Cromatografía Gaseosa: conozca este análisis esencial
Articulo25 de noviembre de 2019
Como técnico de mantenimiento, usted debe apreciar la durabilidad y confiabilidad de su equipo. Para ello, conocer los análisis y las técnicas de mantenimiento predictivo es muy importante. La cromatografía gaseosa es una de esas técnicas y debe tenerse en cuenta cuando hablamos de equipos eléctricos utilizados en industrias. Descubre a continuación la importancia de la cromatografía gaseosa para la salud y funcionalidad de esos equipos y por qué usted puede beneficiarse de ella.
¿Qué es la cromatografía gaseosa?
La cromatografía gaseosa es un método físico de separación de los componentes de una mezcla a través de una interacción diferencial de sus componentes entre una FASE ESTACIONARIA (líquido o sólido) y una FASE MÓVIL (gas).
Bueno, si parece complicado, no te preocupes. Es realmente muy complicado. Entonces, veamos una analogía bien simplificada (libertad poética) para, al menos, entender el concepto:
Imagine un tubo capilar largo y lleno de polvo muy fino. Un polvo tan fino que funciona como tamiz molecular. Si pasamos dos gases de moléculas con diferentes tamaños (A y B), veremos en la otra punta que el gas de molécula menor (A) va a salir primero y el mayor (B) saldrá por último. Un detector instalado en la salida nos permitirá decir cuándo y cuánto de gas está saliendo. Porque el «cuándo» está relacionado con un gas específico. Nunca veremos B salir antes de A y cada uno de ellos saldrá siempre con el mismo tiempo. Y el «cuánto» está relacionado con la concentración de estos gases en la mezcla.
La importancia de la Cromatografía Gaseosa
Ya sabemos un poco sobre cómo la cromatografía gaseosa identifica y cuantifica los gases. Pero ¿para qué necesitamos de ella?
Los transformadores eléctricos necesitan aislamiento contra descargas y refrigeración para disipar el calor. En general, se utiliza aceite mineral aislante para este propósito.
Durante el funcionamiento del transformador ocurre un proceso normal de envejecimiento, el cual genera gases característicos. Si hay algún cambio en el transformador por defecto o incluso por simple variación de carga, se perciben variaciones en las concentraciones de esos gases.
Por medio del análisis de cromatografía gaseosa es posible definir la composición de la mezcla de gases disuelta en el aceite aislante. Se trata de un ensayo de monitoreo muy sensible que detecta la presencia de nueve gases, conforme regulado por la NBR 7070 (Tabla 1).
La evaluación se realiza mediante muestreos utilizando jeringas de vidrio. Las colecciones pueden ser recogidas por el técnico responsable de la empresa o por una tercerizada. Algunas industrias cuentan con laboratorio propio, otras, debido al altísimo costo de adquisición, calibración, mantenimiento de los equipos y calificación profesional del químico, optan por la tercerización de este servicio.
En cualquier caso, se recomienda que las colectas se hagan siempre de la misma manera, con los mismos instrumentos, para evitar errores muestrales.
El laboratorio, tan pronto como recibe la jeringa con la muestra, hace preparaciones especiales para extraer los gases en ella disueltos. A continuación, sólo los gases extraídos se inyectan en el cromatógrafo para la identificación y la cuantificación.
Para un diagnóstico confiable, son necesarios análisis periódicos y continuos, ya que la concentración de los gases varía a lo largo del tiempo. Así, para verificar la evolución de la concentración de compuestos improductivos diluidos en el aceite, se deben mantener análisis sistemáticos que puedan ser comparados entre sí.
A través de la cromatografía gaseosa, es posible detectar problemas en su origen y adoptar medidas correctivas acertadas que garanticen la operacionalidad y seguridad del equipo.

Fuente: El autor.
De esta manera, es posible diagnosticar un problema antes de que ocurran fallas en la unidad, adoptando un procedimiento adecuado de reparación en el equipo. Cuando el problema sigue siendo pequeño, el tiempo necesario de desactivación programada de la unidad es mínimo, cuando se compara al período demandado en caso de accidente o de pane en el equipo.
Además, dependiendo de la gravedad de la situación, el mantenimiento predictivo realizado a partir del análisis de cromatografía gaseosa puede evitar situaciones drásticas, como la pérdida total del equipo y pérdidas en función de la parada total de la producción de esa unidad.
Cursos recomendados






%252FImagen%252FRAMPREDYC-1730060420837.webp%3Falt%3Dmedia%26token%3D2634a7f0-988e-4022-b91f-382503e6e9db&w=3840&q=75)

Realice el análisis de Cromatografía Gaseosa
El técnico encargado de las operaciones de mantenimiento debe mantener en su rutina diaria procedimientos que autorresguarden la seguridad de los equipos, así como proteja el equipo de daños y, consecuentemente, de pérdidas financieras.
Para ello, debe estar bien organizado y tener una planificación de los mantenimientos predictivos a ser realizados periódicamente. En el caso de equipos eléctricos, el diagnóstico obtenido a partir de la cromatografía gaseosa permite que el técnico o técnica tenga una visión detallada de los equipos por los cuales es responsable.
Con estas informaciones, él o ella puede tomar decisiones a tiempo, para prevenir accidentes de trabajo, fallas en los equipos y pérdidas en la producción oriundas de paradas no programadas.
Es importante resaltar que la persona responsable de los análisis debe ser entrenada en procedimientos de muestreo y análisis e interpretación estadística de los datos recolectados, que debe ser basada en la NBR 7274.

Fuente: El autor.
Se destaca, también, la imprescindibilidad de la creación de un banco de datos organizado conteniendo los informes de los análisis. No se controla lo que no se monitorea. Y para un efectivo monitoreo, se debe cuantificar lo que se pretende controlar.
Así, para el efectivo control de costos y uso racional de los recursos empleados en la industria, es esencial que las informaciones sean fácilmente localizables y estén presentadas de manera clara para consultas posteriores.
Autor: Prof. Tarcisio Baroni
Brasil
Director Técnico de Tribología
Empresa: ALS Global
Correo: tarcisio.baroni@alsglobal.com
Síntesis curricular: Especialista en monitoreo de máquinas, gestión de mantenimiento, análisis de sistemas, instrumentación industrial y control de procesos y automatización industrial. Pionero de la técnica de ferrografía en Brasil. Profesor de posgrado de Ingeniería de Mantenimiento, investigador de accidentes aeronáuticos y consultor en el área de Tribología. Fundador de Tribolab, actual ALS Tribology Brazil. Director Técnico Latinoamericano de Tribología en ALS.
Dinos qué te ha parecido el artículo
Artículos recomendados
TERMOGRAFIA II

La facilitación del RCM y el Mantenimiento Efectivo

Evolución de la ingeniería industrial

Cálculo de cantidad de grasa para llenado inicial de rodamientos

Publica tu artículo en la revista #1 de Mantenimiento Industrial
Publicar un artículo en la revista es gratis, no tiene costo.
Solo debes asegurarte que no sea un artículo comercial.
¿Qué esperas?
O envía tu artículo directo: articulos@predictiva21.com
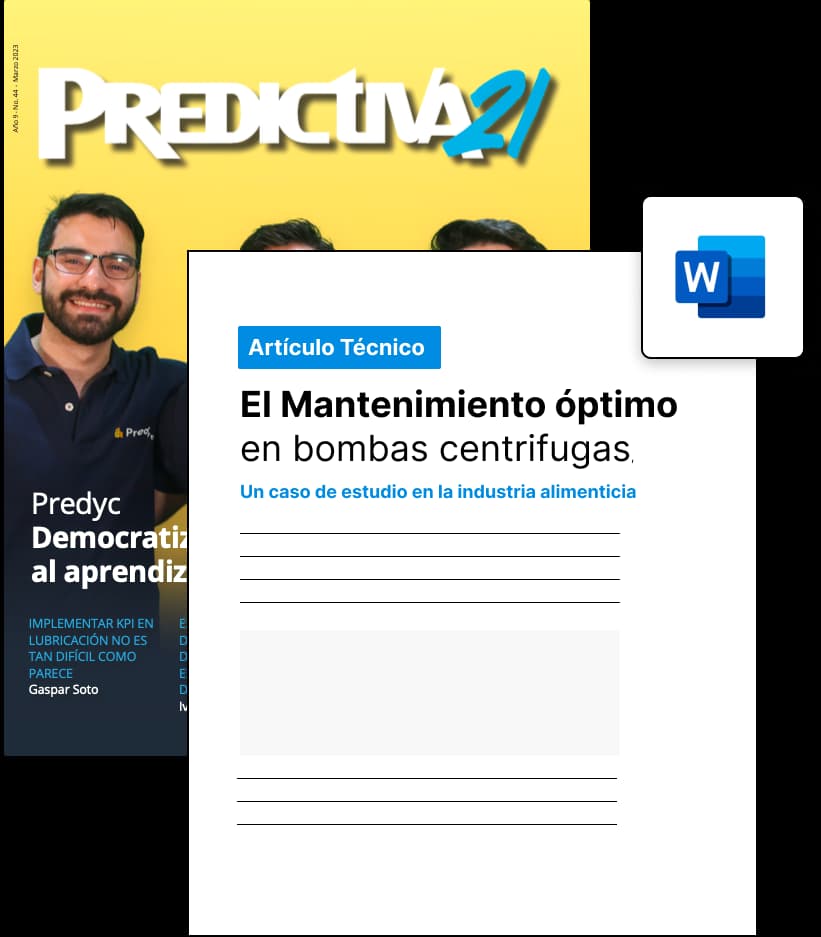
Cromatografía Gaseosa: conozca este análisis esencial
Articulo 25 de noviembre de 2019Como técnico de mantenimiento, usted debe apreciar la durabilidad y confiabilidad de su equipo. Para ello, conocer los análisis y las técnicas de mantenimiento predictivo es muy importante. La cromatografía gaseosa es una de esas técnicas y debe tenerse en cuenta cuando hablamos de equipos eléctricos utilizados en industrias. Descubre a continuación la importancia de la cromatografía gaseosa para la salud y funcionalidad de esos equipos y por qué usted puede beneficiarse de ella.
¿Qué es la cromatografía gaseosa?
La cromatografía gaseosa es un método físico de separación de los componentes de una mezcla a través de una interacción diferencial de sus componentes entre una FASE ESTACIONARIA (líquido o sólido) y una FASE MÓVIL (gas).
Bueno, si parece complicado, no te preocupes. Es realmente muy complicado. Entonces, veamos una analogía bien simplificada (libertad poética) para, al menos, entender el concepto:
Imagine un tubo capilar largo y lleno de polvo muy fino. Un polvo tan fino que funciona como tamiz molecular. Si pasamos dos gases de moléculas con diferentes tamaños (A y B), veremos en la otra punta que el gas de molécula menor (A) va a salir primero y el mayor (B) saldrá por último. Un detector instalado en la salida nos permitirá decir cuándo y cuánto de gas está saliendo. Porque el «cuándo» está relacionado con un gas específico. Nunca veremos B salir antes de A y cada uno de ellos saldrá siempre con el mismo tiempo. Y el «cuánto» está relacionado con la concentración de estos gases en la mezcla.
La importancia de la Cromatografía Gaseosa
Ya sabemos un poco sobre cómo la cromatografía gaseosa identifica y cuantifica los gases. Pero ¿para qué necesitamos de ella?
Los transformadores eléctricos necesitan aislamiento contra descargas y refrigeración para disipar el calor. En general, se utiliza aceite mineral aislante para este propósito.
Durante el funcionamiento del transformador ocurre un proceso normal de envejecimiento, el cual genera gases característicos. Si hay algún cambio en el transformador por defecto o incluso por simple variación de carga, se perciben variaciones en las concentraciones de esos gases.
Por medio del análisis de cromatografía gaseosa es posible definir la composición de la mezcla de gases disuelta en el aceite aislante. Se trata de un ensayo de monitoreo muy sensible que detecta la presencia de nueve gases, conforme regulado por la NBR 7070 (Tabla 1).
La evaluación se realiza mediante muestreos utilizando jeringas de vidrio. Las colecciones pueden ser recogidas por el técnico responsable de la empresa o por una tercerizada. Algunas industrias cuentan con laboratorio propio, otras, debido al altísimo costo de adquisición, calibración, mantenimiento de los equipos y calificación profesional del químico, optan por la tercerización de este servicio.
En cualquier caso, se recomienda que las colectas se hagan siempre de la misma manera, con los mismos instrumentos, para evitar errores muestrales.
El laboratorio, tan pronto como recibe la jeringa con la muestra, hace preparaciones especiales para extraer los gases en ella disueltos. A continuación, sólo los gases extraídos se inyectan en el cromatógrafo para la identificación y la cuantificación.
Para un diagnóstico confiable, son necesarios análisis periódicos y continuos, ya que la concentración de los gases varía a lo largo del tiempo. Así, para verificar la evolución de la concentración de compuestos improductivos diluidos en el aceite, se deben mantener análisis sistemáticos que puedan ser comparados entre sí.
A través de la cromatografía gaseosa, es posible detectar problemas en su origen y adoptar medidas correctivas acertadas que garanticen la operacionalidad y seguridad del equipo.

Fuente: El autor.
De esta manera, es posible diagnosticar un problema antes de que ocurran fallas en la unidad, adoptando un procedimiento adecuado de reparación en el equipo. Cuando el problema sigue siendo pequeño, el tiempo necesario de desactivación programada de la unidad es mínimo, cuando se compara al período demandado en caso de accidente o de pane en el equipo.
Además, dependiendo de la gravedad de la situación, el mantenimiento predictivo realizado a partir del análisis de cromatografía gaseosa puede evitar situaciones drásticas, como la pérdida total del equipo y pérdidas en función de la parada total de la producción de esa unidad.
Cursos recomendados






%252FImagen%252FRAMPREDYC-1730060420837.webp%3Falt%3Dmedia%26token%3D2634a7f0-988e-4022-b91f-382503e6e9db&w=3840&q=75)

Realice el análisis de Cromatografía Gaseosa
El técnico encargado de las operaciones de mantenimiento debe mantener en su rutina diaria procedimientos que autorresguarden la seguridad de los equipos, así como proteja el equipo de daños y, consecuentemente, de pérdidas financieras.
Para ello, debe estar bien organizado y tener una planificación de los mantenimientos predictivos a ser realizados periódicamente. En el caso de equipos eléctricos, el diagnóstico obtenido a partir de la cromatografía gaseosa permite que el técnico o técnica tenga una visión detallada de los equipos por los cuales es responsable.
Con estas informaciones, él o ella puede tomar decisiones a tiempo, para prevenir accidentes de trabajo, fallas en los equipos y pérdidas en la producción oriundas de paradas no programadas.
Es importante resaltar que la persona responsable de los análisis debe ser entrenada en procedimientos de muestreo y análisis e interpretación estadística de los datos recolectados, que debe ser basada en la NBR 7274.

Fuente: El autor.
Se destaca, también, la imprescindibilidad de la creación de un banco de datos organizado conteniendo los informes de los análisis. No se controla lo que no se monitorea. Y para un efectivo monitoreo, se debe cuantificar lo que se pretende controlar.
Así, para el efectivo control de costos y uso racional de los recursos empleados en la industria, es esencial que las informaciones sean fácilmente localizables y estén presentadas de manera clara para consultas posteriores.
Autor: Prof. Tarcisio Baroni
Brasil
Director Técnico de Tribología
Empresa: ALS Global
Correo: tarcisio.baroni@alsglobal.com
Síntesis curricular: Especialista en monitoreo de máquinas, gestión de mantenimiento, análisis de sistemas, instrumentación industrial y control de procesos y automatización industrial. Pionero de la técnica de ferrografía en Brasil. Profesor de posgrado de Ingeniería de Mantenimiento, investigador de accidentes aeronáuticos y consultor en el área de Tribología. Fundador de Tribolab, actual ALS Tribology Brazil. Director Técnico Latinoamericano de Tribología en ALS.
Dinos qué te ha parecido el artículo
Artículos recomendados
Optimización de Inventarios de Partes y Repuestos para el Mantenimiento (II Parte)

Gestión de Estrategia de Activos: Realizar Valor - Mejorar Desempeño

La Industria y los Protocolos de Comunicación

Descubre los softwares GMAO para la gestión de mantenimiento

Publica tu artículo en la revista #1 de Mantenimiento Industrial
Publicar un artículo en la revista es gratis, no tiene costo.
Solo debes asegurarte que no sea un artículo comercial.
¿Qué esperas?
O envía tu artículo directo: articulos@predictiva21.com
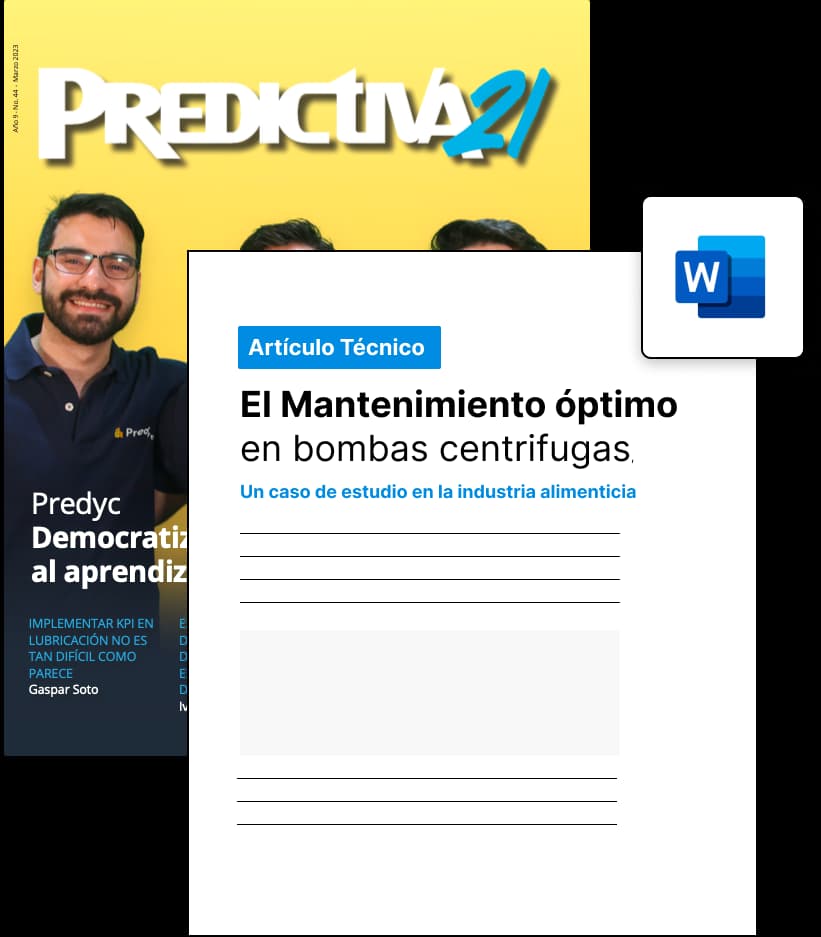