo de Planeación.
- Coordinador de Logística.
- Equipo de Logística.

3. Determinar el Alcance de la Parada
Se desarrolla un plan maestro para elaborar un documento consistente y coherente que sirva de guía para la ejecución y control de la parada planta. Este proceso se repite varias veces durante la parada de planta.
El alcance del trabajo es preparado por todos los departamentos de ingeniería y revisado por los líderes de cada área (Mantenimiento, Producción, Proyectos, Construcción, HSE, Supervisores, Eléctricos, Mecánicos, Instrumentistas). Los líderes son miembros de la lista maestra de recursos de tiempo completo para la expansión del proyecto.


4. Determinar el Tiempo de la Parada
Son los procesos requeridos para asegurar que el proyecto sea completado en el tiempo ideal. Se definen, se identifican, y se documentan las actividades específicas que deben desarrollarse con el fin de cumplir con la Estructura de Descomposición del Proyecto (EDP), (Construction Extension to PMBOK, 2007).

Estructura De Descomposición Del Proyecto
La estructura de desglose de trabajo es una representación gráfica del proyecto, que desglosa el proyecto (áreas, sistema operativo) a su más bajo nivel en subproyectos, paquetes de trabajo y finalmente en actividades.
- Ingeniería constructiva de detalle.
- Gestión de compras y aprovisionamientos. Gestión de contratos.
- Fabricación y suministro (logística y tráfico hasta el lugar de los trabajos).
- Movilización en campo.
- Obra Civil, incluyendo y arquitectura y urbanización, conducciones, etc.
- Montaje mecánico (equipos, tuberías, estructuras).
- Montaje eléctrico (cableados y tendidos, montaje de equipos eléctricos: transformadores, etc.).
- Montaje de instrumentación en campo: válvulas, instrumentos, transmisores, cableado, cajas, cuadros.
- Montaje y configuración del sistema de control.
- Pre-comisionado y comisionado de sistemas, unidades.
- Puesta en marcha de la planta.
5. Planeación Detallada del Proyecto
- Establecer el plan HSE.
- Preparar, revisar y aprobar el alcance de los trabajos.
- Definir los paquetes de trabajo de la parada.
- Establecer una fecha tope de solicitudes de trabajo para realizar en la Parada.
- Planificación de las actividades y avance de la parada.
- Integrar el capital de trabajo con mantenimiento y producción en el cronograma de actividades de la parada.
- Nombramiento del equipo de dirección y coordinadores de la Parada de Planta.
- Recursos clave: Mantener la disciplina para cumplir con la Parada Planta, reuniones de control de la parada, el calendario, mantener políticas de no cambio.
- La realización de planes de contingencia para el peor de los escenarios.
6. Plan de Costos del Proyecto
Comprende la determinación de la clase y cantidad de recursos físicos que deben emplearse para desarrollar las tareas de la Parada de Planta, (Construction Extension to PMBOK, 2007).

7. Plan de Calidad del Proyecto
La gestión de la calidad de la Parada son los procesos requeridos para asegurar que la Parada de Planta satisface las necesidades para las cuales fue realizada.


8. Plan de Recursos Humanos del Proyecto
Son los procesos requeridos para usar de la manera más efectiva al personal necesario para el desarrollo de la Parada de Planta. De acuerdo al PMBOK, los procesos son:
- Planificación de la Organización.
- Adquisición de Personal.
- Desarrollo del Equipo.
- Movilización en campo.
- Dirigir al Equipo del Proyecto.
9. Plan de Comunicaciones del Proyecto
El plan de comunicación en la Parada de Planta, son los procesos requeridos para asegurar que la información fluya de una forma adecuada y sea almacenada para su uso correcto. De acuerdo al PMBOK, un plan de comunicación debe ser claro, conciso, relevante y a tiempo.
El siguiente diagrama muestras los pasos para crear un Plan de Comunicación para una Parada de Planta. Figura 8, Descripción General de las Comunicaciones en la Parada Planta, (PMBOK, 2008).

10. Plan de Administración Riesgos y Seguridad del Proyecto
Son los procesos requeridos para minimizar la posibilidad e impacto de hechos fortuitos en la parada de planta. El plan de gestión de riesgos describe como se estructura y se realiza la gestión de riesgos en el proyecto; el cual pasa a ser un subconjunto del plan de gestión del proyecto, (PMBOK, 2008).
Identificación de Riesgos: La identificación de riesgos consiste en determinar qué tipos de riesgos son los más probables y documentar las características de cada uno de ellos.
RPN= Factor detección x Impacto x Probabilidad, en donde el valor más alto de RPN, el riesgo tiene mayor relevancia, (Muiño, 2011).



El plan de HSE incluye: Fase planeación (Elaboración Plan Integral HSE), Fase de ejecución (Desarrollo e implementación del Plan HSE, Seguimiento y control del Plan HSE, Elaboración y Ejecución del Plan de desarrollo de competencias en HSE) y Fase de cierre (Lecciones aprendidas, Evaluación contratistas, Informe final HSE).
- Ejecutar el 100% del Plan de Gestión Integral HSE, Cero tolerancia al incumplimiento de las Reglas HSE.

11. Plan de Adquisiciones del Proyecto
Son los procesos requeridos para adquirir los equipos, repuestos, materiales y servicios necesarios para la parada de planta.
12. Ejecución del Proyecto Parada
El proceso de ejecución, el objetivo principal es el monitoreo y control de todas las tareas que se desarrollan durante el proyecto, se controla el cronograma y los costos de la Parada de Planta. Consiste en varios procesos claves que incluyen:
- 1. El plan está terminado y el hito que se programó está finalizado.
- 2. Desarrollar un plan de trabajos inesperados o tarde.
- 3. Desarrollar una rutina para dirección y gestión de la parada.
- 4. Trabajos que se realizan en cada turno de día.
- 5. Un procedimiento de control cambio para cada turno.
- 6. Trabajos que se realizan durante el tercer turno (turno de noche).
- 7. El control de los trabajos.
- 8. El control de costos.
- 9. Control programa diario.
- 10. Reporte diario de cada actividad.
- 11. Recuperación y la puesta en marcha de la planta.





Cursos recomendados




%252FImagen%252FRAMPREDYC-1730060420837.webp%3Falt%3Dmedia%26token%3D2634a7f0-988e-4022-b91f-382503e6e9db&w=3840&q=75)



Lecciones aprendidas y cierre de la Parada de Planta
- 1. Informe Final de Costos.
- 2. Informe Final del Cronograma.
- 3. Informe Final de Control de Calidad.
- 4. Informe Final de las Inspecciones y Especificaciones Técnicas.
- 5. Informe Final de Seguridad y Medio Ambiente.
- 6. Informe Final de la Organización del proyecto.
- 7. Informe Final Gestión Parada Planta.
- 8. Informe Final de los Contratos y Contratistas.
- 9. Informe Final de la Ejecución e Inspecciones de la Parada Planta.
- 10. Informe Final de las Herramientas disponibles que dejo la Parada.
- 11. Informe Final de la Cadena de Suministro de la Parada de Planta (Repuestos, Materiales).
- 12. Informe Final del Clima (Tiempo meteorológico).
- 13. Informe Final de las Obras, Construcción y Fabricación de la parada.
- 14. Informe Final de los Controles y Sistemas.
- 15. Informe Final fuerza laboral en la Parada.
- 16. Informe Final del Almacén y Compras.
- 17. El libro queda disponible para uso del personal interno y para el desarrollo de la siguiente Parada.
Conclusiones
La investigación aporta a los comités centrales de paradas de planta y sus líderes, una metodología que permite definir, planificar y ejecutar una parada de planta. Además la investigación da las pautas para el desarrollo del libro de lecciones aprendidas con el objetivo de idenficar y sugerir oportunidades de mejora para la siguiente parada.
De la revisión bibliográfica se puede concluir que los procesos de toma de decisiones en los Proyectos de Parada de Planta ocurren a menudo en una atmosfera de limitada racionalidad empresarial en donde los conflictos de intereses son raramente resueltos por completo, se evitan la incertidumbre, y los que toman las decisiones aprenden sobre la marcha.
Empresas que han adaptado la Guía del PMBOK, cuarta edición, han logrado excelentes resultados en la realización de sus proyectos, estos logros son presentados en el documento final de Parada de Planta en el cual realizan un benchmarking con empresas filiales, o empresas del mismo sector industrial, (IPA, 2011).
Adoptar los lineamientos del PMI para la dirección y gestión de Paradas de Planta para sectores industriales como el Petrolero, Petroquímico y Minero, ha sido un total éxito debido a la complejidad de sus proyectos y su alto costo. Este modelo de gestión de proyectos, lo están adoptando las grandes y medianas empresas de otros sectores de la economía internacional.
Las personas que dirigen y supervisan la parada planta influyen notablemente en el éxito o fracaso del proyecto. Para un proyecto de parada de planta es necesario disponer de un ambiente de trabajo y un equipo humano de alto desempeño para cumplir eficientemente con los objetivos del proyecto.
De la revisión bibliográfica y en el desarrollo del proyecto se concluye que es de suma importancia contar con herramientas informáticas o software para el desarrollo de proyectos, por la necesidad de informar a los interesados del proyecto en el escenario y tiempo adecuado, y a medida que avanza el proyecto la información se vuelve más compleja para llevarla en formatos.
Referencias
- 1. Alkemade, J, Jackson, J.A & Schroeder, B. (2011) ‘TRADE-OFF ECONOMICS IN REFINERY AND PLANT TURNAROUNDS’, AP Networks, consultado 10 agosto 2011.
- 2. Amendola, Luis. (2005) Dirección y Gestión de Paradas de Planta (The Theory of Constraints), Ediciones Espuela de Plata, España.
- 3. Amendola, Luis. (2006) Estrategias y Tácticas en la Dirección y Gestión de Proyectos, Editorial Universidad Politécnica de Valencia, España.
- 4. Amendola, L & Depool, T. (2006) ‘Mitigar los Riesgos en la Gestión de Paradas de Planta EDP”Estructura de Descomposición del Proyecto” WBS “Work Breakdown Structure” Mantenimiento’, PMM Institute for Learning, consultado 13 octubre 2011.
- 5. Amendola, L, Depool, T & Gonzáles, J.M. (2011) ‘STRATEGIC MODEL TO MANAGEMENT MULTIPROJECTS BASED ON THE CRITICAL CHAIN METODOLOGY (CCPM)’, PMM Institute for Learning, consultado 1 febrero 2012.
- 6. Amendola, Luis. (2011) ‘Metodología de Dirección y Gestión de Proyectos de Paradas de Planta de Proceso’, consultado 6 agosto 2011.
- 7. Apaolaza, U & Oyarbide, A. (2005) ‘La aportación de la Cadena Crítica frente a la gestión clásica de proyectos’, IX Congreso de Ingeniería de Organización Gijón, España.
- 8. Contruction Industry Institute. (2011) ‘Project Life Cycle Matrix’, Construction-Institute.org, consultado 5 octubre 2011.
- 9. Duffuaa, S.O & Ben Daya, M.A. (2004) ‘Turnaround maintenance in petrochemical industry: Practices and suggested improvements’, Journal of Quality in Maintenance Engineering, vol. 10, no. 3, pp. 184-190, consultado 1 agosto 2011.
- 10. Duggan, M & Blayden, R. (2001) ‘Venture maintainability: a path to project success Why are some projects less successful than others and what can we do to improve?’, Journal of Quality in Maintenance Engineering, vol. 7, no. 4, pp. 241-251, consultado 12 agosto 2011.
- 11. Ertl, B. (2011) ‘Applying PMBOK to Shutdowns, Turnarounds and Outages’, Inter Plan Systems Inc, consultado 6 agosto 2011.
- 12. Gadze, J. (2011) ‘Demo Front End Loading (FEL)’, CVPRO.com, consultado 5 octubre 2011.
- 13. García, Santiago. (2010) La Contratación del Mantenimiento Industrial, Ediciones Díaz de Santos, España.
- 14. Gonzales, Francisco Javier. 2010 Reducción de Costes y Mejora de Resultados en Mantenimiento, FC Editorial, España.
- 15. Industrial Info Resources. (2011) ‘Intelligence on Petroleum Refineries throughout Latin America’, consultado 2 diciembre 2011.
- 16. Inter Plan Systems Inc. (2011) ‘Turnaround Project Management Primer – Justification for Managing Turnarounds’, consultado 10 agosto 2011.
- 17. IPA. (2011) ‘IPA’s Turnaround Evaluations’, Ipaglobal.com, consultado 5 octubre 2011.
- 18. Jones, M. (2004) ‘The Case for Front End Loading (FEL) and Constructability Reviews’, Professional Paper Delivered to the Greater New Orleans Chapter, Project Management Institute, consultado 5 octubre 2011.
- 19. Joshi, N. (2003) ‘Benchmarking and Best Practices for Turnarounds’, IQPC Turnaround Conference, London, England.
- 20. Lenahan, Tom. (1999) Turnaround Management, Butterworth-Heinemann, Oxford.
- 21. Levitt, A & Wurtmann, B. (2008) Shutdown Risk Management, New Standard Institute, consultado 6 agosto.
- 22. McLay, John. (2011) ‘Practical Management for Plant Turnarounds’, ReliabilityWeb.com, consultado 15 agosto 2011.
- 23. Method 123. (2011) ‘Risk Management’, Method 123, consultado 3 octubre 2011.
- 24. Muiño, A. (2011) ‘Real Risk’, PMI Global Congress Proceedings, Dublin, Ireland.
- 25. Parra, M. (2011) ‘Planificación de una parada de refinería: Caso Proyecto RLP10.1b Refinería La Pampilla Perú’, Encuentro de Directores de Proyectos PMI Chapter de Madrid, consultado 5 octubre 2011.
- 26. Pockarel, S & Jiao, J.R. (2008) ‘Turnaround maintenance management in a processing industry: A case study’, Journal of Quality in Maintenance Engineering, vol. 14, no. 2, pp. 109-122, consultado 6 agosto 2011.
Autor: Nain Aguado Quintero
Ingeniero Mecánico, con especialización en diseño de maquinaria y equipo agroindustrial y MBA en Dirección
Proyectos, Universidad Viña del Mar (Chile).
Consultor en gestión de mantenimiento y conabilidad lubricación y dirección de proyectos en ABSG Colombia
Director General de LubricarOnLine.com.co.
Bogotá, Colombia
Correo: naguado@absconsulting.com
Dinos qué te ha parecido el artículo
Artículos recomendados
La Confiabilidad Humana Estrategia para la Gestión de Activos

Cómo perder la inocencia

Si usted no construye su filosofía de mantenimiento, ninguna estrategia que utilice le servirá completamente

Consecuencias de la Desinformación

Publica tu artículo en la revista #1 de Mantenimiento Industrial
Publicar un artículo en la revista es gratis, no tiene costo.
Solo debes asegurarte que no sea un artículo comercial.
¿Qué esperas?
O envía tu artículo directo: articulos@predictiva21.com
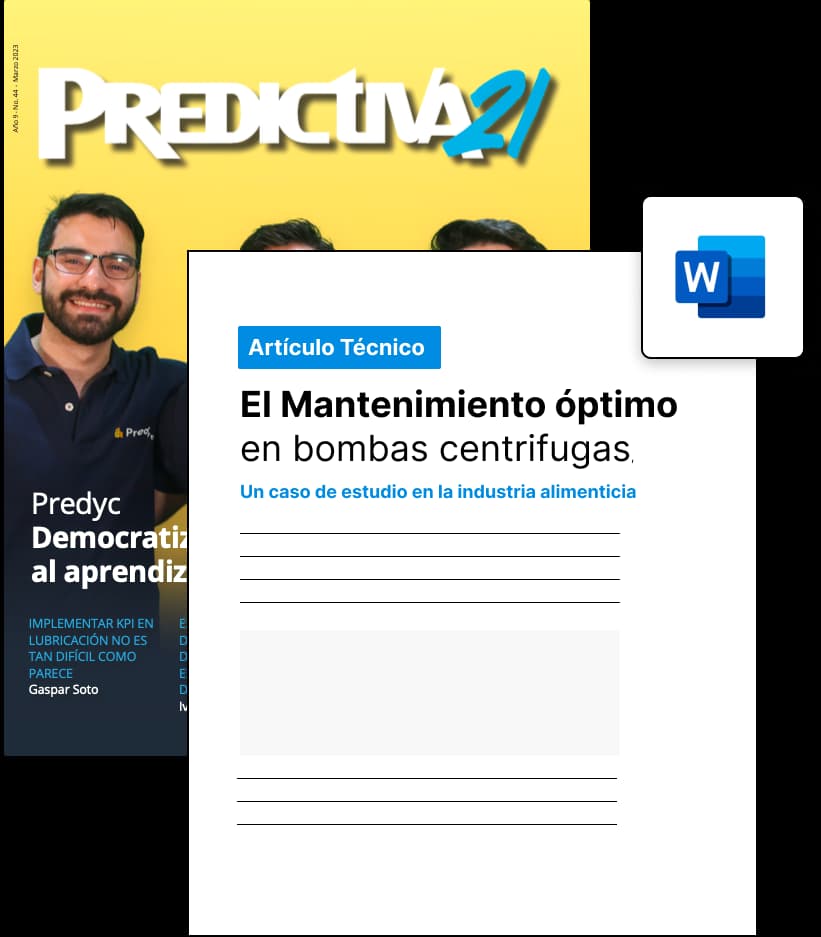