Mantenibilidad
Articulo13 de octubre de 2021
Breve historia de la mantenibilidad
Una de las primeras referencias a la mantenibilidad se remonta al año 1901, al contrato del Cuerpo de Señales del Ejército de los Estados Unidos de América. Esto, para el desarrollo del avión de los hermanos Wright, en el que se establecía claramente que el avión debía ser sencillo de manejar y mantener.
Entonces, el inicio formal de esta disciplina se remonta al periodo entre la Segunda Guerra Mundial y la década de 1950. De ahí, se iniciaron varios esfuerzos directa o indirectamente con la mantenibilidad. Por ejemplo, uno de estos esfuerzos es una serie de 12 artículos en 1956. Estos cubrían temas como el diseño de equipos electrónicos para su mantenimiento. Asimismo, incluían recomendaciones para el diseño de acceso al mantenimiento en los equipos electrónicos, y el diseño para la instalación.
El primer libro comercial sobre esta disciplina fue el Electronic Maintainability. Este libro fue publicado en 1960. A lo largo de los años se han producido muchos otros desarrollos en el campo de la mantenibilidad.
La mantenibilidad en la industria
La industria estadounidense gasta alrededor de 300 billones de dólares en mantenimiento de plantas y operaciones. Por tal motivo, la mantenibilidad se está convirtiendo en un factor muy portante debido a los altos costos de mantenimiento de los equipos y sistemas.
Así, algunos de los objetivos de la aplicación de los principios de la ingeniería de la mantenibilidad a los sistemas y equipos son reducir el coste y el tiempo de mantenimiento previstos. Esto, mediante modificaciones de diseño dirigidas simplificación del mantenimiento. Asimismo, utilizando los datos de mantenibilidad para estimar la disponibilidad o indisponibilidad del equipo. De esta forma, se puede determinar las horas de trabajo y otros recursos relacionados necesarios para realizar el mantenimiento previsto.
Ingeniería en mantenibilidad vs ingeniería en mantenimiento
Como la mantenibilidad y el mantenimiento están estrechamente relacionados, a muchas personas les resulta difícil distinguirlos. La mantenibilidad se refiere a las medidas o pasos tomados durante la fase de diseño del producto. Esto, para incluir características que aumenten la facilidad de mantenimiento y garanticen el menor tiempo de inactividad y bajos costes de soporte del ciclo de vida.
Por otro lado, el mantenimiento son las medidas adoptadas por los usuarios del producto para mantenerlo en estado operativo o repararlo para devolverlo al mismo. En otras palabras, la mantenibilidad es un parámetro de diseño destinado a minimizar el tiempo de reparación de los equipos. Al contrario, el mantenimiento es el acto de revisar y reparar los equipos.
La responsabilidad de los ingenieros de mantenimiento es garantizar que los requisitos de diseño y desarrollo del producto o equipo reflejen las necesidades de mantenimiento de los usuarios. Por eso, se ocupan de factores como el entorno en el que se va a utilizar y mantener el producto. Por ejemplo, los perfiles de misión, operación y soporte del producto y del sistema; y los niveles y tipos de mantenimiento necesarios.
Mantenibilidad vs confiabilidad
La capacidad de mantenimiento es una característica de diseño e instalación incorporada que proporciona al equipo o producto resultante con una capacidad inherente de ser mantenido. Esto, le permite mejorar la disponibilidad de la misión y reducir los costes de mantenimiento. Asimismo, reduce las herramientas y los equipos necesarios, el nivel de conocimientos y las horas de trabajo.
Por el contrario, la fiabilidad es una característica de diseño que conduce a la durabilidad del equipo. Esto, porque realiza la función que se le ha asignado de acuerdo con una condición y período de tiempo especificado. Se consigue mediante acciones como la elección de principios óptimos de ingeniería: las pruebas, el control de los procesos y el dimensionamiento satisfactorio de los componentes.
Cálculo de la mantenibilidad
El cálculo de la mantenibilidad es una disciplina compleja en sí misma. Como se trata de una probabilidad, es una estimación basada en otros indicadores de mantenimiento.
Tiempo Medio de Reparación (MTTR)
El tiempo medio de reparación es una de las principales métricas del mantenimiento industrial. La fórmula es la siguiente:

El MTTR es un buen indicador de la mantenibilidad en sí mismo. Es decir, cuanto menor sea el tiempo medio de reparación, más probable será que se corrija una avería. Asimismo, el downtime (o tiempo muerto) es menor en los activos con mayor mantenibilidad. Entonces, si deseamos guiarnos por esta métrica, un buen estándar a considerar sería un MTTR de 5 horas. Así, un downtime de 50H a lo largo del año debería corresponder a por lo menos 10 averías.
Existe una función de mantenibilidad, M(t), que corresponde a la estimación de la probabilidad de completar una acción de reparación en un período de tiempo determinado. Así, la forma más común de hacer el cálculo es a través de la distribución logarítmica normal que resulta de los valores asociados con el MTTR y otros dos indicadores (vea gráfica de figura 2).
Cursos recomendados




%252FImagen%252FRAMPREDYC-1730060420837.webp%3Falt%3Dmedia%26token%3D2634a7f0-988e-4022-b91f-382503e6e9db&w=3840&q=75)



Mediana del Tiempo Medio de Reparación
El tiempo necesario para realizar la mitad de las acciones de reparación. A continuación, veremos un gráfico donde se representa:

Tiempo Máximo de Reparación
Mmax es el tiempo máximo establecido para completar un determinado porcentaje de todas las acciones de reparación. Por ejemplo, el 90% de las acciones de reparación deben realizarse en una hora.
Consejos para mejorar la Mantenibilidad
Para mejorar la mantenibilidad de nuestros activos es necesario empezar a reparar las averías lo más rápido posible. Para hacerlo, dejamos 4 ideas para empezar:
- Entrenar mejor a tu equipo.
Cuanta más formación se le ofrezca a los técnicos, especialmente a los nuevos contratados, mejor. Si nuestro equipo tiene horarios rotación, más rápido podrán actuar ante una emergencia. Asimismo, debemos fomentar el trabajo en equipo y reunir a todos los técnicos en torno a un objetivo común, en lugar de centrarse sólo en el rendimiento individual.
- Concentrar más información en cada activo.
Concentrar toda la información sobre el activo y las tareas de reparación. Eso hace que los técnicos de mantenimiento tarden menos tiempo en darse cuenta de lo que necesitan hacer y cuáles piezas puedan necesitar. Preferiblemente, se puede usar un software o una app con versión para móvil para que puedan acceder a esa información desde cualquier lugar.
- Adquirir equipos similares.
Otra forma de ahorrar tiempo en las reparaciones es adquirir equipos similares, como hacen las aerolíneas. Así, los técnicos se familiarizarán más fácilmente con todos los equipos; por otra parte, es probable que las piezas sean compatibles con varios equipos, lo que facilita la gestión de las existencias.
- Aumentar el mantenimiento planificado.
Cuando se trata de mantenimiento industrial, el mantenimiento correctivo casi siempre implica largos períodos de downtime. Así, una de las mejores estrategias que se pueden adoptar para aumentar la mantenibilidad es aumentar el porcentaje de mantenimiento planificado.
Dinos qué te ha parecido el artículo
Artículos recomendados
7.5 Importancia del ACR

Dónde estudiar técnico en mantenimiento industrial

Iso 55000: norma de activos físicos

Análisis dinámico

Publica tu artículo en la revista #1 de Mantenimiento Industrial
Publicar un artículo en la revista es gratis, no tiene costo.
Solo debes asegurarte que no sea un artículo comercial.
¿Qué esperas?
O envía tu artículo directo: articulos@predictiva21.com
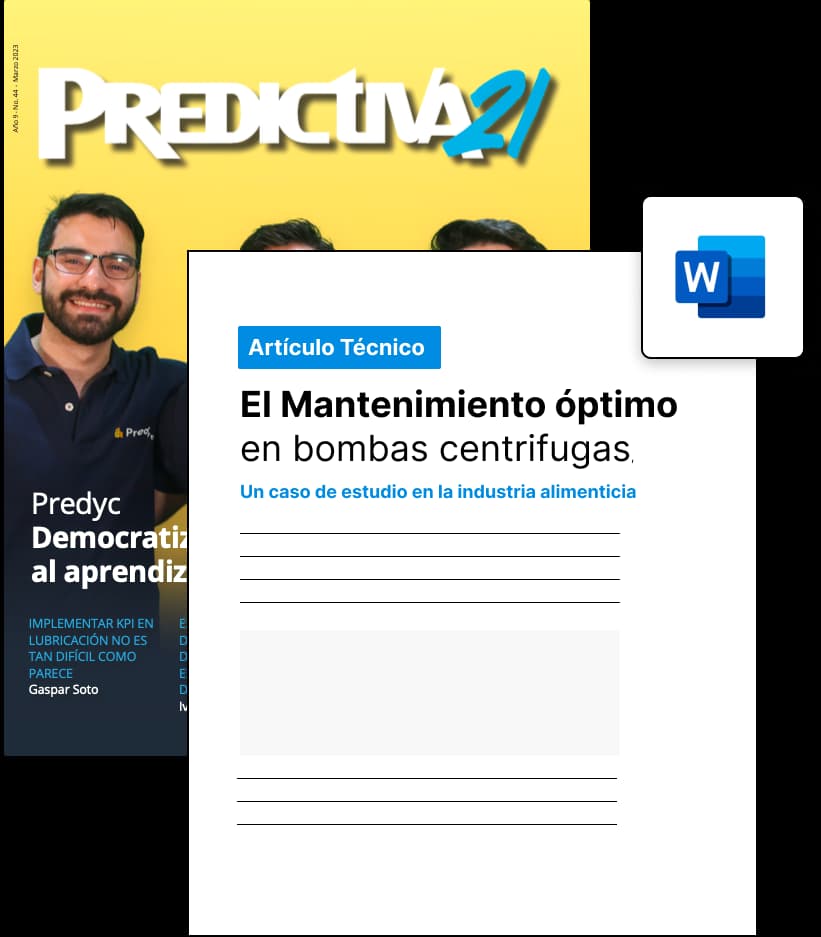
Mantenibilidad
Articulo 13 de octubre de 2021Breve historia de la mantenibilidad
Una de las primeras referencias a la mantenibilidad se remonta al año 1901, al contrato del Cuerpo de Señales del Ejército de los Estados Unidos de América. Esto, para el desarrollo del avión de los hermanos Wright, en el que se establecía claramente que el avión debía ser sencillo de manejar y mantener.
Entonces, el inicio formal de esta disciplina se remonta al periodo entre la Segunda Guerra Mundial y la década de 1950. De ahí, se iniciaron varios esfuerzos directa o indirectamente con la mantenibilidad. Por ejemplo, uno de estos esfuerzos es una serie de 12 artículos en 1956. Estos cubrían temas como el diseño de equipos electrónicos para su mantenimiento. Asimismo, incluían recomendaciones para el diseño de acceso al mantenimiento en los equipos electrónicos, y el diseño para la instalación.
El primer libro comercial sobre esta disciplina fue el Electronic Maintainability. Este libro fue publicado en 1960. A lo largo de los años se han producido muchos otros desarrollos en el campo de la mantenibilidad.
La mantenibilidad en la industria
La industria estadounidense gasta alrededor de 300 billones de dólares en mantenimiento de plantas y operaciones. Por tal motivo, la mantenibilidad se está convirtiendo en un factor muy portante debido a los altos costos de mantenimiento de los equipos y sistemas.
Así, algunos de los objetivos de la aplicación de los principios de la ingeniería de la mantenibilidad a los sistemas y equipos son reducir el coste y el tiempo de mantenimiento previstos. Esto, mediante modificaciones de diseño dirigidas simplificación del mantenimiento. Asimismo, utilizando los datos de mantenibilidad para estimar la disponibilidad o indisponibilidad del equipo. De esta forma, se puede determinar las horas de trabajo y otros recursos relacionados necesarios para realizar el mantenimiento previsto.
Ingeniería en mantenibilidad vs ingeniería en mantenimiento
Como la mantenibilidad y el mantenimiento están estrechamente relacionados, a muchas personas les resulta difícil distinguirlos. La mantenibilidad se refiere a las medidas o pasos tomados durante la fase de diseño del producto. Esto, para incluir características que aumenten la facilidad de mantenimiento y garanticen el menor tiempo de inactividad y bajos costes de soporte del ciclo de vida.
Por otro lado, el mantenimiento son las medidas adoptadas por los usuarios del producto para mantenerlo en estado operativo o repararlo para devolverlo al mismo. En otras palabras, la mantenibilidad es un parámetro de diseño destinado a minimizar el tiempo de reparación de los equipos. Al contrario, el mantenimiento es el acto de revisar y reparar los equipos.
La responsabilidad de los ingenieros de mantenimiento es garantizar que los requisitos de diseño y desarrollo del producto o equipo reflejen las necesidades de mantenimiento de los usuarios. Por eso, se ocupan de factores como el entorno en el que se va a utilizar y mantener el producto. Por ejemplo, los perfiles de misión, operación y soporte del producto y del sistema; y los niveles y tipos de mantenimiento necesarios.
Mantenibilidad vs confiabilidad
La capacidad de mantenimiento es una característica de diseño e instalación incorporada que proporciona al equipo o producto resultante con una capacidad inherente de ser mantenido. Esto, le permite mejorar la disponibilidad de la misión y reducir los costes de mantenimiento. Asimismo, reduce las herramientas y los equipos necesarios, el nivel de conocimientos y las horas de trabajo.
Por el contrario, la fiabilidad es una característica de diseño que conduce a la durabilidad del equipo. Esto, porque realiza la función que se le ha asignado de acuerdo con una condición y período de tiempo especificado. Se consigue mediante acciones como la elección de principios óptimos de ingeniería: las pruebas, el control de los procesos y el dimensionamiento satisfactorio de los componentes.
Cálculo de la mantenibilidad
El cálculo de la mantenibilidad es una disciplina compleja en sí misma. Como se trata de una probabilidad, es una estimación basada en otros indicadores de mantenimiento.
Tiempo Medio de Reparación (MTTR)
El tiempo medio de reparación es una de las principales métricas del mantenimiento industrial. La fórmula es la siguiente:

El MTTR es un buen indicador de la mantenibilidad en sí mismo. Es decir, cuanto menor sea el tiempo medio de reparación, más probable será que se corrija una avería. Asimismo, el downtime (o tiempo muerto) es menor en los activos con mayor mantenibilidad. Entonces, si deseamos guiarnos por esta métrica, un buen estándar a considerar sería un MTTR de 5 horas. Así, un downtime de 50H a lo largo del año debería corresponder a por lo menos 10 averías.
Existe una función de mantenibilidad, M(t), que corresponde a la estimación de la probabilidad de completar una acción de reparación en un período de tiempo determinado. Así, la forma más común de hacer el cálculo es a través de la distribución logarítmica normal que resulta de los valores asociados con el MTTR y otros dos indicadores (vea gráfica de figura 2).
Cursos recomendados




%252FImagen%252FRAMPREDYC-1730060420837.webp%3Falt%3Dmedia%26token%3D2634a7f0-988e-4022-b91f-382503e6e9db&w=3840&q=75)



Mediana del Tiempo Medio de Reparación
El tiempo necesario para realizar la mitad de las acciones de reparación. A continuación, veremos un gráfico donde se representa:

Tiempo Máximo de Reparación
Mmax es el tiempo máximo establecido para completar un determinado porcentaje de todas las acciones de reparación. Por ejemplo, el 90% de las acciones de reparación deben realizarse en una hora.
Consejos para mejorar la Mantenibilidad
Para mejorar la mantenibilidad de nuestros activos es necesario empezar a reparar las averías lo más rápido posible. Para hacerlo, dejamos 4 ideas para empezar:
- Entrenar mejor a tu equipo.
Cuanta más formación se le ofrezca a los técnicos, especialmente a los nuevos contratados, mejor. Si nuestro equipo tiene horarios rotación, más rápido podrán actuar ante una emergencia. Asimismo, debemos fomentar el trabajo en equipo y reunir a todos los técnicos en torno a un objetivo común, en lugar de centrarse sólo en el rendimiento individual.
- Concentrar más información en cada activo.
Concentrar toda la información sobre el activo y las tareas de reparación. Eso hace que los técnicos de mantenimiento tarden menos tiempo en darse cuenta de lo que necesitan hacer y cuáles piezas puedan necesitar. Preferiblemente, se puede usar un software o una app con versión para móvil para que puedan acceder a esa información desde cualquier lugar.
- Adquirir equipos similares.
Otra forma de ahorrar tiempo en las reparaciones es adquirir equipos similares, como hacen las aerolíneas. Así, los técnicos se familiarizarán más fácilmente con todos los equipos; por otra parte, es probable que las piezas sean compatibles con varios equipos, lo que facilita la gestión de las existencias.
- Aumentar el mantenimiento planificado.
Cuando se trata de mantenimiento industrial, el mantenimiento correctivo casi siempre implica largos períodos de downtime. Así, una de las mejores estrategias que se pueden adoptar para aumentar la mantenibilidad es aumentar el porcentaje de mantenimiento planificado.
Dinos qué te ha parecido el artículo
Artículos recomendados
Educación Formal para el Mantenimiento

Optimizando las finanzas de tu empresa a través de estrategias de confiabilidad

Tribología Centrada en Confiabilidad

Integración de la Termografía Infrarroja como técnica del Mantenimiento Predictivo en el diagnóstico de condiciones de compresores reciprocantes

Publica tu artículo en la revista #1 de Mantenimiento Industrial
Publicar un artículo en la revista es gratis, no tiene costo.
Solo debes asegurarte que no sea un artículo comercial.
¿Qué esperas?
O envía tu artículo directo: articulos@predictiva21.com
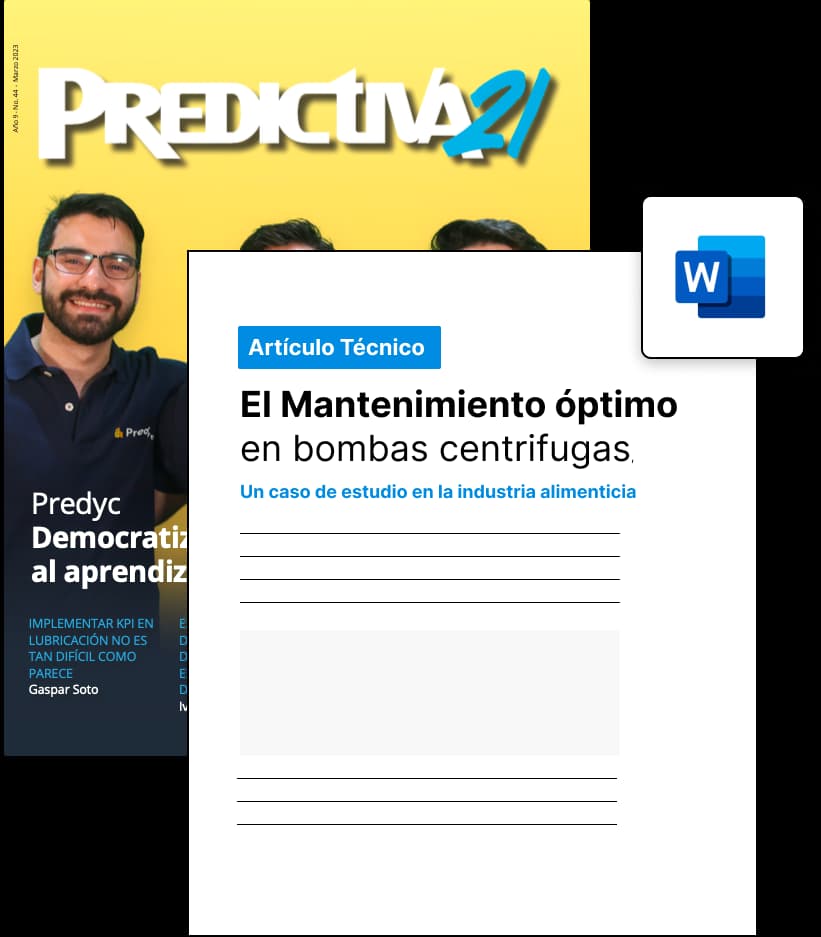