Advantages & disdvantages using active magnetic bearings vs gas/air barings vs lube oil bearings in turbomachinery
Articulo13 de mayo de 2024
Summary
This article discusses the different options available for turbomachinery regarding the use of radial and axial bearings in turbomachines. In particular, it focuses on bearings that maintain the separation between the moving rotor and the fixed or static section, which is the equipment housing. We refer to those that are oil-lubricated under pressure, those that maintain separation through the application of gas or pressurized air to avoid friction and rubbing between the rotor and housing, and the active magnetic type bearings, now increasingly critical in heavy industry worldwide. Here, we will explore the advantages and disadvantages of using these, the limits in design, selection, and the development of their engineering applied to turbomachinery. The associated questions of why to use them, when to use them, where to apply them, which one to apply, what kind of considerations to apply, and how to use them in each case are addressed. The critical steps to follow for their use are summarized through methods, procedures, specific actions, studies to consider, types of mitigations to apply, and recommendations to follow in general global industry usage.

Active Magnetic Bearings (AMBs):
Advantages:
- Non-contact operation: AMBs eliminate physical contact, minimizing wear and reducing the risk of failures caused by friction.
- High reliability: AMBs provide precise control over rotor position, reducing the chances of misalignment and vibration-related failures.
- Enhanced safety: AMBs offer advanced condition monitoring capabilities, enabling early fault detection and prevention of catastrophic failures.
- Improved efficiency: The absence of friction reduces energy losses, leading to higher overall system efficiency.
- Environmental benefits: AMBs eliminate the need for lubricating oil, reducing the risk of oil leakage and environmental contamination.
Disadvantages:
- Friction and wear: Lube oil bearings rely on a lubricating film, making them susceptible to wear and requiring regular oil analysis and maintenance.
- Oil leakage and environmental concerns: The presence of lubricating oil increases the risk of leaks and environmental contamination if not properly managed.
- Maintenance requirements: Lube oil bearings necessitate regular maintenance, including oil changes, filtration, and monitoring of oil quality.
Air/Gas bearings:
Advantages:
- Contactless operation: Air/gas bearings eliminate mechanical contact, reducing wear and the risk of failures associated with friction.
- High-speed capability: Air/gas bearings can support high-speed operation, making them suitable for turbomachinery applications.
- Simplified lubrication system: Air/gas bearings do not require complex lubrication systems, reducing maintenance needs.
- Cooling effect: The flow of compressed air or gas can provide cooling to the rotor, helping manage temperature rise.
Disadvantages:
- Limited load capacity: Air/gas bearings may have lower load capacity compared to other bearing types, limiting their suitability for certain applications.
- Sensitivity to contamination: Air/gas bearings are sensitive to particulate contamination, requiring careful control of the operating environment.
- Reduced precision: Compared to AMBs, air/gas bearings may offer lower precision in rotor position control.
Lube oil bearings:
Advantages:
- Proven technology: Lube oil bearings have a long history of successful application in turbomachinery and centrifugal compressors.
- Load capacity: Lube oil bearings can handle higher loads and accommodate larger clearances.
- Tolerance to contaminants: Lube oil bearings can withstand certain levels of oil contamination without immediate adverse effects.
- Cost-effective: Lube oil bearing systems are generally less expensive to implement and maintain.
Disadvantages:
- Friction and wear: Lube oil bearings rely on a lubricating film, making them susceptible to wear and requiring regular oil analysis and maintenance.
- Oil leakage and environmental concerns: The presence of lubricating oil increases the risk of leaks and environmental contamination if not properly managed.
- Maintenance requirements: Lube oil bearings necessitate regular maintenance, including oil changes, filtration, and monitoring of oil quality.
It’s important to note that the selection of a bearing system should consider the specific application requirements, operating conditions, budget constraints, and risk mitigation strategies. Each bearing type has its own set of advantages and disadvantages. Collaborating with experienced engineers and considering a comprehensive risk assessment can help in making an informed decision that prioritizes reliability, availability, and safety while minimizing critical and environmental risks and failures in the oil and gas industries.
Limits in engineering & design for different bearings types
When applying active magnetic bearings (AMBs), air/gas bearings, and lube oil bearings in centrifugal compressors and turbomachinery to enhance reliability, availability, and safety while avoiding critical and environmental risks and failures in the oil and gas industries, certain limits in engineering and design should be considered. These limits include:
Active Magnetic Bearings (AMBs):
- Power supply reliability: AMBs require a continuous and reliable power supply. Any power interruptions or failures can lead to an immediate loss of rotor support, potentially causing a catastrophic failure.
- Control System Complexity: The design and implementation of the control system for AMBs involve sophisticated electronics and software. Adequate expertise and maintenance resources are necessary to ensure the proper functioning and performance of the control system.
- Cost: The initial capital cost of installing AMBs can be higher compared to other bearing types, making it essential to evaluate the economic feasibility and benefits of using AMBs in each specific application.
Air/Gas Bearings:
- Contamination sensitivity: Air/gas bearings are susceptible to particulate contamination, which can affect their performance and lifespan. The operating environment must be carefully controlled to prevent contamination that could compromise the bearing operation.
- Load capacity: Air/gas bearings may have limitations on load capacity, making them less suitable for applications with high axial or radial loads.
- Precision and stability: Achieving high precision and stability in rotor positioning can be challenging with air/gas bearings, particularly at lower speeds. Design considerations are necessary to ensure sufficient accuracy and stability for the specific application.
Lube Oil Bearings:
- Friction and wear: Lube oil bearings rely on a lubricating film to reduce friction and wear. However, over time, wear can occur, and the lubrication film may degrade, requiring regular maintenance and monitoring to prevent failures.
- Oil leakage: The presence of lubricating oil increases the risk of leaks, which can result in environmental contamination and safety hazards. Proper design measures and maintenance practices are necessary to prevent oil leakage.
- Temperature control: Lube oil bearings require effective temperature control to prevent overheating, especially in high-speed applications. Cooling systems and monitoring of oil temperature are essential to maintain reliable and safe operation.
When implementing these bearing types in existing plants or new projects, it is crucial to consider the specific application requirements, operational conditions, and risk mitigation strategies. Conducting thorough risk assessments, engaging experienced engineers, and adhering to industry standards and best practices will help overcome the limits and ensure the appropriate engineering and design of these bearings to improve reliability, availability, and safety while minimizing critical and environmental risks and failures in the oil and gas industries.
Why, When, Where, What, Which, How to use different bearing types
Why use and apply these bearing types?
- Improve reliability: These bearing types offer various advantages such as reduced friction, wear, and vibration, leading to improved reliability and longer equipment lifespan.
- Enhance availability: By minimizing failures and maintenance requirements, these bearings can increase equipment uptime and availability, resulting in improved overall plant productivity.
- Ensure safety: Proper bearing selection and design contribute to safe and stable equipment operation, reducing the risk of accidents and safety hazards.
- Mitigate risks and failures: Each bearing type has specific features and benefits that help mitigate critical risks, such as oil leakage, power interruptions, and contamination issues.
When to use and apply each bearing type?
- Active Magnetic Bearings (AMBs): Consider using AMBs when high precision, control, and condition monitoring are required, and when minimizing mechanical wear and friction is crucial.
- Air/Gas Bearings: Choose air/gas bearings for applications demanding high speeds, low friction, and simplified lubrication systems, such as high-speed turbomachinery.
- Lube Oil Bearings: Select lube oil bearings for applications with moderate loads, lower speeds, and where proven technology, load capacity, and cost-effectiveness are priorities.
Where to use and apply each bearing type?
- Existing plants: Evaluate the feasibility and benefits of retrofitting or upgrading existing centrifugal compressors or turbomachinery with the desired bearing type based on the specific goals and requirements.
- New projects: During the design and engineering phase of new projects, carefully consider the application requirements, operating conditions, and project goals to determine the most suitable bearing type.
Cursos recomendados




%252FImagen%252FRAMPREDYC-1730060420837.webp%3Falt%3Dmedia%26token%3D2634a7f0-988e-4022-b91f-382503e6e9db&w=3840&q=75)



What are the considerations when selecting a bearing type?
- Application requirements: Assess the specific requirements of the compressor or turbomachinery, including load capacity, speed range, precision, and stability.
- Environmental factors: Consider the presence of corrosive or hazardous gases, potential for oil leaks, or sensitivity to contaminants in the operating environment.
- Safety considerations: Evaluate the safety implications of each bearing type, such as the risk of catastrophic failures, power interruptions, or environmental hazards.
Which bearing type to choose?
The selection depends on factors such as speed, load capacity, precision, maintenance requirements, power availability, cost, and specific application considerations.
Engage with experienced engineers, bearing manufacturers, and consultants to assess the specific requirements and make an informed decision.
How to use and apply each bearing type effectively?
- Design and engineering: Ensure that the bearing system is integrated correctly into the overall design of the compressor or turbomachinery, considering factors such as rotor dynamics, thermal management, and control systems.
- Installation and commissioning: Follow the manufacturer’s guidelines and best practices during the installation and commissioning process to ensure proper alignment, balancing, and calibration.
- Maintenance and monitoring: Implement a comprehensive maintenance program that includes regular inspection, lubrication (if applicable), condition monitoring, and predictive maintenance techniques.
By carefully considering the why, when, where, what, which, and how aspects of using and applying these bearing types, you can optimize reliability, availability, and safety while minimizing critical and environmental risks and failures in the oil and gas industries, whether in existing plants or new projects. Collaboration with experts and adherence to industry standards and best practices play a crucial role in successful implementation.
Advantages & disdvantages using active magnetic bearings vs gas/air barings vs lube oil bearings in turbomachinery
Procedures and actions:
a. Comprehensive risk assessment: Conduct a thorough risk assessment to identify potential failure modes, critical risks, and environmental concerns associated with the bearing types and specific applications.
b. Application-specific analysis: Perform detailed analysis of the system requirements, including load capacity, speed range, precision, temperature, and environmental conditions.
c. Bearing selection: Evaluate the advantages, disadvantages, and limitations of each bearing type against the identified application requirements to determine the most suitable option.
d. Engineering design: Ensure that the bearing system is appropriately integrated into the overall design, considering factors such as rotor dynamics, thermal management, and control systems.
e. Installation and commissioning: Follow manufacturer guidelines and best practices for proper installation, alignment, balancing, and calibration of the bearing system.
f. Maintenance and monitoring: Implement a proactive maintenance program that includes regular inspection, lubrication (if applicable), condition monitoring, and predictive maintenance techniques.
g. Training and expertise: Provide training for operators, maintenance personnel, and engineers involved in the installation, operation, and maintenance of the chosen bearing system.
Studies and mitigation:
a. Failure Modes and Effects Analysis (FMEA): Conduct FMEA studies to identify potential failure modes, their effects on system performance, and mitigation strategies.
b. Fault detection and diagnostic studies: Develop or utilize advanced condition monitoring techniques to detect and diagnose potential issues in real-time, enabling timely intervention and preventive actions.
c. Contamination control: Implement effective contamination control measures, such as filtration systems, to mitigate the risk of contaminants adversely affecting bearing performance and system reliability.
d. Temperature management: Develop appropriate cooling systems and monitoring mechanisms to control bearing temperature and prevent overheating.
e. Redundancy and backup systems: Consider the implementation of redundant systems or backup solutions to ensure continued operation in case of bearing failure or power interruptions.
f. Environmental protection: Implement measures to prevent oil leakage, control emissions, and minimize the environmental impact of bearing systems, particularly in sensitive or regulated environments.
Recommendations:
a. Collaborative approach: Engage with bearing manufacturers, industry experts, and consultants to benefit from their expertise and gain insights into the best practices for bearing selection, installation, operation, and maintenance.
b. Compliance with standards: Adhere to industry standards, guidelines, and regulations relevant to bearing design, installation, and safety to ensure compliance and mitigate risks.
c. Continuous improvement: Foster a culture of continuous improvement by monitoring system performance, gathering feedback, and implementing lessons learned to optimize bearing usage and performance over time.
d. Documentation and knowledge management: Maintain comprehensive documentation of bearing-related procedures, maintenance records, and lessons learned to facilitate knowledge transfer, troubleshooting, and decision-making in the future.
By following these procedures, actions, studies, mitigations, and recommendations, you can enhance the reliability, availability, maintainability, and safety of centrifugal compressors and turbomachinery, while reducing critical and environmental risks and failures in both existing plants and new projects within the oil and gas industries.
Autor: Alberto Martínez Llaurado
Ingeniero Mecánico, Especialista en Equipos Rotativos
Dinos qué te ha parecido el artículo
Artículos recomendados
Cálculo de la Tasa de Falla de Tuberías usando Confiabilidad Estructural

Termografía I

Autodiagnóstico de Fallas con Sensores Inteligentes

El PMO o planned maintenance optimization

Publica tu artículo en la revista #1 de Mantenimiento Industrial
Publicar un artículo en la revista es gratis, no tiene costo.
Solo debes asegurarte que no sea un artículo comercial.
¿Qué esperas?
O envía tu artículo directo: articulos@predictiva21.com
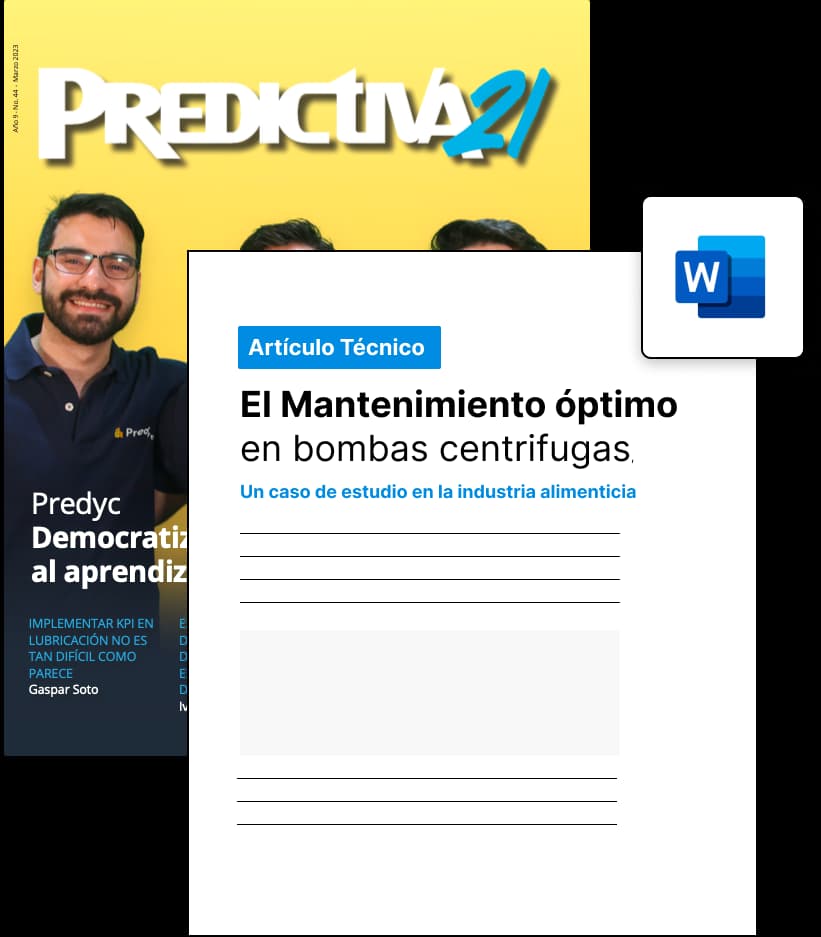
Advantages & disdvantages using active magnetic bearings vs gas/air barings vs lube oil bearings in turbomachinery
Articulo 13 de mayo de 2024Summary
This article discusses the different options available for turbomachinery regarding the use of radial and axial bearings in turbomachines. In particular, it focuses on bearings that maintain the separation between the moving rotor and the fixed or static section, which is the equipment housing. We refer to those that are oil-lubricated under pressure, those that maintain separation through the application of gas or pressurized air to avoid friction and rubbing between the rotor and housing, and the active magnetic type bearings, now increasingly critical in heavy industry worldwide. Here, we will explore the advantages and disadvantages of using these, the limits in design, selection, and the development of their engineering applied to turbomachinery. The associated questions of why to use them, when to use them, where to apply them, which one to apply, what kind of considerations to apply, and how to use them in each case are addressed. The critical steps to follow for their use are summarized through methods, procedures, specific actions, studies to consider, types of mitigations to apply, and recommendations to follow in general global industry usage.

Active Magnetic Bearings (AMBs):
Advantages:
- Non-contact operation: AMBs eliminate physical contact, minimizing wear and reducing the risk of failures caused by friction.
- High reliability: AMBs provide precise control over rotor position, reducing the chances of misalignment and vibration-related failures.
- Enhanced safety: AMBs offer advanced condition monitoring capabilities, enabling early fault detection and prevention of catastrophic failures.
- Improved efficiency: The absence of friction reduces energy losses, leading to higher overall system efficiency.
- Environmental benefits: AMBs eliminate the need for lubricating oil, reducing the risk of oil leakage and environmental contamination.
Disadvantages:
- Friction and wear: Lube oil bearings rely on a lubricating film, making them susceptible to wear and requiring regular oil analysis and maintenance.
- Oil leakage and environmental concerns: The presence of lubricating oil increases the risk of leaks and environmental contamination if not properly managed.
- Maintenance requirements: Lube oil bearings necessitate regular maintenance, including oil changes, filtration, and monitoring of oil quality.
Air/Gas bearings:
Advantages:
- Contactless operation: Air/gas bearings eliminate mechanical contact, reducing wear and the risk of failures associated with friction.
- High-speed capability: Air/gas bearings can support high-speed operation, making them suitable for turbomachinery applications.
- Simplified lubrication system: Air/gas bearings do not require complex lubrication systems, reducing maintenance needs.
- Cooling effect: The flow of compressed air or gas can provide cooling to the rotor, helping manage temperature rise.
Disadvantages:
- Limited load capacity: Air/gas bearings may have lower load capacity compared to other bearing types, limiting their suitability for certain applications.
- Sensitivity to contamination: Air/gas bearings are sensitive to particulate contamination, requiring careful control of the operating environment.
- Reduced precision: Compared to AMBs, air/gas bearings may offer lower precision in rotor position control.
Lube oil bearings:
Advantages:
- Proven technology: Lube oil bearings have a long history of successful application in turbomachinery and centrifugal compressors.
- Load capacity: Lube oil bearings can handle higher loads and accommodate larger clearances.
- Tolerance to contaminants: Lube oil bearings can withstand certain levels of oil contamination without immediate adverse effects.
- Cost-effective: Lube oil bearing systems are generally less expensive to implement and maintain.
Disadvantages:
- Friction and wear: Lube oil bearings rely on a lubricating film, making them susceptible to wear and requiring regular oil analysis and maintenance.
- Oil leakage and environmental concerns: The presence of lubricating oil increases the risk of leaks and environmental contamination if not properly managed.
- Maintenance requirements: Lube oil bearings necessitate regular maintenance, including oil changes, filtration, and monitoring of oil quality.
It’s important to note that the selection of a bearing system should consider the specific application requirements, operating conditions, budget constraints, and risk mitigation strategies. Each bearing type has its own set of advantages and disadvantages. Collaborating with experienced engineers and considering a comprehensive risk assessment can help in making an informed decision that prioritizes reliability, availability, and safety while minimizing critical and environmental risks and failures in the oil and gas industries.
Limits in engineering & design for different bearings types
When applying active magnetic bearings (AMBs), air/gas bearings, and lube oil bearings in centrifugal compressors and turbomachinery to enhance reliability, availability, and safety while avoiding critical and environmental risks and failures in the oil and gas industries, certain limits in engineering and design should be considered. These limits include:
Active Magnetic Bearings (AMBs):
- Power supply reliability: AMBs require a continuous and reliable power supply. Any power interruptions or failures can lead to an immediate loss of rotor support, potentially causing a catastrophic failure.
- Control System Complexity: The design and implementation of the control system for AMBs involve sophisticated electronics and software. Adequate expertise and maintenance resources are necessary to ensure the proper functioning and performance of the control system.
- Cost: The initial capital cost of installing AMBs can be higher compared to other bearing types, making it essential to evaluate the economic feasibility and benefits of using AMBs in each specific application.
Air/Gas Bearings:
- Contamination sensitivity: Air/gas bearings are susceptible to particulate contamination, which can affect their performance and lifespan. The operating environment must be carefully controlled to prevent contamination that could compromise the bearing operation.
- Load capacity: Air/gas bearings may have limitations on load capacity, making them less suitable for applications with high axial or radial loads.
- Precision and stability: Achieving high precision and stability in rotor positioning can be challenging with air/gas bearings, particularly at lower speeds. Design considerations are necessary to ensure sufficient accuracy and stability for the specific application.
Lube Oil Bearings:
- Friction and wear: Lube oil bearings rely on a lubricating film to reduce friction and wear. However, over time, wear can occur, and the lubrication film may degrade, requiring regular maintenance and monitoring to prevent failures.
- Oil leakage: The presence of lubricating oil increases the risk of leaks, which can result in environmental contamination and safety hazards. Proper design measures and maintenance practices are necessary to prevent oil leakage.
- Temperature control: Lube oil bearings require effective temperature control to prevent overheating, especially in high-speed applications. Cooling systems and monitoring of oil temperature are essential to maintain reliable and safe operation.
When implementing these bearing types in existing plants or new projects, it is crucial to consider the specific application requirements, operational conditions, and risk mitigation strategies. Conducting thorough risk assessments, engaging experienced engineers, and adhering to industry standards and best practices will help overcome the limits and ensure the appropriate engineering and design of these bearings to improve reliability, availability, and safety while minimizing critical and environmental risks and failures in the oil and gas industries.
Why, When, Where, What, Which, How to use different bearing types
Why use and apply these bearing types?
- Improve reliability: These bearing types offer various advantages such as reduced friction, wear, and vibration, leading to improved reliability and longer equipment lifespan.
- Enhance availability: By minimizing failures and maintenance requirements, these bearings can increase equipment uptime and availability, resulting in improved overall plant productivity.
- Ensure safety: Proper bearing selection and design contribute to safe and stable equipment operation, reducing the risk of accidents and safety hazards.
- Mitigate risks and failures: Each bearing type has specific features and benefits that help mitigate critical risks, such as oil leakage, power interruptions, and contamination issues.
When to use and apply each bearing type?
- Active Magnetic Bearings (AMBs): Consider using AMBs when high precision, control, and condition monitoring are required, and when minimizing mechanical wear and friction is crucial.
- Air/Gas Bearings: Choose air/gas bearings for applications demanding high speeds, low friction, and simplified lubrication systems, such as high-speed turbomachinery.
- Lube Oil Bearings: Select lube oil bearings for applications with moderate loads, lower speeds, and where proven technology, load capacity, and cost-effectiveness are priorities.
Where to use and apply each bearing type?
- Existing plants: Evaluate the feasibility and benefits of retrofitting or upgrading existing centrifugal compressors or turbomachinery with the desired bearing type based on the specific goals and requirements.
- New projects: During the design and engineering phase of new projects, carefully consider the application requirements, operating conditions, and project goals to determine the most suitable bearing type.
Cursos recomendados




%252FImagen%252FRAMPREDYC-1730060420837.webp%3Falt%3Dmedia%26token%3D2634a7f0-988e-4022-b91f-382503e6e9db&w=3840&q=75)



What are the considerations when selecting a bearing type?
- Application requirements: Assess the specific requirements of the compressor or turbomachinery, including load capacity, speed range, precision, and stability.
- Environmental factors: Consider the presence of corrosive or hazardous gases, potential for oil leaks, or sensitivity to contaminants in the operating environment.
- Safety considerations: Evaluate the safety implications of each bearing type, such as the risk of catastrophic failures, power interruptions, or environmental hazards.
Which bearing type to choose?
The selection depends on factors such as speed, load capacity, precision, maintenance requirements, power availability, cost, and specific application considerations.
Engage with experienced engineers, bearing manufacturers, and consultants to assess the specific requirements and make an informed decision.
How to use and apply each bearing type effectively?
- Design and engineering: Ensure that the bearing system is integrated correctly into the overall design of the compressor or turbomachinery, considering factors such as rotor dynamics, thermal management, and control systems.
- Installation and commissioning: Follow the manufacturer’s guidelines and best practices during the installation and commissioning process to ensure proper alignment, balancing, and calibration.
- Maintenance and monitoring: Implement a comprehensive maintenance program that includes regular inspection, lubrication (if applicable), condition monitoring, and predictive maintenance techniques.
By carefully considering the why, when, where, what, which, and how aspects of using and applying these bearing types, you can optimize reliability, availability, and safety while minimizing critical and environmental risks and failures in the oil and gas industries, whether in existing plants or new projects. Collaboration with experts and adherence to industry standards and best practices play a crucial role in successful implementation.
Advantages & disdvantages using active magnetic bearings vs gas/air barings vs lube oil bearings in turbomachinery
Procedures and actions:
a. Comprehensive risk assessment: Conduct a thorough risk assessment to identify potential failure modes, critical risks, and environmental concerns associated with the bearing types and specific applications.
b. Application-specific analysis: Perform detailed analysis of the system requirements, including load capacity, speed range, precision, temperature, and environmental conditions.
c. Bearing selection: Evaluate the advantages, disadvantages, and limitations of each bearing type against the identified application requirements to determine the most suitable option.
d. Engineering design: Ensure that the bearing system is appropriately integrated into the overall design, considering factors such as rotor dynamics, thermal management, and control systems.
e. Installation and commissioning: Follow manufacturer guidelines and best practices for proper installation, alignment, balancing, and calibration of the bearing system.
f. Maintenance and monitoring: Implement a proactive maintenance program that includes regular inspection, lubrication (if applicable), condition monitoring, and predictive maintenance techniques.
g. Training and expertise: Provide training for operators, maintenance personnel, and engineers involved in the installation, operation, and maintenance of the chosen bearing system.
Studies and mitigation:
a. Failure Modes and Effects Analysis (FMEA): Conduct FMEA studies to identify potential failure modes, their effects on system performance, and mitigation strategies.
b. Fault detection and diagnostic studies: Develop or utilize advanced condition monitoring techniques to detect and diagnose potential issues in real-time, enabling timely intervention and preventive actions.
c. Contamination control: Implement effective contamination control measures, such as filtration systems, to mitigate the risk of contaminants adversely affecting bearing performance and system reliability.
d. Temperature management: Develop appropriate cooling systems and monitoring mechanisms to control bearing temperature and prevent overheating.
e. Redundancy and backup systems: Consider the implementation of redundant systems or backup solutions to ensure continued operation in case of bearing failure or power interruptions.
f. Environmental protection: Implement measures to prevent oil leakage, control emissions, and minimize the environmental impact of bearing systems, particularly in sensitive or regulated environments.
Recommendations:
a. Collaborative approach: Engage with bearing manufacturers, industry experts, and consultants to benefit from their expertise and gain insights into the best practices for bearing selection, installation, operation, and maintenance.
b. Compliance with standards: Adhere to industry standards, guidelines, and regulations relevant to bearing design, installation, and safety to ensure compliance and mitigate risks.
c. Continuous improvement: Foster a culture of continuous improvement by monitoring system performance, gathering feedback, and implementing lessons learned to optimize bearing usage and performance over time.
d. Documentation and knowledge management: Maintain comprehensive documentation of bearing-related procedures, maintenance records, and lessons learned to facilitate knowledge transfer, troubleshooting, and decision-making in the future.
By following these procedures, actions, studies, mitigations, and recommendations, you can enhance the reliability, availability, maintainability, and safety of centrifugal compressors and turbomachinery, while reducing critical and environmental risks and failures in both existing plants and new projects within the oil and gas industries.
Autor: Alberto Martínez Llaurado
Ingeniero Mecánico, Especialista en Equipos Rotativos
Dinos qué te ha parecido el artículo
Artículos recomendados
¿Realiza mantenimientos preventivos a sus robots con personal interno? Entonces debe saber esto.

Detección temperatura anormal por daños en el asiento de la válvula compresora interna de cuarta etapa, compresor dresser rand

¿Cómo medir la Calidad de servicio? El nuevo indicador de Gestión de Activos

Gestión de Mantenimiento: 7 KPIs imprescindibles

Publica tu artículo en la revista #1 de Mantenimiento Industrial
Publicar un artículo en la revista es gratis, no tiene costo.
Solo debes asegurarte que no sea un artículo comercial.
¿Qué esperas?
O envía tu artículo directo: articulos@predictiva21.com
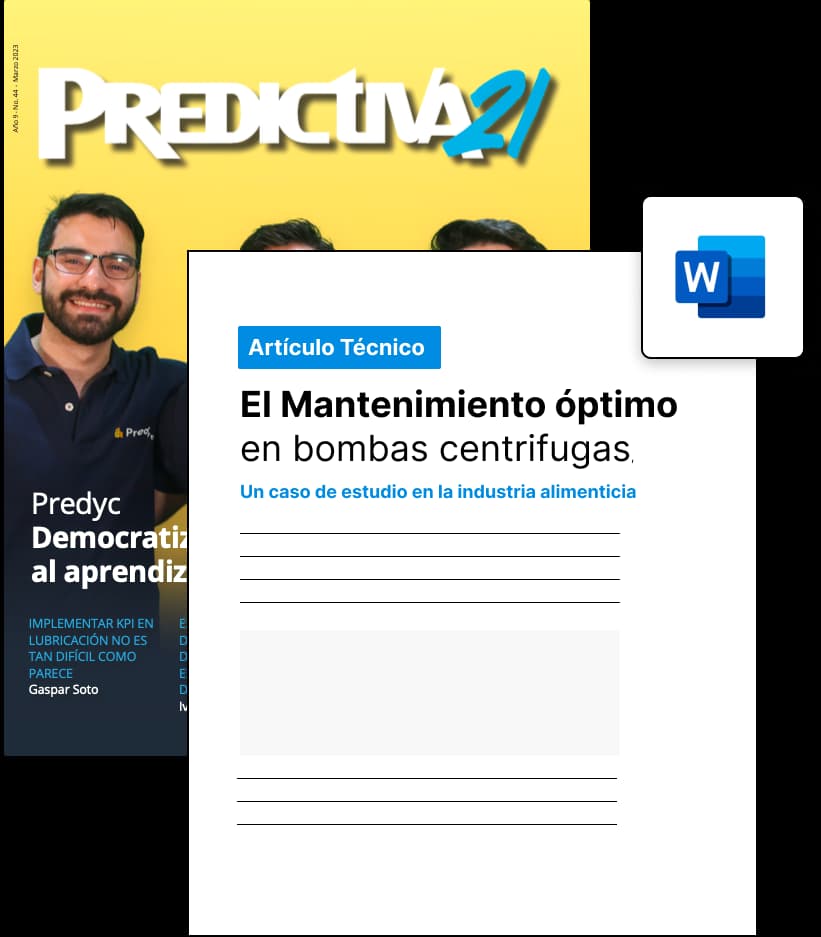