Disminuir el valor no agregado de mantenimiento
Articulo23 de abril de 2019
Lean Manufacturing
En todo negocio, sea una empresa de transformación o de servicios, se cuenta con una serie de insumos que se resumen en cinco grandes grupos básicos: los materiales, las máquinas, la mano de obra, los métodos y el medio ambiente. Muchos autores han coincidido en referirse a ellos como las 5 M´s. Es importante reconocer que cada uno de estos grupos es muy diferente a los otros, pero existe un factor común inherente a todos ellos: el dinero.
En esta época de competitividad internacional solamente prevalecerán las empresas cuyos objetivos primarios sean la velocidad de entrega y la calidad. Ya no son los grandes corporativos los que determinan el rumbo, sino las compañías más veloces en respuesta al cliente y en innovación.
Lean Manufacturing (o manufactura esbelta) es el nombre que se le da al sistema Just in Time en occidente. También se ha llamado Manufactura de Clase Mundial y Sistema de Producción Toyota.
Se puede definir como un proceso continuo y sistemático de identificación y eliminación de desperdicios o excesos, entendiendo como exceso toda aquella actividad que no agrega valor al proceso, pero si costo y trabajo. Esta eliminación sistemática se lleva a cabo mediante trabajo con equipos de personas bien organizadas y capacitadas.
El uso de la metodología para la eliminación de desperdicios o mudas en las empresas para alcanzar ventajas competitivas dentro de una organización, fue iniciado en los 80’s por el principal ingeniero de Toyota Taiichi Ohno y el Sensei Shigeo Shingo, orientados fundamentalmente hacia la productividad y a la calidad.
Es justo aquí donde se popularizó el término “valor no agregado”.
El pensamiento tradicional nos incita a agregar valor en lo que hacemos: Mejorar las actividades de valor, mejorar disponibilidad, hacer más rápido el tiempo de ciclo, remplazar personal con equipos automatizados y así sucesivamente. Mejorar lo que hacemos bien, y sobre todo, producir más.
Departamento de Mantenimiento Valor no agregado en su máximo esplendor
Siempre me sentí orgulloso de pertenecer al departamento de mantenimiento, me enseñaron que, de todos, era el departamento más completo. Cuando inicié mi carrera como mantenedor, la guerra entre operaciones y mantenimiento esta en pleno apogeo. ¿Quién era mejor? Por desgracia siempre teníamos las de perder.
“¡Producción sin mantenimiento no es nada!” Eran frases populares dentro del departamento de mantenimiento. Por el contrario, una de las frases más comunes del departamento de operaciones es: “¡mantenimiento es un mal necesario!”.
Cuando me cambié a trabajar para una compañía de Outsourcing de Mantenimiento, caí en cuenta de que somos un departamento de servicio, y al poco tiempo descubrí la triste realidad. ¿Realmente somos un mal necesario?
Quiero hacer la aclaración al lector, sobre todo si éste pertenece a un departamento de mantenimiento, que mi intención no es herir sus sentimientos con lo que voy a declarar a continuación, como ya mencioné, toda mi carrera la he realizado en el departamento de mantenimiento, pero no por esto tengo mis sentimientos encajonados y mis sentidos aturdidos.
Favor de tomar lo siguiente de la mejor forma posible. El departamento de mantenimiento es un departamento que no genera valor a la empresa. Y todo lo que no agrega valor a un producto o un servicio se considera como “desperdicio”.
Valor agregado
Nos han domesticado con esta palabra y para muchos el paradigma es que “valor agregado” es dar más de algo. Hay muchos ejemplos de esto: “quedarse más tiempo por valor agregado”, “dar algo de más, como valor agregado”, “regalar trabajo o tiempo”. Todos estos ejemplos hablan del concepto erróneo sobre valor agregado.
De acuerdo al TPS (Toyota Production System), todo aquel paso de un proceso que produce un cambio en el producto o servicio y que el cliente está dispuesto a pagar por él, se define como valor agregado.
Desde la perspectiva del cliente, podemos descomponer los pasos para realizar un producto o un servicio en cualquier industria en cualquier proceso y separar aquellos pasos que agregan valor y los que no agregan valor.
Si analizamos un Mapa de Cadena de Valor (VSM) de productos o servicios de las empresas de cualquier tipo, en ninguna de éstas se contempla como pasos del proceso al “mantenimiento”, ni siquiera al mantenimiento proactivo (preventivo o predictivo). Y cuando este es contemplado se considera como “valor no agregado” representándolo como un desperdicio de “espera”.

He visto y escuchado como se ha tratado de exaltar al departamento de mantenimiento y títulos como lean maintenance han surgido a causa de la moda del propio TPS, sin embargo, no hay nada de valor agregado en las actividades de mantenimiento.
¿Entonces qué podemos hacer? Simple. Hacer bien las cosas a la primera. De esta forma no agregaremos valor, pero trataremos de agregar el menos “valor no agregado” al proceso de operaciones.
Un simple cambio en la forma de ver las cosas, un cambio en este paradigma puede dar enormes resultados.
En donde comenzar. Con el personal principalmente. Haciéndoles entender que no estamos aquí para perder el tiempo, que mantenimiento es una de las grandes restricciones para las operaciones, y cuando hay una falla, mantenimiento es una restricción, cuando hay un mantenimiento preventivo, el equipo está detenido, mantenimiento sigue siendo una restricción.
¿Dónde no generar el menos “valor no agregado”?, en definitiva, se encuentran en dos áreas. Hacer mantenimientos mientras el equipo está produciendo, mantenimiento predictivo o basado en condición. Y una de las más importantes es arreglar los problemas que se van presentando día a día de raíz para que estos no vuelvan a ocurrir mediante el mantenimiento correctivo.
Dos herramientas esenciales para mejorar esto es sin duda la optimización de los mantenimiento planeados (PMO) y por otro lado la aplicación correcta de las herramientas de análisis de falla y causa raíz.
No se trata de aplicar estas herramientas a todo, aquí es donde el VSM ayuda mucho. Siempre hay una relación directa entre el Costo y la Confiabilidad como lo muestra la figura 2.

Si tenemos baja confiabilidad operacional, los costos se elevan, sin embargo, aumentar la confiabilidad por aumentarla, también trae costos asociados.
Nuestro deber es encontrar el punto óptimo entre costo y confiabilidad. No podemos implementar RCM, PMO, RCA, Six Sgma a todo solo porque sí, solo porque están de moda o por el afán de mejorar un indicador de disponibilidad. Tenemos que ser inteligentes en este aspecto, aplicar las herramientas donde mayor beneficio vayamos a obtener. Así es donde entra un buen VSM que nos indique por dónde comenzar.
Haciendo hincapié que la implementación de estas herramientas debe ser realizada por los mismos técnicos de mantenimiento, puesto que estos son la base de la estructura de mantenimiento. Aquí es donde comienza el cambio cultural. Dejar de pensar en los ingenieros como los indicados para realizarlas y olvidar al personal de piso en el involucramiento de las mismas.
Cursos recomendados




%252FImagen%252FRAMPREDYC-1730060420837.webp%3Falt%3Dmedia%26token%3D2634a7f0-988e-4022-b91f-382503e6e9db&w=3840&q=75)



Referencias
- Desperdicio o muda. La eliminación de desperdicios o mudas dentro de los principios del TPS (Toyota Production System) es la actividad principal en la que se basa el JIS (Just in Time) o mejor conocido en occidente como Lean Manufacturing o Manufactura Esbelta.
- Valor agregado. Se dice de las actividades de un proceso que genera alguna transformación a un producto o servicio y que el cliente final esta dispuesto a pagar por ella.
- Los mapas de cadena de valor (VSM) se utilizan para conocer a fondo el proceso tanto dentro de la planta como en la cadena de suministro. Es una representación gráfica de elementos de producción e información que permite conocer y documentar el estado actual y futuro de un proceso, es la base para el análisis del valor que se aporta al producto o servicio y es la fuente del conocimiento de las restricciones reales de una empresa, ya que permite visualizar en dónde se encuentra el valor y en dónde el desperdicio.
Autor: Edwin Guzmán King CMRP
Saltillo, Coahuila
www.gkconsulting.mx
Correo: eguzman@gkconsulting.mx
Dinos qué te ha parecido el artículo
Artículos recomendados
19.3.- Causas de las Vibraciones en las Bombas Centrífugas

Mobius Institute lanza RELIABILITY CONNECT® y RELIABILITY CONNECT® en Español.

Disminución de los costos por hora en neumáticos de camiones mineros

Mantenimiento preventivo de las fábricas y su impacto en la eficiencia global de equipos

Publica tu artículo en la revista #1 de Mantenimiento Industrial
Publicar un artículo en la revista es gratis, no tiene costo.
Solo debes asegurarte que no sea un artículo comercial.
¿Qué esperas?
O envía tu artículo directo: articulos@predictiva21.com
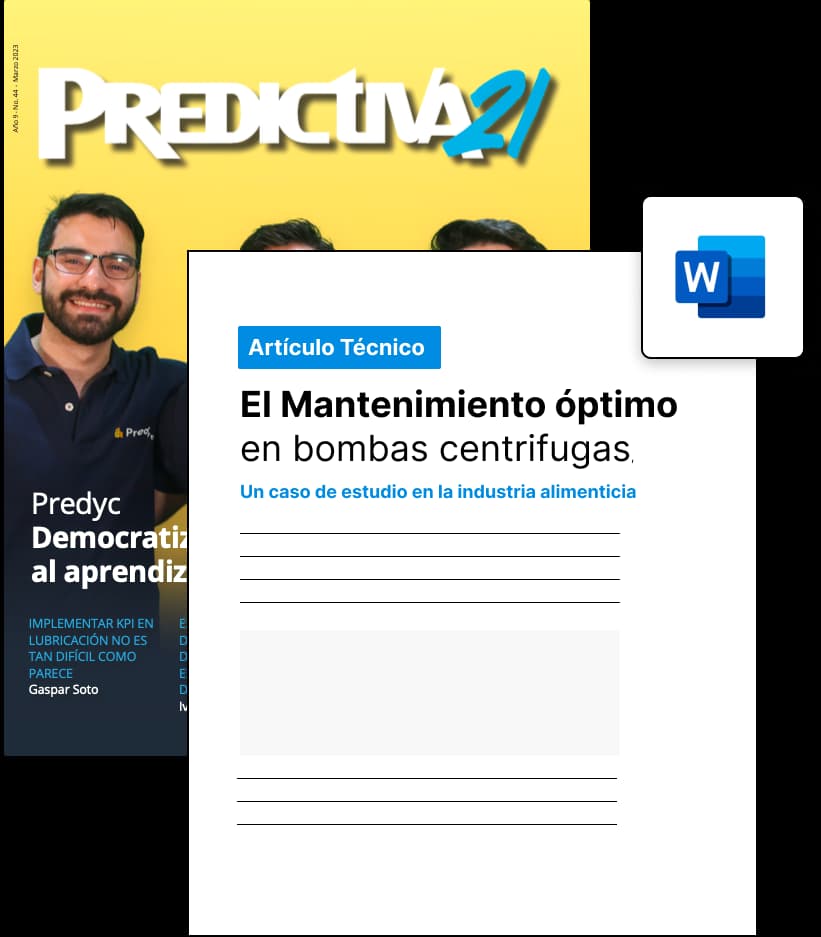
Disminuir el valor no agregado de mantenimiento
Articulo 23 de abril de 2019Lean Manufacturing
En todo negocio, sea una empresa de transformación o de servicios, se cuenta con una serie de insumos que se resumen en cinco grandes grupos básicos: los materiales, las máquinas, la mano de obra, los métodos y el medio ambiente. Muchos autores han coincidido en referirse a ellos como las 5 M´s. Es importante reconocer que cada uno de estos grupos es muy diferente a los otros, pero existe un factor común inherente a todos ellos: el dinero.
En esta época de competitividad internacional solamente prevalecerán las empresas cuyos objetivos primarios sean la velocidad de entrega y la calidad. Ya no son los grandes corporativos los que determinan el rumbo, sino las compañías más veloces en respuesta al cliente y en innovación.
Lean Manufacturing (o manufactura esbelta) es el nombre que se le da al sistema Just in Time en occidente. También se ha llamado Manufactura de Clase Mundial y Sistema de Producción Toyota.
Se puede definir como un proceso continuo y sistemático de identificación y eliminación de desperdicios o excesos, entendiendo como exceso toda aquella actividad que no agrega valor al proceso, pero si costo y trabajo. Esta eliminación sistemática se lleva a cabo mediante trabajo con equipos de personas bien organizadas y capacitadas.
El uso de la metodología para la eliminación de desperdicios o mudas en las empresas para alcanzar ventajas competitivas dentro de una organización, fue iniciado en los 80’s por el principal ingeniero de Toyota Taiichi Ohno y el Sensei Shigeo Shingo, orientados fundamentalmente hacia la productividad y a la calidad.
Es justo aquí donde se popularizó el término “valor no agregado”.
El pensamiento tradicional nos incita a agregar valor en lo que hacemos: Mejorar las actividades de valor, mejorar disponibilidad, hacer más rápido el tiempo de ciclo, remplazar personal con equipos automatizados y así sucesivamente. Mejorar lo que hacemos bien, y sobre todo, producir más.
Departamento de Mantenimiento Valor no agregado en su máximo esplendor
Siempre me sentí orgulloso de pertenecer al departamento de mantenimiento, me enseñaron que, de todos, era el departamento más completo. Cuando inicié mi carrera como mantenedor, la guerra entre operaciones y mantenimiento esta en pleno apogeo. ¿Quién era mejor? Por desgracia siempre teníamos las de perder.
“¡Producción sin mantenimiento no es nada!” Eran frases populares dentro del departamento de mantenimiento. Por el contrario, una de las frases más comunes del departamento de operaciones es: “¡mantenimiento es un mal necesario!”.
Cuando me cambié a trabajar para una compañía de Outsourcing de Mantenimiento, caí en cuenta de que somos un departamento de servicio, y al poco tiempo descubrí la triste realidad. ¿Realmente somos un mal necesario?
Quiero hacer la aclaración al lector, sobre todo si éste pertenece a un departamento de mantenimiento, que mi intención no es herir sus sentimientos con lo que voy a declarar a continuación, como ya mencioné, toda mi carrera la he realizado en el departamento de mantenimiento, pero no por esto tengo mis sentimientos encajonados y mis sentidos aturdidos.
Favor de tomar lo siguiente de la mejor forma posible. El departamento de mantenimiento es un departamento que no genera valor a la empresa. Y todo lo que no agrega valor a un producto o un servicio se considera como “desperdicio”.
Valor agregado
Nos han domesticado con esta palabra y para muchos el paradigma es que “valor agregado” es dar más de algo. Hay muchos ejemplos de esto: “quedarse más tiempo por valor agregado”, “dar algo de más, como valor agregado”, “regalar trabajo o tiempo”. Todos estos ejemplos hablan del concepto erróneo sobre valor agregado.
De acuerdo al TPS (Toyota Production System), todo aquel paso de un proceso que produce un cambio en el producto o servicio y que el cliente está dispuesto a pagar por él, se define como valor agregado.
Desde la perspectiva del cliente, podemos descomponer los pasos para realizar un producto o un servicio en cualquier industria en cualquier proceso y separar aquellos pasos que agregan valor y los que no agregan valor.
Si analizamos un Mapa de Cadena de Valor (VSM) de productos o servicios de las empresas de cualquier tipo, en ninguna de éstas se contempla como pasos del proceso al “mantenimiento”, ni siquiera al mantenimiento proactivo (preventivo o predictivo). Y cuando este es contemplado se considera como “valor no agregado” representándolo como un desperdicio de “espera”.

He visto y escuchado como se ha tratado de exaltar al departamento de mantenimiento y títulos como lean maintenance han surgido a causa de la moda del propio TPS, sin embargo, no hay nada de valor agregado en las actividades de mantenimiento.
¿Entonces qué podemos hacer? Simple. Hacer bien las cosas a la primera. De esta forma no agregaremos valor, pero trataremos de agregar el menos “valor no agregado” al proceso de operaciones.
Un simple cambio en la forma de ver las cosas, un cambio en este paradigma puede dar enormes resultados.
En donde comenzar. Con el personal principalmente. Haciéndoles entender que no estamos aquí para perder el tiempo, que mantenimiento es una de las grandes restricciones para las operaciones, y cuando hay una falla, mantenimiento es una restricción, cuando hay un mantenimiento preventivo, el equipo está detenido, mantenimiento sigue siendo una restricción.
¿Dónde no generar el menos “valor no agregado”?, en definitiva, se encuentran en dos áreas. Hacer mantenimientos mientras el equipo está produciendo, mantenimiento predictivo o basado en condición. Y una de las más importantes es arreglar los problemas que se van presentando día a día de raíz para que estos no vuelvan a ocurrir mediante el mantenimiento correctivo.
Dos herramientas esenciales para mejorar esto es sin duda la optimización de los mantenimiento planeados (PMO) y por otro lado la aplicación correcta de las herramientas de análisis de falla y causa raíz.
No se trata de aplicar estas herramientas a todo, aquí es donde el VSM ayuda mucho. Siempre hay una relación directa entre el Costo y la Confiabilidad como lo muestra la figura 2.

Si tenemos baja confiabilidad operacional, los costos se elevan, sin embargo, aumentar la confiabilidad por aumentarla, también trae costos asociados.
Nuestro deber es encontrar el punto óptimo entre costo y confiabilidad. No podemos implementar RCM, PMO, RCA, Six Sgma a todo solo porque sí, solo porque están de moda o por el afán de mejorar un indicador de disponibilidad. Tenemos que ser inteligentes en este aspecto, aplicar las herramientas donde mayor beneficio vayamos a obtener. Así es donde entra un buen VSM que nos indique por dónde comenzar.
Haciendo hincapié que la implementación de estas herramientas debe ser realizada por los mismos técnicos de mantenimiento, puesto que estos son la base de la estructura de mantenimiento. Aquí es donde comienza el cambio cultural. Dejar de pensar en los ingenieros como los indicados para realizarlas y olvidar al personal de piso en el involucramiento de las mismas.
Cursos recomendados




%252FImagen%252FRAMPREDYC-1730060420837.webp%3Falt%3Dmedia%26token%3D2634a7f0-988e-4022-b91f-382503e6e9db&w=3840&q=75)



Referencias
- Desperdicio o muda. La eliminación de desperdicios o mudas dentro de los principios del TPS (Toyota Production System) es la actividad principal en la que se basa el JIS (Just in Time) o mejor conocido en occidente como Lean Manufacturing o Manufactura Esbelta.
- Valor agregado. Se dice de las actividades de un proceso que genera alguna transformación a un producto o servicio y que el cliente final esta dispuesto a pagar por ella.
- Los mapas de cadena de valor (VSM) se utilizan para conocer a fondo el proceso tanto dentro de la planta como en la cadena de suministro. Es una representación gráfica de elementos de producción e información que permite conocer y documentar el estado actual y futuro de un proceso, es la base para el análisis del valor que se aporta al producto o servicio y es la fuente del conocimiento de las restricciones reales de una empresa, ya que permite visualizar en dónde se encuentra el valor y en dónde el desperdicio.
Autor: Edwin Guzmán King CMRP
Saltillo, Coahuila
www.gkconsulting.mx
Correo: eguzman@gkconsulting.mx
Dinos qué te ha parecido el artículo
Artículos recomendados
Tolerancias en rodamientos

ISO Commitee works on revision of ISO55002

Recolección de datos

Una Propuesta de Gestión de Activos Intangibles basada en ISO 55001 e ISO 30401 para Gestión del Conocimiento

Publica tu artículo en la revista #1 de Mantenimiento Industrial
Publicar un artículo en la revista es gratis, no tiene costo.
Solo debes asegurarte que no sea un artículo comercial.
¿Qué esperas?
O envía tu artículo directo: articulos@predictiva21.com
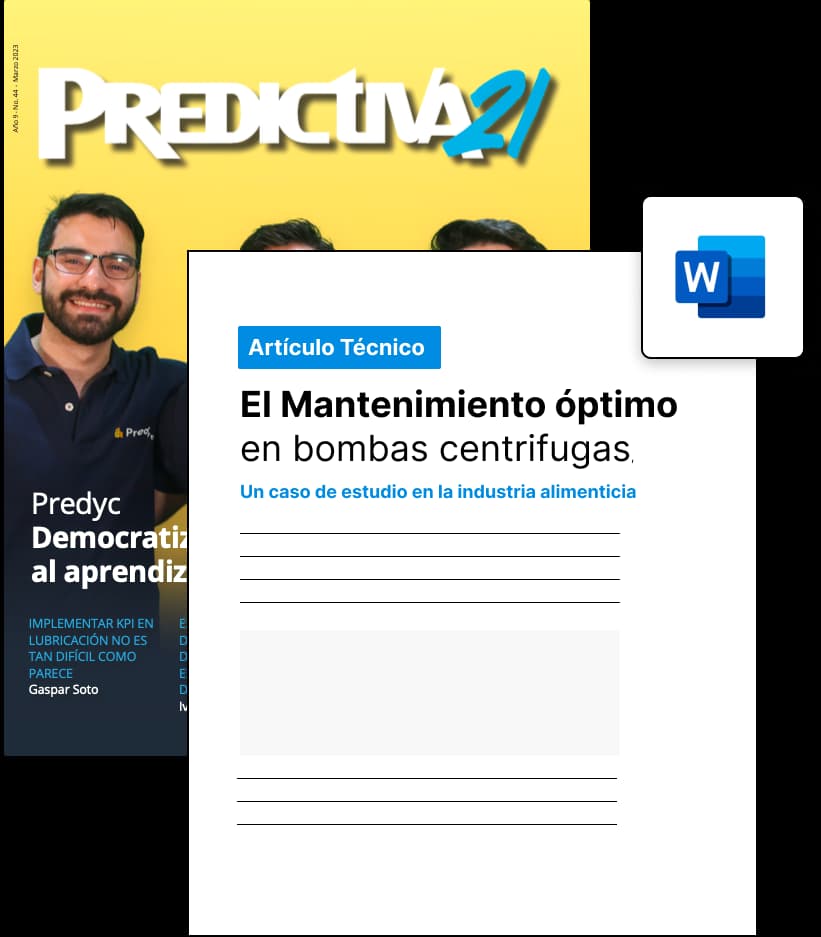