

Índice
Edición 51
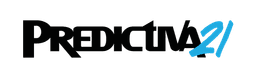
Índice
-1736548234131.png%3Falt%3Dmedia%26token%3D736c3425-6f93-423e-8703-0940d8e9afec&w=2048&q=75)
Alejandro José Godoy Rodríguez
Editor y CEO de Predictiva21.
alejandro.godoy@predictiva21.com
Enrique Javier González Hernández
Fundador y Chairman de Predictiva21.
enrique.gonzalez@predictiva21.com
Lisset Chávez González
Dirección Editorial.
lisset.chavez@predictiva21.com

EDITORIAL
Estimados lectores, colaboradores y miembros de la comunidad Predictiva21,
Es un honor darles la bienvenida a este 2025, un año que llega cargado de nuevas oportunidades, aprendizajes y retos emocionantes. Les deseo de todo corazón un año lleno de éxitos, bienestar y crecimiento en cada uno de sus proyectos personales y profesionales.
En esta edición especial, nos sentimos profundamente honrados de contar con la participación de Doc Palmer, autor del emblemático libro McGraw-Hill’s “Maintenance Planning and Scheduling Handbook”. Su experiencia y visión han sido fuente de inspiración para muchos en nuestra comunidad, y tener la oportunidad de entrevistarlo es un privilegio que nos llena de orgullo.
Asimismo, quiero expresar mi más sincero agradecimiento por la oportunidad de liderar Predictiva21 como su nuevo CEO a partir de este año. Es un inmenso privilegio formar parte de un equipo tan apasionado y comprometido, y mi compromiso es apoyar y fortalecer a nuestra comunidad de mantenimiento, confiabilidad y gestión de activos. Juntos, seguiremos construyendo el futuro con excelencia y dedicación.
Gracias por acompañarnos en este viaje. Estoy seguro de que, con su apoyo y colaboración, este 2025 será un año memorable para todos.
Alejandro Godoy
Editor y CEO Predictiva21
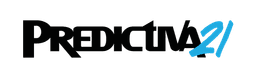
-1736548234131.png%3Falt%3Dmedia%26token%3D736c3425-6f93-423e-8703-0940d8e9afec&w=2048&q=75)
Alejandro José Godoy Rodríguez
Editor y CEO de Predictiva21.
alejandro.godoy@predictiva21.com
Enrique Javier González Hernández
Fundador y Chairman de Predictiva21.
enrique.gonzalez@predictiva21.com
Lisset Chávez González
Dirección Editorial.
lisset.chavez@predictiva21.com

EDITORIAL
Estimados lectores, colaboradores y miembros de la comunidad Predictiva21,
Es un honor darles la bienvenida a este 2025, un año que llega cargado de nuevas oportunidades, aprendizajes y retos emocionantes. Les deseo de todo corazón un año lleno de éxitos, bienestar y crecimiento en cada uno de sus proyectos personales y profesionales.
En esta edición especial, nos sentimos profundamente honrados de contar con la participación de Doc Palmer, autor del emblemático libro McGraw-Hill’s “Maintenance Planning and Scheduling Handbook”. Su experiencia y visión han sido fuente de inspiración para muchos en nuestra comunidad, y tener la oportunidad de entrevistarlo es un privilegio que nos llena de orgullo.
Asimismo, quiero expresar mi más sincero agradecimiento por la oportunidad de liderar Predictiva21 como su nuevo CEO a partir de este año. Es un inmenso privilegio formar parte de un equipo tan apasionado y comprometido, y mi compromiso es apoyar y fortalecer a nuestra comunidad de mantenimiento, confiabilidad y gestión de activos. Juntos, seguiremos construyendo el futuro con excelencia y dedicación.
Gracias por acompañarnos en este viaje. Estoy seguro de que, con su apoyo y colaboración, este 2025 será un año memorable para todos.
Alejandro Godoy
Editor y CEO Predictiva21
Calendario de cursos
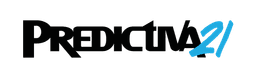
Calendario de cursos
Septiembre 2025
Octubre 2025
%252FImagen%252Frcm-1730083250826.webp%3Falt%3Dmedia%26token%3D3775356a-7b11-4c44-b21f-45b3409fb9ed&w=128&q=75)
04 de octubre: Mantenimiento Centrado en Confiabilidad (RCM)
Instructor: Andrés González
En línea en vivo%252FImagen%252FCausa-Raiz%2520(1)-1730084035822.webp%3Falt%3Dmedia%26token%3D6a899482-2409-4068-acf2-34abe035ded6&w=128&q=75)
04 de octubre: Análisis Causa Raíz (RCA)
Instructor: Guillermo Morán
En línea en vivo
15 de octubre: Planificación, Programación y Costos de Mantenimiento
Instructor: Jose Contreras Marquez
En línea en vivo
25 de octubre: Aplicación de la ISO 14224 en la Gestión de Mantenimiento y Confiabilidad
Instructor: Carlos Villegas
En línea en vivoNoviembre 2025
%252FImagen%252FRAMPREDYC-1730060420837.webp%3Falt%3Dmedia%26token%3D2634a7f0-988e-4022-b91f-382503e6e9db&w=128&q=75)
01 de noviembre: Análisis de Confiabilidad, Disponibilidad y Mantenibilidad (RAM)
Instructor: Enrique González
En línea en vivo
11 de noviembre: Costos y Presupuestos de Mantenimiento
Instructor: Jose Contreras Marquez
En línea en vivo
22 de noviembre: Preparación para la certificación CMRP
Instructor: Gyogi Mitsuta
En línea en vivo%2520D.%2520Palmer%2520-%2520Espa%25C3%25B1ol%252Fbanner%2520palmenr-1738359252325.png%3Falt%3Dmedia%26token%3D29e44409-8d11-4253-8700-286468e1ea21&w=3840&q=100)
Entrevista Richard (Doc) D. Palmer - Español
Entrevista
Gracias por permitirme compartir mi pasión: la planificación y programación del mantenimiento.
Por favor, acompáñame también en YouTube.com@palmerplanning, LinkedIn y en mi sitio web www.palmerplanning.com, donde también podrás ver mi calendario con los próximos talleres públicos, además de artículos y presentaciones anteriores. Puedes contactarme en docpalmer@palmerplanning.com
%2520D.%2520Palmer%2520-%2520Espa%25C3%25B1ol%252Fimage-1741365694331-1741365694332.png%3Falt%3Dmedia%26token%3D9192c656-cdad-4726-8ba8-05c432aaeaa4&w=640&q=75)
1) ¿Cómo surgió la idea de escribir el "Maintenance Planning and Scheduling Handbook" de McGraw-Hill, y cuál fue tu objetivo al crearlo?
Curiosamente, fue el editor McGraw-Hill quien me pidió escribir el manual. Recientemente había obtenido mi MBA y había sido seleccionado por un Director Asociado (vicepresidente) de la compañía eléctrica JEA para unirme a su equipo. Pronto me asignó a un proyecto en curso para mejorar el mantenimiento de las plantas de energía. Las habilidades empresariales que había adquirido, incluyendo la teoría organizacional (¡un tema fascinante sin duda!), me ayudaron a “ajustar” la planificación y programación del mantenimiento, lo que resultó en un gran aumento de la productividad laboral. Poco después, en 1995, escribí un artículo para una revista titulado Un día en la vida de un planificador. Este artículo mostraba cómo imaginaba que los planificadores llevarían a cabo su jornada, lo que llevó a McGraw-Hill a contactarme. Me sentí muy honrado y agradecido por la oportunidad de ayudar a otros, ya que en su momento no había podido encontrar un manual ni mucha literatura que me ayudara.
2) ¿Puedes destacar algunos desafíos específicos que las organizaciones suelen enfrentar al implementar una planificación y programación de mantenimiento efectiva, y cómo aborda tu manual estos desafíos?
La planificación y programación exitosas involucran conceptos complejos, y las empresas no manejan fácilmente lo complejo. El éxito requiere, sin duda, la comprensión y el impulso por parte de la dirección. Mi manual se enfoca en darle al agente de cambio de la empresa un “control absoluto” sobre el qué, por qué y cómo funciona, y cómo obtener el apoyo de la dirección.
La mayoría de las personas piensa que la planificación se trata de decirles a los operarios qué hacer. Pero los operarios resienten ese enfoque, y estos programas de planificación fracasan, a menudo de manera espectacular y frustrante. En cambio, una planificación adecuada consiste en aplicar un ciclo Deming de mejora continua, donde la dirección explica claramente que los planificadores simplemente brindan “arranques” que mejoran con el tiempo gracias a la retroalimentación de los operarios. En efecto, los planificadores deben ser “historiadores de oficio” para los operarios que “poseen” el plan. (En el lenguaje de la teoría organizacional de Dr. Mintzberg, la coordinación adecuada del mantenimiento consiste en tratar el mantenimiento como una burocracia profesional con los operarios profesionales desempeñando la función de planificación como apoyo. No es una burocracia mecánica con los planificadores establecidos como una tecnostructura que da reglas a los operarios. jajaja) Implementado correctamente, el Ciclo Deming mejora los planes con los años, llevando a una ejecución del trabajo de mayor calidad.
De manera similar, la mayoría de las personas cree que la programación consiste en dictar por adelantado lo que todos harán la próxima semana, y que el propósito de la programación es completar el programa. Estos programas de programación suelen fracasar, a veces manifestándose en frustración y otras veces en la duda: "¿qué estamos logrando con esto?". En cambio, una programación adecuada se trata de derrotar la Ley de Parkinson para aumentar la productividad, ayudándonos a completar más trabajo del que normalmente completaríamos. La Ley de Parkinson (la cantidad de trabajo asignado expande hasta llenar el tiempo disponible) requiere que carguemos completamente los horarios semanales y aceptemos una menor adhesión al horario; ¡no debemos esperar completar todo el programa! Con la incertidumbre de las duraciones exactas de los trabajos y la incidencia de trabajos reactivos nuevos, no podemos hacer programas diarios elaborados con una semana de antelación. Pero no necesitamos hacerlo. Lo único que necesitamos es comenzar a cada equipo con una lista sencilla de órdenes de trabajo que coincidan con las horas disponibles para cada oficio durante toda la semana. Esta semana completa sirve como una “misión” que acelera la finalización de las órdenes de trabajo. (En el lenguaje empresarial de Dr. Drucker, la mayoría de las empresas malinterpreta el verdadero objetivo de la programación.) El verdadero objetivo es ayudarnos a completar más trabajo del que normalmente completaríamos. Sin embargo, la mayoría de las empresas cree que el objetivo de la programación es completar el programa o saber lo que todos harán por adelantado. Subcargan el programa para asegurar su cumplimiento y así no logran vencer la Ley de Parkinson, y no obtienen un aumento en la productividad. Muchas empresas también desperdician una enorme cantidad de tiempo haciendo programas diarios anticipados y luego modificándolos completamente cada día durante el resto de la semana.
El Maintenance Planning and Scheduling Handbook explica estos conceptos y establece principios orientadores para hacerlos funcionar con ejemplos de la planificación de órdenes de trabajo y creación de horarios. Varios capítulos y apéndices también tratan sobre computadoras, mantenimiento preventivo, mantenimiento predictivo, proyectos, almacenes, auditorías y otros aspectos asociados con la planificación y programación. El manual proporciona ejemplos reales de empresas que han tenido éxito.
3) Con la evolución de la tecnología, ¿cómo han impactado las herramientas digitales y el software en el campo de la planificación y programación del mantenimiento, y cómo deben adaptarse los profesionales a estos cambios?
La digitalización de CMMS (Sistemas de Gestión de Mantenimiento Computarizados) y EAM (Gestión de Activos Empresariales) ha mejorado definitivamente el mantenimiento, incluida la planificación y programación. Los planificadores pueden crear y reutilizar más fácilmente planes de trabajo vivos. Pueden encontrar planes de trabajo similares a nivel global como punto de partida. Los analistas de mantenimiento predictivo (PdM) tienen una cantidad creciente de tecnologías más allá del análisis de vibraciones, infrarrojos y ultrasonido. Con PdM, el truco está en que la dirección debe fomentar una cultura que impulse la búsqueda, planificación, programación y ejecución del trabajo en equipos que funcionen “suavemente”. Los ingenieros pueden resolver problemas más fácilmente investigando bases de datos y situaciones similares (¿Dónde hemos encontrado antes este modo de falla?). Los gerentes pueden ver más fácilmente las tendencias (¿Estamos haciendo más PM o menos PM?).
El libro de William Biekert, que se publicará próximamente, Beyond the Delusion, habla perfectamente sobre la necesidad absoluta de que la dirección insista en que los ingenieros de proyectos entreguen un activo digital correspondiente cada vez que instalen un activo físico. La planta debe tener su gemelo electrónico al finalizar la puesta en marcha.
Un inconveniente de la digitalización es suponer que la computadora nos dirá cómo hacer el mantenimiento. “Tan pronto como el CMMS esté completamente implementado, todo estará bien” son dos mentiras. Una persona que no sabe sumar, multiplicar, restar ni dividir no tiene nada que hacer con una calculadora de mano. La computadora no sabe que el mantenimiento se trata de evitar que las cosas se rompan, no simplemente de arreglar rápidamente las cosas cuando se rompen. La computadora nos permitirá hacer lo incorrecto más rápido. Debemos tener cuidado de que la computadora no nos distraiga de las estrategias adecuadas.
4) ¿Podrías compartir una historia de éxito memorable en la que la implementación de una planificación y programación de mantenimiento sólida mejoró significativamente el rendimiento y la confiabilidad general de una instalación u operación?
La planificación y programación no son la “bala de plata”. Las plantas deben implementar todas las partes de la ecuación del mantenimiento. En JEA en los años 90, “arreglamos” la planificación y programación, el almacén, el mantenimiento predictivo, el análisis de causa raíz, la clasificación de proyectos, la disponibilidad de supervisores en campo, la formación e incluso las herramientas manuales. Pasamos de ser una empresa eléctrica con la peor disponibilidad y las tarifas eléctricas más altas a tener una de las mejores disponibilidades y las tarifas más bajas. En otra empresa en la que ayudé después, el Distrito Metropolitano de Alcantarillado de Cincinnati ganó el premio de Uptime Magazine al Mejor Programa Emergente de Confiabilidad de Mantenimiento en 2013. Cincinnati desarrolló su programa de PdM y renovó los PM para sus sistemas más necesitados con RCM (Mantenimiento Centrado en la Confiabilidad). La planificación y programación proporcionaron la productividad que estos programas necesitaban para ejecutar el trabajo proactivo adicional y mejorar la confiabilidad general.
5) Dado tu vasta experiencia, ¿qué consejo le darías a los jóvenes profesionales que ingresan al campo de la planificación y programación del mantenimiento, y qué habilidades consideras cruciales para tener éxito en este rol?
Nunca debemos dejar de aprender. Hay tantas empresas por ahí con diferentes partes del conocimiento que funciona. Obviamente, la habilidad necesaria es tener sed de aprendizaje continuo. Debemos asistir a conferencias de mantenimiento y conocer a otros profesionales para ver qué están haciendo. Necesitamos desarrollar redes personales donde podamos “saber a quién preguntar” y preguntar sin temor. La mayoría de la gente está dispuesta a compartir.
6) ¿Cómo ves la evolución futura de la planificación y programación del mantenimiento, y qué tendencias o innovaciones crees que jugarán un papel significativo en los próximos años?
Creo que cada vez más empresas adoptarán las mejores prácticas de planificación y programación, pero al mismo tiempo, el mantenimiento como profesión parece tener una puerta giratoria, sus líderes van y vienen. Los líderes pasan por el mantenimiento en su camino hacia roles generales de planta o incluso corporativos. Veo muchas caras nuevas en las mismas empresas que visito a lo largo de los años.
Creo que veremos que la inteligencia artificial (IA) nos ayudará a identificar más rápido los problemas y planes de trabajo, pero debemos ser cautelosos. La IA nos proporcionará el consenso del pensamiento de la industria. Por definición, el consenso es una buena práctica, pero no la mejor práctica de las pocas empresas que son excepcionalmente buenas. La IA nos dará un rápido impulso, desde cero hasta competir, pero no nos dará una ventaja competitiva. La precisión de los datos numéricos y las referencias también puede ser dudosa.
7) En tus interacciones con profesionales y empresas a nivel mundial, ¿has observado diferencias culturales que impacten el enfoque hacia la planificación y programación del mantenimiento, y cómo recomiendas abordar estas diferencias para una implementación efectiva?
He tenido la bendición de ver la "alegría de entender" la planificación y programación adecuadas en todo el mundo, a través de diferentes industrias y culturas. Los seres humanos nos beneficiamos todos de la ayuda del Dr. Deming, quien nos enseña que debemos admitir que los planes no son perfectos, y del Dr. Drucker, quien nos recuerda que el verdadero objetivo de la programación es completar más trabajo, no completar el cronograma. No obstante, la dirección en todos estos lugares también muestra reticencia a aceptar los planes como meros puntos de partida, y a que los cronogramas no deben conducir a una alta conformidad con ellos. (¡Porque es raro!) Pero, precisamente por eso, la planificación y programación adecuadas son una ventaja competitiva.
8) ¿Puedes compartir algunos comentarios o historias de éxito de profesionales u organizaciones que hayan implementado las estrategias y principios delineados en tu manual, destacando el impacto positivo en sus operaciones?
Similar al éxito de JEA y Cincinnati mencionado anteriormente, he disfrutado escuchar de varias empresas que me han pedido ayuda. Aquí hay algunos ejemplos. Una empresa de agua en Texas logró un aumento del 40% en la tasa de finalización de órdenes de trabajo, pasando de 7 órdenes de trabajo por persona por semana a 10. Para su fuerza laboral de 50 personas, consiguieron el equivalente a 20 personas adicionales de manera gratuita para realizar más trabajo proactivo. Un gerente de mantenimiento de una empresa química en Ohio me contó que habían agotado todo su atraso dos meses después de mi visita. Una empresa de grano en España pasó de completar 339 órdenes de trabajo al mes a 228. ¡Este tipo de resultados realmente es emocionante!
9) Dado el creciente enfoque en la sostenibilidad en las industrias, ¿cómo puede la planificación y programación del mantenimiento contribuir a reducir el impacto ambiental y promover prácticas ecológicas?
Maravillosamente, la planificación y programación fomentan realizar más trabajo proactivo, lo cual reduce el trabajo reactivo. Engrasamos adecuadamente un cojinete a tiempo, en lugar de reemplazar el cojinete, causando daños colaterales y perdiendo producto. Reducimos el trabajo reactivo, que es inherentemente menos seguro porque tendríamos que apresurarnos. Reducimos el trabajo reactivo, que es inherentemente más perjudicial para el medio ambiente, porque ya estaríamos, o estaríamos a punto de, exceder los límites ambientales o cualquier situación ecológica. El mantenimiento proactivo es ese trabajo aburrido en las cosas antes de que se rompan, para evitar que se rompan, y nadie está gritando ni volviéndose loco.
10) Reflexionando sobre tu carrera, ¿cuál ha sido el aspecto más gratificante o satisfactorio de tu trabajo en el campo de la planificación y programación del mantenimiento?
Realmente he disfrutado mucho viajar y conocer amigos que comparten los mismos intereses por la excelencia en mantenimiento.
11) Más allá de tus contribuciones al campo del mantenimiento, ¿cómo imaginas tu legado en la formación y desarrollo de futuros profesionales en esta industria?
Me gustaría pensar que he ayudado a mis colegas a aprender y crecer, así como los colegas antes que yo me han ayudado a mí.
12) Dada la naturaleza dinámica de las industrias, ¿cómo te mantienes actualizado sobre las últimas tendencias y desarrollos en la planificación y programación del mantenimiento, y cómo recomiendas que los profesionales mantengan un aprendizaje continuo a lo largo de sus carreras?
De nuevo, asistir a conferencias me ayuda a estar al tanto de nuevos pensamientos e ideas. Personalmente, hacer presentaciones (aunque a veces resulta ser un dolor de cabeza en términos de tiempo) motiva a otros a venir a saludarme. Estas charlas fomentan el encuentro con personas y el desarrollo de redes.
13) Dada tu exitosa experiencia y el impacto significativo en la comunidad de profesionales del mantenimiento con el Maintenance Planning and Scheduling Handbook de McGraw-Hill, ¿tienes planes de escribir otro libro en el futuro cercano? Si es así, ¿podrías darnos un adelanto del tema que podría abordar?
El manual inicialmente me tomó CINCO años de escritura en mi tiempo libre mientras trabajaba a tiempo completo. Ahora, mientras consulto, sigo bastante ocupado. Me gusta escribir artículos para revistas y actualizo el manual cada cinco años con nuevos pensamientos y áreas temáticas, pero no habrá una secuela ni otro libro. Por otro lado, Jason Bolte (un colega de la industria que conocí en una conferencia) me ayudó a configurar un canal de YouTube. Cada semana charlo por unos minutos sobre planificación y programación. ¡Por favor, suscríbete y únete a mí! YouTube.com@docpalmerplanning
14) Fuera de tu carrera profesional, ¿puedes compartir una experiencia que haya tenido un impacto significativo en tu vida y que haya influido en tu perspectiva sobre la importancia de equilibrar el trabajo y la vida personal?
Mi padre siempre tuvo tiempo para nuestra familia e incluso fue Scoutmaster durante un tiempo en mi tropa de Boy Scouts. Nunca he visto el trabajo como un fin en sí mismo.
15) Además de tu destacada carrera profesional y contribuciones al campo del mantenimiento, ¿puedes compartir algunos de tus intereses o pasatiempos personales que te apasionan fuera del entorno laboral?
Mis intereses y mi tiempo definitivamente incluyen a mi esposa, hijas, iglesia, golf, jardinería y paisajismo (tengo una motosierra y sé cómo usarla). Me pregunto cómo tengo tiempo para disfrutar hablando sobre planificación y programación, ¡pero lo hago!
Gracias por permitirme ser parte de tu familia de mantenimiento y compartir hoy.
Dinos qué te ha parecido el artículo
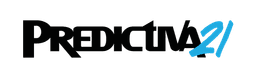
%2520D.%2520Palmer%2520-%2520Espa%25C3%25B1ol%252Fbanner%2520palmenr-1738359252325.png%3Falt%3Dmedia%26token%3D29e44409-8d11-4253-8700-286468e1ea21&w=3840&q=100)
Gracias por permitirme compartir mi pasión: la planificación y programación del mantenimiento.
Por favor, acompáñame también en YouTube.com@palmerplanning, LinkedIn y en mi sitio web www.palmerplanning.com, donde también podrás ver mi calendario con los próximos talleres públicos, además de artículos y presentaciones anteriores. Puedes contactarme en docpalmer@palmerplanning.com
%2520D.%2520Palmer%2520-%2520Espa%25C3%25B1ol%252Fimage-1741365694331-1741365694332.png%3Falt%3Dmedia%26token%3D9192c656-cdad-4726-8ba8-05c432aaeaa4&w=640&q=75)
1) ¿Cómo surgió la idea de escribir el "Maintenance Planning and Scheduling Handbook" de McGraw-Hill, y cuál fue tu objetivo al crearlo?
Curiosamente, fue el editor McGraw-Hill quien me pidió escribir el manual. Recientemente había obtenido mi MBA y había sido seleccionado por un Director Asociado (vicepresidente) de la compañía eléctrica JEA para unirme a su equipo. Pronto me asignó a un proyecto en curso para mejorar el mantenimiento de las plantas de energía. Las habilidades empresariales que había adquirido, incluyendo la teoría organizacional (¡un tema fascinante sin duda!), me ayudaron a “ajustar” la planificación y programación del mantenimiento, lo que resultó en un gran aumento de la productividad laboral. Poco después, en 1995, escribí un artículo para una revista titulado Un día en la vida de un planificador. Este artículo mostraba cómo imaginaba que los planificadores llevarían a cabo su jornada, lo que llevó a McGraw-Hill a contactarme. Me sentí muy honrado y agradecido por la oportunidad de ayudar a otros, ya que en su momento no había podido encontrar un manual ni mucha literatura que me ayudara.
2) ¿Puedes destacar algunos desafíos específicos que las organizaciones suelen enfrentar al implementar una planificación y programación de mantenimiento efectiva, y cómo aborda tu manual estos desafíos?
La planificación y programación exitosas involucran conceptos complejos, y las empresas no manejan fácilmente lo complejo. El éxito requiere, sin duda, la comprensión y el impulso por parte de la dirección. Mi manual se enfoca en darle al agente de cambio de la empresa un “control absoluto” sobre el qué, por qué y cómo funciona, y cómo obtener el apoyo de la dirección.
La mayoría de las personas piensa que la planificación se trata de decirles a los operarios qué hacer. Pero los operarios resienten ese enfoque, y estos programas de planificación fracasan, a menudo de manera espectacular y frustrante. En cambio, una planificación adecuada consiste en aplicar un ciclo Deming de mejora continua, donde la dirección explica claramente que los planificadores simplemente brindan “arranques” que mejoran con el tiempo gracias a la retroalimentación de los operarios. En efecto, los planificadores deben ser “historiadores de oficio” para los operarios que “poseen” el plan. (En el lenguaje de la teoría organizacional de Dr. Mintzberg, la coordinación adecuada del mantenimiento consiste en tratar el mantenimiento como una burocracia profesional con los operarios profesionales desempeñando la función de planificación como apoyo. No es una burocracia mecánica con los planificadores establecidos como una tecnostructura que da reglas a los operarios. jajaja) Implementado correctamente, el Ciclo Deming mejora los planes con los años, llevando a una ejecución del trabajo de mayor calidad.
De manera similar, la mayoría de las personas cree que la programación consiste en dictar por adelantado lo que todos harán la próxima semana, y que el propósito de la programación es completar el programa. Estos programas de programación suelen fracasar, a veces manifestándose en frustración y otras veces en la duda: "¿qué estamos logrando con esto?". En cambio, una programación adecuada se trata de derrotar la Ley de Parkinson para aumentar la productividad, ayudándonos a completar más trabajo del que normalmente completaríamos. La Ley de Parkinson (la cantidad de trabajo asignado expande hasta llenar el tiempo disponible) requiere que carguemos completamente los horarios semanales y aceptemos una menor adhesión al horario; ¡no debemos esperar completar todo el programa! Con la incertidumbre de las duraciones exactas de los trabajos y la incidencia de trabajos reactivos nuevos, no podemos hacer programas diarios elaborados con una semana de antelación. Pero no necesitamos hacerlo. Lo único que necesitamos es comenzar a cada equipo con una lista sencilla de órdenes de trabajo que coincidan con las horas disponibles para cada oficio durante toda la semana. Esta semana completa sirve como una “misión” que acelera la finalización de las órdenes de trabajo. (En el lenguaje empresarial de Dr. Drucker, la mayoría de las empresas malinterpreta el verdadero objetivo de la programación.) El verdadero objetivo es ayudarnos a completar más trabajo del que normalmente completaríamos. Sin embargo, la mayoría de las empresas cree que el objetivo de la programación es completar el programa o saber lo que todos harán por adelantado. Subcargan el programa para asegurar su cumplimiento y así no logran vencer la Ley de Parkinson, y no obtienen un aumento en la productividad. Muchas empresas también desperdician una enorme cantidad de tiempo haciendo programas diarios anticipados y luego modificándolos completamente cada día durante el resto de la semana.
El Maintenance Planning and Scheduling Handbook explica estos conceptos y establece principios orientadores para hacerlos funcionar con ejemplos de la planificación de órdenes de trabajo y creación de horarios. Varios capítulos y apéndices también tratan sobre computadoras, mantenimiento preventivo, mantenimiento predictivo, proyectos, almacenes, auditorías y otros aspectos asociados con la planificación y programación. El manual proporciona ejemplos reales de empresas que han tenido éxito.
3) Con la evolución de la tecnología, ¿cómo han impactado las herramientas digitales y el software en el campo de la planificación y programación del mantenimiento, y cómo deben adaptarse los profesionales a estos cambios?
La digitalización de CMMS (Sistemas de Gestión de Mantenimiento Computarizados) y EAM (Gestión de Activos Empresariales) ha mejorado definitivamente el mantenimiento, incluida la planificación y programación. Los planificadores pueden crear y reutilizar más fácilmente planes de trabajo vivos. Pueden encontrar planes de trabajo similares a nivel global como punto de partida. Los analistas de mantenimiento predictivo (PdM) tienen una cantidad creciente de tecnologías más allá del análisis de vibraciones, infrarrojos y ultrasonido. Con PdM, el truco está en que la dirección debe fomentar una cultura que impulse la búsqueda, planificación, programación y ejecución del trabajo en equipos que funcionen “suavemente”. Los ingenieros pueden resolver problemas más fácilmente investigando bases de datos y situaciones similares (¿Dónde hemos encontrado antes este modo de falla?). Los gerentes pueden ver más fácilmente las tendencias (¿Estamos haciendo más PM o menos PM?).
El libro de William Biekert, que se publicará próximamente, Beyond the Delusion, habla perfectamente sobre la necesidad absoluta de que la dirección insista en que los ingenieros de proyectos entreguen un activo digital correspondiente cada vez que instalen un activo físico. La planta debe tener su gemelo electrónico al finalizar la puesta en marcha.
Un inconveniente de la digitalización es suponer que la computadora nos dirá cómo hacer el mantenimiento. “Tan pronto como el CMMS esté completamente implementado, todo estará bien” son dos mentiras. Una persona que no sabe sumar, multiplicar, restar ni dividir no tiene nada que hacer con una calculadora de mano. La computadora no sabe que el mantenimiento se trata de evitar que las cosas se rompan, no simplemente de arreglar rápidamente las cosas cuando se rompen. La computadora nos permitirá hacer lo incorrecto más rápido. Debemos tener cuidado de que la computadora no nos distraiga de las estrategias adecuadas.
4) ¿Podrías compartir una historia de éxito memorable en la que la implementación de una planificación y programación de mantenimiento sólida mejoró significativamente el rendimiento y la confiabilidad general de una instalación u operación?
La planificación y programación no son la “bala de plata”. Las plantas deben implementar todas las partes de la ecuación del mantenimiento. En JEA en los años 90, “arreglamos” la planificación y programación, el almacén, el mantenimiento predictivo, el análisis de causa raíz, la clasificación de proyectos, la disponibilidad de supervisores en campo, la formación e incluso las herramientas manuales. Pasamos de ser una empresa eléctrica con la peor disponibilidad y las tarifas eléctricas más altas a tener una de las mejores disponibilidades y las tarifas más bajas. En otra empresa en la que ayudé después, el Distrito Metropolitano de Alcantarillado de Cincinnati ganó el premio de Uptime Magazine al Mejor Programa Emergente de Confiabilidad de Mantenimiento en 2013. Cincinnati desarrolló su programa de PdM y renovó los PM para sus sistemas más necesitados con RCM (Mantenimiento Centrado en la Confiabilidad). La planificación y programación proporcionaron la productividad que estos programas necesitaban para ejecutar el trabajo proactivo adicional y mejorar la confiabilidad general.
5) Dado tu vasta experiencia, ¿qué consejo le darías a los jóvenes profesionales que ingresan al campo de la planificación y programación del mantenimiento, y qué habilidades consideras cruciales para tener éxito en este rol?
Nunca debemos dejar de aprender. Hay tantas empresas por ahí con diferentes partes del conocimiento que funciona. Obviamente, la habilidad necesaria es tener sed de aprendizaje continuo. Debemos asistir a conferencias de mantenimiento y conocer a otros profesionales para ver qué están haciendo. Necesitamos desarrollar redes personales donde podamos “saber a quién preguntar” y preguntar sin temor. La mayoría de la gente está dispuesta a compartir.
6) ¿Cómo ves la evolución futura de la planificación y programación del mantenimiento, y qué tendencias o innovaciones crees que jugarán un papel significativo en los próximos años?
Creo que cada vez más empresas adoptarán las mejores prácticas de planificación y programación, pero al mismo tiempo, el mantenimiento como profesión parece tener una puerta giratoria, sus líderes van y vienen. Los líderes pasan por el mantenimiento en su camino hacia roles generales de planta o incluso corporativos. Veo muchas caras nuevas en las mismas empresas que visito a lo largo de los años.
Creo que veremos que la inteligencia artificial (IA) nos ayudará a identificar más rápido los problemas y planes de trabajo, pero debemos ser cautelosos. La IA nos proporcionará el consenso del pensamiento de la industria. Por definición, el consenso es una buena práctica, pero no la mejor práctica de las pocas empresas que son excepcionalmente buenas. La IA nos dará un rápido impulso, desde cero hasta competir, pero no nos dará una ventaja competitiva. La precisión de los datos numéricos y las referencias también puede ser dudosa.
7) En tus interacciones con profesionales y empresas a nivel mundial, ¿has observado diferencias culturales que impacten el enfoque hacia la planificación y programación del mantenimiento, y cómo recomiendas abordar estas diferencias para una implementación efectiva?
He tenido la bendición de ver la "alegría de entender" la planificación y programación adecuadas en todo el mundo, a través de diferentes industrias y culturas. Los seres humanos nos beneficiamos todos de la ayuda del Dr. Deming, quien nos enseña que debemos admitir que los planes no son perfectos, y del Dr. Drucker, quien nos recuerda que el verdadero objetivo de la programación es completar más trabajo, no completar el cronograma. No obstante, la dirección en todos estos lugares también muestra reticencia a aceptar los planes como meros puntos de partida, y a que los cronogramas no deben conducir a una alta conformidad con ellos. (¡Porque es raro!) Pero, precisamente por eso, la planificación y programación adecuadas son una ventaja competitiva.
8) ¿Puedes compartir algunos comentarios o historias de éxito de profesionales u organizaciones que hayan implementado las estrategias y principios delineados en tu manual, destacando el impacto positivo en sus operaciones?
Similar al éxito de JEA y Cincinnati mencionado anteriormente, he disfrutado escuchar de varias empresas que me han pedido ayuda. Aquí hay algunos ejemplos. Una empresa de agua en Texas logró un aumento del 40% en la tasa de finalización de órdenes de trabajo, pasando de 7 órdenes de trabajo por persona por semana a 10. Para su fuerza laboral de 50 personas, consiguieron el equivalente a 20 personas adicionales de manera gratuita para realizar más trabajo proactivo. Un gerente de mantenimiento de una empresa química en Ohio me contó que habían agotado todo su atraso dos meses después de mi visita. Una empresa de grano en España pasó de completar 339 órdenes de trabajo al mes a 228. ¡Este tipo de resultados realmente es emocionante!
9) Dado el creciente enfoque en la sostenibilidad en las industrias, ¿cómo puede la planificación y programación del mantenimiento contribuir a reducir el impacto ambiental y promover prácticas ecológicas?
Maravillosamente, la planificación y programación fomentan realizar más trabajo proactivo, lo cual reduce el trabajo reactivo. Engrasamos adecuadamente un cojinete a tiempo, en lugar de reemplazar el cojinete, causando daños colaterales y perdiendo producto. Reducimos el trabajo reactivo, que es inherentemente menos seguro porque tendríamos que apresurarnos. Reducimos el trabajo reactivo, que es inherentemente más perjudicial para el medio ambiente, porque ya estaríamos, o estaríamos a punto de, exceder los límites ambientales o cualquier situación ecológica. El mantenimiento proactivo es ese trabajo aburrido en las cosas antes de que se rompan, para evitar que se rompan, y nadie está gritando ni volviéndose loco.
10) Reflexionando sobre tu carrera, ¿cuál ha sido el aspecto más gratificante o satisfactorio de tu trabajo en el campo de la planificación y programación del mantenimiento?
Realmente he disfrutado mucho viajar y conocer amigos que comparten los mismos intereses por la excelencia en mantenimiento.
11) Más allá de tus contribuciones al campo del mantenimiento, ¿cómo imaginas tu legado en la formación y desarrollo de futuros profesionales en esta industria?
Me gustaría pensar que he ayudado a mis colegas a aprender y crecer, así como los colegas antes que yo me han ayudado a mí.
12) Dada la naturaleza dinámica de las industrias, ¿cómo te mantienes actualizado sobre las últimas tendencias y desarrollos en la planificación y programación del mantenimiento, y cómo recomiendas que los profesionales mantengan un aprendizaje continuo a lo largo de sus carreras?
De nuevo, asistir a conferencias me ayuda a estar al tanto de nuevos pensamientos e ideas. Personalmente, hacer presentaciones (aunque a veces resulta ser un dolor de cabeza en términos de tiempo) motiva a otros a venir a saludarme. Estas charlas fomentan el encuentro con personas y el desarrollo de redes.
13) Dada tu exitosa experiencia y el impacto significativo en la comunidad de profesionales del mantenimiento con el Maintenance Planning and Scheduling Handbook de McGraw-Hill, ¿tienes planes de escribir otro libro en el futuro cercano? Si es así, ¿podrías darnos un adelanto del tema que podría abordar?
El manual inicialmente me tomó CINCO años de escritura en mi tiempo libre mientras trabajaba a tiempo completo. Ahora, mientras consulto, sigo bastante ocupado. Me gusta escribir artículos para revistas y actualizo el manual cada cinco años con nuevos pensamientos y áreas temáticas, pero no habrá una secuela ni otro libro. Por otro lado, Jason Bolte (un colega de la industria que conocí en una conferencia) me ayudó a configurar un canal de YouTube. Cada semana charlo por unos minutos sobre planificación y programación. ¡Por favor, suscríbete y únete a mí! YouTube.com@docpalmerplanning
14) Fuera de tu carrera profesional, ¿puedes compartir una experiencia que haya tenido un impacto significativo en tu vida y que haya influido en tu perspectiva sobre la importancia de equilibrar el trabajo y la vida personal?
Mi padre siempre tuvo tiempo para nuestra familia e incluso fue Scoutmaster durante un tiempo en mi tropa de Boy Scouts. Nunca he visto el trabajo como un fin en sí mismo.
15) Además de tu destacada carrera profesional y contribuciones al campo del mantenimiento, ¿puedes compartir algunos de tus intereses o pasatiempos personales que te apasionan fuera del entorno laboral?
Mis intereses y mi tiempo definitivamente incluyen a mi esposa, hijas, iglesia, golf, jardinería y paisajismo (tengo una motosierra y sé cómo usarla). Me pregunto cómo tengo tiempo para disfrutar hablando sobre planificación y programación, ¡pero lo hago!
Gracias por permitirme ser parte de tu familia de mantenimiento y compartir hoy.
Dinos qué te ha parecido el artículo
%2520D.%2520Palmer%2520-%2520Ingl%25C3%25A9s%252Fbanner%2520entrevista%2520palmer-1738359432757.png%3Falt%3Dmedia%26token%3D0cdb308f-6523-4643-8bc9-1ea2d57dac6f&w=3840&q=100)
Entrevista Richard (Doc) D. Palmer - Inglés
Entrevista
Thank you for letting me share my passion for maintenance planning and scheduling. Please also join me on YouTube (youtube.com/@palmerplanning), LinkedIn, and my website (www.palmerplanning.com), which also shows my schedule for upcoming public workshops, in addition to past articles and presentations. You can contact me at docpalmer@palmerplanning.com.
%2520D.%2520Palmer%2520-%2520Ingl%25C3%25A9s%252Fimage-1741365719570-1741365719571.png%3Falt%3Dmedia%26token%3D98c38437-2c89-4122-951f-2e8461e4d96f&w=640&q=75)
1.- How did the idea to write the McGraw-Hill's Maintenance Planning and Scheduling Handbook come about, and what was your goal in creating it?
Interestingly, publisher McGraw-Hill asked me to write the handbook. I had recently earned my MBA and been selected by an Associate Managing Director (vice-president) of the JEA electric utility to join his staff. He soon placed me within an ongoing project to improve powerplant maintenance. My newly acquired business skills including organizational theory (an exciting subject, no doubt!) helped me “adjust” maintenance planning and scheduling leading to a huge pop in work productivity. Soon after in 1995, I wrote a magazine article, A Day in the Life of a Planner. This article showed how I envisioned planners going about their day and led to McGraw-Hill calling me. I really felt honored and welcomed the opportunity to help others because earlier I had been unable to find any handbook or much literature to help me.
2.- Can you highlight some specific challenges that organizations commonly face in implementing effective maintenance planning and scheduling, and how does your handbook address these challenges?
Successful planning and scheduling both involve weird concepts and companies just don’t do weird easily. Success definitely requires management understanding and driving. My handbook focus is on giving the company change agent a “death grip” on the what, why, and how it works and how to get management support.
Most people think planning is about telling craftspersons what to do. But craftspersons resent that approach and these planning programs fail, spectacularly in frustration. Instead, proper planning is about running a Deming cycle of continuous improvement where management clearly explains planners are simply giving head starts that improve over time with craftsperson feedback. In effect, planners should be “craft historians” for the craftspersons who “own” the plan. (In the organizational theory language of Dr. Mintzberg, the proper coordination of maintenance is treating maintenance as a professional bureaucracy with professional craftspersons having the staff function of planning as an aid. It is not a machine bureaucracy with planners set up as a technostructure giving rules to the craftspersons. lol) Properly implemented, the Deming Cycle improves plans over the years leading to superior quality of job execution.
Similarly, most people think scheduling is dictating in advance what everyone will do next week and that the purpose of scheduling is to complete the schedule. These scheduling programs result in failure sometimes manifested as frustration and sometimes as wondering “what are we getting out of it.” Instead, proper scheduling is about defeating Parkinson’s Law to increase productivity, helping us complete more work than we would normally complete. Parkinson’s Law (the amount of work assigned expands to fill the time available) requires that we fully load weekly schedules and accept lower schedule compliance, we should not expect to complete the schedule! With the real-life churn of uncertainty of exact job durations and incidence of new reactive work, we cannot make elaborate daily schedules a week in advance. But we do not need to. Instead, all we need to do is start each crew off with a simple list of work orders matching the craft available hours for the entire week. This full week serves as a “mission” that accelerates craft work order completion. (In the business language of Dr. Drucker, most companies misunderstand the true objective of scheduling.) The true objective is to help us complete more work than we would normally complete. Instead, most companies think the objective of scheduling is to complete the schedule or know what everyone is doing in advance. They underload the schedule to ensure its completion and so fail to defeat Parkinson’s Law and do not get a productivity increase. Many companies also waste an enormous amount of time making advance daily schedules and then totally revising them every day for the rest of the week.)
The Maintenance Planning and Scheduling Handbook explains these concepts and sets forth guiding principles for making them work with examples of planning work orders and creating schedules. A number of chapters and appendices also deal with computers, preventive maintenance, predictive maintenance, projects, storerooms, audits, and other associated aspects of planning and scheduling. The handbook helpfully provides a number of real company examples of success.
3.- With the evolution of technology, how have digital tools and software impacted the field of maintenance planning and scheduling, and how should professionals adapt to these changes?
CMMS (Computerized Maintenance Management System) and EAM (Enterprise Asset Management) computerization definitely has improved maintenance, including planning and scheduling. Planners can more easily create and reuse living job plans. They can find similar job plans across global platforms as a head start. Predictive maintenance (PdM) analysts have an ever-increasing wealth of technology beyond vibration analysis, infra-red, and ultra sound. With PdM, the trick is that management must drive a culture of encouraging finding, planning, scheduling, and executing work on “smoothly” running equipment. The Engineers can solve more easily problems by researching data bases and similar situations (Where have we ever encountered this failure mode?) Managers can more easily see trends (Are we doing more and more PM or less and less PM?)
William Biekert’s soon-to-be-released book, Beyond the Delusion, speaks perfectly to the absolute need for management to insist that project engineers deliver a matching digital asset whenever they install a physical asset. The plant must have its electronic twin upon completion of commissioning.
A downside of computerization is presuming the computer will tell us how to do maintenance. “As soon as the CMMS is fully implemented, everything will be fine” is two lies. A person that does not know how to add, multiple, subtract, and divide has no business with a hand-held calculator. The computer does not know that maintenance is about keeping things from breaking and not simply about quickly fixing things when they break. The computer will let you do the wrong thing faster. Be cautious that the computer does not distract us from proper strategies.
4.- Could you share a memorable success story where the implementation of robust maintenance planning and scheduling significantly improved the overall performance and reliability of a facility or operation?
Planning and scheduling is (are) not the “silver bullet.” Plants have to implement all of the parts of the maintenance equation. At JEA in the 1990’s, we “fixed” planning and scheduling, the storeroom, PdM, root cause analysis, project ranking, field availability of supervisors, training, and even hand tools. We rose from an electric utility having the worst availability and the highest electric rates to having among the best availability and lowest rates. At another company I helped later, the Metropolitan Sewer District of Greater Cincinnati won Uptime magazine’s award for Best Emerging Maintenance Reliability Program in 2013. Cincinnati developed its PdM program and revamped PMs for its needy systems with RCM (Reliability Centered Maintenance). Planning and scheduling provided the productivity these programs needed to execute the extra proactive work to improve overall reliability.
5.- Given your extensive experience, what advice would you give to young professionals entering the field of maintenance planning and scheduling, and what skills do you consider crucial for success in this role?
We absolutely need never to stop learning. There are so many companies out there with different parts of knowing what works. Obviously, the skill needed is a thirst to keep learning. We must attend maintenance conferences and meet other professionals to see what everyone is doing. We need to develop personal networks where we can “know who to ask” and ask away. Most people are willing to share.
6.- How do you see the future of maintenance planning and scheduling evolving, and what trends or innovations do you anticipate playing a significant role in the years to come?
I think more and more companies will adopt best planning and scheduling practices, but at the same time, maintenance as a profession seems to have a revolving door, its leaders come and go. Leaders pass through maintenance on their way to overall plant or even corporate roles. I see many fresh faces at the same companies I visit over the years.
I think we’ll see AI (Artificial Intelligence) help us faster figure out issues and job plans, but we must be cautious. AI will give us the consensus of the industry thinking. By definition, the consensus is good practice, but not the best practice of the few companies that are unusually good. AI will give us a quick step up from scratch to competing, but not to a competitive edge. The accuracy of numerical data and references may also be suspect.
7.- In your interactions with professionals and companies globally, have you observed any cultural differences that impact the approach to maintenance planning and scheduling, and how do you recommend addressing these differences for effective implementation?
I’ve been blessed in seeing the common “joy of getting it” regarding proper planning and scheduling around the world across industries and cultures. Humans all benefit from Dr. Deming’s help that we must admit plans are not perfect and Dr. Drucker’s help that the real objective of scheduling is to complete more work, not complete the schedule. Nonetheless, management in all these places also has a reluctance to embrace plans as just head starts and schedules should not lead to high schedule compliance. (Because it’s weird!) But, that’s exactly why proper planning and scheduling is a competitive edge.
8.- Can you share some feedback or success stories from professionals or organizations that have implemented the strategies and principles outlined in your handbook, highlighting the positive impact on their operations?
Similar to JEA’s and Cincinnati’s success above, I have enjoyed hearing from a number of companies that have had me help out. Here are a few. A Texas water company achieved a 40% pop in work order completion rate going from 7 work orders per person per week to 10. For their 50-person workforce, they got the equivalent of an extra 20 persons for free to do more proactive work. A maintenance manager from an Ohio chemical company told me they had drained their entire backlog two months after I had left. A grain company in Spain went from completing 339 work orders a month from 228. This stuff is really exciting!
9.- Considering the increasing focus on sustainability in industries, how can maintenance planning and scheduling contribute to reducing environmental impact and promoting eco-friendly practices?
Wonderfully, planning and scheduling promotes doing more proactive work which reduces reactive work. We properly grease a bearing in time instead of replacing the bearing, having collateral damage, and losing product. We reduce reactive work which is inherently less safe because we would be rushing. We reduce reactive work which is inherently more against the environment because we would be already, or imminently about to be, exceeding environmental limits or any eco-friendly situations. Proactive maintenance is that boring work on things before things break to keep things from breaking and no one is shouting at anyone or going crazy.
10.- Reflecting on your career, what has been the most fulfilling or rewarding aspect of your work in the field of maintenance planning and scheduling?
I’ve really, really enjoyed traveling and meeting friends that share like interests in maintenance excellence.
11.- Beyond your contributions to the maintenance field, how do you envision your legacy in shaping the education and development of future professionals in this industry?
I’d like to think I’ve helped colleagues learn and grow, just as colleagues before me have helped me.
12.- Given the dynamic nature of industries, how do you stay updated on the latest trends and developments in maintenance planning and scheduling, and how do you recommend professionals maintain continuous learning throughout their careers?
Again, attending conferences helps me stay abreast of new thoughts and ideas. Personally presenting presentations myself (a pain in the neck sometimes time-wise) encourage others to come and greet me. These chats encourage meeting people and developing networks.
13.- Given your successful experience and significant impact on the maintenance professionals' community with McGraw-Hill's Maintenance Planning and Scheduling Handbook, do you have plans to write another book in the near future? If so, could you give us a preview of the topic it might cover?
The handbook initially took FIVE years to write on my own time while working a full-time job. Now, while consulting, I am still pretty busy. I like writing magazine articles and update the handbook every five years for new thoughts and subject areas, but there will not be a sequel or another book. On the other hand, Jason Bolte (an industry colleague I met at a conference!) helped me set up a YouTube channel. I chat each week for a few minutes about planning and scheduling. Please subscribe and join me! YouTube.com@docpalmerplanning
14.- Outside of your professional career, can you share an experience that has had a significant impact on your life and influenced your perspective on the importance of balancing work and personal life?
My father always had time for our family and was even Scoutmaster for a while for my Boy Scout troop. I’ve never thought of work as an end unto itself.
15.- In addition to your outstanding professional career and contributions to the field of maintenance, can you share some of your personal interests or hobbies that passionately engage you outside the work environment?
My interests and time definitely include my wife, daughters, church, golf, gardening, and landscaping (I have a chainsaw and I know how to use it). I wonder how I have time for enjoying talking about planning and scheduling, but I do.
Thank you for letting me be part of your maintenance family and sharing today!
Dinos qué te ha parecido el artículo
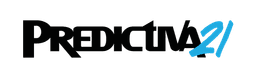
%2520D.%2520Palmer%2520-%2520Ingl%25C3%25A9s%252Fbanner%2520entrevista%2520palmer-1738359432757.png%3Falt%3Dmedia%26token%3D0cdb308f-6523-4643-8bc9-1ea2d57dac6f&w=3840&q=100)
Thank you for letting me share my passion for maintenance planning and scheduling. Please also join me on YouTube (youtube.com/@palmerplanning), LinkedIn, and my website (www.palmerplanning.com), which also shows my schedule for upcoming public workshops, in addition to past articles and presentations. You can contact me at docpalmer@palmerplanning.com.
%2520D.%2520Palmer%2520-%2520Ingl%25C3%25A9s%252Fimage-1741365719570-1741365719571.png%3Falt%3Dmedia%26token%3D98c38437-2c89-4122-951f-2e8461e4d96f&w=640&q=75)
1.- How did the idea to write the McGraw-Hill's Maintenance Planning and Scheduling Handbook come about, and what was your goal in creating it?
Interestingly, publisher McGraw-Hill asked me to write the handbook. I had recently earned my MBA and been selected by an Associate Managing Director (vice-president) of the JEA electric utility to join his staff. He soon placed me within an ongoing project to improve powerplant maintenance. My newly acquired business skills including organizational theory (an exciting subject, no doubt!) helped me “adjust” maintenance planning and scheduling leading to a huge pop in work productivity. Soon after in 1995, I wrote a magazine article, A Day in the Life of a Planner. This article showed how I envisioned planners going about their day and led to McGraw-Hill calling me. I really felt honored and welcomed the opportunity to help others because earlier I had been unable to find any handbook or much literature to help me.
2.- Can you highlight some specific challenges that organizations commonly face in implementing effective maintenance planning and scheduling, and how does your handbook address these challenges?
Successful planning and scheduling both involve weird concepts and companies just don’t do weird easily. Success definitely requires management understanding and driving. My handbook focus is on giving the company change agent a “death grip” on the what, why, and how it works and how to get management support.
Most people think planning is about telling craftspersons what to do. But craftspersons resent that approach and these planning programs fail, spectacularly in frustration. Instead, proper planning is about running a Deming cycle of continuous improvement where management clearly explains planners are simply giving head starts that improve over time with craftsperson feedback. In effect, planners should be “craft historians” for the craftspersons who “own” the plan. (In the organizational theory language of Dr. Mintzberg, the proper coordination of maintenance is treating maintenance as a professional bureaucracy with professional craftspersons having the staff function of planning as an aid. It is not a machine bureaucracy with planners set up as a technostructure giving rules to the craftspersons. lol) Properly implemented, the Deming Cycle improves plans over the years leading to superior quality of job execution.
Similarly, most people think scheduling is dictating in advance what everyone will do next week and that the purpose of scheduling is to complete the schedule. These scheduling programs result in failure sometimes manifested as frustration and sometimes as wondering “what are we getting out of it.” Instead, proper scheduling is about defeating Parkinson’s Law to increase productivity, helping us complete more work than we would normally complete. Parkinson’s Law (the amount of work assigned expands to fill the time available) requires that we fully load weekly schedules and accept lower schedule compliance, we should not expect to complete the schedule! With the real-life churn of uncertainty of exact job durations and incidence of new reactive work, we cannot make elaborate daily schedules a week in advance. But we do not need to. Instead, all we need to do is start each crew off with a simple list of work orders matching the craft available hours for the entire week. This full week serves as a “mission” that accelerates craft work order completion. (In the business language of Dr. Drucker, most companies misunderstand the true objective of scheduling.) The true objective is to help us complete more work than we would normally complete. Instead, most companies think the objective of scheduling is to complete the schedule or know what everyone is doing in advance. They underload the schedule to ensure its completion and so fail to defeat Parkinson’s Law and do not get a productivity increase. Many companies also waste an enormous amount of time making advance daily schedules and then totally revising them every day for the rest of the week.)
The Maintenance Planning and Scheduling Handbook explains these concepts and sets forth guiding principles for making them work with examples of planning work orders and creating schedules. A number of chapters and appendices also deal with computers, preventive maintenance, predictive maintenance, projects, storerooms, audits, and other associated aspects of planning and scheduling. The handbook helpfully provides a number of real company examples of success.
3.- With the evolution of technology, how have digital tools and software impacted the field of maintenance planning and scheduling, and how should professionals adapt to these changes?
CMMS (Computerized Maintenance Management System) and EAM (Enterprise Asset Management) computerization definitely has improved maintenance, including planning and scheduling. Planners can more easily create and reuse living job plans. They can find similar job plans across global platforms as a head start. Predictive maintenance (PdM) analysts have an ever-increasing wealth of technology beyond vibration analysis, infra-red, and ultra sound. With PdM, the trick is that management must drive a culture of encouraging finding, planning, scheduling, and executing work on “smoothly” running equipment. The Engineers can solve more easily problems by researching data bases and similar situations (Where have we ever encountered this failure mode?) Managers can more easily see trends (Are we doing more and more PM or less and less PM?)
William Biekert’s soon-to-be-released book, Beyond the Delusion, speaks perfectly to the absolute need for management to insist that project engineers deliver a matching digital asset whenever they install a physical asset. The plant must have its electronic twin upon completion of commissioning.
A downside of computerization is presuming the computer will tell us how to do maintenance. “As soon as the CMMS is fully implemented, everything will be fine” is two lies. A person that does not know how to add, multiple, subtract, and divide has no business with a hand-held calculator. The computer does not know that maintenance is about keeping things from breaking and not simply about quickly fixing things when they break. The computer will let you do the wrong thing faster. Be cautious that the computer does not distract us from proper strategies.
4.- Could you share a memorable success story where the implementation of robust maintenance planning and scheduling significantly improved the overall performance and reliability of a facility or operation?
Planning and scheduling is (are) not the “silver bullet.” Plants have to implement all of the parts of the maintenance equation. At JEA in the 1990’s, we “fixed” planning and scheduling, the storeroom, PdM, root cause analysis, project ranking, field availability of supervisors, training, and even hand tools. We rose from an electric utility having the worst availability and the highest electric rates to having among the best availability and lowest rates. At another company I helped later, the Metropolitan Sewer District of Greater Cincinnati won Uptime magazine’s award for Best Emerging Maintenance Reliability Program in 2013. Cincinnati developed its PdM program and revamped PMs for its needy systems with RCM (Reliability Centered Maintenance). Planning and scheduling provided the productivity these programs needed to execute the extra proactive work to improve overall reliability.
5.- Given your extensive experience, what advice would you give to young professionals entering the field of maintenance planning and scheduling, and what skills do you consider crucial for success in this role?
We absolutely need never to stop learning. There are so many companies out there with different parts of knowing what works. Obviously, the skill needed is a thirst to keep learning. We must attend maintenance conferences and meet other professionals to see what everyone is doing. We need to develop personal networks where we can “know who to ask” and ask away. Most people are willing to share.
6.- How do you see the future of maintenance planning and scheduling evolving, and what trends or innovations do you anticipate playing a significant role in the years to come?
I think more and more companies will adopt best planning and scheduling practices, but at the same time, maintenance as a profession seems to have a revolving door, its leaders come and go. Leaders pass through maintenance on their way to overall plant or even corporate roles. I see many fresh faces at the same companies I visit over the years.
I think we’ll see AI (Artificial Intelligence) help us faster figure out issues and job plans, but we must be cautious. AI will give us the consensus of the industry thinking. By definition, the consensus is good practice, but not the best practice of the few companies that are unusually good. AI will give us a quick step up from scratch to competing, but not to a competitive edge. The accuracy of numerical data and references may also be suspect.
7.- In your interactions with professionals and companies globally, have you observed any cultural differences that impact the approach to maintenance planning and scheduling, and how do you recommend addressing these differences for effective implementation?
I’ve been blessed in seeing the common “joy of getting it” regarding proper planning and scheduling around the world across industries and cultures. Humans all benefit from Dr. Deming’s help that we must admit plans are not perfect and Dr. Drucker’s help that the real objective of scheduling is to complete more work, not complete the schedule. Nonetheless, management in all these places also has a reluctance to embrace plans as just head starts and schedules should not lead to high schedule compliance. (Because it’s weird!) But, that’s exactly why proper planning and scheduling is a competitive edge.
8.- Can you share some feedback or success stories from professionals or organizations that have implemented the strategies and principles outlined in your handbook, highlighting the positive impact on their operations?
Similar to JEA’s and Cincinnati’s success above, I have enjoyed hearing from a number of companies that have had me help out. Here are a few. A Texas water company achieved a 40% pop in work order completion rate going from 7 work orders per person per week to 10. For their 50-person workforce, they got the equivalent of an extra 20 persons for free to do more proactive work. A maintenance manager from an Ohio chemical company told me they had drained their entire backlog two months after I had left. A grain company in Spain went from completing 339 work orders a month from 228. This stuff is really exciting!
9.- Considering the increasing focus on sustainability in industries, how can maintenance planning and scheduling contribute to reducing environmental impact and promoting eco-friendly practices?
Wonderfully, planning and scheduling promotes doing more proactive work which reduces reactive work. We properly grease a bearing in time instead of replacing the bearing, having collateral damage, and losing product. We reduce reactive work which is inherently less safe because we would be rushing. We reduce reactive work which is inherently more against the environment because we would be already, or imminently about to be, exceeding environmental limits or any eco-friendly situations. Proactive maintenance is that boring work on things before things break to keep things from breaking and no one is shouting at anyone or going crazy.
10.- Reflecting on your career, what has been the most fulfilling or rewarding aspect of your work in the field of maintenance planning and scheduling?
I’ve really, really enjoyed traveling and meeting friends that share like interests in maintenance excellence.
11.- Beyond your contributions to the maintenance field, how do you envision your legacy in shaping the education and development of future professionals in this industry?
I’d like to think I’ve helped colleagues learn and grow, just as colleagues before me have helped me.
12.- Given the dynamic nature of industries, how do you stay updated on the latest trends and developments in maintenance planning and scheduling, and how do you recommend professionals maintain continuous learning throughout their careers?
Again, attending conferences helps me stay abreast of new thoughts and ideas. Personally presenting presentations myself (a pain in the neck sometimes time-wise) encourage others to come and greet me. These chats encourage meeting people and developing networks.
13.- Given your successful experience and significant impact on the maintenance professionals' community with McGraw-Hill's Maintenance Planning and Scheduling Handbook, do you have plans to write another book in the near future? If so, could you give us a preview of the topic it might cover?
The handbook initially took FIVE years to write on my own time while working a full-time job. Now, while consulting, I am still pretty busy. I like writing magazine articles and update the handbook every five years for new thoughts and subject areas, but there will not be a sequel or another book. On the other hand, Jason Bolte (an industry colleague I met at a conference!) helped me set up a YouTube channel. I chat each week for a few minutes about planning and scheduling. Please subscribe and join me! YouTube.com@docpalmerplanning
14.- Outside of your professional career, can you share an experience that has had a significant impact on your life and influenced your perspective on the importance of balancing work and personal life?
My father always had time for our family and was even Scoutmaster for a while for my Boy Scout troop. I’ve never thought of work as an end unto itself.
15.- In addition to your outstanding professional career and contributions to the field of maintenance, can you share some of your personal interests or hobbies that passionately engage you outside the work environment?
My interests and time definitely include my wife, daughters, church, golf, gardening, and landscaping (I have a chainsaw and I know how to use it). I wonder how I have time for enjoying talking about planning and scheduling, but I do.
Thank you for letting me be part of your maintenance family and sharing today!
Dinos qué te ha parecido el artículo

Madurez del Mantenimiento
Artículo
Introducción
En las auditorías administrativas se evalúan, junto al personal de nivel de gestión de la propia empresa, sus condiciones funcionales y administrativas utilizando técnicas sencillas para la identificación de puntos donde puedan aplicarse acciones de mejora.Una de estas técnicas es la evaluación del grado de madurez de la empresa, desarrollado por Du Pont (1990) y perfeccionado por McKinsey (1995) y Topkins (2000).En esta técnica se establecen varios pilares, cada uno con varios niveles, donde dos gestores posicionan, según su juicio, la condición en que se encuentra su empresa.
Propuesta Du Pont
En la propuesta original de Du Pont se establecen 3 pilares:
- Características de una organización de mantenimiento;
- Prácticas y métodos típicos usados por las organizaciones de mantenimiento;
- Medidas de desempeño que tipifican una organización.
Para cada pilar se propone evaluar 3 niveles:
- Personas y Organización (Estructura, Formación, Supervisión, Apoyo, Administración, Sindicato, Terceros);
- Sistemas (Planificación, Sistema de gestión, Capacitación);
- Filosofías (Materiales, Misión, Metas, Expectativas de desempeño, Proyectos esenciales).
La propuesta de Du Pont, a la que siguieron las de McKinsey y Topkins, es que los directivos evalúen el grado de madurez de la empresa en la que trabajan, asignando una calificación (del 1 al 10) para cada pilar según su punto de vista. Para cada uno, también se asigna una calificación del 1 al 10. Es decir, cada pilar tendría su número de evaluación multiplicado por los números de evaluación de cada nivel, lo que daría, para cada evaluador, un mínimo total de 3 puntos (producto de 1 por el pilar por 1 por cada nivel) hasta 300, obteniéndose este valor máximo sumando los valores de los productos de los pilares con los tres niveles respectivos.Dado que el evaluador estaría asignando sus puntos a los tres pilares, su valor máximo general para la empresa sería de 900 puntos.
Por ejemplo: Si un evaluador asignara al pilar 1 una calificación de 8 y para los tres niveles de este pilar los valores de 9, 6 y 9, tendríamos un resultado de 8x9 + 8x6 + 8x9 para este pilar, totalizando 192 puntos. El mismo criterio se aplicaría a los pilares 2 y 3, donde, por ejemplo, el evaluador obtuvo totales de 161 y 180. Por lo tanto, este evaluador estaría obteniendo un total de 533 puntos. Se observa que, en este caso, el evaluador obtuvo una puntuación cercana al 59% del valor máximo, lo que puede considerarse razonable. Tomando las medias de otros tres evaluadores, por ejemplo 580, 605 y 701 puntos, tendríamos una visión de la madurez de esta empresa, que resaltaría los aspectos que es necesario mejorar, dentro de los recursos disponibles (financieros, logísticos, operativos, técnicos, estratégicos, etc.).
Propuesta McKinsey
En la propuesta de McKinsey se establece 12 pilares:
- Características de una organización de mantenimiento.
- Definición y selección de estrategias de mantenimiento (predictivo, preventivo, correctivo).
- Planificación del mantenimiento preventivo.
- Aplicación del mantenimiento predictivo.
- Mantenimiento correctivo.
- Control de resultados.
- Cultura de desempeño.
- Definición de la estrategia de reparaciones con recursos propios vs. Terceros.
- Equipo técnico - Plan de desarrollo del equipo.
- Gestión del equipo de terceros.
- Gestión de suministros - Control de stock.
- Gestión de suministros - Disponibilidad de repuestos.
Para cada pilar se establecen 5 niveles de elección:
- Débil
- Abajo del promedio
- Satisfactorio
- Arriba del promedio
- Clase mundial
Pilar 01 - Evaluación y segmentación de posibles fallas
- Débil: No hay análisis cuantitativo de fallas históricas;
- Abajo del Promedio: Hay un análisis de frecuencia de fallas de forma consolidada para la planta, que subsidia las estrategias de mantenimiento;
- Satisfactorio: Hay un análisis detallado de las posibles fallas por equipo con estimativas de impacto de downtime y pérdida de producción;
- Arriba del Promedio: Además de detallado por máquina y componentes, el análisis considera el grado de previsibilidad y frecuencia de las fallas;
- Clase Mundial: Criterio anterior + los análisis detallados son revisados y realimentan la estrategia de mantenimiento de la planta.
Pilar 02 - Definición y selección de estrategias de mantenimiento (predictivo, preventivo, correctivo)
- Débil: No hay análisis económico para la definición de la estrategia de mantenimiento;
- Abajo del Promedio: Hay una estimativa simple de los costos de suministro de reposición y de mano de obra con cada una de las estrategias;
- Satisfactorio: Hay un análisis detallado del impacto de la posible estrategia de mantenimiento en la probabilidad y en la frecuencia de falla. También hay comprensión de TCO (Total Cost of Ownership) de cada estrategia;
- Arriba del Promedio: Criterio anterior + Hay un análisis detallado de costos del impacto de las posibles estrategias de mantenimiento, considerando frecuencias de fallas, costos hora/máquina, tiempo de corrección y utilización del equipo;
- Clase Mundial: Criterio anterior + Hay una total integración entre los análisis de las posibles estrategias de mantenimiento y las definiciones de CAPEX para la planta, con foco en creación de valor.
Pilar 03 - Planificación del mantenimiento preventivo
- Débil: El planeamiento no posee un estándar definido;
- Abajo del Promedio: El planeamiento incluye la descripción general del trabajo y los materiales;
- Satisfactorio: El planeamiento incluye la descripción general del trabajo, los materiales y el número de horas de técnicos involucrados;
- Arriba del Promedio: El planeamiento incluye la descripción general del trabajo, los materiales, el número de horas de técnicos y el horario para inicio y finalización;
- Clase Mundial: Criterio anterior + Acompañamiento de la curva de aprendizaje (reducción de tiempo y costo). Integración entre predictiva y correctiva con intercambio de datos históricos y análisis.
Pilar 04 - Aplicación del mantenimiento predictivo
- Débil: No hay mantenimiento predictivo;
- Abajo del Promedio: Hay mantenimiento predictivo, pero solo en situaciones visibles de problemas en el funcionamiento;
- Satisfactorio: Hay mantenimiento predictivo para las partes/equipos de fácil identificación y previsibilidad de problemas. Hay análisis estadísticos de fallas;
- Arriba del Promedio: Criterio anterior + Se utilizan herramientas sofisticadas para procesamiento de señales (térmicos, vibratorios, eléctricos, etc.) recolectadas periódicamente;
- Clase Mundial: Criterio anterior + Las señales se recolectan en tiempo real. Acompañamiento de la curva de aprendizaje (reducción de tiempo y costo). Integración entre predictivo y correctivo con intercambio de datos históricos y análisis.
Pilar 05 - Mantenimiento Correctivo
- Débil: La identificación del problema se hace de forma empírica después de la rotura, sin apoyo de la ingeniería. Los operadores no están involucrados en el proceso;
- Abajo del Promedio: Hay un previo estudio de las principales fallas posibles y el proceso de acción sobre esas fallas se mantiene informal. Los operadores no están involucrados en el proceso;
- Satisfactorio: Hay una previsión de las fallas de mayor impacto y probabilidad, y un plan de acción detallado para el abordaje. Los operadores son capaces de realizar pequeñas reparaciones;
- Arriba del Promedio: Criterio anterior + Alto grado de participación de la ingeniería de mantenimiento y de procesos en la identificación de los problemas y en el plan de acción. Los operadores son capaces de prever problemas mayores;
- Clase Mundial: Criterio anterior + Acompañamiento de la curva de aprendizaje (reducción de tiempos y costos). Integración entre predictivo y correctivo con intercambio de datos históricos y análisis.
Pilar 06 - Control de Resultados
- Débil: No hay control de costos ni de tiempo;
- Abajo del Promedio: Hay controles rudimentarios de los principales centros de costos y del tiempo total de parada para actividades de mantenimiento;
- Satisfactorio: Hay controles para todos los costos de mantenimiento y el tiempo gastado en el desempeño de funciones de mantenimiento;
- Arriba del Promedio: Hay controles para todos los costos de mantenimiento, incluidos los costos de pérdida de ingresos y el tiempo gastado en las funciones. Estos controles son utilizados para benchmarking interno;
- Clase Mundial: Los controles son utilizados para imponer metas de mejora continua de tiempo y costo en todos los procesos.
Pilar 07 - Cultura de Desempeño
- Débil: No hay metas de desempeño específicas. Los equipos interfuncionales (Operación y Mantenimiento) tienen poca o ninguna participación en la resolución de problemas;
- Abajo del Promedio: Hay metas, pero no son monitoreadas ni seguidas. Los equipos interfuncionales (mantenimiento y operación) se usan muy raramente;
- Satisfactorio: Hay metas y son monitoreadas, pero poco divulgadas. La responsabilidad por las metas es informal. Los equipos interfuncionales están institucionalizados, pero no logran resultados en la creación de mejores prácticas;
- Arriba del Promedio: Las metas son monitoreadas y divulgadas, pero no existe una cultura de desempeño. Los equipos interfuncionales tienen un alto impacto con ideas generadas por la alta gerencia;
- Clase Mundial: Las metas son monitoreadas, divulgadas y sirven de base para la remuneración variable. Los equipos interfuncionales aportan ideas de mejora a la alta gestión y generan un alto impacto en los cambios.
Pilar 08 - Definición de la estrategia de reparaciones con recursos propios vs. terceros
- Débil: Todos los reparos se hacen internamente, sin análisis crítico;
- Abajo del Promedio: Algunas reparaciones se hacen por terceros, pero no hay un proceso claro de decisión;
- Satisfactorio: Hay un proceso de decisión que toma en cuenta el impacto potencial de reducción de costo con materiales y mano de obra;
- Arriba del Promedio: Criterio anterior + Hay un proceso de decisión que considera el nivel de servicio (grado de habilidad de los terceros vs. el equipo interno) y posibles sinergias o beneficios estratégicos de no tercerizar;
- Clase Mundial: Criterio anterior + Las decisiones de tercerización o no de funciones de mantenimiento son revisadas periódicamente para todos los equipos.
Pilar 09 - Equipo técnico - Plan de desarrollo del equipo
- Débil: No hay un plan de desarrollo definido;
- Abajo del Promedio: Hay un plan de desarrollo, pero las atribuciones y calificaciones en cada nivel no son claras;
- Satisfactorio: Hay una visión clara de las calificaciones necesarias por función en cada nivel, sin embargo, el sistema de evaluación de desempeño y retroalimentación es informal y de bajo impacto;
- Arriba del Promedio: Criterio anterior + Hay gran armonía entre los sistemas de evaluación de desempeño/retroalimentación y el plan de desarrollo/funciones;
- Clase Mundial: Criterio anterior + Los atributos y calificaciones necesarios son constantemente reevaluados según cambios tecnológicos o estratégicos.
Pilar 10 - Gestión del equipo de terceros
- Débil: No hay tercerización de funciones de mantenimiento;
- Abajo del Promedio: No hay monitoreo ni evaluación del prestador de servicios;
- Satisfactorio: El prestador de servicios es evaluado de manera informal o en grandes tareas;
- Arriba del Promedio: La mayor parte de los trabajos son acompañados. El prestador de servicios es evaluado según calidad, cumplimiento de plazos y tareas propuestas;
- Clase Mundial: Todos los trabajos son evaluados (o por lo menos de forma estadística). El pago de los servicios está directamente ligado al desempeño, plazos y desarrollo de las tareas. Hay un esfuerzo de mejora continua junto a los proveedores.
Pilar 11 - Gestión de Suministros - Control de Stock
- Débil: No hay control formal de ítems de mantenimiento. Hay muchas piezas para equipos ya desactivados. No existen intenciones de desarrollo de contratos de suministro;
- Abajo del Promedio: El control de ítems está constantemente desactualizado. Niveles mínimos y máximos de stock no son definidos. Se desarrollan contratos de suministro sin un plan preestablecido;
- Satisfactorio: Control de stock actualizado para algunos ítems. Niveles mínimos y máximos establecidos para algunos ítems. Existe un plan de desarrollo de contratos de suministro;
- Arriba del Promedio: Control de ítems actualizado para la mayoría de los ítems. Niveles mínimos y máximos establecidos para la mayoría de los ítems. Ítem anterior + 50% de los ítems de stock evaluados con base en el riesgo/frecuencia;
- Clase Mundial: Control de ítems actualizado para todos los ítems. Niveles mínimos y máximos establecidos para todos los ítems. Ítem anterior + 100% de los ítems de stock evaluados con base en el riesgo/frecuencia.
Pilar 12 - Gestión de Suministros - Disponibilidad de repuestos
- Débil: No hay una metodología para la ubicación de las piezas. Menos del 30% de las piezas están disponibles en una primera tentativa. No existe acondicionamiento adecuado. Menos del 30% de las piezas son inspeccionadas o tienen calidad asegurada;
- Abajo del Promedio: Hay diversas metodologías no integradas de búsqueda de piezas. El 30-50% de las piezas están disponibles en la primera búsqueda. Acondicionadas de forma adecuada. El 30-50% de las piezas son inspeccionadas o tienen calidad asegurada;
- Satisfactorio: Hay una metodología única de búsqueda de piezas, pero es poco amigable y de poca confianza. El 50-75% de las piezas están disponibles en la primera búsqueda. Acondicionadas de forma adecuada. El 50-75% de las piezas son inspeccionadas o tienen calidad asegurada;
- Arriba del Promedio: La metodología de búsqueda de piezas tiene un alto grado de confianza, pero es difícil de utilizar. El 75-90% de las piezas están disponibles en la primera búsqueda. Acondicionadas de forma adecuada y 50-75% de los casos entregados en el área. El 75-90% de las piezas son inspeccionadas o tienen calidad asegurada;
- Clase Mundial: La herramienta de búsqueda es fácil de usar y muy confiable. El 95-100% de las piezas están disponibles en la primera búsqueda. Acondicionadas de forma adecuada y más del 75% entregadas en el área. El 100% de las piezas tienen calidad asegurada.
A continuación, el promedio de la aplicación del método en más de 50 empresas:

Propuesta de Topkins
En la propuesta de Topkins se encuentran 7 pilares:
- Actitud de la gestión corporativa de la planta
- Estado organizacional del mantenimiento
- Porcentaje de pérdida de recursos debido al mantenimiento
- Solución de problemas de mantenimiento
- Calificación/entrenamiento del personal de mantenimiento
- Información de mantenimiento y desarrollo de acciones
- Resumen de la posición del mantenimiento en la compañía
Pilar 1 - Actitud de la gestión corporativa de la planta
- Inconsciente: No comprende lo que es mantenimiento preventivo, se repara solo cuando se rompe.
- Despertando: Reconoce que el mantenimiento puede ser mejorado, pero se siente incapaz de implementar cambios.
- Desarrollando: Aprende sobre ROI (retorno de inversión), desarrolla mayor interés y seguridad en mejorar el mantenimiento.
- Capacitado: Actitud participativa, reconoce que la gestión de mantenimiento es esencial y debe ser mandataria.
- Consciente: Integra el mantenimiento como una parte fundamental del sistema global de la compañía.
Pilar 2 - Estado organizacional del mantenimiento
- Inconsciente: Reactivo, trabaja en el equipo solo cuando falla; baja productividad del personal.
- Despertando: Aún reactivo, pero logra mejores recuperaciones de componentes y tiene repuestos disponibles cuando ocurre una falla.
- Desarrollando: Preventivo, realiza rutinas de inspección, lubricación, ajustes y pequeños servicios para mejorar el MTBF (tiempo medio entre fallas).
- Capacitado: Predictivo, utiliza técnicas como análisis de vibración, termografía, ultrasonido, etc., para monitorear la condición de los equipos y anticipar problemas.
- Consciente: Productivo, combina técnicas predictivas con la participación activa de los operadores para liberar a los técnicos de mantenimiento, mejorando la mantenibilidad.
Pilar 3 - Porcentual pérdida de recursos debido al mantenimiento
- Inconsciente: Más del 30%.
- Despertando: Entre 20% y 30%.
- Desarrollando: Entre 10% y 20%.
- Capacitado: Entre 5% y 10%.
- Consciente: Menos del 5%.
Pilar 4 - Solución de problemas de mantenimiento
- Inconsciente: Los problemas se desarrollan hasta que son descubiertos.
- Despertando: Se elaboran algunas acciones básicas. Comienza el análisis de fallas de manera elemental.
- Desarrollando: Los problemas se resuelven mediante la implementación de acciones de mantenimiento e ingeniería.
- Capacitado: Los problemas son anticipados. Se utiliza un fuerte equipo interdisciplinario de solución de problemas.
- Consciente: Los problemas son prevenidos.
Pilar 5 - Calificación/entrenamiento del personal de mantenimiento
- Inconsciente: Baja calidad de mano de obra, supervisión rígida, conocimientos obsoletos, pagos por antigüedad.
- Despertando: El personal siente que falta conocimiento para analizar fallas y comienza a cuestionar la especialización. Se reconoce la necesidad de capacitación.
- Desarrollando: Calidad en el trabajo. Se distribuye el desempeño de tareas, inversión en investigación, pagos por capacidad para resolver problemas.
- Capacitado: Expectativa de calidad en el trabajo. Realización de tareas por "multiespecialistas", conocimiento actualizado.
- Consciente: Orgullo y profesionalismo. Flexibilidad en la designación de tareas. Capacitación constante de los operadores por los mantenedores. Pago basado en la productividad de la planta.
Pilar 6 - Información de mantenimiento y desarrollo de acciones
- Inconsciente: El mantenimiento intenta realizar registros, pero la disciplina no es exigida y los datos son deficientes.
- Despertando: Se utiliza una orden de trabajo manual o computarizada, pero la planificación y programación son escasas o nulas.
- Desarrollando: Se utiliza una orden de trabajo manual o computarizada por mantenimiento, operación e ingeniería, con planificación e implementación de programación de servicios.
- Capacitado: Se utiliza un sistema de control de mantenimiento para todas las áreas de la compañía, con información disponible y consistente.
- Consciente: El sistema de información de mantenimiento está integrado con el sistema de información corporativo.
Pilar 7 - Resumen de la posición del mantenimiento en la compañía
- Inconsciente: “No sabemos cuál equipo se va a romper y por eso pagamos al mantenimiento. Las tasas de pérdidas son altas, pero no es un problema de mantenimiento.”
- Despertando: “¿Acaso nuestros competidores tienen estos problemas con sus equipos? ¡Las refacciones nos están costando mucho!”
- Desarrollando: “Con el nuevo criterio de gestión, empezamos a identificar y resolver los problemas.”
- Capacitado: “Todos reconocen que el mantenimiento es parte de nuestra rutina de calidad operacional. No podemos hacer productos de calidad con un mantenimiento deficiente.”
- Consciente: “No esperamos fallas y es una sorpresa cuando ocurren. ¡El mantenimiento contribuye para mantenernos entre los mejores!”
A continuación, se presenta el promedio de la aplicación del método en más de 100 empresas:

Conclusión
Lo importante de las Técnicas McKinsey y Topkins es que detallan la información de cada nivel en cada pilar.
Dado que estos métodos se aplican a directivos de los niveles operativo, ejecutivo y estratégico, esta información facilita la comprensión de sus posiciones, según el punto de vista de cada uno, sobre la situación de la empresa.
Al final de la evaluación de los directivos, se obtiene un valor promedio que es analizado por un grupo designado por la empresa para valorar la posibilidad de mejorar los niveles obtenidos.
Dinos qué te ha parecido el artículo
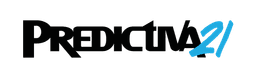
Introducción
En las auditorías administrativas se evalúan, junto al personal de nivel de gestión de la propia empresa, sus condiciones funcionales y administrativas utilizando técnicas sencillas para la identificación de puntos donde puedan aplicarse acciones de mejora.Una de estas técnicas es la evaluación del grado de madurez de la empresa, desarrollado por Du Pont (1990) y perfeccionado por McKinsey (1995) y Topkins (2000).En esta técnica se establecen varios pilares, cada uno con varios niveles, donde dos gestores posicionan, según su juicio, la condición en que se encuentra su empresa.
Propuesta Du Pont
En la propuesta original de Du Pont se establecen 3 pilares:
- Características de una organización de mantenimiento;
- Prácticas y métodos típicos usados por las organizaciones de mantenimiento;
- Medidas de desempeño que tipifican una organización.
Para cada pilar se propone evaluar 3 niveles:
- Personas y Organización (Estructura, Formación, Supervisión, Apoyo, Administración, Sindicato, Terceros);
- Sistemas (Planificación, Sistema de gestión, Capacitación);
- Filosofías (Materiales, Misión, Metas, Expectativas de desempeño, Proyectos esenciales).
La propuesta de Du Pont, a la que siguieron las de McKinsey y Topkins, es que los directivos evalúen el grado de madurez de la empresa en la que trabajan, asignando una calificación (del 1 al 10) para cada pilar según su punto de vista. Para cada uno, también se asigna una calificación del 1 al 10. Es decir, cada pilar tendría su número de evaluación multiplicado por los números de evaluación de cada nivel, lo que daría, para cada evaluador, un mínimo total de 3 puntos (producto de 1 por el pilar por 1 por cada nivel) hasta 300, obteniéndose este valor máximo sumando los valores de los productos de los pilares con los tres niveles respectivos.Dado que el evaluador estaría asignando sus puntos a los tres pilares, su valor máximo general para la empresa sería de 900 puntos.
Por ejemplo: Si un evaluador asignara al pilar 1 una calificación de 8 y para los tres niveles de este pilar los valores de 9, 6 y 9, tendríamos un resultado de 8x9 + 8x6 + 8x9 para este pilar, totalizando 192 puntos. El mismo criterio se aplicaría a los pilares 2 y 3, donde, por ejemplo, el evaluador obtuvo totales de 161 y 180. Por lo tanto, este evaluador estaría obteniendo un total de 533 puntos. Se observa que, en este caso, el evaluador obtuvo una puntuación cercana al 59% del valor máximo, lo que puede considerarse razonable. Tomando las medias de otros tres evaluadores, por ejemplo 580, 605 y 701 puntos, tendríamos una visión de la madurez de esta empresa, que resaltaría los aspectos que es necesario mejorar, dentro de los recursos disponibles (financieros, logísticos, operativos, técnicos, estratégicos, etc.).
Propuesta McKinsey
En la propuesta de McKinsey se establece 12 pilares:
- Características de una organización de mantenimiento.
- Definición y selección de estrategias de mantenimiento (predictivo, preventivo, correctivo).
- Planificación del mantenimiento preventivo.
- Aplicación del mantenimiento predictivo.
- Mantenimiento correctivo.
- Control de resultados.
- Cultura de desempeño.
- Definición de la estrategia de reparaciones con recursos propios vs. Terceros.
- Equipo técnico - Plan de desarrollo del equipo.
- Gestión del equipo de terceros.
- Gestión de suministros - Control de stock.
- Gestión de suministros - Disponibilidad de repuestos.
Para cada pilar se establecen 5 niveles de elección:
- Débil
- Abajo del promedio
- Satisfactorio
- Arriba del promedio
- Clase mundial
Pilar 01 - Evaluación y segmentación de posibles fallas
- Débil: No hay análisis cuantitativo de fallas históricas;
- Abajo del Promedio: Hay un análisis de frecuencia de fallas de forma consolidada para la planta, que subsidia las estrategias de mantenimiento;
- Satisfactorio: Hay un análisis detallado de las posibles fallas por equipo con estimativas de impacto de downtime y pérdida de producción;
- Arriba del Promedio: Además de detallado por máquina y componentes, el análisis considera el grado de previsibilidad y frecuencia de las fallas;
- Clase Mundial: Criterio anterior + los análisis detallados son revisados y realimentan la estrategia de mantenimiento de la planta.
Pilar 02 - Definición y selección de estrategias de mantenimiento (predictivo, preventivo, correctivo)
- Débil: No hay análisis económico para la definición de la estrategia de mantenimiento;
- Abajo del Promedio: Hay una estimativa simple de los costos de suministro de reposición y de mano de obra con cada una de las estrategias;
- Satisfactorio: Hay un análisis detallado del impacto de la posible estrategia de mantenimiento en la probabilidad y en la frecuencia de falla. También hay comprensión de TCO (Total Cost of Ownership) de cada estrategia;
- Arriba del Promedio: Criterio anterior + Hay un análisis detallado de costos del impacto de las posibles estrategias de mantenimiento, considerando frecuencias de fallas, costos hora/máquina, tiempo de corrección y utilización del equipo;
- Clase Mundial: Criterio anterior + Hay una total integración entre los análisis de las posibles estrategias de mantenimiento y las definiciones de CAPEX para la planta, con foco en creación de valor.
Pilar 03 - Planificación del mantenimiento preventivo
- Débil: El planeamiento no posee un estándar definido;
- Abajo del Promedio: El planeamiento incluye la descripción general del trabajo y los materiales;
- Satisfactorio: El planeamiento incluye la descripción general del trabajo, los materiales y el número de horas de técnicos involucrados;
- Arriba del Promedio: El planeamiento incluye la descripción general del trabajo, los materiales, el número de horas de técnicos y el horario para inicio y finalización;
- Clase Mundial: Criterio anterior + Acompañamiento de la curva de aprendizaje (reducción de tiempo y costo). Integración entre predictiva y correctiva con intercambio de datos históricos y análisis.
Pilar 04 - Aplicación del mantenimiento predictivo
- Débil: No hay mantenimiento predictivo;
- Abajo del Promedio: Hay mantenimiento predictivo, pero solo en situaciones visibles de problemas en el funcionamiento;
- Satisfactorio: Hay mantenimiento predictivo para las partes/equipos de fácil identificación y previsibilidad de problemas. Hay análisis estadísticos de fallas;
- Arriba del Promedio: Criterio anterior + Se utilizan herramientas sofisticadas para procesamiento de señales (térmicos, vibratorios, eléctricos, etc.) recolectadas periódicamente;
- Clase Mundial: Criterio anterior + Las señales se recolectan en tiempo real. Acompañamiento de la curva de aprendizaje (reducción de tiempo y costo). Integración entre predictivo y correctivo con intercambio de datos históricos y análisis.
Pilar 05 - Mantenimiento Correctivo
- Débil: La identificación del problema se hace de forma empírica después de la rotura, sin apoyo de la ingeniería. Los operadores no están involucrados en el proceso;
- Abajo del Promedio: Hay un previo estudio de las principales fallas posibles y el proceso de acción sobre esas fallas se mantiene informal. Los operadores no están involucrados en el proceso;
- Satisfactorio: Hay una previsión de las fallas de mayor impacto y probabilidad, y un plan de acción detallado para el abordaje. Los operadores son capaces de realizar pequeñas reparaciones;
- Arriba del Promedio: Criterio anterior + Alto grado de participación de la ingeniería de mantenimiento y de procesos en la identificación de los problemas y en el plan de acción. Los operadores son capaces de prever problemas mayores;
- Clase Mundial: Criterio anterior + Acompañamiento de la curva de aprendizaje (reducción de tiempos y costos). Integración entre predictivo y correctivo con intercambio de datos históricos y análisis.
Pilar 06 - Control de Resultados
- Débil: No hay control de costos ni de tiempo;
- Abajo del Promedio: Hay controles rudimentarios de los principales centros de costos y del tiempo total de parada para actividades de mantenimiento;
- Satisfactorio: Hay controles para todos los costos de mantenimiento y el tiempo gastado en el desempeño de funciones de mantenimiento;
- Arriba del Promedio: Hay controles para todos los costos de mantenimiento, incluidos los costos de pérdida de ingresos y el tiempo gastado en las funciones. Estos controles son utilizados para benchmarking interno;
- Clase Mundial: Los controles son utilizados para imponer metas de mejora continua de tiempo y costo en todos los procesos.
Pilar 07 - Cultura de Desempeño
- Débil: No hay metas de desempeño específicas. Los equipos interfuncionales (Operación y Mantenimiento) tienen poca o ninguna participación en la resolución de problemas;
- Abajo del Promedio: Hay metas, pero no son monitoreadas ni seguidas. Los equipos interfuncionales (mantenimiento y operación) se usan muy raramente;
- Satisfactorio: Hay metas y son monitoreadas, pero poco divulgadas. La responsabilidad por las metas es informal. Los equipos interfuncionales están institucionalizados, pero no logran resultados en la creación de mejores prácticas;
- Arriba del Promedio: Las metas son monitoreadas y divulgadas, pero no existe una cultura de desempeño. Los equipos interfuncionales tienen un alto impacto con ideas generadas por la alta gerencia;
- Clase Mundial: Las metas son monitoreadas, divulgadas y sirven de base para la remuneración variable. Los equipos interfuncionales aportan ideas de mejora a la alta gestión y generan un alto impacto en los cambios.
Pilar 08 - Definición de la estrategia de reparaciones con recursos propios vs. terceros
- Débil: Todos los reparos se hacen internamente, sin análisis crítico;
- Abajo del Promedio: Algunas reparaciones se hacen por terceros, pero no hay un proceso claro de decisión;
- Satisfactorio: Hay un proceso de decisión que toma en cuenta el impacto potencial de reducción de costo con materiales y mano de obra;
- Arriba del Promedio: Criterio anterior + Hay un proceso de decisión que considera el nivel de servicio (grado de habilidad de los terceros vs. el equipo interno) y posibles sinergias o beneficios estratégicos de no tercerizar;
- Clase Mundial: Criterio anterior + Las decisiones de tercerización o no de funciones de mantenimiento son revisadas periódicamente para todos los equipos.
Pilar 09 - Equipo técnico - Plan de desarrollo del equipo
- Débil: No hay un plan de desarrollo definido;
- Abajo del Promedio: Hay un plan de desarrollo, pero las atribuciones y calificaciones en cada nivel no son claras;
- Satisfactorio: Hay una visión clara de las calificaciones necesarias por función en cada nivel, sin embargo, el sistema de evaluación de desempeño y retroalimentación es informal y de bajo impacto;
- Arriba del Promedio: Criterio anterior + Hay gran armonía entre los sistemas de evaluación de desempeño/retroalimentación y el plan de desarrollo/funciones;
- Clase Mundial: Criterio anterior + Los atributos y calificaciones necesarios son constantemente reevaluados según cambios tecnológicos o estratégicos.
Pilar 10 - Gestión del equipo de terceros
- Débil: No hay tercerización de funciones de mantenimiento;
- Abajo del Promedio: No hay monitoreo ni evaluación del prestador de servicios;
- Satisfactorio: El prestador de servicios es evaluado de manera informal o en grandes tareas;
- Arriba del Promedio: La mayor parte de los trabajos son acompañados. El prestador de servicios es evaluado según calidad, cumplimiento de plazos y tareas propuestas;
- Clase Mundial: Todos los trabajos son evaluados (o por lo menos de forma estadística). El pago de los servicios está directamente ligado al desempeño, plazos y desarrollo de las tareas. Hay un esfuerzo de mejora continua junto a los proveedores.
Pilar 11 - Gestión de Suministros - Control de Stock
- Débil: No hay control formal de ítems de mantenimiento. Hay muchas piezas para equipos ya desactivados. No existen intenciones de desarrollo de contratos de suministro;
- Abajo del Promedio: El control de ítems está constantemente desactualizado. Niveles mínimos y máximos de stock no son definidos. Se desarrollan contratos de suministro sin un plan preestablecido;
- Satisfactorio: Control de stock actualizado para algunos ítems. Niveles mínimos y máximos establecidos para algunos ítems. Existe un plan de desarrollo de contratos de suministro;
- Arriba del Promedio: Control de ítems actualizado para la mayoría de los ítems. Niveles mínimos y máximos establecidos para la mayoría de los ítems. Ítem anterior + 50% de los ítems de stock evaluados con base en el riesgo/frecuencia;
- Clase Mundial: Control de ítems actualizado para todos los ítems. Niveles mínimos y máximos establecidos para todos los ítems. Ítem anterior + 100% de los ítems de stock evaluados con base en el riesgo/frecuencia.
Pilar 12 - Gestión de Suministros - Disponibilidad de repuestos
- Débil: No hay una metodología para la ubicación de las piezas. Menos del 30% de las piezas están disponibles en una primera tentativa. No existe acondicionamiento adecuado. Menos del 30% de las piezas son inspeccionadas o tienen calidad asegurada;
- Abajo del Promedio: Hay diversas metodologías no integradas de búsqueda de piezas. El 30-50% de las piezas están disponibles en la primera búsqueda. Acondicionadas de forma adecuada. El 30-50% de las piezas son inspeccionadas o tienen calidad asegurada;
- Satisfactorio: Hay una metodología única de búsqueda de piezas, pero es poco amigable y de poca confianza. El 50-75% de las piezas están disponibles en la primera búsqueda. Acondicionadas de forma adecuada. El 50-75% de las piezas son inspeccionadas o tienen calidad asegurada;
- Arriba del Promedio: La metodología de búsqueda de piezas tiene un alto grado de confianza, pero es difícil de utilizar. El 75-90% de las piezas están disponibles en la primera búsqueda. Acondicionadas de forma adecuada y 50-75% de los casos entregados en el área. El 75-90% de las piezas son inspeccionadas o tienen calidad asegurada;
- Clase Mundial: La herramienta de búsqueda es fácil de usar y muy confiable. El 95-100% de las piezas están disponibles en la primera búsqueda. Acondicionadas de forma adecuada y más del 75% entregadas en el área. El 100% de las piezas tienen calidad asegurada.
A continuación, el promedio de la aplicación del método en más de 50 empresas:

Propuesta de Topkins
En la propuesta de Topkins se encuentran 7 pilares:
- Actitud de la gestión corporativa de la planta
- Estado organizacional del mantenimiento
- Porcentaje de pérdida de recursos debido al mantenimiento
- Solución de problemas de mantenimiento
- Calificación/entrenamiento del personal de mantenimiento
- Información de mantenimiento y desarrollo de acciones
- Resumen de la posición del mantenimiento en la compañía
Pilar 1 - Actitud de la gestión corporativa de la planta
- Inconsciente: No comprende lo que es mantenimiento preventivo, se repara solo cuando se rompe.
- Despertando: Reconoce que el mantenimiento puede ser mejorado, pero se siente incapaz de implementar cambios.
- Desarrollando: Aprende sobre ROI (retorno de inversión), desarrolla mayor interés y seguridad en mejorar el mantenimiento.
- Capacitado: Actitud participativa, reconoce que la gestión de mantenimiento es esencial y debe ser mandataria.
- Consciente: Integra el mantenimiento como una parte fundamental del sistema global de la compañía.
Pilar 2 - Estado organizacional del mantenimiento
- Inconsciente: Reactivo, trabaja en el equipo solo cuando falla; baja productividad del personal.
- Despertando: Aún reactivo, pero logra mejores recuperaciones de componentes y tiene repuestos disponibles cuando ocurre una falla.
- Desarrollando: Preventivo, realiza rutinas de inspección, lubricación, ajustes y pequeños servicios para mejorar el MTBF (tiempo medio entre fallas).
- Capacitado: Predictivo, utiliza técnicas como análisis de vibración, termografía, ultrasonido, etc., para monitorear la condición de los equipos y anticipar problemas.
- Consciente: Productivo, combina técnicas predictivas con la participación activa de los operadores para liberar a los técnicos de mantenimiento, mejorando la mantenibilidad.
Pilar 3 - Porcentual pérdida de recursos debido al mantenimiento
- Inconsciente: Más del 30%.
- Despertando: Entre 20% y 30%.
- Desarrollando: Entre 10% y 20%.
- Capacitado: Entre 5% y 10%.
- Consciente: Menos del 5%.
Pilar 4 - Solución de problemas de mantenimiento
- Inconsciente: Los problemas se desarrollan hasta que son descubiertos.
- Despertando: Se elaboran algunas acciones básicas. Comienza el análisis de fallas de manera elemental.
- Desarrollando: Los problemas se resuelven mediante la implementación de acciones de mantenimiento e ingeniería.
- Capacitado: Los problemas son anticipados. Se utiliza un fuerte equipo interdisciplinario de solución de problemas.
- Consciente: Los problemas son prevenidos.
Pilar 5 - Calificación/entrenamiento del personal de mantenimiento
- Inconsciente: Baja calidad de mano de obra, supervisión rígida, conocimientos obsoletos, pagos por antigüedad.
- Despertando: El personal siente que falta conocimiento para analizar fallas y comienza a cuestionar la especialización. Se reconoce la necesidad de capacitación.
- Desarrollando: Calidad en el trabajo. Se distribuye el desempeño de tareas, inversión en investigación, pagos por capacidad para resolver problemas.
- Capacitado: Expectativa de calidad en el trabajo. Realización de tareas por "multiespecialistas", conocimiento actualizado.
- Consciente: Orgullo y profesionalismo. Flexibilidad en la designación de tareas. Capacitación constante de los operadores por los mantenedores. Pago basado en la productividad de la planta.
Pilar 6 - Información de mantenimiento y desarrollo de acciones
- Inconsciente: El mantenimiento intenta realizar registros, pero la disciplina no es exigida y los datos son deficientes.
- Despertando: Se utiliza una orden de trabajo manual o computarizada, pero la planificación y programación son escasas o nulas.
- Desarrollando: Se utiliza una orden de trabajo manual o computarizada por mantenimiento, operación e ingeniería, con planificación e implementación de programación de servicios.
- Capacitado: Se utiliza un sistema de control de mantenimiento para todas las áreas de la compañía, con información disponible y consistente.
- Consciente: El sistema de información de mantenimiento está integrado con el sistema de información corporativo.
Pilar 7 - Resumen de la posición del mantenimiento en la compañía
- Inconsciente: “No sabemos cuál equipo se va a romper y por eso pagamos al mantenimiento. Las tasas de pérdidas son altas, pero no es un problema de mantenimiento.”
- Despertando: “¿Acaso nuestros competidores tienen estos problemas con sus equipos? ¡Las refacciones nos están costando mucho!”
- Desarrollando: “Con el nuevo criterio de gestión, empezamos a identificar y resolver los problemas.”
- Capacitado: “Todos reconocen que el mantenimiento es parte de nuestra rutina de calidad operacional. No podemos hacer productos de calidad con un mantenimiento deficiente.”
- Consciente: “No esperamos fallas y es una sorpresa cuando ocurren. ¡El mantenimiento contribuye para mantenernos entre los mejores!”
A continuación, se presenta el promedio de la aplicación del método en más de 100 empresas:

Conclusión
Lo importante de las Técnicas McKinsey y Topkins es que detallan la información de cada nivel en cada pilar.
Dado que estos métodos se aplican a directivos de los niveles operativo, ejecutivo y estratégico, esta información facilita la comprensión de sus posiciones, según el punto de vista de cada uno, sobre la situación de la empresa.
Al final de la evaluación de los directivos, se obtiene un valor promedio que es analizado por un grupo designado por la empresa para valorar la posibilidad de mejorar los niveles obtenidos.
Dinos qué te ha parecido el artículo

Mundo ACR Predictiva21 - Un nuevo Año, una Nueva Etapa
Columna
Un nuevo año, una nueva etapa
Quiero comenzar esta columna felicitando a Predictiva 21 por haber alcanzado 50 ediciones, un logro magnífico y un hito importante en el mundo del mantenimiento y la confiabilidad. A sus editores, mis más sinceras felicitaciones por su esfuerzo y constancia, algo no tan común en estos tiempos de velocidad y vértigo. A los lectores, gracias por hacer de esta publicación un medio referente en la comunicación y transmisión del conocimiento. Y a quienes participan activamente con sus artículos, comentarios, capacitaciones y demás aportes a la especialidad: ¡Felicitaciones y gracias a todos!
Entramos en un año emblemático que marca el cumplimiento del primer cuarto de este siglo XXI. Atrás quedó el año 2000 con sus temores de colapso y las posibles amenazas místicas que, finalmente, no se materializaron. Desde entonces, muchas cosas han ocurrido, y, sin lugar a dudas, muchas más pasarán, marcando una nueva etapa. Nuevos desafíos nos esperan, así como nuevos conocimientos, tareas, proyectos y mucho más.
En este contexto quiero analizar algunos aspectos relacionados con el ACR, así como otros planes que llevaré adelante este año con el apoyo de mi equipo, a quienes no puedo dejar de mencionar por su constante trabajo y colaboración en la difusión del conocimiento en esta área.
La resolución de problemas complejos (CPS)
Todo comenzó con una proyección del World Economic Forum (WEF) realizada hace algunos años, en la que se mencionaba que la resolución de problemas complejos (CPS, por sus siglas en inglés) sería una de las habilidades clave del futuro. Desde entonces, se ha hablado con mayor intensidad sobre el tema, transformando la visión acerca de la necesidad de resolver problemas de manera efectiva dentro de las organizaciones. Resolver problemas se ha convertido en una prioridad, y esta creciente demanda ha impulsado la creación de cursos y seminarios especializados, además de abrir espacios en congresos donde estos temas y la participación de especialistas han ganado gran relevancia.
Más recientemente, el WEF llevó a cabo otra investigación que posicionó al CPS algunos escalones por debajo en la lista de prioridades. Sin embargo, este cambio dio lugar a un enfoque en habilidades complementarias, como el pensamiento crítico, la innovación y la creatividad aplicada a la resolución de problemas. Esto permitió que el CPS evolucionara hacia un programa más amplio, integrado por estas y otras competencias esenciales en los procesos de capacitación y entrenamiento.
Asimismo, el WEF destacó la importancia del reskilling y el upskilling en las organizaciones, proponiendo un reentrenamiento de al menos el 50 % de los empleados en los próximos dos años. Esta proyección ya es una realidad visible en nuestro día a día, impulsada por los vertiginosos cambios que enfrentamos.
La complejidad y el ACR
Siguiendo el tema del CPS y para complementar el concepto, es importante reconocer que los problemas evolucionan de lo simple a lo complicado y de ahí a lo complejo, según el modelo Cynefin de Dave Snowden.
En el caso de los problemas simples, se aplican prácticas conocidas que se basan en relaciones causa-efecto evidentes y lineales. Sin embargo, con la introducción de la inteligencia artificial (IA), estas prácticas serán más fáciles de aplicar, permitiendo un análisis más claro y rápido.
Por otro lado, los problemas complicados requieren un análisis más profundo, con el apoyo de especialistas y recursos más sólidos. Este tipo de problemas, que aumentarán en frecuencia debido al avance tecnológico, demandará habilidades de investigación avanzadas. Además, será necesario establecer departamentos dedicados exclusivamente a la resolución de problemas, integrados por especialistas capaces de enfrentar estos desafíos.
Finalmente, los problemas complejos requieren un enfoque y un análisis completamente diferentes. En este caso, la linealidad y la relación causa-efecto están presentes solo de forma parcial, lo que impide dividirlos en partes manejables. Estos problemas exigen un abordaje integral y el uso de una “caja de herramientas” diversa, en lugar de depender de una única solución. Por ello, los investigadores con un perfil generalista serán más efectivos que los especialistas al abordar estos retos.
Esta situación representa una evolución del enfoque tradicional del ACR, que históricamente se ha centrado en problemas simples y complicados. Pero, ¿qué sucedería si llevamos el ACR hacia el CPS? ¿Existirá una forma de adaptarlo a este nuevo marco? ¿Las prácticas y el marco de trabajo seguirán siendo los mismos?
Este es un desafío para el futuro que propongo. Mi curiosidad, experiencia y nuevos proyectos me están llevando a enfocarme en esta apasionante y prometedora dirección.
La Inteligencia Artificial
La nueva propuesta para la resolución de problemas se enfoca en la necesidad de personas con perfiles diversos y, dentro del ámbito del ACR, será fundamental el conocimiento necesario para gestionar problemas más allá de la simple aplicación de las prácticas tradicionales. Si bien muchas de estas prácticas continuarán siendo utilizadas, surgirán otras más adecuadas para la investigación, donde la Inteligencia Artificial (IA) desempeñará un papel cada vez más relevante.
La irrupción de la IA, especialmente en el último año, junto con la proliferación de nuevas aplicaciones basadas en esta tecnología, ha transformado el enfoque en la implementación de prácticas de ACR. Ahora, el conocimiento técnico aplicado está evolucionando hacia un énfasis mayor en el análisis y la gestión. Esto ocurre porque la IA puede realizar de manera autónoma una parte de las tareas que anteriormente ejecutaba una persona. En consecuencia, las personas deberán adoptar un perfil más analítico para garantizar que la práctica sea efectivamente aplicada y cumpla con los resultados esperados; de lo contrario, la implementación perderá efectividad.
Prácticas tradicionales de ACR, algunas de ellas en uso desde mediados del siglo pasado, seguirán vigentes, aunque no de la misma manera que conocemos hoy. La incorporación de herramientas basadas en IA no solo cambiará su aplicación, sino que también las hará más eficientes. Sin embargo, estas herramientas serán particularmente útiles en la resolución de problemas simples, mientras que los problemas más complejos exigirán nuevas prácticas y habilidades avanzadas. La tecnología, al igual que las máquinas y equipos utilizados, continuará evolucionando, aumentando la complejidad de los problemas asociados a ellos. Por lo tanto, la capacitación será crucial para adaptarse a este nuevo escenario, respaldando las proyecciones del WEF.
El ACR como modelo de sistema de gestión
Retrocediendo en el tiempo, y más específicamente al período posterior a la Segunda Guerra Mundial en Japón, encontramos el origen de muchas prácticas de resolución de problemas y mejora continua. Estas metodologías surgieron con el propósito de impulsar el crecimiento y la mejora de las organizaciones mediante la resolución constante de problemas, en un contexto donde los sistemas de gestión no existían tal como los conocemos hoy. En aquella época, mejorar la gestión significaba esencialmente saber resolver problemas.
Con el paso del tiempo, se han incorporado más prácticas de mejora y resolución de problemas, lo que ha permitido optimizar la gestión de manera más eficaz.
Hoy en día, existen prácticas sólidas y ampliamente aceptadas. Entonces, ¿por qué no establecer un sistema de mejora continua basado en la resolución de problemas? El ACR, entendido de esta forma, podría utilizarse inicialmente, e incluso de manera continua, como un modelo de sistema de gestión. Por ejemplo, si una organización desea iniciar un proyecto para mejorar su gestión de calidad, podría comenzar implementando un programa integral de ACR. Este programa abarcaría no solo las prácticas a utilizar, sino también la capacitación de facilitadores de ACR, la definición de indicadores de gestión relacionados, el uso de software especializado, auditorías, y otros elementos clave.
En resumen, un programa de ACR podría servir como un modelo de gestión hacia la mejora continua, similar a lo que hizo Japón en su momento. Este enfoque no solo sería un excelente punto de partida, sino que podría evolucionar y mantenerse, facilitando la transición hacia otros sistemas de gestión más avanzados como los que conocemos hoy en día.
Las habilidades blandas
Como he mencionado anteriormente, el World Economic Forum (WEF) identificó las habilidades del futuro a través de una investigación basada en encuestas realizadas a organizaciones de todo el mundo. De este análisis surgen dos conclusiones importantes. En primer lugar, el perfil de las personas dentro de las organizaciones cambiará significativamente debido a la intervención de la inteligencia artificial (IA), que reemplazará a los trabajadores en tareas rutinarias. En segundo lugar, los modelos de trabajo del futuro serán diferentes a los actuales, una realidad que ya estamos empezando a experimentar.
En el ámbito de la gestión del Análisis Causa Raíz (ACR), serán esenciales nuevas habilidades complementarias para llevar a cabo investigaciones y resolver problemas de manera efectiva. Un Facilitador de ACR deberá poseer competencias clave, como la capacidad de liderar personas y equipos, gestionar situaciones complejas derivadas de problemas críticos (accidentes, incidentes o pérdidas materiales, por ejemplo), y mantener la objetividad mediante el pensamiento crítico. Otras habilidades imprescindibles incluyen la creatividad para encontrar soluciones, el manejo de datos para potenciar los análisis, y el pensamiento sistémico, analítico, creativo e innovador.
Así, el Facilitador de ACR del futuro será muy distinto al de épocas anteriores. Ya no bastará con conocer una práctica específica para destacar dentro de una organización. Hoy en día, el acceso al conocimiento es más democrático, y con una capacitación básica se puede adquirir un buen perfil para abordar problemas simples. Sin embargo, el entorno actual y futuro requiere un enfoque más integral y habilidades más avanzadas.
Las nuevas tendencias en la formación
Otro aspecto que está en constante transformación es la capacitación y el entrenamiento de las personas. No son lo mismo que hace algunos años, especialmente tras el impacto de la reciente pandemia, que aceleró la adopción de modalidades virtuales. Aunque estas ya venían ganando terreno, la crisis sanitaria global forzó una rápida evolución en este ámbito.
Además, la forma en que se imparten los entrenamientos también ha cambiado. Ahora se busca mayor efectividad en el corto plazo, dado que el avance vertiginoso de la tecnología hace que las capacitaciones extensas puedan quedar obsoletas rápidamente. Por este motivo, muchas carreras profesionales están siendo revisadas para adaptarse a esta nueva realidad.
Otra de las dificultades que enfrentan las organizaciones es la rotación de personal. Invertir en entrenar a personas que luego dejan la organización es un desafío recurrente. Por ello, será crucial priorizar la capacitación de aquellos colaboradores con mayor previsión de permanencia o cuyo plan de carrera esté alineado con los objetivos de la organización.
En el contexto del ACR, esta realidad también aplica. Será necesario formar especialistas dentro de las organizaciones, enfocándose no solo en generalistas que conozcan un poco de cada cosa, sino también en la creación de departamentos exclusivos de resolución de problemas. Estas unidades serán esenciales en aquellas organizaciones cuyo tamaño y nivel de actividades relacionadas con el ACR lo justifiquen.
Con estas adaptaciones, el ACR no solo se mantendrá como una herramienta eficaz, sino que también evolucionará para responder a las necesidades cambiantes de un mundo en constante transformación.
¿Qué haremos en el 2025?
Este nuevo año nos trae grandes desafíos, y estamos preparados para afrontarlos con entusiasmo. Estas son algunas de las actividades que seguiremos desarrollando o que iniciaremos:
7mo. Encuentro entre Pares
Este evento se llevará a cabo el próximo 5 de junio, y en esta edición será aún más amplio, adoptando una modalidad híbrida. Contaremos con la participación de especialistas en vivo y una transmisión en línea para toda Latinoamérica.
Comunidad ACR
Lo invitamos a unirse a nuestro grupo de WhatsApp, un espacio dedicado a compartir información, conocimientos y experiencias relacionadas con el ACR.
Página web www.analisisdecausaraiz.com
Continuaremos publicando notas, artículos, novedades y recursos útiles para todos los interesados en el Análisis de Causa Raíz.
Podcast "Mundo ACR"
Lanzaremos una nueva temporada, renovada y con propuestas frescas, para seguir explorando temas de interés en el ámbito del ACR.
Canal de YouTube "Análisis Causa Raíz ACR"
Seguiremos produciendo y compartiendo videos de diversas actividades, contribuyendo al conocimiento y la difusión del ACR.
LinkedIn: Grupo "Análisis de Causa Raíz ACR"
Este grupo será un punto de encuentro para compartir información, casos prácticos, notas y otras actividades relacionadas con el ACR.
Cursos y seminarios
Como novedad, introduciremos cursos y seminarios en modalidades autogestionables, adaptados a las necesidades de las organizaciones interesadas en capacitar a sus equipo
Dinos qué te ha parecido el artículo
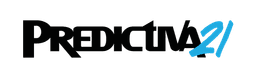

Un nuevo año, una nueva etapa
Quiero comenzar esta columna felicitando a Predictiva 21 por haber alcanzado 50 ediciones, un logro magnífico y un hito importante en el mundo del mantenimiento y la confiabilidad. A sus editores, mis más sinceras felicitaciones por su esfuerzo y constancia, algo no tan común en estos tiempos de velocidad y vértigo. A los lectores, gracias por hacer de esta publicación un medio referente en la comunicación y transmisión del conocimiento. Y a quienes participan activamente con sus artículos, comentarios, capacitaciones y demás aportes a la especialidad: ¡Felicitaciones y gracias a todos!
Entramos en un año emblemático que marca el cumplimiento del primer cuarto de este siglo XXI. Atrás quedó el año 2000 con sus temores de colapso y las posibles amenazas místicas que, finalmente, no se materializaron. Desde entonces, muchas cosas han ocurrido, y, sin lugar a dudas, muchas más pasarán, marcando una nueva etapa. Nuevos desafíos nos esperan, así como nuevos conocimientos, tareas, proyectos y mucho más.
En este contexto quiero analizar algunos aspectos relacionados con el ACR, así como otros planes que llevaré adelante este año con el apoyo de mi equipo, a quienes no puedo dejar de mencionar por su constante trabajo y colaboración en la difusión del conocimiento en esta área.
La resolución de problemas complejos (CPS)
Todo comenzó con una proyección del World Economic Forum (WEF) realizada hace algunos años, en la que se mencionaba que la resolución de problemas complejos (CPS, por sus siglas en inglés) sería una de las habilidades clave del futuro. Desde entonces, se ha hablado con mayor intensidad sobre el tema, transformando la visión acerca de la necesidad de resolver problemas de manera efectiva dentro de las organizaciones. Resolver problemas se ha convertido en una prioridad, y esta creciente demanda ha impulsado la creación de cursos y seminarios especializados, además de abrir espacios en congresos donde estos temas y la participación de especialistas han ganado gran relevancia.
Más recientemente, el WEF llevó a cabo otra investigación que posicionó al CPS algunos escalones por debajo en la lista de prioridades. Sin embargo, este cambio dio lugar a un enfoque en habilidades complementarias, como el pensamiento crítico, la innovación y la creatividad aplicada a la resolución de problemas. Esto permitió que el CPS evolucionara hacia un programa más amplio, integrado por estas y otras competencias esenciales en los procesos de capacitación y entrenamiento.
Asimismo, el WEF destacó la importancia del reskilling y el upskilling en las organizaciones, proponiendo un reentrenamiento de al menos el 50 % de los empleados en los próximos dos años. Esta proyección ya es una realidad visible en nuestro día a día, impulsada por los vertiginosos cambios que enfrentamos.
La complejidad y el ACR
Siguiendo el tema del CPS y para complementar el concepto, es importante reconocer que los problemas evolucionan de lo simple a lo complicado y de ahí a lo complejo, según el modelo Cynefin de Dave Snowden.
En el caso de los problemas simples, se aplican prácticas conocidas que se basan en relaciones causa-efecto evidentes y lineales. Sin embargo, con la introducción de la inteligencia artificial (IA), estas prácticas serán más fáciles de aplicar, permitiendo un análisis más claro y rápido.
Por otro lado, los problemas complicados requieren un análisis más profundo, con el apoyo de especialistas y recursos más sólidos. Este tipo de problemas, que aumentarán en frecuencia debido al avance tecnológico, demandará habilidades de investigación avanzadas. Además, será necesario establecer departamentos dedicados exclusivamente a la resolución de problemas, integrados por especialistas capaces de enfrentar estos desafíos.
Finalmente, los problemas complejos requieren un enfoque y un análisis completamente diferentes. En este caso, la linealidad y la relación causa-efecto están presentes solo de forma parcial, lo que impide dividirlos en partes manejables. Estos problemas exigen un abordaje integral y el uso de una “caja de herramientas” diversa, en lugar de depender de una única solución. Por ello, los investigadores con un perfil generalista serán más efectivos que los especialistas al abordar estos retos.
Esta situación representa una evolución del enfoque tradicional del ACR, que históricamente se ha centrado en problemas simples y complicados. Pero, ¿qué sucedería si llevamos el ACR hacia el CPS? ¿Existirá una forma de adaptarlo a este nuevo marco? ¿Las prácticas y el marco de trabajo seguirán siendo los mismos?
Este es un desafío para el futuro que propongo. Mi curiosidad, experiencia y nuevos proyectos me están llevando a enfocarme en esta apasionante y prometedora dirección.
La Inteligencia Artificial
La nueva propuesta para la resolución de problemas se enfoca en la necesidad de personas con perfiles diversos y, dentro del ámbito del ACR, será fundamental el conocimiento necesario para gestionar problemas más allá de la simple aplicación de las prácticas tradicionales. Si bien muchas de estas prácticas continuarán siendo utilizadas, surgirán otras más adecuadas para la investigación, donde la Inteligencia Artificial (IA) desempeñará un papel cada vez más relevante.
La irrupción de la IA, especialmente en el último año, junto con la proliferación de nuevas aplicaciones basadas en esta tecnología, ha transformado el enfoque en la implementación de prácticas de ACR. Ahora, el conocimiento técnico aplicado está evolucionando hacia un énfasis mayor en el análisis y la gestión. Esto ocurre porque la IA puede realizar de manera autónoma una parte de las tareas que anteriormente ejecutaba una persona. En consecuencia, las personas deberán adoptar un perfil más analítico para garantizar que la práctica sea efectivamente aplicada y cumpla con los resultados esperados; de lo contrario, la implementación perderá efectividad.
Prácticas tradicionales de ACR, algunas de ellas en uso desde mediados del siglo pasado, seguirán vigentes, aunque no de la misma manera que conocemos hoy. La incorporación de herramientas basadas en IA no solo cambiará su aplicación, sino que también las hará más eficientes. Sin embargo, estas herramientas serán particularmente útiles en la resolución de problemas simples, mientras que los problemas más complejos exigirán nuevas prácticas y habilidades avanzadas. La tecnología, al igual que las máquinas y equipos utilizados, continuará evolucionando, aumentando la complejidad de los problemas asociados a ellos. Por lo tanto, la capacitación será crucial para adaptarse a este nuevo escenario, respaldando las proyecciones del WEF.
El ACR como modelo de sistema de gestión
Retrocediendo en el tiempo, y más específicamente al período posterior a la Segunda Guerra Mundial en Japón, encontramos el origen de muchas prácticas de resolución de problemas y mejora continua. Estas metodologías surgieron con el propósito de impulsar el crecimiento y la mejora de las organizaciones mediante la resolución constante de problemas, en un contexto donde los sistemas de gestión no existían tal como los conocemos hoy. En aquella época, mejorar la gestión significaba esencialmente saber resolver problemas.
Con el paso del tiempo, se han incorporado más prácticas de mejora y resolución de problemas, lo que ha permitido optimizar la gestión de manera más eficaz.
Hoy en día, existen prácticas sólidas y ampliamente aceptadas. Entonces, ¿por qué no establecer un sistema de mejora continua basado en la resolución de problemas? El ACR, entendido de esta forma, podría utilizarse inicialmente, e incluso de manera continua, como un modelo de sistema de gestión. Por ejemplo, si una organización desea iniciar un proyecto para mejorar su gestión de calidad, podría comenzar implementando un programa integral de ACR. Este programa abarcaría no solo las prácticas a utilizar, sino también la capacitación de facilitadores de ACR, la definición de indicadores de gestión relacionados, el uso de software especializado, auditorías, y otros elementos clave.
En resumen, un programa de ACR podría servir como un modelo de gestión hacia la mejora continua, similar a lo que hizo Japón en su momento. Este enfoque no solo sería un excelente punto de partida, sino que podría evolucionar y mantenerse, facilitando la transición hacia otros sistemas de gestión más avanzados como los que conocemos hoy en día.
Las habilidades blandas
Como he mencionado anteriormente, el World Economic Forum (WEF) identificó las habilidades del futuro a través de una investigación basada en encuestas realizadas a organizaciones de todo el mundo. De este análisis surgen dos conclusiones importantes. En primer lugar, el perfil de las personas dentro de las organizaciones cambiará significativamente debido a la intervención de la inteligencia artificial (IA), que reemplazará a los trabajadores en tareas rutinarias. En segundo lugar, los modelos de trabajo del futuro serán diferentes a los actuales, una realidad que ya estamos empezando a experimentar.
En el ámbito de la gestión del Análisis Causa Raíz (ACR), serán esenciales nuevas habilidades complementarias para llevar a cabo investigaciones y resolver problemas de manera efectiva. Un Facilitador de ACR deberá poseer competencias clave, como la capacidad de liderar personas y equipos, gestionar situaciones complejas derivadas de problemas críticos (accidentes, incidentes o pérdidas materiales, por ejemplo), y mantener la objetividad mediante el pensamiento crítico. Otras habilidades imprescindibles incluyen la creatividad para encontrar soluciones, el manejo de datos para potenciar los análisis, y el pensamiento sistémico, analítico, creativo e innovador.
Así, el Facilitador de ACR del futuro será muy distinto al de épocas anteriores. Ya no bastará con conocer una práctica específica para destacar dentro de una organización. Hoy en día, el acceso al conocimiento es más democrático, y con una capacitación básica se puede adquirir un buen perfil para abordar problemas simples. Sin embargo, el entorno actual y futuro requiere un enfoque más integral y habilidades más avanzadas.
Las nuevas tendencias en la formación
Otro aspecto que está en constante transformación es la capacitación y el entrenamiento de las personas. No son lo mismo que hace algunos años, especialmente tras el impacto de la reciente pandemia, que aceleró la adopción de modalidades virtuales. Aunque estas ya venían ganando terreno, la crisis sanitaria global forzó una rápida evolución en este ámbito.
Además, la forma en que se imparten los entrenamientos también ha cambiado. Ahora se busca mayor efectividad en el corto plazo, dado que el avance vertiginoso de la tecnología hace que las capacitaciones extensas puedan quedar obsoletas rápidamente. Por este motivo, muchas carreras profesionales están siendo revisadas para adaptarse a esta nueva realidad.
Otra de las dificultades que enfrentan las organizaciones es la rotación de personal. Invertir en entrenar a personas que luego dejan la organización es un desafío recurrente. Por ello, será crucial priorizar la capacitación de aquellos colaboradores con mayor previsión de permanencia o cuyo plan de carrera esté alineado con los objetivos de la organización.
En el contexto del ACR, esta realidad también aplica. Será necesario formar especialistas dentro de las organizaciones, enfocándose no solo en generalistas que conozcan un poco de cada cosa, sino también en la creación de departamentos exclusivos de resolución de problemas. Estas unidades serán esenciales en aquellas organizaciones cuyo tamaño y nivel de actividades relacionadas con el ACR lo justifiquen.
Con estas adaptaciones, el ACR no solo se mantendrá como una herramienta eficaz, sino que también evolucionará para responder a las necesidades cambiantes de un mundo en constante transformación.
¿Qué haremos en el 2025?
Este nuevo año nos trae grandes desafíos, y estamos preparados para afrontarlos con entusiasmo. Estas son algunas de las actividades que seguiremos desarrollando o que iniciaremos:
7mo. Encuentro entre Pares
Este evento se llevará a cabo el próximo 5 de junio, y en esta edición será aún más amplio, adoptando una modalidad híbrida. Contaremos con la participación de especialistas en vivo y una transmisión en línea para toda Latinoamérica.
Comunidad ACR
Lo invitamos a unirse a nuestro grupo de WhatsApp, un espacio dedicado a compartir información, conocimientos y experiencias relacionadas con el ACR.
Página web www.analisisdecausaraiz.com
Continuaremos publicando notas, artículos, novedades y recursos útiles para todos los interesados en el Análisis de Causa Raíz.
Podcast "Mundo ACR"
Lanzaremos una nueva temporada, renovada y con propuestas frescas, para seguir explorando temas de interés en el ámbito del ACR.
Canal de YouTube "Análisis Causa Raíz ACR"
Seguiremos produciendo y compartiendo videos de diversas actividades, contribuyendo al conocimiento y la difusión del ACR.
LinkedIn: Grupo "Análisis de Causa Raíz ACR"
Este grupo será un punto de encuentro para compartir información, casos prácticos, notas y otras actividades relacionadas con el ACR.
Cursos y seminarios
Como novedad, introduciremos cursos y seminarios en modalidades autogestionables, adaptados a las necesidades de las organizaciones interesadas en capacitar a sus equipo
Dinos qué te ha parecido el artículo

Excentricidad Dinámica Motores Eléctricos de Inducción
Artículo
Durante muchos años, se han utilizado los motores de inducción en la industria debido a su menor costo de adquisición y mantenimiento en comparación con otros tipos de motores.
Algunas de sus características más importantes, además de su construcción, están relacionadas con su principio de funcionamiento. El campo magnético giratorio inducirá una fuerza electromotriz (a la que se denominará f.e.m.), que el rotor intenta seguir pero nunca alcanza. Por ejemplo, un motor diseñado con 2 polos tiene una velocidad producida por la f.e.m. de 3600 RPM, mientras que el rotor, en su intento de igualarla, alcanza 3505 RPM. A esta diferencia de velocidad se le llama resbalamiento.
En vibraciones mecánicas, el resbalamiento se traduce como la frecuencia de deslizamiento, que está dada por la ecuación: Fs=Ns−RPM
Donde:
- Fs = Frecuencia de deslizamiento.
- Ns = Velocidad síncrona (producida por la f.e.m.).
- RPM = Velocidad del rotor físicamente.
Para este caso: Fs= 3600 − 3505 = 95CPM
Una vez conocida la frecuencia de deslizamiento, podemos calcular la frecuencia de paso de polos, que está dada por la ecuación:Fp=P×Fs
Donde:
- Fp = Frecuencia de paso de polos.
- P = Número de polos.
- Fs = Frecuencia de deslizamiento.
Para este caso: Fp= 2 × 95CPM = 190CPM = 3.16Hz
Con este contexto y conociendo estas frecuencias, podemos asociarlas con una variedad de problemas eléctricos que pueden apreciarse desde el punto de vista mecánico a través de las vibraciones. Aunque esta no es la mejor manera de determinar problemas eléctricos, sí es una herramienta útil para detectar comportamientos anómalos. Asociando estas frecuencias a tendencias aplicadas en el mantenimiento predictivo (PdM), podemos realizar un seguimiento puntual en términos de frecuencia y amplitud.
Estas frecuencias se presentan en un espectro de vibración, incluyendo la presencia de la 2FL, que corresponde a 2 veces la frecuencia de suministro eléctrico o de línea. En México, esta frecuencia es de 60 Hz, por lo que la 2FL sería:2×60Hz=120Hz
En campo, se detecta un aumento de la amplitud de la vibración de un motor de inducción de dos polos. En este caso, se observan múltiplos de la frecuencia fundamental (1X, 2X, 3X, 4X...), indicando holgura rotativa. Esto apunta principalmente a un desajuste en las cajas del rodamiento del motor.
En la resolución del espectro de vibración, se observan "picos" de amplitud en banda ancha debido a frecuencias muy cercanas entre sí. Para estudiar estas frecuencias, es necesario configurar adecuadamente la resolución del espectro.

Se emplea el método de demodulación para buscar frecuencias altas o de tildeo que aporten al diagnóstico, enfocándose en detectar algún desajuste en el rodamiento o frecuencias de falla asociadas a los rodamientos. Durante el análisis, se identifican valores síncronos (no relacionados con los rodamientos) y una pronunciación marcada de la frecuencia 2FL.

Se configura la resolución del espectro. En este, se pueden apreciar los múltiplos de la frecuencia fundamental, como ya se había mencionado. Además, se observan bandas laterales en cada uno de ellos. Estas bandas laterales tienen una frecuencia de 3.16 Hz, lo cual está completamente ligado a la frecuencia de paso de polos calculada al principio del artículo.

La aparición de las bandas laterales a múltiplos de giro se presenta cuando existe una excentricidad en el rotor. Esto ocurre debido a un entrehierro variable de manera giratoria entre el rotor y el estátor, lo que induce una vibración pulsante. Las frecuencias que generan solo un par de bandas laterales suelen corresponder a modulaciones de amplitud.
En la medición de aceleración en el dominio del tiempo, la velocidad de rotación (58.41 Hz / T=0.017s) está siendo modulada en amplitud por la frecuencia de paso de polos (3.16 Hz / T=0.316s). Este efecto puede ser percibido durante inspecciones visuales, manifestándose como sonidos de motor "rugiendo" o "mufeando", como se le llama coloquialmente. Esto es causado por oscilaciones grandes y rápidas bajo carga.

La variación del entrehierro puede ser producida por muchos factores. Centrar la armadura para eliminar la distorsión del estátor puede ser una solución, pero en este caso, se sospecha la presencia de una holgura rotativa severa debido a los múltiplos de la velocidad fundamental, lo cual tiene su origen en un claro excesivo entre los cojinetes.
Un rotor excéntrico significa que el diámetro exterior del núcleo del rotor no es concéntrico con los muñones del rodamiento. Esto crea un punto mínimo de espacio de aire que gira con el rotor a la frecuencia de rotación. Asociado a este fenómeno, habrá una fuerza magnética desequilibrada actuando en el punto mínimo del entrehierro, ya que la fuerza en el entrehierro mínimo es mayor que la fuerza en el entrehierro máximo, como se ilustra en la figura. Esta fuerza neta de desequilibrio girará junto con el entrehierro mínimo a la frecuencia de rotación, causando vibración en dicha frecuencia.

En recomendación a las observaciones en campo y al análisis del espectro, se sugiere revisar y centrar la armadura del motor, eliminar la distorsión del estátor, inspeccionar el claro excesivo y corregir el desajuste de los rodamientos, o cualquier otra condición que pueda causar que el rotor esté excéntrico con respecto al estátor.
Bibliografía - Excentricidad dinámica en motores de inducción
Artículo técnico
Análisis de vibraciones en motores eléctricos - Carlos Aroeira.
Vibraciones básicas de maquinaria
Introducción al análisis básico de maquinaria - Ronald L. Eshleman.
Tablas ilustradas de diagnóstico de vibraciones - Tablas de Charlotte
Dinos qué te ha parecido el artículo
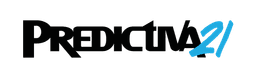

Durante muchos años, se han utilizado los motores de inducción en la industria debido a su menor costo de adquisición y mantenimiento en comparación con otros tipos de motores.
Algunas de sus características más importantes, además de su construcción, están relacionadas con su principio de funcionamiento. El campo magnético giratorio inducirá una fuerza electromotriz (a la que se denominará f.e.m.), que el rotor intenta seguir pero nunca alcanza. Por ejemplo, un motor diseñado con 2 polos tiene una velocidad producida por la f.e.m. de 3600 RPM, mientras que el rotor, en su intento de igualarla, alcanza 3505 RPM. A esta diferencia de velocidad se le llama resbalamiento.
En vibraciones mecánicas, el resbalamiento se traduce como la frecuencia de deslizamiento, que está dada por la ecuación: Fs=Ns−RPM
Donde:
- Fs = Frecuencia de deslizamiento.
- Ns = Velocidad síncrona (producida por la f.e.m.).
- RPM = Velocidad del rotor físicamente.
Para este caso: Fs= 3600 − 3505 = 95CPM
Una vez conocida la frecuencia de deslizamiento, podemos calcular la frecuencia de paso de polos, que está dada por la ecuación:Fp=P×Fs
Donde:
- Fp = Frecuencia de paso de polos.
- P = Número de polos.
- Fs = Frecuencia de deslizamiento.
Para este caso: Fp= 2 × 95CPM = 190CPM = 3.16Hz
Con este contexto y conociendo estas frecuencias, podemos asociarlas con una variedad de problemas eléctricos que pueden apreciarse desde el punto de vista mecánico a través de las vibraciones. Aunque esta no es la mejor manera de determinar problemas eléctricos, sí es una herramienta útil para detectar comportamientos anómalos. Asociando estas frecuencias a tendencias aplicadas en el mantenimiento predictivo (PdM), podemos realizar un seguimiento puntual en términos de frecuencia y amplitud.
Estas frecuencias se presentan en un espectro de vibración, incluyendo la presencia de la 2FL, que corresponde a 2 veces la frecuencia de suministro eléctrico o de línea. En México, esta frecuencia es de 60 Hz, por lo que la 2FL sería:2×60Hz=120Hz
En campo, se detecta un aumento de la amplitud de la vibración de un motor de inducción de dos polos. En este caso, se observan múltiplos de la frecuencia fundamental (1X, 2X, 3X, 4X...), indicando holgura rotativa. Esto apunta principalmente a un desajuste en las cajas del rodamiento del motor.
En la resolución del espectro de vibración, se observan "picos" de amplitud en banda ancha debido a frecuencias muy cercanas entre sí. Para estudiar estas frecuencias, es necesario configurar adecuadamente la resolución del espectro.

Se emplea el método de demodulación para buscar frecuencias altas o de tildeo que aporten al diagnóstico, enfocándose en detectar algún desajuste en el rodamiento o frecuencias de falla asociadas a los rodamientos. Durante el análisis, se identifican valores síncronos (no relacionados con los rodamientos) y una pronunciación marcada de la frecuencia 2FL.

Se configura la resolución del espectro. En este, se pueden apreciar los múltiplos de la frecuencia fundamental, como ya se había mencionado. Además, se observan bandas laterales en cada uno de ellos. Estas bandas laterales tienen una frecuencia de 3.16 Hz, lo cual está completamente ligado a la frecuencia de paso de polos calculada al principio del artículo.

La aparición de las bandas laterales a múltiplos de giro se presenta cuando existe una excentricidad en el rotor. Esto ocurre debido a un entrehierro variable de manera giratoria entre el rotor y el estátor, lo que induce una vibración pulsante. Las frecuencias que generan solo un par de bandas laterales suelen corresponder a modulaciones de amplitud.
En la medición de aceleración en el dominio del tiempo, la velocidad de rotación (58.41 Hz / T=0.017s) está siendo modulada en amplitud por la frecuencia de paso de polos (3.16 Hz / T=0.316s). Este efecto puede ser percibido durante inspecciones visuales, manifestándose como sonidos de motor "rugiendo" o "mufeando", como se le llama coloquialmente. Esto es causado por oscilaciones grandes y rápidas bajo carga.

La variación del entrehierro puede ser producida por muchos factores. Centrar la armadura para eliminar la distorsión del estátor puede ser una solución, pero en este caso, se sospecha la presencia de una holgura rotativa severa debido a los múltiplos de la velocidad fundamental, lo cual tiene su origen en un claro excesivo entre los cojinetes.
Un rotor excéntrico significa que el diámetro exterior del núcleo del rotor no es concéntrico con los muñones del rodamiento. Esto crea un punto mínimo de espacio de aire que gira con el rotor a la frecuencia de rotación. Asociado a este fenómeno, habrá una fuerza magnética desequilibrada actuando en el punto mínimo del entrehierro, ya que la fuerza en el entrehierro mínimo es mayor que la fuerza en el entrehierro máximo, como se ilustra en la figura. Esta fuerza neta de desequilibrio girará junto con el entrehierro mínimo a la frecuencia de rotación, causando vibración en dicha frecuencia.

En recomendación a las observaciones en campo y al análisis del espectro, se sugiere revisar y centrar la armadura del motor, eliminar la distorsión del estátor, inspeccionar el claro excesivo y corregir el desajuste de los rodamientos, o cualquier otra condición que pueda causar que el rotor esté excéntrico con respecto al estátor.
Bibliografía - Excentricidad dinámica en motores de inducción
Artículo técnico
Análisis de vibraciones en motores eléctricos - Carlos Aroeira.
Vibraciones básicas de maquinaria
Introducción al análisis básico de maquinaria - Ronald L. Eshleman.
Tablas ilustradas de diagnóstico de vibraciones - Tablas de Charlotte
Dinos qué te ha parecido el artículo

HxGN EAM: Un Enfoque Estratégico para la Gestión Eficiente de Activos
Artículo
En un entorno de creciente presión por optimizar el uso de los activos existentes, HxGN EAM (Enterprise Asset Management) es una solución líder diseñada para maximizar la vida útil de los activos y mejorar la productividad. Este software avanzado permite a las organizaciones tomar decisiones estratégicas y efectivas, enfocándose en la reducción de costos, el aumento de la confiabilidad y el incremento de la seguridad.
Adaptabilidad y Escalabilidad
HxGN EAM se adapta a las necesidades específicas de cada industria. Con una plataforma basada en la nube (AWS), garantiza alta disponibilidad, confiabilidad y la capacidad de escalar según los requisitos de cada organización. Las capacidades modulares de HxGN EAM permiten la integración de alertas automáticas, gestión de activos, presupuestos y mantenimiento preventivo, entre otras funciones esenciales para garantizar una operación eficiente.
Uno de los aspectos más destacados de HxGN EAM es su capacidad para gestionar todo el ciclo de vida de los activos, desde su adquisición hasta el final de su vida útil. El sistema permite la captura detallada de información técnica y comercial de los activos, incluyendo su estructura, historial de mantenimiento, costos y análisis de fallos, proporcionando una visión integral de su rendimiento.
Seguridad y Cumplimiento Normativo
HxGN EAM integra módulos específicos para la identificación y control de riesgos asociados con materiales peligrosos y actividades peligrosas. Esto protege a los empleados, al entorno y asegura un cumplimiento riguroso de las normativas de salud, seguridad y medio ambiente.
Impacto en la Productividad y Reducción de CostosLas organizaciones que han implementado HxGN EAM han reportado beneficios significativos, como una reducción del 50% en los costos asociados al mantenimiento y una disminución del 20% en el tiempo de inactividad. Estos resultados son consecuencia directa de una gestión más eficiente de los recursos y una mejor planificación del mantenimiento.
Funcionalidades avanzadas que cubren aspectos críticos de la gestión de activos:
- Gestión de alertas: Monitoreo automático de la base de datos para identificar eventos relevantes, permitiendo la creación de órdenes de trabajo o la emisión de notificaciones.
- Mantenimiento preventivo y predictivo: Permite planificar y gestionar el mantenimiento, reduciendo el riesgo de fallos inesperados.
- Gestión de inventarios: Ayuda a mantener niveles de stock adecuados, optimizando la inversión en repuestos y minimizando costos.
- Rendimiento energético: Herramientas para monitorear y comparar el rendimiento energético del activo, ahorrando recursos.
HxGN EAM transforma la gestión de activos en una ventaja competitiva para enfrentar los desafíos actuales y asegurar un uso óptimo de los recursos a largo plazo, proporcionando las herramientas necesarias para mejorar la productividad.
¡Lleva tu gestión de activos al siguiente nivel!
Dinos qué te ha parecido el artículo
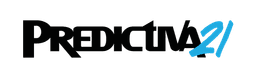

En un entorno de creciente presión por optimizar el uso de los activos existentes, HxGN EAM (Enterprise Asset Management) es una solución líder diseñada para maximizar la vida útil de los activos y mejorar la productividad. Este software avanzado permite a las organizaciones tomar decisiones estratégicas y efectivas, enfocándose en la reducción de costos, el aumento de la confiabilidad y el incremento de la seguridad.
Adaptabilidad y Escalabilidad
HxGN EAM se adapta a las necesidades específicas de cada industria. Con una plataforma basada en la nube (AWS), garantiza alta disponibilidad, confiabilidad y la capacidad de escalar según los requisitos de cada organización. Las capacidades modulares de HxGN EAM permiten la integración de alertas automáticas, gestión de activos, presupuestos y mantenimiento preventivo, entre otras funciones esenciales para garantizar una operación eficiente.
Uno de los aspectos más destacados de HxGN EAM es su capacidad para gestionar todo el ciclo de vida de los activos, desde su adquisición hasta el final de su vida útil. El sistema permite la captura detallada de información técnica y comercial de los activos, incluyendo su estructura, historial de mantenimiento, costos y análisis de fallos, proporcionando una visión integral de su rendimiento.
Seguridad y Cumplimiento Normativo
HxGN EAM integra módulos específicos para la identificación y control de riesgos asociados con materiales peligrosos y actividades peligrosas. Esto protege a los empleados, al entorno y asegura un cumplimiento riguroso de las normativas de salud, seguridad y medio ambiente.
Impacto en la Productividad y Reducción de CostosLas organizaciones que han implementado HxGN EAM han reportado beneficios significativos, como una reducción del 50% en los costos asociados al mantenimiento y una disminución del 20% en el tiempo de inactividad. Estos resultados son consecuencia directa de una gestión más eficiente de los recursos y una mejor planificación del mantenimiento.
Funcionalidades avanzadas que cubren aspectos críticos de la gestión de activos:
- Gestión de alertas: Monitoreo automático de la base de datos para identificar eventos relevantes, permitiendo la creación de órdenes de trabajo o la emisión de notificaciones.
- Mantenimiento preventivo y predictivo: Permite planificar y gestionar el mantenimiento, reduciendo el riesgo de fallos inesperados.
- Gestión de inventarios: Ayuda a mantener niveles de stock adecuados, optimizando la inversión en repuestos y minimizando costos.
- Rendimiento energético: Herramientas para monitorear y comparar el rendimiento energético del activo, ahorrando recursos.
HxGN EAM transforma la gestión de activos en una ventaja competitiva para enfrentar los desafíos actuales y asegurar un uso óptimo de los recursos a largo plazo, proporcionando las herramientas necesarias para mejorar la productividad.
¡Lleva tu gestión de activos al siguiente nivel!
Dinos qué te ha parecido el artículo

Análisis de Grasa y Ultrasonido para Rodamientos
Artículo
A principios del 2010 tuve mi primer encuentro con una de las tecnologías del mantenimiento predictivo que, desde que la aprendí a utilizar, vi el potencial que tiene, y sobre todo, cuando se utiliza en combinación con otras herramientas del PdM.El ultrasonido propagado en aire para la inspección de rodamientos es, probablemente, una de las herramientas más sencillas y versátiles de utilizar, cuyos resultados pueden observarse casi inmediatamente.
Dependiendo de la fuente y el autor, el ultrasonido suele estar al inicio de la curva P-F, por delante de otras herramientas. Si bien esto es discutible y habrá casos en los que sí y otros en los que no, en lo que estamos de acuerdo es en que no podemos negar su valor y el beneficio que tiene en la determinación de la condición del rodamiento. En el peor de los escenarios, y si no se aplica ningún remedio, el ultrasonido inaudible tenderá a volverse audible, y el rodamiento estará muy cerca de un fallo funcional.

De manera muy simplista, la teoría que rige esta herramienta dice que el ultrasonido (dB) es el resultado de la fricción entre el elemento rodante, la pista interna, la jaula, el lubricante y otros elementos como la contaminación externa y el desgaste generado internamente. Para mantener el ultrasonido en un rango de normalidad, el lubricante —grasa, en el análisis del presente estudio— se añade para minimizar la fricción entre los componentes del rodamiento. De esta manera, se reduce el contacto, el desgaste y se extiende la vida en servicio del rodamiento para intentar alcanzar la vida esperada.
Alrededor de este concepto, y con el pujante ingreso de la Industria 4.0 al sector del PdM, se han diseñado sensores que añaden grasa de manera automática, en un volumen preciso para no sobrecargar de grasa el poco espacio que existe en el rodamiento, siempre que se detecten valores anómalos de ultrasonido.
Hasta aquí todo parece andar sobre ruedas, de manera tal que el engrase de rodamientos representa un antes y un después tras esta tecnología.Pero, ¿qué pasa con la grasa que está en servicio? Si hiciésemos un interrogatorio a dicha grasa, ¿qué nos diría? ¿Qué valor nos aportaría?
Grasa, ¿qué puede decirnos?
El primer informe de análisis de grasa en servicio en un rodamiento de motor eléctrico que tuve en mis manos databa de 1994. Año del mundial de fútbol, mientras yo veía el partido inaugural que enfrentaba al todopoderoso conjunto alemán contra 11 guerreros bolivianos, alguien bajo el sol del pleno verano estaba tomando una muestra de grasa de un rodamiento que había fallado, con la intención de saber si esa muestra podía dar alguna pista del fallo. Para ese tiempo, el análisis de aceite ya llevaba unas cuantas décadas reportando beneficios, pero la grasa… ¡a quién se le ocurriría analizar grasa!
Ahora sabemos que el análisis de grasa puede aportar mucho al mantenimiento y a la fiabilidad. Al menos algunos lo tenemos claro y sabemos cómo extraer el máximo provecho de esto.Una muestra de grasa obtenida adecuadamente evidencia la condición del rodamiento, puede desvelar si existe contaminación, de qué tipo, cuánta contaminación, si existe paso de corriente, si hubo mezcla de grasas, si esa mezcla es incompatible, y un largo etcétera. Esto es mucho pedir, al menos a un fluido no newtoniano.
[TIP] En la industria de procesado de grano para obtención de harinas, los rodamientos sufren un modo de fallo único, que no se observa en otras industrias. Se debe precisamente a la propiedad de los fluidos no newtonianos sometidos a altas cargas y presiones. ¿Te interesa saber más?
Volviendo a la grasa, su análisis es tan importante que, en la industria de aerogeneración, por citar un ejemplo, un análisis apropiado puede advertir de un fallo funcional del rodamiento principal, evitando así incurrir en un alto costo prevenible de mantenimiento.
Ultrasonido & Análisis de grasa, ¿qué aportan en conjunto?
Como hemos visto, de manera aislada ambas herramientas son increíbles, y si se utilizan adecuadamente, aportan muchos beneficios.
Pero, ¿podrían utilizarse en conjunto?
Llevaba años haciéndome esta pregunta. Había sido capaz de analizar unos 30 rodamientos, obteniendo muestras de grasas y ultrasonido, pero puntualmente, sin lograr la trazabilidad adecuada. Se necesita al menos dos puntos para trazar una recta, y con solo un punto no tenía más que suposiciones y no resultados coherentes.
Fue en una planta petroquímica donde pude calmar esa sed de conocimiento y durante dos años recolecté muestras tanto de grasa como de ultrasonido en un grupo de alrededor de 60 activos de diferentes características y condiciones. Los resultados y conclusiones presentadas en este artículo no pueden ser generalizados, ya que dependen mucho de factores como el tipo de rodamiento, la velocidad, las condiciones de operación, el ambiente operativo, los tipos de grasa utilizados en planta y el factor humano, además de la variabilidad del reengrase manual —no podemos sensorizar el 100% de los activos— al menos de momento.
Si bien la medida obtenida por el ultrasonido es única y se expresa en dB, el resultado del análisis de grasa está dividido en las siguientes variables:
- Desgastes ≤ 7 μ
- Desgastes ≥ 5 μ
- Desgaste de jaula (teniendo en cuenta que no había jaulas de poliamida)
- Consistencia de la grasa
- Incompatibilidad entre espesantes
- Diferentes viscosidades de aceite
De estas seis variables, los resultados mostrados en este breve artículo se centran únicamente en las dos primeras: desgastes del rodamiento. Por otro lado, se muestran únicamente resultados del rodamiento del lado del acoplamiento.
Al cabo de los dos años se obtuvieron alrededor de 500 muestras de cada tecnología. Utilizando un sistema de colores, de manera aislada, los resultados son los siguientes:

A grandes rasgos, la mayoría de los rodamientos tiene un comportamiento similar en función de los desgastes y el nivel de decibelios, y es posible sacar bastantes conclusiones de un análisis de este tipo.Tomaremos como ejemplo el rodamiento del lado de acoplamiento correspondiente a la unidad JBX – 102A.Este rodamiento tuvo que ser reemplazado al mes siguiente del último análisis, debido a que se podía oír la fricción producida internamente, y un posterior análisis evidenció un daño irreparable en la pista interna.
Es importante mencionar los siguientes puntos:
- El engrase se realiza dentro del concepto de mantenimiento preventivo, con una frecuencia definida.
- Los rodamientos se cambian en función del mantenimiento correctivo; es decir, operan hasta el fallo.
- La frecuencia de reengrase es bimensual, marcada con un recuadro en la figura 2.
- En los meses en los que no se realiza el reengrase, solo se recolecta información.
- El volumen de grasa añadido no supera el volumen calculado.


Resultados iniciales
Siguiendo la línea de tiempo, podemos ver algunos resultados remarcables:
- La línea base de ultrasonido para este rodamiento se sitúa en 38 dB, y la tecnología alerta que se ha rebasado este límite al cabo del tercer mes (Jun-18). ¡Punto a favor para el ultrasonido! El análisis de grasa no muestra que los desgastes se encuentren dentro de valores anómalos.
- Avanzamos en el tiempo y, tras el reengrase habitual, el ultrasonido regresa a valores normales. Cuando todo parece estar bien, los desgastes medidos por partículas inferiores a 7 μm superan el límite establecido (Sep-18). ¡Punto para el análisis de grasa! El análisis por ultrasonido se encuentra dentro de valores normales.
- Tras el reengrase de Nov-18, el ultrasonido está dentro de niveles normales, pero ambos tipos de desgastes han superado sus límites admisibles.
- A partir de este punto, entramos en una zona de no retorno con unas tendencias crecientes para las tres variables. A esto se debe sumar que, por fallo humano, no se realizó el reengrase de Feb-19 y, para cuadrar cuentas con el sistema de gestión de mantenimiento, se reengrasó dos meses seguidos: Mar-19 y Abr-19.
- Pasado este punto, los dB no se incrementan de manera exagerada como sí lo hacen los desgastes, hasta acabar en un fallo funcional del rodamiento.
Conclusiones: quizá sirvan de algo
Volviendo a la curva P-F, ¿quién se adelanta al fallo funcional del rodamiento en este caso? Difícil decir quién. Lo cierto es que podemos aprender cosas interesantes de esta situación:
- El ultrasonido, al menos en esta situación, es un gran indicador del resultado cualitativo de la condición del rodamiento. Sí, nos da un valor en dB y este resultado es cuantificable, pero no nos dice cómo es el desgaste.
- El análisis de grasa, al menos en esta situación, es un gran indicador del resultado cuantitativo de la condición del rodamiento. Sí, nos dice cuánto se desgasta, pero no cómo es la fricción entre los elementos del rodamiento.
- El desgaste de los componentes del rodamiento es resultado de la fricción, y esta a su vez genera más desgaste.
- El valor agregado cuando se trabaja con ambas tecnologías radica precisamente en determinar cómo es la fricción y cómo son los desgastes.
- Desafortunadamente, la grasa no fluye con facilidad y tiende a retener las partículas de desgaste generadas por fricción.
- Muchas configuraciones de rodamientos no tienen un punto de purga para eliminar la grasa y partículas incluidas de manera adecuada, por lo que los desgastes, en muchos casos, forman parte del sistema.
- Pasar de un mantenimiento preventivo, donde se engrasa en función de frecuencia, a uno predictivo, donde se engrasa en función de condición, requiere un sistema de seguimiento casi perfecto; la fricción y los desgastes no conocen límites.
- Los límites hay que respetarlos. Ya sean 80 km/h, 38 dB o 50 ppm de hierro, han sido puestos por alguna razón.
- Las acciones correctivas de mantenimiento deben ser apropiadas a los resultados obtenidos. Quizá no sea necesario reemplazar el rodamiento a los 44 dB/40 ppm Fe, pero será imprescindible definir qué se debe hacer; caso contrario, el fallo funcional decidirá por nosotros.

Dinos qué te ha parecido el artículo
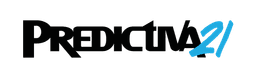

A principios del 2010 tuve mi primer encuentro con una de las tecnologías del mantenimiento predictivo que, desde que la aprendí a utilizar, vi el potencial que tiene, y sobre todo, cuando se utiliza en combinación con otras herramientas del PdM.El ultrasonido propagado en aire para la inspección de rodamientos es, probablemente, una de las herramientas más sencillas y versátiles de utilizar, cuyos resultados pueden observarse casi inmediatamente.
Dependiendo de la fuente y el autor, el ultrasonido suele estar al inicio de la curva P-F, por delante de otras herramientas. Si bien esto es discutible y habrá casos en los que sí y otros en los que no, en lo que estamos de acuerdo es en que no podemos negar su valor y el beneficio que tiene en la determinación de la condición del rodamiento. En el peor de los escenarios, y si no se aplica ningún remedio, el ultrasonido inaudible tenderá a volverse audible, y el rodamiento estará muy cerca de un fallo funcional.

De manera muy simplista, la teoría que rige esta herramienta dice que el ultrasonido (dB) es el resultado de la fricción entre el elemento rodante, la pista interna, la jaula, el lubricante y otros elementos como la contaminación externa y el desgaste generado internamente. Para mantener el ultrasonido en un rango de normalidad, el lubricante —grasa, en el análisis del presente estudio— se añade para minimizar la fricción entre los componentes del rodamiento. De esta manera, se reduce el contacto, el desgaste y se extiende la vida en servicio del rodamiento para intentar alcanzar la vida esperada.
Alrededor de este concepto, y con el pujante ingreso de la Industria 4.0 al sector del PdM, se han diseñado sensores que añaden grasa de manera automática, en un volumen preciso para no sobrecargar de grasa el poco espacio que existe en el rodamiento, siempre que se detecten valores anómalos de ultrasonido.
Hasta aquí todo parece andar sobre ruedas, de manera tal que el engrase de rodamientos representa un antes y un después tras esta tecnología.Pero, ¿qué pasa con la grasa que está en servicio? Si hiciésemos un interrogatorio a dicha grasa, ¿qué nos diría? ¿Qué valor nos aportaría?
Grasa, ¿qué puede decirnos?
El primer informe de análisis de grasa en servicio en un rodamiento de motor eléctrico que tuve en mis manos databa de 1994. Año del mundial de fútbol, mientras yo veía el partido inaugural que enfrentaba al todopoderoso conjunto alemán contra 11 guerreros bolivianos, alguien bajo el sol del pleno verano estaba tomando una muestra de grasa de un rodamiento que había fallado, con la intención de saber si esa muestra podía dar alguna pista del fallo. Para ese tiempo, el análisis de aceite ya llevaba unas cuantas décadas reportando beneficios, pero la grasa… ¡a quién se le ocurriría analizar grasa!
Ahora sabemos que el análisis de grasa puede aportar mucho al mantenimiento y a la fiabilidad. Al menos algunos lo tenemos claro y sabemos cómo extraer el máximo provecho de esto.Una muestra de grasa obtenida adecuadamente evidencia la condición del rodamiento, puede desvelar si existe contaminación, de qué tipo, cuánta contaminación, si existe paso de corriente, si hubo mezcla de grasas, si esa mezcla es incompatible, y un largo etcétera. Esto es mucho pedir, al menos a un fluido no newtoniano.
[TIP] En la industria de procesado de grano para obtención de harinas, los rodamientos sufren un modo de fallo único, que no se observa en otras industrias. Se debe precisamente a la propiedad de los fluidos no newtonianos sometidos a altas cargas y presiones. ¿Te interesa saber más?
Volviendo a la grasa, su análisis es tan importante que, en la industria de aerogeneración, por citar un ejemplo, un análisis apropiado puede advertir de un fallo funcional del rodamiento principal, evitando así incurrir en un alto costo prevenible de mantenimiento.
Ultrasonido & Análisis de grasa, ¿qué aportan en conjunto?
Como hemos visto, de manera aislada ambas herramientas son increíbles, y si se utilizan adecuadamente, aportan muchos beneficios.
Pero, ¿podrían utilizarse en conjunto?
Llevaba años haciéndome esta pregunta. Había sido capaz de analizar unos 30 rodamientos, obteniendo muestras de grasas y ultrasonido, pero puntualmente, sin lograr la trazabilidad adecuada. Se necesita al menos dos puntos para trazar una recta, y con solo un punto no tenía más que suposiciones y no resultados coherentes.
Fue en una planta petroquímica donde pude calmar esa sed de conocimiento y durante dos años recolecté muestras tanto de grasa como de ultrasonido en un grupo de alrededor de 60 activos de diferentes características y condiciones. Los resultados y conclusiones presentadas en este artículo no pueden ser generalizados, ya que dependen mucho de factores como el tipo de rodamiento, la velocidad, las condiciones de operación, el ambiente operativo, los tipos de grasa utilizados en planta y el factor humano, además de la variabilidad del reengrase manual —no podemos sensorizar el 100% de los activos— al menos de momento.
Si bien la medida obtenida por el ultrasonido es única y se expresa en dB, el resultado del análisis de grasa está dividido en las siguientes variables:
- Desgastes ≤ 7 μ
- Desgastes ≥ 5 μ
- Desgaste de jaula (teniendo en cuenta que no había jaulas de poliamida)
- Consistencia de la grasa
- Incompatibilidad entre espesantes
- Diferentes viscosidades de aceite
De estas seis variables, los resultados mostrados en este breve artículo se centran únicamente en las dos primeras: desgastes del rodamiento. Por otro lado, se muestran únicamente resultados del rodamiento del lado del acoplamiento.
Al cabo de los dos años se obtuvieron alrededor de 500 muestras de cada tecnología. Utilizando un sistema de colores, de manera aislada, los resultados son los siguientes:

A grandes rasgos, la mayoría de los rodamientos tiene un comportamiento similar en función de los desgastes y el nivel de decibelios, y es posible sacar bastantes conclusiones de un análisis de este tipo.Tomaremos como ejemplo el rodamiento del lado de acoplamiento correspondiente a la unidad JBX – 102A.Este rodamiento tuvo que ser reemplazado al mes siguiente del último análisis, debido a que se podía oír la fricción producida internamente, y un posterior análisis evidenció un daño irreparable en la pista interna.
Es importante mencionar los siguientes puntos:
- El engrase se realiza dentro del concepto de mantenimiento preventivo, con una frecuencia definida.
- Los rodamientos se cambian en función del mantenimiento correctivo; es decir, operan hasta el fallo.
- La frecuencia de reengrase es bimensual, marcada con un recuadro en la figura 2.
- En los meses en los que no se realiza el reengrase, solo se recolecta información.
- El volumen de grasa añadido no supera el volumen calculado.


Resultados iniciales
Siguiendo la línea de tiempo, podemos ver algunos resultados remarcables:
- La línea base de ultrasonido para este rodamiento se sitúa en 38 dB, y la tecnología alerta que se ha rebasado este límite al cabo del tercer mes (Jun-18). ¡Punto a favor para el ultrasonido! El análisis de grasa no muestra que los desgastes se encuentren dentro de valores anómalos.
- Avanzamos en el tiempo y, tras el reengrase habitual, el ultrasonido regresa a valores normales. Cuando todo parece estar bien, los desgastes medidos por partículas inferiores a 7 μm superan el límite establecido (Sep-18). ¡Punto para el análisis de grasa! El análisis por ultrasonido se encuentra dentro de valores normales.
- Tras el reengrase de Nov-18, el ultrasonido está dentro de niveles normales, pero ambos tipos de desgastes han superado sus límites admisibles.
- A partir de este punto, entramos en una zona de no retorno con unas tendencias crecientes para las tres variables. A esto se debe sumar que, por fallo humano, no se realizó el reengrase de Feb-19 y, para cuadrar cuentas con el sistema de gestión de mantenimiento, se reengrasó dos meses seguidos: Mar-19 y Abr-19.
- Pasado este punto, los dB no se incrementan de manera exagerada como sí lo hacen los desgastes, hasta acabar en un fallo funcional del rodamiento.
Conclusiones: quizá sirvan de algo
Volviendo a la curva P-F, ¿quién se adelanta al fallo funcional del rodamiento en este caso? Difícil decir quién. Lo cierto es que podemos aprender cosas interesantes de esta situación:
- El ultrasonido, al menos en esta situación, es un gran indicador del resultado cualitativo de la condición del rodamiento. Sí, nos da un valor en dB y este resultado es cuantificable, pero no nos dice cómo es el desgaste.
- El análisis de grasa, al menos en esta situación, es un gran indicador del resultado cuantitativo de la condición del rodamiento. Sí, nos dice cuánto se desgasta, pero no cómo es la fricción entre los elementos del rodamiento.
- El desgaste de los componentes del rodamiento es resultado de la fricción, y esta a su vez genera más desgaste.
- El valor agregado cuando se trabaja con ambas tecnologías radica precisamente en determinar cómo es la fricción y cómo son los desgastes.
- Desafortunadamente, la grasa no fluye con facilidad y tiende a retener las partículas de desgaste generadas por fricción.
- Muchas configuraciones de rodamientos no tienen un punto de purga para eliminar la grasa y partículas incluidas de manera adecuada, por lo que los desgastes, en muchos casos, forman parte del sistema.
- Pasar de un mantenimiento preventivo, donde se engrasa en función de frecuencia, a uno predictivo, donde se engrasa en función de condición, requiere un sistema de seguimiento casi perfecto; la fricción y los desgastes no conocen límites.
- Los límites hay que respetarlos. Ya sean 80 km/h, 38 dB o 50 ppm de hierro, han sido puestos por alguna razón.
- Las acciones correctivas de mantenimiento deben ser apropiadas a los resultados obtenidos. Quizá no sea necesario reemplazar el rodamiento a los 44 dB/40 ppm Fe, pero será imprescindible definir qué se debe hacer; caso contrario, el fallo funcional decidirá por nosotros.

Dinos qué te ha parecido el artículo

El internista de la 21, Edición 51
Columna-1736967700910.png%3Falt%3Dmedia%26token%3Da793b062-6090-4b84-b596-192dde707bc4&w=640&q=75)
Soy Rafael Arguelles F., TSU en Informática, Ingeniero Electricista y MSc en Administración de Negocios, con más de 38 años de experiencia en el ámbito técnico, profesional y gerencial. Practico el silogismo en mi forma de pensar y actuar, lo que me convierte en un estoico en mi manera de ser. No les contaré mucho más de mí, ya que este no es el propósito de esta columna.
En esta columna exploraremos el diseño a la medida —como un traje de sastre hecho especialmente— del proceso de gestión del mantenimiento, considerando este como una parte fundamental del ciclo de vida de un activo durante su fase operacional (la zona plana de la curva de desempeño), enmarcado en su función dentro de un proceso. Dado lo extenso del tema, estimo que lo desarrollaremos en al menos dos, posiblemente tres entregas.
En columnas anteriores, definimos los tipos de mantenimiento que pueden contemplarse desde el punto de vista normativo clásico. Estas definiciones son esenciales para el desarrollo de esta columna, ya que nos centraremos en cómo combinarlos dentro de distintas estrategias. Además, a partir de esta entrega, abordaremos la optimización de costos (no hablaremos de reducción de costos, ya que no es la estrategia correcta en ningún caso), así como la planificación de actividades con un enfoque en activos que no están en servicio. También profundizaremos en el diseño de la Orden de Trabajo, un documento clave para optimizar las estrategias y sus resultados. Cabe destacar que no nos enfocaremos en adaptarnos a ninguna normativa específica, ya que el objetivo principal es maximizar el retorno desde el punto de vista de la utilización de los activos.
Premisas fundamentales
Diseño desde cero:Partiremos de la premisa de que estamos diseñando el proceso desde cero. Esta aproximación simplifica el diseño, ya que no es necesario diagnosticar la gestión actual, un paso que, de manera general, siempre resulta indispensable para identificar áreas susceptibles de mejora.
Recursos disponibles:Otra premisa clave es que contamos con recursos financieros potencialmente suficientes para implementar el diseño y con personal técnico necesario y adecuado, tanto en cantidad como en experiencia, para ejecutar las estrategias concebidas en el proceso. Esto no supone partir de un mundo ideal, sino de un escenario completamente factible, en el que, eso sí, deberá demostrarse que todo lo propuesto en el diseño contribuye a generar un retorno positivo.
En las próximas entregas, profundizaremos en estos aspectos, buscando siempre diseñar estrategias que no solo sean efectivas, sino que también optimicen los recursos y aseguren el máximo desempeño de los activos.
También mencionamos un “documento” muy importante: la orden de trabajo, o como también es conocida, la OT. Uso las comillas porque la orden de trabajo es mucho más que un simple documento. La OT es, en síntesis, la definición funcional del proceso necesario para ejecutar una labor de mantenimiento correctivo (programado o no) o de mantenimiento preventivo (necesariamente programado). Pero, ¿qué pasa con el documento de soporte del Mantenimiento Predictivo? ¿O del Mantenimiento Proactivo?
Las órdenes de trabajo se generan y gestionan desde un software de gestión de mantenimiento (CMMS, por sus siglas en inglés: Computerized Maintenance Management System). En cambio, las herramientas y estrategias de Mantenimiento Predictivo y Mantenimiento Proactivo son generadas y gestionadas en un software para la gestión de activos (EAMS, por sus siglas en inglés: Enterprise Asset Management System). Esta diferenciación en la gestión, a mi juicio, nos ofrece una pista importante sobre dónde no debería residir la gestión de activos. Pero dejaré el comentario hasta aquí, porque, como mencioné en la primera entrega, este tema genera polémicas, y lo más relevante es enfocarnos en el KIR.
Ejemplos de sistemas de gestión
Existen muchos ejemplos de sistemas para la gestión de mantenimiento y activos. A continuación, menciono algunos con los que he trabajado:
- CMMS: Maximo, SAP MM, JDEdwards. De los mencionados, el único diseñado exclusivamente como CMMS es Maximo. Los otros dos son módulos de gestión de mantenimiento incluidos en suites empresariales más amplias que abarcan compras, inventarios, finanzas, nóminas, entre otros.
- EAMS: Meridium (hoy día conocido como GE APM) y AMS (de Emerson). De estos, puedo destacar que Meridium incluye módulos que, además del monitoreo de condiciones (RCM, IBR, etc.), permiten gestionar casos documentados de Mantenimiento Proactivo (como ACR, Control de Corrosión, Métricas de Gestión de Activos Físicos, entre otros).
La importancia de la integración
Es altamente deseable que estos dos sistemas (CMMS y EAMS) estén completamente integrados. ¿Por qué?
En primer lugar, porque ambos gestionan los mismos activos. Además, como vimos en la primera parte de este artículo, la gestión de mantenimiento es una parte necesaria e imprescindible de la gestión de activos.
Como se observa en la Figura 1, las distintas fases del KIR se interrelacionan con las diversas herramientas y entornos de gestión. Las líneas terminadas en punta de flecha que se muestran en el diagrama ilustran cómo ocurre esta interacción de manera secuencial.
Recordemos que el KIR, al que de ahora en adelante llamaremos por su verdadero nombre, nació como una estrategia para evidenciar el principal objetivo de implementar la Confiabilidad Operacional: aumentar la disponibilidad de los activos físicos para la producción.

Logremos, entonces, establecer un recorrido por cada una de esas fases, para algunos ejemplos de casos hipotéticos.
CASO 1
En un equipo rotativo, de criticidad operacional alta, con monitoreo continuo de vibraciones, se produce una alarma por alta vibración en el sistema de control. Esto provoca una solicitud por parte del equipo de operaciones a los técnicos o ingenieros que realizan toma y análisis de estos datos, los cuales se presentan a ejecutar el diagnóstico solicitado. Una vez hechas las mediciones, al analizar el espectro, determinan que existe un juego radial mayor al esperado, por lo cual recomiendan reemplazar el cojinete en cuestión. De la misma manera, indican que la máquina puede seguir trabajando, con un monitoreo y análisis más frecuente, de forma de poder preparar el trabajo y hacer una parada ordenada.
Una vez descrito el caso, pasemos a formularnos algunas preguntas:
- La intervención del técnico que acude a realizar la medición y análisis del caso, ¿en qué fase transcurre? ¿En cuál sistema se gestiona?
- El siguiente paso, ¿en qué fase se encuentra y con cuál sistema se gestiona?
- El trabajo de llevar el activo a una condición normal de trabajo, ¿en qué fase ocurre? ¿Con cuál sistema se gestiona?
- Una vez hecho el trabajo, ¿cuál sería el próximo paso y en qué fase ocurre?
- ¿Qué tipos de mantenimiento hemos ejecutado hasta ahora?
- El monitoreo frecuente que se menciona, ¿en qué fase ocurre?
Procedamos, pues, a responder estas preguntas, invitando al análisis de la respuesta.
La intervención del técnico transcurre en la FASE 1: HERRAMIENTAS DE DIAGNÓSTICO APLICADAS EN LA FASE DE OPERACIÓN DEL ACTIVO. Esta estaba muy fácil de responder, pues de hecho, en el enunciado se indicó que haría una “toma y análisis de estos datos” para “ejecutar el diagnóstico solicitado”. Por supuesto, se gestiona en el EAMS. Si el EAMS y el CMMS están realmente integrados, desde el EAMS saldrá la OT para la corrección del defecto. De no estarlo, alguien tendrá que generar dicha orden de forma manual.
Luego de generarse la orden de trabajo, y ser evaluada por el personal técnico para garantizar que el alcance del trabajo que se especificó realmente es el requerido, se inicia la fase de PLANIFICACIÓN DE LA OT. Ya esto responde una parte de la siguiente pregunta: ¿Dónde ocurre el siguiente paso? Este paso, evidentemente, transcurre en la fase 2, “HERRAMIENTAS DE PLANIFICACIÓN PARA KIR,” y por supuesto, debe gestionarse en el CMMS. Esta fase incluye múltiples etapas, como la preparación, asignación de recursos, gestión de ventana operacional y ejecución del trabajo, que finaliza con la adecuada retroalimentación de la OT, este último un paso muy importante de la gestión que con frecuencia no es debidamente potenciado. Pero del flujo de trabajo del mantenimiento nos ocuparemos en una entrega posterior, en la que hablaremos del flujo de trabajo en distintas facetas del mantenimiento.
Pues bien, ya se hizo el diagnóstico, se especificó el trabajo, luego el mismo se planificó adecuadamente y se gestionó la ventana operacional... Nos corresponde ahora proceder a corregir el defecto, y llevar el activo a su condición de operación normal. Se reemplaza, en consecuencia, el cojinete con excesivo juego axial, se miden los cojinetes planos que no se cambiaron, se retroalimenta la orden, y se procede a su cierre. La ejecución del trabajo descrito transcurre en la FASE 3: CORRECCIÓN DEL DESPERFECTO. Y, por supuesto, se gestiona en el CMMS.
Ya se hizo el trabajo. ¿Qué debe ocurrir ahora? Este próximo paso depende en grado sumo de la madurez de la organización. Debería, en esta fase, iniciarse una gestión de pesquisa de fallas para determinar la causa del desgaste inesperado del cojinete. En este caso particular, se podría iniciar un Análisis de Causa Raíz (ACR), que nos ayude a determinar por qué la falla ocurrió, cómo evitamos una nueva ocurrencia y, muy importante, si genera una lección aprendida que nos ayude a prevenir el mismo tipo de falla en otros activos de la misma familia.
Y entonces, ¿qué tipos de mantenimiento hemos hecho hasta acá?
- Al diagnosticar, hemos hecho mantenimiento predictivo, o basado en condición.
- Al corregir un defecto que se ha presentado y hemos podido identificar, estamos haciendo mantenimiento correctivo.
- Dado que pudimos planificar las actividades requeridas, el mantenimiento correctivo realizado es de tipo planificado.
- Si, además de esto, hemos iniciado una pesquisa de fallas, hemos ejecutado mantenimiento proactivo.
Procedamos ahora a responder la última pregunta, la cual citaré textualmente: “El monitoreo frecuente que se menciona, ¿en qué fase ocurre?” Esta respuesta es quizás la más inesperada de todas: En ninguna.
¡Justifique su respuesta! No es necesario hacer un monitoreo y análisis más continuo. Si ya hemos determinado la causa de la alta vibración, tomando en cuenta la dimensión y frecuencia de la señal, y siendo que tenemos un monitoreo continuo con alarmas en el sistema de control, no se justifica que se tome una medida como la mencionada. Que tomes muestras de espectro y analices más a menudo no cambiará el estado. Si lo que necesitas es saber si el problema se está incrementando, en mi experiencia, lo recomendable es realizar un documento de gestión de cambio temporal para incrementar el valor de alarma en tu sistema de gestión de alarmas. Esto permitirá que tu equipo no esté en falla permanente en el sistema, a la vez que te permitirá saber cuándo el problema ha aumentado. Por supuesto, es necesario también garantizar que, una vez resuelto el problema, el valor de set de la alarma sea restituido a su valor original.
Como indiqué en un principio, este caso, acá descrito, es un caso hipotético. Cualquier parecido con la realidad es pura coincidencia.
CASO 2
Partamos del caso 1. Dado que estaremos interviniendo el equipo rotativo en cuestión, se decide adelantar algunos mantenimientos preventivos que estaban previstos para paradas cortas y que fueron debidamente planificados. Una de esas actividades preventivas es el ajuste de las conexiones eléctricas, tanto en la caja de conexiones del motor como en la salida del CCM hacia el motor. Cuando se ejecuta el trabajo, se encuentran conexiones recalentadas a una muy alta temperatura, por lo que se decide reemplazar terminales.¿Respondemos las mismas preguntas? Veamos:
La intervención original, donde se procede a realizar el reajuste de las conexiones, transcurre en la Fase 3. ¡Atención! Esta fase está enunciada como "corrección del desperfecto". Es cierto, al acudir a ejecutar una tarea de mantenimiento preventivo (reajuste de conexiones cada 3000 horas, por ejemplo), en la práctica, no hemos visualizado ningún defecto. Pero, conceptualmente, el mantenimiento preventivo está concebido para corregir un defecto que estadísticamente está por ocurrir o está ocurriendo. Así que sí, es en esta fase que ocurre. Y, por supuesto, se gestiona en el CMMS.
El siguiente paso, en este segundo ejemplo, es la corrección de la falla funcional detectada. Sí, se ha encontrado una falla funcional, que se ha detectado de forma incipiente, pero que está presente de forma indudable. Por supuesto, la ejecución de este trabajo se encuentra también en la Fase 3, “CORRECCIÓN DEL DEFECTO,” y como ya sabemos, se gestiona en el CMMS. Pero... ¡qué cosa con los "peros" en el mantenimiento! Debemos ahora preguntarnos: ¿este trabajo, a todas luces correctivo, debe ejecutarse y documentarse con la misma orden de trabajo? El reemplazo de terminales NO es parte del trabajo preventivo. Por lo tanto, NO debe documentarse con la misma orden. Si nuestro deseo es que el CMMS sea alimentado de forma correcta, este es un trabajo que debe clasificarse como un Mantenimiento Correctivo.
¿Planificado o no planificado? Evidentemente, no es planificado.¿Es un correctivo de emergencia? Evidentemente, no ocasionó paros de equipos, por lo que no es de emergencia.Entonces, ¿qué tipo de mantenimiento correctivo es? Es un mantenimiento correctivo de aprovechamiento (el calificativo es mío, pues nunca he visto este concepto debidamente documentado). Digamos que es de aprovechamiento o de oportunidad, pues es un correctivo que se ejecutó sin parada, y no fue programado ni planificado, sino que es fruto de otro mantenimiento efectuado. Esto debemos documentarlo, pues este tipo de información nos ayuda a demostrar qué actividades de mantenimiento se justifica ejecutar. Esto lleva el activo a operar funcionalmente al 100%, lo cual es de resaltar.
El siguiente paso, una vez ejecutado el trabajo, será nuevamente documentar la ejecución del mismo, cerrar las órdenes de trabajo (tanto la orden de mantenimiento preventivo de reajuste de las conexiones como la de mantenimiento correctivo de reemplazo de terminales) e iniciar una labor de pesquisa para identificar la causa por la cual la conexión se sobrecalentó. Como ya mencionamos, este trabajo inició como un mantenimiento preventivo (ajuste de las conexiones eléctricas cada 3000 horas) y generó un trabajo correctivo de aprovechamiento (reemplazo de las conexiones).
Nuestra próxima columna transcurrirá en el tema de la celebración del “DÍA INTERNACIONAL DE LA SALUD Y SEGURIDAD EN EL TRABAJO.” Como todos sabemos, la SST es algo que nos atañe a todos los que de alguna manera participamos en la cadena de generación de valor del mismo. Este año, el tema de la conmemoración es el cambio climático y cómo este afecta la SST.
Posteriormente, estaremos hablando un poco de los flujos de trabajo requeridos para organizar debidamente la forma en la que la gestión se lleva en el CMMS. Para alimentar, desde ya, esa edición, dejaré una pregunta en el aire: Si, como estrategia al diseñar los planes de mantenimiento centrado en confiabilidad, se decide aplicar “run to failure” a un activo, ¿cómo debe calificarse ese evento cuando ocurre? ¿Es un evento de mantenimiento correctivo? Al levantar mis KPIs, ¿a cuál estrategia de mantenimiento debe sumar? Esta discusión la iniciaremos prontamente en una nueva entrega del Internista de la 21, exclusivamente en Predictiva21.
¡Hasta la próxima entrega!
Normas/Documentos:Familia ISO55000EN 16646
Dinos qué te ha parecido el artículo
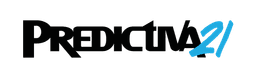

Soy Rafael Arguelles F., TSU en Informática, Ingeniero Electricista y MSc en Administración de Negocios, con más de 38 años de experiencia en el ámbito técnico, profesional y gerencial. Practico el silogismo en mi forma de pensar y actuar, lo que me convierte en un estoico en mi manera de ser. No les contaré mucho más de mí, ya que este no es el propósito de esta columna.
En esta columna exploraremos el diseño a la medida —como un traje de sastre hecho especialmente— del proceso de gestión del mantenimiento, considerando este como una parte fundamental del ciclo de vida de un activo durante su fase operacional (la zona plana de la curva de desempeño), enmarcado en su función dentro de un proceso. Dado lo extenso del tema, estimo que lo desarrollaremos en al menos dos, posiblemente tres entregas.
En columnas anteriores, definimos los tipos de mantenimiento que pueden contemplarse desde el punto de vista normativo clásico. Estas definiciones son esenciales para el desarrollo de esta columna, ya que nos centraremos en cómo combinarlos dentro de distintas estrategias. Además, a partir de esta entrega, abordaremos la optimización de costos (no hablaremos de reducción de costos, ya que no es la estrategia correcta en ningún caso), así como la planificación de actividades con un enfoque en activos que no están en servicio. También profundizaremos en el diseño de la Orden de Trabajo, un documento clave para optimizar las estrategias y sus resultados. Cabe destacar que no nos enfocaremos en adaptarnos a ninguna normativa específica, ya que el objetivo principal es maximizar el retorno desde el punto de vista de la utilización de los activos.
Premisas fundamentales
Diseño desde cero:Partiremos de la premisa de que estamos diseñando el proceso desde cero. Esta aproximación simplifica el diseño, ya que no es necesario diagnosticar la gestión actual, un paso que, de manera general, siempre resulta indispensable para identificar áreas susceptibles de mejora.
Recursos disponibles:Otra premisa clave es que contamos con recursos financieros potencialmente suficientes para implementar el diseño y con personal técnico necesario y adecuado, tanto en cantidad como en experiencia, para ejecutar las estrategias concebidas en el proceso. Esto no supone partir de un mundo ideal, sino de un escenario completamente factible, en el que, eso sí, deberá demostrarse que todo lo propuesto en el diseño contribuye a generar un retorno positivo.
En las próximas entregas, profundizaremos en estos aspectos, buscando siempre diseñar estrategias que no solo sean efectivas, sino que también optimicen los recursos y aseguren el máximo desempeño de los activos.
También mencionamos un “documento” muy importante: la orden de trabajo, o como también es conocida, la OT. Uso las comillas porque la orden de trabajo es mucho más que un simple documento. La OT es, en síntesis, la definición funcional del proceso necesario para ejecutar una labor de mantenimiento correctivo (programado o no) o de mantenimiento preventivo (necesariamente programado). Pero, ¿qué pasa con el documento de soporte del Mantenimiento Predictivo? ¿O del Mantenimiento Proactivo?
Las órdenes de trabajo se generan y gestionan desde un software de gestión de mantenimiento (CMMS, por sus siglas en inglés: Computerized Maintenance Management System). En cambio, las herramientas y estrategias de Mantenimiento Predictivo y Mantenimiento Proactivo son generadas y gestionadas en un software para la gestión de activos (EAMS, por sus siglas en inglés: Enterprise Asset Management System). Esta diferenciación en la gestión, a mi juicio, nos ofrece una pista importante sobre dónde no debería residir la gestión de activos. Pero dejaré el comentario hasta aquí, porque, como mencioné en la primera entrega, este tema genera polémicas, y lo más relevante es enfocarnos en el KIR.
Ejemplos de sistemas de gestión
Existen muchos ejemplos de sistemas para la gestión de mantenimiento y activos. A continuación, menciono algunos con los que he trabajado:
- CMMS: Maximo, SAP MM, JDEdwards. De los mencionados, el único diseñado exclusivamente como CMMS es Maximo. Los otros dos son módulos de gestión de mantenimiento incluidos en suites empresariales más amplias que abarcan compras, inventarios, finanzas, nóminas, entre otros.
- EAMS: Meridium (hoy día conocido como GE APM) y AMS (de Emerson). De estos, puedo destacar que Meridium incluye módulos que, además del monitoreo de condiciones (RCM, IBR, etc.), permiten gestionar casos documentados de Mantenimiento Proactivo (como ACR, Control de Corrosión, Métricas de Gestión de Activos Físicos, entre otros).
La importancia de la integración
Es altamente deseable que estos dos sistemas (CMMS y EAMS) estén completamente integrados. ¿Por qué?
En primer lugar, porque ambos gestionan los mismos activos. Además, como vimos en la primera parte de este artículo, la gestión de mantenimiento es una parte necesaria e imprescindible de la gestión de activos.
Como se observa en la Figura 1, las distintas fases del KIR se interrelacionan con las diversas herramientas y entornos de gestión. Las líneas terminadas en punta de flecha que se muestran en el diagrama ilustran cómo ocurre esta interacción de manera secuencial.
Recordemos que el KIR, al que de ahora en adelante llamaremos por su verdadero nombre, nació como una estrategia para evidenciar el principal objetivo de implementar la Confiabilidad Operacional: aumentar la disponibilidad de los activos físicos para la producción.

Logremos, entonces, establecer un recorrido por cada una de esas fases, para algunos ejemplos de casos hipotéticos.
CASO 1
En un equipo rotativo, de criticidad operacional alta, con monitoreo continuo de vibraciones, se produce una alarma por alta vibración en el sistema de control. Esto provoca una solicitud por parte del equipo de operaciones a los técnicos o ingenieros que realizan toma y análisis de estos datos, los cuales se presentan a ejecutar el diagnóstico solicitado. Una vez hechas las mediciones, al analizar el espectro, determinan que existe un juego radial mayor al esperado, por lo cual recomiendan reemplazar el cojinete en cuestión. De la misma manera, indican que la máquina puede seguir trabajando, con un monitoreo y análisis más frecuente, de forma de poder preparar el trabajo y hacer una parada ordenada.
Una vez descrito el caso, pasemos a formularnos algunas preguntas:
- La intervención del técnico que acude a realizar la medición y análisis del caso, ¿en qué fase transcurre? ¿En cuál sistema se gestiona?
- El siguiente paso, ¿en qué fase se encuentra y con cuál sistema se gestiona?
- El trabajo de llevar el activo a una condición normal de trabajo, ¿en qué fase ocurre? ¿Con cuál sistema se gestiona?
- Una vez hecho el trabajo, ¿cuál sería el próximo paso y en qué fase ocurre?
- ¿Qué tipos de mantenimiento hemos ejecutado hasta ahora?
- El monitoreo frecuente que se menciona, ¿en qué fase ocurre?
Procedamos, pues, a responder estas preguntas, invitando al análisis de la respuesta.
La intervención del técnico transcurre en la FASE 1: HERRAMIENTAS DE DIAGNÓSTICO APLICADAS EN LA FASE DE OPERACIÓN DEL ACTIVO. Esta estaba muy fácil de responder, pues de hecho, en el enunciado se indicó que haría una “toma y análisis de estos datos” para “ejecutar el diagnóstico solicitado”. Por supuesto, se gestiona en el EAMS. Si el EAMS y el CMMS están realmente integrados, desde el EAMS saldrá la OT para la corrección del defecto. De no estarlo, alguien tendrá que generar dicha orden de forma manual.
Luego de generarse la orden de trabajo, y ser evaluada por el personal técnico para garantizar que el alcance del trabajo que se especificó realmente es el requerido, se inicia la fase de PLANIFICACIÓN DE LA OT. Ya esto responde una parte de la siguiente pregunta: ¿Dónde ocurre el siguiente paso? Este paso, evidentemente, transcurre en la fase 2, “HERRAMIENTAS DE PLANIFICACIÓN PARA KIR,” y por supuesto, debe gestionarse en el CMMS. Esta fase incluye múltiples etapas, como la preparación, asignación de recursos, gestión de ventana operacional y ejecución del trabajo, que finaliza con la adecuada retroalimentación de la OT, este último un paso muy importante de la gestión que con frecuencia no es debidamente potenciado. Pero del flujo de trabajo del mantenimiento nos ocuparemos en una entrega posterior, en la que hablaremos del flujo de trabajo en distintas facetas del mantenimiento.
Pues bien, ya se hizo el diagnóstico, se especificó el trabajo, luego el mismo se planificó adecuadamente y se gestionó la ventana operacional... Nos corresponde ahora proceder a corregir el defecto, y llevar el activo a su condición de operación normal. Se reemplaza, en consecuencia, el cojinete con excesivo juego axial, se miden los cojinetes planos que no se cambiaron, se retroalimenta la orden, y se procede a su cierre. La ejecución del trabajo descrito transcurre en la FASE 3: CORRECCIÓN DEL DESPERFECTO. Y, por supuesto, se gestiona en el CMMS.
Ya se hizo el trabajo. ¿Qué debe ocurrir ahora? Este próximo paso depende en grado sumo de la madurez de la organización. Debería, en esta fase, iniciarse una gestión de pesquisa de fallas para determinar la causa del desgaste inesperado del cojinete. En este caso particular, se podría iniciar un Análisis de Causa Raíz (ACR), que nos ayude a determinar por qué la falla ocurrió, cómo evitamos una nueva ocurrencia y, muy importante, si genera una lección aprendida que nos ayude a prevenir el mismo tipo de falla en otros activos de la misma familia.
Y entonces, ¿qué tipos de mantenimiento hemos hecho hasta acá?
- Al diagnosticar, hemos hecho mantenimiento predictivo, o basado en condición.
- Al corregir un defecto que se ha presentado y hemos podido identificar, estamos haciendo mantenimiento correctivo.
- Dado que pudimos planificar las actividades requeridas, el mantenimiento correctivo realizado es de tipo planificado.
- Si, además de esto, hemos iniciado una pesquisa de fallas, hemos ejecutado mantenimiento proactivo.
Procedamos ahora a responder la última pregunta, la cual citaré textualmente: “El monitoreo frecuente que se menciona, ¿en qué fase ocurre?” Esta respuesta es quizás la más inesperada de todas: En ninguna.
¡Justifique su respuesta! No es necesario hacer un monitoreo y análisis más continuo. Si ya hemos determinado la causa de la alta vibración, tomando en cuenta la dimensión y frecuencia de la señal, y siendo que tenemos un monitoreo continuo con alarmas en el sistema de control, no se justifica que se tome una medida como la mencionada. Que tomes muestras de espectro y analices más a menudo no cambiará el estado. Si lo que necesitas es saber si el problema se está incrementando, en mi experiencia, lo recomendable es realizar un documento de gestión de cambio temporal para incrementar el valor de alarma en tu sistema de gestión de alarmas. Esto permitirá que tu equipo no esté en falla permanente en el sistema, a la vez que te permitirá saber cuándo el problema ha aumentado. Por supuesto, es necesario también garantizar que, una vez resuelto el problema, el valor de set de la alarma sea restituido a su valor original.
Como indiqué en un principio, este caso, acá descrito, es un caso hipotético. Cualquier parecido con la realidad es pura coincidencia.
CASO 2
Partamos del caso 1. Dado que estaremos interviniendo el equipo rotativo en cuestión, se decide adelantar algunos mantenimientos preventivos que estaban previstos para paradas cortas y que fueron debidamente planificados. Una de esas actividades preventivas es el ajuste de las conexiones eléctricas, tanto en la caja de conexiones del motor como en la salida del CCM hacia el motor. Cuando se ejecuta el trabajo, se encuentran conexiones recalentadas a una muy alta temperatura, por lo que se decide reemplazar terminales.¿Respondemos las mismas preguntas? Veamos:
La intervención original, donde se procede a realizar el reajuste de las conexiones, transcurre en la Fase 3. ¡Atención! Esta fase está enunciada como "corrección del desperfecto". Es cierto, al acudir a ejecutar una tarea de mantenimiento preventivo (reajuste de conexiones cada 3000 horas, por ejemplo), en la práctica, no hemos visualizado ningún defecto. Pero, conceptualmente, el mantenimiento preventivo está concebido para corregir un defecto que estadísticamente está por ocurrir o está ocurriendo. Así que sí, es en esta fase que ocurre. Y, por supuesto, se gestiona en el CMMS.
El siguiente paso, en este segundo ejemplo, es la corrección de la falla funcional detectada. Sí, se ha encontrado una falla funcional, que se ha detectado de forma incipiente, pero que está presente de forma indudable. Por supuesto, la ejecución de este trabajo se encuentra también en la Fase 3, “CORRECCIÓN DEL DEFECTO,” y como ya sabemos, se gestiona en el CMMS. Pero... ¡qué cosa con los "peros" en el mantenimiento! Debemos ahora preguntarnos: ¿este trabajo, a todas luces correctivo, debe ejecutarse y documentarse con la misma orden de trabajo? El reemplazo de terminales NO es parte del trabajo preventivo. Por lo tanto, NO debe documentarse con la misma orden. Si nuestro deseo es que el CMMS sea alimentado de forma correcta, este es un trabajo que debe clasificarse como un Mantenimiento Correctivo.
¿Planificado o no planificado? Evidentemente, no es planificado.¿Es un correctivo de emergencia? Evidentemente, no ocasionó paros de equipos, por lo que no es de emergencia.Entonces, ¿qué tipo de mantenimiento correctivo es? Es un mantenimiento correctivo de aprovechamiento (el calificativo es mío, pues nunca he visto este concepto debidamente documentado). Digamos que es de aprovechamiento o de oportunidad, pues es un correctivo que se ejecutó sin parada, y no fue programado ni planificado, sino que es fruto de otro mantenimiento efectuado. Esto debemos documentarlo, pues este tipo de información nos ayuda a demostrar qué actividades de mantenimiento se justifica ejecutar. Esto lleva el activo a operar funcionalmente al 100%, lo cual es de resaltar.
El siguiente paso, una vez ejecutado el trabajo, será nuevamente documentar la ejecución del mismo, cerrar las órdenes de trabajo (tanto la orden de mantenimiento preventivo de reajuste de las conexiones como la de mantenimiento correctivo de reemplazo de terminales) e iniciar una labor de pesquisa para identificar la causa por la cual la conexión se sobrecalentó. Como ya mencionamos, este trabajo inició como un mantenimiento preventivo (ajuste de las conexiones eléctricas cada 3000 horas) y generó un trabajo correctivo de aprovechamiento (reemplazo de las conexiones).
Nuestra próxima columna transcurrirá en el tema de la celebración del “DÍA INTERNACIONAL DE LA SALUD Y SEGURIDAD EN EL TRABAJO.” Como todos sabemos, la SST es algo que nos atañe a todos los que de alguna manera participamos en la cadena de generación de valor del mismo. Este año, el tema de la conmemoración es el cambio climático y cómo este afecta la SST.
Posteriormente, estaremos hablando un poco de los flujos de trabajo requeridos para organizar debidamente la forma en la que la gestión se lleva en el CMMS. Para alimentar, desde ya, esa edición, dejaré una pregunta en el aire: Si, como estrategia al diseñar los planes de mantenimiento centrado en confiabilidad, se decide aplicar “run to failure” a un activo, ¿cómo debe calificarse ese evento cuando ocurre? ¿Es un evento de mantenimiento correctivo? Al levantar mis KPIs, ¿a cuál estrategia de mantenimiento debe sumar? Esta discusión la iniciaremos prontamente en una nueva entrega del Internista de la 21, exclusivamente en Predictiva21.
¡Hasta la próxima entrega!
Normas/Documentos:Familia ISO55000EN 16646
Dinos qué te ha parecido el artículo

Aplicación de un Estudio RAM a un Sistema de Bombeo
Artículo
Resumen
En este trabajo, el autor presenta la aplicación de un Estudio RAM (Reliability, Availability, Maintainability, por sus siglas en inglés) en un sistema de bombeo de condensado instalado en una planta de proceso industrial. Basándose en el pronóstico de los escenarios de fallas, la configuración de los equipos, las políticas de mantenimiento, la filosofía operacional y la confiabilidad de los mismos, se identifican las consecuencias de dichas fallas, así como los subsistemas o componentes de mayor impacto. Esto permite definir acciones que adecúen los eventos no deseados y su impacto a los requerimientos de la organización.
El estudio se enfocó en realizar un diagnóstico de la confiabilidad, disponibilidad, mantenibilidad y el factor de servicio del proceso durante un período representativo en años (correspondiente al tiempo de mantenimiento mayor de los equipos). Se caracterizó el estado actual y futuro basado en los tiempos promedio para fallar (TPPF) y los tiempos promedio para reparar (TPPR).
La organización dispone de bancos de información propia recolectada de manera continua en las bombas. Sin embargo, en muchos casos, la información específica sobre los modos de fallas predominantes puede ser limitada. Por este motivo, se consideró necesario utilizar la opinión de expertos y complementar con información de bases de datos genéricas de fallas y reparaciones, como OREDA, IEEE, PARLOC, WELL MASTER, EXIDA, PHMSA, entre otras.
Palabras clave: Falla, Deterioro, Mejorabilidad, Confiabilidad, Disponibilidad, Ingeniería de Confiabilidad, Mantenibilidad, Simulación de Monte Carlo.
1.- Introducción
En los últimos años, las industrias han orientado sus esfuerzos hacia la maximización de sus ganancias, utilizando diversos enfoques que faciliten la toma de decisiones para realizar inversiones acertadas y de alta rentabilidad. Ejemplos de estos enfoques incluyen fusiones entre grandes corporaciones, estilos de gestión como la Gerencia Integral de Activos y la cuantificación del riesgo para evaluar escenarios. Todas estas estrategias tienen como objetivo, de manera implícita o explícita, optimizar la inversión de millones de dólares para reducir costos y aumentar los márgenes de ganancias.
La toma de decisiones sobre inversiones de capital es un aspecto crucial para cualquier gerencia, ya que la mayoría de las situaciones o escenarios suelen basarse en datos con poca certidumbre. Esto puede llevar a destinar los recursos financieros hacia oportunidades de menor valor para el negocio.
El análisis RAM (Reliability, Availability, Maintainability) permite pronosticar, para un período determinado, la disponibilidad y el factor de producción diferida de un sistema o proceso de producción. Este análisis se basa en la configuración del sistema, la confiabilidad de sus componentes, la filosofía de operación y mantenimiento, y, fundamentalmente, en los tiempos promedio para fallar (TPPF) y los tiempos promedio para reparar (TPPR) de los diversos componentes. Para ello, se utiliza información proveniente de bases de datos propias, bases genéricas de la industria y la opinión de expertos. El equipo de trabajo establece las premisas relacionadas con la confiabilidad de los equipos, considerando todas las fuentes posibles para conformar una base de datos que permita obtener las mejores estimaciones de los TPPF y TPPR.
El análisis RAM también facilita la realización de sensibilidades entre la capacidad instalada y la requerida, la modificación de planes de mantenimiento, y la identificación de diferencias respecto a una condición específica. Esto permite planificar opciones de redimensionamiento y generar planes de acción que cumplan con los compromisos de producción y seguridad exigidos.
Tal como se ilustra en la Figura 1, el análisis RAM comienza con la estimación de las tasas de falla y reparación de cada uno de los componentes o equipos que conforman los sistemas analizados. Esta estimación mejorada de las tasas de falla alimenta un modelo de Diagramas de Bloques de Confiabilidad (RBD), que representa la arquitectura del sistema y su filosofía de operación. Este modelo está soportado por una simulación que considera la configuración de los equipos, fallas aleatorias, reparaciones, mantenimiento planificado, así como paradas parciales y totales de los componentes del sistema.

Durante la ejecución de un estudio RAM, se lleva a cabo una adecuada caracterización probabilística de los procesos de deterioro que afectan los equipos, subsistemas y sistemas asociados al proceso de producción. Esto permite pronosticar la mayoría de los escenarios de paros o fallas. El objetivo principal de un estudio RAM es estimar la producción diferida de un sistema productivo. Una vez realizada la simulación, es posible determinar la disponibilidad promedio del sistema y, como complemento, su indisponibilidad.
Adicionalmente, con los resultados obtenidos, se pueden identificar acciones para minimizar la ocurrencia de estos escenarios y analizar sus implicaciones al compararlos con un escenario basado en las "Buenas Prácticas", tal como lo establece el estándar ISO 55001 en sus requerimientos. Esto contribuye al establecimiento de estrategias óptimas de mantenimiento, orientadas a gestionar el negocio de manera optimizada.
2.- Marco Conceptual
2.1 Confiabilidad
La confiabilidad se define como la probabilidad de que un sistema o equipo opere sin fallar durante un período de tiempo determinado, bajo condiciones operacionales específicas y constantes, tales como presión, temperatura, caudal, densidad o pH. Dado que la función de confiabilidad depende del tiempo, esta disminuye a medida que aumenta su complemento, es decir, la probabilidad de falla.

Esta ecuación refleja la relación inversamente proporcional entre la confiabilidad y la tasa de falla: a medida que la confiabilidad disminuye, la tasa de falla aumenta. Además, muestra que la confiabilidad es una función acumulativa inversa del tiempo hasta la falla, ya que expresa la probabilidad de que el tiempo de falla (t) sea mayor o igual al tiempo misión (tm).
Para estudiar esta probabilidad, se recopilan datos y parámetros que afectan directamente la confiabilidad. Entre estos parámetros se encuentran el ambiente, la temperatura, las presiones y otros factores que influyen en el sistema. Sin embargo, la teoría de confiabilidad, utilizada como herramienta para optimizar el desempeño de los activos, se enfoca principalmente en las fallas de los sistemas. Aunque no profundiza en los fenómenos que las originan, se centra en la frecuencia con la que ocurren. No se trata de una teoría física de las fallas, sino de una teoría estadística.
Por este motivo, los datos empleados en el análisis son principalmente los relacionados con los "tiempos" del activo, ya que estos representan información concreta y con menor incertidumbre, siendo fundamentales para el estudio de la confiabilidad.
2.2 Datos Censurados a la Izquierda
Los datos censurados a la izquierda corresponden a situaciones en las que un ítem se encuentra en estado de falla solo después de un cierto período de tiempo, pero el momento exacto en el que ocurrió la falla es desconocido. Es decir, no se sabe cuándo falló exactamente, solo que la falla ocurrió en algún punto anterior al momento en que fue detectada.

2.3 Datos Censurados a la Derecha
Si nosotros ensayamos cinco ítems, pero solo tres fallan, en este caso nuestros datos están compuestos por tres ítems que fallaron, es decir, ítems de los que conocemos los tiempos hasta la falla, y dos ítems que no fallaron, que se consideran como datos censurados. Este es el tipo más común de datos censurados. Incluir datos censurados en un análisis de datos es conveniente porque hace menos pesimista el estudio de confiabilidad.

2.4 Disponibilidad
La disponibilidad es un término probabilístico exclusivo de los “equipos reparables” que se define como la probabilidad de que el equipo esté operando (es decir, que no esté en reparación) en un tiempo “t”. Para estimar la disponibilidad se requiere estimar la “tasa de falla λ(t)” y la “tasa de reparación µ(t)”; es decir, se requiere analizar estadísticamente los tiempos hasta la falla y los tiempos en reparación para un periodo de tiempo “t”.

2.4.1 Disponibilidad Inherente
La Disponibilidad Inherente representa el porcentaje del tiempo que un equipo está en condiciones de operar durante un periodo de análisis, teniendo en cuenta solo los paros no programados. El objetivo de este indicador es medir la disponibilidad inherente de los equipos, con la finalidad de incrementarla, ya que en la medida que esto ocurra, significara que se disminuye el tiempo de los paros por falla o paros no programados del equipo.

Donde:
MTTF: Tiempo Medio para la Falla
MTTR: Tiempo Medio para Reparar
2.4.2 Disponibilidad Alcanzada
La disponibilidad alcanzada representa el porcentaje de tiempo que el equipo estuvo disponible para el área de operación y pudo desempeñar su función durante un periodo de análisis. Esto toma en cuenta el tiempo que el equipo estuvo fuera de operación, tanto por paros programados como no programados. El objetivo de este indicador es medir el desempeño de los equipos y la eficiencia en la gestión de mantenimiento, comparándolos con los objetivos y metas del negocio. Esto tiene como finalidad que la operación disponga de más tiempo con el equipo disponible y que este pueda cumplir con la función para la que fue diseñado.

Donde:
MTBM: Tiempo Medio entre Mantenimiento, tanto correctivas como preventivas
M=MDT: Tiempo Medio Abajo, incluye MTTR más tiempo fuera de control
2.4.3 Disponibilidad Operacional
La disponibilidad operacional incluye todos los tipos de paradas: administrativas, atrasos logísticos, entre otras. Es la disponibilidad más perceptible para el usuario o dueño del activo. En muchos casos, no es fácil controlarla. Esta disponibilidad es la más utilizada o calculada por las diferentes organizaciones para mostrar su desempeño durante el periodo de análisis y ayudar en la toma de decisiones, con el fin de direccionar los recursos y esfuerzos disponibles a las verdaderas oportunidades para mejorar el desempeño de los activos físicos.

Un ejemplo de la aplicación de la ecuación de la disponibilidad operacional sería si disponemos de un tiempo total del ciclo de operación para un año de 8,760 horas y el tiempo de operación fue de 7,000 horas debido a los paros programados y no programados. En un estudio RAM, esta disponibilidad es muy utilizada debido a la información valiosa que muestra en cada corrida de la simulación.
2.5 Mantenibilidad
La mantenibilidad trata sobre la duración de paros por fallas y paros por mantenimiento, o cuánto tiempo toma lograr (facilidad y velocidad) restituir las condiciones del equipo a su condición operativa después de una parada por falla o para realizar una actividad planificada.
Las características de mantenibilidad son normalmente determinadas por el diseño del equipo, el cual especifica los procedimientos de mantenimiento y determina la duración de los tiempos de reparación.
La figura clave de mérito para la mantenibilidad es, a menudo, el tiempo promedio para reparar (TPPR). Cualitativamente se refiere a la facilidad con que el equipo se restaura a un estado funcional. Cuantitativamente se define como la probabilidad de restaurar la condición operativa del equipo en un período de tiempo o tiempo misión. Se expresa a menudo como:

Donde µ= Tasa de Reparación
Esta ecuación es valida para tiempos para reparar que sigan la distribución exponencial.
2.6 Diagrama de Bloques de Confiabilidad
Los diagramas de bloques de confiabilidad, DBC (RBD, por sus siglas en inglés), ilustran la funcionalidad de un sistema. La confiabilidad es la probabilidad de operación exitosa durante un intervalo de tiempo dado. En un diagrama de bloques se considera que cada elemento funciona (opera exitosamente) o falla independientemente de los otros. En un RBD, cada componente debe ser caracterizado probabilísticamente. Podemos tener tres tipos de arreglos en un sistema:
- Sistemas en Serie
- Sistemas en Paralelo
- Sistemas "k" de "n"
2.7 Sistemas en Serie
Si un sistema funciona si y solo si todos sus componentes funcionan, se dice que el sistema tiene una estructura en serie. Desde el punto de vista de confiabilidad, un sistema en serie es definido como aquel sistema en el que todos sus componentes deben operar para que el sistema en su totalidad opere. La confiabilidad del sistema es menor que la de la menor confiabilidad de los elementos del sistema.

2.8 Sistemas en Paralelo
Un sistema que funciona si al menos uno de sus componentes está funcionando se dice que tiene una estructura en paralelo. Desde el punto de vista de confiabilidad, un sistema en paralelo se define como aquel sistema en el que todos sus componentes deben fallar para que el sistema en su totalidad no opere.

2.9 Sistemas “k” de “n”
Algunos esquemas de redundancia contemplan el uso de un número de componentes o equipos mayor que el requerido, a fin de poder establecer esquemas de votación que permitan incrementar la confiabilidad global del sistema. La siguiente gráfica muestra la matemática que corresponde a un sistema con redundancia o respaldo a través de la distribución binomial.
De igual manera, se muestra una gráfica con la relación de la confiabilidad en función de la cantidad de equipos o componentes en operación, lo que demuestra que, a medida que se colocan más equipos en operación, la confiabilidad del sistema se hace vulnerable y se comporta como un sistema en serie, donde si falla uno, se afecta la producción del proceso productivo de manera correspondiente al porcentaje que contribuya en el sistema.


2.10 Simulación de Monte Carlo
En este trabajo se utilizó la simulación con el método de Monte Carlo para estimar la confiabilidad, disponibilidad y mantenibilidad de los equipos dinámicos del sistema de bombeo de condensado. El método de Monte Carlo es una técnica que involucra el uso de números aleatorios y probabilidad para resolver problemas complejos, ya que el sistema es muestreado en un número de configuraciones aleatorias, y los datos pueden ser usados para describir el sistema como un todo. Por sus propiedades, la simulación de Monte Carlo es el método prominente para la solución de problemas dinámicos de confiabilidad, disponibilidad y mantenibilidad de sistemas industriales.
Así, dados los desarrollos actuales en software y hardware, la simulación de Monte Carlo es una técnica poderosa para desarrollar análisis de confiabilidad-disponibilidad-mantenibilidad de sistemas industriales que están muy apegados a la realidad de los sistemas complejos. A través de esta simulación se generan números aleatorios que permiten realizar diferentes escenarios para tomar decisiones acertadas respecto a la dirección de los recursos financieros de la organización, disminuyendo en lo posible el impacto total al negocio.
3. Procedimiento de Trabajo
La metodología se concentra en utilizar los principios de Ingeniería de Confiabilidad e Ingeniería de Mantenimiento para estimar el valor esperado de confiabilidad, disponibilidad y mantenibilidad de sistemas industriales. El arreglo matemático para las simulaciones y el cálculo de los parámetros se enfoca inicialmente en los componentes principales del sistema, fundamentalmente en los equipos rotativos y estacionarios, manejando a discreción los componentes de electricidad, instrumentación y control. A continuación, se describen algunos de los aspectos fundamentales requeridos para un estudio RAM:
- Diagramas de flujo de proceso y diagramas de tuberías e instrumentación de las instalaciones de superficie.
- Bases de datos propias disponibles que contengan tasas de fallas y tiempos de reparación de los equipos que conforman el sistema (bombas, separadores, líneas de flujo, líneas de gas, compresores, tanques, válvulas, instrumentos, generadores, pozos, etc.).
- Descripción de la filosofía de operaciones del campo o planta.
- Plan de mantenimiento de las instalaciones.
- Simulación del fluido de proceso, con la finalidad de conocer el impacto en la producción en caso de ocurrir una falla en cualquier elemento o equipo del sistema.
- Entrevistas con el personal de operaciones, mantenimiento, optimización de producción, ingenieros de producción y planificadores (durante el desarrollo del proyecto).
Estas son las fases en las cuales se debe desarrollar un estudio RAM:
- Evaluación general del sistema.
- Diseño del arreglo físico del sistema.
- Revisión de referencias internacionales y/o históricos reales del sistema.
- Estimación de la confiabilidad, disponibilidad y mantenibilidad del sistema.
- Estimación de la capacidad efectiva del sistema.
- Conclusiones y recomendaciones.

4. Caso de Estudio
En el siguiente caso de estudio se dispone de los datos propios de los activos físicos que conforman el sistema, los cuales fueron complementados con datos genéricos del comportamiento típico de los equipos, basados en información tomada de fuentes como OREDA, Reliability Handbook, entre otros. Se generaron datos aleatorios tanto para los tiempos para falla (TPF) como para los tiempos para reparar (TPR), con los cuales se estimaron la disponibilidad y confiabilidad de cada uno de los equipos principales que conforman el sistema de bombeo.
En la siguiente imagen se muestran los resultados de la caracterización probabilística y el respectivo análisis de datos a través del uso de la herramienta computacional ADA-CONFIABILIDAD para una de las bombas del sistema. Estos datos, luego de ser tratados probabilísticamente, permitieron, mediante las expresiones matemáticas explicadas en el marco conceptual, estimar la disponibilidad, confiabilidad y mantenibilidad esperadas de cada equipo del sistema.

Como se puede observar en la ilustración anterior, de acuerdo con la caracterización probabilística, el mejor ajuste lo realiza la distribución de Weibull. Sin embargo, la herramienta, de manera simultánea, compara la distribución de Weibull con las distribuciones Exponencial, Normal, Lognormal y Gamma, en base al valor del test y el respectivo valor crítico para cada nivel de significancia. Para un tiempo misión de 100 horas, se estima que la confiabilidad sea igual al 87.06%, y los parámetros de Weibull son: Eta = 595 horas y Beta = 1.11. Esto indica que el equipo se encuentra en la etapa de desgaste, de acuerdo con un patrón de falla característico, lo cual sirve como apoyo para la toma de decisiones.

En la figura 4 se puede observar que el coeficiente de correlación R2=0.97 corrobora el buen ajuste de la distribución de Weibull. En la figura 5, se muestra el diagrama de bloques de confiabilidad (RBD) elaborado en el software RAPTOR 7, donde se aprecia la relación entre los diferentes componentes que conforman el sistema de bombeo, tales como bombas, válvulas y filtros.

En la tabla 1 se muestran los resultados obtenidos de la simulación, distribuidos mediante el uso del software RAPTOR 7. Lo recomendable es seleccionar el valor promedio de la disponibilidad, el cual nos ayudará a estimar la producción diferida del sistema de bombeo. De igual manera, se presentan los valores distribuidos de la confiabilidad y el número esperado de fallas. Esta simulación debe realizarse para diferentes tiempos de misión.

En la tabla 2 se muestran los resultados de la disponibilidad por año para el sistema de bombeo analizado. Además, se estima la pérdida anual de la producción del sistema, información que puede ayudar a la alta dirección a tomar decisiones para evitar la pérdida o el no aprovechamiento de esta cantidad de unidades. Este análisis tiene como objetivo principal anticiparse a las posibles fallas, estableciendo planes de acción que minimicen al máximo el impacto total al negocio y, de esta manera, contribuyan a mejorar la rentabilidad de la organización. El análisis se realiza considerando la capacidad instalada del sistema.

5. Conclusiones
- En el pronóstico de comportamiento de la capacidad efectiva de un proceso productivo, la indisponibilidad operacional por mantenimiento planeado y la indisponibilidad operacional por fallas deben ser analizadas tanto de forma independiente como en conjunto, con la finalidad de diagnosticar y predecir estrategias que aseguren el cumplimiento de la producción.
- El efecto del plan de mantenimiento preventivo y correctivo sobre la capacidad efectiva del sistema evidencia la necesidad de realizar análisis de mantenibilidad en los sistemas y subsistemas, en la búsqueda por disminuir los tiempos de parada por mantenimiento.
- El Análisis de Confiabilidad, Disponibilidad y Mantenibilidad (RAM) permite pronosticar el impacto en la disponibilidad y la producción diferida mediante una simulación "what if" de las siguientes variables:
- Nuevas políticas de mantenimiento.
- Aplicación de nuevas tecnologías.
- Cambios en la mantenibilidad de los equipos.
- Modificaciones en la configuración de los procesos de producción.
- Cambios en la política de inventarios.
- Implantación de nuevos métodos de producción.
6. Referencia
- Mohammad Modarres, Mark P. Kaminskry, Vasily Krivtsov, 2017: Reliability Engineering and Risk Analysis: A Practical Guide, Third Edition.
- Blas Galván y Ernesto Primera, 2017: Estudios e Ingeniería RAM, MRI Institute.
- Andrew K.S. Jardine and Albert H. C. Tsang, 2014: Maintenance, Replacement, and Reliability (Theory and Applications), Second Edition, CRC Press.
- Edgar Fuenmayor, 2014: Análisis de Confiabilidad, Disponibilidad y Mantenibilidad de un Sistema de Bombeo, PMM Project Magazine Vol 29, ISSN 1887-018X.
- D.T. O’Connor, Andre Kleyner, 2012: Practical Reliability Engineering, Fifth Edition.
- R2M - Reliability and Risk Management Mexico S.A. de C.V., 2010: Confiabilidad Integral: Sinergias de Disciplinas Tomo I, II, III.
- ReliaSoft RS403, 2008: Confiabilidad de Sistemas, Master the Subject Seminar Series.
- ReliaSoft RS401, 2008: Análisis de Datos de Vida, Master the Subject Seminar Series.
- Medardo Yáñez, Hernando Gómez de la Vega, Genebelin Valbuena, 2004: Ingeniería de Confiabilidad y Análisis Probabilístico de Riesgo, Venezuela, R2M.
Dinos qué te ha parecido el artículo
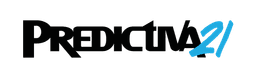

Resumen
En este trabajo, el autor presenta la aplicación de un Estudio RAM (Reliability, Availability, Maintainability, por sus siglas en inglés) en un sistema de bombeo de condensado instalado en una planta de proceso industrial. Basándose en el pronóstico de los escenarios de fallas, la configuración de los equipos, las políticas de mantenimiento, la filosofía operacional y la confiabilidad de los mismos, se identifican las consecuencias de dichas fallas, así como los subsistemas o componentes de mayor impacto. Esto permite definir acciones que adecúen los eventos no deseados y su impacto a los requerimientos de la organización.
El estudio se enfocó en realizar un diagnóstico de la confiabilidad, disponibilidad, mantenibilidad y el factor de servicio del proceso durante un período representativo en años (correspondiente al tiempo de mantenimiento mayor de los equipos). Se caracterizó el estado actual y futuro basado en los tiempos promedio para fallar (TPPF) y los tiempos promedio para reparar (TPPR).
La organización dispone de bancos de información propia recolectada de manera continua en las bombas. Sin embargo, en muchos casos, la información específica sobre los modos de fallas predominantes puede ser limitada. Por este motivo, se consideró necesario utilizar la opinión de expertos y complementar con información de bases de datos genéricas de fallas y reparaciones, como OREDA, IEEE, PARLOC, WELL MASTER, EXIDA, PHMSA, entre otras.
Palabras clave: Falla, Deterioro, Mejorabilidad, Confiabilidad, Disponibilidad, Ingeniería de Confiabilidad, Mantenibilidad, Simulación de Monte Carlo.
1.- Introducción
En los últimos años, las industrias han orientado sus esfuerzos hacia la maximización de sus ganancias, utilizando diversos enfoques que faciliten la toma de decisiones para realizar inversiones acertadas y de alta rentabilidad. Ejemplos de estos enfoques incluyen fusiones entre grandes corporaciones, estilos de gestión como la Gerencia Integral de Activos y la cuantificación del riesgo para evaluar escenarios. Todas estas estrategias tienen como objetivo, de manera implícita o explícita, optimizar la inversión de millones de dólares para reducir costos y aumentar los márgenes de ganancias.
La toma de decisiones sobre inversiones de capital es un aspecto crucial para cualquier gerencia, ya que la mayoría de las situaciones o escenarios suelen basarse en datos con poca certidumbre. Esto puede llevar a destinar los recursos financieros hacia oportunidades de menor valor para el negocio.
El análisis RAM (Reliability, Availability, Maintainability) permite pronosticar, para un período determinado, la disponibilidad y el factor de producción diferida de un sistema o proceso de producción. Este análisis se basa en la configuración del sistema, la confiabilidad de sus componentes, la filosofía de operación y mantenimiento, y, fundamentalmente, en los tiempos promedio para fallar (TPPF) y los tiempos promedio para reparar (TPPR) de los diversos componentes. Para ello, se utiliza información proveniente de bases de datos propias, bases genéricas de la industria y la opinión de expertos. El equipo de trabajo establece las premisas relacionadas con la confiabilidad de los equipos, considerando todas las fuentes posibles para conformar una base de datos que permita obtener las mejores estimaciones de los TPPF y TPPR.
El análisis RAM también facilita la realización de sensibilidades entre la capacidad instalada y la requerida, la modificación de planes de mantenimiento, y la identificación de diferencias respecto a una condición específica. Esto permite planificar opciones de redimensionamiento y generar planes de acción que cumplan con los compromisos de producción y seguridad exigidos.
Tal como se ilustra en la Figura 1, el análisis RAM comienza con la estimación de las tasas de falla y reparación de cada uno de los componentes o equipos que conforman los sistemas analizados. Esta estimación mejorada de las tasas de falla alimenta un modelo de Diagramas de Bloques de Confiabilidad (RBD), que representa la arquitectura del sistema y su filosofía de operación. Este modelo está soportado por una simulación que considera la configuración de los equipos, fallas aleatorias, reparaciones, mantenimiento planificado, así como paradas parciales y totales de los componentes del sistema.

Durante la ejecución de un estudio RAM, se lleva a cabo una adecuada caracterización probabilística de los procesos de deterioro que afectan los equipos, subsistemas y sistemas asociados al proceso de producción. Esto permite pronosticar la mayoría de los escenarios de paros o fallas. El objetivo principal de un estudio RAM es estimar la producción diferida de un sistema productivo. Una vez realizada la simulación, es posible determinar la disponibilidad promedio del sistema y, como complemento, su indisponibilidad.
Adicionalmente, con los resultados obtenidos, se pueden identificar acciones para minimizar la ocurrencia de estos escenarios y analizar sus implicaciones al compararlos con un escenario basado en las "Buenas Prácticas", tal como lo establece el estándar ISO 55001 en sus requerimientos. Esto contribuye al establecimiento de estrategias óptimas de mantenimiento, orientadas a gestionar el negocio de manera optimizada.
2.- Marco Conceptual
2.1 Confiabilidad
La confiabilidad se define como la probabilidad de que un sistema o equipo opere sin fallar durante un período de tiempo determinado, bajo condiciones operacionales específicas y constantes, tales como presión, temperatura, caudal, densidad o pH. Dado que la función de confiabilidad depende del tiempo, esta disminuye a medida que aumenta su complemento, es decir, la probabilidad de falla.

Esta ecuación refleja la relación inversamente proporcional entre la confiabilidad y la tasa de falla: a medida que la confiabilidad disminuye, la tasa de falla aumenta. Además, muestra que la confiabilidad es una función acumulativa inversa del tiempo hasta la falla, ya que expresa la probabilidad de que el tiempo de falla (t) sea mayor o igual al tiempo misión (tm).
Para estudiar esta probabilidad, se recopilan datos y parámetros que afectan directamente la confiabilidad. Entre estos parámetros se encuentran el ambiente, la temperatura, las presiones y otros factores que influyen en el sistema. Sin embargo, la teoría de confiabilidad, utilizada como herramienta para optimizar el desempeño de los activos, se enfoca principalmente en las fallas de los sistemas. Aunque no profundiza en los fenómenos que las originan, se centra en la frecuencia con la que ocurren. No se trata de una teoría física de las fallas, sino de una teoría estadística.
Por este motivo, los datos empleados en el análisis son principalmente los relacionados con los "tiempos" del activo, ya que estos representan información concreta y con menor incertidumbre, siendo fundamentales para el estudio de la confiabilidad.
2.2 Datos Censurados a la Izquierda
Los datos censurados a la izquierda corresponden a situaciones en las que un ítem se encuentra en estado de falla solo después de un cierto período de tiempo, pero el momento exacto en el que ocurrió la falla es desconocido. Es decir, no se sabe cuándo falló exactamente, solo que la falla ocurrió en algún punto anterior al momento en que fue detectada.

2.3 Datos Censurados a la Derecha
Si nosotros ensayamos cinco ítems, pero solo tres fallan, en este caso nuestros datos están compuestos por tres ítems que fallaron, es decir, ítems de los que conocemos los tiempos hasta la falla, y dos ítems que no fallaron, que se consideran como datos censurados. Este es el tipo más común de datos censurados. Incluir datos censurados en un análisis de datos es conveniente porque hace menos pesimista el estudio de confiabilidad.

2.4 Disponibilidad
La disponibilidad es un término probabilístico exclusivo de los “equipos reparables” que se define como la probabilidad de que el equipo esté operando (es decir, que no esté en reparación) en un tiempo “t”. Para estimar la disponibilidad se requiere estimar la “tasa de falla λ(t)” y la “tasa de reparación µ(t)”; es decir, se requiere analizar estadísticamente los tiempos hasta la falla y los tiempos en reparación para un periodo de tiempo “t”.

2.4.1 Disponibilidad Inherente
La Disponibilidad Inherente representa el porcentaje del tiempo que un equipo está en condiciones de operar durante un periodo de análisis, teniendo en cuenta solo los paros no programados. El objetivo de este indicador es medir la disponibilidad inherente de los equipos, con la finalidad de incrementarla, ya que en la medida que esto ocurra, significara que se disminuye el tiempo de los paros por falla o paros no programados del equipo.

Donde:
MTTF: Tiempo Medio para la Falla
MTTR: Tiempo Medio para Reparar
2.4.2 Disponibilidad Alcanzada
La disponibilidad alcanzada representa el porcentaje de tiempo que el equipo estuvo disponible para el área de operación y pudo desempeñar su función durante un periodo de análisis. Esto toma en cuenta el tiempo que el equipo estuvo fuera de operación, tanto por paros programados como no programados. El objetivo de este indicador es medir el desempeño de los equipos y la eficiencia en la gestión de mantenimiento, comparándolos con los objetivos y metas del negocio. Esto tiene como finalidad que la operación disponga de más tiempo con el equipo disponible y que este pueda cumplir con la función para la que fue diseñado.

Donde:
MTBM: Tiempo Medio entre Mantenimiento, tanto correctivas como preventivas
M=MDT: Tiempo Medio Abajo, incluye MTTR más tiempo fuera de control
2.4.3 Disponibilidad Operacional
La disponibilidad operacional incluye todos los tipos de paradas: administrativas, atrasos logísticos, entre otras. Es la disponibilidad más perceptible para el usuario o dueño del activo. En muchos casos, no es fácil controlarla. Esta disponibilidad es la más utilizada o calculada por las diferentes organizaciones para mostrar su desempeño durante el periodo de análisis y ayudar en la toma de decisiones, con el fin de direccionar los recursos y esfuerzos disponibles a las verdaderas oportunidades para mejorar el desempeño de los activos físicos.

Un ejemplo de la aplicación de la ecuación de la disponibilidad operacional sería si disponemos de un tiempo total del ciclo de operación para un año de 8,760 horas y el tiempo de operación fue de 7,000 horas debido a los paros programados y no programados. En un estudio RAM, esta disponibilidad es muy utilizada debido a la información valiosa que muestra en cada corrida de la simulación.
2.5 Mantenibilidad
La mantenibilidad trata sobre la duración de paros por fallas y paros por mantenimiento, o cuánto tiempo toma lograr (facilidad y velocidad) restituir las condiciones del equipo a su condición operativa después de una parada por falla o para realizar una actividad planificada.
Las características de mantenibilidad son normalmente determinadas por el diseño del equipo, el cual especifica los procedimientos de mantenimiento y determina la duración de los tiempos de reparación.
La figura clave de mérito para la mantenibilidad es, a menudo, el tiempo promedio para reparar (TPPR). Cualitativamente se refiere a la facilidad con que el equipo se restaura a un estado funcional. Cuantitativamente se define como la probabilidad de restaurar la condición operativa del equipo en un período de tiempo o tiempo misión. Se expresa a menudo como:

Donde µ= Tasa de Reparación
Esta ecuación es valida para tiempos para reparar que sigan la distribución exponencial.
2.6 Diagrama de Bloques de Confiabilidad
Los diagramas de bloques de confiabilidad, DBC (RBD, por sus siglas en inglés), ilustran la funcionalidad de un sistema. La confiabilidad es la probabilidad de operación exitosa durante un intervalo de tiempo dado. En un diagrama de bloques se considera que cada elemento funciona (opera exitosamente) o falla independientemente de los otros. En un RBD, cada componente debe ser caracterizado probabilísticamente. Podemos tener tres tipos de arreglos en un sistema:
- Sistemas en Serie
- Sistemas en Paralelo
- Sistemas "k" de "n"
2.7 Sistemas en Serie
Si un sistema funciona si y solo si todos sus componentes funcionan, se dice que el sistema tiene una estructura en serie. Desde el punto de vista de confiabilidad, un sistema en serie es definido como aquel sistema en el que todos sus componentes deben operar para que el sistema en su totalidad opere. La confiabilidad del sistema es menor que la de la menor confiabilidad de los elementos del sistema.

2.8 Sistemas en Paralelo
Un sistema que funciona si al menos uno de sus componentes está funcionando se dice que tiene una estructura en paralelo. Desde el punto de vista de confiabilidad, un sistema en paralelo se define como aquel sistema en el que todos sus componentes deben fallar para que el sistema en su totalidad no opere.

2.9 Sistemas “k” de “n”
Algunos esquemas de redundancia contemplan el uso de un número de componentes o equipos mayor que el requerido, a fin de poder establecer esquemas de votación que permitan incrementar la confiabilidad global del sistema. La siguiente gráfica muestra la matemática que corresponde a un sistema con redundancia o respaldo a través de la distribución binomial.
De igual manera, se muestra una gráfica con la relación de la confiabilidad en función de la cantidad de equipos o componentes en operación, lo que demuestra que, a medida que se colocan más equipos en operación, la confiabilidad del sistema se hace vulnerable y se comporta como un sistema en serie, donde si falla uno, se afecta la producción del proceso productivo de manera correspondiente al porcentaje que contribuya en el sistema.


2.10 Simulación de Monte Carlo
En este trabajo se utilizó la simulación con el método de Monte Carlo para estimar la confiabilidad, disponibilidad y mantenibilidad de los equipos dinámicos del sistema de bombeo de condensado. El método de Monte Carlo es una técnica que involucra el uso de números aleatorios y probabilidad para resolver problemas complejos, ya que el sistema es muestreado en un número de configuraciones aleatorias, y los datos pueden ser usados para describir el sistema como un todo. Por sus propiedades, la simulación de Monte Carlo es el método prominente para la solución de problemas dinámicos de confiabilidad, disponibilidad y mantenibilidad de sistemas industriales.
Así, dados los desarrollos actuales en software y hardware, la simulación de Monte Carlo es una técnica poderosa para desarrollar análisis de confiabilidad-disponibilidad-mantenibilidad de sistemas industriales que están muy apegados a la realidad de los sistemas complejos. A través de esta simulación se generan números aleatorios que permiten realizar diferentes escenarios para tomar decisiones acertadas respecto a la dirección de los recursos financieros de la organización, disminuyendo en lo posible el impacto total al negocio.
3. Procedimiento de Trabajo
La metodología se concentra en utilizar los principios de Ingeniería de Confiabilidad e Ingeniería de Mantenimiento para estimar el valor esperado de confiabilidad, disponibilidad y mantenibilidad de sistemas industriales. El arreglo matemático para las simulaciones y el cálculo de los parámetros se enfoca inicialmente en los componentes principales del sistema, fundamentalmente en los equipos rotativos y estacionarios, manejando a discreción los componentes de electricidad, instrumentación y control. A continuación, se describen algunos de los aspectos fundamentales requeridos para un estudio RAM:
- Diagramas de flujo de proceso y diagramas de tuberías e instrumentación de las instalaciones de superficie.
- Bases de datos propias disponibles que contengan tasas de fallas y tiempos de reparación de los equipos que conforman el sistema (bombas, separadores, líneas de flujo, líneas de gas, compresores, tanques, válvulas, instrumentos, generadores, pozos, etc.).
- Descripción de la filosofía de operaciones del campo o planta.
- Plan de mantenimiento de las instalaciones.
- Simulación del fluido de proceso, con la finalidad de conocer el impacto en la producción en caso de ocurrir una falla en cualquier elemento o equipo del sistema.
- Entrevistas con el personal de operaciones, mantenimiento, optimización de producción, ingenieros de producción y planificadores (durante el desarrollo del proyecto).
Estas son las fases en las cuales se debe desarrollar un estudio RAM:
- Evaluación general del sistema.
- Diseño del arreglo físico del sistema.
- Revisión de referencias internacionales y/o históricos reales del sistema.
- Estimación de la confiabilidad, disponibilidad y mantenibilidad del sistema.
- Estimación de la capacidad efectiva del sistema.
- Conclusiones y recomendaciones.

4. Caso de Estudio
En el siguiente caso de estudio se dispone de los datos propios de los activos físicos que conforman el sistema, los cuales fueron complementados con datos genéricos del comportamiento típico de los equipos, basados en información tomada de fuentes como OREDA, Reliability Handbook, entre otros. Se generaron datos aleatorios tanto para los tiempos para falla (TPF) como para los tiempos para reparar (TPR), con los cuales se estimaron la disponibilidad y confiabilidad de cada uno de los equipos principales que conforman el sistema de bombeo.
En la siguiente imagen se muestran los resultados de la caracterización probabilística y el respectivo análisis de datos a través del uso de la herramienta computacional ADA-CONFIABILIDAD para una de las bombas del sistema. Estos datos, luego de ser tratados probabilísticamente, permitieron, mediante las expresiones matemáticas explicadas en el marco conceptual, estimar la disponibilidad, confiabilidad y mantenibilidad esperadas de cada equipo del sistema.

Como se puede observar en la ilustración anterior, de acuerdo con la caracterización probabilística, el mejor ajuste lo realiza la distribución de Weibull. Sin embargo, la herramienta, de manera simultánea, compara la distribución de Weibull con las distribuciones Exponencial, Normal, Lognormal y Gamma, en base al valor del test y el respectivo valor crítico para cada nivel de significancia. Para un tiempo misión de 100 horas, se estima que la confiabilidad sea igual al 87.06%, y los parámetros de Weibull son: Eta = 595 horas y Beta = 1.11. Esto indica que el equipo se encuentra en la etapa de desgaste, de acuerdo con un patrón de falla característico, lo cual sirve como apoyo para la toma de decisiones.

En la figura 4 se puede observar que el coeficiente de correlación R2=0.97 corrobora el buen ajuste de la distribución de Weibull. En la figura 5, se muestra el diagrama de bloques de confiabilidad (RBD) elaborado en el software RAPTOR 7, donde se aprecia la relación entre los diferentes componentes que conforman el sistema de bombeo, tales como bombas, válvulas y filtros.

En la tabla 1 se muestran los resultados obtenidos de la simulación, distribuidos mediante el uso del software RAPTOR 7. Lo recomendable es seleccionar el valor promedio de la disponibilidad, el cual nos ayudará a estimar la producción diferida del sistema de bombeo. De igual manera, se presentan los valores distribuidos de la confiabilidad y el número esperado de fallas. Esta simulación debe realizarse para diferentes tiempos de misión.

En la tabla 2 se muestran los resultados de la disponibilidad por año para el sistema de bombeo analizado. Además, se estima la pérdida anual de la producción del sistema, información que puede ayudar a la alta dirección a tomar decisiones para evitar la pérdida o el no aprovechamiento de esta cantidad de unidades. Este análisis tiene como objetivo principal anticiparse a las posibles fallas, estableciendo planes de acción que minimicen al máximo el impacto total al negocio y, de esta manera, contribuyan a mejorar la rentabilidad de la organización. El análisis se realiza considerando la capacidad instalada del sistema.

5. Conclusiones
- En el pronóstico de comportamiento de la capacidad efectiva de un proceso productivo, la indisponibilidad operacional por mantenimiento planeado y la indisponibilidad operacional por fallas deben ser analizadas tanto de forma independiente como en conjunto, con la finalidad de diagnosticar y predecir estrategias que aseguren el cumplimiento de la producción.
- El efecto del plan de mantenimiento preventivo y correctivo sobre la capacidad efectiva del sistema evidencia la necesidad de realizar análisis de mantenibilidad en los sistemas y subsistemas, en la búsqueda por disminuir los tiempos de parada por mantenimiento.
- El Análisis de Confiabilidad, Disponibilidad y Mantenibilidad (RAM) permite pronosticar el impacto en la disponibilidad y la producción diferida mediante una simulación "what if" de las siguientes variables:
- Nuevas políticas de mantenimiento.
- Aplicación de nuevas tecnologías.
- Cambios en la mantenibilidad de los equipos.
- Modificaciones en la configuración de los procesos de producción.
- Cambios en la política de inventarios.
- Implantación de nuevos métodos de producción.
6. Referencia
- Mohammad Modarres, Mark P. Kaminskry, Vasily Krivtsov, 2017: Reliability Engineering and Risk Analysis: A Practical Guide, Third Edition.
- Blas Galván y Ernesto Primera, 2017: Estudios e Ingeniería RAM, MRI Institute.
- Andrew K.S. Jardine and Albert H. C. Tsang, 2014: Maintenance, Replacement, and Reliability (Theory and Applications), Second Edition, CRC Press.
- Edgar Fuenmayor, 2014: Análisis de Confiabilidad, Disponibilidad y Mantenibilidad de un Sistema de Bombeo, PMM Project Magazine Vol 29, ISSN 1887-018X.
- D.T. O’Connor, Andre Kleyner, 2012: Practical Reliability Engineering, Fifth Edition.
- R2M - Reliability and Risk Management Mexico S.A. de C.V., 2010: Confiabilidad Integral: Sinergias de Disciplinas Tomo I, II, III.
- ReliaSoft RS403, 2008: Confiabilidad de Sistemas, Master the Subject Seminar Series.
- ReliaSoft RS401, 2008: Análisis de Datos de Vida, Master the Subject Seminar Series.
- Medardo Yáñez, Hernando Gómez de la Vega, Genebelin Valbuena, 2004: Ingeniería de Confiabilidad y Análisis Probabilístico de Riesgo, Venezuela, R2M.
Dinos qué te ha parecido el artículo
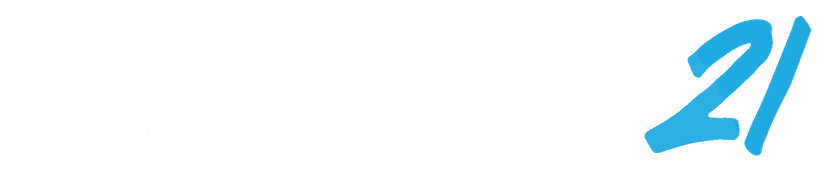
Publica tu artículo en la revista #1 de Mantenimiento Industrial
Publicar un artículo en la revista es gratis, no tiene costo.
Solo debes asegurarte que no sea un artículo comercial.
¿Qué esperas?
O envía tu artículo directo: articulos@predictiva21.com
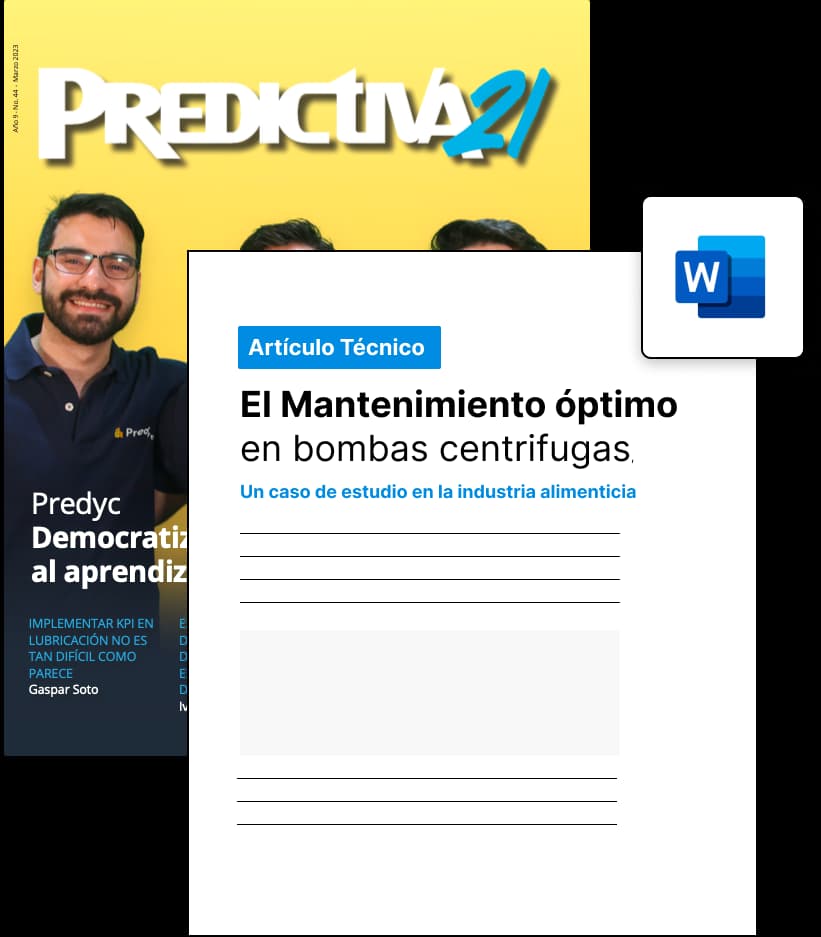
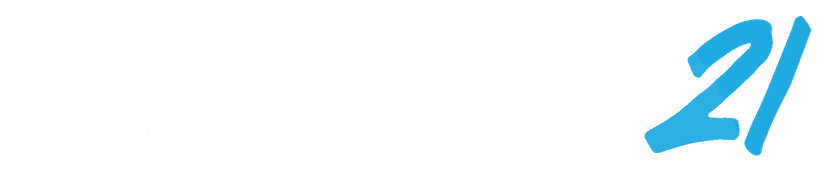
Publica tu artículo en la revista #1 de Mantenimiento Industrial
Publicar un artículo en la revista es gratis, no tiene costo.
Solo debes asegurarte que no sea un artículo comercial.
¿Qué esperas?
O envía tu artículo directo: articulos@predictiva21.com
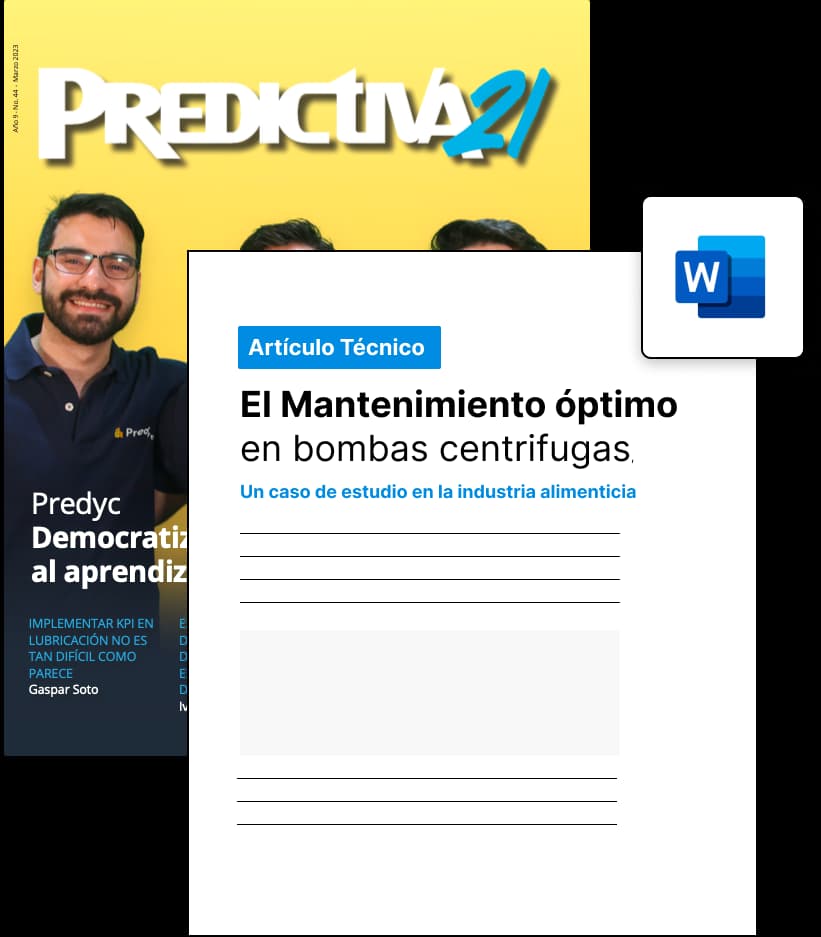